Impresión 3D por láser en polvo Para aplicaciones aeroespaciales
Índice
Impresión 3D por láser en polvotambién conocido como fusión por lecho de polvo láser (LPBF), desempeña un papel vital en el campo aeroespacial, ya que ofrece varias ventajas sobre las técnicas de fabricación tradicionales.
1. Componentes ligeros y complejos:
1. Fabricación de piezas de aviones
¿Pueden utilizarse las impresoras 3D láser de polvo para fabricar componentes de motores de aviones?
Sin duda Las impresoras 3D láser de polvo desempeñan un papel cada vez más importante en la fabricación de componentes de motores de avión. He aquí por qué:
Ventajas:
Diseños complejos y ligeros: La impresión 3D permite diseños intrincados con canales internos y celosías, imposibles con las técnicas tradicionales. Esto puede dar lugar a componentes más ligeros y resistentes, que mejoren la eficiencia del combustible y el rendimiento.
Materiales de alto rendimiento: Las impresoras LPBF pueden trabajar con aleaciones metálicas avanzadas como el titanio y el Inconel, cruciales para soportar las altas temperaturas y presiones de los motores a reacción.
Reducción de residuos y plazos de entrega: La impresión 3D suele utilizar menos material que la fabricación sustractiva tradicional, lo que minimiza los residuos. Además, puede agilizar la producción y reducir los plazos de entrega en comparación con la fundición o la forja.
Ejemplos:
Rolls-Royce: En su motor Pearl 10X, utilizan LPBF para las complejas placas de la cámara de combustión, y afirman que su eficiencia ha aumentado un 5%.
GE Aviation: Están construyendo la mayor impresora LPBF del mundo para fabricar componentes estructurales de motores a reacción para aviones de pasillo único.
Honeywell: Utilizan la impresión 3D para las toberas de combustible y otros componentes del motor, con el objetivo de reducir el peso y las emisiones.
Desafíos:
Costo: Actualmente, las impresoras LPBF son caras, aunque los costes están disminuyendo.
Titulación: Las piezas críticas para la seguridad, como los componentes del motor, requieren pruebas y certificaciones exhaustivas.
Tamaño de construcción limitado: Algunas impresoras tienen limitaciones de tamaño, aunque se están desarrollando sistemas más grandes.
LPBF destaca en la creación de piezas intrincadas y ligeras con canales internos y celosías, imposibles con los métodos convencionales. Esto reduce el peso sin comprometer la resistencia, crucial para la eficiencia del combustible y el rendimiento. Algunos ejemplos son:
Inyectores de combustible: Geometrías internas complejas para una mezcla y combustión óptimas del combustible.
Soportes satélite: Ligero y resistente para reducir el peso de la carga útil.
Intercambiadores de calor: Canales internos complejos para una transferencia de calor eficaz.
2. ejemplos de componentes de aeronaves
Componentes del sistema de combustible: Las boquillas, los inyectores y los intercambiadores de calor pueden imprimirse en 3D con canales internos complejos para mejorar el flujo de combustible y la transferencia de calor.
Componentes interiores: Los soportes, clips y otras piezas no críticas pueden imprimirse en 3D para reducir el peso y personalizarlas.
Componentes del motor: Algunas empresas están experimentando con la impresión en 3D de determinados componentes de los motores, como las cámaras de combustión y los álabes de las turbinas.
Vehículos aéreos no tripulados (UAV): Debido a su ligereza y complejidad, los vehículos aéreos no tripulados son un candidato ideal para los componentes impresos en 3D.
