Vibration Isolator Housings
Índice
Introduction – The Critical Role of Vibration Isolator Housings in Aerospace Applications
In the demanding realm of aerospace engineering, every component plays a crucial role in ensuring the safety, performance, and longevity of aircraft and spacecraft. Among these critical parts, vibration isolator housings stand as unsung heroes, diligently working to mitigate the detrimental effects of mechanical vibrations. These vibrations, generated by engines, rotors, and other dynamic systems, can lead to structural fatigue, noise pollution, and compromised operational efficiency if not effectively controlled.
The housing of a vibration isolator is the structural backbone of the entire assembly. It must be robust enough to withstand significant mechanical loads while providing a stable and precise interface for the damping elements. The material and manufacturing process of these housings are therefore paramount. Traditionally, these components have been manufactured using conventional methods such as machining or casting. However, the advent of metal Impresión 3D, also known as additive manufacturing (AM), presents a paradigm shift in how these critical aerospace parts can be designed and produced. This innovative technology offers unprecedented design freedom, material optimization, and the potential for significant performance enhancements. As a leading provider of additive manufacturing solutions, Metal3DP is at the forefront of enabling these advancements, offering industry-leading print volume, accuracy, and reliability for mission-critical parts like aerospace vibration isolator housings. Our commitment to quality and innovation ensures that components manufactured using our technologies meet the stringent demands of the aerospace sector.
What are Aerospace Vibration Isolator Housings Used For? Key Applications and Industries
Aerospace vibration isolator housings serve as the structural foundation for vibration isolation systems across a multitude of applications within the industry. Their primary function is to encase and support the elastomeric or metallic elements that absorb and dampen vibrations, preventing their transmission to sensitive equipment, the airframe, or the passenger cabin. The effectiveness and durability of these housings directly impact the overall performance and safety of aerospace vehicles.
Here are some key applications and industries where these housings are critically important:
- Motores de aviación: Vibration isolators are essential in mounting jet engines to the airframe, reducing the transmission of high-frequency vibrations that can cause fatigue and noise. The housings must withstand extreme temperatures and mechanical stresses.
- Helicopter Rotor Systems: Helicopters generate significant vibrations from their main and tail rotors. Isolator housings are crucial for protecting the airframe and ensuring a smoother flight experience.
- Avionics and Sensitive Equipment: Delicate electronic equipment, sensors, and navigation systems require isolation from vibrations that could impair their accuracy and reliability. Housings provide a stable and protective enclosure for these isolators.
- Spacecraft and Satellite Systems: In the harsh environment of space, vibration isolation is vital for the precise operation of scientific instruments, communication systems, and structural integrity during launch and orbital maneuvers.
- Sistemas del tren de aterrizaje: Isolators within the landing gear help to absorb the shock and vibrations during takeoff and landing, contributing to passenger comfort and structural integrity.
- Unidades de potencia auxiliar (APU): APUs generate their own set of vibrations, which need to be isolated from the main airframe to prevent noise and fatigue.
The industries benefiting from high-quality aerospace vibration isolator housings include:
- Aviación comercial: For passenger comfort, safety, and the longevity of aircraft.
- Aviación militar: For the reliability and performance of fighter jets, transport aircraft, and helicopters under demanding conditions.
- Exploración espacial: For the structural integrity and operational accuracy of spacecraft and satellites.
- Aerospace Manufacturing and Suppliers: Companies involved in the design, production, and supply of aircraft and spacecraft components.
Metal 3D printing, offered by pioneers like Metal3DP, provides a unique advantage in creating these complex housings with optimized geometries and material properties tailored to these specific applications. Our advanced metal powders and printing technologies ensure the production of dense, high-quality parts that meet the rigorous standards of the aerospace industry.
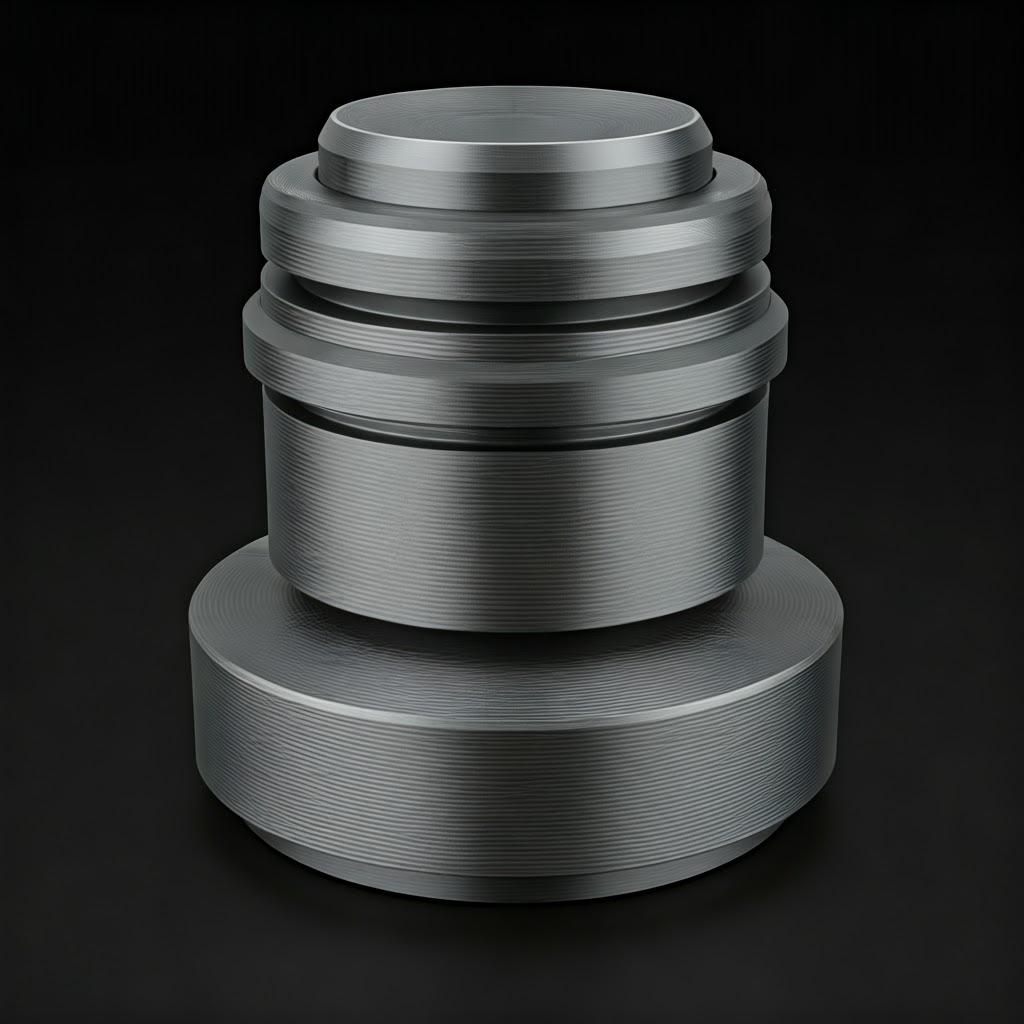
