3D Printed Surgical Drill Templates: Precision and Efficiency in the Operating Room
목차
Introduction – Revolutionizing Surgical Procedures with Metal 3D Printing
In the intricate world of surgery, precision is paramount. Every millimeter counts, and the accuracy of surgical tools directly impacts patient outcomes. Traditional methods of creating surgical guides often involve time-consuming processes and may lack the level of customization required for complex cases. Enter metal 3D 프린팅, a transformative technology that is revolutionizing the creation of surgical drill templates. These patient-specific guides, manufactured with exceptional accuracy using advanced metal powders, are enhancing the efficiency, safety, and predictability of a wide range of surgical procedures. At Metal3DP, we are at the forefront of this innovation, providing high-quality metal 3D printing services and materials that empower medical professionals to achieve unprecedented levels of surgical precision.
What are 3D Printed Surgical Drill Templates Used For?
3D printed surgical drill templates, also known as surgical guides, are custom-made instruments designed to assist surgeons in accurately positioning drills during various surgical procedures. These templates act as a physical guide, ensuring that the drill is placed at the precise location, angle, and depth dictated by the pre-operative surgical plan. Their applications span across numerous medical specialties, including:
- Implant Dentistry: Guiding the placement of dental implants with optimal angulation and depth for long-term stability and prosthetic fit.
- Orthopedic Surgery: Assisting in the precise placement of screws, pins, and other fixation devices in procedures such as fracture repair, joint reconstruction, and spinal fusion.
- Cranio-Maxillofacial Surgery: Facilitating accurate drilling for reconstructive surgeries, trauma cases, and the placement of craniofacial implants.
- ENT Surgery: Guiding the placement of instruments in delicate procedures involving the ear, nose, and throat.
By utilizing these templates, surgeons can minimize the risk of off-target drilling, reduce surgical time, improve implant stability, and ultimately enhance patient outcomes. The single-use nature of these templates also contributes to maintaining sterility and reducing the risk of infection.
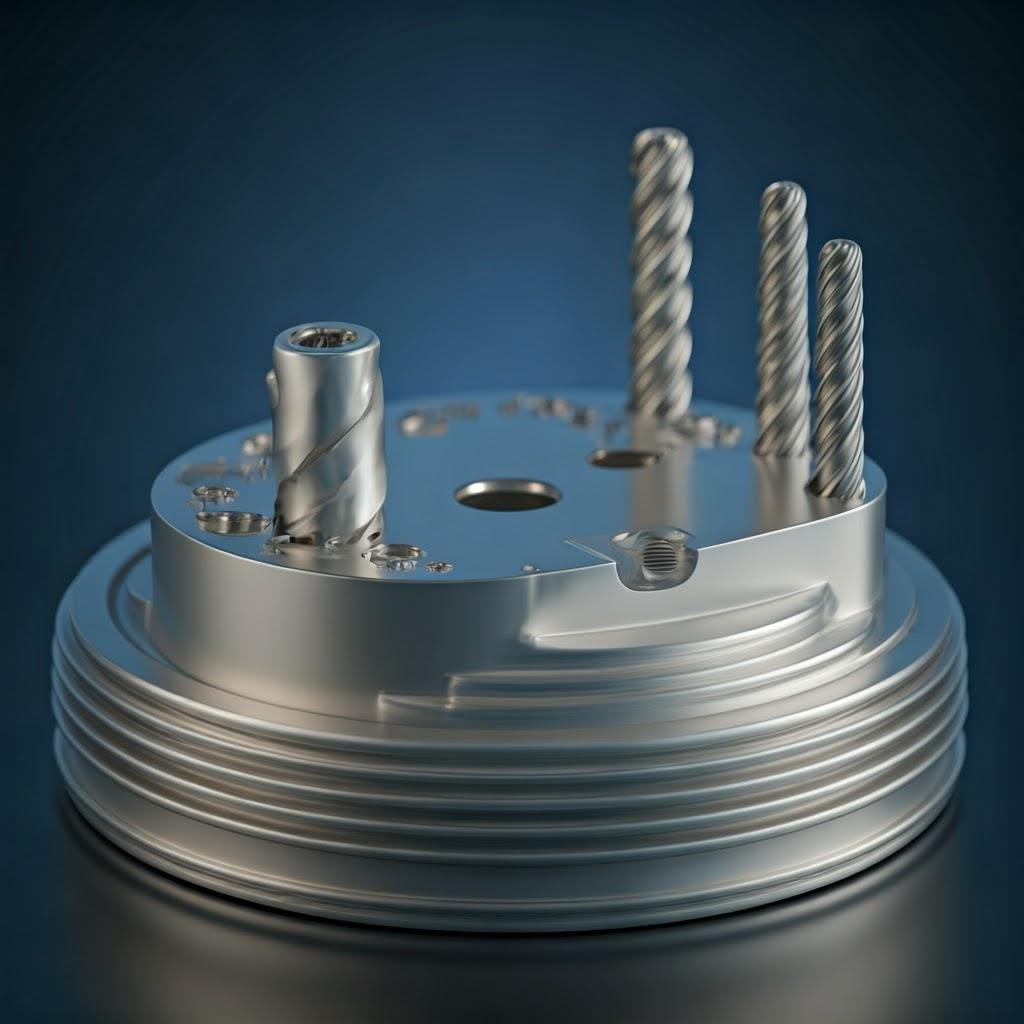
Why Use Metal 3D Printing for Surgical Drill Templates?
