3D Printed Mounts for Optical Instruments
İçindekiler
Introduction – The Critical Role of Precision Mounting in Aerospace Optical Instruments and the Emergence of Metal 3D Printing
In the demanding realm of aerospace engineering, the performance of optical instruments hinges critically on the stability and precision of their mounting systems. Whether it’s a sophisticated telescope peering into the cosmos, a high-resolution sensor monitoring Earth, or a laser communication system transmitting vital data, the ability of the mount to maintain alignment, withstand extreme conditions, and minimize vibrations is paramount. Traditional manufacturing methods for these intricate components often involve complex machining processes, multiple parts requiring assembly, and limitations in achieving optimal designs for weight and functionality. Enter metal 3D baskı, also known as metal additive manufacturing (AM), a transformative technology that is revolutionizing the creation of aerospace optical instrument mounts. By building parts layer by layer from metal powders, metal 3D printing offers unprecedented design freedom, the potential for significant weight reduction without compromising stiffness, and the ability to integrate multiple functionalities into a single component. This capability is not just an incremental improvement; it’s a paradigm shift that enables the development of next-generation aerospace optical systems with enhanced performance and efficiency. At Metal3DP, we understand the critical nature of these applications and provide industry-leading solutions in both metal 3D printing equipment and high-performance metal powders, empowering our clients to push the boundaries of aerospace innovation. Our commitment to accuracy and reliability ensures that the mounts produced using our technologies meet the stringent demands of the aerospace sector.
What are 3D Printed Mounts Used For in Aerospace Optics? – Exploring Applications in Telescopes, Sensors, and Laser Systems
The versatility of metal 3D printing allows for the creation of highly specialized mounts tailored to a wide array of aerospace optical instruments. These instruments play crucial roles in various missions, and the performance of their mounts directly impacts the quality of the data they gather and transmit. Here are some key applications of 3D printed mounts in aerospace optics:
- Telescope Mounts: In space-based and airborne telescopes, the stability of the optical elements is crucial for achieving high-resolution imagery. 3D printing enables the creation of lightweight yet rigid telescope mounts that can withstand the vibrations and stresses of launch and operation. Integrated features such as cooling channels and cable pathways can also be incorporated into the design.
- Sensor Mounts: Aerospace sensors, including Earth observation cameras, infrared detectors, and spectrometers, require precise alignment to capture accurate data. 3D printed mounts can be designed with intricate geometries to ensure optimal sensor positioning and thermal stability, contributing to improved data quality.
- Laser System Mounts: Laser communication systems, lidar for atmospheric sensing, and directed energy applications demand highly stable mounts for laser emitters and receivers. Metal 3D printing allows for the creation of mounts with excellent vibration damping properties and precise alignment mechanisms.
- Mirror Mounts: Optical systems often employ multiple mirrors to direct and focus light. 3D printed mirror mounts can be designed to be lightweight and stiff, minimizing deformation and ensuring accurate optical paths.
- Gimbal Systems: For instruments that require pointing and tracking capabilities, 3D printed components can be used in gimbal systems, offering reduced weight and complexity compared to traditional assemblies.
- Custom Brackets and Fixtures: Beyond primary optical components, 3D printing is also ideal for creating custom brackets, enclosures, and alignment fixtures for auxiliary optical elements and systems within aerospace platforms.
At Metal3DP, our advanced metal powders, such as Ti-6Al-4V and Invar, are ideally suited for these demanding applications, providing the necessary strength, stiffness, and thermal stability. Explore our range of yüksek kaliteli metal tozları for your aerospace optical mounting needs.
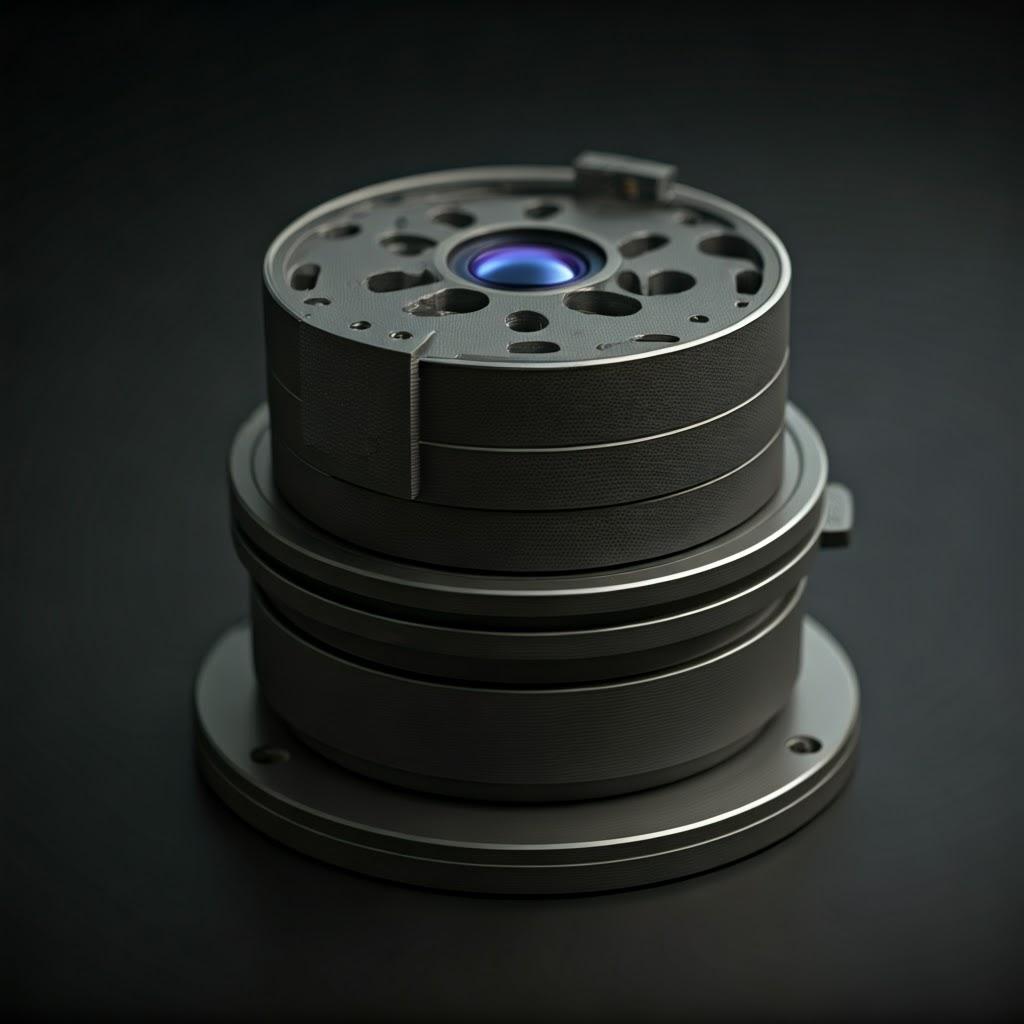
Why Choose Metal 3D Printing for Aerospace Optical Instrument Mounts? – Advantages Over Traditional Manufacturing Methods
The adoption of metal 3D printing for aerospace optical instrument mounts is driven by a multitude of advantages it offers over conventional manufacturing techniques like CNC machining and casting:
