3D Printed Suspension Components for EVs
İçindekiler
Introduction: The Drive Towards Lightweighting and Performance in EV Suspensions
The automotive industry is undergoing its most significant transformation in a century, driven by the accelerating shift towards electric mobility. Electric vehicles (EVs) are no longer a niche segment but are rapidly becoming mainstream, fueled by consumer demand, regulatory pressures, and advancements in battery technology. However, this transition presents unique engineering challenges. EVs typically carry heavy battery packs, significantly increasing overall vehicle mass. This added weight places immense strain on components like the suspension system and directly impacts crucial performance metrics such as driving range, handling dynamics, and ride comfort.
Range anxiety remains a primary concern for potential EV buyers. Every kilogram saved translates directly into extended driving distance or allows for smaller, lighter, and potentially cheaper battery packs. Consequently, lightweighting has become a critical engineering imperative across the entire EV architecture. The suspension system, which constitutes a significant portion of the vehicle’s unsprung mass (the mass not supported by the springs, such as wheels, tires, brakes, and suspension components themselves), is a prime target for weight reduction. Reducing unsprung mass improves not only range but also enhances vehicle agility, responsiveness, and ride quality by allowing the wheels to follow road contours more effectively.
Simultaneously, the instantaneous torque delivery of electric motors demands robust and precisely engineered suspension systems capable of handling significant forces while providing a refined driving experience. Consumers expect EVs to offer not just environmental benefits but also superior performance and comfort. Achieving this delicate balance between lightweight design, structural integrity, and dynamic performance requires innovative approaches that push beyond the limitations of traditional manufacturing methods.
Girmek metal katkılı üretim (AM), more commonly known as metal 3D baskı. This transformative technology is rapidly maturing from a prototyping tool into a viable solution for producing complex, high-performance end-use parts. For EV suspension components, metal AM offers unprecedented opportunities to:
- Radically reduce weight through topology optimization and intricate lattice structures, designs impossible to achieve through casting or machining alone.
- Consolidate multiple parts into a single, complex component, reducing assembly time, weight, and potential points of failure.
- Enhance performance by enabling optimized geometries that improve stiffness, durability, and load distribution.
- Accelerate development cycles by allowing rapid iteration and production of functional prototypes and low-volume series parts without the need for expensive tooling.
As engineers and procurement managers in the automotive sector navigate the complexities of EV development, understanding the potential of metal AM is crucial. It offers a pathway to creating lighter, stronger, and more efficient suspension systems that directly address the core challenges of electric mobility. Companies like Met3dp, with deep expertise in both advanced metal AM equipment and the production of high-quality metal powders, are at the forefront of this revolution. Headquartered in Qingdao, China, Met3dp provides comprehensive additive manufacturing solutions, empowering automotive innovators to rethink component design and unlock new levels of performance and efficiency for the next generation of electric vehicles. Partnering with knowledgeable suppliers who understand both the materials and the process is key to successfully implementing AM for critical applications like EV suspension.
What are 3D Printed EV Suspension Components Used For? Applications and Opportunities
The application of metal additive manufacturing in EV suspension systems extends far beyond theoretical possibilities; it’s actively being implemented and explored for a variety of critical components where its benefits deliver tangible advantages. The design freedom offered by AM allows engineers to completely reimagine parts traditionally constrained by casting molds or machining limitations. This opens doors for performance enhancements and weight savings previously unattainable.
Here’s a breakdown of specific suspension components being targeted for metal 3D printing in the EV space:
- Control Arms (Wishbones): These crucial links connect the chassis to the wheel hub or knuckle, controlling wheel movement. 3D printing allows for highly optimized, hollow, or lattice-filled designs that maintain or increase stiffness while dramatically reducing mass compared to solid cast or forged aluminum or steel arms. This directly lowers unsprung weight.
