금속 3D 프린팅 파우더
목차
개요 금속 3D 프린팅 파우더
금속 3D 프린팅 파우더는 다양한 금속 적층 제조 공정에서 3차원 금속 부품을 한 층씩 제작하는 데 사용되는 원료를 말합니다. 재료를 제거하는 기존의 감산 제조와 달리 적층 제조는 디지털 3D 모델을 기반으로 재료를 녹이고 융합하여 부품을 제작합니다.
3D 프린팅에 사용되는 금속 분말을 사용하면 기존 방법으로는 제조하기 어렵거나 불가능한 복잡한 형상의 정교하고 가벼운 고성능 금속 부품을 제작할 수 있습니다. 금속 분말을 활용하는 가장 일반적인 금속 3D 프린팅 기술은 다음과 같습니다:
- 직접 금속 레이저 소결(DMLS) - 레이저를 사용하여 3D CAD 모델을 기반으로 금속 분말 층을 선택적으로 녹여 융합합니다.
- 전자빔 용융(EBM) - 진공 상태에서 전자빔을 사용하여 분말을 한 층씩 녹여 융합합니다.
- 바인더 분사 - 액체 결합제는 분말 재료를 결합하기 위해 선택적으로 증착되며, 이후 소결로에서 청동과 함께 주입됩니다.
금속 3D 프린팅 파우더 유형
금속 | 설명 | 속성 | 애플리케이션 |
---|---|---|---|
스테인리스 스틸 | 경제성, 내식성, 용접성이 결합되어 3D 프린팅에서 가장 널리 사용되는 금속 분말입니다. 일반적인 등급으로는 316L(해양 등급), 17-4 PH(고강도 및 침전 경화), 304(범용) 등이 있습니다. | - 우수한 내식성 - 고강도 - 우수한 연성 - 생체 적합성(특정 등급) | - 항공우주 부품(비임계) - 의료용 임플란트 및 장치 - 화학 처리 장비 - 자동차 부품 - 보석류 |
티타늄 | 생체 적합성과 우수한 중량 대비 강도 비율로 높이 평가되는 고강도, 저중량 금속입니다. 가장 일반적인 합금은 Ti6Al4V(티타늄 6% 알루미늄, 바나듐 4%)입니다. | - 높은 중량 대비 강도 - 우수한 내식성 - 생체 적합성 - 높은 융점 | - 항공우주 부품(중요) - 생체의료용 임플란트(무릎 인공관절, 뼈판) - 해양 부품 - 스포츠용품(골프채, 자전거) |
알루미늄 | 가볍고 저렴한 금속으로 전도성과 가공성이 우수합니다. 일반적인 합금으로는 6061(범용), 7075(고강도), 2024(항공우주) 등이 있습니다. | - 경량 - 우수한 전도성 - 우수한 가공성 - 재활용 가능 | - 자동차 부품(프레임, 휠) - 항공우주 부품(비임계) - 가전제품 - 방열판 |
니켈 합금 | 뛰어난 내열성, 내식성 및 기계적 강도로 잘 알려진 고성능 합금의 한 종류입니다. 일반적인 종류로는 인코넬 625(열악한 환경에 대한 뛰어난 내성)와 인코넬 718(고온에서 높은 강도)이 있습니다. | - 뛰어난 내열성 - 우수한 내식성 - 고온에서의 높은 강도 - 내산화성 | - 가스터빈 엔진 부품 - 열교환기 - 화학 처리 장비 - 원자로 |
