High Temperature Iron Powder
Table of Contents
Overview
High temperature iron powders are specialized metallic powders made from iron-based alloys designed to operate at elevated temperatures exceeding 850°C without rapidly losing strength. Conventional iron and steel powders oxidize and deteriorate faster beyond this threshold.
By carefully tailoring powder chemistry and processing treatments, high temperature strength and environmental resistance is enhanced. Key application areas demanding such extreme thermal structural materials include automotive, aerospace, power generation equipment and chemical processing industries.
Types of High Temperature Iron Powders
Type | Production Method | Key Characteristics | Applications (Due to High-Temperature Performance) |
---|---|---|---|
Carbonyl Iron Powder | Decomposition of iron pentacarbonyl vapor at high temperatures | – High purity (>99% Fe) – Spherical particle morphology – Smooth surface – Tight size control – Soft magnetic properties | – High-performance magnetic components (e.g., inductors for high-frequency applications) – Soft magnetic cores for transformers and motors – Microwave absorbers – Catalyst applications due to high surface area |
Electrolytic Iron Powder | Electrolysis of iron chloride solutions | – Very high purity (often exceeding 99.5% Fe) – Dense, spherical particles – Excellent flowability – High compressibility | – Soft magnetic cores for high-frequency applications like transformers and inductors – Electronic components requiring high purity (e.g., electromagnetic shielding) – Additive manufacturing of complex, near-net-shape metal parts – Applications leveraging good electrical conductivity at elevated temperatures |
Water Atomized Iron Powder | Molten iron is broken into fine particles using high-pressure water jets | – High production rate – Lowest cost among high-temperature iron powders – Relatively high oxygen content – Irregular particle shapes – Broad particle size distribution | – Applications where cost is a primary concern (e.g., some metal injection molding processes) – Parts requiring good machinability after sintering – High-temperature brazing due to presence of oxygen – Applications benefiting from irregular particle packing (e.g., some filtration media) |
Vacuum Annealed Iron Powder | Further processing of other iron powders (often water atomized) by annealing in a hydrogen atmosphere | – Improves properties of base powder (e.g., reduces oxygen content, enhances particle shape) – Tailored properties based on the starting powder | – Applications requiring a balance between cost and high-temperature performance (e.g., some soft magnetic components) – Additive manufacturing processes where specific powder characteristics are needed – Brazing applications demanding good performance at elevated temperatures |
Production Methods for High Temperature Powders
Method | Description | Advantages | Disadvantages | Typical Materials Produced |
---|---|---|---|---|
Gas Atomization | Molten metal is disintegrated into fine droplets using a high-velocity inert gas stream | – High purity powders – Spherical particle morphology – Narrow size distribution – Good flowability – Suitable for a wide range of materials | – High energy consumption – Relatively expensive compared to some other methods – Potential for oxide formation in some materials | – High-temperature alloys (e.g., nickel superalloys, titanium aluminides) – Refractory metals (e.g., tungsten, molybdenum) – Tool steels |
Water Atomization | Molten metal is broken up into droplets using high-pressure water jets | – High production rate – Low cost – Applicable to a wide range of materials | – Irregular particle shapes – Broad particle size distribution – Higher oxygen content compared to gas atomization | – Low-alloy steels and irons – Stainless steels (for some applications) – Metal injection molding (MIM) powders |
