3D Yazıcı Alüminyum Tozu
İçindekiler
3d yazıcı alüminyum tozu havacılık, otomotiv ve genel endüstriyel pazarlarda toz yataklı füzyon katkılı üretim için temel bir metal hammaddesi olarak hizmet vermektedir. Bu kılavuzda alüminyum kaliteleri, toz özellikleri, baskı süreci hususları, sinterleme yöntemleri, mekanik özellikler, işlem sonrası, uygulanabilir bileşenler ve lazer toz yataklı 3D baskıda alüminyum tozundan yararlanmaya ilişkin daha fazlası incelenmektedir.
3D Yazıcı Alüminyum Tozu Genel Bakış
Alüminyumun yüksek mukavemet/ağırlık oranı, korozyon direnci, termal özellikleri ve mekanik özellikleri onu yaygın olarak talep edilen bir mühendislik malzemesi haline getirmektedir. Külçenin atomize toz form faktörlerine dönüştürülmesi, eklemeli üretime olanak tanıyarak kilidi açar:
- Hafifletme - Araçlarda ve uçaklarda yakıt tasarrufu için azaltılmış bileşen kütlesi
- Parça Konsolidasyonu - Etkileşimli bileşenleri bir araya getiren basılı çok işlevli düzenekler
- Özel Alaşımlar - Basılı bölgeleri konuma göre seçici olarak güçlendiren kimyayı uyarlayın
- Toplu Özelleştirme - Dijital envanterler ve baskı otomasyonu yüksek ürün karışımlarını mümkün kılıyor
Uygun alüminyum alaşım kalitelerinin seçilmesi ve ilgili lazer baskı süreci parametrelerinin ayarlanması, kaliteli toz hammaddeleri aracılığıyla işleme kusurlarını azaltırken katmanlı üretim avantajlarından yararlanılmasını sağlar.
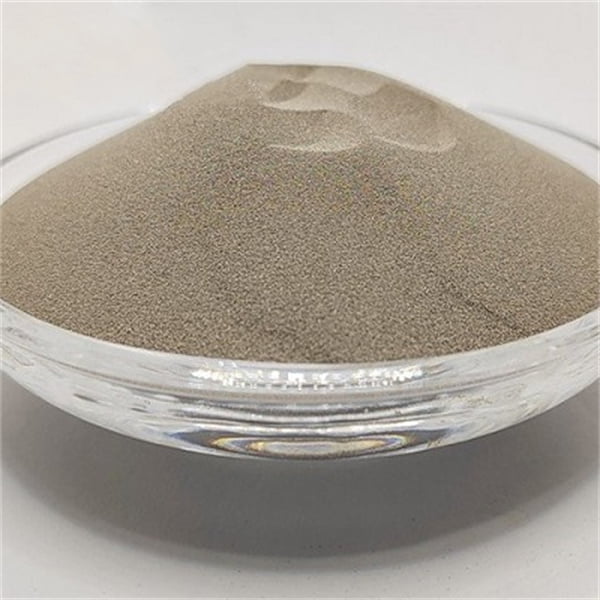
3d yazıcı alüminyum tozu Çeşitleri ve Bileşimleri
Alaşım | Açıklama | 3D Baskı için Faydalar | Tipik Uygulamalar |
---|---|---|---|
AlSi10Mg (Alüminyum Silisyum Magnezyum) | Bu, 3D baskı için en yaygın kullanılan alüminyum alaşımlarından biridir. Birincil alaşım elementi olarak silikon (Si) (yaklaşık 9-11%) ve daha fazla güçlendirme için magnezyum (Mg) (0,25-0,45%) içerir. | Mükemmel dökülebilirlik, 3D baskı sürecine iyi uyum sağlar. İyi bir mukavemet, süneklik ve korozyon direnci dengesi. Sonradan işleme veya geleneksel olarak imal edilen bileşenlerle entegrasyon için nispeten iyi kaynaklanabilirlik sunar. | Otomotiv bileşenleri (braketler, motor bileşenleri) Denizcilik bileşenleri (pervaneler, muhafazalar) İşlenebilirlik, mukavemet ve korozyon direnci dengesi gerektiren genel amaçlı parçalar. |
AlSi7Mg (Alüminyum Silisyum Magnezyum) | AlSi10Mg'ye çok benzer ancak silikon içeriği biraz daha düşüktür (yaklaşık 7%). | AlSi10Mg'ye benzer özelliklerin iyi bir dengesini sunar. Biraz daha düşük silikon içeriği nedeniyle ağırlığın en aza indirilmesinin öncelikli olduğu uygulamalar için tercih edilebilir. | Havacılık ve uzay bileşenleri (hafif yapılar) İyi bir güç/ağırlık oranı gerektiren fonksiyonel prototipler. |
Al-5%Si (Alüminyum 5% Silikon) | Bu alüminyum alaşımı, AlSi10Mg ve AlSi7Mg ile karşılaştırıldığında daha düşük bir silikon içeriği (yaklaşık 5%) içerir. | Daha yüksek silisyum içerikli alaşımlara kıyasla gelişmiş süneklik ve işlenebilirlik sunar. Daha fazla şekillendirilebilirlik veya işleme sonrası gerektiren uygulamalar için uygun olabilir. | Baralar ve elektrik bileşenleri İyi termal iletkenlik gerektiren ısı alıcıları. |
AlSiCuMg (Alüminyum Silisyum Bakır Magnezyum) | Bu alaşım, ilave güçlendirme için silikon ve magnezyumun yanı sıra bakır (Cu) içerir. | Standart AlSi alaşımlarına kıyasla daha yüksek mukavemet sunar. Yüksek sıcaklıklarda iyi mekanik özellikler gerektiren uygulamalar için uygun olabilir. | Yapısal bileşenler Havacılık ve uzay parçaları (iniş takımı bileşenleri). |
AlMnSi (Alüminyum Manganez Silisyum) | Bu alaşım, silikonun yanı sıra manganezi (Mn) birincil güçlendirme elementi olarak kullanır. | İyi mukavemet ve aşınma direnci sunar. Yüksek aşınma direnci veya aşındırıcı ortamlar gerektiren uygulamalar için uygun olabilir. | Dişliler, zincir dişlileri ve aşınma plakaları. |
