電子ビーム溶解装置
目次
概要 電子ビーム溶解機
電子ビーム溶解(EBM)は、真空条件下で高出力の電子ビームを使用して、金属粉末を層ごとに完全に緻密な部品に融合させるために使用される積層造形技術です。EBMマシンは、他の金属3Dプリンティング手法では達成できない比類のない造形速度と機械的特性を提供します。
EBM技術の主な特徴は以下の通りである:
表1:電子ビーム溶解技術の概要
属性 | 説明 |
---|---|
熱源 | 高強度電子ビーム |
環境 | 高真空 |
原料 | 金属製パウダーベッド |
ビーム制御 | 電磁レンズとコイル |
ビルドモード | 金属粉末の層間融合 |
アプリケーション | 航空宇宙、医療、自動車、工具 |
精密なビーム集束と迅速なスキャニングを活用することで、EBMはチタン、ニッケル合金、工具鋼、耐火金属のような導電性材料を、溶製材を凌ぐ優れた特性を持つ完全な高密度部品へと融合させる。
制御された真空環境は汚染を防ぎ、インテリジェントなエネルギー供給と高い予熱温度は、反りや亀裂につながる残留応力を最小限に抑える。
これらの基本原理を理解することは、なぜEBMが最も要求の厳しい産業用途のためにオーダーメイドで卓越した機械的性能を提供するのかを説明するのに役立ちます。
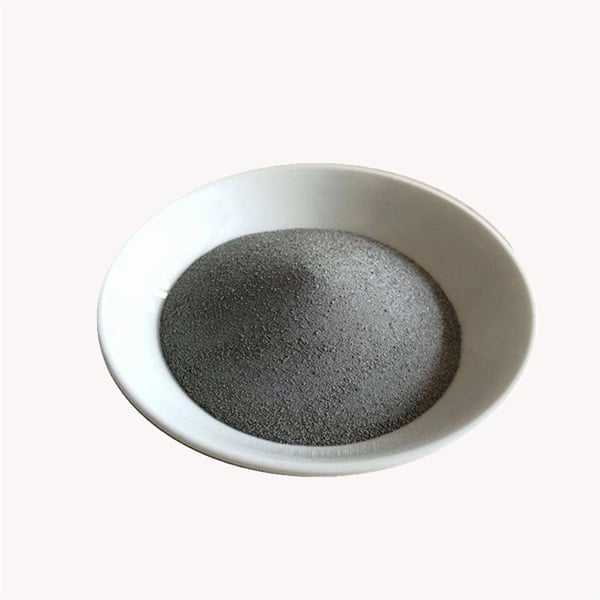
電子ビーム溶解システムの種類
特徴 | 説明 | システム利用への影響 |
---|---|---|
電子銃の構成 | 電子ビーム溶解システムは、金属粉末を選択的に溶解する高エネルギービームを生成するために電子銃を利用します。電子銃には主に2つの構成がある: * サイドワインダー 電子ビーム源は、ビルドチャンバーと並んで水平に配置されている。この設計により、ビルドチャンバーの容積を大きくすることができますが、後処理のためのアクセスが制限される場合があります。 * トップガン 電子ビーム源はビルドチャンバーの真上に位置する。この構成は、部品の取り外しやモニタリングのためのアクセスが容易ですが、最大ビルドエンベロープが制限される可能性があります。 | ガン構成の選択は、造形量とアクセス性の優先順位によって決まります。サイドワインダーは大型部品の高スループット生産に理想的ですが、トップガンは頻繁な部品のモニタリングや操作が必要な研究開発用途に適しています。 |
ビーム溶解モード | EBMシステムは、2つの主要なビーム溶融モードで動作することができる: * ラスタースキャン: 電子ビームは、粉末ベッドを所定のパターンで高速走査し、指定された領域を層ごとに溶融する。この方法は単純な形状には効率的ですが、曲面では階段状のアーチファクトが発生することがあります。 * ベクター・スキャン 電子ビームは、定義されたベクトル経路に従って粉末を溶融する。この方法は、特に複雑な形状に対して、溶融プールの形状と表面仕上げをより細かく制御することができます。しかし、単純な形状の場合、ベクトルスキャニングはラスタースキャニングよりも時間がかかります。 | ラスタースキャンとベクタースキャンのどちらを選択するかは、速度、解像度、表面品質のバランスによって決まります。ラスタースキャンは基本的な形状を持つパーツの大量生産に適しており、ベクタースキャンは高精度と表面仕上げが要求される複雑なパーツに適しています。 |
