Machines de fusion par faisceau d'électrons
Table des matières
Vue d'ensemble machine de fusion par faisceau d'électrons
La fusion par faisceau d'électrons (EBM) est une technologie de fabrication additive utilisée pour fusionner des poudres métalliques en pièces entièrement denses, couche par couche, à l'aide d'un faisceau d'électrons de grande puissance dans des conditions de vide. Les machines EBM offrent des vitesses de fabrication inégalées et des propriétés mécaniques impossibles à obtenir avec d'autres méthodes d'impression 3D de métaux.
Les principales caractéristiques de la technologie EBM sont les suivantes
Tableau 1 : Aperçu de la technologie de fusion par faisceau d'électrons
Attribut | Description |
---|---|
Source de chaleur | Faisceau d'électrons à haute intensité |
Environnement | Vide poussé |
Matières premières | Lit de poudre métallique |
Contrôle du faisceau | Lentilles et bobines électromagnétiques |
Mode construction | Fusion couche par couche de poudres métalliques |
Applications | Aérospatiale, médecine, automobile, outillage |
Grâce à une focalisation précise du faisceau et à un balayage rapide, EBM fusionne des matériaux conducteurs tels que le titane, les alliages de nickel, les aciers à outils et les métaux réfractaires pour en faire des composants entièrement denses dont les propriétés supérieures ne sont surpassées que par les produits corroyés.
L'environnement sous vide contrôlé empêche toute contamination, tandis que la distribution intelligente de l'énergie et les températures de préchauffage élevées minimisent les contraintes résiduelles susceptibles d'entraîner des déformations ou des fissures.
La compréhension de ces principes fondamentaux permet de comprendre pourquoi EBM fournit des performances mécaniques exceptionnelles, adaptées aux applications industrielles les plus exigeantes.
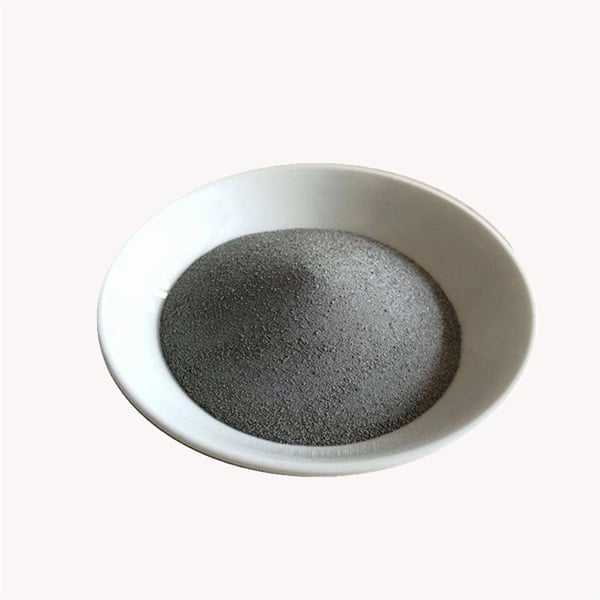
Types de systèmes de fusion par faisceau d'électrons
Fonctionnalité | Description | Impact sur l'utilisation du système |
---|---|---|
Configuration du canon à électrons | Les systèmes de fusion par faisceau d'électrons utilisent un canon à électrons pour générer un faisceau à haute énergie qui fait fondre sélectivement la poudre métallique. Il existe deux configurations principales pour les canons à électrons : * Sidewinder : La source du faisceau d'électrons est positionnée horizontalement à côté de la chambre de construction. Cette conception permet d'augmenter le volume de la chambre de construction, mais peut limiter l'accès pour le post-traitement. * Top Gun : La source du faisceau d'électrons est située directement au-dessus de la chambre de fabrication. Cette configuration facilite l'accès pour le retrait et le contrôle des pièces, mais peut limiter l'enveloppe de construction maximale. | Le choix de la configuration du pistolet dépend de la priorité accordée au volume de production et à l'accessibilité. Les Sidewinders sont idéaux pour la production à haut débit de pièces de grande taille, tandis que les Top Guns conviennent mieux aux applications de recherche et de développement qui nécessitent un contrôle et une manipulation fréquents des pièces. |
Mode de fusion des faisceaux | Les systèmes EBM peuvent fonctionner selon deux modes principaux de fusion du faisceau : * Numérisation matricielle : Le faisceau d'électrons parcourt rapidement le lit de poudre selon un schéma prédéterminé, faisant fondre les zones désignées couche par couche. Cette méthode est efficace pour les géométries simples, mais peut créer des artefacts en escalier sur les surfaces courbes. * Balayage vectoriel : Le faisceau d'électrons suit une trajectoire vectorielle définie pour faire fondre la poudre. Cette méthode permet de mieux contrôler la géométrie du bain de fusion et l'état de surface, en particulier pour les caractéristiques complexes. Toutefois, le balayage vectoriel peut être plus lent que le balayage matriciel pour les géométries simples. | Le choix entre les modes de numérisation matricielle et vectorielle dépend de l'équilibre souhaité entre la vitesse, la résolution et la qualité de surface. Le balayage matriciel est préférable pour la production en grande quantité de pièces à géométrie basique, tandis que le balayage vectoriel convient mieux aux pièces complexes exigeant une grande précision et un bon état de surface. |
