Comparación entre la tecnología DED y la tecnología WAAM
Índice
Introducción
Gancho: Imagine la creación de objetos metálicos complejos capa a capa, con metal fundido depositado meticulosamente para construir cualquier cosa, desde altísimos componentes de turbinas eólicas hasta intrincados implantes médicos. Este cautivador mundo pertenece a la deposición de energía dirigida (DED) y la fabricación aditiva por arco de alambre (WAAM), dos técnicas revolucionarias de fabricación aditiva (AM) de metales.
Problema: Elegir entre DED y WAAM puede ser una tarea desalentadora. Ambos ofrecen prestaciones impresionantes, pero sus matices pueden influir significativamente en los resultados del proyecto.
Solución: Esta exploración en profundidad diseccionará DED y WAAM, comparando sus aspectos centrales, aplicaciones y adecuación a diversos escenarios.
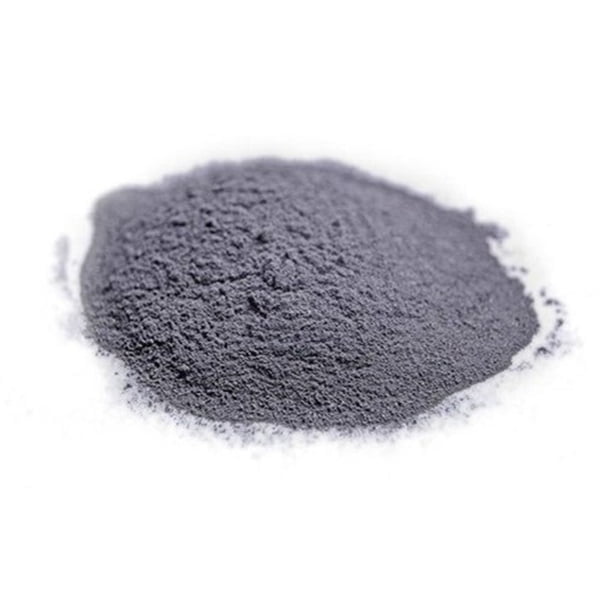
Entender la tecnología DED
Definición: DED es una amplia categoría de procesos de AM que utilizan una fuente de energía concentrada (láser, haz de electrones, arco de plasma) para fundir y fusionar material (normalmente polvo metálico) en una plataforma de construcción, creando un objeto 3D capa a capa.
Fuentes de calor:
DED láser: Los láseres de alta potencia ofrecen un control preciso y una excelente resolución, ideales para geometrías complejas. Los materiales más utilizados son el acero inoxidable, las aleaciones de titanio y el Inconel.
Haz de electrones DED: Genera haces de energía altamente focalizados en una cámara de vacío, lo que permite una profundidad de fusión superior y compatibilidad con metales reactivos como el titanio.
DED por arco de plasma: Utiliza un soplete de plasma para fundir la materia prima, lo que ofrece tasas de deposición más rápidas y rentabilidad para estructuras más grandes, a menudo utilizando hilos de soldadura comunes.
Polvos metálicos para DED:
Polvo metálico | Descripción | Ventajas | Limitaciones |
---|---|---|---|
Acero inoxidable 316L | Acero austenítico versátil conocido por su excelente resistencia a la corrosión, biocompatibilidad y alta resistencia. | Ampliamente utilizado en el sector aeroespacial, implantes médicos y procesamiento químico. | Puede requerir un tratamiento posterior para obtener un acabado superficial óptimo. |
Inconel 625 | Superaleación de níquel-cromo conocida por su resistencia a altas temperaturas, a la oxidación y a la fluencia. | Empleado en aplicaciones aeroespaciales, de turbinas de gas y nucleares exigentes. | Más caros que los aceros comunes. |
Titanio Ti-6Al-4V | Aleación de titanio que ofrece un buen equilibrio entre resistencia, peso y resistencia a la corrosión. | Popular en los sectores aeroespacial, biomédico y de artículos deportivos debido a su biocompatibilidad. | Propensa a la contaminación por oxígeno durante la impresión, lo que requiere una manipulación cuidadosa. |
Aluminio AlSi10Mg | Aleación que combina una buena resistencia con propiedades ligeras y una mejor colabilidad. | Se utiliza en aplicaciones de automoción, aeroespaciales y marinas para reducir el peso. | Altamente reactivo, requiere entornos de gas inerte para la impresión. |
Acero para herramientas H13 | Acero para herramientas para trabajo en caliente conocido por su excelente resistencia al desgaste y resistencia en caliente. | Se emplea para moldes, matrices y punzones utilizados en procesos de conformado y forjado de metales. | Puede ser difícil de imprimir debido a su alto contenido en carbono. |
Aleación de níquel 718 | Aleación de níquel de alta resistencia y endurecimiento por precipitación que ofrece excelentes propiedades mecánicas a temperaturas elevadas. | Se utiliza en componentes aeroespaciales por su solidez y resistencia a la fluencia. | Más caro que otras opciones. |
