3D Printed Wing Spar Caps
Índice
Introduction – The Critical Role of Wing Spar Caps and the Advent of Metal 3D Printing
In the demanding realm of aerospace engineering, every component plays a pivotal role in ensuring the safety, performance, and longevity of aircraft. Among these critical elements, the wing spar cap stands out as a primary load-bearing structure within the aircraft wing. These vital components, typically manufactured from high-strength materials, are responsible for withstanding immense bending and shear forces experienced during flight. The integrity of the wing spar cap directly impacts the overall structural stability and aerodynamic efficiency of the aircraft. Traditionally, these complex parts have been produced using conventional manufacturing methods such as machining from solid billets or forging, often involving significant material waste and lengthy production times.
However, a paradigm shift is underway in aerospace manufacturing, driven by the advancements in metal additive manufacturing, commonly known as metal 3D printing. This innovative technology offers unprecedented design freedom, the ability to optimize part weight, and the potential for significant reductions in material waste and lead times. For critical components like wing spar caps, metal 3D printing presents a compelling alternative, enabling the creation of complex geometries tailored for optimal performance while potentially streamlining the supply chain. Companies like Metal3DP Technology Co., LTD, headquartered in Qingdao, China, are at the forefront of this revolution, providing industry-leading metal Impresión 3D equipment and high-performance metal powders specifically designed for demanding applications in aerospace and beyond. Their commitment to accuracy and reliability makes them a trusted partner for producing mission-critical parts. To learn more about Metal3DP, visite su Quiénes somos.
What are 3D Printed Wing Spar Caps Used For?
3D printed wing spar caps serve the same fundamental purpose as their traditionally manufactured counterparts: they are integral to the structural framework of an aircraft wing. Specifically, they are primary components of the main spar, which is the principal spanwise structural member of the wing. The spar caps, located at the top and bottom of the spar web, bear the majority of the bending loads experienced by the wing during flight. These loads arise from lift, gravity, and various aerodynamic forces.
Beyond simply withstanding these forces, 3D printed wing spar caps can be designed with intricate internal structures and optimized geometries that are difficult or impossible to achieve with conventional methods. This allows for:
- Reducción de peso: Through topology optimization and the creation of internal lattices or hollow structures, 3D printing enables the production of spar caps with significantly reduced weight without compromising structural integrity. This is crucial in aerospace, where every kilogram saved translates to improved fuel efficiency and performance.
- Rendimiento mejorado: The design freedom offered by metal 3D printing allows for the integration of features that can improve the aerodynamic performance of the wing or provide better stress distribution within the component.
- Consolidación de piezas: In some cases, 3D printing can facilitate the consolidation of multiple traditionally manufactured parts into a single, more efficient component, reducing assembly time and potential failure points.
- Customization and Complexity: For specialized aircraft or low-volume production, 3D printing offers the flexibility to create highly customized wing spar caps tailored to specific design requirements without the high tooling costs associated with traditional methods.
The versatility and precision of metal 3D printing make it an increasingly attractive option for producing these critical aerospace components. Metal3DP‘s advanced metal powders are specifically engineered to meet the stringent performance requirements of aerospace applications, ensuring the reliability and durability of 3D printed wing spar caps. Explore the range of high-quality metal powders offered by Metal3DP en su Página de producto.
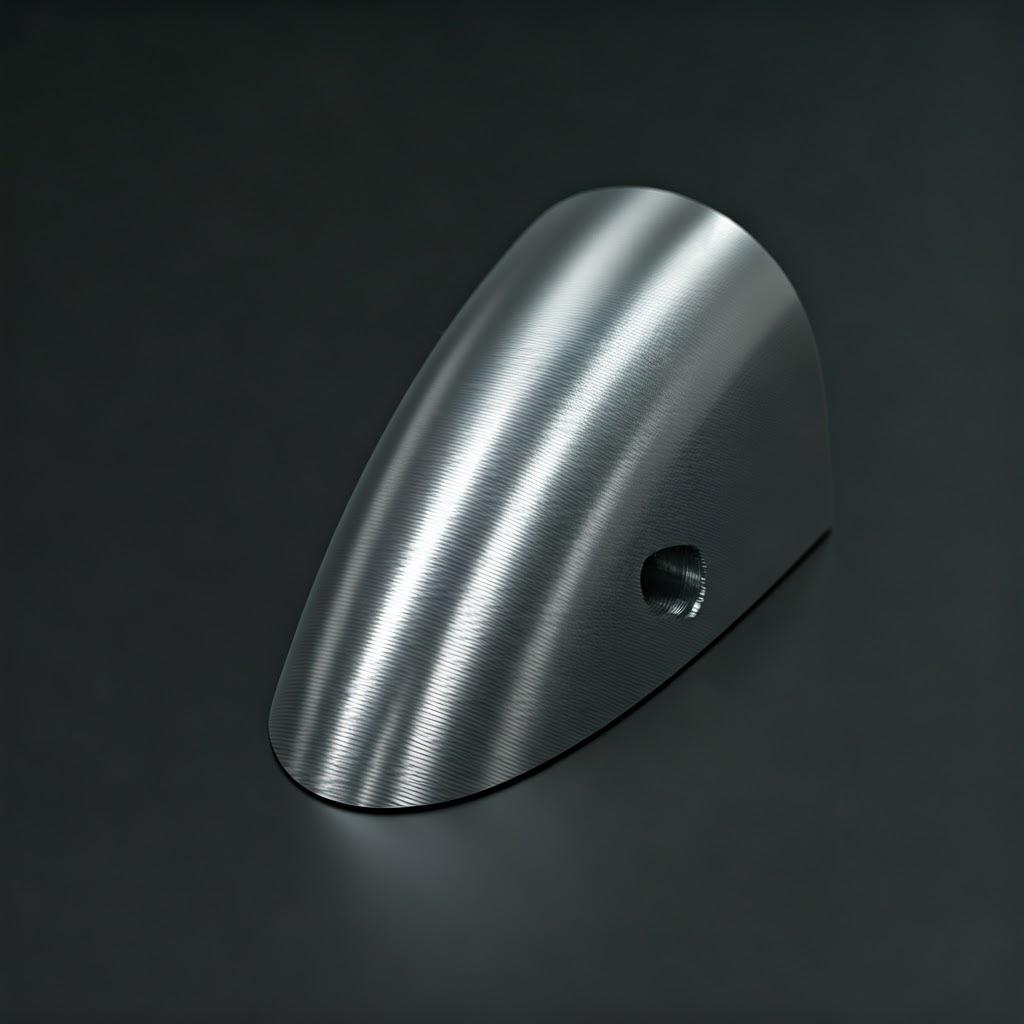
Why Use Metal 3D Printing for Aerospace Wing Spar Caps?
