Высокотемпературный железный порошок
Оглавление
Обзор
Высокотемпературные железные порошки это специализированные металлические порошки из сплавов на основе железа, предназначенные для работы при повышенных температурах, превышающих 850°C, без быстрой потери прочности. Обычные железные и стальные порошки быстрее окисляются и разрушаются за этим порогом.
Тщательно подобранный химический состав порошка и обработка позволяют повысить прочность при высоких температурах и устойчивость к воздействию окружающей среды. К основным областям применения, где требуются такие термостойкие конструкционные материалы, относятся автомобильная, аэрокосмическая, энергетическая и химическая промышленность.
Виды Высокотемпературные железные порошки
Тип | Метод производства | Основные характеристики | Применение (благодаря высокотемпературным характеристикам) |
---|---|---|---|
Порошок карбонильного железа | Разложение паров пентакарбонила железа при высоких температурах | - Высокая чистота (>99% Fe) - Сферическая морфология частиц - Гладкая поверхность - Тщательный контроль размера - Мягкие магнитные свойства | - Высокопроизводительные магнитные компоненты (например, индукторы для высокочастотных применений) - Мягкие магнитопроводы для трансформаторов и двигателей - Микроволновые поглотители - Применение катализаторов благодаря высокой площади поверхности |
Электролитический железный порошок | Электролиз растворов хлорида железа | - Очень высокая чистота (часто превышает 99,5% Fe) - Плотные, сферические частицы - Отличная текучесть - Высокая сжимаемость | - Мягкие магнитопроводы для высокочастотных приложений, таких как трансформаторы и индукторы - Электронные компоненты, требующие высокой чистоты (например, электромагнитное экранирование) - Аддитивное производство сложных металлических деталей, близких по форме к сетке - Приложения, использующие хорошую электропроводность при повышенных температурах |
Железный порошок, распыляемый водой | Расплавленное железо разбивается на мелкие частицы с помощью струй воды под высоким давлением | - Высокая производительность - Самая низкая стоимость среди высокотемпературных железных порошков - Относительно высокое содержание кислорода - Неправильная форма частиц - Широкий гранулометрический состав | - Области применения, где стоимость имеет первостепенное значение (например, некоторые процессы литья металлов под давлением) - Детали, требующие хорошей обрабатываемости после спекания - Высокотемпературная пайка из-за присутствия кислорода - Области применения, выигрывающие от неравномерной упаковки частиц (например, некоторые фильтрующие материалы) |
Железный порошок, отожженный в вакууме | Дальнейшая обработка других железных порошков (часто распыляемых водой) путем отжига в атмосфере водорода | - Улучшает свойства базового порошка (например, снижает содержание кислорода, улучшает форму частиц) - Индивидуальные свойства на основе исходного порошка | - Области применения, требующие баланса между стоимостью и высокотемпературными характеристиками (например, некоторые магнитомягкие компоненты) - Процессы аддитивного производства, где требуются особые характеристики порошка - Области применения пайки, требующие хороших характеристик при повышенных температурах |
Методы производства высокотемпературных порошков
Метод | Описание | Преимущества | Недостатки | Типичные производимые материалы |
---|---|---|---|---|