- Tasarım Özgürlüğü ve Karmaşıklık: Metal 3D printing allows for the creation of intricate geometries that are difficult or impossible to achieve with traditional methods. This enables the optimization of mounts for weight reduction, improved stiffness, and the integration of multiple functions into a single part, reducing assembly requirements and potential failure points.
- Hafifletme: In aerospace, every gram counts. Additive manufacturing facilitates the design of topologically optimized structures with internal lattices and hollow features, significantly reducing the weight of mounts without sacrificing structural integrity. This leads to fuel savings and increased payload capacity.
- Malzeme Verimliliği: Unlike subtractive methods like machining, which can result in significant material waste, 3D printing uses only the material needed to build the part. This is particularly beneficial when working with expensive aerospace-grade alloys.
- Hızlı Prototipleme ve Yineleme: Metal 3D printing drastically reduces lead times for prototypes, allowing engineers to quickly iterate on designs and test their performance. This accelerates the development cycle and enables faster innovation.
- Customization and Low-Volume Production: Additive manufacturing is highly flexible and cost-effective for producing small batches or highly customized parts, which is often the case with specialized aerospace optical instruments.
- Geliştirilmiş Performans: By tailoring the design and material selection, 3D printed mounts can offer superior vibration damping, thermal stability, and overall performance compared to traditionally manufactured components.
- Reduced Assembly: Integrating multiple components into a single 3D printed part minimizes the need for fasteners and assembly processes, leading to increased reliability and reduced manufacturing time and cost.
Metal3DP’nin metal 3D baskı hizmetleri leverage these advantages to provide aerospace clients with high-performance, custom-designed optical instrument mounts. Our industry-leading print volume and accuracy ensure that even the most complex geometries are produced with exceptional quality.
Recommended Materials: Ti-6Al-4V and Invar for Optimal Performance – Properties and Benefits for Aerospace Applications
The choice of material is critical for the performance of aerospace optical instrument mounts, as they must withstand extreme temperature variations, vibrations, and mechanical stresses while maintaining dimensional stability. Metal3DP recommends two high-performance alloys that are particularly well-suited for these applications: Ti-6Al-4V and Invar.
Ti-6Al-4V (Titanyum Alaşımı)
- Özellikler: Ti-6Al-4V is an alpha-beta titanium alloy known for its excellent strength-to-weight ratio, high tensile strength, good corrosion resistance, and biocompatibility. It has a relatively low density (around 4.43 g/cm³) and a high melting point (around 1660 °C).
- Benefits for Aerospace Optical Mounts:
- Hafifletme: Its high strength-to-weight ratio makes it ideal for reducing the overall mass of aerospace components, contributing to fuel efficiency.
- High Stiffness: Titanium alloys offer good stiffness, which is essential for maintaining the alignment of sensitive optical elements under vibration and acceleration.
- Termal Kararlılık: Ti-6Al-4V exhibits relatively low thermal expansion compared to some other metals, contributing to the stability of optical alignment over a range of temperatures.
- Korozyon Direnci: The harsh environments of aerospace applications require materials that can withstand corrosion, and Ti-6Al-4V offers excellent resistance to many corrosive agents.
- 成熟的3D打印工艺: Ti-6Al-4V is a well-established material for metal 3D printing, with readily available process parameters and a wealth of application data.
Invar (Nickel-Iron Alloy)
- Özellikler: Invar, also known as FeNi36, is a nickel-iron alloy notable for its exceptionally low coefficient of thermal expansion (CTE) over a significant temperature range around room temperature. It typically consists of around 36% nickel and 64% iron.
- Benefits for Aerospace Optical Mounts:
- Olağanüstü Termal Kararlılık: The ultra-low CTE of Invar is crucial for applications where minimal thermal expansion is required to maintain precise optical alignment, especially in environments with fluctuating temperatures.
- Boyutsal Kararlılık: This alloy’s resistance to thermal expansion ensures that the dimensions of the mount remain consistent, preventing shifts in optical elements.
- Good Weldability and Machinability: While primarily used for its thermal properties, Invar also offers reasonable workability for post-processing if required.