Plasma Atomization | Molten metal is injected into a high-temperature, high-velocity plasma stream, leading to rapid solidification | – Ultrafine powders (<10 micrometers) – Spherical particles – Narrow size distribution – Potential for producing metastable phases | – Very high energy consumption – Limited production capacity – Complex and expensive process | – Amorphous metal powders – High-performance alloys for aerospace and turbine applications |
Carbonyl Decomposition | Thermal decomposition of metal carbonyls (metal compounds containing carbon monoxide) at high temperatures | – High purity powders – Spherical particle morphology – Tight control over particle size and morphology | – Limited to a few metals that form stable carbonyls (e.g., iron, nickel) – Complex and relatively slow process | – High-purity iron powders for magnetic applications – Catalyst materials |
Electrolysis | Deposition of metal from a molten salt or aqueous solution using an electric current | – Very high purity powders – Dense, spherical particles – Excellent flowability | – Limited production rate – High cost – Applicable to a limited range of materials | – Electrolytic iron powder for high-performance magnetic components – Copper powders for electrical applications |
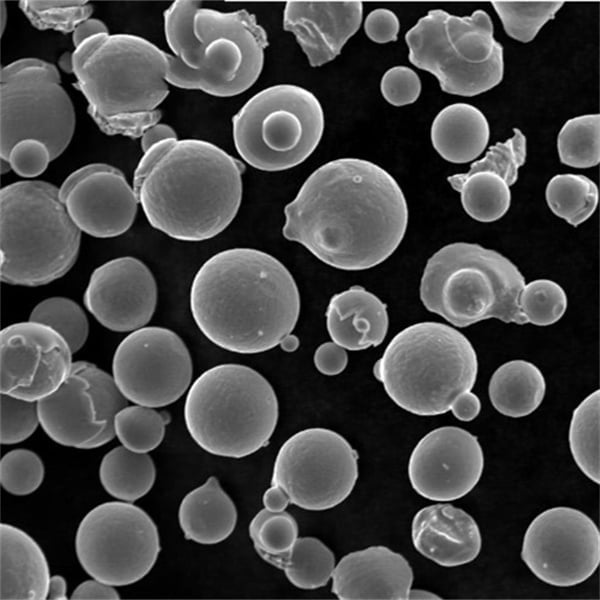
Alloy Types and Compositions
There are four primary categories of specialty iron alloy powders designed for prolonged use at temperatures exceeding 850°C:
Austenitic Stainless Steel Powders
Alloys like 316L, 304L, and 301L stainless steels contain nickel to maintain an austenitic FCC crystal structure up to 1100°C and chromium for oxidation resistance through protective chromia (Cr2O3) surface films at high temperatures.
Alloying Element | Role | Weight % Range |
---|---|---|
Nickel (Ni) | Austenite stabilizer | 8 – 12% |
Chromium (Cr) | Oxidation resistance | 16 – 18% |
Manganese (Mn) | Strength and grain refinement | Up to 2% |
Nitrogen (N) | Strengthening | 0.1 – 0.25% |
Benefits: Excellent “hot strength”, ease of compaction and sintering, lower cost than superalloys.
Limitations: Prone to creep above 1000°C, not suitable for load bearing dynamic applications.
High Nickel Iron Alloys
Nickel-iron alloys containing 25 – 60 wt% nickel offer the optimum combination of high temperature strength, toughness and corrosion resistance. Nickel additions dramatically slow down diffusion rates and reduce detrimental microstructural changes up to 1150°C.
Other key alloying elements are:
Alloying Element | Role | Weight % Range |
---|---|---|
Nickel (Ni) | Solid solution strengthening | 25 – 60% |
Chromium (Cr) | Oxidation resistance | 10 – 25% |
Cobalt (Co) | Enhances high temperature mechanical properties | 10 – 25% |
Molybdenum (Mo) | Creep resistance | 2 – 6% |
Benefits: Unmatched mechanical performance at 1100°C+, slower degradation kinetics. Thermally stable microstructure.
Limitations: Very high alloy prices, porosity control difficulties, requiring HIP densification.
Oxide Dispersion Strengthened Iron Alloys
In oxide dispersion strengthened alloys, very fine (50-100 nm) inert yttrium oxide particles are embedded within the material matrix. These nano-scale oxides hinder dislocation motion thereby maintaining strength above 1000°C.
Alloying Element | Role | Weight % Range |
---|---|---|
Yttrium oxide (Y2O3) | Nano-oxide particles providing thermal stability | 0.25% – 1% |
Chromium (Cr) | Environmental resistance | Up to 20% |
Aluminum (Al) | Enhances oxide dispersion | Up to 4% |
Benefits: Exceptional microstructural stability and creep strength at 1100°C+ operating conditions.
Limitations: Very high cost, processing difficulties – traditionally made through mechanical alloying and consolidation.
Iron Aluminide (FeAl) Alloys
Iron aluminide alloys having 10- 40% aluminum content offer excellent oxidation and sulfidation resistance up to 900°C through the formation of a durable alumina (Al2O3) protective top layer. Chromium aids surface protection.