코발트 크롬 | 강도, 내식성, 내마모성 때문에 일반적으로 사용되는 생체 적합성 합금입니다. | - 고강도 - 우수한 내마모성 - 우수한 내식성 - 생체 적합성 | - 생체 의학 임플란트(관절 대체물, 치과 임플란트) - 절삭 공구 - 마모 플레이트 |
공구강 | 절삭, 성형, 전단 등 특정 공구 가공을 위해 제조된 강재 그룹입니다. 일반적인 유형으로는 H13(열간 가공 공구강)과 A2(냉간 가공 공구강)가 있습니다. | - 높은 경도 - 내마모성 - 치수 안정성 - 인성(유형에 따라 다름) | - 절삭 공구 - 금형 및 금형 - 펀치 및 가위 - 마모 부품 |
귀금속 | 높은 비용으로 인해 금속 3D 프린팅에서는 덜 일반적이지만 높은 전기 전도도, 내식성, 생체 적합성 등의 고유한 특성을 제공합니다. 예를 들면 금, 은, 백금 등이 있습니다. | - 높은 전기 전도성 - 우수한 내식성 - 생체 적합성(특정 유형) - 높은 반사율(금속에 따라 다름) | - 전기 커넥터 - 쥬얼리 - 생체 의료용 임플란트(제한적 사용) - 고성능 방열판 |
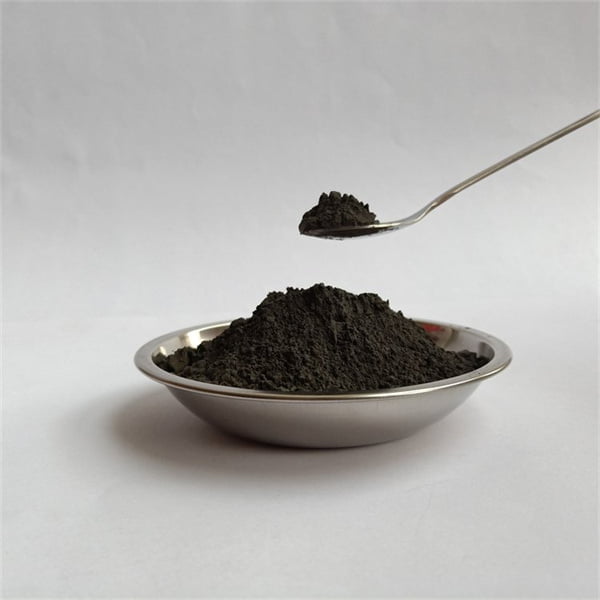
금속 분말 생산
스테이지 | 프로세스 | 설명 | 품질 관리 |
---|---|---|---|
공급 원료 확보 | 재료 선택 | 티타늄, 강철 또는 알루미늄 합금과 같은 다양한 순도의 고품질 원료를 선택하여 원하는 최종 부품 특성을 충족합니다. | X-선 형광(XRF) 또는 광학 방출 분광법(OES)과 같은 기술을 사용한 화학 성분 분석 |
** | 사전 처리** | 벌크 재료를 더 작은 조각으로 분쇄 및 분쇄하여 추가 가공에 적합한 일관된 입자 크기 분포를 가진 공급 원료를 생성합니다. | 체질 또는 레이저 회절을 이용한 입자 크기 분석으로 분무에 적합한 공급 원료를 보장합니다. |
원자화 | 가스 분무** | 용융 금속을 고압 불활성 가스 흐름에 주입하여 미세한 안개를 만들어 빠르게 냉각하고 구형 금속 입자로 응고시킵니다. | 레이저 회절 및 유량계를 이용한 입자 크기 분포, 형태(모양) 및 유동성 분석을 통해 최적의 분말 특성을 보장합니다. |
