Tecnología MIM
Índice
Visión general de Tecnología MIM
El moldeo por inyección de metales (MIM), también conocido como moldeo por inyección de polvo (PIM), es un proceso de fabricación avanzado utilizado para producir piezas metálicas pequeñas y complejas en grandes volúmenes.
El MIM combina la flexibilidad de diseño y la precisión del moldeo por inyección de plástico con la resistencia y el rendimiento de las piezas metálicas mecanizadas. Permite la producción rentable de componentes intrincados con buenas propiedades mecánicas a partir de aleaciones metálicas avanzadas.
El proceso MIM comienza con una materia prima hecha de polvo metálico fino mezclado con un material aglutinante. A continuación, esta materia prima se inyecta en un molde mediante un equipo de moldeo por inyección de plástico. El aglutinante mantiene unido el polvo metálico y le confiere fluidez para el moldeo.
Tras el moldeo, se elimina el aglutinante de la pieza verde moldeada mediante un proceso de desbobinado. La pieza sin aglutinante, denominada pieza marrón, se sinteriza a altas temperaturas, lo que fusiona las partículas metálicas en una pieza metálica sólida con propiedades similares a las de una pieza forjada.
El MIM es adecuado para fabricar piezas pequeñas y complejas utilizando diversos metales como acero inoxidable, aceros de baja aleación, aceros para herramientas, aleaciones magnéticas, superaleaciones, aleaciones de titanio y aleaciones pesadas de tungsteno. Combina la versatilidad del moldeo por inyección de plástico con la flexibilidad de materiales de la pulvimetalurgia.
Las principales ventajas de la tecnología MIM son:
- Gran capacidad de producción de componentes metálicos complejos y detallados
- Fabricación de formas casi netas que reduce los residuos y minimiza el mecanizado
- Buenas propiedades mecánicas próximas a las de los materiales forjados
- Amplia gama de metales, incluidos acero inoxidable, acero para herramientas y superaleaciones
- Permite la consolidación de piezas en componentes individuales
- Bajo coste unitario gracias a los grandes volúmenes
- Coherencia y repetibilidad del proceso automatizado
La tecnología MIM es ideal para piezas pequeñas y complejas, como dispositivos médicos, componentes de armas de fuego, componentes de relojes y piezas de automóviles, que requieren precisión, resistencia, economía y escala de producción en serie.
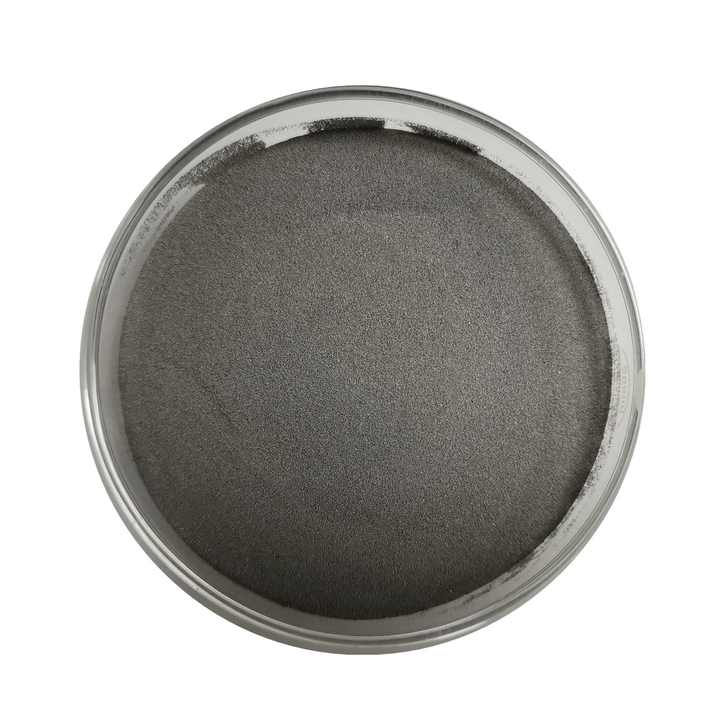
Aplicaciones y usos de la tecnología MIM
La tecnología MIM se utiliza en diversos sectores para fabricar piezas metálicas pequeñas de alta precisión de forma eficiente y en grandes volúmenes. Estas son algunas de las principales áreas de aplicación y usos de la tecnología MIM:
Industria | Aplicaciones y usos |
---|---|
Medicina y odontología | Instrumental quirúrgico, implantes dentales, implantes ortopédicos, componentes de catéteres, cánulas de agujas, mangos de bisturí, fórceps, pinzas, sujetadores quirúrgicos, instrumental quirúrgico reutilizable. |
Armas de fuego y defensa | Gatillos, martillos, seguros, eyectores, cargadores, casquillos usados, proyectiles, componentes de ojivas. |
Automoción | Componentes del sistema de combustible, engranajes de la bomba de aceite, impulsores, válvulas, piezas del turbocompresor, piezas electrónicas, componentes de la dirección/transmisión. |
Aeroespacial | Álabes de turbina, rodetes, dientes de engranaje, bujes, componentes de bombas, piezas de motores |
Productos de consumo | Componentes de relojes, fornituras de joyería, cuchillería, tijeras, maquinillas de afeitar, herramientas manuales, piezas de cremalleras |
Ferretería industrial | Pomos, racores, fijaciones, enchufes, conectores, aspersores, boquillas |