Conception du système de vide | La fusion par faisceau d'électrons nécessite un vide poussé (généralement inférieur à 10^-4mbar) afin d'éviter l'oxydation du métal en fusion et d'assurer la stabilité du faisceau. Il existe deux types de systèmes de vide : * Pompe à diffusion : Cette conception traditionnelle utilise des pompes à diffusion pour atteindre le niveau de vide requis. Les pompes à diffusion sont fiables et bien établies, mais elles nécessitent un entretien régulier et peuvent être relativement lentes à atteindre les niveaux de vide optimaux. * Cryopompage : Cette technologie plus récente utilise des cryopompes pour capturer les molécules de gaz par un refroidissement extrême. Les cryopompes offrent des temps de vidange plus rapides et des besoins de maintenance réduits par rapport aux pompes à diffusion. Toutefois, leur coût d'investissement initial est plus élevé et elles peuvent nécessiter une tuyauterie supplémentaire pour l'alimentation en azote liquide. | Le choix d'un système de vide dépend de facteurs tels que le budget, les exigences en matière de maintenance et les temps de cycle souhaités. Les pompes à diffusion constituent un choix rentable pour les environnements de production établis, tandis que le pompage cryogénique offre des avantages pour les applications à haut débit ou les environnements de recherche qui privilégient les délais d'exécution rapides. |
Système de distribution de poudre | La répartition uniforme de la poudre métallique sur la plate-forme de construction est essentielle pour la réussite des constructions EBM. Deux systèmes principaux de distribution de la poudre sont utilisés : * Revêtement de la lame : Une lame ou un râteau étale une fine couche de poudre sur la plate-forme de construction après chaque cycle de fusion. Le revêtement par lame est une méthode simple et fiable, mais peut entraîner des incohérences dans la densité de la poudre en raison des variations de la pression et de l'angle de la lame. * Répartition du recul : Un flux de gaz à haute pression perturbe le lit de poudre, provoquant le recul des particules de poudre et le dépôt d'une nouvelle couche. L'épandage par recul offre une distribution plus uniforme de la poudre par rapport au revêtement par lame, mais nécessite une optimisation minutieuse de la pression du gaz afin d'éviter de perturber les couches précédemment fondues. | Le choix du système d'administration de la poudre a un impact sur la qualité et la répétabilité de la couche. Le revêtement par lame convient à la production de faibles volumes ou aux applications où la densité de la poudre est moins critique. L'épandage par enroulement est préférable pour les pièces de haute précision exigeant une distribution uniforme de la poudre. |
Principes de base du processus de fusion par faisceau d'électrons
Stade | Description | Avantages | Considérations |
---|---|---|---|
Préparation de la poudre | Les poudres métalliques utilisées dans l'EBM sont méticuleusement produites pour garantir une fluidité, une distribution granulométrique et une pureté chimique optimales. La taille des particules joue un rôle crucial, car des poudres trop fines peuvent entraver l'étalement de la couche, tandis que des poudres trop grossières peuvent entraîner la formation de billes et une mauvaise fusion. Un contrôle strict de l'oxygène, de l'azote et d'autres éléments est essentiel pour minimiser la porosité et obtenir les propriétés mécaniques souhaitées. | * Propriétés des matériaux cohérentes tout au long de la construction * Réduction du risque de défauts tels que la porosité et la fissuration | * Coût initial élevé des poudres métalliques de haute qualité * Nécessité d'une manipulation et d'un stockage spécialisés en raison de la réactivité potentielle |
