Structural Support Beams via 3D Printed Aluminum Alloys
Índice
Introduction: Revolutionizing Aerospace Structures with Additive Manufacturing
The aerospace industry operates at the zenith of engineering ambition, constantly pushing the boundaries of performance, efficiency, and safety. Central to achieving these goals are the structural components that form the skeleton of every aircraft, satellite, and launch vehicle. Among these, aerospace support beams play a critical, albeit often unseen, role. These components are fundamental to distributing loads, maintaining structural integrity under extreme conditions, and ensuring the overall resilience of the airframe. Traditionally, manufacturing these vital parts involved subtractive methods like CNC machining from large billets of material, or complex casting and forging processes. While effective, these methods often come with limitations in terms of design complexity, material waste, and lead times.
Enter the era of fabricación aditiva (AM)más conocido como metal Impresión 3D. This transformative technology is fundamentally altering the landscape of aerospace design and production. Instead of removing material, AM builds parts layer by layer directly from digital models, using high-energy sources like lasers or electron beams to fuse fine metal powders. This approach unlocks unprecedented design freedom, enabling the creation of highly complex, estructuras ligeras that were previously impossible or prohibitively expensive to manufacture.
For aerospace support beams, the implications are profound. Engineers can now leverage sophisticated design tools like topology optimization to create beams that are significantly lighter yet maintain or even exceed the required strength and stiffness properties. This weight reduction directly translates to fuel savings, increased payload capacity, and enhanced overall aircraft performance – critical metrics in the aerospace sector. Furthermore, AM facilitates part consolidation, where multiple components of a traditional assembly can be redesigned and printed as a single, integrated unit, reducing part count, assembly time, and potential points of failure.
The materials driving this revolution in aerospace are advanced metal alloys, particularly high-performance aluminum alloys like AlSi10Mg and the specialist material Scalmalloy. These materials offer an exceptional balance of low density, good mechanical properties, and processability via AM techniques like Laser Powder Bed Fusion (L-PBF). Their adoption allows manufacturers to produce intricate componentes estructurales optimized for specific load cases and spatial constraints.
At Met3dp, headquartered in Qingdao, China, we are at the forefront of this manufacturing evolution. Specializing in industrial impresión 3D en metal solutions, including advanced printing equipment and high-performance metal powders, we empower aerospace companies to harness the full potential of additive manufacturing. Our commitment to industry-leading accuracy, reliability, and material quality ensures that the components produced using our technologies meet the stringent demands of mission-critical aerospace applications. This blog post delves into the specifics of utilizing 3D printed aluminum alloys, particularly AlSi10Mg and Scalmalloy®, for manufacturing robust, lightweight aerospace support beams, exploring the applications, advantages, materials, and key considerations for implementation.
Applications: Where 3D Printed Aluminum Beams Take Flight
The versatility and benefits of metal additive manufacturing, combined with the favorable properties of aluminum alloys, have opened up a wide range of applications for 3D printed support beams within the aerospace and related high-technology sectors. Procurement managers and engineers seeking innovative aerospace manufacturing solutions are increasingly turning to AM for components where weight savings, complex geometries, or consolidated designs offer significant advantages.
Here are some key application areas:
- Aircraft Structural Components:
- Fuselage Frames & Stringers: Optimized beam structures contributing to the overall skeletal integrity of the aircraft body, designed using topology optimization for maximum load-bearing efficiency with minimum weight.
- Wing Ribs & Spar Elements: Complex internal beam structures within wings that need to withstand significant aerodynamic loads while minimizing mass. AM allows for intricate internal lattice structures.
- Bracketry & Mounts: Highly customized brackets for mounting engines, systems, or interior components. AM enables the creation of non-standard, organically shaped brackets perfectly tailored to their specific location and load requirements, often consolidating multiple parts into one.
- Door and Hatch Frames: Structural beams surrounding openings in the fuselage, requiring high strength and precise geometry.
- Componentes del tren de aterrizaje: Certain structural elements within landing gear assemblies can benefit from the lightweighting potential of optimized aluminum AM parts, provided fatigue and impact requirements are met.
- Satellite Components:
- Bus Structures: The primary structure of a satellite, often a complex framework of beams and panels. Reducing the mass of these beams is critical for lowering launch costs. AM allows for highly optimized, complex truss-like structures.
- Antenna Supports & Booms: Lightweight yet stiff beams required for deploying and supporting large antennas or scientific instruments. Design complexity enabled by AM is a major advantage here.
- Optical Benches: Structures requiring high stability and low thermal expansion, where optimized beam designs can help achieve performance targets.
- Unmanned Aerial Vehicles (UAVs) & Drones:
- Estructuras de fuselaje: The entire airframe of smaller UAVs can incorporate 3D printed beams for maximum aligeramiento, extending flight endurance and payload capacity.
- Internal Support Structures: Beams supporting batteries, sensors, and other internal hardware, optimized for space and weight constraints.
- Defense Applications:
- Missile Components: Structural elements within missile airframes where weight reduction and performance are paramount.
- Military Aircraft: Custom support beams for specialized equipment or modifications in military aircraft, benefiting from AM’s ability to produce bespoke components rapidly.
- High-Performance Automotive & Motorsport:
- Chassis Components: Structural beams and nodes within the chassis of high-performance vehicles where reducing weight enhances acceleration, handling, and fuel efficiency.
- Suspension Components: Optimized support arms and linkages where stiffness-to-weight ratio is critical.
The demand for these components comes from major aerospace OEMs (Original Equipment Manufacturers), Tier 1 and Tier 2 suppliers, satellite manufacturers, defense contractors, and specialized engineering firms. As an experienced aluminum alloy parts supplier utilizing advanced additive manufacturing, Met3dp works closely with these industry players to develop and produce custom support beams that meet exacting performance specifications. Our capability extends from prototyping single complex beams to handling series production requirements, ensuring a reliable supply chain for these critical parts. The ability to produce bespoke component production runs efficiently makes AM particularly attractive for specialized platforms or upgrade programs where traditional tooling costs would be prohibitive.