Alüminyum-Zirkonyum Alaşımları (Al-Zr) | Bu alaşımlar, gelişmiş yüksek sıcaklık performansı için zirkonyum (Zr) içerir. | Yüksek sıcaklıklarda mükemmel mukavemet ve sürünme direnci sunar. Yüksek çalışma sıcaklıkları gerektiren uygulamalar için uygundur. | Motor bileşenleri (pistonlar, silindir kapakları) Isı eşanjörleri |
Alüminyum Tozu Üretim Yöntemleri ve Özellikleri
Yöntem | Açıklama | Alüminyum Tozu Özellikleri Üzerindeki Etkisi |
---|---|---|
Atomizasyon | Bu, 3D baskı için alüminyum tozu üretmek için en yaygın kullanılan yöntemdir. Erimiş alüminyum, yüksek basınçlı bir gaz (argon gibi inert gaz) veya sıvı (su) akışı kullanılarak ince damlacıklar halinde parçalanır. Damlacıklar, atomize edici ortama maruz kaldığında hızla küresel parçacıklar olarak katılaşır. | Partikül Boyutu ve Dağılımı: Atomizasyon, basılabilirlik ve nihai parça özellikleri için çok önemli olan partikül boyutu ve dağılımı üzerinde iyi bir kontrol sunar. Daha ince tozlar genellikle paketleme yoğunluğunu artırır, ancak akışkanlık zorluklarına yol açabilir. |
Gaz Atomizasyonu: | Erimiş metal akışını parçalamak için inert gaz (tipik olarak argon) kullanan bir atomizasyon çeşididir. Su atomizasyonuna kıyasla daha temiz ve daha kontrollü bir ortam sunar. | Toz Saflığı: Gaz atomizasyonu, atomizasyon prosesinde su kullanımıyla ilişkili kontaminasyon risklerini en aza indirerek potansiyel olarak daha yüksek toz saflığı sağlar. |
Su Atomizasyonu: | Yüksek basınçlı su jetinin erimiş alüminyum akışını bozduğu uygun maliyetli bir yöntem. | Parçacık Morfolojisi: Su atomizasyonu, su ile etkileşim sırasında katılaşma süreci nedeniyle gaz atomizasyonuna kıyasla biraz daha az küresel partiküllerle sonuçlanabilir. |
Hızlı Katılaşma | Eriyik Eğirme ve Hızlı Katılaştırma gibi gelişmekte olan teknikler, ince, amorf (kristal olmayan) bir metalik yapı oluşturmak için erimiş alüminyumun hızlı bir şekilde söndürülmesini içerir. Bu malzeme daha sonra ezilerek toz haline getirilir. | Benzersiz Mikroyapı: Hızlı katılaştırma, benzersiz mikro yapılara sahip tozlar oluşturabilir ve potansiyel olarak nihai basılı parçada gelişmiş mekanik özelliklere yol açabilir. Bununla birlikte, bu tür tozların basılabilirlik özelliklerinin daha fazla geliştirilmesi gerekebilir. |
Toz Özellikleri | Açıklama | 3D Baskıdaki Önemi |
---|---|---|
Partikül Boyutu ve Dağılımı | Daha önce de belirtildiği gibi, partikül boyutu ve dağılımı, 3D baskılı parçanın hem basılabilirliğini hem de nihai özelliklerini önemli ölçüde etkiler. Daha ince tozlar daha iyi paketleme yoğunluğu sunar ancak baskı sırasında akışkanlık sorunlarına yol açabilir. Dar bir partikül boyutu dağılımı, tutarlı bir paketleme sağlar ve basılı parça içindeki boşlukları en aza indirir. | Yazdırılabilirlik: Toz akışkanlığı ve paketleme yoğunluğu, iyi kalitede basılı parçalar elde etmek için çok önemlidir. Mekanik Özellikler: Parçacık boyutu ve dağılımı, 3D baskılı bileşenin nihai yoğunluğunu ve gücünü etkileyebilir. |
Parçacık Morfolojisi | İdeal olarak, 3D baskı için alüminyum tozu küresel veya küresele yakın bir morfolojiye sahip olmalıdır. Küresel partiküller daha kolay akar, paketleme yoğunluğunu artırır ve basılı parça içindeki boşlukları en aza indirir. Düzensiz şekilli partiküller akışkanlığı engelleyebilir ve potansiyel olarak kusurlara yol açabilir. | Akışkanlık: İyi akışkanlık, 3D baskı işlemi sırasında homojen toz dağılımı için gereklidir. |
