Poudre de fer à haute température
Table des matières
Vue d'ensemble
Poudres de fer à haute température sont des poudres métalliques spécialisées composées d'alliages à base de fer, conçues pour fonctionner à des températures élevées dépassant 850°C sans perdre rapidement leur résistance. Les poudres de fer et d'acier conventionnelles s'oxydent et se détériorent plus rapidement au-delà de ce seuil.
En adaptant soigneusement la chimie des poudres et les traitements de transformation, la résistance aux températures élevées et à l'environnement est améliorée. Les principaux domaines d'application exigeant de tels matériaux structurels thermiques extrêmes sont l'automobile, l'aérospatiale, les équipements de production d'énergie et les industries de traitement chimique.
Types de Poudres de fer à haute température
Type | Méthode de production | Caractéristiques principales | Applications (en raison des performances à haute température) |
---|---|---|---|
Poudre de fer carbonique | Décomposition de la vapeur de pentacarbonyle de fer à haute température | - Haute pureté (>99% Fe) - Morphologie des particules sphériques - Surface lisse - Contrôle étroit de la taille - Propriétés magnétiques douces | - Composants magnétiques à haute performance (par exemple, inductances pour les applications à haute fréquence) - Noyaux magnétiques doux pour les transformateurs et les moteurs - Absorbeurs de micro-ondes - Applications catalytiques en raison de leur surface élevée |
Poudre de fer électrolytique | Électrolyse de solutions de chlorure de fer | - Très grande pureté (souvent supérieure à 99,5% Fe) - Particules denses et sphériques - Excellente fluidité - Grande compressibilité | - Noyaux magnétiques doux pour les applications à haute fréquence telles que les transformateurs et les inductances - Composants électroniques nécessitant une grande pureté (par exemple, blindage électromagnétique) - Fabrication additive de pièces métalliques complexes de forme proche du filet - Applications tirant parti d'une bonne conductivité électrique à des températures élevées |
Poudre de fer atomisée à l'eau | Le fer fondu est brisé en fines particules à l'aide de jets d'eau à haute pression. | - Taux de production élevé - Coût le plus bas parmi les poudres de fer à haute température - Teneur en oxygène relativement élevée - Forme irrégulière des particules - Large distribution de la taille des particules | - Applications pour lesquelles le coût est une préoccupation majeure (par exemple, certains procédés de moulage par injection de métaux) - Pièces nécessitant une bonne usinabilité après frittage - Brasage à haute température en raison de la présence d'oxygène - Applications bénéficiant d'un conditionnement irrégulier des particules (par exemple, certains milieux filtrants) |
Poudre de fer recuit sous vide | Traitement ultérieur d'autres poudres de fer (souvent atomisées à l'eau) par recuit dans une atmosphère d'hydrogène. | - Améliore les propriétés de la poudre de base (par exemple, réduit la teneur en oxygène, améliore la forme des particules) - Propriétés personnalisées en fonction de la poudre de départ | - Applications nécessitant un équilibre entre le coût et la performance à haute température (par exemple, certains composants magnétiques doux) - Procédés de fabrication additive nécessitant des caractéristiques de poudre spécifiques - Applications de brasage nécessitant une bonne performance à des températures élevées |
Méthodes de production de poudres à haute température
Méthode | Description | Avantages | Inconvénients | Matériaux typiques produits |
---|---|---|---|---|
Atomisation des gaz | Le métal en fusion est désintégré en fines gouttelettes à l'aide d'un flux de gaz inerte à grande vitesse. | - Poudres de haute pureté - Morphologie des particules sphériques - Distribution granulométrique étroite - Bonne fluidité - Convient à une large gamme de matériaux | - Consommation d'énergie élevée - Coût relativement élevé par rapport à d'autres méthodes - Risque de formation d'oxyde dans certains matériaux | - Alliages à haute température (par exemple, superalliages de nickel, aluminiures de titane) - Métaux réfractaires (par exemple, tungstène, molybdène) - Aciers à outils |
