3D Printed Rocket Nozzles Using High-Temperature Alloys
İçindekiler
Introduction: The Critical Role of Rocket Nozzles and Additive Manufacturing’s Ascent
Rocket nozzles stand as one of the most demanding and critical components in aerospace propulsion systems. Tasked with accelerating scorching hot, high-pressure combustion gases to supersonic (often hypersonic) speeds, these components endure extreme thermal, mechanical, and chemical stresses. The efficiency, reliability, and performance of an entire launch vehicle or satellite propulsion system hinge significantly on the nozzle’s design and material integrity. Its primary function is to convert the thermal energy generated in the combustion chamber into kinetic energy, producing the thrust necessary to overcome gravity and propel spacecraft. Any failure or underperformance in the nozzle can have catastrophic consequences, making its design, material selection, and manufacturing process paramount considerations for aerospace engineers and manufacturers.
Traditionally, manufacturing these intricate components involved complex, multi-stage processes like casting, forging, and extensive subtractive machining, often from difficult-to-work high-temperature materials. These methods, while proven, present significant limitations:
- Design Constraints: Complex internal features, such as intricate cooling channels essential for managing extreme temperatures, are difficult or impossible to achieve with traditional methods. This often forces compromises in design optimality.
- Long Lead Times: The multi-step nature of conventional manufacturing, coupled with tooling requirements, results in lengthy production cycles, hindering rapid iteration and development programs.
- Malzeme Atıkları: Subtractive machining inherently generates significant material scrap, particularly costly when working with expensive superalloys.
- Weight Penalties: Traditional methods can struggle to produce lightweight structures without sacrificing strength, a critical factor in aerospace where every gram saved translates to payload capacity or fuel efficiency gains.
- Assembly Complexity: Nozzles often require assembling multiple machined or cast parts, introducing potential failure points at joints and increasing assembly time and cost.
Enter metal additive manufacturing (AM), more commonly known as metal 3D printing. This transformative technology is rapidly ascending as a powerful solution for manufacturing critical aerospace components like rocket nozzles. By building parts layer by layer directly from digital models using high-energy sources (lasers or electron beams) to fuse fine metal powders, AM shatters many of the limitations associated with traditional manufacturing.
Key Advantages of AM for Rocket Nozzles:
- Benzersiz Tasarım Özgürlüğü: AM enables the creation of highly complex geometries, including integrated conformal cooling channels that closely follow the nozzle’s contours for maximum heat transfer efficiency. This allows for designs previously deemed unmanufacturable.
- Accelerated Development Cycles: Prototypes and design iterations can be produced significantly faster, allowing engineers to test and refine nozzle concepts much more quickly, speeding up engine development programs.
- Weight Optimization: Techniques like topology optimization and the incorporation of lattice structures allow for material placement only where structurally necessary, leading to substantial weight savings without compromising performance.
- Parça Konsolidasyonu: Multiple components that previously required assembly can often be consolidated into a single, monolithic 3D printed part, reducing part count, eliminating joints (potential failure points), and simplifying logistics.
- Malzeme Verimliliği: As an additive process, AM uses material primarily where needed, drastically reducing the waste associated with subtractive methods, a crucial benefit when dealing with expensive high-temperature superalloys.
- Tedarik Zinciri Dayanıklılığı: AM offers the potential for distributed manufacturing and on-demand production, reducing reliance on complex global supply chains and long lead-time forgings or castings.
The aerospace industry, constantly pushing the frontiers of performance and efficiency, has recognized the immense potential of metal 3D printing. For rocket nozzles, operating at the sharp end of extreme environments, AM offers a pathway to enhanced thermal management, reduced weight, faster innovation, and ultimately, more capable and cost-effective propulsion systems. As companies like Met3dp continue to refine both AM processes and specialized high-performance metal powders, the ascent of additive manufacturing in producing flight-critical hardware like rocket nozzles is set to accelerate, reshaping the future of space exploration and access.
Applications of 3D Printed Rocket Nozzles: Pushing Aerospace Boundaries
The unique capabilities offered by metal additive manufacturing have unlocked a diverse and growing range of applications for 3D yazdırılmış rocket nozzles across the aerospace and defense sectors. The ability to rapidly iterate complex designs, optimize for weight, and integrate advanced features like sophisticated cooling channels makes AM particularly suitable for demanding propulsion applications where performance is paramount.
1. Launch Vehicle Main and Upper Stage Engines:
- Primary Application: Perhaps the most prominent use is in the main propulsion systems of launch vehicles, responsible for lifting payloads from Earth into orbit. This includes both first-stage booster engines and upper-stage engines that perform orbital insertion or interplanetary burns.
- Why AM?
- Performans: Complex cooling channel designs enabled by AM (e.g., regenerative cooling circuits where fuel flows through channels in the nozzle wall before combustion) allow engines to run at higher chamber pressures and temperatures, increasing specific impulse (Isp) – a key measure of engine efficiency.
- Ağırlık Azaltma: Every kilogram saved on the rocket structure translates directly into increased payload capacity or mission capability. AM allows for significant weight savings in the nozzle assembly through topology optimization and part consolidation.
- Faster Development: Launch vehicle development cycles are notoriously long and expensive. AM significantly accelerates the iteration process for nozzle designs, enabling quicker testing and refinement, crucial for both established players and new space entrants looking for cost-effective solutions.
- Maliyet Azaltma: While the initial AM part cost might be comparable or higher in some cases, the overall system cost can be reduced through part consolidation (fewer components to manufacture, track, and assemble), reduced tooling costs, and faster development timelines. Wholesale buyers and procurement managers benefit from streamlined logistics and potentially lower total program costs.
2. Satellite Propulsion Systems:
- Uygulama: Satellites require smaller thrusters for station-keeping (maintaining their correct orbit), attitude control (orientation), and sometimes orbital maneuvering or de-orbiting. These often involve monopropellant or bipropellant systems operating on a smaller scale than launch vehicle engines.
- Why AM?
- Miniaturization & Integration: AM excels at producing small, intricate components. Thruster nozzles, often part of a larger integrated propulsion module, can be printed with features like injector heads or valve interfaces combined into a single unit, reducing mass and potential leak points.
- Özelleştirme: Satellite constellations may require slightly different thruster configurations. AM allows for efficient production of customized nozzle designs without the need for dedicated tooling for each variant.
- Novel Materials: AM facilitates the use of advanced or specialized alloys tailored for specific propellant chemistries or long-duration space exposure, potentially improving thruster lifetime and performance.
3. Reaction Control Systems (RCS):
- Uygulama: RCS thrusters are small rocket engines used on spacecraft and launch vehicle upper stages primarily for attitude control and precise maneuvering in space, rather than generating large amounts of thrust.
- Why AM?
- Karmaşık Geometriler: RCS systems often involve multiple nozzles clustered together at specific angles. AM allows these clusters, along with associated manifolds and mounting features, to be printed as a single integrated component.
- Weight Savings: As with larger nozzles, minimizing the mass of RCS components is critical, especially for deep-space missions or weight-sensitive satellites.
- Hızlı Prototipleme: Fine-tuning the performance and plume characteristics of RCS thrusters often requires iterative testing. AM enables rapid production of design variants.
4. Hypersonic Vehicle Propulsion:
- Uygulama: Emerging hypersonic vehicles (aircraft or missiles travelling above Mach 5) require advanced air-breathing engines (like scramjets) or rocket boosters that operate under extreme aerodynamic heating and mechanical stress. Nozzle design is critical for performance and thermal management.
- Why AM?
- Extreme Temperature Management: AM enables the integration of highly complex, transpiration or regenerative cooling systems directly into the nozzle walls, essential for surviving the multi-thousand-degree temperatures encountered during hypersonic flight.
- İleri Malzemeler: Hypersonic applications demand materials capable of withstanding extreme conditions. AM processes are being adapted to work with cutting-edge refractory metals and ceramic matrix composites (CMCs), potentially suitable for these demanding nozzle applications.
- Shape Optimization: The complex flow paths and nozzle geometries required for efficient hypersonic propulsion are often ideally suited to the design freedom offered by AM.
5. Research and Development / Test Articles:
- Uygulama: Before committing to flight hardware, extensive ground testing is required. AM is heavily utilized to produce prototype nozzles and combustion chamber components for test campaigns.
- Why AM?
- Hız: Quickly manufacturing test articles allows research programs to progress faster.
- Maliyet-Etkinlik: Producing one-off or small batches of test hardware via AM is often more economical than setting up traditional manufacturing lines.
- Instrumentation: AM allows for the integration of ports and channels for sensors and diagnostic equipment directly into the test nozzle.
Industry Impact:
The adoption of 3D printed rocket nozzles is impacting various players in the aerospace supply chain:
- Engine Manufacturers: Directly benefit from enhanced performance, reduced weight, and faster development.
- Launch Service Providers: Gain competitive advantages through more efficient and potentially lower-cost launch vehicles.
- Satellite Operators: Benefit from lighter, more integrated, and potentially longer-lasting propulsion systems.
- Defense Contractors: Leverage AM for rapid development and production of advanced missile and hypersonic systems.
- Aerospace Component Suppliers & Distributors: Need to adapt their offerings and capabilities to include AM parts and materials, becoming key partners in the evolving manufacturing landscape. Companies specializing in high-quality metal powders and gelişmiş baskı yöntemleri like Met3dp are crucial enablers in this ecosystem.
In essence, 3D printed rocket nozzles are not just a manufacturing novelty; they are a critical enabler for the next generation of aerospace systems, pushing the boundaries of performance, efficiency, and mission capability across a wide spectrum of applications.