Chambre à vide | La fusion par faisceau d'électrons nécessite un vide poussé (généralement entre 10-⁴ et 10-⁹ Pa) pour éviter l'oxydation et la contamination du métal en fusion. Ce résultat est obtenu grâce à de puissantes pompes à vide qui extraient les molécules d'air de la chambre. L'absence d'oxygène permet de traiter des métaux réactifs comme le titane et le tantale. | * Minimise l'interaction entre le métal en fusion et les gaz atmosphériques * Permet la production de pièces de haute densité avec d'excellentes propriétés mécaniques | * Systèmes de pompage à vide complexes et coûteux * Considérations supplémentaires pour le contrôle de l'humidité afin d'éviter les éclaboussures et les incohérences |
Génération de faisceaux d'électrons | Au cœur de l'EBM se trouve un canon à électrons, qui émet un faisceau focalisé d'électrons à haute énergie. Un champ électrique chauffe un filament (cathode) qui libère des électrons. Ces électrons sont accélérés par une haute tension vers une anode et concentrés par des bobines électromagnétiques. Le faisceau qui en résulte présente une densité de puissance exceptionnelle, capable de faire fondre même les métaux réfractaires à point de fusion élevé. | * Contrôle précis de la taille et de la profondeur du bassin de fusion * Pénétration profonde pour les géométries complexes avec des caractéristiques internes | * Nécessite une haute tension et des systèmes sophistiqués de contrôle des faisceaux. * L'entretien et l'étalonnage du canon à électrons sont essentiels. |
Distribution et épandage de poudre | Un mécanisme à lames ou à rouleaux étale méticuleusement une fine couche de poudre métallique sur la plate-forme de fabrication. L'épaisseur de cette couche, généralement comprise entre 30 et 100 microns, est prédéterminée par la résolution souhaitée et la géométrie de la pièce. | * Assure l'uniformité de l'épaisseur de la couche pour des propriétés matérielles constantes * Permet la création d'éléments complexes | * Le contrôle précis du mécanisme d'épandage de la poudre est essentiel. * La fluidité de la poudre et la distribution de la taille des particules peuvent avoir un impact sur l'efficacité de l'épandage. |
Fusion sélective | Le faisceau d'électrons, guidé par des miroirs de balayage commandés par ordinateur, fait fondre sélectivement des régions spécifiques du lit de poudre en fonction d'un modèle 3D découpé. La poudre non fondue sert de support aux structures en surplomb, ce qui évite d'avoir recours à des structures de support externes, courantes dans d'autres techniques de fabrication additive. | * Haute précision et exactitude dans la construction de géométries complexes * Capacité à créer des fonctionnalités et des canaux internes | * Une planification minutieuse de la trajectoire de balayage est nécessaire pour optimiser la fusion et minimiser les contraintes résiduelles. |
Construction couche par couche | Après la fusion d'une seule couche, une nouvelle couche de poudre est déposée par-dessus. Le faisceau d'électrons fait alors fondre sélectivement des zones désignées de cette nouvelle couche, la fusionnant avec la couche précédemment fondue. Ce processus se poursuit de manière itérative jusqu'à ce que l'objet 3D soit complet. | * Création de géométries complexes par étapes * Permet une utilisation efficace des matériaux, en minimisant les déchets | * Le temps de fabrication peut être plus long que pour d'autres procédés AM en raison de l'approche couche par couche. |
Plateforme de gestion de la chaleur et de construction | La gestion thermique joue un rôle essentiel dans l'EBM. La plate-forme de construction est généralement préchauffée à une température légèrement inférieure au point de fusion de la poudre afin d'améliorer la fluidité et de favoriser l'adhérence. Un creuset en cuivre refroidi à l'eau facilite en outre la dissipation de la chaleur et empêche le gauchissement de la pièce finale. | * Minimise les contraintes thermiques et l'accumulation de contraintes résiduelles * Contribue à la précision dimensionnelle et à la qualité des pièces | * Un contrôle minutieux de la température de préchauffage et de la vitesse de refroidissement est nécessaire. |