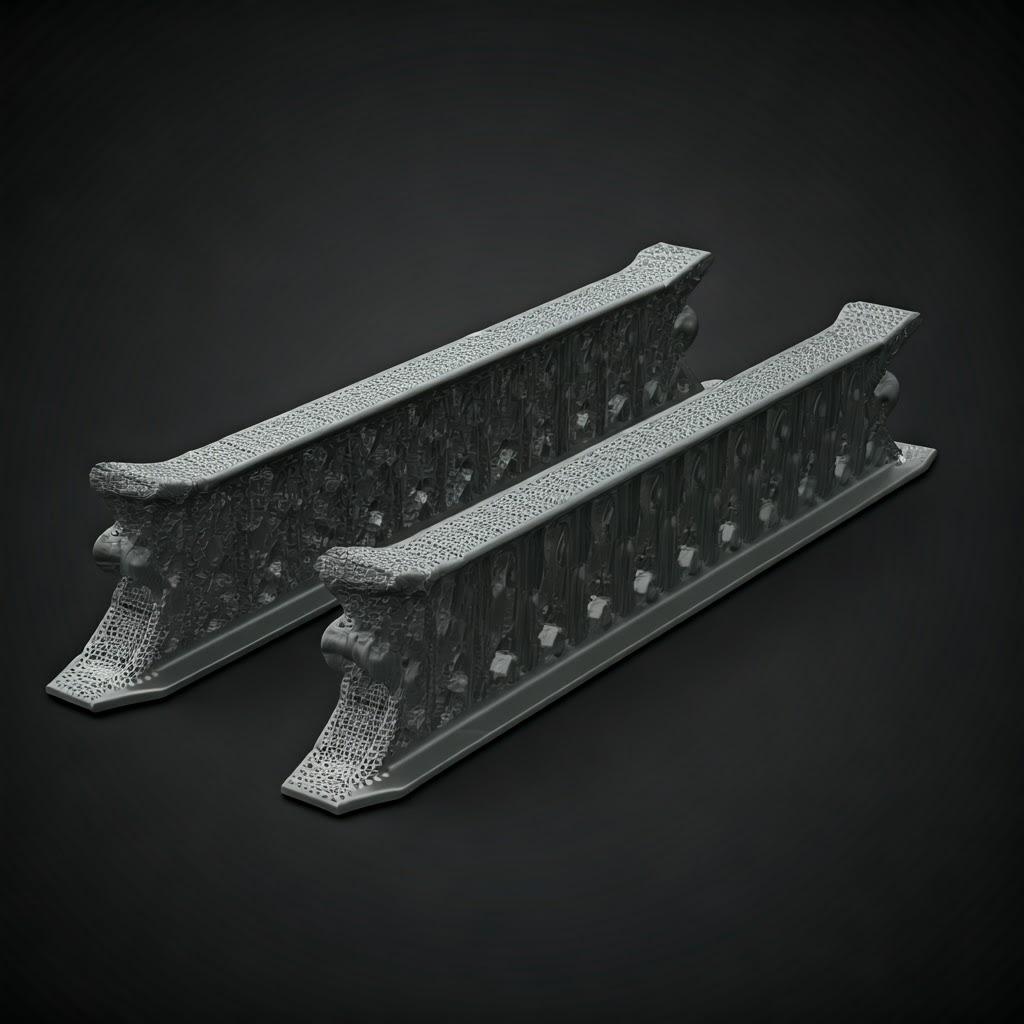
Advantages: Why Choose Metal 3D Printing for Aerospace Beams?
While traditional manufacturing methods have served the aerospace industry well for decades, impresión 3D en metal offers a compelling suite of advantages, particularly for components like structural support beams where optimization yields significant payoffs. Engineers and procurement specialists evaluating manufacturing routes should consider the unique benefits additive manufacturing brings to the table compared to conventional machining, casting, or fabrication approaches.
Key Advantages of AM for Aerospace Support Beams:
- Unmatched Design Freedom & Complexity:
- Optimización de la topología: AM seamlessly integrates with topology optimization software. This allows engineers to define load cases and design constraints, letting algorithms generate highly efficient, often organic-looking beam structures that place material only where it’s structurally necessary. This leads to maximum performance with minimal weight.
- Geometrías complejas: Internal channels for cooling or wiring, intricate lattice structures for enhanced stiffness-to-weight ratios, and smoothly blended variable cross-sections are all feasible with AM. Such features are often impossible or extremely costly to produce using traditional methods.
- Generative Design: Similar to topology optimization, generative design tools can explore hundreds or thousands of design variations based on performance criteria, resulting in innovative and high-performing beam designs.
- Significant Weight Reduction (Lightweighting):
- This is arguably the most critical advantage for aerospace. By leveraging topology optimization and complex geometries, AM can produce support beams that are 20-50% lighter (or sometimes more) than their traditionally manufactured counterparts while maintaining or exceeding strength and stiffness requirements.
- Every kilogram saved on an aircraft translates directly into lower fuel consumption, reduced emissions, increased payload capacity, or extended range over the aircraft’s lifespan.
- Consolidación de piezas:
- Complex assemblies consisting of multiple individual beams, brackets, and fasteners can often be redesigned and manufactured as a single, monolithic 3D printed component.
- Ventajas: Reduced part count simplifies inventory and logistics, eliminates assembly labor and time, reduces potential points of failure (like fastener joints), and often results in a lighter, stiffer final structure.
- Reduced Lead Times (Especially for Prototypes & Low Volumes):
- AM eliminates the need for expensive and time-consuming tooling (e.g., molds, dies, jigs, fixtures) required for casting, forging, or complex machining setups.
- Digital design files can be sent directly to the printer, allowing for rapid prototyping and design iteration cycles. This accelerates product development significantly.
- Para bespoke component production or small series runs common in aerospace upgrades or specialized platforms, AM is often faster and more cost-effective than setting up traditional manufacturing lines.
- Material Efficiency & Reduced Waste:
- Subtractive manufacturing, like CNC machining, starts with a large block of material and removes potentially 80-90% of it to arrive at the final shape, generating significant waste (swarf).
- Additive manufacturing, while not entirely waste-free (support structures, some powder loss), uses material much more efficiently, adding it only where needed. This is particularly advantageous when working with expensive aerospace-grade alloys.
- Supply Chain Optimization:
- Digital manufacturing allows for distributed production. Designs can be digitally transmitted and printed closer to the point of need, potentially reducing shipping costs and lead times.
- On-demand production capability reduces the need for large inventories of spare parts.
- Rendimiento mejorado:
- Optimized designs can lead to components with superior stiffness-to-weight ratios.
- Features like conformal cooling channels (if needed for specific beam applications near heat sources) can be integrated directly into the design.
While AM offers these substantial benefits, it’s crucial to partner with an experienced provider like Met3dp. Our deep understanding of aerospace manufacturing solutions ensures that these advantages are realized effectively. We leverage our advanced printers and process controls to maximize the potential of AM for producing high-quality, reliable aerospace support beams.
Material Focus: AlSi10Mg and Scalmalloy® for Demanding Aerospace Needs
The choice of material is paramount in aerospace engineering, directly impacting component weight, strength, durability, and resistance to environmental factors. For 3D printed aerospace support beams, aluminum alloys are often preferred due to their inherent low density combined with good mechanical properties. Among the additive manufacturing-compatible aluminum alloys, AlSi10Mg y Scalmalloy stand out as leading candidates, each offering distinct advantages.
AlSi10Mg: The Workhorse Aluminum Alloy
AlSi10Mg is a well-established aluminum alloy containing silicon and magnesium, traditionally used in casting. Its adaptation for Laser Powder Bed Fusion (L-PBF) has made it one of the most widely used materials in metal AM.
- Key Properties & Advantages:
- Buena relación resistencia-peso: Offers respectable mechanical properties suitable for many structural applications, especially after appropriate heat treatment (typically T6).
- Excellent Processability: It is relatively easy to process using L-PBF, with well-understood parameter sets leading to dense, reliable parts.
- Good Thermal Properties: Suitable for applications requiring good thermal conductivity.
- Resistencia a la corrosión: Exhibits decent resistance to corrosion.
- Rentabilidad: Generally more affordable than higher-performance or specialized alloys like Scalmalloy®.
- Disponibilidad: Widely available from numerous proveedores de polvo de metal.
- Consideraciones:
- Lower absolute strength and fatigue performance compared to high-strength aluminum alloys or Scalmalloy®.
