Rocket Injector Plates 3D Printed with Nickel Superalloys
İçindekiler
Introduction: The Critical Role of Rocket Injector Plates in Modern Aerospace
In the demanding realm of aerospace engineering, few components play as pivotal a role in mission success as the rocket injector plate. Situated at the heart of liquid rocket engines (LREs), these intricate components are the gatekeepers of propulsion, meticulously controlling the introduction and mixing of fuel and oxidizer into the combustion chamber. Their performance directly dictates engine efficiency, stability, and overall reliability – factors that are non-negotiable when launching payloads into orbit or propelling spacecraft through the cosmos. The injector plate doesn’t just facilitate combustion; it orchestrates it, ensuring propellants mix at precise ratios and patterns to achieve optimal thrust and prevent potentially catastrophic combustion instabilities. Operating under conditions of extreme temperature gradients, immense pressures, and exposure to highly reactive propellants, the injector plate represents a significant engineering challenge, demanding materials and manufacturing processes capable of meeting extraordinary requirements.
Traditionally, manufacturing these critical components involved complex multi-part assemblies, often requiring intricate machining and high-risk brazing or welding operations. These methods, while established, present limitations in design complexity, lead time, and potential points of failure at joints. Enter the transformative technology of metal additive manufacturing (AM), commonly known as metal 3D baskı. This advanced manufacturing approach offers unprecedented design freedom, enabling the creation of highly complex, monolithic injector plates with integrated features previously impossible or prohibitively expensive to produce. By building parts layer by layer directly from metal powder, AM allows engineers to optimize flow paths, integrate sophisticated cooling channels, and consolidate multiple components into a single, robust part. This not only enhances performance and reliability but also significantly reduces weight and accelerates development cycles.
The materials used are just as crucial as the manufacturing method. Nickel superalloys, such as IN625 (Inconel 625) and IN718 (Inconel 718), have emerged as leading candidates for 3D yazdırılmış injector plates due to their exceptional high-temperature strength, superior corrosion resistance, and excellent fatigue life – properties essential for surviving the harsh LRE environment. The synergy between advanced nickel superalloys and the geometric freedom of metal AM is unlocking new possibilities in rocket engine design and performance. Companies seeking a reliable aerospace manufacturing supplier for these critical components are increasingly turning to specialized providers. Met3dp, a leader in metal additive manufacturing solutions, leverages decades of expertise and state-of-the-art equipment, including industry-leading Selective Electron Beam Melting (SEBM) printers and advanced powder production facilities, to deliver high-performance, mission-critical components like rocket injector plates, empowering the next generation of space exploration.
Functionality and Applications: Precision Engineering for Peak Propulsion Performance
The rocket injector plate is far more than a simple interface; it is a marvel of precision fluid dynamics engineering. Its primary functions are threefold:
- Atomizasyon: Breaking down the incoming streams of liquid fuel and oxidizer into incredibly fine droplets. Smaller droplets have a much larger surface area-to-volume ratio, which significantly accelerates vaporization and enables more rapid and complete mixing and combustion. The efficiency of atomization directly impacts combustion efficiency and stability. Different injector element designs (like pintle, coaxial swirl, or impinging jets) are employed to achieve specific atomization characteristics tailored to the engine’s requirements.
- Karıştırma: Ensuring the atomized fuel and oxidizer droplets are intimately mixed in the correct proportions across the face of the combustion chamber. Uniform mixing is critical for stable combustion and preventing localized areas of rich or lean mixtures, which can lead to performance loss, increased thermal stress, or damaging combustion instabilities like screech or rumble. The pattern and placement of injection orifices on the plate are meticulously designed to achieve the desired mixing profile.
- Thermal Management (Cooling): Injector plates often incorporate intricate internal passages for regenerative cooling. A portion of the cold fuel (or sometimes oxidizer) is circulated through these channels before injection. This process serves a dual purpose: it preheats the propellant slightly before combustion (improving efficiency) and, more importantly, it absorbs heat conducted from the combustion chamber, keeping the injector plate material below its critical temperature limits and preventing thermal failure. The ability to integrate these complex cooling networks directly into the injector plate structure is a key advantage offered by additive manufacturing.
The performance demanded of these functions varies depending on the application. Rocket injector plates are crucial components in a wide range of tahri̇k si̇stemleri̇:
- Launch Vehicle Main Engines: Powering rockets like Falcon 9, Ariane, or Atlas requires large, high-thrust engines. Their injector plates must handle enormous propellant flow rates, intense heat loads, and significant pressure drops while ensuring stable, high-efficiency combustion throughout the ascent phase. Reliability is paramount.
- Upper Stage Engines: These engines operate in the vacuum of space, often requiring multiple restarts. Their injector plates must be designed for high performance, precise mixture control, and reliable ignition sequences. Weight is often a critical factor for upper stages.
- Satellite Propulsion Systems: Smaller thrusters used for orbital maneuvering, station-keeping, and attitude control on satellites utilize highly optimized injector plates. These focus on precision impulse delivery, long operational life, and often employ hypergolic propellants (which ignite on contact), demanding excellent material compatibility.
- Spacecraft Engines: Engines for interplanetary missions or landers have unique requirements, often balancing thrust, specific impulse (efficiency), and long-duration operation. Injector plate design plays a key role in meeting these mission-specific demands.
Across all these applications, the injector plate function is central to achieving the desired engine performance, combustion stability, and overall mission success. Even minor variations in manufacturing quality or deviations from the intended design can have significant consequences. This underscores the need for yüksek performanslı bileşenler manufactured using processes that guarantee precision, repeatability, and material integrity – strengths inherent in advanced metal additive manufacturing techniques employed by expert havacılık ve uzay mühendisliği partners like Met3dp.
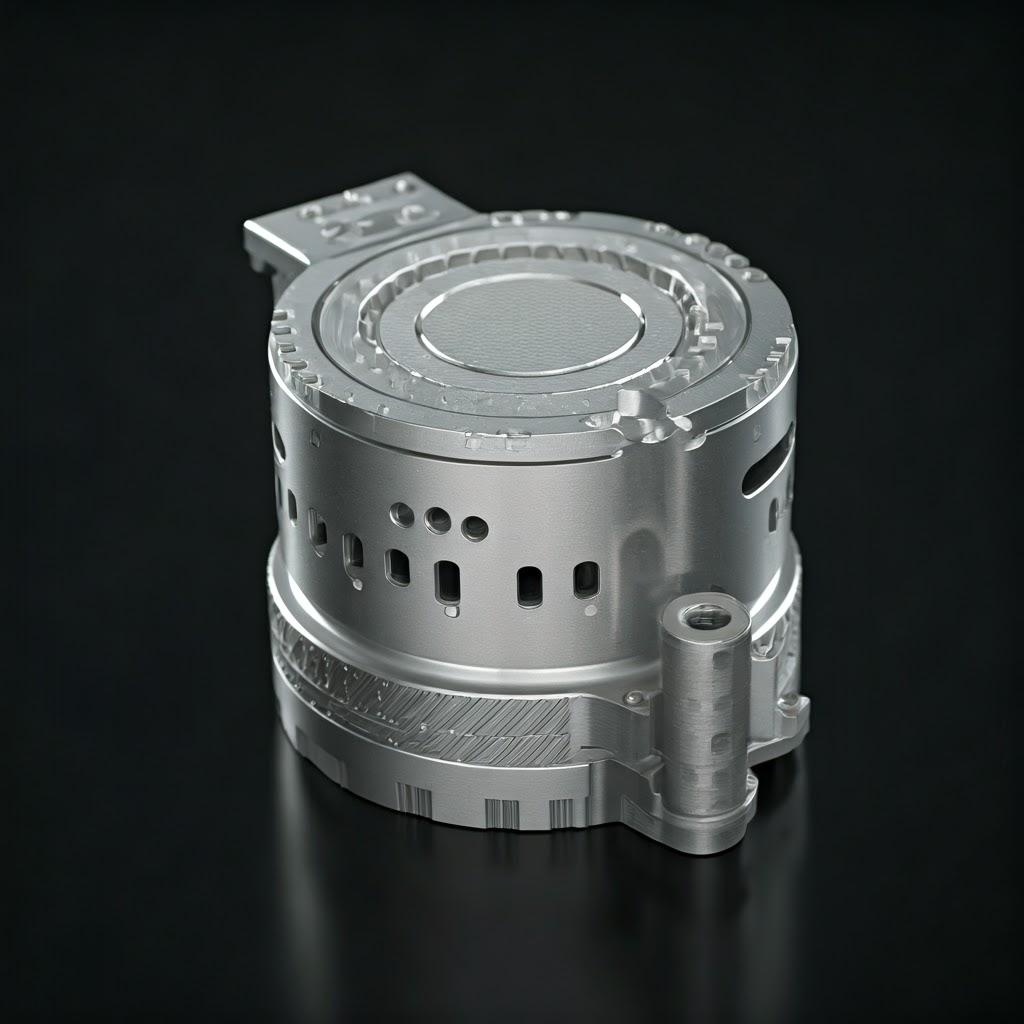
Why Metal Additive Manufacturing for Rocket Injector Plates? Unlocking Design Freedom and Performance Gains
The decision to utilize metal additive manufacturing for rocket injector plates stems from the significant advantages it offers over conventional methods like multi-axis CNC machining, casting, and complex brazing or welding assemblies. While traditional techniques have served the aerospace industry for decades, they often impose constraints that limit performance, increase complexity, and extend development timelines. Metal AM, particularly Powder Bed Fusion (PBF) processes like Selective Laser Melting (SLM) or Direct Metal Laser Sintering (DMLS), shatters many of these limitations.