- Uprights (Knuckles): Connecting the suspension arms, strut/damper, and steering tie rod to the wheel bearing/hub, uprights are complex, load-bearing components. AM enables the creation of topologically optimized uprights integrating mounting points and complex internal structures, consolidating brackets and reducing part count, while maximizing strength-to-weight ratio.
- Shock Absorber Components: Internal pistons, housings, and complex brackets for advanced adaptive damping systems can benefit from AM. Intricate fluid channels or unique mounting geometries that improve performance or packaging efficiency are possible.
- Bell Cranks and Pushrods: Common in high-performance or motorsport-derived inboard suspension systems, these components transfer loads from the wheel to inboard springs and dampers. AM allows for extremely lightweight and stiff designs tailored to specific kinematic requirements.
- Subframe Nodes and Brackets: Complex joining elements within the suspension subframe can be optimized for load paths and consolidated using AM, simplifying assembly and reducing weight. Mounting brackets for sensors, reservoirs, or auxiliary components can be integrated directly into larger structural parts.
- Anti-Roll Bar Components: Mounts, linkages, and even potentially sections of the bar itself (in specialized cases) could be optimized using AM for weight savings or unique kinematic properties.
The use cases for these 3D printed components span various segments within the automotive industry, each leveraging different strengths of additive manufacturing:
- High-Performance EVs & Motorsport: This is often the proving ground for advanced technologies. Teams demand maximum performance and minimal weight. AM allows for bespoke, highly optimized suspension components tailored to specific vehicle dynamics and track conditions, where cost is secondary to performance gains and rapid iteration is key. Procurement managers for racing teams seek suppliers capable of quick turnaround and cutting-edge designs.
- Niche & Luxury EVs: For low-volume production runs of specialized or high-end electric vehicles, the tooling costs associated with traditional casting or forging can be prohibitive. Metal AM offers a cost-effective way to produce complex suspension parts without investing in expensive molds or dies, enabling greater design differentiation.
- Prototip Oluşturma ve Geliştirme: AM drastically accelerates the design-build-test cycle. Engineers can produce functional suspension prototypes in days rather than weeks or months, allowing for rapid validation of new geometries, lightweighting strategies, and kinematic concepts before committing to mass production tooling. This reduces development risk and time-to-market.
- Aftermarket & Customization: The performance aftermarket thrives on differentiation and enhanced capability. Metal AM enables the production of bespoke, high-performance suspension upgrades (e.g., ultra-lightweight control arms, adjustable components) for EV owners seeking improved handling or specific aesthetics. Suppliers catering to the wholesale EV parts market can leverage AM for unique product offerings.
- Spare Parts & Legacy Systems: For older or out-of-production EV models, AM can provide a solution for producing obsolete suspension components on demand, avoiding the need for large inventory holdings or restarting traditional production lines.
Key B2B target audiences actively exploring or benefiting from 3D printed EV suspension components include:
- Automotive OEMs: Integrating AM into their R&D for next-generation platforms and potentially for series production of specific high-value or complex components.
- Tier 1 Suppliers: Developing innovative suspension modules incorporating AM parts to offer enhanced value (weight reduction, performance) to their OEM customers. They often seek reliable AM partners or wholesale EV suspension parts manufacturers.
- Electric Motorsport Teams (Formula E, etc.): Early adopters pushing the boundaries of performance through heavily optimized, custom AM components.
- EV Conversion Specialists & Custom Builders: Utilizing AM for unique solutions needed when adapting powertrains and chassis.
- Specialized Engineering Consultancies: Designing and validating advanced suspension systems incorporating AM principles for various clients.
The opportunity lies in leveraging AM not just as a direct replacement, but as an enabler for entirely new design paradigms in EV suspension systems, ultimately contributing to lighter, more efficient, and better-performing electric vehicles. Finding a capable EV component manufacturer or automotive additive manufacturing partner like Met3dp, with the right equipment and material expertise, is crucial for realizing these opportunities.
