Introducción a la fabricación aditiva por arco de alambre
Índice
Imagine construir grandes y robustas piezas metálicas capa a capa, no mediante técnicas de fabricación sustractivas como el mecanizado, sino añadiendo material meticulosamente. Esta tecnología transformadora es Fabricación aditiva por arco de alambre (WAAM), preparada para remodelar la forma en que creamos componentes críticos en diversas industrias.
Principio de funcionamiento de la fabricación aditiva por arco de alambre
WAAM, también conocida como deposición de energía dirigida por arco (DED-Arc), se engloba dentro de las tecnologías de impresión 3D de deposición directa de energía (DED). Aprovecha un arco eléctrico controlado como fuente de calor para fundir alambre metálico consumible. A continuación, este metal fundido se deposita meticulosamente, capa sobre capa, para construir la estructura 3D deseada.
Es como un proceso de soldadura de alta tecnología con esteroides. En lugar de limitarse a unir piezas existentes, WAAM crea objetos completamente nuevos desde cero. Un brazo robótico maneja con precisión el alambre y el soplete, siguiendo un plano digital preprogramado. A medida que cada capa se solidifica, una nueva se deposita encima, dando vida gradualmente al diseño digital.
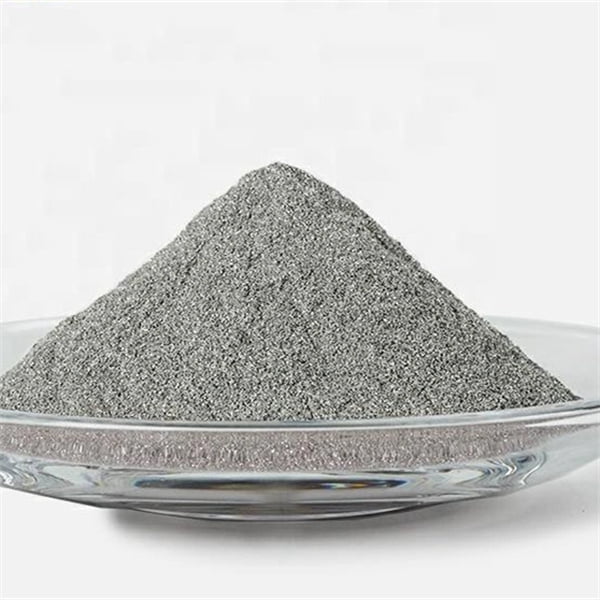
Características del proceso de Fabricación aditiva por arco de alambre
WAAM ofrece varias ventajas claras sobre los métodos de fabricación tradicionales:
- Alta tasa de deposición: En comparación con las técnicas de impresión 3D de metales basadas en polvo, WAAM presenta tasas de deposición significativamente más rápidas. Esto se traduce en tiempos de producción más rápidos, especialmente para componentes a gran escala.
- Eficiencia del material: WAAM utiliza alambre como materia prima, lo que minimiza el desperdicio de material en comparación con los procesos de fabricación sustractivos que retiran el material sobrante de un bloque sólido.
- Impresión a gran escala: WAAM destaca en la creación de estructuras metálicas grandes y complejas. A diferencia de otros métodos basados en polvo y limitados por el tamaño de la cámara de construcción, los sistemas WAAM pueden funcionar en entornos abiertos, lo que permite fabricar objetos de gran tamaño.
- Versatilidad de materiales: WAAM es compatible con una amplia gama de aleaciones metálicas, como aceros, aluminio, aleaciones de níquel y titanio. Este amplio espectro de materiales satisface diversas aplicaciones que requieren propiedades mecánicas específicas.
Sin embargo, WAAM también tiene limitaciones que hay que tener en cuenta:
- Acabado superficial: El proceso de deposición de metal fundido en WAAM puede dar lugar a un acabado superficial más rugoso en comparación con algunos métodos basados en polvo. Dependiendo de la aplicación, pueden ser necesarias técnicas de postprocesado como el rectificado o el mecanizado para conseguir una superficie más lisa.
- Tensión residual: Los rápidos ciclos de calentamiento y enfriamiento inherentes al WAAM pueden introducir tensiones residuales en la pieza impresa. Esto debe abordarse mediante un tratamiento térmico adecuado o consideraciones de diseño para garantizar la estabilidad dimensional y evitar posibles grietas.
- Precisión: Aunque la tecnología WAAM ofrece una resolución impresionante, puede que no alcance el nivel de detalle que se consigue con determinadas técnicas basadas en polvo. La elección depende de las tolerancias dimensionales de la pieza y de los requisitos de complejidad.