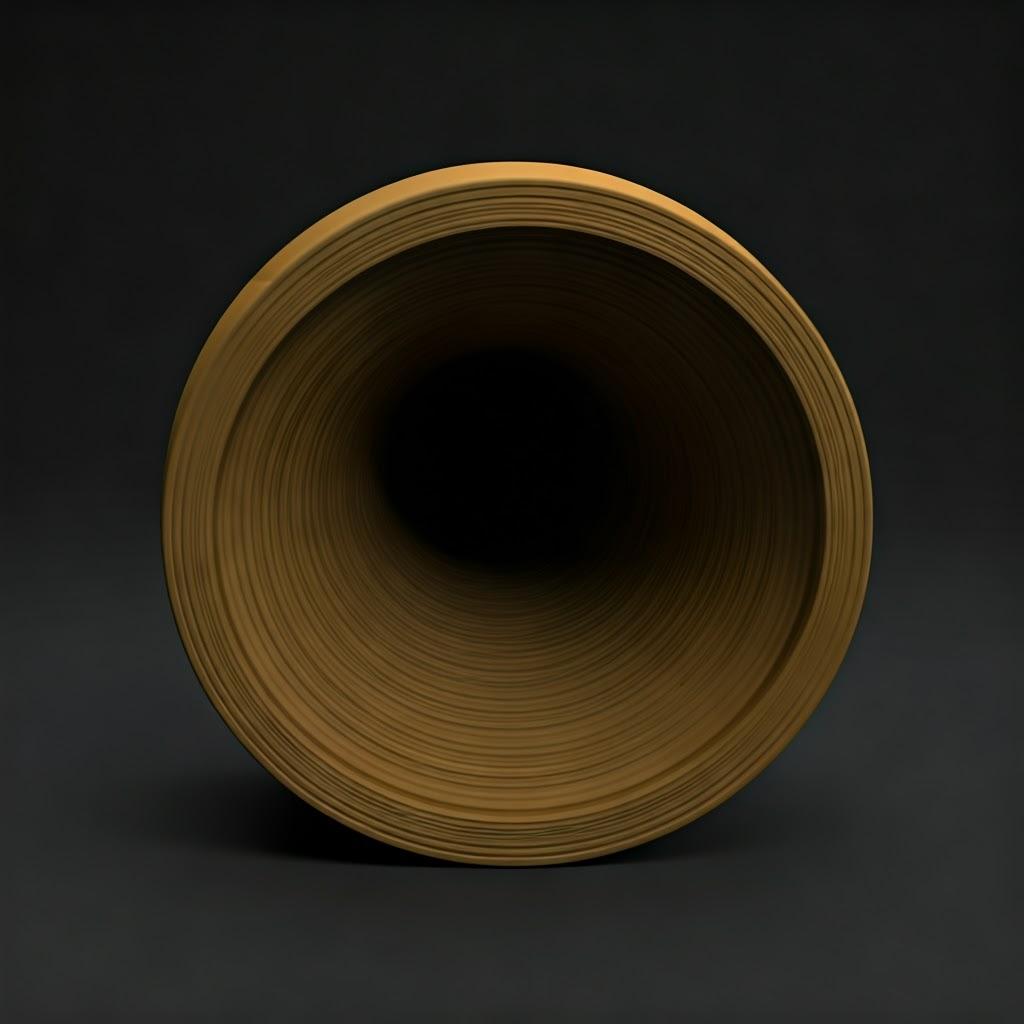
Why Metal 3D Printing Excels for Rocket Nozzle Production
The decision to shift from established, traditional manufacturing methods (like casting, forging, spin forming, and machining) to metal additive manufacturing for a component as critical as a rocket nozzle is driven by a compelling set of advantages. Metal 3D printing offers solutions to inherent challenges in conventional processes, particularly when dealing with the complex designs and demanding materials required for optimal nozzle performance. Procurement managers, engineers, and aerospace component suppliers recognize these benefits as key drivers for adoption.
1. Unmatched Geometric Complexity:
- Challenge (Traditional): Manufacturing intricate internal features, such as optimized conformal cooling channels that precisely follow the nozzle’s inner wall contour, is extremely difficult or impossible with casting or machining. Channels often had to be milled into simpler shapes and then covered or formed by brazing multiple sections together.
- AM Solution: Layer-by-layer construction allows for the creation of virtually any internal geometry. This enables:
- Konformal Soğutma Kanalları: Highly efficient cooling paths that significantly improve heat transfer, allowing for higher operating temperatures/pressures and thus better engine performance (higher Isp).
- Integrated Features: Features like injector faceplates, mounting flanges, or internal stiffening structures can be built directly into the nozzle as a single piece.
- Optimized Flow Paths: The internal contours of the nozzle itself can be optimized for fluid dynamics without being constrained by traditional manufacturing limitations.
2. Accelerated Design Iteration and Rapid Prototyping:
- Challenge (Traditional): Creating new tooling (molds, dies, fixtures) for each design iteration is time-consuming and expensive. Testing new concepts involves long lead times, slowing down engine development programs significantly.
- AM Solution: AM is a tool-less process. Designs go directly from CAD model to physical part.
- Hız: Prototype nozzles can often be printed in days or weeks, compared to months for traditional methods.
- Esneklik: Multiple design variations can be printed simultaneously in a single build for comparative testing.
- Reduced Development Cost: Faster iteration cycles lead to shorter development timelines and lower overall program costs, even if the per-part cost of early prototypes is higher.
3. Significant Weight Reduction Potential:
- Challenge (Traditional): Achieving low weight while maintaining structural integrity often involves extensive, costly machining operations and may still result in suboptimal designs.
- AM Solution:
- Topology Optimization: Software algorithms can determine the most efficient load paths, allowing material to be placed only where structurally required, resulting in organic-looking, highly optimized, lightweight designs.
- Kafes Yapılar: Internal lattice or honeycomb structures can provide high stiffness and strength at very low densities, further reducing component weight.
- Malzeme Seçimi: While traditional methods might force the use of a denser alloy due to manufacturability constraints, AM can often handle optimized designs in slightly less dense but equally strong high-temperature alloys.
4. Part Consolidation:
- Challenge (Traditional): Complex assemblies like nozzles often consist of multiple individual parts (e.g., combustion chamber interface, throat section, expansion cone, cooling jackets) that need to be manufactured separately and then joined, typically by brazing or welding.
- AM Solution: AM allows for the consolidation of these multiple parts into a single, monolithic component.
- Reduced Assembly Time & Cost: Eliminates the need for complex joining processes and associated labor/inspection.
- Improved Reliability: Removes joints, which are potential weak points, leak paths, or sources of residual stress.
- Simplified Logistics: Reduces the number of individual parts that need to be sourced, tracked, and managed by procurement teams and suppliers.
5. Enhanced Material Utilization and Reduced Waste:
- Challenge (Traditional): Subtractive machining, especially from large billets or forgings of expensive superalloys like Inconel or Haynes, generates substantial material waste (often >50-80% of the initial material).
- AM Solution: As an additive process, material is only fused where needed.
- Lower “Buy-to-Fly” Ratio: Significantly less raw material is required to produce the final part, drastically reducing waste. While unused powder needs recycling, the overall material efficiency is much higher.
- Maliyet Tasarrufu: Particularly impactful for high-cost superalloys commonly used in nozzles, leading to direct cost savings appreciated by wholesale buyers and manufacturers.
6. Supply Chain Optimization and Agility:
- Challenge (Traditional): Reliance on specialized foundries or forges often involves long lead times (months or even years for certain alloys/forms) and complex global supply chains.
- AM Solution:
- İsteğe Bağlı Üretim: Enables production closer to the point of need or assembly, potentially reducing inventory requirements.
- Azaltılmış Teslim Süreleri: For established designs, AM can offer shorter production lead times compared to waiting for forgings or castings.
- Dijital Envanter: Designs can be stored digitally and printed when required, offering greater flexibility than maintaining physical stock. This agility benefits aerospace component suppliers and distributors managing diverse inventories.
Comparative Overview: AM vs. Traditional for Rocket Nozzles
Özellik | Traditional Manufacturing (Casting/Machining) | Metal Additive Manufacturing (e.g., LPBF/SEBM) | Advantage of AM |
---|---|---|---|
Geometrik Karmaşıklık | Limited, especially internal features | Very high, enables conformal cooling | Enhanced performance, optimized designs |
Design Iteration | Slow, requires tooling | Fast, tool-less | Rapid prototyping, faster development cycles |
Ağırlık | Often heavier, optimization limited | Potential for significant weight reduction | Increased payload capacity, better efficiency |
Part Count | Often requires assembly of multiple parts | Enables consolidation into single parts | Reduced assembly, improved reliability, simpler logistics |
Malzeme Atıkları | Yüksek (eksiltici süreç) | Düşük (katkı maddesi işlemi) | Cost savings (especially with superalloys) |
Kurşun Zamanları | Long (tooling, multi-step processes) | Potentially shorter, especially for prototypes | Increased supply chain agility |
Kalıp Maliyeti | Yüksek | Hiçbiri | Lower barrier for new designs/low volumes |
Sayfalara Aktar
While metal 3D printing presents some unique challenges (discussed later), its inherent advantages in design freedom, speed, weight reduction, and part consolidation make it an exceptionally compelling technology for producing high-performance rocket nozzles, driving innovation across the aerospace manufacturing landscape.
High-Temperature Heroes: Recommended Metal Powders for Rocket Nozzles (IN718, IN625, Haynes 282)
The heart of a rocket nozzle’s ability to withstand the inferno of combustion lies in the material it’s made from. For 3D printed nozzles, this translates directly to the choice of metal powder. The extreme temperatures (often exceeding 1000°C, sometimes much higher), high pressures, corrosive combustion products, and significant thermal cycling demand materials with exceptional properties. Nickel-based superalloys are the workhorses in this domain due to their ability to retain strength at elevated temperatures, resist oxidation and corrosion, and offer good fatigue life. Among the most prominent and well-suited for additive manufacturing of rocket nozzles are Inconel 718 (IN718), Inconel 625 (IN625), and Haynes 282.
Selecting the right powder is critical, and sourcing high-quality, consistent powder is equally important. Procurement managers and engineers should partner with reputable metal powder suppliers who understand the stringent requirements of aerospace applications. Companies like Met3dp, leveraging advanced powder production techniques like gas atomization and Plasma Rotating Electrode Process (PREP), specialize in producing yüksek performanslı küresel metal tozları optimized for AM processes like Selective Electron Beam Melting (SEBM) and Laser Powder Bed Fusion (LPBF). Their portfolio includes not only standard superalloys but also innovative alloys tailored for specific demanding environments.
Let’s delve into the properties and suitability of the recommended powders:
1. Inconel 718 (IN718 / Alloy 718)
- Kompozisyon: Nickel-Chromium alloy, precipitation-hardenable with Niobium and Molybdenum.
- Anahtar Özellikler:
- Yüksek Mukavemet: Excellent tensile, fatigue, and creep-rupture strength up to ~700°C (1300°F). It maintains good strength at even higher temperatures for short durations.
- Good Weldability/Printability: One of the most readily processable superalloys via AM, exhibiting good fusion characteristics and relative resistance to cracking during printing compared to some other nickel alloys.
- Korozyon Direnci: Good resistance to oxidation and corrosion in typical combustion environments.
- Availability & Cost: Relatively widely available and generally less expensive than IN625 or Haynes 282.
- Isıl İşlem: Requires specific precipitation hardening heat treatments after printing to achieve optimal mechanical properties.
- Suitability for Rocket Nozzles:
- Excellent choice for applications where operating temperatures are demanding but may not reach the absolute extremes handled by Haynes 282.
