Corrosion-Resistant Pump Housings via Additive Manufacturing
Índice
Introduction: The Critical Role of Corrosion-Resistant Pump Housings in Marine Environments
The maritime world, encompassing everything from global commercial shipping and naval defense to offshore energy exploration and aquaculture, operates under some of the most demanding conditions on Earth. Central to the functionality and safety of countless marine systems are pumps, tireless workhorses circulating vital fluids like seawater for cooling, ballast water for stability, bilge water for safety, and potable water for crew. At the heart of these pumps lies the housing – the protective shell that contains the impeller, seals, and bearings, guides fluid flow, and withstands immense operational pressures. However, in the marine environment, pump housings face a relentless adversary: corrosion.
Seawater, a complex electrolyte rich in chloride ions, is notoriously aggressive towards most metals. This leads to various forms of corrosion, including:
- General Corrosion: Uniform thinning of the material surface.
- Pitting Corrosion: Localized attack creating small holes or pits, which can penetrate the housing wall.
- Crevice Corrosion: Intense localized corrosion occurring in stagnant microenvironments like gasket seals or under deposits.
- Galvanic Corrosion: Accelerated corrosion when dissimilar metals are in electrical contact in an electrolyte (seawater).
- Erosion-Corrosion: Combined mechanical wear from flowing fluids (especially those containing abrasives like sand) and electrochemical corrosion.
- Stress Corrosion Cracking (SCC): Cracking caused by the combined action of tensile stress and a corrosive environment.
Furthermore, marine growth (biofouling) can attach to surfaces, impeding flow, accelerating localized corrosion beneath the organisms, and increasing maintenance requirements. The failure of a pump housing due to corrosion can have severe consequences, ranging from costly downtime and repairs to catastrophic system failures compromising vessel safety or operational integrity. Imagine a critical cooling pump failing on a large container ship, or a ballast pump malfunctioning during a delicate offshore operation – the implications are significant.
Traditionally, marine pump housings have been manufactured using methods like sand casting, investment casting, or machining from wrought stock, often employing materials like bronze, certain stainless steels, or specialized alloys. While effective, these methods can have limitations:
- Design Constraints: Casting tooling imposes limitations on geometric complexity, potentially hindering optimal hydraulic efficiency. Internal features can be difficult or impossible to create.
- Long Lead Times: Pattern making, casting, and subsequent machining can take weeks or months, especially for custom designs or low-volume replacements.
- Residuos materiales: Machining from solid blocks generates significant scrap material (buy-to-fly ratio).
- Inventory Costs: Maintaining stocks of diverse spare pump housings for various systems across a fleet or platform is expensive.
Aquí es donde Fabricación aditiva (AM), commonly known as metal Impresión 3D, emerges as a transformative technology for producing high-performance, corrosion-resistant marine pump housings. By building parts layer-by-layer directly from digital designs using specialized metal powders, AM overcomes many traditional limitations. It enables the creation of highly complex, optimized geometries that were previously unmanufacturable, facilitates rapid prototyping and on-demand production, and allows for the use of advanced, highly corrosion-resistant alloys tailored to the harsh marine environment. This shift towards additive techniques represents a significant leap forward, offering engineers and procurement managers unprecedented flexibility, speed, and performance potential for critical marine components. Companies specializing in impresión 3D en metal, like Met3dp, provide the expertise and advanced capabilities needed to leverage this technology effectively for demanding applications like marine pump housings.
Demanding Applications: Where are Corrosion-Resistant Pump Housings Utilized?
The need for robust, corrosion-resistant pump housings permeates virtually every sector operating on or interacting with the sea. The specific demands may vary, but the fundamental requirement for longevity and reliability in the face of saltwater and harsh conditions remains constant. Let’s explore the key application areas:
1. Commercial Shipping & Naval Vessels:
- Engine Cooling Systems: Seawater cooling pumps are vital for main engines and auxiliary generators. Housing failure leads directly to overheating and potential engine damage or shutdown. Materials must resist hot saltwater and potential contaminants.
- Ballast Water Systems: Pumps manage the intake, discharge, and treatment of ballast water for vessel stability. Housings must withstand varying water quality, potential sediment abrasion, and any chemicals used in ballast water treatment systems (BWTS). Regulations often mandate specific performance and material standards.
- Bilge Pumping Systems: Removing accumulated water from the hull is critical for safety. Bilge pumps handle oily water, seawater ingress, and potential debris. Housings need durability and resistance to mixed contaminants.
- Firefighting Systems: Seawater fire pumps must be instantly ready. Housings require high reliability and resistance to corrosion during long periods of standby in a saltwater-charged system.
- Sanitary & Potable Water Systems: While often handling fresh water, these systems can still be susceptible to corrosion, especially components near saltwater interfaces or if desalination systems are employed.
2. Offshore Oil & Gas Platforms:
- Seawater Lift Pumps: Huge pumps lift massive volumes of seawater onto platforms for cooling, injection (to maintain reservoir pressure), and utility purposes. Housings must handle high flow rates, high pressures, and potentially abrasive particles or H2S (sour) environments. Reliability is paramount due to the remote location and high cost of failure.
- Firewater Pumps: Similar to ships, offshore platforms rely on robust firewater systems charged with seawater. Pump housings must guarantee performance after potentially long standby periods.
- Cooling Water Circulation: Numerous processes on platforms require cooling, often using seawater. Pump housings in these circuits face continuous exposure.
- Subsea Pumping Systems: Pumps located on the seabed for boosting oil/gas flow or injection face extreme pressures and the corrosive deep-sea environment. Housings require exceptional material integrity and design sophistication.
3. Desalination Plants:
- Seawater Intake Pumps: The first stage involves pumping large volumes of raw seawater. Housings face direct exposure to saltwater, marine life, and potential abrasives.
- High-Pressure Pumps (Reverse Osmosis): These pumps operate at very high pressures to force water through RO membranes. Housings must withstand these pressures while resisting the concentrated brine reject stream, which is even more corrosive than standard seawater. Materials like Duplex or Super Duplex stainless steels are common, but AM offers potential with materials like 316L or even custom alloys for specific conditions.
- Brine Discharge Pumps: Handling the highly concentrated, corrosive brine byproduct requires robust housing materials.
4. Aquaculture (Fish Farming):
- Water Circulation Pumps: Maintaining water quality in fish pens or onshore tanks requires continuous pumping and circulation, often using seawater. Housings need long-term corrosion resistance and must not leach harmful substances into the water. Biofouling resistance (offered by CuNi alloys) is a significant advantage here to maintain flow rates and reduce cleaning cycles.
- Feeding Systems: Pumps may be used in automated liquid feed delivery systems.
5. Marine Research & Exploration:
- Sampling Pumps: Used on research vessels or autonomous underwater vehicles (AUVs) to collect water samples at various depths. Housings must be corrosion-resistant and potentially pressure-resistant for deep-sea applications.
- Equipment Cooling: Scientific equipment onboard may require seawater cooling loops.
6. Power Generation (Coastal Plants):
- Cooling Water Intake: Similar to desalination, coastal power plants often use vast quantities of seawater for cooling condensers. Pump housings in these systems must be durable and resistant to corrosion and biofouling.
Functional Requirements Across Applications:
- Resistencia a la corrosión: Primary requirement – resistance to general, pitting, crevice, and galvanic corrosion from seawater, brine, or treated water.
- Pressure Containment: Ability to withstand operating pressures without leaking or bursting.
- Resistencia a la abrasión: Necessary where fluids contain sand, silt, or other abrasive particles (e.g., intake pumps, bilge).
- Resistencia a las bioincrustaciones: Desirable to maintain hydraulic efficiency and reduce cleaning maintenance, especially in static or low-flow conditions. Copper-nickel alloys excel here.
- Mechanical Strength & Toughness: Ability to handle operational stresses, vibrations, and potential impacts.
- Resistencia a la temperatura: Relevant for engine cooling or other systems operating at elevated temperatures.
- Manufacturability/Repairability: While AM offers new manufacturing routes, considerations for integration and potential field repair might influence design or material choices.
Understanding these diverse and demanding applications underscores why generic solutions often fall short. The ability of metal additive manufacturing to create tailored pump housings from highly resistant materials like 316L stainless steel or specialized CuNi alloys offers a significant advantage in meeting these specific challenges head-on. Procurement managers and engineers sourcing components for these critical systems must prioritize suppliers with proven expertise in handling these demanding requirements and the advanced materials needed.
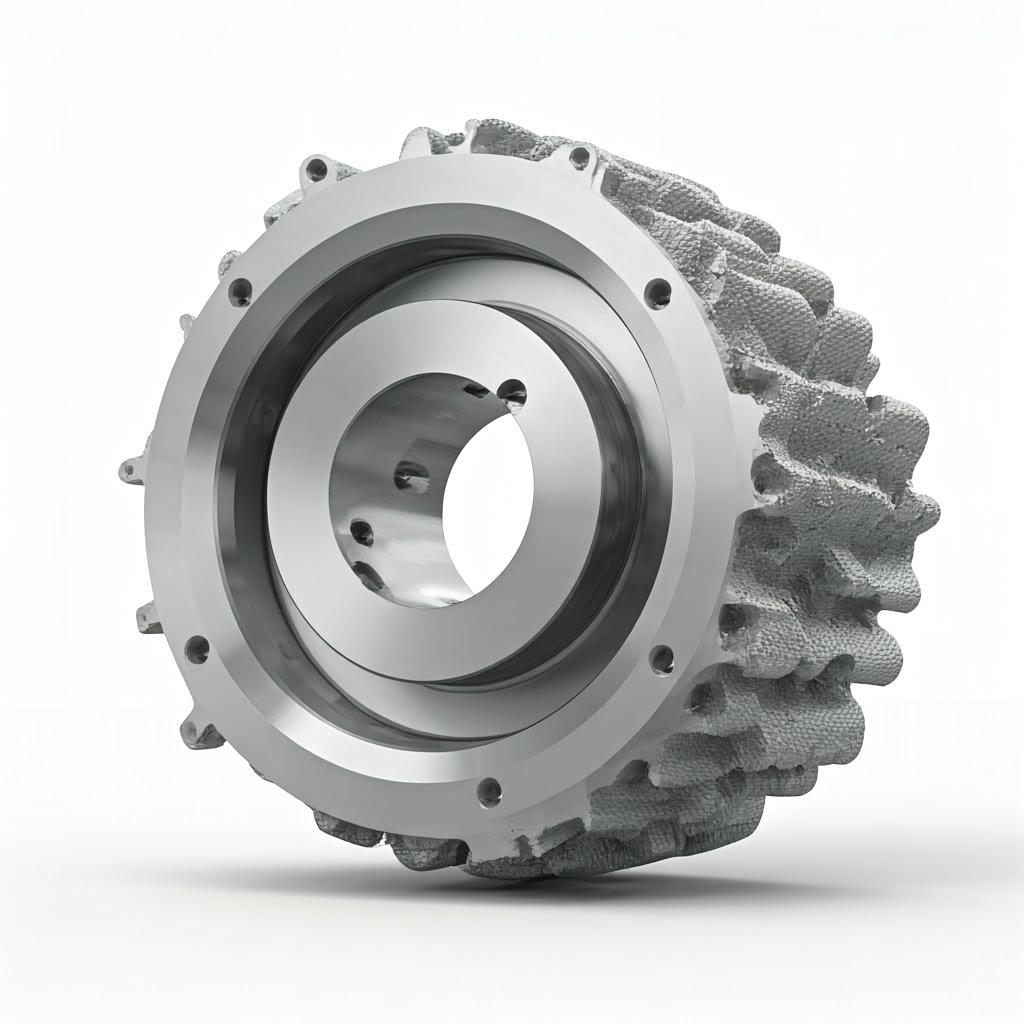
Additive Advantage: Why Choose Metal 3D Printing for Marine Pump Housings?
