High-Temperature Exhaust Manifolds via 3D Printing
İçindekiler
Introduction: The Critical Role of Exhaust Manifolds in High-Temperature Performance
Exhaust manifolds are unsung heroes in the powertrain ecosystem. Bolted directly to the engine’s cylinder head, their primary function is crucial yet challenging: collect scorching exhaust gases from multiple cylinders and funnel them into a single exhaust pipe. This process occurs under extreme conditions, involving exposure to temperatures that can easily exceed 800-1000°C (1472-1832°F) in high-performance applications, coupled with significant thermal cycling, vibration, and corrosive combustion byproducts.
Key Functions and Challenges:
- Gas Collection & Routing: Efficiently channels high-velocity, high-temperature gases.
- Termal Yönetim: Must withstand extreme heat without failing, warping, or cracking. Repeated heating and cooling cycles induce significant thermal stress.
- Basınç Muhafazası: Handles fluctuating exhaust gas pressures.
- Vibration Damping: Absorbs engine vibrations transmitted through the mounting points.
- Korozyon Direnci: Resists oxidation and chemical attack from exhaust gases.
- Flow Efficiency: The internal geometry directly impacts engine performance, backpressure, and scavenging effects.
Traditionally, exhaust manifolds are manufactured using casting (typically cast iron or stainless steel) or fabrication (welding bent tubes, often stainless steel). While effective for mass production and lower-performance applications, these methods face limitations when dealing with the demands of modern high-output engines, motorsport, or aerospace auxiliary power units (APUs). Geometric complexity for optimal flow is often constrained by casting mold limitations or the difficulty of fabricating intricate tube assemblies. Furthermore, achieving lightweight designs without compromising durability is a constant battle.
This is where the landscape is shifting. The pursuit of higher efficiency, reduced emissions, and enhanced performance, particularly in sectors demanding custom or low-volume solutions, necessitates exploring advanced manufacturing techniques. Metal 3D baskı, also known as additive manufacturing (AM), emerges as a powerful alternative, offering unprecedented design freedom and the ability to utilize high-performance superalloys specifically suited for extreme temperature environments. For engineers and procurement managers in demanding industries, understanding the potential of AM for components like exhaust manifolds is becoming increasingly vital for maintaining a competitive edge.
Applications: Where are High-Temperature 3D Printed Exhaust Manifolds Utilized?
The unique capabilities of metal additive manufacturing make it particularly suitable for producing high-temperature exhaust manifolds where performance, complex geometries, low volume, customization, or rapid development are key drivers. The ability to work with advanced superalloys pushes the boundaries of operational temperature and component longevity.
Key Industries and Use Cases:
- Motorsport & High-Performance Automotive:
- Optimized Flow Paths: AM allows for intricate internal geometries, smoothed bends, and precisely calculated runner lengths that maximize exhaust scavenging and minimize backpressure, directly translating to increased horsepower and torque.
- Hafifletme: Using superalloys and topology optimization, 3D printed manifolds can be significantly lighter than cast or fabricated counterparts, crucial for improving vehicle dynamics and fuel efficiency in racing.
- Rapid Prototyping & Iteration: Teams can quickly design, print, and test multiple manifold iterations to fine-tune engine performance, drastically reducing development cycles compared to traditional tooling methods.
- Özelleştirme: Tailor-made manifolds for specific engine builds, chassis constraints, or turbocharger placements become feasible and cost-effective, even for one-off vehicles or limited production runs. B2B suppliers specializing in performance parts leverage AM for bespoke customer solutions.
- Havacılık ve uzay:
- Auxiliary Power Units (APUs): APU exhausts operate at very high temperatures and demand exceptional reliability and low weight. AM enables complex, consolidated designs using certified aerospace superalloys like Inconel.
- İnsansız Hava Araçları (İHA'lar): Weight is paramount in UAVs. 3D printed manifolds offer significant weight savings for internal combustion engine exhausts used in larger drones.
- Component Consolidation: Multiple fabricated parts can often be redesigned and printed as a single, more robust component, reducing potential failure points (like welds) and simplifying assembly.
- Industrial Power Generation & Heavy Machinery:
- Specialized Engines: Exhaust manifolds for large stationary engines, generators, or specialized off-highway equipment often require robust materials and unique designs not suited for mass production tooling.
- Harsh Environments: Applications involving continuous high-temperature operation or exposure to corrosive industrial atmospheres benefit from the superior material properties offered by AM superalloys.
- Replacement Parts: Creating replacements for obsolete or difficult-to-source manifolds for legacy equipment becomes possible without needing original tooling. Distributors find AM valuable for fulfilling niche B2B part demands.
- Prototyping & Research:
- Engine Development: Researchers and engine developers use 3D printed manifolds to quickly test new concepts related to emissions control, thermal management, or acoustic tuning.
- Material Testing: Provides a platform for evaluating the performance of new high-temperature alloys in real-world engine conditions.
Market Demand Drivers:
Sürücü | Industries Primarily Affected | Benefit of 3D Baskı | Target Audience |
---|---|---|---|
Performans Geliştirme | Motorsport, High-Performance Auto | Optimized flow, lightweighting, rapid iteration | Engineers, Race Teams |
Ağırlık Azaltma | Aerospace, Motorsport | Topology optimization, material selection, part consolidation | Design Engineers |
Karmaşık Geometriler | All (esp. Motorsport, Aerospace) | Design freedom beyond casting/fabrication constraints | Design Engineers |
Hızlı Prototipleme | All (esp. Automotive, R&D) | Faster development cycles, reduced tooling costs | R&D Managers, Engineers |
Customization/Low Volume | Motorsport, Industrial, Replacement Parts | Cost-effective production without dedicated tooling | Procurement, MRO |
High-Temperature Alloys | Aerospace, Industrial, Performance Auto | Access to materials like IN625, IN718, Hastelloy X | Materials Engineers |
Parça Konsolidasyonu | Havacılık ve Uzay, Endüstriyel | Reduced part count, improved reliability, simpler assembly | Design & Mfg Engineers |
Sayfalara Aktar
The adoption of metal 3D printing for exhaust manifolds is driven by a clear need for solutions that push beyond the limitations of conventional manufacturing, particularly where extreme temperatures and performance are paramount.
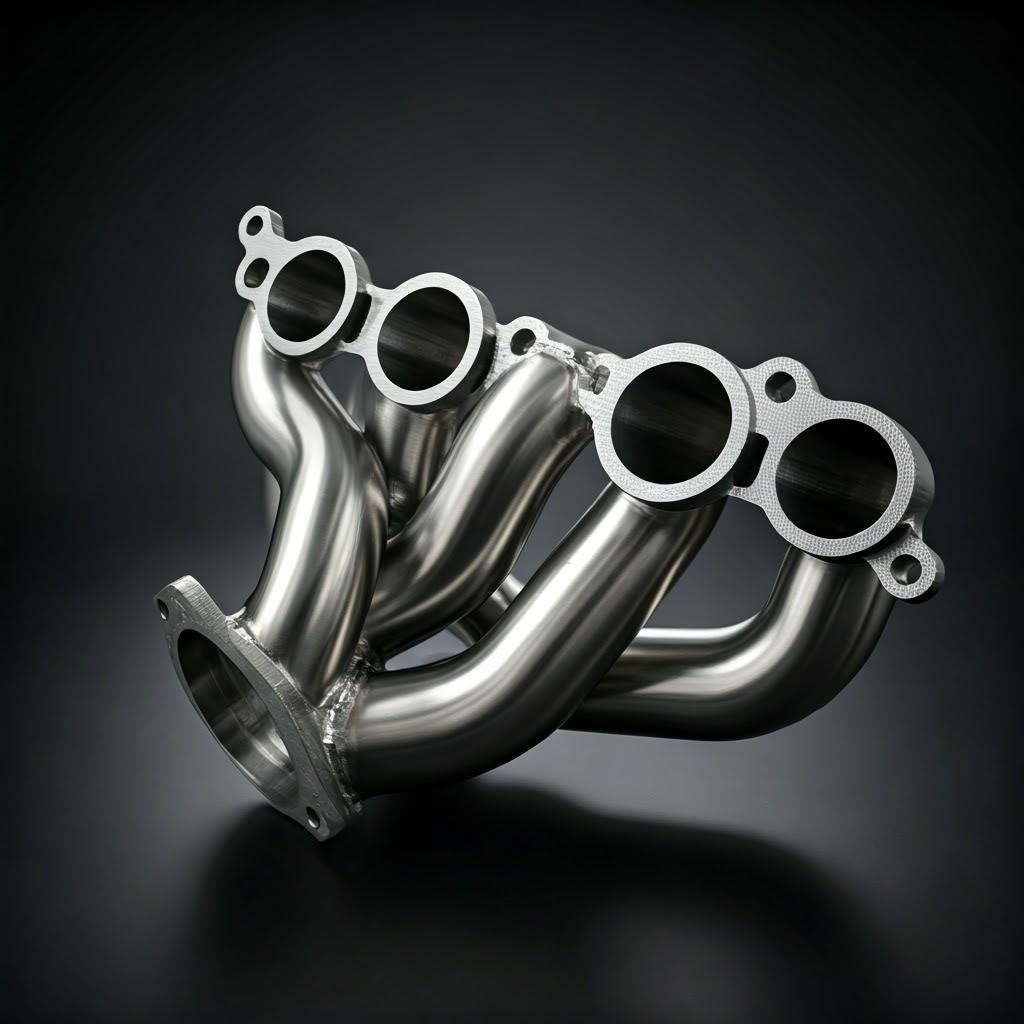
Why Metal 3D Printing for High-Temperature Exhaust Manifolds? Unlocking Performance Gains
While traditional manufacturing methods like casting and fabrication have served the industry well, metal additive manufacturing offers a compelling suite of advantages specifically beneficial for the design and production of high-temperature exhaust manifolds. These benefits address the inherent challenges of extreme heat, complex flow requirements, and the need for lightweight, durable components.