Atomisation de l'eau | Le métal en fusion est brisé en gouttelettes à l'aide de jets d'eau à haute pression. | - Taux de production élevé - Faible coût - Applicable à une large gamme de matériaux | - Forme irrégulière des particules - Large distribution de la taille des particules - Teneur en oxygène plus élevée par rapport à l'atomisation au gaz | - Aciers et fers faiblement alliés - Aciers inoxydables (pour certaines applications) - Poudres pour moulage par injection de métaux (MIM) |
Atomisation par plasma | Le métal en fusion est injecté dans un flux de plasma à haute température et à grande vitesse, ce qui entraîne une solidification rapide. | - Poudres ultrafines (<10 micromètres) - Particules sphériques - Distribution granulométrique étroite - Potentiel de production de phases métastables | - Consommation d'énergie très élevée - Capacité de production limitée - Processus complexe et coûteux | - Poudres métalliques amorphes - Alliages à haute performance pour les applications aérospatiales et les turbines |
Décomposition des carbonyles | Décomposition thermique des carbonyles métalliques (composés métalliques contenant du monoxyde de carbone) à haute température | - Poudres de haute pureté - Morphologie des particules sphériques - Contrôle étroit de la taille et de la morphologie des particules | - Limité à quelques métaux qui forment des carbonyles stables (par exemple, le fer, le nickel) - Processus complexe et relativement lent | - Poudres de fer de haute pureté pour applications magnétiques - Matériaux catalytiques |
Électrolyse | Dépôt de métal à partir d'un sel fondu ou d'une solution aqueuse à l'aide d'un courant électrique | - Poudres de très haute pureté - Particules denses et sphériques - Excellente fluidité | - Taux de production limité - Coût élevé - Applicable à une gamme limitée de matériaux | - Poudre de fer électrolytique pour composants magnétiques de haute performance - Poudres de cuivre pour applications électriques |
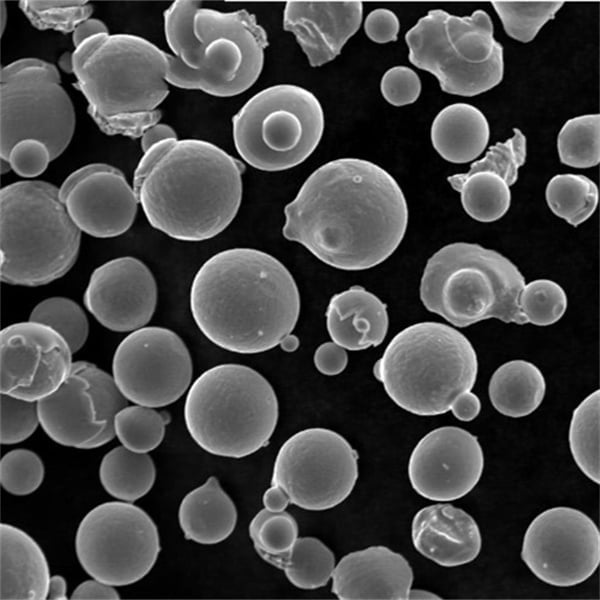
Types d'alliages et compositions
Il existe quatre catégories principales de poudres d'alliages de fer spéciaux conçues pour une utilisation prolongée à des températures supérieures à 850°C :
Poudres d'acier inoxydable austénitique
Les alliages tels que les aciers inoxydables 316L, 304L et 301L contiennent du nickel pour maintenir une structure cristalline austénitique FCC jusqu'à 1100°C et du chrome pour la résistance à l'oxydation par le biais de films de surface protecteurs de chromie (Cr2O3) à haute température.
Élément d'alliage | Rôle | Poids % Gamme |
---|---|---|
Nickel (Ni) | Stabilisateur d'austénite | 8 – 12% |
Chrome (Cr) | Résistance à l'oxydation | 16 – 18% |
Manganèse (Mn) | Résistance et raffinement du grain | Jusqu'à 2% |
Azote (N) | Renforcement | 0.1 – 0.25% |
Avantages: Excellente résistance à chaud, facilité de compactage et de frittage, coût inférieur à celui des superalliages.
Limites: Susceptible de fluer au-dessus de 1000°C, ne convient pas aux applications dynamiques porteuses.
Alliages de fer à haute teneur en nickel
Les alliages nickel-fer contenant 25 à 60 wt% de nickel offrent une combinaison optimale de résistance à haute température, de ténacité et de résistance à la corrosion. Les ajouts de nickel ralentissent considérablement les taux de diffusion et réduisent les changements microstructuraux préjudiciables jusqu'à 1150°C.
Les autres éléments d'alliage clés sont les suivants :
Élément d'alliage | Rôle | Poids % Gamme |
---|---|---|
Nickel (Ni) | Renforcement de la solution solide | 25 – 60% |
Chrome (Cr) | Résistance à l'oxydation | 10 – 25% |
Cobalt (Co) | Améliore les propriétés mécaniques à haute température | 10 – 25% |
Molybdène (Mo) | Résistance au fluage | 2 – 6% |
Avantages: Performance mécanique inégalée à 1100°C+, cinétique de dégradation plus lente. Microstructure thermiquement stable.