- Widely used for structural components within the engine, nozzle flanges, and less intensely heated sections of the nozzle.
- Its good printability makes it a common choice for complex geometries and initial development programs.
- Düşünceler: Strength drops off more significantly than Haynes 282 above ~700°C.
2. Inconel 625 (IN625 / Alloy 625)
- Kompozisyon: Nickel-Chromium-Molybdenum-Niobium alloy, solid-solution strengthened.
- Anahtar Özellikler:
- Mükemmel Korozyon Direnci: Superior resistance to a wide range of corrosive environments, including oxidation and acidic combustion byproducts, even at high temperatures. Often considered more corrosion-resistant than IN718.
- High Strength & Toughness: Maintains good strength and toughness over a broad temperature range, from cryogenic up to ~815°C (1500°F). It doesn’t rely on precipitation hardening like IN718.
- Good Fabricability/Printability: Generally considered to have good printability in AM processes, similar to IN718.
- Yorulma Dayanımı: Exhibits excellent fatigue strength.
- Suitability for Rocket Nozzles:
- Ideal for components exposed to highly corrosive propellant combinations or environments.
- Used for nozzle liners, combustion chambers, and sections requiring exceptional toughness and fatigue resistance across a wide temperature spectrum.
- Its strength profile complements IN718, offering better performance in certain temperature/corrosion regimes.
- Düşünceler: Typically lower strength than optimally heat-treated IN718 at moderate temperatures (below ~650°C), but maintains strength better at slightly higher temperatures. Generally more expensive than IN718.
3. Haynes 282
- Kompozisyon: Nickel-Cobalt-Chromium-Molybdenum-Titanium-Aluminum alloy, precipitation-hardenable. Developed specifically for high-temperature structural applications.
- Anahtar Özellikler:
- Olağanüstü Yüksek Sıcaklık Dayanımı: Offers superior creep strength, stress rupture properties, and tensile strength compared to IN718 and IN625 at temperatures above ~700°C, extending operational capability towards 900°C (1650°F) and higher for certain load conditions.
- Good Fabricability/Printability: Developed with fabricability in mind, it exhibits relatively good printability for such a high-performance alloy, though potentially requiring more careful parameter optimization than IN718/IN625.
- Good Oxidation Resistance: Excellent resistance to high-temperature oxidation.
- Termal Kararlılık: Maintains microstructural stability after long exposures at high temperatures.
- Isıl İşlem: Requires precipitation hardening heat treatment.
- Suitability for Rocket Nozzles:
- The premium choice for the most demanding applications, such as the hottest sections of the nozzle throat and expansion cone in high-performance liquid rocket engines or hypersonic air-breathing engines.
- Selected when IN718 or IN625 cannot meet the required strength or creep resistance criteria at peak operating temperatures.
- Düşünceler: The most expensive of the three alloys. Processing parameters in AM need careful control to manage residual stress and ensure optimal microstructure.
Powder Quality – A Critical Factor
Regardless of the alloy chosen, the quality of the metal powder feedstock is non-negotiable for producing reliable, flight-worthy rocket nozzles. Key powder characteristics include:
- Küresellik: Highly spherical particles ensure good powder flowability and high packing density in the powder bed, leading to denser, more uniform parts. Technologies like PREP, utilized by providers such as Met3dp, excel at producing highly spherical powders.
- Parçacık Boyutu Dağılımı (PSD): A controlled PSD is crucial for consistent melting behavior and final part resolution. The optimal PSD depends on the specific AM machine and process (LPBF typically uses finer powders than SEBM).
- Purity & Chemistry: Low levels of impurities (especially oxygen and nitrogen) and precise adherence to the alloy’s chemical specification are essential for achieving the desired mechanical properties and preventing defects.
- Akışkanlık: Good flowability ensures uniform spreading of powder layers during the printing process, preventing voids and inconsistencies.
- Absence of Satellites: Minimizing smaller particles attached to larger ones (satellites) improves flowability and packing density.
Material Properties Comparison (Typical Values at Room Temperature after Appropriate Heat Treatment)
Mülkiyet | IN718 (AMS 5663) | IN625 (AMS 5666) | Haynes 282 (AMS 5951) | Birim | Notlar |
---|---|---|---|---|---|
Nihai Çekme Dayanımı | ~1380 (200) | ~930 (135) | ~1180 (171) | MPa (ksi) | Strength varies significantly with temp. |
Akma Dayanımı (0,2%) | ~1170 (170) | ~520 (75) | ~780 (113) | MPa (ksi) | Strength varies significantly with temp. |
Uzama | ~20% | ~45% | ~30% | % | Indicator of ductility |
Max Use Temperature (Strength Limited) | ~700 (1300) | ~815 (1500) | ~900+ (1650+) | °C (°F) | Approximate, depends on stress & time |
Yoğunluk | 8.19 | 8.44 | 8.33 | g/cm³ | |
Göreceli Maliyet | Üs | Daha yüksek | En yüksek | – | General comparison |
Primary Strength Mechanism | Çökelme Sertleşmesi | Solid Solution | Çökelme Sertleşmesi | – | Influences heat treatment needs |
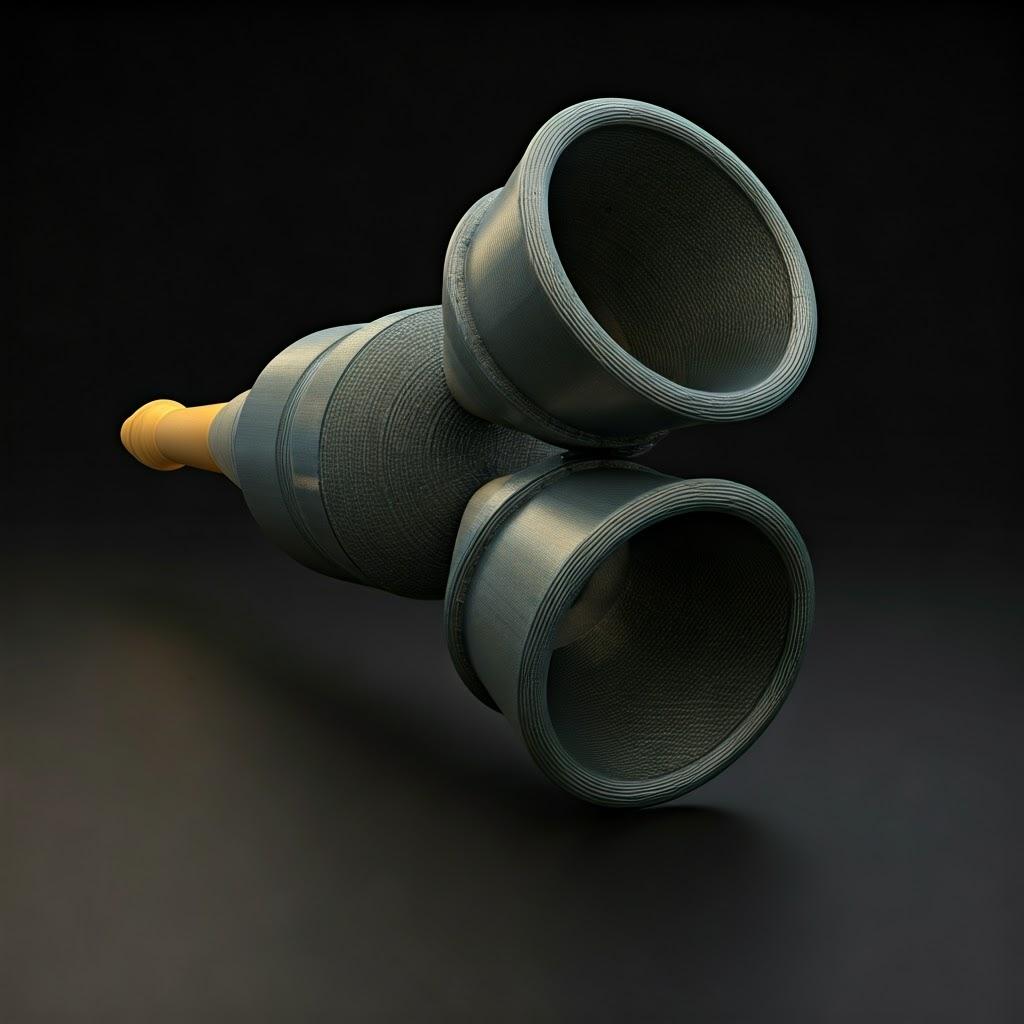
Sayfalara Aktar
Note: These are typical values; actual properties of AM parts depend heavily on print parameters, build orientation, and post-process heat treatments.
Choosing the right high-temperature superalloy powder is a balance between performance requirements (temperature, stress, corrosion), manufacturability via AM, and cost. IN718 provides a strong baseline, IN625 offers superior corrosion resistance and toughness, while Haynes 282 delivers unparalleled strength at the highest temperatures, enabling the production of robust and efficient 3D printed rocket nozzles for the most demanding aerospace applications. Partnering with knowledgeable material suppliers and AM service providers is key to navigating these choices successfully. Sources and related content
Designing for Additive Success: Optimizing Rocket Nozzles for 3D Printing
Additive manufacturing unlocks incredible design freedom, but simply taking a conventionally designed rocket nozzle and printing it rarely yields optimal results. To fully leverage the benefits of AM—especially for complex components like nozzles operating under extreme conditions—engineers must embrace Design for Additive Manufacturing (DfAM) principles. DfAM involves rethinking the design process from the ground up, considering the unique capabilities and constraints of the chosen AM process (like LPBF or SEBM) and material (like IN718, IN625, or Haynes 282). Optimizing a rocket nozzle design for AM is crucial for achieving desired performance, ensuring manufacturability, minimizing post-processing, and controlling costs.
Key DfAM Considerations for Rocket Nozzles:
- Leveraging Geometric Complexity for Performance:
- Konformal Soğutma Kanalları: This is perhaps the most significant advantage AM offers for nozzles. Instead of simple drilled or milled channels, AM allows designers to create intricate networks that follow the exact contour of the nozzle wall, maintaining a precise distance from the hot gas flow.
- Avantajlar: Maximized heat extraction, more uniform wall temperatures, reduced thermal stress, potential for higher chamber pressures/temperatures, leading to improved specific impulse (Isp).
- DfAM Tactics: Design channels with smooth curves, avoid sharp corners where stress can concentrate, consider varying channel cross-sections (e.g., elliptical or rectangular) for optimized flow and heat transfer, and ensure channels are self-supporting where possible or design them for easy powder removal.