The adoption of metal 3D printing for the production of aerospace wing spar caps offers a multitude of compelling advantages over traditional manufacturing methods:
- Design Freedom and Optimization: Metal 3D printing empowers engineers to create complex geometries that are simply not feasible with subtractive or formative manufacturing processes. This allows for topology optimization, where material is strategically placed only where it is needed for structural integrity, leading to significant weight savings. Lightweighting is paramount in aerospace, directly impacting fuel efficiency, range, and payload capacity.
- Reducción de los residuos materiales: Traditional manufacturing of complex parts like wing spar caps often involves machining away a significant portion of the raw material, resulting in substantial waste. Additive manufacturing, as the name suggests, builds parts layer by layer, using only the necessary material. This leads to a more sustainable and cost-effective production process, especially when using expensive aerospace-grade alloys.
- Plazos de entrega más cortos: The production of tooling required for traditional methods like forging can take weeks or even months. Metal 3D printing bypasses this step, enabling the direct fabrication of parts from digital designs. This significantly reduces lead times, allowing for faster prototyping, design iterations, and potentially quicker delivery of final components. Metal3DP‘s industry-leading print volume and reliability contribute to efficient production schedules.
- Personalización y fabricación bajo demanda: Aerospace often involves low-volume production or the need for highly customized parts for specific aircraft models. Metal 3D printing is ideally suited for this, as it does not incur the high fixed costs associated with tooling, making it economically viable for small production runs and bespoke designs.
- Propiedades del material mejoradas: When using high-quality metal powders and optimized printing parameters, 3D printed parts can exhibit mechanical properties comparable to or even exceeding those of traditionally manufactured components. Metal3DP‘s advanced powder making systems, including gas atomization and PREP technologies, ensure the production of high-sphericity, high-flowability metallic powders that result in dense, high-quality printed parts with superior mechanical properties.
- Integración de características: Additive manufacturing allows for the integration of multiple functionalities into a single part. For example, internal cooling channels or complex internal support structures can be incorporated directly into the wing spar cap during the printing process, reducing the need for secondary assembly operations and improving overall performance.
Considering these significant benefits, it’s clear why metal 3D printing is increasingly being explored and adopted for the production of critical aerospace components like wing spar caps. Understanding the different Métodos de impresión available is crucial for selecting the optimal approach for specific applications.
Recommended Materials for 3D Printed Wing Spar Caps and Why They Matter
The selection of the appropriate metal powder is paramount in achieving the desired performance characteristics for 3D printed aerospace wing spar caps. Two materials stand out as particularly well-suited for this demanding application: Scalmalloy® and AlSi10Mg.
1. Scalmalloy®:
- Composición: Scalmalloy® is a high-strength aluminum-magnesium-scandium alloy specifically developed for additive manufacturing. Its unique composition results in an exceptional strength-to-weight ratio, making it highly desirable for aerospace applications where minimizing weight is critical.
- Key Properties and Benefits:
- Ultraalta resistencia: Scalmalloy® exhibits significantly higher tensile and yield strength compared to conventional aluminum alloys used in aerospace.
- Ligero: Its low density contributes to substantial weight savings in aircraft structures.
- Excelente resistencia a la fatiga: This is crucial for components like wing spar caps that are subjected to cyclic loading during flight.
- Good Weldability and Corrosion Resistance: Important factors for the long-term durability and maintainability of aerospace parts.
- Microestructura fina: Optimized for laser powder bed fusion (LPBF) and electron beam powder bed fusion (EBPBF), resulting in dense, homogeneous parts with consistent properties.
- Why it Matters for Wing Spar Caps: The exceptional strength-to-weight ratio of Scalmalloy® allows for the design of lighter wing spar caps without compromising structural integrity, leading to improved fuel efficiency and aircraft performance. Its excellent fatigue resistance ensures the long-term reliability of this critical component under demanding flight conditions. Metal3DP offers high-quality Scalmalloy® powder optimized for their advanced 3D printing systems.
2. AlSi10Mg:
- Composición: AlSi10Mg is a widely used aluminum alloy in additive manufacturing, known for its good strength, hardness, and dynamic properties. It offers a good balance of performance and cost-effectiveness.
- Key Properties and Benefits:
- Buena resistencia y dureza: Provides sufficient mechanical properties for many aerospace structural applications.
- Excelente conductividad térmica: Can be advantageous in certain wing designs.
- Buena resistencia a la corrosión: Ensures the longevity of the component in various environmental conditions.
- High Processability: Well-suited for laser powder bed fusion (LPBF) processes, offering good printability and consistent results.
- Rentable: Generally more affordable than specialized alloys like Scalmalloy®, making it a viable option for certain applications where the absolute highest strength-to-weight ratio is not the primary requirement.