Limites: Prix très élevés des alliages, difficultés de contrôle de la porosité, nécessitant une densification HIP.
Alliages de fer renforcés par dispersion d'oxyde
Dans les alliages renforcés par dispersion d'oxyde, de très fines particules d'oxyde d'yttrium inerte (50-100 nm) sont intégrées dans la matrice du matériau. Ces oxydes à l'échelle nanométrique entravent le mouvement des dislocations, ce qui permet de maintenir la résistance à plus de 1000°C.
Élément d'alliage | Rôle | Poids % Gamme |
---|---|---|
Oxyde d'yttrium (Y2O3) | Particules de nano-oxydes assurant la stabilité thermique | 0.25% – 1% |
Chrome (Cr) | Résistance à l'environnement | Jusqu'à 20% |
Aluminium (Al) | Améliore la dispersion des oxydes | Jusqu'à 4% |
Avantages: Stabilité microstructurale et résistance au fluage exceptionnelles dans des conditions de fonctionnement à 1100°C+.
Limites: Coût très élevé, difficultés de mise en œuvre - traditionnellement fabriqué par alliage mécanique et consolidation.
Alliages d'aluminure de fer (FeAl)
Les alliages d'aluminure de fer ayant une teneur en aluminium de 10- 40% offrent une excellente résistance à l'oxydation et à la sulfuration jusqu'à 900°C grâce à la formation d'une couche protectrice durable d'alumine (Al2O3). Le chrome contribue à la protection de la surface.
Élément d'alliage | Rôle | Poids % Gamme |
---|---|---|
Aluminium (Al) | Résistance à l'oxydation | 10 – 40% |
Chrome (Cr) | Améliore la résistance à l'environnement | 5 – 10% |
Carbone, Zr (C, Zr) | Renforçateurs en carbure | Jusqu'à 0,5% |
Avantages: Grande stabilité environnementale, densité inférieure à celle des aciers, facilité de fabrication par rapport aux superalliages.
Limites: Perte de résistance au-dessus de 750°C, mauvaise résistance au fluage, les contraintes appliquées augmentent les phénomènes parasitaires.
Méthodes de production
Des techniques spéciales sont utilisées pour produire des poudres d'alliage de fer à haute température sur mesure avec des caractéristiques appropriées :
Atomisation des gaz
- Le refroidissement rapide et contrôlé du flux de métal en fusion permet de conserver les éléments d'alliage en solution plutôt que de former des précipités.
Sphéroïdisation du plasma
- Les poudres irrégulières issues des processus d'atomisation à l'eau sont refondues à l'aide d'une torche à plasma et re-solidifiées en poudres sphériques idéales pour les méthodes d'AM.
Cycles multiples Frittage-emboutissage
- Les poudres sont compactées à plusieurs reprises à haute température, broyées et tamisées pour affiner la distribution des poudres, ce qui est idéal pour la mise en œuvre du MIM.
Alliage mécanique
- Le broyage à billes de poudres métalliques élémentaires crée des distributions de particules et de grappes nanodispersées dans les alliages ODS
Raffinage des carbonyles
- Production de poudres métalliques d'une très grande pureté lorsque des méthodes de production moins coûteuses entraînent une contamination.
Comparaison des méthodes de production
Méthode | Niveaux de pureté | Teneur en oxygène | Options de morphologie | Débit (tonnes/an) |
---|---|---|---|---|
Atomisation des gaz | Modéré | <1000 ppm | Surtout sphérique | Élevée >20 000 |
Atomisation de l'eau | Faible | 2000-4000 ppm | Irrégulier | Très élevé >50 000 |
Sphéroïdisation du plasma | Moyen | 500-2000 ppm | Sphérique | Faible <5 000 |
Alliage mécanique | Haut | <1500 ppm | Formes de particules variables | Faibles centaines |
Processus de carbonylation | Extrêmement élevé | <200 ppm | Sphérique/nodulaire | Élevée >25 000 |
Méthodes de caractérisation
Plusieurs méthodes analytiques sont essentielles pour qualifier les alliages en poudre à haute température :
Composition chimique
- Les techniques spectrographiques et de chimie humide permettent d'identifier les constituants et les quantités d'éléments, ce qui est nécessaire pour vérifier la conception des alliages.