While surgical guides can be manufactured using various materials and techniques, metal 3D printing offers distinct advantages that make it an ideal choice for creating high-precision drill templates:
- Enhanced Accuracy: Metal 3D printing, particularly technologies like Selective Laser Melting (SLM) and Electron Beam Melting (EBM), can achieve intricate geometries and fine details with exceptional dimensional accuracy. This ensures that the drill template precisely matches the patient’s unique anatomy as derived from CT scans or other medical imaging.
- 생체 적합성: Certain metal powders specifically designed for medical applications, such as 316L stainless steel and Ti-6Al-4V ELI (Extra Low Interstitial) titanium alloy, offer excellent biocompatibility. This is crucial for surgical instruments that come into contact with patient tissue. Metal3DP offers a range of these high-quality metal powders.
- Sterilizability: Metal 3D printed templates can withstand standard sterilization methods, such as autoclaving, ensuring a sterile environment during surgery and minimizing the risk of infection.
- 사용자 지정: Additive manufacturing allows for the creation of fully customized templates tailored to the specific anatomical features of each patient and the requirements of the surgical plan. This level of personalization is difficult to achieve with traditional manufacturing methods.
- 복잡한 지오메트리: 3D printing enables the creation of complex template designs that can incorporate features such as drill sleeves, fixation points, and anatomical landmarks, further enhancing surgical accuracy and ease of use. Our printing methods support the fabrication of such intricate designs.
- Material Strength and Durability: Metals like stainless steel and titanium alloys offer high strength and durability, ensuring that the drill template can withstand the forces encountered during surgery without deformation or failure.
Recommended Materials and Why They Matter
The choice of metal powder is critical for the performance and biocompatibility of 3D printed surgical drill templates. At Metal3DP, we recommend the following materials for this application:
316L 스테인리스 스틸
- 속성: 316L is an austenitic stainless steel known for its excellent corrosion resistance, high strength, and good biocompatibility. The “L” designation indicates a low carbon content, which further enhances its resistance to corrosion, particularly after welding or heat treatment. Its high strength ensures the template’s structural integrity during surgical procedures.
- Why it Matters: In the medical field, corrosion resistance is paramount to prevent the degradation of the instrument and the release of potentially harmful ions into the body. The biocompatibility of 316L ensures minimal adverse tissue reactions. Its strength and durability guarantee the template’s reliability during critical surgical steps. You can learn more about the properties of 316L on our dedicated 316L stainless steel powder page.
Ti-6Al-4V ELI (Grade 23) Titanium Alloy
- 속성: Ti-6Al-4V ELI is an extra-low interstitial grade of the widely used Ti-6Al-4V titanium alloy. The reduced levels of oxygen, nitrogen, and carbon in ELI grade enhance its ductility, fracture toughness, and biocompatibility compared to standard Ti-6Al-4V. It boasts an exceptional strength-to-weight ratio and excellent corrosion resistance.
- Why it Matters: Titanium alloys, especially Ti-6Al-4V ELI, are highly biocompatible and exhibit excellent osseointegration, making them ideal for medical devices that interact with bone. The high strength-to-weight ratio allows for the creation of lightweight yet robust templates. The enhanced ductility and fracture toughness of the ELI grade ensure the template’s reliability and prevent brittle failure during use. Our range of titanium 3D printing powders includes this high-performance alloy.
By offering these high-quality metal powders and leveraging our expertise in metal additive manufacturing, Metal3DP empowers medical device manufacturers and healthcare professionals to create surgical drill templates that meet the most demanding requirements for precision, safety, and biocompatibility. Contact us today to explore how our metal 3D printing solutions can advance your surgical applications.