- Why it Matters for Wing Spar Caps: AlSi10Mg offers a robust and cost-effective alternative for 3D printing wing spar caps, particularly for applications where moderate weight savings and good overall mechanical properties are required. Its excellent processability ensures reliable and consistent production. Metal3DP‘s range of high-quality metal powders includes AlSi10Mg, manufactured with their industry-leading gas atomization technology to ensure high sphericity and flowability.
The choice between Scalmalloy® and AlSi10Mg will depend on the specific performance requirements, budget considerations, and design goals for the 3D printed wing spar caps. Both materials offer significant advantages over traditional alloys when processed using advanced metal 3D printing techniques.
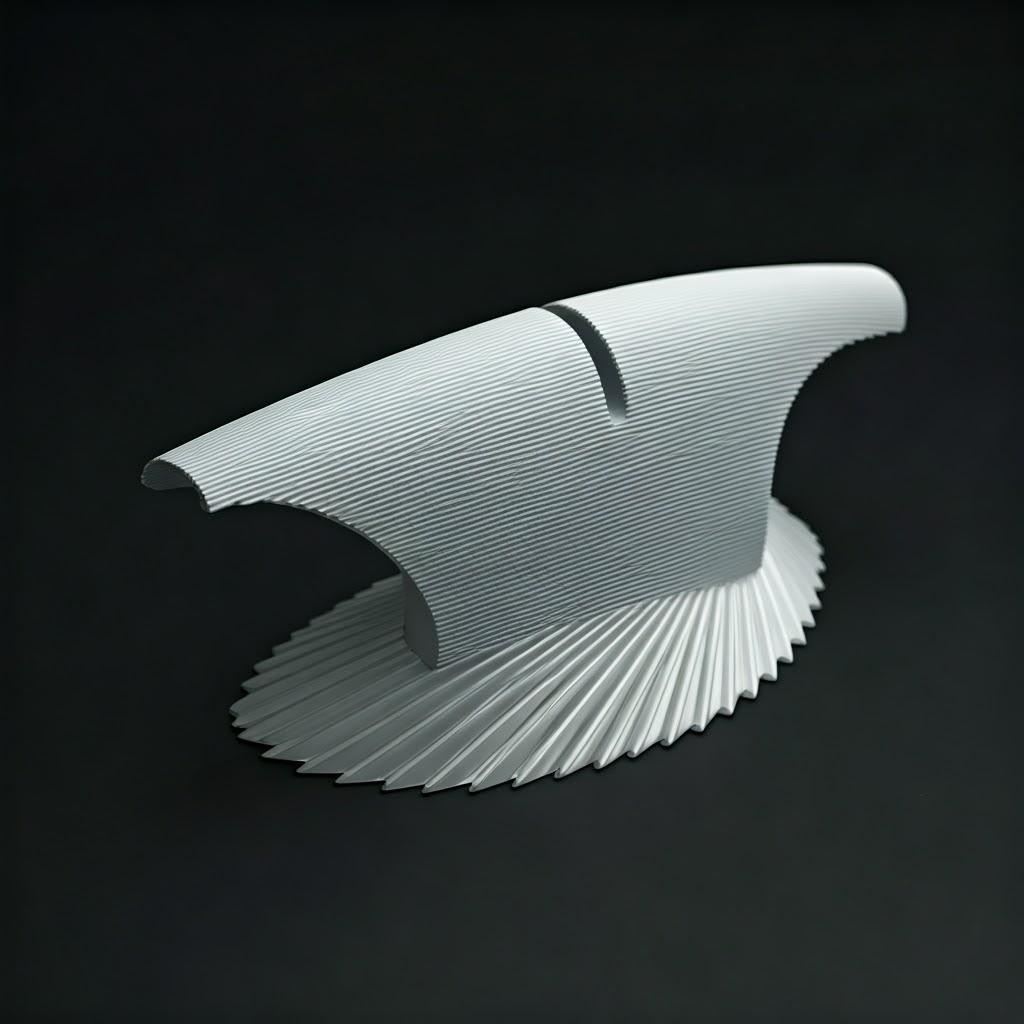
Design Considerations for Additive Manufacturing of Wing Spar Caps
Designing aerospace wing spar caps for metal 3D printing requires a shift in mindset compared to traditional manufacturing. The layer-by-layer additive process offers unique opportunities for optimization but also introduces specific design considerations that engineers must address to ensure structural integrity, printability, and performance.
- Optimización de la topología: One of the most significant advantages of using metal 3D printing is the ability to perform topology optimization. This computational method allows for the removal of material from low-stress areas of the design, resulting in lightweight yet structurally sound parts. For wing spar caps, topology optimization can lead to significant weight reductions, a critical factor in aerospace. Engineers can use specialized software to define load cases and constraints, and the software will then generate an optimized geometry that uses the minimum amount of material required to withstand the applied forces.
- Estructuras reticulares: Internal lattice structures can be incorporated into the design of wing spar caps to further reduce weight while maintaining stiffness. These intricate networks of interconnected struts and nodes can be tailored to provide specific mechanical properties in different areas of the component. The design of the lattice structure, including cell size, strut thickness, and orientation, needs careful consideration based on the anticipated loads.
- Orientation and Support Structures: The orientation of the part during the 3D printing process significantly impacts surface finish, support requirements, and mechanical properties. Careful consideration must be given to orienting the wing spar cap in a way that minimizes the need for support structures, especially in critical areas. Support structures are temporary elements added to the design to prevent overhangs from collapsing during printing and to anchor the part to the build platform. Their removal can sometimes leave surface imperfections, so minimizing their use is often desirable.
- Wall Thickness and Ribbing: Maintaining adequate wall thickness is crucial for the structural integrity of the wing spar cap. However, excessively thick walls can add unnecessary weight. Utilizing internal ribbing or stiffening features can provide the required strength and stiffness with thinner overall walls. These features can be designed with complex geometries that are only achievable through additive manufacturing.