- Les teneurs en carbone, en soufre, en oxygène et en azote révèlent une contamination induite par le processus qui a une incidence sur les performances du matériau.
Taille et morphologie des particules
- Les granulomètres à diffraction laser déterminent la granulométrie complète de 10 nm à 3 mm.
- L'imagerie SEM permet de visualiser la forme, les caractéristiques de surface, les particules satellites et la porosité, ce qui est utile pour l'évaluation de l'adéquation du processus de fabrication et l'analyse des défauts.
Cristallographie
- La XRD montre les phases présentes, les états de précipitation, l'analyse quantitative des propriétés cristallines.
- Évaluation des effets de l'exposition thermique sur les fractions de phase par l'évolution de la microstructure
Test des propriétés des poudres
- La débitmétrie Hall, la densité apparente et la compressibilité quantifient le comportement de la poudre pour faciliter sa manipulation et sa consolidation.
Applications et utilisations des poudres à haute température
Domaine d'application | Type de poudre (exemples) | Propriétés clés utilisées | Avantages |
---|---|---|---|
Fabrication additive métallique (AM) | Superalliages de nickel atomisés au gaz, aciers inoxydables atomisés à l'eau | - Morphologie sphérique pour une bonne fluidité - Distribution de taille étroite pour un dépôt uniforme - Performance à haute température pour la construction de pièces fonctionnelles | - Permet la création de composants complexes, de forme proche de celle d'un filet - Propriétés des matériaux adaptées à des applications spécifiques - Réduction des déchets par rapport à la fabrication soustractive traditionnelle |
Composants magnétiques haute performance | Poudre de fer carbonique, poudre de fer électrolytique | - Haute pureté pour de faibles pertes d'énergie - Morphologie sphérique pour une bonne densité du noyau - Propriétés magnétiques douces pour un transfert d'énergie efficace | - Amélioration de l'efficacité des transformateurs, des inductances et des moteurs - Réduction des températures de fonctionnement et des niveaux de bruit - Miniaturisation des dispositifs grâce à de meilleures performances magnétiques |
Brasage à haute température | Poudre de fer atomisée à l'eau, alliages de nickel atomisés au gaz | - Point de fusion contrôlé pour le brasage de différents matériaux - Présence d'oxydes (dans certaines poudres) pour améliorer le mouillage et l'adhérence - Résistance à haute température pour des joints robustes | - Assemblage de métaux et d'alliages dissemblables - Création de joints solides et étanches dans des environnements difficiles - Applications dans les secteurs de l'aérospatiale, de l'automobile et de la production d'énergie |
Revêtements par projection thermique | Alliages d'aluminium atomisés à l'eau, superalliages de nickel atomisés au gaz | - Large gamme de points de fusion pour diverses applications de revêtement - Formes de particules irrégulières pour un verrouillage mécanique - Résistance aux hautes températures pour la protection des substrats | - Amélioration de la résistance à l'usure et à la corrosion - Isolation thermique - Restauration de composants usés - Applications dans les moteurs, les turbines et les échangeurs de chaleur |
Moulage par injection de métal (MIM) | Aciers atomisés à l'eau, poudres pré-alliées | - Granulométrie fine pour des géométries de pièces complexes - Bonne fluidité pour un remplissage uniforme des moules - Propriétés de la poudre contrôlées pour une précision dimensionnelle | - Production rentable de pièces métalliques complexes de forme presque nette - Possibilité d'atteindre une résistance et une densité élevées - Applications dans les secteurs de l'automobile, de la médecine et de l'électronique |
Applications catalytiques | Poudre de fer carbonique, métaux de transition atomisés au gaz | - Surface élevée pour des réactions catalytiques efficaces - Structure des pores contrôlée pour une catalyse sélective - Morphologie des particules adaptée pour une activité catalytique améliorée | - Contrôle des émissions dans les systèmes d'échappement automobiles - Réactions chimiques - Production de carburants propres et d'énergie renouvelable |
Spécifications et grades
Les alliages en poudre pour hautes températures doivent répondre à des spécifications minimales en matière de chimie, de propreté, de caractéristiques et de propriétés des particules :
Fonctionnalité | Description | Principales considérations |
---|---|---|