Key Advantages of Metal AM:
- Unmatched Design Freedom & Complexity:
- Meydan okumak: Traditional methods struggle with intricate internal channels, smooth, organic transitions, and complex collector designs needed for optimal exhaust flow and scavenging. Casting requires draft angles and core limitations, while fabrication involves complex tube bending and welding.
- AM Solution: Layer-by-layer construction allows for virtually unlimited geometric complexity. Engineers can design manifolds with:
- Optimized Runner Paths: Smooth, mathematically derived curves minimizing flow restriction.
- Integrated Features: Turbocharger flanges, wastegate ports, O2 sensor bungs, and mounting brackets can be printed as part of the manifold, eliminating welding and potential leak points.
- Internal Cooling Channels (Advanced): For extreme applications, internal channels for air or liquid cooling could potentially be integrated.
- Variable Wall Thickness: Material can be placed precisely where needed for strength, while non-critical areas can be thinned to save weight.
- Parça Konsolidasyonu:
- Meydan okumak: Fabricated manifolds often consist of multiple bent tubes, flanges, and collectors welded together. Each weld introduces residual stress, potential failure points, and added assembly time/cost.
- AM Solution: Multiple components can be redesigned and printed as a single, monolithic part. This reduces:
- Part count and assembly labor.
- Potential leak paths and failure points (welds).
- Overall weight and tolerance stack-up.
- Hafifletme:
- Meydan okumak: High-temperature capability often requires dense materials (like stainless steels or cast iron). Reducing weight without compromising strength or thermal resistance is difficult with traditional methods.
- AM Solution:
- Topology Optimization: Software can analyze stress loads and remove material from non-critical areas, creating organically shaped, lightweight structures impossible to cast or fabricate.
- İleri Malzemeler: While superalloys are dense, the design freedom allows for optimized structures that use less material overall compared to a bulkier traditional design achieving the same strength.
- Access to High-Performance Superalloys:
- Meydan okumak: While some high-performance alloys olabilmek be cast or fabricated, certain materials ideally suited for extreme heat and corrosion (like specific grades of Inconel or Hastelloy) can be difficult or very expensive to process traditionally. Welding dissimilar sections or achieving consistent properties in complex castings can be problematic.
- AM Solution: Powder Bed Fusion (PBF) techniques like Selective Laser Melting (SLM) or Electron Beam Melting (EBM) excel at processing high-performance superalloys. Leading providers like Met3dp specialize in developing and utilizing advanced metal powders, ensuring high-density, homogenous parts with excellent mechanical properties tailored for demanding thermal environments. Their expertise spans materials specifically chosen for applications like exhaust manifolds.
- Rapid Prototyping and Development:
- Meydan okumak: Creating tooling for casting or jigs for fabrication is time-consuming and expensive, especially for iterative design changes during development or prototyping.
- AM Solution: Designs can go directly from CAD model to physical part in days, not weeks or months. This allows for:
- Faster design validation and performance testing.
- Cost-effective exploration of multiple design variations.
- Reduced time-to-market for new engine platforms or performance upgrades.
- Cost-Effectiveness for Low Volumes & Customization:
- Meydan okumak: Tooling costs make traditional manufacturing prohibitively expensive for one-off parts, prototypes, or small production runs (e.g., motorsport, bespoke builds, replacement parts).
- AM Solution: AM is tool-less manufacturing. The cost per part is less dependent on volume, making it economically viable for:
- Custom manifolds tailored to specific vehicle or engine requirements.
- Small batch production for niche markets.
- On-demand manufacturing of spare parts for distributors and service centers.
Comparison Table: Traditional vs. Metal AM for Exhaust Manifolds
Özellik | Geleneksel Döküm | Geleneksel İmalat | Metal 3D Printing (PBF) |
---|---|---|---|
Tasarım Karmaşıklığı | Limited by molds, draft angles | Limited by tube bending/welding | High (complex internal channels, organic shapes) |
Parça Konsolidasyonu | Sınırlı | Low (many welded components) | High (can print monolithic parts) |
Hafifletme | Moderate (material removal limited) | Moderate (thin tubes possible) | High (topology optimization, optimized structures) |
Malzeme Seçenekleri | Good (Cast Iron, Stainless) | Good (Stainless, Titanium) | Excellent (Superalloys like IN625/718, Hastelloy X) |
Prototipleme Hızı | Slow (tooling required) | Moderate-to-Slow (jigs required) | Fast (tool-less) |
Low Volume Cost | High (due to tooling) | Moderate-to-High (labor intensive) | Moderate (ideal for low volumes) |
Lead Time (New Part) | Weeks/Months | Haftalar | Days/Weeks |
Optimal Flow | Orta düzeyde | İyi | Excellent (highly optimized designs possible) |
Sayfalara Aktar
By leveraging these advantages, metal 3D printing empowers engineers and manufacturers to create high-temperature exhaust manifolds that were previously impossible or impractical, unlocking new levels of performance, efficiency, and design innovation.
Recommended Materials for 3D Printing Exhaust Manifolds: IN625, IN718, Hastelloy X
The selection of the right material is paramount for the success of a 3D printed exhaust manifold, given the extreme operating conditions. The material must possess exceptional high-temperature strength, resistance to thermal fatigue, excellent corrosion and oxidation resistance, and good processability via additive manufacturing techniques like Powder Bed Fusion (PBF). Nickel-based superalloys are the primary candidates due to their proven performance in harsh environments. Among these, Inconel 625 (IN625), Inconel 718 (IN718), and Hastelloy X stand out as highly recommended choices.
Choosing a reputable powder supplier is as critical as selecting the right alloy. Companies like Met3dp, leveraging advanced powder production techniques like gas atomization and PREP (Plasma Rotating Electrode Process), ensure the availability of high-quality, spherical metal powders optimized for additive manufacturing. Onların product portfolio includes a range of superalloys suitable for demanding applications. High sphericity and good flowability, characteristics emphasized by Met3dp’s manufacturing process, are crucial for achieving densely packed powder beds and producing high-quality, defect-free printed parts.
1. Inconel 625 (IN625 / Alloy 625)
- Kompozisyon: Nickel-Chromium-Molybdenum-Niobium alloy (NiCrMoNb).
- Anahtar Özellikler:
- Excellent High-Temperature Strength: Maintains good tensile, creep, and rupture strength at temperatures up to ~815°C (1500°F), with useful properties extending even higher for short durations or lower stress applications.
- Üstün Korozyon Direnci: Highly resistant to a wide range of corrosive environments, including oxidation, carburization, and attack from exhaust gas condensates (acids). The high chromium and molybdenum content provide superb resistance to pitting and crevice corrosion.
- Superb Fabricability & Weldability: While less critical for monolithic AM parts, its inherent weldability translates to good processability in PBF systems, reducing susceptibility to cracking during printing and cooling.
- High Fatigue Strength: Resists failure under cyclic loading caused by engine vibration and thermal cycling.
- Why it Matters for Exhaust Manifolds: IN625 offers a fantastic balance of high-temperature strength, exceptional corrosion resistance (critical for dealing with acidic byproducts and atmospheric exposure), and robust performance under thermal cycling. It’s often considered a go-to material for demanding exhaust applications, including motorsport and aerospace components.
2. Inconel 718 (IN718 / Alloy 718)
- Kompozisyon: Nickel-Chromium alloy, precipitation-hardenable with Niobium and Molybdenum, plus additions of Iron, Titanium, and Aluminum (NiCrFeNbMoTiAl).
