polvo resistente al desgaste
Índice
Imagine un mundo en el que sus engranajes se paran tras un uso mínimo, sus brocas se desafilan después de un solo proyecto y su equipo de minería se rinde tras unos meses de trabajo. Esa es la dura realidad sin los polvos antidesgaste. Estos héroes anónimos actúan como un escudo protector, prolongando la vida útil de los componentes industriales críticos y ahorrando a las empresas mucho tiempo y dinero.
Profundicemos en el mundo del polvos resistentes al desgasteEn este artículo, exploramos su composición, propiedades, aplicaciones y a los campeones en este campo de batalla: los modelos específicos de polvo metálico. Prepárese para una exploración en profundidad.
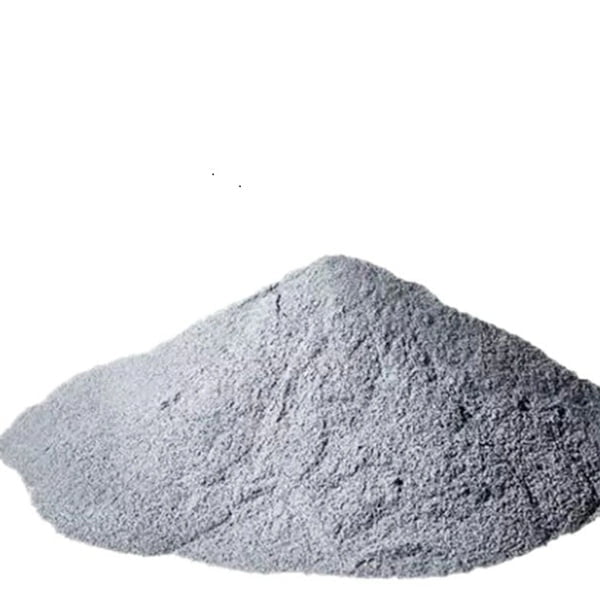
Composición química de los polvos antidesgaste
Los polvos resistentes al desgaste son un grupo diverso, pero normalmente se dividen en dos categorías principales:
- Polvos metálicos: Estos caballos de batalla se componen de varios metales conocidos por su excepcional dureza y durabilidad. Son como pequeñas armaduras para sus componentes. Algunos ejemplos comunes son:
- Carburo de wolframio (WC): Rey indiscutible de la resistencia al desgaste, el WC posee una dureza excepcional, superior incluso a la del diamante en la escala de Mohs. Destaca en entornos de alta fricción y abrasión.
- Carburo de cromo (CrC): Muy similar al WC, el CrC ofrece una excelente resistencia al desgaste y la corrosión. Destaca en aplicaciones con altas temperaturas y oxidación.
- Níquel Cromo (NiCr): Este versátil polvo combina una buena resistencia al desgaste con una excelente resistencia a la corrosión. Es una opción popular para aplicaciones expuestas a productos químicos agresivos y desgaste abrasivo.
- Polvos de acero: Al ofrecer un equilibrio entre asequibilidad y resistencia al desgaste, los polvos de acero se presentan en varios grados, cada uno de ellos adaptado a aplicaciones específicas.
- Polvos cerámicos: Para aplicaciones de alta temperatura, los polvos cerámicos como la alúmina (Al2O3) y la circonia (ZrO2) son los más adecuados. Presentan una estabilidad térmica y una resistencia al desgaste excepcionales, pero pueden ser más frágiles que las opciones metálicas.
Elementos adicionales como el cobalto (Co) o el boro (B) se añaden a menudo a los polvos metálicos para mejorar las propiedades aglutinantes y mejorar la resistencia al desgaste en condiciones específicas.
Las ventajas de Polvos antidesgaste
Entonces, ¿por qué debería considerar la incorporación de polvos resistentes al desgaste en sus procesos industriales? He aquí algunas razones de peso:
- Mayor vida útil de los componentes: Al crear una capa exterior más dura, los polvos resistentes al desgaste reducen significativamente el desgaste de los componentes. Esto se traduce en menos sustituciones, menor tiempo de inactividad y, en última instancia, un importante ahorro de costes. Imagínese una situación en la que un componente de una bomba tradicionalmente tuviera que sustituirse cada trimestre. Al incorporar un revestimiento en polvo resistente al desgaste, podría ampliar su vida útil a un año o más. Se trata de una mejora sustancial tanto en términos de costes de mantenimiento como de eficacia operativa.