While traditional manufacturing methods like casting and machining have served the marine industry for decades, metal additive manufacturing presents a compelling suite of advantages, particularly for complex, high-performance components like pump housings operating in corrosive environments. Opting for AM isn’t just about adopting a new technology; it’s about unlocking tangible benefits in performance, speed, design flexibility, and supply chain efficiency. Let’s break down why metal 3D printing is increasingly the preferred choice for forward-thinking marine engineers and procurement specialists:
1. Unprecedented Design Freedom & Performance Optimization:
- Geometrías complejas: Traditional methods struggle with intricate internal channels, complex volute shapes, or integrated features. AM builds layer-by-layer, enabling the creation of highly optimized internal flow paths (volutes, diffusers) designed using Computational Fluid Dynamics (CFD) to maximize hydraulic efficiency, minimize cavitation, and reduce energy consumption.
- Optimización de la topología: Algorithms can redesign the housing structure to place material only where it’s structurally needed, significantly reducing weight while maintaining or even increasing strength. This is crucial for weight-sensitive applications on ships or offshore platforms.
- Consolidación de piezas: Multiple components previously manufactured separately and then assembled (e.g., housing body, mounting flanges, internal guide vanes) can potentially be printed as a single, monolithic part. This eliminates joints (potential leak paths or corrosion sites), simplifies assembly, and reduces inventory complexity.
- Personalización: AM allows for easy design iteration and customization without the prohibitive costs of new tooling associated with casting. Need a slightly modified port configuration or mounting point for a specific installation? AM makes it feasible even for small batches or single units.
2. Accelerated Prototyping and Reduced Lead Times:
- Iteración rápida: Developing new pump designs or optimizing existing ones often requires multiple prototypes. AM allows engineers to print and test functional prototypes in days or weeks, compared to months for traditional casting tooling and production. This dramatically speeds up the R&D cycle.
- Producción a la carta: For spare parts or urgent replacements, AM offers a significant advantage. Instead of relying on large inventories or facing long lead times for traditionally manufactured spares (especially for older or obsolete pump models), a digital file can be printed on demand when needed. This minimizes downtime and reduces warehousing costs. A reliable AM service provider with efficient operations can deliver critical parts much faster than conventional supply chains.
3. Material Versatility and Optimized Properties:
- Aleaciones avanzadas: AM processes like Laser Powder Bed Fusion (LPBF) and Selective Electron Beam Melting (SEBM) can effectively process highly corrosion-resistant materials like marine-grade 316L stainless steel, specialized copper-nickel alloys (like CuNi30Mn1Fe for biofouling resistance), duplex/super duplex steels, and even titanium alloys for specific high-performance or lightweight needs.
- Fine Microstructure: The rapid solidification inherent in many AM processes can lead to fine-grained microstructures, which can enhance mechanical properties and, in some cases, corrosion resistance compared to coarser-grained cast materials. Proper process control and post-processing (like heat treatment) are crucial to achieve these benefits consistently. Companies like Met3dp, with expertise in both producción avanzada de polvo and printing processes, ensure optimal material properties.
4. Supply Chain Resilience and Digital Inventory:
- Reduced Reliance on Traditional Foundries: Diversifying manufacturing methods reduces risk. AM provides an alternative production route, less susceptible to disruptions that might affect traditional casting foundries (e.g., tooling issues, capacity limitations).
- Digital Warehouse: Instead of physical stock, designs are stored as digital files (CAD data). Parts can be printed anywhere in the world where a suitable AM facility exists, closer to the point of need, reducing shipping times and costs. This concept of a “digital inventory” is particularly valuable for global maritime operations.
- Obsolescence Management: Finding spare parts for aging equipment can be a major headache. If the original casting patterns are lost or the manufacturer is out of business, AM allows reverse engineering (via 3D scanning) and direct printing of replacement parts, extending the life of valuable assets.
5. Potential for Cost-Effectiveness (Beyond Piece Price):
- Reducción de los residuos materiales: AM is an additive process, using only the material needed for the part and support structures. This contrasts sharply with subtractive machining, which can waste a significant amount of expensive raw material.
- Eliminación de herramientas: The high cost and long lead times associated with creating molds or patterns for casting are completely eliminated. This makes AM highly competitive for low-to-medium volume production runs, prototypes, and custom parts.
- Total Cost of Ownership: While the per-part cost of an AM component might sometimes be higher than a mass-produced cast part, considering factors like reduced downtime (faster replacement), lower inventory holding costs, improved performance/efficiency leading to energy savings, and extended component lifespan due to optimized design and materials often reveals a lower total cost of ownership.
Comparison: AM vs. Traditional Methods for Marine Pump Housings
Característica | Fabricación aditiva de metales (AM) | Traditional Casting (e.g., Sand Casting) | Traditional Machining (from Billet) |
---|---|---|---|
Libertad de diseño | Very High (complex internal channels, topology optimization) | Moderate (limited by tooling, draft angles) | Moderate (depends on tool access) |
Complejidad | Handles high complexity efficiently | High complexity increases tooling cost/difficulty | High complexity increases machining time/cost |
Plazo de entrega (Proto) | Short (Days/Weeks) | Long (Weeks/Months – pattern making) | Moderate (depends on complexity/setup) |
Plazo de entrega (Prod) | Moderate (Scalable, good for low/medium vol) | Moderate-Long (Depends on tooling/foundry schedule) | Moderate-Long (Depends on machining time) |
Coste de utillaje | Ninguno | High (Patterns, Molds) | Low (Fixturing may be needed) |
Residuos materiales | Low (Support structures) | Moderate (Gating, Risers) | High (Chips, Swarf) |
Consolidación de piezas | Excellent Potential | Limitado | Limitado |
Opciones de material | Growing Range (incl. 316L, CuNi, Ti, Duplex) | Established Range (Bronze, Cast Iron, SS) | Wide Range (Wrought alloys) |
Min. Order Qty | One (Ideal for spares/custom) | Higher (Economies of scale needed for casting) | One (Can be costly for single complex parts) |
Optimización | High (CFD-driven shapes, topology opt.) | Limited (Restricted by casting process) | Limited (Restricted by machining access) |
Exportar a hojas
In summary, metal 3D printing offers a powerful combination of design agility, speed, material capability, and supply chain advantages that directly address the challenges of producing reliable, high-performance pump housings for the demanding marine industry. It empowers engineers to design better, more efficient pumps and provides procurement managers with a flexible, responsive manufacturing solution for critical components.
Material Matters: Selecting the Right Metal Powders for Marine Pump Durability
Choosing the correct material is arguably the most critical decision when designing and manufacturing pump housings destined for the corrosive marine environment. While additive manufacturing offers design flexibility, the inherent properties of the chosen metal powder dictate the component’s ultimate resistance to saltwater attack, its mechanical integrity under pressure, and its overall lifespan. For marine applications, two materials stand out due to their excellent performance profile and suitability for AM processes: Acero inoxidable 316L y Copper-Nickel Alloy CuNi30Mn1Fe.
Understanding the characteristics of these materials, and why high-quality powder is essential, is key for engineers and procurement managers aiming for long-term reliability.
1. 316L Stainless Steel (UNS S31603): The Workhorse for Marine Corrosion Resistance
- Composición: An austenitic stainless steel alloy containing Chromium (Cr), Nickel (Ni), and crucially, Molybdenum (Mo). The ‘L’ denotes low carbon content (<0.03%), which improves weldability and prevents sensitization (loss of corrosion resistance near welds due to chromium carbide precipitation). Typical composition: ~16-18% Cr, ~10-14% Ni, ~2-3% Mo, <0.03% C, balance Fe.
- Key Properties for Marine Pumps:
- Excellent Pitting and Crevice Corrosion Resistance: The addition of Molybdenum significantly enhances resistance to localized chloride attack (pitting and crevice corrosion), which is the primary threat from seawater. This makes 316L far superior to other common stainless grades like 304 in marine environments.
- Buena resistencia general a la corrosión: Offers robust resistance to uniform corrosion in marine atmospheres and splash zones.
- Good Mechanical Strength and Ductility: Provides adequate strength for typical pump housing pressure requirements and good toughness to resist fracture. AM-produced 316L often exhibits higher strength than its wrought or cast counterparts due to the fine microstructure, although heat treatment is usually required to optimize ductility and relieve stress.
- Buena conformabilidad y soldabilidad: The low carbon content makes it readily weldable if post-fabrication assembly is needed, without requiring post-weld heat treatment to restore corrosion resistance (unlike standard 316).
- Availability and Cost-Effectiveness: 316L is a widely available and relatively cost-effective corrosion-resistant alloy, making it a popular choice for many marine components.
- AM Suitability: 316L is one of the most well-characterized and commonly used materials in metal AM (especially LPBF). It processes well, resulting in dense parts with good mechanical properties when using optimized parameters and high-quality powder.