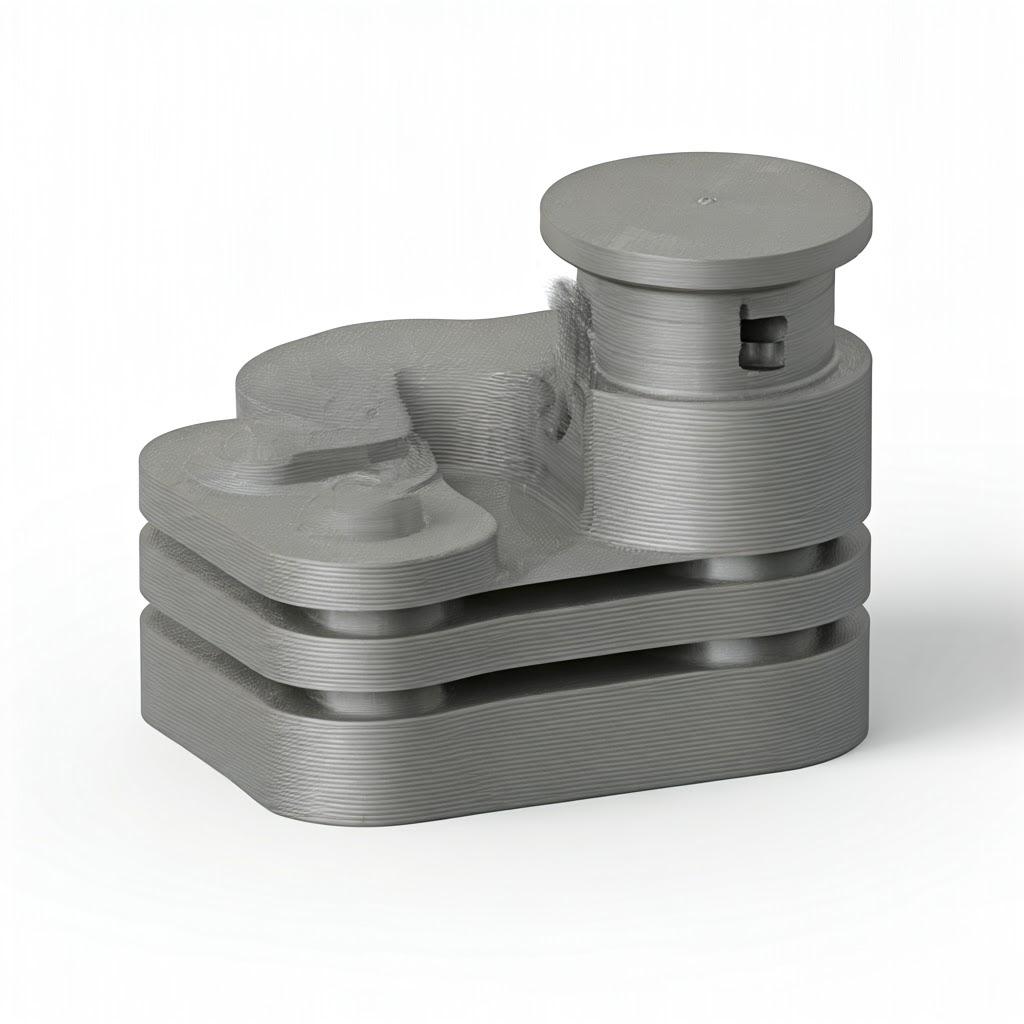
Design Considerations for Additive Manufacturing of Surgical Drill Templates
Designing surgical drill templates for metal 3D printing requires a different mindset compared to traditional manufacturing methods. To fully leverage the capabilities of additive manufacturing and ensure optimal functionality, accuracy, and cost-effectiveness, several design considerations must be taken into account:
- Patient-Specific Anatomy Integration: The design should precisely conform to the patient’s unique anatomical contours derived from medical imaging data (e.g., CT scans, MRI). This ensures accurate placement and stability of the template during surgery. Features like registration surfaces, anatomical landmarks, and fixation points should be incorporated based on the specific surgical site and procedure.
- Drill Sleeve Integration: The design must include precise housings or channels for drill sleeves. These sleeves guide the drill bit to the intended location, angle, and depth. The inner diameter of the sleeve should be carefully matched to the drill bit size, and the outer diameter should be securely integrated into the template design. Considerations for press-fit or other securement methods are crucial.
- Wall Thickness and Structural Integrity: While minimizing material usage is often desired in 3D printing, sufficient wall thickness is essential to ensure the template’s structural integrity and prevent deformation during the drilling process. The design should balance weight reduction with the need for robustness. Finite element analysis (FEA) can be employed to optimize the template’s geometry and ensure it can withstand the anticipated surgical forces.
- Support Structure Optimization: Metal 3D printing often requires support structures to prevent warping, sagging, and collapse of overhanging features during the build process. The design should aim to minimize the need for extensive support structures while ensuring the successful fabrication of critical features. Strategically placed self-supporting angles and optimized part orientation on the build platform can help reduce support material and post-processing time.
- Surface Finish Considerations: The surface finish of the template, particularly the inner surfaces of drill sleeves and registration areas, can impact the accuracy and ease of use. While metal 3D printed parts typically have a rougher surface finish compared to machined parts, careful process parameter optimization and potential post-processing steps (e.g., polishing, media blasting) can improve surface quality.
- Biocompatibility and Sterilization: The design should avoid sharp edges or intricate features that could complicate cleaning and sterilization. Smooth, accessible surfaces are preferred. The chosen metal powder must be biocompatible and able to withstand the intended sterilization methods (e.g., autoclaving).
- Identification and Traceability: Incorporating features like serial numbers, QR codes, or other identifiers directly into the template design through 3D printing can facilitate traceability and ensure the correct template is used for the intended patient.
- Design for Assembly (DfA): If the template consists of multiple parts, the design should consider ease of assembly and securement of the components. This might involve features like interlocking mechanisms or precise fitting surfaces.
By carefully considering these design principles, engineers and surgeons can collaborate to create metal 3D printed surgical drill templates that are highly accurate, functional, and tailored to the specific needs of each surgical case. Metal3DP의 expertise in design optimization for additive manufacturing can help streamline this process and ensure optimal outcomes.
Tolerance, Surface Finish, and Dimensional Accuracy of 3D Printed Surgical Drill Templates
Achieving the required tolerance, surface finish, and dimensional accuracy is paramount for the clinical success of 3D printed surgical drill templates. These factors directly influence the precision of drill placement and the overall outcome of the surgical procedure.
