Acero inoxidable 316L Polvo
Índice
Polvo de acero inoxidable 316L es un material popular para muchas aplicaciones debido a su excelente resistencia a la corrosión, propiedades mecánicas y biocompatibilidad. Esta guía ofrece una descripción detallada del polvo 316L, incluidas sus propiedades, métodos de producción, aplicaciones, proveedores, etc.
Descripción general del polvo de acero inoxidable 316L
El polvo de acero inoxidable 316L es un tipo de aleación de acero inoxidable que contiene molibdeno para mejorar la resistencia a la corrosión. La "L" se refiere al bajo contenido en carbono, que mejora la soldabilidad.
Algunas propiedades y características clave del polvo 316L son:
- Excelente resistencia a la corrosión, especialmente contra la corrosión por picaduras y grietas
- Alta resistencia y buena ductilidad
- Excelente biocompatibilidad y apto para implantes médicos
- Estructura austenítica no magnética
- Alta resistencia a la oxidación y a la fluencia a temperaturas elevadas
- Disponible en varios tamaños de partícula y morfologías
El polvo 316L puede producirse mediante atomización con gas, atomización con agua y otros métodos. El proceso de producción de polvo influye en las características del polvo, como la forma de las partículas, la distribución del tamaño, la fluidez, etc.
He aquí una comparación de los distintos tipos de polvo 316L y sus aplicaciones típicas:
Tipo de polvo | Tamaño de las partículas | Morfología | Aplicaciones |
---|---|---|---|
Gas atomizado | 15-150 μm | Esférica | Fabricación aditiva, MIM |
Agua atomizada | 10-300 μm | Irregular, dendrítico | Moldeo por inyección de metales |
Plasma atomizado | <100 μm | Esférica | Fabricación aditiva |
Electrolítico | <150 μm | Dendrítico, puntiagudo | Fabricación aditiva, prensado |
Carbonilo | <10 μm | Esférica | Pulvimetalurgia, prensado |
El polvo 316L se valora por su combinación de fuerza, resistencia a la corrosión y biocompatibilidad. Algunas de las principales aplicaciones incluyen:
- Fabricación aditiva - Fusión selectiva por láser, sinterización directa de metales por láser, inyección de ligantes
- Moldeo por inyección de metales - Piezas pequeñas y complejas como implantes ortopédicos
- Prensado y sinterizado - Filtros, estructuras porosas, cojinetes autolubricantes
- Recubrimiento superficial - Para mejorar la resistencia al desgaste y a la corrosión
- Soldadura fuerte y blanda - Como material de aportación
A continuación se ofrece una visión general de cómo se utiliza el polvo 316L en diferentes procesos de fabricación:
Proceso de fabricación | Cómo se utiliza el polvo 316L |
---|---|
Fabricación aditiva | El lecho de polvo se funde selectivamente por láser para construir piezas en 3D |
Moldeo por inyección de metales | Polvo mezclado con aglutinante, moldeado y luego sinterizado |
Prensar y sinterizar | El polvo se prensa para darle forma y luego se sinteriza |
Revestimiento de superficies | Pulverizado o fundido sobre la superficie mediante pulverización térmica, revestimiento láser, etc. |
Soldadura fuerte y blanda | Se utiliza como material de relleno para uniones |
La estructura de grano ultrafino y la consistencia homogénea que se obtiene de los polvos hacen del 316L un material ideal para aplicaciones críticas en los sectores aeroespacial, médico y de procesamiento químico, entre otros.