Polvos metálicos para Fabricación aditiva por arco de alambre
Aunque la WAAM utiliza alambre continuo como materia prima, es fundamental conocer las propiedades de los polvos metálicos correspondientes utilizados para crear estos alambres. He aquí un desglose de algunos de los polvos metálicos más utilizados en WAAM:
Material | Composición | Propiedades | Aplicaciones |
---|---|---|---|
Acero bajo en carbono (SAE 1005, AISI 1008) | Fe (hierro) con un contenido mínimo de carbono | Alta ductilidad, buena soldabilidad, excelente maquinabilidad | Componentes estructurales de uso general, soportes, armarios |
Acero de alta resistencia y baja aleación (ASTM A514) | Fe con mayor contenido de carbono y elementos de microaleación como manganeso, vanadio y niobio. | Mejor relación resistencia/peso, buena tenacidad | Equipos de construcción, componentes de transporte, recipientes a presión |
Acero inoxidable (304L, 316L) | Fe con cromo, níquel y molibdeno para mayor resistencia a la corrosión | Excelente resistencia a la corrosión, buena conformabilidad | Equipos de procesamiento de alimentos, dispositivos médicos, tanques de procesamiento químico |
Aluminio (AA 5356, AA 6061) | Al (aluminio) con magnesio para aumentar la resistencia | Elevada relación resistencia/peso, buena resistencia a la corrosión | Componentes aeroespaciales, piezas de automoción, aplicaciones marinas |
Aleaciones de níquel (Inconel 625, Inconel 718) | Ni (níquel) con cromo, molibdeno y otros elementos para altas temperaturas | Excepcional solidez y resistencia a la oxidación a temperaturas elevadas | Componentes de turbinas de gas, intercambiadores de calor, recipientes a presión para entornos difíciles |
Titanio (Ti-6Al-4V) | Ti (titanio) con aluminio y vanadio para aumentar la resistencia | Elevada relación resistencia/peso, excelente biocompatibilidad | Componentes aeroespaciales, implantes biomédicos, artículos deportivos |
Esta tabla proporciona una visión de los diversos polvos metálicos utilizados en la materia prima del alambre WAAM. La selección del material específico depende de las propiedades mecánicas deseadas, la resistencia a la corrosión y los requisitos de la aplicación.
Consideraciones adicionales:
- Diámetro del alambre: El diámetro del alambre de alimentación desempeña un papel fundamental en la WAAM. Los alambres más gruesos permiten velocidades de deposición más rápidas, pero pueden dar lugar a un acabado superficial más rugoso. Por el contrario, los alambres más finos ofrecen detalles más precisos, pero los tiempos de fabricación son más lentos. El diámetro óptimo depende del equilibrio deseado entre velocidad de construcción, resolución y necesidades de postprocesado.
- Calidad de la materia prima: Un diámetro de hilo constante, unos defectos superficiales mínimos y una composición química adecuada son esenciales para el éxito de la impresión WAAM. Un alambre de alta calidad garantiza una deposición uniforme, minimiza las salpicaduras (gotas de metal fundido expulsadas durante la soldadura) y permite predecir las propiedades mecánicas de la pieza acabada.
Las tendencias de desarrollo de Fabricación aditiva por arco de alambre
La tecnología WAAM evoluciona rápidamente. Estas son algunas de las tendencias que configuran su futuro:
- Sistemas WAAM híbridos: La integración de WAAM con otras técnicas de fabricación aditiva, como la fusión de lecho de polvo, está ganando adeptos. Esto permite combinar las ventajas de la alta velocidad de deposición de WAAM para piezas de gran tamaño con la mayor precisión de los métodos basados en polvo para detalles intrincados.
- Sistemas de automatización y control: Los avances en los sistemas de automatización y control están mejorando la estabilidad y repetibilidad de los procesos de WAAM. Esto incluye avances en la supervisión en tiempo real, la integración de sensores y los ajustes automatizados del proceso, lo que conduce a una producción de piezas más consistente y fiable.
- Desarrollo del material: Se están explorando nuevas aleaciones metálicas y materiales compuestos específicamente adaptados a la WAAM. Esto abre las puertas a la creación de componentes con propiedades mecánicas aún mejores, rendimiento a altas temperaturas y funcionalidades a medida.
Estos avances allanan el camino para que WAAM se convierta en una herramienta aún más versátil y potente en diversos sectores.
Aplicaciones de la fabricación aditiva por arco de alambre
Las capacidades únicas de WAAM lo convierten en una opción convincente para una amplia gama de aplicaciones, entre las que se incluyen:
- Aeroespacial: Fabricación de componentes estructurales grandes y ligeros para aviones y naves espaciales, aprovechando la capacidad de WAAM para manipular aleaciones de aluminio y titanio de alta resistencia.