Why Choose Metal 3D Printing for Aerospace Vibration Isolator Housings? Advantages Over Traditional Manufacturing
The adoption of metal 3D printing for the manufacturing of aerospace vibration isolator housings offers a compelling array of advantages over traditional methods such as machining from billet or casting. These benefits are particularly significant in the aerospace industry, where performance, weight, and customization are paramount.
- Libertad de diseño y complejidad: Additive manufacturing allows for the creation of intricate geometries that are simply not achievable with traditional methods. This enables engineers to design housings with optimized shapes, internal lattice structures for weight reduction, and integrated features, leading to improved performance and reduced part count. Metal3DP’s advanced Selective Electron Beam Melting (SEBM) printers excel in producing complex geometries with high precision.
- Optimización del peso: In aerospace, every gram counts. 3D printing facilitates the creation of lightweight designs through topology optimization and the use of lattice structures within the housing. This reduces material usage and overall aircraft weight, leading to better fuel efficiency and performance.
- Eficiencia del material: Traditional subtractive manufacturing methods often result in significant material waste. Additive manufacturing, on the other hand, builds parts layer by layer, using only the necessary material. This is particularly beneficial when working with expensive aerospace-grade alloys like titanium.
- Personalización y producción de bajo volumen: 3D printing is ideal for producing customized housings or small batches of parts without the need for expensive tooling. This is crucial for specialized aerospace applications or for prototyping and testing new designs.
- Creación rápida de prototipos e iteración: The speed and flexibility of 3D printing significantly accelerate the design and development process. Engineers can quickly iterate on designs and produce functional prototypes for testing, reducing time-to-market for new aerospace technologies.
- Rendimiento mejorado: By optimizing the design and material selection, 3D printed housings can offer superior performance characteristics, such as improved stiffness-to-weight ratio and better vibration damping properties. Metal3DP’s wide range of high-quality metal powders, including innovative alloys, enables the production of parts with superior mechanical properties.
- Ensamblaje reducido: Complex housings can be designed as single, consolidated parts, reducing the need for multiple components and assembly processes. This not only saves time and cost but also improves the reliability of the final assembly by eliminating potential weak points at joints.
By leveraging the capabilities of metal 3D printing, aerospace manufacturers can achieve significant improvements in the design, production, and performance of vibration isolator housings, ultimately contributing to safer, more efficient, and more advanced aircraft and spacecraft.
Recommended Materials: Ti-6Al-4V and Ti-6Al-4V ELI for High-Performance Housings
The selection of the right material is paramount for aerospace vibration isolator housings, as they must withstand demanding operational conditions, including high stresses, temperature variations, and corrosive environments. Titanium alloys, particularly Ti-6Al-4V and its extra-low interstitial (ELI) variant, are highly favored in aerospace due to their exceptional combination of properties. Metal3DP specializes in providing high-quality metal powders, including these titanium alloys, specifically optimized for laser and electron beam powder bed fusion processes.
Ti-6Al-4V (titanio de grado 5)
- Composición: This alloy consists primarily of titanium, with approximately 6% aluminum and 4% vanadium.
- Propiedades clave:
- Alta relación resistencia-peso: Offers excellent strength while being significantly lighter than steel alloys, crucial for aerospace applications.
- Excelente resistencia a la corrosión: Highly resistant to corrosion from salt water, atmospheric exposure, and many chemicals.
- Buena resistencia a la fatiga: Capable of withstanding cyclic loading, essential for components subjected to vibrations.
- Biocompatibilidad: Although primarily used for structural aerospace components, its biocompatibility is relevant in certain specialized applications.
- Soldabilidad: Can be welded using various techniques.
- Why it Matters for Vibration Isolator Housings: The high strength-to-weight ratio of Ti-6Al-4V allows for the design of lightweight yet robust housings that can effectively support the isolator elements and withstand operational stresses. Its excellent corrosion resistance ensures long-term durability in various environmental conditions encountered by aircraft and spacecraft.