- Requires heat treatment (typically Solution Treatment and Artificial Aging – T6) after printing to achieve optimal mechanical properties. This adds a post-processing step and can potentially cause distortion if not managed carefully.
Scalmalloy®: High-Performance Aluminum for AM
Scalmalloy® is a patented high-performance aluminum-magnesium-scandium alloy specifically designed for additive manufacturing by APWORKS. It pushes the boundaries of what’s achievable with 3D printed aluminum.
- Key Properties & Advantages:
- Fuerza excepcional: Offers mechanical properties (yield strength, ultimate tensile strength) significantly higher than AlSi10Mg, approaching or even exceeding those of some traditional high-strength 7xxx series aluminum alloys.
- Excellent Ductility & Fatigue Life: Maintains good ductility despite its high strength, leading to superior fatigue performance, which is critical for aerospace components subjected to cyclic loading.
- Alta resistencia específica: Its outstanding strength combined with low density results in an exceptional specific strength (strength-to-weight ratio), ideal for lightweighting aerospace structures.
- Good Weldability & Processability: Designed for good performance during the L-PBF process.
- Stable at Elevated Temperatures: Retains properties better at moderately elevated temperatures compared to AlSi10Mg.
- Consideraciones:
- Mayor coste: Scalmalloy® powder is significantly more expensive than AlSi10Mg due to its composition (including scandium) and licensing.
- Procesamiento especializado: May require more finely tuned L-PBF process parameters compared to AlSi10Mg.
- Disponibilidad: Primarily available through licensed suppliers.
Material Properties Comparison (Typical values after appropriate heat treatment):
Propiedad | Unidad | AlSi10Mg (T6 Condition) | Scalmalloy® (Heat Treated) | Notas |
---|---|---|---|---|
Densidad | g/cm3 | ~2.67 | ~2.68 | Very similar, both lightweight |
Yield Strength (Rp0.2) | MPa | ~230 – 280 | ~450 – 520 | Scalmalloy® significantly stronger |
Resistencia a la tracción | MPa | ~330 – 430 | ~500 – 580 | Scalmalloy® significantly stronger |
Alargamiento a la rotura | % | ~6 – 10 | ~10 – 18 | Scalmalloy® generally more ductile |
Módulo de elasticidad | GPa | ~70 – 75 | ~70 – 75 | Similar stiffness |
Dureza | HBW | ~100 – 120 | ~140 – 160 | Scalmalloy® harder |
Temperatura máxima de servicio | °C | ~100 – 150 | ~200 – 250 | Scalmalloy® better at higher temperatures |
Exportar a hojas
Note: Properties can vary based on printing parameters, build orientation, heat treatment, and specific powder batch.
Met3dp’s Material Capabilities:
As a leader in metal additive manufacturing, Met3dp understands the critical role of powder quality. Our company employs industry-leading atomización de gas techniques to produce high-quality spherical metal powders, including aluminum alloys optimized for L-PBF. Our advanced powder making system ensures high sphericity, good flowability, and controlled particle size distribution – factors essential for printing dense, high-quality parts with superior and consistent mechanical properties. Whether your application demands the reliable performance of AlSi10Mg or the exceptional strength of Scalmalloy®, Met3dp possesses the expertise and polvos metálicos de alta calidad to meet your needs. We work with aerospace clients to select the optimal material based on performance requirements, budget constraints, and application specifics, ensuring the final 3D printed support beam delivers uncompromising performance and reliability.
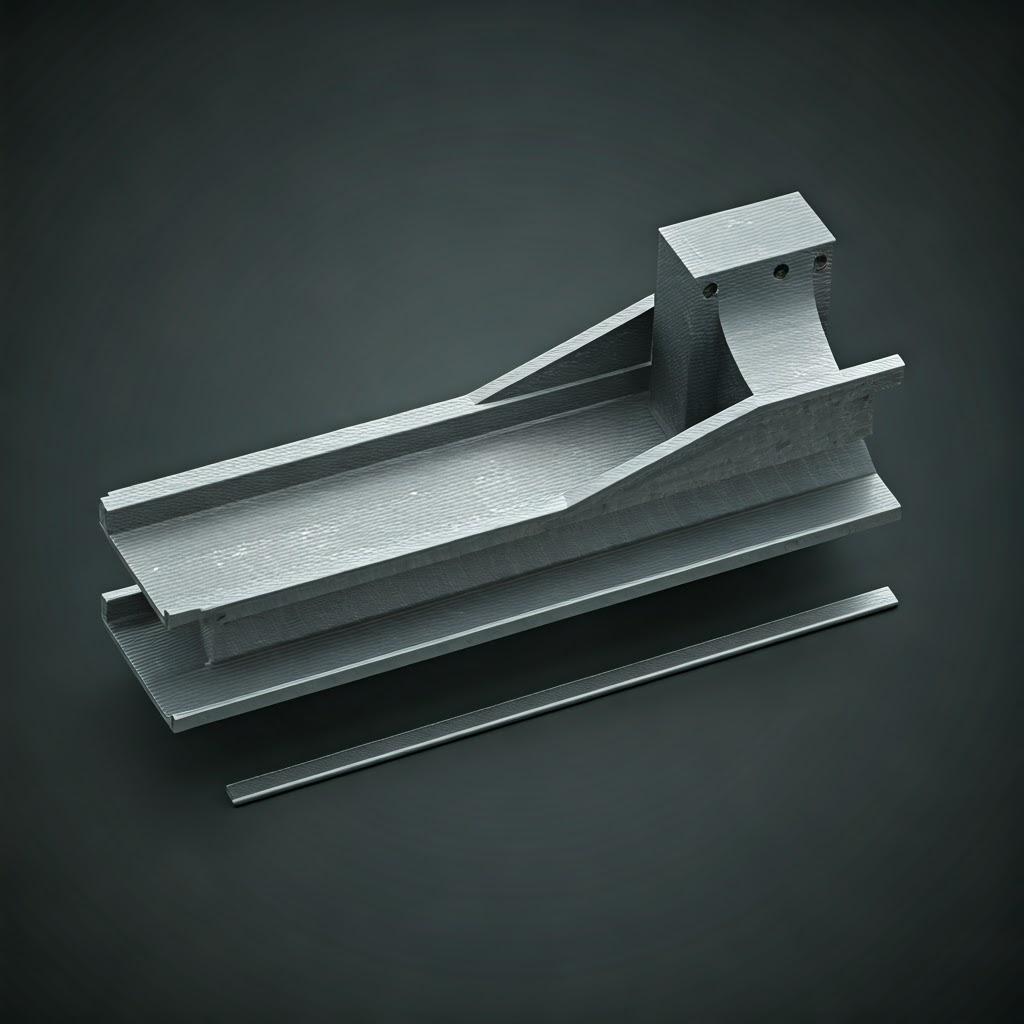
Design for Additive Manufacturing (DfAM): Optimizing Beams for Printability
Simply replicating a design intended for traditional manufacturing using additive manufacturing rarely unlocks the full potential of the technology. To truly leverage the benefits of 3D printing for aerospace support beams – particularly achieving significant weight savings and performance gains – engineers must embrace Diseño para fabricación aditiva (DfAM) principles. DfAM is a design methodology that considers the capabilities and constraints of the AM process from the outset, leading to parts that are not only functional but also optimized for successful, efficient printing. Applying DfAM is crucial when working with aluminum alloys like AlSi10Mg and Scalmalloy® using Laser Powder Bed Fusion (L-PBF).