- Suitability for Precision Instruments: The dimensional stability of Invar makes it an excellent choice for critical components in high-precision optical instruments used in space and airborne platforms.
Metal3DP’nin advanced powder making system ensures that our Ti-6Al-4V and Invar powders exhibit high sphericity and good flowability, essential for producing dense, high-quality 3D printed parts with superior mechanical properties. By choosing these recommended powders, aerospace engineers can achieve optimal performance and reliability in their optical instrument mounts.
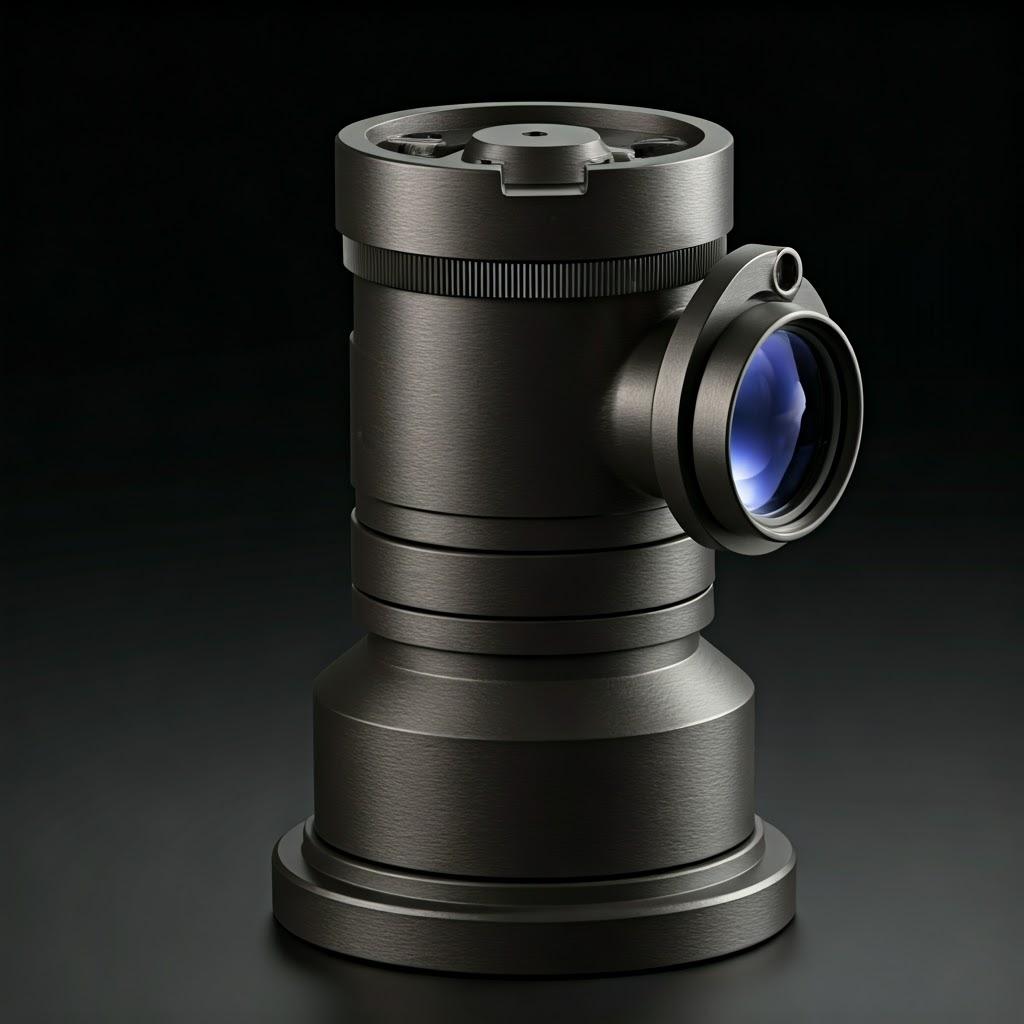
Design Considerations for Additive Manufacturing of Optical Mounts – Lightweighting, Stiffness, and Integration of Features
Designing aerospace optical instrument mounts for metal 3D printing requires a shift in mindset compared to traditional manufacturing. The layer-by-layer fabrication process opens up new possibilities for optimizing part geometry, reducing weight, and integrating functionalities. Here are key design considerations:
- Topology Optimization: This computational technique can be used to determine the optimal material distribution for a given set of loads and constraints. By removing material from low-stress areas, topology optimization can yield lightweight yet structurally sound mounts. Metal3DP‘s expertise can help guide you in leveraging these advanced design tools for your specific application.
- Kafes Yapılar: Internal lattice structures can provide significant weight reduction while maintaining or even increasing stiffness. Different lattice patterns (e.g., gyroid, cubic, diamond) offer varying levels of strength and density, allowing for tailored performance.
- Hollow Features: Designing hollow interiors with strategically placed support ribs can further reduce weight without compromising structural integrity. Careful consideration of powder removal strategies is essential when designing hollow parts.
- Integration of Features: Metal 3D printing allows for the integration of features such as cooling channels, cable pathways, mounting interfaces, and even intricate alignment mechanisms directly into the mount design. This reduces the need for separate components and assembly steps, enhancing reliability and potentially lowering costs.
- Minimizing Support Structures: While support structures are often necessary to prevent collapse or distortion during printing, their design should be optimized for easy removal and minimal impact on the final part’s surface finish. Design features like self-supporting angles and strategic part orientation can help reduce the need for extensive supports.
- Termal Yönetim: For optical instruments that generate or are sensitive to heat, incorporating cooling channels directly into the mount design can be a highly effective thermal management solution. Additive manufacturing provides the flexibility to create complex internal channel geometries.