- Anahtar Özellikler:
- Exceptional Mechanical Strength: Offers significantly higher tensile and yield strength compared to IN625, especially at temperatures up to ~700°C (1300°F), due to its precipitation-hardening mechanism (gamma double prime phase).
- Good Creep-Rupture Strength: Maintains integrity under sustained load at high temperatures.
- İyi Korozyon Direnci: While generally very good, it can be slightly less resistant than IN625 in certain highly specific corrosive environments. Still excellent for most exhaust applications.
- Good Weldability/Processability: Readily processed using AM techniques, though post-print heat treatments (solution annealing and aging) are required to achieve its optimal high-strength properties.
- Why it Matters for Exhaust Manifolds: IN718 is chosen when maximum strength and creep resistance at very high temperatures (up to ~700°C) are the primary design drivers. Its superior strength-to-weight ratio compared to IN625 can be advantageous in weight-critical applications like aerospace and top-tier motorsport, provided the necessary heat treatment is performed.
3. Hastelloy X (Alloy X)
- Kompozisyon: Nickel-Chromium-Iron-Molybdenum alloy (NiCrFeMo).
- Anahtar Özellikler:
- Üstün Oksidasyon Direnci: Forms a tenacious, protective oxide scale, providing excellent resistance to oxidation at very high temperatures, potentially exceeding IN625 and IN718 in oxidizing atmospheres up to 1200°C (2200°F).
- Very Good High-Temperature Strength: Retains good strength at elevated temperatures, though typically not as high as age-hardened IN718 below ~700°C.
- Excellent Fabricability: Known for good forming and welding characteristics in traditional manufacturing, which translates well to AM processability.
- Resistance to Stress Corrosion Cracking: Performs well in environments where chloride stress corrosion cracking might be a concern.
- Why it Matters for Exhaust Manifolds: Hastelloy X is often selected for applications where resistance to oxidation in extreme temperature, gas turbine-like environments is the most critical factor, potentially surpassing the Inconel grades in purely oxidizing conditions. It’s a common choice for combustion zone components, afterburners, and industrial furnace parts, making it highly suitable for the hottest sections of some exhaust systems.
Material Selection Guide:
Özellik | IN625 | IN718 | Hastelloy X |
---|---|---|---|
Primary Strength | Balanced Strength & Corrosion Resistance | Highest Strength (up to ~700°C) | Best Oxidation Resistance (at highest temps) |
Max Use Temp (Strength) | ~815°C (1500°F) | ~700°C (1300°F) – Strength drops faster above | ~900°C+ (1650°F+), excels >1000°C oxidation |
Korozyon Direnci | Outstanding (Broad Spectrum) | Çok iyi | Very Good (Exceptional Oxidation) |
Requires Heat Treatment? | No (or simple stress relief) | Yes (Solution + Age Hardening essential) | No (or simple stress relief) |
Göreceli Maliyet | Yüksek | Yüksek | Yüksek |
Typical Application Focus | Motorsport, Marine, Chemical Processing | Aerospace, Gas Turbines, High-Strength Needs | Combustion Liners, Afterburners, Furnaces |
Sayfalara Aktar
Choosing the Right Powder and Process:
Selecting the appropriate superalloy is only part of the equation. The quality of the metal powder and the chosen 3D baskı yöntemi (typically SLM or DMLS for these alloys) are crucial.
- Toz Kalitesi: Parameters like particle size distribution (PSD), sphericity, flowability, and low oxygen/interstitial content directly impact the density, microstructure, and final mechanical properties of the printed part. Using powders from specialized suppliers like Met3dp, produced via controlled processes like VIGA (Vacuum Induction Gas Atomization) or PREP, ensures consistency and quality.
- Süreç Parametreleri: Optimized laser power, scan speed, layer thickness, and build chamber atmosphere control are essential to minimize defects like porosity or residual stress and achieve the desired material properties for the chosen alloy.
By carefully considering the specific operating conditions (temperature, atmosphere, stress) and leveraging the unique strengths of materials like IN625, IN718, and Hastelloy X, combined with high-quality metal powders and optimized AM processes, engineers can produce exhaust manifolds that deliver exceptional performance and durability in the most demanding applications.
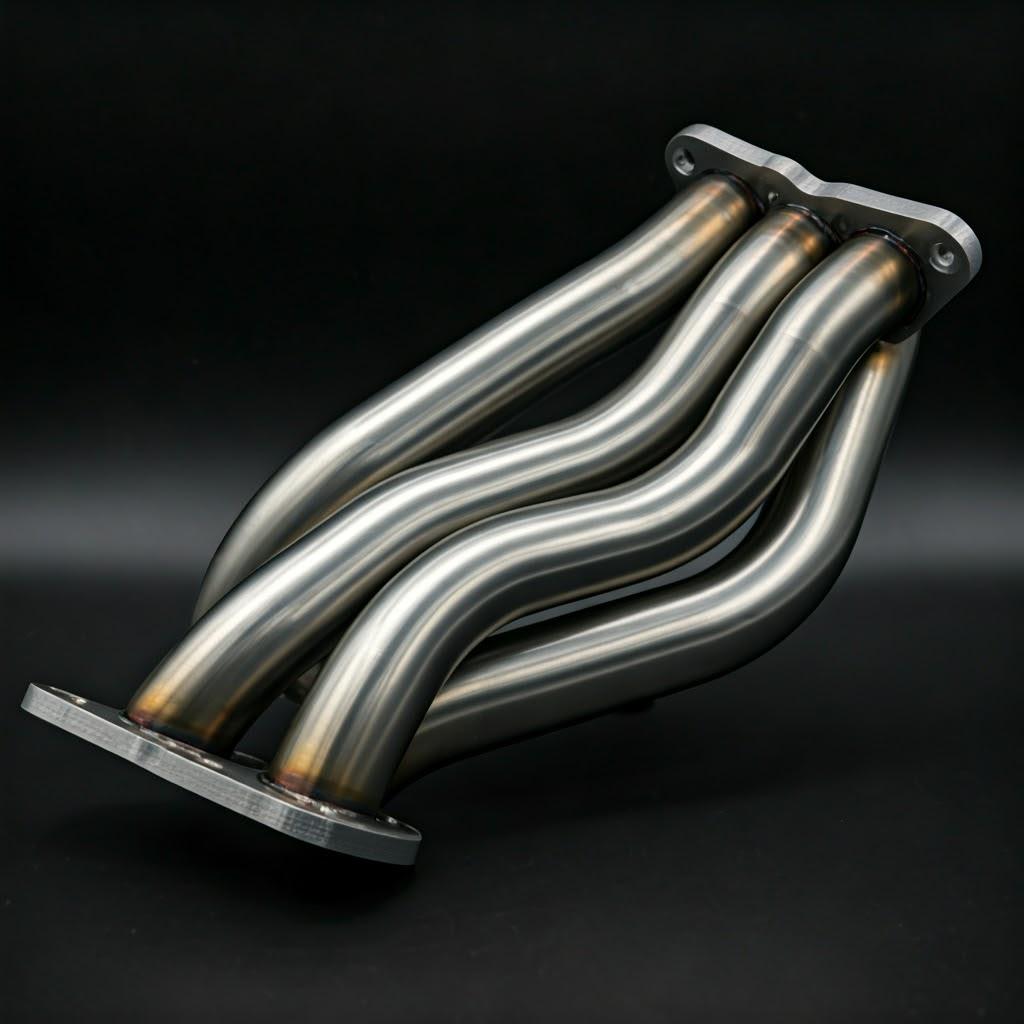
Design Considerations for Additive Manufacturing of Exhaust Manifolds
Transitioning from traditional manufacturing methods to metal additive manufacturing (AM) for exhaust manifolds requires a shift in design philosophy. Simply converting a cast or fabricated design for 3D printing rarely leverages the full potential of AM and can even introduce new challenges. Designing için Additive Manufacturing (DfAM) is crucial to maximize performance, minimize cost, and ensure successful printing.
Key DfAM Principles for Exhaust Manifolds:
- Flow Path Optimization:
- Goal: Minimize backpressure, maximize exhaust gas velocity and scavenging effects.
- AM Advantage: Create smooth, sweeping bends and complex collector geometries impossible with traditional methods.
- Düşünceler:
- Utilize Computational Fluid Dynamics (CFD) simulation early in the design phase to model gas flow and iterate on runner shapes, lengths, and convergence angles.
- Avoid sharp internal corners or abrupt changes in cross-section that can cause turbulence.
- Design smooth transitions between runners and the collector/turbo flange.
- Wall Thickness Management:
- Goal: Ensure structural integrity under thermal and mechanical loads while minimizing weight and material usage.