Retrait des pièces et post-traitement | Une fois le processus de construction terminé, la chambre est ramenée à la pression atmosphérique. La pièce construite reste collée à la plate-forme de construction et doit être séparée. Les structures de soutien, le cas échéant, sont soigneusement retirées à l'aide de techniques mécaniques. En fonction de l'application, des étapes de post-traitement telles que le traitement thermique, le pressage isostatique à chaud ou l'usinage peuvent être utilisées pour obtenir la finition de surface et les propriétés mécaniques souhaitées. | * Minimise les étapes de post-traitement grâce à sa haute densité et à sa capacité de former des filets. * Permet la création de pièces fonctionnelles | * Le processus d'enlèvement nécessite des précautions pour éviter d'endommager les éléments délicats. * Le traitement thermique ou d'autres étapes de post-traitement peuvent allonger le temps de traitement global. |
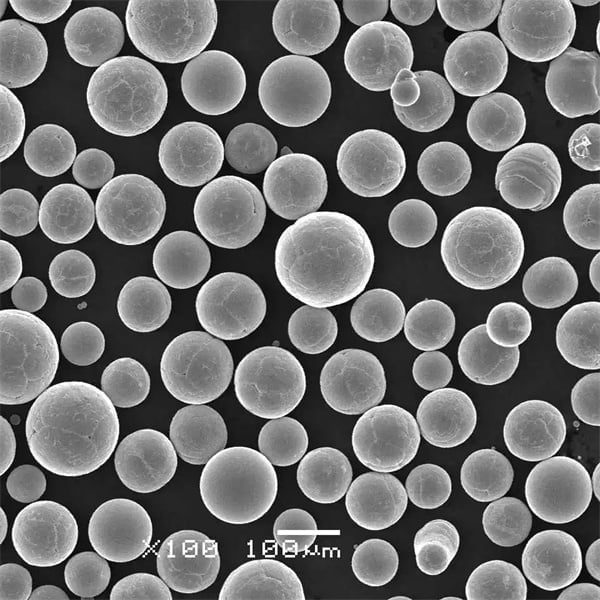
Principales spécifications machine de fusion par faisceau d'électrons
Spécifications | Description | Impact sur la qualité des pièces et la production |
---|---|---|
Puissance du faisceau (kW) | Il s'agit de la puissance totale du faisceau d'électrons. | Une puissance de faisceau plus élevée se traduit par des vitesses de fusion plus rapides et un débit plus important. Elle permet également de traiter des couches plus épaisses et des matériaux plus denses. Toutefois, une puissance excessive peut entraîner une surchauffe et un gauchissement de la pièce. |
Construire l'enveloppe (mm) | Elle définit les dimensions maximales (longueur, largeur, hauteur) d'une pièce qui peut être fabriquée en une seule fois. | Une enveloppe de fabrication plus grande offre une plus grande souplesse de conception pour les géométries complexes. Cependant, elle augmente également l'encombrement de la machine, la consommation de poudre et le temps de construction total. |
Niveau de vide (Pa) | La pression à l'intérieur de la chambre EBM est cruciale pour éviter l'oxydation et la contamination pendant le processus de fusion. | Un vide élevé (valeur Pa inférieure) garantit une interaction minimale entre le métal en fusion et les gaz atmosphériques, ce qui permet d'obtenir des pièces aux propriétés mécaniques supérieures et à la densité élevée. Cependant, l'obtention et le maintien d'un vide plus poussé nécessitent des pompes plus puissantes, ce qui augmente le coût et la complexité de la machine. |
Épaisseur de la couche (μm) | L'épaisseur de chaque couche individuelle de poudre métallique étalée et fondue pendant le processus de construction. | Les couches plus fines permettent d'obtenir des détails plus fins et des finitions de surface plus lisses. Cependant, elles nécessitent plus de temps de construction en raison du nombre plus élevé de couches nécessaires. Inversement, les couches plus épaisses peuvent être plus rapides à fabriquer, mais peuvent donner une surface plus rugueuse et une porosité interne potentielle. |
Compatibilité des matériaux | La gamme de poudres métalliques que le système EBM peut traiter. | Une plus grande compatibilité des matériaux permet de créer des pièces à partir de divers alliages ayant des propriétés spécifiques adaptées à diverses applications. Toutefois, certains matériaux ont des points de fusion plus élevés ou nécessitent une manipulation spécialisée, ce qui peut limiter les options de la machine. |
Surveillance in situ | La possibilité de surveiller le processus de fusion en temps réel à l'aide de caméras ou d'autres capteurs. | Le contrôle in situ permet une détection précoce des défauts tels que les éclaboussures ou la fissuration de la couche, ce qui permet de prendre des mesures correctives au cours de la fabrication. Cela permet d'améliorer considérablement le rendement et de réduire le risque de défaillance des pièces. |
Contrôle de la géométrie du bassin de fusion | Le niveau de précision avec lequel le faisceau d'électrons peut être focalisé et manipulé pour contrôler la forme du bain de métal en fusion. | Le contrôle précis du bain de fusion minimise les zones affectées par la chaleur et les contraintes résiduelles, ce qui permet d'améliorer les performances mécaniques et la résistance à la fatigue des pièces. Cela est particulièrement important pour les applications soumises à des contraintes élevées. |