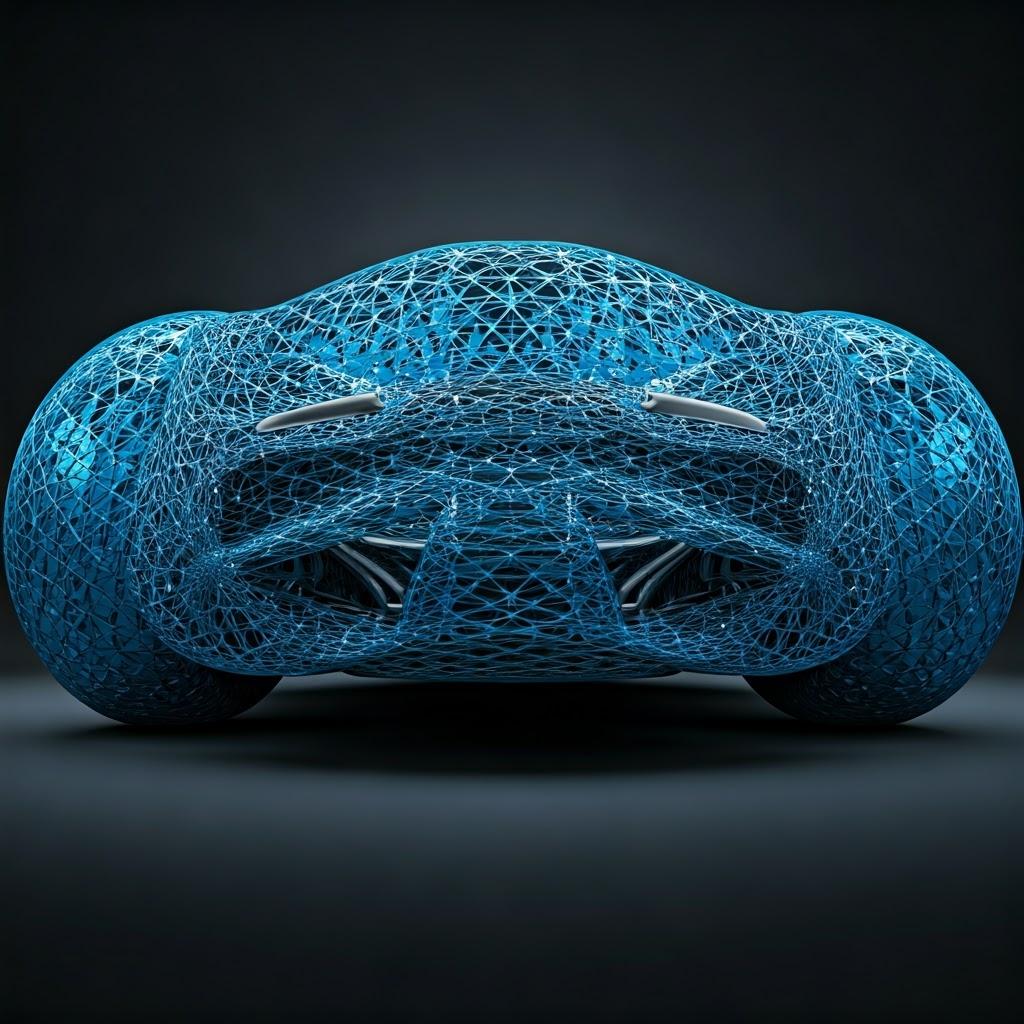
Why Use Metal 3D Printing for EV Suspension Components? Unlocking Design Freedom and Performance Gains
While traditional manufacturing methods like casting, forging, and CNC machining have served the automotive industry well for decades, they inherently possess limitations, particularly when striving for the aggressive lightweighting and design optimization required for modern EVs. Metal additive manufacturing offers a compelling alternative by overcoming many of these constraints, unlocking significant potential for enhancing EV suspension systems. Understanding these differences is key for engineers designing next-generation vehicles and procurement managers sourcing innovative components.