- Integrated Features: Combine elements like injector faces, gimbal interfaces, mounting flanges, sensor ports, or even structural brackets directly into the nozzle print.
- Avantajlar: Reduced part count, eliminated joints (welds/brazes), lower assembly complexity, weight savings.
- DfAM Tactics: Ensure smooth transitions between features, consider stress concentrations at junctions, and design interfaces with appropriate tolerances for potential post-machining.
- Konformal Soğutma Kanalları: This is perhaps the most significant advantage AM offers for nozzles. Instead of simple drilled or milled channels, AM allows designers to create intricate networks that follow the exact contour of the nozzle wall, maintaining a precise distance from the hot gas flow.
- Managing Supports and Overhangs:
- Kendini Destekleyen Açılar: Most powder bed fusion processes can print overhangs up to a certain angle (typically around 45 degrees from the horizontal) without requiring support structures. Designing features to stay within this limit minimizes support usage.
- Support Strategy: Where supports are necessary (e.g., for horizontal surfaces, steep overhangs, or large internal cavities), they must be carefully designed.
- Amacımız: Anchor the part to the build plate, prevent warping due to thermal stress, support overhanging features during the build.
- DfAM Tactics: Design supports that are strong enough but easy to remove without damaging the part surface, minimize the contact area between the support and the part (‘support scarring’), use tree-like or lattice supports to save material and reduce removal time, and orient the part on the build plate to minimize the need for critical-surface supports. For internal channels, designing them to be self-supporting or ensuring clear pathways for powder removal is vital.
- Toz Giderme: Internal channels and complex cavities must be designed with access points for removing unfused powder after the build. Trapped powder can add weight and potentially sinter during heat treatment, causing issues.
- Wall Thickness and Feature Size:
- Minimum Wall Thickness: AM processes have limitations on the minimum wall thickness they can reliably produce (dependent on machine, material, parameters). Designers must ensure walls, especially in thin sections of the nozzle extension or cooling channels, meet these minimums (often ~0.4-1.0 mm).
- Feature Resolution: Small features like cooling channel inlets/outlets or fine details need to be designed considering the resolution limits of the AM process (beam spot size, layer thickness).
- Tekdüzelik: While possible to vary thickness, maintaining relatively uniform wall thickness can help manage thermal gradients and reduce residual stress during printing. Abrupt changes should be transitioned smoothly.
- Thermal Management and Residual Stress:
- Mechanism: The rapid heating and cooling inherent in AM create significant thermal gradients, leading to internal residual stresses within the part. Excessive stress can cause warping, distortion during removal from the build plate, or even cracking, especially in brittle high-temperature alloys.
- DfAM Tactics:
- Oryantasyon: Carefully select the build orientation to manage stress accumulation and minimize the need for supports in critical areas.
- Geometry: Incorporate fillets and radii instead of sharp corners, aim for uniform material distribution where possible, and use topology optimization to remove unnecessary material that could contribute to stress.
- Simulation: Utilize process simulation software to predict thermal gradients and residual stress distribution based on the design and planned print parameters. This allows for design modifications önce printing to mitigate potential issues.
- Destek Yapıları: Well-designed supports can help anchor the part and resist warping forces.
- Topoloji Optimizasyonu ve Hafifletme:
- Concept: Use software tools to optimize the material layout within a defined design space based on applied loads, constraints, and performance objectives (e.g., maximizing stiffness while minimizing weight).
- Application to Nozzles: While the primary nozzle contour is dictated by fluid dynamics, structural elements like flanges, ribs, or mounting brackets can often be topologically optimized.
- Kafes Yapılar: Replacing solid sections with internal lattice structures can dramatically reduce weight while maintaining required stiffness and strength. This is particularly useful for structural jackets or support elements around the nozzle.
- Düşünceler: Ensure optimized structures are manufacturable via AM (e.g., lattice strut thickness, node connections), consider fatigue performance, and validate designs through simulation and testing.
- Designing for Post-Processing:
- Machining Allowances: If critical interfaces (e.g., mounting flanges, seal surfaces) require tight tolerances achievable only through CNC machining, designers must add extra material (machining stock) to these areas in the AM design.
- Yüzey İşlemi: Understand the as-built surface finish capabilities of the chosen AM process (SEBM generally produces rougher surfaces than LPBF). If a smoother finish is required for fluid dynamics or sealing, design the part to allow access for polishing or machining.
- Inspection Access: Design the part considering how Non-Destructive Testing (NDT) like CT scanning or ultrasonic testing will be performed to ensure internal integrity can be verified.
Embracing DfAM:
Successfully implementing DfAM requires close collaboration between design engineers, materials scientists, and AM process experts. It often involves an iterative process of design, simulation, printing test coupons or prototypes, and refinement. While it demands a different way of thinking compared to traditional design-for-machining, the payoff in terms of performance gains, weight reduction, and manufacturing efficiency for components like rocket nozzles is substantial. Partnering with an experienced metal 3D printing service provider who understands DfAM principles is crucial for translating advanced designs into flight-worthy hardware.
Achieving Precision: Tolerance, Surface Finish, and Dimensional Accuracy in 3D Printed Nozzles
While additive manufacturing offers unparalleled geometric freedom, understanding and controlling the achievable precision—tolerances, surface finish, and overall dimensional accuracy—is critical for functional components like rocket nozzles. Interfaces must mate correctly, fluid dynamic surfaces need predictable characteristics, and the final part must match the engineering specifications within acceptable limits. Aerospace engineers and procurement managers must have realistic expectations based on the chosen AM process, material, and post-processing steps.
1. Dimensional Accuracy:
- Tanım: How closely the dimensions of the final printed part match the nominal dimensions specified in the CAD model.
- Etkileyen Faktörler:
- AM Süreci: Different AM technologies have inherent accuracy levels. Laser Powder Bed Fusion (LPBF) generally offers higher accuracy and finer feature resolution than Electron Beam Melting (SEBM) due to its smaller beam spot size and finer powder/layer thickness. However, SEBM often experiences lower residual stress, potentially leading to less distortion in larger parts.
- Machine Calibration: Regular calibration of the AM system’s scanners, energy source, and motion systems is crucial.
- Malzeme Özellikleri: Thermal expansion and shrinkage characteristics of the specific alloy (IN718, IN625, Haynes 282) affect final dimensions.
- Part Size and Geometry: Larger parts and complex geometries are more susceptible to thermal distortion and deviation.
- Yapı Oryantasyonu: How the part is oriented on the build plate affects heat distribution, support requirements, and potential shrinkage/warping directions.
- Thermal Stress: Residual stresses built up during printing can cause distortion, especially after the part is removed from the build plate or during stress-relieving heat treatments.
- İşlem sonrası: Heat treatments (like HIP or stress relief) can cause slight dimensional changes. Machining is often used to achieve final accuracy on critical features.
- Typical Achievable Accuracy (As-Built):
- LPBF: Generally in the range of ±0.1 mm to ±0.2 mm (±0.004″ to ±0.008″) or ±0.1-0.2% of the dimension for well-controlled processes.
- SEBM: Typically in the range of ±0.2 mm to ±0.4 mm (±0.008″ to ±0.016″) or ±0.2-0.4% of the dimension.
- Achieving Tighter Tolerances: For critical dimensions (e.g., throat diameter, flange interfaces, seal grooves), tolerances tighter than the as-built capability are often required. These are typically achieved through post-print CNC machining, where tolerances of ±0.01 mm to ±0.05 mm (±0.0004″ to ±0.002″) are feasible. DfAM principles dictate adding machining stock to these areas.
2. Surface Finish (Roughness):
- Tanım: The measure of the fine-scale irregularities on a part’s surface, typically quantified by Ra (average roughness).
- Etkileyen Faktörler:
- AM Süreci: SEBM inherently produces rougher surfaces (Ra typically 20-40 µm) due to larger powder particles and higher energy input causing partial sintering of surrounding powder. LPBF produces smoother surfaces (Ra typically 5-15 µm) due to finer powder and smaller melt pools.
- Katman Kalınlığı: Thinner layers generally result in smoother surfaces, especially on angled or curved faces (reducing the staircase effect).
- Yapı Oryantasyonu: Surfaces parallel to the build plate (up-facing/down-facing) tend to have different roughness characteristics than vertical walls. Down-facing surfaces requiring supports often exhibit the poorest finish after support removal.
- Toz Özellikleri: Particle size distribution and sphericity influence the finish.
- Laser/Electron Beam Parameters: Energy density, scan speed, and hatching strategy affect melt pool dynamics and surface texture.
- Destek Kaldırma: Mechanical removal of supports can leave witness marks or scarring, increasing local roughness.
- Importance for Nozzles:
- Internal Surfaces: Surface roughness inside the nozzle affects fluid dynamics (boundary layer development, friction losses) and heat transfer. While extreme smoothness isn’t always necessary or beneficial (slight roughness can sometimes enhance turbulent heat transfer), a controlled and predictable finish is important.
- External Surfaces: Less critical for performance but may be important for inspection or aesthetics.
- Sızdırmazlık Yüzeyleri: Interfaces requiring seals need a much smoother finish than achievable in the as-built state, necessitating post-processing like machining or polishing.
- Yüzey İşleminin İyileştirilmesi:
- Parametre Optimizasyonu: Fine-tuning AM process parameters can modestly improve the as-built finish.
- Abrasive Blasting/Tumbling: Can provide a more uniform matte finish and remove some loosely adhered particles but only slightly reduces Ra.
- Chemical Polishing/Etching: Can significantly smooth surfaces but needs careful control to avoid altering dimensions.
- Abrasive Flow Machining (AFM): Flows abrasive media through internal channels to smooth them.
- CNC Machining/Grinding/Polishing: The most common methods for achieving smooth (Ra < 1 µm) and precise surfaces on accessible features.
3. Tolerancing Standards:
- GD&T (Geometric Dimensioning and Tolerancing): Essential for communicating design intent clearly. Drawings for AM parts should use GD&T callouts just like traditionally manufactured parts, specifying tolerances for size, form, orientation, location, and runout.
- ISO/ASTM Standards: Standards specific to additive manufacturing (e.g., ISO/ASTM 52900 series) provide terminology and frameworks, but specific tolerance grades often still refer back to general engineering standards (like ISO 2768 for general tolerances, though its direct applicability to AM can be debated). Designers must explicitly state required tolerances on drawings.
Achieving Precision in Practice:
Achieving the required precision for a 3D printed rocket nozzle involves a holistic approach:
- DfAM: Designing with process limitations and post-processing needs in mind.