Composition du matériau | Les poudres pour hautes températures se présentent sous la forme de divers matériaux, chacun ayant des propriétés distinctes adaptées à des applications spécifiques. Les matériaux les plus courants sont les suivants Alliages à base de nickel : Offrant une résistance exceptionnelle à l'oxydation et une résistance à haute température, il est idéal pour les composants de moteurs à réaction, les échangeurs de chaleur et les pièces de turbines à gaz. Alliages à base de cobalt : Connus pour leur résistance à l'usure et leur stabilité à la chaleur, ils sont fréquemment utilisés dans les outils de coupe, les pales de turbines et les implants biomédicaux. Aciers inoxydables : Il offre un équilibre entre la résistance à la corrosion et les performances à haute température, et convient aux collecteurs d'échappement, aux chaudières et aux équipements de transformation des aliments. Aciers à outils : Dureté et résistance à l'usure exceptionnelles à des températures élevées, parfaites pour les moules, les matrices et les poinçons. Céramiques réfractaires : Offrant des capacités supérieures d'isolation thermique, il est couramment utilisé dans les revêtements de fours, les creusets et les tuyères de fusées. | Le choix du matériau dépend du cas d'utilisation prévu. Il faut tenir compte de facteurs tels que la température maximale de fonctionnement, les propriétés mécaniques souhaitées (solidité, résistance à l'usure), la résistance à l'oxydation et la compatibilité avec le milieu environnant. |
Taille et distribution des particules | La taille et la distribution des particules de poudre influencent considérablement le processus d'application et les caractéristiques du produit final. Poudres plus fines (10-45 microns) : Améliore la finition de la surface et produit des revêtements minces et lisses. Convient parfaitement au dépôt par pulvérisation électrostatique et aux applications en lit fluidisé. Poudres plus grossières (45-150 microns) : Offrent une meilleure fluidité et permettent de créer des revêtements plus épais. S'applique davantage aux techniques de pressage et de frittage. | La taille des particules est cruciale pour obtenir l'épaisseur de revêtement et l'esthétique souhaitées. Une distribution équilibrée garantit une application efficace et minimise les déchets. |
Capacité d'écoulement | La facilité avec laquelle la poudre s'écoule est essentielle pour une application cohérente et une utilisation efficace. Les poudres ayant une bonne fluidité permettent une alimentation en douceur dans les pistolets de pulvérisation et les trémies, minimisant ainsi l'agglutination et les blocages. | Une fluidité insuffisante peut entraîner des incohérences dans l'application, des revêtements irréguliers et des retards de production. Les fabricants utilisent souvent des additifs ou ajustent la distribution de la taille des particules pour optimiser l'écoulement. |
Densité apparente | Il s'agit du poids de la poudre par unité de volume, ce qui a un impact sur des facteurs tels que les besoins de stockage, la capacité de la trémie et l'épaisseur du revêtement. * Poudres à haute densité apparente : Ils offrent des avantages en termes de stockage efficace et nécessitent potentiellement moins de matériau pour obtenir une épaisseur de revêtement spécifique. * Poudres à faible densité apparente : Ils peuvent nécessiter des espaces de stockage plus importants, mais ils sont plus faciles à manipuler et permettent d'obtenir des revêtements plus épais en une seule application. | La densité apparente influence la manipulation des matériaux, les besoins de stockage et l'efficacité du revêtement. Le choix de la bonne densité dépend des exigences de l'application et de l'équipement disponible. |
Point de fusion et dilatation thermique | Le point de fusion détermine la température maximale d'utilisation de la poudre, tandis que l'expansion thermique détermine les changements de dimension lors du chauffage. * Poudres à point de fusion élevé : Ils peuvent résister à des températures extrêmes, ce qui les rend adaptés à des applications exigeantes telles que les composants de moteurs de fusée. * Poudres à faible expansion thermique : Minimiser les variations dimensionnelles pendant les cycles de chauffage, ce qui est essentiel pour maintenir des tolérances précises dans les environnements à haute température. | Il est essentiel de comprendre ces propriétés pour s'assurer que la poudre peut supporter la température de fonctionnement prévue sans compromettre la fonctionnalité ou la stabilité dimensionnelle. |