Cobre | Metal altamente conductor con aplicaciones térmicas y eléctricas. | Se utiliza en conductores eléctricos, intercambiadores de calor y componentes electrónicos. | Propenso a la oxidación durante la impresión, lo que requiere medidas de control. |
Cromo-cobalto (CoCr) | Aleación biocompatible utilizada para implantes médicos resistentes al desgaste. | Se emplea en prótesis de cadera y rodilla por su excelente resistencia al desgaste. | Puede requerir una manipulación especial y un tratamiento posterior para optimizar la biocompatibilidad. |
Inconel 718C | Variación de Inconel 625 con características de fundición y soldabilidad mejoradas. | Se emplea en álabes de turbinas y otras aplicaciones de alta temperatura. | Similar al Inconel 625 en propiedades y limitaciones. |
Aplicaciones de la DED: Componentes aeroespaciales, implantes médicos, reparación de piezas desgastadas, utillaje y estructuras metálicas a gran escala.
Desmitificar WAAM Tecnología
Definición: WAAM, o fabricación aditiva por arco de alambre, es una variante de DED que utiliza un alambre continuo de alimentación y un arco eléctrico (normalmente soldadura por arco metálico con gas) para fundir y depositar el material.
Ventajas:
Rentabilidad: WAAM aprovecha la tecnología de soldadura por arco existente y el alambre fácilmente disponible, lo que lo convierte en una opción más asequible en comparación con los procesos DED basados en polvo.
Altas tasas de deposición: WAAM ofrece velocidades de deposición más rápidas gracias a la alimentación continua del hilo y a la mayor densidad energética del arco, lo que lo hace adecuado para proyectos a gran escala.
Compatibilidad de materiales: WAAM ofrece una amplia compatibilidad de materiales con varios alambres de soldadura comunes, incluidos:
Acero: Acero dulce, grados de acero inoxidable (304L, 316L), acero inoxidable dúplex y aceros para herramientas.
Aluminio: Aleaciones de aluminio como AlSi10Mg y Al 6061.
Aleaciones de níquel: Inconel 625 y aleación de níquel 718.
Otros metales: Cobre, aleaciones de titanio (uso limitado debido a problemas de oxidación).
Aplicaciones de WAAM: Construcción naval, construcción (componentes de puentes, vigas), recipientes a presión a gran escala, reparación de maquinaria pesada y creación rápida de prototipos de grandes estructuras metálicas.
Consideraciones clave: DED frente a WAAM
La velocidad de impresión de la tecnología DED y WAAM La tecnología es diferente
- DED: Ofrece una gama más amplia de velocidades de impresión en función de la fuente de calor y la velocidad de alimentación de polvo. La DED por láser ofrece velocidades más lentas para trabajos de alta precisión, mientras que la DED por arco de plasma logra velocidades más rápidas para construcciones más grandes.
- WAAM: Generalmente presenta las tasas de deposición más rápidas entre los procesos DED gracias a la alimentación continua del hilo y a la mayor densidad de energía del arco.
Los costes de material de la tecnología DED y de la tecnología WAAM son diferentes
- DED: Puede ser más caro, sobre todo para los procesos que utilizan polvos metálicos especializados como el Inconel o metales reactivos como el titanio.
- WAAM: Suele ser más rentable debido al uso de alambres de soldadura fácilmente disponibles y a menudo más baratos.
El acabado superficial de la tecnología DED y la tecnología WAAM es diferente
- DED: El DED por láser ofrece los acabados superficiales más suaves gracias al control preciso del haz láser. La DED por haz de electrones también produce buenos acabados superficiales. El DED por arco de plasma, aunque es más rápido, puede requerir más postprocesado para lograr la calidad superficial deseada.
