Conocimiento del moldeo por inyección de metal (MIM)
Índice
Moldeo por inyección de metales (MIM) es un proceso de fabricación utilizado para producir piezas metálicas pequeñas y complejas con tolerancias estrechas. El MIM combina la versatilidad del moldeo por inyección de plástico con la resistencia e integridad de los metales mecanizados. Este artículo ofrece una visión detallada de la tecnología MIM, sus aplicaciones, equipos, procesos y consideraciones de diseño, entre otros aspectos.
Visión general del moldeo por inyección de metales
El moldeo por inyección de metales es un proceso pulvimetalúrgico que permite producir grandes volúmenes de pequeños componentes metálicos de precisión mediante técnicas de moldeo por inyección.
Cómo funciona el MIM
El proceso MIM consiste en mezclar polvo metálico fino con un material aglutinante para crear una materia prima que pueda inyectarse en moldes. A continuación, las piezas moldeadas, conocidas como piezas verdes, se sinterizan para eliminar el aglutinante y consolidar el polvo metálico en una estructura sólida. Los pasos básicos son:
- Mezcla - El polvo metálico fino se mezcla con aglutinantes para crear una materia prima homogénea
- Moldeo por inyección - La materia prima se funde y se inyecta en el molde para formar piezas verdes
- Desbobinado - El aglutinante se elimina mediante disolvente, térmico o catalítico.
- Sinterización - Las piezas desbastadas se sinterizan para densificar y reforzar la estructura metálica
- Operaciones secundarias - Pasos de acabado adicionales como mecanizado, taladrado, roscado, etc.
Ventajas del MIM
El MIM ofrece varias ventajas en comparación con otras técnicas de fabricación:
- Producción de gran volumen con bajo coste por pieza
- Geometrías complejas con tolerancias estrechas
- Variedad de materiales como acero inoxidable, titanio, tungsteno, cromo cobalto, etc.
- Pérdidas mínimas de chatarra y desperdicio de material
- Fabricación con forma casi de red que reduce el mecanizado
- Piezas pequeñas de 0,005 lbs a 0,5 lbs
- Consolidación de piezas mediante la combinación de conjuntos
- Superficies lisas y buen acabado
Limitaciones del MIM
Algunas de las limitaciones del moldeo por inyección de metales son
- Elevados costes de puesta en marcha y utillaje
- Gama de tamaños limitada para las piezas
- Se requiere equipo especializado
- Proceso de varios pasos con una producción más lenta
- Limitaciones dimensionales basadas en las características del polvo
- Restricciones en la geometría de la pieza basadas en el flujo de polvo
Aplicaciones del MIM
El MIM se utiliza ampliamente para fabricar piezas pequeñas y complejas con tolerancias estrictas en sectores como:
- Medicina: implantes ortopédicos, implantes dentales, instrumental quirúrgico
- Automoción: componentes del motor, válvulas, engranajes
- Aeroespacial: álabes de turbina, impulsores, toberas
- Electrónica: conectores, microengranajes, blindaje
- Armas de fuego: gatillos, martillos, seguros
- Relojes: cajas, pulseras, corona
- Industrial: pomos, fijaciones, herramientas de corte
El MIM compite con otros procesos, como la fundición a presión, el mecanizado y la estampación, en la producción de piezas metálicas.