Газовая атомизация | Расплавленный металл распадается на мелкие капли с помощью высокоскоростного потока инертного газа | - Порошки высокой чистоты - Сферическая морфология частиц - Узкое распределение по размерам - Хорошая текучесть - Подходит для широкого спектра материалов | - Высокое потребление энергии - Относительно высокая стоимость по сравнению с некоторыми другими методами - Возможность образования оксидов в некоторых материалах | - Высокотемпературные сплавы (например, никелевые суперсплавы, алюминиды титана) - Тугоплавкие металлы (например, вольфрам, молибден) - Инструментальные стали |
Распыление воды | Расплавленный металл разбивается на капли с помощью струй воды под высоким давлением | - Высокая производительность - Низкая стоимость - Применимость к широкому спектру материалов | - Неправильная форма частиц - Широкий гранулометрический состав - Более высокое содержание кислорода по сравнению с газовым распылением | - Низколегированные стали и чугуны - Нержавеющие стали (для некоторых применений) - Порошки для литья металлов под давлением (MIM) |
Плазменное распыление | Расплавленный металл впрыскивается в высокотемпературный и высокоскоростной поток плазмы, что приводит к быстрому затвердеванию | - Ультратонкие порошки (<10 микрометров) - Сферические частицы - Узкое распределение по размерам - Потенциал для образования метастабильных фаз | - Очень высокое потребление энергии - Ограниченные производственные мощности - Сложный и дорогой процесс | - Аморфные металлические порошки - высокопроизводительные сплавы для аэрокосмической и турбинной промышленности |
Разложение карбонилов | Термическое разложение карбонилов металлов (соединений металлов, содержащих монооксид углерода) при высоких температурах | - Порошки высокой чистоты - Сферическая морфология частиц - Строгий контроль над размером и морфологией частиц | - Ограничен несколькими металлами, образующими стабильные карбонилы (например, железо, никель) - Сложный и относительно медленный процесс | - Высокочистые железные порошки для магнитных применений - Катализаторные материалы |
Электролиз | Осаждение металла из расплавленной соли или водного раствора с помощью электрического тока | - Порошки очень высокой чистоты - Плотные, сферические частицы - Отличная текучесть | - Ограниченная скорость производства - Высокая стоимость - Применимо к ограниченному спектру материалов | - Порошок электролитического железа для высокоэффективных магнитных компонентов - Медные порошки для электротехнических применений |
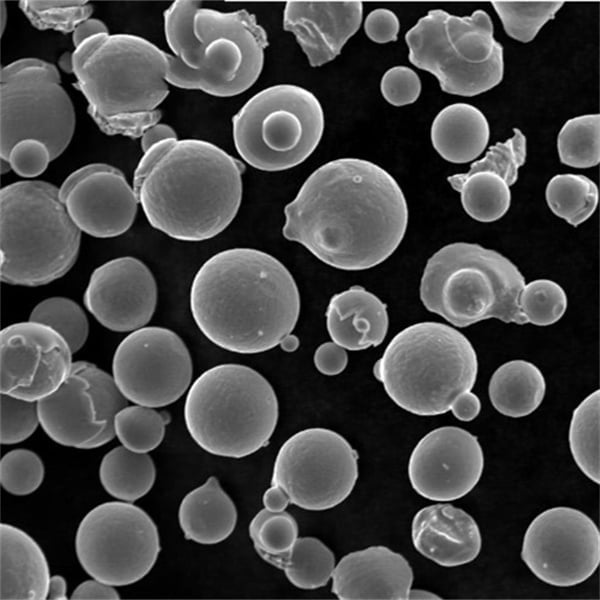
Типы и составы сплавов
Существует четыре основные категории специальных порошков железных сплавов, предназначенных для длительного использования при температурах свыше 850°C:
Порошки из аустенитной нержавеющей стали
Такие сплавы, как нержавеющие стали 316L, 304L и 301L, содержат никель для поддержания аустенитной кристаллической структуры FCC при температуре до 1100°C и хром для устойчивости к окислению благодаря защитным поверхностным пленкам хрома (Cr2O3) при высоких температурах.
Легирующий элемент | Роль | Вес % Диапазон |
---|---|---|
Никель (Ni) | Стабилизатор аустенита | 8 – 12% |
Хром (Cr) | Устойчивость к окислению | 16 – 18% |
Марганец (Mn) | Прочность и утонченность зерен | До 2% |
Азот (N) | Укрепление | 0.1 – 0.25% |
Преимущества: Отличная "горячая прочность", легкость уплотнения и спекания, более низкая стоимость по сравнению с суперсплавами.
Ограничения: Склонны к ползучести при температуре выше 1000°C, не подходят для динамических нагрузок.
Железные сплавы с высоким содержанием никеля
Сплавы никель-железо с содержанием никеля 25-60 масс% обеспечивают оптимальное сочетание высокотемпературной прочности, вязкости и коррозионной стойкости. Добавки никеля значительно замедляют скорость диффузии и снижают вредные микроструктурные изменения вплоть до 1150°C.