Comparing Manufacturing Approaches:
Özellik | Traditional Manufacturing (Machining/Brazing) | Metal Additive Manufacturing (SLM/DMLS) | Impact on Injector Plates |
---|---|---|---|
Geometrik Karmaşıklık | Limited by tool access, machining paths, assembly feasibility. | Highly complex, intricate internal features, organic shapes possible. | Enables optimized spray patterns, integrated regenerative cooling channels previously impossible. |
Parça Konsolidasyonu | Multiple components often required, joined by brazing/welding. | Single monolithic part can replace complex assemblies. | Reduces potential failure points (joints), simplifies assembly, decreases weight. |
İç Özellikler | Difficult or impossible to create complex internal channels. | Easily integrates complex cooling passages, optimized flow paths. | Enhanced thermal management, improved propellant mixing efficiency. |
Malzeme Atıkları | Subtractive processes generate significant material scrap (buy-to-fly ratio). | Additive process uses material primarily where needed, less waste. | More sustainable, cost-effective for expensive superalloys. |
Teslim Süresi | Long lead times due to complex tooling, multi-step processing, assembly. | Shorter lead times, especially for prototypes and complex parts. | Faster design iteration (rapid prototyping rocket parts), quicker development cycles. |
Ağırlık | Limited opportunities for significant weight reduction beyond material choice. | Enables topology optimization and lattice structures for hafifletme. | Crucial for improving payload capacity and overall vehicle performance. |
Design Iteration | Costly and time-consuming to modify designs (new tooling/fixtures). | Relatively easy and fast to modify digital models and print new versions. | Accelerates engine development and optimization cycles significantly. |
Sayfalara Aktar
Key AM Advantages for Injector Plates:
- Benzersiz Tasarım Özgürlüğü: AM allows engineers to escape the constraints of traditional manufacturability. This means designing injector faces with highly optimized orifice patterns for superior atomization and mixing, tailored precisely to the engine’s combustion dynamics.
- Integrated Cooling: Perhaps the most significant advantage is the ability to incorporate intricate, conformal regenerative cooling channels directly within the injector plate structure. These channels can follow complex paths, maximizing heat transfer efficiency and allowing the plate to withstand higher combustion temperatures, leading to potentially higher engine performance. Met3dp’s expertise ensures these complex internal geometries are realized with high fidelity.
- Parça Konsolidasyonu: An injector plate assembly traditionally consisting of numerous machined parts, seals, and brazed joints can often be redesigned and printed as a single, monolithic component. This drastically reduces the number of potential leak paths and failure points, enhancing reliability while often lowering assembly time and costs. This aligns with industry demand for robust aerospace component suppliers.
- Hafifletme: Utilizing topology optimization algorithms during the design phase, material can be placed only where structurally necessary, significantly reducing the component’s weight without compromising strength. This is particularly valuable for upper stages and spacecraft where every gram saved translates to increased payload capacity or delta-v (change in velocity).
- Hızlı Prototipleme ve Yineleme: The speed at which designs can be modified and reprinted allows engineering teams to test multiple injector configurations quickly and affordably. This accelerates the learning cycle and leads to more optimized final designs compared to the slower, more expensive iteration process with traditional methods. This agility makes AM an ideal choice for companies seeking advanced manufacturing solutions.
By leveraging these metal AM benefits, aerospace companies can develop rocket engines that are lighter, more efficient, more reliable, and brought to market faster. Choosing an experienced additive manufacturing vs traditional technology provider like Met3dp, with proven capabilities in handling complex geometries and high-performance materials, is crucial for realizing the full potential of AM for these critical components.
Material Spotlight: IN625 & IN718 Nickel Superalloys for Extreme Environments
The selection of materials for rocket injector plates is driven by the extreme conditions within a liquid rocket engine: temperatures soaring potentially thousands of degrees Celsius near the combustion zone, immense pressures, steep thermal gradients, and exposure to chemically reactive fuels and oxidizers. Only a select few materials can withstand this onslaught reliably. Nikel süper alaşımları, specifically IN625 (Inconel 625) ve IN718 (Inconel 718), have become materials of choice for additively manufactured injector plates due to their exceptional combination of properties.
Understanding Nickel Superalloys:
Nickel superalloys are a class of metals based primarily on nickel, with significant additions of elements like chromium, iron, niobium, molybdenum, and titanium. These alloying elements create a complex microstructure that provides outstanding mechanical strength, resistance to thermal creep deformation, good surface stability, and exceptional corrosion and oxidation resistance, particularly at elevated temperatures.
Inconel 625 (IN625): The Corrosion-Resistant Workhorse
- Anahtar Özellikler: IN625 is renowned for its superb corrosion resistance in a wide range of aggressive environments, including resistance to oxidation and scaling at high temperatures. It possesses high strength and toughness from cryogenic temperatures up to around 815°C (1500°F). It also exhibits excellent fatigue strength and resistance to chloride-ion stress-corrosion cracking. Crucially for additive manufacturing, IN625 generally demonstrates good printability and weldability (important for post-processing repairs if needed).
- Why for Injector Plates: Its outstanding corrosion resistance is vital for handling various propellant combinations, some of which can be highly corrosive. Its strength and toughness ensure structural integrity under high pressure and thermal cycling. While not as strong as IN718 at the highest temperatures, its overall balance of properties and processability makes it a common choice, especially where extreme corrosion is a primary concern.
Inconel 718 (IN718): The High-Temperature Strength Champion
- Anahtar Özellikler: IN718 is arguably the most widely used nickel superalloy. Its defining characteristic is its exceptional strength at elevated temperatures, maintaining high tensile, yield, and creep-rupture strength up to approximately 700°C (1300°F), and usable strength up to 980°C (1800°F). This is achieved through precipitation hardening (age hardening) heat treatments after printing. It also possesses good corrosion resistance and excellent yorulma ömrü. While slightly more challenging to print than IN625 due to its susceptibility to solidification cracking if parameters are not optimized, established processes yield excellent results.
- Why for Injector Plates: For injector plates operating closer to the intense heat of the combustion chamber or in very high-pressure engines, the superior high-temperature strength and creep resistance of IN718 are critical. It allows the injector plate to maintain its shape and integrity under severe thermal and mechanical loads over time.