Electrónica | Conectores, interruptores, micromotores, microengranajes, máscaras de cribado, inductores, rotores magnéticos |
** Ventajas del MIM para aplicaciones específicas
- Precisión: Ideal para piezas en miniatura como dispositivos médicos o componentes de relojes con geometrías intrincadas.
- Resistencia: Adecuado para componentes que requieren alta resistencia, como turbocompresores de automóviles y gatillos de armas de fuego.
- Resistencia al desgaste: Las piezas MIM fabricadas con aleaciones de acero para herramientas tienen una excelente resistencia al desgaste para una larga vida útil.
- Resistencia a la corrosión: Las piezas MIM de acero inoxidable resisten la corrosión para herramientas quirúrgicas reutilizables, implantes, etc.
- Alta dureza: El MIM puede producir piezas con dureza superior a 40 HRC como cuchillería, utillaje, troqueles, etc.
- Propiedades eléctricas: El MIM se utiliza para fabricar componentes magnéticos blandos como inductores, rotores de motor, etc.
- Rentable: Los grandes volúmenes reducen sustancialmente el coste de las piezas en comparación con el mecanizado.
Guías de equipos y herramientas MIM
Los principales equipos utilizados en el proceso MIM son las máquinas de moldeo por inyección y los hornos de desbobinado y sinterización. He aquí un resumen:
Equipamiento | Propósito | Consideraciones |
---|---|---|
Máquina de moldeo por inyección | Inyectar la materia prima MIM en las cavidades del molde bajo calor y presión. | Fuerza de sujeción del molde, velocidad de inyección y capacidad de presión, precisión y repetibilidad, controles y características de automatización. |
Horno de eliminación de ligantes | Para eliminar el aglutinante térmica o químicamente de las piezas moldeadas | Rango de temperatura, control de la atmósfera, capacidad de carga, uniformidad del desbobinado. |
Horno de sinterización | Densificar las partes marrones deshilachadas calentándolas hasta cerca del punto de fusión. | Gama de temperaturas, control de la atmósfera, uniformidad del calentamiento, capacidad de lotes, preferiblemente totalmente automatizada. |
Moldes y utillaje | Cavidades moldeadas para dar a la materia prima MIM la geometría requerida | Soporta presiones y temperaturas de moldeo, mecanizado de precisión, buen acabado superficial, permite un calentamiento/enfriamiento rápido. |
Equipo de materia prima | Mezclar el polvo metálico y el aglutinante para obtener una materia prima MIM homogénea. | Mezcladores, controladores de temperatura, granuladores. |
Tratamiento secundario | Pasos adicionales como mecanizado, unión, tratamiento de superficies | Según las necesidades de la pieza, como mecanizado CNC, soldadura, electroerosión, revestimiento. |
Control de calidad | Comprobar las propiedades de la materia prima y las piezas sinterizadas | Morfología del polvo, densidad, velocidad de flujo, analizadores de viscosidad, equipos de ensayos mecánicos. |
Equipamiento de seguridad | Para manipular polvos finos con seguridad | Guantes, mascarillas, sistemas de recogida de polvo. |
Normas de diseño y rendimiento
- ISO 21227 - Polvos para el moldeo por inyección de metales
- ASTM F2885 - Proceso de moldeo por inyección de metales
- MPIF 35 - Normas para la materia prima del MIM
- ASTM E2781 - Diseño de probetas de ensayo de tracción MIM
- ISO 2740 - Piezas de moldeo por inyección de metal sinterizado
Desglose de costes
La distribución típica de costes en la producción de MIM es:
- Materias primas (polvo + aglutinante): 50-60%
- Fabricación (Moldeo + Desbobinado + Sinterizado): 25-35%
- Procesamiento secundario: 5-10%
- Control de calidad: 2-5%
- Ingeniería (I+D, Diseño): 2-5%
Proveedores y precios