- WAAM: Generalmente produce acabados superficiales más rugosos en comparación con el DED láser debido a las salpicaduras asociadas al proceso de soldadura por arco. No obstante, las superficies WAAM pueden mecanizarse o rectificarse para obtener los acabados deseados.
Los campos de aplicación son diferentes
- DED: Muy adecuado para componentes intrincados de alta precisión que requieren un excelente acabado superficial, como piezas aeroespaciales, implantes médicos y moldes.
- WAAM: Destaca en estructuras metálicas a gran escala, prototipado rápido de piezas voluminosas, componentes de construcción naval y reparación de maquinaria masiva gracias a sus elevados índices de deposición y rentabilidad.
Costes de equipamiento de la tecnología DED y la tecnología WAAM
- DED: Los sistemas DED, especialmente los que utilizan láser o haces de electrones, suelen ser más caros que las máquinas WAAM debido a la complejidad de la tecnología implicada.
- WAAM: Los sistemas WAAM suelen aprovechar la tecnología de soldadura por arco existente, lo que los convierte en una opción de DED más asequible.
Tabla comparativa de ventajas y limitaciones
Característica | DED | WAAM |
---|---|---|
Fuente de calor | Láser, haz de electrones, arco de plasma | Arco eléctrico (soldadura por arco metálico con gas) |
Materia prima | Polvo metálico | Alambre continuo |
Tasa de deposición | Varía (láser DED: lento, arco de plasma DED: más rápido) | Alta |
Compatibilidad de materiales | Gama más amplia de materiales, incluidos los metales reactivos | Materiales de alambre de soldadura principalmente comunes |
Acabado superficial | Puede ser muy suave (Laser DED) | Generalmente más áspero |
Aplicaciones | Componentes intrincados, implantes médicos, moldes | Estructuras a gran escala, prototipado rápido, reparación |
Coste del equipo | Generalmente superior | Generalmente inferior |
Costo material | Puede ser mayor para polvos especializados | Inferior para alambres de soldadura comunes |
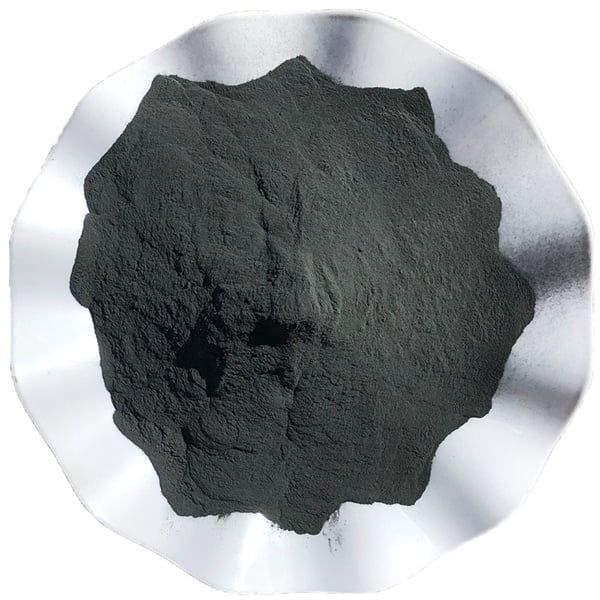
Elegir entre DED y WAAM
La elección óptima entre DED y WAAM depende de los requisitos específicos de su proyecto:
Para piezas complejas con acabados superficiales críticos y una selección de materiales más amplia, el DED (especialmente el DED láser) es probablemente la mejor opción.
Para aplicaciones a gran escala y sensibles a los costes, en las que la velocidad de deposición y la disponibilidad de materiales son prioritarias, WAAM brilla con luz propia.
Consideraciones adicionales:
- Complejidad del proyecto: El DED destaca en geometrías complejas.
- Requisitos materiales: DED ofrece opciones de materiales más amplias, incluidos los metales reactivos.
- Volumen de producción: La velocidad de WAAM es ventajosa para proyectos de gran volumen.
- Presupuesto: La WAAM suele ser más rentable.
Futuro de DED y WAAM
Las tecnologías DED y WAAM evolucionan rápidamente. Podemos esperar avances en:
- Capacidad multimaterial: DED y WAAM pueden integrar funcionalidades para depositar diferentes materiales dentro de la misma construcción para estructuras compuestas.