- Limitaciones: While excellent, 316L can still be susceptible to crevice corrosion in very aggressive, stagnant conditions (e.g., under gaskets or deposits) and offers limited resistance to biofouling. In highly demanding applications (e.g., high-pressure brine, very high temperatures), more specialized alloys might be considered.
2. CuNi30Mn1Fe (e.g., C71500 based): The Anti-Biofouling Champion
- Composición: A copper-nickel alloy, typically containing around 70% Copper (Cu), 30% Nickel (Ni), with small but important additions of Manganese (Mn) and Iron (Fe) for improved strength and corrosion resistance, particularly erosion-corrosion resistance.
- Key Properties for Marine Pumps:
- Outstanding Biofouling Resistance: This is the defining characteristic of CuNi alloys. Copper ions released from the surface are toxic to marine organisms, preventing the attachment and growth of barnacles, mussels, algae, etc. This maintains smooth surfaces for optimal hydraulic efficiency and significantly reduces the need for mechanical cleaning. Ideal for intake screens, piping, and pump housings where flow could be impeded by marine growth.
- Excellent General Seawater Corrosion Resistance: Forms a stable, adherent protective film in seawater, offering long service life even with continuous immersion.
- Good Resistance to Erosion-Corrosion: The Mn and Fe additions improve resistance to the combined effects of flowing seawater (especially containing sand/silt) and corrosion. Crucial for pump impellers and housings handling abrasive fluids.
- Buena resistencia y ductilidad: Offers sufficient mechanical properties for many pump housing applications.
- Good Thermal Conductivity: Can be advantageous in heat exchanger applications, though less critical for standard pump housings.
- AM Suitability: Copper alloys can be more challenging to process via AM (especially LPBF) due to their high reflectivity and thermal conductivity compared to steels or titanium. However, significant progress has been made, and specialized parameters and machine modifications allow successful printing of CuNi alloys. Achieving high density and desired properties requires careful process control and often specific powder characteristics (e.g., morphology, particle size distribution). Electron Beam Melting (SEBM) can sometimes be advantageous for processing copper alloys due to better energy absorption.
- Limitaciones: Generally lower strength compared to stainless steels like 316L or duplex grades. Higher cost than 316L. May be susceptible to sulfide attack in polluted or stagnant seawater conditions.
Comparison Table: 316L vs. CuNi30Mn1Fe for Marine Pump Housings
Propiedad | Acero inoxidable 316L | CuNi30Mn1Fe (Copper-Nickel) | Comentarios |
---|---|---|---|
Pitting/Crevice Resist. | Excellent (due to Mo) | Bien | 316L generally better in stagnant chloride conditions without biofouling. |
General Corrosion | Bien | Excelente | Both perform well, CuNi often forms a more passive protective layer. |
Resistencia a las bioincrustaciones | Pobre | Destacado | Key advantage for CuNi in many marine applications. |
Erosion-Corrosion Resist. | Moderado | Very Good (due to Mn, Fe additions) | CuNi often preferred for flows containing abrasives. |
Resistencia mecánica | Good (Higher than CuNi) | Moderado | 316L typically stronger, especially AM-processed. |
Ductility/Toughness | Bien | Bien | Both offer good toughness. |
Soldabilidad | Excellent (Low Carbon) | Bien | Both are weldable with appropriate procedures. |
AM Processability | Excellent (Well-established for LPBF) | Moderate-Good (Requires optimization) | 316L is easier to print; CuNi requires more careful parameter control. |
Coste | Moderado | Más alto | 316L is generally more cost-effective raw material. |
Primary Advantage | Pitting resistance, Strength, Cost | Biofouling & Erosion-Corrosion Resist. | Choose based on the most critical failure mode or performance requirement. |
Exportar a hojas
La importancia de los polvos metálicos de alta calidad:
Regardless of the alloy chosen, the quality of the metal powder used in the AM process is paramount to achieving a dense, defect-free pump housing with the expected mechanical properties and corrosion resistance.
- Esfericidad y fluidez: Powders must be highly spherical with good flowability to ensure uniform spreading across the build plate in Powder Bed Fusion processes (LPBF/SEBM). Poor flow can lead to uneven layers, voids, and defects.
- Distribución del tamaño de las partículas (PSD): A controlled PSD is critical for achieving high packing density in the powder bed, which translates to higher density in the final part. Fines can affect flowability, while overly large particles can lead to poor surface finish.
- Chemical Purity: Impurities (like excessive oxygen or nitrogen) or cross-contamination can significantly degrade the mechanical properties and corrosion resistance of the final part. Strict quality control during powder manufacturing and handling is essential.
- Absence of Satellites and Porosity: High-quality powders should have minimal ‘satellites’ (smaller particles attached to larger ones) and low internal porosity, both of which can negatively impact flow, packing, and final part density.
Met3dp’s Commitment to Powder Quality: Recognizing the critical link between powder quality and final part performance, companies like Met3dp invest heavily in advanced powder production technologies. Met3dp utilizes industry-leading Atomización de gas (GA) y Proceso de electrodos rotativos de plasma (PREP) tecnologías.
- Atomización de gases: Employs unique nozzle and gas flow designs to produce metallic spheres with exceptional sphericity and flowability, crucial for reliable AM processing.
- PREP: Known for producing highly spherical powders with very low satellite content and high purity, ideal for demanding applications where material integrity is non-negotiable.
By manufacturing a wide range of high-quality metal powders, including stainless steels and potentially custom alloys suitable for marine environments like specialized CuNi grades, Met3dp ensures that the starting material meets the stringent requirements for producing reliable, corrosion-resistant marine pump housings via additive manufacturing. Their expertise covers the entire chain, from powder creation to printing using advanced SEBM printers, ensuring optimal outcomes for clients in demanding sectors like marine engineering. Selecting a supplier like Met3dp, with demonstrated control over powder quality, provides confidence that the chosen material’s potential will be fully realized in the final component. Sources and related content
Designing for Additive Success: Optimizing Marine Pump Housings for 3D Printing
Leveraging metal additive manufacturing for marine pump housings goes beyond simply replicating existing cast or machined designs. To truly unlock the benefits of AM – improved performance, reduced weight, faster production, and enhanced features – components must be designed para the process. This philosophy, known as Design for Additive Manufacturing (DfAM), involves rethinking the part’s geometry to suit the layer-by-layer building process, capitalize on its strengths, and mitigate its constraints. Optimizing a marine pump housing for AM requires collaboration between hydraulic engineers, mechanical designers, and AM specialists. Here are key considerations for success:
1. Embracing Geometric Complexity for Hydraulic Efficiency:
- Vías de flujo optimizadas: Traditional manufacturing often compromises hydraulic efficiency due to limitations in creating smooth, complex curves internally. AM excels here. Computational Fluid Dynamics (CFD) can be used to simulate fluid flow within the pump housing, allowing designers to sculpt volutes, diffusers, and internal passages with organic, highly efficient shapes that minimize turbulence, pressure drops, and the risk of cavitation. This can lead to significant improvements in pump efficiency and energy savings over the component’s lifetime.
- Integrated Features: Features like guide vanes, flow straighteners, or even integrated sensor ports (for pressure, temperature, or vibration monitoring) can be designed directly into the housing structure. This eliminates assembly steps, potential leak points, and reduces overall part count.
- Conformal Cooling/Heating Channels (Advanced): For specific applications requiring temperature control (e.g., pumping viscous fluids or in extreme ambient conditions), AM allows the integration of complex internal channels that conform precisely to the housing’s shape, providing highly efficient heating or cooling right where it’s needed.
2. Designing for Self-Support and Reduced Build Time/Cost:
- Estructuras de apoyo: Most metal AM processes, particularly Laser Powder Bed Fusion (LPBF), require support structures for overhanging features (typically below 45 degrees from the horizontal) and to anchor the part to the build plate, managing thermal stresses. These supports consume extra material, add build time, and require removal in post-processing, adding cost and complexity.
- Ángulos autoportantes: Designing features with angles greater than 45 degrees eliminates the need for supports in those areas. Where overhangs are unavoidable, aim for the steepest possible angle the specific machine/material combination can reliably produce without supports.
- Chamfers and Fillets: Replacing sharp horizontal overhangs with chamfers or fillets can often make them self-supporting.
- Teardrop/Diamond Shapes for Horizontal Holes: Instead of printing perfectly circular horizontal holes (which require support at the top), designing them with a “teardrop” or diamond profile allows them to be self-supporting. Critical circularity can be achieved later via machining if required.
- Build Orientation Planning: The orientation in which the pump housing is printed significantly impacts support requirements, surface finish on different faces, build time, and potential residual stresses. Design with a preferred build orientation in mind, often collaborating with the AM service provider like Met3dp, whose application engineers can advise on the optimal strategy based on their métodos de impresión and machine capabilities.
3. Minimum Feature Sizes and Wall Thickness:
- Resolvable Features: AM processes have limits on the smallest features they can accurately produce. This includes pin diameters, slot widths, and embossed/engraved details. Designers must adhere to the minimum feature size guidelines provided by the AM service partner for the specific machine and material.
- Espesor de pared: Very thin walls can be challenging to print reliably, prone to distortion, and may lack structural integrity or pressure containment capability. Conversely, overly thick sections can increase build time, material consumption, and residual stresses. Aim for optimized, relatively uniform wall thicknesses where possible, typically above 0.5mm – 1mm depending on the process and geometry. Consult with the AM provider for specific recommendations.
4. Powder Removal Considerations:
- Polvo atrapado: Complex internal channels, inherent in many pump designs, can trap unfused metal powder after the build. Designers must incorporate escape holes or access points to allow for effective powder removal during post-processing (typically via vibration, compressed air, or specialized flushing). Incomplete powder removal can add weight, potentially contaminate the system fluid, or sinter during heat treatment, blocking channels.
- Internal Channel Design: Design internal channels to be large enough and smooth enough to facilitate powder flow-out. Avoid sharp corners or dead ends where powder can easily become trapped.
5. Topology Optimization and Lightweighting:
- Structural Efficiency: Marine applications, especially onboard ships or subsea equipment, often benefit from weight reduction. Topology optimization software analyzes the load paths within the pump housing and removes material from non-critical areas, resulting in an organic, load-bearing structure that is significantly lighter but meets all strength and stiffness requirements.
- Estructuras reticulares: For non-pressure-bearing sections or where specific stiffness/vibration damping is needed, internal lattice structures can be incorporated to reduce mass while maintaining structural integrity.