- AM Advantage: Ability to vary wall thickness precisely and apply topology optimization.
- Düşünceler:
- Tekdüzelik: Aim for relatively uniform wall thickness where possible to promote consistent cooling and reduce thermal stress during printing. Minimum printable wall thickness depends on the machine, material, and orientation (typically ~0.4-1.0 mm).
- Topology Optimization: Use software to remove material from low-stress areas, resulting in organic, load-bearing structures. Ensure optimized designs still meet thermal fatigue and vibration requirements.
- Termal İletkenlik: Thicker sections retain heat longer; consider this impact on thermal gradients during printing and operation.
- Destek Yapısı Stratejisi:
- Goal: Anchor the part to the build plate, support overhanging features (typically angles <45° from horizontal need support), and manage thermal stress.
- AM Challenge: Supports consume extra material, add print time, require removal (post-processing), and can impact surface finish. Internal supports in complex manifold channels are particularly challenging to remove.
- Düşünceler:
- Kendini Destekleyen Açılar: Design overhangs greater than ~45° wherever possible. Orient the part on the build plate strategically to minimize the need for supports in critical or inaccessible areas.
- Internal Channels: Design internal passages to be self-supporting (e.g., using diamond or teardrop shapes instead of circular for horizontally oriented sections) or ensure clear access paths for support removal tools or abrasive flow machining.
- Support Type: Choose appropriate support structures (e.g., block, cone, line) based on the feature being supported and ease of removal. Consider specialized software features for generating easily removable or optimized supports.
- Termal Yönetim: Dense supports can act as heat sinks, influencing cooling rates. This needs to be factored into the build strategy.
- Feature Integration:
- Goal: Reduce part count, eliminate welds/joints, and improve overall robustness.
- AM Advantage: Print flanges, sensor bosses (O2, EGT), wastegate connections, heat shields, and mounting brackets as integral parts of the manifold.
- Düşünceler:
- Ensure sufficient material/thickness around integrated features for strength and sealing (if applicable).
- Design features with AM process limitations in mind (e.g., minimum hole sizes, feature resolution).
- Consider access for post-machining if critical tolerances are required on integrated features (e.g., flange faces).
- Thermal Management During Printing:
- Goal: Minimize residual stress, warping, and potential cracking caused by rapid heating and cooling cycles inherent in Powder Bed Fusion.
- Düşünceler:
- Oryantasyon: Part orientation affects heat distribution and support needs.
- Tarama Stratejisi: The laser or electron beam path influences local heat buildup. Experienced AM service providers optimize scan strategies.
- Parça Geometrisi: Large, flat sections or abrupt thickness changes can be prone to warping. Incorporating gentle transitions or stiffening ribs (where appropriate) can help.
- Toz Giderme:
- Goal: Ensure all unfused powder, especially from internal channels, can be removed after printing.
- Düşünceler:
- Design internal channels with sufficient diameter and smooth paths for powder evacuation.
- Incorporate strategically placed drain/access holes (which might be plugged or welded shut later if necessary). Avoid intricate internal voids with no escape path.
By thoughtfully applying these DfAM principles, engineers can create 3D printed exhaust manifolds that are not only functional but also optimized for performance, durability, weight, and manufacturability using additive techniques. Partnering with an experienced AM service provider familiar with high-temperature applications is invaluable during the design phase.
Achievable Tolerance, Surface Finish, and Dimensional Accuracy in 3D Printed Manifolds
Understanding the achievable precision is critical for engineers and procurement managers specifying 3D printed exhaust manifolds. While metal AM offers incredible geometric freedom, it has inherent characteristics regarding tolerances, surface finish, and overall accuracy. These aspects often necessitate post-processing steps for critical features.
1. Tolerances:
- As-Printed Tolerances: Metal Powder Bed Fusion (PBF) processes like SLM/DMLS typically achieve general dimensional tolerances comparable to ISO 2768-m (medium) or sometimes ISO 2768-f (fine) for smaller, well-supported features. This generally translates to:
- +/- 0.1 mm to +/- 0.3 mm for features up to ~100 mm.
- +/- 0.1% to +/- 0.2% of the nominal dimension for larger features.
- Factors Influencing Tolerance:
- Machine Calibration: Regular calibration and maintenance are crucial.
- Malzeme Özellikleri: Different alloys exhibit varying shrinkage and thermal behavior.
- Part Size & Geometry: Larger parts and complex geometries are more susceptible to thermal distortion, impacting final tolerances.
- Orientation & Supports: How the part is oriented and supported affects stress and potential deformation.
- Thermal Stress: Residual stress build-up can cause slight warping.
- Kritik Toleranslar: Features requiring high precision, such as:
- Flange mating surfaces (flatness, perpendicularity)
- Bolt hole diameters and positions
- Interfaces with other components (e.g., turbocharger inlet) Will almost always require post-machining (CNC milling/turning) to achieve tight tolerances (e.g., within +/- 0.025 mm to +/- 0.05 mm or better). Designating these critical features clearly on drawings is essential.
2. Surface Finish (Roughness):
- As-Printed Surface Finish: The nature of layer-by-layer fusion results in a characteristic surface texture.
- Top Surfaces: Generally smoother, often in the range of Ra 5-15 µm (micrometers).
- Side Walls (Vertical/Stepped): Show layer lines, typically Ra 8-20 µm.
- Supported Surfaces (Down-Facing): Roughest areas where support structures were attached, potentially Ra 15-30 µm or higher before extensive finishing.
- Internal Channels: Finish depends heavily on orientation and whether supports were needed. Can be challenging to achieve a very smooth internal finish without secondary processing.
- Yüzey İşleminin İyileştirilmesi: Various post-processing techniques can significantly improve the surface finish:
- Abrasive Blasting (Bead/Sand): Provides a uniform matte finish, effective for removing semi-sintered particles (Ra 5-10 µm).
- Tumbling/Vibratory Finishing: Smoothes surfaces and edges, especially for smaller parts (Can achieve Ra < 5 µm).
- Abrasive Flow Machining (AFM): Particularly useful for smoothing internal channels by flowing abrasive media through them.
- Manual Polishing/Grinding: For achieving very smooth, mirror-like finishes on specific external areas.
- İşleme: Provides the best surface finish on specific features like flange faces.
3. Dimensional Accuracy:
- Tanım: How closely the printed part conforms to the original CAD model dimensions.
- Factors Influencing Accuracy: Includes all factors affecting tolerance (machine, material, size, geometry, stress) plus:
- CAD Model Quality: Ensuring a watertight, error-free STL or 3MF file.
- Slice Preparation: Correct scaling and slice parameter settings.
- Post-Processing Effects: Stress relief can cause minor dimensional changes; machining introduces its own accuracy level.
- Achieving High Accuracy: Requires careful process control, robust support strategies, effective thermal management (including post-print stress relief), and often targeted machining for critical dimensions. Validation through 3D scanning or CMM inspection is common practice for high-value parts.
Expectation Management:
It’s crucial for designers and buyers to understand that metal AM is not inherently a high-precision process for all features straight off the machine. While capable of incredible complexity, achieving tight tolerances and specific surface finishes typically involves planning for and incorporating post-processing steps into the manufacturing workflow and budget. Communicating critical dimension and surface finish requirements clearly to the AM service provider is essential.
Özellik | As-Printed Typical Range | Post-Processed Potential | Control Method |
---|---|---|---|
General Tolerance | ISO 2768-m/f (~ +/- 0.1-0.3mm) | N/A (Defined by process) | Process Control, Machine Cal. |
Critical Tolerance | As above | +/- 0.025mm or better | CNC İşleme |
Yüzey Pürüzlülüğü (Ra) | 8-20 µm (Side Walls) | < 1 µm (Polished), 3-8 µm (Blasted) | Blasting, Tumbling, AFM, Polish |
Flange Flatness | Orta düzeyde | High (<0.05mm typical) | CNC İşleme |
Internal Channel Finish | Ra 10-30 µm+ | Ra < 10 µm (AFM possible) | DfAM, AFM, Process Control |
Sayfalara Aktar
Essential Post-Processing Requirements for 3D Printed Exhaust Manifolds
A metal 3D printed part, especially a high-performance component like an exhaust manifold made from superalloys, is rarely ready for use straight off the build plate. Post-processing is a critical stage in the manufacturing workflow, necessary to relieve stress, remove support structures, achieve required tolerances and surface finishes, and ensure the material possesses the desired mechanical properties.
Common Post-Processing Steps:
- Stres Giderici:
- Why: The rapid heating and cooling during PBF introduces significant internal stresses within the part. If not relieved, this stress can lead to distortion, cracking (potentially even days or weeks after printing), and reduced fatigue life. This is especially critical for nickel-based superalloys like IN625, IN718, and Hastelloy X.
