UAV Mounting Plates in Lightweight Aluminum
İçindekiler
Introduction: Revolutionizing UAV Design with Advanced Mounting Plates
The Unmanned Aerial Vehicle (UAV), or drone, sector is experiencing exponential growth, transforming industries from logistics and agriculture to surveillance and cinematography. At the heart of these sophisticated flying machines lies a complex interplay of components, each critical to performance, reliability, and mission success. Among these, the humble UAV mounting plate plays a pivotal role, acting as the structural interface for securing essential payloads, sensors, cameras, and other equipment. While seemingly simple, the design and material composition of these plates directly impact the UAV’s overall weight, flight time, payload capacity, and operational stability.
Traditionally, mounting plates were manufactured using subtractive methods like CNC machining from billet materials. However, the relentless drive for enhanced performance – particularly longer flight durations and increased payload capabilities – necessitates lighter, stronger, and often more complex designs. This is where eklemeli üretim (AM), specifically metal 3D baskı, enters the picture, offering unprecedented design freedom and the ability to produce highly optimized, lightweight components. Utilizing advanced aluminum alloys, manufacturers can now create mounting plates that are significantly lighter than their machined counterparts without compromising strength or structural integrity. This shift towards advanced manufacturing techniques, like those pioneered by industry leaders such as Met3dp, is not just an incremental improvement; it represents a fundamental revolution in UAV component design and production, enabling next-generation drone capabilities. For procurement managers and engineers in the aerospace, defense, and commercial drone industries, understanding the potential of metal 3D printed UAV mounting plates is crucial for staying competitive and pushing the boundaries of aerial innovation. This article delves into the specifics of using lightweight aluminum alloys like AlSi10Mg and A7075 via additive manufacturing for creating superior UAV mounting solutions.
Core Functions: What Are UAV Mounting Plates Used For?
UAV mounting plates are fundamental structural components designed to securely attach various payloads and equipment to the drone’s airframe. Their primary function is to provide a stable, reliable interface, ensuring that attached devices remain fixed during flight maneuvers, vibrations, and potential impacts. The specific application dictates the design complexity, load-bearing requirements, and integration features of the mounting plate. Key use cases span across diverse UAV applications:
- Payload Integration: This is the most common function. Mounting plates serve as the primary attachment point for mission-specific payloads.
- Cameras & Imaging Systems: High-resolution cameras, thermal imagers, multispectral sensors for aerial photography, surveillance, inspection, and agricultural monitoring. The plate must ensure stability to prevent image blur and maintain sensor alignment.
- LiDAR & Surveying Equipment: Securely holding expensive and sensitive LiDAR units or GPS/GNSS receivers for mapping, surveying, and environmental monitoring. Vibration damping might be integrated into the plate design.
- Delivery Mechanisms: For logistics drones, plates might integrate hooks, clamps, or release mechanisms for package delivery.
- Scientific Instruments: Mounting specialized sensors for atmospheric research, environmental sampling, or other scientific data collection.
- Sensor Mounting: UAVs rely on numerous sensors for navigation, obstacle avoidance, and flight control.
- IMUs (Inertial Measurement Units): Plates provide a rigid base for IMUs, critical for accurate flight data.
- GPS/GNSS Antennas: Ensuring optimal placement and orientation for signal reception.
- Obstacle Avoidance Sensors: Mounting ultrasonic, infrared, or vision-based sensors at strategic locations around the airframe.
- Gimbal Brackets: Stabilized gimbals, which house cameras or other sensors, require robust mounting points. The plate acts as the interface between the gimbal mechanism and the UAV frame, needing to withstand dynamic loads and vibrations while allowing the gimbal its full range of motion. Custom gimbal brackets are often required depending on the specific gimbal and UAV model.
- Avionics & Electronics Housing: In smaller UAVs, mounting plates might double as enclosures or attachment points for flight controllers, power distribution boards, or communication systems.
- Structural Reinforcement: In some designs, mounting plates can also contribute to the overall structural rigidity of the UAV airframe, particularly around payload bays or attachment hardpoints.
- Customization and Modularity: Mounting plates facilitate drone customization. Standardized mounting patterns (e.g., Picatinny rails, specific hole patterns) allow users to easily swap payloads, enhancing the UAV’s versatility for different missions. B2B drone parts suppliers often offer various plate configurations to meet diverse integration needs.
The industries leveraging these functions are broad:
- Havacılık ve Savunma: Surveillance, reconnaissance, target acquisition, communications relays. Reliability and adherence to stringent standards (e.g., AS9100) are paramount. Defense drone applications often require robust mounting for sensitive equipment.
- Commercial Operations: Infrastructure inspection (bridges, power lines, wind turbines), precision agriculture, aerial mapping, cinematography, search and rescue, logistics. Cost-effectiveness and durability are key drivers.
- Araştırma ve Geliştirme: Providing flexible platforms for testing new sensors, payloads, and flight control algorithms.
Ultimately, the UAV mounting plate is far more than just a piece of metal; it’s an enabling component that allows the drone to perform its designated tasks effectively and reliably. The ability to customize these plates for specific UAV payload integration challenges is a critical factor in optimizing drone performance across all sectors. Procurement managers sourcing UAV components wholesale must consider the specific application, load requirements, and potential for customization when specifying mounting solutions.
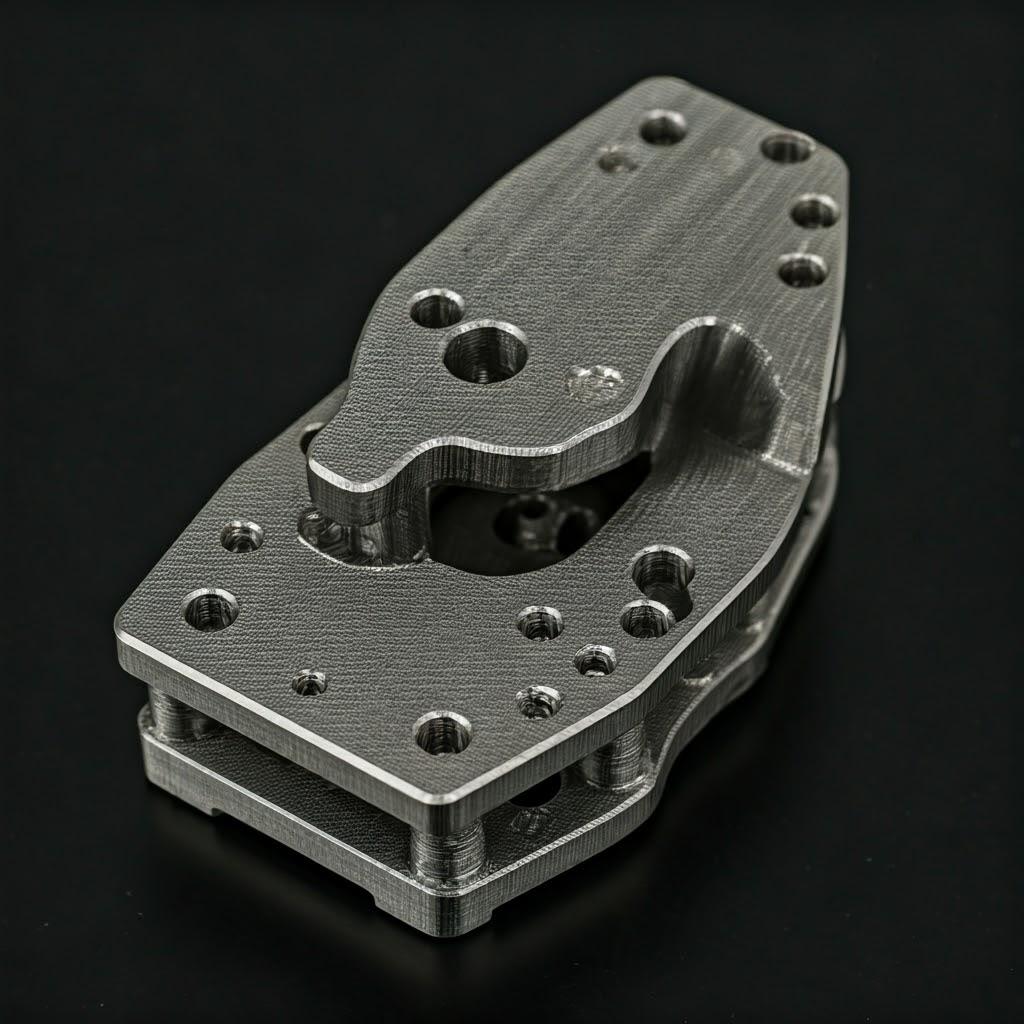
The Additive Advantage: Why Use Metal 3D Printing for UAV Mounting Plates?
While traditional manufacturing methods like CNC machining have served the UAV industry well, metal katkılı üretim (AM), or 3D printing, offers compelling advantages specifically suited to the evolving demands for higher performance, lighter weight, and greater design complexity in drone components like mounting plates. The shift towards AM is driven by its ability to overcome limitations inherent in subtractive processes, providing significant benefits for engineers and UAV parts manufacturers.