Résistance à la corrosion | La capacité du matériau en poudre à résister à la dégradation due à des facteurs environnementaux tels que l'oxydation ou l'attaque chimique est essentielle pour une performance à long terme. Poudres à haute résistance à la corrosion : Ils conservent leur intégrité dans les environnements difficiles, ce qui est idéal pour les applications exposées aux produits chimiques, à une humidité élevée ou au brouillard salin. Poudres moins résistantes à la corrosion : Peut nécessiter des traitements de surface supplémentaires ou des revêtements protecteurs pour une durée de vie plus longue. | Le choix de la résistance à la corrosion dépend des conditions d'exposition prévues. Le choix d'une poudre hautement résistante à la corrosion peut prolonger la durée de vie du produit final. |
Analyse des coûts des poudres à haute température
Facteur | Description | Impact sur les coûts |
---|---|---|
Type de matériau | Comme nous l'avons vu précédemment, les poudres pour hautes températures sont disponibles dans différents matériaux, chacun avec des prix distincts. Alliages à base de nickel : Généralement les plus chers en raison de leurs performances exceptionnelles à haute température et de leurs processus de fabrication complexes. Alliages à base de cobalt : Ils se situent souvent dans une fourchette de prix similaire à celle des alliages à base de nickel, mais peuvent varier en fonction de la teneur en cobalt et des propriétés souhaitées. Aciers inoxydables : Généralement plus abordable que les alliages à base de nickel ou de cobalt, il offre un équilibre entre coût et performance. Aciers à outils : Le coût peut varier en fonction des éléments d'alliage spécifiques et des propriétés souhaitées. Généralement moins coûteux que les options à base de nickel ou de cobalt. Céramiques réfractaires : Tout en présentant une excellente résistance à la chaleur, certaines céramiques réfractaires peuvent être relativement peu coûteuses, en particulier les matériaux courants comme l'alumine. Toutefois, les céramiques plus spécialisées ou de haute pureté peuvent être nettement plus coûteuses. | Le choix des matériaux influe considérablement sur le coût global du projet. Évaluer soigneusement les exigences de performance en fonction des contraintes budgétaires. |
Pureté de la poudre | Le niveau de pureté d'une poudre haute température a une incidence directe sur ses propriétés et son prix. Poudres de haute pureté : Ils offrent des caractéristiques de performance supérieures, telles qu'une résistance accrue, une meilleure résistance à l'oxydation et un meilleur comportement au frittage. Cependant, ils coûtent cher en raison des processus de purification complexes qu'ils impliquent. Poudres de moindre pureté : Peut suffire pour certaines applications où il n'est pas essentiel de maximiser les performances. Ces poudres sont généralement plus économiques. | Examinez le compromis entre les performances souhaitées et le rapport coût-efficacité. Dans certains cas, une légère réduction de la pureté peut être acceptable si elle se traduit par des économies significatives. |
Taille et distribution des particules | La taille et la distribution des particules de poudre peuvent influencer à la fois le coût du matériau et les coûts de traitement. Poudres plus fines : Ils nécessitent généralement des processus de fabrication plus complexes et plus gourmands en énergie, ce qui se traduit par un coût plus élevé par unité de poids. Poudres plus grossières : Bien qu'ils soient potentiellement moins coûteux à produire, ils peuvent nécessiter des étapes de traitement supplémentaires (par exemple, le broyage) pour obtenir la distribution granulométrique souhaitée pour des applications spécifiques, ce qui pourrait annuler une partie de l'avantage initial en termes de coûts. | L'optimisation de la taille des particules en fonction de l'application choisie permet de trouver un équilibre entre les coûts des matériaux et les coûts de traitement. |
Quantité minimale de commande (MOQ) | De nombreux fournisseurs fixent des quantités minimales de commande (MOQ) pour les poudres à haute température. Grandes quantités : Peut entraîner des coûts initiaux importants, en particulier pour les poudres les moins utilisées ou les poudres spécialisées. MOQs plus petits : Peut être disponible à un prix plus élevé en raison de la manipulation et de l'administration accrues pour les petits lots. | Tenez compte des exigences du projet et des possibilités de gaspillage. Si une grande quantité n'est pas entièrement utilisée, il convient de rechercher d'autres fournisseurs proposant des quantités plus faibles ou de collaborer avec d'autres utilisateurs pour partager une commande plus importante. |
