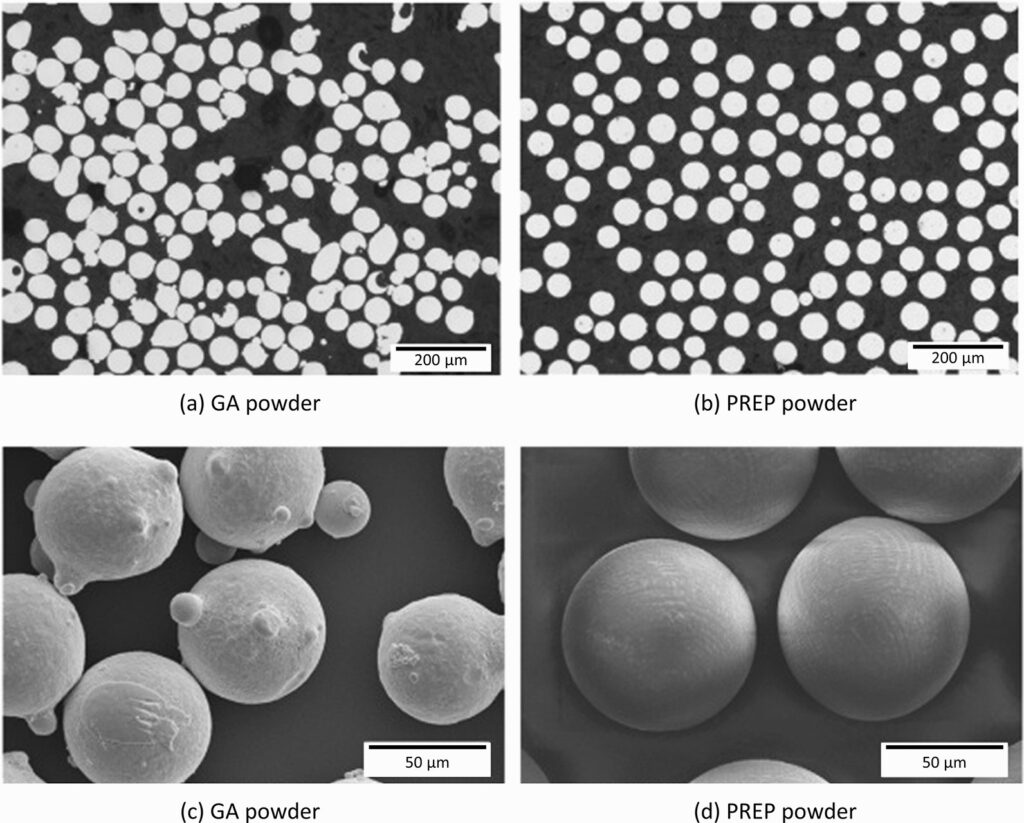
Poudre IN690 : Pourquoi cet alliage est parfait pour les exigences des hautes températures
Faible MOQ
Les quantités minimales de commande sont peu élevées, ce qui permet de répondre à différents besoins.
OEM & ODM
Fournir des produits et des services de conception personnalisés pour répondre aux besoins uniques des clients.
Stock suffisant
Assurer un traitement rapide des commandes et fournir un service fiable et efficace.
Satisfaction des clients
Fournir des produits de haute qualité en mettant l'accent sur la satisfaction du client.
partager cet article
Table des matières
Lorsqu'il s'agit de matériaux de haute performance capables de résister à l'usure du temps, il est important d'en tenir compte. températures extrêmes et environnements corrosifs, Poudre IN690 s'impose comme un candidat de premier plan. Il s'agit superalliage à base de nickel est conçu pour les industries qui ont besoin de matériaux excellente résistance à la corrosion, en particulier dans les environnements oxydants tels que les centrales nucléaires, installations de traitement chimiqueet applications aérospatiales.
Dans cette guide completNous allons couvrir tous les aspects de la Poudre IN690-de son composition et propriétés à son applications, la tarificationet fournisseurs. Que vous soyez ingénieur, spécialiste des matériaux ou simplement curieux des alliages à haute performance, ce guide vous permettra de comprendre en profondeur les raisons pour lesquelles les alliages à haute performance sont si importants pour la santé humaine. Poudre IN690 est un matériau de choix pour les projets critiques.
Aperçu de la poudre IN690
Poudre IN690également connu sous le nom de Alliage 690est un superalliage à base de nickel qui contient des niveaux élevés d'oxydes d'azote. chrome. La teneur élevée en chrome est à l'origine de la IN690 sa résistance supérieure aux oxydation et corrosion en aqueux et environnements à haute température. Il est donc particulièrement adapté à des applications telles que réacteurs nucléaires, échangeurs de chaleuret équipement de traitement chimique.