Key Advantages of Metal AM for UAV Mounting Plates:
- Unprecedented Design Freedom & Complexity:
- Karmaşık Geometriler: AM builds parts layer-by-layer, enabling the creation of intricate internal structures, curved surfaces, and organic shapes that are difficult or impossible to achieve with machining. This allows for highly optimized designs tailored to specific load paths and spatial constraints within the UAV.
- Topology Optimization: Engineers can use software tools to determine the most efficient material distribution for a given set of load conditions. AM can directly produce these highly optimized, often skeletal-looking structures, removing unnecessary material and drastically reducing weight while maintaining or even increasing strength in critical areas. This is ideal for ağırlık azaltma in UAVs.
- Parça Konsolidasyonu: Multiple components that would traditionally be assembled (e.g., a bracket, fasteners, stiffeners) can potentially be consolidated into a single, complex 3D printed part. This reduces assembly time, part count, potential points of failure, and overall weight.
- Significant Weight Reduction (Lightweighting):
- Optimized Structures: As mentioned, topology optimization and the ability to create internal lattice structures allow for mounting plates that are significantly lighter than solid machined parts, directly improving the güç/ağırlık oranı.
- Impact on Performance: Reduced component weight translates directly to longer flight times, increased payload capacity, or improved maneuverability – critical performance metrics for any UAV.
- Hızlı Prototipleme ve Yineleme:
- Hız: Producing functional metal prototypes can be significantly faster with AM compared to setting up traditional tooling or complex multi-axis machining processes. Design modifications can be implemented and tested quickly.
- Cost-Effective Iteration: Creating multiple design variations for testing and validation is more economical with AM, as it avoids the high initial costs associated with tooling or complex machining setups. This accelerates the development cycle for new UAV parts.
- Özelleştirme ve İsteğe Bağlı Üretim:
- Bespoke Designs: AM is ideal for producing custom mounting plates tailored to specific, non-standard payloads or unique UAV airframe integrations without the prohibitive costs of custom tooling.
- Küçük Parti Üretim: Manufacturing small-to-medium batches of specialized mounting plates is economically viable with AM, catering to niche applications or limited production runs often seen in the defense drone or R&D sectors.
- Dijital Envanter: Designs can be stored digitally and printed on demand, reducing the need for large physical inventories, especially relevant for UAV procurement and MRO (Maintenance, Repair, Overhaul) operations.
- Malzeme Verimliliği:
- Near-Net Shape: Additive processes typically use only the material needed to build the part and its supports, resulting in less material waste compared to subtractive methods where significant amounts of stock material are machined away. While powder recycling is essential, the buy-to-fly ratio can be improved.
- Enhanced Functionality Integration:
- Internal cooling channels, integrated vibration damping structures, or embedded features for cable routing can be designed directly into the mounting plate during the AM process, adding value beyond simple structural support.
Comparing AM vs. Traditional Machining for UAV Mounting Plates:
Özellik | Metal Katmanlı Üretim (AM) | Geleneksel CNC İşleme | Advantage Notes for UAV Plates |
---|---|---|---|
Tasarım Özgürlüğü | Very High (Complex geometries, internal features) | Moderate (Limited by tool access & axes) | AM enables topology optimization for extreme lightweighting. |
Ağırlık Azaltma | Excellent potential via optimization & lattices | Good, but limited by subtractive nature | AM is superior for achieving minimal weight. |
Complexity Cost | Less sensitive to geometric complexity | Increases significantly with complexity | AM makes complex, optimized designs more cost-effective. |
Lead Time (Proto) | Often Faster (No tooling needed) | Can be fast for simple parts, slower for complex | AM accelerates design iteration cycles. |
Lead Time (Prod) | Competitive for small/medium batches, complex parts | Often faster for high volumes, simple parts | Depends on volume; AM excels for customization. |
Malzeme Atıkları | Lower (Near-net shape, powder reuse) | Higher (Material removed from billet) | AM can be more sustainable, lower buy-to-fly ratio. |
Parça Konsolidasyonu | High Potential | Sınırlı | AM reduces assembly needs, weight, and failure points. |
Customization Cost | Low (No tooling changes needed) | High (Requires new setups/fixtures) | AM ideal for bespoke UAV payload integration. |
Yüzey İşlemi | Typically rougher as-built, requires post-processing | Generally smoother as-machined | Post-processing needed for AM, adds cost/time. |
Boyutsal Doğruluk | Good, improving (Requires process control) | Generally Very High | Machining often superior for tight tolerances without post-processing. |
Sayfalara Aktar
Şirketler gibi Met3dp, with their deep expertise in metal katkılı üretim and high-performance materials, leverage these advantages to provide optimized solutions. Their advanced printing systems ensure accuracy and reliability, crucial for mission-critical components in aerospace and defense applications. Choosing AM, particularly with a knowledgeable partner, empowers designers and procurement teams to move beyond traditional constraints and unlock superior performance for UAV platforms.
Material Matters: Recommended Aluminum Powders (AlSi10Mg & A7075) for Performance
The choice of material is as critical as the manufacturing method when designing high-performance UAV components. For mounting plates, where a balance of low weight, sufficient strength, stiffness, and environmental resistance is required, aluminum alloys are often the preferred choice. Within the realm of metal additive manufacturing, two aluminum alloys stand out for their suitability: AlSi10Mg ve A7075. Selecting the right powder is essential, and sourcing high-quality, consistent powders from reputable metal tozu tedarikçileri like Met3dp is crucial for achieving optimal part properties. Met3dp utilizes advanced gas atomization and PREP technologies to produce spherical metal powders with excellent flowability and high purity, ensuring dense, reliable prints.
1. AlSi10Mg: The Workhorse Alloy
AlSi10Mg is one of the most widely used aluminum alloys in metal AM, particularly Laser Powder Bed Fusion (LPBF), often referred to as Selective Laser Melting (SLM) or Direct Metal Laser Sintering (DMLS). It’s essentially an aluminum-silicon-magnesium casting alloy adapted for additive processes.
- Key Properties & Advantages:
- Mükemmel Basılabilirlik: AlSi10Mg generally exhibits good behavior during the LPBF process, with a relatively wide processing window, making it easier to produce dense, crack-free parts. This contributes to its popularity among metal AM service bureaus.
- İyi Güç-Ağırlık Oranı: While not the strongest aluminum alloy, it offers a respectable balance of strength and low density, making it suitable for many UAV structural components, including mounting plates where extreme loads aren’t the primary concern.
- Good Thermal Properties: It possesses good thermal conductivity.
- Korozyon Direnci: Offers adequate corrosion resistance for typical operating environments.
- İşlem sonrası: Can be readily heat-treated (e.g., T6 conditioning) to significantly improve mechanical properties (strength and hardness). It’s also amenable to standard finishing processes like machining, polishing, and anodizing.
- Typical Applications for UAV Mounting Plates:
- General-purpose mounting plates for cameras, sensors, and auxiliary equipment on commercial and research UAVs.
- Brackets where intricate design features and moderate strength are required.
- Prototypes requiring functional testing with representative material properties.
- Düşünceler:
- Its strength (especially yield strength and fatigue strength) is lower than high-strength alloys like A7075.
- Mechanical properties can be highly dependent on print parameters and post-process heat treatment.
2. A7075 (Scalmalloy® often used as AM equivalent): The High-Strength Champion
A7075 is a well-known high-strength aerospace aluminum alloy (Aluminum-Zinc-Magnesium-Copper). Traditionally used in wrought form, specialized variants or similar high-strength Al-Zn-Mg-(Sc)-(Zr) alloys (like Scalmalloy® or equivalents developed by powder manufacturers) have been optimized for additive manufacturing. These powders push the boundaries of what’s possible with 3D printed aluminum.
- Key Properties & Advantages:
- Olağanüstü Güç-Ağırlık Oranı: This is the primary advantage. AM versions of A7075 can achieve mechanical properties (yield strength, ultimate tensile strength) comparable to or even exceeding those of wrought 7075-T6, making it one of the highest-strength printable aluminum alloys available. This is ideal for demanding aerospace grade aluminum uygulamalar.
- Mükemmel Yorulma Dayanımı: Crucial for components subjected to vibrations and cyclic loading, common in UAV operations.
- Allows for Further Lightweighting: Because the material itself is stronger, designs can often be made even thinner and lighter compared to using AlSi10Mg for the same load requirements.
- Typical Applications for UAV Mounting Plates:
- Highly loaded structural mounts for heavy payloads or gimbals.
- Critical components on high-performance or defense drones where maximum strength and minimum weight are paramount.
- Applications requiring superior fatigue resistance.
- Direct replacement/upgrade for components traditionally machined from 7075 billet.
- Düşünceler:
- Basılabilirlik Zorlukları: High-strength aluminum alloys like A7075 equivalents can be more challenging to print reliably compared to AlSi10Mg. They often have a narrower processing window and can be more susceptible to issues like hot cracking if parameters are not precisely controlled. This necessitates advanced printing equipment and deep process expertise, such as that offered by Met3dp.
- Maliyet: The powder itself is typically more expensive than AlSi10Mg, and the potentially more complex printing process can increase manufacturing costs.
- Korozyon Direnci: While generally good, specific formulations might be slightly less corrosion-resistant than AlSi10Mg in certain environments and may benefit more from surface treatments like anodizing.
- Isıl İşlem: Requires specific, carefully controlled heat treatment cycles to achieve optimal mechanical properties.