Key DfAM Considerations for Aluminum Aerospace Beams:
- Leverage Topology Optimization & Generative Design:
- These computational tools are essential for lightweighting structural components like beams. Start with the design space, load conditions, constraints, and performance targets (e.g., stiffness, stress limits).
- Allow topology optimization software to remove material from low-stress areas, resulting in efficient, often organic-looking structures that inherently minimize weight while meeting structural requirements.
- Utilize generative design tools to explore a wider range of manufacturable design possibilities based on defined goals and constraints.
- Optimize Build Orientation:
- The orientation of the beam on the build plate significantly impacts print time, support structure requirements, surface finish, residual stress accumulation, and potentially anisotropic mechanical properties.
- Aim to orient the part to minimize the need for support structures, especially on critical functional surfaces or hard-to-reach internal areas.
- Consider the primary load directions; aligning critical tensile load paths perpendicular to the build layers is sometimes preferred, though properties in aluminum AM tend to be relatively isotropic compared to some other materials or processes. Collaborate with your AM service provider, like Met3dp, to determine the optimal orientation strategy.
- Design for Support Structures:
- L-PBF requires support structures for overhanging features (typically angles less than 45 degrees from the horizontal plane) and to anchor the part to the build plate, managing thermal stresses.
- Minimice los voladizos: Design with self-supporting angles (ideally >45 degrees) wherever possible. Utilize chamfers or fillets instead of sharp horizontal overhangs.
- Accessibility for Removal: Ensure supports are placed in locations where they can be easily accessed and removed during post-processing without damaging the part. Avoid complex internal supports if feasible.
- Support Optimization: Use specialized software tools to generate optimized support structures (e.g., block, cone, tree supports) that use minimal material, are easy to remove, and effectively manage heat dissipation and warping.
- Incorporate Lattice Structures:
- For beams requiring high stiffness with minimal weight, consider replacing solid sections with internal lattice structures.
- Various lattice types (e.g., cubic, octet-truss, gyroid) offer different structural and thermal properties. Select the appropriate type and density based on the specific load case and desired performance.
- Ensure lattice cell sizes are large enough for effective powder removal during post-processing.
- Espesor de la pared y tamaño de las características:
- Respect minimum printable wall thicknesses (typically 0.4-0.8 mm for L-PBF aluminum, depending on the machine and geometry) to ensure features resolve correctly.
- Avoid overly thick sections where possible, as these can accumulate more residual stress and increase print time and material consumption. Topology optimization naturally helps avoid unnecessarily thick regions.
- Manage Residual Stress:
- The rapid heating and cooling inherent in L-PBF can induce residual stresses, potentially causing warping or cracking, especially in large or complex beams.
- Design Strategies: Use rounded corners instead of sharp edges, maintain uniform wall thicknesses where possible, and incorporate stress-relieving features if necessary. Proper build orientation and support strategy are also critical.
- Post-procesamiento: A mandatory stress relief heat treatment is typically required immediately after printing aluminum parts.
- Consider Post-Processing Needs:
- Designate critical surfaces or features that require tight tolerances or specific surface finishes. Add extra material (machining stock) to these areas if subsequent CNC machining is planned.
- Design features like holes or channels slightly undersized if they will be finished via machining or reaming to achieve final tolerances.
By integrating these design guidelines for metal AM early in the development process, engineers can create aerospace support beams that are lighter, stronger, and more efficiently manufactured. Partnering with an AM specialist like Met3dp provides access to expertise in DfAM, ensuring your designs are optimized for our advanced métodos de impresión and materials.
Achievable Precision: Tolerance, Surface Finish, and Dimensional Accuracy
For aerospace components, precision is non-negotiable. Support beams must fit correctly within assemblies and perform reliably under load, necessitating strict adherence to dimensional tolerances and surface finish requirements. While metal additive manufacturing offers incredible design freedom, it’s important for engineers and procurement managers to understand the levels of precision achievable directly from the L-PBF process and what can be attained through post-processing.
Dimensional Accuracy and Tolerance:
- As-Built Tolerance: The dimensional accuracy achievable directly after printing with L-PBF for aluminum alloys like AlSi10Mg and Scalmalloy® typically falls within the range of ±0.1 mm to ±0.3 mm for smaller features (e.g., up to 50-100 mm), or ±0.1% to ±0.2% of the overall dimension for larger parts.
- Factors influencing this include machine calibration, laser spot size, layer thickness, thermal stability during the build, powder characteristics, and part geometry/orientation.
- Heat Treatment Effects: Post-print heat treatment (especially stress relief and T6 aging for AlSi10Mg) is crucial for achieving desired mechanical properties but can cause slight dimensional changes (shrinkage or growth) and potential distortion. These effects must be anticipated and compensated for, either in the initial design or through subsequent machining.
- Achieving Tighter Tolerances: For critical interfaces, mounting points, or bearing surfaces requiring tolerances tighter than the as-built capability (e.g., ±0.025 mm to ±0.05 mm), post-process CNC machining is typically employed. Sufficient machining stock must be included in the AM design for these features.
Acabado superficial (rugosidad):
- As-Built Surface Roughness (Ra): The surface finish of L-PBF parts is inherently rougher than machined surfaces due to the layer-by-layer process and partially melted powder particles adhering to the surface.
- Top Surfaces: Generally exhibit the smoothest finish, often in the range of Ra 5-10 µm.
- Vertical Walls: Typically have Ra values between 8-15 µm.
- Up-facing/Down-facing Surfaces: Surfaces angled relative to the build plate vary, with down-facing surfaces (supported) usually being rougher (Ra 15-25 µm or more) due to support contact points.
- Canales internos: Can be challenging to finish and may retain a rougher surface unless specifically targeted with abrasive flow machining or similar techniques.
- Mejora del acabado superficial: Various post-processing techniques can significantly improve the surface finish:
- Bead Blasting / Shot Peening: Common for achieving a uniform matte finish (Ra 3-6 µm) and can impart beneficial compressive stresses.
- Tumbling / Vibratory Finishing: Effective for deburring and smoothing external surfaces of smaller parts (Ra 1-3 µm possible).
- Pulido: Manual or automated polishing can achieve very smooth, mirror-like finishes (Ra < 0.5 µm) but is labor-intensive and typically reserved for specific areas.
- Electrochemical Polishing / Chemical Etching: Can smooth surfaces, including complex geometries, but requires careful process control.
- Mecanizado: Provides the best control over both surface finish (Ra < 1 µm easily achievable) and dimensional accuracy on specific features.
Quality Control and Inspection:
- Meeting stringent quality control aerospace standards is essential. This involves rigorous inspection throughout the process.
- Análisis de polvo: Ensuring incoming metal powder meets specifications (chemistry, particle size distribution, flowability).
- Supervisión durante el proceso: Utilizing melt pool monitoring or thermal imaging systems during the build to detect potential anomalies. Met3dp utilizes advanced process monitoring to ensure build consistency.
- Inspección dimensional: Using Coordinate Measuring Machines (CMM), 3D scanning, or traditional metrology tools to verify dimensional accuracy against the design specifications.