Comparative Properties (Typical Values):
Mülkiyet | IN625 (Annealed) | IN718 (Age Hardened) | Significance for Injector Plates |
---|---|---|---|
Yield Strength (RT) | ~520 MPa (75 ksi) | ~1035 MPa (150 ksi) | Resistance to deformation under pressure. |
Ultimate Tensile (RT) | ~930 MPa (135 ksi) | ~1240 MPa (180 ksi) | Maximum stress before fracture. |
Yield Strength (650°C) | ~380 MPa (55 ksi) | ~895 MPa (130 ksi) | Strength retention at operating temperatures (IN718 superior). |
Max Operating Temp. | Up to ~815°C (1500°F) | Up to ~700°C (1300°F) (High Strength) | Defines the thermal limits of the material under load. |
Korozyon Direnci | Mükemmel | Çok iyi | Crucial for propellant compatibility and resisting combustion gases. |
Sürünme Direnci | İyi | Mükemmel | Resistance to slow deformation under sustained high temp/stress. |
Yorgunluk Ömrü | Mükemmel | Mükemmel | Durability under cyclic loading (engine starts/stops). |
Yazdırılabilirlik | Generally Good | Good (Requires Careful Control) | Ease of processing via additive manufacturing. |
Sayfalara Aktar
Met3dp’s Material Advantage:
The performance of the final 3D printed part is heavily dependent on the quality of the initial metal powder. As a leading metal tozu tedarikçisi, Met3dp utilizes industry-leading gaz atomizasyonu and Plasma Rotating Electrode Process (PREP) technologies. These advanced methods produce Met3dp metal powders, including IN625 and IN718, with key characteristics essential for high-quality additive manufacturing:
- Yüksek Küresellik: Spherical powder particles flow easily and pack densely in the powder bed, leading to more uniform layers and final parts with higher density and better mechanical properties.
- Good Flowability: Ensures consistent powder deposition across the build plate, crucial for process stability and dimensional accuracy.
- Controlled Particle Size Distribution (PSD): Optimized PSD ensures good packing density and resolution for fine features.
- Low Satellite Content: Minimizes irregularities that can affect flowability and packing.
- Yüksek Saflıkta: Reduces inclusions and contaminants that could compromise material properties and performance.
By combining the inherent advantages of IN625 and IN718 with meticulously produced, high-quality powders, Met3dp provides the foundation for manufacturing rocket injector plates that meet the stringent demands of the aerospace industry, ensuring reliability and performance in the most critical applications. Choosing the right yüksek sıcaklık malzemeleri and ensuring their quality through advanced powder manufacturing is paramount for mission success.
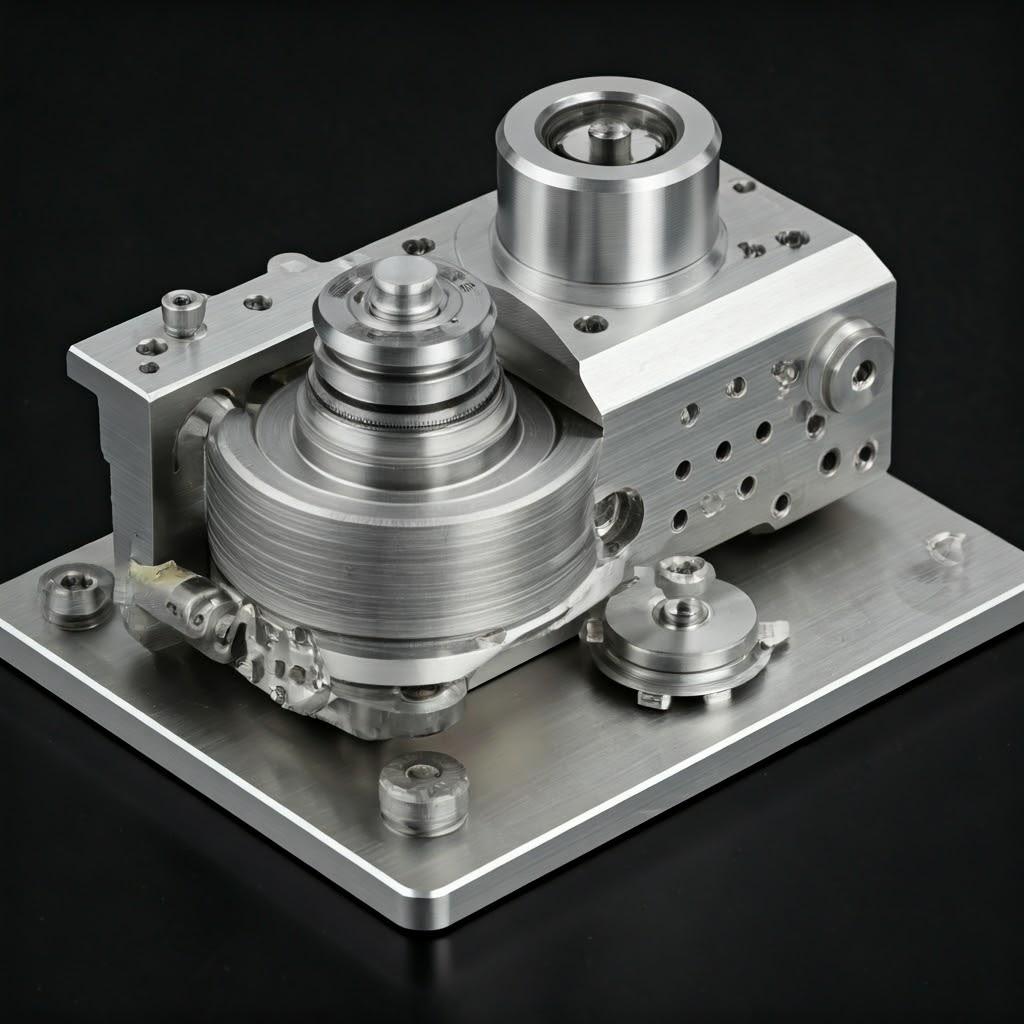
Design for Additive Manufacturing (DfAM): Optimizing Injector Plates for 3D Printing Success
Successfully leveraging metal 3D baskı for rocket injector plates requires more than simply converting a traditional design file into an AM-compatible format. It demands a fundamental shift in design thinking, embracing the principles of Design for Additive Manufacturing (DfAM). DfAM is not just about making a part printable; it’s about strategically utilizing the unique capabilities of AM to enhance performance, reduce weight, minimize post-processing, and ultimately create a superior component. Failing to apply DfAM principles often leads to printing failures, extensive post-processing requirements, suboptimal performance, and increased costs – negating many of the potential benefits of AM.
For rocket injector plates, with their complex internal features and critical performance requirements, DfAM is paramount. Here are key considerations for optimizing these components for additive success:
- Embrace Geometric Freedom for Functionality:
- Internal Channels: Instead of straight, drilled cooling channels common in traditional designs, AM allows for smooth, curved, conformal channels that follow the contours of the injector face or combustion chamber interface. This maximizes heat transfer efficiency. Design channels with smooth bends (avoiding sharp corners which create stress concentrations and flow issues) and consider teardrop or diamond shapes for horizontal channels to make them more self-supporting during the build process. Minimum printable channel diameters depend on the machine and parameters but are typically around 0.5mm – 1mm.
- Injection Orifices: Optimize the shape, angle, and grouping of injection orifices beyond what traditional machining allows. Explore non-circular orifice designs or intricate patterns aimed at enhancing propellant atomization and mixing based on Computational Fluid Dynamics (CFD) analysis.
- Manage Overhangs and Critical Angles:
- Powder Bed Fusion processes require support structures for features overhanging the build plate at angles typically less than 45 degrees from the horizontal. Relying heavily on supports increases print time, material usage, and post-processing effort (support removal).
- Strategy: Orient the part on the build plate strategically to minimize the number and extent of overhangs. Where possible, design features to be self-supporting by using chamfers or fillets to increase the angle above the critical threshold. Redesign features like horizontal internal cavities into more printable shapes (e.g., diamond or teardrop).
- Optimize Wall Thickness:
- AM processes have limitations on minimum printable wall thickness (often around 0.4mm – 0.8mm, depending on the specific machine and material). Ensure all walls meet this minimum requirement.
- Balancing Act: Thicker walls provide more strength but add weight and increase print time/cost. Use Finite Element Analysis (FEA) to determine stress distributions and optimize wall thicknesses, making them thicker only where necessary for structural integrity or pressure containment.
- Strategic Support Structure Planning:
- While minimizing supports is ideal, they are often unavoidable, especially for complex injector geometries.
- DfAM Approach: Design support structures concurrently with the part. Plan for supports that are strong enough to prevent warping but designed for relatively easy removal without damaging critical surfaces (like sealing faces or injector orifices). Use features like perforation or specific contact point designs to facilitate removal. Consider accessibility for removal tools (manual or machining).
- Leverage Lightweighting Techniques:
- Topology Optimization: Use software tools to computationally determine the most efficient material distribution to meet structural requirements, removing material from low-stress areas. This can lead to significant weight savings, often resulting in organic-looking structures.