Görünür ve Dokunma Yoğunluğu | Bu özellikler, farklı koşullar altında tozun yığın yoğunluğunu temsil eder. Görünür Yoğunluk: Bu, partiküller arasındaki boşluklar dikkate alındığında, tozun hareketsiz haldeki yoğunluğunu ifade eder. Musluk Yoğunluğu: Bu, standartlaştırılmış bir kılavuz çekme işlemiyle elde edilen daha yoğun bir durumu yansıtmaktadır. | Malzeme Kullanımı: Nihai 3D baskılı parçada verimli malzeme kullanımı ve iyi boyutsal doğruluk için genellikle daha yüksek kademe yoğunluğu istenir. |
Akışkanlık | Bu, tozun yerçekimi veya uygulanan kuvvetler altında akma kolaylığını ifade eder. İyi akışkanlık, 3D baskı işlemi sırasında homojen toz dağılımı için gereklidir. Akışkanlığı zayıf olan tozlar, paketleme yoğunluğunda tutarsızlıklara ve nihai parçada potansiyel kusurlara yol açabilir. | Baskı Kalitesi: Tutarlı akışkanlık, baskı sırasında düzgün toz birikimi sağlayarak katman yapışma sorunları veya tutarsızlık riskini en aza indirir. |
Alüminyum Baskı Tozları için Spesifikasyon Standartları
Standart Gövde | Standart | Açıklama | Alüminyum Baskı Tozlarında Önem |
---|---|---|---|
ASTM Uluslararası (ASTM) | ASTM B299 - Elektronik Sayım ile Metallerin ve İlgili Malzemelerin Parçacık Boyutunun Ölçümü için Standart Test Yöntemi | Bu standart, elektronik sayım teknikleri kullanılarak metal tozlarının partikül boyutu dağılımını ölçmek için bir yöntemi ana hatlarıyla belirtir. | Basılabilirlik ve nihai parça özellikleri için kritik bir faktör olan alüminyum tozlarının partikül boyutu dağılımını karakterize etmek için standartlaştırılmış bir yaklaşım sağlar. |
ASTM B822 - Katmanlı Üretim için Gaz Atomize Dövme Alüminyum Tozları için Standart Şartname | Bu standart, katkılı üretimde kullanılan gaz atomize alüminyum tozlarının kimyasal bileşimi, parçacık boyutu dağılımı, akışkanlığı ve görünür yoğunluğu için özel gereksinimleri tanımlar. | 3D baskıda yaygın olarak kullanılan gaz atomize alüminyum tozları için temel bir kalite ve performans seviyesi sağlar. Tutarlı özellikler, baskı sırasında öngörülebilir davranışa ve güvenilir parça kalitesine katkıda bulunur. | |
ASTM F3054 - Metal Katmanlı Üretim Hammaddesi için Standart Şartname | Bu daha geniş kapsamlı standart, alüminyum da dahil olmak üzere eklemeli üretimde kullanılan metal tozları için gereklilikleri belirlemeye yönelik bir çerçeve sağlar. Kimyasal bileşim, parçacık boyutu dağılımı, akışkanlık ve safsızlık seviyeleri gibi hususları kapsar. | Katmanlı üretimle ilgili alüminyum tozu özelliklerini belirlemek için kapsamlı bir yaklaşım sunar. Toz üreticileri, 3D baskı ekipmanı sağlayıcıları ve son kullanıcılar arasındaki iletişimi standartlaştırır. | |
Uluslararası Standardizasyon Örgütü (ISO) | ISO 14644 - Temiz odalar ve ilgili kontrollü ortamlar | Alüminyum tozlarına özel olmamakla birlikte, bu ISO standardı toz üretimi ve kullanımında kullanılan temiz oda ortamları için yönergeler belirler. | Yazdırılabilirliği ve nihai parça kalitesini etkileyebilen alüminyum tozu ile ilişkili kontaminasyon risklerini en aza indirir. Toz saflığını korumak için temiz oda uygulamaları çok önemlidir. |
ISO 3262-1 - Soğuk haddelenmiş kaplanmamış şerit - Bölüm 1: Terimlerin tanımları, teslimat koşulları, toleranslar | Bu standart, alüminyum şeritlere odaklanmış olsa da, alüminyum tozları için de geçerli olan görünür yoğunluk ve kademe yoğunluğu gibi ilgili özellikler için tanımlar sağlar. | Toz yoğunluğu özellikleri için ortak bir terminoloji oluşturarak alüminyum baskı endüstrisinde iletişim ve veri alışverişini kolaylaştırır. |
Alüminyum Tozları için 3D Baskı Sürecinde Dikkat Edilmesi Gerekenler
Faktör | Açıklama | Önem |
---|---|---|