真空システム設計 | 電子ビーム溶解では、溶融金属の酸化を防ぎ、ビームの安定性を確保するため、高真空環境(通常10^-4mbar以下)が必要です。一般的な真空システムには2つの設計がある: * 拡散ポンプ: この伝統的な設計では、必要な真空レベルを達成するために拡散ポンプを利用している。拡散ポンプは信頼性が高く定評があるが、定期的なメンテナンスが必要で、最適な真空レベルに達するまでに比較的時間がかかる。 * クライオポンプ: この新しい技術は、極端な冷却によってガス分子を捕捉するクライオポンプを採用している。クライオポンプは、ディフュージョンポンプに比べてポンプ停止時間が短く、メンテナンスの必要性も少ない。しかし、初期投資コストが高く、液体窒素供給用の追加配管が必要になる場合がある。 | 真空システム設計の選択は、予算、メンテナンス要件、希望するサイクル時間などの要因に左右される。ディフュージョンポンプは、確立された生産環境では費用対効果の高い選択であり、一方、クライオポンプは、高スループットアプリケーションや、迅速なターンアラウンドタイムを優先する研究環境では利点があります。 |
パウダー・デリバリー・システム | EBM造形を成功させるには、造形プラットフォーム全体に金属粉末を均一に分布させることが重要である。2つの主要な粉末供給システムが採用されている: * ブレード・コーティング: ブレードまたはレーキは、各溶融サイクルの後に、造形プラットフォーム上に粉末の薄い層を広げます。ブレードコーティングはシンプルで信頼性の高い方法ですが、ブレードの圧力や角度のばらつきにより、パウダー密度にばらつきが生じることがあります。 * リコイルの広がり: 高圧ガス流がパウダーベッドを破壊し、パウダー粒子を反跳させて新しい層を堆積させます。反跳散布は、ブレードコーティングと比較してより均一な粉末分布を提供しますが、以前に溶融した層を乱さないようにガス圧を慎重に最適化する必要があります。 | パウダー供給システムの選択は、層の品質と再現性に影響します。ブレードコーティングは、少量生産や粉末密度がそれほど重要でない用途に適しています。リコイル散布は、均一な粉末分布が要求される高精度部品に適しています。 |
電子ビーム溶解プロセスの基礎
ステージ | 説明 | メリット | 考察 |
---|---|---|---|
パウダーの準備 | EBMに使用される金属粉末は、最適な流動性、粒度分布、化学的純度を確保するために細心の注意を払って製造されます。粒子径は極めて重要な役割を果たし、過度に微細な粉末は層の広がりを妨げ、過度に粗い粉末はボール化や融着不良の原因となります。気孔率を最小限に抑え、望ましい機械的特性を得るためには、酸素、窒素、その他の元素を厳密に管理することが不可欠です。 | * 一貫した材料特性 * ポロシティやクラックのような欠陥のリスク低減 | * 高品質金属粉末の高い初期費用 * 潜在的な反応性のため、特別な取り扱いと保管が必要である。 |