Comparison: Metal AM vs. Traditional Manufacturing for EV Suspension Parts
Özellik | Metal Additive Manufacturing (e.g., LPBF) | Traditional Casting (e.g., Aluminum) | Traditional Forging (e.g., Aluminum) | Geleneksel CNC İşleme |
---|---|---|---|---|
Tasarım Karmaşıklığı | Very High (complex geometries, internal channels, lattices) | Moderate (limited by mold design) | Low to Moderate (simpler shapes) | High (but subtractive, can be limited) |
Hafifletme | Excellent (topology optimization, thin walls, lattices) | Moderate (requires thick sections) | Good (good strength, but limited shapes) | Good (material removal, but starts solid) |
Parça Konsolidasyonu | Excellent (can combine multiple parts into one) | Sınırlı | Very Limited | Sınırlı |
Kalıp Maliyeti | None (direct digital manufacturing) | High (mold creation) | Very High (die creation) | Low (fixtures may be needed) |
Lead Time (Proto) | Very Fast (days) | Slow (weeks/months for tooling) | Very Slow (months for tooling) | Fast (days/weeks, depends on complexity) |
Lead Time (Series) | Moderate (depends on part size/quantity, improving rapidly) | Fast (once tooling exists) | Fast (once tooling exists) | Moderate to Slow (depends on complexity) |
Malzeme Atıkları | Low (near-net shape, powder recyclability) | Moderate (runners, gates, machining) | Moderate (flash, machining) | High (significant material removal) |
Malzeme Seçenekleri | Growing range (Al, Ti, Steel, Ni alloys), some limitations | Established range (specific casting alloys) | Established range (specific forging alloys) | Wide range (any machinable block/bar) |
Ideal Volume | Prototypes, Low-to-Medium Volume, Custom Parts | Medium-to-High Volume | High Volume | Prototypes, Low-to-Medium Volume |
Sayfalara Aktar
Based on this comparison, the specific advantages of using metal AM for EV suspension components become clear:
- Unparalleled Lightweighting: This is arguably the most significant driver for AM adoption in EV suspensions.
- Topology Optimization: Software algorithms can redesign a part based on load paths, removing material where it’s not needed while maintaining structural integrity. This often results in organic, bone-like structures that are impossible to cast or forge.
- Kafes Yapılar: AM can create internal lattice structures within components, drastically reducing weight while maintaining specific stiffness or energy absorption characteristics. Control arms or uprights can be partially hollowed and filled with optimized lattices.
- Reduced Unsprung Mass: As discussed earlier, lightweighting suspension components directly reduces unsprung mass, leading to significant improvements in handling, ride comfort, and energy efficiency (range).
- Parça Konsolidasyonu: Complex assemblies involving multiple brackets, fasteners, and individual components can often be redesigned and printed as a single, integrated part.
- Avantajlar: Reduced part count simplifies inventory and assembly, lowers overall weight by eliminating fasteners, and removes potential failure points at joints, improving reliability. An upright, for instance, might integrate brake caliper mounts, sensor brackets, and dust shield attachments into one printed piece.
- Geometric Freedom & Performance Optimization: AM liberates designers from the constraints of draft angles (casting), die limitations (forging), or tool access (machining).
- Complex Shapes: Engineers can design components with internal cooling channels (e.g., for high-performance brake integration), optimized fluid paths for dampers, or complex curved surfaces that perfectly match packaging constraints within the chassis.
- Geliştirilmiş İşlevsellik: Mounting points, cable routing channels, and sensor housings can be integrated seamlessly into the design.
- Hızlı Prototipleme ve Tasarım İterasyonu: The ability to go directly from a CAD file to a functional metal part in days is transformative for the development process.
- Faster Validation: Engineers can test multiple design variations of a suspension component quickly and cost-effectively on prototype vehicles.
- Reduced Risk: Performance and fitment can be confirmed early in the design cycle before committing to expensive tooling for mass production (if AM is used only for prototyping).
- Malzeme Verimliliği: Powder bed fusion processes typically use only the material needed for the part and support structures.