- Vibration Damping: The design of the mount can influence its vibration damping characteristics. Features like ribs, strategically placed mass concentrations, and the choice of lattice structures can be used to mitigate unwanted vibrations that could affect optical performance.
By considering these design principles and leveraging the capabilities of metal 3D printing, engineers can create aerospace optical instrument mounts with superior performance, reduced weight, and integrated functionality. Metal3DP‘s comprehensive solutions, from advanced metal powders to application development services, support these innovative design approaches.
Achieving Precision: Tolerance, Surface Finish, and Dimensional Accuracy in 3D Printed Mounts – Meeting Stringent Aerospace Requirements
Aerospace optical instruments demand exceptional precision in terms of tolerance, surface finish, and dimensional accuracy to ensure optimal performance. Metal 3D printing technologies, when properly implemented, can meet these stringent requirements.
- Tolerance: The achievable tolerance in metal 3D printing depends on the specific printing technology (e.g., Selective Electron Beam Melting (SEBM), Laser Powder Bed Fusion (LPBF)), the material used, and the design of the part. Generally, tolerances in the range of ±0.1 to ±0.05 mm can be achieved for critical features. Post-processing techniques like precision machining can further tighten tolerances if required. Metal3DP‘s SEBM yazıcıları are known for their accuracy and ability to produce complex parts with tight tolerances.
- Yüzey İşlemi: The as-printed surface finish in metal 3D printing is typically rougher than that achieved by machining. The surface roughness (Ra) can range from 5 to 20 µm depending on the printing parameters and material. For optical mounting surfaces, post-processing steps like polishing, grinding, or even coating may be necessary to achieve the required smoothness and reflectivity.
- Boyutsal Doğruluk: Dimensional accuracy refers to how closely the printed part matches the intended design dimensions. Factors affecting accuracy include material shrinkage during solidification, thermal gradients during printing, and the calibration of the 3D printer. Careful process control, optimized build parameters, and经验丰富的操作人员 are crucial for achieving high dimensional accuracy.
To ensure that 3D printed aerospace optical mounts meet the required precision levels, it is essential to:
- Optimize Part Orientation: The orientation of the part on the build platform can significantly impact tolerance and surface finish of specific features.
- Utilize Support Structures Strategically: While necessary for complex geometries, supports can leave surface artifacts upon removal. Their placement and design should minimize these effects on critical surfaces.
- Employ High-Resolution Printing Parameters: Finer layer thicknesses and optimized laser or electron beam parameters can improve surface finish and accuracy.
- Incorporate Post-Processing: For critical surfaces, post-processing steps like CNC machining, grinding, lapping, or polishing can be used to achieve the required tolerance and surface finish.
- Perform Rigorous Inspection: Utilizing coordinate measuring machines (CMMs) and other metrology equipment is essential to verify that the printed parts meet the specified dimensional and tolerance requirements.
Metal3DP is committed to delivering parts with industry-leading accuracy. Our expertise in both printing equipment and materials ensures that your aerospace optical mounts meet the most demanding specifications.
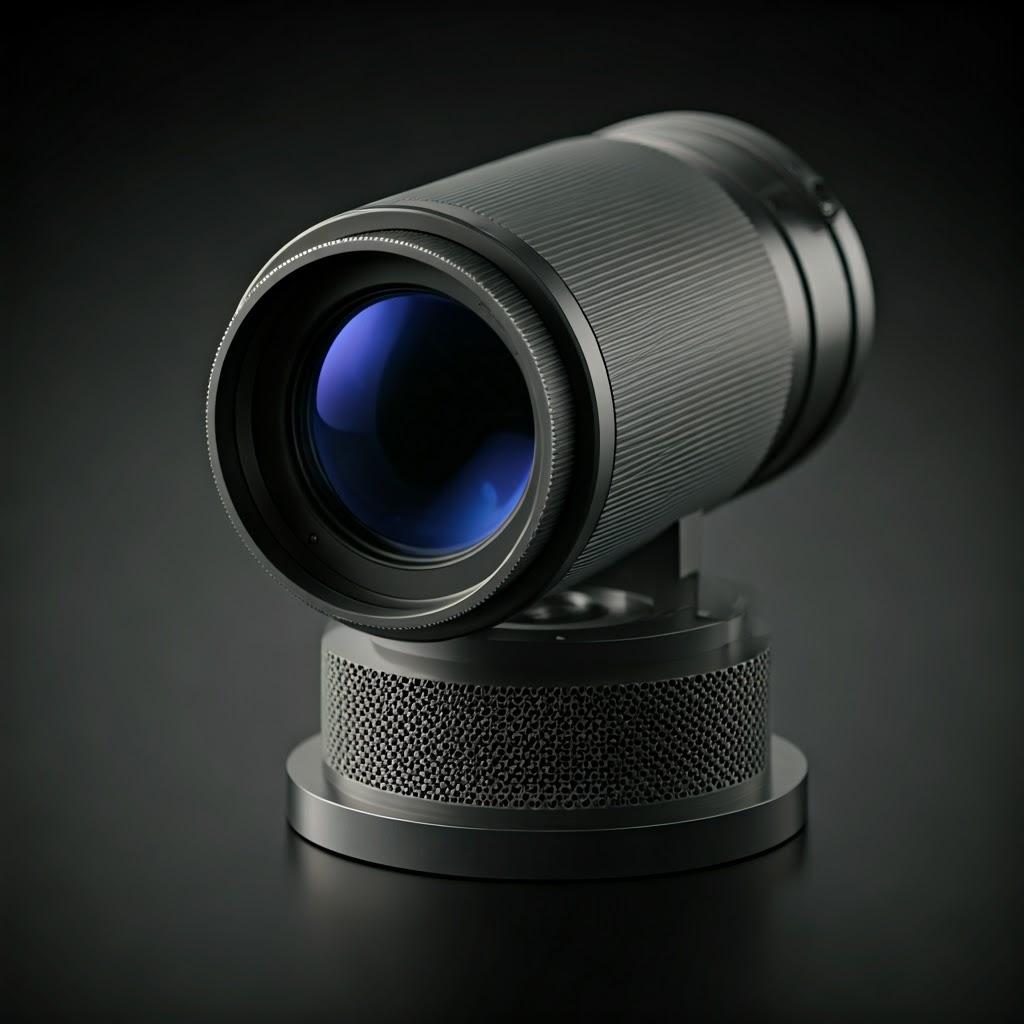
Post-Processing for Aerospace-Grade Optical Mounts – Ensuring Cleanliness, Stability, and Protective Coatings
While metal 3D printing can produce near-net-shape parts, post-processing is often necessary to meet the stringent requirements of aerospace optical applications. These steps ensure the cleanliness, stability, and protection of the mounts.