真空チャンバー | 電子ビーム溶解では、溶融金属の酸化と汚染を防ぐため、高真空環境(通常10-⁴~10-⁹Pa)が必要である。これは、チャンバーから空気分子を抽出する強力な真空ポンプによって達成される。酸素がないため、チタンやタンタルのような反応性の高い金属の処理が可能になります。 | * 溶融金属と大気ガスとの相互作用を最小限に抑える。 * 優れた機械的特性を持つ高密度部品の製造を可能にする。 | * 複雑で高価な真空ポンプシステムが必要 * スパッタやムラを防ぐための水分管理に関する追加事項 |
電子ビーム発生 | EBMの心臓部には電子銃があり、集束した高エネルギー電子ビームを放出する。電界によってフィラメント(陰極)が加熱され、電子が放出される。これらの電子は高電圧によって陽極に向かって加速され、電磁コイルによってさらに集束される。その結果、ビームは非常に高い出力密度を誇り、融点の高い難溶性金属も溶かすことができる。 | * 溶融プールのサイズと深さを正確に制御 * 内部形状のある複雑な形状への深い浸透 | * 高電圧と高度なビーム制御システムが必要 * 電子銃のメンテナンスと校正は非常に重要である。 |
粉体の供給と散布 | ブレードまたはローラー機構が、ビルド・プラットフォーム上に金属粉末の薄い層を丹念に広げていく。この層の厚さは、通常30ミクロンから100ミクロンで、希望する解像度と部品の形状によって決定されます。 | * 均一な層厚を確保し、一貫した材料特性を実現 * 複雑な機能の作成が可能 | * 粉体散布メカニズムの正確な制御が重要 * 粉体の流動性と粒度分布は、散布効率に影響を与える。 |
選択的溶解 | 電子ビームは、コンピューター制御のスキャニングミラーによって誘導され、スライスされた3Dモデルに従って粉末層の特定領域を選択的に溶融する。未溶融の粉末は、はみ出した構造の支持体として機能するため、他の積層造形技術で一般的な外部支持構造が不要になる。 | * 複雑な形状の構築における高い精度と正確さ * 内部機能とチャンネルを作成する能力 | * 溶融を最適化し、残留応力を最小化するためには、慎重なスキャン経路計画が必要である。 |
レイヤーごとの構築 | 一つの層が溶けた後、新しい粉末の層が上に堆積される。その後、電子ビームがこの新しい層内の指定領域を選択的に溶かし、先に溶けた層と融合させる。このプロセスは、3Dオブジェクト全体が完成するまで繰り返し続けられる。 | * 複雑な形状を段階的に作成することができます。 * 材料の効率的な使用を可能にし、無駄を最小限に抑える。 | * レイヤー・バイ・レイヤー・アプローチのため、他のAMプロセスに比べて造形時間が長くなる可能性がある。 |
熱管理とビルド・プラットフォーム | EBMでは熱管理が重要な役割を果たす。ビルドプラットフォームは通常、流動性を向上させ、結合を促進するために、粉末の融点よりわずかに低い温度まで予熱されます。水冷式の銅製るつぼはさらに放熱を助け、最終部品の反りを防ぎます。 | * 熱応力と残留応力の蓄積を最小限に抑える * 寸法精度と部品品質に貢献する。 | * 予熱温度と冷却速度の慎重なコントロールが必要である。 |