Material Selection Summary Table:
Özellik | AlSi10Mg | A7075 (AM Equivalents) | Selection Guidance for UAV Plates |
---|---|---|---|
Primary Advantage | Good printability, balanced properties | Very high strength-to-weight ratio | Choose A7075 for maximum performance/weight saving; AlSi10Mg for general use & cost-effectiveness. |
Akma Dayanımı | Moderate (Improved significantly by T6) | Very High (Comparable to wrought 7075-T6) | A7075 is superior for high-load applications. |
Yoğunluk | Low (~2.67 g/cm³) | Low (~2.80-2.85 g/cm³, depending on specific alloy) | Both offer significant weight savings over steel/titanium. A7075 slightly denser. |
Yazdırılabilirlik | Generally Easier | More Challenging (Requires expertise) | AlSi10Mg preferred if AM process expertise/equipment is limited. |
Yorulma Dayanımı | Orta düzeyde | Mükemmel | A7075 better for high-vibration environments. |
Maliyet | Lower Powder & Processing Cost | Higher Powder & Processing Cost | Consider budget constraints; AlSi10Mg is more economical. |
Typical Use Case | General mounts, prototypes, complex shapes | Critical structural mounts, high-load parts | Match material to the mechanical demands of the specific mounting application. |
Supplier Focus | Yaygın olarak mevcuttur | Specialized suppliers (e.g., Met3dp) | Ensure your metal tozu tedarikçisi has proven experience with the chosen alloy. |
Sayfalara Aktar
Why Met3dp Powders Matter:
Kaynak Kullanımı yüksek kaliteli metal tozları is non-negotiable for demanding applications like UAV components. Met3dp’s commitment to quality, utilizing industry-leading gas atomization (producing high sphericity and flowability) and PREP technologies, ensures:
- Powder Consistency: Uniform particle size distribution and shape lead to predictable melting behavior and consistent material properties in the final part.
- Yüksek Saflıkta: Low levels of impurities and oxygen content minimize defects like porosity, leading to denser, stronger parts.
- Optimized Flowability: Crucial for uniform powder bed layering in LPBF systems, ensuring geometric accuracy and surface quality.
By partnering with a provider like Met3dp, who not only offers advanced printing services but also manufactures their own optimized metal tozları, engineers and procurement managers can be confident in the material integrity and performance of their 3D printed UAV mounting plates, whether choosing the reliable AlSi10Mg or the high-strength A7075.
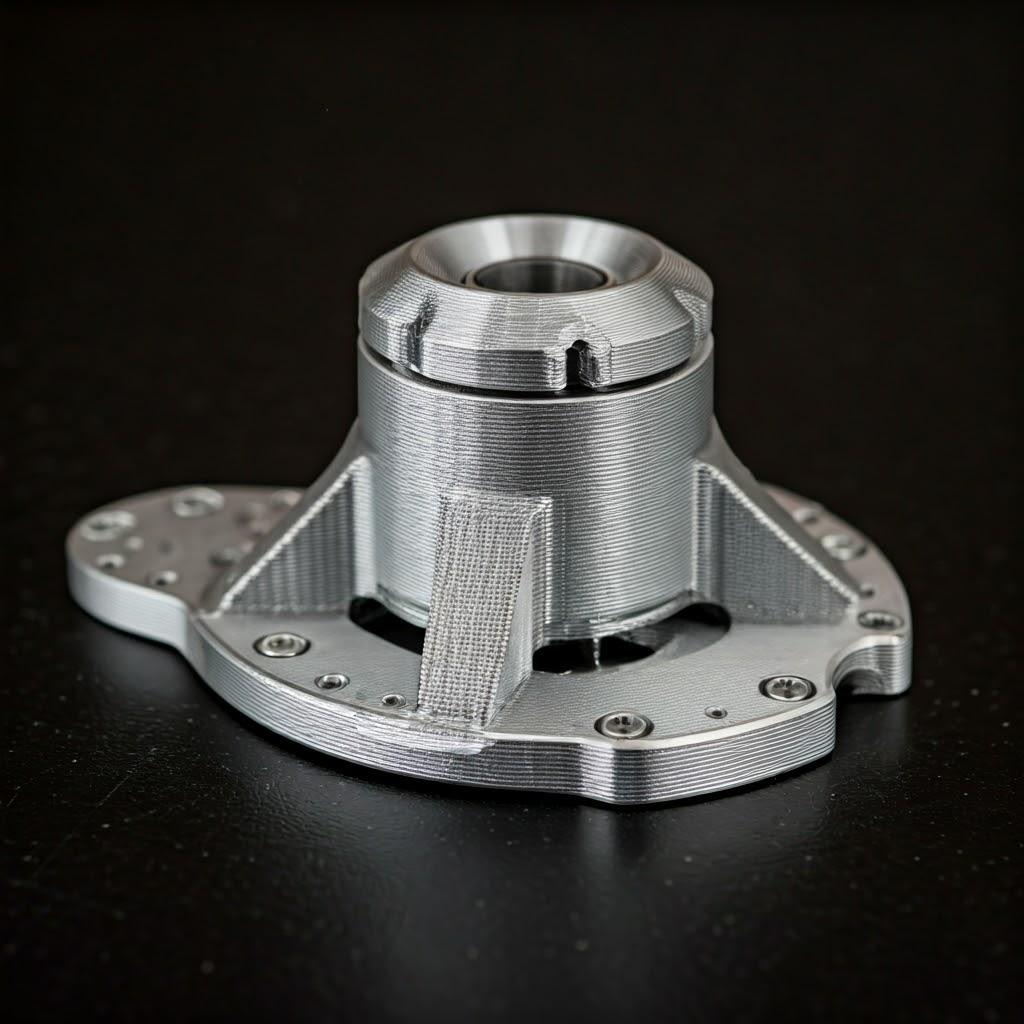
Design for Additive Success: Optimizing UAV Mounting Plates for 3D Printing
Additive Manufacturing isn’t just a different way to make the same part; it’s a paradigm shift that unlocks new design possibilities. To fully leverage the benefits of metal 3D printing for UAV mounting plates – particularly weight reduction and performance optimization – engineers must embrace Design for Additive Manufacturing (DfAM) principles. Simply taking a design intended for CNC machining and sending it to a 3D printer often fails to capitalize on AM’s unique strengths and can even introduce manufacturing challenges. Optimizing designs specifically for the chosen AM process, like Laser Powder Bed Fusion (LPBF) used for AlSi10Mg and A7075, is critical for success. Collaboration with experienced B2B UAV design services or AM providers like Met3dp, who understand the nuances of various baskı yöntemleri, can significantly streamline this optimization process.
Key DfAM Principles for UAV Mounting Plates:
- Topology Optimization:
- Concept: Use software algorithms to intelligently remove material from areas that don’t experience significant stress, leaving behind an optimized load-bearing structure. This often results in organic, skeletal-looking designs.
- Uygulama: Ideal for UAV mounting plates where minimizing weight is paramount. The software analyzes load cases (e.g., payload weight, vibration forces, flight loads) and generates the most materially efficient geometry possible.
- Benefit: Achieves maximum possible weight reduction while meeting structural requirements, directly improving UAV flight time and payload capacity.
- Kafes Yapılar:
- Concept: Incorporate internal, repeating geometric patterns (lattices) within the solid volume of the part. These structures can significantly reduce mass while maintaining good stiffness and strength, and can also be designed for energy absorption (vibration damping).
- Uygulama: Fill internal volumes of thicker sections of a mounting plate or create entire structures from lattice beams. Can be uniform or graded (varying density) based on local stress levels.
- Benefit: Provides excellent stiffness-to-weight ratio, potential for vibration damping, and facilitates powder removal from internal cavities.
- Parça Konsolidasyonu:
- Concept: Redesign assemblies consisting of multiple components (e.g., bracket, fasteners, stiffeners) into a single, monolithic part printable via AM.
- Uygulama: If a mounting plate assembly involves several bolted or welded pieces, explore if they can be combined into one complex AM part.
- Benefit: Reduces part count, eliminates fasteners (weight savings), simplifies assembly, reduces potential failure points (joints), and shortens the supply chain for procurement teams.
- Support Structure Optimization:
- Concept: LPBF requires support structures for overhanging features (typically below 45 degrees from horizontal) and to anchor the part to the build plate, managing thermal stress. Designing to minimize the need for supports is crucial.
- Kendini Destekleyen Açılar: Design overhangs to be greater than 45 degrees wherever possible.
- Feature Orientation: Orient the part on the build plate strategically to reduce the volume of supports needed.
- Accessible Supports: Ensure necessary support structures are accessible for easy removal during post-processing without damaging the part surface. Designing features that simplify support removal (e.g., adding chamfers) can save time and cost.
- Benefit: Reduces print time, material consumption (supports are waste), post-processing effort (support removal is often manual), and minimizes surface marks where supports were attached.
- Wall Thickness and Feature Size:
- Minimum Wall Thickness: AM processes have limitations on how thin features can be reliably printed. For aluminum alloys in LPBF, this is typically around 0.4-0.8 mm, depending on the machine and parameters. Designs must respect these limits.
- Hole Sizes: Small holes (typically < 0.5mm) may seal themselves during printing or be difficult to clear of powder. Design critical small holes slightly larger or plan for post-machining. Horizontal holes often require teardrop shapes or support.