Другими ключевыми легирующими элементами являются:
Легирующий элемент | Роль | Вес % Диапазон |
---|---|---|
Никель (Ni) | Упрочнение твердых растворов | 25 – 60% |
Хром (Cr) | Устойчивость к окислению | 10 – 25% |
Кобальт (Co) | Улучшает механические свойства при высоких температурах | 10 – 25% |
Молибден (Mo) | Устойчивость к ползучести | 2 – 6% |
Преимущества: Непревзойденные механические характеристики при 1100°C+, замедленная кинетика деградации. Термически стабильная микроструктура.
Ограничения: Очень высокие цены на сплавы, сложности с контролем пористости, требующие HIP-уплотнения.
Упрочнение железных сплавов оксидной дисперсией
В сплавах, упрочненных оксидной дисперсией, очень мелкие (50-100 нм) инертные частицы оксида иттрия вкраплены в матрицу материала. Эти наноразмерные оксиды препятствуют движению дислокаций, тем самым сохраняя прочность при температурах выше 1000°C.
Легирующий элемент | Роль | Вес % Диапазон |
---|---|---|
Оксид иттрия (Y2O3) | Нанооксидные частицы, обеспечивающие термическую стабильность | 0.25% – 1% |
Хром (Cr) | Устойчивость к воздействию окружающей среды | До 20% |
Алюминий (Al) | Улучшает дисперсию оксидов | До 4% |
Преимущества: Исключительная микроструктурная стабильность и прочность при ползучести в условиях эксплуатации 1100°C+.
Ограничения: Очень высокая стоимость, сложность обработки - традиционно изготавливается путем механического легирования и консолидации.
Сплавы на основе алюминида железа (FeAl)
Железоалюминидные сплавы с содержанием алюминия 10- 40% обеспечивают превосходную стойкость к окислению и сульфидированию до 900°C благодаря образованию прочного защитного верхнего слоя из глинозема (Al2O3). Хром способствует защите поверхности.
Легирующий элемент | Роль | Вес % Диапазон |
---|---|---|
Алюминий (Al) | Устойчивость к окислению | 10 – 40% |
Хром (Cr) | Повышает устойчивость к воздействию окружающей среды | 5 – 10% |
Углерод, Zr (C, Zr) | Твердосплавные укрепители | До 0,5% |
Преимущества: Высокая экологическая стабильность, более низкая плотность по сравнению со сталями, простота изготовления по сравнению с суперсплавами.
Ограничения: Потеря прочности выше 750°C, плохое сопротивление ползучести, приложенные напряжения увеличивают вредительские явления.
Методы производства
Для получения порошков из высокотемпературных железных сплавов с подходящими характеристиками используются специальные технологии:
Газовая атомизация
- Контролируемое быстрое охлаждение потока расплавленного металла позволяет удерживать легирующие элементы в растворе, а не образовывать осадки
Сфероидизация плазмы
- Порошки неправильной формы, полученные в процессе распыления воды, повторно расплавляются с помощью плазменной горелки и вновь затвердевают, превращаясь в сферические порошки, идеальные для методов AM
Многократные циклы спекания
- Порошки многократно уплотняются при высоких температурах, измельчаются и просеиваются для улучшения распределения порошка, что идеально подходит для MIM-технологий.
Механическое легирование
- Шаровой размол порошков элементарных металлов создает нанодисперсное распределение частиц и кластеров в сплавах ODS
Рафинирование карбонилов
- Производство металлических порошков исключительно высокой чистоты, когда более дешевые методы производства приводят к загрязнению
Сравнение методов производства
Метод | Уровни чистоты | Содержание кислорода | Варианты морфологии | Производительность (тонн/год) |
---|---|---|---|---|
Газовая атомизация | Умеренный | <1000 ppm | Преимущественно сферическая | Высокий >20 000 |
Распыление воды | Низкий | 2000-4000 стр. | Нерегулярный | Очень высокий >50 000 |
Сфероидизация плазмы | Средний | 500-2000 ppm | Сферическая | Низкий <5 000 |
Механическое легирование | Высокая | <1500 ppm | Различные формы частиц | Низкие сотни |
Карбонильный процесс | Чрезвычайно высокий | <200 ppm | Сферический/узловатый | Высокий >25 000 |
Методы определения характеристик
Для определения качества высокотемпературных порошковых сплавов необходимо использовать несколько аналитических методов:
Химический состав
- Спектрографические методы и методы мокрой химии определяют состав и количество элементов - это необходимо для проверки конструкции сплава
- Содержание углерода, серы, кислорода, азота свидетельствует о загрязнении, вызванном технологическим процессом и влияющем на характеристики материала
Размер и морфология частиц
- Лазерные дифракционные анализаторы размеров частиц определяют полную гранулометрию от 10 нм до 3 мм.