- Material Savings: While driven by performance, lightweighting also directly translates to reduced material consumption and potentially faster build times, contributing to cost savings.
6. Designing for Post-Processing:
- Tolerancias de mecanizado: Critical interfaces like flange faces, O-ring grooves, bearing seats, and threaded ports will typically require post-machining to achieve the necessary tolerances and surface finishes. Designers must add sufficient extra material (machining stock, typically 0.5mm – 2mm) in these areas to allow for clean-up during CNC machining.
- Accesibilidad: Ensure that areas requiring machining or specific surface finishing are accessible to tools after printing and support removal.
- Puntos de fijación: Consider adding temporary features or designing existing features to facilitate secure and accurate fixturing of the part during post-machining operations.
DfAM Principles Summary Table:
DfAM Principle | Benefit(s) | Consideraciones clave |
---|---|---|
Geometrías complejas | Improved hydraulic efficiency, reduced cavitation, integrated features | CFD analysis, smooth transitions, minimum feature size |
Self-Supporting Design | Reduced support material, faster build, lower post-processing cost | Angles >45°, chamfers/fillets, teardrop holes, build orientation planning |
Optimized Wall Thickness | Structural integrity, reduced stress/distortion, material/time savings | Process limitations (min/max thickness), uniformity, pressure containment needs |
Powder Removal Access | Complete powder evacuation, prevents contamination/blockages | Escape holes, channel diameter/smoothness, avoid dead ends |
Topology Optimization | Significant weight reduction, improved structural efficiency, material savings | Load case definition, software use, manufacturability checks |
Designing for Machining | Achieves tight tolerances/finishes on critical surfaces | Adding machining stock, tool accessibility, fixturing strategies |
Exportar a hojas
By embracing DfAM principles, manufacturers can move beyond simply replacing traditionally made pump housings and start creating next-generation components specifically tailored to the unique capabilities of metal 3D printing, delivering superior performance and reliability in demanding marine environments. Partnering with an experienced AM provider who offers engineering support is crucial for effective DfAM implementation.
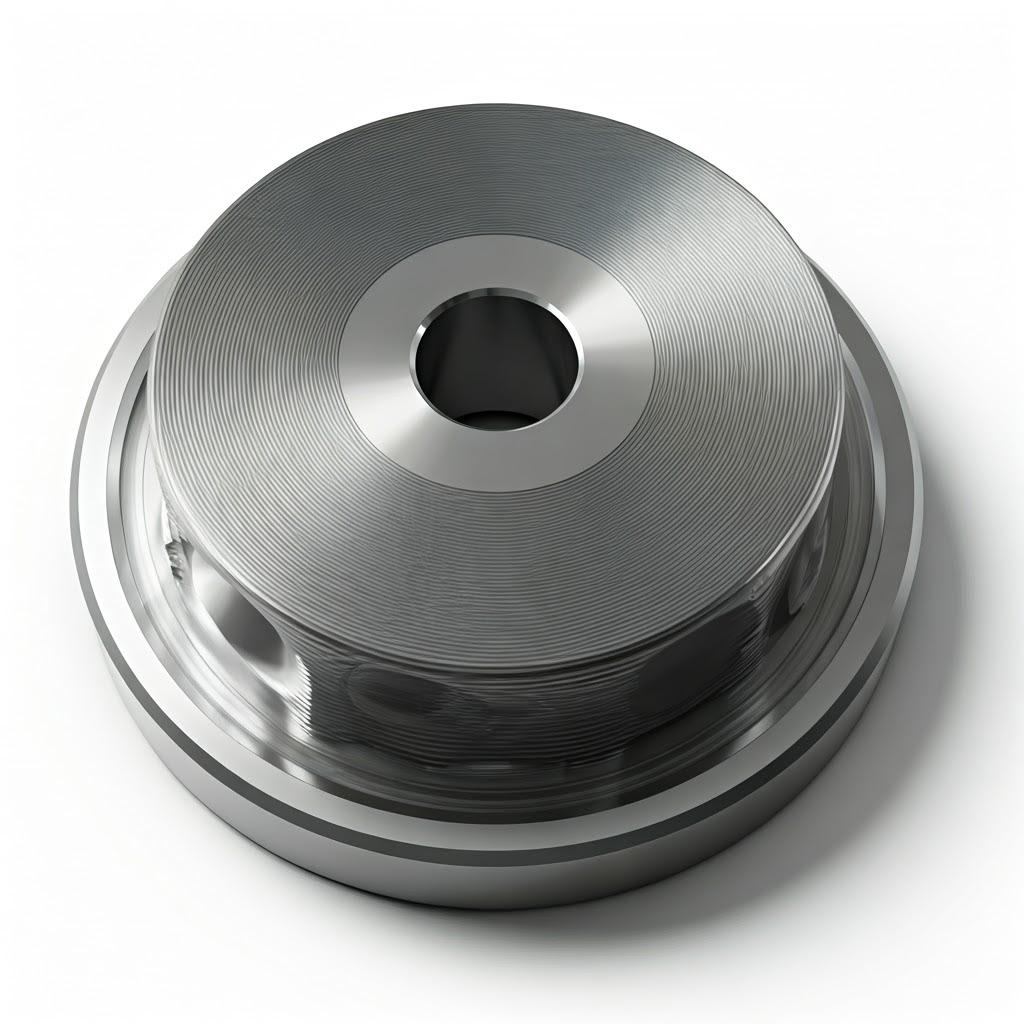
Precision Under Pressure: Achieving Tight Tolerances and Surface Finish in AM Pump Housings
While AM offers design freedom, components like pump housings still operate within systems requiring precise fits and specific surface characteristics for optimal performance and sealing. Understanding the achievable levels of dimensional accuracy (tolerances) and surface finish (roughness) with metal 3D printing, and how they compare to requirements, is vital for engineers and procurement managers.
Dimensional Accuracy and Tolerances:
- As-Built Tolerances: The tolerances achievable directly from the AM build process depend heavily on the specific technology (LPBF, SEBM), the machine calibration, the material being processed, the part size and geometry, and the build orientation.
- Tolerancias generales: For well-controlled processes and medium-sized parts (e.g., up to 150-250 mm), typical as-built tolerances might fall within the range of ±0.1 mm to ±0.3 mm or slightly larger for bigger dimensions. This might be comparable to ISO 2768-m (medium) for some features, but variations are common.
- Factores que influyen en la precisión: Thermal expansion/contraction during the build, residual stresses causing minor warping (even after stress relief), layer thickness, and beam spot size all play a role. Large, complex parts may exhibit greater deviation.
- Capacidades de Met3dp: Utilizing industry-leading printers known for accuracy and reliability, like those offered by Met3dp, combined with meticulous process control, helps minimize deviations and achieve the best possible as-built tolerances.
- Machined Tolerances: For critical features requiring tighter control than the as-built process can deliver, post-machining is essential.
- Flange Faces & Mounting Points: Need to be flat and perpendicular to ensure proper sealing and alignment. Machining can easily achieve flatness tolerances in the range of 0.02 mm to 0.05 mm.
- Bearing Seats & Seal Grooves: Require precise diameters and concentricity. CNC machining can achieve tolerances common for bearing fits (e.g., H7/g6) and O-ring grooves, typically within ±0.01 mm to ±0.05 mm depending on the specific requirement.
- Port Threads: Threads are almost always created or finished by machining (tapping or thread milling) after printing to ensure correct form and tolerance for standard fittings.
- Overall Profile: If the overall envelope or specific mating features require tight control, multi-axis CNC machining can bring the entire printed part, or specific sections, within demanding tolerance bands (e.g., ISO 2768-f or even tighter).
Acabado superficial (rugosidad):
Surface finish, typically measured as Ra (average roughness), is critical for pump housings as it impacts:
- Hydraulic Efficiency: Rough internal surfaces increase friction losses, reducing pump efficiency. Smoother surfaces promote laminar flow.
- Sealing: Rough flange faces or O-ring grooves can create leak paths. Smooth, uniform surfaces are required for effective sealing.
- Corrosion Initiation: Rough surfaces have higher surface area and can provide sites for corrosion (especially crevice corrosion) to initiate more easily.
- Wear: In areas with close clearances or dynamic seals, surface roughness influences wear rates.
- As-Built Surface Finish:
- LPBF: Typically produces Ra values ranging from 6 µm to 20 µm (240 µin to 800 µin), depending on the material, layer thickness, particle size, and surface orientation (upward-facing surfaces are generally smoother than downward-facing or side walls). Steeper angles tend to be rougher due to the stair-stepping effect.
- SEBM: Often results in slightly rougher surfaces than LPBF, potentially Ra 15 µm to 35 µm (600 µin to 1400 µin), due to larger layer thicknesses and powder partially sintering.
- Support Removal Scars: Areas where support structures were attached will inevitably be rougher and require post-processing attention.
- Post-Processed Surface Finish: Various techniques can significantly improve the as-built surface finish:
- Bead Blasting / Sand Blasting: Creates a uniform, matte finish, typically improving Ra slightly and removing loose particles. Ra might be in the 5 µm to 15 µm range. Good for general clean-up and aesthetics.
- Tumbling / Vibratory Finishing: Uses abrasive media in a tumbling barrel or vibratory bowl to smooth surfaces and edges. Can achieve Ra values down to 1-5 µm, depending on media and cycle time. Effective for external surfaces and some accessible internal areas.
- Mecanizado CNC: Provides the smoothest, most controlled finishes on specific features. Machined surfaces can easily achieve Ra < 1.6 µm (63 µin), Ra < 0.8 µm (32 µin), or even better for critical sealing or bearing surfaces.
- Polishing / Lapping: Manual or automated polishing can achieve very smooth, mirror-like finishes (Ra < 0.4 µm or 16 µin) where required for specific applications (e.g., hygienic pumps, though less common for standard marine pumps).
- Electropulido: An electrochemical process that removes a microscopic layer of material, preferentially smoothing peaks. Very effective for complex shapes and internal channels, improving cleanability and corrosion resistance. Can achieve Ra values similar to tumbling or better, while also passivating stainless steel surfaces.