- Ensayos no destructivos (END): Employing methods like X-ray computed tomography (CT scanning) to detect internal defects (porosity, inclusions) and verify internal geometries, especially for complex beams with internal features.
- Pruebas de materiales: Performing tensile tests, hardness tests, and microstructural analysis on sample coupons printed alongside the parts to verify material properties meet requirements.
Understanding these precision aspects allows for realistic design specifications and informs the necessary post-processing steps to ensure the final 3D printed aluminum beam meets all functional and aerospace component finishing requisitos.
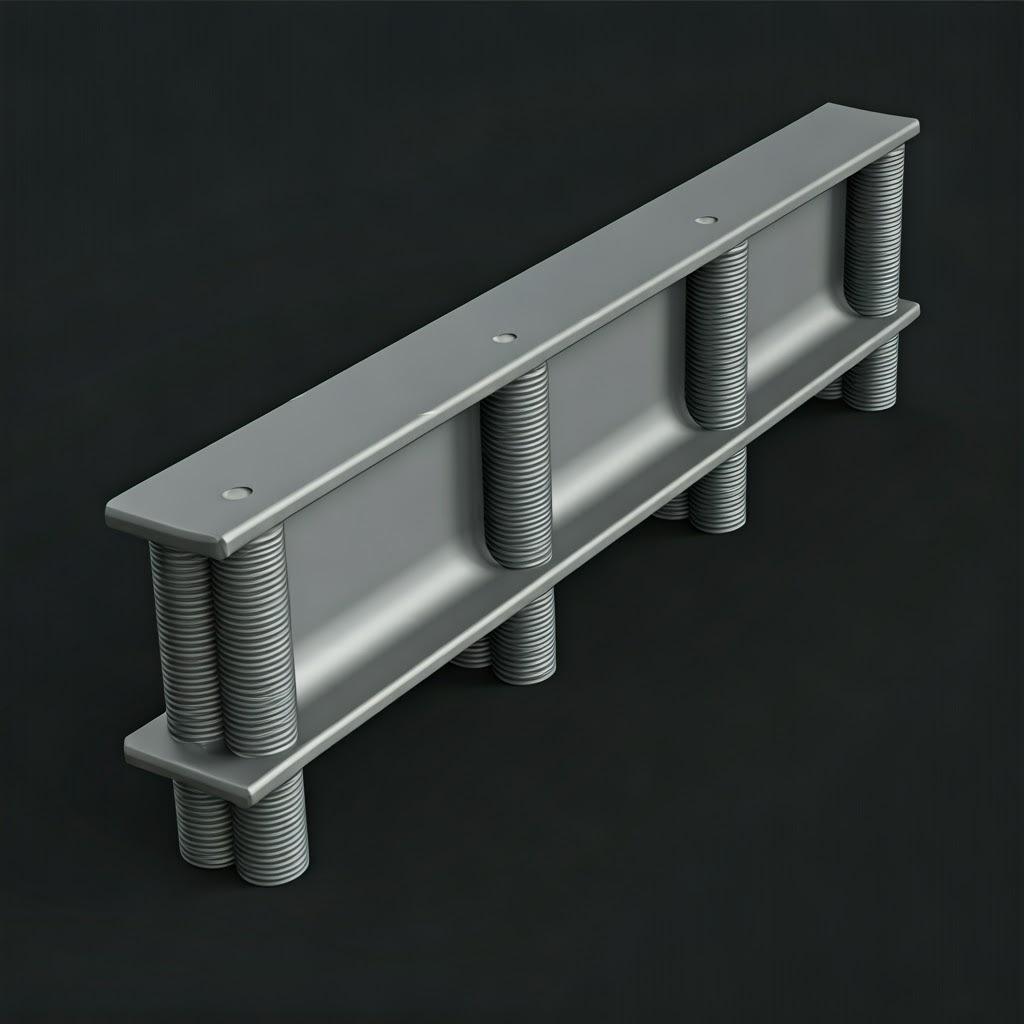
Post-Processing: Refining 3D Printed Aluminum Beams
Parts produced by Laser Powder Bed Fusion, especially critical aerospace components like support beams made from AlSi10Mg or Scalmalloy®, are rarely ready for use immediately after emerging from the printer. A series of essential post-procesamiento steps are required to transform the as-built part into a functional, reliable component meeting stringent aerospace standards. These steps address residual stresses, achieve desired material properties, remove support structures, refine surface finish, and ensure dimensional accuracy.
Common Post-Processing Workflow for Aluminum AM Beams:
- Powder Removal / Depowdering:
- Carefully removing the component from the build plate, which often contains loose and semi-sintered powder.
- Thoroughly cleaning the part to remove trapped powder, especially from internal channels or complex features, using compressed air, brushing, or ultrasonic cleaning. Effective depowdering is crucial for subsequent steps like heat treatment and HIP (if required).
- Tratamiento térmico antiestrés:
- Crucial Step: This is typically the first thermal treatment performed, often while the part is still attached to the build plate (though sometimes after careful removal).
- Propósito: To relieve internal stresses built up during the rapid heating and cooling cycles of the L-PBF process, minimizing the risk of distortion or cracking during subsequent handling or support removal.
- Proceso: Heating the part to a specific temperature below the alloy’s aging temperature (e.g., ~300°C for AlSi10Mg), holding it for a defined period (e.g., 1-2 hours), and then slowly cooling it.
- Extracción de la placa de construcción:
- If not done before stress relief, the part is carefully separated from the build plate, typically using wire EDM (Electrical Discharge Machining), sawing, or machining.
- Retirada de la estructura de soporte:
- Removing the support structures generated during the build process.
- Métodos: This can involve manual breaking and cutting (for easily accessible supports), CNC machining, grinding, or sometimes wire EDM for delicate or hard-to-reach supports. Care must be taken to avoid damaging the part surface. Effective support removal metal AM requires planning during the DfAM phase.
- Solution Treatment and Aging (Precipitation Hardening – e.g., T6 for AlSi10Mg):
- Propósito: To achieve the final desired mechanical properties (strength, hardness, ductility). This is particularly important for AlSi10Mg. Scalmalloy® also benefits from specific aging treatments.
- Process (AlSi10Mg T6 example):
- Solución Tratamiento: Heating to a high temperature (~500-540°C) to dissolve alloying elements into the aluminum matrix.
- Enfriamiento: Rapidly cooling (e.g., in water or polymer) to lock the elements in solution.
- Artificial Aging: Reheating to a lower temperature (~150-180°C) for several hours to allow controlled precipitation of strengthening phases.
- Control: Precise control of temperatures and times is critical. This step can potentially cause distortion, which needs to be managed.
- Hot Isostatic Pressing (HIP) – (Optional but common for critical parts):
- Propósito: To close internal microporosity, improving fatigue life, ductility, and fracture toughness. Often required for demanding aerospace applications.
- Proceso: Subjecting the part to high temperature (below melting point) and high inert gas pressure (e.g., Argon) simultaneously. The pressure collapses internal voids.
- Consideración: HIP can cause slight dimensional changes and may affect surface finish.
- Acabado superficial:
- Applying appropriate surface finishing techniques to meet requirements for roughness, aesthetics, or preparation for coatings.