Estos son algunos de los principales proveedores mundiales de equipos MIM y sus gamas de precios:
Proveedor | Categoría de productos | Precios |
---|---|---|
ARBURG | Máquinas de moldeo por inyección | $100,000 – $500,000 |
MIM indoamericano | Materias primas y servicios MIM | $5 - $50 por Kg |
Elnik | Hornos de descortezado y sinterización | $50,000 – $1,000,000 |
FineMIM | Producción MIM de principio a fin | $0,5 - $5 por pieza |
Parmatech | Polvo metálico Atomización | $250,000 – $1,000,000 |
Tecnologías Meridian | Diseño de herramientas y moldes | $5,000 – $100,000 |
Instalación, funcionamiento y mantenimiento
El MIM es un proceso automatizado, pero requiere una instalación, un funcionamiento y un mantenimiento cuidadosos para un rendimiento óptimo:
Actividad | Detalles |
---|---|
Instalación | Alineación de precisión de la máquina de moldeo por inyección y los moldes. Calibración de los controladores de temperatura. Prueba de funcionamiento con lotes de prueba. |
Operación | Garantizar el control de calidad de la materia prima según las normas. Conseguir parámetros de proceso como la presión de inyección, la temperatura y la velocidad. |
Mantenimiento | Programar el mantenimiento preventivo de los barriles, tornillos y moldes de las máquinas de moldeo. Mantener la atmósfera del horno de descortezado. Calibrar instrumentos. |
Limpieza | Siga los procedimientos normalizados de trabajo para la limpieza de los barriles de la máquina después de las pasadas. Asegúrese de que no haya acumulación de polvo en el horno o los conductos. Limpieza del molde con los medios diseñados. |
Seguridad | Utilizar equipo de protección individual durante la manipulación de polvos finos. Eliminar correctamente los aglutinantes químicos. Dejar enfriar el horno antes del mantenimiento. |
Formación | Formar a los operadores de máquinas y hornos sobre los procedimientos. Impartir sesiones de actualización sobre seguridad y mantenimiento. |
Optimización | Ajustar los parámetros del proceso hasta que la calidad de la pieza se estabilice dentro de las especificaciones. Mantener registros detallados del proceso. |
Actividades típicas de mantenimiento y frecuencia
Actividad | Frecuencia |
---|---|
Limpieza de boquillas de máquinas de moldeo por inyección | Después de cada lote |
Pulido de moldes | Semanal |
Limpieza de barriles a máquina | Mensualmente |
Comprobación de la atmósfera del horno de eliminación de ligantes | Mensualmente |
Calibrado del termopar del horno de sinterización | 6 meses |
Estudios de flujo de moldes | Anualmente |
Cómo elegir un proveedor de MIM
Elegir un proveedor de MIM competente es fundamental para obtener piezas de buena calidad a tiempo y a un coste razonable. He aquí algunos factores importantes a tener en cuenta:
Factor | Criterios |
---|---|
Capacidad técnica | Equipos avanzados, años de experiencia, conocimientos técnicos |
Opciones de material | Gama de materiales como acero inoxidable, acero para herramientas, aleaciones de tungsteno |
Tratamiento secundario | Instalaciones propias de mecanizado, unión y revestimiento |
Sistemas de calidad | Certificación ISO 9001, control de calidad y procedimientos de inspección |
Capacidad de producción | Capacidad de producción de gran volumen para la estabilidad |
Tiempo de espera | Rapidez desde el diseño hasta la entrega |
Ubicación | Proximidad geográfica para la eficiencia logística |
Coste | Modelo de fijación de precios: se prefiere la fijación de precios por pieza |
Atención al cliente | Capacidad de respuesta a las consultas, asistencia técnica, gestión de proyectos |
Preguntas a los posibles proveedores de MIM
- ¿Con qué materiales y tamaños de piezas tiene experiencia?