- Sistemas híbridos DED/WAAM: La combinación de DED y WAAM en una sola máquina podría ofrecer más flexibilidad en la selección de materiales y las tasas de deposición.
- Mayor control y automatización: La mejora de la integración del software y los sensores permitirá un control más preciso del proceso de impresión.
PREGUNTAS FRECUENTES
P: ¿Qué tecnología es más rápida, DED o WAAM?
R: En general, WAAM presenta las tasas de deposición más rápidas entre los procesos DED. La alimentación continua del hilo y la mayor densidad de energía del arco en WAAM permiten una deposición de material más rápida en comparación con DED, en particular los métodos DED basados en polvo. Sin embargo, el DED por láser puede alcanzar velocidades moderadas para trabajos intrincados que requieren gran precisión.
P: ¿Es más caro el DED o el WAAM?
R: WAAM suele ser la opción más rentable. Aquí tienes un desglose:
- Equipamiento: Los sistemas WAAM aprovechan la tecnología de soldadura por arco existente, lo que los hace más asequibles que las máquinas DED, especialmente las que utilizan láser o haces de electrones.
- Material: El DED puede ser más caro si se necesitan polvos metálicos especializados como el Inconel o metales reactivos como el titanio. WAAM utiliza alambres de soldadura fácilmente disponibles y a menudo más baratos.
P: ¿Qué tecnología ofrece un mejor acabado superficial?
R: El DED, especialmente el DED por láser, destaca en la producción de acabados superficiales lisos gracias al control preciso del haz láser. La DED por haz de electrones también da buenos resultados. El DED por arco de plasma, aunque es más rápido, puede requerir más tratamiento posterior para obtener la calidad de superficie deseada. La WAAM suele producir acabados más rugosos que la DED por láser debido a las salpicaduras asociadas al proceso de soldadura por arco. Sin embargo, las superficies WAAM pueden mecanizarse o rectificarse para obtener un acabado más liso.
P: ¿Para qué tipo de piezas son adecuados los sistemas DED y WAAM?
R: El DED y el WAAM responden a distintos ámbitos de aplicación:
- DED: Ideal para componentes intrincados de alta precisión que requieren un excelente acabado superficial, como:
- Piezas aeroespaciales (álabes de turbina, componentes de motor)
- Implantes médicos (prótesis de cadera, prótesis dentales)
- Moldes e insertos para herramientas
- WAAM: Destaca en estructuras metálicas a gran escala y en aplicaciones en las que:
- Las altas tasas de deposición son cruciales (componentes de construcción naval, vigas de puentes)
- Se necesitan prototipos rápidos de piezas voluminosas
- La rentabilidad es una consideración importante (reparación de maquinaria masiva)
P: ¿Es el DED o el WAAM más respetuoso con el medio ambiente?
R: Tanto la DED como la WAAM pueden considerarse respetuosas con el medio ambiente en comparación con las técnicas tradicionales de fabricación sustractiva, como el mecanizado. He aquí por qué:
- Reducción de los residuos materiales: DED y WAAM utilizan procesos aditivos, construyendo piezas capa a capa con un desperdicio mínimo de material en comparación con el mecanizado, que elimina el material sobrante.
- Potencial de reciclaje: Los polvos metálicos utilizados en el DED pueden reciclarse y reutilizarse en futuras construcciones, lo que minimiza el impacto medioambiental.
En conclusión, DED y WAAM son potentes tecnologías de fabricación aditiva de metales con distintos puntos fuertes y aplicaciones. Si conoce sus principios básicos, la compatibilidad de los materiales y su adecuación a los requisitos de los distintos proyectos, podrá decidir con conocimiento de causa qué tecnología se ajusta mejor a sus necesidades. A medida que estas tecnologías sigan evolucionando, podemos esperar capacidades aún mayores y una adopción más amplia en diversas industrias.
Compartir
MET3DP Technology Co., LTD es un proveedor líder de soluciones de fabricación aditiva con sede en Qingdao, China. Nuestra empresa está especializada en equipos de impresión 3D y polvos metálicos de alto rendimiento para aplicaciones industriales.
Solicite información para obtener el mejor precio y una solución personalizada para su empresa.
Artículos relacionados
Acerca de Met3DP
Actualización reciente
Nuestro producto
CONTACTO
¿Tiene alguna pregunta? ¡Envíenos un mensaje ahora! Atenderemos su solicitud con todo un equipo tras recibir su mensaje.