- Toz Giderme: After printing, any loose or partially sintered powder must be carefully removed from internal channels and surfaces. Techniques such as brushing, vacuuming, and ultrasonic cleaning are commonly used. For intricate internal geometries, specialized powder removal methods may be required.
- Stress Relief Heat Treatment: To alleviate residual stresses that can build up during the printing process, a stress relief heat treatment is often performed. This improves the dimensional stability of the part and reduces the risk of warping or cracking during service.
- Destek Yapısının Kaldırılması: Support structures used during printing must be removed. This can be done manually using cutting tools or automatically using specialized equipment. The removal process should be carefully controlled to avoid damaging the part’s surface.
- Yüzey İşlemi: As mentioned earlier, post-processing techniques like machining, grinding, polishing, or abrasive flow machining can be employed to achieve the required surface finish for optical interfaces and other critical areas.
- Cleaning and Contamination Control: Aerospace components, especially those used in optical systems, must be free of contaminants. Rigorous cleaning procedures are essential to remove any residual powder, oils, or other impurities. Cleanroom environments may be required for final assembly and handling.
- Kaplamalar: Depending on the application and the material used, protective coatings may be applied to enhance corrosion resistance, improve wear properties, or provide specific optical characteristics (e.g., reflective or absorptive coatings).
- Tahribatsız Muayene (NDT): Techniques like dye penetrant inspection, ultrasonic testing, or X-ray radiography may be used to ensure the structural integrity of the printed parts and detect any internal defects.
- Boyutsal Muayene: Final dimensional inspection using CMMs or other precise measurement tools is crucial to verify that the post-processed parts meet the specified tolerances.
Metal3DP offers comprehensive post-processing services to ensure that your 3D printed aerospace optical mounts meet the highest standards of quality and performance. Our expertise in material science and manufacturing processes allows us to tailor post-processing steps to the specific requirements of your application.
Addressing Challenges in 3D Printing Aerospace Optical Mounts – Warping, Thermal Management, and Material Certification
While metal 3D printing offers numerous advantages, there are also challenges that need to be addressed to successfully produce high-quality aerospace optical instrument mounts.
- Çarpıtma ve Bozulma: Thermal gradients during the printing process can lead to residual stresses, which can cause warping or distortion of the part, especially for large or complex geometries. Optimized build parameters, support structure design, and stress relief heat treatment are crucial for mitigating these issues.
- Thermal Management During Operation: Aerospace optical instruments often operate in environments with significant temperature variations or generate heat internally. Designing mounts that can effectively manage thermal expansion and dissipate heat is critical for maintaining optical alignment. Material selection (e.g., Invar for low CTE) and integrated cooling channels are important considerations.
- Porosity and Density: Achieving high density and minimizing porosity in 3D printed metal parts is essential for mechanical strength and reliability. Optimized printing parameters, high-quality metal powders (like those offered by Metal3DP), and appropriate post-processing (e.g., Hot Isostatic Pressing – HIP) can help achieve near full density.
- Support Removal Damage: Removing support structures can sometimes leave surface artifacts or even damage delicate features. Careful design of support structures and the use of appropriate removal techniques are necessary to minimize these risks.
- Material Certification and Traceability: For aerospace applications, material certification and traceability are paramount. Ensuring that the metal powders used meet stringent quality standards and that the entire manufacturing process is well-documented is crucial for regulatory compliance. Metal3DP provides high-quality metal powders with comprehensive material data sheets and traceability.
- Achieving Smooth Optical Surfaces: Directly 3D printed metal surfaces may not be smooth enough for optical interfaces. Post-processing techniques like precision machining and polishing are often required to achieve the necessary surface finish.
- Cost of Production: While 3D printing can be cost-effective for low-volume or complex parts, the cost per part can be higher than traditional methods for large production runs or simpler geometries. A thorough cost analysis is essential to determine the most economical manufacturing approach.
By understanding these challenges and implementing appropriate design strategies, process controls, and post-processing techniques, it is possible to successfully leverage metal 3D printing for the production of high-performance aerospace optical instrument mounts. Metal3DP‘s expertise and comprehensive solutions are designed to help our clients overcome these challenges and realize the full potential of metal additive manufacturing.