- Common Methods: Bead blasting (uniform matte finish), shot peening (compressive stress), tumbling/vibratory finishing (smoothing, deburring), polishing (specific areas), or specialized treatments like electrochemical polishing.
- Final Machining (CNC):
- Performing high-precision CNC machining 3D prints on critical features, interfaces, mounting holes, or surfaces that require tighter tolerances or smoother finishes than achievable through AM and other finishing steps.
- Ensures the final part meets all dimensional specifications detailed in the engineering drawing.
- Final Cleaning and Inspection:
- Thoroughly cleaning the part to remove any machining fluids, debris, or residues.
- Conducting final dimensional inspection (CMM, scanning), NDT (CT scanning if required), and surface finish verification to ensure full quality assurance AM parts.
The complexity and sequence of these steps depend heavily on the specific alloy, part geometry, and application requirements. Met3dp provides comprehensive solutions, managing the entire post-processing chain to deliver aerospace support beams that meet the highest standards of quality and performance.
Overcoming Challenges in Printing Aerospace Beams
While metal additive manufacturing offers transformative potential for aerospace components like support beams, the process is not without its challenges. Successfully printing large, complex, or mission-critical aluminum parts requires careful process control, material understanding, and robust quality management systems. Awareness of these potential hurdles allows engineers and manufacturers to implement mitigation strategies proactively.
Common Metal AM Challenges and Solutions for Aluminum Beams:
- Residual Stress, Distortion, and Warping:
- Desafío: The high thermal gradients inherent in L-PBF create internal stresses as layers heat and cool rapidly. These stresses can cause parts to warp during the build, detach from supports, or distort after removal from the build plate, particularly with large flat sections or asymmetric geometries common in beams. Warping distortion aluminum is a known issue.
- Solutions:
- DfAM: Design features to minimize stress concentration (fillets, uniform thickness).
- Orientación y soportes optimizados: Strategically orient the part and design robust support structures to anchor the part effectively and draw heat away.
- Optimización de los parámetros del proceso: Fine-tuning laser power, scan speed, and scan strategy (e.g., island scanning) to minimize thermal gradients.
- Gestión térmica: Using heated build plates and controlled chamber atmospheres.
- Mandatory Stress Relief: Performing stress relief heat treatment immediately after printing.
- Control de la porosidad:
- Desafío: Small internal voids (pores) can form during printing due to gas entrapment (from powder or shield gas) or incomplete fusion (lack-of-fusion voids). Porosity can significantly degrade mechanical properties, especially fatigue life, which is critical for structural beams.
- Solutions:
- Polvo de alta calidad: Using powder with low internal gas porosity, controlled particle size distribution, and good flowability (Met3dp’s focus on advanced powder handling safety and production is key here).
- Parámetros de proceso optimizados: Ensuring sufficient energy density for complete melting without keyholing (vapor depression instability).
- Control de la atmósfera inerte: Maintaining a high-purity inert gas environment (Argon) in the build chamber to minimize oxidation and gas pickup.
- Prensado isostático en caliente (HIP): An effective post-processing step to close residual porosity.
- NDT Inspection: Using CT scanning to detect and quantify porosity.
- Dificultades para retirar la ayuda:
- Desafío: Supports, while necessary, must be removed. Complex internal channels or tightly packed lattice structures within beams can make support removal issues particularly challenging, time-consuming, and potentially damaging to the part.
- Solutions:
- DfAM: Design for support minimization and accessibility. Use self-supporting angles (>45°) where possible. Design internal channels large enough for access and powder/support removal.
- Optimized Support Structures: Utilize support types (e.g., tree, cone) that are easier to remove and minimize contact points with the part surface.
- Técnicas de eliminación especializadas: Employing appropriate tools and methods (manual, machining, EDM) based on support location and complexity.
- Surface Finish Limitations:
- Desafío: The as-built surface roughness of L-PBF parts may not meet aerospace requirements for fatigue performance or aerodynamic smoothness on external surfaces.
- Solutions:
- Orientación: Orienting critical surfaces upwards or vertically for better as-built finish.
- Post-procesamiento: Implementing appropriate finishing steps (bead blasting, machining, polishing) as planned during the DfAM phase.
- Process Repeatability and Consistency:
- Desafío: Ensuring that every beam produced has the same dimensions, microstructure, and mechanical properties requires tight control over the entire process chain, from powder batch to final inspection.
- Solutions:
- Sólido sistema de gestión de la calidad (SGC): Implementing rigorous procedures for machine calibration, maintenance, powder handling, process parameter control, and operator training (essential for aerospace certification like AS9100).
- AM Process Monitoring: Utilizing sensors and monitoring systems (e.g., melt pool monitoring) to track build consistency in real-time.
- Comprehensive Testing: Consistent material testing (tensile coupons) with each build.
Met3dp addresses these challenges through decades of collective expertise in metal additive manufacturing. Our comprehensive approach, spanning advanced SEBM (Note: L-PBF is used for Aluminum) and L-PBF printers, high-quality powder production via gas atomization and PREP technologies, and dedicated application development services, ensures we can reliably produce complex aerospace support beams that meet the industry’s demanding standards. Our focus on process control and quality assurance minimizes risks and delivers dependable components. Explore Quiénes somos to learn more about Met3dp’s commitment to advancing additive manufacturing.