- Integración de características: Metal 3D printing allows for the integration of features such as mounting holes, channels for wiring or fluid transfer, and even sensors directly into the wing spar cap design. This reduces the need for secondary machining operations and can streamline assembly.
- Design for Manufacturing (DFAM): It’s essential to consider the limitations and capabilities of the chosen metal 3D printing process and material right from the initial design stage. Factors such as minimum feature size, achievable tolerances, and potential for warping need to be taken into account. Collaborating with a knowledgeable metal 3D printing service provider like Metal3DP, who possess deep expertise in additive manufacturing processes, can be invaluable in optimizing designs for printability and performance. Their understanding of design rules for their equipment and materials ensures a smoother transition from design to final part.
By carefully considering these design aspects, engineers can leverage the unique capabilities of metal 3D printing to create high-performance, lightweight, and efficient wing spar caps for aerospace applications.
Tolerance, Surface Finish, and Dimensional Accuracy of 3D Printed Wing Spar Caps
In the aerospace industry, precision and reliability are paramount. Therefore, the tolerance, surface finish, and dimensional accuracy achievable with 3D printed wing spar caps are critical considerations. Metal 3D printing technologies have advanced significantly, offering impressive levels of accuracy and surface quality, although these can vary depending on the printing process, material, and post-processing techniques employed.
- Precisión dimensional: Laser Powder Bed Fusion (LPBF) and Electron Beam Powder Bed Fusion (EBPBF), the primary metal 3D printing technologies for high-performance aerospace components, can achieve dimensional accuracies in the range of ±0.1 to ±0.05 mm, or even better in some cases, depending on the size and complexity of the part. This level of precision is often sufficient for many aerospace structural components, including wing spar caps. However, it’s crucial to consider the specific tolerances required for interfaces with other parts and to design accordingly. Factors such as thermal expansion and shrinkage during the printing process can influence final dimensions, and these need to be accounted for in the design and process parameters.
- Tolerancia: Tolerances define the allowable variation in a dimension. Metal 3D printing can achieve tight tolerances, but these are generally wider than those achievable with precision machining. Typical tolerances for LPBF and EBPBF parts range from ±0.1 mm for smaller features to ±0.2 mm or slightly more for larger dimensions. Achieving tighter tolerances may require post-processing steps like CNC machining. When selecting a metal 3D printing service, it’s essential to discuss the achievable tolerances for the specific material and printing process with the provider. Metal3DP‘s commitment to accuracy ensures that they can meet the demanding tolerance requirements of aerospace components.
- Acabado superficial: The surface finish of 3D printed metal parts is typically rougher than that of machined parts due to the layer-by-layer build process and the partially melted powder particles on the surface. The surface roughness (Ra) for as-printed LPBF and EBPBF parts can range from 5 to 20 µm or higher. For aerospace applications, where aerodynamic performance and fatigue resistance are critical, smoother surface finishes may be required. Post-processing techniques such as shot peening, polishing, and machining can be employed to achieve the desired surface finish. The choice of post-processing will depend on the specific requirements of the wing spar cap and the overall application.
Table: Typical Tolerance and Surface Finish for Metal 3D Printing Processes
Proceso | Typical Dimensional Accuracy | Tolerancia típica | As-Printed Surface Roughness (Ra) |
---|---|---|---|
LPBF | ±0.05−0.1 mm | ±0.1−0.2 mm | 5 - 20 µm |
EBPBF | ±0.1−0.2 mm | ±0.2−0.3 mm | 10 – 25 µm |
Exportar a hojas
It’s important for engineers to understand the capabilities and limitations of metal 3D printing in terms of tolerance and surface finish and to incorporate these considerations into their design and material selection process. Specifying appropriate post-processing steps and working with a knowledgeable service provider like Metal3DP are crucial for achieving the required levels of precision and surface quality for aerospace wing spar caps.
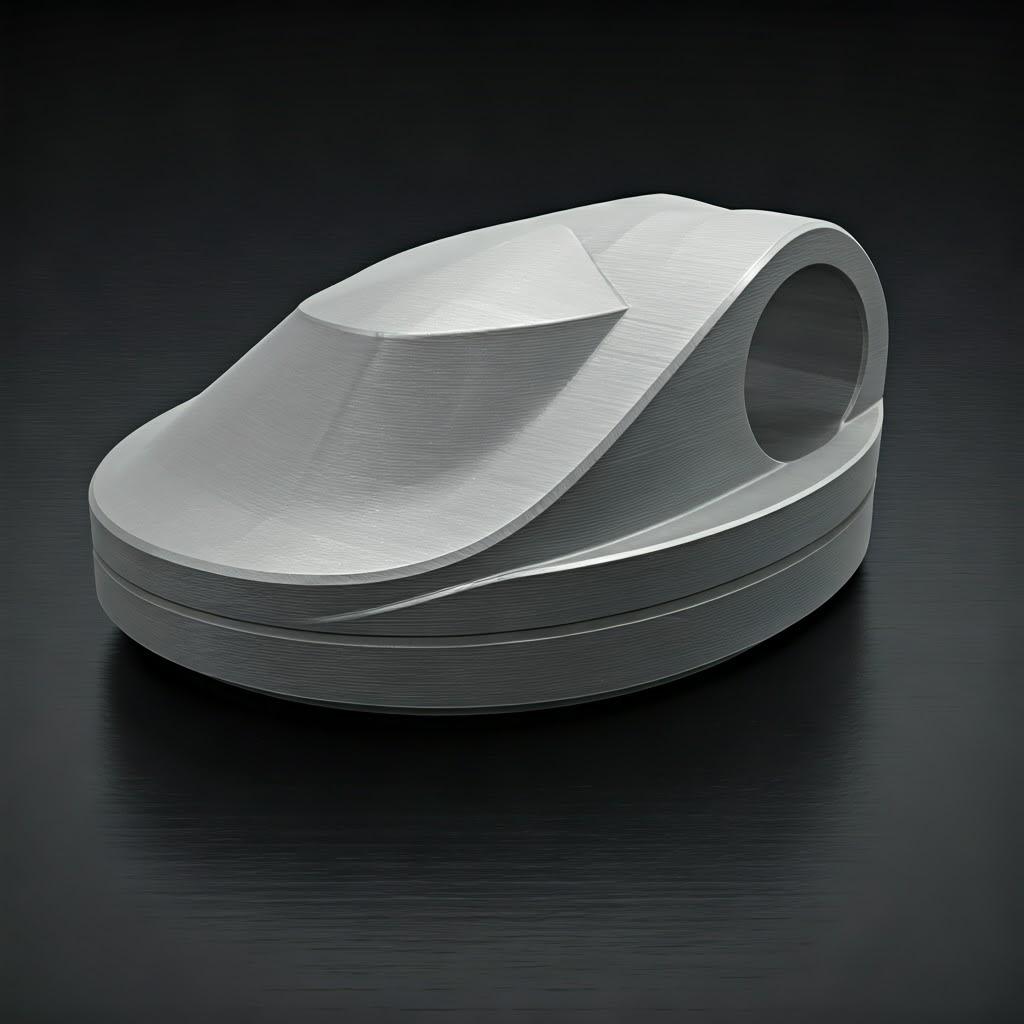
Post-Processing Requirements for 3D Printed Aerospace Wing Spar Caps
While metal 3D printing offers significant advantages in creating complex geometries, post-processing is often necessary to achieve the final desired properties, surface finish, and dimensional accuracy for aerospace wing spar caps. The specific post-processing steps required will depend on the material, printing process, and the intended application.