- Kafes Yapılar: Incorporate internal lattice structures in lower-stress regions to further reduce weight while maintaining required stiffness. This is particularly useful for the main body of the injector plate.
- Minimize Stress Concentrations:
- Sharp internal corners act as stress raisers, potentially leading to fatigue failure under cyclic loading (engine starts/stops).
- Çözüm: Incorporate generous fillets and smooth transitions between features to distribute stress more evenly. This is easily achieved with the design freedom of AM.
- Integrate Simulation Early:
- Kullanım CFD analysis to simulate propellant flow through the designed injection orifices and cooling channels, iterating on the design to achieve desired performance before committing to printing.
- Kullanım FEA to predict thermal and mechanical stresses during operation, ensuring the design can withstand the loads. Build process simulation can also predict potential warping and residual stress issues, allowing for design or orientation adjustments.
By proactively applying these DfAM principles, engineering teams can unlock the full potential of additive manufacturing, creating rocket injector plates that are not only manufacturable but also optimized for performance, weight, and reliability. Collaborating with an experienced AM provider like Met3dp, who understands the nuances of 3D printing design guidelines ve manufacturability analysis, is key to navigating the complexities of DfAM for such critical havacılık ve uzay Bileşenler.
Achieving Precision: Tolerances, Surface Finish, and Dimensional Accuracy in 3D Printed Injectors
While metal additive manufacturing offers remarkable geometric freedom, understanding its achievable precision is crucial for managing expectations and planning necessary post-processing steps, especially for high-performance components like rocket injector plates where tight control over dimensions and surface characteristics is vital. Key aspects include tolerance, surface finish, and overall dimensional accuracy.
- Tolerance: This refers to the permissible limit or limits of variation in a physical dimension. In metal AM (specifically PBF processes like SLM/DMLS), typical achievable ‘as-printed’ tolerances for well-calibrated machines and optimized processes are often in the range of:
- +/- 0.1 mm to +/- 0.2 mm for smaller features (e.g., below 100 mm).
- +/- 0.1% to +/- 0.2% for larger dimensions.
- It’s important to note these are general guidelines; specific tolerances depend heavily on the part geometry, material (nickel superalloys can be prone to thermal stress), build orientation, machine calibration, and process parameters. Achieving tighter tolerances often requires post-processing machining.
- Yüzey İşlemi (Pürüzlülük): This describes the texture of a surface, typically quantified by the arithmetic average roughness (Ra).
- As-Printed: The ‘as-printed’ surface finish of PBF parts is inherently rougher than machined surfaces due to the layer-by-layer process and partially melted powder particles adhering to the surface. Typical Ra values can range from 6 µm to over 25 µm, heavily influenced by:
- Oryantasyon: Upward-facing surfaces tend to be smoother than downward-facing surfaces (which are influenced by support structures) or vertical walls (showing layer lines).
- Parameters: Layer thickness, laser power, scan speed, and powder characteristics all affect the final surface texture.
- Implications for Injectors: Rough internal surfaces in cooling channels or injection orifices can impede flow, increase pressure drop, and potentially affect atomization characteristics. Rough sealing surfaces will not provide a reliable seal without further treatment. Therefore, critical surfaces almost always require finishing operations.
- As-Printed: The ‘as-printed’ surface finish of PBF parts is inherently rougher than machined surfaces due to the layer-by-layer process and partially melted powder particles adhering to the surface. Typical Ra values can range from 6 µm to over 25 µm, heavily influenced by:
- Boyutsal Doğruluk: This refers to the degree of conformity of a manufactured part to its intended design dimensions. Factors influencing overall dimensional accuracy in metal AM include:
- Machine Calibration: Precise laser spot positioning, scanner calibration, and build platform leveling are essential.
- Thermal Effects: The rapid heating and cooling inherent in PBF can cause thermal expansion and contraction, leading to internal stresses and potential warping or distortion, especially in large or complex parts made from materials like IN625/IN718. Careful thermal management during the build and appropriate support strategies are critical.
- Katman Kalınlığı: Thinner layers generally allow for finer feature resolution and potentially better accuracy but increase build time.
- Support Strategy: Improperly designed or placed supports can fail to prevent warping or may cause distortion upon removal.
- Toz Kalitesi: Consistent particle size and morphology contribute to more stable melting and solidification behavior.
Achieving Required Precision for Injector Plates:
Given the critical nature of injector plates, achieving the necessary precision often involves a combination of AM process control and targeted post-processing:
- AM Process Optimization: Utilizing high-resolution machines, fine-tuned process parameters specific to IN625/IN718, meticulous machine calibration, and optimized build orientation and support strategies lay the foundation for the best possible ‘as-printed’ accuracy. Met3dp emphasizes reliable additive manufacturing through rigorous process control and adherence to stringent quality standards.
- Targeted Post-Machining: For critical features like sealing surfaces, interfaces with other engine components, and precise injection orifice diameters and geometries, post-processing machining (e.g., CNC milling, turning, EDM) is typically required to achieve the final metal 3D printing tolerances and surface finish specified by Geometric Dimensioning and Tolerancing (GD&T) requirements. Design engineers must account for machining allowances (extra material) in the AM design for these features.
- Yüzey İşlemi: Techniques like abrasive flow machining (AFM), micro-machining, or electro-chemical polishing may be used to improve the surface finish Ra of internal channels or complex external surfaces where conventional machining access is limited.
- Rigorous Inspection: Kapsayıcı quality control 3D printing measures, including CMM (Coordinate Measuring Machine) checks and potentially CT scanning, are used to verify dimensional accuracy against the design specifications.
By understanding the inherent capabilities and limitations of AM regarding precision and planning for necessary finishing steps, aerospace companies can confidently employ 3D printing to produce highly complex and functional rocket injector plates that meet demanding precision manufacturing aerospace standards. Met3dp’s commitment to Met3dp accuracy ensures parts are produced with the highest fidelity possible within the AM process, providing a solid basis for final machining and finishing.
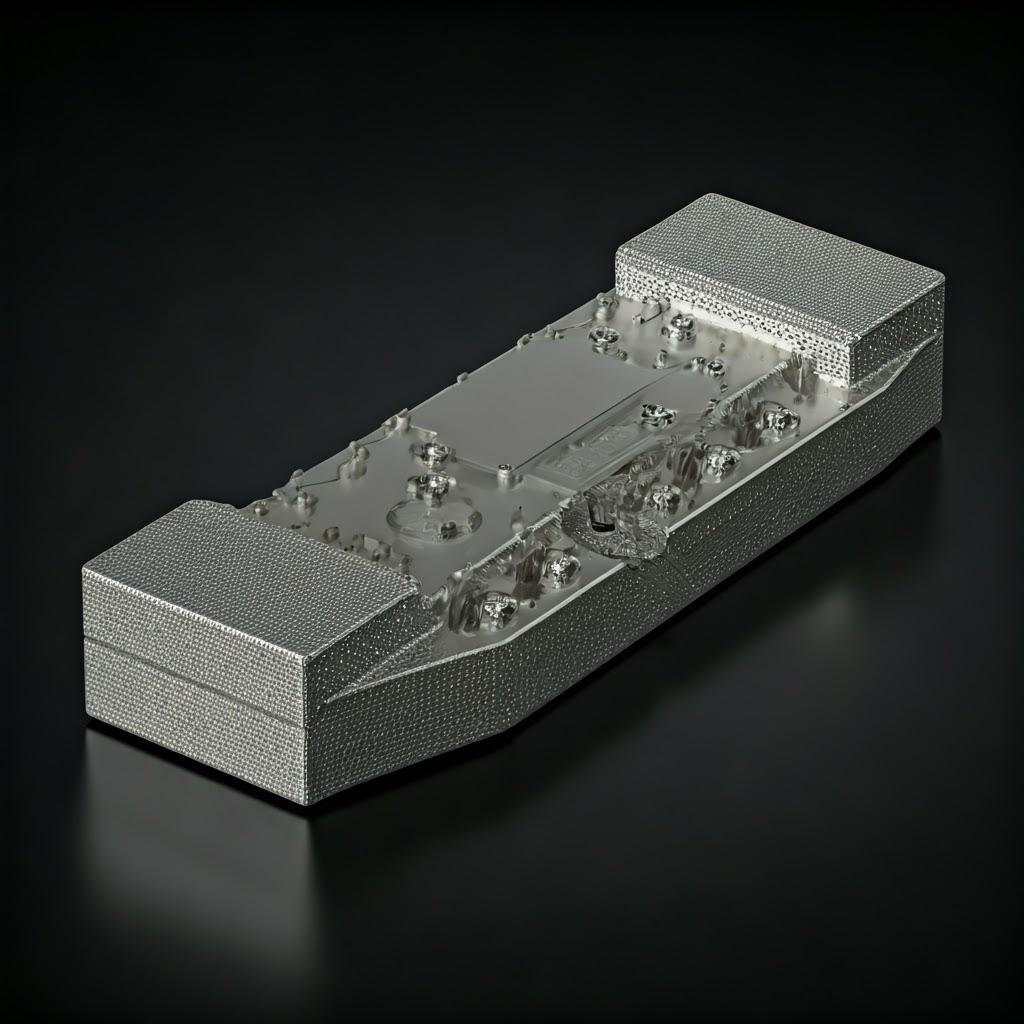
Essential Post-Processing Steps for Mission-Critical Injector Plates
The journey of a 3D printed rocket injector plate doesn’t end when the printer stops. A series of crucial post-processing metal AM steps are required to transform the ‘as-printed’ part into a flight-ready component, ensuring it possesses the necessary mechanical properties, dimensional accuracy, surface characteristics, and internal integrity. For mission-critical applications using nickel superalloys like IN625 and IN718, these steps are non-negotiable and require careful execution.