Ti-6Al-4V ELI (Extra-Low Interstitial, Grade 23 Titanium)
- Composición: Similar to Ti-6Al-4V, but with lower levels of interstitial elements such as oxygen, carbon, nitrogen, and hydrogen.
- Key Properties (in addition to those of Ti-6Al-4V):
- Enhanced Ductility and Toughness: The lower interstitial content results in improved ductility and fracture toughness, making it more resistant to cracking and failure under stress.
- Superior Fatigue Resistance: Offers even better resistance to fatigue compared to standard Ti-6Al-4V, which is critical for components subjected to continuous vibrations.
- Excelente biocompatibilidad: Often the preferred titanium alloy for medical implants due to its enhanced biocompatibility.
- Why it Matters for Vibration Isolator Housings: For aerospace vibration isolator housings, especially those in critical applications or subjected to extreme vibrational loads, Ti-6Al-4V ELI provides an extra margin of safety and reliability due to its superior ductility and fatigue resistance. While slightly more expensive than standard Ti-6Al-4V, the enhanced performance can justify the cost in demanding scenarios.
Metal3DP’s advanced powder making system, utilizing industry-leading gas atomization and PREP technologies, ensures that our Ti-6Al-4V and Ti-6Al-4V ELI powders exhibit high sphericity and excellent flowability, which are essential for producing dense, high-quality metal parts with superior mechanical properties through 3D printing. Our comprehensive solutions, spanning SEBM printers and advanced metal powders, empower our customers to achieve next-generation manufacturing for critical aerospace components.
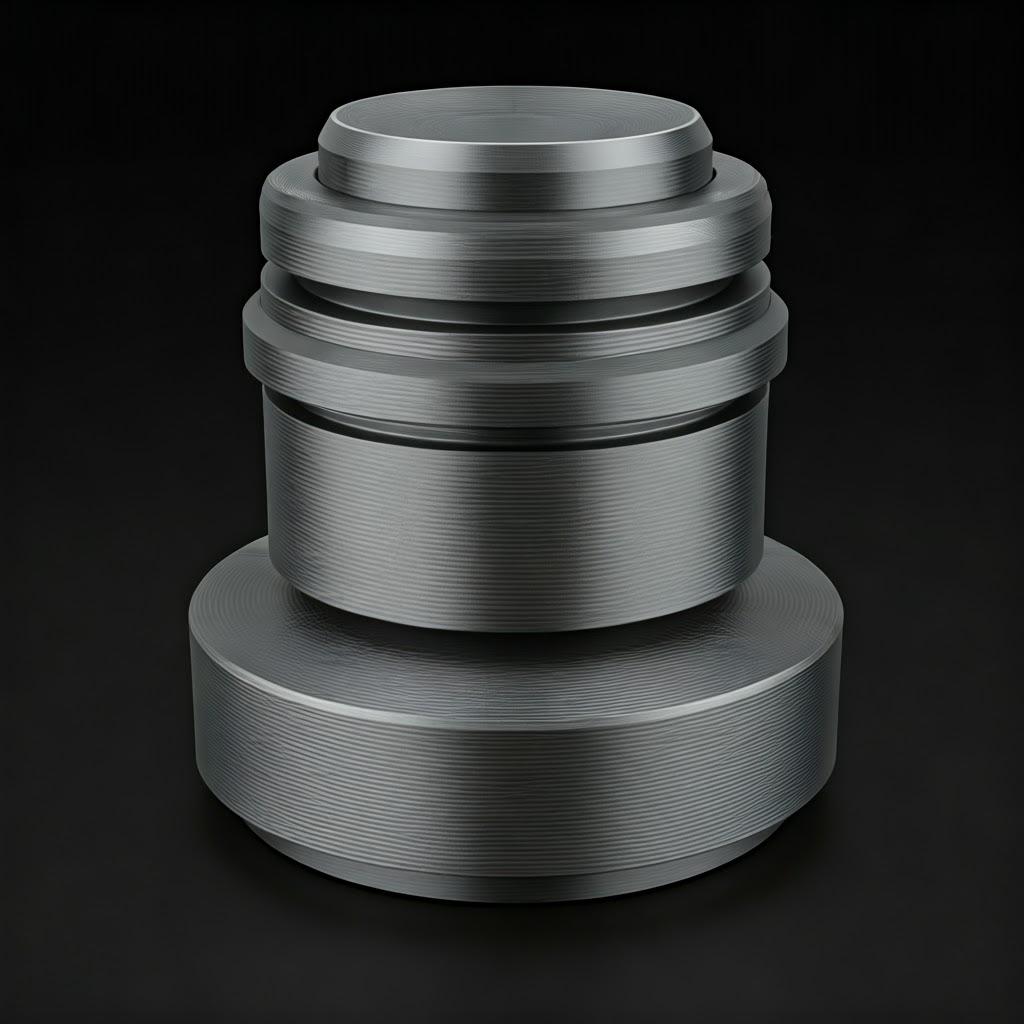
Design Considerations for Additive Manufacturing of Vibration Isolator Housings: Optimizing for Performance and Weight
Designing aerospace components for additive manufacturing requires a shift in mindset compared to traditional methods. The layer-by-layer build process offers unique opportunities for optimization but also introduces specific design considerations. For vibration isolator housings, the focus is often on maximizing performance while minimizing weight.
- Optimización de la topología: This computational technique allows engineers to identify and remove material from low-stress areas of a design, resulting in lightweight yet structurally sound parts. For vibration isolator housings, topology optimization can be used to create organic, free-form shapes that efficiently distribute loads while minimizing mass.