Alloying Element | Role | Weight % Range |
---|---|---|
Aluminum (Al) | Oxidation resistance | 10 – 40% |
Chromium (Cr) | Enhances environmental resistance | 5 – 10% |
Carbon, Zr (C, Zr) | Carbide strengtheners | Up to 0.5% |
Benefits: Great environmental stability, lower densities than steels, ease of fabrication relative to superalloys.
Limitations: Strength loss above 750°C, poor creep resistance, applied stresses increase pest phenomena.
Production Methods
Special techniques are utilized to produce tailored high temperature iron alloy powders with suitable characteristics:
Gas Atomization
- Controlled rapid cooling of the molten metal stream enables retention of alloying elements in solution rather than formation of precipitates
Plasma Spheroidization
- Irregular powders from water atomization processes are re-melted using a plasma torch and re-solidified into spherical powders ideal for AM methods
Multiple Cycles Sinter-Crush
- Powders are repeatedly compacted at high temperatures, crushed and sieved to refine powder distribution ideal for MIM processability
Mechanical Alloying
- Ball milling elemental metal powders creates nano-dispersed particle and cluster distributions in ODS alloys
Carbonyl Refining
- Produces extremely high purity metal powders when lower cost production methods yield contamination
Comparison of Production Methods
Method | Purity Levels | Oxygen Content | Morphology Options | Throughput (tons/year) |
---|---|---|---|---|
Gas Atomization | Moderate | <1000 ppm | Mostly spherical | High >20,000 |
Water Atomization | Low | 2000-4000 ppm | Irregular | Very high >50,000 |
Plasma Spheroidization | Medium | 500-2000 ppm | Spherical | Low <5,000 |
Mechanical Alloying | High | <1500 ppm | Variable particle shapes | Low hundreds |
Carbonyl Process | Extremely High | <200 ppm | Spherical/nodular | High >25,000 |
Characterization Methods
Several analytical methods are vital for qualifying high temperature powder alloys:
Chemical Composition
- Spectrographic and wet chemistry techniques identify elemental constituents and quantities – necessary for alloy design verification
- Carbon, sulfur, oxygen, nitrogen contents show process-induced contamination that impacts material performance
Particle Size and Morphology
- Laser diffraction particle size analyzers determine full granulometry from 10 nm to 3 mm sizes
- SEM imaging visualizes shape, surface features, satellite particles, porosity useful for build process suitability assessments and defect analysis
Crystallography
- XRD shows phases present, precipitation states, quantitative analysis of crystalline properties
- Assesses effects of thermal exposure on phase fractions by microstructural evolution
Powder Properties Testing
- Hall flowmetry, apparent density and compressibility quantify powder behavior for ease of handling and consolidation
Applications and Uses of High Temperature Powders
Application Area | Powder Type (Examples) | Key Properties Utilized | Benefits |
---|---|---|---|
Metal Additive Manufacturing (AM) | Gas-atomized nickel superalloys, water-atomized stainless steels | – Spherical morphology for good flowability – Narrow size distribution for even deposition – High-temperature performance for building functional parts | – Enables creation of complex, near-net-shape components – Tailored material properties for specific applications – Reduced waste compared to traditional subtractive manufacturing |
High-Performance Magnetic Components | Carbonyl iron powder, electrolytic iron powder | – High purity for low energy losses – Spherical morphology for good core density – Soft magnetic properties for efficient energy transfer | – Improved efficiency in transformers, inductors, and motors – Reduced operating temperatures and noise levels – Miniaturization of devices due to better magnetic performance |
High-Temperature Brazing | Water-atomized iron powder, gas-atomized nickel alloys | – Controlled melting point for brazing different materials – Presence of oxides (in some powders) for improved wetting and bonding – High-temperature strength for robust joints | – Joining dissimilar metals and alloys – Creating strong, leak-proof seals in harsh environments – Applications in aerospace, automotive, and power generation industries |
Thermal Sprayed Coatings | Water-atomized aluminum alloys, gas-atomized nickel superalloys | – Wide range of melting points for diverse coating applications – Irregular particle shapes for mechanical interlocking – High-temperature resistance for protecting substrates | – Improved wear and corrosion resistance – Thermal insulation – Restoration of worn-out components – Applications in engines, turbines, and heat exchangers |