Toz Yatak Füzyon (PBF) Teknikleri | Çeşitli 3D baskı teknolojileri alüminyum tozlarını kullanabilirken, Lazer Toz Yatağı Füzyonu (LPBF) ve Elektron Işını Eritme (EBM) alüminyum baskı için en yaygın PBF teknikleridir. LPBF: İstenen 3D parçayı oluşturmak için alüminyum toz parçacıklarını katman katman seçici olarak eritmek ve kaynaştırmak için yüksek güçlü bir lazer kullanır. EBM: Alüminyum tozunu eritmek için odaklanmış bir elektron ışını kullanır. EBM, LPBF'ye kıyasla daha derin eriyik penetrasyonu sunar. | PBF tekniğinin seçimi (LPBF veya EBM), enerji kaynağı ve ısıtma mekanizmalarındaki farklılıklar nedeniyle elde edilebilir parça boyutu, yüzey kalitesi ve mekanik özellikler gibi faktörleri etkileyebilir. |
Lazer/Elektron Işını Parametreleri | PBF'de lazerin (veya elektron ışınının) gücü, tarama hızı ve odağı, alüminyum tozunun erime davranışını ve nihai parça özelliklerini önemli ölçüde etkiler. | Bu parametrelerin optimize edilmesi, uygun erime, yeterli katman bağlanması ve basılı parça içindeki artık gerilmelerin en aza indirilmesi için çok önemlidir. |
Ön ısıtma | Baskıdan önce alüminyum toz yatağının önceden ısıtılması, toz akışkanlığını artırabilir ve nihai parçada çatlama riskini azaltabilir. | Ön ısıtma, daha kalın kesitler veya yüksek en-boy oranlarına sahip parçalar için özellikle faydalı olabilir ve baskı sırasında daha düzgün termal dağılımı teşvik eder. |
Destek Yapıları | PBF teknikleri kullanılarak basılan alüminyum parçalar, yüksek sıcaklıklar nedeniyle baskı işlemi sırasında bükülmeyi veya sarkmayı önlemek için genellikle destek yapılarına ihtiyaç duyar. Bu destekler tipik olarak aynı alüminyum tozundan yapılır ve daha sonra işlem sonrası adımlarla çıkarılır. | Destek yapılarının dikkatli bir şekilde tasarlanması ve yerleştirilmesi, baskı sırasında parça bütünlüğünü sağlamak ve desteğin çıkarılması sırasındaki zorlukları en aza indirmek için gereklidir. |
İşlem Sonrası | PBF kullanılarak basılan alüminyum parçalar, aşağıdakiler gibi çeşitli işlem sonrası adımlardan geçebilir: Sıcak İzostatik Presleme (HIP): Basılı parça içindeki iç gözenekliliği ortadan kaldırmaya yardımcı olan ve mekanik özellikleri iyileştiren yüksek basınçlı, yüksek sıcaklıkta bir işlem. Isıl İşlem: Kontrollü ısıtma döngüleri, mukavemet veya süneklik gibi belirli mekanik özellikleri daha da geliştirmek için kullanılabilir. İşleme: Hassas boyut toleransları veya yüzey kalitesi elde etmek için. | İşlem sonrası işlemler, 3D baskılı alüminyum parçanın nihai performansını ve estetiğini önemli ölçüde etkileyebilir. |
Alüminyum Toz Baskı Mekanik Özellikleri
Mülkiyet | Açıklama | İşlevsellik Üzerindeki Etkisi | Yaygın Alaşımlar |
---|---|---|---|
Çekme Dayanımı (MPa) | Basılı bir parçanın ayrılmadan önce dayanabileceği maksimum gerilim. | Parçanın yük taşıma kapasitesini belirler. Daha yüksek gerilme mukavemeti, daha yüksek gerilimli uygulamalarda kullanıma olanak tanır. | AlSi10Mg (410-460 MPa), 6061 (200-310 MPa), 7075 (460-570 MPa) |
Akma Dayanımı (MPa) | Basılı bir parçanın plastik olarak deforme olmaya başladığı gerilim. | Parçanın yük altında kalıcı olarak büküleceği noktayı gösterir. Daha yüksek akma dayanımı, stres altında elastik davranışa izin verir. | AlSi10Mg (245-270 MPa), 6061 (130-200 MPa), 7075 (320-450 MPa) |
Kopma Uzaması (%) | Basılı bir parçanın kırılmadan önce esneme miktarı. | Parçanın sünekliğini ve kırılmadan önce enerjiyi absorbe etme kabiliyetini etkiler. Daha yüksek uzama daha fazla esnekliği gösterir. | AlSi10Mg (5-9%), 6061 (12-35%), 7075 (6-14%) |
Yorulma Dayanımı (MPa) | Basılı bir parçanın belirli sayıda yükleme döngüsü için dayanabileceği maksimum gerilim. | Tekrarlanan gerilimlere maruz kalan parçalar için çok önemlidir. Daha yüksek yorulma mukavemeti daha uzun hizmet ömrü sağlar. | Sınırlı veri mevcut, tipik olarak dökme muadillerinden daha düşük |
Yoğunluk (g/cm³) | Basılı parçanın birim hacmi başına kütle. | Ağırlığı etkiler ve uygulamaları etkiler. Alüminyum doğal hafiflik özellikleri sunar. | AlSi10Mg (2.67), 6061 (2.70), 7075 (2.81) |