- Süreç Kontrolü: Utilizing high-quality AM systems with robust process monitoring and control. Met3dp emphasizes industry-leading print volume, accuracy, and reliability in their printers.
- Malzeme Kalitesi: Using consistent, high-quality metal powders.
- Simulation: Predicting and compensating for distortion.
- Strategic Post-Processing: Planning for and executing necessary steps like heat treatment and precision machining.
- Metrology & Inspection: Employing accurate measurement techniques (CMM, 3D scanning) to verify conformance.
By understanding the capabilities and limitations of AM processes and integrating DfAM and post-processing strategies, engineers can confidently design and manufacture 3D printed rocket nozzles that meet the demanding precision requirements of aerospace applications.
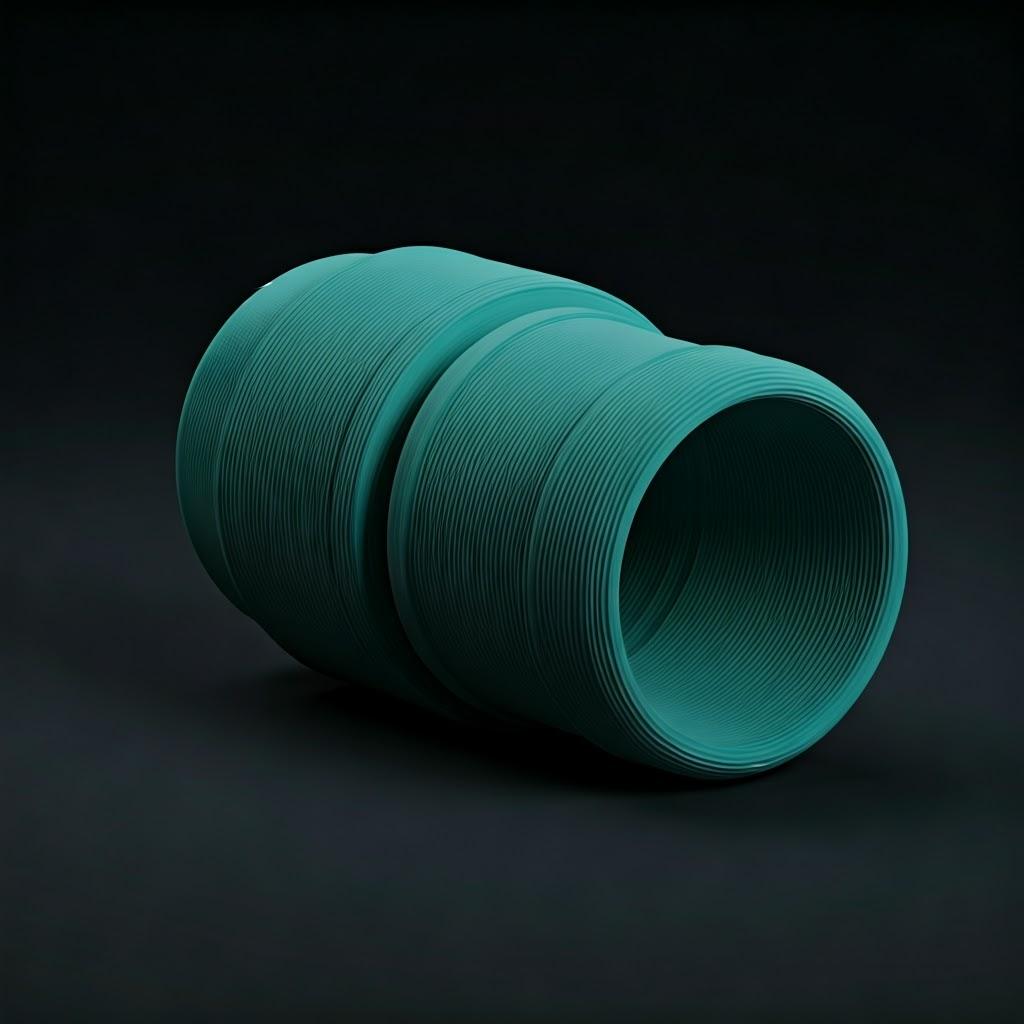
Beyond the Build: Essential Post-Processing for 3D Printed Rocket Nozzles
Completing the print cycle on an additive manufacturing machine is a significant milestone, but it’s rarely the final step in producing a functional, flight-ready rocket nozzle. A series of crucial post-processing steps are typically required to transform the as-built component into a finished part that meets the stringent requirements for mechanical properties, dimensional accuracy, surface finish, and overall integrity demanded by the aerospace industry. Planning for these steps is integral to the manufacturing workflow and impacts overall cost and lead time.
Common Post-Processing Steps for AM Rocket Nozzles:
- Powder Removal / Depowdering:
- Amacımız: To remove all unfused metal powder from the completed build, especially from internal channels, cavities, and complex geometries.
- Yöntemler: Manual brushing, vacuuming, compressed air blowing, gentle vibration or tumbling. Automated depowdering systems are becoming more common. Access ports designed during the DfAM phase are crucial for effectively cleaning internal cooling channels.
- Importance: Trapped powder adds unnecessary weight, can interfere with subsequent processes (like HIP), and could potentially dislodge during operation. Incomplete powder removal is a significant quality concern.
- Stress Relief Heat Treatment:
- Amacımız: To reduce the high internal residual stresses built up during the rapid heating and cooling cycles of the AM process. These stresses can cause distortion when the part is removed from the build plate or lead to premature failure.
- Method: Heating the part (often while still attached to the build plate) to a specific temperature below the alloy’s aging or solutioning temperature, holding it for a defined period, and then slowly cooling it. Parameters depend heavily on the alloy (IN718, IN625, Haynes 282) and part geometry.
- Importance: Essential for dimensional stability and preventing cracking, especially before removing supports or the part from the build plate.
- Removal from Build Plate & Support Structure Removal:
- Amacımız: To separate the printed nozzle(s) from the metal base plate they were built upon and remove any temporary support structures used during the build.
- Yöntemler: Typically done using wire EDM (Electrical Discharge Machining) or band sawing to cut the part free from the plate. Supports are removed manually (breaking, cutting, grinding) or sometimes via machining.
- Importance: Requires careful handling to avoid damaging the part. Support removal can affect the surface finish in contact areas (‘witness marks’). DfAM aims to minimize supports and make them easily accessible.
- Sıcak İzostatik Presleme (HIP):
- Amacımız: To eliminate internal porosity (small voids) that can be present in as-built AM parts, thereby improving mechanical properties like fatigue life, ductility, and fracture toughness.
- Method: Subjecting the part to high temperature (below melting point) and high inert gas pressure (typically Argon) simultaneously in a specialized HIP vessel. The pressure closes internal voids, and the high temperature allows metallurgical bonds to form across the closed pore interfaces.
- Importance: Often considered mandatory for critical aerospace components, including nozzles, to achieve properties equivalent or superior to wrought or cast materials and ensure maximum density (typically >99.9%). It also helps further reduce residual stress.
- Solution Annealing & Aging Heat Treatments (Precipitation Hardening):
- Amacımız: To achieve the final desired microstructure and optimal mechanical properties (strength, hardness, creep resistance) for precipitation-hardenable alloys like IN718 and Haynes 282. (IN625 is solid-solution strengthened and may only require annealing).
- Method: Involves specific heating cycles:
- Çözelti Tavlama: Heating to a high temperature to dissolve precipitates and create a homogenous solid solution, followed by rapid cooling.
- Yaşlanma (Çökelme Sertleşmesi): Reheating to one or more intermediate temperatures for specific times to allow controlled formation of fine strengthening precipitates within the metal matrix.
- Importance: Absolutely critical for developing the high-temperature strength required for nozzle operation. Heat treatment recipes are specific to the alloy and must be carefully controlled.
- CNC İşleme:
- Amacımız: To achieve tight tolerances on critical dimensions and interfaces, create specific features (like O-ring grooves or threaded holes) that are difficult to print accurately, and obtain very smooth surface finishes on sealing or mating surfaces.
- Method: Using multi-axis CNC milling or turning centers to precisely remove material from designated areas of the AM part. Requires careful fixture design to hold the complex geometry of the nozzle securely without distortion.
- Importance: Bridges the gap between the inherent accuracy/finish of AM and the stringent requirements for final assembly and function. DfAM planning (adding machining stock) is essential.
- Yüzey İşlemi:
- Amacımız: To improve the surface finish beyond the as-built or HIPed state for reasons of fluid dynamics, heat transfer, sealing, or inspection.
- Yöntemler:
- Abrasive Blasting (Grit/Bead): Creates a uniform matte finish.
- Tumbling/Vibratory Finishing: Uses media to smooth surfaces and deburr edges, suitable for batches of smaller parts.
- Polishing/Lapping: Manual or automated processes to achieve very smooth, mirror-like finishes (low Ra) on specific surfaces.
- Abrasive Flow Machining (AFM): Useful for smoothing internal channels by flowing abrasive putty through them.
- Elektro parlatma: Electrochemical process to remove material and smooth surfaces, effective for complex shapes.
- Importance: Requirements depend on the specific application area of the nozzle surface (internal flow path vs. external structure vs. sealing face).
- Non-Destructive Testing (NDT) and Inspection:
- Amacımız: To verify the integrity of the finished nozzle, ensuring it is free from critical defects (cracks, porosity clusters, inclusions) and meets all dimensional specifications.
- Yöntemler:
- Visual Inspection: Basic check for surface defects.
- Dimensional Metrology: Coordinate Measuring Machines (CMM), 3D laser scanning to verify dimensions and GD&T.
- Computed Tomography (CT Scanning): X-ray based method to inspect internal structures and detect volumetric flaws (porosity) without destroying the part. Increasingly vital for AM parts.
- Ultrasonic Testing (UT): Uses sound waves to detect internal flaws.
- Fluorescent Penetrant Inspection (FPI): Detects surface-breaking cracks.
- Radiographic Testing (RT): Traditional X-ray inspection.
- Importance: Mandatory quality assurance step for flight-critical aerospace hardware. Provides confidence in the part’s structural integrity.
Workflow Integration:
These post-processing steps are not always performed sequentially as listed; the exact workflow depends on the material, design complexity, and specific requirements. For instance, machining might occur before final heat treatment, or HIP might be combined with part of the heat treatment cycle. Careful planning and process control are essential throughout. The cost and time associated with post-processing can be significant, often comparable to or even exceeding the initial printing cost, and must be factored into project budgets and timelines by procurement managers and engineers.