- Benefit: Ensures manufacturability, structural integrity, and functional performance of small features.
- Managing Thermal Stress and Warping:
- Concept: The rapid heating and cooling during LPBF can induce internal stresses, potentially causing warping or cracking, especially in large flat sections or thin features connected to thick ones.
- Design Strategies: Avoid large, flat bases parallel to the build plate. Use topology optimization to break up solid masses. Incorporate smooth transitions between thick and thin sections. Orient the part carefully.
- Benefit: Improves dimensional stability, reduces print failures, and minimizes residual stress that might require extensive heat treatment.
- Designing for Post-Processing:
- Machining Allowances: If tight tolerances or specific surface finishes are required on certain features (e.g., mating surfaces, bearing bores), add extra material (machining stock) in the AM design to be removed via CNC machining later.
- Toz Giderme: Design internal channels or cavities with escape holes to allow unfused powder to be easily removed after printing. Avoid complex, inescapable internal voids.
- Surface Finish Considerations: Understand that different orientations produce different surface roughness. Design critical surfaces to be oriented optimally or plan for post-finishing.
DfAM Workflow Considerations:
- Collaboration: Engage with your chosen metal AM service bureau early in the design process. Their expertise can guide DfAM choices and ensure the design is optimized for their specific machines and processes.
- Simulation: Utilize AM simulation software to predict thermal stresses, potential warping, and optimize support structures before committing to a print.
- Yineleme: Leverage AM’s rapid prototyping capabilities to print and test design variations quickly, refining the optimization based on real-world results.
By thoughtfully applying these DfAM principles, engineers can unlock the full potential of metal AM, creating UAV mounting plates that are lighter, stronger, more functional, and tailored perfectly to the demanding requirements of modern drone applications. This strategic approach is essential for companies seeking to innovate and gain a competitive edge in the rapidly evolving UAV market.
Precision Defined: Tolerance, Surface Finish, and Dimensional Accuracy in Metal AM
While metal additive manufacturing offers incredible design freedom, understanding the achievable levels of precision – encompassing dimensional accuracy, tolerances, and surface finish – is crucial for engineers and procurement managers specifying UAV mounting plates. These factors directly impact component fit, function, and assembly. While AM technology is constantly improving, it’s important to have realistic expectations and understand how these aspects compare to traditional manufacturing methods like CNC machining. The capabilities of the specific AM system, material used, and process control implemented by the UAV parts supplier significantly influence the final outcome.
1. Dimensional Accuracy:
- Tanım: How closely the dimensions of the printed part match the nominal dimensions specified in the CAD model.
- Typical Values: For well-controlled LPBF processes using aluminum alloys like AlSi10Mg or A7075, typical dimensional accuracy is often in the range of ±0.1 mm to ±0.2 mm (or ±0.1% to ±0.2% for larger dimensions), although this can vary significantly. Leading providers like Met3dp, utilizing their industry-leading printers known for accuracy and reliability, often achieve tighter tolerances through rigorous process control and calibration.
- Factors Influencing Accuracy:
- Machine Calibration: Precision of the laser system, scanner accuracy, and build platform leveling.
- Thermal Effects: Shrinkage and potential warping during heating/cooling cycles.
- Toz Özellikleri: Consistency of powder particle size and morphology.
- Tarama Stratejisi: The pattern and speed used by the laser to melt the powder.
- Part Geometry & Orientation: Complex shapes and build orientation can affect localized accuracy.
- Destek Yapıları: How well supports manage stress and prevent distortion.
- İşlem sonrası: Stress relief heat treatments can sometimes cause minor dimensional changes.
2. Tolerances:
- Tanım: The permissible range of variation for a specific dimension. Engineers define tolerances based on functional requirements (e.g., hole diameters for fasteners, mating surface flatness).
- Achievable Tolerances (As-Built): While general accuracy might be ±0.1-0.2 mm, achieving tighter tolerances (e.g., below ±0.05 mm) on specific critical features directly from the AM process can be challenging and often requires careful process optimization and validation.
- Achieving Tight Tolerances: For features requiring high precision (e.g., bearing fits, interface planes), it’s standard practice to design the part with additional material (machining stock) in those areas and use post-process CNC machining to achieve the final required tolerances. This hybrid approach combines the design freedom of AM with the precision of subtractive machining.
- Specification: It’s crucial to clearly specify required tolerances on engineering drawings. Avoid over-tolerancing, as demanding tighter tolerances than necessary increases inspection requirements and potentially manufacturing costs.
3. Surface Finish (Roughness):
- Tanım: The texture of the part’s surface, typically measured as average roughness (Ra).
- As-Built Surface Finish: Metal AM parts, particularly from LPBF, have a characteristic surface roughness due to the layer-by-layer process and partially melted powder particles adhering to the surface.
- Top Surfaces: Generally smoother.
- Vertical Walls: Show layer lines, typically Ra 6 µm – 15 µm.
- Down-Facing/Supported Surfaces: Tend to be the roughest (Ra > 15 µm) due to contact with support structures.
- Factors Influencing Roughness:
- Katman Kalınlığı: Thinner layers generally produce smoother vertical walls but increase print time.
- Powder Particle Size: Finer powders can lead to smoother surfaces.
- Laser Parameters: Energy density and scan speed affect melt pool characteristics.
- Oryantasyon: Surface angle relative to the build direction significantly impacts roughness.
- Yüzey İşleminin İyileştirilmesi: If a smoother finish is required for functional (e.g., sealing surfaces) or aesthetic reasons, post-processing steps are necessary. These can include:
- Bead Blasting / Sand Blasting (common for a uniform matte finish)
- Tumbling / Vibratory Finishing
- Parlatma
- Talaşlı İmalat
- Electrochemical Polishing
Precision Expectations Summary Table:
Parametre | Typical As-Built AM (Al Alloys) | Achieved with Post-Machining | Notes for UAV Plates |
---|---|---|---|
General Accuracy | ±0.1 mm to ±0.2 mm (or ±0.1-0.2%) | N/A (Defined by machining) | Sufficient for many features, but consider critical interfaces. |
Tight Tolerances | Challenging (< ±0.05 mm) | High (±0.01 mm or better) | Plan for post-machining on critical tolerance features (e.g., mounting holes, interfaces). |
Surface Finish (Ra) | 6 µm – 25 µm+ (Varies by orientation) | < 1 µm possible | Specify required finish; expect post-processing for smooth surfaces. |
Sayfalara Aktar
Quality Control in AM:
Achieving consistent precision requires robust quality control UAV parts processes:
- Powder Management: Strict control over powder quality, storage, and reuse.
- Süreç İzleme: In-situ monitoring of melt pool characteristics, layer consistency, and thermal conditions (offered by advanced AM systems).
- Post-Print Inspection: Dimensional checks (e.g., CMM, 3D scanning), material density tests, and potentially NDT (Non-Destructive Testing) for critical components.
- Supplier Certification: Choosing suppliers with relevant certifications (e.g., ISO 9001, AS9100 for aerospace) often indicates strong quality management systems. Met3dp’s focus on industry-leading accuracy and reliability highlights the importance they place on process control for mission-critical parts.
Engineers designing UAV mounting plates must understand these precision characteristics. By designing appropriately (e.g., allowing for machining stock) and collaborating with capable AM providers who employ rigorous quality control, it’s possible to achieve the necessary fit, form, and function for even demanding drone applications.