Elastisite Modülü (GPa) | Basılı malzemenin sertliği, yük altında ne kadar deforme olduğunu gösterir. | Parçanın sertliğini ve bükülmeye karşı koyma kabiliyetini belirler. Daha yüksek modül daha sert bir malzemeyi gösterir. | AlSi10Mg (70-75), 6061 (68-70), 7075 (71-78) |
Sertlik (HV) | Basılı malzemenin yüzey girintisine karşı direnci. | Aşınma direncini ve çizilme hassasiyetini etkiler. Daha yüksek sertlik aşınmaya karşı daha iyi direnç gösterir. | AlSi10Mg (100-130), 6061 (90-130), 7075 (150-180) |
Gözeneklilik (%) | Yazdırılan parça içindeki boş alan miktarı. | Mekanik mukavemeti ve yorulma performansını etkileyebilir. Daha düşük gözeneklilik genellikle arzu edilir. | Baskı işlemine ve parametrelere bağlı olarak değişir, tipik olarak 0,1-5% |
Anizotropi | Baskı yönüne bağlı olarak mekanik özelliklerin değişimi. | Baskı sürecinin katman katman doğası nedeniyle oluşabilir. Dikkatli tasarım ve işlem sonrası anizotropiyi en aza indirebilir. | Belirli alaşımlarda ve baskı işlemlerinde daha belirgin |
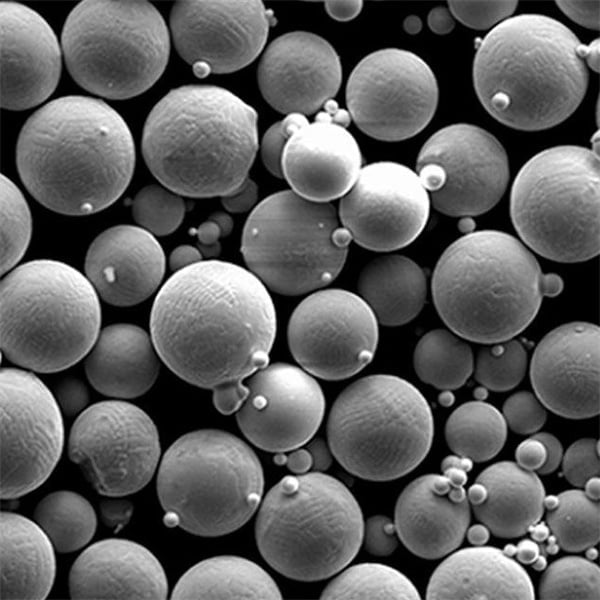
Alüminyum Baskılı Parçalar için İşlem Sonrası Yöntemler
Süreç | Açıklama | Avantajlar | Dezavantajlar | Uygulamalar |
---|---|---|---|---|
Destek Kaldırma | Bu ilk adım, baskı sırasında parçayı havada tutan geçici yapıları ortadan kaldırır. Alüminyum baskı sürecine bağlı olarak, yöntemler şunları içerir: Tel EDM (Elektrik Deşarjlı İşleme): İnce bir tel, elektrik kıvılcımlarını kullanarak destekleri hassas bir şekilde keser ve termal bozulmayı en aza indirir. Şerit Testere: Basit geometriler için hızlı ve uygun maliyetli bir seçenektir, ancak pürüzlü kenarlar bırakabilir. Manuel Kaldırma: Hassas parçalar veya küçük destekler için, dikkatli bir şekilde çıkarmak üzere pense veya makas kullanılır. | Parça hasarını en aza indirir. Dahili özelliklere erişim sağlar. | Tel EDM karmaşık parçalar için yavaş olabilir. Şerit testereyle kesme işlemi ilave son işlem gerektirebilir. Karmaşık destekler için manuel kaldırma zaman alıcıdır. | Tüm alüminyum baskı işlemleri Özellikle iç kanalları veya karmaşık geometrileri olan parçalar için kritiktir. |
Yüzey İşlemleri | Alüminyum parçalar, baskının katman katman doğası nedeniyle pürüzlü bir dokuya sahip olabilir. Çeşitli teknikler farklı estetik ve işlevsel hedeflere ulaşır: Zımparalama/Patlatma: Aşındırıcı parçacıklar yüzeyi pürüzsüzleştirir, kum boyutu pürüzsüzlük seviyesini belirler. Vibrasyonlu Son İşlem: Parçalar, su bileşimli bir ortam yatağında yuvarlanarak düzgün bir mat yüzey oluşturur. Parlatma: Parlatma diskleri ve bileşikleri kullanmak yüksek parlaklıkta, yansıtıcı bir yüzey oluşturur. Kimyasal Frezeleme: Kontrollü bir kimyasal banyo, pürüzsüz bir yüzey ve hassas boyut kontrolü için malzemeyi temizler. | Estetiği ve parça uyumunu iyileştirir. Korozyon direncini artırır. Bazı yöntemler için iç gözenekliliği açığa çıkarabilir. | Büyük parçalar için zımparalama/kumlama yoğun emek gerektirebilir. Ortam kumlaması yüzey kirleticilerini ortaya çıkarabilir. Parlatma için yetenekli operatörler gerekir. Kimyasal frezeleme, pürüzsüz bir yüzey için ek işlem sonrası gerektirebilir. | Tüm alüminyum baskı işlemleri Hafif pürüzsüzleştirme veya diğer yöntemler için ön işlem olarak zımparalama/patlatma. Karmaşık parçalarda düzgün, mat bir finisaj için titreşimli finisaj. Görünür bileşenlerde yüksek parlaklıkta bir yüzey için parlatma. Yüksek hassasiyetli parçalar veya ağırlık azaltma gerektiren parçalar için kimyasal frezeleme. |
