La transformación del SLM en el sector aeroespacial
Índice
La industria aeroespacial siempre ha sido pionera en ampliar los límites del diseño y la tecnología. Imagine un mundo en el que los aviones sean más ligeros, resistentes y consuman menos combustible. Este sueño se está haciendo realidad gracias a la fusión selectiva por láser (SLM), una revolucionaria técnica de impresión 3D que está causando sensación en este campo. La SLM está transformando el modo en que se fabrican los componentes aeroespaciales, abriendo las puertas a diseños innovadores y a la optimización del rendimiento. Pero, ¿cómo está despegando exactamente la SLM en el mundo de los aviones, los cohetes y más allá? Profundicemos y exploremos las aplicaciones específicas de la SLM en la industria aeroespacial.
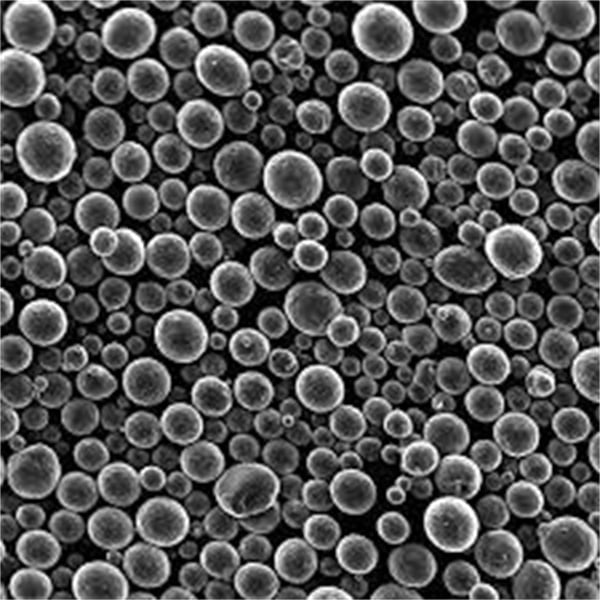
Polvos metálicos para SLM aeroespacial
En el corazón de la SLM se encuentra la magia de los polvos metálicos. Estas finas partículas metálicas se colocan meticulosamente en capas y se fusionan mediante un láser de alta potencia, creando complejas estructuras tridimensionales bajo demanda. El polvo metálico utilizado desempeña un papel crucial a la hora de determinar las propiedades y el rendimiento del componente final. A continuación se describen algunos de los principales polvos metálicos utilizados en la SLM para aplicaciones aeroespaciales:
Polvos metálicos para SLM aeroespacial
Polvo metálico | Composición | Propiedades | Características | Aplicaciones aeroespaciales |
---|---|---|---|---|
Aleaciones de titanio (Ti-6Al-4V, Ti-6Al-4V ELI) | Titanio (Ti), Aluminio (Al), Vanadio (V) | Elevada relación resistencia/peso, excelente resistencia a la corrosión, biocompatible | Las partículas de polvo son esféricas para un flujo y una fusión por láser óptimos | Palas de turbina, componentes del tren de aterrizaje, componentes estructurales del fuselaje, |
Superaleaciones a base de níquel (Inconel 625, Inconel 718) | Níquel (Ni), cromo (Cr), cobalto (Co), molibdeno (Mo) y otros elementos | Resistencia a altas temperaturas y a la oxidación | Más difíciles de procesar que las aleaciones de titanio | Discos de turbina, camisas de cámara de combustión, componentes de postcombustión |
Aleaciones de aluminio (AlSi10Mg, Scalmalloy) | Aluminio (Al), Silicio (Si), Magnesio (Mg) | Ligereza, buena resistencia, soldabilidad | Ofrece una alta conductividad térmica en comparación con otras aleaciones | Intercambiadores de calor, componentes del ala, componentes del fuselaje |
Cromo-cobalto (CoCr) | Cobalto (Co), Cromo (Cr) | Alta resistencia al desgaste, biocompatible | Se utiliza a menudo en aplicaciones médicas y está ganando terreno en el sector aeroespacial para piezas de desgaste específicas. | Cojinetes, engranajes, componentes del tren de aterrizaje |
Acero inoxidable (316L, 17-4 PH) | Hierro (Fe), Cromo (Cr), Níquel (Ni), Molibdeno (Mo) | Resistencia a la corrosión, buena resistencia | Relativamente asequible en comparación con otros polvos metálicos | Componentes de sistemas de fluidos, componentes estructurales que requieren una buena resistencia a la corrosión |
Aleaciones de cobre (CuNi) | Cobre (Cu), Níquel (Ni) | Alta conductividad térmica, buena conductividad eléctrica | Se utiliza para aplicaciones que requieren una transferencia de calor eficaz | Disipadores térmicos, barras colectoras para sistemas eléctricos |
Tántalo (Ta) | Tántalo (Ta) | Alto punto de fusión, excelente resistencia a la corrosión | Polvo metálico relativamente caro | Revestimientos de crisoles para aplicaciones de alta temperatura, escudos térmicos |
Molibdeno (Mo) | Molibdeno (Mo) | Alto punto de fusión, buena conductividad térmica | Se utiliza en combinación con otros metales en superaleaciones | Componentes de alta temperatura en motores de cohetes |