Système de rechargement par poudre | Mécanisme utilisé pour distribuer et répandre de la poudre métallique fraîche sur la plate-forme de construction après la fonte de chaque couche. | Un système de revêtement efficace garantit une épaisseur constante de la couche de poudre et minimise le risque de contamination par les particules de poudre résiduelles. Les systèmes à lames et à rouleaux sont courants, chacun avec ses avantages et ses limites. |
Logiciel de génération de support | Le logiciel utilisé pour concevoir et générer des structures de soutien dans le modèle 3D. | Des structures de support bien conçues sont essentielles pour éviter la déformation des pièces et assurer une bonne dissipation de la chaleur pendant la fabrication. Un logiciel avancé permet d'optimiser le placement des supports et de minimiser le gaspillage de matériaux. |
Exigences en matière de post-traitement | Le niveau de post-traitement nécessaire pour obtenir les propriétés finales souhaitées de la pièce. | Les pièces EBM nécessitent généralement un post-traitement minimal par rapport à d'autres techniques de fabrication additive. Toutefois, l'enlèvement de la structure de support et la finition de la surface peuvent être nécessaires en fonction de l'application. |
Économie de l'adoption de la fusion par faisceau d'électrons
Facteur | Impact sur l'adoption | Explication |
---|---|---|
Dépenses en capital | Haut | Les machines EBM ont un coût initial élevé, allant de $500 000 à plusieurs millions de dollars en fonction du volume de construction et des capacités. Ce coût peut constituer un obstacle important pour les petits fabricants ou ceux qui débutent dans la fabrication additive. |
Coûts opérationnels | Mixte | Si l'EBM présente des avantages tels que la réduction des déchets de matériaux et la fabrication de formes presque nettes, elle entraîne également des coûts pour la poudre, la consommation d'énergie (en raison du faisceau d'électrons à haute puissance) et d'éventuels traitements ultérieurs tels que l'enlèvement du support. Toutefois, ces coûts peuvent être compensés par la réduction des besoins d'usinage et l'amélioration des performances des pièces. |
Complexité des pièces | Positif | EBM excelle dans la création de géométries complexes, presque impossibles à réaliser, avec des canaux et des réseaux internes. Cela libère la liberté de conception pour des composants légers et très résistants dans l'aérospatiale, la médecine et d'autres industries. La capacité de créer des caractéristiques complexes peut justifier les coûts plus élevés associés à l'EBM. |
Volume de production | Limitée | Les machines EBM ont des vitesses de fabrication plus lentes que certaines autres technologies de fabrication additive. Elles sont donc moins adaptées à la production en grande série. Cependant, l'EBM se distingue dans les applications où la personnalisation, les petites tailles de lots et la performance sont primordiales. |
Compatibilité des matériaux | Élargissement | L'EBM peut traiter une gamme de matériaux plus large que beaucoup d'autres procédés d'impression 3D, y compris les métaux réactifs et réfractaires, certains alliages et même certaines céramiques. Cette polyvalence ouvre la voie à de nouvelles applications dans des environnements exigeants. La poursuite du développement de matériaux compatibles favorisera l'adoption de ce procédé. |
Travail et expertise | Spécialisé | L'utilisation et l'entretien des machines EBM nécessitent un personnel qualifié connaissant les systèmes à vide, la technologie des faisceaux d'électrons et la manipulation des poudres métalliques. La rareté de cette expertise peut constituer un obstacle pour certaines entreprises, ce qui a un impact sur les taux d'adoption. |
Retour sur investissement (ROI) | Long terme | La viabilité économique de l'EBM repose sur une perspective à long terme. Si les coûts initiaux sont élevés, les avantages de l'EBM (pièces plus légères et plus résistantes, réduction des déchets) se traduisent souvent par des économies et des améliorations des performances tout au long du cycle de vie d'un produit. |