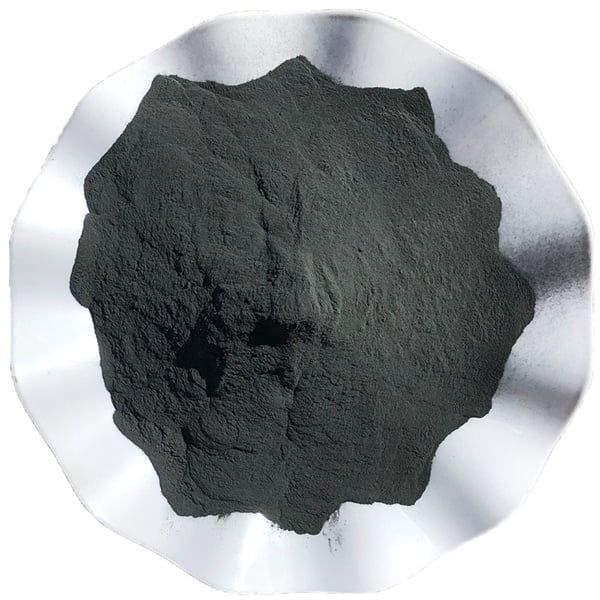
Propiedades del polvo de acero inoxidable 316L
Propiedad | Descripción | Impacto en la usabilidad |
---|---|---|
Composición química | Compuesto principalmente de hierro (Fe), cromo (Cr) (16-18%), níquel (Ni) (10-12%), molibdeno (Mo) (2-3%), con pequeñas adiciones de silicio (Si), manganeso (Mn), fósforo (P), azufre (S), nitrógeno (N). Bajo contenido en carbono (menos de 0,03%). | El alto contenido en cromo garantiza una excelente resistencia a la corrosión, especialmente contra la corrosión por picaduras y grietas. El níquel aumenta la resistencia y la ductilidad, mientras que el molibdeno mejora la resistencia a los ataques localizados, en particular por cloruros. El bajo contenido en carbono minimiza el riesgo de precipitación de carburos durante la soldadura o los procesos a alta temperatura. |
Tamaño y distribución de partículas | Se mide en micrómetros (µm), con un rango típico de 15-50 µm. La distribución del tamaño de las partículas dentro de este rango es crucial. | El tamaño y la distribución de las partículas influyen significativamente en la fluidez, la densidad de empaquetamiento y las propiedades mecánicas del producto final. Las partículas más finas suelen ofrecer un mejor acabado superficial, pero pueden ser difíciles de manipular debido a su escasa fluidez. Una distribución bien controlada con una mezcla de tamaños de partículas optimiza el empaquetado y minimiza los huecos en el producto final. |
Densidad aparente y densidad de toma | La densidad aparente se refiere a la densidad del polvo vertido suelto. La densidad del grifo se mide después de golpear el contenedor de polvo para conseguir un empaquetado más denso. Las unidades suelen ser g/cm³. | La diferencia entre la densidad aparente y la aparente refleja la fluidez del polvo. Una mayor densidad aparente en relación con la densidad aparente indica mejores características de fluidez, esenciales para la creación eficiente del lecho de polvo en los procesos de fabricación aditiva. |
Fluidez | La facilidad con la que el polvo fluye bajo su propio peso. Se mide con técnicas como el caudalímetro Hall o el índice de Carr. | Una buena fluidez permite un esparcimiento uniforme del polvo y minimiza la segregación (separación de diferentes tamaños de partículas) durante la manipulación y la deposición. Esto se traduce en una densidad y unas propiedades uniformes en el producto final. |
Esfericidad y morfología | La esfericidad se refiere al grado de semejanza de una partícula con una esfera perfecta. La morfología describe la forma general de las partículas (esférica, angular, irregular). | Las partículas esféricas suelen fluir mejor y empaquetarse más densamente que las irregulares. Sin embargo, algunas aplicaciones pueden beneficiarse de una morfología específica de las partículas para lograr la textura superficial deseada o el entrelazamiento de las partículas. |
Punto de fusión y alcance | Alrededor de 1400°C (2552°F). El intervalo de fusión puede variar ligeramente en función de la composición específica del polvo. | El punto de fusión es crucial para determinar las temperaturas de procesamiento adecuadas en técnicas como la sinterización o la fabricación aditiva. |
Conductividad térmica | Aproximadamente 16 W/mK. | La conductividad térmica influye en la transferencia de calor dentro del lecho de polvo durante el procesamiento. Esto puede influir en factores como la velocidad de enfriamiento, las tensiones residuales y la formación de fases no deseadas en el producto final. |
Comportamiento de la sinterización | Capacidad de las partículas de polvo de unirse durante un proceso de calentamiento a alta temperatura (sinterización) para formar un objeto sólido. | El comportamiento de la sinterización depende de factores como la distribución del tamaño de las partículas, la química de la superficie del polvo y los parámetros de sinterización. Una sinterización bien controlada permite densificar el lecho de polvo, consiguiendo las propiedades mecánicas deseadas en el producto final. |
Resistencia a la corrosión | Hereda una excelente resistencia a la corrosión de su homólogo a granel, el acero inoxidable 316L. Ofrece resistencia a una amplia gama de entornos, incluidos los ácidos oxidantes, los ácidos reductores y la niebla salina. | El contenido de molibdeno del polvo de 316L proporciona una resistencia superior a la corrosión por picaduras, especialmente en entornos con cloruros, en comparación con el polvo de acero inoxidable 304L. Esto lo hace adecuado para aplicaciones que exigen una alta resistencia a la corrosión. |
Métodos de producción del polvo 316L
Método | Descripción | Características de las partículas | Ventajas | Desventajas | Aplicaciones |
---|---|---|---|---|---|