部品の取り外しと後処理 | 造形プロセスが完了すると、チャンバーは大気圧に戻される。造形された部品は造形プラットフォームに付着したままなので、分離する必要がある。支持構造物がある場合は、機械的な技術を使って慎重に取り除かれる。用途によっては、熱処理、熱間静水圧プレス、機械加工などの後処理工程を経て、所望の表面仕上げや機械的特性を得ることができる。 | * 高密度とニアネットシェイプ機能により、後処理工程を最小化。 * 機能部品の作成が可能 | * 取り外しには、デリケートな部分を傷つけないよう注意が必要です。 * 熱処理やその他の後処理工程は、全体的な処理時間を増加させる可能性がある。 |
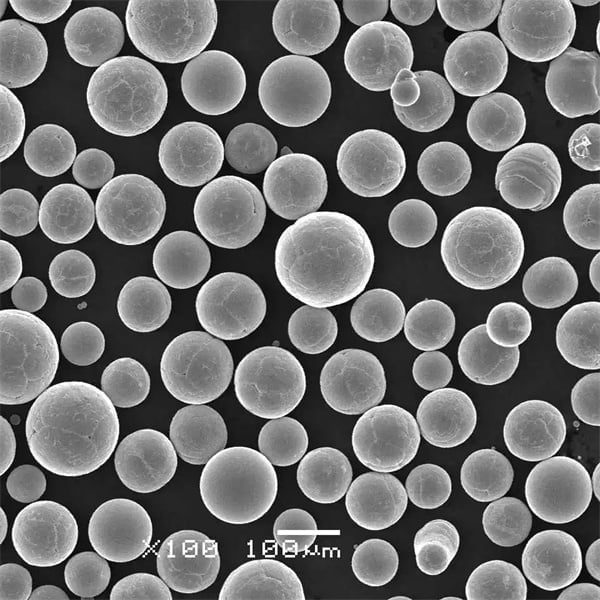
主な仕様 電子ビーム溶解機
仕様 | 説明 | 部品の品質と生産への影響 |
---|---|---|
ビームパワー (kW) | これは電子ビームの総出力を意味する。 | ビーム出力が高いほど、溶融速度が速くなり、スループットが向上する。また、厚い層や高密度の材料の加工も可能になる。しかし、過剰な出力は部品の過熱や反りにつながる可能性があります。 |
ビルド・エンベロープ (mm) | これは、1回のビルドで製造可能な部品の最大寸法(長さ、幅、高さ)を定義します。 | より大きな造形エンベロープは、複雑な形状に対する設計の柔軟性を高める。しかし、機械の設置面積、パウダーの消費量、全体的な造形時間が増加します。 |
真空レベル (パ) | EBMチャンバー内の圧力は、溶解プロセス中の酸化や汚染を防ぐために非常に重要である。 | 高真空(より低いPa値)であれば、溶融金属と大気ガスとの相互作用が最小限に抑えられ、その結果、優れた機械的特性と高密度を持つ部品が得られる。しかし、より深い真空を達成・維持するには、より強力なポンプが必要となり、機械コストと複雑さが増す。 |
レイヤーの厚さ (μm) | 金属粉末の個々の層の厚さは、製造プロセス中に広がり、溶ける。 | より薄いレイヤーは、より細かいディテールと滑らかな表面仕上げを提供する。しかし、必要な層数が増えるため、造形時間が長くなる。逆に、厚い層は造形時間が短いが、表面が粗くなり、内部空隙が生じる可能性がある。 |
材質の適合性 | EBMシステムが処理できる金属粉末の範囲。 | 幅広い材料互換性により、様々な用途に適した特定の特性を持つ多様な合金から部品を作ることができる。しかし、融点が高い材料や特殊な取り扱いを必要とする材料もあるため、機械のオプションが制限される場合があります。 |
現場モニタリング | カメラやその他のセンサーを使って、溶融プロセスをリアルタイムで監視できること。 | In-situモニタリングにより、スパッタやレイヤークラックなどの欠陥を早期に検出することができ、造形中に是正措置を講じることができる。これにより、歩留まりを大幅に改善し、部品不良のリスクを低減することができます。 |
メルトプール・ジオメトリー・コントロール | 溶融金属プールの形状を制御するために、電子ビームを集束させて操作できる精度の高さ。 | 正確なメルトプール制御により、熱影響部や残留応力が最小限に抑えられ、機械的性能や耐疲労性が向上した部品が得られます。これは、高応力が要求される用途では特に重要です。 |