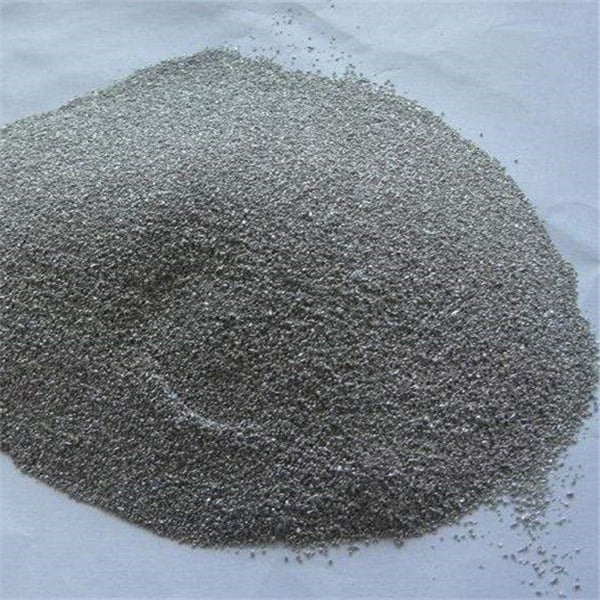
2. Piezas a medida y fabricación bajo demanda:
LPBF permite la producción rápida de piezas personalizadas, esenciales para reparaciones, prototipos y aplicaciones de bajo volumen. Esto reduce la dependencia de la fabricación a gran escala y permite plazos de entrega más rápidos. Algunos ejemplos son:
1. Velocidad y personalización:
Plazos de entrega más rápidos: LPBF elimina el utillaje tradicional, reduciendo drásticamente los plazos de entrega de piezas personalizadas. Imagine que necesita un soporte único para su avión; en lugar de meses de espera, puede imprimirlo en días.
Personalización inigualable: Las geometrías complejas y los diseños intrincados son pan comido para LPBF. Piense en paneles ligeros con estructuras internas de celosía para aviones, o accesorios a medida para experimentos en naves espaciales - las posibilidades son infinitas.
2. Ventajas para aplicaciones específicas:
Componentes interiores de aeronaves: Imagine paneles personalizados con iluminación integrada o soportes que se adaptan perfectamente a espacios no estándar. Esto ahorra peso, reduce el tiempo de montaje y mejora la estética.
Componentes de la nave espacial: El LPBF brilla con luz propia para piezas únicas y específicas de una misión, como antenas, soportes o incluso pequeños componentes de motores. Imagine imprimir un intercambiador de calor personalizado para una misión lunar específica, adaptado al entorno y a los requisitos de la misión.
Piezas de recambio: Se acabaron las esperas por piezas obsoletas o dañadas. LPBF permite la impresión bajo demanda, minimizando el tiempo de inactividad y garantizando un funcionamiento sin problemas. Imagine imprimir un engranaje poco común para un avión antiguo o una carcasa de sensor crítica para una nave espacial en órbita.
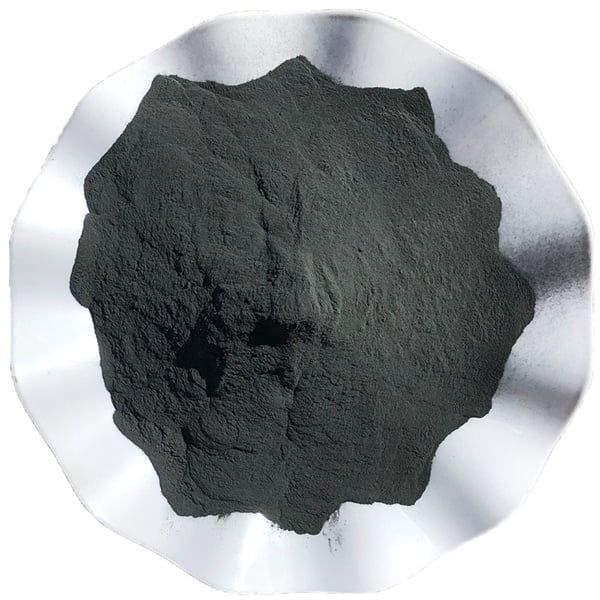
3. Materiales avanzados y rendimiento de Impresión 3D por láser en polvo
LPBF, o Laser Powder Bed Fusion, no se limita a crear piezas personalizadas, sino que libera el potencial del materiales de alto rendimiento que antes eran difíciles o imposibles de utilizar en la fabricación tradicional. Profundicemos en cómo LPBF permite a industrias como tecnología aeroespacial, cohetería y turbinas:
1. Maravillas materiales:
Aleaciones de titanio: Imagine álabes de turbina que soportan temperaturas abrasadoras y presiones intensas. El LPBF permite imprimir complejos canales de refrigeración dentro de estas palas utilizando aleaciones de titanio de alta resistencia, lo que maximiza el rendimiento y la eficiencia.