- Tratamiento térmico antiestrés: Metal 3D printed parts can have residual stresses due to the rapid heating and cooling cycles during the printing process. Stress relief heat treatment is often performed to reduce these internal stresses, which can lead to warping or cracking. The specific temperature and duration of the heat treatment cycle will depend on the alloy being used.
- Prensado isostático en caliente (HIP): HIP is a process that involves subjecting the printed part to high pressure and temperature in an inert gas environment. This process helps to eliminate internal porosity, increase density, and improve the mechanical properties of the material, which is particularly important for critical aerospace components like wing spar caps.
- Retirada de la estructura de soporte: As mentioned earlier, support structures are often required during the printing process to support overhanging features. These structures need to be carefully removed after printing. The method of removal can vary depending on the geometry and the type of support used, ranging from manual removal to machining or chemical dissolution.
- Acabado superficial: To achieve the desired surface finish for aerodynamic performance or fatigue resistance, various post-processing techniques can be employed:
- Granallado: This process involves bombarding the surface with small spherical media to induce compressive stresses, which can improve fatigue life.
- Pulido: Mechanical or chemical polishing can be used to reduce surface roughness.
- Mecanizado (CNC): For critical surfaces that require very tight tolerances or specific surface finishes, CNC machining can be used as a secondary operation.
- Revestimiento: Depending on the application and environmental conditions, coatings may be applied to enhance corrosion resistance, wear resistance, or other properties.
- Ensayos no destructivos (END): Aerospace components often require rigorous quality control and inspection. NDT methods such as ultrasonic testing, radiographic testing, and dye penetrant inspection may be used to ensure the integrity of the 3D printed wing spar caps and to detect any internal flaws.
The selection and execution of post-processing steps are crucial for ensuring that 3D printed aerospace wing spar caps meet the stringent requirements of the industry. It’s essential to work with a metal 3D printing service provider like Metal3DP who have the expertise and capabilities to perform the necessary post-processing operations to the required standards. Their comprehensive solutions encompass not only advanced printing but also the critical post-processing steps needed for high-performance applications.
Common Challenges in 3D Printing Wing Spar Caps and How to Avoid Them
While metal 3D printing offers numerous advantages, there are also potential challenges that need to be addressed to ensure the successful production of high-quality aerospace wing spar caps. Understanding these challenges and implementing appropriate strategies to avoid them is crucial.
- Deformación y distorsión: Residual stresses built up during the rapid heating and cooling cycles of the printing process can lead to warping or distortion of the part, especially for large or complex geometries like wing spar caps.
- How to Avoid: Optimizing part orientation on the build platform, using appropriate support structures, employing stress relief heat treatment after printing, and carefully controlling the printing parameters can help minimize warping.
- Problemas de eliminación de soportes: Removing support structures can sometimes be challenging, especially for intricate internal features. Incomplete removal can leave surface imperfections, while aggressive removal can damage the part.
- How to Avoid: Designing parts with self-supporting geometries where possible, using optimized support structures that are easier to remove, and employing appropriate removal techniques are key.
- Porosidad y densidad: Achieving high density and minimizing porosity are critical for the mechanical properties of aerospace components. Insufficient density or internal voids can compromise the strength and fatigue resistance of the wing spar cap.
- How to Avoid: Selecting high-quality metal powders like those offered by Metal3DP, optimizing printing parameters (laser power, scan speed, layer thickness), and employing post-processing techniques like Hot Isostatic Pressing (HIP) can significantly reduce porosity and increase density.
- Rugosidad superficial: As discussed earlier, the as-printed surface finish of metal 3D printed parts can be rough. This may not be acceptable for aerodynamic surfaces or areas requiring high fatigue performance.
- How to Avoid: Designing with optimal build orientation to minimize stepped surfaces, using finer powder particles, and employing appropriate post-processing techniques like polishing or machining can improve surface finish.
