Especialidades metálicas en polvo
Índice
Polvos metálicos especiales se refiere a metales que han sido procesados en forma de partículas finas para su uso en técnicas de fabricación avanzadas. Presentan propiedades únicas que los hacen idóneos para aplicaciones especializadas en sectores como el aeroespacial, el médico y el electrónico, entre otros.
Este artículo ofrece una visión general de los distintos tipos de polvos metálicos especiales, su composición y características, aplicaciones, especificaciones y grados, proveedores, precios y ventajas frente a limitaciones.
Tipos de polvos metálicos especiales
Existen muchas categorías y variedades de polvos metálicos especiales utilizados en diferentes tecnologías. Algunos de los principales tipos son:
Tipo | Descripción |
---|---|
Aleaciones de níquel | Inconel, Monel, Hastelloy, aleaciones Nilo con níquel más cromo, hierro, molibdeno, etc. Alta resistencia y resistencia a la corrosión a altas temperaturas |
Aleaciones de cobalto | Aleaciones Haynes con cobalto y cromo/tungsteno/molibdeno. Biocompatibilidad para implantes |
Aleaciones de titanio | Ti-6Al-4V, Ti-6Al-7Nb, etc. Ligereza, resistencia, biocompatibilidad |
Metales refractarios | Tungsteno, molibdeno, tántalo. Puntos de fusión extremadamente altos |
Aleaciones magnéticas | Aleaciones de hierro, níquel o cobalto con alta permeabilidad y baja coercitividad |
Polvos de proyección térmica | Polvos esferoidales para revestimientos resistentes al desgaste, la corrosión, etc. |
Ventajas de la pulvimetalurgia
Ventaja | Descripción | Beneficio | Ejemplo |
---|---|---|---|
Residuos mínimos | La pulvimetalurgia presenta una tasa de utilización de material excepcionalmente alta, que a menudo supera los 97%. Esto se debe a que las piezas se forman a partir de cantidades de polvo metálico medidas con precisión, lo que minimiza los desechos en comparación con los procesos sustractivos tradicionales, como el mecanizado. | Costes de producción reducidos, fabricación respetuosa con el medio ambiente y limpieza mínima tras la producción. | Los engranajes, cojinetes y otros componentes intrincados pueden conformarse con formas cercanas a la red, lo que requiere un mecanizado mínimo y genera muy poca chatarra. |
Flexibilidad de diseño | A diferencia de las técnicas tradicionales, limitadas por la conformabilidad de los materiales a granel, la pulvimetalurgia se nutre de formas intrincadas. Gracias a la libertad de prensado de los moldes, es posible incorporar al diseño geometrías complejas, rebajes e incluso canales internos. | Las piezas con características intrincadas o geometrías difíciles pueden producirse de forma eficiente, eliminando la necesidad de ensamblar múltiples componentes. | La pulvimetalurgia permite fabricar contactos eléctricos con detalles intrincados y disipadores de calor con canales internos para mejorar la disipación del calor. |
Versatilidad de materiales | El mundo de las aleaciones metálicas está a su alcance con la pulvimetalurgia. Mezclando diferentes polvos metálicos o incorporando elementos adicionales, se puede conseguir una amplia gama de propiedades de los materiales. Esto incluye el control de factores como la porosidad, la resistencia y la conductividad. | Los componentes que requieren una combinación específica de propiedades, como alta resistencia al desgaste y conductividad eléctrica, pueden adaptarse mediante la selección de materiales en la fase de polvo. | Los cojinetes autolubricantes pueden fabricarse incorporando partículas lubricantes a la mezcla de polvo metálico. Además, los componentes que requieren una elevada relación resistencia-peso pueden conseguirse mediante el uso de aleaciones metálicas ligeras. |