- Automóvil: Creación de componentes complejos del motor, soportes personalizados y piezas ligeras del chasis, aprovechando la velocidad y la eficiencia de los materiales de WAAM.
- Petróleo y gas: Impresión de intrincados sistemas de tuberías, recipientes a presión y piezas de reparación para entornos difíciles, donde entran en juego la versatilidad de los materiales de WAAM y su capacidad para manejar estructuras de paredes gruesas.
- Construcción: Construcción de elementos arquitectónicos personalizados, puentes y componentes a gran escala in situ, donde la capacidad de WAAM para operar en entornos abiertos es ventajosa.
- Construcción naval: Fabricación de robustos componentes para buques, hélices y piezas de reparación, beneficiándose de la idoneidad de WAAM para trabajar con grandes estructuras de acero.
- Productos sanitarios: Creación de prótesis, implantes e instrumentos quirúrgicos personalizados con materiales biocompatibles como el titanio, aprovechando la capacidad de WAAM para producir geometrías complejas.
Estos son sólo algunos ejemplos, y a medida que la tecnología WAAM siga madurando, se espera que su ámbito de aplicación se amplíe aún más.
Ventajas y limitaciones de Fabricación aditiva por arco de alambre
Ventajas:
- Alta tasa de deposición: Permite tiempos de producción más rápidos, especialmente para componentes a gran escala.
- Eficiencia del material: Minimiza los residuos en comparación con la fabricación sustractiva.
- Impresión a gran escala: Ideal para crear estructuras metálicas grandes y complejas.
- Versatilidad de materiales: Compatible con una amplia gama de aleaciones metálicas.
- Rentabilidad: Puede ser una opción competitiva en costes para determinadas aplicaciones en comparación con los métodos de fabricación tradicionales.
Limitaciones:
- Acabado superficial: Puede requerir un tratamiento posterior para un acabado liso.
- Tensión residual: Requiere tratamiento térmico o consideraciones de diseño para su gestión.
- Precisión: Puede que no se consigan los detalles finos de algunas técnicas basadas en polvo.
- Entorno de construcción limitado: Los sistemas al aire libre pueden ser susceptibles a factores ambientales como el viento.
A la hora de determinar si la tecnología WAAM es la más adecuada para una aplicación concreta, es fundamental considerar detenidamente tanto las ventajas como las limitaciones.
Comparación de WAAM con otras técnicas de fabricación aditiva de metales
WAAM no es el único participante en el juego de la impresión 3D en metal. Aquí tienes un desglose de cómo se compara con otros métodos destacados:
Característica | WAAM | Fusión selectiva por láser (SLM) | Fusión por haz de electrones (EBM) | Chorro aglomerante (BJ) |
---|---|---|---|---|
Tasa de deposición | Alta | Bajo | Bajo | Media a alta |
Versatilidad de materiales | Amplia gama de aleaciones metálicas | Limitado a aleaciones compatibles | Limitado a aleaciones compatibles | Amplia gama de metales y cerámicas |
Acabado superficial | Más rugoso, puede requerir tratamiento posterior | Suave | Suave | Difícil, requiere tratamiento posterior |
Construir la envoltura | Posibilidad de un entorno amplio y abierto | Limitado por el tamaño de la cámara | Limitado por el tamaño de la cámara | Limitado por el tamaño de la cámara |
Residuos materiales | Bajo | Moderado | Moderado | Bajo |
Coste por unidad | Puede ser rentable para piezas grandes | Alta | Alta | Moderada a baja |
Aplicaciones | Grandes componentes, industrias diversas | Aeroespacial, médica, piezas de alto valor | Aeroespacial, médica, piezas de alto valor | Prototipos, utillaje, formas complejas |
Elegir la técnica adecuada de fabricación aditiva de metales
La técnica óptima de fabricación aditiva de metales depende de varios factores, entre ellos:
- Tamaño y complejidad de las piezas: WAAM destaca en piezas a gran escala, mientras que SLM y EBM podrían ser más adecuados para componentes intrincados y más pequeños. BJ ofrece un equilibrio para piezas de tamaño medio con geometrías complejas.
- Requisitos materiales: Tenga en cuenta las propiedades necesarias del material y la compatibilidad con cada técnica. WAAM cuenta con una amplia versatilidad de materiales, mientras que SLM y EBM tienen limitaciones. BJ puede trabajar con una amplia gama de metales e incluso cerámicas.
- Necesidades de acabado superficial: Si el acabado liso es fundamental, es preferible utilizar SLM o EBM, mientras que WAAM puede requerir un tratamiento posterior. La BJ suele requerir un tratamiento posterior para obtener un acabado liso.