** | 물 분무** | 가스 분무와 유사하지만 용융 금속을 고압의 물 흐름에 주입합니다. 이 방법은 일반적으로 알루미늄과 같이 반응성이 낮은 금속에 사용됩니다. | 가스 분무와 유사한 품질 관리 조치를 통해 일관된 입자 특성을 보장합니다. |
포스트 프로세싱 | 심사 및 분류** | 파우더는 체를 통과하여 크기가 크거나 크기가 작은 입자를 제거하여 최적의 인쇄를 위한 좁은 입자 크기 분포를 달성합니다. | 입자 크기 분포 분석을 통해 원하는 입자 크기 범위의 준수 여부를 확인합니다. |
** | 먼지 제거 및 청소** | 분무 시 사용되는 산화물, 수분, 윤활제 등의 불순물을 제거하여 높은 분말 순도를 보장합니다. | 산소 함량을 측정하고 표면 오염 물질을 최소화하기 위해 XRF와 같은 화학 분석 기술을 사용합니다. |
** | 구상화** | 특정 용도의 경우 선택적 단계입니다. 분말은 구형성을 개선하기 위해 추가 가공을 거쳐 유동성과 인쇄성이 향상됩니다. | 형태학적 분석을 통해 입자의 둥근 정도를 평가하고 높은 수준의 구형성을 보장합니다. |
** | 진공 건조** | 진공 챔버를 사용하여 파우더 입자 내에 갇힌 수분을 제거하여 인쇄 중 불량을 방지합니다. | 칼 피셔 적정법을 사용하여 수분 함량을 측정하고 허용 범위 내에 있는지 확인합니다. |
** | 불활성 가스 포장** | 완성된 파우더를 아르곤과 같은 불활성 가스로 채워진 밀폐 용기에 포장하여 보관 및 운송 중에 산화를 최소화하고 파우더 품질을 유지합니다. | 용기의 누출 테스트 및 잔류 산소 분석을 통해 적절한 포장과 산소 노출 최소화를 보장합니다. |
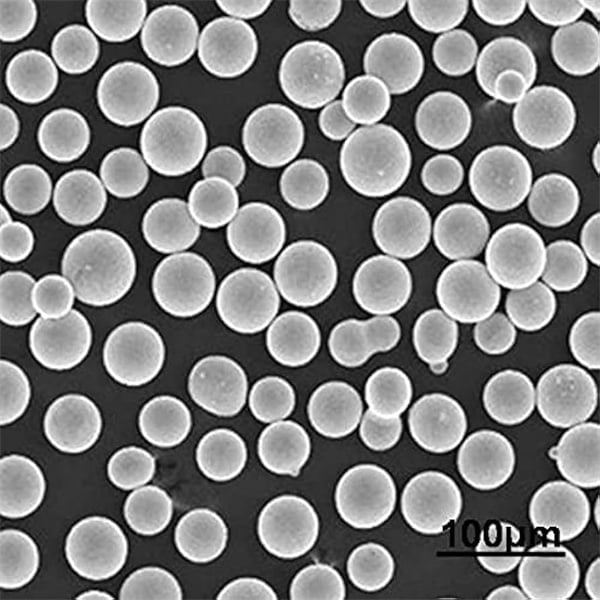
금속 분말 속성
3D 프린팅을 위한 주요 파우더 속성은 다음과 같습니다:
매개변수 | 설명 |
---|---|
파티클 모양 | 구형, 위성, 각형 |
입자 크기 | 공통 범위 10-100미크론 |
크기 분포 | 미세 입자와 거친 입자의 혼합 |
유동성 | 입자가 자체 무게로 유동하는 능력 |
겉보기 밀도 | 정상 조건에서의 분말 밀도 |
탭 밀도 | 기계적 두드림/교반 후 밀도 |
순도 | 산화물 및 질화물과 같은 오염 물질이 없습니다. |
마이크로 구조 | 입자 크기, 상 분포, 결함 |
수분 함량 | 불활성 대기에서 낮게 유지해야 합니다. |
입자 크기 및 분포 분말 흐름, 용융 효율, 표면 품질, 다공성 및 기계적 특성에 직접적인 영향을 미칩니다. 크기가 미세할수록 해상도가 향상되고 크기가 클수록 비용이 절감됩니다. 혼합이 이상적입니다.
파우더 모양 및 표면 질감 입자 간 마찰, 유동성, 확산성 및 벌크 밀도를 결정합니다. 매끄러운 구형 분말은 높은 포장 밀도로 최적으로 흐르고 퍼집니다.
분말 특성을 제어하고 합금을 맞춤화하려면 야금, 분말 생산, 적층 제조 공정 및 재료 과학에 대한 전문 지식이 필요합니다.