- How: The part, often while still attached to the build plate, undergoes a controlled heating and cooling cycle in a furnace. The specific temperature and duration depend heavily on the alloy and part geometry but typically involve heating to several hundred degrees Celsius below the annealing or aging temperature.
- Importance: Consider this a mandatory first step after printing, before any significant handling or removal from the build plate.
- Yapı Plakasından Çıkarma:
- Why: The part is fused to a thick metal build plate during printing.
- How: Typically done using Wire EDM (Electrical Discharge Machining) or a band saw. Care must be taken not to damage the part.
- Destek Yapısının Kaldırılması:
- Why: Supports are necessary during printing but must be removed for the final part.
- How: This can be labor-intensive. Methods include:
- Manuel Kaldırma: Breaking or cutting away accessible supports using hand tools (pliers, cutters, grinders).
- CNC İşleme: Milling or grinding away support structures, especially near critical surfaces.
- Wire EDM: Sometimes used for intricate support removal.
- Zorluklar: Removing supports from complex internal channels is particularly difficult and requires careful DfAM planning (see previous section). Marks left by supports on the part surface often require further finishing.
- Heat Treatment (Solution Annealing & Aging – Primarily for IN718):
- Why: Certain alloys, notably precipitation-hardenable ones like IN718, require specific heat treatment cycles to achieve their full mechanical properties (strength, hardness, creep resistance). As-printed IN718 has significantly lower strength than in its fully heat-treated state. IN625 and Hastelloy X are solid-solution strengthened and typically only require stress relief, though annealing might sometimes be used.
- How: Involves heating the part to a specific high temperature (solution annealing) to dissolve precipitates, followed by quenching, and then one or more lower temperature holds (aging) to precipitate the strengthening phases (gamma prime and gamma double-prime in IN718). These cycles must be precisely controlled in a calibrated furnace, often under vacuum or inert atmosphere.
- Importance: Absolutely essential for IN718 to meet performance specifications. Less critical but sometimes specified for other alloys depending on the application requirements.
- Machining (Critical Dimensions & Features):
- Why: To achieve tight tolerances, specific surface finishes, and ensure proper sealing/mating surfaces.
- How: CNC milling, turning, or grinding are used to machine:
- Flange faces (engine head and outlet/turbo connections) for flatness and surface finish.
- Bolt holes to precise diameters and locations.
- Any other critical interface dimensions.
- Importance: Mandatory for ensuring proper fitment and sealing in most exhaust manifold applications.
- Yüzey İşlemi:
- Why: To improve aesthetics, potentially enhance fatigue life (by removing surface imperfections), clean the part, and achieve a desired surface texture.
- How:
- Abrasive Blasting (Bead, Sand, Grit): Common for a uniform matte finish.
- Tumbling/Vibratory Finishing: Smoothes surfaces and edges.
- Abrasive Flow Machining (AFM) or Extrude Hone: Used to smooth internal channels.
- Manual Grinding/Polishing: For specific aesthetic or functional requirements.
- Cleaning & Inspection:
- Why: Ensure all support material, loose powder, machining swarf, and contaminants are removed. Verify part integrity and dimensional accuracy.
- How: Ultrasonic cleaning, solvent washing, visual inspection, dimensional inspection (CMM, 3D scanning), Non-Destructive Testing (NDT) like CT scanning or FPI (Fluorescent Penetrant Inspection) may be required for critical applications (especially aerospace) to check for internal defects or surface cracks.
The extent and sequence of these post-processing steps depend on the material, design complexity, and application requirements. Integrating these steps into the production plan and budget is crucial. Partnering with a full-service provider like Met3dp, who understands the entire workflow from powder to finished part, including necessary post-processing for high-temperature alloys, can streamline the process and ensure optimal results.
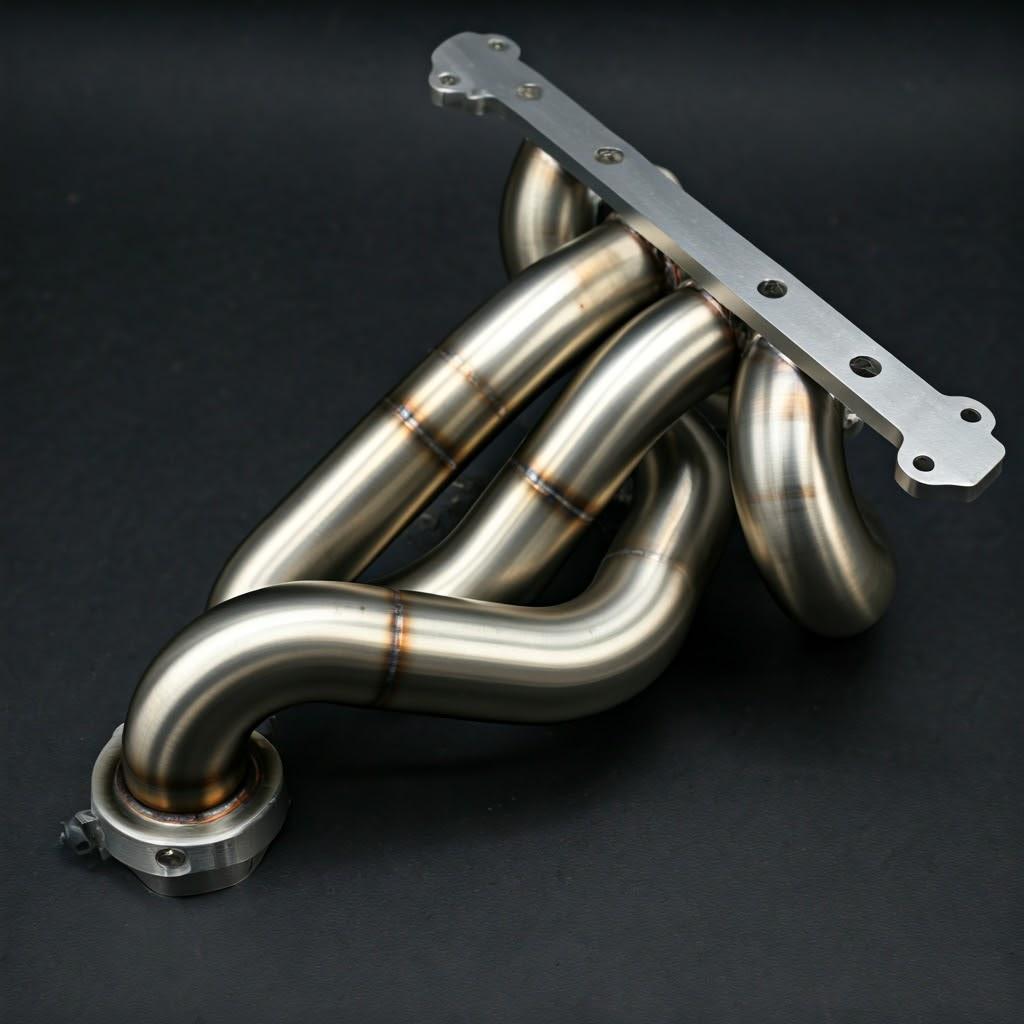
Common Challenges in 3D Printing Exhaust Manifolds and Mitigation Strategies
While metal AM offers significant advantages for producing high-temperature exhaust manifolds, it’s not without its challenges. Understanding these potential issues and implementing effective mitigation strategies is key to successfully manufacturing reliable, high-performance parts.
1. Warping and Distortion:
- Sebep: Uneven heating and cooling during the layer-by-layer PBF process induce significant thermal gradients and residual stresses, causing the part to deform or pull away from the build plate. Large flat areas and asymmetric designs are particularly susceptible. Nickel superalloys have high thermal expansion coefficients, exacerbating this issue.
- Hafifletme:
- Optimize Edilmiş Yönlendirme: Position the part on the build plate to minimize large flat surfaces parallel to the plate and reduce unsupported overhangs.
- Robust Support Strategy: Use well-designed support structures to anchor the part firmly and act as heat sinks to draw away thermal energy more evenly.
- Süreç Parametre Optimizasyonu: Fine-tuning laser/beam power, scan speed, and scan strategy (e.g., island scanning) can minimize localized overheating.
- Plaka Isıtması Oluşturun: Pre-heating the build plate reduces the thermal gradient between the solidified material and the surrounding powder/plate.
- Stres Giderici: Performing a stress relief cycle immediately after printing is crucial to relax internal stresses before significant distortion occurs.
- DfAM: Designing features like ribs or corrugations can increase stiffness; aiming for more uniform wall thickness helps manage thermal gradients.
2. Cracking (Solidification or Heat Treatment):
- Sebep:
- Solidification Cracking: Occurs during printing if localized stresses exceed the material’s strength as it solidifies and cools. Certain alloys are more susceptible.