- 치수 정확도: Metal 3D printing technologies like SLM and EBM offer high levels of dimensional accuracy, typically within tens of micrometers. However, the achievable accuracy can be influenced by factors such as the size and complexity of the part, the chosen metal powder, and the process parameters. At Metal3DP, our advanced printing equipment and optimized process parameters ensure industry-leading accuracy for mission-critical medical parts.
- Tolerance: Tolerances specify the allowable variation in the dimensions of a part. For surgical drill templates, tight tolerances are crucial, especially for the inner diameter of drill sleeves and the fitment of the template to the patient’s anatomy. Metal 3D printing can achieve tight tolerances, but these should be carefully considered during the design phase and communicated to the manufacturing service provider. Post-processing steps like precision machining can be employed for features requiring extremely tight tolerances.
- 표면 마감: The surface finish of metal 3D printed parts is typically rougher than that of machined parts due to the layer-by-layer build process and the partially melted powder particles on the surface. The surface roughness can be quantified using parameters like Ra (average roughness). For surgical drill templates, the surface finish of critical areas, such as the inner diameter of drill sleeves, can affect the friction and guidance of the drill bit. Post-processing techniques like polishing, media blasting, and chemical etching can be used to improve the surface finish as needed.
Factors Affecting Accuracy and Surface Finish:
팩터 | Influence on Accuracy & Surface Finish |
---|---|
3D 프린팅 기술 | SLM and EBM generally offer higher accuracy and finer feature resolution compared to other metal AM technologies. |
금속분말 | The particle size distribution, sphericity, and flowability of the metal powder can impact the achievable density, surface finish, and accuracy of the printed part. Metal3DP’s advanced powder making system ensures high-quality metal powders with optimal characteristics. |
프로세스 매개변수 | Laser power, scan speed, layer thickness, and build orientation are critical parameters that influence the melting and solidification process, thereby affecting the accuracy and surface finish. |
Build Orientation | The orientation of the part on the build platform can affect the surface finish of downward-facing surfaces and the need for support structures, which can impact dimensional accuracy. |
포스트 프로세싱 | Techniques like CNC machining, polishing, media blasting, and coating can significantly improve the dimensional accuracy and surface finish of 3D printed parts. |
시트로 내보내기
Understanding these factors and collaborating closely with an experienced metal 3D printing service provider like Metal3DP is essential to achieve the required tolerance, surface finish, and dimensional accuracy for 3D printed surgical drill templates, ensuring their precise and reliable performance in the operating room.
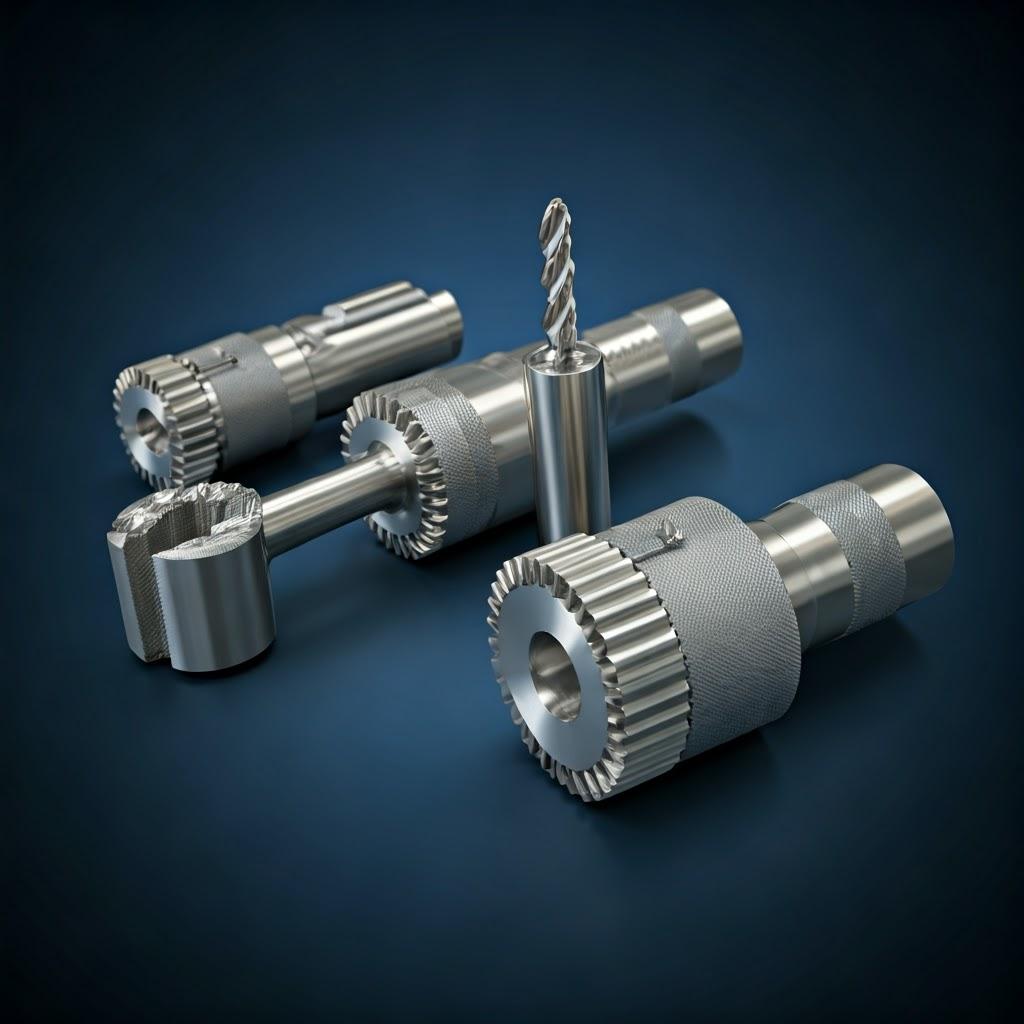
Post-Processing Requirements for Metal 3D Printed Surgical Drill Templates
While metal 3D printing offers significant advantages in creating complex and customized surgical drill templates, post-processing steps are often necessary to achieve the desired functional properties, surface finish, and sterility for medical applications. Common post-processing requirements for these templates include:
- 지원 구조 제거: Metal 3D printed parts often require support structures to maintain their geometry during the build process. These supports need to be carefully removed after printing. The removal process can involve manual methods (e.g., cutting, grinding) or automated techniques (e.g., wire EDM). The design of the template should aim to minimize the need for extensive and difficult-to-remove support structures.