- Estructuras reticulares: Instead of solid infill, 3D printing enables the use of intricate lattice structures within the housing. These structures offer a high strength-to-weight ratio and can be tailored to provide specific stiffness or energy absorption characteristics. Different lattice patterns (e.g., gyroid, cubic, diamond) can be chosen based on the application requirements.
- Integración de características: Additive manufacturing allows for the integration of multiple features into a single part, reducing the need for assembly. For vibration isolator housings, this could include integrated mounting features, cooling channels (if necessary), or even internal damping elements.
- Wall Thickness and Ribbing: Careful consideration of wall thickness is crucial to balance weight and structural integrity. Ribs and stiffeners can be incorporated into the design to enhance the stiffness of thin-walled sections without significantly increasing weight.
- Estructuras de apoyo: Overhanging features and complex geometries often require support structures during the 3D printing process. These supports need to be carefully designed to ensure they can be easily removed without damaging the part’s surface. The orientation of the part during printing can significantly impact the need for and complexity of support structures. Metal3DP’s expertise in Selective Electron Beam Melting (SEBM) allows for efficient support structure design and removal.
- Consideraciones sobre el acabado de la superficie: The layer-by-layer nature of 3D printing can result in a stepped surface finish. The orientation of the part and the layer height used during printing affect the surface roughness. For critical mating surfaces or areas requiring smooth operation, post-processing techniques may be necessary.
- Gestión térmica: In some aerospace applications, vibration isolator housings may be exposed to elevated temperatures. Designing with internal cooling channels or selecting materials with appropriate thermal properties is essential.
By thoughtfully addressing these design considerations, engineers can leverage the unique capabilities of metal 3D printing to create aerospace vibration isolator housings that offer superior performance, reduced weight, and enhanced functionality compared to traditionally manufactured parts.
Lograr precisión: Tolerancia, acabado superficial y precisión dimensional en carcasas impresas en 3D
In the aerospace industry, precision is paramount. Vibration isolator housings must adhere to strict dimensional tolerances and possess appropriate surface finishes to ensure proper fit, functionality, and long-term reliability. Metal 3D printing technologies have made significant strides in achieving the required levels of accuracy and surface quality.
- Precisión dimensional: The accuracy achievable in metal 3D printing depends on several factors, including the printing technology used (e.g., DMLS, SLM, EBM), the material, the part geometry, and the calibration of the printer. Metal3DP’s SEBM printers are engineered to deliver industry-leading accuracy, ensuring that critical dimensions of the vibration isolator housings meet stringent aerospace specifications.
- Capacidades de tolerancia: While 3D printing can achieve tight tolerances, it’s important for designers to understand the achievable limits and design accordingly. Specifying overly tight tolerances can increase manufacturing costs and potentially lead to higher rejection rates. Design for Additive Manufacturing (DfAM) principles emphasize designing with achievable tolerances in mind. Typical tolerances for metal 3D printed parts can range from ±0.1 mm to ±0.05 mm, depending on the size and complexity of the feature.
- Acabado superficial: The as-built surface finish of a metal 3D printed part is typically rougher than that achieved by machining. The surface roughness is influenced by the powder particle size, layer thickness, and the build orientation. Typical surface roughness (Ra) values for metal 3D printed parts range from 5 to 20 $\mu$m.
- Post-Processing for Improved Precision: To meet the demanding surface finish and tolerance requirements of aerospace applications, post-processing techniques are often employed. These can include:
- Mecanizado: Precision CNC machining can be used to achieve tight tolerances on critical features and smooth surface finishes on mating surfaces.
- Pulido: Various polishing methods (e.g., abrasive polishing, electrochemical polishing) can be used to improve surface smoothness.
- Granallado: This surface treatment can improve fatigue resistance and surface finish.
- Tratamiento térmico: While primarily used to optimize material properties, heat treatment can also reduce internal stresses that might affect dimensional accuracy.
By carefully selecting the 3D printing process, optimizing the design for manufacturability, and employing appropriate post-processing techniques, it is possible to achieve the high levels of precision required for aerospace vibration isolator housings.