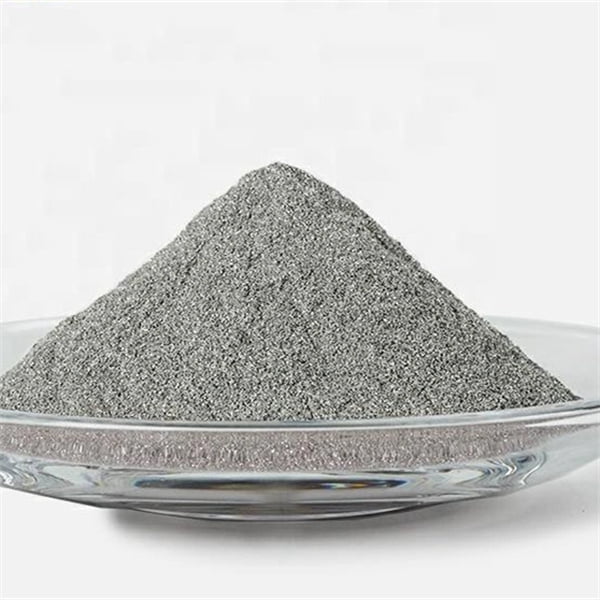
Guía de equipos de moldeo por inyección de metal
Cada etapa del proceso MIM requiere un equipo especializado. Estos son los principales tipos de equipos MIM:
Equipamiento | Función |
---|---|
Alimentadores de polvo | Medición precisa de polvos finos |
Mezcladoras | Mezcla homogénea de polvo y aglutinante |
Granuladores | Transformar la materia prima en gránulos para el moldeo |
Máquinas de moldeo por inyección | Moldear la materia prima en las formas requeridas |
Hornos de descortezado | Retirar el aglutinante de las piezas moldeadas |
Hornos de sinterización | Densificar y reforzar la estructura metálica |
Rectificadoras | Retirar verjas, correderas y superficies lisas |
Centros de mecanizado | Taladrado, torneado, fresado de características en piezas sinterizadas |
Se utilizan sistemas avanzados de automatización, manipulación y control para integrar el proceso y maximizar la productividad. El equipo debe seleccionarse cuidadosamente en función de factores como el material, el tamaño de las piezas, el volumen de producción y los requisitos de calidad.
moldeo por inyección de metal Proceso paso a paso
El procesamiento MIM implica múltiples pasos para transformar el fino polvo metálico en componentes de uso final totalmente densos.
Paso 1 - Mezcla
- El polvo metálico y el aglutinante se mezclan a fondo en una batidora para obtener una materia prima homogénea.
- El tamaño, la forma y la distribución de las partículas de polvo influyen en la moldeabilidad y la sinterización.
- Los aglutinantes proporcionan fluidez y adherencia durante el moldeo por inyección
- Ceras, termoplásticos como PP, PE, PVC y polímeros utilizados como aglutinantes.
- Mezclado con palas sigma, palas Z y mezcladores planetarios dobles
Etapa 2 - Granulación
- La mezcla de materias primas se granula en pequeños gránulos para el moldeo por inyección
- Mejora el flujo de material y evita la segregación en el barril
- Las granuladoras utilizan cuchillas giratorias para cortar la materia prima en gránulos uniformes.
- La forma y el tamaño de los gránulos afectan a la densidad de empaquetado y a la moldeabilidad
Paso 3 - Moldeo por inyección
- Los gránulos de materia prima se moldean para dar a la pieza la forma y el tamaño requeridos
- Utiliza máquinas de moldeo por inyección modificadas con temperatura y presión controladas
- Es importante optimizar los parámetros de moldeo para minimizar los defectos
- Las piezas moldeadas en bruto, denominadas piezas verdes, han adquirido forma pero no resistencia.
Paso 4 - Desencuadernado
- El aglutinante se extrae de las partes verdes por medios disolventes, térmicos o catalíticos
- El desligante con disolvente utiliza la acción capilar para disolver el aglutinante.
- El desencolado térmico descompone el aglutinante en un horno
- El desligante catalítico acelera la eliminación de aglutinantes con un catalizador
- El desbastado crea piezas marrones con una estructura porosa de partículas metálicas
Etapa 5 - Sinterización
- Las piezas marrones se sinterizan en un horno de atmósfera controlada
- Los enlaces entre partículas metálicas se forman por difusión y transporte de masas
- Densidad casi total de hasta 96-99% alcanzada durante la sinterización
- Atmósfera, temperatura y tiempo optimizados para evitar defectos
- La contracción por sinterización se tiene en cuenta durante el moldeo
Paso 6 - Operaciones secundarias
- Pasos adicionales de trabajo del metal como recocido, mecanizado, taladrado, chapado
- El recocido alivia las tensiones internas de la sinterización
- El mecanizado CNC elimina los bebederos, alisa las superficies y añade características
- Chapado y pintura aplicados para mejorar o proteger contra la corrosión
El proceso MIM permite fabricar piezas metálicas complejas de alta precisión combinando las ventajas del moldeo por inyección de plástico y la pulvimetalurgia.