- Material Property Variability: Ensuring consistent material properties throughout the printed part and from one build to another is crucial for aerospace applications. Variations in process parameters or powder quality can lead to inconsistencies.
- How to Avoid: Working with a reputable metal powder supplier like Metal3DP who have stringent quality control processes, carefully calibrating and maintaining the 3D printing equipment, and establishing robust process control procedures are essential.
- Cost and Scalability: While metal 3D printing can be cost-effective for low to medium volumes and complex parts, the cost per part can be higher than traditional methods for very high volumes. Scalability can also be a challenge for very large production runs.
- How to Avoid: Carefully evaluating the overall lifecycle cost, considering factors like tooling, material waste, and lead time. For scalability, working with a printing service provider with multiple machines and robust production capabilities is important.
By proactively addressing these potential challenges through careful design, process optimization, and collaboration with experienced partners like Metal3DP, aerospace manufacturers can successfully leverage the benefits of metal 3D printing for critical components like wing spar caps.
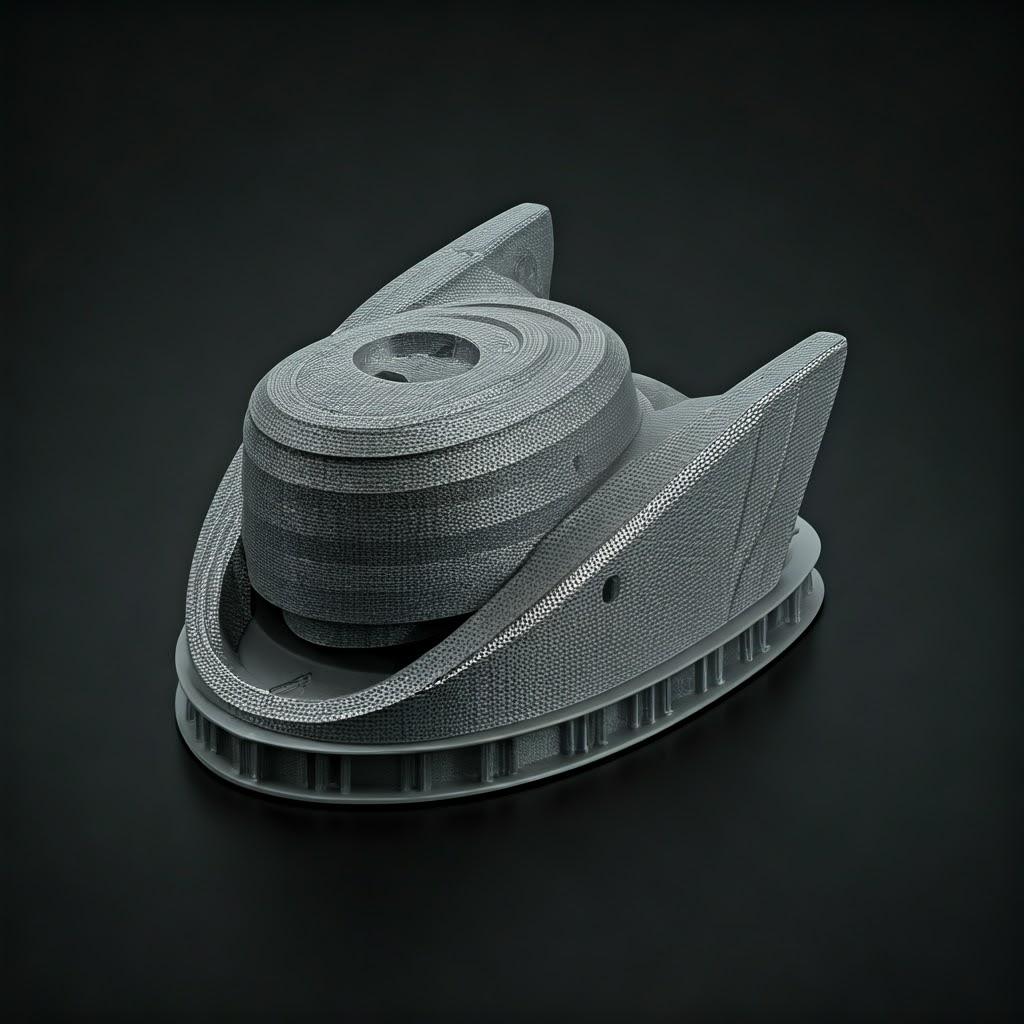
Cómo elegir el proveedor de servicios de impresión 3D sobre metal adecuado para componentes aeroespaciales
Selecting the right metal 3D printing service provider is a critical decision for aerospace companies looking to leverage this advanced manufacturing technology for components like wing spar caps. Given the stringent quality and safety requirements of the aerospace industry, it’s essential to partner with a provider that possesses the necessary expertise, certifications, and capabilities. Here are key factors to consider:
- Industry Experience and Certifications: Look for a provider with a proven track record in serving the aerospace industry. Relevant certifications such as AS9100 (the quality management system standard for the aerospace industry) are crucial indicators of a provider’s commitment to quality and compliance. Metal3DP‘s dedication to accuracy and reliability positions them as a trustworthy partner for mission-critical aerospace parts.
- Capacidades de los materiales: Ensure the service provider has experience working with the specific aerospace-grade alloys required for your application, such as Scalmalloy® and AlSi10Mg. They should also have a deep understanding of the material properties and the optimal printing parameters for these alloys. Metal3DP manufactures a wide range of high-quality metal powders optimized for laser and electron beam powder bed fusion, including innovative alloys suitable for aerospace.
- Printing Technology and Equipment: The type of metal 3D printing technology (e.g., LPBF, EBPBF) and the quality of the equipment used by the service provider will impact the accuracy, surface finish, and mechanical properties of the printed parts. Industry-leading print volume, accuracy, and reliability are hallmarks of Metal3DP‘s printing solutions. You can explore their capabilities further on their Página de impresión 3D en metal.