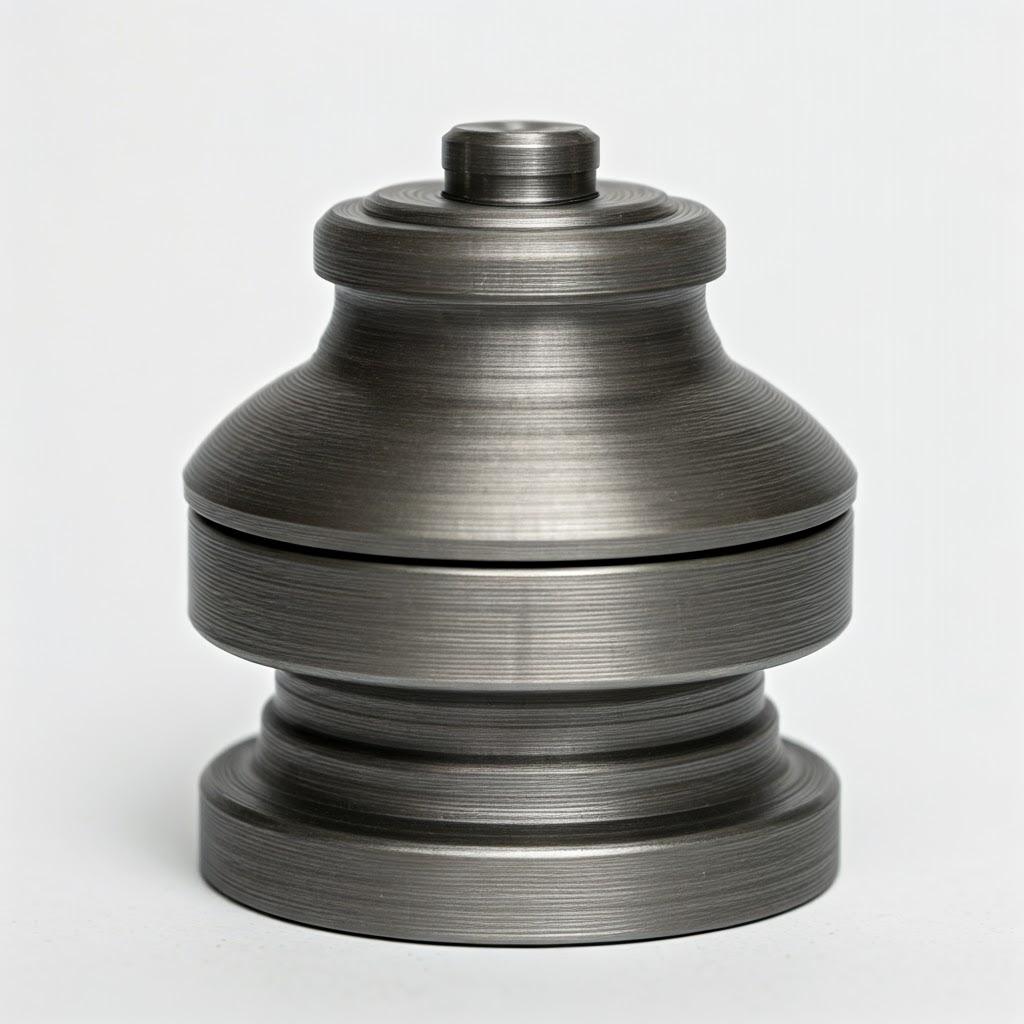
Post-Processing of 3D Printed Aerospace Housings: Ensuring Optimal Material Properties and Surface Quality
While the metal 3D printing process itself creates near-net-shape parts, post-processing steps are often essential to achieve the final required material properties, surface finish, and dimensional accuracy for aerospace vibration isolator housings. These steps ensure that the components meet the stringent demands of the industry.
- Stress Relief and Heat Treatment: Metal 3D printed parts can contain residual stresses due to the rapid heating and cooling cycles during the build process. Stress relief annealing is crucial to mitigate these stresses and prevent warping or cracking. Subsequent heat treatments, such as hot isostatic pressing (HIP), can further densify the material, reduce porosity, and enhance mechanical properties like fatigue strength and ductility. The specific heat treatment protocols are tailored to the alloy being used (e.g., Ti-6Al-4V requires specific annealing and aging cycles).
- Retirada de la estructura de soporte: Support structures are often necessary to build complex geometries. Their removal must be done carefully to avoid damaging the part’s surface. Techniques include manual removal, machining, wire EDM, or chemical dissolution, depending on the material and support structure design. Metal3DP’s SEBM technology often results in less adhered support structures compared to other powder bed fusion methods, simplifying removal.
- Acabado superficial: As mentioned earlier, the as-built surface finish may not be suitable for all aerospace applications. Various methods are used to improve surface quality:
- Granallado: Used to remove partially sintered powder and achieve a more uniform surface texture.
- Grinding and Polishing: Abrasive processes used to achieve smoother surfaces and tighter tolerances on specific features.
- Grabado químico: Can be used to remove a thin layer of material and reduce surface roughness.
- Revestimientos: Surface coatings, such as anodizing for titanium or corrosion-resistant paints, can be applied to enhance durability and performance in specific environments.
- Inspección y control de calidad: After post-processing, rigorous inspection is crucial to ensure that the housings meet the required dimensional tolerances, surface finish specifications, and material properties. Techniques such as coordinate measuring machines (CMM), non-destructive testing (NDT) methods (e.g., ultrasonic testing, dye penetrant inspection), and metallographic analysis are employed to verify the quality and integrity of the parts.
By implementing appropriate post-processing procedures, manufacturers can transform as-built 3D printed parts into high-performance, reliable aerospace vibration isolator housings that meet the demanding standards of the industry.
Common Challenges and How to Avoid Them – Highlighting Potential Problems in 3D Printing Vibration Isolator Housings
While metal 3D printing offers numerous advantages, several challenges can arise during the manufacturing of aerospace vibration isolator housings. Understanding these potential issues and implementing strategies to avoid them is crucial for successful production.
- Deformación y distorsión: Thermal stresses during the printing process can lead to warping or distortion of the part, especially for large or complex geometries.
- How to Avoid: Optimize part orientation on the build plate, use appropriate support structures to anchor the part, employ stress-relieving heat treatments after printing, and consider using simulation software to predict and mitigate potential distortion. Metal3DP’s SEBM process, with its higher build temperatures, can sometimes reduce residual stresses compared to laser-based methods, potentially minimizing warping.
- Support Structure Removal Damage: Aggressive removal of support structures can damage the delicate surfaces of the housing.
- How to Avoid: Design support structures that are easily removable, use appropriate removal tools and techniques, and consider the placement of supports in non-critical areas.
- Porosity and Lack of Fusion: Insufficient laser or electron beam energy or improper process parameters can lead to porosity (internal voids) or lack of fusion (incomplete bonding between layers), weakening the part.
- How to Avoid: Optimize printing parameters based on the material and geometry, ensure proper powder flowability and packing density, and conduct thorough process validation. Metal3DP’s expertise in metal powder characterization and process optimization helps ensure high-density, defect-free parts.