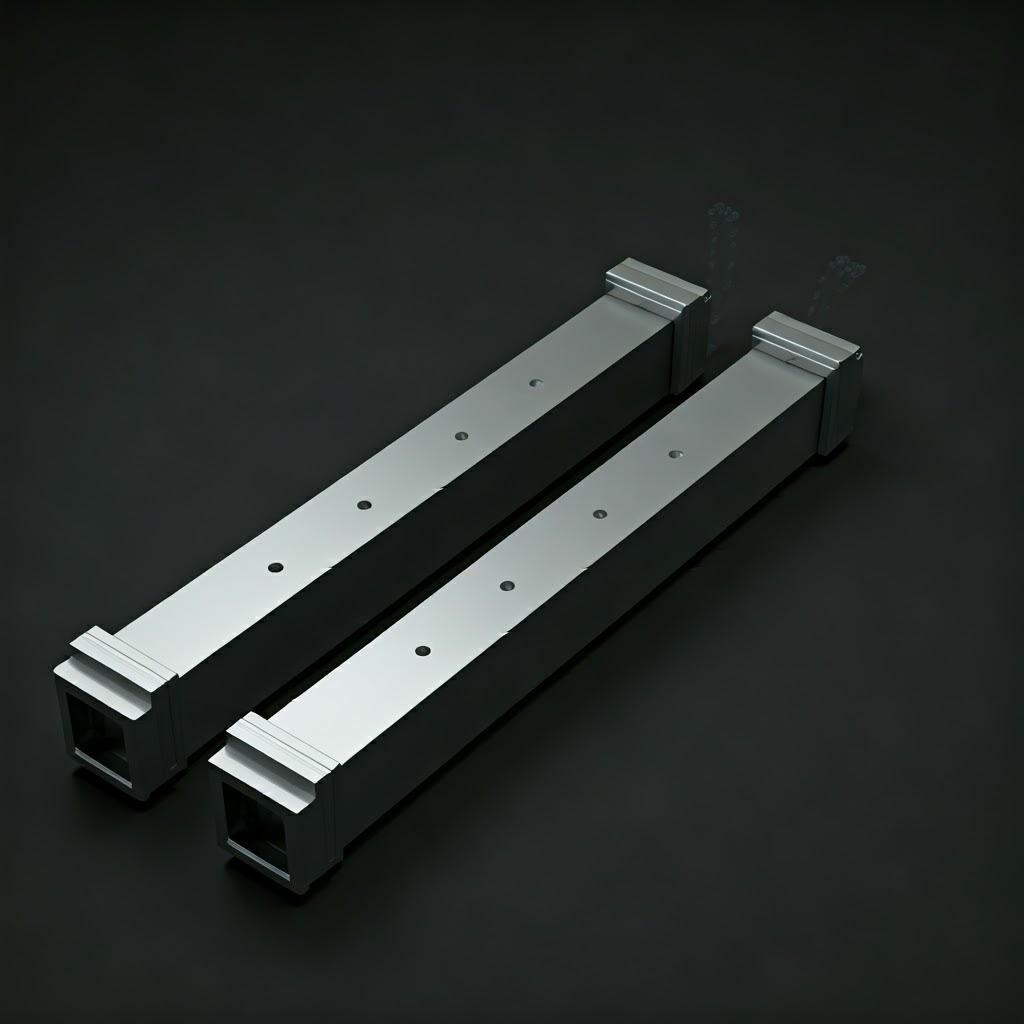
Selecting Your Partner: Choosing the Right Metal 3D Printing Service Provider
The success of incorporating 3D printed aluminum support beams into your aerospace projects hinges significantly on the capabilities and reliability of your manufacturing partner. Choosing the right metal 3D printing service bureau o proveedor de fabricación aditiva aeroespacial is a critical decision for engineers and procurement managers. The unique demands of the aerospace industry – stringent quality requirements, complex geometries, advanced materials, and rigorous certification needs – necessitate a provider with specialized expertise and proven performance.
Key Criteria for Evaluating AM Providers for Aerospace Beams:
- Aerospace Certifications & Quality Management:
- Certificación AS9100: This is the gold standard quality management system (QMS) for the aviation, space, and defense industries. Ensure the provider holds a current AS9100 certification (or equivalent, like EN 9100), demonstrating robust processes for traceability, risk management, process control, and quality assurance tailored to aerospace requirements.
- Documented QMS: Even beyond certification, review their overall QMS documentation, including procedures for material handling, machine calibration, operator training, process validation, and non-conformance management.
- Material Expertise & Capability:
- Proven Experience with AlSi10Mg & Scalmalloy®: Verify the supplier has extensive, documented experience printing the specific aluminum alloy required for your beam. Ask for case studies, parameter development data, or material property test results specific to these alloys processed on their machines.
- Powder Quality Control: Inquire about their procedures for sourcing, testing, handling, storing, and recycling metal powders to prevent contamination and ensure consistency batch-to-batch. Providers like Met3dp, who manufacture their own high-quality powders using advanced methods like gas atomization, offer significant advantages in material control and traceability.
- Equipment & Technology:
- Machine Platform: Understand the specific L-PBF machines they operate. Are they industrial-grade machines known for reliability and consistency? (Met3dp utilizes industry-leading printers optimized for demanding applications).
- Construir volumen: Ensure their machines have a large enough build envelope to accommodate the size of your support beam.
- Supervisión de procesos: Do their machines incorporate in-situ process monitoring capabilities (e.g., melt pool monitoring, thermal imaging) to enhance quality control during the build?
- Technical Expertise & Engineering Support:
- Apoyo al DfAM: Does the provider offer Design for Additive Manufacturing (DfAM) consultation to help optimize your beam design for printability, weight reduction, and performance?
- Application Engineering: Can their team provide insights into material selection, orientation strategies, support generation, and post-processing planning?
- Resolución de problemas: Do they have experienced engineers capable of troubleshooting potential issues during production?
- Capacidades de postprocesado:
- In-House vs. Outsourced: Determine which post-processing steps (stress relief, heat treatment, HIP, support removal, machining, finishing, inspection) they perform in-house versus outsource. In-house capabilities generally offer better control over quality, lead time, and communication.
- Equipment & Expertise: Verify they have the necessary equipment (furnaces, CNC machines, CMMs, NDT equipment) and trained personnel for required post-processing steps.
- Capacity & Lead Time:
- Capacidad de producción: Can they handle your required volume, whether for prototypes or series production?
- Quoted Lead Times: Are their lead times competitive and realistic? Understand their process for scheduling and managing production workflows.
- Request for Quote (RFQ) Process & Communication:
- Evaluate their responsiveness and clarity during the request for quote (RFQ) AM process. Do they provide detailed quotes outlining all costs and steps?
- Assess their communication protocols and willingness to collaborate throughout the project.
Met3dp, headquartered in Qingdao, China, embodies these criteria, positioning itself as a premier partner for aerospace additive manufacturing. With decades of collective expertise, industry-leading printing technology, advanced polvo metálico production systems (gas atomization and PREP), and a comprehensive suite of services spanning DfAM support to final inspection, Met3dp delivers end-to-end solutions. Our commitment to quality and innovation enables us to partner with leading aerospace organizations worldwide, helping them accelerate the adoption of metal AM for critical components like structural support beams.
Cost Drivers and Lead Time Expectations for 3D Printed Beams
Understanding the factors that influence the cost and production timeline is essential for project planning and budgeting when considering 3D printed aluminum support beams. While AM can offer long-term savings through lightweighting and part consolidation, the initial component cost needs careful evaluation.
Key Cost Factors in Metal 3D Printing:
- Material Consumption:
- Part Volume: The amount of AlSi10Mg or Scalmalloy® powder required to print the beam itself. Scalmalloy® is significantly more expensive per kilogram than AlSi10Mg.
- Volumen de la estructura de soporte: The material needed for support structures, which is later removed but still consumed during printing. Optimized design (DfAM) minimizes support needs.
- Powder Waste/Recycling: Some powder cannot be fully recycled or is lost during handling, contributing slightly to costs.
- Tiempo de máquina (tiempo de construcción):
- Part Height & Volume: Taller parts and parts with larger cross-sectional areas take longer to print layer by layer.
- Complejidad: Intricate features or extensive lattice structures can increase scanning time per layer.
- Nesting: Printing multiple parts simultaneously in one build (nesting) can improve machine utilization and reduce cost per part, especially relevant for compradores mayoristas or larger production runs.
- Máquina Tarifa por hora: Based on the capital cost, maintenance, operation, and depreciation of the industrial L-PBF machine.
- Post-procesamiento:
- Labor & Equipment: The time and resources required for powder removal, stress relief, heat treatment, support removal, HIP (if needed), surface finishing, and CNC machining add significantly to the final cost.
- Complejidad: Difficult support removal or extensive machining requirements increase post-processing costs.
- Quality Control & Inspection:
- Nivel de inspección: Basic dimensional checks are standard, but rigorous aerospace requirements like CT scanning, detailed CMM reports, or extensive material coupon testing add cost.
- Engineering & Setup:
- File Preparation: Time taken to prepare the CAD file, orient the part, generate supports, and slice the model for printing.