금속 3D 프린팅 파우더의 응용 분야
산업 | 애플리케이션 | 혜택 | 자료 고려 사항 |
---|---|---|---|
항공우주 | 항공기용 경량, 고강도 부품(예: 브래킷, 열교환기) 로켓 엔진 부품 연료 인젝터 | 연비 향상을 위한 무게 감소 최적화된 성능을 위한 복잡한 내부 형상 방열을 위한 복잡한 격자 구조의 제작 | 뛰어난 중량 대비 강도와 고온 성능을 제공하는 티타늄 합금 극한의 열과 압력을 견딜 수 있는 인코넬 중요하지 않은 영역의 경량 구조물을 위한 알루미늄 합금 |
의료 | 맞춤형 보철 및 임플란트(예: 고관절 치환술, 치과 크라운) 인체공학적으로 개선된 수술 기구 뼈 재생 스캐폴드를 위한 생체 적합성 재료 | 환자 해부학적 구조와 완벽하게 일치하는 개인 맞춤형 의료 기기 다공성 구조로 뼈의 성장을 촉진하여 골유착을 개선합니다. 환자 맞춤형 기기로 침습적 수술의 필요성 감소 | 생체 적합성과 우수한 골유착 특성을 지닌 티타늄 및 탄탈륨 특정 응용 분야에서 강도와 내식성을 갖춘 스테인리스 스틸 고응력 임플란트의 내마모성을 위한 코발트-크롬 합금 |
자동차 | 경량화 및 연비 향상을 위한 부품 경량화(예: 휠, 서스펜션 부품) 고성능 엔진 구성 요소 커스터마이징 가능한 레이싱 부품 | 성능을 향상시키는 복잡한 형상을 자유롭게 설계할 수 있습니다. 빠른 디자인 반복을 위한 신속한 프로토타이핑 한정판 또는 일회성 부품 생산 | 강도가 우수한 경량 구조용 알루미늄 합금 고응력 애플리케이션의 고강도 부품을 위한 티타늄 합금 극한의 온도와 압력을 견딜 수 있는 니켈 합금 |
소비재 | 럭셔리 주얼리 및 맞춤형 디자인 제품 한정판 스포츠 용품 맞춤형 소비자 가전 부품 | 복잡하고 독특한 디자인 제작 기존 감산 제조 방식에 비해 낭비 감소 개인화된 제품을 위한 대량 사용자 지정 | 금, 은, 백금과 같은 귀금속으로 고가의 보석류 구매 가능 내구성이 뛰어난 소비재를 위한 스테인리스 스틸 및 알루미늄 합금 전자제품의 미적 매력과 열 전도성을 위한 구리 |
에너지 | * 열교환기 및 원자로용 부품 * 복잡한 터빈 블레이드의 적층 제조 * 석유 및 가스 탐사를 위한 맞춤형 부품 생산 | * 까다로운 환경에서 사용하기 위한 고성능 소재 * 효율성 향상을 위한 경량 구조 * 열 전달 및 유체 흐름 최적화를 위한 자유로운 설계 | 탁월한 고온 강도와 내식성을 갖춘 니켈 합금 내구성과 열악한 환경에서도 견딜 수 있는 스테인리스 스틸 원자력 응용 분야에서 극한의 열과 압력을 견딜 수 있는 인코넬 |
금속 3D 프린팅 분말 공급업체
3D 프린팅에 특화된 표준 및 맞춤형 금속 분말을 제조하는 여러 글로벌 공급업체가 있습니다:
공급업체 | 본사 | 파우더 재료 |
---|---|---|
샌드빅 | 스웨덴 | 스테인리스강, 니켈 합금, 티타늄 합금, 공구강 |
목수 첨가제 | 미국 | 스테인리스강, 코발트 크롬, 구리, 니켈 합금 |
프렉스에어 | 미국 | 티타늄, 니켈 초합금, 스테인리스 스틸 |
GKN 분말 야금 | 미국 | 스테인리스강, 티타늄, 알루미늄 합금 |
LPW 기술 | UK | 티타늄 합금, 알루미늄 합금, 스테인리스강 |
합금 화학을 맞춤화하고, 분말 특성을 수정하고, 배치 간 일관성을 보장하고, 부품 품질을 위해 협업할 수 있는 공급업체의 역량은 분말 소싱 결정에 있어 중요한 요소입니다.