Caractéristiques principales de la poudre IN690 :
- Superbe Corrosion Résistance: Bonne performance dans les deux oxydant et sulfurique environnements.
- Stabilité à haute température: Conserve sa résistance et sa stabilité à des températures élevées.
- Fabrication polyvalente: Convient pour Impression 3D, métallurgie des poudreset pulvérisation thermique processus.
- Applications dans les industries critiques: Utilisé dans énergie nucléaire, traitement chimiqueet aérospatiale.
Voyons maintenant ce qu'il en est de la composition chimique et propriétés mécaniques qui font Poudre IN690 une merveille d'ingénierie.
Composition et principales propriétés de la poudre IN690
Comprendre la composition de Poudre IN690 Il est essentiel de comprendre pourquoi elle excelle dans les domaines suivants haute température et environnements corrosifs. La combinaison de nickel, chromeet d'autres éléments tels que fer et molybdène garantit qu'il peut résister à la fois acides oxydants et gaz contenant du soufre.
Composition chimique
Élément | Pourcentage (%) | Rôle dans l'alliage |
---|---|---|
Nickel (Ni) | 58.0-63.0 | Élément de base fournissant excellente résistance à la corrosion et stabilité à haute température. |
Chrome (Cr) | 27.0-31.0 | Offre une résistance supérieure aux environnements oxydants et milieux corrosifs comme acide sulfurique. |
Fer (Fe) | 7.0-11.0 | Améliore résistance mécanique et ajoute à la valeur globale de l'alliage la durabilité. |
Molybdène (Mo) | 0.0-0.5 | Augmentations résistance à la corrosion en environnements non oxydants et améliore les performances à haute température. |
Carbone (C) | 0,05 max | Contribue à améliorer la résistance mécanique mais doivent être contrôlées pour éviter fragilisation des joints de grains. |
Silicium (Si) | 0,5 max | Améliore résistance à l'oxydation et améliore coulabilité. |
Manganèse (Mn) | 0,5 max | S'ajoute à résistance à l'oxydation et améliore l'efficacité de l'alliage soudabilité. |
Propriétés mécaniques et thermiques
Poudre IN690 est conçu pour fonctionner sous stress et à températures élevées. Voici quelques-unes des principales mécanique et propriétés thermiques qui font qu'il est très recherché dans diverses industries.
Propriété | Valeur/Description |
---|---|
Densité | 8,19 g/cm³ |
Point de fusion | 1343°C |
Résistance à la traction | 600-650 MPa à température ambiante |
Limite d'élasticité | 240-280 MPa à température ambiante |
Allongement à la rupture | 30% |
Résistance au fluage | Excellent, en particulier jusqu'à 870°C |
Résistance à l'oxydation | Bonne performance dans les environnements oxydatifs jusqu'à 1000°C |
Conductivité thermique | 13,3 W/m-K |
Soudabilité | Bon, mais nécessite préchauffage et traitements thermiques post-soudure pour éviter les fissures. |
Avantages de la poudre IN690 : pourquoi c'est un choix populaire
Vous vous demandez probablement ce qui fait que Poudre IN690 un choix si populaire pour les haute température et environnements sujets à la corrosion? Voyons ce qu'il en est.
1. Résistance exceptionnelle à la corrosion
Poudre IN690 a une teneur élevée en chrome, ce qui le rend incroyablement résistant à la corrosion. acides oxydants et produits chimiques agressifs. Qu'il s'agisse de acide sulfurique, acide nitriqueou même chlorures, IN690 peut le supporter. C'est pourquoi c'est le matériau de choix pour réacteurs nucléaires, usines de traitement chimiqueet systèmes de contrôle de la pollution.
2. Stabilité à haute température
Certains matériaux se décomposent ou perdent leurs propriétés lorsqu'ils sont exposés à chaleur extrêmemais pas Poudre IN690. Avec un point de fusion de plus de 1300°CCet alliage conserve son la force et résistance à l'oxydation même à des températures aussi élevées que 1000°C. Il s'agit donc d'un outil précieux pour turbines à gaz, échangeurs de chaleuret composants du four.
3. Polyvalence des processus de fabrication
Non seulement le Poudre IN690 excellent pour les méthodes de fabrication traditionnelles telles que coulée et soudagemais il excelle également dans les domaines suivants fabrication additive et métallurgie des poudres. Cela signifie que vous pouvez l'utiliser pour Impression 3D de pièces complexes qui sont à la fois durables et résistants à la corrosion.
4. Durabilité à long terme
Lorsque vous investissez dans des matériaux pour des applications critiques, la durabilité à long terme est essentiel. Poudre IN690 est connue pour ses résistance au fluage et sa capacité à résister stress sur de longues périodes, ce qui en fait la solution idéale pour les composants qui doivent durer dans le temps. environnements difficiles.