Precisión dimensional y repetibilidad | La pulvimetalurgia destaca en la producción de piezas con tolerancias estrictas. El control preciso de las características del polvo y las fuerzas de prensado se traduce en piezas de dimensiones uniformes en grandes volúmenes de producción. | Reducción de los requisitos de mecanizado posterior, mejora de la calidad del producto y piezas intercambiables. | Los engranajes, pistones y otros componentes mecánicos pueden fabricarse con gran precisión dimensional, lo que garantiza un funcionamiento suave y un montaje correcto. |
Formas cercanas a la red y mecanizado reducido | La capacidad de conformar formas complejas con gran precisión minimiza la necesidad de un extenso mecanizado posterior a la producción. Esto se traduce en un importante ahorro de costes y tiempo. | Tiempos de producción más rápidos, menores costes de fabricación y mejores acabados superficiales. | Los componentes complejos, como levas y piñones, pueden tener una forma casi de red, lo que requiere un mecanizado mínimo para conseguir las dimensiones finales. |
Porosidad controlada | La pulvimetalurgia ofrece una ventaja única: la capacidad de adaptar la porosidad de una pieza. Este volumen de poros controlado puede ser beneficioso para aplicaciones que requieren depósitos de lubricación, elementos de filtración o incluso implantes óseos que favorecen el crecimiento de los tejidos. | Mejora de la funcionalidad, la capacidad de filtración o la biocompatibilidad. | Los filtros de aceite y los cojinetes autolubricantes pueden aprovechar la porosidad controlada del material para mejorar su rendimiento. |
Capacidad de tratamiento térmico | Al igual que los metales forjados, las piezas pulvimetalúrgicas pueden someterse a procesos de tratamiento térmico para mejorar sus propiedades mecánicas, como la resistencia, la dureza y la resistencia al desgaste. | Mejores prestaciones y mayor idoneidad para las aplicaciones. | Los engranajes y ruedas dentadas pueden someterse a tratamiento térmico para conseguir una mayor resistencia al desgaste y a la fatiga. |
Automatización y producción a gran escala | La pulvimetalurgia es idónea para la automatización, ya que permite producir grandes volúmenes con una calidad constante. Todo el proceso, desde el llenado de polvo hasta la compactación y sinterización, puede automatizarse para lograr una fabricación eficiente. | Producción en serie rentable, reducción de los costes de mano de obra y calidad constante del producto. | Los procesos pulvimetalúrgicos automatizados permiten fabricar grandes volúmenes de piezas pequeñas y complejas, como cierres y conectores electrónicos. |
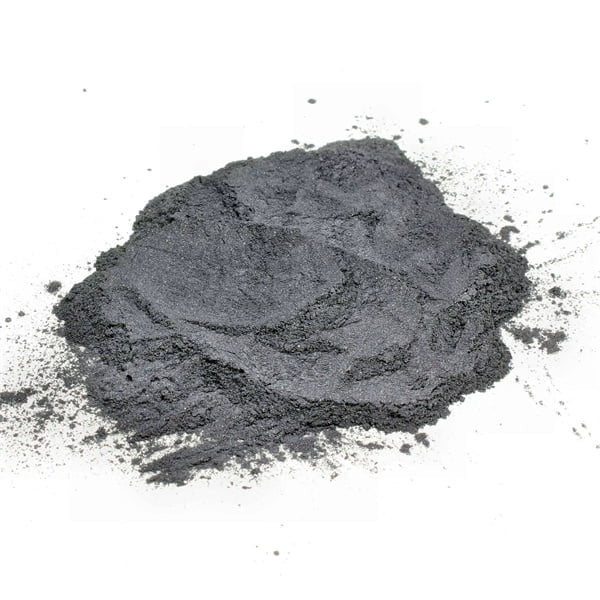
Composición y características
Polvos metálicos especiales pueden contener diversos elementos de aleación para conseguir las propiedades deseadas. A continuación se describen algunas composiciones y características típicas:
Material | Composición típica | Características |
---|---|---|
Aleaciones de níquel | Ni, Cr, Fe, Nb, Mo | Resistente al calor y a la corrosión. Buena resistencia y tenacidad |
Aleaciones de cobalto | Co, Cr, W, Ni, Mo | Biocompatible, gran dureza y resistencia al desgaste |
Aleaciones de titanio | Ti, Al, V, Nb, Ta | Extremadamente resistente pero ligero. Bioinercia |
Metales refractarios | W, Mo, Ta | Excelentes propiedades a altas temperaturas, conductividad térmica/eléctrica |
Aleaciones magnéticas | Fe, Ni, Co, Nd, Sm | Elevada magnetización de saturación y permeabilidad magnética |
Los porcentajes específicos de cada elemento pueden variar para producir polvos con propiedades ligeramente diferentes para las aplicaciones previstas. También es posible obtener aleaciones especiales más exóticas mezclando varios metales.
Características de las partículas
Además de la composición, las características del polvo, como la forma de las partículas, la distribución del tamaño, la fluidez y la pureza, también influyen en el rendimiento.