粉体塗装システム | 各層が溶融した後、新しい金属粉末を造形プラットフォームに供給し、広げるために使用される機構。 | 効率的な再コーティングシステムは、パウダー層の厚みを一定に保ち、残留パウダー粒子による汚染のリスクを最小限に抑えます。ブレード方式とローラー方式が一般的で、それぞれに利点と限界があります。 |
サポート・ジェネレーション・ソフトウェア | 3Dモデル内の支持構造を設計・生成するためのソフトウェア。 | うまく設計されたサポート構造は、パーツの歪みを防ぎ、製造中の適切な熱放散を確保するために非常に重要です。高度なソフトウェアは、サポート配置を最適化し、材料の無駄を最小限に抑えることができます。 |
後処理の要件 | 希望する最終的な部品特性を達成するために必要な後処理のレベル。 | EBM部品は通常、他の付加製造技術に比べて後処理が最小限で済む。ただし、用途によってはサポート構造の除去や表面仕上げが必要になる場合があります。 |
電子ビーム溶解導入の経済性
ファクター | 採用への影響 | 説明 |
---|---|---|
資本支出 | 高い | EBMマシンの初期費用は高額で、造形量や機能によって$50万ドルから数百万ドルに及ぶ。これは、小規模な製造業者や付加製造の初心者にとっては大きな障壁となる。 |
運営コスト | ミックス | EBMは、材料廃棄の削減やニアネットシェイプ製造などの利点がある一方で、粉末材料、エネルギー消費(高出力の電子ビームによる)、サポート除去などの潜在的な後処理にかかるコストも発生する。しかし、これらのコストは、機械加工の必要性を減らし、部品の性能を向上させることで相殺することができます。 |
部品の複雑さ | ポジティブ | EBMは、内部チャンネルや格子を持つ複雑で不可能に近い形状を作り出すことに優れています。これにより、航空宇宙、医療、その他の産業において、軽量で高強度なコンポーネントの設計の自由度が高まります。複雑な形状を作成する能力は、EBMに関連する高いコストを正当化することができます。 |
生産量 | 限定 | EBM機は、他の付加製造技術に比べて造形速度が遅い。そのため、大量生産には適していない。しかし、EBMは、カスタマイズ、小ロットサイズ、パフォーマンスが最優先される用途で輝きを放ちます。 |
材質の適合性 | 拡大 | EBMは、反応性金属や耐火性金属、一部の合金、さらには特定のセラミックなど、他の多くの3Dプリンティングプロセスよりも幅広い材料を扱うことができます。この多用途性は、要求の厳しい環境における新たな用途への扉を開く。互換性のある材料の開発が続けば、さらに普及が進むだろう。 |
労働と専門知識 | スペシャライズド | EBM装置の操作と保守には、真空システム、電子ビーム技術、金属粉末の取り扱いに関する知識を持つ熟練工が必要である。そのような専門知識の乏しさは、一部の企業にとってハードルとなり、採用率に影響を与える可能性がある。 |
投資収益率(ROI) | 長期 | EBMの経済的な実行可能性は、長期的な視点にかかっている。初期コストは高いが、EBMのメリット(軽量化、部品強度の向上、廃棄物の削減など)は、製品のライフサイクルにわたるコスト削減や性能向上につながることが多い。 |