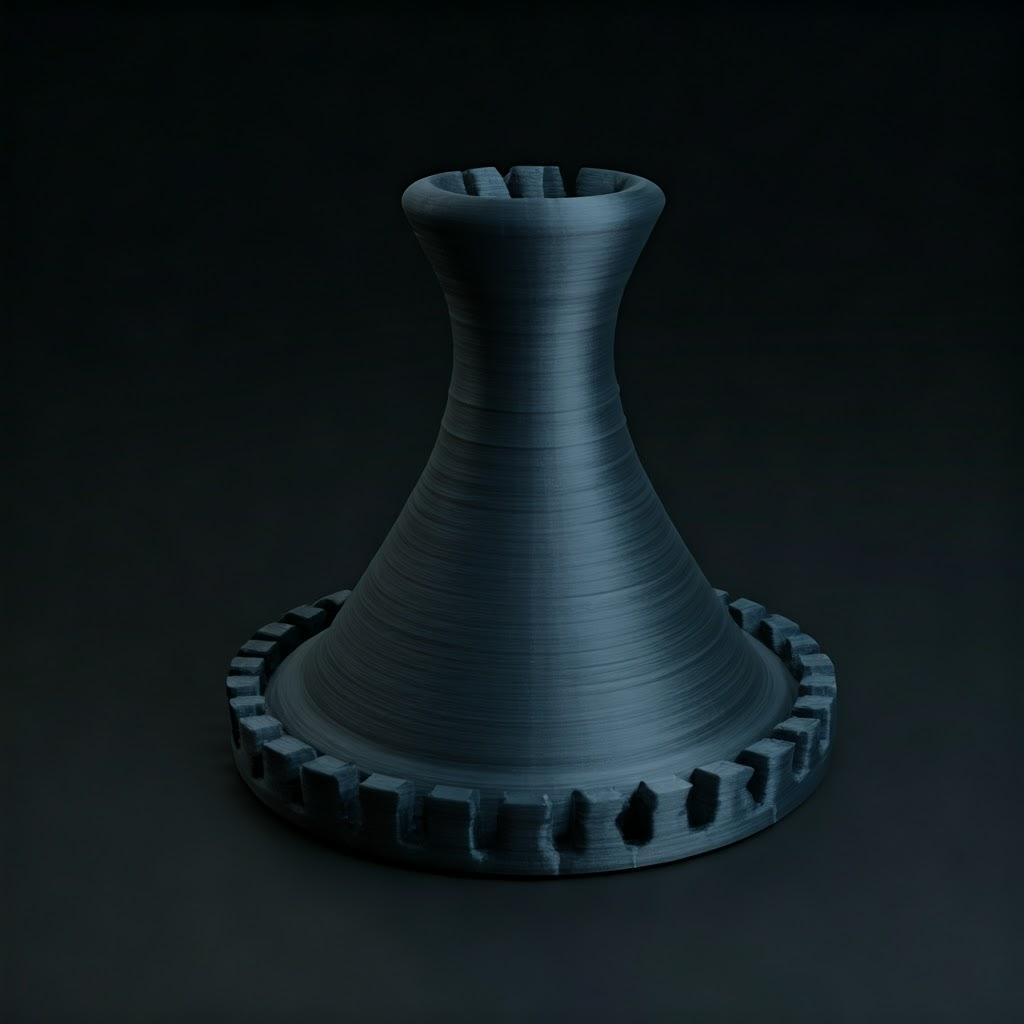
Navigating Challenges: Common Issues in 3D Printing Rocket Nozzles and Solutions
While metal additive manufacturing offers transformative potential for rocket nozzle production, it’s not without its challenges. The combination of complex geometries, demanding high-temperature superalloys, and the inherent physics of layer-by-layer fusion can lead to various defects or issues if not properly managed. Understanding these potential problems and implementing robust process controls and mitigation strategies is crucial for producing reliable, high-quality nozzles.
Common Challenges and Mitigation Strategies:
- Residual Stress, Warping, and Distortion:
- Sorun: Large thermal gradients during printing cause internal stresses. As these stresses relax, they can cause the part to warp, distort from its intended geometry, or even crack, especially upon removal from the build plate or during post-processing. Nickel superalloys are particularly prone due to their high thermal expansion and strength.
- Causes: Rapid heating/cooling cycles, large temperature differences between molten pool and surrounding material, part geometry (thick sections adjacent to thin), material properties.
- Hafifletme:
- Process Simulation: Predict stress accumulation and distortion to optimize build orientation and support strategy önce baskı.
- Optimized Scan Strategies: Use specific laser/electron beam scan patterns (e.g., island scanning, checkerboard patterns) to distribute heat more evenly and reduce localized stress buildup.
- Platform Heating (LPBF & SEBM): Maintaining an elevated temperature in the build chamber reduces thermal gradients. SEBM inherently uses higher chamber temperatures, which helps significantly.
- Sağlam Destek Yapıları: Design supports to effectively anchor the part and counteract warping forces.
- İnşaat Sonrası Stres Giderme: Perform an appropriate heat treatment cycle önce removing the part from the build plate.
- DfAM: Design features with gradual transitions, avoid large bulky sections where possible, and consider topology optimization.
- Gözeneklilik:
- Sorun: Small internal voids or pores within the printed material. Porosity can reduce density, degrade mechanical properties (especially fatigue life and ductility), and act as crack initiation sites.
- Causes:
- Gas Porosity: Trapped gas (e.g., Argon shield gas in LPBF, dissolved gases in powder) within the melt pool that doesn’t escape before solidification.
- Lack-of-Fusion Porosity: Insufficient energy input or inadequate overlap between melt pools leaves unfused powder particles or voids between layers/tracks. Keyhole instability/porosity can occur with excessive energy density.
- Powder Quality Issues: Irregular powder shapes, internal gas pores within powder particles, or contamination.
- Hafifletme:
- Optimize Edilmiş Süreç Parametreleri: Careful control of laser/beam power, scan speed, layer thickness, hatch spacing, and focus to ensure complete melting and stable melt pool dynamics. Extensive parameter development is key.
- Yüksek Kaliteli Toz: Use powder with high sphericity, controlled particle size distribution, low internal gas content, and high purity. Sourcing from reputable suppliers like Met3dp, known for their advanced powder making systems, is critical.
- Kontrollü Atmosfer: Maintain a high-purity inert gas environment (LPBF) or high vacuum (SEBM) to minimize gas pickup.
- Sıcak İzostatik Presleme (HIP): Highly effective post-processing step to close internal pores and achieve full density (>99.9%). Often mandatory for critical nozzle components.
- Cracking (Solidification or Liquation Cracking):
- Sorun: Formation of cracks during solidification or in the heat-affected zone during subsequent passes, particularly common in certain complex, high-strength nickel superalloys (though IN718, IN625, and Haynes 282 generally have better weldability/printability than some others).
- Causes: High residual stresses exceeding the material’s strength at elevated temperatures, presence of low-melting-point phases or impurities segregating at grain boundaries, unfavorable grain structures.
- Hafifletme:
- Alloy Selection: Choose alloys known for better printability/weldability where possible (IN718/IN625 are generally good).
- Parametre Optimizasyonu: Control heat input and cooling rates through scan strategy and parameters to minimize stress and promote favorable microstructures.
- Platform Heating: Reduces thermal shock and stress.
- Stress Relief Heat Treatment: Reduces overall stress levels.
- Toz Saflığı: Minimize impurities that can contribute to liquation cracking.
- DfAM: Avoid sharp corners and abrupt geometric changes where stress concentrates.
- Surface Roughness and Feature Resolution Issues:
- Sorun: As-built surfaces may be too rough for fluid dynamic requirements, or fine features (small channels, thin walls) may not be accurately resolved. Stair-stepping effect on angled surfaces.
- Causes: Layer-by-layer process, powder particle size, melt pool dynamics, adherence of partially sintered powder (especially SEBM), support contact points.
- Hafifletme:
- Process Selection: LPBF generally offers better finish and resolution than SEBM.
- Parametre Ayarlama: Optimize layer thickness, beam/laser spot size, and energy input.
- Yapı Oryantasyonu: Orient part to minimize stair-stepping on critical surfaces or place them where post-processing is feasible.
- DfAM: Design features within the resolution limits of the chosen process. Ensure minimum wall thicknesses are respected.
- İşlem sonrası: Plan for machining, polishing, or AFM for critical surfaces requiring high smoothness or accuracy.
- Incomplete Powder Removal:
- Sorun: Difficulty in removing all unfused powder from complex internal channels or cavities.
- Causes: Highly intricate or tortuous channel designs, inadequate access points, powder characteristics (poor flowability).
- Hafifletme:
- DfAM: Design channels with smooth bends, sufficient diameter, and strategically placed access/drain holes. Consider designing channels to be self-draining based on build orientation.
- Optimized Depowdering Procedures: Use appropriate combinations of vibration, rotation, and targeted compressed air/vacuum.
- Teftiş: Utilize methods like CT scanning or endoscopy to verify complete powder removal from critical internal passages.
Overcoming Challenges – The Importance of Expertise:
Successfully navigating these challenges requires deep expertise in materials science, AM process physics, simulation, and rigorous quality control. This involves:
- Thorough Parameter Development: Extensive testing to establish robust process windows for specific alloy/machine combinations.
- Süreç İçi İzleme: Utilizing sensors (thermal cameras, photodiodes) to monitor the melt pool and detect anomalies during the build in real-time.
- Titiz Kalite Kontrol: Implementing comprehensive NDT and metrology throughout the workflow.
- Partnership: Collaborating closely with experienced AM service providers and material suppliers who have a proven track record in producing high-quality aerospace components. Organizations like Met3dp, with their focus on both advanced SEBM printers and high-quality metal powders, combined with application development services, embody the integrated expertise needed to tackle these challenges effectively.
By proactively addressing these potential issues through careful design, process control, and post-processing, manufacturers can harness the power of AM to produce complex, high-performance rocket nozzles reliably and repeatably.
Selecting Your Partner: Choosing the Right Metal 3D Printing Service Provider for Aerospace Components
Manufacturing flight-critical hardware like rocket nozzles using additive manufacturing is not a task to be entrusted to just any service bureau. The stakes are incredibly high, and the technical complexities involved demand a partner with specialized expertise, robust quality systems, and a deep understanding of the aerospace industry’s stringent requirements. Selecting the right metal 3D printing service provider is a critical decision for engineers, program managers, and procurement specialists aiming to leverage AM successfully. Here’s a breakdown of key criteria to evaluate potential suppliers:
- Aerospace Certifications and Quality Management System (QMS):
- Requirement: The provider must have a certified and rigorously maintained QMS specifically tailored for the aerospace industry. The primary standard is AS9100. This certification demonstrates that the supplier adheres to strict processes for traceability, configuration management, process control, inspection, and continuous improvement required for aerospace components.