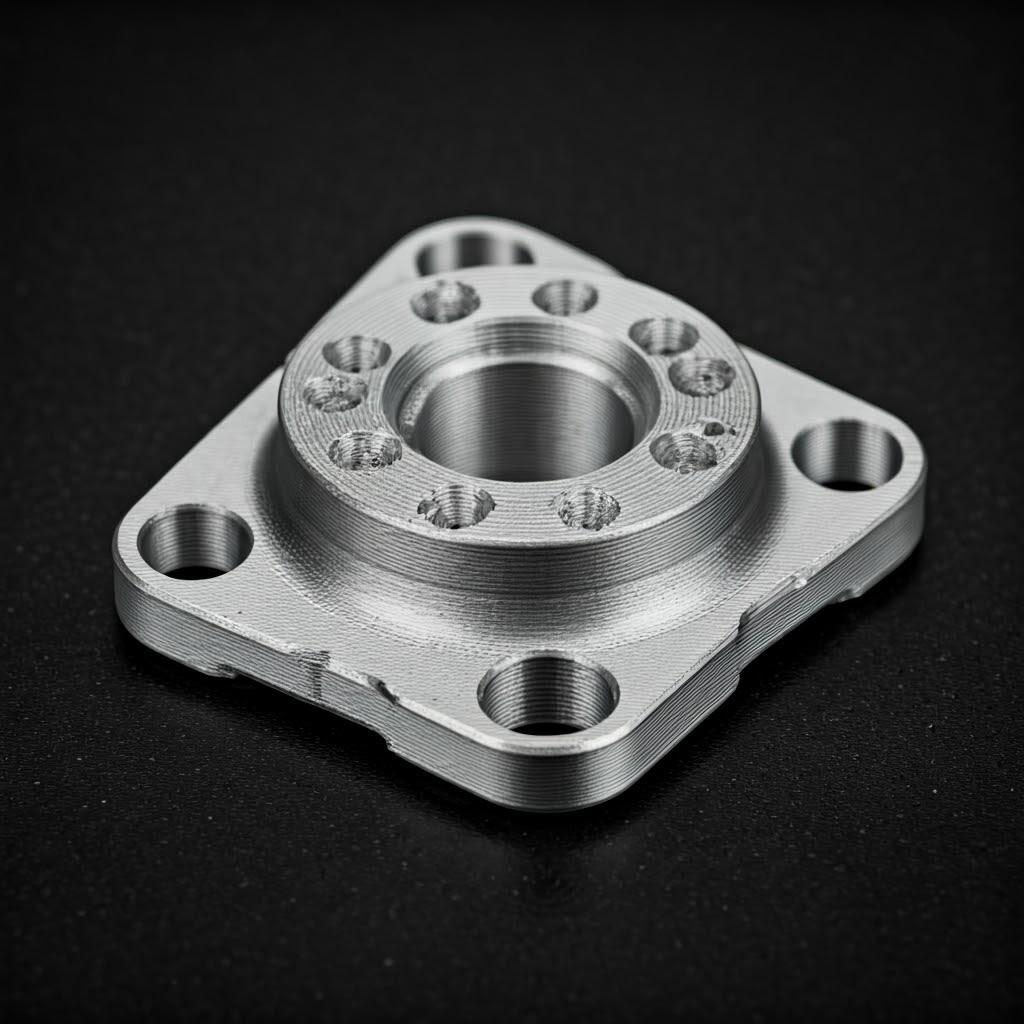
Beyond the Print: Essential Post-Processing for UAV Mounting Plates
The journey of a metal 3D printed UAV mounting plate doesn’t end when the printer stops. The “as-built” part, fresh off the build plate, typically requires several crucial post-processing steps to achieve the desired final properties, dimensions, surface finish, and overall quality. These steps are integral to the manufacturing workflow and must be considered by engineers during design and by procurement managers when evaluating metal AM service bureau quotes and lead times. Neglecting proper post-processing can compromise the component’s performance and integrity.
Common Post-Processing Steps for Metal AM UAV Plates (AlSi10Mg, A7075):
- Stres Giderici / Isıl İşlem:
- Amacımız: To relieve internal stresses built up during the rapid heating and cooling cycles of the printing process, reducing the risk of distortion or cracking, and to achieve the desired final material properties (hardness, strength, ductility).
- Süreç: The part is heated in a controlled furnace environment to specific temperatures for a defined duration, followed by controlled cooling. The exact cycle (temperature, time, atmosphere, cooling rate) depends heavily on the alloy (AlSi10Mg and A7075 require different treatments) and the desired final properties (e.g., T6 condition for AlSi10Mg).
- Importance: Often mandatory, especially for structural components like mounting plates, to ensure dimensional stability and optimal mechanical performance. Skipping or improperly performing heat treatment can lead to premature failure.
- Yapı Plakasından Parça Çıkarma:
- Amacımız: To separate the printed part(s) from the metal base plate they were fused onto during printing.
- Yöntemler: Typically done using wire EDM (Electrical Discharge Machining) or a band saw. Care must be taken to avoid damaging the parts.
- Destek Yapısının Kaldırılması:
- Amacımız: To remove the temporary support structures required during printing for overhangs and thermal management.
- Yöntemler: This is often a manual process using hand tools (pliers, cutters, grinders). It can be labor-intensive and requires skill to avoid damaging the part surface. Designing for minimal, accessible supports (DfAM) significantly simplifies this step. Sometimes CNC machining is used for precise removal of support interface points.
- Etki: Affects final surface finish where supports were attached; these areas are typically rougher.
- Powder Removal (Depowdering):
- Amacımız: To remove any unfused metal powder trapped within internal channels, cavities, or lattice structures.
- Yöntemler: Compressed air blowing, vibration, ultrasonic cleaning baths. Access holes designed into the part are crucial for effective depowdering, especially for complex internal geometries. Incomplete powder removal can add weight and potentially compromise performance.
- Importance: Critical for lightweighting and ensuring channels are clear if designed for functional purposes (e.g., cooling).
- Yüzey İşlemi:
- Amacımız: To achieve the desired surface texture, remove layer lines, improve aesthetics, or prepare the surface for subsequent coatings.
- Common Methods for UAV Plates:
- Bead/Sand Blasting: Creates a uniform, matte finish; good for general appearance and removing loose particles.
- Tumbling/Vibratory Finishing: Smoothes surfaces and edges using media in a rotating or vibrating drum; good for batch processing.
- CNC İşleme: Used on specific surfaces requiring tight tolerances or very smooth finishes (Ra < 1.6 µm).
- Parlatma: Manual or automated polishing for mirror-like finishes (less common for typical mounting plates unless aesthetically critical).
- CNC Machining (for Critical Features):
- Amacımız: To achieve tight tolerances (typically tighter than ±0.1mm) on specific features like mounting holes, mating surfaces, or bearing seats.
- Süreç: Uses traditional CNC milling or turning to precisely remove the pre-designed machining stock from specific areas of the AM part.
- Importance: Essential when the as-built AM tolerances are insufficient for functional requirements. Ensures proper fit and alignment during UAV assembly.
- Inspection and Quality Control:
- Amacımız: To verify that the part meets all dimensional, material, and functional specifications.
- Yöntemler:
- Boyutsal Muayene: Calipers, CMM (Coordinate Measuring Machine), 3D scanning.
- Material Testing: Hardness testing, tensile testing (on sample coupons printed alongside the part).
- NDT (Non-Destructive Testing): CT scanning (Computed Tomography) to check for internal porosity or defects, dye penetrant testing for surface cracks (less common for aluminum unless highly critical).
- Importance: Final verification step before the component is cleared for assembly. Rigorous kalite denetimi is key for aerospace and defense applications.
- Optional Coating/Anodizing:
- Amacımız: To enhance corrosion resistance, improve wear resistance, or provide a specific surface color/finish.
- Yöntemler: Anodizing is common for aluminum alloys, creating a hard, protective oxide layer. Other coatings (paint, chemical films) may also be applied.
- Consideration: Ensure compatibility with the specific aluminum alloy and intended operating environment.
Integrating Post-Processing into the Workflow:
Procurement managers should ensure that quotes from UAV component finishing suppliers clearly outline all included post-processing steps, associated costs, and impact on lead times. Engineers should design with post-processing in mind (DfAM), considering factors like support accessibility and machining stock allowances. A reliable AM partner like Met3dp can provide guidance on necessary post-processing steps and often manage the entire workflow, delivering finished components ready for integration. Understanding this full sequence is vital for accurate project planning and cost estimation.
Navigating Challenges: Common Issues in 3D Printing UAV Plates and Solutions
While metal 3D printing offers transformative potential for UAV mounting plates, it’s not without its challenges. Awareness of common issues and implementing preventative strategies are key to achieving successful, high-quality prints consistently. Collaborating with experienced AM providers who possess deep process knowledge and robust troubleshooting capabilities is invaluable for mitigating these risks. UAV parts supplier reliability often hinges on their ability to anticipate and overcome these common hurdles.
Common Challenges and Mitigation Strategies:
- Çarpıtma ve Bozulma:
- Sebep: Uneven heating and cooling during the layer-by-layer fusion process induce internal stresses (residual stress). If these stresses exceed the material’s yield strength at elevated temperatures, the part can deform or warp, especially large flat sections or parts detaching from supports.
- Hafifletme:
- Termal Simülasyon: Use software to predict stress accumulation and deformation.
- Optimize Edilmiş Yönlendirme: Orient the part on the build plate to minimize large flat areas parallel to the recoater blade and distribute thermal mass effectively.
- Sağlam Destek Yapıları: Use well-designed supports to anchor the part securely and help dissipate heat. Specialized support strategies might be needed.
- Optimized Scan Strategy: Employ techniques like island scanning or checkerboard patterns to manage localized heat input.
- Stress Relief Heat Treatment: Essential post-processing step to reduce residual stress in the final part.
- Design Modification (DfAM): Avoid large, solid blocks; use topology optimization or lattice structures to reduce thermal mass. Add ribs or stiffening features.
- Cracking (Hot Cracking / Solidification Cracking):
- Sebep: Occurs during solidification, particularly in alloys with a wide freezing range (like some high-strength aluminums, e.g., A7075 variants). Thermal stresses can pull the semi-solid material apart if not managed.
- Hafifletme:
- Malzeme Seçimi: Some alloys are inherently more prone to cracking. Ensure the correct, AM-optimized powder variant is used (e.g., specific formulations of A7075 designed for printability).
- Parametre Optimizasyonu: Precise control over laser power, scan speed, and hatch spacing is crucial. Requires deep process expertise for challenging alloys. Collaboration with material/powder experts like Met3dp, who develop their own powders, is beneficial.
- Optimized Scan Strategy: Reduces localized overheating and stress.
- Platform Heating: Pre-heating the build plate can reduce thermal gradients.
- Post-Print HIP (Hot Isostatic Pressing): Can sometimes close internal cracks, but it’s an additional costly step.
- Gözeneklilik:
- Sebep: Small voids or gas bubbles trapped within the printed material. Can result from gas trapped in the powder, insufficient energy density (lack-of-fusion porosity), or keyholing (instability caused by excessive energy density trapping shielding gas).