政府インセンティブ | ポジティブ | EBMを含む積層造形の研究開発に対する政府の支援は、参入障壁を下げ、技術革新を奨励することにより、採用を加速させることができる。税制優遇措置や助成金は、企業がEBM技術に投資するインセンティブを与えることができる。 |
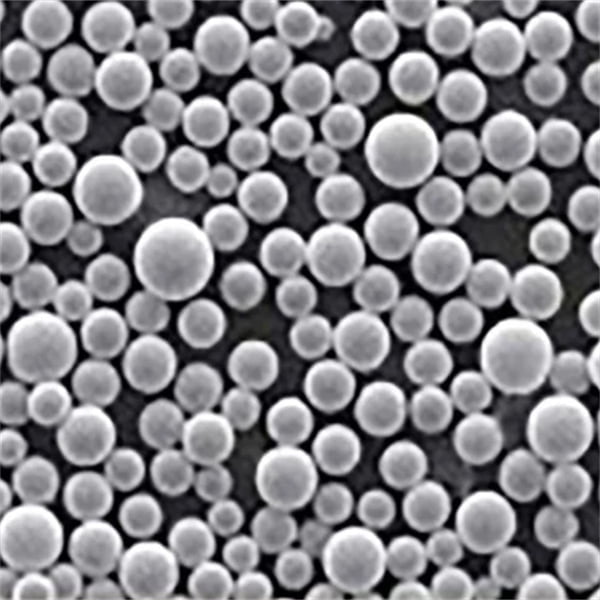
EBMに人気の素材
素材クラス | 合金例 | プロパティ | アプリケーション |
---|---|---|---|
チタン合金 | Ti-6Al-4V, Ti-6Al-4V ELI | * 優れた強度対重量比 * 高い生体適合性 * 耐腐食性 | * 航空宇宙部品(翼、着陸装置) * 医療用インプラント(人工膝関節、歯科用インプラント) * スポーツ用品(ゴルフクラブ、自転車フレーム) |
ニッケル基合金 | インコネル625、インコネル718 | * 卓越した高温強度 * 耐酸化性と耐食性 * 良好な溶接性 | * ジェットエンジン用タービンブレードおよびディスク * 化学処理用熱交換器 * ポンプ用インペラシャフト |
コバルトクロム合金 | CoCrMo、ヘインズ 214 | * 高い耐摩耗性 * 生体適合性(用途限定) * 良好な硬度 | * 人工関節置換術(股関節、膝関節) * 切削工具および摩耗部品 * 歯科インプラント(クロムに関する懸念があるため、使用は制限されている) |
ステンレス鋼 | 17-4PH、316L | * 良好な耐食性 * 適度な強さ * 生体適合性(用途限定) | * 医療器具 * 化学処理装置 * 食品・飲料加工部品 |
新素材 | * タングステン(W) * タンタル(Ta) * ニオブ(Nb) * モリブデン(Mo) | * 超高融点 * 優れた高温特性 * 限定的な研究開発 | * 航空宇宙、防衛、原子力産業における潜在的用途(高融点と極限環境に対する耐性による) |
電子ビーム溶解の利点
ベネフィット | 説明 | インパクト |
---|---|---|
高密度、ニアネットシェイプ部品 | EBMは、使用する金属粉末の理論密度の99.5%を超える密度でパーツを作成します。これにより、他の積層造形法で一般的な気孔(小さなエアポケット)がなくなり、優れた強度、耐疲労性、寸法精度を持つ部品が得られます。 | これにより、航空宇宙産業(タービンブレード、エンジンハウジング)、医療産業(歯科インプラント、補綴物)、自動車産業(軽量、高性能部品)など、要求の厳しい用途向けの機能的金属部品の製造が可能になる。 |
優れた機械的特性 | EBMの高真空環境と精密な溶解プロセスにより、酸化と汚染が最小限に抑えられ、金属粉末本来の特性が維持されます。これにより、優れた引張強度、耐クリープ性(高温での応力下での変形に耐える能力)、破壊靭性を持つ部品が得られます。 | EBMで製造された部品は、大きな荷重に耐え、高温でも効果的に作動し、亀裂の進展に耐えることができるため、過酷な環境下での耐久性と構造的完全性を必要とする用途に最適です。 |