Incitations gouvernementales | Positif | Le soutien des pouvoirs publics à la recherche et au développement dans le domaine de la fabrication additive, y compris l'EBM, peut accélérer l'adoption de cette technologie en abaissant les barrières à l'entrée et en encourageant l'innovation. Les allègements fiscaux ou les subventions peuvent inciter les entreprises à investir dans la technologie EBM. |
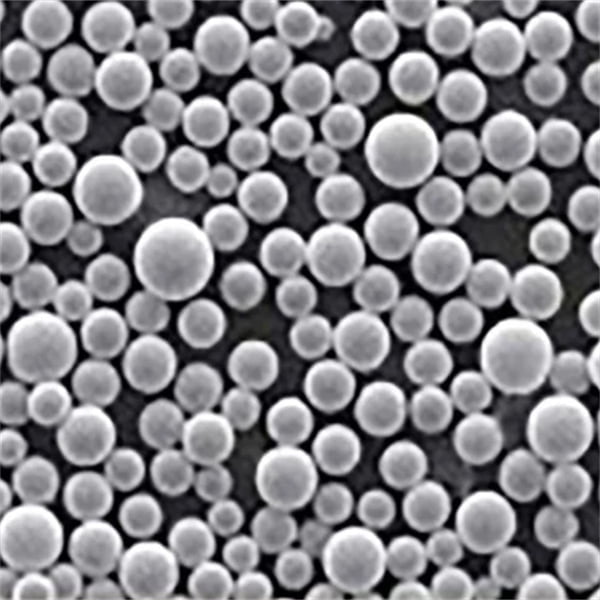
Matériaux populaires pour l'EBM
Classe de matériaux | Exemples d'alliages | Propriétés | Applications |
---|---|---|---|
Alliages de titane | Ti-6Al-4V, Ti-6Al-4V ELI | * Excellent rapport résistance/poids * Biocompatibilité élevée * Résistant à la corrosion | * Composants aérospatiaux (ailes, trains d'atterrissage) * Implants médicaux (prothèses de genou, implants dentaires) * Articles de sport (clubs de golf, cadres de bicyclettes) |
Alliages à base de nickel | Inconel 625, Inconel 718 | * Résistance exceptionnelle à haute température * Résistance à l'oxydation et à la corrosion * Bonne soudabilité | * Aubes et disques de turbines pour moteurs à réaction * Échangeurs de chaleur pour le traitement chimique * Arbres de roue pour pompes |
Alliages de cobalt et de chrome | CoCrMo, Haynes 214 | * Haute résistance à l'usure * Biocompatible (applications limitées) * Bonne dureté | * Remplacement des articulations (hanches, genoux) * Outils de coupe et pièces d'usure * Implants dentaires (utilisation limitée en raison de problèmes potentiels liés au chrome) |
Aciers inoxydables | 17-4PH, 316L | * Bonne résistance à la corrosion * Résistance modérée * Biocompatible (applications limitées) | * Instruments médicaux * Équipement de traitement chimique * Composants pour la transformation des aliments et des boissons |
Matériaux émergents | * Tungstène (W) * Tantale (Ta) * Niobium (Nb) * Molybdène (Mo) | * Points de fusion très élevés * Excellentes propriétés à haute température * Recherche et développement limités | * Applications potentielles dans les secteurs de l'aérospatiale, de la défense et du nucléaire (en raison des points de fusion élevés et de la résistance aux environnements extrêmes). |
Avantages de la fusion par faisceau d'électrons
Bénéfice | Description | Impact |
---|---|---|
Pièces de haute densité et de forme proche du filet | L'EBM crée des pièces d'une densité supérieure à 99,5% de la densité théorique de la poudre métallique utilisée. Cela élimine la porosité (minuscules poches d'air) commune à d'autres méthodes de fabrication additive, ce qui permet d'obtenir des pièces d'une solidité, d'une résistance à la fatigue et d'une précision dimensionnelle exceptionnelles. | Cela permet de créer des composants métalliques fonctionnels pour des applications exigeantes dans les secteurs de l'aérospatiale (pales de turbines, carters de moteurs), de la médecine (implants dentaires, prothèses) et de l'automobile (pièces légères et performantes). |
Propriétés mécaniques supérieures | L'environnement sous vide poussé et le processus de fusion précis de l'EBM minimisent l'oxydation et la contamination, préservant ainsi les propriétés inhérentes de la poudre métallique. Cela se traduit par des pièces présentant une excellente résistance à la traction, au fluage (capacité à résister à la déformation sous contrainte à des températures élevées) et à la rupture. | Les pièces produites par EBM peuvent supporter des charges importantes, fonctionner efficacement à des températures élevées et résister à la propagation des fissures, ce qui les rend idéales pour les applications nécessitant une durabilité et une intégrité structurelle dans des environnements difficiles. |
Traitement des métaux réfractaires et réactifs | Contrairement aux méthodes de fabrication traditionnelles limitées par des points de fusion élevés et la réactivité, EBM excelle dans le traitement de matériaux difficiles comme les alliages de titane, le tantale et l'Inconel. L'environnement sous vide empêche l'oxydation et permet un contrôle précis du processus de fusion, ce qui garantit une fabrication réussie. | Cela élargit les possibilités de conception pour des industries telles que l'aérospatiale et le biomédical, où les composants doivent présenter un rapport résistance/poids exceptionnel, une biocompatibilité (compatibilité avec les tissus vivants) et des performances à haute température. |