- Hafifletme:
- Yüksek Kaliteli Toz: Use powder with low gas content, controlled particle size distribution, and good flowability (Met3dp’s focus on advanced atomization techniques like gas atomization helps ensure this). Proper powder handling and storage are vital.
- Optimized Print Parameters: Finding the right balance of laser power, scan speed, layer thickness, and hatch spacing to ensure complete melting without keyholing.
- Atmosphere Control: Maintain a high-purity inert gas atmosphere (e.g., Argon) in the build chamber to minimize oxidation and contamination.
- Post-Print HIP: Can effectively close internal porosity, increasing density and improving mechanical properties, especially fatigue life. Often specified for critical aerospace parts.
- Support Structure Issues:
- Difficult Removal: Supports that are too dense, poorly designed, or located in inaccessible areas can be extremely difficult and time-consuming to remove, potentially damaging the part.
- Support Failure: Insufficiently strong supports can break during printing, leading to part deformation or complete build failure.
- Yüzey Kalitesi: Support contact points leave rough surfaces (‘witness marks’) that require finishing.
- Hafifletme:
- DfAM: Design parts to be self-supporting where possible. Optimize orientation.
- Support Strategy Software: Use advanced software to generate optimized, easily removable support structures (e.g., tree supports, block supports with appropriate fragmentation).
- Parametre Ayarlama: Adjust support interface parameters for easier detachment.
- Nitelikli Teknisyenler: Post-processing requires careful manual work.
- Poor Surface Finish:
- Sebep: Inherent nature of layer-wise manufacturing, powder particle adhesion, support contact points, incorrect parameters (“balling” effect).
- Hafifletme:
- Oryantasyon: Optimize part orientation for critical surfaces.
- Parametre Optimizasyonu: Fine-tune laser parameters and layer thickness.
- İşlem sonrası: Implement appropriate finishing steps (blasting, tumbling, machining) as planned during the design phase.
- Dimensional Inaccuracy:
- Sebep: Thermal shrinkage/warping, machine calibration drift, scan strategy effects, STL file resolution errors.
- Hafifletme:
- Machine Calibration: Regular and thorough calibration of the AM system.
- Compensation Factors: Applying scaling factors based on empirical data to account for known shrinkage.
- Termal Yönetim: Effective support strategies and scan patterns.
- High-Resolution CAD/STL: Ensure input files are accurate.
- Post-Machining: Plan for machining critical tolerance features.
Troubleshooting Metal AM – The Supplier Role:
Overcoming these challenges requires a combination of robust machine technology, high-quality materials, optimized process parameters, and experienced personnel. When selecting a metal 3D printing service provider, inquire about their experience with your chosen material (especially challenging ones like A7075), their quality control procedures, and their strategies for mitigating these common issues. A proactive and knowledgeable supplier is essential for reliable production of mission-critical components like UAV mounting plates.
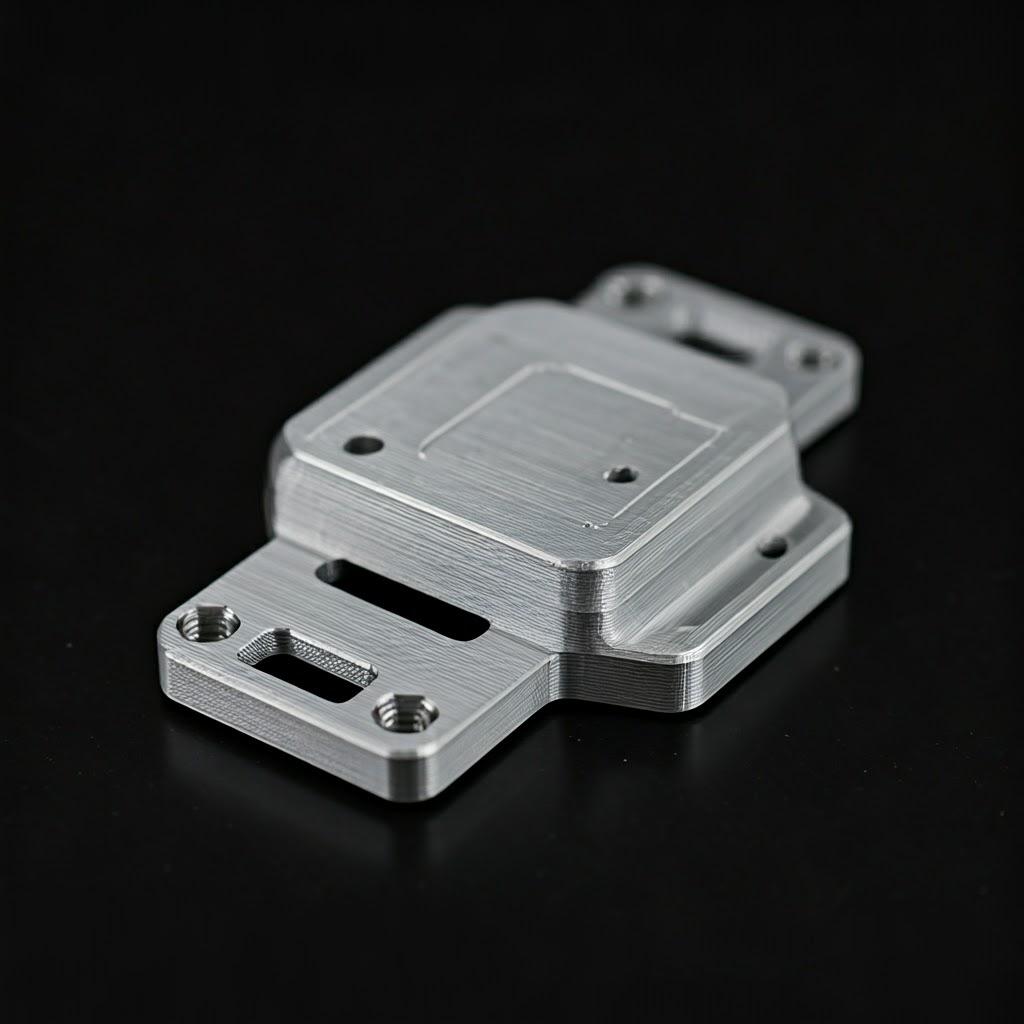
Supplier Selection: How to Choose the Right Metal 3D Printing Service Provider
Selecting the right manufacturing partner is as critical as perfecting the design and choosing the appropriate material for your UAV mounting plates. The quality, reliability, and performance of the final component heavily depend on the expertise, capabilities, and quality systems of the chosen metal AM service bureau. For engineers and procurement managers navigating the landscape of additive manufacturing providers, making an informed decision requires careful evaluation of several key factors. Partnering with a capable supplier ensures not only high-quality parts but also valuable technical support and a smooth procurement process for drone parçaları.
Key Criteria for Evaluating Metal AM Suppliers:
- Technical Expertise and Experience:
- Malzeme Uzmanlığı: Does the supplier have proven experience with the specific aluminum alloy you require (AlSi10Mg, A7075/equivalents)? Printing high-strength alloys like A7075 demands specific process knowledge. Ask for case studies or examples of similar parts they have produced.
- DfAM Capabilities: Can they offer Design for Additive Manufacturing support? A good partner can review your design and suggest optimizations for better printability, weight reduction, or cost-effectiveness.
- Process Knowledge: Do they understand the nuances of parameter optimization, support strategy, thermal management, and post-processing required for your specific application and material? Companies like Met3dp, with decades of collective expertise in metal AM, often provide comprehensive solutions spanning equipment, materials, and application development.
- Sektör Deneyimi: Have they worked with clients in demanding sectors like aerospace, defense, or medical? This often indicates experience with stringent quality requirements.
- Equipment and Technology:
- Machine Fleet: What type of metal AM systems do they operate (e.g., LPBF/SLM/DMLS)? Do they have machines suitable for the required part size and material? Do they have redundancy in case of machine downtime?
- Technology Level: Are their machines state-of-the-art? Do they incorporate process monitoring capabilities for better quality control? Met3dp, for instance, highlights its printers’ industry-leading print volume, accuracy, and reliability.
- Toz İşleme: What are their procedures for powder handling, storage, testing, and traceability? This is crucial for material quality and consistency. Look for providers using advanced powder production like gas atomization or PREP, ensuring high sphericity and purity.
- Material Capabilities and Quality:
- Malzeme Portföyü: Do they offer the specific alloys you need? Can they provide material certifications and datasheets detailing the expected mechanical properties based on their process?
- Powder Sourcing: Do they source powders from reputable suppliers, or, like Met3dp, manufacture their own high-quality powders optimized for AM? In-house powder production can offer greater control over quality and consistency.
- Kalite Kontrol: What tests do they perform on incoming powder and finished parts (e.g., density checks, chemical analysis, mechanical testing)?
- Quality Management Systems and Certifications:
- ISO 9001: A fundamental certification indicating a structured quality management system.
- AS9100: Essential for aerospace and defense applications, indicating compliance with rigorous industry-specific quality standards. If your UAV plates are for these sectors, AS9100 certification is often non-negotiable.
- Traceability: Can they provide full traceability from raw material batch to finished part?