Inconel: Esta aleación de níquel-cromo ofrece una resistencia térmica y una solidez excepcionales, por lo que resulta ideal para componentes de motores de cohetes. El LPBF permite diseños complejos como cámaras de combustión e inyectores, optimizando el empuje y la eficiencia del combustible.
Aluminio-litio: Esta maravilla de la ligereza ahorra un peso precioso en las estructuras aeroespaciales. El LPBF permite imprimir costillas complejas, entramados y estructuras de nido de abeja, creando componentes resistentes pero flexibles para aviones y naves espaciales.
2. Más allá de los ejemplos:
Implantes médicos: Las aleaciones de titanio biocompatibles impresas con LPBF crean implantes duraderos y ligeros que se adaptan perfectamente a la anatomía del paciente.
Prótesis dentales: Para las prótesis y coronas impresas con LPBF se utilizan materiales resistentes y biocompatibles, como el cromo-cobalto, que ofrecen un ajuste y una función superiores.
Herramientas de vanguardia: Imagine instrumentos quirúrgicos o moldes con características intrincadas, impresos a partir de materiales resistentes al desgaste como el carburo de tungsteno - LPBF lo hace posible.
3. Desbloquear el rendimiento:
Relación resistencia-peso: El LPBF permite imprimir estructuras ligeras y complejas que son increíblemente resistentes, lo que resulta crucial para maximizar el rendimiento en el sector aeroespacial y otras aplicaciones sensibles al peso.
Resistencia a altas temperaturas: Materiales como el Inconel pueden soportar un calor extremo, lo que permite a LPBF crear componentes para motores a reacción, motores de cohetes y otros entornos de alta temperatura.
Propiedades de fatiga: Las piezas impresas con LPBF presentan una excelente resistencia a la fatiga, esencial para componentes sometidos a esfuerzos repetidos en aplicaciones como turbinas y estructuras aeronáuticas.
Material | Propiedades clave | Aplicaciones | Ventajas | Desventajas | Coste | Tratamiento posterior | Certificación |
---|---|---|---|---|---|---|---|
Aleaciones de titanio | Elevada relación resistencia/peso, resistencia a altas temperaturas, resistencia a la corrosión | Aeroespacial, médica, automoción | Excelentes propiedades mecánicas, biocompatibilidad, ligereza | Alto coste del material, complejo tratamiento posterior | Alta | Tratamiento térmico, mecanizado | Normativa estricta |
Inconel | Resistencia a altas temperaturas, solidez, resistencia a la corrosión | Aeroespacial, energía, procesamiento químico | Excelente rendimiento a altas temperaturas, resistencia a entornos agresivos | Alto coste del material, complejo tratamiento posterior | Alta | Tratamiento térmico, mecanizado | Normativa estricta |
Aluminio-Litio | Ligereza, alta resistencia, buena rigidez | Aeroespacial, automoción, defensa | Menor peso y mayor ahorro de combustible | Menor resistencia que las aleaciones de titanio, más propensas a la corrosión | Medio | Tratamiento térmico, mecanizado | Normativa menos estricta |
Acero inoxidable | Alta resistencia, resistencia a la corrosión, biocompatibilidad | Medicina, automoción, industria | Buena combinación de propiedades, rentable | Menor relación resistencia/peso que las aleaciones de titanio, no tan resistentes a la corrosión como el Inconel. | Bajo | Tratamiento térmico, mecanizado | Varía en función de la aplicación |