- Rendimiento mejorado: Los polvos antidesgaste no sólo protegen los componentes, sino que también pueden mejorar su rendimiento general. Por ejemplo, una broca recubierta con polvo antidesgaste conservará su filo durante más tiempo, lo que se traduce en cortes más limpios y tiempos de perforación más rápidos.
- Versatilidad en todas las aplicaciones: La belleza de los polvos resistentes al desgaste reside en su adaptabilidad. Desde equipos de minería y piezas de automoción hasta herramientas de corte y válvulas, estos polvos encuentran aplicación en un amplio abanico de industrias.
- Mejora de la eficiencia: Al minimizar el desgaste, los polvos resistentes al desgaste contribuyen a mejorar la eficacia general. Menos tiempo de inactividad para sustituciones se traduce en más horas de producción y un flujo de trabajo más fluido.
Desventajas de los polvos antidesgaste
Aunque los polvos resistentes al desgaste ofrecen ventajas innegables, es importante reconocer algunos posibles inconvenientes:
- Costo: Dependiendo del material elegido y del método de aplicación, los recubrimientos en polvo resistentes al desgaste pueden ser más caros que las técnicas tradicionales. Sin embargo, el ahorro a largo plazo gracias a la mayor vida útil de los componentes suele compensar la inversión inicial.
- Experiencia en aplicaciones: La aplicación satisfactoria de polvos resistentes al desgaste suele requerir equipos y conocimientos especializados. Asociarse con una empresa de revestimientos de confianza garantiza unos resultados óptimos.
- Limitaciones materiales: Aunque los polvos resistentes al desgaste son increíblemente resistentes, no son invencibles. Es fundamental elegir el polvo adecuado para cada aplicación y mecanismo de desgaste. Por ejemplo, un polvo cerámico puede ser una buena elección para entornos de altas temperaturas, pero no para cargas de impacto fuertes.
Modelos de polvo metálico para la resistencia al desgaste: Una alineación de campeones
Conozcamos ahora algunos de los principales modelos de polvo metálico que dominan el campo de batalla de la resistencia al desgaste:
1. Carburo de tungsteno (WC): Como ya se ha mencionado, el WC reina en términos de dureza. Es particularmente eficaz contra el desgaste abrasivo y se utiliza comúnmente en:
- Herramientas de corte: Las brocas, plaquitas de fresado y fresas de mango se benefician significativamente de la excepcional resistencia al desgaste del WC.
- Equipos de minería y construcción: Las trituradoras, los equipos de molienda y las placas de desgaste aprovechan la capacidad de WC para resistir entornos difíciles.
- Perforaciones de petróleo y gas: Las herramientas y componentes de fondo de pozo expuestos a presiones extremas y condiciones abrasivas dependen de la resistencia del WC.
2. Carburo de cromo (CrC): Digno competidor del WC, el CrC ofrece una excepcional resistencia al desgaste y a la corrosión. Destaca en aplicaciones con:
- Entornos de alta temperatura: El CrC mantiene su fuerza y resistencia al desgaste incluso a temperaturas elevadas, lo que lo hace ideal para aplicaciones como matrices de estampación en caliente e intercambiadores de calor.
- Resistencia a la oxidación: El CrC forma una capa de óxido estable que protege contra la oxidación y la degradación a altas temperaturas. Esto lo convierte en una opción popular para componentes de hornos y sistemas de escape.
- Equipos de procesamiento de alimentos: La naturaleza no tóxica del CrC y su excelente resistencia al desgaste lo hacen adecuado para su uso en equipos de procesamiento de alimentos, como tornillos y sinfines.
3. Níquel Cromo (NiCr): Este versátil polvo combina una buena resistencia al desgaste con una excelente resistencia a la corrosión. Es una opción popular para aplicaciones expuestas a:
- Productos químicos agresivos: La resistencia del NiCr a diversos productos químicos, incluidos ácidos y álcalis, lo hace adecuado para su uso en bombas, válvulas y tuberías que manipulan fluidos corrosivos.
- Desgaste abrasivo: Aunque no es tan duro como el WC o el CrC, el NiCr ofrece un buen equilibrio entre resistencia al desgaste y asequibilidad. Se utiliza en componentes como engranajes, ruedas dentadas y placas de desgaste deslizantes.
- Entornos de alta humedad: La resistencia a la corrosión del NiCr lo convierte en un valioso activo en aplicaciones expuestas a la humedad, como los equipos marinos y las plantas de tratamiento de aguas residuales.