Key post-processing stages typically include:
- Stres Giderici Tavlama:
- Amacımız: The rapid heating and cooling cycles during the PBF process induce significant residual stresses within the printed part. If not relieved, these stresses can cause warping or cracking, especially when the part is cut from the build plate or during subsequent machining.
- Süreç: The entire build plate with the part(s) still attached is typically heated in a furnace to a specific temperature (below the aging temperature for IN718, e.g., 850-980°C for IN625, potentially higher for IN718 depending on the goal), held for a defined time, and then slowly cooled. This allows the internal stresses to relax without significantly altering the microstructure.
- Importance: This is often the very first step after printing and is critical for dimensional stability.
- Removal from Build Plate & Support Removal:
- Süreç: Once stress-relieved, the part is separated from the build plate, usually using wire EDM (Electrical Discharge Machining) or a band saw. Subsequently, the support structures must be removed.
- Techniques: This can involve manual breaking (for well-designed, accessible supports), cutting with hand tools, or precision machining (milling, grinding, EDM) for supports in difficult-to-reach areas or on critical surfaces.
- Zorluklar: Support removal can be labor-intensive and risks damaging the part surface if not done carefully. Support removal strategies planned during the DfAM phase are vital.
- Heat Treatment (Solution Annealing & Aging – Especially for IN718):
- Amacımız: To achieve the final desired mechanical properties (strength, hardness, ductility, creep resistance) optimized for the demanding operating environment. Nickel superalloys, particularly precipitation-hardenable ones like IN718, derive their exceptional high-temperature strength from carefully controlled heat treatment nickel alloys.
- Süreç:
- Çözelti Tavlama: Heating the part to a high temperature (e.g., 950-1050°C for IN718) to dissolve precipitates and homogenize the microstructure, followed by rapid cooling (quenching).
- Yaşlanma (Çökelme Sertleşmesi): Reheating the part to one or more intermediate temperatures (e.g., 720°C followed by 620°C for IN718) for specific durations. This causes fine, strengthening precipitates (gamma prime and gamma double prime phases in IN718) to form within the metal matrix.
- Importance: Absolutely critical for developing the high-temperature strength and creep resistance that makes IN718 suitable for injector plates. IN625 is typically used in the annealed state but may undergo aging for specific property enhancements.
- Sıcak İzostatik Presleme (HIP):
- Amacımız: To eliminate internal porosity (like small gas bubbles or lack-of-fusion voids) that might remain after printing, thereby improving fatigue life, fracture toughness, and overall material integrity.
- Süreç: The part is placed in a specialized vessel and subjected to both high temperature (below melting point but high enough for diffusion, e.g., 1100-1200°C) and high-pressure inert gas (typically Argon, e.g., 100-200 MPa) simultaneously for several hours. The combination of heat and pressure causes internal voids to collapse and diffusionally bond closed.
- Importance: Often considered mandatory for critical aerospace components (‘Class A’ or ‘Fracture Critical’ parts) as it significantly enhances reliability and mechanical properties, bringing them closer to wrought material performance. HIP benefits include achieving near-full theoretical density.
- Final Machining & Surface Finishing:
- Amacımız: To achieve critical dimensional tolerances, specific surface finishes on sealing faces or flow paths, and remove any surface irregularities remaining after support removal or HIP.
- Süreç: CNC machining 3D parts (milling, turning) is used for precise dimensional control of interfaces and features. Specialized techniques like abrasive flow machining (AFM) or electro-chemical polishing may be employed for smoothing internal channels or complex surfaces. Surface polishing techniques might be used on external surfaces for aerodynamic or other reasons.
- Importance: Ensures proper fit, sealing, and optimal fluid dynamic performance.
- Inspection and Non-Destructive Testing (NDT):
- Amacımız: To verify the part meets all dimensional specifications and is free from internal or external defects that could compromise performance or safety. This is a cornerstone of quality assurance AM.
- Techniques:
- Dimensional Inspection: Using CMMs, 3D scanners, or traditional metrology tools.
- CT Scanning Inspection (Computed Tomography): Increasingly used for AM parts to non-destructively visualize and inspect internal geometries (like cooling channels) and detect internal flaws (porosity, inclusions).
- Surface Defect Inspection: Visual inspection, dye penetrant testing (DPT), or fluorescent penetrant inspection (FPI).
- Other NDT methods like ultrasonic testing (UT) or radiographic testing (RT) may also be employed depending on criticality and specifications.
- Importance: Provides final verification that the injector plate is fit for purpose before assembly into the rocket engine.
Successfully navigating these intricate post-processing steps requires significant expertise, specialized equipment, and robust quality control systems. Partnering with a full-service provider like Met3dp, experienced in the end-to-end manufacturing workflow from powder to finished, inspected component, ensures that 3D printed rocket injector plates achieve the demanding standards required for havacılık ve uzay uygulamalar.
Common Challenges in AM for Injector Plates and Mitigation Strategies
While metal additive manufacturing offers tremendous advantages for producing complex rocket injector plates, the process is not without its challenges. Understanding these potential hurdles and implementing effective mitigation strategies is crucial for consistent success and achieving high-quality, reliable components. Collaborating with experienced AM providers who have honed their processes, like Met3dp, can significantly de-risk production.
Here are some common challenges and how they are addressed:
- Residual Stress and Warping:
- Meydan okumak: The intense, localized heating and rapid cooling inherent in PBF processes create significant thermal gradients, leading to the buildup of internal residual stresses within the part. These stresses can cause distortion (warping) during the build, cracking, or unexpected movement after the part is removed from the build plate. Nickel superalloys, with their relatively high thermal expansion and strength, can be particularly susceptible.
- Mitigation Strategies:
- Optimized Build Orientation: Orienting the part to minimize large flat surfaces parallel to the build plate and manage thermal gradients.
- Sağlam Destek Yapıları: Well-designed supports anchor the part securely to the build plate, resisting warping forces during the build. Finite element simulation can help optimize support placement and design.
- Süreç Parametre Optimizasyonu: Fine-tuning laser power, scan speed, and scan strategy (e.g., using an island scanning pattern) to manage heat input and reduce stress accumulation.
- Termal Yönetim: Maintaining a consistent, elevated temperature in the build chamber reduces thermal gradients.
- Immediate Stress Relief: Performing a stress relief annealing cycle önce removing the part from the build plate is critical for dimensional stability.
- Gözeneklilik:
- Meydan okumak: Small voids or pores can form within the printed material, potentially degrading mechanical properties like fatigue life and fracture toughness. Common types include:
- Lack-of-Fusion Porosity: Insufficient melting between layers or adjacent scan tracks, often due to low energy input or improper powder spreading.
- Keyhole Porosity: Gas bubbles trapped during excessive melting caused by too high energy density, forming deep, unstable melt pools.
- Mitigation Strategies:
- Optimize Edilmiş Süreç Parametreleri: Rigorous development and control of laser power, scan speed, hatch spacing, and layer thickness are essential to ensure complete melting and stable melt pool behavior. This is a core competency of additive manufacturing troubleshooting.