Liberté de conception pour les géométries complexes | L'approche couche par couche d'EBM permet de créer des caractéristiques internes complexes, des canaux et des structures en treillis impossibles à réaliser avec les techniques conventionnelles. Cette souplesse de conception optimise la répartition du poids, améliore le transfert de chaleur et permet de créer des composants dotés d'une fonctionnalité supérieure. | Cet avantage révolutionne la conception de produits dans des secteurs tels que l'aérospatiale, où les composants légers, très résistants et dotés de canaux de refroidissement complexes sont essentiels à l'efficacité des moteurs. Il permet également de créer des implants médicaux personnalisés qui s'adaptent parfaitement à l'anatomie du patient. |
Structures de soutien minimales | En raison de la grande résistance inhérente des pièces produites par EBM, des structures de soutien minimales sont nécessaires au cours du processus de construction. Cela réduit le temps de post-traitement et le gaspillage de matériaux, ainsi que le risque d'endommagement de la structure de soutien sur le composant final. | Cela se traduit par des délais de production plus courts, des coûts globaux moins élevés et la possibilité de créer des géométries complexes qu'il serait difficile, voire impossible, de réaliser avec les méthodes traditionnelles. |
Réduction des déchets matériels | L'EBM est un processus de fabrication additive, ce qui signifie que le matériau est ajouté couche par couche pour créer la forme souhaitée. Ce procédé minimise les pertes de matériaux par rapport aux techniques soustractives telles que l'usinage, où une partie importante du matériau brut est enlevée pour obtenir la forme finale. | Cet avantage favorise la durabilité et réduit les coûts de production en maximisant l'utilisation des matériaux. En outre, la poudre inutilisée de la chambre de construction peut souvent être réutilisée pour des constructions ultérieures, ce qui minimise encore les déchets. |
Vue d'ensemble machine de fusion par faisceau d'électrons Fournisseurs
Divers fabricants industriels établis et de nouveaux venus spécialisés proposent des solutions de fusion par faisceau d'électrons modulables de la recherche à la production en grande quantité dans les secteurs de l'aérospatiale, de la médecine, de l'automobile et de l'industrie.
Tableau 8 : Principaux fabricants de systèmes de fusion par faisceau d'électrons
Fournisseur | Détails | Segments cibles |
---|---|---|
GE Additive | Pionnier de la technologie EBM | Aérospatiale, médecine, automobile |
Sciaky | Taille de l'enveloppe la plus grande | Structures aérospatiales |
Wayland Additive | Plates-formes d'AM métal à petit budget | Petits ateliers d'usinage |
JEOL | Systèmes EBM de niveau recherche | Universités |
Nanodimension | Capacités multimatériaux | Électronique, défense |
Le leader du secteur, Arcam EBM, qui fait désormais partie de GE Additive, s'est imposé très tôt grâce à des solutions brevetées et continue de dominer les catégories établies des implants médicaux et de l'aérospatiale.
De leur côté, les nouveaux venus comme Wayland visent à étendre l'adoption en ciblant les petits et moyens fabricants avec des plates-formes de départ économiques.
Les collaborations sur les matériaux, la qualification des pièces et l'optimisation des machines entre les producteurs, les chercheurs et les groupes d'utilisateurs finaux permettront à terme d'étendre la pénétration de l'EBM à d'autres applications critiques.
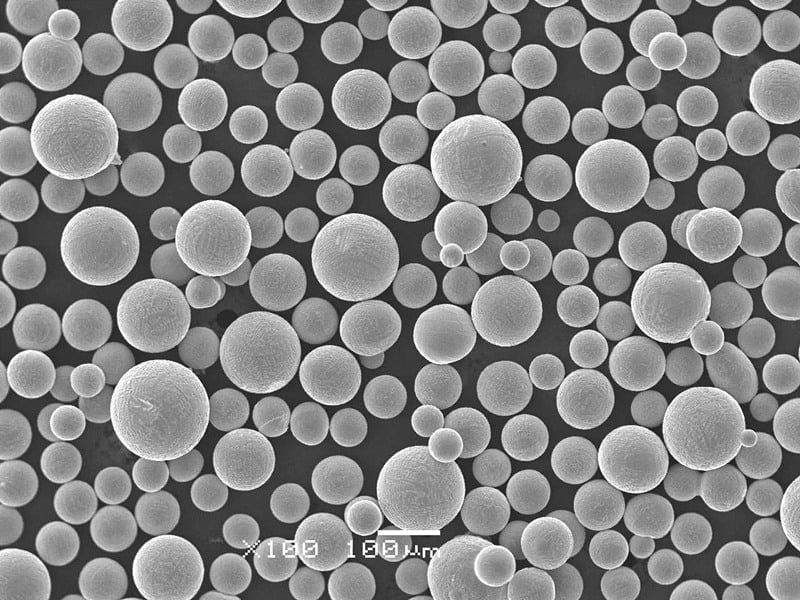
Perspectives d'avenir pour l'adoption de la fusion par faisceau d'électrons
Propulsée par une vitesse de production supérieure et des propriétés mécaniques exceptionnelles impossibles à obtenir par d'autres procédés additifs ou conventionnels, l'adoption de l'EBM semble en passe de connaître une expansion massive dans les secteurs de l'aérospatiale, des appareils médicaux, de l'automobile et de l'industrie au cours des 5 à 7 prochaines années.