Metal Injection Molding (MIM) | Water-atomized steels, pre-alloyed powders | – Fine particle size for intricate part geometries – Good flowability for uniform mold filling – Controlled powder properties for dimensional accuracy | – Cost-effective production of complex, near-net-shape metal parts – High strength and density achievable – Applications in automotive, medical, and electronics industries |
Catalytic Applications | Carbonyl iron powder, gas-atomized transition metals | – High surface area for efficient catalytic reactions – Controlled pore structure for selective catalysis – Tailored particle morphology for improved catalyst activity | – Emission control in automotive exhaust systems – Chemical processing reactions – Production of clean fuels and renewable energy |
Specifications and Grades
High temperature powder alloys must meet minimum specifications for chemistry, cleanliness, particle characteristics and properties:
Feature | Description | Key Considerations |
---|---|---|
Material Composition | High temperature powders come in a variety of materials, each with distinct properties suited for specific applications. Common materials include: Nickel-based alloys: Offering exceptional resistance to oxidation and high-temperature strength, ideal for jet engine components, heat exchangers, and gas turbine parts. Cobalt-based alloys: Known for their wear resistance and heat stability, frequently used in cutting tools, turbine blades, and biomedical implants. Stainless steels: Providing a balance of corrosion resistance and high-temperature performance, suitable for exhaust manifolds, boilers, and food processing equipment. Tool steels: Delivering exceptional hardness and wear resistance at elevated temperatures, perfect for molds, dies, and punches. Refractory ceramics: Offering superior heat insulation capabilities, commonly used in furnace linings, crucibles, and rocket nozzles. | Material selection hinges on the intended use case. Consider factors like peak operating temperature, desired mechanical properties (strength, wear resistance), oxidation resistance, and compatibility with the surrounding environment. |
Particle Size & Distribution | The size and distribution of powder particles significantly influence the application process and final product characteristics. Finer powders (10-45 microns): Enhance surface finish and produce thin, smooth coatings. Well-suited for electrostatic spray deposition and fluidized bed applications. Coarser powders (45-150 microns): Offer better flowability and can create thicker coatings. More applicable for press and sinter techniques. | Particle size is crucial for achieving the desired coating thickness and aesthetics. A balanced distribution ensures efficient application and minimizes waste. |
Flowability | The ease with which powder flows is essential for consistent application and efficient use. Powders with good flowability enable smooth feeding into spray guns and hoppers, minimizing clumping and blockages. | Inadequate flowability can lead to application inconsistencies, uneven coatings, and production delays. Manufacturers often utilize additives or adjust particle size distribution to optimize flow. |
Apparent Density | This refers to the weight of powder per unit volume, impacting factors like storage requirements, hopper capacity, and coating thickness. * High apparent density powders: Offer advantages in terms of efficient storage and potentially require less material for achieving a specific coating thickness. * Low apparent density powders: May require larger storage spaces but can be easier to handle and create thicker coatings with a single application. | Apparent density influences material handling, storage needs, and coating efficiency. Selecting the right density depends on application requirements and available equipment. |
Melting Point & Thermal Expansion | The melting point determines the maximum usable temperature of the powder, while thermal expansion dictates dimensional changes upon heating. * High melting point powders: Can withstand extreme temperatures, making them suitable for demanding applications like rocket engine components. * Low thermal expansion powders: Minimize dimensional changes during heating cycles, crucial for maintaining precise tolerances in high-temperature environments. | Understanding these properties is vital for ensuring the powder can withstand the intended operating temperature without compromising functionality or dimensional stability. |
Corrosion Resistance | The ability of the powder material to resist degradation from environmental factors like oxidation or chemical attack is critical for long-term performance. High corrosion-resistant powders: Maintain their integrity in harsh environments, ideal for applications exposed to chemicals, high humidity, or salt spray. Lower corrosion-resistant powders: Might require additional surface treatments or protective coatings for extended service life. | Corrosion resistance selection depends on the anticipated exposure conditions. Choosing a highly corrosion-resistant powder can extend the lifespan of the final product. |