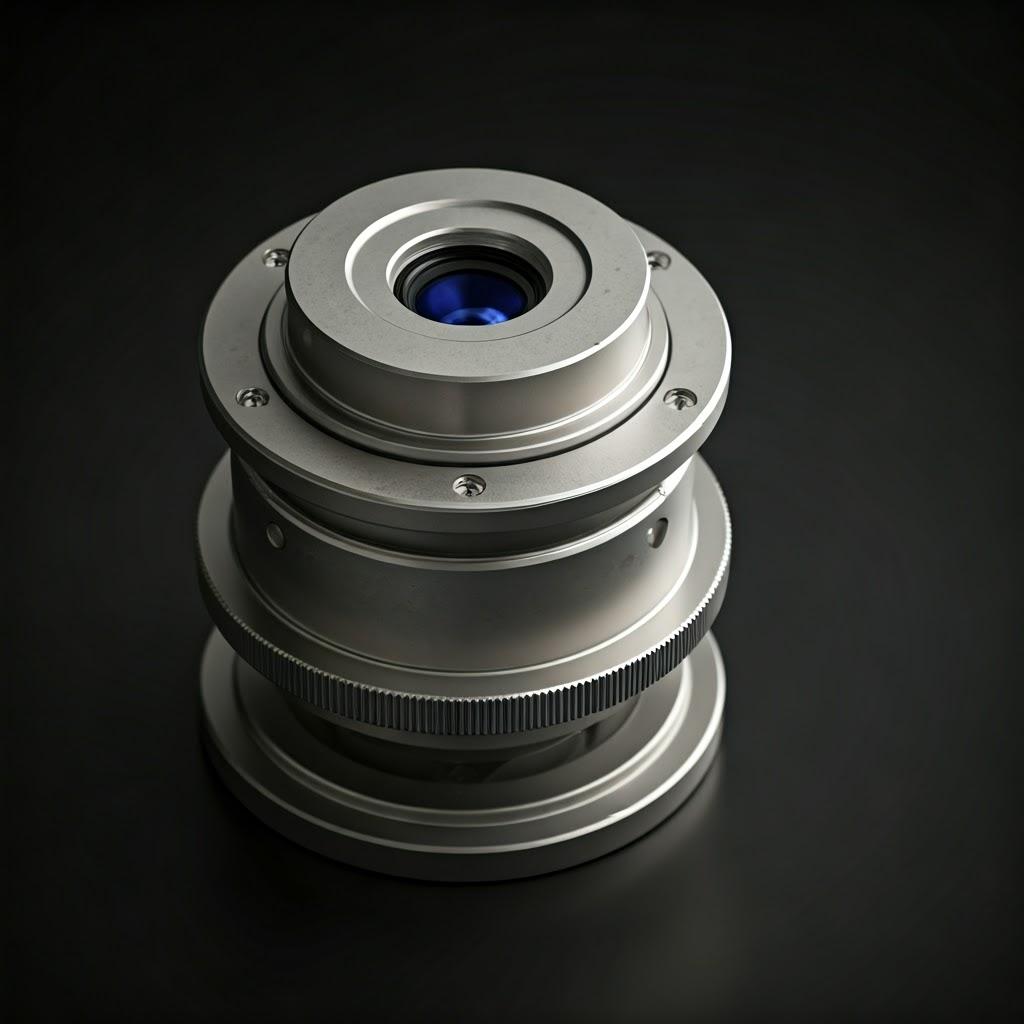
Selecting a Metal 3D Printing Service Provider for Aerospace Applications – Key Factors in Evaluation
Choosing the right metal 3D printing service provider is crucial for the success of your aerospace optical instrument mount project. Given the stringent requirements of the aerospace industry, careful evaluation of potential partners is essential. Here are key factors to consider:
- Aerospace Certifications and Standards: Ensure the service provider holds relevant aerospace certifications such as AS9100. These certifications demonstrate a commitment to quality management systems required for aerospace components.
- Material Capabilities: Verify that the provider has experience working with the recommended materials for your application, specifically Ti-6Al-4V and Invar. They should also have a robust understanding of the material properties and processing parameters for these alloys. Metal3DP specializes in these and other high-performance metal powders.
- Printing Technology and Equipment: Understand the types of metal 3D printing technologies the provider utilizes (e.g., SEBM, LPBF). The choice of technology can impact the achievable tolerance, surface finish, and material properties. Inquire about the accuracy and reliability of their printing equipment.
- Post-Processing Capabilities: Determine if the provider offers the necessary post-processing services required for aerospace optical mounts, including stress relief heat treatment, precision machining, polishing, cleaning, and coating. An in-house capability can streamline the production process.
- Quality Control and Inspection: Inquire about the provider’s quality control procedures and inspection capabilities. They should have robust processes in place to ensure dimensional accuracy, material integrity, and adherence to specifications. The use of CMMs and NDT methods is a good indicator.
- Experience and Expertise: Look for a provider with a proven track record of producing high-quality metal 3D printed parts for aerospace applications. Case studies and testimonials can provide valuable insights into their experience and capabilities.
- Design Optimization Support: A strong service provider should offer expertise in design for additive manufacturing (DfAM) to help optimize your mount for weight reduction, performance enhancement, and efficient printing. Metal3DP offers application development services to assist with design optimization.
- Lead Times and Production Capacity: Discuss lead times for prototyping and production, as well as their capacity to handle your anticipated volumes. Ensure their timelines align with your project requirements.
- Communication and Customer Support: Effective communication and responsive customer support are essential for a smooth collaboration. Assess their responsiveness and willingness to understand your specific needs.
- Traceability and Documentation: For aerospace components, full material traceability and comprehensive documentation are critical. Ensure the provider can provide detailed records of the materials used and the manufacturing process.
By carefully evaluating potential metal 3D printing service providers based on these factors, you can select a partner that can reliably produce high-performance aerospace optical instrument mounts that meet your stringent requirements. Consider contacting Metal3DP to discuss your specific needs and learn how our expertise can support your project.