Isıl İşlem | Kontrollü ısıtma ve soğutma döngüleri alüminyumun mikro yapısını değiştirerek mekanik özelliklerini geliştirir: Çözelti Tavlama: Güçlendirici çökeltileri çözmek için parçayı ısıtır, ardından yumuşak, sünek bir durum için hızlı soğutma yapar. Yaşlanma Sertleşmesi: Çözelti tavlamasının ardından yüksek sıcaklıkta kontrollü yaşlandırma, güçlü ve sert bir mikroyapı oluşturur. | Mukavemeti, sertliği ve yorulma direncini artırır. Özellikleri belirli uygulamalara göre uyarlar. | Düzgün kontrol edilmezse parçaları deforme edebilir. Isıl işlemden sonra ek işleme gerektirebilir. | Tüm alüminyum alaşımları ısıl işleme tabi tutulamaz. Yüksek mukavemet/ağırlık oranı veya iyileştirilmiş yorulma ömrü gerektiren parçalar için kullanılır. |
Sıcak İzostatik Presleme (HIP) | Bu yüksek basınçlı, yüksek sıcaklıklı işlem, basılı parçadaki iç gözenekliliği ortadan kaldırır: Parça, yüksek sıcaklıkta inert gaz basıncına maruz bırakılarak boşlukların çökmesi sağlanır. | Parça yoğunluğunu ve mekanik özellikleri iyileştirir. Yorulma çatlağı oluşumunu azaltır. | Özel ekipman gerektiren pahalı bir süreç. Boyutsal değişikliklere neden olabilir. | Yüksek gerilimli uygulamalardaki veya sızdırmazlık gerektiren parçalar için kritiktir. Genellikle güvenlik açısından kritik bileşenler için kullanılır. |
Talaşlı İmalat | Hassas toleranslar ve özellikler elde etmek için CNC frezeleme ve delme gibi geleneksel işleme teknikleri kullanılabilir: Baskı ile kolayca elde edilemeyen delikler, dişler ve diğer özellikleri oluşturabilir. Boyutsal doğruluğu artırır. | İşlem süresini ve maliyetini artırır. Malzemeyi kaldırarak iç gözenekliliği açığa çıkarabilir. | Baskı kapasitesinin ötesinde dar toleranslar veya belirli özellikler gerektiren parçalar için. Genellikle diğer post-processing yöntemleriyle birlikte kullanılır. |
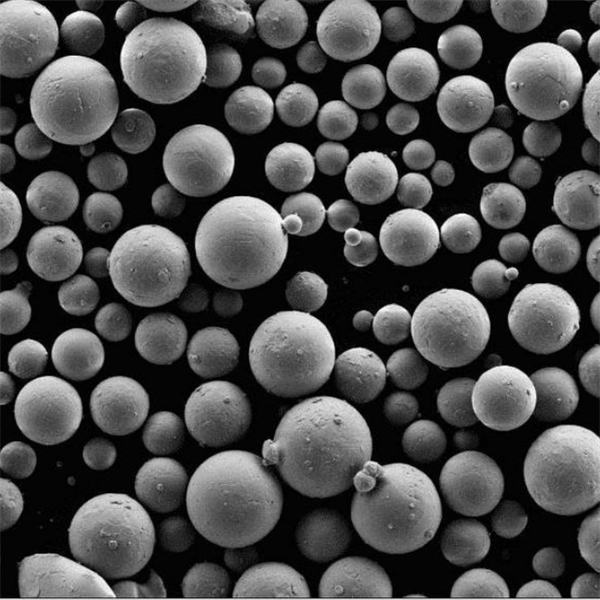
3D Yazıcı Alüminyum Toz Uygulamaları
Uygulama | Kaldıraçlı Mülkler | Avantajlar | Örnekler |
---|---|---|---|
Havacılık ve Uzay Bileşenleri | Yüksek mukavemet/ağırlık oranı, mükemmel yorulma direnci | Optimize edilmiş uçuş verimliliği ve yakıt ekonomisi için olağanüstü mekanik performansa sahip hafif yapılar | - Uçak kanatları ve gövdeleri - Motor bileşenleri - İniş takımı bileşenleri |
Otomotiv Parçaları | İyi işlenebilirlik, kaynaklanabilirlik ve dökülebilirlik | Yakıt verimliliği ve performans artışına katkıda bulunan karmaşık, hafif bileşenler | - Özel braketler ve bağlantılar - Yapısal bileşenler - Isı eşanjörleri |
Robotik ve Otomasyon | Özel ihtiyaçlar için uyarlanabilir mekanik özellikler | Hassas manipülasyon için yüksek mukavemet ve sertliğe sahip hafif robotik kollar ve tutucular | - Uç efektörler - Bağlantılar - Robotların yapısal bileşenleri |
Tıbbi İmplantlar | Biyouyumlu alaşımlar, uyarlanabilir yüzey özellikleri | Gelişmiş hasta sonuçları için iyi biyouyumluluk ve osseointegrasyona (kemik büyümesi) sahip özelleştirilebilir implantlar | - Diz ve kalça protezleri - Kraniyoplasti implantları - Diş implantları |
Tüketim Malları | Estetik, korozyon direnci | Benzersiz metalik görünüme ve dayanıklılığa sahip yüksek kaliteli, hafif son kullanım ürünleri | - Bisiklet çerçeveleri - Spor malzemeleri bileşenleri - Lüks saat bileşenleri |
Prototipleme ve Düşük Hacimli Üretim | Tasarım özgürlüğü, hızlı yineleme | Geleneksel kalıplara ihtiyaç duymadan karmaşık alüminyum parçaların fonksiyonel prototipleri ve düşük hacimli üretimi | - Tasarım doğrulaması için konsept modeller - Test için işlevsel prototipler - Sınırlı sayıda üretilen veya özelleştirilmiş ürünler |
Isı Eşanjörleri | Yüksek ısı iletkenliği | Çeşitli uygulamalarda termal yönetim için hafif, verimli ısı eşanjörleri | - Otomotiv radyatörleri ve ara soğutucular - Elektronik soğutma bileşenleri - Güç elektroniği için ısı alıcıları |
Kalıplar ve Aletler | Konformal soğutma kanalları | Enjeksiyon kalıplamada hızlı katılaşma ve düşük çevrim süreleri için konformal soğutma kanalları | - Enjeksiyon kalıp uçları - Döküm kalıpları - Katmanlı imalat takımları |