- Evaluation: Verify the supplier’s AS9100 certification status and scope. Inquire about their quality manual, internal audit processes, and how they handle non-conformances. A robust QMS is non-negotiable.
- Expertise with High-Temperature Superalloys:
- Requirement: Printing materials like IN718, IN625, and especially Haynes 282 requires specific knowledge and validated process parameters. These alloys behave differently in AM processes compared to more common materials like aluminum or titanium alloys.
- Evaluation: Ask about the provider’s experience with the specific alloys required for your nozzle. Request case studies, material property data from their machines (tensile, fatigue, creep data if available), and evidence of successful prints with similar materials and complexity. Do they understand the necessary heat treatments? Do they have established and validated print parameters for these alloys?
- Relevant Technology and Equipment:
- Requirement: The supplier should possess the appropriate AM technology (e.g., LPBF, SEBM) suitable for your nozzle’s requirements (accuracy, surface finish, material). Their machines should be industrial-grade, well-maintained, and capable of producing parts that meet aerospace standards.
- Evaluation: Understand the specific make and model of printers they use. What is the build volume capacity? How do they ensure machine calibration and consistency? Does their technology align with your design needs (e.g., SEBM for lower residual stress in large parts vs. LPBF for finer features)? Companies like Met3dp, which not only provide services but also manufacture their own endüstri lideri SEBM yazıcıları and powders, often possess deep technical expertise in their specific systems.
- In-House Capabilities vs. Outsourced Processes:
- Requirement: A provider with comprehensive in-house capabilities for key post-processing steps (stress relief, HIP, heat treatment, basic machining, NDT) can offer better control, potentially faster lead times, and clearer accountability.
- Evaluation: Determine which processes are performed in-house versus outsourced. If key steps like HIP or final heat treatment are outsourced, understand the supplier’s relationship with their vendors and how quality control is maintained throughout the extended supply chain. How is traceability managed across different facilities?
- Engineering and DfAM Support:
- Requirement: Ideally, the provider should offer more than just “print-to-print” services. Look for partners who can provide Design for Additive Manufacturing (DfAM) support, helping you optimize your nozzle design for printability, performance, and cost-effectiveness.
- Evaluation: Do they have application engineers or metallurgists on staff who can review your design and offer DfAM recommendations? Can they assist with optimizing build orientation, support strategies, or suggesting design modifications to mitigate risks like residual stress?
- Process Control and Monitoring:
- Requirement: Robust process control is vital for repeatability and quality. This includes monitoring key parameters during the build (e.g., oxygen levels, chamber temperature, melt pool characteristics if available) and maintaining detailed build logs.
- Evaluation: Ask about their methods for process monitoring. Do they use melt pool monitoring or thermal imaging? How are build logs maintained and reviewed? How do they ensure consistency from build to build?
- Material Handling and Traceability:
- Requirement: Strict procedures for handling, storing, testing, and recycling metal powders are essential to prevent contamination and ensure material quality. Full traceability from raw powder batch to finished part is required.
- Evaluation: Inspect their powder handling procedures. How do they qualify incoming powder batches? How is powder stored and reused? What measures are in place to prevent cross-contamination between different alloys? How is batch traceability documented?
- Inspection and Non-Destructive Testing (NDT) Capabilities:
- Requirement: The provider must have the necessary equipment and certified personnel to perform required inspections (dimensional metrology using CMM/3D scanning) and NDT (CT scanning, FPI, UT, RT) to verify part integrity according to aerospace specifications.
- Evaluation: Confirm their in-house NDT capabilities and personnel certifications (e.g., NAS 410). If NDT is outsourced, verify the qualifications of the third-party provider. Can they provide detailed inspection reports, including CT scan analysis?
- Proven Track Record and Experience:
- Requirement: Look for providers with demonstrated experience in producing complex, high-value components for the aerospace or similarly demanding industries (e.g., medical, defense).
- Evaluation: Request references, case studies of similar projects (respecting NDAs), and inquire about their history working with aerospace primes or tier-one suppliers. How long have they been providing metal AM services for critical applications?
- Capacity, Lead Time, and Communication:
- Requirement: Ensure the provider has the capacity to meet your project timelines and production volume needs. Clear communication and project management are also vital.
- Evaluation: Discuss their current machine availability and typical lead times for parts of similar complexity and material. What is their process for providing quotes and status updates? Who will be your primary point of contact? This is crucial for procurement managers managing project schedules and wholesale buyers requiring reliable delivery estimates.
Supplier Evaluation Checklist:
Kriterler | Anahtar Sorular | Önem |
---|---|---|
AS9100 Sertifikasyonu | Is certification current? What is the scope? Can quality manual be reviewed? | Kritik |
High-Temp Alloy Expertise | Experience with IN718/IN625/Haynes 282? Parameter validation? Material data available? | Kritik |
Teknoloji ve Ekipman | Appropriate AM process (LPBF/SEBM)? Industrial grade? Build volume? Maintenance/calibration records? | Yüksek |
In-House vs. Outsourced | Which post-processing steps are in-house (HIP, Heat Treat, Machining, NDT)? How are vendors managed? | Yüksek |
DfAM Support | Offer design review/optimization? Staff expertise (engineers, metallurgists)? | Yüksek |
Process Control/Monitoring | In-process monitoring techniques? Build logs? Consistency measures? | Yüksek |
Material Handling/Traceability | Powder qualification? Storage/reuse procedures? Contamination prevention? Full lot traceability? | Kritik |
Inspection & NDT | In-house NDT (CT, FPI, etc.)? Personnel certified (NAS 410)? Dimensional inspection capabilities (CMM/Scan)? | Kritik |
Track Record & Experience | Aerospace project examples? References? Years in business? | Yüksek |
Capacity & Lead Time | Machine availability? Realistic lead times? Project management process? Communication clarity? | Yüksek |
Sayfalara Aktar
Choosing the right AM service provider is about finding a true partner who understands the technical nuances and quality imperatives of aerospace manufacturing. Thorough due diligence using these criteria will significantly increase the probability of success for your 3D printed rocket nozzle project.
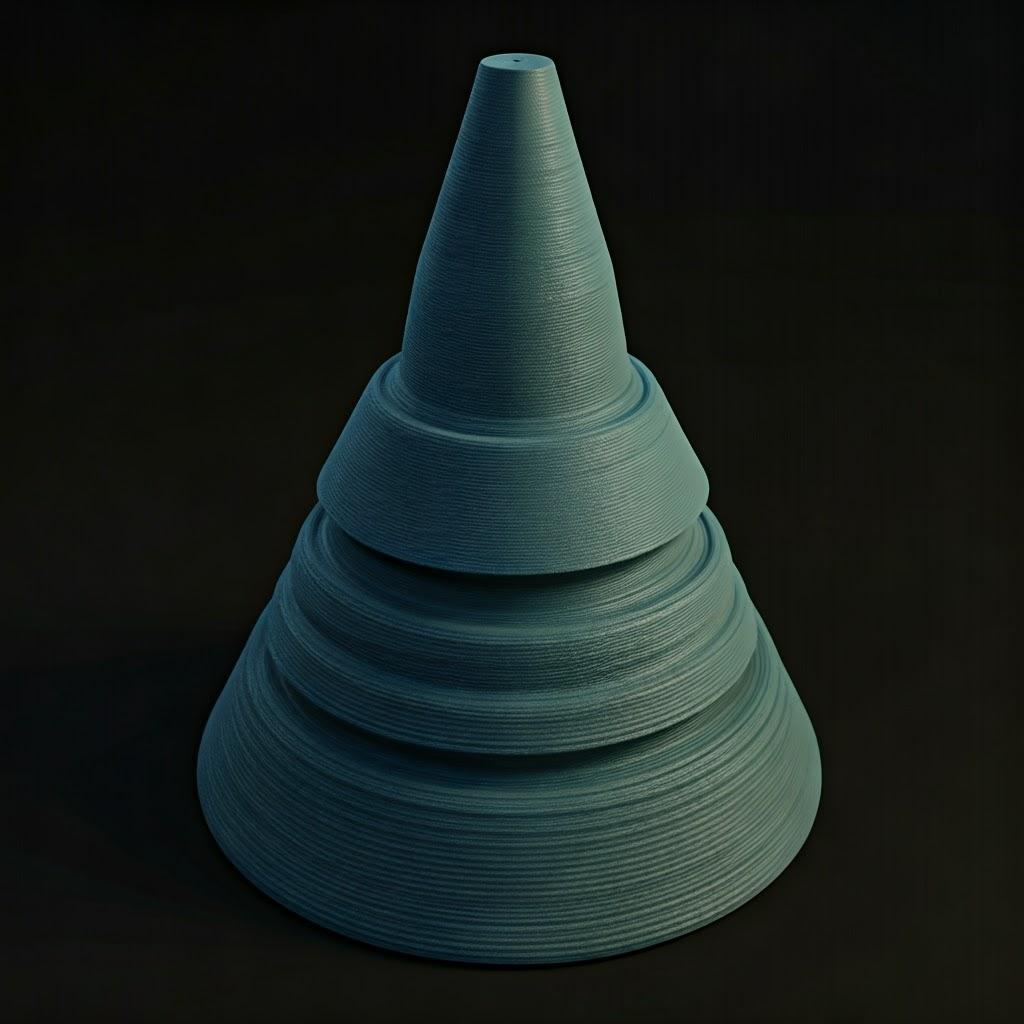
Understanding the Investment: Cost Factors and Lead Times for 3D Printed Rocket Nozzles
Additive manufacturing offers compelling technical advantages for rocket nozzles, but understanding the associated costs and typical lead times is crucial for project planning, budgeting, and comparing AM against traditional methods. Procurement managers, project engineers, and wholesale buyers need a clear picture of what drives the final price and delivery schedule for these complex, high-value components.
Key Cost Drivers for 3D Printed Rocket Nozzles:
- Malzeme Türü ve Tüketimi:
- Alloy Cost: High-temperature nickel superalloys (IN718, IN625, Haynes 282) are significantly more expensive than common engineering metals like stainless steel or aluminum. Haynes 282 is generally the costliest, followed by IN625, then IN718. Powder cost is a major component of the overall price.
- Part Volume & Density: The sheer volume of material required directly impacts cost. Larger or denser nozzles consume more expensive powder. DfAM techniques like topology optimization and lattice structures can reduce material usage and thus cost.
- Support Structure Volume: Material used for support structures also adds to the cost, although unused powder can often be recycled (with strict quality control). Minimizing supports through DfAM helps reduce this factor.