- ¿Ofrecen procesos secundarios como mecanizado o revestimiento?
- ¿Qué certificaciones de calidad y procedimientos de inspección se siguen?
- ¿Cómo se manipulan materiales sensibles como las aleaciones de titanio o los carburos de wolframio?
- ¿Qué volúmenes de producción puede entregar mensualmente de forma fiable?
- ¿Cómo se minimiza la chatarra y se maximiza el rendimiento?
- ¿Cuál es la variabilidad entre piezas en cuanto a dimensiones y propiedades?
- ¿Cómo se optimizará el diseño para el proceso MIM?
- ¿Qué informes de calidad y gráficos de control se facilitarán?
Comparación del MIM con otros procesos
Comparación entre el MIM y otros procesos de fabricación de metales:
Proceso | Ventajas | Desventajas |
---|---|---|
MIM | Geometrías complejas, producción en serie, forma casi neta, amplia selección de materiales | Inversión inicial en utillaje, limitaciones de tamaño |
Mecanizado CNC | Flexibilidad de materiales, rapidez de entrega de prototipos | Complejidad limitada, menores volúmenes |
Fundición de metales | Bajo coste de las piezas, grandes volúmenes | Limitaciones de forma, menor resistencia |
Estampación de metales | Alta velocidad, grandes volúmenes, bajos costes | Sólo se adapta a geometrías 2D |
Impresión 3D | Libertad de diseño, creación rápida de prototipos | Menor resistencia, mayor coste, tamaños y materiales limitados |
Ventajas del MIM frente al mecanizado
- Mayor aprovechamiento del material con forma casi neta
- Sin costosos mecanizados para formas complejas
- Propiedades mecánicas superiores
- Menores costes de utillaje en comparación con el mecanizado de troqueles
- El proceso automatizado permite la producción en serie
- Posibilidad de mejores acabados superficiales
Ventajas del MIM sobre la fundición de metales
- Mejor precisión dimensional y acabado superficial
- Menos defectos como la porosidad en comparación con las piezas de fundición
- Propiedades isotrópicas a diferencia de la fundición direccional
- Poca o ninguna rebaba o abertura, a diferencia de las piezas moldeadas
- Sin reacciones relacionadas con la fusión ni cambios en la composición
- A diferencia de la fundición, es posible realizar machos y rebajes
- Amplias opciones de materiales más allá de las aleaciones moldeables
- Coherencia de las propiedades con la pulvimetalurgia
Limitaciones del MIM frente al mecanizado CNC
- Tamaño limitado por la capacidad de la máquina de moldeo por inyección
- Más tiempo y costes iniciales de utillaje
- Tolerancias estrechas +/- 0,5% frente a +/- 0,1% para mecanizado CNC
- Limitaciones geométricas frente a mecanizado sin restricciones
- Menor dureza máxima alcanzable en comparación con el mecanizado
- A menudo sigue siendo necesario un mecanizado secundario para alcanzar las tolerancias
Cuándo no utilizar el MIM
- Piezas muy grandes que superan la capacidad de los equipos MIM
- Piezas que requieren tolerancias extremadamente estrechas por debajo de 0,5%
- Aplicaciones que requieren una dureza superficial superior a 50 HRC
- Productos con requisitos de volumen muy bajos
- Componentes con relaciones de aspecto extremas inadecuadas para el moldeo
- Cuando no hay tiempo para optimizar el diseño del proceso MIM
- Aplicaciones sensibles a los costes con opciones de fabricación más baratas
Consideraciones sobre el diseño y modelado del MIM
El diseño adecuado de la pieza y de la materia prima es crucial para que el MIM consiga las propiedades y el rendimiento requeridos. Estas son las consideraciones clave para el diseño:
Fase de diseño de la pieza
- Optimizar el grosor de las paredes para un llenado uniforme del molde durante la inyección
- Incluyen generosos radios internos y filetes para facilitar el llenado
- Evitar cambios bruscos en la sección transversal a lo largo de la trayectoria del flujo
- Diseñar compuertas de molde y canales adecuados para patrones de flujo apropiados
- Añada refuerzos y refuerzos para evitar el hundimiento o el alabeo.
- Tener en cuenta la contracción de la pieza durante la sinterización en las dimensiones iniciales
- Desarrollar moldes prototipo para la validación del diseño antes de la producción completa.