- Consideraciones sobre los costes: WAAM puede ser rentable para piezas grandes, mientras que SLM y EBM suelen tener costes más elevados. BJ ofrece una opción intermedia.
Si evalúa detenidamente estos factores y los puntos fuertes y las limitaciones de cada técnica, podrá tomar una decisión informada sobre el método más adecuado para su aplicación específica.
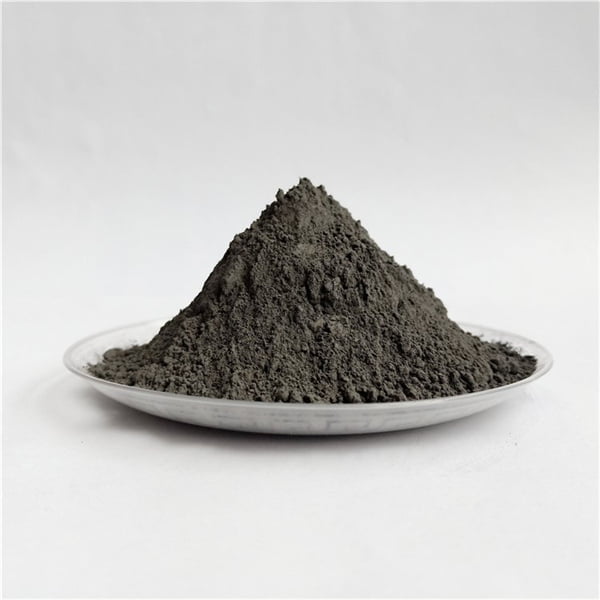
PREGUNTAS FRECUENTES
P: ¿Cuáles son las consideraciones de seguridad de WAAM?
La WAAM implica altas temperaturas, metal fundido y corrientes eléctricas. Los protocolos de seguridad adecuados son esenciales, incluido el uso de equipos de protección individual (EPI) adecuados, como cascos de soldadura, guantes y ropa ignífuga. Es fundamental utilizar el sistema en un entorno bien ventilado y seguir las directrices de seguridad recomendadas.
P: ¿Qué resistencia tienen las piezas fabricadas con WAAM?
La resistencia de las piezas impresas con WAAM depende de la aleación metálica elegida, de los parámetros adecuados del proceso y del tratamiento térmico (si procede). WAAM puede producir componentes con excelentes propiedades mecánicas comparables a las de sus homólogos fabricados tradicionalmente.
P: ¿Puede WAAM imprimir en color?
Actualmente, WAAM no ofrece capacidades de impresión multicolor directa. Sin embargo, pueden utilizarse técnicas de postprocesado como la pintura o el anodizado para añadir color a las piezas acabadas.
P: ¿Cuál es el futuro de WAAM?
Como ya se ha dicho, el futuro de la WAAM es prometedor. Los avances en automatización, sistemas de control y desarrollo de materiales están preparados para impulsar aún más las capacidades de la WAAM. Los sistemas WAAM híbridos que combinan WAAM con otros métodos de fabricación aditiva prometen una versatilidad aún mayor. Se espera que la exploración de nuevas aplicaciones en diversos sectores se acelere a medida que madure la tecnología WAAM.
En conclusión, La fabricación aditiva por arco de alambre (WAAM) presenta un enfoque revolucionario de la impresión 3D de metales. Su alta tasa de deposición, la eficiencia de los materiales y la capacidad de manejar estructuras a gran escala la convierten en una opción convincente para diversas industrias. Aunque hay que tener en cuenta factores como el acabado superficial y la tensión residual, las ventajas de la WAAM y su desarrollo continuo la sitúan como una potente herramienta para dar forma al futuro de la fabricación de metales.
Compartir
MET3DP Technology Co., LTD es un proveedor líder de soluciones de fabricación aditiva con sede en Qingdao, China. Nuestra empresa está especializada en equipos de impresión 3D y polvos metálicos de alto rendimiento para aplicaciones industriales.
Solicite información para obtener el mejor precio y una solución personalizada para su empresa.
Artículos relacionados
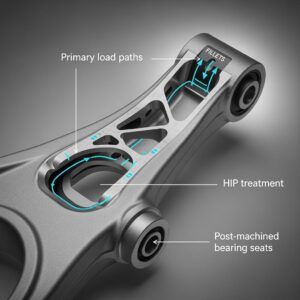
Metal 3D Printing for U.S. Automotive Lightweight Structural Brackets and Suspension Components
Leer Más "Acerca de Met3DP
Actualización reciente
Nuestro producto
CONTACTO
¿Tiene alguna pregunta? ¡Envíenos un mensaje ahora! Atenderemos su solicitud con todo un equipo tras recibir su mensaje.