- С помощью РЭМ-изображений можно визуализировать форму, особенности поверхности, частицы-спутники, пористость, что полезно для оценки пригодности процесса сборки и анализа дефектов.
Кристаллография
- XRD показывает наличие фаз, состояние осадка, количественный анализ кристаллических свойств
- Оценка влияния термического воздействия на фазовые фракции по микроструктурной эволюции
Испытание свойств порошка
- Расходометрия Холла, кажущаяся плотность и сжимаемость количественно определяют поведение порошка, облегчая его обработку и консолидацию
Применение и использование высокотемпературных порошков
Область применения | Тип порошка (примеры) | Основные используемые свойства | Преимущества |
---|---|---|---|
Аддитивное производство металлов (AM) | Газоатомизированные никелевые суперсплавы, водоатомизированные нержавеющие стали | - Сферическая морфология для хорошей текучести - Узкое распределение по размерам для равномерного осаждения - Высокотемпературные характеристики для создания функциональных деталей | - Позволяет создавать сложные компоненты, близкие к сетчатой форме - Индивидуальные свойства материалов для конкретных применений - Сокращение отходов по сравнению с традиционным субтрактивным производством |
Высокопроизводительные магнитные компоненты | Порошок карбонильного железа, порошок электролитического железа | - Высокая чистота для низких потерь энергии - Сферическая морфология для хорошей плотности сердечника - Мягкие магнитные свойства для эффективной передачи энергии | - Повышение эффективности трансформаторов, индукторов и двигателей - Снижение рабочих температур и уровня шума - Миниатюризация устройств за счет улучшения магнитных характеристик |
Высокотемпературная пайка | Водоатомизированный железный порошок, газоатомизированные никелевые сплавы | - Контролируемая температура плавления для пайки различных материалов - Наличие оксидов (в некоторых порошках) для улучшения смачивания и сцепления - Высокотемпературная прочность для прочных соединений | - Соединение разнородных металлов и сплавов - Создание прочных, герметичных уплотнений в суровых условиях - Применение в аэрокосмической, автомобильной и энергетической промышленности |
Покрытия, наносимые термическим напылением | Водоатомизированные алюминиевые сплавы, газоатомизированные никелевые суперсплавы | - Широкий диапазон температур плавления для различных видов покрытий - Неправильная форма частиц для механического сцепления - Высокотемпературная стойкость для защиты субстратов | - Улучшенная износостойкость и коррозионная стойкость - Теплоизоляция - Восстановление изношенных компонентов - Применение в двигателях, турбинах и теплообменниках |
Литье металлов под давлением (MIM) | Водоатомизированные стали, предварительно легированные порошки | - Тонкий размер частиц для сложных геометрических форм деталей - Хорошая текучесть для равномерного заполнения пресс-форм - Контролируемые свойства порошка для точности размеров | - Экономически эффективное производство сложных металлических деталей, близких по форме к сетке - Достигается высокая прочность и плотность - Применение в автомобильной, медицинской и электронной промышленности |
Каталитическое применение | Порошок карбонильного железа, газоатомизированные переходные металлы | - Высокая площадь поверхности для эффективных каталитических реакций - Контролируемая структура пор для селективного катализа - Индивидуальная морфология частиц для улучшения активности катализатора | - Контроль выбросов в автомобильных выхлопных системах - Реакции химической переработки - Производство чистого топлива и возобновляемых источников энергии |
Технические характеристики и классы
Высокотемпературные порошковые сплавы должны соответствовать минимальным спецификациям по химическому составу, чистоте, характеристикам и свойствам частиц:
Характеристика | Описание | Ключевые соображения |
---|---|---|