Desarrollo de materias primas
- Adaptar la viscosidad de la materia prima a la complejidad del molde a las temperaturas de moldeo
- Garantizar una carga de polvo suficiente para la densidad sinterizada requerida
- Seleccionar los componentes aglutinantes y la proporción de polvo adecuados para la mezclabilidad
- Optimización de la distribución granulométrica del polvo para la densidad de empaquetamiento del polvo
- Ajustar las fórmulas de las materias primas para eliminar los defectos del ligante
- Validación de las propiedades de las materias primas mediante simulaciones del flujo del molde
- Probar múltiples iteraciones de materias primas para lograr una moldeabilidad total
Simulación y modelización
- Modelado del flujo del molde para optimizar la ubicación de las compuertas y los canales
- AEF estructural para predecir el alabeo y optimizar la geometría de la pieza
- Simulaciones CFD para la eliminación uniforme del ligante y la sinterización
- Modelado térmico para minimizar las tensiones residuales
- Modelado mecánico para maximizar la resistencia y el rendimiento
- Software de modelización de procesos para estudiar las interacciones entre parámetros
- Validación experimental de las predicciones del software mediante moldes prototipo
Principales resultados de la modelización
- Tiempo de llenado del molde, viscosidad de la materia prima, temperatura del frente de flujo
- Predicciones de líneas de soldadura, purgadores de aire y otros defectos de moldeo
- Gradientes espaciales de contenido de ligante, temperatura y disolución
- Velocidad de sinterización, gradientes de densidad, contracción, tendencias de alabeo
- Distribución de la tensión residual, desgarro en caliente y estimación de grietas
- Resistencia mecánica, vida a la fatiga, análisis de tolerancia al daño
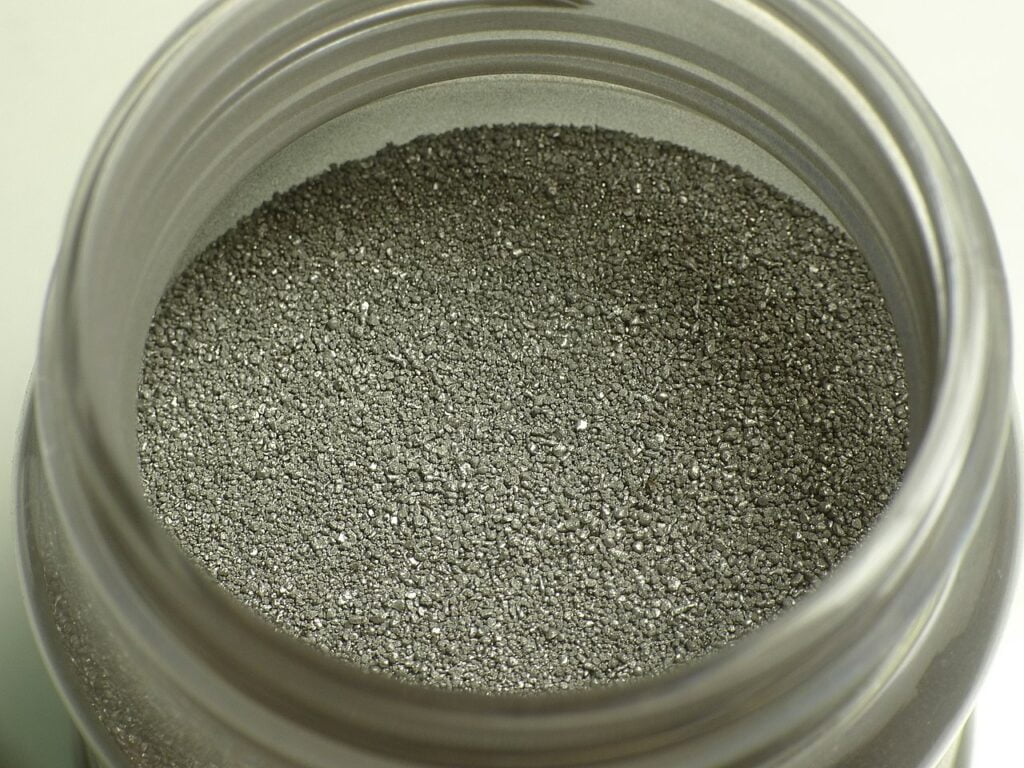
Defectos MIM y métodos de mitigación
Pueden surgir defectos en las piezas MIM debido a la falta de optimización de la materia prima, los parámetros de moldeo o las condiciones del horno. A continuación se describen los defectos comunes del MIM y los métodos para mitigarlos:
Defecto | Causas profundas | Métodos de mitigación |
---|---|---|
Defectos superficiales | Baja temperatura de molde, alta fricción, componentes aglutinantes | Optimizar el pulido del molde, utilizar agentes desmoldeantes, reducir gradualmente la temperatura del molde. |
Líneas de soldadura | Frentes de flujo de materias primas indeseables | Optimización del diseño de compuertas y canales mediante modelado para evitar líneas de soldadura |
Alabeo | Calentamiento no uniforme en el horno, tensiones residuales | Optimización estructural, alivio de tensiones previo a la sinterización, ajustes optimizados del horno |
Grietas | Sinterización rápida, alto contenido de aglutinante, gradientes térmicos pronunciados | Menor velocidad de calentamiento, optimización del sistema aglutinante, rediseño estructural |
Porosidad | Baja carga de polvo en la materia prima, mezcla deficiente | Aumentar el contenido de polvo en la materia prima, mejorar el proceso de mezcla |