4. Polvos de acero: Como ya se ha mencionado, el acero en polvo está disponible en varios grados, cada uno de ellos adaptado a las necesidades específicas de resistencia al desgaste. He aquí un desglose de algunas opciones populares:
- Polvos de acero de baja aleación: Ofrecen una solución rentable para aplicaciones de desgaste moderado como engranajes, cojinetes y levas.
- Polvos de acero de aleación media: Aumentan la resistencia al desgaste en comparación con las opciones de baja aleación y son adecuadas para aplicaciones como mandíbulas de trituradoras y revestimientos antidesgaste.
- Polvos de acero de alta aleación: Ofrecen la mayor resistencia al desgaste entre los polvos de acero y se utilizan en aplicaciones exigentes como los medios de molienda y las cuchillas trituradoras.
5. Polvos de superaleación a base de níquel: Para lo último en resistencia al desgaste a altas temperaturas, entran en escena los polvos de superaleaciones con base de níquel. Estos polvos exóticos son especialmente adecuados para:
- Componentes aeroespaciales: Las piezas de los motores de turbina de gas y los trenes de aterrizaje sufren un desgaste y un calor extremos, por lo que los polvos de superaleación a base de níquel son la elección perfecta.
- Equipos de procesamiento químico: Los componentes que manipulan productos químicos altamente corrosivos a temperaturas elevadas se benefician de las excepcionales propiedades de estos polvos.
6. Polvos de estelita: Los polvos de estelita, otro grupo de aleaciones de alto rendimiento a base de cobalto-cromo, ofrecen una excepcional resistencia al desgaste y a la corrosión. Son especialmente útiles para:
- Componentes de la válvula: Los polvos de estelita destacan en aplicaciones como asientos y bolas de válvulas, donde la resistencia al desgaste, la corrosión y las altas temperaturas es crucial.
- Llevar almohadillas y plantillas: Componentes como las almohadillas de desgaste de los mecanismos de alimentación y las tolvas aprovechan la capacidad de los polvos de Stellite para resistir la abrasión y los impactos.
7. Polvos de molibdeno: Aunque no son tan comunes como otras opciones, los polvos de molibdeno ofrecen excelentes propiedades para aplicaciones específicas:
- Entornos de alta temperatura y alta presión: El alto punto de fusión del molibdeno y su buena resistencia al desgaste lo hacen adecuado para componentes de hornos, moldes y matrices.
- Aplicaciones eléctricas: La buena conductividad eléctrica del molibdeno puede ser beneficiosa en aplicaciones como contactos eléctricos y electrodos.
8. Polvos de carburo de boro: Para una combinación única de resistencia al desgaste y baja densidad, entran en juego los polvos de carburo de boro. Son especialmente útiles para:
- Aplicaciones ligeras: Los componentes aeroespaciales y otras aplicaciones sensibles al peso pueden beneficiarse de la capacidad del carburo de boro para ofrecer resistencia al desgaste sin añadir un peso excesivo.
- Aplicaciones de alta velocidad: El bajo coeficiente de fricción del carburo de boro lo convierte en una buena elección para componentes como cojinetes y casquillos que funcionan a altas velocidades.
9. Polvos de carburo de silicio (SiC): El SiC, otra opción cerámica, ofrece una excelente resistencia al desgaste y a las altas temperaturas. Se utiliza en:
- Herramientas de corte: El SiC puede utilizarse en determinadas herramientas de corte para aplicaciones con altas temperaturas y materiales abrasivos.
- Revestimientos de desgaste y tolvas: La capacidad del SiC para resistir la abrasión lo hace adecuado para revestir tolvas y vertederos en diversas industrias.
10. Polvos de carburo de titanio (TiC): Completando nuestra gama, los polvos de TiC ofrecen un buen equilibrio entre resistencia al desgaste, rendimiento a altas temperaturas y resistencia a la corrosión. Se utilizan en:
- Herramientas de corte: El TiC puede utilizarse en determinadas herramientas de corte para aplicaciones que impliquen altas temperaturas y un desgaste abrasivo de moderado a alto.
- Equipos de procesamiento químico: Los componentes que manipulan productos químicos corrosivos a temperaturas elevadas pueden beneficiarse de las propiedades del TiC.