Tungsteno (W) | Tungsteno (W) | Punto de fusión muy alto, excelente resistencia al desgaste | Difícil de procesar debido a su alto punto de fusión | Toberas para motores de cohetes, escudos térmicos para vehículos de reentrada |
Inconel de fabricación aditiva (AM) | Níquel (Ni), cromo (Cr), cobalto (Co), molibdeno (Mo) y otros elementos | Propiedades a medida mediante el proceso AM | Permite crear microestructuras únicas con propiedades específicas | Álabes de turbina de alto rendimiento con canales de refrigeración optimizados |
Como puede ver, la selección de polvos metálicos para SLM en el sector aeroespacial es amplia y se elige cuidadosamente en función de los requisitos específicos de la aplicación. Desde la robusta resistencia de las aleaciones de titanio para álabes de turbinas hasta la eficiencia ligera del aluminio para componentes de fuselajes, la SLM permite crear piezas con propiedades excepcionales antes inalcanzables con los métodos de fabricación tradicionales.
Aplicaciones de SLM en Aeroespacial
El impacto de la SLM en el sector aeroespacial va mucho más allá de los materiales utilizados. Esta tecnología está revolucionando la forma de diseñar y fabricar componentes aeronáuticos, dando lugar a una nueva era de innovación. Estas son algunas de las aplicaciones clave de la SLM en el campo aeroespacial:
Aplicaciones de SLM en el sector aeroespacial
Aplicación | Beneficios | Ejemplos |
---|---|---|
Álabes de turbina | Canales de refrigeración internos complejos para mejorar la eficiencia, reducir el peso y crear geometrías de álabes complejas para mejorar el rendimiento. | Álabes de turbina de alta presión, álabes de turbina de baja presión, blisks (álabe y disco de turbina integrados) |
Componentes del tren de aterrizaje | Menor peso para una mayor eficiencia de combustible, libertad de diseño para estructuras reticulares complejas para una mejor absorción de impactos. | Soportes del tren de aterrizaje, puntales, componentes estructurales |
Componentes estructurales del fuselaje | Optimización de la topología para reducir el peso, capacidad de fabricar formas complejas difíciles con los métodos tradicionales. | Costillas, largueros, largueros (elementos estructurales) |
Camisas de combustión | Canales de refrigeración conformados para una mejor gestión térmica, capacidad de crear intrincadas características superficiales para una mejor mezcla de combustible y aire. | Camisas de cámara de combustión para mejorar la eficiencia y reducir las emisiones |
Intercambiadores de calor | Diseños ligeros con gran superficie para una transferencia de calor eficaz | Intercambiadores de calor aire-aire, enfriadores de aceite |
Componentes de satélite | Reducción del peso para aumentar la capacidad de carga útil, capacidad de fabricar estructuras intrincadas para funcionalidades específicas. | Soportes, antenas, componentes estructurales |
Componentes de motores de cohetes | Materiales resistentes a altas temperaturas para entornos extremos, capacidad de crear canales de refrigeración complejos para la gestión del calor. | Toberas, cámaras de combustión, cámaras de empuje |
Las ventajas de utilizar SLM en estas aplicaciones son numerosas. Por ejemplo, la capacidad de crear intrincados canales de refrigeración interna en los álabes de las turbinas permite una gestión más eficaz del calor, lo que aumenta el rendimiento del motor y la eficiencia del combustible. Del mismo modo, el SLM permite diseñar y fabricar componentes ligeros para fuselajes y trenes de aterrizaje, lo que contribuye directamente a reducir el consumo de combustible y aumentar la autonomía de los aviones. Además, la SLM permite a los ingenieros crear geometrías complejas que antes eran imposibles con las técnicas de fabricación tradicionales, lo que abre nuevas posibilidades de optimización del diseño y mejora del rendimiento.