Atomización de gases | El acero 316L fundido se inyecta en una corriente de gas inerte a alta velocidad, que lo rompe en finas gotas que se solidifican rápidamente en partículas esféricas. | - Forma esférica - Distribución de tamaños ajustada (15-45 micras) - Excelente fluidez - Alta densidad de empaquetamiento | - Calidad constante: buena para procesos de fabricación aditiva (AM) como la fusión por haz de láser (LBM) y la fusión por haz de electrones (EBM). | - Alto consumo de energía - Potencial de captación de oxígeno y nitrógeno | - Componentes aeroespaciales (álabes de turbina, intercambiadores de calor) - Implantes médicos (por su biocompatibilidad) - Piezas de automoción de alto rendimiento |
Atomización del agua | Similar a la atomización con gas, pero utiliza un chorro de agua a alta presión para romper el metal fundido. | - Forma irregular con algunos satélites (partículas fundidas) - Distribución de tamaños más amplia (10-100 micras) - Menor fluidez en comparación con la atomización con gas | - Más rentable que la atomización con gas - Adecuado para aplicaciones en las que la forma esférica es menos crítica | - Mayor contenido de oxígeno debido a la interacción con el agua - Puede requerir un tratamiento posterior adicional para AM | - Reactores de lecho fluidizado (portadores de catalizador) - Materia prima para moldeo por inyección de metales (MIM) |
Atomización por plasma | Utiliza un soplete de plasma de alta temperatura y alta velocidad para fundir y atomizar la materia prima de acero 316L. | - Forma muy esférica - Distribución de tamaños ajustada con posibilidad de partículas más finas (hasta 5 micras) - Excelente fluidez | - Calidad superior para aplicaciones AM exigentes - Puede conseguir polvos más finos para características intrincadas | - Consumo de energía más elevado de los tres métodos - Requiere equipos especializados | - Palas de turbina de alto rendimiento - Componentes microfluídicos - Implantes biomédicos que requieren un alto acabado superficial |
Aleación mecánica | Los polvos sólidos elementales o prealeados se mezclan y muelen juntos en un molino de bolas de alta energía para conseguir una composición uniforme de 316L. | - Forma irregular con facetas angulosas - Amplia distribución de tamaños - Menor fluidez | - Altamente personalizable para crear composiciones de aleación únicas que no pueden conseguirse con otros métodos. | - Mayor tiempo de procesamiento en comparación con las técnicas de atomización - Puede requerir pasos adicionales para mejorar la fluidez para AM | - Componentes especializados que requieren propiedades específicas de los materiales - Desarrollo de nuevas aleaciones para AM |
Electrólisis | Proceso de base acuosa en el que un ánodo de 316L se disuelve en la solución electrolítica y los iones metálicos se depositan en forma de polvo en el cátodo. | - Formas esféricas o dendríticas - Amplia distribución de tamaños - Puede ser poroso | - Posibilidad de fabricar polvos de gran pureza - Posibilidad de fabricar formas casi netas | - Capacidad de producción limitada - Proceso relativamente lento | - Implantes biomédicos que requieren gran pureza - Soportes catalíticos - Aplicaciones especializadas que exigen propiedades específicas del polvo |
Aplicaciones del polvo de acero inoxidable 316L
Industria | Aplicación | Propiedades apalancadas | Notas adicionales |
---|---|---|---|
Medicina y odontología | * Implantes (rodilla, cadera, dentales) * Instrumentos quirúrgicos * Prótesis | * Biocompatible (seguro para el contacto con el cuerpo) * Excelente resistencia a la corrosión * Alta resistencia * Formabilidad para diseños complejos | * El 316L minimiza el riesgo de rechazo e infección. * El polvo permite crear estructuras porosas para el crecimiento óseo. * Puede esterilizarse para un uso quirúrgico seguro. |
Procesado de alimentos | * Recipientes * Tubos * Válvulas * Accesorios * Fijaciones | * Resistencia superior a la corrosión de ácidos alimentarios y salmueras * Fácil de limpiar y mantener * Cumple las normas de higiene y seguridad | * El 316L garantiza la calidad de los alimentos y evita la contaminación. * Las superficies lisas minimizan los puntos de refugio bacteriano. * Soporta repetidos ciclos de limpieza. |
Marina | * Ejes de hélice * Piezas de motores diesel * Equipo de cubierta | * Resistencia excepcional a la corrosión del agua salada * Alta resistencia mecánica * Durabilidad en entornos difíciles | * El 316L prolonga la vida útil de los componentes marinos críticos. * Mantiene la integridad estructural bajo tensión y cargas pesadas. * Funciona de forma fiable a temperaturas variables. |
Química y petroquímica | * Recipientes de reacción * Sistemas de tuberías * Válvulas * Bombas | * Impermeable a una amplia gama de productos químicos * Resistencia a altas temperaturas * Tolerancia a la presión | * El 316L soporta productos químicos agresivos sin degradarse. * Soporta altas temperaturas de proceso para reacciones eficientes. * Adecuado para entornos de alta presión en refinerías y plantas. |