Cost-Effectiveness and Lead Time Benefits of 3D Printed Aerospace Mounts – A Comparative Analysis
The cost-effectiveness and lead time benefits of using metal 3D printing for aerospace optical instrument mounts can be significant, although they depend on several factors, including part complexity, volume, material, and the chosen manufacturing method for comparison.
Maliyet-Etkinlik:
- Reduced Tooling Costs: Unlike traditional manufacturing methods that often require expensive molds or fixtures, 3D printing typically involves minimal or no tooling costs. This can be particularly advantageous for low-volume production or highly customized parts.
- Malzeme Verimliliği: Additive manufacturing uses material only where needed, reducing waste compared to subtractive methods 1 like machining, especially when working with expensive aerospace alloys. 1. abdulghaffarkhan0.exblog.jp abdulghaffarkhan0.exblog.jp
- Simplified Assembly: By integrating multiple components into a single 3D printed part, assembly costs and the number of fasteners can be reduced, leading to potential cost savings.
- Lightweighting Benefits: Reduced weight translates to lower fuel consumption in aerospace applications, resulting in long-term operational cost savings.
- Cost-Competitive for Complex Geometries: For intricate designs that would require extensive machining or multiple manufacturing steps using traditional methods, 3D printing can be a more cost-effective solution.
Lead Time Benefits:
- Hızlı Prototipleme: Metal 3D printing significantly reduces the lead time for producing prototypes, allowing for faster design iteration and testing.
- İsteğe Bağlı Üretim: 3D printing enables on-demand production, eliminating the need for long lead times associated with tooling and setup for traditional manufacturing.
- Faster Production of Complex Parts: For complex geometries, 3D printing can often produce parts much faster than traditional methods that may involve multiple machining operations and specialized tooling.
- Reduced Supply Chain Complexity: By consolidating multiple parts into a single printed component, the complexity of the supply chain can be reduced, potentially shortening overall lead times.
Comparative Analysis:
Faktör | Metal 3D Baskı | Traditional Manufacturing (e.g., CNC Machining) |
---|---|---|
Kalıp Maliyetleri | Low to None | Yüksek |
Malzeme Atıkları | Düşük | Yüksek |
Assembly Costs | Potentially Lower (part integration) | Potentially Higher (multiple parts) |
Prototyping Lead Time | Kısa | Uzun |
Production Lead Time (Complex Parts) | Short to Medium | Medium to Long |
Cost per Part (Low Volume/Complex) | Rekabetçi | Yüksek |
Cost per Part (High Volume/Simple) | Potansiyel Olarak Daha Yüksek | Rekabetçi |
Sayfalara Aktar
It’s important to conduct a thorough cost analysis for your specific application and volume requirements to determine the most cost-effective manufacturing approach. Metal3DP can provide insights into the cost and lead time benefits of using our metal 3D printing services for your aerospace optical instrument mounts.
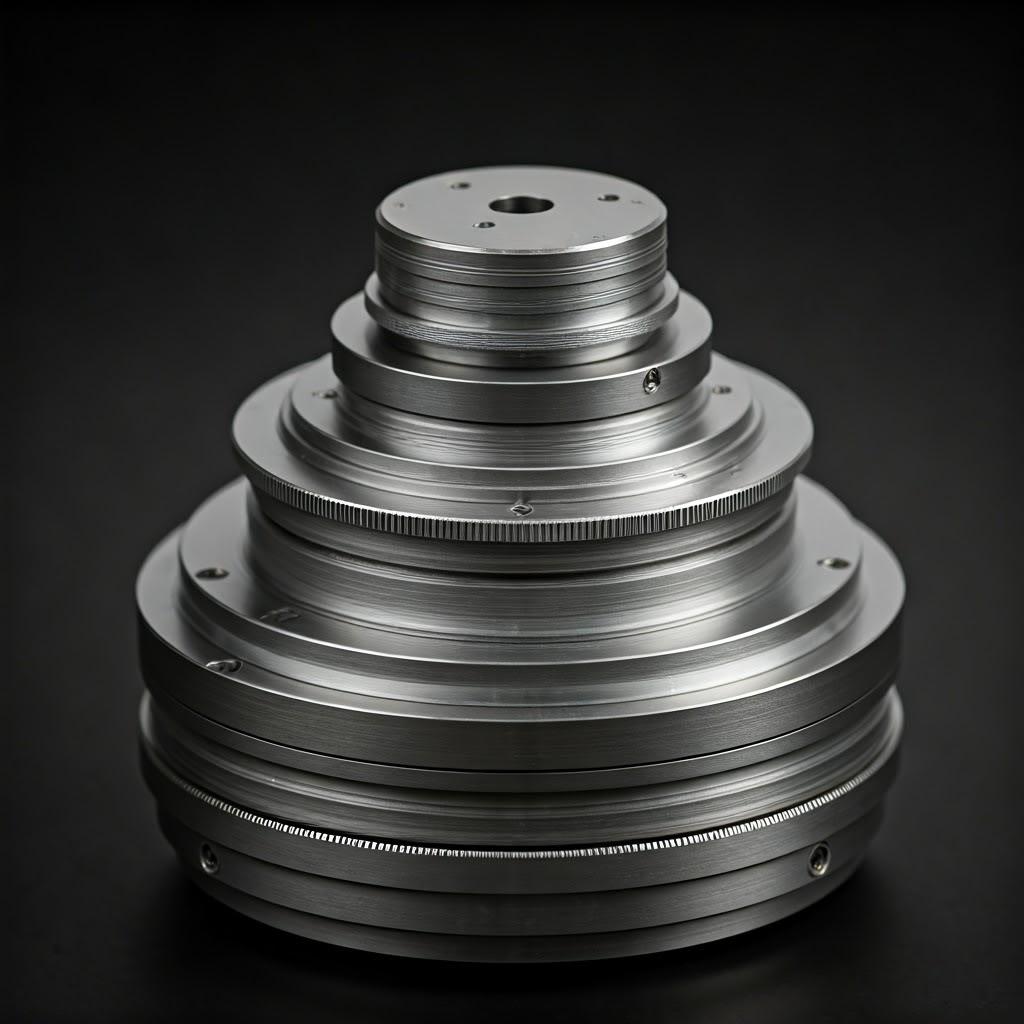
Frequently Asked Questions (FAQ) – Addressing Common Queries from Engineers and Procurement Managers
Here are some frequently asked questions related to using metal 3D printing for aerospace optical instrument mounts:
Q: What level of dimensional accuracy can be achieved with metal 3D printing for optical mounts? A: Depending on the printing technology and material, tolerances in the range of ±0.1 to ±0.05 mm are achievable for critical features. Post-processing can further improve accuracy if needed. Metal3DP‘s SEBM technology offers high accuracy for complex parts.