Retos y consideraciones para SLM en Aeroespacial
Aunque la SLM ofrece un enorme potencial para la industria aeroespacial, aún quedan retos por superar. He aquí algunas consideraciones clave para utilizar SLM en aplicaciones aeroespaciales:
- Costes de la máquina y el polvo: Actualmente, las máquinas SLM tienen un precio elevado y los polvos metálicos diseñados específicamente para aplicaciones aeroespaciales pueden ser caros.
- Control y cualificación de procesos: La SLM es un proceso complejo que requiere un control estricto de los parámetros para garantizar una calidad constante y fiable de las piezas. La cualificación del proceso SLM para componentes aeroespaciales exige rigurosos procedimientos de ensayo y certificación.
- Rugosidad superficial: Las piezas SLM pueden presentar un acabado superficial más rugoso en comparación con los componentes fabricados de forma tradicional. En función de la aplicación, pueden ser necesarias técnicas de postprocesado como el mecanizado o el pulido.
- Limitaciones del tamaño de las piezas: Las máquinas SLM actuales tienen limitaciones en cuanto al tamaño de las piezas que pueden producir. La fabricación de componentes aeroespaciales de mayor tamaño podría requerir la segmentación y el ensamblaje de varias piezas impresas por SLM.
A pesar de estos retos, las ventajas potenciales de la SLM son innegables. A medida que la tecnología madure y los costes de producción disminuyan, la SLM se convertirá en un método de fabricación de uso generalizado en la industria aeroespacial. Los esfuerzos de investigación y desarrollo están mejorando continuamente las capacidades de las máquinas, la calidad del polvo y el control de los procesos, allanando el camino para una mayor adopción de la SLM. SLM en los próximos años.
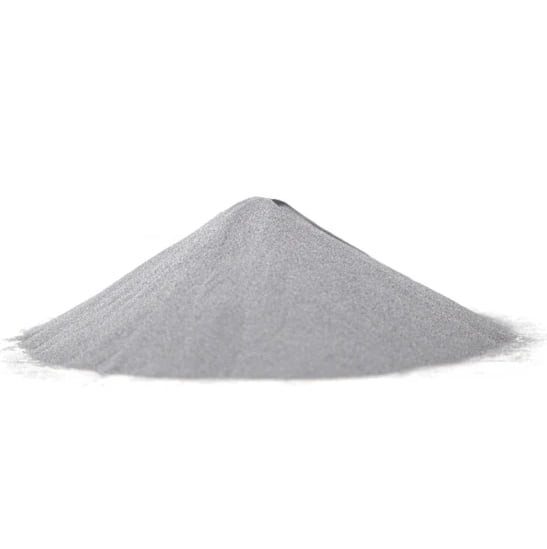
PREGUNTAS FRECUENTES
P: ¿Cuáles son las ventajas de utilizar SLM para componentes aeroespaciales?
R: La SLM ofrece varias ventajas:
- Piezas ligeras: El SLM permite crear componentes más ligeros que los métodos de fabricación tradicionales, lo que se traduce en una mayor eficiencia en el consumo de combustible y un aumento de la autonomía de los aviones.
- Libertad de diseño: La SLM permite diseñar y fabricar geometrías complejas antes imposibles con las técnicas tradicionales, lo que abre nuevas posibilidades de optimización del rendimiento.
- Propiedades del material: Las piezas SLM pueden fabricarse con materiales de alto rendimiento con propiedades excepcionales, como una elevada relación resistencia-peso y resistencia a altas temperaturas.