Alüminyum Baskı Tozları Sunan Tedarikçiler
Tedarikçi Adı | Ürün Açıklaması | Ek Bilgi | Web sitesi |
---|---|---|---|
MSE Supplies LLC | Katmanlı üretim (3D baskı) için çeşitli sınıflarda ve parçacık boyutlarında alüminyum bazlı metal tozları sunar. Popüler seçenekler şunları içerir: MSE PRO 6061: İyi mekanik özelliklere ve kaynaklanabilirliğe sahip genel amaçlı alüminyum alaşım tozu. MSE PRO AlSi10Mg: Havacılık ve otomotiv uygulamaları için ideal, iyi dökülebilirliğe sahip yüksek mukavemetli alüminyum alaşımlı toz. MSE PRO 2024: Uçak bileşenleri için uygun, yüksek mukavemet-ağırlık oranı ve yorulma direnci ile bilinen alüminyum alaşımlı toz. | Minimum sipariş miktarı geçerli olabilir. Talep üzerine partikül boyutunun özelleştirilmesini sağlar. Her bir toz için teknik veri sayfaları sağlar. | https://www.msesupplies.com/ |
Atlantik Ekipman Mühendisleri (AEE) | Dahil olmak üzere yüksek saflıkta alüminyum tozlarının lider tedarikçisi: Atomize alüminyum tozları: İyi akışkanlık ve paketleme yoğunluğu sunan çeşitli partikül morfolojilerinde mevcuttur. Alüminyum pullar ve granüller: Belirli uygulamalar için benzersiz yüzey özellikleri sağlayın. | Farklı baskı işlemlerine uygun geniş bir partikül boyutu yelpazesi sunar. Özel alüminyum tozu ihtiyaçları için özel çözümler sağlayabilir. Kapsamlı endüstri deneyimi ve sertifikalar. | https://micronmetals.com/product-category/high-purity-metal-powders-compounds/ |
Praxair Yüzey Teknolojileri (Astro Alloys Inc. aracılığıyla) | Distribütörü TruForm Katmanlı üretim uygulamaları için özel olarak tasarlanmış alüminyum tozları da dahil olmak üzere metal tozları. Optimum akış ve biriktirme için küresel morfolojiye sahip tozlar sunar. Çeşitli havacılık sınıfı alüminyum alaşımları mevcuttur. | Özelleştirme seçenekleri ile geniş ürün portföyü. DMLS ve SLM gibi farklı AM prosesleri için tasarlanmış tozlar. Metal tozu endüstrisinde köklü bir itibar. | https://www.astroalloys.com/ |
Eplus3D | Yüksek performanslı alüminyum alaşımlarına odaklanarak 3D baskı için alüminyum tozu konusunda uzmanlaşmıştır: AlSi7Mg ve AlSi10Mg: İyi mukavemetleri ve dökülebilirlikleri nedeniyle havacılık ve otomotiv endüstrileri için popüler seçenekler. | Optimum sonuçlar için uygulamaya özel tozlar sunar. Seçim kolaylığı için modernize edilmiş ürün yelpazesi. Gelişmiş alüminyum baskı tozlarının araştırma ve geliştirilmesine odaklanın. | https://www.eplus3d.com/products/aluminum-3d-printing-material/ |
Diğer Potansiyel Tedarikçiler | Farklı ürün grupları ve uzmanlık alanlarıyla alüminyum baskı tozları dağıtan başka şirketler de vardır. Örnekler şunları içerir: SLM Çözümleri Höganäs AB APEX Katmanlı Üretim | Belirli toz özellikleri ve hedef uygulamalar için ayrı ayrı tedarikçileri araştırın. Fiyatlandırma, minimum sipariş miktarı ve teknik destek gibi faktörleri göz önünde bulundurun. |
Alüminyum Tozu Fiyatlandırmasında Dikkat Edilmesi Gerekenler
Parametre | Fiyat Etkileri |
---|---|
Dağıtım Boyutu | Daha sıkı dağıtımlar maliyetleri artıran getirileri zorluyor |
Kalite Standartları | Sıkı kusur tarama testleri gerektiren havacılık ve uzay kaliteleri |
Sipariş Hacmi | Küçük ölçekli prototip projeler prim getiriyor |
Müşteri Özellikleri | Benzersiz yağ/nem hedefleri, ambalajlama fiyatlandırmayı etkiler |
Alaşım İlaveleri | Daha yüksek saflıktaki element karışımları yükleri iletir |
Tablo 7. Temel alüminyum emtia spot fiyatının 5-10 katına kadar alüminyum tozu fiyatlandırmasını etkileyen tedarik kanalı faktörleri
Büyük baskı projelerinden 12-18 ay önce hacim gereksinimlerini tahmin etmek, toplu iş ve kalifikasyon testi giderlerini en aza indirerek en büyük kaldıracı sunar.