- 열처리: Depending on the metal alloy and the intended application, heat treatment may be required to relieve internal stresses, improve mechanical properties (e.g., strength, hardness), or achieve the desired microstructure. For example, stainless steel might undergo stress relieving, while titanium alloys may require annealing or solution treatment followed by aging. The specific heat treatment cycle must be carefully controlled to ensure the desired material properties are achieved without compromising the dimensional accuracy of the template.
- 표면 마감: As mentioned earlier, metal 3D printed surfaces can be relatively rough. For surgical drill templates, smoother surfaces may be required for biocompatibility, ease of cleaning, and optimal interaction with surgical instruments. Common surface finishing techniques include:
- Media Blasting: Using abrasive media to remove partially sintered powder and reduce surface roughness.
- 연마: Mechanically or chemically smoothing the surface to achieve a desired level of finish. Electrochemical polishing is particularly useful for complex geometries.
- Passivation (for Stainless Steel): A chemical treatment to enhance the corrosion resistance of stainless steel by forming a protective oxide layer on the surface. 1 1. vinssco.com vinssco.com
- CNC 가공: For features requiring very tight tolerances or specific surface finishes that are difficult to achieve directly through 3D printing, precision CNC machining may be employed as a secondary operation. This can be used to refine the inner diameter of drill sleeves or create precise registration surfaces.
- Cleaning and Sterilization Preparation: Thorough cleaning is essential to remove any residual powder particles or contaminants from the 3D printed template. This typically involves ultrasonic cleaning and rinsing. The template must also be prepared for sterilization according to medical device regulations. This might involve packaging in sterile pouches after cleaning.
- Inspection and Quality Control: After all post-processing steps are completed, rigorous inspection and quality control procedures are necessary to verify the dimensional accuracy, surface finish, and material properties of the template. This may involve coordinate measuring machines (CMMs), optical scanners, and material testing.
The specific post-processing requirements for a metal 3D printed surgical drill template will depend on the material, the intended surgical application, and the regulatory requirements for medical devices. Collaborating with an experienced metal 3D printing service provider like Metal3DP ensures that all necessary post-processing steps are performed correctly to deliver a high-quality, safe, and effective surgical tool.
Common Challenges and How to Avoid Them in Metal 3D Printing of Surgical Drill Templates
While metal 3D printing offers numerous advantages for creating surgical drill templates, several challenges can arise during the design and manufacturing process. Understanding these potential issues and implementing appropriate strategies can help avoid complications and ensure the production of high-quality, accurate templates.
- Warping and Distortion: Thermal stresses generated during the layer-by-layer melting and solidification process can lead to warping or distortion of the printed part, particularly for complex geometries or thin-walled features.
- How to Avoid:
- Optimize Part Orientation: Orienting the part strategically on the build platform can minimize the build height and the extent of overhanging features, reducing the likelihood of warping.
- Support Structure Optimization: Properly designed support structures can anchor the part to the build plate and counteract thermal stresses. However, excessive support can also induce stresses, so a balance is crucial.
- 프로세스 매개변수 최적화: Adjusting laser power, scan speed, and layer thickness can influence the heat input and cooling rates, thereby minimizing thermal stresses.
- 스트레스 완화 열처리: Performing a stress relief heat treatment after printing can alleviate internal stresses and reduce the risk of post-build distortion.
- How to Avoid:
- 다공성: The presence of voids or pores within the printed part can compromise its mechanical strength and biocompatibility.
- How to Avoid:
- Optimize Process Parameters: Using appropriate laser power, scan speed, and hatch spacing ensures sufficient melting and fusion of the metal powder particles, leading to a dense and solid part.
- 고품질 금속 분말: Employing high-quality metal powders with good flowability and sphericity, like those produced by Metal3DP’s advanced powder making system, promotes uniform powder bed packing and consistent melting.
- Inert Atmosphere Control: Maintaining a pure inert atmosphere within the build chamber minimizes oxidation and contamination, which can contribute to porosity.