- Capacidades de postprocesado: As discussed earlier, post-processing is often essential for aerospace components. The service provider should have in-house or access to reliable partners for critical processes such as heat treatment, HIP, surface finishing, and NDT.
- Design and Engineering Support: A strong service provider will offer design and engineering support to help optimize parts for additive manufacturing, ensuring printability and performance. Their expertise in DFAM can be invaluable in achieving the best results. Metal3DP provides comprehensive solutions spanning SEBM printers, advanced metal powders, and application development services, demonstrating their commitment to supporting customers throughout the entire process.
- Control de Calidad e Inspección: Robust quality control procedures and inspection processes are non-negotiable for aerospace components. The provider should have established protocols for ensuring the dimensional accuracy, material integrity, and overall quality of the printed parts.
- Lead Times and Production Capacity: Understand the service provider’s lead times and production capacity to ensure they can meet your project timelines and volume requirements.
- Comunicación y Colaboración: Effective communication and a collaborative approach are essential for a successful partnership. Choose a provider that is responsive, transparent, and willing to work closely with your team.
By carefully evaluating these factors, aerospace companies can select a metal 3D printing service provider that can reliably produce high-quality wing spar caps and other critical components that meet the stringent demands of the industry.
Cost Factors and Lead Time for 3D Printed Wing Spar Caps
Understanding the cost and lead time associated with 3D printed aerospace wing spar caps is crucial for budgeting and project planning. These factors can vary significantly depending on several parameters:
- Costes de material: The cost of the metal powder is a significant factor. Aerospace-grade alloys like Scalmalloy® tend to be more expensive than standard alloys like AlSi10Mg. The quantity of material required for the part, which is influenced by the design and any support structures, will also impact the overall material cost.
- Tiempo de impresión: The build time on the 3D printer is a key cost driver. Larger parts, more complex geometries, and denser builds will take longer to print, increasing machine time costs.
- Costes de postprocesamiento: The extent and complexity of required post-processing steps will add to the overall cost. Processes like HIP, CNC machining, and specialized coatings can be significant cost factors.
- Costes de diseño e ingeniería: If you require assistance with design optimization for additive manufacturing, this will incur additional costs. However, the long-term benefits of a well-optimized design can outweigh these initial costs.
- Volumen de producción: The cost per part generally decreases as the production volume increases, although metal 3D printing is often most cost-effective for low to medium volumes compared to traditional methods.
- Service Provider Costs: Different service providers will have different pricing structures based on their equipment, expertise, and overhead costs. Obtaining quotes from multiple reputable providers like Metal3DP is advisable to get a clear understanding of the market rates.
Plazo de entrega:
The lead time for 3D printed wing spar caps is typically shorter than that for traditionally manufactured parts, especially for complex geometries that would require extensive tooling. However, the exact lead time will depend on:
- Complejidad y tamaño de la pieza: More complex and larger parts will generally take longer to print.
- Disponibilidad de material: The lead time for acquiring the specific metal powder can vary. Metal3DP‘s in-house powder manufacturing capabilities can potentially reduce material lead times.
- Printing Queue: The service provider’s current workload and the availability of their printing equipment will affect the lead time.
- Requisitos de postprocesamiento: Extensive post-processing will add to the overall lead time.
- Control de Calidad e Inspección: Thorough inspection processes can also impact the final delivery time.
While it’s difficult to provide exact figures without specific part details, metal 3D printing can often reduce the lead time for aerospace components from months (associated with tooling for traditional methods) to weeks or even days, depending on the factors mentioned above. Engaging with Metal3DP to discuss your specific requirements will provide a more accurate estimate of both cost and lead time.
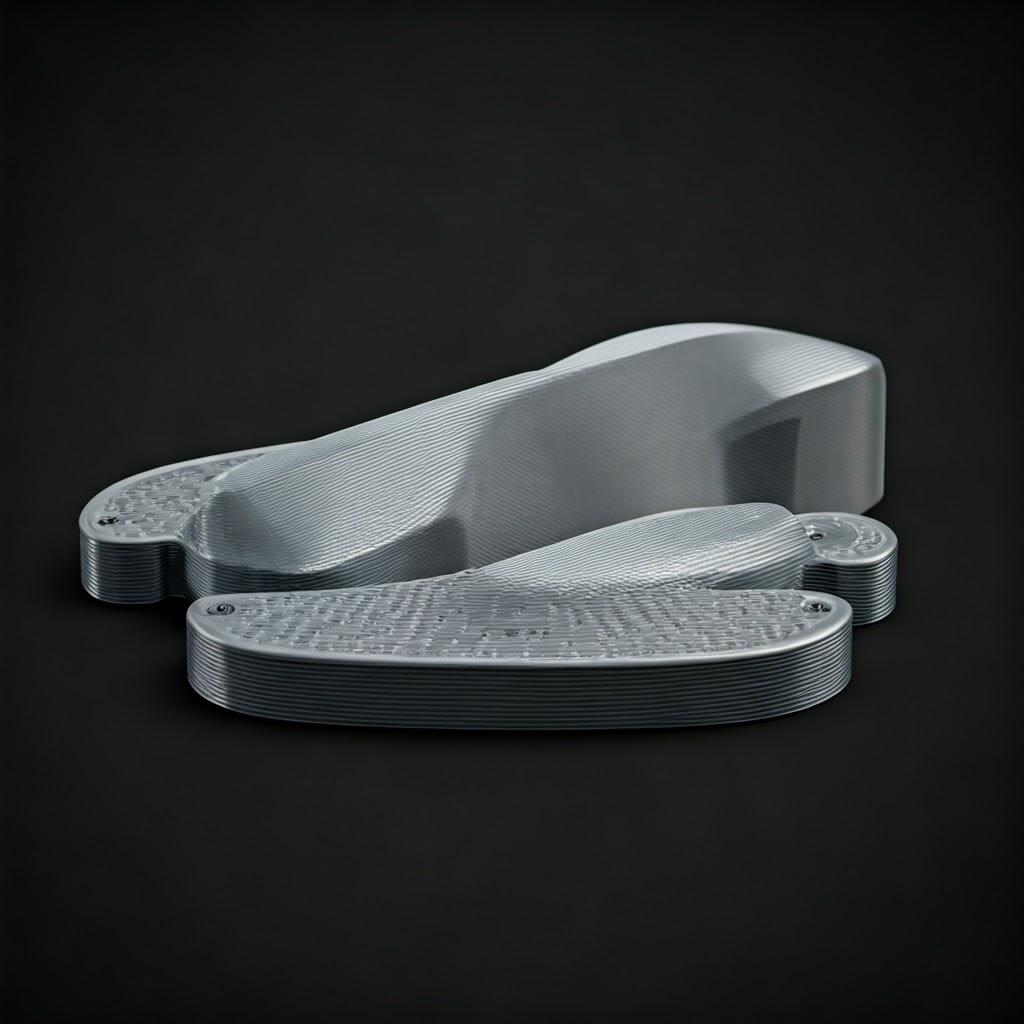
Frequently Asked Questions (FAQ) about 3D Printed Aerospace Wing Spar Caps
Here are some common questions engineers and procurement managers have regarding the use of metal 3D printing for aerospace wing spar caps:
- Q: Are 3D printed metal parts strong enough for aerospace applications?