- Yüksek Kaliteli Toz: Using highly spherical, flowable powder with a controlled particle size distribution, like the gas atomization powder produced by Met3dp, ensures uniform powder bed density and consistent melting. Met3dp’s commitment to quality starts with the powder.
- Kontrollü Atmosfer: Maintaining a high-purity inert gas atmosphere (Argon or Nitrogen) in the build chamber minimizes oxidation and gas pickup.
- Sıcak İzostatik Presleme (HIP): As mentioned earlier, HIP is highly effective at closing internal pores and achieving near-full density, often mandated for critical parts.
- Meydan okumak: Small voids or pores can form within the printed material, potentially degrading mechanical properties like fatigue life and fracture toughness. Common types include:
- Support Removal Difficulties:
- Meydan okumak: Removing support structures, especially from complex internal geometries or delicate features on injector plates, can be time-consuming, costly, and risks damaging the part surface.
- Mitigation Strategies:
- DfAM Focus: Designing parts to be as self-supporting as possible is the best approach. Planning support locations and types for ease of access and removal during the design stage.
- Specialized Removal Techniques: Employing wire EDM, multi-axis CNC machining, or electrochemical methods for precise, non-damaging removal where manual access is impossible.
- Nitelikli Teknisyenler: Experienced personnel are crucial for careful manual support removal.
- Achieving Fine Features and Internal Channels:
- Meydan okumak: Reproducing very fine details, sharp edges, or small-diameter internal channels (like those needed for cooling or injection) pushes the limits of PBF resolution. Powder adhesion, melt pool dynamics, and heat dissipation can affect the fidelity of small features.
- Mitigation Strategies:
- High-Resolution Machines: Utilizing AM systems with smaller laser spot sizes and thinner layer capabilities.
- Parametre Optimizasyonu: Fine-tuning parameters specifically for feature resolution.
- Design Adjustments: Slightly modifying designs (e.g., minimum channel diameters, feature aspect ratios) based on process limitations identified through prototyping or simulation.
- Hibrit Üretim: Considering approaches where AM creates the overall complex shape, and critical fine features are finished using micro-machining or EDM.
- Material Property Consistency:
- Meydan okumak: Ensuring that the mechanical properties (strength, ductility, fatigue life) of the final AM part are consistent throughout the component and from build to build is critical for aerospace applications. Variations can arise from fluctuations in process parameters, powder quality, or heat treatment.
- Mitigation Strategies:
- Strict Process Control: Implementing rigorous quality management systems (like AS9100) covering machine calibration, parameter monitoring, and environmental controls.
- Toz Yaşam Döngüsü Yönetimi: Controlling metal powder handling safety and quality throughout its lifecycle, including incoming inspection, storage, use, sieving/recycling protocols, and batch tracking to prevent contamination or degradation.
- Standardized Post-Processing: Ensuring consistent execution of stress relief, heat treatment, and HIP cycles according to validated procedures.
- Material Testing: Regular testing of witness coupons printed alongside parts to verify mechanical properties for each build or batch.
By acknowledging these metal AM challenges and proactively implementing robust mitigation strategies grounded in deep process knowledge and quality control, manufacturers like Met3dp can reliably produce high-integrity rocket injector plates using IN625 and IN718, meeting the stringent requirements of the aerospace industry.
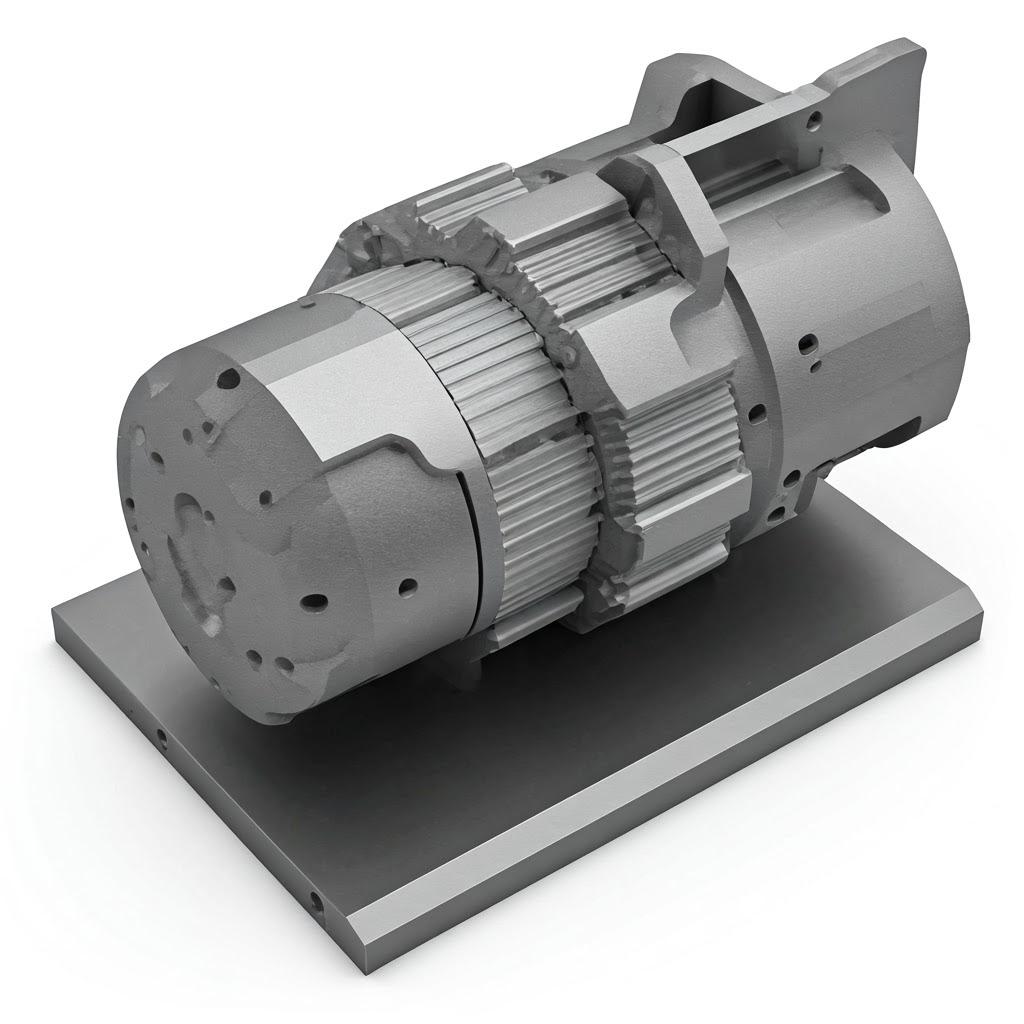
Partner Selection: Choosing the Right Metal AM Service Provider for Aerospace Components
Selecting the right manufacturing partner is always critical, but when dealing with mission-critical aerospace components like rocket injector plates produced via metal additive manufacturing, the stakes are exceptionally high. The complexity of the technology, the demanding nature of the materials (IN625/IN718), and the stringent quality requirements of the aerospace industry necessitate partnering with a specialist metal AM service provider possessing deep expertise and robust systems. Simply having a metal 3D printer is not enough; true capability lies in the integration of materials science, process control, engineering support, and quality assurance.
For procurement managers and engineering teams evaluating potential suppliers for aerospace 3D printing, here are key criteria to consider:
- Aerospace Certifications & Compliance:
- AS9100 Certification: This is the internationally recognized Quality Management System (QMS) standard for the Aviation, Space, and Defense industries. It demonstrates a provider’s commitment to quality, traceability, and continuous improvement, tailored to aerospace requirements. Lack of AS9100 is often a non-starter for critical components.
- NADCAP Accreditation: While AS9100 covers the overall QMS, NADCAP (National Aerospace and Defense Contractors Accreditation Program) provides specific accreditation for special processes like heat treatment, non-destructive testing (NDT), and potentially welding or materials testing. Ensure the provider or their approved subcontractors hold relevant NADCAP accreditations for required post-processing steps.
- Material Expertise (Nickel Superalloys):
- Demonstrated experience specifically with IN625, IN718, and potentially other relevant superalloys is crucial. This includes:
- Toz İşleme: Strict protocols for storing, handling, sieving, and recycling these reactive powders to maintain purity and prevent contamination.