- Forma de las partículas - Esférica, irregular, mixta. Determina la densidad de empaquetamiento y el comportamiento de sinterización.
- Distribución por tamaños - Gama y distribución de tamaños. Afecta a la densificación y a las propiedades.
- Fluidez - Crucial para la precisión de dispensación en AM. Mejora con la esfericidad y la uniformidad de tamaño.
- Pureza - El contenido de oxígeno/nitrógeno afecta a la calidad. Cuanto más alto, mejor.
Los fabricantes controlan estrechamente estos atributos del polvo para garantizar la homogeneidad entre lotes.
Aplicaciones de los polvos metálicos especiales
Las ventajas exclusivas de los polvos metálicos especiales los hacen idóneos para nichos de aplicación en los que los productos metálicos tradicionales se quedan cortos. Algunos ejemplos son:
Industria | Aplicaciones |
---|---|
Aeroespacial | Palas de turbina, accesorios de aeronaves, toberas de cohetes |
Médico | Implantes ortopédicos/dentales, instrumental quirúrgico |
Automoción | Piezas de chasis ligeras, componentes de alto rendimiento |
Electrónica | Blindaje, contactos, marcos conductores, conectores |
Industrial | Utillaje, dispositivos de tratamiento térmico, revestimientos resistentes al desgaste y a la corrosión |
Otras aplicaciones comunes son los equipos de procesamiento químico, los artículos deportivos, los componentes de relojería, etc. Su uso sigue creciendo con la adopción de la fabricación aditiva.
Grados y especificaciones
Al igual que los metales convencionales, los grados pulvimetalúrgicos están normalizados por organizaciones profesionales para permitir una calidad y un rendimiento uniformes. Algunas normas clave son:
Estándar | Organización | Materiales |
---|---|---|
ASTM | ASTM Internacional | Aleaciones de níquel, cobalto y titanio |
UNS | SAE Internacional | Aleaciones metálicas especiales |
ISO | Organización Internacional de Normalización | Amplia gama de metales y cerámicas |
Dentro de cada norma, los materiales se designan con códigos únicos para su identificación. Además, se incluyen especificaciones relativas a los límites de composición, las características del polvo, el muestreo, los ensayos, etc., para regular la calidad.
Los fabricantes de renombre suministran certificados de conformidad química e informes de pruebas para validar el cumplimiento de la especificación adquirida. También son posibles grados personalizados fuera de las normas para aplicaciones propias.
Proveedores y precios
Hay una serie de proveedores líderes mundiales que suministran polvos metálicos especiales para uso comercial:
Proveedor | Materiales típicos | Precios medios |
---|---|---|
Sandvik | Aleaciones de níquel, cobalto y titanio | $50 - $100 por kg |
Praxair | Aleaciones de níquel, hierro y wolframio | $75 - $250 por kg |
Hoganas | Aceros para herramientas, aceros inoxidables | $30 - $150 por kg |
GKN | Titanio, aleaciones de aluminio. | $100 - $300 por kg |
Técnico carpintero | Amplia gama de aleaciones especiales | $250 - $500 por kg |
Los precios varían considerablemente en función de la complejidad de la aleación, el volumen del pedido, las características del polvo y las normas de calidad. En general, los polvos esféricos con distribución de tamaño controlada tienen un precio superior.
Comparación entre materiales
No existe una aleación especial que sea universalmente la mejor, sino que existen ventajas y desventajas específicas entre las distintas opciones de metal en polvo:
Parámetro | Aleaciones de níquel | Aleaciones de titanio | Metales refractarios |
---|---|---|---|
Fuerza | Muy buena | Excelente | Bien |
Dureza | Bien | Muy buena | Excelente |
Dureza | Excelente | Bien | Media |
Resistencia a la corrosión | Excelente | Muy buena | Media |
Resistencia a altas temperaturas | Excelente | Media | Excelente |
Biocompatibilidad | Media | Excelente | Media |
Coste | Alta | Muy alta | Media |
Principales conclusiones:
- Las aleaciones de níquel ofrecen las mejores propiedades generales, pero son caras
- Las aleaciones de titanio tienen una excelente relación resistencia-peso, pero pueden carecer de ductilidad.