Aplicaciones, especificaciones y más
Una vez explorados los polvos metálicos campeones, profundicemos en los aspectos prácticos de polvos resistentes al desgaste. Descubriremos sus aplicaciones en diversos sectores, junto con especificaciones, comparaciones y algunas preguntas frecuentes.
La versatilidad de los polvos resistentes al desgaste es realmente impresionante. He aquí un vistazo a algunas de las industrias clave que aprovechan sus ventajas:
- Minería y construcción: Trituradoras, equipos de molienda, placas de desgaste, brocas: todos estos componentes sufren un desgaste considerable. Los polvos resistentes al desgaste prolongan significativamente su vida útil, reduciendo los tiempos de inactividad y los costes de mantenimiento en estos exigentes entornos.
- Petróleo y gas: Las herramientas de fondo de pozo, los componentes de perforación y las tuberías se enfrentan a presiones extremas, abrasión y corrosión. Los polvos resistentes al desgaste crean una barrera protectora que garantiza un funcionamiento más suave y una mayor longevidad de los equipos.
- Fabricación: Desde herramientas de corte y matrices hasta engranajes, ruedas dentadas y moldes, los polvos resistentes al desgaste desempeñan un papel crucial en diversos procesos de fabricación. Mejoran la vida útil de las herramientas, reducen las paradas de producción y aumentan la eficiencia general.
- Generación de energía: Los componentes de las centrales eléctricas, como válvulas, bombas y álabes de turbina, están expuestos a altas temperaturas, desgaste y corrosión. Los polvos resistentes al desgaste ofrecen una defensa sólida, garantizando una generación de energía fiable.
- Procesado de alimentos: Los polvos resistentes al desgaste, en particular los que tienen propiedades no tóxicas como el carburo de cromo, pueden utilizarse en equipos de procesamiento de alimentos como tornillos, sinfines y cuchillas mezcladoras. De este modo se salvaguardan la calidad y la higiene de los alimentos y se garantiza la longevidad de los equipos.
Además de en estas industrias principales, los polvos resistentes al desgaste se utilizan en otros sectores, entre ellos:
- Aeroespacial
- Procesado químico
- Fabricación textil
- Producción de papel
- Tratamiento de aguas residuales
Especificaciones y consideraciones: Elegir la pólvora adecuada
La selección del polvo resistente al desgaste más adecuado requiere una cuidadosa consideración de varios factores:
- Material del sustrato: El material del componente que se va a recubrir desempeña un papel crucial. Por ejemplo, un polvo con excelentes propiedades de adherencia para el acero puede no ser ideal para el aluminio.
- Mecanismo de desgaste: Es esencial conocer el mecanismo principal de desgaste: abrasión, impacto, erosión o una combinación de ambos. Los distintos polvos ofrecen diferentes grados de resistencia a mecanismos de desgaste específicos.
- Entorno operativo: La temperatura, la presión y la exposición a productos químicos influyen en la selección del polvo. Por ejemplo, un entorno de altas temperaturas puede requerir un polvo con una estabilidad térmica excepcional.
He aquí una tabla que resume algunas especificaciones clave a tener en cuenta a la hora de elegir el polvo resistente al desgaste:
Especificación | Descripción | Ejemplo |
---|---|---|
Material en polvo | El tipo de metal o cerámica utilizado en el polvo | Carburo de wolframio (WC), carburo de cromo (CrC), níquel-cromo (NiCr) |
Tamaño de las partículas | El tamaño de las partículas individuales de polvo | 5 micras, 10 micras, 50 micras |
Distribución del tamaño de las partículas | La gama de tamaños de partículas dentro del polvo | Distribución estrecha para un recubrimiento uniforme, distribución más amplia para aplicaciones específicas |
Fluidez | La facilidad con la que fluye el polvo | Crucial para una aplicación uniforme durante los procesos de recubrimiento |
Dureza | Resistencia del polvo a la indentación | Medido en la escala Vickers o Rockwell |
Punto de fusión | La temperatura a la que se funde el polvo | Importante para aplicaciones de alta temperatura |
Fichas de datos de seguridad (FDS): Consulte siempre la ficha de datos de seguridad del polvo antidesgaste específico que esté considerando. Este documento proporciona información vital sobre precauciones de seguridad, procedimientos de manipulación y peligros potenciales.