- Parameter Development: Proven, validated process parameters optimized for density, microstructure, and mechanical properties for the specific alloys and machines used.
- Post-Processing Knowledge: In-depth understanding of the required stress relief and heat treatment cycles (especially complex aging cycles for IN718) to achieve desired properties. Met3dp’s foundation in producing high-quality gas atomization powder provides a distinct advantage here.
- Demonstrated experience specifically with IN625, IN718, and potentially other relevant superalloys is crucial. This includes:
- Equipment Capability & Process Control:
- Appropriate Technology: Access to well-maintained, industrial-grade PBF machines (SLM, DMLS, or SEBM depending on the application) suitable for nickel superalloys.
- Build Volume & Accuracy: Machines capable of handling the required part size and achieving necessary precision.
- Süreç İzleme: Ideally, machines equipped with in-situ monitoring capabilities (e.g., melt pool monitoring, thermal imaging) to provide real-time quality indicators.
- Calibration & Maintenance: Rigorous schedules for machine calibration and preventative maintenance to ensure consistent performance.
- Robust Quality Management System (QMS):
- Beyond certifications, evaluate the depth and implementation of their QMS. This includes traceability (powder batch to final part), documentation control, handling of non-conformances, corrective action processes, and comprehensive inspection procedures.
- Engineering & DfAM Support:
- Look for a partner who can provide more than just “print-to-file” services. Valuable partners offer DfAM consultation, helping optimize designs for manufacturability, performance, and cost-effectiveness. Simulation capabilities (process, thermal, stress) are also beneficial.
- Kapsamlı İşlem Sonrası Yetenekleri:
- Assess their ability to manage the entire post-processing workflow, either in-house or through rigorously qualified partners. This includes stress relief, support removal, heat treatment (with certified furnaces), HIP, precision machining, surface finishing, and comprehensive NDT. A vertically integrated provider often offers better control and potentially shorter lead times.
- Track Record & Experience:
- Request evidence of successful projects involving similar complexity, materials, and industry standards. Case studies, references, and demonstrated experience in the aerospace sector build confidence.
Met3dp embodies these characteristics, positioning itself as a trusted AM partner for demanding aerospace applications. With decades of collective expertise, industry-leading equipment, advanced material capabilities rooted in our own powder production, and a commitment to additive manufacturing quality control evidenced by our comprehensive solutions, Met3dp collaborates closely with clients from design through to finished part validation. Our Met3dp capabilities span the entire additive manufacturing ecosystem, providing the reliability and expertise required for flight-critical components like rocket injector plates. When submitting an RFQ additive manufacturing request, ensuring potential partners meet these stringent criteria is paramount for successful procurement additive manufacturing.
Understanding Cost Drivers and Lead Times for 3D Printed Injector Plates
Budgeting and scheduling are critical aspects of any engineering project. When considering metal additive manufacturing for rocket injector plates, understanding the factors that influence cost and lead time is essential for effective planning and management. While AM offers significant long-term value through performance gains and design possibilities, the initial metal 3D printing cost factors and production timelines differ from traditional methods.
Key Cost Drivers:
The price of a 3D printed rocket injector plate is influenced by a complex interplay of factors:
- Material Consumption:
- Hacim: The sheer amount of material required for the part, including support structures, is a primary driver. Larger and denser parts cost more.
- Toz Maliyeti: Aerospace materials like IN625 and IN718 nickel superalloy powders are inherently expensive due to their composition and complex production processes. The material cost AM component is significant.
- Makine Zamanı (İnşa Zamanı):
- Part Volume & Height: The larger and taller the part, the longer it takes to print layer by layer.
- Karmaşıklık: Intricate features and extensive support structures increase the required scanning time for the laser or electron beam.
- Machine Rate: Industrial metal AM systems represent substantial capital investment, and their hourly operating rate (factoring in depreciation, maintenance, energy, inert gas, labor) is a major component of the additive manufacturing pricing model.
- Post-Processing Complexity:
- This can be a very significant portion of the total cost. Factors include:
- Destek Kaldırma: Labor-intensive, especially for complex internal supports requiring specialized techniques (e.g., EDM).
- Heat Treatment/HIP: Requires specialized furnaces/HIP units and long cycle times.
- İşleme: Precision CNC machining of multiple critical surfaces adds considerable cost.
- Yüzey İşlemi: Techniques like AFM for internal channels increase cost.
- NDT & Inspection: Comprehensive inspection (especially CT scanning) adds cost but is essential for quality assurance.
- This can be a very significant portion of the total cost. Factors include:
- Engineering & Setup:
- Initial design optimization (DfAM), simulation work, build preparation, and fixture design contribute to the cost, particularly for first articles or complex new designs.
- Quality Requirements:
- Higher criticality levels demanding more rigorous process control, documentation, traceability, and inspection naturally increase costs.
- Sipariş Hacmi:
- While setup costs remain, per-part costs can decrease with larger batch sizes due to efficiencies in build nesting, post-processing, and material usage. Inquire about wholesale 3D printing services veya volume production AM pricing for recurring orders.
Typical Lead Times:
Bu lead time additive manufacturing for a rocket injector plate, from final design approval to delivery of a finished, inspected part, can typically range from several weeks to a few months, depending heavily on complexity and requirements. Key contributing factors include:
- Design Finalization & Prep: DfAM review, simulation, support design, build file generation (few days to a week+).
- Baskı: Actual machine time can range from 2-3 days for smaller/simpler parts to over a week or even two for very large or complex injector plates built with fine resolution.
- İşlem sonrası: This often consumes the largest portion of the lead time:
- Stress Relief & Support Removal: 1-3 days.
- Heat Treatment Cycles: Can take several days including furnace time and controlled cooling.
- HIP Cycle: Typically adds 2-4 days (including setup and cycle time).
- Machining & Finishing: Highly variable, from a few days to several weeks depending on complexity and machine shop scheduling.
- NDT & Inspection: 1-5 days depending on the extent of testing required.
- Queue Time: The service provider’s current workload and machine availability.
- Nakliye: Standard shipping times apply.
For accurate budget planning aerospace projects, it is essential to obtain detailed quotes (RFQ 3D printing) based on final part geometry, material specifications, required tolerances, post-processing steps, and inspection criteria. Transparent communication with your AM partner regarding cost drivers and lead time expectations is vital for project success.
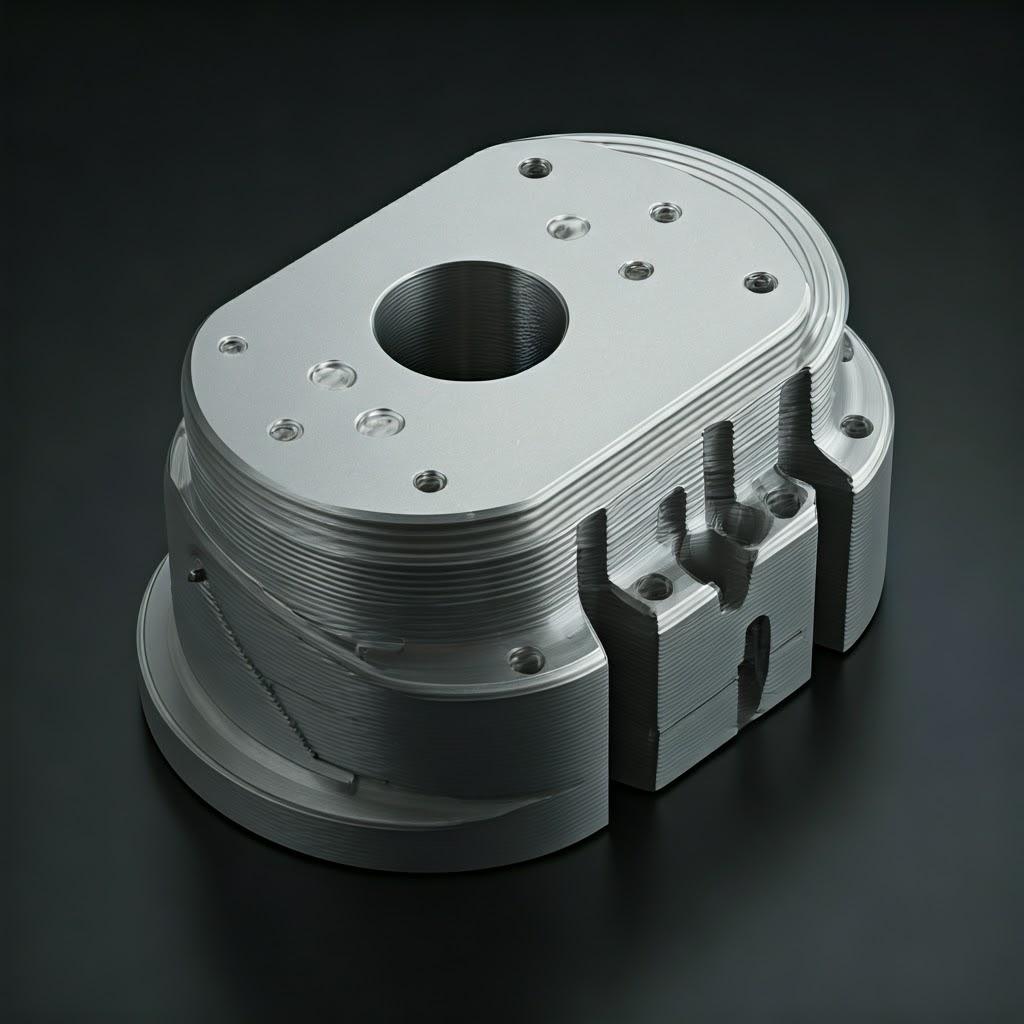
Frequently Asked Questions (FAQ) about 3D Printed Rocket Injectors
As metal additive manufacturing becomes increasingly adopted for critical aerospace components, engineers and procurement specialists often have questions about its application for rocket injector plates. Here are answers to some common queries:
Q1: How does the performance of an AM injector plate compare to one made by traditional casting or brazing?