금속 분말 비용
금속 유형 | 가격 범위(kg당 USD) | 일반적인 애플리케이션 | 주요 고려 사항 |
---|---|---|---|
표준 금속 | $50 – $100 | * 알루미늄(AlSi10Mg) * 스테인리스 스틸(316L) * 티타늄(Ti6Al4V) | * 일반적으로 프로토타입 및 저응력 부품에 적합한 비용 효율적인 옵션입니다. * 알루미늄은 중량 대비 강도와 가공성이 우수합니다. * 316L 스테인리스 스틸은 내식성으로 유명합니다. * Ti6Al4V는 생체 적합성과 높은 중량 대비 강도 비율로 인해 항공우주 및 의료 분야에서 사용됩니다. |
고성능 금속 | $300 – $600 | * 니켈 초합금(인코넬 625) * 코발트 크롬(CoCr) * 공구강(H13) | * 고온에서 뛰어난 기계적 특성 또는 내마모성이 요구되는 응용 분야를 대상으로 합니다. * 인코넬 625는 극한의 온도를 견디고 강도를 유지하는 능력으로 인해 항공우주 분야에서 널리 사용됩니다. * CoCr은 생체 적합성과 높은 강도로 인해 의료용 임플란트에서 널리 사용됩니다. * H13은 뛰어난 경도와 내마모성으로 인해 툴링 분야에 많이 사용됩니다. |
귀금속 | $1,000 – $50,000+ | * 골드 * 실버 * 플래티넘 | * 주로 보석, 전자, 항공우주 분야의 미적 또는 고부가가치 애플리케이션에 사용됩니다. * 금은 전기 전도성과 내식성이 뛰어납니다. * 은은 항균성과 높은 열전도율로 유명합니다. * 백금은 녹는점과 부식에 대한 저항성으로 인해 고온의 도가니와 전기 접점에 사용됩니다. |
희토류 금속 | 공급업체에 문의 | * 이트륨 * 네오디뮴 * 에르븀 | * 제한된 가용성과 고유한 특성으로 인해 비용이 증가합니다. * 이트륨은 고체 레이저와 초전도체에 사용됩니다. * 네오디뮴은 고출력 자석의 핵심 구성 요소입니다. * 에르븀은 광섬유 증폭기 및 레이저에 사용됩니다. |
금속 분말 사양
사양, 테스트 방법, 파우더 인증에 대한 업계 표준이 진화하고 있습니다:
표준 | 조직 | 범위 |
---|---|---|
ASTM F3049 | ASTM 국제 | 적층 제조용 금속 분말 특성 분석을 위한 표준 가이드 |
ASTM F3056 | ASTM 국제 | 적층 제조 니켈 합금 사양 |
AS9100 개정 D | SAE 국제 | 항공우주 품질 관리 시스템 |
ISO/ASTM 52900 | ISO/ASTM | AM 표준 용어 - 일반 원칙 |
ISO/ASTM 52921 | ISO/ASTM | DMLS/SLM에 사용되는 금속 분말 표준 |
입자 크기 분포, 유량, 밀도, 조성과 같은 주요 분말 특성은 이러한 사양에 따라 테스트됩니다. 고객은 금속 분말 제조업체로부터 추가 테스트 데이터, 배치 분석 보고서, 규정 준수 인증서를 요구할 수 있습니다.