Surface Finish Comparison Table:
Finishing Method | Typical Ra Range (µm) | Typical Ra Range (µin) | Notas |
---|---|---|---|
As-Built (LPBF) | 6 – 20 | 240 – 800 | Varies with orientation, material, parameters |
As-Built (SEBM) | 15 – 35 | 600 – 1400 | Generally rougher than LPBF |
Bead Blasting | 5 – 15 | 200 – 600 | Uniform matte finish, good clean-up |
Tumbling/Vibratory | 1 – 5 | 40 – 200 | Good for external surfaces, edge breaking |
Mecanizado CNC | < 0.4 – 1.6 | < 16 – 63 | Precise, controlled finish on specific features; required for tolerances |
Polishing/Lapping | < 0.1 – 0.4 | < 4 – 16 | Very smooth, mirror finish; labor-intensive |
Electropulido | 0.5 – 5 | 20 – 200 | Smooths complex shapes, improves corrosion resistance (esp. SS) |
Exportar a hojas
Achieving the Requirements:
Engineers must clearly specify the required tolerances (using standards like ISO 2768 or geometric dimensioning and tolerancing – GD&T) and surface finishes (Ra values) for all critical features on the pump housing drawing. Procurement managers should ensure the selected AM service provider has the necessary metrology equipment (CMMs, surface profilometers) and post-processing capabilities (CNC machining, finishing) to meet these specifications reliably. A provider like Met3dp, offering comprehensive solutions from printing to finishing, simplifies the process and ensures accountability for the final part quality. Relying solely on as-built dimensions and finishes is often insufficient for demanding pump applications; a well-defined post-processing plan is crucial.
Beyond the Build: Essential Post-Processing Steps for Marine Pump Housings
Creating a dimensionally accurate marine pump housing using metal AM is only part of the journey. The “as-built” part, fresh from the printer, requires several critical post-processing steps to relieve internal stresses, remove temporary supports, achieve final dimensions and surface finishes, and ultimately ensure the component possesses the necessary mechanical properties and corrosion resistance for long-term marine service. Overlooking or improperly executing these steps can compromise the integrity and performance of the final product.
Here’s a breakdown of the typical post-processing workflow for AM marine pump housings:
1. Stress Relief Heat Treatment:
- Why it’s Critical: The rapid heating and cooling cycles inherent in Powder Bed Fusion (LPBF/SEBM) create significant residual stresses within the printed part. These stresses can cause distortion (warping) during or after the build (especially after removal from the build plate), reduce fatigue life, and potentially lead to premature failure under load or promote stress corrosion cracking.
- The Process: Immediately after printing, often while still attached to the build plate, the part undergoes a specific heat treatment cycle in a controlled atmosphere furnace (e.g., vacuum or inert gas like Argon). The exact temperature and duration depend heavily on the alloy (e.g., 316L typically requires different parameters than CuNi alloys) and the part’s geometry/mass. The goal is to heat the part enough to allow atoms to rearrange and relieve internal stresses without significantly altering the desired microstructure (like causing excessive grain growth).
- Ventajas: Significantly reduces residual stress, improves dimensional stability for subsequent machining, and enhances overall part performance and reliability. This step is generally considered mandatory for functional metal AM parts.
2. Removal from Build Plate & Support Structure Removal:
- Separation: Once stress relieved, the pump housing needs to be separated from the build plate. This is typically done using wire EDM (Electrical Discharge Machining), sawing, or machining.
- Retirada del soporte: This can be one of the most labor-intensive steps, especially for complex internal geometries.
- Eliminación manual: Supports in easily accessible areas are often broken away manually using pliers, cutters, or grinders. This leaves rough witness marks that need further finishing.
- Mecanizado: CNC machining or EDM can be used for more precise removal of supports, especially near critical surfaces or in harder-to-reach areas.
- Abrasive Flow Machining (AFM) / Electrochemical Machining (ECM): For complex internal channels where manual or conventional machining access is impossible, specialized techniques like AFM (forcing abrasive putty through channels) or ECM might be employed, though these add cost and complexity.
- Design Impact: Effective DfAM (designing for self-support) significantly reduces the time, cost, and difficulty associated with this step.
3. Solution Annealing / Homogenization / Aging (If Required):
- Propósito: Depending on the alloy and the desired final properties, additional heat treatments beyond stress relief may be necessary.
- Solution Annealing (Austenitic Steels like 316L): Involves heating to a higher temperature (e.g., ~1050-1150°C for 316L) followed by rapid cooling (quenching). This dissolves any detrimental precipitates (like chromium carbides) that might have formed during printing or stress relief, ensuring maximum corrosion resistance and restoring ductility.
- Homogenization: A high-temperature treatment used to create a more uniform chemical composition throughout the part, which can be beneficial for certain alloys or very large components.
- Aging/Precipitation Hardening: For specific alloys (less common for standard 316L or CuNi, but relevant for some high-strength stainless steels or other alloys), a controlled aging heat treatment is used to precipitate secondary phases that increase strength and hardness.
- Consideraciones: These additional heat treatments must be carefully specified based on material science principles and application requirements. They can affect final dimensions (requiring machining afterwards) and surface oxidation.
4. CNC Machining for Critical Dimensions:
- Why it’s Essential: As discussed previously, AM processes cannot typically achieve the tight tolerances required for sealing faces, bearing fits, port connections, or precise alignment features directly.
- Operations: Multi-axis CNC milling and turning centers are used to machine:
- Flange faces (flatness, parallelism, surface finish for gaskets)
- O-ring grooves (diameter, concentricity, surface finish)
- Bearing bores (diameter, roundness, concentricity)
- Shaft seal areas
- Threaded ports (tapping or thread milling)
- Critical mounting surfaces
- Precisión: CNC machining ensures these features meet the exact specifications on the engineering drawing, guaranteeing proper assembly, sealing, and function.
5. Acabado de superficies:
- Propósito: To improve hydraulic efficiency, enhance corrosion resistance, improve cleanability, meet sealing requirements, or achieve a desired aesthetic.
- Methods (as detailed in previous section):
- Bead/Grit Blasting: General clean-up, uniform matte finish.
- Tumbling/Vibratory Finishing: Smoothing external surfaces, deburring edges.
- Pulido/Lapado: For very smooth finishes where required.
- Electropulido: Excellent for smoothing complex shapes, improving corrosion resistance (passivation of stainless steel), and reaching internal channels. Particularly beneficial for 316L to maximize its passive layer formation.
6. Cleaning and Inspection:
- Final Cleaning: Thorough cleaning is required to remove any machining fluids, blasting media, polishing compounds, or other contaminants before final inspection and assembly.
- Garantía de calidad: Dimensional inspection (using CMMs, calipers, micrometers, profilometers), potentially non-destructive testing (NDT) like X-ray or CT scanning (to check for internal defects/porosity if required by specification), pressure testing, and material certification verification are crucial final steps.
Post-Processing Workflow Summary:
Build -> Stress Relief -> Part/Support Removal -> Optional Advanced Heat Treat -> CNC Machining -> Surface Finishing -> Cleaning & Inspection -> Ship
Capacidad del proveedor: Handling this multi-stage post-processing workflow requires significant infrastructure and expertise. Procurement managers should verify that potential AM service providers either have these capabilities in-house or have established partnerships with qualified subcontractors. A provider offering an end-to-end solution, from printing through final machining and inspection, simplifies the supply chain and ensures accountability. Met3dp’s focus on providing comprehensive solutions, including application development services, suggests an understanding of these critical downstream processes necessary to deliver truly functional, high-quality marine components. Partnering with a knowledgeable supplier minimizes the risk of post-processing errors that could compromise the final pump housing’s performance.
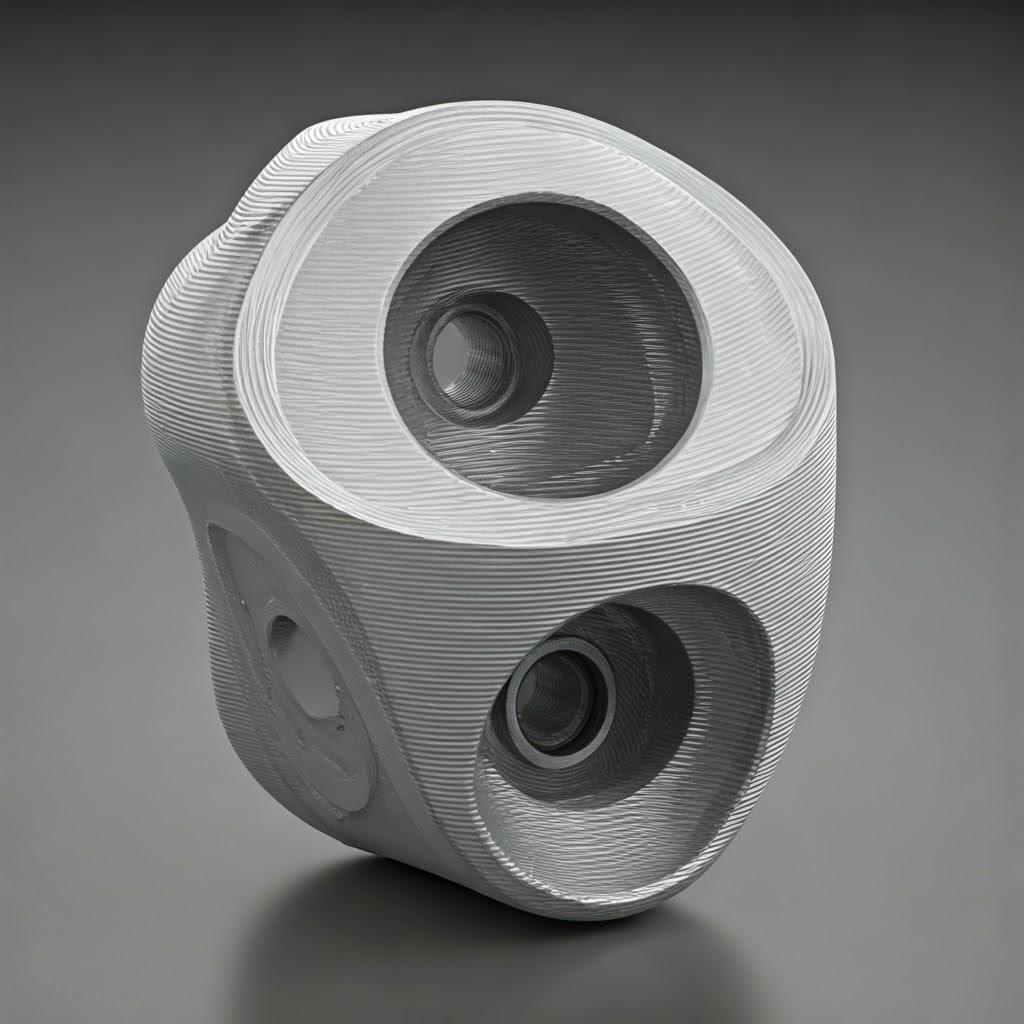
Navigating Challenges: Overcoming Potential Hurdles in 3D Printing Pump Housings
While metal additive manufacturing offers significant advantages for marine pump housings, it’s not without potential challenges. Understanding these hurdles and the strategies to mitigate them is crucial for successful implementation. Engineers and procurement managers should be aware of these potential issues and discuss them proactively with their AM service providers.