- How to Avoid:
- 표면 거칠기: Metal 3D printed surfaces can be rough, which may not be ideal for all applications of surgical drill templates, particularly internal surfaces of drill sleeves.
- How to Avoid:
- Optimize Process Parameters: Reducing layer thickness and adjusting laser parameters can improve surface finish, although it may increase build time.
- 포스트 프로세싱 기법: Employing surface finishing techniques like media blasting, polishing, or chemical etching can significantly reduce surface roughness.
- How to Avoid:
- Support Removal Challenges: Removing support structures from intricate geometries can be difficult and may leave behind surface blemishes.
- How to Avoid:
- Design for Minimal Supports: Designing self-supporting angles and minimizing overhanging features can reduce the need for extensive support structures.
- Strategic Support Placement: Placing supports in less critical areas and using breakaway supports can simplify the removal process.
- Specialized Support Removal Techniques: Utilizing techniques like dissolvable supports or wire EDM for support removal can be beneficial for complex parts.
- How to Avoid:
- Dimensional Inaccuracy: Deviations from the intended dimensions can compromise the accuracy of the surgical drill template.
- How to Avoid:
- Accurate Design and File Preparation: Ensuring the 3D model is accurate and properly oriented for printing is crucial.
- Machine Calibration and Maintenance: Regularly calibrating and maintaining the 3D printer ensures consistent and accurate printing.
- Material Property Compensation: Accounting for material shrinkage during the solidification process in the design phase can improve dimensional accuracy.
- Post-Printing Inspection: Thoroughly inspecting the printed part using CMMs or other metrology equipment helps identify and address any dimensional inaccuracies.
- How to Avoid:
By proactively addressing these common challenges through careful design, optimized process parameters, the use of high-quality materials from trusted suppliers like Metal3DP, and appropriate post-processing techniques, manufacturers can consistently produce accurate and reliable metal 3D printed surgical drill templates.
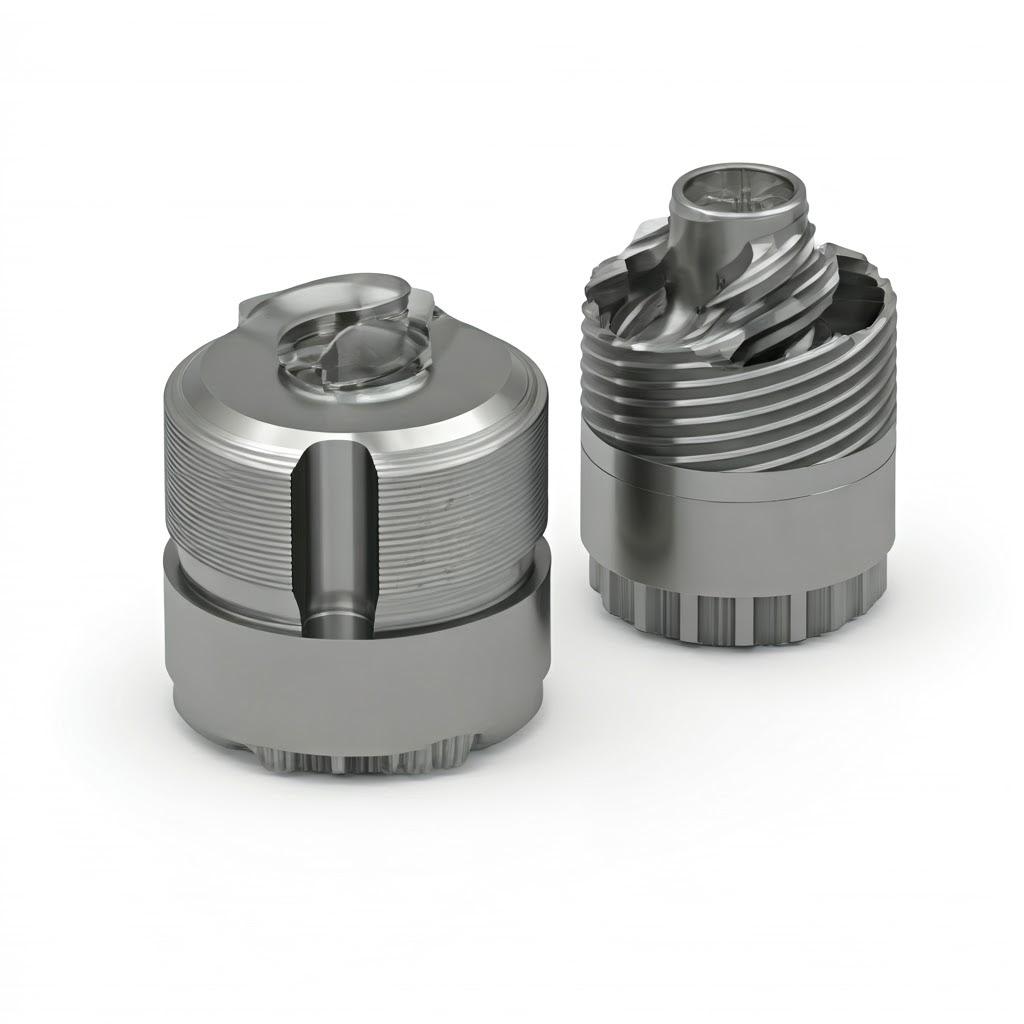
How to Choose the Right Metal 3D Printing Service Provider for Surgical Drill Templates
Selecting the right metal 3D printing service provider is crucial for obtaining high-quality surgical drill templates that meet stringent medical requirements. Here are key factors to consider when evaluating potential suppliers:
- Experience and Expertise in Medical Device Manufacturing: Look for a provider with a proven track record of manufacturing medical devices or components. Experience with regulatory requirements (e.g., ISO 13485 certification) and understanding the specific needs of the medical industry are essential.