- Material Inconsistency: Variations in the properties of the metal powder feedstock can lead to inconsistencies in the final part.
- How to Avoid: Source high-quality metal powders from reputable suppliers with strict quality control measures. Metal3DP employs advanced powder making systems to ensure the consistency and quality of our metal powders.
- Rugosidad superficial: Achieving the required surface finish can be challenging directly from the printing process.
- How to Avoid: Optimize build orientation and layer thickness, and plan for appropriate post-processing steps like machining or polishing for critical surfaces.
- Imprecisión Dimensional: Deviations from the intended dimensions can occur due to shrinkage, thermal expansion, or printer calibration issues.
- How to Avoid: Calibrate the 3D printer regularly, apply scaling factors to the design to compensate for predictable shrinkage, and use precise measurement techniques during post-processing inspection.
By proactively addressing these potential challenges through careful design, optimized process parameters, and appropriate post-processing, manufacturers can reliably produce high-quality aerospace vibration isolator housings using metal 3D printing.
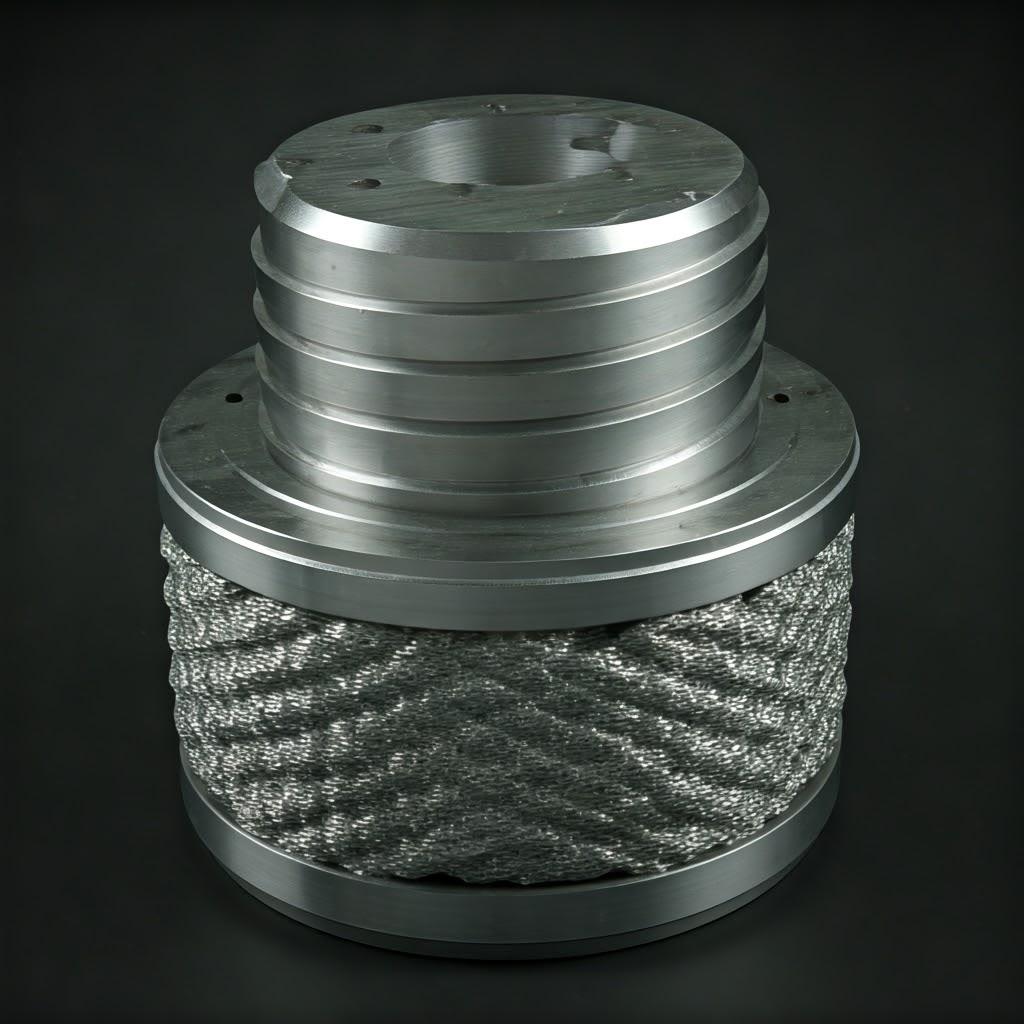
Cómo elegir el proveedor de servicios de impresión 3D sobre metal adecuado para componentes aeroespaciales
Selecting the right metal 3D printing service provider is a critical decision for aerospace companies seeking to leverage this advanced manufacturing technology. The quality, reliability, and compliance of the printed components are paramount in this highly regulated industry. Here are key factors to consider when evaluating potential service providers:
- Industry Experience and Certifications: Look for a provider with a proven track record in serving the aerospace industry. Relevant certifications, such as AS9100 (aerospace quality management system), are strong indicators of their commitment to quality and process control. Inquire about their experience with similar aerospace applications and the types of components they have produced.
- Capacidades de los materiales: Ensure the service provider offers the specific metal alloys required for your application, such as Ti-6Al-4V or Ti-6Al-4V ELI. Verify that they have experience processing these materials and can provide material data sheets and traceability. Metal3DP offers a wide range of high-quality metal powders optimized for aerospace applications.