Aeroespacial | * Componentes de motores de aeronaves * Sistemas de control de fluidos * Piezas estructurales | * Alta relación resistencia-peso * Excelentes propiedades mecánicas a temperaturas elevadas * Resistencia a la corrosión en entornos difíciles | * El 316L reduce el peso para mejorar la eficiencia del combustible. * Mantiene el rendimiento en condiciones extremas de calor y presión. * Resiste la corrosión del combustible de aviación y otros fluidos aeroespaciales. |
Automoción | * Componentes del tubo de escape * Piezas del motor * Elementos decorativos y embellecedores | * Resistencia a altas temperaturas * Conformabilidad para formas complejas * Resistencia a la corrosión para una mayor vida útil | * El 316L puede soportar gases de escape calientes sin deformarse. * Puede moldearse para formar intrincados colectores y tubos de escape. * Resiste la corrosión de las sales de la carretera y las condiciones climáticas adversas. |
Bienes de consumo | * Relojes * Joyas * Cubiertos * Electrodomésticos | * Atractivo estético gracias al acabado pulido * Alta resistencia y resistencia al desgaste * Resistencia a la corrosión para facilitar la limpieza y la higiene | * El 316L ofrece un aspecto elegante y lujoso para artículos de gama alta. * Los utensilios y electrodomésticos mantienen su nitidez y durabilidad. * Superficie limpia e higiénica fácil de mantener. |
Construcción | * Revestimientos arquitectónicos * Fijaciones * Barandillas * Ferretería | * Resistencia a la corrosión para aplicaciones exteriores * Alta resistencia y resistencia a la intemperie * Atractivo estético para diseños modernos | * El 316L soporta condiciones climáticas adversas sin oxidarse. * Mantiene la integridad estructural y la funcionalidad a lo largo del tiempo. * Ofrece un aspecto elegante y contemporáneo para elementos arquitectónicos. |
Especificaciones y normas
La composición, calidad y propiedades del polvo 316L se rigen por diversas especificaciones y normas internacionales.
Normas ASTM
- ASTM A240 - Norma para chapas, hojas y bandas de acero inoxidable al cromo y al cromo-níquel para recipientes a presión y aplicaciones generales. Define los límites de composición y las propiedades mecánicas de la aleación 316L.
- ASTM B822 - Método de ensayo estándar para la distribución del tamaño de partículas de polvos metálicos y compuestos relacionados mediante dispersión de luz. Se utiliza para caracterizar la distribución del tamaño del polvo.
- ASTM F3055 - Especificación estándar para polvo de aleación de níquel de fabricación aditiva destinado a su uso en aplicaciones de fusión de lecho de polvo. Define requisitos estrictos para el polvo de aleación de níquel AM, incluido el 316L.
- ASTM F3049 - Guía para caracterizar las propiedades de los polvos metálicos utilizados en los procesos de fabricación aditiva. Proporciona orientación sobre la medición de características como el flujo, la densidad, la morfología, etc.
Otras normas
- ISO 9001 - Gestión de calidad para la producción de polvos metálicos
- ISO 13485 - Gestión de calidad de polvos metálicos para aplicaciones médicas
- Código ASME de Calderas y Recipientes a Presión - Requisitos de materiales para aplicaciones en recipientes a presión
Los proveedores de polvo 316L de renombre cuentan con sistemas de calidad certificados según las normas ISO y ASTM. La trazabilidad de los lotes y las pruebas exhaustivas se mantienen para garantizar el cumplimiento.
Proveedores de polvo 316L
Algunos de los principales proveedores mundiales de polvo de acero inoxidable 316L son:
Empresa | Métodos de producción | Tipos de polvo | Tamaño de las partículas |
---|---|---|---|
Sandvik | Atomización de gas | Osprey® 316L | 15-45 μm |
Tecnología LPW | Atomización de gas | LPW 316L | 15-63 μm |
Carpintero | Atomización de gas | Carpintero 316L | 15-150 μm |
Höganäs | Atomización del agua | 316L | 10-45 μm |
CNPC | Atomización de gas y agua | 316L | 10-150 μm |
Pometon | Atomización de gas y agua | 316L | 10-150 μm |
ATI | Atomización de gas | 316L | 10-63 μm |
El precio del polvo 316L depende de factores como:
- Calidad del polvo, composición, tamaño de las partículas y morfología
- Método de producción
- Cantidad del pedido y tamaño del lote
- Nivel de control de calidad y pruebas
- Requisitos de embalaje y entrega
El precio indicativo del polvo 316L atomizado con gas oscila entre $50-100 por kg para pedidos estándar. Los pedidos personalizados con requisitos especiales pueden costar más.
Al seleccionar un proveedor de polvo 316L, algunas consideraciones clave incluyen:
- Las características del polvo (distribución granulométrica, morfología, fluidez, etc.) deben ajustarse a las necesidades de la aplicación.
- Calidad y composición uniformes según las especificaciones
- Cadena de suministro y logística fiables
- Cumplimiento de normas y certificaciones internacionales
- Experiencia técnica y servicio al cliente
- Precios y cantidad mínima de pedido
Los principales fabricantes de polvo de 316L tienen décadas de experiencia en la producción de polvos adaptados a AM, MIM y otras aplicaciones con un estricto control de calidad.