Consideraciones sobre el diseño de piezas MIM
El MIM permite libertades geométricas que no son posibles con el mecanizado, pero requiere ciertas consideraciones de diseño:
- Grosor de la pared - Rango típico de 0,3 - 4,0 mm con algunos polvos que soportan paredes de hasta 6 mm.
- Acabado superficial - Acabado más suave que la fundición pero no tan fino como el mecanizado; el valor Ra de 1 - 4 μm es típico para MIM.
- Tolerancias dimensionales - De ±0,1% a ±0,5% en función de la geometría de la pieza, con posibilidad de precisión a nivel de micras.
- Densidad - Se puede alcanzar una densidad total de hasta 99% con una sinterización optimizada
- Geometría - Es fundamental evitar que queden polvos atrapados y permitir la salida del aglutinante
- Ángulos de giro - Paredes cónicas con ángulos de inclinación de 1-3° para facilitar la expulsión de las piezas
- Radios y filetes - Se prefieren las transiciones graduales a los ángulos agudos
- Agujeros y cavidades - Diámetros mínimos de 0,25 - 0,5 mm para orificios pasantes
- Hilos - Puede moldearse, pero a menudo se mecaniza tras la sinterización para mejorar la precisión
- Detalles de la superficie - Limitar los detalles finos para reducir el desgaste del molde; los procesos posteriores al moldeo pueden mejorar
El diseño MIM debe centrarse en una geometría que maximice el rendimiento en lugar de la facilidad de fabricación. El proceso permite consolidar ensamblajes de varias piezas en una sola, con importantes ahorros de costes y peso.
Materiales utilizados en el moldeo por inyección de metales
El MIM puede producir piezas a partir de una amplia gama de metales, aleaciones y cerámicas en diversas industrias.
Material | Aplicaciones | Propiedades |
---|---|---|
Acero inoxidable | Medicina, armas de fuego, marina | Resistencia a la corrosión, solidez |
Acero de baja aleación | Automoción, industria | Respuesta magnética, maquinabilidad |
Aleaciones magnéticas blandas | Sensores, actuadores | Alta permeabilidad |
Aleaciones de metales duros | Herramientas de corte | Resistencia al desgaste, dureza |
Aleaciones de cobre | Electrónica, térmica | Conductividad eléctrica |
Aleaciones de aluminio | Eléctrico, térmico | Ligereza, conductividad |
Aleaciones de titanio | Aeroespacial, automoción | Resistencia, biocompatibilidad |
Aleaciones de tungsteno | Blindaje contra las radiaciones | Alta densidad |
Cermets | Electrónica, óptica | Resistencia a la oxidación |
Factores como la función de la pieza, el coste, los pasos de postprocesado y la compatibilidad de la aleación determinan la elección del material MIM ideal.
Proveedores y fabricantes de equipos MIM
Muchas empresas ofrecen materiales, servicios, producción y equipos de MIM en todo el mundo. Estos son algunos de los principales proveedores de MIM en toda la cadena de valor:
Empresa | Productos y servicios |
---|---|
BASF | Materias primas, aglutinantes |
Sandvik Osprey | Polvos metálicos |
Höganäs | Polvos metálicos |
CNPC Polvo | Polvos metálicos |
Indo-Mim | Productos y servicios MIM |
MPP | Productos y servicios MIM |
Grupo ARC | Productos y servicios MIM |
Atlas Metales prensados | Producción de piezas MIM |
Epson Atmix | Equipos MIM |
Milacron | Máquinas de moldeo por inyección |
Elnik | Hornos de sinterización |
TCN | Hornos de descortezado y sinterización |
En la cadena de suministro del MIM también intervienen muchas empresas regionales más pequeñas. Los usuarios finales que deseen adoptar el MIM pueden asociarse con proveedores de materiales y fabricantes por contrato en función de las capacidades requeridas.