Variación dimensional | Contracción incoherente, desgaste del molde, gradientes de densidad | Control estadístico de procesos, mantenimiento de moldes, optimización del desbobinado y la sinterización |
Contaminación | Mala manipulación, control de la atmósfera del horno | EPI adecuados, mejorar los filtros de aire, evitar la contaminación cruzada en los lotes de hornos |
Relleno incompleto | Alta temperatura del molde, alta viscosidad | Aumentar la temperatura del molde y de la materia prima, utilizar un aglutinante de menor viscosidad |
Datos y tendencias de la industria MIM
MIM Tamaño del mercado mundial
El mercado mundial de MIM se valoró en 1.500 millones de USD en 2022 y se prevé que alcance los 3.100 millones de USD en 2030, con un crecimiento del 8,7% CAGR, impulsado por la demanda de los sectores sanitario, automovilístico y aeroespacial.
Factores de crecimiento del sector
- Tendencias en aligeramiento en los sectores automovilístico, aeroespacial y electrónico
- Demanda de componentes metálicos pequeños y complejos en dispositivos médicos
- Más viable con una gama más amplia de materiales aptos para MIM
- La automatización reduce los costes de producción
- Crecimiento de la fabricación de componentes de precisión
- Mayor adopción en aplicaciones emergentes como la relojería
TACC prevista por región
- Asia-Pacífico: 9,3% CAGR
- Europa: 10,2% TACC
- Norteamérica: 7,6% CAGR
- Resto del mundo: 7,9% TCAC
Porcentaje de piezas MIM por sector
- Productos de consumo: 22%
- Automóvil: 21%
- Armas de fuego: 15%
- Médico: 14%
- Industrial: 13%
- Aeroespacial: 8%
- Otros: 7%
Tendencias en el desarrollo de la tecnología MIM
- Nuevos sistemas aglutinantes para reducir defectos y permitir geometrías complejas
- Nuevas formulaciones de materias primas para mejorar la carga de polvo y la sinterización
- MIM multimaterial que combina diferentes polvos en un solo componente
- Automatización del procesamiento posterior, como mecanizado, unión, roscado, etc.
- Técnicas híbridas MIM + fabricación aditiva
- Nuevos métodos de calentamiento, como el sinterizado por microondas, para un procesado más rápido
- Simulaciones integradas que combinan múltiples fases físicas y de fabricación
- Mayor adopción de sistemas de gestión de la calidad
Resumen
Principales conclusiones:
- El MIM permite producir grandes volúmenes de componentes metálicos complejos combinando el moldeo por inyección y la pulvimetalurgia.
- Adecuado para piezas pequeñas, complejas y de alta precisión en las industrias médica, de armas de fuego, automovilística, aeroespacial y de consumo.
- Entre sus ventajas, cabe citar la forma casi neta, la amplia gama de materiales y las buenas propiedades mecánicas próximas a las de los materiales forjados.
- Implica el moldeo de la materia prima, el desbobinado y las fases de sinterización mediante equipos especializados.
- Requiere experiencia en diseño de piezas, desarrollo de materias primas, modelado de procesos, control de defectos y gestión de calidad.
- Se prevé un crecimiento de 8,7% CAGR en todo el mundo impulsado por la demanda en todos los sectores.