Applications de la poudre IN690 : Où est-elle utilisée ?
Grâce à sa combinaison unique de résistance à la corrosion, stabilité à haute températureet résistance mécanique, Poudre IN690 est utilisé dans certaines des applications les plus exigeantes d'un grand nombre d'industries.
Utilisations courantes
L'industrie | Application |
---|---|
L'énergie nucléaire | Générateurs de vapeur, échangeurs de chaleuret barres de contrôle en réacteurs nucléaires en raison de sa résistance supérieure à la corrosion. |
Traitement chimique | Navires, tuyauterieet échangeurs de chaleur exposés à acide sulfurique et chlorures. |
Aérospatiale | Composants de turbines à gaz, postcombustionet boucliers thermiques qui nécessitent une stabilité à haute température et une résistance à l'oxydation. |
Lutte contre la pollution | Systèmes de désulfuration des gaz de combustion, revêtements de cheminéeet incinérateurs de déchets exposés à des gaz agressifs. |
Pétrole et gaz | Équipement de fond de puits, soupapeset scellés qui fonctionnent dans des environnements corrosifs et à haute pression. |
Fabrication additive | Pièces imprimées en 3D pour aérospatiale, énergieet composants de traitement chimique qui exigent une résistance à la corrosion et à la chaleur. |
Il ne s'agit là que de quelques exemples des industries et des applications dans lesquelles les Poudre IN690 excelle.
Spécifications, tailles et normes pour la poudre IN690
Avant de commander Poudre IN690Il est donc essentiel de connaître le bon spécifications pour votre application spécifique. Jetons un coup d'œil sur les tailles, gradeset normes que vous devez connaître.
Spécifications
Spécifications | Détails |
---|---|
Taille des particules | La fourchette est généralement comprise entre 15 à 45 microns pour métallurgie des poudres et fabrication additive. |
Morphologie des poudres | En général sphérique pour une fluidité supérieure dans les Impression 3D et pulvérisation thermique des applications. |
Normes ASTM | ASTM B163 pour les alliages à base de nickel utilisés dans échangeurs de chaleur et équipement de traitement chimique. |
Normes ISO | ISO 15156 pour les matériaux utilisés dans les environnements de gaz acides. |
Numéro UNS | UNS N06690 |
Normes AMS | AMS 5580couvrant les alliages à base de nickel tels que IN690 pour les applications à haute température. |
Ces spécifications s'assurer que vous obtenez la bonne grade et taille des particules pour votre cas particulier application industrielle.
Fournisseurs et prix de la poudre IN690
Le prix des Poudre IN690 peut varier en fonction de facteurs tels que fournisseur, taille des particuleset volume des commandes. Voici un aperçu des principaux fournisseurs et de la fourchette de prix générale à laquelle vous pouvez vous attendre.
Fournisseurs et prix
Fournisseur | Fourchette de prix (par kg) | Notes |
---|---|---|
Höganäs AB | $700 – $900 | Un chef de file en matière de poudres métalliques, en proposant l'IN690 pour les fabrication additive et métallurgie des poudres. |
Technologie des charpentiers | $720 – $950 | Spécialisé dans alliages haute performanceLa taille des particules peut être adaptée à des applications spécifiques. |
Oerlikon Metco | $710 – $940 | Fournit de la poudre IN690 pour pulvérisation thermique et Impression 3D. |
Sandvik | $730 – $960 | Offre des matériaux avancés pour aérospatiale et secteurs de l'énergiey compris la poudre IN690. |
Kennametal | $720 – $945 | Fournisseur d'alliages de nickel de première qualité, y compris IN690 pour applications industrielles critiques. |
En général, le prix du kilogramme de Poudre IN690 s'échelonne de $700 à $960, en fonction de la fournisseur et l'objectif spécifique de la taille et grade vous avez besoin.
Comparaison des avantages et des inconvénients de la poudre IN690
Comme tout autre matériau, Poudre IN690 est accompagné de son avantages et limitations. Nous allons les détailler afin que vous puissiez décider s'il s'agit du bon matériau pour votre prochain projet.