1. Residual Stress, Distortion, and Warping:
- El desafío: The rapid, localized heating and cooling during layer-wise fusion creates internal stresses. If not managed, these stresses can cause the part to warp during the build, distort after removal from the build plate, or even crack. Complex geometries like pump housings with varying thicknesses are susceptible.
- Estrategias de mitigación:
- DfAM: Designing parts with more uniform wall thicknesses, incorporating ribs or fillets to increase stiffness, and minimizing large, flat sections can help.
- Build Strategy: Optimizing part orientation on the build plate, using appropriate support strategies (anchoring, thermal supports), and optimizing laser/electron beam scan patterns can distribute heat more evenly.
- Parámetros del proceso: Fine-tuning parameters like laser power, scan speed, and layer thickness for the specific alloy and geometry.
- Tratamiento térmico antiestrés: As discussed, this is a critical, non-negotiable step performed immediately after printing to significantly reduce built-up stresses before part removal.
- Tolerancias de mecanizado: Factoring in potential minor distortion by leaving adequate stock for final machining ensures critical dimensions can still be met.
2. Porosity:
- El desafío: Small voids or pores within the printed material can act as stress concentrators, reduce fatigue life, potentially create leak paths in pressure-containing components like pump housings, and degrade overall mechanical properties and corrosion resistance.
- Causes:
- Porosidad del gas: Trapped shielding gas (e.g., Argon in LPBF) or dissolved gases within the powder that come out of solution during melting/solidification.
- Porosidad por falta de fusión: Insufficient energy input leading to incomplete melting between layers or scan tracks.
- Porosidad del ojo de la cerradura: Excessive energy density causing vaporization of the metal and instability in the melt pool, leading to trapped voids.
- Calidad del polvo: Hollow powder particles or gas trapped within the powder itself.
- Estrategias de mitigación:
- Polvo de alta calidad: Using powders with high sphericity, controlled PSD, low internal porosity, and low gas content is fundamental. This is where Met3dp’s investment in advanced powder production (Gas Atomization, PREP) provides a distinct advantage.
- Parámetros de proceso optimizados: Extensive development is required to find the optimal balance of laser/beam power, scan speed, hatch spacing, and layer thickness (the “processing window”) for each alloy to achieve >99.5% density. Experienced AM providers invest heavily in this parameter development.
- Proper Shielding Gas Flow: Ensuring laminar, consistent flow of high-purity inert gas to protect the melt pool from atmospheric contamination and remove process byproducts.
- Prensado isostático en caliente (HIP): A post-processing step involving high temperature and high isostatic pressure (using inert gas like Argon). HIP can effectively close internal pores (excluding those open to the surface), significantly improving density, ductility, and fatigue life. It’s often specified for critical applications but adds cost and lead time.
3. Support Structure Removal Complexity:
- El desafío: Pump housings often feature complex internal volutes, passages, and undercuts that require internal support structures. Removing these supports effectively without damaging the part can be difficult, time-consuming, and costly, especially if access is limited. Incomplete removal can impede flow or act as corrosion initiation sites.
- Estrategias de mitigación:
- DfAM: The most effective approach. Designing for self-support by using optimal angles, chamfers, and teardrop shapes wherever possible minimizes the necesita for internal supports. Planning build orientation carefully is also key.
- Soluble/Breakaway Supports (Emerging): Research is ongoing into dissimilar support materials that could be more easily removed chemically or mechanically, but this is not yet standard for reactive metals like Ti or challenging alloys like CuNi.
- Optimized Support Design: Using easily removable support types (e.g., thin pins, conical points, perforated structures) where supports are necessary. Software tools are improving in this area.
- Técnicas de eliminación especializadas: Utilizing tools like long-reach grinders, abrasive flow machining, or electrochemical machining for inaccessible areas, while acknowledging the added cost.
- Inspection: Using borescopes or CT scanning to verify complete removal from critical internal channels.
4. Achieving Consistent Material Properties:
- El desafío: Ensuring that the mechanical properties (strength, ductility, hardness) and corrosion resistance are consistent throughout the entire pump housing, especially for large or geometrically complex parts, can be challenging. Variations in thermal history across the part can lead to microstructural differences.
- Estrategias de mitigación:
- Control robusto de procesos: Maintaining tight control over all printing parameters (power, speed, gas flow, temperature) throughout the build. Utilizing machines with in-situ monitoring capabilities can help detect potential deviations.
- Powder Quality Consistency: Ensuring consistent powder characteristics batch-to-batch. Reputable powder suppliers like Met3dp have stringent quality control measures.
- Standardized Heat Treatment: Applying well-defined, validated heat treatment cycles (stress relief, solution annealing) appropriate for the alloy and geometry ensures homogenization and optimization of properties.
- Testing and Validation: Performing mechanical testing (tensile tests on samples printed alongside the part or cut from sacrificial sections) and potentially corrosion testing to verify that the final component meets specifications.
5. Cost and Lead Time:
- El desafío: While offering many advantages, the cost per part for AM can sometimes be higher than traditional methods, especially compared to high-volume casting. Build times can also be significant for large parts.
- Estrategias de mitigación:
- DfAM for Efficiency: Optimizing designs to reduce volume/mass (topology optimization) and minimize support structures directly reduces material cost and build time.
- Nesting: Printing multiple parts simultaneously on the build plate improves machine utilization and reduces cost per part.
- Focus on Total Cost of Ownership: Emphasize the value proposition beyond piece price – reduced lead time for spares (less downtime), improved performance (efficiency), lower inventory costs, and extended component life.
- Realistic Expectations: Understand that AM is often best suited for complex, low-to-medium volume, or custom parts where its unique benefits outweigh potentially higher direct costs. Discuss cost drivers and lead times openly with the AM service provider.
By acknowledging these potential challenges and working with an experienced and well-equipped AM partner like Met3dp, known for its high-quality powders, reliable printing systems, and comprehensive sobre nosotros expertise, manufacturers can successfully navigate the complexities of producing robust, high-performance marine pump housings via additive manufacturing. Proactive planning and collaboration are key to mitigating risks and maximizing the benefits of this transformative technology.
Supplier Selection: Choosing the Right Metal AM Service Provider for Marine Components
Selecting the right additive manufacturing partner is as critical as the design and material choices for ensuring the success of your 3D printed marine pump housing project. The quality, reliability, and performance of the final component are directly linked to the expertise, equipment, and processes of the service provider. For engineers and procurement managers navigating the AM landscape, especially those sourcing parts for demanding B2B industrial or wholesale requirements, a rigorous evaluation process is essential. Here’s a breakdown of key criteria to consider when choosing a metal AM supplier for corrosion-resistant marine components:
1. Material Expertise and Powder Quality Control:
- Alloy Experience: Does the supplier have proven, documented experience printing the specific alloys required, such as 316L stainless steel and CuNi30Mn1Fe? Ask for evidence, parameter sheets, or case studies involving these materials. Expertise with marine-grade alloys is paramount.
- Powder Sourcing & Quality: Where does the supplier source their metal powders? Do they manufacture their own, like Met3dp with its advanced Gas Atomization and PREP systems, ensuring strict control over sphericity, purity, and particle size distribution? Or do they source from reputable suppliers with batch traceability and certificates of conformity? High-quality powder is the foundation of a high-quality part. Request information on their powder handling and testing procedures.
- Material Property Validation: Can the supplier provide data demonstrating that their printed and post-processed materials meet expected standards (e.g., ASTM, ISO) for mechanical properties (tensile strength, yield, elongation) and microstructure?
2. Technology, Equipment, and Capacity:
- AM Process Suitability: Do they offer the appropriate printing technology (e.g., LPBF for fine features and surface finish, SEBM for certain reactive or crack-prone materials)?
- Machine Fleet: What is the make, model, age, and maintenance status of their printers? Do they operate industry-leading systems known for accuracy and reliability? What is their build envelope capacity – can they accommodate the size of your pump housing?
- Capacity & Scalability: Can they handle your required production volume, from prototypes to potential serial production or wholesale orders? Do they have sufficient machine capacity to meet agreed-upon lead times?
3. Comprehensive Post-Processing Capabilities:
- In-House vs. Outsourced: Does the supplier perform critical post-processing steps like stress relief heat treatment, CNC machining, and surface finishing in-house, or do they rely on subcontractors? In-house capabilities generally offer better control, traceability, and potentially faster turnaround.
- Range of Services: Verify they possess the necessary equipment and expertise for all required steps: calibrated furnaces for heat treatment (with controlled atmospheres), multi-axis CNC machines for tight tolerances, various finishing options (blasting, tumbling, polishing, electropolishing), and potentially advanced services like HIP if needed.
- Metrology and Inspection: Do they have calibrated CMMs, profilometers, NDT equipment (X-ray, CT, dye penetrant), and material analysis tools to verify conformance to specifications?
4. Quality Management System (QMS) and Certifications:
- ISO 9001: This is the baseline certification indicating a documented and audited QMS. Ensure the supplier holds a current ISO 9001 certificate relevant to additive manufacturing activities.
- Industry-Specific Certifications: While marine-specific AM certifications are still evolving, certifications from demanding industries like Aerospace (AS9100) or Medical (ISO 13485) demonstrate a higher level of process control, traceability, and risk management, which is highly beneficial for critical marine components.
- Marine Classification Societies: Has the supplier worked with or received any level of approval or certification from marine bodies like DNV, ABS, Lloyd’s Register, or Bureau Veritas for specific materials or processes? This is a significant advantage for parts intended for classed vessels or offshore structures.
- Documentation & Traceability: Ensure the supplier can provide full traceability, including powder batch certificates, build logs, heat treatment records, machining reports, and final inspection data.