- Heat Treatment Cracking: Can occur during post-print heat treatment (stress relief or aging) if heating/cooling rates are too fast or if pre-existing defects act as stress concentrators. Superalloys can be sensitive.
- Hafifletme:
- Alloy Selection: Choose alloys with good AM processability (IN625 and Hastelloy X generally have better printability than IN718, though IN718 is very commonly printed successfully).
- Parametre Optimizasyonu: Careful control over energy input and scan strategy is critical.
- Sıcak İzostatik Presleme (HIP): While adding cost, HIP can close internal voids and may help heal micro-cracks, improving fatigue life (often required for critical aerospace parts).
- Controlled Heat Treatment Cycles: Use slow, controlled heating and cooling rates during stress relief and aging, following established protocols for the specific alloy. Ensure proper furnace calibration and atmosphere control.
- Robust Supports: Adequate support helps manage stress during the build.
3. Support Removal Difficulties (Especially Internal):
- Sebep: Complex internal geometries of manifolds make accessing and removing support structures challenging without damaging the part. Fused supports can be very strong.
- Hafifletme:
- DfAM for Access: Design internal channels to be self-supporting where possible (e.g., teardrop/diamond cross-sections). If supports are unavoidable, ensure there are access ports or straight-line paths for tools or AFM media.
- Optimized Support Design: Use support types designed for easier removal (e.g., lower density, specific contact points). Specialized software can help generate these.
- Post-Processing Teknikleri: Utilize methods like CNC machining for external supports near critical faces, or consider AFM for internal channel support remnants and surface smoothing. Plan for this during the design phase.
4. Trapped Powder Removal:
- Sebep: Unfused powder can become trapped within intricate internal passages or partially sintered voids.
- Hafifletme:
- DfAM for Depowdering: Design clear drainage paths and access holes. Avoid creating closed internal cavities. Ensure minimum channel diameters allow for powder flow.
- Optimize Edilmiş Yönlendirme: Orient the part to facilitate powder drainage during the build break-out process.
- Thorough Cleaning: Utilize vibration, compressed air, and potentially ultrasonic cleaning combined with specialized depowdering equipment to dislodge trapped powder after the build. CT scanning can verify complete powder removal if required.
5. Internal Surface Finish:
- Sebep: Down-facing surfaces and areas requiring internal supports naturally have rougher finishes in PBF processes. Achieving smooth internal flow paths can be difficult.
- Hafifletme:
- DfAM & Orientation: Design self-supporting internal channels and orient the part optimally.
- Abrasive Flow Machining (AFM): The most effective method for significantly improving internal surface finish by flowing abrasive media through the channels.
- Parametre Optimizasyonu: Certain process parameters can slightly influence internal finish, but DfAM and post-processing have a larger impact.
6. Quality Control and Consistency:
- Sebep: Ensuring every part meets density requirements, is free from critical defects (porosity, cracks), and achieves the desired mechanical properties requires rigorous process control and inspection.
- Hafifletme:
- Robust Quality Management System (QMS): Work with suppliers having certifications like ISO 9001 or AS9100 (for aerospace).
- Süreç İzleme: In-situ monitoring tools (melt pool monitoring, thermal imaging) can provide real-time quality indicators.
- Powder Quality Control: Ensuring consistent, high-quality powder feedstock is essential.
- Tahribatsız Muayene (NDT): Utilize CT scanning, FPI, or ultrasonic testing as appropriate for the application’s criticality to verify internal integrity.
- Mechanical Testing: Perform tensile tests, hardness tests, etc., on representative samples or test coupons built alongside the parts.
Addressing these challenges requires a combination of smart design practices (DfAM), careful material selection, optimized process parameters, appropriate post-processing, and rigorous quality control. Collaborating with an experienced metal AM provider who understands the intricacies of printing high-temperature superalloys for applications like exhaust manifolds is often the key to overcoming these hurdles successfully.
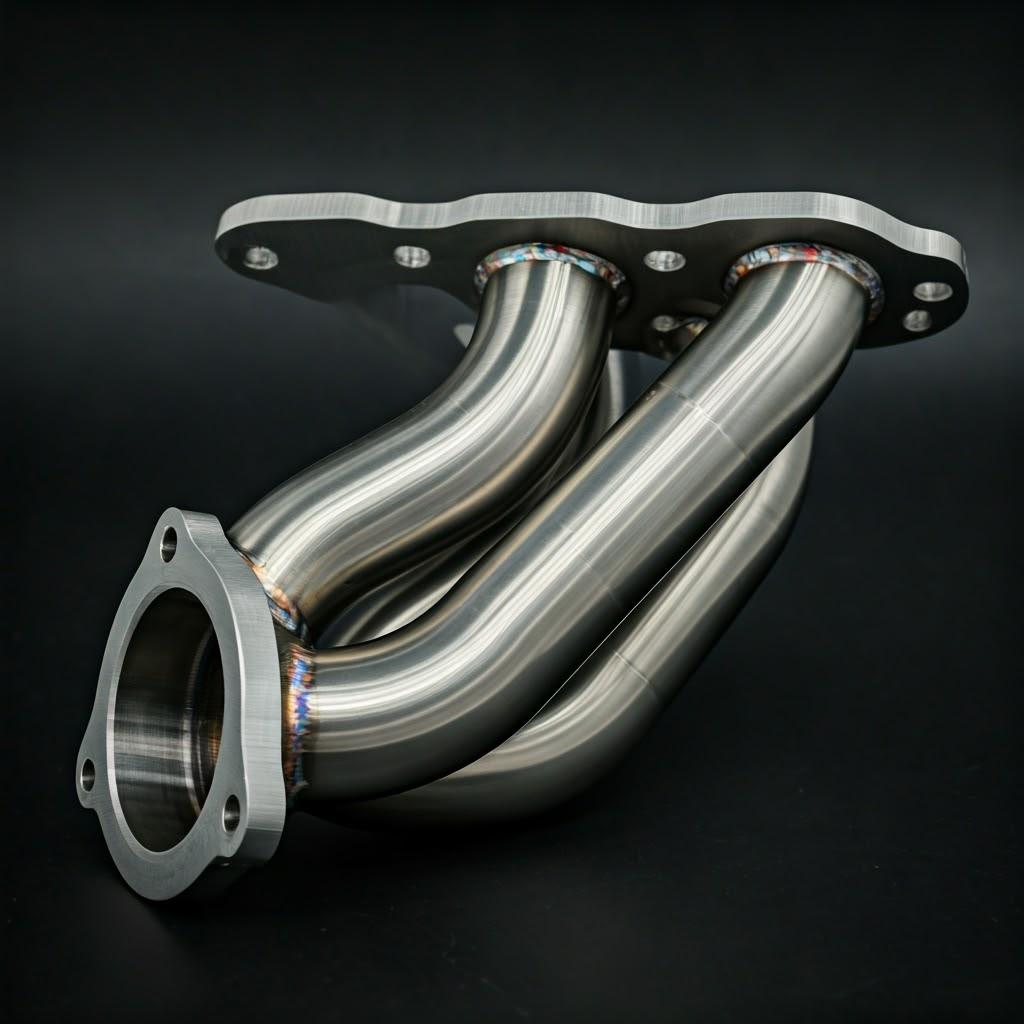
How to Choose the Right Metal 3D Printing Service Provider for Exhaust Manifolds
Selecting the right manufacturing partner is as crucial as perfecting the design and choosing the right material, especially for demanding components like high-temperature exhaust manifolds. Not all metal additive manufacturing (AM) service providers have the specific expertise, equipment, and quality systems required to successfully produce these challenging parts using superalloys. For engineers and procurement managers, careful evaluation of potential suppliers is essential.
Key Factors to Evaluate:
- Expertise with High-Temperature Superalloys:
- Requirement: Proven experience printing IN625, IN718, Hastelloy X, or other relevant high-temperature materials. This includes understanding their unique processing requirements, potential challenges (like cracking susceptibility), and necessary post-processing heat treatments.
- Look For: Case studies, examples of similar parts produced, material datasheets based on their printed results, and knowledgeable technical staff who can discuss material specifics. Companies like Met3dp, which not only provide printing services but also specialize in developing and manufacturing yüksek performanslı metal tozları, possess deep material science expertise.
- Appropriate Technology and Equipment:
- Requirement: Access to suitable Powder Bed Fusion (PBF) technologies (Selective Laser Melting – SLM / Direct Metal Laser Sintering – DMLS, or potentially Electron Beam Melting – EBM) with adequate build volume for the manifold size. Machines should be well-maintained and calibrated.