Q: Is Ti-6Al-4V suitable for space applications with extreme temperature variations? A: Ti-6Al-4V offers good thermal stability compared to many other metals. However, for applications with extreme temperature fluctuations where minimal thermal expansion is critical, Invar with its ultra-low CTE may be a more suitable choice.
Q: What post-processing steps are typically required for 3D printed aerospace optical mounts? A: Common post-processing steps include powder removal, stress relief heat treatment, support structure removal, surface finishing (e.g., polishing for optical interfaces), cleaning, and potentially coatings.
Q: How does metal 3D printing contribute to weight reduction in aerospace components? A: Metal 3D printing enables design optimization techniques like topology optimization and the use of lattice structures and hollow features, which can significantly reduce the weight of parts without compromising structural integrity.
Q: What are the key considerations when selecting a metal 3D printing service provider for aerospace applications? A: Key considerations include aerospace certifications (e.g., AS9100), experience with relevant materials (like Ti-6Al-4V and Invar), printing technology and equipment, post-processing capabilities, quality control procedures, and design optimization support.
Q: Can metal 3D printed parts meet the strict material traceability requirements of the aerospace industry? A: Yes, reputable metal 3D printing service providers, including Metal3DP, can provide full material traceability and comprehensive documentation to meet aerospace industry standards.
Q: What is the typical lead time for producing a custom 3D printed aerospace optical mount? A: Lead times vary depending on the complexity of the part, the printing technology used, and the required post-processing. However, 3D printing generally offers faster prototyping and can expedite the production of complex, low-volume parts compared to traditional methods.
Conclusion – The Future of Aerospace Optical Instrument Mounting with Metal Additive Manufacturing
Metal additive manufacturing is rapidly transforming the landscape of aerospace optical instrument mounting. The ability to create complex, lightweight, and highly customized mounts with integrated features offers significant advantages over traditional manufacturing methods. Materials like Ti-6Al-4V and Invar, processed through advanced 3D printing technologies, provide the necessary strength, stability, and thermal characteristics for demanding aerospace applications.
By embracing metal 3D printing, aerospace engineers and procurement managers can achieve:
- Geliştirilmiş Performans: Optimized designs and material selection lead to improved stability and functionality of optical instruments.
- Reduced Weight: Lightweight mounts contribute to fuel efficiency and increased payload capacity.
- Daha Hızlı İnovasyon: Rapid prototyping and design iteration accelerate the development of new aerospace optical systems.
- Greater Design Freedom: Complex geometries and integrated features enable the creation of innovative mounting solutions.
Metal3DP is at the forefront of this revolution, providing industry-leading metal 3D printing equipment, yüksek kaliteli metal tozları, and comprehensive application development services. Our commitment to accuracy, reliability, and material expertise empowers our clients to push the boundaries of aerospace technology.
As the demands for more sophisticated and efficient aerospace optical instruments continue to grow, metal 3D printing will play an increasingly critical role in their development and deployment. Contact Metal3DP today to explore how our capabilities can power your organization’s additive manufacturing goals and help you realize the full potential of this transformative technology.
Paylaş
MET3DP Technology Co, LTD, merkezi Qingdao, Çin'de bulunan lider bir katmanlı üretim çözümleri sağlayıcısıdır. Şirketimiz, endüstriyel uygulamalar için 3D baskı ekipmanları ve yüksek performanslı metal tozları konusunda uzmanlaşmıştır.
İşletmeniz için en iyi fiyatı ve özelleştirilmiş Çözümü almak için sorgulayın!
İlgili Makaleler
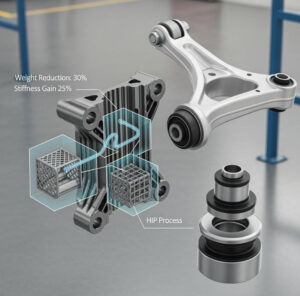
Metal 3D Printed Subframe Connection Mounts and Blocks for EV and Motorsport Chassis
Daha Fazla Oku "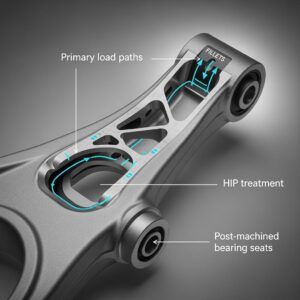
Metal 3D Printing for U.S. Automotive Lightweight Structural Brackets and Suspension Components
Daha Fazla Oku "Met3DP Hakkında
Son Güncelleme
Bizim Ürünümüz
BİZE ULAŞIN
Herhangi bir sorunuz var mı? Bize şimdi mesaj gönderin! Mesajınızı aldıktan sonra tüm ekibimizle talebinize hizmet edeceğiz.