5. Engineering Support and Collaboration:
- DfAM Expertise: Does the supplier offer Design for Additive Manufacturing support? Can their engineers collaborate with your team to optimize the pump housing design for printability, performance, and cost-effectiveness?
- Application Knowledge: Do they understand the specific challenges of marine environments (corrosion, biofouling, pressure requirements)? Experience in related fields like oil & gas or industrial pumps is also valuable.
- Simulación de construcción: Do they utilize simulation software to predict potential build issues like distortion or thermal stresses, allowing for mitigation strategies before printing?
- Communication & Responsiveness: Evaluate their communication channels, project management approach, and responsiveness to inquiries and technical questions.
6. Track Record, Reputation, and Stability:
- Case Studies & References: Ask for examples of similar projects or components they have successfully produced. Can they provide customer references or testimonials, particularly from B2B clients in relevant industries?
- Company Stability: Consider the supplier’s history, financial stability, and position in the market. Partnering with an established, reputable company reduces supply chain risk. Visiting the facility can provide valuable insights. Explore their overall capabilities and market presence on their main sitio web.
Supplier Evaluation Checklist:
Criterios | Preguntas clave | Importancia |
---|---|---|
Experiencia en materiales | Experience with 316L/CuNi? Powder quality control? Property validation data? | Muy alta |
Tecnología y equipos | Suitable AM process? Reliable machines? Build size adequate? Capacity for volume? | Muy alta |
Tratamiento posterior | In-house capabilities (Heat Treat, CNC, Finish)? Necessary equipment/expertise? Metrology tools? | Muy alta |
Quality System/Certs | ISO 9001? AS9100/ISO 13485? Marine certs? Traceability procedures? | Muy alta |
Soporte de ingeniería | DfAM assistance? Application knowledge (Marine)? Simulation capability? Collaboration approach? | Alta |
Track Record & Reputation | Relevant case studies? B2B references? Market stability? Facility audit possible? | Alta |
Costo y plazo de entrega | Competitive pricing structure? Ability to meet delivery schedules? Transparency in quoting? | Alta |
Location & Logistics | Shipping costs/times? Communication ease (time zones, language)? | Medio-Alto |
Exportar a hojas
Choosing the right metal AM service provider is a strategic decision. Thorough vetting against these criteria will help ensure you partner with a supplier, like Met3dp, that possesses the technical prowess, quality systems, and collaborative approach needed to deliver high-performance, corrosion-resistant marine pump housings that meet the demanding requirements of the maritime industry.
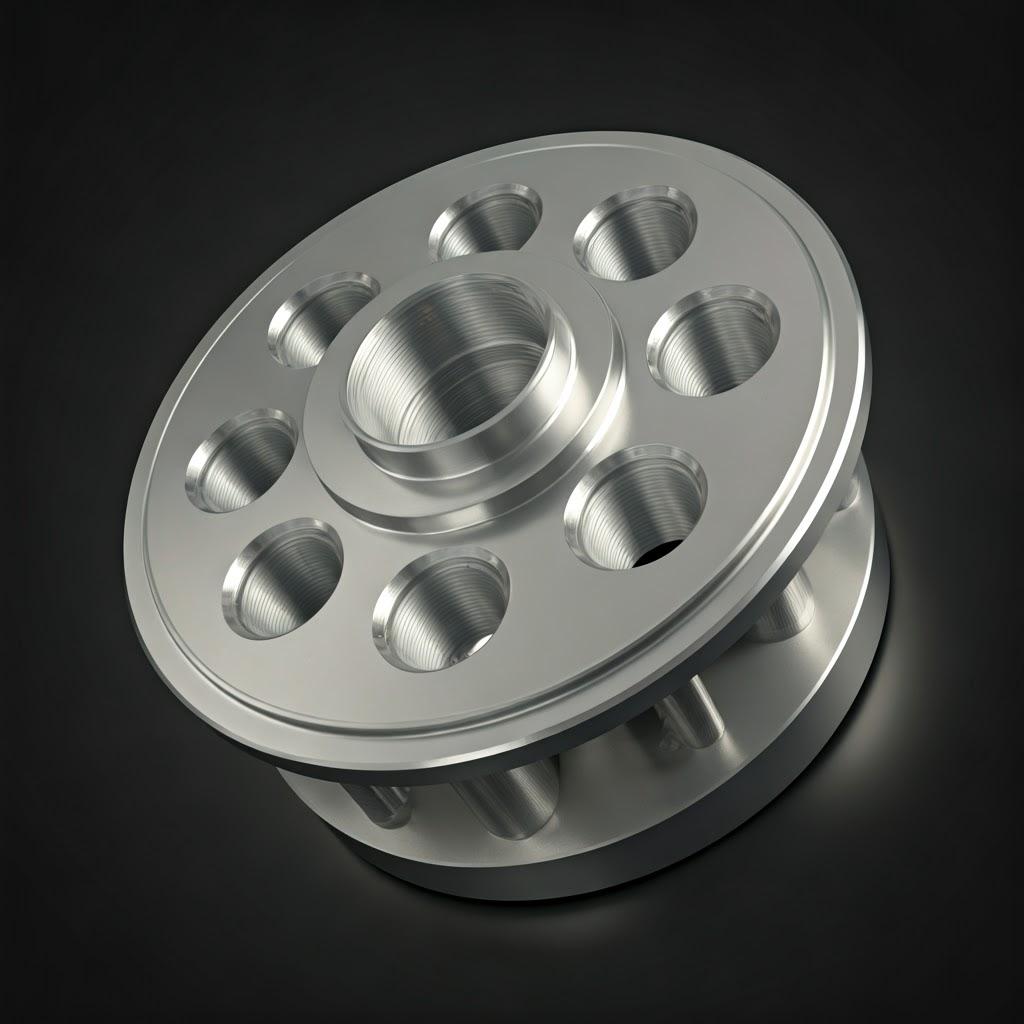
Understanding Investment: Cost Drivers and Lead Times for AM Marine Pump Housings
Making the switch to additive manufacturing for components like marine pump housings involves understanding the factors that influence project costs and delivery timelines. While AM offers unique benefits, its cost structure differs from traditional methods. A clear understanding helps engineers justify the investment and allows procurement managers to budget effectively and manage supply chain expectations, especially for wholesale or volume purchases.
Principales factores de coste:
- Coste del material:
- Powder Price: The cost per kilogram of high-quality, AM-grade metal powder varies significantly by alloy. Specialized alloys like copper-nickel (CuNi30Mn1Fe) are generally more expensive than widely used materials like 316L stainless steel. Titanium alloys would be even higher.
- Material Consumption: This includes the volume of the final part plus the volume of support structures required during the build. Design optimization (topology optimization, minimizing supports) directly impacts material consumption and cost. Unused powder can often be recycled, but there are costs associated with sieving, testing, and requalifying it.
- Tiempo de máquina (tiempo de construcción):
- Máquina Tarifa por hora: Metal AM machines represent a significant capital investment, and their operation incurs costs (energy, maintenance, skilled labor, inert gas). Service providers charge an hourly rate for machine usage.
- Build Duration: The total time required to print the part(s). This is influenced by:
- Part Volume: Larger parts naturally take longer.
- Part Height: Build time is primarily driven by the number of layers, so taller parts take longer than flatter parts of the same volume.
- Complejidad: Intricate details might require slower scan speeds.
- Estructuras de apoyo: Printing supports adds significant time to the build.
- Nesting Efficiency: Printing multiple parts in a single build (nesting) utilizes the machine more efficiently and reduces the effective time per part, lowering costs for batch or wholesale orders.
- Costes de postprocesamiento:
- Labor Intensity: Many post-processing steps, particularly support removal and manual finishing, are labor-intensive. Complexity drives labor hours.
- Tratamiento térmico: Furnace time, energy consumption, and controlled atmosphere costs (vacuum or inert gas).
- Mecanizado CNC: Machine time and skilled machinist labor for achieving tight tolerances and specific finishes on critical features. The amount of machining required (number of features, material removal volume) is a major factor.
- Acabado superficial: Costs associated with bead blasting, tumbling, polishing, or electropolishing (equipment, media, labor, cycle times).
- HIP (if required): Hot Isostatic Pressing is a specialized, high-cost process typically reserved for the most critical applications requiring maximum density and fatigue performance.
- Engineering and Setup Costs:
- DfAM Consultation: Initial design review and optimization efforts.
- Preparación de la construcción: Time spent by AM engineers setting up the build file, orienting the part, designing supports, and generating the machine toolpath. These costs are often amortized over the number of parts in a build, making prototypes relatively more expensive per piece than production runs.
- Quality Assurance and Inspection:
- Nivel de inspección: Basic dimensional checks vs. comprehensive CMM reports, surface finish measurements, NDT (X-ray, CT scan, dye penetrant), material testing – the required level of QA significantly impacts cost.
- Documentación: Creating detailed quality reports and traceability documentation requires time and resources.
- Order Volume (Economies of Scale):
- Prototipos: Typically have the highest cost per part due to amortization of setup/engineering costs over a single unit.
- Batch Production / Wholesale Orders: Lower cost per part due to amortization of setup costs, more efficient machine utilization (nesting), potential bulk powder purchasing advantages, and streamlined post-processing workflows.
Typical Lead Times:
Lead time refers to the total time from order placement (with a finalized design) to shipment of the finished part. It’s the sum of several stages:
- Queue Time: Time waiting for machine availability (can vary from days to weeks depending on supplier workload).
- Tiempo de construcción: Actual printing time (can range from hours for small parts to several days for large, complex housings).
- Post-Processing Time:
- Cooling & Stress Relief: Typically 1-2 days.
- Support Removal & Basic Finishing: 1-3 days (highly dependent on complexity).
- CNC Machining: 1-5 days (dependent on complexity and machine availability).
- Advanced Heat Treatment/HIP: Adds several days.
- Specialized Finishing (e.g., Electropolishing): Adds 1-3 days.
- Quality Assurance & Shipping Prep: 1-2 days.
Estimated Total Lead Time: For a typical marine pump housing of moderate complexity requiring standard post-processing (stress relief, support removal, machining of critical features, basic finishing), expect lead times in the range of 2 a 6 semanas. This can be shorter for urgent prototypes (with expedited fees) or longer for very large/complex parts, orders requiring extensive post-processing (like HIP), or during periods of high demand at the service provider.