- Printing Technologies and Equipment: Understand the types of metal 3D printing technologies the provider utilizes (e.g., DMLS, SLM, EBM). Each technology has its strengths and weaknesses in terms of accuracy, surface finish, build volume, and material compatibility. Metal3DP specializes in Selective Electron Beam Melting (SEBM), which offers unique advantages for certain aerospace applications.
- Experiencia en diseño para la fabricación aditiva (DfAM): A knowledgeable service provider should offer expertise in DfAM principles to help optimize your designs for the 3D printing process, ensuring manufacturability, performance, and cost-effectiveness.
- Capacidades de postprocesado: Determine if the provider offers the necessary post-processing services, such as stress relief, heat treatment, surface finishing, and machining, to meet the final specifications of your components.
- Quality Control and Inspection Processes: Inquire about their quality control procedures, including dimensional inspection, non-destructive testing (NDT), and material testing. Robust quality assurance is essential for aerospace parts.
- Volumen y capacidad de construcción: Ensure the provider has the build volume and production capacity to handle your project requirements, especially for larger components or serial production. Metal3DP’s printers deliver industry-leading print volume.
- Lead Times and Scalability: Discuss lead times for prototyping and production, as well as their ability to scale up manufacturing to meet future demands.
- Communication and Support: A responsive and communicative service provider is crucial for a smooth and efficient collaboration. Assess their technical support capabilities and their willingness to work closely with your engineering team.
By carefully evaluating these factors, you can select a metal 3D printing service provider that aligns with your aerospace project requirements and ensures the delivery of high-quality, reliable components.
Cost Factors and Lead Time – Understanding the Economics of 3D Printing Aerospace Housings
Understanding the cost drivers and lead times associated with metal 3D printing is essential for aerospace companies to effectively budget and plan their projects. While 3D printing can offer long-term cost savings and reduced lead times in certain scenarios, the initial considerations are crucial.
- Costes de material: Aerospace-grade metal powders, such as Ti-6Al-4V and Ti-6Al-4V ELI, can be expensive. The amount of material used for the part and support structures significantly impacts the overall cost. Design optimization for weight reduction is key to minimizing material costs. Metal3DP offers high-quality metal powders at competitive prices.
- Tiempo de impresión: The build time depends on the part’s size, complexity, and the chosen printing technology. Longer print times translate to higher machine operating costs. Optimizing part orientation and minimizing build volume can help reduce printing time.
- Costes de postprocesamiento: The cost of post-processing steps, such as support removal, heat treatment, machining, and surface finishing, can be substantial and should be factored into the overall cost. Complex geometries often require more extensive post-processing.
- Costes laborales: Skilled technicians are required to operate the 3D printers, perform post-processing, and conduct quality control. Labor costs are part of the overall manufacturing expense.
- Equipment and Maintenance Costs: The cost of the 3D printing equipment and its maintenance are factored into the pricing by service providers.
- Tooling Costs (vs. Traditional Manufacturing): One of the significant advantages of 3D printing is the elimination or reduction of tooling costs associated with traditional methods like injection molding or casting. For low-volume production or complex geometries, this can lead to significant cost savings.
- Plazos de entrega: Lead times for metal 3D printed parts can vary depending on the complexity of the part, the availability of materials, the printing capacity of the service provider, and the required post-processing steps.
- Creación de prototipos: 3D printing offers significantly faster lead times for prototyping compared to traditional methods, allowing for rapid design iteration and testing.
- Producción de bajo volumen: For small to medium production runs, 3D printing can often offer shorter lead times than tooling-dependent processes.
- Producción de gran volumen: For very high volumes, traditional manufacturing methods may still be more cost-effective and offer shorter lead times once tooling is established. However, advancements in 3D printing technology are continuously expanding its scalability.