- Post-Processing Capabilities:
- Şirket İçi ve Dış Kaynaklı: Do they handle essential post-processing steps like heat treatment, support removal, machining, and surface finishing in-house, or do they outsource them? In-house capabilities generally offer better control over the entire workflow, lead times, and quality.
- Range of Services: Can they provide all the necessary steps to deliver a finished component ready for assembly?
- Lead Time and Capacity:
- Quoted Lead Times: Are their quoted lead times B2B competitive and realistic for your project timeline? Understand what drives their lead times (e.g., machine availability, post-processing complexity).
- Üretim Kapasitesi: Can they handle your required volume, whether it’s for prototypes, small batches, or potentially larger bulk order pricing UAV components?
- Cost and Quoting:
- Şeffaflık: Is their quoting clear and detailed, breaking down costs for printing, material, supports, post-processing, and quality control?
- Value: Don’t choose solely based on the lowest price. Consider the provider’s expertise, quality, reliability, and support – factors that contribute to the overall value and reduce risks.
- Customer Service and Communication:
- Responsiveness: Are they responsive to inquiries and requests for technical support?
- Collaboration: Are they willing to work collaboratively to solve challenges and optimize your project?
Evaluating Potential Suppliers:
Evaluation Area | Key Questions to Ask | Why It Matters for UAV Plates |
---|---|---|
Teknik Uzmanlık | Experience with AlSi10Mg/A7075? DfAM support? Aerospace experience? | Ensures understanding of material challenges & quality needs for critical components. |
Equipment/Technology | Machine type/age? Process monitoring? Powder handling procedures? | Impacts part quality, consistency, accuracy, and reliability. |
Malzeme Kalitesi | Datasheets provided? Powder sourcing/manufacturing? QC tests on powder/parts? | Guarantees material properties meet design specifications. Crucial for performance. |
Sertifikalar | ISO 9001? AS9100 (if applicable)? Full traceability? | Demonstrates commitment to quality standards required for aerospace/defense. |
İşlem Sonrası | In-house capabilities (heat treat, machining, finishing)? | Streamlines workflow, ensures quality control over all steps, impacts lead time. |
Lead Time & Capacity | Standard lead times? Ability to handle required volume? | Ensures parts are delivered on schedule to meet project milestones. |
Cost & Quoting | Transparent cost breakdown? Competitive pricing considering value? | Allows accurate budgeting and comparison between suppliers. |
Communication | Responsiveness? Willingness to collaborate? | Facilitates smooth project execution and problem-solving. |
Sayfalara Aktar
Doğru seçimi yapmak metal 3D printing service provider is a strategic decision. Look for a partner, like Met3dp, that offers a comprehensive solution – combining advanced printing technology, high-quality materials, robust quality systems, and deep application expertise – to ensure the success of your UAV mounting plate project.
Understanding Investment: Cost Factors and Lead Times for Printed UAV Plates
When adopting metal additive manufacturing for UAV mounting plates, understanding the associated costs and typical lead times is crucial for project planning, budgeting, and managing expectations within procurement and engineering teams. Unlike traditional manufacturing where tooling costs might dominate, the metal 3D printing cost breakdown is influenced by a different set of factors.
Key Cost Drivers for Metal AM UAV Plates:
- Material Consumption:
- Part Volume: The actual volume of the final part directly consumes expensive, highly engineered metal powder (e.g., AlSi10Mg, A7075). Larger or denser parts cost more.
- Support Structure Volume: Material used for support structures also adds to the cost. Optimized designs (DfAM) minimizing supports can significantly reduce material usage.
- Powder Type: High-performance alloys like A7075 equivalents are generally more expensive per kilogram than standard AlSi10Mg. Sourcing wholesale UAV components may offer volume discounts on materials.
- Makine Zamanı:
- Yapım süresi: This is often a primary cost driver. It depends on:
- Part Height (Z-Height): Taller parts take longer as more layers are required.
- Part Volume/Density: Melting more material per layer takes time.
- Number of Parts per Build: Utilizing the build platform efficiently by nesting multiple parts can reduce the per-part machine time cost. Providers aim for high machine utilization.
- Katman Kalınlığı: Thinner layers improve surface finish but significantly increase build time.
- Tarama Stratejisi: Complex scan patterns might take longer.
- Machine Depreciation & Operating Costs: These are factored into the hourly rate charged for machine usage. Advanced, high-precision machines represent a significant investment for the service provider.
- Yapım süresi: This is often a primary cost driver. It depends on:
- Labor and Setup:
- Build Preparation: Loading the CAD file, setting up the build parameters, preparing the machine, loading powder.
- Post-Processing Labor: Manual tasks like depowdering, support removal, basic surface finishing. This can be significant, especially for complex parts with intricate supports.
- Quality Control & Inspection: Time spent on dimensional checks, NDT, documentation.
- İşlem Sonrası Maliyetler:
- Isıl İşlem: Furnace time and energy consumption.
- CNC İşleme: Costs associated with programming, setup, and machining time if tight tolerances or specific finishes are required.
- Yüzey İşlemi: Costs for blasting, tumbling, polishing, or anodizing.
- Destek Kaldırma: Can be a significant labor cost component.
- Complexity and Design:
- Intricacy: While AM handles complexity well, highly intricate designs might require more complex support strategies or more intensive post-processing (e.g., powder removal from complex internal channels), potentially increasing labor costs.
- Optimization Level: Investing time in DfAM upfront can reduce material consumption and post-processing needs, lowering overall part cost despite potentially increasing design time.
- Sipariş Hacmi:
- Prototyping vs. Production: One-off prototypes will have higher per-part costs due to setup overheads.
- Parti Boyutu: Larger batch sizes allow for better machine utilization (nesting parts) and can distribute setup costs, leading to lower per-part pricing. Inquire about bulk order pricing UAV seçenekler.
Typical Lead Times:
Lead time is the total time from order placement to receiving the finished parts. It comprises several stages:
- Order Processing & Scheduling: 1-3 days (depending on supplier workload).
- Build Preparation: < 1 day.
- Baskı Süresi: Highly variable – from hours for a small, single part to several days for a large build plate full of complex components. A typical UAV mounting plate might take 12-48 hours of print time depending on size and complexity.
- Cool Down: Several hours after printing.
- İşlem sonrası: Highly variable, often the longest part of the lead time:
- Stress Relief/Heat Treatment: 1-2 days (including furnace cycles).
- Part Removal/Support Removal/Depowdering: 1-3 days (can be labor-intensive).
- CNC Machining (if required): 2-5 days (depending on complexity and machine availability).
- Surface Finishing/Coating: 1-3 days.
- Inspection: < 1 day.
- Nakliye: Depends on location and method.
Estimated Total Lead Time: For a typical metal AM UAV mounting plate requiring standard post-processing, expect lead times ranging from 1 to 3 weeks. If complex machining or specific coatings are needed, or if the supplier has a backlog, this could extend further. Rush services are often available at a premium cost.
Cost vs. Lead Time Trade-offs:
Faktör | To Reduce Cost | To Reduce Lead Time | Dikkate Alınması Gerekenler |
---|---|---|---|
Tasarım | Optimize for min. material/supports (DfAM) | Simplify design (less complex supports/features) | DfAM often yields best long-term value despite initial design effort. |
Malzeme | Use AlSi10Mg if A7075 strength isn’t essential | N/A (Material choice based on performance) | Performance requirements usually dictate material choice. |
İşlem Sonrası | Minimize requirements (tolerances, finish) | Streamline steps, use supplier w/ in-house capabilities | Don’t sacrifice necessary steps for speed/cost if function is compromised. |
Sipariş Hacmi | Increase batch size | Discuss expedite options (may increase cost) | Balance inventory needs with per-part cost benefits. |
Tedarikçi Seçimi | Compare quotes transparently | Choose supplier with efficient workflow/capacity | Ensure supplier can meet both quality and delivery needs. |
Sayfalara Aktar
Understanding these factors allows for better budgeting, realistic scheduling, and informed discussions with potential metal AM service providers. Clear communication about requirements and priorities (cost vs. speed vs. performance) is key to a successful partnership.