Cost Analysis of High Temperature Powders
Factor | Description | Impact on Cost |
---|---|---|
Material Type | As explored previously, high temperature powders come in various materials, each with distinct price points. Nickel-based alloys: Generally the most expensive due to their exceptional high-temperature performance and complex manufacturing processes. Cobalt-based alloys: Often fall within a similar price range to nickel-based alloys but can vary depending on the specific cobalt content and desired properties. Stainless steels: Typically more affordable than nickel or cobalt-based alloys, offering a balance between cost and performance. Tool steels: Can range in cost depending on the specific alloying elements and desired properties. Generally less expensive than nickel or cobalt-based options. Refractory ceramics: While exhibiting excellent heat resistance, some refractory ceramics can be relatively inexpensive, particularly for common materials like alumina. However, more specialized or high-purity ceramics can be significantly more costly. | Material selection significantly influences overall project cost. Carefully evaluate performance requirements against budget constraints. |
Powder Purity | The level of purity in a high-temperature powder directly affects its properties and price. High purity powders: Offer superior performance characteristics like increased strength, improved oxidation resistance, and better sintering behavior. However, they come at a premium due to the complex purification processes involved. Lower purity powders: May be sufficient for some applications where maximizing performance is not critical. These powders are typically more cost-effective. | Consider the trade-off between achieving desired performance and cost efficiency. In some cases, a slight reduction in purity might be acceptable if it translates to significant cost savings. |
Particle Size & Distribution | The size and distribution of powder particles can influence both material cost and processing costs. Finer powders: Generally require more complex and energy-intensive manufacturing processes, leading to a higher cost per unit weight. Coarser powders: While potentially less expensive to produce, they might necessitate additional processing steps (e.g., grinding) to achieve the desired particle size distribution for specific applications, potentially offsetting some of the initial cost advantage. | Optimizing particle size for the chosen application can help strike a balance between material and processing costs. |
Minimum Order Quantity (MOQ) | Many suppliers establish minimum order quantities (MOQ) for high-temperature powders. Large MOQs: Can lead to significant upfront costs, particularly for less commonly used or specialized powders. Smaller MOQs: May be available at a premium price due to the increased handling and administration involved for smaller batches. | Consider the project requirements and potential for waste. If a large MOQ is not fully utilized, explore alternative suppliers offering smaller quantities or collaborate with other users to share a larger order. |
Supplier Reputation & Location | The reputation of the powder supplier significantly impacts cost and overall project success. Reputable suppliers: Implement stringent quality control measures, ensuring consistent material properties and minimizing the risk of receiving unusable powders. This reliability can come at a premium. Less established suppliers: May offer lower prices but might lack rigorous quality control procedures, potentially leading to higher rejection rates or inconsistent performance. | Carefully evaluate supplier qualifications and prioritize consistent quality over potentially lower initial costs. |
Delivery Lead Time | The time it takes for the powder to be delivered can influence project timelines and potentially impact costs. Shorter lead times: May require expedited shipping options, which can be more expensive. Longer lead times: Can be more cost-effective but necessitate careful planning and inventory management to avoid production delays. | Evaluate the trade-off between cost and project schedule. If lead times are critical, explore options for expedited shipping or buffer stock to mitigate potential delays. |
Pros and Cons of High Temperature Iron Alloys
Feature | Advantage | Disadvantage |
---|---|---|
Cost-Effectiveness | Compared to other high-temperature materials like nickel or cobalt-based superalloys, iron-based alloys offer a significant cost advantage. Iron is a readily available element, making these alloys generally less expensive to produce. | While cost-effective, high-temperature iron alloys may not always achieve the same level of performance as some nickel or cobalt-based options in terms of peak operating temperature or specific mechanical properties. |