Состав материала | Высокотемпературные порошки выпускаются из различных материалов, каждый из которых обладает определенными свойствами, подходящими для конкретных применений. К распространенным материалам относятся: Сплавы на основе никеля: Обладая исключительной стойкостью к окислению и высокотемпературной прочностью, идеально подходит для деталей реактивных двигателей, теплообменников и газовых турбин. Сплавы на основе кобальта: Известны своей износостойкостью и термостойкостью, часто используются в режущих инструментах, лопатках турбин и биомедицинских имплантатах. Нержавеющие стали: Обеспечивает баланс коррозионной стойкости и высокотемпературных характеристик, подходит для выпускных коллекторов, котлов и оборудования для пищевой промышленности. Инструментальные стали: Обеспечивает исключительную твердость и износостойкость при повышенных температурах, идеально подходит для пресс-форм, штампов и пуансонов. Огнеупорная керамика: Обладая превосходными теплоизоляционными свойствами, обычно используется для футеровки печей, тиглей и ракетных сопел. | Выбор материала зависит от предполагаемой области применения. Учитывайте такие факторы, как максимальная рабочая температура, требуемые механические свойства (прочность, износостойкость), устойчивость к окислению и совместимость с окружающей средой. |
Размер и распределение частиц | Размер и распределение частиц порошка существенно влияют на процесс нанесения и характеристики конечного продукта. Более мелкие порошки (10-45 микрон): Улучшают качество поверхности и создают тонкие, гладкие покрытия. Хорошо подходит для электростатического напыления и применения в кипящем слое. Более грубые порошки (45-150 мкм): Обладают лучшей текучестью и позволяют создавать более толстые покрытия. Более применимы для технологий прессования и спекания. | Размер частиц имеет решающее значение для достижения желаемой толщины покрытия и эстетики. Сбалансированное распределение обеспечивает эффективное нанесение и минимизирует количество отходов. |
Текучесть | Легкость подачи порошка важна для равномерного нанесения и эффективного использования. Порошки с хорошей текучестью обеспечивают беспрепятственную подачу в распылительные пистолеты и бункеры, сводя к минимуму образование комков и засорение. | Недостаточная текучесть может привести к несоответствиям в нанесении, неравномерному покрытию и задержкам в производстве. Производители часто используют добавки или регулируют гранулометрический состав для оптимизации текучести. |
Кажущаяся плотность | Это вес порошка на единицу объема, влияющий на такие факторы, как требования к хранению, вместимость бункера и толщина покрытия. * Порошки с высокой кажущейся плотностью: Имеют преимущества с точки зрения эффективного хранения и потенциально требуют меньше материала для достижения определенной толщины покрытия. * Порошки с низкой кажущейся плотностью: Может требовать больших складских помещений, но зато легче обрабатывается и позволяет создавать более толстые слои за одно нанесение. | Кажущаяся плотность влияет на перемещение материала, необходимость хранения и эффективность покрытия. Выбор правильной плотности зависит от требований к применению и имеющегося оборудования. |
Температура плавления и тепловое расширение | Температура плавления определяет максимальную температуру использования порошка, а тепловое расширение диктует изменение размеров при нагревании. * Порошки с высокой температурой плавления: Выдерживают экстремальные температуры, что делает их пригодными для использования в таких сложных условиях, как компоненты ракетных двигателей. * Порошки с низким тепловым расширением: Минимизация изменений размеров во время циклов нагрева, что очень важно для поддержания точных допусков в высокотемпературных средах. | Понимание этих свойств жизненно важно для обеспечения того, чтобы порошок мог выдерживать заданную рабочую температуру без ущерба для функциональности и стабильности размеров. |
Коррозионная стойкость | Способность порошкового материала противостоять разрушению под воздействием таких факторов окружающей среды, как окисление или химическое воздействие, имеет решающее значение для долгосрочной работы. Порошки с высокой коррозионной стойкостью: Сохраняют целостность в жестких условиях эксплуатации, идеально подходят для приложений, подверженных воздействию химикатов, высокой влажности или соляного тумана. Порошки с пониженной коррозионной стойкостью: Может потребовать дополнительной обработки поверхности или нанесения защитных покрытий для продления срока службы. | Выбор коррозионной стойкости зависит от предполагаемых условий эксплуатации. Выбор порошка с высокой коррозионной стойкостью может продлить срок службы конечного продукта. |
