SLM: fabricación de diversos componentes de automoción
Índice
Las aplicaciones específicas de SLM en Aeroespacial
Imagine construir un complejo componente aeronáutico no soldando o mecanizando trozos de metal, sino superponiendo meticulosamente partículas microscópicas con un rayo láser. Esta es la magia de la fusión selectiva por láser (SLM), una tecnología de impresión 3D que está revolucionando la industria aeroespacial.
La SLM, también conocida como fusión por lecho de polvo láser (LPBF), ofrece un tesoro de ventajas a los fabricantes del sector aeroespacial. Permite crear piezas intrincadas y ligeras con una relación resistencia-peso excepcional, una combinación de ensueño para construir aviones de bajo consumo y alto rendimiento. Pero, ¿cuáles son exactamente estas aplicaciones específicas y qué polvos metálicos impulsan esta innovación? Adentrémonos en el fascinante mundo de la SLM en el sector aeroespacial.
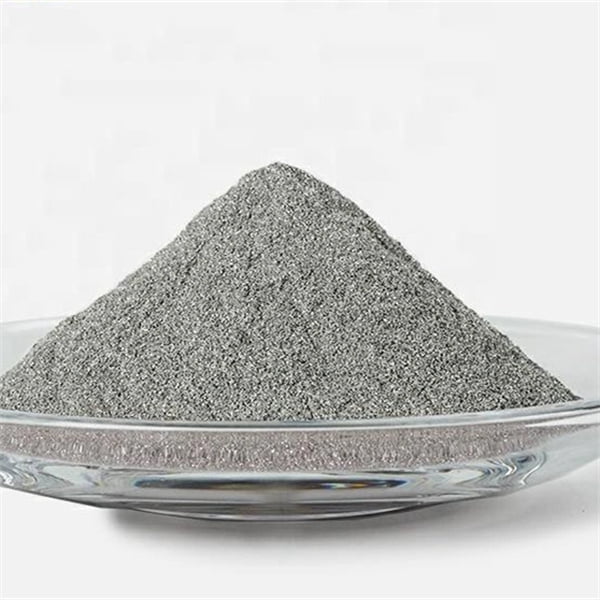
Polvos metálicos para SLM
El éxito de la SLM depende de las propiedades únicas de los polvos metálicos utilizados en el proceso de impresión. Estas partículas finas y meticulosamente elaboradas se transforman a partir de un lecho de polvo en componentes de formas intrincadas bajo la guía precisa del rayo láser. A continuación se describen diez polvos metálicos muy utilizados en aplicaciones de SLM aeroespaciales:
Polvos metálicos para SLM en el sector aeroespacial
Polvo metálico | Composición (wt%) | Propiedades clave | Aplicaciones |
---|---|---|---|
Ti-6Al-4V (Grado 23) | Ti (equilibrio), Al (6,0-6,8), V (3,5-4,5) | Elevada relación resistencia/peso, excelente biocompatibilidad | Componentes de trenes de aterrizaje, soportes de motores, estructuras de fuselajes, implantes protésicos (aplicaciones médicas) |
Inconel 718 | Ni (equilibrado), Cr (17-21), Fe (equilibrado), Nb (5,0-5,5), Mo (2,8-3,3) | Alta resistencia, buena resistencia a la corrosión, rendimiento a altas temperaturas | Álabes de turbina, camisas de cámara de combustión, intercambiadores de calor, componentes de motores de cohetes |
Aluminio AlSi10Mg | Al (equilibrio), Si (9-11), Mg (0,3-0,6) | Buena resistencia, peso ligero, excelente soldabilidad | Disipadores de calor, componentes de conductos, piezas estructurales ligeras |
Acero martensítico envejecido 1.2709 (AMS 5644) | Fe (equilibrio), Ni (18-20), Mo (4,8-5,3), Ti (1,7-2,0), Al (0,8-1,2) | Alta resistencia, buena tenacidad, excelente estabilidad dimensional | Componentes del tren de aterrizaje, piezas estructurales sometidas a grandes esfuerzos |
Titanio Ti-6Al-4V ELI (Extra Low Interstitials) | Ti (equilibrio), Al (6,0-6,8), V (3,5-4,5), Bajo O, N, C, H | Alta resistencia, excelente biocompatibilidad, ductilidad mejorada en comparación con el Grado 23 | Implantes médicos, componentes aeroespaciales que requieren una mayor resistencia a la fatiga |
Aleación de níquel 282 (Inconel 625) | Ni (saldo), Cr (20-23), Mo (5-7), Fe (saldo) | Excelente resistencia a la corrosión, rendimiento a altas temperaturas | Sistemas de escape, intercambiadores de calor, componentes expuestos a entornos agresivos |
Aluminio Scalmalloy (AA7075) | Al (equilibrio), Zn (5,6-6,1), Mg (2,1-2,6), Cu (1,2-1,6) | Alta resistencia, buena maquinabilidad | Componentes de alas, estructuras de fuselaje, piezas aeroespaciales que requieren una elevada relación resistencia/peso |
Cromo-cobalto CoCrMo (ASTM F75) | Co (equilibrio), Cr (27-30), Mo (5-7) | Alta resistencia al desgaste, biocompatible | Componentes de prótesis de cadera y rodilla (aplicaciones médicas), componentes de motores a reacción que requieren resistencia al desgaste |