- Los metales refractarios soportan temperaturas extremas pero son menos resistentes a la corrosión
- La selección correcta depende de las necesidades críticas de rendimiento de la aplicación
Ventajas de la pulvimetalurgia
Algunas ventajas notables de polvos metálicos especiales:
Mayor pureza - La solidificación rápida en atomización permite alcanzar una pureza superior a la de los metales fundidos/forjados convencionales. Esto amplía las aplicaciones viables y los ámbitos operativos.
Atributos de precisión - Las características uniformes del polvo permiten una producción repetible, tolerancias más estrictas y control de calidad para componentes críticos como turbinas aeroespaciales e implantes médicos.
Geometrías complejas - Los polvos especiales permiten la producción de componentes topológicamente optimizados, ligeros o porosos, imposibles mediante técnicas sustractivas.
Personalización - La química de la aleación y los atributos del polvo pueden adaptarse para satisfacer necesidades específicas de propiedades mecánicas, físicas o biológicas.
Sostenibilidad - Las técnicas aditivas tienen una menor relación compra-voladura y utilizan menos material que el mecanizado a partir de existencias a granel. Esto favorece una fabricación más ecológica.
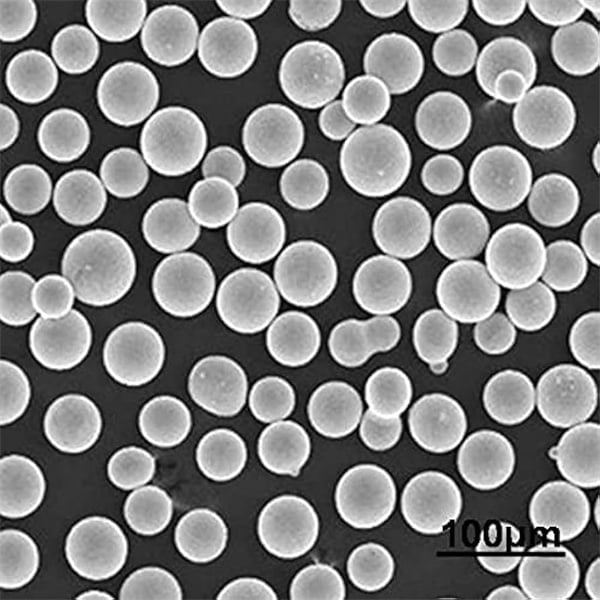
Retos de la pulvimetalurgia
Desafío | Descripción | Impacto | Posibles soluciones |
---|---|---|---|
Características del polvo y fluidez | El tamaño, la forma y la distribución incoherentes de las partículas del polvo pueden dar lugar a una densidad, porosidad y rugosidad de la superficie desiguales en el producto final. La escasa fluidez del polvo puede dificultar el llenado eficaz de los moldes, provocando defectos y retrasos en la producción. | Reducción de las propiedades mecánicas, compromiso de la integridad de las piezas y posibilidad de fallo de los componentes. Ineficacia de la producción y aumento de las tasas de desecho. | Rigurosa caracterización del polvo y control de la distribución del tamaño de las partículas. Utilización de polvos esféricos o angulares en función de la densidad y las propiedades deseadas. Utilización de lubricantes o aditivos de fluidez para mejorar la fluidez del polvo. |
Variaciones de densidad y porosidad | Conseguir una densidad uniforme en geometrías complejas puede resultar difícil. Los huecos internos o la porosidad pueden debilitar la pieza y afectar a su funcionalidad. | Fuerza, ductilidad y resistencia a la fatiga reducidas. Posibilidad de fugas en aplicaciones presurizadas. | Utilización de técnicas de compactación como el prensado o el prensado isostático para lograr una densidad óptima. Realización de simulaciones asistidas por ordenador para predecir y mitigar las variaciones de densidad. Optimizar el diseño de las piezas para minimizar las características complejas y favorecer un flujo uniforme del polvo. |
Delaminación y grietas | Una unión débil entre las partículas durante la compactación puede provocar delaminación (separación interna) o agrietamiento dentro de la pieza. | Propiedades mecánicas comprometidas y potencial de fallo catastrófico bajo tensión. | Optimizar las propiedades del polvo, como la morfología de la superficie y la composición química, para mejorar la adhesión. Utilizar mayores presiones de compactación o temperaturas de sinterización. Aplicar operaciones secundarias como el prensado isostático en caliente para eliminar defectos internos. |
Consideraciones económicas | Los polvos de gran pureza, las complejas técnicas de fabricación con forma casi de red y los tratamientos posteriores al procesado pueden aumentar considerablemente los costes de producción. | Rentabilidad limitada en comparación con los métodos tradicionales de trabajo del metal para determinadas aplicaciones. | Utilización de materiales en polvo rentables y optimización del diseño de las piezas para un uso eficiente del polvo. Explorar tecnologías de compactación alternativas con menores requisitos energéticos. Aplicar estrategias de reciclaje de polvo para minimizar el desperdicio de material. |