Consideraciones de diseño para el polvo 316L
Consideraciones de diseño para el polvo de acero inoxidable 316L
Aspecto | Consideración | Impacto en la pieza impresa | Recomendaciones |
---|---|---|---|
Espesor de pared | El grosor mínimo debe ser de 0,8-1 mm | Las piezas con paredes más finas pueden ser débiles y propensas a agrietarse. | * Diseñe paredes de al menos 1 mm de grosor para una resistencia óptima. * Considerar el uso de nervaduras internas o celosías para reforzar las secciones finas. * Para piezas que requieran un grosor de pared mínimo, explore procesos alternativos de AM con mayor resolución. |
Voladizos y ángulos | Las esquinas afiladas y los voladizos sin soporte pueden provocar alabeo y delaminación. | * Minimizar las esquinas afiladas incorporando filetes y curvas. * Diseñe voladizos con ángulos de entre 30 y 45 grados para mejorar el soporte. * Utilice estructuras de soporte estratégicamente colocadas durante la impresión para evitar la caída. | |
Acabado superficial y orientación | Las características del polvo y la orientación de las capas pueden influir en la textura de la superficie. | * Comprender cómo el tamaño del polvo y la morfología afectan a la rugosidad de la superficie. * Considerar la orientación de la pieza para minimizar la visibilidad de la estratificación en superficies críticas. * Las técnicas de postprocesado, como el pulido o el granallado, pueden mejorar el acabado superficial. | |
Porosidad | Las bolsas de aire atrapadas en la pieza pueden comprometer las propiedades mecánicas. | * Optimizar los parámetros de impresión, como la potencia del láser y la velocidad de escaneado, para lograr una alta densidad. * Explorar técnicas como el prensado isostático en caliente (HIP) para minimizar aún más la porosidad. * Diseñar canales internos u orificios de ventilación para facilitar la eliminación del polvo durante la impresión. | |
Gestión del estrés | Las tensiones residuales del proceso de impresión pueden provocar alabeos o grietas. | * Utilizar las estructuras de soporte estratégicamente para minimizar los puntos de concentración de tensiones. * Diseñar elementos como filetes y transiciones graduales para reducir la acumulación de tensiones. * Considere el tratamiento térmico posterior a la impresión para el recocido de alivio de tensiones. | |
Precisión dimensional | La distribución del tamaño del polvo y la contracción durante la sinterización pueden afectar a las dimensiones finales. | * Tener en cuenta las tasas de contracción (normalmente en torno a 20%) al diseñar el modelo. * Utilizar los principios del diseño para la fabricación aditiva (DfAM) para optimizar la imprimibilidad y minimizar las desviaciones dimensionales. * Imprimir piezas de prueba para calibrar los parámetros de impresión y garantizar la precisión dimensional. | |
Estructuras de apoyo | Las estructuras temporales necesarias para geometrías complejas pueden dejar marcas. | * Diseñar estructuras de soporte con una superficie de contacto mínima para minimizar las marcas de extracción. * Explorar materiales de soporte solubles para facilitar el tratamiento posterior. * Optimizar el diseño de la estructura de soporte para un uso eficiente del material y una retirada sencilla. | |
Eliminación de polvo | El polvo no eliminado atrapado en el interior de las cavidades puede afectar a la funcionalidad. | * Diseñar canales internos u orificios de drenaje para facilitar la eliminación del polvo. * Utilizar ángulos y estrategias de ventilación para evitar que el polvo quede atrapado. * Optimizar los parámetros de impresión para minimizar la adherencia del polvo y mejorar la fluidez. |
Postprocesado de piezas de 316L
Postprocesado de piezas de acero inoxidable 316L
Proceso | Descripción | Beneficios | Consideraciones |
---|---|---|---|
Retirada del soporte | Retirada de las estructuras temporales utilizadas durante la impresión. | * Esencial para conseguir la geometría final de la pieza. * Permite acceder a las características internas. | * La selección del método de retirada depende del tipo de material de soporte (manual, mecánico, disolución química). * Se requiere una manipulación cuidadosa para evitar dañar la pieza. |
Tratamiento térmico | * Recocido antiestrés: Reduce las tensiones residuales de la impresión para mejorar la estabilidad dimensional y evitar el agrietamiento. * Recocido de soluciones: Refina la microestructura para mejorar las propiedades mecánicas y la resistencia a la corrosión. | * Optimiza el rendimiento y la longevidad de la pieza. * Permite el cumplimiento de especificaciones concretas del material. | * Requiere un control preciso de la temperatura y el tiempo en función de la geometría de la pieza y el resultado deseado. * Las técnicas de enfriamiento rápido, como el temple, pueden ser necesarias para el recocido por disolución. |
Granallado | Bombardear la superficie con pequeñas esferas metálicas para crear una capa de tensión compresiva. | * Mejora la resistencia a la fatiga y al desgaste. * Mejora la resistencia al agrietamiento por corrosión bajo tensión. | * La selección de la granalla y de los parámetros de granallado depende del acabado superficial deseado y de la profundidad del efecto. * Un granallado excesivo puede introducir rugosidad en la superficie. |
Decapado y pasivado | Proceso de limpieza química para eliminar los contaminantes de la superficie y mejorar la resistencia a la corrosión. | * Esencial para piezas expuestas a ambientes agresivos. * Crea una capa de óxido pasiva para mejorar la protección contra la corrosión. | * La selección de las soluciones de decapado y pasivado depende de la calidad del material y del estado de la superficie. * La manipulación incorrecta de los productos químicos requiere la adopción de precauciones de seguridad adecuadas. |