- Apoyo al DfAM: If extensive design consultation is required, this may be factored in.
- Volumen del pedido:
- Prototypes vs. Production: One-off prototypes typically have a higher cost per part compared to series production runs due to setup costs being amortized over more units.
- Bulk Discounts: Suppliers often offer descuentos por volumen for larger quantity orders, benefiting procurement managers sourcing parts at scale.
Typical Lead Time Expectations:
Lead time is the duration from order confirmation to final part delivery. It depends on part complexity, size, quantity, current machine availability, and the extent of post-processing required.
- Prototyping (1-10 parts): Normalmente oscila entre De 1 a 4 semanas. This includes printing, basic post-processing (stress relief, support removal, bead blast), and standard inspection. Expedited options may be available at a higher cost.
- Low-Volume Production (10-100 parts): May range from 3 to 8 weeks, depending on the factors above and the supplier’s capacity. Scheduling becomes more critical.
- Series Production (100+ parts): Lead times are highly dependent on the part, required throughput, and contractual agreements. Dedicated production planning is necessary, often involving phased deliveries over several weeks or months.
Note: As of late April 2025, these are general estimates. Always obtain specific quotes and lead times from your chosen supplier based on your exact part geometry, material, and requirements.
It’s crucial to engage with potential suppliers like Met3dp early to get accurate additive manufacturing pricing and lead time estimates based on your specific aerospace support beam design and project needs.

Frequently Asked Questions (FAQ) about 3D Printed Aluminum Beams
Here are answers to some common questions engineers and procurement managers have about using additive manufacturing for aluminum aerospace support beams:
1. How does the strength of 3D printed AlSi10Mg/Scalmalloy® compare to wrought aluminum alloys?
- AlSi10Mg (T6): Generally exhibits strength comparable to mid-range cast aluminum alloys or some 6xxx series wrought alloys. It typically doesn’t match the high strength of aerospace-grade wrought alloys like 7075-T6 or 2024-T3 directly in terms of raw tensile strength. However, its advantage lies in the ability to create optimized, lightweight designs (via DfAM) that achieve required structural performance with less material.
- Scalmalloy® (Heat Treated): This alloy was specifically designed for AM and offers significantly higher strength than AlSi10Mg. Its yield and tensile strength can approach or even exceed those of some high-strength 7xxx series wrought alloys, combined with excellent ductility and fatigue properties. This makes it a very competitive option for demanding structural applications where weight saving is critical.
- Lo más importante: Direct material-for-material substitution based purely on datasheet strength isn’t the goal. AM’s value comes from design optimization combined with appropriate material selection (like high-performance Scalmalloy®) to achieve superior structural efficiency.
2. What are the typical lead times for a prototype aerospace beam?
- As mentioned previously, typical lead times for a single or small batch of prototype aluminum support beams (including printing, standard heat treatment, support removal, and basic finishing/inspection) usually range from De 1 a 4 semanas. This can vary based on part size, complexity, the specific alloy (Scalmalloy® might have slightly different heat treat cycles), the supplier’s current workload, and whether optional processes like HIP or extensive machining are required. Always confirm with your supplier.
3. Are 3D printed aluminum beams flight-certified?
- En aerospace certification AM parts process is complex and applies to the entire manufacturing process, not just the part itself. A 3D printed beam isn’t inherently “flight-certified” just because it’s printed.
- Certification Pathway: Achieving flight certification involves:
- Using a qualified manufacturing process (machines, parameters, post-processing) that is highly controlled and repeatable.
- Manufacturing within an AS9100 certified facility.
- Utilizing qualified material (powder that meets aerospace specifications like AMS standards).
- Rigorous process documentation, traceability, and quality control.
- Extensive part testing (static, fatigue, environmental) and analysis to demonstrate airworthiness requirements are met, often defined by regulatory bodies (FAA, EASA) and the aerospace OEM.
- Many companies are successfully flying 3D printed structural components, including beams and brackets made from aluminum and titanium alloys, but it requires a dedicated qualification and certification effort involving the part designer, manufacturer (like Met3dp), and the aircraft/system integrator.
4. Can Met3dp handle large-volume production orders for aerospace beams?
- Yes, Met3dp is equipped to handle requirements ranging from rapid prototyping to large-volume series production. Our facility houses multiple industry-leading L-PBF printers, enabling scalable production capacity. We partner with aerospace clients to establish robust production workflows, quality plans, and delivery schedules tailored to meet high-volume demand for critical components like structural support beams, ensuring a reliable supply chain for compradores mayoristas and OEMs. Our comprehensive capabilities in powder production, printing, post-processing, and quality assurance support seamless transitions from prototype to full-scale manufacturing.
Conclusion: The Future of Aerospace Structures is Additive
The journey through the intricacies of manufacturing aerospace support beams utilizando 3D printed aluminum alloys like AlSi10Mg and Scalmalloy® highlights a clear trajectory: additive manufacturing is no longer a niche prototyping tool but a powerful enabler of next-generation aerospace design and production. The ability to create highly optimized, estructuras ligeras through topology optimization, consolidate complex assemblies into single parts, and utilize high-performance materials like Scalmalloy® offers tangible benefits in fuel efficiency, payload capacity, and overall aircraft performance.
From initial design considerations guided by DfAM principles to navigating the crucial steps of post-processing and overcoming inherent manufacturing challenges, the successful implementation of AM requires expertise, precision, and rigorous quality control. Materials like AlSi10Mg provide a reliable and cost-effective solution for many applications, while Scalmalloy® pushes the performance envelope for the most demanding structural requirements.
Choosing the right manufacturing partner is paramount. A supplier like Met3dp, with deep expertise in aerospace applications, advanced material capabilities including in-house powder production, state-of-the-art L-PBF technology, comprehensive post-processing, and a commitment to AS9100-level quality, is essential for translating the potential of AM into flight-worthy reality.
As the aerospace industry continues to seek innovative ways to build lighter, faster, and more efficient aircraft and spacecraft, metal additive manufacturing will undoubtedly play an increasingly vital role. The future of aerospace manufacturing involves leveraging these advanced techniques to produce components previously thought impossible.
Met3dp stands ready to be your additive manufacturing partner in this evolution. We invite engineers, designers, and procurement managers in the aerospace, automotive, medical, and industrial sectors to explore how our capabilities can power your organization’s goals. Visit our website at https://met3dp.com/ or contact us today to discuss your specific project requirements and discover how 3D printed aluminum support beams can elevate your designs.
Compartir
MET3DP Technology Co., LTD es un proveedor líder de soluciones de fabricación aditiva con sede en Qingdao, China. Nuestra empresa está especializada en equipos de impresión 3D y polvos metálicos de alto rendimiento para aplicaciones industriales.
Solicite información para obtener el mejor precio y una solución personalizada para su empresa.
Artículos relacionados
Acerca de Met3DP
Actualización reciente
Nuestro producto
CONTACTO
¿Tiene alguna pregunta? ¡Envíenos un mensaje ahora! Atenderemos su solicitud con todo un equipo tras recibir su mensaje.
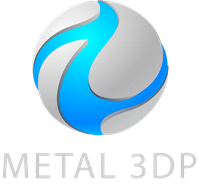
Polvos metálicos para impresión 3D y fabricación aditiva