금속 3D 프린팅 파우더의 장단점
기능 | 장점 | 단점 |
---|---|---|
자유로운 디자인 | * 기존 방식으로는 불가능한 복잡한 형상을 구현합니다. * 내부 격자로 경량 구조를 생성하여 뛰어난 중량 대비 강도 비율을 제공합니다. * 부품의 온디맨드 커스터마이징이 가능합니다. | * 프린터의 제작 용량과 소프트웨어 기능에 따라 제한됩니다. |
머티리얼 속성 | * 고강도, 내열성 또는 생체 적합성과 같은 고유한 특성을 지닌 다양한 금속 분말을 사용할 수 있습니다. * 전통적으로 제조된 금속과 유사한 특성을 가진 부품을 제작할 수 있습니다. | * 분말 특성은 인쇄성과 최종 제품 품질에 영향을 미칠 수 있습니다. * 일부 고성능 금속은 특수 인쇄 환경이 필요합니다. |
생산 효율성 | * 감산 제조 기술에 비해 폐기물이 감소합니다. * 복잡한 부품을 한 번에 생산할 수 있어 조립이 필요 없습니다. * 프로토타이핑 및 소량 생산 시 리드 타임을 단축합니다. | * 인쇄 속도가 느리고 재료 비용이 높아 대량 생산에는 적합하지 않습니다. * 원하는 표면 마감과 치수 정확도를 얻기 위해 세심한 후처리가 필요합니다. |
안전 | * 특정 금속 분말은 인화성 또는 독성으로 인해 위험할 수 있습니다. * 위험을 최소화하기 위해 적절한 취급 절차와 개인 보호 장비(PPE)가 필요합니다. | * 결합된 금속 필라멘트는 일부 애플리케이션에서 더 안전한 대안을 제공합니다. * 분말 처리 기술의 발전으로 안전성이 향상되고 있습니다. |
비용 | * 금속 3D 프린터 및 파우더 재료에 대한 높은 초기 투자 비용. * 파우더 취급, 유지보수 및 폐기물 처리와 관련된 지속적인 비용. | * 기존 방식에 비해 복잡한 부품이나 소규모 생산에 비용 효율적일 수 있습니다. * 인건비 절감 및 생산 워크플로 간소화 가능성. |
환경 영향 | * 감산 제조에 비해 자재 낭비 감소. * 주문형 생산이 가능하여 초과 재고 및 운송 수요를 최소화할 수 있습니다. | * 에너지 집약적인 인쇄 공정은 환경 발자국이 더 클 수 있습니다. * 폐 분말을 처리할 때는 환경에 미치는 영향을 최소화하기 위해 적절한 처리가 필요합니다. |
금속 3D 프린팅 파우더의 미래
금속 분말의 미래 로드맵을 형성하는 주요 트렌드:
새로운 합금: 단조 알루미늄과 티타늄의 특성에 맞는 합금 선택의 폭이 넓어지면서 구조용 부품의 채택이 확대될 것입니다. 고강도 강철, 구리 합금 및 귀금속에 대한 연구개발이 진행 중입니다.
개선된 파우더: 크기 분포, 모양 및 미세 구조를 보다 엄격하게 제어하면 특정 적층 제조 공정 및 응용 분야에 맞는 파우더를 만들 수 있습니다. 이를 통해 품질과 재료 특성이 향상됩니다.
재활용 시스템: 폐쇄형 루프에서 금속 분말을 수집, 특성화 및 재사용하는 산업 간 인프라는 3D 프린팅의 지속 가능성을 높일 것입니다.
자동화된 워크플로: 컨테이너, 센서, 무인 운반차를 이용한 분말 취급의 간소화된 워크플로로 안전성, 일관성, 생산성을 개선할 수 있습니다.
인증 인프라: 분말 인증 및 부품 검증 서비스를 제공하는 중앙 집중식 기관은 의료 및 항공우주와 같은 핵심 산업에서 적층 가공을 도입할 수 있도록 자신감을 심어줄 것입니다.
전문화: 적층 제조 가치 사슬의 틈새 분야를 전문으로 하는 시스템 제조업체, 금속 분말 생산업체, 부품 구매업체, 소프트웨어 회사, 재료 과학자들이 집중적인 혁신을 주도할 것입니다.
비용 절감: 대량 분말 제조, 표준화된 합금, 자동화된 후처리 및 디지털 재고 관리와 같은 접근 방식은 경제성을 개선합니다.
이러한 분야에서 지속적인 발전이 이루어지면서 금속 3D 프린팅의 산업화와 주류 채택은 여러 주요 시장에서 향후 10년간 강력한 성장세를 보일 것으로 예상됩니다.