Comparar manzanas con naranjas: Ventajas e inconvenientes
Al evaluar diferentes polvo resistente al desgaste opciones, es útil comparar sus ventajas y limitaciones:
Polvo | Pros | Contras |
---|---|---|
Carburo de wolframio (WC) | Dureza excepcional, excelente resistencia a la abrasión | Coste elevado, relativamente frágil |
Carburo de cromo (CrC) | Buena resistencia al desgaste, rendimiento a altas temperaturas, resistencia a la corrosión | No tan difícil como WC |
Níquel Cromo (NiCr) | Buen equilibrio entre resistencia al desgaste y a la corrosión, rentable | Menor dureza que el WC y el CrC |
Polvo de acero | Asequible, buena para aplicaciones de desgaste moderado | Menor resistencia al desgaste que las opciones de carburo o cerámica |
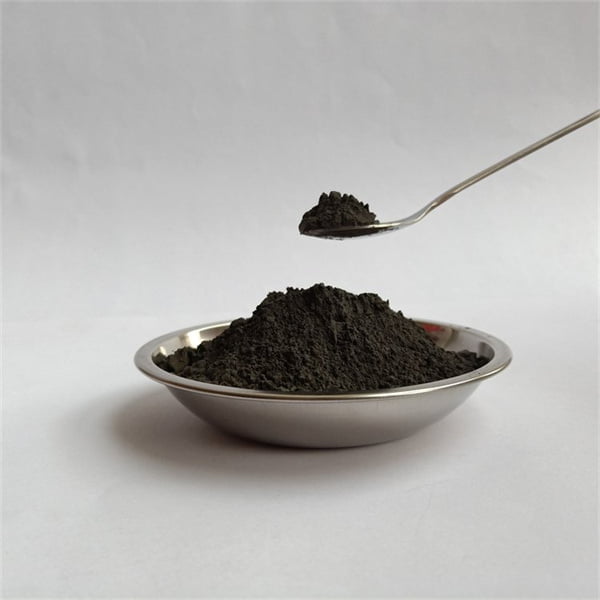
Preguntas frecuentes
¿Qué son los polvos antidesgaste?
Los polvos antidesgaste no son un producto habitual en el comercio. Suelen ser materiales industriales utilizados en revestimientos o procesos de fabricación para mejorar la durabilidad y vida útil de un material o componente. Estos polvos suelen ser muy duros y pueden formularse a partir de cerámicas, metales o incluso materiales compuestos.
¿Cuáles son algunas de las aplicaciones de los polvos resistentes al desgaste?
- Medios de chorreado: Algunos abrasivos de chorreado están formulados a partir de materiales en polvo como el óxido de aluminio o el carburo de silicio para limpiar o texturizar superficies.
- Revestimientos por pulverización térmica: Estos revestimientos se aplican fundiendo polvos resistentes al desgaste y pulverizándolos sobre una superficie. Pueden utilizarse para proteger contra la corrosión, la erosión y el desgaste.
- Fabricación aditiva: Los polvos se utilizan en procesos de impresión 3D para crear piezas resistentes al desgaste.
¿Cuáles son las ventajas de utilizar polvos resistentes al desgaste?
- Mayor durabilidad y vida útil de los componentes
- Mayor resistencia a la abrasión, la corrosión y la erosión
- Puede utilizarse para proteger una gran variedad de materiales
¿Hay algún inconveniente en utilizar polvos resistentes al desgaste?
- Puede ser caro
- Algunos polvos pueden ser difíciles de trabajar
- Puede no ser adecuado para todas las aplicaciones
¿Cuáles son los tipos más comunes de polvos resistentes al desgaste?
- Carburo de tungsteno
- Carburo de cromo
- Oxido de aluminio
- Carburo de silicio
- Óxidos cerámicos (por ejemplo, circonio, titania)
Compartir
MET3DP Technology Co., LTD es un proveedor líder de soluciones de fabricación aditiva con sede en Qingdao, China. Nuestra empresa está especializada en equipos de impresión 3D y polvos metálicos de alto rendimiento para aplicaciones industriales.
Solicite información para obtener el mejor precio y una solución personalizada para su empresa.
Artículos relacionados
Acerca de Met3DP
Actualización reciente
Nuestro producto
CONTACTO
¿Tiene alguna pregunta? ¡Envíenos un mensaje ahora! Atenderemos su solicitud con todo un equipo tras recibir su mensaje.
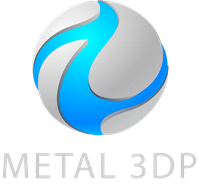
Polvos metálicos para impresión 3D y fabricación aditiva