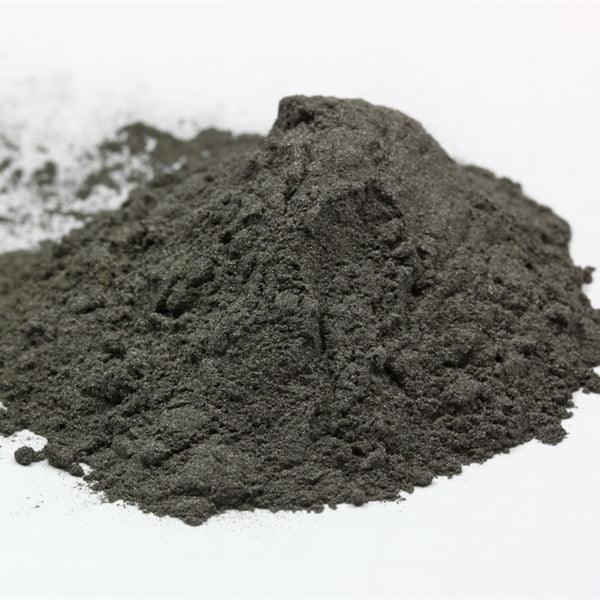
Sıkça Sorulan Sorular
S: Alüminyum tozunun yeniden kullanımı özelliklerini korur mu?
C: Evet, tozlar, yeniden kullanım karışımları zararlı hale gelmeden önce izlenmesi gereken sadece mütevazı oksijen ve nem toplama ile iyi bir şekilde yeniden işlenir.
S: Alüminyum baskı parçalarında gözeneklilik sorunlarına ne sebep olur?
C: Kötü toz depolama ve işleme veya eritme sırasında havalandırma eksikliğinden kaynaklanan sıkışmış gaz gözenekleri birleşerek mukavemeti azaltan kusurlara dönüşür.
S: Isıl işlem alüminyum baskılı bileşenler için faydalı mıdır?
C: Evet, uygun şekilde tasarlanmış ısıl işlem, sünekliği artıran ve kontrollü baskı katılaşma yollarına özgü ambulant mekanik özellikleri en üst düzeye çıkaran temperleri yeniden üretir.
S: Lazer toz yatağı füzyon katkısı için en uygun alüminyum alaşımı hangisidir?
C: APWorks tarafından patentli bir alüminyum, skandiyum, zirkonyum alaşımı olan Scalmalloy tozu, tamamen sonradan işlendiğinde eşsiz bir güç ve sıcaklık direnci kombinasyonu sağlar.
Paylaş
MET3DP Technology Co, LTD, merkezi Qingdao, Çin'de bulunan lider bir katmanlı üretim çözümleri sağlayıcısıdır. Şirketimiz, endüstriyel uygulamalar için 3D baskı ekipmanları ve yüksek performanslı metal tozları konusunda uzmanlaşmıştır.
İşletmeniz için en iyi fiyatı ve özelleştirilmiş Çözümü almak için sorgulayın!
İlgili Makaleler
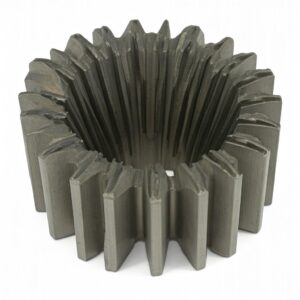
Yüksek Performanslı Nozul Kanat Segmentleri: Metal 3D Baskı ile Türbin Verimliliğinde Devrim
Daha Fazla Oku "Met3DP Hakkında
Son Güncelleme
Bizim Ürünümüz
BİZE ULAŞIN
Herhangi bir sorunuz var mı? Bize şimdi mesaj gönderin! Mesajınızı aldıktan sonra tüm ekibimizle talebinize hizmet edeceğiz.
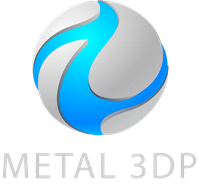
3D Baskı ve Katmanlı Üretim için Metal Tozları