Acero inoxidable 17-4PH | Fe (equilibrado), Cr (15,5-17,5), Ni (3,0-5,0), Cu (3,0-5,0) | Alta resistencia, buena resistencia a la corrosión, endurecimiento por precipitación | Muelles, cojinetes, componentes aeroespaciales que requieren una combinación de fuerza y resistencia a la corrosión. |
Aleación de níquel Rene 41 | Ni (equilibrio), Cr (18-21), Co (9-11), Mo (9-11), Ti (1,0-1,5), Al (0,8-1,2) | Rendimiento a altas temperaturas, excelente resistencia a la fluencia | Álabes de turbina, camisas de cámara de combustión, componentes aeroespaciales expuestos a temperaturas extremas |
La tabla anterior ofrece una visión de los diversos polvos metálicos que impulsan la SLM en el sector aeroespacial. Profundicemos en algunas consideraciones clave a la hora de seleccionar el polvo adecuado para una aplicación específica:
- Relación resistencia-peso: Esto es primordial en el sector aeroespacial, donde los componentes deben ser increíblemente resistentes pero ligeros para optimizar la eficiencia del combustible. Aleaciones como Ti-6Al-4V y Scalmalloy (AA7075) destacan en esta categoría.
- Rendimiento a altas temperaturas: Los componentes de los motores a reacción y otros entornos de alto calor exigen polvos como el Inconel 718 y el René 41, que pueden soportar temperaturas extremas sin comprometer la integridad estructural.
- Resistencia a la corrosión: Las aeronaves deben soportar condiciones meteorológicas adversas. Las aleaciones de níquel como el Inconel 625 y el acero inoxidable 17-4PH ofrecen una excelente resistencia a la corrosión.
- Biocompatibilidad: Para aplicaciones aeroespaciales que encajan con campos médicos, como los implantes protésicos, polvos como el Ti-6Al-4V ELI resultan cruciales por su naturaleza biocompatible.
- Soldabilidad: Si las técnicas de postprocesado, como la soldadura, forman parte del proceso de fabricación, se prefieren polvos como el aluminio AlSi10Mg por su buena soldabilidad.
Más allá de la tabla, he aquí algunos factores adicionales a tener en cuenta a la hora de elegir un polvo metálico para SLM:
- Fluidez del polvo: El polvo debe fluir libre y uniformemente para que la formación de capas durante el proceso de impresión sea óptima.
- Absortividad del láser: La capacidad del polvo para absorber eficazmente la energía del rayo láser es crucial para la correcta fusión y unión de las partículas.
- Rugosidad de la superficie: El acabado superficial deseado del componente final puede influir en la elección del polvo, ya que algunos polvos dan lugar a superficies más rugosas que otros.
Seleccionar el polvo metálico óptimo es un paso fundamental para garantizar el éxito de un proyecto de SLM en el sector aeroespacial. Si se tienen en cuenta los requisitos específicos de la aplicación y las propiedades de los polvos disponibles, los fabricantes pueden aprovechar todo el potencial de esta tecnología transformadora.
SLM en acción: Alzar el vuelo con aplicaciones específicas
La capacidad de la SLM para crear geometrías complejas con una precisión excepcional ha abierto las puertas a multitud de aplicaciones en la industria aeroespacial. He aquí algunas áreas clave en las que la SLM está logrando avances significativos:
La SLM puede utilizarse para fabricar diversos componentes de motores:
- Álabes de turbina: Los intrincados canales de refrigeración internos de los álabes de las turbinas son candidatos ideales para la SLM. Esto permite diseñar álabes más ligeros y eficientes, lo que contribuye a mejorar el rendimiento de los motores.