Mecanizado y acabado | Técnicas sustractivas tradicionales para conseguir dimensiones, tolerancias y acabados superficiales precisos. | * Permite crear características que no pueden conseguirse con AM. * Mejora la estética y la funcionalidad de las superficies. | * Requiere experiencia y equipos de mecanizado adicionales. * Puede introducir calor y tensiones que requieran un tratamiento posterior. |
Pulido | Métodos mecánicos o químicos para conseguir una superficie lisa y reflectante. | * Mejora el atractivo estético para aplicaciones decorativas. * Mejora la higiene de la superficie para dispositivos médicos. * Reduce la rugosidad de la superficie para mejorar la resistencia al desgaste. | * La selección del método de pulido depende del nivel de acabado deseado. * Un pulido excesivo puede eliminar material y alterar las dimensiones de la pieza. |
Galvanoplastia | Depositar una fina capa de otro metal sobre la superficie para mejorar sus propiedades. | * Mejora la conductividad eléctrica, la resistencia al desgaste o la resistencia a la corrosión. * Ofrece acabados decorativos como el cromado o el dorado. | * Requiere equipos y conocimientos especializados para los baños galvánicos. * El espesor del revestimiento debe controlarse cuidadosamente para evitar la delaminación. |
Defectos comunes en piezas de 316L
Defecto | Descripción | Causa | Impacto | Estrategias de mitigación |
---|---|---|---|---|
Porosidad | Bolsas de aire atrapadas en la pieza durante la impresión. | * Potencia láser o velocidad de escaneado subóptimas. * Fluidez inadecuada del polvo. * Purga de gas inadecuada. | * Menor resistencia mecánica, a la fatiga y a la corrosión. * Puede crear vías de fuga en aplicaciones de fluidos. | * Optimizar los parámetros de impresión para una fusión y densidad adecuadas. * Precalentar el lecho de polvo para mejorar el flujo. * Utilizar la purga de gas inerte para minimizar el aire atrapado. * Considerar técnicas de postprocesado como el prensado isostático en caliente (HIP) para una mayor densificación. |
Falta de fusión | Fusión incompleta entre capas de polvo adyacentes. | * Densidad de potencia láser insuficiente. * Espesor inconsistente de la capa de polvo. * Contaminación en la superficie del polvo. | * Adhesión débil entre capas, lo que puede provocar grietas y el fallo de la pieza. | * Calibrar la potencia del láser y la velocidad de exploración para una profundidad de fusión adecuada. * Garantizar un espesor constante de la capa de polvo mediante mecanismos de recubrimiento adecuados. * Mantener un lecho de polvo limpio, sin humedad ni contaminantes. |
Balloning | Acumulación excesiva de metal fundido en la superficie superior. | * Densidad de potencia láser excesiva. * Velocidad de exploración inadecuada. * Distribución incorrecta del tamaño del polvo. | * Acabado superficial rugoso con una estética pobre. * Posibilidad de salpicaduras e inestabilidad del proceso. | * Reducir la potencia del láser o aumentar la velocidad de exploración para evitar el sobrecalentamiento. * Optimizar los patrones de escaneado para evitar un tiempo de permanencia excesivo en una sola zona. * Utilizar una distribución más uniforme del tamaño del polvo para obtener un comportamiento de fusión uniforme. |
Grietas | Fracturas en la pieza debidas a tensiones residuales o choques térmicos. | * Enfriamiento rápido durante la impresión. * Insuficiente alivio de la tensión después del proceso. * Esquinas afiladas o características de diseño que concentran la tensión. | * Integridad estructural comprometida y posibilidad de fallo de las piezas. | * Aplicar velocidades de enfriamiento más lentas durante la impresión para minimizar los gradientes térmicos. * Realice un recocido de alivio de tensiones para reducir las tensiones residuales. * Diseñar elementos con transiciones suaves y evitar las esquinas afiladas. |
Alabeo | Distorsión de la pieza con respecto a su geometría prevista. | * Expansión y contracción térmicas desiguales durante la impresión. * Estructuras de soporte inadecuadas para geometrías complejas. * Tensiones residuales bloqueadas en la pieza. | * Imprecisiones dimensionales y posibilidad de mal funcionamiento de la pieza. | * Optimizar los parámetros de impresión para minimizar los gradientes térmicos. * Utilizar estructuras de soporte estratégicamente situadas para un apoyo adecuado durante la impresión. * Aplicar un recocido de alivio de tensiones para reducir las tendencias al alabeo. |
Delaminación | Separación de capas dentro de la pieza. | * Débil unión entre capas por falta de fusión. * Contenido excesivo de humedad en el polvo. * Contaminación en el lecho de polvo. | * Pérdida de la integridad estructural y posibilidad de delaminación de la pieza. | * Garantizar una fusión adecuada entre las capas optimizando los parámetros de impresión. * Mantener un bajo contenido de humedad del polvo mediante un almacenamiento y manipulación adecuados. * Utilizar un lecho de polvo limpio y libre de contaminantes. |
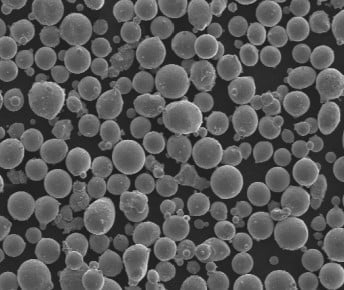
Cómo elegir un proveedor de polvo 316L
He aquí una guía paso a paso para seleccionar un proveedor de polvo de acero inoxidable 316L:
Paso 1: Determinar los requisitos de la solicitud
- Considere qué proceso de fabricación se utilizará: AM, MIM, etc.