Análisis de costes de piezas MIM frente a alternativas
A continuación se muestra una comparación de los costes estimados para producir 1.000 piezas utilizando diferentes procesos de fabricación:
Proceso | Gastos de instalación | Costes de la máquina | Costes de utillaje | Coste parcial | Total (1000 partes) |
---|---|---|---|---|---|
Mecanizado CNC | Bajo | $100,000 | $2,000 | $50 | $52,000 |
Fundición a la cera perdida | Alta | $500,000 | $40,000 | $20 | $60,000 |
Moldeo por inyección de metales | Alta | $750,000 | $100,000 | $15 | $115,000 |
Estampación | Alta | $1,000,000 | $150,000 | $10 | $160,000 |
- El mecanizado CNC tiene volúmenes bajos, costes de pieza elevados, complejidad limitada
- La fundición a la cera perdida es mejor para volúmenes de hasta 10.000 unidades
- El MIM tiene ventajas para volúmenes medios y altos con geometría compleja
- La estampación tiene unos costes de utillaje muy elevados, pero el precio de la pieza es el más bajo en volúmenes elevados, superiores a 100.000 piezas.
El punto de inflexión en el que el MIM resulta más económico que otros procesos depende de los volúmenes, la complejidad y el tamaño.
Elegir un proveedor o socio de MIM
Seleccionar un proveedor o socio de producción MIM competente es crucial para una producción de piezas rentable. He aquí algunas consideraciones clave:
- Conocimientos técnicos - Experiencia previa con piezas MIM similares, materiales, industria
- Sistemas de calidad - Certificación ISO 9001, prácticas de control de calidad
- Capacidad de producción - Capacidad para satisfacer las necesidades de volumen presentes y futuras
- Procesos secundarios - Capacidad de mecanizado, estampado, chapado y pintura
- Optimización parcial - Diseñar el soporte MIM para maximizar los beneficios
- Creación de prototipos - Servicios de prototipado rápido para validar diseños
- Capacidad de mecanizado - Preferiblemente, diseño y fabricación de utillaje interno
- Acceso a las materias primas - Canales de suministro de materias primas establecidos
- Capacidades de I+D - I+D en curso sobre materiales y técnicas de fabricación avanzados
- Orientación al cliente - Capacidad de respuesta a las necesidades y enfoque de colaboración
- Estructura de costes - Modelo de precios y competitividad para los volúmenes previstos
- Logística - Capacidad para entregar piezas de forma fiable cumpliendo los plazos de entrega.
La priorización de estos factores ayudará a identificar al socio estratégico de MIM adecuado para una aplicación concreta.
Instalación del equipo MIM
Para las empresas que instalan sistemas MIM en sus propias instalaciones, es fundamental que la instalación de los equipos sea correcta. He aquí algunas consideraciones clave:
- Se necesita una superficie de entre 2.000 y 1.000 metros cuadrados para la línea MIM
- Se requiere una fuente de alimentación estable con una capacidad de 200-600 kVA
- Líneas de aire comprimido con una presión nominal de 100 psi
- Ventilación de escape para calor, emisiones y recogida de polvo
- Servicios públicos como suministro de nitrógeno, agua de proceso y gas
- Control de temperatura y humedad de unos 20±3 °C, 50±20%
- Entreplantas, plataformas para instalar equipos auxiliares
- Sistemas de manipulación de materiales como elevadores, carretillas elevadoras, contenedores
- Sala de control, sistemas informáticos de supervisión
- Formación del personal sobre la seguridad de los procesos y el funcionamiento de los equipos
- Simulaciones de procesos, pruebas de funcionamiento para validar la instalación
- Calibración y programas de mantenimiento preventivo
Un espacio adecuado, servicios y condiciones controladas son esenciales para el buen funcionamiento del equipo MIM. Unas pruebas y una formación exhaustivas preparan para la producción real.