- Camisas de combustión: Estos componentes están expuestos a temperaturas extremas y requieren materiales resistentes a altas temperaturas como el Inconel 718. La SLM permite crear complejos canales de refrigeración dentro de los revestimientos, lo que mejora su durabilidad y eficacia.
- Intercambiadores de calor: La SLM facilita la fabricación de intercambiadores de calor con intrincadas trayectorias de flujo interno, optimizando la transferencia de calor en los motores de los aviones.
La SLM puede utilizarse para fabricar estructuras de fuselajes:
- Componentes del tren de aterrizaje: La SLM permite crear componentes del tren de aterrizaje ligeros pero de alta resistencia utilizando aleaciones como Ti-6Al-4V y acero martensítico envejecido.
- Componentes del ala: La SLM puede utilizarse para fabricar componentes de alas ligeros y estructuralmente sólidos a partir de aleaciones de aluminio como Scalmalloy (AA7075).
- Estructuras del fuselaje: La SLM ofrece la posibilidad de crear estructuras de fuselaje complejas y ligeras, lo que contribuye a la reducción del peso total de los aviones.
La SLM puede utilizarse para fabricar otros componentes aeroespaciales:
- Componentes de satélite: La capacidad de crear piezas para satélites altamente personalizadas y ligeras convierte a la SLM en una valiosa herramienta en la industria espacial.
- Vehículos aéreos no tripulados (UAV): La SLM es idónea para fabricar componentes ligeros y de alto rendimiento para vehículos aéreos no tripulados.
- Componentes de motores de cohetes: La SLM puede producir componentes complejos y resistentes a altas temperaturas para motores de cohetes utilizando aleaciones como René 41.
Las aplicaciones de la SLM en el sector aeroespacial no dejan de crecer a medida que madure la tecnología y se amplíe la gama de polvos metálicos adecuados. Esto promete revolucionar el diseño y la fabricación de aviones, dando lugar a una nueva generación de aeronaves de bajo consumo, ligeras y de alto rendimiento.
La SLM ofrece varias ventajas adicionales para la industria aeroespacial
- Libertad de diseño: La SLM permite crear geometrías complejas que serían difíciles o imposibles de fabricar con métodos tradicionales como el mecanizado o la fundición. Esto abre las puertas a diseños ligeros con celosías y canales internos, que optimizan el rendimiento y la eficiencia del combustible.
- Reducción de peso: Un principio básico de la ingeniería aeroespacial es lograr la mayor relación resistencia-peso posible. La SLM facilita el uso de aleaciones metálicas ligeras como el titanio y el aluminio, reduciendo significativamente el peso de los aviones en comparación con las técnicas de fabricación tradicionales. Un menor peso se traduce en una mayor eficiencia en el consumo de combustible, un aumento de la autonomía y una mayor capacidad de carga útil.
- Consolidación parcial: La SLM permite consolidar varias piezas en un único componente. Esto simplifica los procesos de fabricación, reduce el tiempo y los costes de montaje y minimiza los posibles puntos de fallo en el producto final.
- Reducción de existencias: Gracias a su capacidad de fabricación bajo demanda, la SLM minimiza la necesidad de grandes reservas de piezas de repuesto. Esto reduce los costes de inventario y mejora la logística de las empresas aeroespaciales.
- Creación rápida de prototipos: La capacidad de crear rápidamente prototipos funcionales mediante SLM acelera el proceso de diseño y desarrollo en la industria aeroespacial. Esto permite a los ingenieros probar e iterar los diseños de forma más eficiente, lo que se traduce en ciclos de innovación más rápidos.