耐火物および反応性金属の加工 | 高融点や反応性に制限された従来の製造方法とは異なり、EBMはチタン合金、タンタル、インコネルなどの難度の高い材料の加工を得意としています。真空環境は酸化を防ぎ、溶融プロセスを正確に制御できるため、製造の成功を確実にします。 | これにより、航空宇宙やバイオメディカルなど、部品に卓越した強度対重量比、生体適合性(生体組織との適合性)、高温性能が要求される産業における設計の可能性が広がる。 |
複雑な形状の設計自由度 | EBMのレイヤー・バイ・レイヤー・アプローチは、従来の技術では不可能だった複雑な内部形状、チャンネル、格子構造の作成を可能にします。この設計の柔軟性により、重量配分が最適化され、熱伝達が改善され、優れた機能性を持つコンポーネントの作成が可能になります。 | この利点は、複雑な冷却チャネルを持つ軽量で高強度の部品がエンジン効率に不可欠な航空宇宙産業などの製品設計に革命をもたらす。また、患者の解剖学的構造に完全に適合する、カスタマイズされた医療用インプラントの作成も可能になる。 |
最小限のサポート体制 | EBMで製造された部品は、固有の強度が高いため、製造工程で必要なサポート構造は最小限です。これにより、後工程の時間と材料の無駄が削減され、最終的な部品にサポート構造が損傷するリスクも低減されます。 | これは、生産時間の短縮、全体的なコストの削減、従来の方法では困難または不可能な複雑な形状の作成につながる。 |
廃棄物の削減 | EBMは付加製造プロセスであり、材料を層ごとに追加して希望の形状を作り出すことを意味する。これは、最終的な形状を達成するために原材料のかなりの部分を除去する機械加工のような減法的技術と比較して、材料の無駄を最小限に抑えることができます。 | この利点は、持続可能性を促進し、材料を最大限に利用することで製造コストを削減する。さらに、ビルドチャンバーから排出される未使用のパウダーは、次のビルドに再利用できる場合が多く、廃棄物をさらに最小限に抑えることができます。 |
概要 電子ビーム溶解機 サプライヤー
航空宇宙、医療、自動車、工業の各分野で、さまざまな老舗工業メーカーや専門的な新規参入企業が、研究から大量生産までスケーラブルな電子ビーム溶解ソリューションを提供している。
表8:主要電子ビーム溶解システムメーカー
サプライヤー | 詳細 | ターゲット・セグメント |
---|---|---|
GEアディティブ | EBM技術のパイオニア | 航空宇宙、医療、自動車 |
シャキー | 最大封筒サイズ | 航空宇宙構造 |
ウェイランド添加剤 | 低予算メタルAMプラットフォーム | 小規模機械工場 |
日本電子 | 研究グレードのEBMシステム | 大学 |
ナノディメンション | マルチマテリアル対応 | エレクトロニクス、防衛 |
業界のリーダーであるArcam EBM(現在はGE Additiveの傘下)は、特許取得済みのソリューションにより早くからリーダーシップを確立し、医療用インプラントや航空宇宙分野で確立されたカテゴリーを支配し続けている。
一方、ウェイランドのような新規参入組は、経済的なスタートプラットフォームで中小メーカーをターゲットにすることで、普及拡大を狙っている。
生産者、研究者、エンドユーザー・グループ間の、材料、部品の適格性、機械の最適化に関する協力は、最終的に、さらなる重要な用途にEBMの浸透を拡大するだろう。