Анализ затрат на высокотемпературные порошки
Фактор | Описание | Влияние на стоимость |
---|---|---|
Тип материала | Как уже говорилось ранее, высокотемпературные порошки выпускаются из различных материалов, каждый из которых имеет свою цену. Сплавы на основе никеля: Как правило, самые дорогие из-за их исключительных высокотемпературных характеристик и сложных производственных процессов. Сплавы на основе кобальта: Часто находятся в схожем ценовом диапазоне со сплавами на основе никеля, но могут варьироваться в зависимости от конкретного содержания кобальта и желаемых свойств. Нержавеющие стали: Обычно более доступны по цене, чем сплавы на основе никеля или кобальта, что обеспечивает баланс между стоимостью и производительностью. Инструментальные стали: Стоимость может варьироваться в зависимости от конкретных легирующих элементов и желаемых свойств. Как правило, дешевле, чем варианты на основе никеля или кобальта. Огнеупорная керамика: Несмотря на отличную термостойкость, некоторые виды огнеупорной керамики могут быть относительно недорогими, особенно это касается таких распространенных материалов, как глинозем. Однако более специализированная или высокочистая керамика может стоить значительно дороже. | Выбор материала существенно влияет на общую стоимость проекта. Тщательно оцените требования к производительности в сравнении с бюджетными ограничениями. |
Чистота порошка | Степень чистоты высокотемпературного порошка напрямую влияет на его свойства и цену. Порошки высокой чистоты: Обладают превосходными эксплуатационными характеристиками, такими как повышенная прочность, улучшенная стойкость к окислению и лучшее спекание. Однако они имеют высокую цену из-за сложных процессов очистки. Порошки низкой чистоты: Может быть достаточно для некоторых применений, где максимальная производительность не является критичной. Эти порошки, как правило, более экономичны. | Рассмотрите компромисс между достижением желаемых характеристик и экономической эффективностью. В некоторых случаях небольшое снижение чистоты может быть приемлемым, если это приведет к значительной экономии средств. |
Размер и распределение частиц | Размер и распределение частиц порошка могут влиять как на стоимость материала, так и на стоимость обработки. Более мелкие порошки: Как правило, требуют более сложных и энергоемких производственных процессов, что приводит к увеличению стоимости единицы веса. Более грубые порошки: Несмотря на потенциально меньшую стоимость производства, они могут потребовать дополнительных этапов обработки (например, измельчения) для достижения желаемого распределения частиц по размерам для конкретных применений, что может свести на нет часть первоначального преимущества в стоимости. | Оптимизация размера частиц для выбранной области применения поможет найти баланс между стоимостью материала и стоимостью обработки. |
Минимальное количество заказа (MOQ) | Многие поставщики устанавливают минимальные объемы заказа (MOQ) для высокотемпературных порошков. Большие MOQ: Это может привести к значительным первоначальным затратам, особенно при использовании менее распространенных или специализированных порошков. Малые размеры MOQ: Может быть доступен по более высокой цене из-за более сложной обработки и администрирования небольших партий. | Учитывайте требования проекта и возможность отходов. Если большой MOQ не будет использован полностью, найдите альтернативных поставщиков, предлагающих меньшие объемы, или объединитесь с другими пользователями для совместного заказа большего объема. |