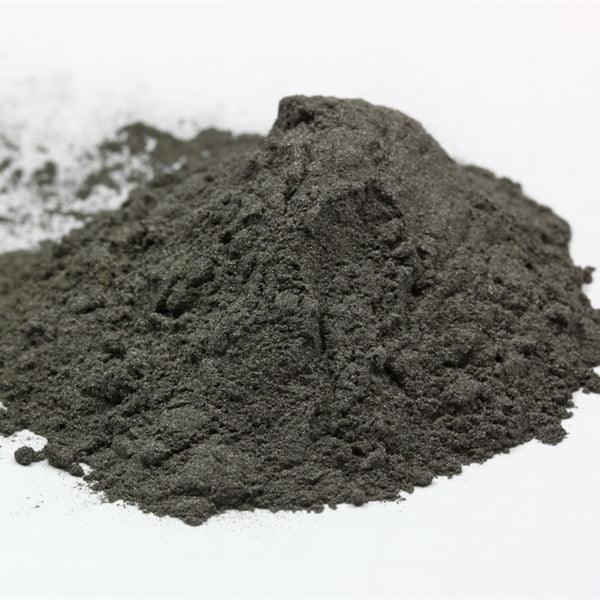
Sin embargo, la SLM en el sector aeroespacial también conlleva algunas consideraciones:
- Costo: Las máquinas SLM y los polvos metálicos pueden ser caros, lo que hace que esta tecnología sea más costosa que los métodos de fabricación tradicionales para la producción de grandes volúmenes.
- Rugosidad de la superficie: Las piezas fabricadas con SLM pueden tener un acabado superficial más rugoso que las piezas mecanizadas. Pueden ser necesarias técnicas de postprocesado como el mecanizado o el pulido para conseguir la calidad superficial deseada.
- Limitaciones del tamaño de las piezas: Las máquinas SLM actuales tienen limitaciones en cuanto al tamaño de las piezas que pueden producir. Esto puede restringir el uso de SLM para determinados componentes aeroespaciales a gran escala.
- Calidad del polvo: La calidad y consistencia del polvo metálico utilizado en la SLM influyen significativamente en las propiedades mecánicas de la pieza acabada. Para que las aplicaciones de SLM tengan éxito, es esencial aplicar estrictas medidas de control de calidad.
A pesar de estas consideraciones, las ventajas de la SLM están impulsando su adopción en la industria aeroespacial. A medida que avanza la tecnología, disminuyen los costes y mejora la calidad del polvo, SLM está a punto de transformar el diseño y la fabricación de aviones, allanando el camino para una nueva era de viajes aéreos de bajo consumo, ligeros y de alto rendimiento.
PREGUNTAS FRECUENTES
P: ¿Cuáles son las principales ventajas de la SLM en el sector aeroespacial?
R: Las principales ventajas son la libertad de diseño de geometrías complejas, la reducción de peso para mejorar la eficiencia del combustible, la consolidación de piezas para simplificar la fabricación y la creación rápida de prototipos para agilizar los ciclos de diseño.
P: ¿Cuáles son algunos de los retos asociados a la SLM en el sector aeroespacial?
R: Los principales retos son los costes más elevados en comparación con los métodos tradicionales, la posibilidad de acabados superficiales rugosos, las limitaciones en el tamaño de las piezas y la dependencia crítica de polvos metálicos de alta calidad.
P: ¿Qué tipos de polvos metálicos se utilizan habitualmente en SLM para aplicaciones aeroespaciales?
R: Entre los polvos metálicos más utilizados se encuentran el Ti-6Al-4V (por su resistencia y biocompatibilidad), el Inconel 718 (por su resistencia a altas temperaturas), el aluminio AlSi10Mg (por su buena resistencia y soldabilidad) y el acero martensítico envejecido (por su alta resistencia y estabilidad dimensional).
P: ¿Cuál es el futuro de la SLM en la industria aeroespacial?
R: ¡El futuro parece prometedor! A medida que avanza la tecnología, disminuyen los costes y se amplía la gama de polvos metálicos adecuados, se espera que la SLM desempeñe un papel cada vez más importante en la revolución del diseño y la fabricación de aviones para la próxima generación de vehículos aeroespaciales.
Compartir
MET3DP Technology Co., LTD es un proveedor líder de soluciones de fabricación aditiva con sede en Qingdao, China. Nuestra empresa está especializada en equipos de impresión 3D y polvos metálicos de alto rendimiento para aplicaciones industriales.
Solicite información para obtener el mejor precio y una solución personalizada para su empresa.
Artículos relacionados
Acerca de Met3DP
Actualización reciente
Nuestro producto
CONTACTO
¿Tiene alguna pregunta? ¡Envíenos un mensaje ahora! Atenderemos su solicitud con todo un equipo tras recibir su mensaje.
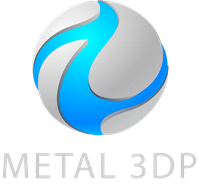
Polvos metálicos para impresión 3D y fabricación aditiva