Une plus grande sensibilisation aux avantages de l'EBM au-delà du prototypage et de la production à grande échelle devrait stimuler les investissements en équipements, car les entreprises utilisent l'impression 3D pour remodeler les chaînes d'approvisionnement.
Les enveloppes de construction plus grandes désormais accessibles dans le commerce permettent également de consolider les assemblages en un nombre réduit de composants, ce qui optimise encore la logistique des stocks et les délais d'exécution.
Toutefois, la baisse des coûts des systèmes, combinée à une plus grande disponibilité des matériaux, doit continuer à améliorer l'accès des petits fabricants à la technologie EBM. La rationalisation des outils auxiliaires de manipulation des poudres et des flux de travail de post-traitement simplifiera également l'adoption de cette technologie.
Dans l'ensemble, l'EBM continue sur sa lancée pour pénétrer une gamme de plus en plus large d'applications de production grâce à des taux de dépôt inégalés et à des propriétés de matériaux exceptionnelles par rapport à d'autres procédés de fabrication additive de métaux ou à d'autres procédés de fabrication traditionnels.
FAQ
Q : Quelle est l'infrastructure nécessaire pour soutenir l'EBM ?
R : Il faut compter plus de 500 m² pour la machine elle-même, et plus d'espace pour les stations de manutention de la poudre et le post-traitement. Les planchers en béton sont généralement renforcés pour supporter des charges d'équipement de plus de 12 000 livres.
Q : Combien faut-il d'opérateurs par machine EBM ?
R : Un technicien peut prendre en charge plusieurs unités EBM en fonction du niveau d'automatisation et des volumes de production. Le personnel supplémentaire s'occupe des opérations sur les poudres, des tâches de post-traitement, de la maintenance et de l'ingénierie.
Q : Quels sont les matériaux qui ne peuvent pas être traités avec la technologie EBM ?
R : Les polymères non conducteurs ne peuvent pas être traités par faisceaux d'électrons. Mais l'EBM permet de traiter pratiquement tous les systèmes d'alliages métalliques conducteurs qu'il est possible de fabriquer.
Q : Quels sont les risques de sécurité associés à la technologie EBM ?
R : Les tensions élevées des faisceaux d'électrons présentent des risques d'éclair d'arc électrique qui nécessitent des enceintes et des contrôles appropriés. L'exposition à des poudres métalliques réactives nécessite également des protocoles pour les risques d'incendie et d'inhalation, qui requièrent un équipement de protection et une formation.
Q : L'EBM nécessite-t-il un traitement thermique secondaire ?
R : Certains alliages bénéficient d'un traitement thermique pour améliorer les microstructures et adapter les propriétés mécaniques. Toutefois, les cycles de solidification rapide et les températures de préchauffage élevées propres au procédé EBM éliminent généralement ces étapes de post-traitement.
Partager sur
MET3DP Technology Co. est un fournisseur de premier plan de solutions de fabrication additive dont le siège se trouve à Qingdao, en Chine. Notre société est spécialisée dans les équipements d'impression 3D et les poudres métalliques de haute performance pour les applications industrielles.
Articles connexes
À propos de Met3DP
Mise à jour récente
Notre produit
CONTACTEZ-NOUS
Vous avez des questions ? Envoyez-nous un message dès maintenant ! Nous répondrons à votre demande avec toute une équipe dès réception de votre message.
Obtenir les informations de Metal3DP
Brochure du produit
Obtenir les derniers produits et la liste des prix
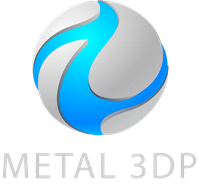
Poudres métalliques pour l'impression 3D et la fabrication additive