Réputation et localisation des fournisseurs | La réputation du fournisseur de poudre a un impact significatif sur le coût et la réussite globale du projet. Fournisseurs réputés : Mettre en œuvre des mesures rigoureuses de contrôle de la qualité, afin de garantir la constance des propriétés des matériaux et de minimiser le risque de recevoir des poudres inutilisables. Cette fiabilité peut avoir un prix. Fournisseurs moins bien établis : Ils peuvent proposer des prix plus bas, mais ne disposent pas de procédures rigoureuses de contrôle de la qualité, ce qui peut entraîner des taux de rejet plus élevés ou des performances irrégulières. | Évaluez soigneusement les qualifications des fournisseurs et donnez la priorité à une qualité constante plutôt qu'à des coûts initiaux potentiellement plus bas. |
Délai de livraison | Le temps nécessaire à la livraison de la poudre peut influencer le calendrier du projet et avoir un impact potentiel sur les coûts. Délais plus courts : Peut nécessiter des options d'expédition accélérée, qui peuvent être plus coûteuses. Délais d'exécution plus longs : Ils peuvent être plus rentables mais nécessitent une planification et une gestion des stocks minutieuses pour éviter les retards de production. | Évaluer le compromis entre le coût et le calendrier du projet. Si les délais d'exécution sont critiques, étudiez les possibilités d'expédition accélérée ou de stock tampon pour atténuer les retards potentiels. |
Avantages et inconvénients des alliages de fer à haute température
Fonctionnalité | Avantage | Inconvénient |
---|---|---|
Rapport coût-efficacité | Par rapport à d'autres matériaux haute température tels que les superalliages à base de nickel ou de cobalt, les alliages à base de fer présentent un avantage significatif en termes de coûts. Le fer est un élément facilement disponible, ce qui rend la production de ces alliages généralement moins coûteuse. | Bien que rentables, les alliages de fer à haute température n'atteignent pas toujours le même niveau de performance que certaines options à base de nickel ou de cobalt en termes de température de fonctionnement maximale ou de propriétés mécaniques spécifiques. |
Résistance à l'oxydation | Certains alliages de fer peuvent présenter une bonne résistance à l'oxydation à des températures modérées (jusqu'à environ 700°C). Les éléments d'alliage comme le chrome et l'aluminium contribuent à la formation d'une couche d'oxyde protectrice qui empêche la poursuite de l'oxydation. | La résistance à l'oxydation des alliages de fer est généralement inférieure à celle des superalliages à base de nickel ou de cobalt, qui peuvent conserver leur intégrité à des températures beaucoup plus élevées. Les alliages de fer peuvent nécessiter des traitements de surface ou des revêtements supplémentaires pour prolonger leur durée de vie dans des environnements très oxydants. |
Solidité et résistance au fluage | Bien qu'ils ne soient pas aussi performants que les meilleurs, certains alliages de fer peuvent offrir une solidité et une résistance au fluage adéquates à des températures élevées. Des éléments d'alliage spécifiques comme le molybdène et le vanadium peuvent améliorer ces propriétés, ce qui les rend adaptés à diverses applications industrielles. | La résistance à haute température et la résistance au fluage des alliages de fer sont généralement inférieures à celles des superalliages à base de nickel ou de cobalt. Pour les applications nécessitant des performances exceptionnelles à des températures extrêmes, d'autres matériaux peuvent s'avérer nécessaires. |
Soudabilité et usinabilité | Les alliages à base de fer offrent généralement une bonne soudabilité et une bonne usinabilité par rapport à d'autres matériaux à haute température. Cela se traduit par une fabrication plus facile et des coûts de traitement globaux moins élevés. | Bien qu'ils soient soudables et usinables, les alliages de fer peuvent nécessiter des techniques de soudage ou des procédures d'usinage spécifiques pour éviter de compromettre leurs propriétés au niveau du joint de soudure ou d'introduire des contraintes d'usinage. |
Recyclabilité | Le fer est l'un des métaux les plus recyclés au monde. Les alliages de fer à haute température peuvent potentiellement être recyclés à la fin de leur durée de vie, minimisant ainsi l'impact sur l'environnement et offrant un certain degré de durabilité des matériaux. | Le processus de recyclage des alliages de fer complexes peut être plus complexe que celui du fer pur, et des facteurs tels que les éléments d'alliage et les contaminants de surface peuvent influer sur la recyclabilité. |
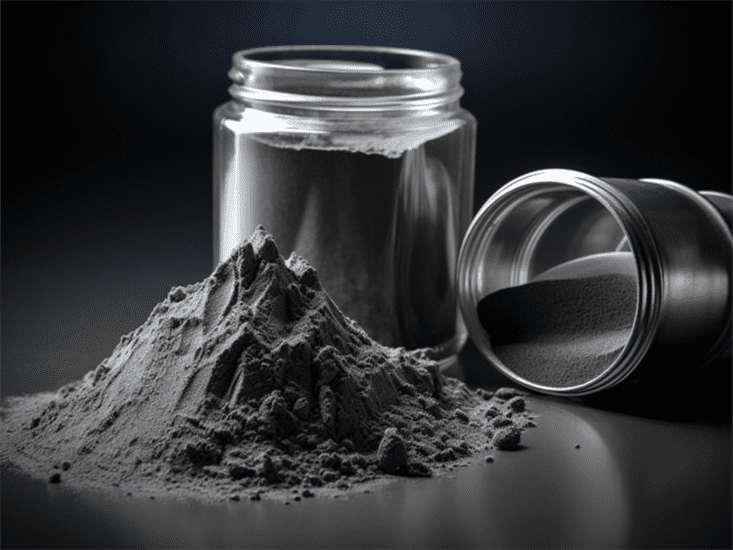
FAQ
Q : Quelle est la distribution granulométrique typique utilisée pour les poudres d'acier inoxydable à haute température dans l'AM métal ?