Transparency and Quoting: A reputable AM service provider should provide a detailed quote outlining the cost breakdown (material, machine time, post-processing steps) and a realistic lead time estimate. Discussing specific requirements for tolerances, finishes, inspection, and certifications upfront is crucial for obtaining an accurate quote and avoiding unexpected delays or cost overruns.
Understanding these cost drivers and typical timelines allows for better project planning, budgeting, and communication within the supply chain when incorporating AM for marine pump housings.
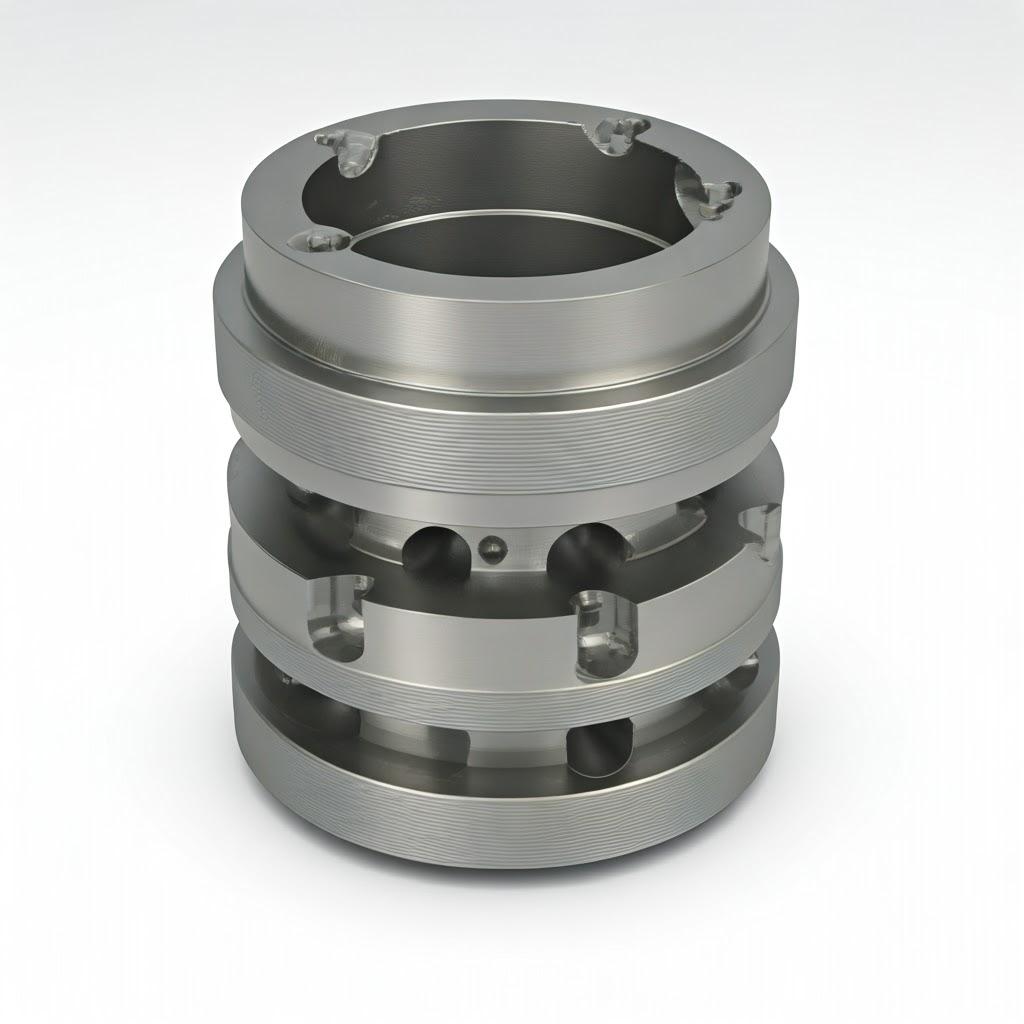
Frequently Asked Questions (FAQ) about 3D Printed Marine Pump Housings
Here are answers to some common questions engineers and procurement managers have when considering metal additive manufacturing for marine pump components:
1. How does the corrosion resistance of 3D printed 316L or CuNi alloys compare to traditional wrought or cast parts?
When produced using optimized process parameters, high-quality powders, and appropriate post-processing (especially stress relief and potentially solution annealing for 316L, or proper heat treatment for CuNi), 3D printed marine alloys can exhibit corrosion resistance that is equivalent to or potentially even better than their traditional counterparts. The rapid solidification in AM often leads to a fine-grained, homogeneous microstructure, which can be beneficial for corrosion performance. For 316L, achieving low porosity and ensuring proper heat treatment to avoid sensitization are critical. For CuNi alloys, achieving full density and the correct phase structure is key to maximizing both corrosion and biofouling resistance. However, improper processing (e.g., high porosity, contamination, incorrect heat treatment) can significantly degrade corrosion resistance. Therefore, partnering with an experienced AM provider with strong process control and material science expertise is crucial to realize the material’s full potential. Always request validation data or perform specific corrosion testing if performance in a particular environment is critical.
2. Can complex internal cooling or flow channels, like optimized volutes, be effectively printed and finished?
Yes, the ability to create complex internal geometries is one of the primary advantages of metal AM. Highly optimized volutes, diffusers, and even integrated cooling channels that would be impossible or prohibitively expensive to produce traditionally can be readily printed. However, there are key considerations:
- Design for Powder Removal: Internal channels must be designed with sufficient diameter and escape holes to allow for complete removal of unfused powder after printing. Trapped powder is detrimental.
- Internal Surface Finish: As-built internal surfaces will have a certain roughness (e.g., Ra 6-20 µm for LPBF). While often acceptable, if smoother surfaces are needed for hydraulic efficiency or cleanability, post-processing methods like Abrasive Flow Machining (AFM) or Electropolishing may be required, adding cost and complexity.
- Retirada del soporte: Internal supports might be needed depending on the geometry. Their removal requires careful planning and potentially specialized techniques. Designing for self-support internally is highly beneficial.
- Inspection: Verifying the integrity and clearance of internal channels may require borescopic inspection or even CT scanning for critical applications.
3. What quality certifications should I look for in a supplier manufacturing critical marine components like pump housings?
For critical components, robust quality assurance is non-negotiable. Look for suppliers who can demonstrate:
- Certificación ISO 9001: This is the fundamental standard for a Quality Management System, indicating documented processes, control, and traceability. Ensure the scope covers additive manufacturing.
- Evidence of Process Control: Beyond ISO 9001, look for evidence of strong internal process controls – parameter validation, machine calibration records, operator training programs, and meticulous record-keeping.
- Material Certifications & Traceability: The ability to provide full traceability from the raw powder batch (with certificates of conformity) through printing, heat treatment, and final inspection is essential.
- Relevant Industry Experience/Certs (Bonus): While marine-specific AM certifications are less common, suppliers holding AS9100 (Aerospace) or ISO 13485 (Medical) certifications demonstrate adherence to extremely rigorous quality standards, which translates well to demanding marine applications. Any experience or qualification with marine classification societies (DNV, ABS, etc.) is a strong indicator of capability for shipboard or offshore components.
- Metrology & Testing Capabilities: Confirmation that they possess the necessary calibrated equipment (CMMs, profilometers, NDT if required) to verify that parts meet all drawing specifications.
Ultimately, supplier transparency and a demonstrated commitment to quality through documented processes and objective evidence are key indicators of reliability.
Conclusion: Embracing Additive Manufacturing for Superior Marine Pump Performance and Longevity
The harsh, unforgiving nature of the marine environment demands components engineered for maximum durability and reliability. Corrosion, biofouling, high pressures, and the need for operational efficiency pose significant challenges for critical equipment like pumps. As we’ve explored, metal additive manufacturing offers a powerful, modern solution for producing marine pump housings that not only meet but often exceed the performance of traditionally manufactured parts.
By leveraging the design freedom of AM, engineers can create pump housings with highly optimized internal geometries for superior hydraulic efficiency, reduced cavitation, and integrated features, leading to better overall system performance. The ability to utilize advanced, highly corrosion-resistant materials like Acero inoxidable 316L for its excellent pitting resistance, or CuNi30Mn1Fe for its outstanding biofouling resistance, directly addresses the primary failure modes in marine applications. High-quality powders, such as those produced using advanced atomization techniques by specialists like Met3dp, form the essential foundation for achieving the desired material properties. See their range of polvos metálicos.
Furthermore, AM provides tangible benefits for procurement managers and the broader supply chain. Reduced lead times for prototypes and spares minimize costly downtime and inventory holding. The elimination of tooling costs makes AM economically viable for custom designs and low-to-medium volume production. The potential for part consolidation and on-demand digital manufacturing streamlines logistics and enhances supply chain resilience.
However, realizing these benefits requires a holistic approach. Success hinges on applying sound Diseño para fabricación aditiva (DfAM) principles, implementing crucial post-processing steps like stress relief heat treatment and precision machining, and meticulously selecting a qualified AM service provider. Careful consideration of tolerances, surface finish requirements, potential challenges like porosity or support removal, and a clear understanding of cost drivers are all part of the equation.
For companies operating in shipbuilding, offshore energy, desalination, aquaculture, and naval sectors, embracing metal additive manufacturing for components like pump housings is no longer a futuristic concept but a practical strategy for enhancing performance, improving reliability, and gaining a competitive edge. By partnering with knowledgeable and capable AM providers who offer comprehensive solutions encompassing advanced materials, cutting-edge printing technology, and robust quality systems, the marine industry can confidently navigate towards a future of more durable, efficient, and resilient fluid handling systems.
Compartir
MET3DP Technology Co., LTD es un proveedor líder de soluciones de fabricación aditiva con sede en Qingdao, China. Nuestra empresa está especializada en equipos de impresión 3D y polvos metálicos de alto rendimiento para aplicaciones industriales.
Solicite información para obtener el mejor precio y una solución personalizada para su empresa.
Artículos relacionados
Acerca de Met3DP
Actualización reciente
Nuestro producto
CONTACTO
¿Tiene alguna pregunta? ¡Envíenos un mensaje ahora! Atenderemos su solicitud con todo un equipo tras recibir su mensaje.
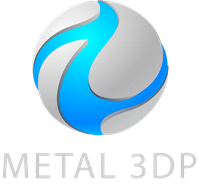
Polvos metálicos para impresión 3D y fabricación aditiva