Репутация и местоположение поставщика | Репутация поставщика порошка существенно влияет на стоимость и общий успех проекта. Авторитетные поставщики: Применяйте строгие меры контроля качества, обеспечивая неизменность свойств материала и сводя к минимуму риск получения непригодных порошков. Такая надежность может стоить дорого. Менее известные поставщики: Могут предлагать более низкие цены, но при этом могут не иметь строгих процедур контроля качества, что может привести к повышенному количеству брака или нестабильной работе. | Тщательно оцените квалификацию поставщика и отдайте предпочтение стабильному качеству перед потенциально низкой первоначальной стоимостью. |
Срок поставки | Время, необходимое для доставки порошка, может повлиять на сроки реализации проекта и потенциально отразиться на стоимости. Сокращение сроков изготовления: Может потребоваться ускоренная доставка, которая может быть дороже. Более длительное время выполнения заказа: Может быть более экономичным, но требует тщательного планирования и управления запасами, чтобы избежать задержек в производстве. | Оцените компромисс между стоимостью и графиком проекта. Если сроки выполнения заказа критичны, изучите варианты ускоренной доставки или создания буферного запаса для смягчения возможных задержек. |
Плюсы и минусы высокотемпературных сплавов железа
Характеристика | Преимущество | Недостаток |
---|---|---|
Экономическая эффективность | По сравнению с другими высокотемпературными материалами, такими как суперсплавы на основе никеля или кобальта, сплавы на основе железа имеют значительное преимущество по стоимости. Железо - легкодоступный элемент, поэтому производство таких сплавов обычно обходится дешевле. | Несмотря на свою экономичность, высокотемпературные сплавы железа не всегда могут обеспечить такой же уровень производительности, как некоторые варианты на основе никеля или кобальта, с точки зрения пиковой рабочей температуры или специфических механических свойств. |
Устойчивость к окислению | Некоторые сплавы железа могут демонстрировать хорошую устойчивость к окислению при умеренных температурах (до 700°C). Легирующие элементы, такие как хром и алюминий, способствуют образованию защитного оксидного слоя, который препятствует дальнейшему окислению. | По устойчивости к окислению железные сплавы обычно не дотягивают до суперсплавов на основе никеля или кобальта, которые могут сохранять свою целостность при гораздо более высоких температурах. Для продления срока службы в сильно окисляющихся средах железные сплавы могут потребовать дополнительной обработки поверхности или нанесения покрытий. |
Прочность и сопротивление ползучести | Хотя некоторые сплавы железа не могут сравниться с лучшими образцами, они способны обеспечить достаточную прочность и сопротивление ползучести при повышенных температурах. Специальные легирующие элементы, такие как молибден и ванадий, могут улучшить эти свойства, делая их пригодными для различных промышленных применений. | Высокотемпературная прочность и сопротивление ползучести железных сплавов, как правило, уступают таковым у суперсплавов на основе никеля или кобальта. Для приложений, требующих исключительных характеристик при экстремальных температурах, могут потребоваться другие варианты материалов. |
Свариваемость и обрабатываемость | Сплавы на основе железа обычно обладают хорошей свариваемостью и обрабатываемостью по сравнению с некоторыми другими высокотемпературными материалами. Это облегчает изготовление и снижает общие затраты на обработку. | Несмотря на то, что сплавы железа поддаются сварке и механической обработке, они могут требовать особых технологий сварки или обработки, чтобы избежать ухудшения их свойств в сварном шве или возникновения напряжений при механической обработке. |
Возможность вторичной переработки | Железо - один из наиболее перерабатываемых металлов во всем мире. Высокотемпературные сплавы железа потенциально могут быть переработаны по окончании срока службы, что минимизирует воздействие на окружающую среду и обеспечивает определенную степень устойчивости материала. | Процесс переработки сложных железных сплавов может быть более сложным по сравнению с чистым железом, а такие факторы, как легирующие элементы и поверхностные загрязнения, могут влиять на пригодность к переработке. |
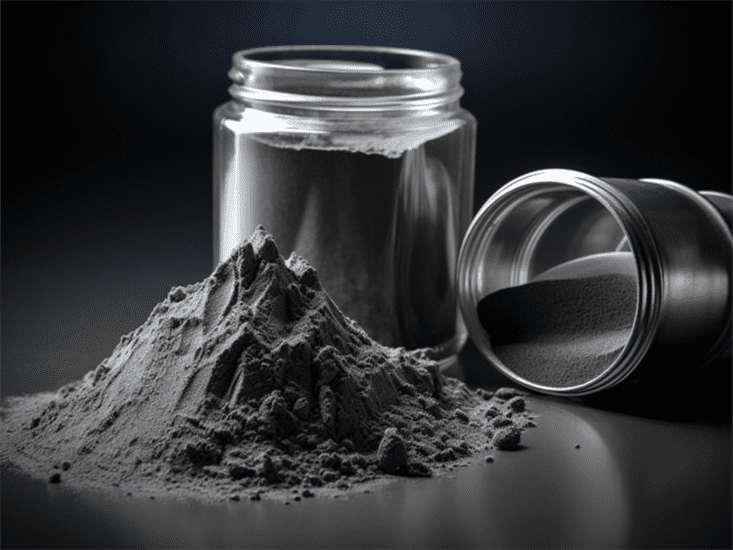
Вопросы и ответы
Вопрос: Какой типичный гранулометрический состав используется для порошков из высокотемпературной нержавеющей стали в металлообработке AM?