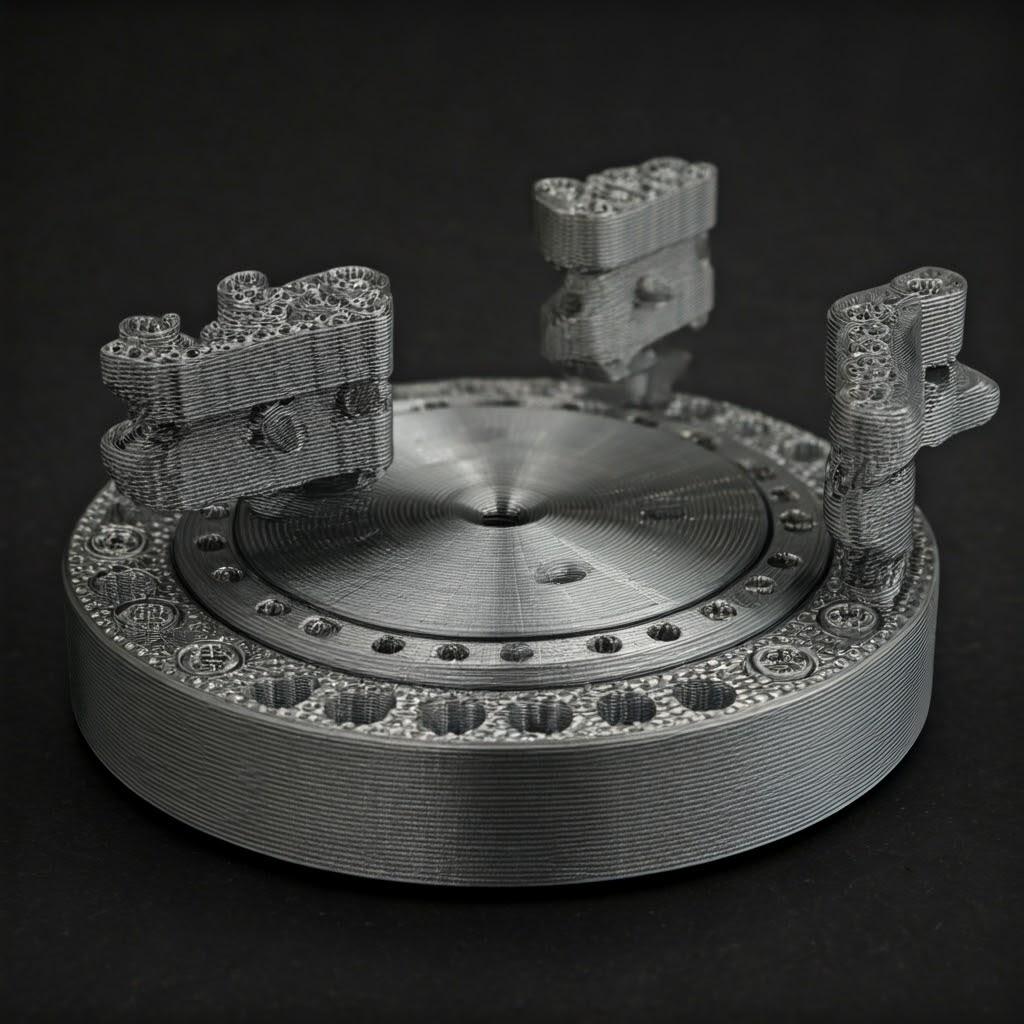
Frequently Asked Questions (FAQ) about 3D Printed UAV Mounting Plates
Here are some common questions engineers and procurement managers have when considering metal additive manufacturing for UAV mounting plates:
- Q: Are 3D printed aluminum mounting plates (AlSi10Mg, A7075) as strong as traditionally machined ones?
- A: Yes, and often they can be designed to be stronger for their weight. With proper process control and post-process heat treatment, the mechanical properties of AM aluminum alloys like AlSi10Mg (especially after T6 treatment) and high-strength AM equivalents of A7075 can meet or exceed those of their cast or even some wrought counterparts. A7075 AM variants, in particular, can achieve exceptionally high strength-to-weight ratios, comparable to wrought 7075-T6. The key lies in using high-quality powder (like those from Met3dp), optimized print parameters, and appropriate post-processing, particularly heat treatment and potentially HIP for critical applications to ensure full density and optimal microstructure. Furthermore, AM allows for topology optimization, placing material only where needed, leading to designs that are structurally efficient and robust despite being significantly lighter than a traditionally shaped machined part designed for the same function.
- Q: How does the cost of metal 3D printing for a UAV mounting plate compare to CNC machining?
- A: It depends heavily on complexity, volume, and design optimization.
- For simple geometries in high volumes: CNC machining is often more cost-effective due to faster cycle times per part once set up.
- For complex geometries (optimized shapes, internal lattices, consolidated parts): Metal AM is often more cost-effective, as complexity adds little to the AM print cost but significantly increases machining time and difficulty.
- For prototypes and low volumes: AM is generally cheaper and faster as it avoids tooling costs and complex setup required for machining one-offs or small batches.
- When weight reduction is critical: While the AM part might have a higher initial piece price, the weight savings achieved through topology optimization can lead to significant operational cost savings over the UAV’s lifetime (longer flight, higher payload), making AM the better value proposition overall.
- A thorough cost analysis should compare not just the piece price but also factor in design freedom, potential for part consolidation, lead time, and the performance benefits gained (especially weight savings).
- A: It depends heavily on complexity, volume, and design optimization.
- Q: Can I get material certifications for 3D printed aluminum parts similar to those for wrought materials?
- A: Yes, reputable metal AM service providers can typically provide comprehensive documentation and certification. This often includes:
- Powder Certification: Certificates of analysis for the specific powder batch used, detailing its chemical composition and particle size distribution.
- Process Documentation: Records of the build parameters used, machine utilized, part orientation, and support strategy.
- Post-Processing Records: Confirmation of heat treatment cycles performed and any other finishing steps.
- Mechanical Test Results: Data from tensile tests, hardness tests, and density measurements performed on witness coupons printed alongside the actual parts within the same build.
- Dimensional Inspection Reports: CMM or 3D scan reports verifying critical dimensions and tolerances.
- Certifications (Supplier Level): Compliance with quality standards like ISO 9001 or AS9100 (if applicable).
- It’s crucial to specify your required documentation and certification needs upfront when requesting quotes from suppliers like Met3dp, especially for aerospace or mission-critical applications.
- A: Yes, reputable metal AM service providers can typically provide comprehensive documentation and certification. This often includes:
Conclusion: Elevating UAV Performance with Met3dp’s Additive Manufacturing Solutions
The landscape of Unmanned Aerial Vehicle technology is characterized by a relentless pursuit of higher performance, greater endurance, and expanded capabilities. In this competitive environment, optimizing every component, including the often-overlooked mounting plate, is essential. As we’ve explored, metal katkılı üretim offers a powerful toolkit for achieving this optimization, enabling the production of UAV mounting plates in lightweight, high-strength aluminum alloys like AlSi10Mg and A7075 that surpass the limitations of traditional manufacturing.
The advantages are clear: unprecedented design freedom through topology optimization and complex geometries, significant weight reduction leading to tangible performance gains, rapid prototyping for accelerated development cycles, and the ability to consolidate parts and customize solutions on demand. By leveraging DfAM principles and understanding the nuances of precision, post-processing, and potential challenges, engineers can design truly innovative mounting solutions.
However, realizing the full potential of metal AM requires more than just advanced technology; it demands expertise, quality control, and a reliable manufacturing partner. Choosing the right metal 3D printing service provider – one with proven experience, robust processes, high-quality materials, and relevant certifications – is paramount.
İşte burası Met3dp emerges as a leader and trusted partner. With headquarters in Qingdao, China, and a focus on industrial applications, Met3dp provides comprehensive katkı üretim çözümleri. Their expertise encompasses:
- Industry-Leading Equipment: Offering printers renowned for accuracy, reliability, and substantial build volumes suitable for mission-critical aerospace components.
- Advanced Powder Technology: Manufacturing their own high-performance spherical metal powders (including innovative alloys alongside staples like aluminum) using cutting-edge gas atomization and PREP techniques, ensuring material quality and consistency.
- End-to-End Support: Providing services that span application development, DfAM consultation, printing, post-processing, and quality assurance.
By partnering with Met3dp, companies developing advanced UAVs gain access to cutting-edge systems and materials, backed by decades of collective expertise. Whether you require optimized AlSi10Mg brackets for commercial drones or high-strength A7075 mounts for demanding defense applications, Met3dp delivers the quality and reliability needed to elevate your UAV’s performance.
Geleceğin UAV manufacturing is intrinsically linked with the advancements in additive manufacturing. Embracing metal 3D printing for components like mounting plates is no longer just an option; it’s a strategic imperative for innovation and competitiveness.
Ready to explore how Met3dp’s capabilities can power your organization’s additive manufacturing goals for UAV components or other industrial applications? Contact Met3dp today to discuss your project requirements and discover the benefits of partnering with a leader in metal AM.
Paylaş
MET3DP Technology Co, LTD, merkezi Qingdao, Çin'de bulunan lider bir katmanlı üretim çözümleri sağlayıcısıdır. Şirketimiz, endüstriyel uygulamalar için 3D baskı ekipmanları ve yüksek performanslı metal tozları konusunda uzmanlaşmıştır.
İşletmeniz için en iyi fiyatı ve özelleştirilmiş Çözümü almak için sorgulayın!
İlgili Makaleler
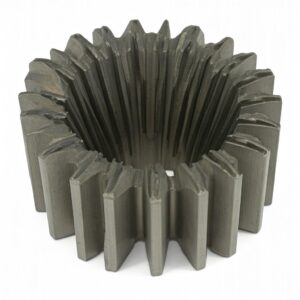
Yüksek Performanslı Nozul Kanat Segmentleri: Metal 3D Baskı ile Türbin Verimliliğinde Devrim
Daha Fazla Oku "Met3DP Hakkında
Son Güncelleme
Bizim Ürünümüz
BİZE ULAŞIN
Herhangi bir sorunuz var mı? Bize şimdi mesaj gönderin! Mesajınızı aldıktan sonra tüm ekibimizle talebinize hizmet edeceğiz.
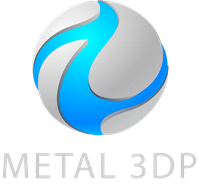
3D Baskı ve Katmanlı Üretim için Metal Tozları