- Look For: Information on their specific printer models, build envelope dimensions, laser/beam power capabilities, and atmosphere control (essential for reactive alloys). Met3dp utilizes industry-leading equipment known for accuracy and reliability, suitable for mission-critical parts.
- Integrated Post-Processing Capabilities:
- Requirement: Ability to perform necessary post-processing steps in-house or through qualified partners. This includes stress relief, specialized heat treatments (like vacuum solution annealing and aging for IN718), support removal, CNC machining for critical features, surface finishing, and cleaning.
- Look For: A comprehensive service offering that covers the entire workflow from print to finished part. Ask about their specific equipment and experience with machining superalloys and handling complex geometries. A provider offering a complete solution simplifies the supply chain and ensures accountability.
- Quality Management System & Certifications:
- Requirement: Robust quality control processes are non-negotiable. Certifications demonstrate a commitment to quality and process control.
- Look For: ISO 9001 certification is a baseline. For aerospace or highly demanding applications, AS9100 certification is often required. Inquire about their inspection capabilities (CMM, 3D scanning) and NDT options (CT scanning, FPI). Met3dp emphasizes industry-leading accuracy and reliability, backed by rigorous quality control.
- DfAM Support and Engineering Expertise:
- Requirement: The ability to collaborate on design optimization for additive manufacturing (DfAM). An experienced partner can provide valuable feedback on improving printability, reducing support needs, and optimizing performance.
- Look For: Providers offering engineering support services, design consultation, or feedback mechanisms during the quoting/onboarding process.
- Proven Track Record and Industry Experience:
- Requirement: Demonstrated success in producing parts for relevant industries (automotive, motorsport, aerospace, industrial).
- Look For: Case studies, testimonials, references, and examples of projects similar in complexity and material requirements.
- Lead Time and Communication:
- Requirement: Realistic lead time estimates and clear, responsive communication throughout the project lifecycle.
- Look For: Transparent quoting process, proactive updates, and accessible technical points of contact.
Evaluation Checklist for Suppliers:
Kriterler | Questions to Ask | Ideal Response Indicator |
---|---|---|
Malzeme Uzmanlığı | Which high-temp superalloys do you regularly print? Can you share datasheets/case studies for IN625/IN718/HastX? | Deep familiarity, proven results, specific experience with relevant alloys. |
Teknoloji ve Ekipman | What PBF machines do you use? What is the build volume? How do you ensure machine calibration? | Modern, well-maintained equipment suitable for part size and material (e.g., SLM/DMLS). |
İşlem Sonrası | Do you offer in-house stress relief, heat treatment (vacuum?), CNC machining, NDT? What finishing options? | Comprehensive in-house capabilities or tightly managed, qualified partners. |
Kalite Sistemleri | Are you ISO 9001 / AS9100 certified? What are your standard inspection methods? Can you provide material certs? | Relevant certifications, detailed quality procedures, traceable material lots. |
DfAM / Engineering Support | Do you review designs for printability? Do you offer DfAM consultation? | Proactive design feedback, collaborative approach. |
İz Kaydı | Can you provide examples of similar projects or references in our industry? | Relevant industry experience, positive customer feedback. |
Lead Time & Communication | What is your typical lead time for such a part? Who is my technical point of contact? | Realistic timelines, clear communication channels, responsiveness. |
Powder Sourcing & Quality | Where do you source your powders? How do you ensure powder quality and consistency? | Reputable sources or in-house production (like Met3dp), rigorous powder management protocols. |
Sayfalara Aktar
Choosing the right partner is an investment in the success of your project. A provider like Met3dp, offering integrated solutions spanning advanced metal 3D baskı equipment, high-quality metal powders produced using cutting-edge atomization techniques, and comprehensive application development services, represents the type of capable and reliable partner needed for manufacturing high-performance 3D printed exhaust manifolds.
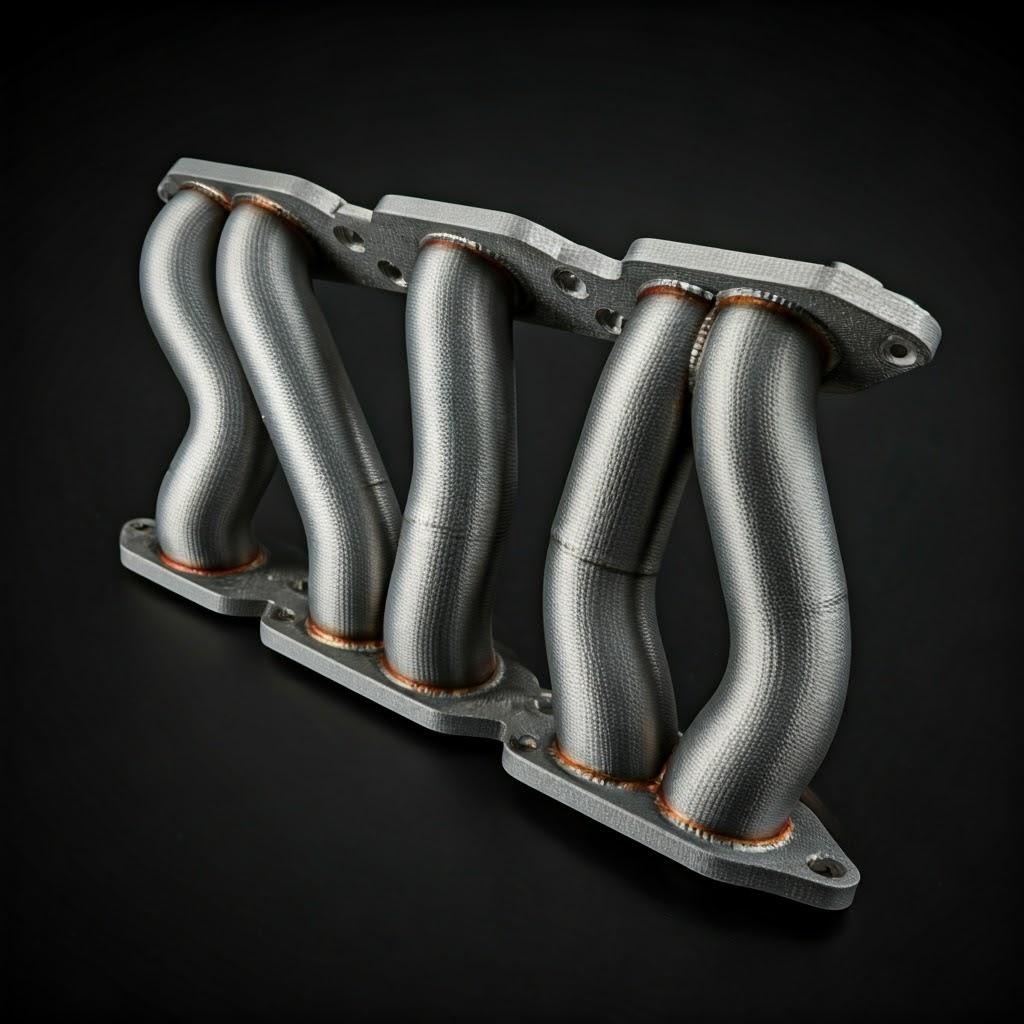
Understanding Cost Factors and Lead Times for 3D Printed Exhaust Manifolds
While metal AM offers significant technical advantages, understanding the associated costs and production timelines is crucial for project planning and budgeting, especially for B2B procurement and wholesale considerations.
Key Cost Drivers:
- Malzeme Maliyeti:
- Factor: Nickel-based superalloys (IN625, IN718, Hastelloy X) are inherently expensive raw materials compared to standard steels or aluminum alloys. Powder production for AM adds further cost.
- Etki: Material consumption (part volume + support volume) is often a primary cost driver. Design optimization to minimize volume while meeting requirements is key.
- Print Time (Machine Time):
- Factor: Calculated based on the total time the AM machine is occupied. Influenced by part height (number of layers), part volume (area to be scanned per layer), and chosen layer thickness/scan parameters. Complex internal structures can increase print time.
- Etki: Larger or taller parts, or very complex geometries requiring intricate scanning, directly increase machine time cost. Multiple parts nested efficiently within a single build can reduce per-part machine time cost.
- Destek Yapıları:
- Factor: Supports consume material and add to print time. More importantly, they require significant post-processing labor/time for removal.
- Etki: Designs requiring extensive or difficult-to-access supports will incur higher costs due to both material usage and removal effort. DfAM aimed at minimizing supports is highly beneficial.
- Post-Processing Intensity:
- Factor: This can be a substantial portion of the total cost. Includes:
- Stress relief (furnace time, energy).
- Heat treatment (complex cycles, vacuum furnace time, skilled labor).
- Support removal (manual labor, machining time).
- CNC machining (setup time, programming, machining time, tooling wear on hard superalloys).