О: Для процессов плавления в порошковом слое, таких как селективное лазерное плавление (SLM) и электронно-лучевое плавление (EBM), обычным диапазоном является размер фракций 15 мкм - 45 мкм. Более мелкие фракции могут улучшить разрешение, но ухудшают распределение порошка при послойном осаждении и снижают характеристики текучести.
Вопрос: Какие скорости охлаждения при газовом распылении сохраняют оптимальные составы порошка сплава?
О: Для наилучшего сочетания сохранения химического состава и соответствующей морфологии порошка широко используются скорости затвердевания в диапазоне 1000 - 3000°C в секунду для высокотемпературных порошков нержавеющей стали и суперсплавов.
Вопрос: Почему высокий уровень содержания оксидных частиц вреден для высокотемпературных сплавов железа?
О: В процессе эксплуатации присутствующие оксиды могут огрубеть и мигрировать, образуя менее защитные и менее стабильные оксидные популяции, что приводит к ускоренному воздействию окислительной, сульфидирующей, науглероживающей или хлорирующей среды, сокращая срок службы деталей. При разработке сплавов необходимо тщательно определять и контролировать уровень содержания кислорода в зависимости от максимальной температуры воздействия и условий эксплуатации.
Вопрос: Какие методы можно использовать для увеличения плотности порошка до теоретической >95%?
О: Горячее изостатическое прессование обычно применяется к высокотемпературным компонентам из нержавеющей стали или сверхпрочных сплавов после первоначального изготовления по технологии AM или MIM для устранения остаточных пор, обеспечивая характеристики материала, близкие к характеристикам деформируемых сплавов в том же усиленном термообработанном состоянии. Плотность, близкая к теоретической, обеспечивает механическую прочность.
Вопрос: Почему контроль содержания азота ниже 1000 ppm является критическим для высокопрочных медных сплавов с высокой проводимостью?
О: При подборе азота образуются очень твердые, хрупкие нитридные фазы, которые резко снижают тепло- и электропроводность, уменьшая функциональность в системах терморегулирования, а также снижают формуемость и пластичность в процессе производства.
Поделиться
MET3DP Technology Co., LTD - ведущий поставщик решений для аддитивного производства со штаб-квартирой в Циндао, Китай. Наша компания специализируется на производстве оборудования для 3D-печати и высокопроизводительных металлических порошков для промышленного применения.
Сделайте запрос, чтобы получить лучшую цену и индивидуальное решение для вашего бизнеса!
Похожие статьи
О компании Met3DP
Последние обновления
Наш продукт
CONTACT US
Есть вопросы? Отправьте нам сообщение прямо сейчас! После получения Вашего сообщения мы всей командой выполним Ваш запрос.
Получите информацию о Metal3DP
Брошюра о продукции
Получить последние продукты и прайс-лист
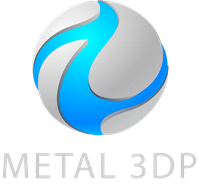
Металлические порошки для 3D-печати и аддитивного производства
КОМПАНИЯ
ПРОДУКТ
ИНФОРМАЦИЯ О КОНТАКТЕ
- Город Циндао, Шаньдун, Китай
- [email protected]
- [email protected]
- +86 19116340731