Impacto medioambiental | La manipulación y el procesamiento del polvo pueden generar polvo en suspensión y humos potencialmente peligrosos, lo que plantea riesgos para la salud y problemas medioambientales. | Efectos perjudiciales para la salud de los trabajadores y posible contaminación del medio ambiente. | Implantación de sólidos sistemas de recogida de polvo y ventilación para mantener un entorno de trabajo seguro. Utilización de lubricantes y aglutinantes ecológicos en la mezcla de polvos. Cumplimiento de estrictas normas medioambientales para la eliminación de residuos. |
Limitaciones en la selección de materiales | No todos los metales y aleaciones están disponibles en forma de polvo, y algunos materiales pueden sufrir degradación durante el proceso de producción de polvo. | Libertad de diseño restringida para aplicaciones que requieren propiedades específicas de los materiales. | Investigación y desarrollo continuos en tecnologías de producción de polvo para ampliar la selección de materiales para PM. Utilización de mezclas de polvos compuestos o moldeo por inyección de metales (MIM) para combinaciones avanzadas de materiales. |
PREGUNTAS FRECUENTES
Esta sección de preguntas frecuentes ofrece respuestas a preguntas habituales sobre pulvimetalurgia como referencia:
¿Cuáles son los polvos metálicos especiales más utilizados en la actualidad?
Las aleaciones de titanio, las superaleaciones con base de níquel, las aleaciones de cobalto-cromo y los aceros para herramientas constituyen la mayor parte de la demanda. Las principales aplicaciones son los motores aeroespaciales, los implantes de prótesis articulares, las herramientas industriales y de automoción y los aceros para moldes y matrices.
¿Qué métodos pueden emplearse para producir polvos metálicos especiales?
Las técnicas de producción comerciales más comunes son la atomización con gas, la atomización con plasma, la electrólisis y la descomposición carbonílica. Cada una de ellas presenta ventajas relativas: la atomización con gas ofrece la mejor combinación de coste y consistencia de tamaño y forma del polvo.
¿Cómo se caracterizan los polvos metálicos?
Las características típicas examinadas son la distribución del tamaño de las partículas, la morfología, la velocidad de flujo, la densidad de toma, la composición química, la microestructura y los niveles de contaminación. Estas características influyen en la idoneidad para los procesos de AM y en las propiedades de la pieza final.
¿A qué tamaño pertenecen los polvos especiales para AM?
La gran mayoría de los polvos se sitúan entre las 10 y las 100 micras. Las partículas más finas pueden combustionar o ser peligrosas de manipular, mientras que las partículas más grandes afectan negativamente a la resolución, la densidad y el acabado superficial.
¿Qué es una aleación especial atomizada con gas inerte?
Se refiere a un polvo de alto rendimiento producido atomizando la corriente de metal fundido utilizando un gas inerte como el argón o el nitrógeno para evitar la contaminación. Es el método de producción preferido para las aleaciones reactivas.
¿Cómo se postprocesan las piezas después de la AM?
El postprocesado habitual incluye el prensado isostático en caliente (HIP), el tratamiento térmico, el prensado isostático en caliente (HIP), el acabado superficial, el revestimiento y la inspección/prueba final para cumplir los requisitos de la aplicación.
Compartir
MET3DP Technology Co., LTD es un proveedor líder de soluciones de fabricación aditiva con sede en Qingdao, China. Nuestra empresa está especializada en equipos de impresión 3D y polvos metálicos de alto rendimiento para aplicaciones industriales.
Solicite información para obtener el mejor precio y una solución personalizada para su empresa.
Artículos relacionados
Acerca de Met3DP
Actualización reciente
Nuestro producto
CONTACTO
¿Tiene alguna pregunta? ¡Envíenos un mensaje ahora! Atenderemos su solicitud con todo un equipo tras recibir su mensaje.
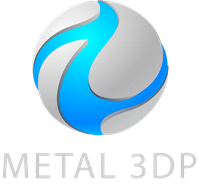
Polvos metálicos para impresión 3D y fabricación aditiva