Oxidation Resistance | Certain iron alloys can exhibit good oxidation resistance at moderate temperatures (up to around 700°C). Alloying elements like chromium and aluminum help form a protective oxide layer that hinders further oxidation. | The oxidation resistance of iron alloys generally falls short of nickel or cobalt-based superalloys, which can maintain their integrity at much higher temperatures. Iron alloys might require additional surface treatments or coatings for extended service life in highly oxidizing environments. |
Strength & Creep Resistance | While not on par with the top performers, some iron alloys can deliver adequate strength and creep resistance at elevated temperatures. Specific alloying elements like molybdenum and vanadium can enhance these properties, making them suitable for various industrial applications. | The high-temperature strength and creep resistance of iron alloys are typically inferior to those of nickel or cobalt-based superalloys. For applications requiring exceptional performance at extreme temperatures, other material options might be necessary. |
Weldability & Machinability | Iron-based alloys generally offer good weldability and machinability compared to some other high-temperature materials. This translates to easier fabrication and lower overall processing costs. | While weldable and machinable, iron alloys might require specific welding techniques or machining procedures to avoid compromising their properties at the weld joint or introducing machining stresses. |
Recyclability | Iron is one of the most recycled metals globally. High-temperature iron alloys can potentially be recycled at the end of their service life, minimizing environmental impact and offering a degree of material sustainability. | The recycling process for complex iron alloys might be more involved compared to pure iron, and factors like alloying elements and surface contaminants can influence recyclability. |
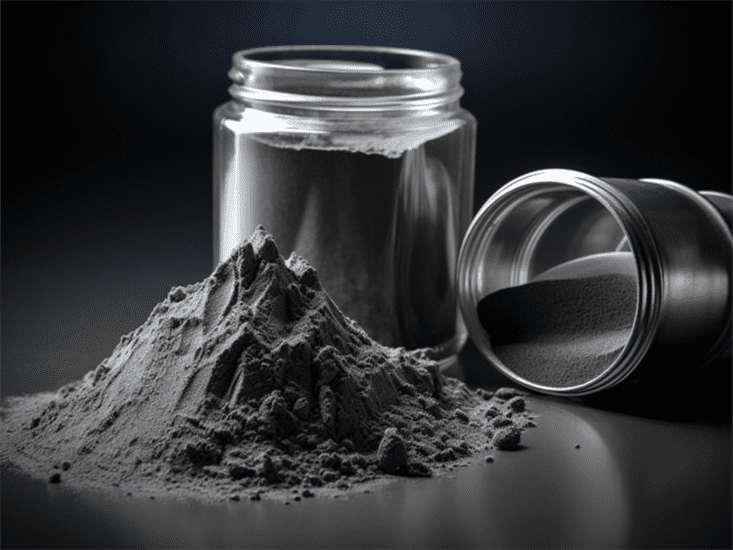
FAQs
Q: What is the typical particle size distribution used for high temperature stainless steel powders in metal AM?
A: For powder bed fusion processes like selective laser melting (SLM) and electron beam melting (EBM), the common range is 15 μm – 45 μm size fractions. Finer distributions can improve resolution but impair powder spreading during layer deposition and reduce flow characteristics.
Q: What gas atomization cooling rates preserve optimal alloy powder compositions?
A: For the best combination of chemistry retention and appropriate powder morphology, solidification rates between 1000 – 3000°C per second are widely used for high temperature stainless steel and superalloy powders.
Q: Why are high levels of oxide particles detrimental in high temperature iron alloys?
A: During service, oxides present can coarsen and migrate forming less protective and less stable oxide populations resulting in accelerated attack from oxidizing, sulfidizing, carburizing or chlorinating environments – reducing component life. Careful determination and control of oxygen levels based on maximum exposure temperatures and operating conditions is necessary in alloy development.
Q: What methods can be used to increase powder densities to >95% theoretical?
A: Hot isostatic pressing is commonly applied on high temperature stainless steel or superalloy components after initial AM or MIM fabrication to eliminate residual pores, creating material performance close to that of wrought alloys in the same strengthened heat treated states. Near theoretical densities ensure mechanical robustness.
Q: Why is nitrogen control below 1000 ppm critical in high strength high conductivity copper alloys?
A: Nitrogen pickup deleteriously forms very hard, brittle nitride phases that drastically lower thermal and electrical conductivities reducing functionality in thermal management applications, while also decreasing formability and ductility during manufacture.
Share On
MET3DP Technology Co., LTD is a leading provider of additive manufacturing solutions headquartered in Qingdao, China. Our company specializes in 3D printing equipment and high-performance metal powders for industrial applications.
Inquiry to get best price and customized Solution for your business!
Related Articles
About Met3DP
Recent Update
Our Product
CONTACT US
Any questions? Send us message now! We’ll serve your request with a whole team after receiving your message.
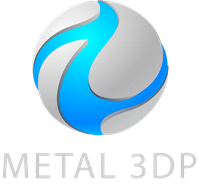
Metal Powders for 3D Printing and Additive Manufacturing
COMPANY
PRODUCT
cONTACT INFO
- Qingdao City, Shandong, China
- [email protected]
- [email protected]
- +86 19116340731