- Material Capabilities and Biocompatibility: Ensure the provider offers the recommended biocompatible metal powders, such as 316L stainless steel and Ti-6Al-4V ELI. Inquire about material certifications and testing procedures to guarantee the quality and biocompatibility of the materials used. Metal3DP offers a comprehensive range of high-quality, certified metal powders suitable for medical applications.
- Printing Technology and Accuracy: Understand the types of metal 3D printing technologies the provider utilizes (e.g., SLM, EBM). Inquire about the achievable dimensional accuracy, tolerance capabilities, and surface finish. For surgical drill templates, high precision is paramount.
- Post-Processing Capabilities: Determine if the provider offers the necessary post-processing services, including support removal, heat treatment, surface finishing (polishing, passivation), and CNC machining if required. Ensure they have validated processes for cleaning and preparing medical devices for sterilization.
- Quality Management System: A robust quality management system (QMS) is critical for medical device manufacturing. Inquire about the provider’s certifications (e.g., ISO 9001, ISO 13485) and their quality control procedures, including inspection processes and documentation.
- Design Support and Collaboration: An experienced provider should be able to offer design consultation and optimization for additive manufacturing. They should be able to work collaboratively with your team to ensure the template design is suitable for metal 3D printing and meets the functional requirements.
- Scalability and Production Capacity: Consider the provider’s ability to scale up production if your needs increase in the future. Evaluate their production capacity and lead times.
- Confidentiality and Intellectual Property Protection: Ensure the provider has strict confidentiality agreements and measures in place to protect your intellectual property.
- Communication and Customer Support: Effective communication and responsive customer support are essential for a smooth and successful collaboration.
By carefully evaluating potential metal 3D printing service providers based on these criteria, you can select a partner like Metal3DP that has the expertise, capabilities, and quality systems to reliably produce high-precision metal 3D printed surgical drill templates that meet the demanding requirements of the medical field.
Cost Factors and Lead Time for Metal 3D Printed Surgical Drill Templates
The cost and lead time for manufacturing metal 3D printed surgical drill templates can vary depending on several factors. Understanding these factors can help in budgeting and planning for the production of these critical medical tools.
비용 요소:
- 재료비: The type and quantity of metal powder used are significant cost drivers. Materials like titanium alloys are generally more expensive than stainless steel. The complexity of the part design can also influence material usage.
- 구축 시간: The time it takes to print a template depends on its size, complexity, and the chosen layer thickness. Longer build times translate to higher machine operating costs.
- 지원 구조 볼륨: The volume and complexity of support structures required can impact material consumption and post-processing time, thus affecting the overall cost.
- 후처리 비용: The extent of post-processing required (e.g., support removal, heat treatment, surface finishing, CNC machining) will add to the manufacturing cost. More complex post-processing steps will result in higher costs.
- Machine and Labor Costs: The hourly operating costs of the metal 3D printer and the labor costs associated with design, printing, and post-processing are factored into the final price.
- Quantity and Batch Size: Similar to traditional manufacturing, producing larger quantities of templates can often lead to economies of scale and lower per-unit costs.
- 디자인 복잡성: More intricate designs may require more design time, complex support structures, and longer build times, increasing the overall cost.
- Quality Assurance and Regulatory Compliance: The costs associated with quality control procedures, material testing, and regulatory compliance for medical devices will be factored into the price.
리드 타임:
- Design and File Preparation: The time required to design the template and prepare the 3D printing files.
- 인쇄 시간: The actual time it takes for the 3D printer to build the template. This depends on the part’s size and complexity.
- 후처리 시간: The time required for support removal, heat treatment, surface finishing, and other post-processing steps. This can vary significantly depending on the complexity of the part and the required finish.
- Quality Control and Inspection: The time taken for thorough inspection and quality checks.
- Shipping and Delivery: The time required to package and ship the finished templates.
Estimating Cost and Lead Time:
It is recommended to provide a detailed design and specifications to potential metal 3D printing service providers like Metal3DP to obtain an accurate quotation for both cost and lead time. Factors such as material selection, design complexity, required post-processing, and quantity will all play a role in the final estimate. Understanding these factors will enable you to make informed decisions and plan effectively for the production of your metal 3D printed surgical drill templates.