Acero para herramientas | Gran dureza, resistencia al desgaste y tenacidad | Herramientas, fabricación, automoción | Excelente resistencia al desgaste, larga vida útil de la herramienta | Alto coste del material, complejo tratamiento posterior | Medio | Tratamiento térmico, mecanizado | Varía en función de la aplicación |
Nylon | Ligero, resistente y flexible | Automoción, bienes de consumo, medicina | Ligero, rentable, biocompatible | Menor fuerza y resistencia a la temperatura que los metales | Bajo | Postprocesamiento mínimo | Varía en función de la aplicación |
Polipropileno | Ligereza, resistencia química, bajo coste | Bienes de consumo, envases, medicina | Ligero, rentable, buena resistencia química | Menor fuerza y resistencia a la temperatura que los metales | Bajo | Postprocesamiento mínimo | Varía en función de la aplicación |
4. Libertad de diseño y optimización:
LPBF, o Laser Powder Bed Fusion (Fusión de Lecho de Polvo Láser), no se trata sólo de imprimir formas complejas; se trata de diseñar piezas que superen los límites de lo posible. A diferencia de la fabricación tradicional, con sus limitaciones, LPBF ofrece unas prestaciones inigualables libertad de diseño y optimizacióny así conseguir componentes más ligeros, resistentes y eficientes. Profundicemos en las apasionantes posibilidades:
1. Desatar la creatividad:
Estructuras de nido de abeja: Imagine alas de avión o paneles de naves espaciales ligeros pero increíblemente resistentes, logrados mediante intrincadas estructuras de panal impresas con LPBF. Estos diseños minimizan el uso de materiales al tiempo que maximizan la resistencia y la rigidez, lo que se traduce en una reducción significativa del peso y una mayor eficiencia en el consumo de combustible.
Piezas topológicamente optimizadas: ¡Diga adiós a los diseños voluminosos e ineficaces! LPBF permite imprimir piezas optimizadas en función de requisitos específicos de carga y tensión. Imagine un componente de la suspensión de un automóvil diseñado mediante optimización topológica, que logra una resistencia óptima con un mínimo de material, ahorrando peso y mejorando el rendimiento.
Diseños biomiméticos: Inspírese en la naturaleza LPBF permite imprimir componentes inspirados en estructuras biológicas, como huesos de pájaros o telas de araña. Imagine un álabe de turbina con canales internos que imiten el ala de un pájaro, consiguiendo una transferencia de calor y una eficiencia superiores.
2. Más allá de los ejemplos:
Implantes médicos: El LPBF permite imprimir implantes con estructuras complejas y porosas que imitan el hueso natural, favoreciendo el crecimiento óseo y la osteointegración.
Bienes de consumo: Imagine bicicletas o equipamiento deportivo ligeros y de diseño ergonómico, impresos con intrincadas estructuras internas para un rendimiento y una comodidad óptimos.
Arquitectura: El LPBF abre las puertas a la impresión de intrincados componentes de construcción con menor uso de material y mayor resistencia, allanando el camino a una arquitectura sostenible e innovadora.
3. Liberar el potencial:
Reducción de peso: Al crear estructuras ligeras con un mínimo de material, el LPBF permite ahorrar mucho peso en aplicaciones críticas como la aeroespacial, la automovilística y la médica.
Rendimiento mejorado: Los diseños optimizados y la inspiración biomimética pueden mejorar el rendimiento en áreas como la transferencia de calor, el flujo de fluidos y la resistencia estructural.
Sostenibilidad: La reducción del uso de materiales y el aligeramiento de los componentes se traducen en un menor impacto ambiental durante todo el ciclo de vida del producto.