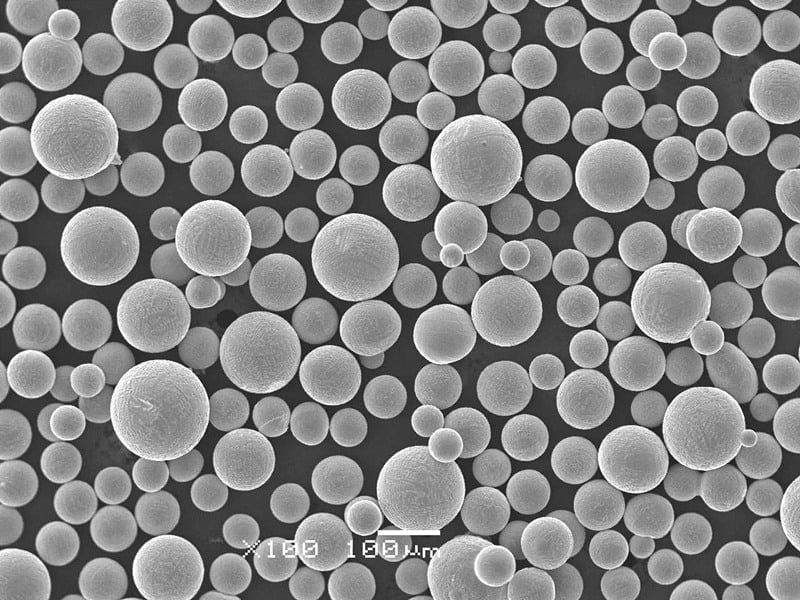
電子ビーム溶解採用の将来展望
優れた生産速度能力に加え、他の金属積層造形や従来のプロセスでは不可能な卓越した機械的特性により、EBMの採用は今後5~7年の間に、航空宇宙、医療機器、自動車、工業の各分野で大規模な拡大が見込まれている。
プロトタイピングから本格的な生産に至るまで、EBMの利点に対する認識が広まることで、企業が3Dプリンティングを活用してサプライチェーンを再構築する際の設備投資が促進されると予想される。
現在商業的に入手可能な、より大きなビルド・エンベロープは、より少ないコンポーネントへのアセンブリの統合を可能にし、在庫ロジスティクスとリードタイムをさらに最適化する。
しかし、システムコストの低下と材料の入手可能性の向上が相まって、中小メーカーのEBM技術へのアクセスは改善され続けなければならない。補助的な粉体ハンドリングツールや後処理ワークフローの合理化も、採用を簡素化する。
全体として、EBMは、代替の金属積層造形プロセスや従来の製造プロセスと比較して、比類のない成膜速度と卓越した結果としての材料特性のおかげで、ますます広範な生産用途に浸透する強い勢いを維持している。
よくあるご質問
Q:EBMをサポートするためには、どのような施設インフラが必要ですか?
A: 機械本体には500平方フィート以上の広さが必要で、粉体ハンドリング・ステーションや後処理にはさらに多くのスペースが必要です。12,000ポンド以上の機器荷重に対応するコンクリート床補強が一般的です。
Q: EBM装置1台につき何人のオペレーターが必要ですか?
A: 1人の技術者が、自動化レベルと生産量に応じて、複数のEBMユニットをサポートすることができます。追加のスタッフが粉体オペレーション、後処理作業、メンテナンス、エンジニアリングを担当します。
Q: EBM技術で処理できない材料は何ですか?
A: 非導電性ポリマーは電子ビームでは加工できません。しかし、EBMは、他の方法で製造可能な導電性金属合金系であれば、実質的にどのようなものにも対応できます。
Q:EBM技術にはどのような安全上のリスクがありますか?
A: 高電力の電子ビーム電圧にはアーク放電の危険があり、適切な囲いと制御が必要です。また、反応性金属粉末への暴露には、火災や吸入の危険性に対するプロトコルが必要であり、保護具やトレーニングが必要となります。
Q: EBMは二次熱処理が必要ですか?
A: 合金によっては、ミクロ組織をさらに強化し、機械的特性を調整するための熱処理が有効な場合があります。しかし、EBMプロセス特有の急速な凝固サイクルと高い予熱温度は、一般的にこれらの後処理工程を不要にします。
シェアする
MET3DP Technology Co., LTDは、中国青島に本社を置く積層造形ソリューションのリーディングプロバイダーです。弊社は3Dプリンティング装置と工業用途の高性能金属粉末を専門としています。
関連記事
Met3DPについて
最新情報
製品
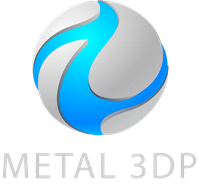
3Dプリンティングと積層造形用金属粉末