- A: Additively manufactured injector plates offer the potential for superior performance. The design freedom allows for highly optimized injection patterns and integrated cooling channels that are difficult or impossible to achieve with casting or brazing. This can lead to improved combustion efficiency, enhanced stability, better thermal management, and potentially higher thrust-to-weight ratios due to part consolidation and lightweighting. However, achieving this potential requires rigorous design optimization (DfAM), process control, and thorough validation testing, including hot-fire tests, to confirm performance meets or exceeds requirements. The monolithic nature of AM parts also eliminates potential failure points associated with brazed joints.
Q2: What level of testing and validation is typically required for 3D printed flight hardware like injector plates?
- A: Qualification for flight is extremely rigorous, regardless of manufacturing method. For AM components, this typically involves a comprehensive component validation testing program that includes:
- Material Characterization: Extensive testing of material properties (tensile, fatigue, creep, fracture toughness) using samples printed alongside the part or representative coupons subjected to identical processing (including heat treatment/HIP).
- Process Validation: Demonstrating consistent process control and repeatability.
- Tahribatsız Muayene (NDT): Extensive use of CT scanning to verify internal geometry and detect defects, alongside surface NDT methods (FPI/DPT).
- Boyutsal Doğrulama: Confirming all critical dimensions meet specifications using CMM or other metrology tools.
- Proof Pressure Testing: Subjecting the part to pressures exceeding operational levels.
- Flow Testing: Verifying pressure drops and potentially spray patterns under simulated conditions.
- Hot-Fire Testing: Integrating the injector into a test engine and conducting multiple firings across various operating conditions to validate performance, stability, and durability under realistic thermal and pressure loads.
Q3: Can we simply take our existing injector design (made by machining/brazing) and print it using AM?
- A: While technically possible, a direct “print-to-file” conversion of a design optimized for traditional manufacturing is rarely the best approach and often leads to suboptimal results or printing challenges. To fully leverage the benefits of AM (complexity, consolidation, lightweighting) and ensure manufacturability (managing supports, stresses, wall thicknesses), a design conversion AM process incorporating DfAM principles is highly recommended. Redesigning the part with AM capabilities in mind from the outset yields the best outcomes. Collaboration with AM experts during this redesign phase is crucial.
Q4: What is the typical lifespan or reusability of 3D printed rocket injector plates?
- A: The expected lifespan and reusability depend entirely on the specific engine design, operating conditions (propellants, pressures, temperatures, number of cycles), the chosen material (IN625/IN718), the quality achieved during manufacturing and post-processing, and the qualification program it successfully undergoes. Metal AM durability, when processes are properly controlled and parts validated, can be excellent, potentially exceeding that of traditionally joined assemblies due to the monolithic structure eliminating joints. They are designed and tested to meet the mission requirements, which may involve single use for expendable launch vehicles or multiple uses (with inspections) for reusable engines or spacecraft thrusters. The goal is always to meet or exceed the required operational life defined by the engine program.
Bunlar 3D printed injector FAQs highlight the technical considerations involved. Addressing these points through careful design, manufacturing control, and rigorous testing ensures the reliability demanded by aerospace procurement queries.
Conclusion: Propelling the Future of Space Exploration with Advanced Additive Manufacturing
The rocket injector plate stands as a testament to the power of precision engineering in the unforgiving environment of space propulsion. As we push the boundaries of exploration and seek more efficient, reliable, and capable launch vehicles and spacecraft, the manufacturing technologies we employ must evolve. Metal additive manufacturing, particularly utilizing robust nickel superalloys like IN625 and IN718, represents a significant leap forward in producing these critical components.
The journey through this post has highlighted the compelling advantages AM brings to injector plate production:
- Eşsiz Tasarım Özgürlüğü: Enabling complex geometries for optimized atomization, mixing, and integrated cooling.
- Geliştirilmiş Performans: Potential for higher efficiency, better combustion stability, and improved thermal management.
- Parça Konsolidasyonu: Reducing complexity, weight, and potential failure points by creating monolithic structures.
- Rapid Innovation: Accelerating design iteration and development cycles compared to traditional methods.
Successfully harnessing these benefits requires navigating challenges related to design optimization (DfAM), precision control, rigorous post-processing, and meticulous quality assurance. The choice of material is paramount, with IN625 and IN718 offering the necessary high-temperature strength and corrosion resistance, especially when derived from high-quality powders and processed under stringent controls.
Metal AM is undeniably shaping the future of aerospace manufacturing. Its ability to create highly optimized, complex components faster and potentially lighter than ever before makes it a key enabler for next-generation propulsion systems and ambitious space exploration technology. Bu additive manufacturing innovation demonstrated in producing components like injector plates directly contributes to more capable and cost-effective access to space.
As a leader in metal additive manufacturing equipment and high-performance powders, Met3dp provides the comprehensive solutions and deep expertise needed to turn advanced designs into flight-ready hardware. We partner with aerospace innovators to leverage the full potential of AM, from material selection and DfAM support to optimized printing and final validation.
Ready to explore how Met3dp’s advanced additive manufacturing capabilities can elevate your next propulsion project?
Contact Met3dp today to discuss your requirements for rocket injector plates or other critical aerospace components. Let our expertise power your journey towards higher performance and reliability in space exploration.
Paylaş
MET3DP Technology Co, LTD, merkezi Qingdao, Çin'de bulunan lider bir katmanlı üretim çözümleri sağlayıcısıdır. Şirketimiz, endüstriyel uygulamalar için 3D baskı ekipmanları ve yüksek performanslı metal tozları konusunda uzmanlaşmıştır.
İşletmeniz için en iyi fiyatı ve özelleştirilmiş Çözümü almak için sorgulayın!
İlgili Makaleler
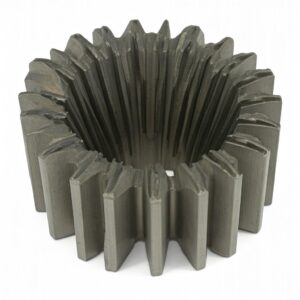
Yüksek Performanslı Nozul Kanat Segmentleri: Metal 3D Baskı ile Türbin Verimliliğinde Devrim
Daha Fazla Oku "Met3DP Hakkında
Son Güncelleme
Bizim Ürünümüz
BİZE ULAŞIN
Herhangi bir sorunuz var mı? Bize şimdi mesaj gönderin! Mesajınızı aldıktan sonra tüm ekibimizle talebinize hizmet edeceğiz.
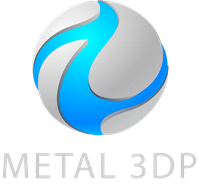
3D Baskı ve Katmanlı Üretim için Metal Tozları