Mantenimiento de equipos MIM
Un mantenimiento constante mejora el tiempo de actividad y el rendimiento de los equipos de producción de MIM. Aspectos clave:
- Programa de mantenimiento preventivo documentado para cada máquina
- Limpieza diaria de derrames de material, fugas, polvo, escombros
- Comprobación de los niveles de líquidos, fugas, ruidos inusuales, vibraciones
- Control de presiones, temperaturas y consumo eléctrico
- Pruebas de sistemas de calefacción, refrigeración y control
- Sustitución de piezas de desgaste como cribas, tornillos, barriles
- Inspecciones de fatiga, daños y alineación de componentes
- Reconstrucciones y revisiones periódicas en función de las horas de funcionamiento
- Seguimiento de los registros de mantenimiento para su análisis
- Almacenamiento del inventario de piezas de repuesto para componentes críticos
- Formación sobre el funcionamiento correcto y la seguridad de los equipos
- Servicio y asistencia puntuales de los proveedores de equipos
Un personal bien formado y la colaboración con los proveedores de equipos contribuyen a maximizar la productividad de los equipos MIM y a minimizar los tiempos de inactividad.
Software de simulación de moldeo por inyección de metales
El software de simulación se utiliza para modelar digitalmente el proceso MIM antes de la producción real. Entre las ventajas se incluyen:
- Predicción de patrones de llenado de moldes y optimización de la ubicación de las compuertas
- Identificación de líneas de soldadura y trampas de aire para evitar defectos
- Estudio de gradientes térmicos y solidificación en geometrías complejas
- Simulación de los efectos del perfil de desbobinado y sinterización en la forma final
- Validación de diseños de utillaje antes de la fabricación
- Reducción de los costes de los ensayos mediante prototipos virtuales
- Formación del personal mediante representaciones visuales
Algunos paquetes comerciales de simulación MIM son:
- MIMSIM - Simulación integrada de moldeo por sinterización
- Sigma Suave - Análisis FEM en 3D del llenado y la distorsión de moldes
- Netzsch MIMPre - Modelización de las propiedades reológicas de las materias primas del MIM
- Aditivo Simufact - Simulación multifísica de procesos de AM
- EOS PSW - Simulación centrada en la sinterización y el tratamiento térmico
El uso de software MIM mejora la coherencia del proceso, optimiza la calidad de las piezas y reduce los costes de creación de prototipos físicos. Es preferible un flujo de trabajo integrado de simulación a producción.
Solución de los defectos más comunes del MIM
Algunos defectos típicos de las piezas MIM y sus posibles causas son:
Defecto | Causas |
---|---|
Tiros cortos | Baja presión de inyección, solidificación prematura |
Flash | Moldes sobreenvasados, daños por moho |
Alabeo | Enfriamiento no uniforme, problemas de aglutinante |
Grietas | Sinterización rápida, alto contenido en aglutinante |
Porosidad | Mala homogeneización, gases atrapados |
Contaminación | Contaminación cruzada, atmósfera del horno |
Variaciones dimensionales | Problemas de materia prima, desgaste del molde, contracción |
Defectos superficiales | Porosidad del gas, fragilización del metal líquido |
Incluye | Materias primas contaminadas, atascos de boquillas |
Debe utilizarse una metodología sistemática de análisis de defectos para aislar los parámetros del proceso que causan defectos y emprender acciones correctivas como ajustar la formulación de la materia prima, los parámetros de moldeo, el desbobinado y los perfiles de sinterización.
Ventajas de la tecnología MIM
El MIM ofrece ventajas significativas sobre otros métodos de producción de piezas metálicas:
- Complejidad - Posibilidad de geometrías 3D complejas, consolidación de conjuntos
- Consistencia - Proceso altamente repetible con baja varianza de piezas
- Eficacia - Fabricación de forma casi neta con menos desperdicio de materia prima
- Automatización - El proceso altamente automatizado reduce la mano de obra
- Flexibilidad - Amplia gama de materiales como metales, cerámica, compuestos
- Calidad - Buen acabado superficial y propiedades mecánicas
- Productividad - Alto volumen de producción con bajo coste por pieza
- Miniaturización - Microcomponentes con detalles de hasta 10 μm
- Sostenibilidad - Eficiencia energética en comparación con el mecanizado
- Coste - Menor coste total para volúmenes de producción medios y altos
Las capacidades únicas del MIM están impulsando su adopción en sectores tan diversos como el automovilístico, el aeroespacial, el médico y el electrónico.