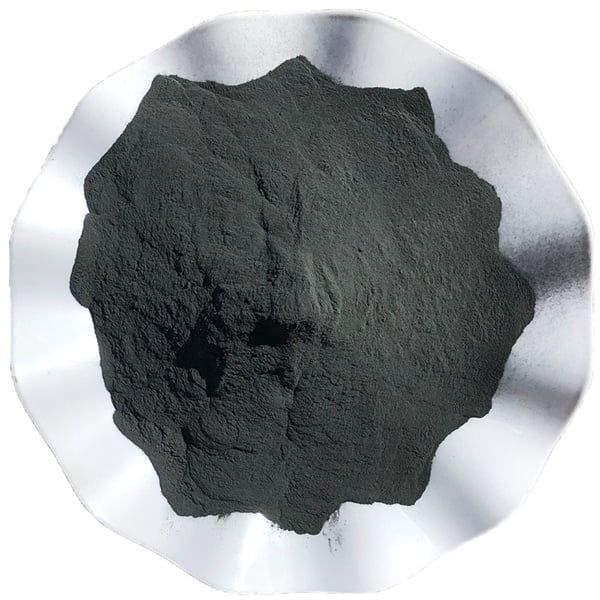
자주 묻는 질문
Q: 3D 프린팅에서 가장 일반적으로 사용되는 금속 파우더는 무엇인가요?
A: 316L 스테인리스 스틸은 우수한 기계적 특성, 용접성 및 내식성으로 인해 오늘날 가장 널리 사용되는 금속 분말입니다. 다른 인기 있는 옵션으로는 티타늄 Ti64와 알루미늄 AlSi10Mg가 있습니다.
Q: 애플리케이션에 적합한 금속 파우더를 선택하는 방법은 무엇인가요?
A: 주요 고려 사항은 작동 온도, 내식성, 내마모성, 부품 강도, 무게 요구 사항, 전도성 요구 사항, 생체 적합성, 식품 접촉 상태 및 후처리 제약 조건입니다. 합금 권장 사항에 대해서는 파우더 제조업체와 애플리케이션 세부 사항을 논의하세요.
Q: 더 미세한 금속 파우더를 사용하면 부품 품질이 향상되나요?
A: 더 미세한 파우더(~10~45미크론)는 더 얇은 층을 융합할 수 있기 때문에 해상도, 표면 마감 및 정밀도가 향상됩니다. 하지만 제작 속도가 느려지고 비용이 증가합니다. 미세 입자와 거친 입자를 혼합하면 균형 잡힌 접근 방식을 제공합니다.
Q: 금속 분말은 어떻게 보관 및 취급 시 오염되지 않고 안전하게 보관할 수 있나요?
A: 금속 분말은 반응성이 높고 산화되기 쉽습니다. 습기를 흡수하면 시간이 지남에 따라 파우더 품질도 저하됩니다. 따라서 불활성 가스 분위기, 진공 보관, 밀폐된 용기, 자동화된 분말 취급을 통한 산소/수분 노출 최소화는 필수적입니다.
Q: 3D 프린팅에서 재료 비용을 줄이기 위해 금속 분말을 재사용할 수 있나요?
A: 예, 하지만 재사용에는 여러 가지 조건이 따릅니다. 사용하지 않은 파우더는 재사용할 수 있지만 여러 번의 주기 동안 오염, 입자 크기 분포 또는 구성의 변화를 확인하려면 광범위한 테스트가 필요합니다. 이러한 특성 분석에는 비용과 위험이 추가됩니다.
공유
중국 칭다오에 본사를 둔 선도적인 적층 제조 솔루션 제공업체인 MET3DP Technology Co. 당사는 산업용 3D 프린팅 장비와 고성능 금속 분말을 전문으로 합니다.
관련 기사
Met3DP 소개
최근 업데이트
제품
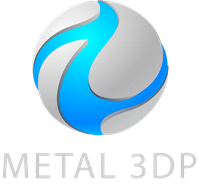
3D 프린팅 및 적층 제조용 금속 분말