By carefully analyzing these cost factors and lead time considerations, aerospace companies can make informed decisions about when and how to best utilize metal 3D printing for their vibration isolator housings and other components.
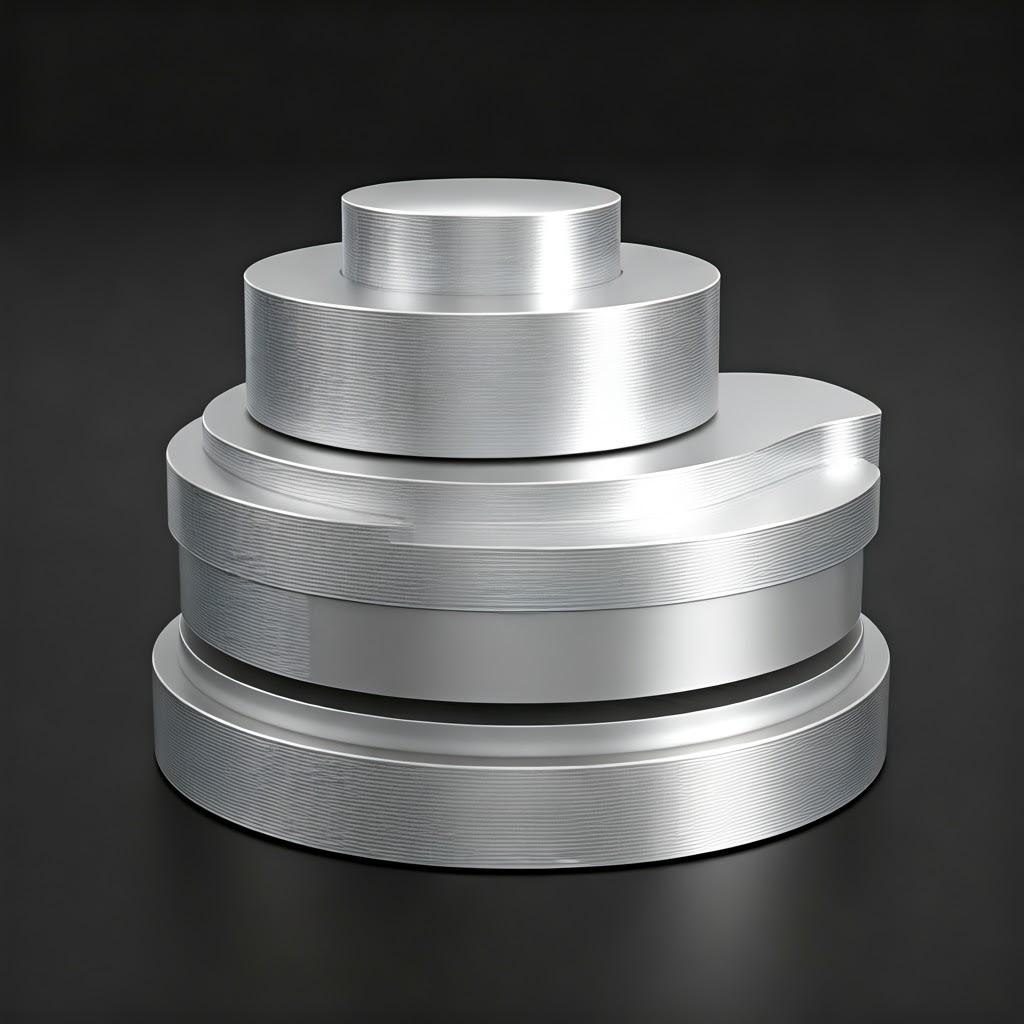
Frequently Asked Questions (FAQ) about 3D Printed Aerospace Vibration Isolator Housings
Here are some frequently asked questions regarding the use of metal 3D printing for aerospace vibration isolator housings:
- Q: Are 3D printed metal parts strong enough for aerospace applications?
- A: Yes, when produced using high-quality metal powders and optimized printing parameters, and subjected to appropriate post-processing, 3D printed metal parts can meet or exceed the strength and durability requirements of many aerospace applications. Alloys like Ti-6Al-4V offer excellent strength-to-weight ratios. Rigorous testing and quality control are essential to ensure the structural integrity of 3D printed aerospace components.
- Q: What is the typical surface finish of a 3D printed metal vibration isolator housing?
- A: The as-built surface finish is typically rougher than that achieved by machining, with Ra values ranging from 5 to 20 $\mu$m. However, various post-processing techniques, such as polishing and machining, can be employed to achieve smoother surface finishes as required by the application.
- Q: Can metal 3D printing be used for mass production of aerospace components?
- A: While traditionally suited for prototyping and low-to-medium volume production, advancements in metal 3D printing technologies, including larger build volumes and faster printing speeds, are increasingly making it viable for higher volume production. The economic feasibility depends on factors such as part complexity, material cost, and post-processing requirements.
- Q: What design considerations are specific to 3D printing aerospace vibration isolator housings?
- A: Key considerations include topology optimization for weight reduction, the use of lattice structures for improved strength-to-weight ratio, feature integration to reduce assembly, careful design of support structures, and consideration of the build orientation to optimize surface finish and minimize material usage.
- Q: How does the cost of 3D printed metal housings compare to traditionally manufactured ones?
- A: The cost-effectiveness of 3D printing depends on factors such as part complexity, production volume, material cost, and the cost of tooling for traditional methods. For complex geometries and low to medium volumes, 3D printing can often be more cost-effective due to the elimination of tooling costs and the potential for material optimization.
Conclusion – The Future of Aerospace Components: Metal 3D Printing and Vibration Isolation
Metal 3D printing is revolutionizing the way aerospace components, including critical vibration isolator housings, are designed and manufactured. The ability to create complex geometries, optimize for weight and performance, and rapidly prototype designs offers significant advantages over traditional manufacturing methods. Materials like Ti-6Al-4V and Ti-6Al-4V ELI, processed using advanced technologies like those offered by Metal3DP, enable the production of high-strength, lightweight, and durable housings that meet the demanding requirements of the aerospace industry.
As the technology continues to mature and material options expand, metal 3D printing will play an increasingly vital role in the aerospace sector, driving innovation, improving efficiency, and enabling the creation of next-generation aircraft and spacecraft. By partnering with experienced providers like Metal3DP, aerospace companies can unlock the full potential of metal additive manufacturing and gain a competitive edge in this dynamic and critical industry. Contact Metal3DP today to explore how our comprehensive metal AM solutions can power your organization’s additive manufacturing goals.
Compartir
MET3DP Technology Co., LTD es un proveedor líder de soluciones de fabricación aditiva con sede en Qingdao, China. Nuestra empresa está especializada en equipos de impresión 3D y polvos metálicos de alto rendimiento para aplicaciones industriales.
Solicite información para obtener el mejor precio y una solución personalizada para su empresa.
Artículos relacionados
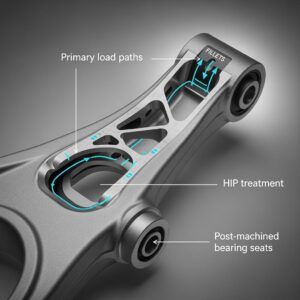
Metal 3D Printing for U.S. Automotive Lightweight Structural Brackets and Suspension Components
Leer Más "Acerca de Met3DP
Actualización reciente
Nuestro producto
CONTACTO
¿Tiene alguna pregunta? ¡Envíenos un mensaje ahora! Atenderemos su solicitud con todo un equipo tras recibir su mensaje.