Limitaciones del moldeo por inyección de metales
A pesar de sus muchas ventajas, el MIM tiene ciertas limitaciones:
- Elevada inversión inicial en utillaje
- Gama de tamaños limitada, normalmente inferior a 65 gramos
- Menor precisión que el mecanizado CNC
- Riesgos de porosidad que requieren controles del proceso
- Selección restringida de materiales en función de las características del polvo
- Peligros para la seguridad de los polvos finos
- Restricciones de la geometría de la pieza relacionadas con la moldeabilidad
- Variabilidad potencial entre lotes
- Propiedades mecánicas inferiores a las de los materiales forjados
- Producción limitada de prototipos en volúmenes menores
- Necesidad de mecanizado secundario en muchas aplicaciones
- Se necesitan equipos especializados y operarios formados
Para piezas metálicas de muy alta precisión o de mayor tamaño producidas en volúmenes reducidos, otros procesos pueden ser más adecuados que el MIM.
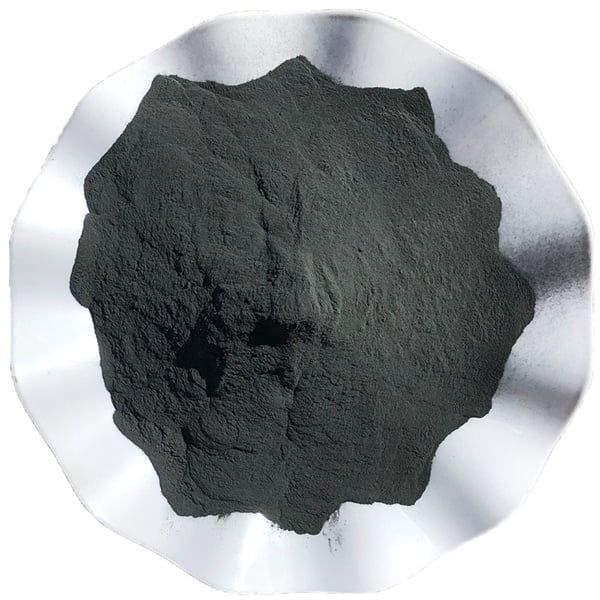
El futuro del moldeo por inyección de metales
Se espera que el MIM experimente un fuerte crecimiento continuo a medida que la tecnología y los materiales sigan mejorando:
- Nuevos sistemas aglutinantes para mejorar la moldeabilidad y la resistencia en verde
- Nuevas formulaciones de materias primas mediante nanocompuestos
- Piezas de mayor tamaño que superan los límites de corriente
- Mayor adopción de cerámica y aleaciones de wolframio
- Fuerte crecimiento de la demanda en los sectores médico y electrónico
- Utilización de la fabricación aditiva para fabricar utillaje MIM
- Automatización mediante robótica e integración de la Industria 4.0
- Más aplicaciones en entornos extremos
- Convergencia con la impresión 3D de metales mediante deposición de metales ligados
Con el aumento de la I+D y una adopción más fácil, el uso de MIM crecerá rápidamente en diversas aplicaciones en los próximos años.
Compartir
MET3DP Technology Co., LTD es un proveedor líder de soluciones de fabricación aditiva con sede en Qingdao, China. Nuestra empresa está especializada en equipos de impresión 3D y polvos metálicos de alto rendimiento para aplicaciones industriales.
Solicite información para obtener el mejor precio y una solución personalizada para su empresa.
Artículos relacionados
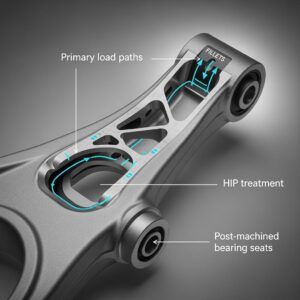
Metal 3D Printing for U.S. Automotive Lightweight Structural Brackets and Suspension Components
Leer Más "Acerca de Met3DP
Actualización reciente
Nuestro producto
CONTACTO
¿Tiene alguna pregunta? ¡Envíenos un mensaje ahora! Atenderemos su solicitud con todo un equipo tras recibir su mensaje.