- A: Yes, when using high-quality metal powders and optimized printing parameters, 3D printed metal parts can achieve mechanical properties comparable to or even exceeding those of traditionally manufactured components. Alloys like Scalmalloy®, specifically designed for additive manufacturing, offer exceptional strength-to-weight ratios suitable for demanding aerospace applications. Metal3DP‘s advanced powder making system ensures the production of high-performance materials for robust parts.
- Q: What is the typical lifespan of a 3D printed metal wing spar cap?
- A: The lifespan of a 3D printed metal wing spar cap depends on factors such as the material used, the design, the manufacturing process, and the operational environment. When manufactured using aerospace-grade alloys and adhering to stringent quality control standards, 3D printed metal parts can meet the long-term durability requirements of aerospace applications.
- Q: Can metal 3D printing be used for mass production of aerospace parts?
- A: While metal 3D printing is often most cost-effective for low to medium volumes and complex parts, advancements in technology and automation are making it increasingly viable for higher production volumes. For very large production runs, hybrid manufacturing approaches combining 3D printing with traditional methods may also be considered.
- Q: How does the cost of 3D printed wing spar caps compare to traditionally manufactured ones?
- A: The cost comparison depends on factors such as part complexity, material, production volume, and tooling costs associated with traditional methods. For complex geometries and low to medium volumes, 3D printing can often be more cost-effective due to reduced material waste and the elimination of tooling. For very high volumes of simpler parts, traditional methods may still be more economical. A thorough cost analysis considering all factors is essential.
- Q: What non-destructive testing methods are used to ensure the quality of 3D printed aerospace parts?
- A: Common NDT methods used for 3D printed aerospace parts include ultrasonic testing, radiographic testing (X-ray), dye penetrant inspection, and magnetic particle inspection. These methods help to detect internal flaws and ensure the structural integrity of the components.
Conclusion – Embracing the Future of Aerospace Manufacturing with Metal 3D Printed Wing Spar Caps
Metal 3D printing is rapidly transforming the landscape of aerospace manufacturing, offering unprecedented opportunities for innovation, efficiency, and performance. The application of this technology to critical structural components like wing spar caps demonstrates its potential to deliver lighter, stronger, and more complex parts with reduced material waste and lead times.
Empresas como Metal3DP Technology Co., LTD are at the forefront of this revolution, providing the advanced metal 3D printing equipment, high-performance metal powders, and application expertise necessary to drive the adoption of additive manufacturing in the aerospace industry. Their commitment to quality, accuracy, and innovation makes them a valuable partner for aerospace companies looking to embrace the future of manufacturing.
By understanding the design considerations, material options, post-processing requirements, and potential challenges associated with 3D printed wing spar caps, aerospace engineers and procurement managers can make informed decisions and leverage the transformative power of metal additive manufacturing to achieve their goals. As the technology continues to evolve, we can expect to see even wider adoption of 3D printed metal components in the skies, paving the way for more efficient, sustainable, and high-performing aircraft. Contact Metal3DP today to explore how their capabilities can power your organization’s additive manufacturing goals. You can find more information on their website at https://met3dp.com/.
Compartir
MET3DP Technology Co., LTD es un proveedor líder de soluciones de fabricación aditiva con sede en Qingdao, China. Nuestra empresa está especializada en equipos de impresión 3D y polvos metálicos de alto rendimiento para aplicaciones industriales.
Solicite información para obtener el mejor precio y una solución personalizada para su empresa.
Artículos relacionados
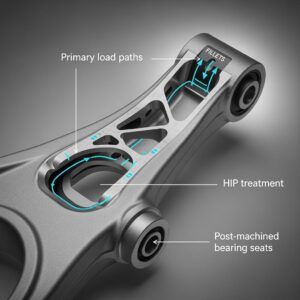
Metal 3D Printing for U.S. Automotive Lightweight Structural Brackets and Suspension Components
Leer Más "Acerca de Met3DP
Actualización reciente
Nuestro producto
CONTACTO
¿Tiene alguna pregunta? ¡Envíenos un mensaje ahora! Atenderemos su solicitud con todo un equipo tras recibir su mensaje.