- Identificar las propiedades críticas del polvo necesarias, como el tamaño de las partículas, la forma, la pureza, etc.
- Tenga en cuenta las especificaciones de la pieza: propiedades mecánicas, precisión, acabado superficial, etc.
Paso 2: Investigar posibles proveedores
- Búsqueda de fabricantes líderes de polvo 316L con larga experiencia
- Comprobar capacidades: métodos de producción, variedades de polvo, pruebas de control de calidad, etc.
- Revise los estudios de casos y las reseñas de clientes relevantes para su aplicación
Paso 3: Evaluar las capacidades técnicas
- ¿Pueden adaptar el polvo 316L a las necesidades de su aplicación?
- ¿Tienen experiencia en AM, MIM u otras tecnologías de polvo?
- ¿Cuál es su nivel de integración vertical y control de calidad?
Paso 4: Evaluar la oferta de servicios
- Asistencia técnica durante la selección del polvo y el desarrollo de la aplicación
- Pruebas de muestras, servicios de ensayo
- Capacidad de respuesta a las consultas, flexibilidad en los plazos de entrega
Paso 5: Revisar certificaciones y conformidad
- Certificaciones internacionales de calidad: ISO 9001, ISO 13485, etc.
- Cumplimiento de normas de composición del polvo como ASTM
- Trazabilidad de los lotes, pruebas exhaustivas y documentación
Paso 6: Comparar precios
- Precio por kg para la granulometría, el nivel de calidad y la cantidad requeridos
- Cantidad mínima de pedido y requisitos de tamaño de lote
- Gastos de envío/logística
Paso 7: Comprobar la disponibilidad y fiabilidad
- Existencias constantes y capacidad para hacer frente a las fluctuaciones de la demanda
- Seguimiento y control de pedidos, plazos de entrega transparentes
- Cumplimiento de los plazos de entrega
La selección de un proveedor con experiencia en aplicaciones, calidad de producto constante y servicio receptivo garantiza una experiencia de compra sin problemas.
Cómo optimizar el polvo 316L para AM
Adaptar el tamaño de las partículas al proceso AM
- Utilice partículas de 10-45 μm para la fusión de lecho de polvo como DMLS, SLM
- Optimizar la distribución de tamaños: una distribución demasiado amplia puede causar problemas de empaquetado.
- Partículas más finas de 1-10 μm más adecuadas para el chorro de ligante
Lograr una alta esfericidad y fluidez
- La fluidez afecta directamente al esparcimiento del polvo y a la uniformidad de la capa
- La atomización con gas produce polvos esféricos y fluidos
- Prueba de flujo de polvo según la norma ASTM B213
Minimizar las partículas del satélite
- Utilizar el tamizado y la clasificación para eliminar los satélites y los finos.
- Los satélites pueden causar aglomeración y defectos
Tolerancia de la composición de control
- Control estricto de la composición elemental dentro del intervalo especificado por ASTM
- Limitar impurezas como O, N, C que afectan a las propiedades
Reducir la porosidad
- Optimizar los parámetros del proceso y los patrones de exploración
- Utilice el prensado isostático en caliente para minimizar la porosidad
- Mantiene una densidad >99% para un alto rendimiento
Minimizar las tensiones residuales
- Optimizar los gradientes térmicos en el proceso de fabricación
- Utilizar tratamientos térmicos adecuados para aliviar las tensiones
Alcanzar las propiedades mecánicas deseadas
- El recocido por disolución y el envejecimiento mejoran la resistencia
- Mantener propiedades uniformes en todas las direcciones de construcción
Una cuidadosa caracterización del polvo, la optimización de los parámetros y el postprocesado son fundamentales para conseguir piezas de 316L sin defectos mediante AM.