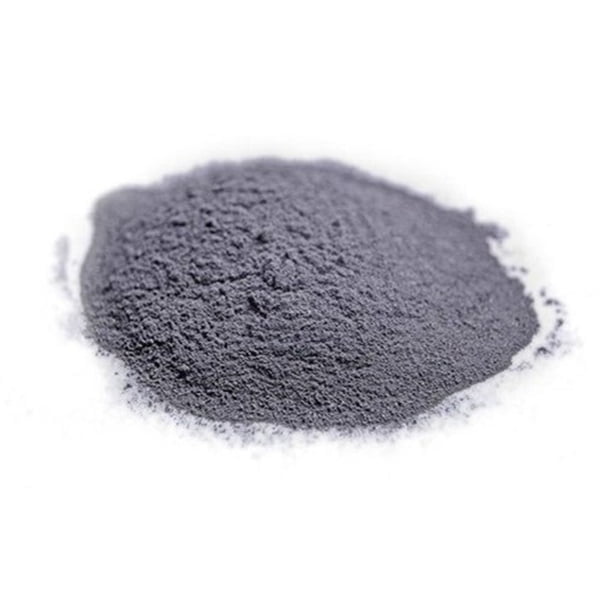
5. Retos y consideraciones:
Aunque el LPBF ofrece posibilidades apasionantes, es crucial reconocer los retos que conlleva esta tecnología:
1. Costo:
Coste de la máquina: En comparación con los equipos de fabricación tradicionales, las máquinas LPBF pueden ser significativamente más caras, especialmente en el caso de las impresoras de alto rendimiento. Esto limita la accesibilidad y aumenta el coste por pieza.
Coste del material: Los materiales de alto rendimiento como las aleaciones de titanio y el Inconel son intrínsecamente caros, y la forma en polvo utilizada en LPBF añade un coste adicional en comparación con los materiales a granel.
2. Postprocesamiento:
Eliminación de soporte: El LPBF suele requerir la impresión de estructuras de soporte para geometrías complejas. Retirar estos soportes puede llevar mucho tiempo y requerir técnicas especializadas, lo que aumenta el coste y la complejidad generales.
Acabado: Dependiendo de la aplicación, las piezas pueden requerir tratamiento térmico, mecanizado u otros pasos de acabado para conseguir las propiedades deseadas, lo que aumenta aún más el tiempo y el coste de procesamiento.
3. Certificación:
Normativa estricta: Para aplicaciones en sectores críticos como el aeroespacial o el médico, las piezas deben cumplir estrictas normativas y normas de seguridad. Esto suele implicar exhaustivos procesos de ensayo y cualificación, que pueden resultar largos y costosos.
Normas limitadas: Aunque las normas de LPBF están evolucionando, no están tan maduras como las de los métodos de fabricación tradicionales. Esto puede crear incertidumbre y obstáculos adicionales para la certificación.
4. Consideraciones adicionales:
Experiencia en diseño: La utilización eficaz de LPBF requiere un conocimiento especializado de las capacidades y limitaciones de la tecnología, lo que aumenta la complejidad general del proyecto.
Control de calidad: Garantizar una calidad y repetibilidad constantes de las piezas puede ser un reto debido a factores como las características del polvo, los parámetros del láser y la calibración de la máquina.
Impacto medioambiental: Aunque el LPBF puede ofrecer un ahorro de material en comparación con los métodos tradicionales, es necesario abordar el consumo de energía y la gestión de los residuos de polvo para una adopción sostenible.
Compartir
MET3DP Technology Co., LTD es un proveedor líder de soluciones de fabricación aditiva con sede en Qingdao, China. Nuestra empresa está especializada en equipos de impresión 3D y polvos metálicos de alto rendimiento para aplicaciones industriales.
Solicite información para obtener el mejor precio y una solución personalizada para su empresa.
Artículos relacionados
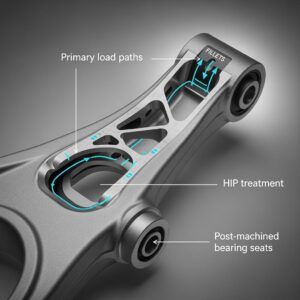
Metal 3D Printing for U.S. Automotive Lightweight Structural Brackets and Suspension Components
Leer Más "Acerca de Met3DP
Actualización reciente
Nuestro producto
CONTACTO
¿Tiene alguna pregunta? ¡Envíenos un mensaje ahora! Atenderemos su solicitud con todo un equipo tras recibir su mensaje.