- Reducción de residuos: La SLM es un proceso más eficaz que los métodos tradicionales, ya que genera menos residuos de material.
P: ¿Cuáles son las limitaciones de la SLM para componentes aeroespaciales?
R: Algunas de las limitaciones de la SLM en el sector aeroespacial son:
- Costes de la máquina y del polvo: Las máquinas SLM y los polvos metálicos pueden ser caros, lo que repercute en los costes de producción.
- Control y cualificación de procesos: La SLM requiere un estricto control de los parámetros y rigurosos procedimientos de cualificación para las aplicaciones aeroespaciales.
- Rugosidad de la superficie: Las piezas SLM pueden requerir un postprocesado para obtener acabados superficiales más lisos en función de la aplicación.
- Limitaciones del tamaño de las piezas: Las máquinas SLM actuales tienen limitaciones en cuanto al tamaño de las piezas que pueden producir.
P: ¿Cuáles son los futuros avances previstos en SLM para aplicaciones aeroespaciales?
R: El futuro de la SLM en el sector aeroespacial es prometedor y se esperan varios avances:
- Reducción de los costes de maquinaria y polvo: A medida que la tecnología madure, se espera que los costes de producción tanto de las máquinas SLM como de los polvos metálicos disminuyan, lo que hará que la SLM sea más accesible para una adopción más amplia.
- Mayores volúmenes de construcción: El desarrollo de máquinas SLM más grandes con mayores volúmenes de construcción permitirá la producción de componentes aeroespaciales más grandes, eliminando la necesidad de segmentación y ensamblaje.
- SLM multimaterial: Los avances en la tecnología SLM podrían permitir la impresión de piezas utilizando múltiples materiales en una sola fabricación, creando componentes con propiedades graduales para un rendimiento óptimo.
- Seguimiento y control de procesos in situ: La supervisión y el control en tiempo real del proceso de SLM garantizarán una calidad constante de las piezas y reducirán el riesgo de defectos.
- Automatización e integración: El aumento de la automatización y la integración de la SLM con otros procesos de fabricación agilizará los flujos de trabajo de producción y mejorará la eficiencia.
P: ¿Es la SLM el futuro de la fabricación aeroespacial?
R: Aunque no es probable que la SLM sustituya a todos los métodos de fabricación tradicionales en el sector aeroespacial, no cabe duda de que está revolucionando la industria. La capacidad de la SLM para crear componentes ligeros y de alto rendimiento con diseños intrincados la hace ideal para una amplia gama de aplicaciones aeroespaciales. A medida que la tecnología siga desarrollándose y superando sus limitaciones, la SLM está llamada a convertirse en una fuerza dominante en la configuración del futuro de la fabricación aeroespacial.
Conclusión
La fusión selectiva por láser (SLM) está transformando la forma de diseñar y fabricar aeronaves. Esta innovadora tecnología de impresión 3D ofrece una combinación única de libertad de diseño, propiedades de los materiales y capacidades de reducción de peso, ampliando los límites de lo que es posible en la industria aeroespacial. Desde aviones más ligeros y eficientes en el consumo de combustible hasta cohetes capaces de alcanzar nuevas cotas, la SLM está desempeñando un papel crucial en la configuración del futuro del vuelo. A medida que la tecnología madura y supera sus retos, el cielo es el límite para el poder transformador de la SLM en el sector aeroespacial.
Compartir
MET3DP Technology Co., LTD es un proveedor líder de soluciones de fabricación aditiva con sede en Qingdao, China. Nuestra empresa está especializada en equipos de impresión 3D y polvos metálicos de alto rendimiento para aplicaciones industriales.
Solicite información para obtener el mejor precio y una solución personalizada para su empresa.
Artículos relacionados
Acerca de Met3DP
Actualización reciente
Nuestro producto
CONTACTO
¿Tiene alguna pregunta? ¡Envíenos un mensaje ahora! Atenderemos su solicitud con todo un equipo tras recibir su mensaje.
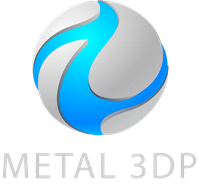
Polvos metálicos para impresión 3D y fabricación aditiva