- Makine Zamanı (İnşa Zamanı):
- Part Size & Complexity: Larger parts or those with very intricate features take longer to print, consuming valuable machine time. Build height is often a primary driver of print time.
- Number of Parts per Build: Print providers aim to maximize the number of parts printed simultaneously on a single build plate (“nesting”) to amortize setup time and maximize machine utilization. For large nozzles, only one might fit per build.
- Layer Thickness & Parameters: Thinner layers provide better resolution but increase build time significantly. Optimized print parameters balance speed and quality.
- Machine Hourly Rate: Service providers factor in the capital cost of expensive industrial AM machines, maintenance, facilities, energy, and skilled labor into their hourly rates.
- Design and Engineering Input (NRE – Non-Recurring Engineering):
- DfAM & Optimization: If the service provider assists with design optimization, simulation, or developing specific build strategies, this initial engineering effort contributes to the NRE cost, especially for first-time prints or complex new designs.
- Parameter Development: If printing a novel geometry or requiring specific properties, extensive parameter development and testing might be needed, adding to upfront costs.
- İşlem Sonrası Gereksinimler:
- Complexity & Extent: Post-processing steps can account for 50% or more of the total cost. The specific steps required (stress relief, HIP, heat treatment, support removal, machining, finishing, NDT) and their complexity heavily influence the price.
- HIP: Hot Isostatic Pressing is an expensive batch process requiring specialized equipment.
- CNC İşleme: The amount of required machining (setup time, programming, machining time) is a major factor, especially for achieving tight tolerances on multiple features.
- NDT & Inspection: Comprehensive inspection, particularly CT scanning for internal validation, adds significant cost but is essential for quality assurance.
- Quality Assurance and Certification:
- Aerospace Standards (AS9100): Maintaining the rigorous quality systems, documentation, and traceability required by AS9100 involves overhead costs factored into the part price.
- Testing Requirements: If specific destructive testing (e.g., tensile tests on build witness coupons) or extensive documentation packages are required, these add to the cost.
- Order Volume and Urgency:
- Miktar: Unit costs typically decrease for larger batch sizes due to amortization of setup costs and potential optimization of build layouts (though the effect may be less pronounced for very large parts limited to one per build). Wholesale inquiries for larger volumes may receive preferential pricing.
- Kurşun zamanı: Expedited requests requiring priority scheduling or overtime will usually incur premium charges.
Typical Lead Times:
Lead times for aerospace-grade 3D printed rocket nozzles are highly variable but generally range from several weeks to several months, depending on complexity, size, material availability, required post-processing, and the provider’s backlog.
- Baskı: Typically takes several days to over a week for large/complex nozzles.
- Queue Time: Waiting for machine availability can add days or weeks.
- İşlem sonrası:
- Stress Relief/Build Plate Removal: 1-3 days
- HIP: Often batched, can add 1-2 weeks (including scheduling and cycle time).
- Heat Treatment (Solution/Aging): Several days, depending on the specific cycles required.
- CNC Machining: Highly variable, from days to weeks, depending on complexity and shop load.
- NDT & Inspection: Days to over a week, depending on the methods and required reporting.
- Shipping: Variable based on location.
Factors Influencing Lead Time:
- Part complexity and size (longer print and machining times).
- Availability of qualified powder.
- Machine availability and scheduling queue.
- Complexity and scheduling of post-processing steps (especially HIP and complex machining).
- Need for iterative NDT or rework.
- Current workload and capacity of the service provider and any external vendors.
Cost vs. Traditional Methods:
Direct part-for-part cost comparison can be misleading. While the AM part cost might sometimes be higher than a traditionally manufactured equivalent (especially for simpler designs), the total value proposition often favors AM due to:
- Azaltılmış Geliştirme Süresi: Faster iterations save significant program costs.
- Geliştirilmiş Performans: Higher efficiency through better cooling can translate to mission benefits.
- Weight Savings: Reduced launch costs or increased payload capacity.
- Parça Konsolidasyonu: Lower assembly costs and improved reliability.
- Reduced Tooling Costs: Eliminates expensive molds, dies, or fixtures.
Engineers and procurement managers should perform a total cost of ownership analysis, considering these broader system-level benefits when evaluating the investment in 3D printed rocket nozzles. Partnering with a transparent service provider who can provide detailed quotes outlining these cost factors is essential for effective budgeting and decision-making.
Frequently Asked Questions (FAQ) about 3D Printed Rocket Nozzles
Here are answers to some common questions regarding the use of additive manufacturing for rocket nozzle production:
1. How does the performance (e.g., efficiency, lifetime) of a 3D printed rocket nozzle compare to a traditionally manufactured one?
- When designed, manufactured, and post-processed correctly using appropriate materials like IN718, IN625, or Haynes 282, 3D printed rocket nozzles can meet or even exceed the performance of their traditional counterparts. The key advantage often lies in the ability to incorporate highly optimized conformal cooling channels via AM. This enhanced cooling allows engines to potentially operate at higher temperatures and pressures, leading to increased specific impulse (Isp) or efficiency. Furthermore, post-processing steps like HIP ensure material density and mechanical properties (strength, fatigue life) are comparable or superior to cast or wrought materials, contributing to a potentially longer operational lifetime, especially under demanding thermal cycling conditions. Performance equivalence or superiority, however, relies heavily on rigorous process control, DfAM, appropriate material selection, and thorough validation testing.
2. Is 3D printing rocket nozzles more expensive than traditional methods like casting and machining?
- The cost comparison is nuanced. For highly complex designs involving intricate internal cooling, significant part consolidation, or low production volumes (prototypes, small series), 3D printing can be more cost-effective overall. This is due to the elimination of tooling costs, reduced assembly labor, potential for weight savings (lowering launch costs), and significantly faster development cycles. For simpler nozzle designs produced in very high volumes, traditional methods might still hold a per-part cost advantage. However, a “total cost of ownership” perspective, including development speed, performance gains, and supply chain factors, often favors AM for advanced nozzle applications. The high cost of superalloy powders and extensive required post-processing (HIP, machining, NDT) are major cost drivers for AM nozzles.
3. How is material quality and certification handled for flight-critical 3D printed nozzles? How can we be sure the material properties are consistent and reliable?
- Ensuring material quality and consistency is paramount and involves a multi-faceted approach mandated by aerospace standards like AS9100:
- Powder Certification: Reputable suppliers (like Met3dp) provide batch-specific certificates of analysis for their powders, verifying chemical composition and physical characteristics (PSD, morphology, flowability). Incoming powder batches are often independently tested by the AM service provider.
- Process Validation: AM parameters (laser/beam power, speed, layer thickness, etc.) are rigorously developed and validated for each specific alloy and machine to ensure consistent melting and microstructure formation.
- Witness Coupons: Test specimens (coupons) are often printed alongside the actual parts on the same build plate. These coupons undergo destructive testing (tensile, fatigue, microstructure analysis) to verify that the build achieved the required mechanical properties for that specific print job.
- Tahribatsız Muayene (NDT): Finished parts undergo extensive NDT (like CT scanning) to ensure internal integrity and check for defects like porosity or cracks.
- Traceability: Strict documentation tracks the powder batch, machine parameters, operator, post-processing steps, and test results for each individual part, ensuring full traceability from raw material to the final certified component.
This combination of controlled input materials, validated processes, in-situ monitoring (where available), post-build testing, and comprehensive NDT provides the necessary confidence in the reliability and consistency of 3D printed nozzles for flight-critical applications.
Conclusion: Launching the Future with Additively Manufactured Rocket Nozzles
The journey of a rocket nozzle, from digital design to enduring the fury of launch, represents a pinnacle of engineering achievement. Additive manufacturing has fundamentally reshaped the possibilities for these critical components, moving beyond the constraints of traditional methods to unlock unprecedented levels of performance, efficiency, and design innovation. By enabling the creation of complex conformal cooling channels, consolidating multiple parts into monolithic structures, significantly reducing weight, and accelerating development cycles, metal 3D printing is not just an alternative manufacturing process – it is a key enabler for the next generation of space exploration and hypersonic flight.
The successful implementation of AM for rocket nozzles hinges on the synergy between advanced design techniques (DfAM), high-performance materials like the nickel superalloys IN718, IN625, and Haynes 282, and meticulously controlled manufacturing processes. The ability to precisely tailor thermal management systems within the nozzle structure allows engines to push performance boundaries, while weight savings contribute directly to mission capability. Challenges remain, particularly around managing residual stress, ensuring material integrity, and refining post-processing workflows, but the industry is rapidly maturing, driven by rigorous quality standards and continuous innovation.
Choosing the right partners is paramount in this demanding field. Collaborating with expert AM service providers and material specialists, such as Met3dp, who possess certified quality systems (AS9100), deep expertise in high-temperature alloys, advanced printing technologies like SEBM, and comprehensive katkı üretim çözümleri, is crucial for navigating the complexities and ensuring the production of reliable, flight-worthy hardware.
As aerospace continues to strive for faster, cheaper, and more capable access to space and beyond, 3D printed rocket nozzles stand as a testament to the power of additive manufacturing. They represent a significant leap forward, promising more efficient propulsion systems, faster innovation, and ultimately, helping humanity launch further into the future.
Paylaş
MET3DP Technology Co, LTD, merkezi Qingdao, Çin'de bulunan lider bir katmanlı üretim çözümleri sağlayıcısıdır. Şirketimiz, endüstriyel uygulamalar için 3D baskı ekipmanları ve yüksek performanslı metal tozları konusunda uzmanlaşmıştır.
İşletmeniz için en iyi fiyatı ve özelleştirilmiş Çözümü almak için sorgulayın!
İlgili Makaleler
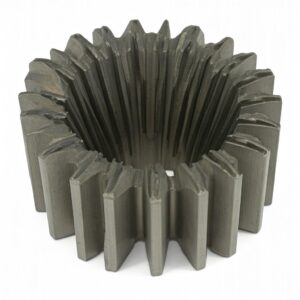
Yüksek Performanslı Nozul Kanat Segmentleri: Metal 3D Baskı ile Türbin Verimliliğinde Devrim
Daha Fazla Oku "Met3DP Hakkında
Son Güncelleme
Bizim Ürünümüz
BİZE ULAŞIN
Herhangi bir sorunuz var mı? Bize şimdi mesaj gönderin! Mesajınızı aldıktan sonra tüm ekibimizle talebinize hizmet edeceğiz.
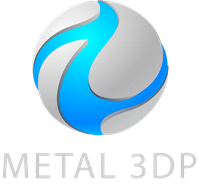
3D Baskı ve Katmanlı Üretim için Metal Tozları