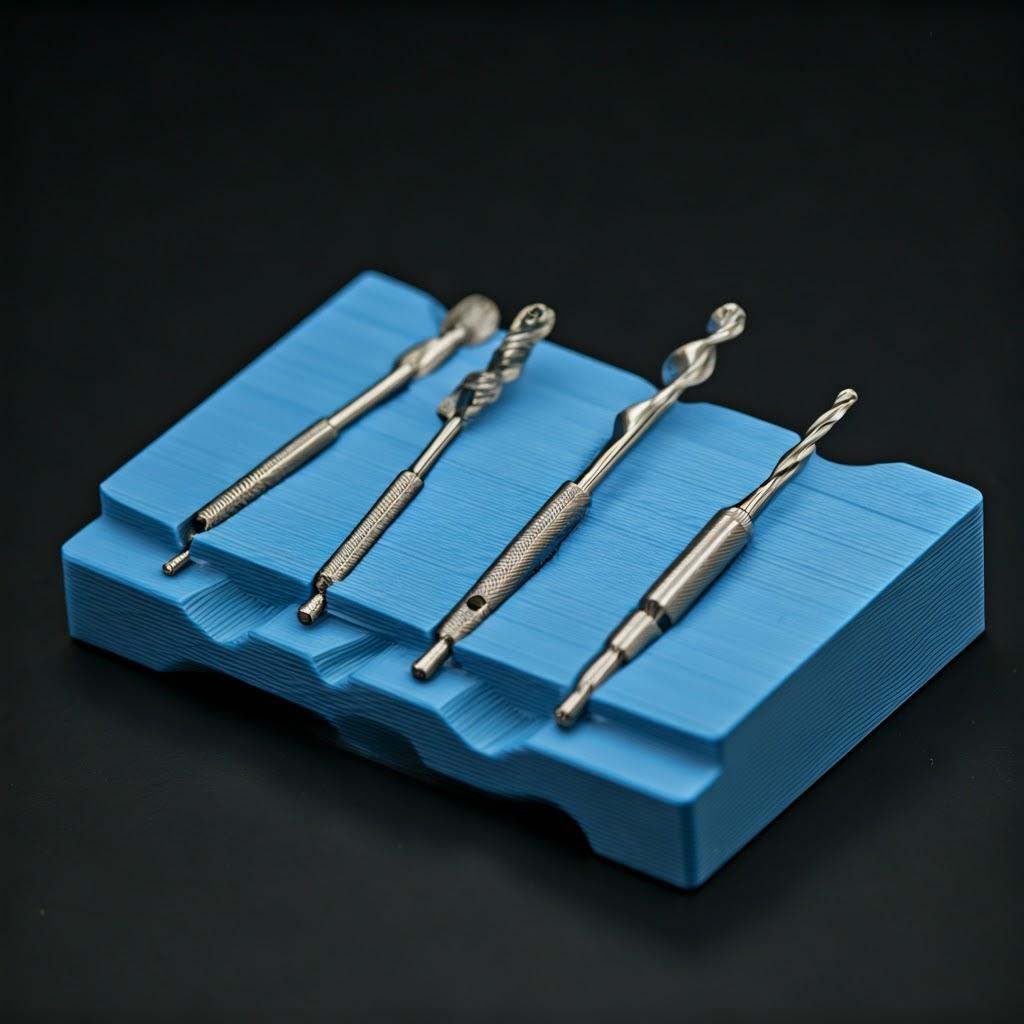
자주 묻는 질문(FAQ)
- What is the typical accuracy achievable with metal 3D printed surgical drill templates? Metal 3D printing technologies like SLM and EBM can achieve high dimensional accuracy, typically within ± 50-100 $\mu$m or even better for certain features. However, the actual accuracy can depend on the part’s size, geometry, and the chosen printing parameters. Post-processing, such as precision machining, can further enhance accuracy for critical features.
- Are metal 3D printed surgical drill templates biocompatible? Yes, when manufactured using biocompatible metal powders like 316L stainless steel and Ti-6Al-4V ELI, metal 3D printed surgical drill templates are biocompatible and suitable for medical applications. It is crucial to ensure that the chosen material has the necessary certifications and that the manufacturing process maintains material purity. Metal3DP provides metal powders with stringent quality control and biocompatibility.
- Can metal 3D printed surgical drill templates be sterilized? Yes, metal 3D printed surgical drill templates made from materials like stainless steel and titanium alloys can withstand common sterilization methods used in healthcare settings, such as autoclaving (steam sterilization). Proper cleaning and validated sterilization procedures are essential before surgical use.
Conclusion – Embracing the Future of Surgical Precision with Metal 3D Printing
Metal 3D printing is transforming the landscape of surgical tool manufacturing, offering unprecedented opportunities for creating highly accurate, patient-specific surgical drill templates. The ability to utilize biocompatible materials like 316L and Ti-6Al-4V ELI, coupled with the design freedom and precision of additive manufacturing, empowers surgeons to achieve enhanced accuracy, efficiency, and predictability in a wide range of surgical procedures.
By understanding the design considerations, material properties, post-processing requirements, and how to choose the right service provider, medical device companies and healthcare professionals can leverage the power of metal 3D printing to create innovative surgical solutions. Metal3DP, with our expertise in advanced metal powders, cutting-edge printing technology, and comprehensive application development services, is your trusted partner in realizing the full potential of metal additive manufacturing for surgical applications. Contact us today to explore how our capabilities can power your organization’s journey towards next-generation surgical precision.
공유
중국 칭다오에 본사를 둔 선도적인 적층 제조 솔루션 제공업체인 MET3DP Technology Co. 당사는 산업용 3D 프린팅 장비와 고성능 금속 분말을 전문으로 합니다.