- Desarrollos tecnológicos continuos para un procesamiento más rápido, más materiales, mayor automatización y mejora de la calidad de las piezas.
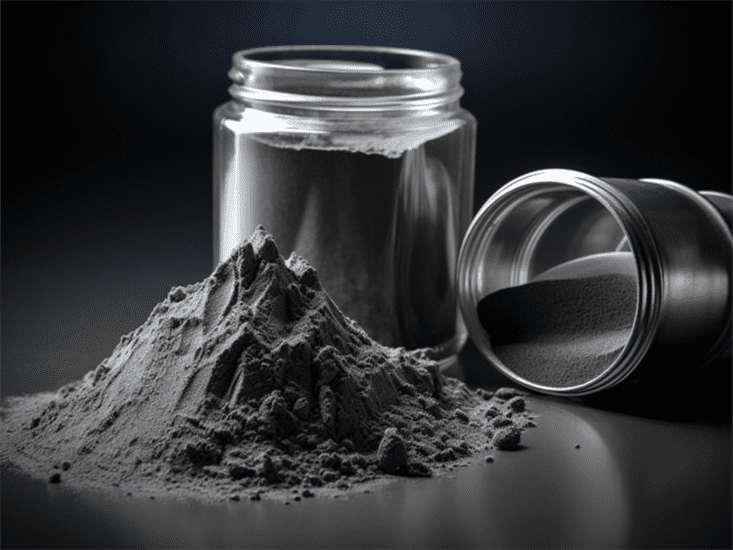
Preguntas frecuentes
P: ¿Cuáles son las principales ventajas de la tecnología MIM?
R: Las principales ventajas del MIM son:
- Capacidad para producir geometrías pequeñas y complejas que no son posibles mediante mecanizado o fundición.
- Fabricación con forma casi neta que da lugar a
P: ¿Cuál es la capacidad de tolerancia típica del MIM?
R: Por lo general, el MIM puede alcanzar tolerancias de +/- 0,5%, aunque es posible alcanzar +/- 0,3% en algunas geometrías y puede ser necesario el mecanizado para tolerancias más estrictas.
P: ¿Qué tamaño de piezas pueden fabricarse con MIM?
R: El MIM puede producir piezas de 0,1 gramos a unos 250 gramos de masa. Se pueden fabricar piezas más grandes, pero es difícil debido a las limitaciones de tamaño de las máquinas de moldeo.
P: ¿En qué se diferencia el MIM del moldeo por inyección de plástico?
R: Aunque ambos utilizan equipos de moldeo por inyección, el MIM puede producir piezas metálicas, mientras que los plásticos tienen una resistencia mucho menor. Pero el MIM tiene índices de producción más bajos y costes más elevados que el moldeo por inyección de plásticos.
P: ¿Qué tratamiento térmico se utiliza en el MIM?
R: El proceso de sinterización del MIM implica el calentamiento hasta casi el punto de fusión del polvo metálico, por lo que no suele ser necesario ningún otro tratamiento térmico. Pueden realizarse tratamientos térmicos adicionales para modificar las propiedades.
P: ¿Qué materiales pueden utilizarse en MIM?
R: Existe una amplia gama de materiales aptos para el MIM, como aceros inoxidables, aceros para herramientas, superaleaciones, titanio, aleaciones pesadas de tungsteno y aleaciones magnéticas, entre otros. El desarrollo de nuevos materiales es un área de investigación clave en el MIM.
P: ¿En qué se diferencia el MIM de la impresión 3D en metal?
R: El MIM puede producir mayores volúmenes con mejor acabado superficial y mejores propiedades mecánicas. Pero la impresión 3D ofrece mayor libertad de diseño y plazos de comercialización más rápidos para prototipos o piezas personalizadas.
Compartir
MET3DP Technology Co., LTD es un proveedor líder de soluciones de fabricación aditiva con sede en Qingdao, China. Nuestra empresa está especializada en equipos de impresión 3D y polvos metálicos de alto rendimiento para aplicaciones industriales.
Solicite información para obtener el mejor precio y una solución personalizada para su empresa.
Artículos relacionados
Acerca de Met3DP
Actualización reciente
Nuestro producto
CONTACTO
¿Tiene alguna pregunta? ¡Envíenos un mensaje ahora! Atenderemos su solicitud con todo un equipo tras recibir su mensaje.