PREGUNTAS FRECUENTES
P: ¿Para qué se suele utilizar el polvo de acero inoxidable 316L?
R: El polvo de 316L es el más utilizado para la fabricación aditiva, el moldeo por inyección de metales y las aplicaciones de prensado y sinterizado debido a su excelente resistencia a la corrosión combinada con buenas propiedades mecánicas y biocompatibilidad. Las aplicaciones más comunes incluyen implantes, componentes aeroespaciales, piezas de automoción, dispositivos biomédicos y utillaje.
P: ¿Qué tamaño de partícula se recomienda para los procesos de AM basados en láser?
R: Para los procesos de fusión de lecho de polvo láser, como DMLS y SLM, se suele recomendar un tamaño de partícula de 10 a 45 micras. Las partículas más finas por debajo de 10 micras pueden causar problemas de flujo y dispersión. La distribución del tamaño de las partículas también debe estar bien controlada.
P: ¿Cómo afecta la morfología del polvo a las propiedades?
R: El polvo altamente esférico y de flujo libre es deseable para aplicaciones AM. El polvo irregular y puntiagudo es adecuado para los métodos de prensado y sinterización. Las partículas satélites y los finos afectan negativamente al flujo del polvo y pueden crear defectos. Controlar la morfología del polvo es clave para un rendimiento óptimo.
P: ¿Cuáles son las principales diferencias entre el polvo 316L atomizado con gas y el atomizado con agua?
R: El polvo de 316L atomizado con gas tiene una morfología más esférica y una mejor fluidez. El polvo atomizado con agua presenta formas más irregulares pero proporciona una mayor compresibilidad deseada para aplicaciones de prensado y sinterizado. El polvo atomizado con gas tiene menor contenido de oxígeno.
P: ¿Qué métodos de posprocesamiento se utilizan en las piezas 316L AM?
R: El postprocesado habitual incluye el tratamiento térmico, el prensado isostático en caliente, el acabado superficial mediante esmerilado/mecanizado, el revestimiento y las pruebas de control de calidad. Esto ayuda a conseguir las propiedades deseadas, la precisión dimensional, la estética y la detección de defectos.
P: ¿Cuáles son los defectos más comunes del polvo 316L y cómo pueden evitarse?
R: Los defectos potenciales son porosidad, agrietamiento, mal acabado superficial, falta de fusión y tensiones residuales. Una cuidadosa optimización de los parámetros del proceso, el control de calidad del polvo, la orientación de la estructura y el postprocesado pueden minimizar estos defectos en las piezas de 316L.
P: ¿Qué normas se aplican al polvo 316L para AM y otras aplicaciones?
R: Las normas clave son la ASTM F3055 para polvos AM, la ASTM B822 para caracterización de polvos, la ASTM A240 para composición de aleaciones y las normas ISO para gestión de calidad. Los principales proveedores de polvo 316L están certificados conforme a estas normas.
P: ¿Qué factores determinan el precio del polvo 316L?
R: Los principales factores que influyen en el precio del polvo 316L son el nivel de calidad, el tamaño y la distribución de las partículas, el método de producción, la cantidad del pedido, los requisitos del comprador en cuanto a pruebas/control de calidad, embalaje y entrega. Las necesidades más estrictas aumentan el precio.
P: ¿Cómo se puede optimizar la resistencia a la corrosión de las piezas de 316L AM?
R: Las soluciones incluyen el control de los niveles de impurezas mediante tolerancias estrictas de composición química, el uso del prensado isostático en caliente para aumentar la densidad y reducir la porosidad, la aplicación de tratamientos de pasivación y el recocido en solución para mejorar la resistencia a la corrosión.
Compartir
MET3DP Technology Co., LTD es un proveedor líder de soluciones de fabricación aditiva con sede en Qingdao, China. Nuestra empresa está especializada en equipos de impresión 3D y polvos metálicos de alto rendimiento para aplicaciones industriales.
Solicite información para obtener el mejor precio y una solución personalizada para su empresa.
Artículos relacionados
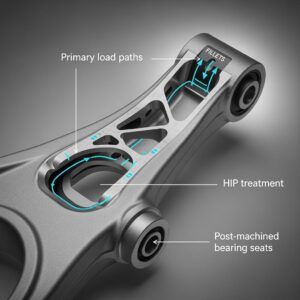
Metal 3D Printing for U.S. Automotive Lightweight Structural Brackets and Suspension Components
Leer Más "Acerca de Met3DP
Actualización reciente
Nuestro producto
CONTACTO
¿Tiene alguna pregunta? ¡Envíenos un mensaje ahora! Atenderemos su solicitud con todo un equipo tras recibir su mensaje.