- Surface finishing (labor, consumables, specialized equipment like AFM).
- Inspection/NDT (equipment time, skilled technicians).
- Etki: The level of finishing, tolerance requirements, and quality assurance needed heavily influences cost. Parts needing extensive machining and NDT will be significantly more expensive than those requiring only basic finishing.
- Factor: This can be a substantial portion of the total cost. Includes:
- Engineering & Setup:
- Factor: Initial file preparation, build simulation, development of optimal orientation and support strategy, and machine setup time.
- Etki: Usually amortized over the production run; more significant as a percentage for single prototypes versus small batch production.
- Miktar:
- Factor: While AM avoids tooling costs, economies of scale are still present. Setup costs are spread over more parts, machines can be run more continuously, and post-processing might be streamlined for batches.
- Etki: Cost per part generally decreases with higher volumes, though the reduction is typically less dramatic than in traditional mass production methods. AM remains most competitive for prototypes, low-to-mid volumes, and highly complex/custom parts.
Typical Lead Time Components:
Lead time for a 3D printed exhaust manifold is the sum of several stages:
- Quoting & Design Finalization: (1-5 days) Initial review, DfAM feedback, quote generation, order confirmation.
- Build Preparation: (1-3 days) Detailed build planning, slicing, support generation, machine scheduling.
- Baskı: (2-7+ days) Highly dependent on part size, complexity, and nesting. Large or complex manifolds can easily take several days of continuous printing.
- Cool-Down & Breakout: (1 day) Allowing the build chamber and part to cool safely, removing the part from the machine, initial powder removal.
- İşlem sonrası: (3-10+ days) This is highly variable and often the longest stage. Includes stress relief, removal from plate, support removal, heat treatment (can take 1-2 days alone), machining, finishing, and inspection. Each step adds time.
- Final Inspection & Shipping: (1-3 days) Final quality checks, packaging, and shipment.
Total Estimated Lead Time: For a complex superalloy exhaust manifold requiring significant post-processing, expect lead times ranging from 3 ila 6 hafta or potentially longer, depending on complexity, quantity, and service provider capacity. Prototyping might be slightly faster if extensive finishing or heat treatment is initially skipped.
It’s essential to discuss specific cost drivers and lead time expectations with potential suppliers based on finalized designs and clear requirements for tolerances, finishing, and quality assurance.
Frequently Asked Questions (FAQ) about 3D Printed Exhaust Manifolds
Q1: What are the main advantages of 3D printing an exhaust manifold compared to traditional casting or fabrication?
A: The key advantages lie in: * Geometric Complexity: Ability to create highly optimized internal flow paths and complex shapes for improved engine performance, which are difficult or impossible to achieve via casting or welding tubes. * Malzeme Seçenekleri: Enables the use of advanced high-temperature superalloys (like IN625, IN718, Hastelloy X) optimized for extreme heat and corrosion resistance. * Parça Konsolidasyonu: Multiple components (runners, collector, flanges, brackets) can be printed as a single piece, reducing weight, potential failure points (welds), and assembly time. * Hafifletme: Design freedom combined with topology optimization allows for significant weight reduction compared to traditional designs, crucial for motorsport and aerospace. * Rapid Prototyping & Low Volume Production: Faster iteration during development and cost-effective manufacturing for custom parts or small batches without expensive tooling.
Q2: What is the typical maximum operating temperature for a 3D printed manifold using Inconel 625 or 718?
A: Maximum operating temperature depends on the specific alloy, the stresses involved, and the required component life. As a general guideline: * Inconel 625 (IN625): Maintains excellent strength and oxidation resistance up to approximately 815-900°C (1500-1650°F), with useful properties potentially extending higher for lower stress or shorter duration exposures. * Inconel 718 (IN718): Offers superior strength up to about 700°C (1300°F) due to its age-hardening nature. Its strength decreases more rapidly above this temperature compared to IN625, although its oxidation resistance remains good at higher temperatures. * Hastelloy X: Known for outstanding oxidation resistance up to 1200°C (2200°F), making it suitable for the absolute hottest applications, though its strength might be lower than IN718 at intermediate temperatures (~650°C). The design must consider creep, fatigue, and thermal cycling within the target operating window.
Q3: How does the cost of a 3D printed exhaust manifold compare to traditional methods?
A: It’s a trade-off: * Prototypes & Low Volumes (1-50 parts): 3D printing is often daha uygun maliyetli because it eliminates the need for expensive tooling (casting molds, fabrication jigs). * High Volumes (100s-1000s+ parts): Traditional casting or high-volume fabrication typically becomes less expensive per part due to amortized tooling costs and faster cycle times. * Performance Value: For high-performance applications, the potentially higher cost of a 3D printed manifold can be justified by significant performance gains (horsepower, efficiency), weight savings, or durability improvements unattainable with traditional methods. The total value proposition, not just the part cost, should be considered.
Q4: Can the internal surfaces of a 3D printed exhaust manifold be made smooth for optimal airflow?
A: Achieving a perfectly smooth internal surface comparable to mandrel-bent tubes can be challenging directly from the printer, especially on down-facing surfaces or where internal supports were required (as-printed Ra might be 10-30µm+). However: * DfAM: Designing self-supporting internal channels helps minimize roughness. * Oryantasyon: Strategic orientation can improve the finish of critical flow paths. * İşlem sonrası: Techniques like Abrasive Flow Machining (AFM) or similar extrusion honing methods are specifically designed to smooth internal passages by flowing abrasive media through them, significantly reducing roughness (potentially to Ra < 5-10 µm) and improving flow characteristics. This adds cost but is effective for performance-critical applications.
Conclusion: Driving the Future of High-Performance Exhaust Systems with Metal Additive Manufacturing
The challenges posed by extreme temperatures, complex flow dynamics, and the relentless pursuit of performance in modern engines demand innovative manufacturing solutions. Metal additive manufacturing has firmly established itself as a transformative technology capable of meeting these demands head-on for components like high-temperature exhaust manifolds.
By unlocking unprecedented design freedom, enabling the use of advanced nickel-based superalloys like IN625, IN718, and Hastelloy X, and facilitating rapid prototyping and part consolidation, metal 3D printing offers tangible benefits that translate directly into enhanced performance, reduced weight, and improved durability. While traditional methods remain viable for standard applications, AM provides a distinct competitive advantage in sectors where optimization is key – including motorsport, aerospace, high-performance automotive, and specialized industrial equipment.
Successfully leveraging this technology requires a holistic approach encompassing Design for Additive Manufacturing (DfAM), careful material selection, controlled processing, thorough post-processing, and rigorous quality assurance. Overcoming challenges like thermal stress management and support removal necessitates expertise and collaboration.
Choosing the right manufacturing partner—one with proven experience in high-temperature alloys, robust quality systems, and comprehensive capabilities—is paramount. Companies like Met3dp, with their deep expertise in both advanced metal powders and additive manufacturing systems, exemplify the integrated approach needed to turn complex designs into reliable, high-performance realities.
As metal AM technologies continue to mature and materials science advances, the possibilities for optimizing exhaust systems and other critical high-temperature components will only expand. For engineers and procurement managers aiming to push the boundaries of performance and efficiency, embracing metal additive manufacturing is no longer just an option; it’s a strategic imperative for driving the future of high-performance systems.
Paylaş
MET3DP Technology Co, LTD, merkezi Qingdao, Çin'de bulunan lider bir katmanlı üretim çözümleri sağlayıcısıdır. Şirketimiz, endüstriyel uygulamalar için 3D baskı ekipmanları ve yüksek performanslı metal tozları konusunda uzmanlaşmıştır.
İşletmeniz için en iyi fiyatı ve özelleştirilmiş Çözümü almak için sorgulayın!
İlgili Makaleler
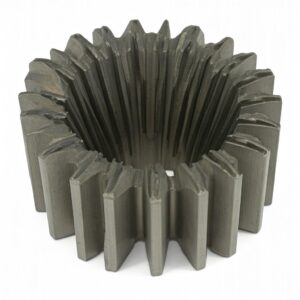
Yüksek Performanslı Nozul Kanat Segmentleri: Metal 3D Baskı ile Türbin Verimliliğinde Devrim
Daha Fazla Oku "Met3DP Hakkında
Son Güncelleme
Bizim Ürünümüz
BİZE ULAŞIN
Herhangi bir sorunuz var mı? Bize şimdi mesaj gönderin! Mesajınızı aldıktan sonra tüm ekibimizle talebinize hizmet edeceğiz.
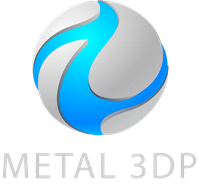
3D Baskı ve Katmanlı Üretim için Metal Tozları