Avantages
Avantage | Description |
---|---|
Résistance à la corrosion: Performances supérieures en environnements oxydants. | Idéal pour traitement chimique et applications dans le domaine de l'énergie nucléaire. |
Stabilité à haute température: Maintient les propriétés mécaniques à des températures élevées. | Parfait pour turbines à gaz, échangeurs de chaleuret composants du four. |
Durabilité à long terme: Excellent résistance au fluage pour les composants soumis à des contraintes dans le temps. | Veille fiabilité en applications critiques comme réacteurs nucléaires. |
Fabrication polyvalente: Convient pour Impression 3D, pulvérisation thermiqueet métallurgie des poudres. | Permet de géométries complexes en fabrication additive. |
Résistance à l'oxydation: Fonctionne bien dans des environnements allant jusqu'à 1000°C. | Utile en applications à haute température comme fours et turbines à gaz. |
Limites
Limitation | Description |
---|---|
Coût élevé: Plus cher que beaucoup d'autres matériaux. | Peut ne pas convenir à sensible au budget des applications. |
Un défi pour les machines: Nécessite des outils spécialisés pour l'usinage de précision. | Peut augmenter temps d'usinage et coûtssurtout pour les pièces complexes. |
Disponibilité limitée: Pas toujours disponible en grandes quantités. | Peut conduire à délais de livraison plus longsnotamment pour les formulations personnalisées ou les commandes importantes. |
Oxydation à très haute température: L'oxydation peut devenir un problème au-dessus 1000°C. | Peut nécessiter revêtements pour des applications à des températures extrêmes. |
FAQ
Si vous avez encore des questions, ne vous inquiétez pas, nous avons tout prévu. Voici quelques-unes des questions les plus questions fréquemment posées à propos de Poudre IN690.
Question | Répondre |
---|---|
À quoi sert la poudre IN690 ? | Il est généralement utilisé dans réacteurs nucléaires, échangeurs de chaleuret équipement de traitement chimique en raison de son excellente résistance à la corrosion. |
Combien coûte la poudre IN690 ? | Le prix moyen varie entre $700 à $960 par kilogramme, en fonction de la fournisseur et taille des particules. |
La poudre IN690 peut-elle être utilisée dans l'impression 3D ? | Oui, il est largement utilisé dans fabrication additive des processus tels que la fusion sélective par laser (SLM) et fusion par faisceau d'électrons (EBM). |
Quelles sont les industries qui utilisent la poudre IN690 ? | Des industries comme énergie nucléaire, traitement chimique, aérospatialeet pétrole et gaz utiliser la poudre IN690 pour des applications de haute performance. |
Qu'est-ce qui rend la poudre IN690 résistante à la corrosion ? | Le haut chrome dans l'IN690 offre une excellente résistance aux acides oxydants et produits chimiques agressifs comme acide sulfurique et chlorures. |
Quels sont les principaux avantages de la poudre IN690 ? | Il offre stabilité à haute température, résistance à la corrosionet la durabilité à long termece qui en fait la solution idéale pour les applications critiques. |
Quelles sont les limites de l'utilisation de la poudre IN690 ? | Les principales limites sont les suivantes coût élevé et difficulté d'usinage, ce qui peut augmenter temps de production et coûts. |
La poudre IN690 est-elle adaptée aux environnements à haute température ? | Oui, il fonctionne bien à des températures allant jusqu'à 1000°CIl s'agit donc d'une solution idéale pour composants du four et turbines à gaz. |
La poudre IN690 peut-elle résister à des environnements corrosifs ? | Absolument. Grâce à son niveau élevé de chrome et nickel l'IN690 offre une excellente résistance à la corrosion dans les environnements exposés à l'humidité. acides. |
Réflexions finales : La poudre IN690 convient-elle à votre projet ?
Si vous avez besoin d'un matériau capable de résister températures extrêmes, oxydationet corrosionIl s'agit de l'un des les meilleures options disponibles. Son haute teneur en chromecombinée à l'expérience inhérente à l'utilisation de la technologie de l'information et de la communication (TIC). résistance du nickelIl s'agit donc d'un excellent choix pour des secteurs tels que énergie nucléaire, traitement chimiqueet aérospatiale.
Alors que la coût peut être un peu plus élevé que celui d'autres matériaux, la performance à long terme et la durabilité de Poudre IN690 compensent souvent l'investissement initial. Que vous l'utilisiez pour fabrication additive, revêtements par pulvérisation thermiqueou moulage traditionnel, Poudre IN690 est un outil polyvalent et un choix fiable pour les applications critiques.
En conclusion, si votre projet exige stabilité à haute température, résistance à la corrosionet fiabilité à long terme, il est un excellent matériau à considérer. Il a fait ses preuves dans certains des domaines les plus importants de l'économie. industries exigeantesVous pouvez faire confiance IN690 pour délivrer le performance et la durabilité vos besoins en matière d'applications.
Obtenir le dernier prix
À propos de Met3DP
Catégorie de produits
HOT SALE
CONTACTEZ-NOUS
Vous avez des questions ? Envoyez-nous un message dès maintenant ! Nous répondrons à votre demande avec toute une équipe dès réception de votre message.
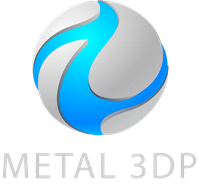
Poudres métalliques pour l'impression 3D et la fabrication additive