R : Pour les procédés de fusion sur lit de poudre tels que la fusion sélective par laser (SLM) et la fusion par faisceau d'électrons (EBM), la gamme courante est constituée de fractions de taille de 15 μm - 45 μm. Des distributions plus fines peuvent améliorer la résolution, mais nuisent à l'étalement de la poudre pendant le dépôt des couches et réduisent les caractéristiques d'écoulement.
Q : Quelles sont les vitesses de refroidissement de l'atomisation à gaz qui permettent d'obtenir des compositions optimales de poudres d'alliage ?
R : Pour obtenir la meilleure combinaison de rétention chimique et de morphologie de poudre appropriée, des vitesses de solidification comprises entre 1000 et 3000°C par seconde sont largement utilisées pour les poudres d'acier inoxydable et de superalliage à haute température.
Q : Pourquoi des niveaux élevés de particules d'oxyde sont-ils préjudiciables dans les alliages de fer à haute température ?
R : Au cours du service, les oxydes présents peuvent s'épaissir et migrer pour former des populations d'oxydes moins protectrices et moins stables, ce qui accélère l'attaque des environnements oxydants, sulfurés, carburigènes ou chlorés, réduisant ainsi la durée de vie des composants. Il est nécessaire de déterminer et de contrôler soigneusement les niveaux d'oxygène en fonction des températures d'exposition maximales et des conditions de fonctionnement lors de l'élaboration des alliages.
Q : Quelles méthodes peuvent être utilisées pour augmenter la densité de la poudre à >95% théorique ?
R : Le pressage isostatique à chaud est couramment appliqué aux composants en acier inoxydable ou en superalliage à haute température après la fabrication initiale par AM ou MIM afin d'éliminer les pores résiduels, ce qui permet d'obtenir des performances matérielles proches de celles des alliages corroyés dans les mêmes états de traitement thermique renforcé. Les densités proches de la théorie garantissent la robustesse mécanique.
Q : Pourquoi le contrôle de l'azote en dessous de 1000 ppm est-il essentiel dans les alliages de cuivre à haute résistance et à haute conductivité ?
R : Le ramassage de l'azote forme des phases de nitrure très dures et cassantes qui réduisent considérablement les conductivités thermique et électrique, réduisant ainsi la fonctionnalité dans les applications de gestion thermique, tout en diminuant la formabilité et la ductilité au cours de la fabrication.
Partager sur
MET3DP Technology Co. est un fournisseur de premier plan de solutions de fabrication additive dont le siège se trouve à Qingdao, en Chine. Notre société est spécialisée dans les équipements d'impression 3D et les poudres métalliques de haute performance pour les applications industrielles.
Articles connexes
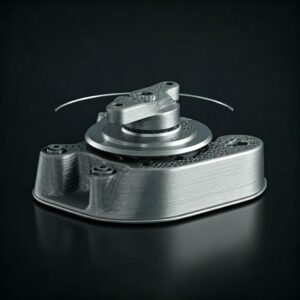
Supports imprimés en 3D pour les capteurs radar automobiles : Précision et performance
Lire la suite "À propos de Met3DP
Mise à jour récente
Notre produit
CONTACTEZ-NOUS
Vous avez des questions ? Envoyez-nous un message dès maintenant ! Nous répondrons à votre demande avec toute une équipe dès réception de votre message.
Obtenir les informations de Metal3DP
Brochure du produit
Obtenir les derniers produits et la liste des prix
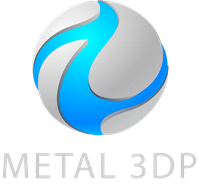
Poudres métalliques pour l'impression 3D et la fabrication additive
PRODUIT
cONTACT INFO
- Ville de Qingdao, Shandong, Chine
- [email protected]
- [email protected]
- +86 19116340731