- Azaltılmış Atık: Unfused powder can often be recycled and reused, making it significantly less wasteful than subtractive CNC machining, which starts with a solid block and removes large amounts of material. This is especially beneficial for expensive alloys.
- Viability for Low-Volume and On-Demand Production: For niche EV models, performance upgrades, or spare parts, AM provides an economically viable manufacturing route without the upfront investment in tooling. This allows manufacturers to cater to specialized market segments and offer greater customization. Wholesale EV parts distributors can leverage this for unique aftermarket offerings.
Met3dp plays a crucial role in enabling automotive companies to harness these advantages. By providing industry-leading metal 3D baskı sistemleri known for their accuracy and reliability, alongside high-quality, optimized metal powders specifically designed for demanding applications, Met3dp empowers engineers to push the boundaries of suspension design. Their expertise ensures that the theoretical benefits of AM translate into tangible performance gains and weight savings for critical EV components. Engaging with an additive manufacturing automotive solutions provider early in the design process is key to maximizing the potential of this technology.
Recommended Materials: AlSi10Mg and A7075 Aluminum Alloys for Optimal Performance
Selecting the right material is paramount for ensuring the safety, performance, and durability of any automotive component, especially load-bearing suspension parts. For metal 3D printed EV suspension components, aluminum alloys are often the primary choice due to their excellent balance of low density and good mechanical properties. Two alloys stand out for their suitability, albeit with different strengths and processing considerations: AlSi10Mg and A7075.
AlSi10Mg: The Versatile Workhorse
AlSi10Mg is one of the most widely used aluminum alloys in additive manufacturing, particularly laser powder bed fusion (LPBF). It’s essentially a casting alloy composition adapted for AM processes.
- Kompozisyon: Primarily aluminum (Al), with significant additions of silicon (Si, ~9-11%) and magnesium (Mg, ~0.2-0.45%). Silicon improves fluidity and castability (beneficial for the melt pool dynamics in AM), while magnesium enables precipitation hardening through heat treatment.
- Key Properties (Post-Heat Treatment, e.g., T6):
- Mükemmel Güç-Ağırlık Oranı: Offers good tensile and yield strength suitable for many moderately loaded suspension components.
- Good Thermal Conductivity: Helps dissipate heat, which can be relevant depending on proximity to brakes or motors.
- İyi Korozyon Direnci: Generally performs well in typical automotive environments.
- Kaynaklanabilirlik: Can be welded, although specific procedures are recommended.
- Yazdırılabilirlik: Exhibits excellent processability in LPBF systems, with relatively well-understood parameter sets leading to dense, reliable parts.
- Advantages for EV Suspension Parts:
- Proven Track Record: Widely used in AM across various industries, including automotive prototyping and some series parts. Extensive data available on properties and performance.
- Good Balance: Offers a solid combination of strength, stiffness, low density, and processability.
- Maliyet-Etkinlik: Generally more affordable than higher-strength alloys or titanium.
- Isıl İşlem Uygulanabilir: T6 heat treatment (solutionizing and artificial aging) significantly boosts mechanical properties, making it suitable for structural applications.
- İşleme ile İlgili Hususlar:
- Requires stress relief post-printing to minimize distortion.
- T6 heat treatment is typically necessary to achieve optimal mechanical properties for structural use.
- While processable, achieving fully dense parts requires optimized parameters and high-quality powder.
- Met3dp’s Role: Met3dp specializes in producing high-quality, spherical AlSi10Mg powder using advanced gas atomization techniques. Their focus on powder characteristics like high sphericity, good flowability, controlled particle size distribution (PSD), and low oxygen content is crucial for achieving consistent, high-density parts with reliable mechanical properties in demanding LPBF processes. Procuring consistent, high-grade AlSi10Mg powder from a reputable supplier is fundamental for reliable production.
A7075: High-Strength Performance
A7075 is a high-performance aluminum alloy known for its exceptional strength-to-weight ratio, often comparable to some steels, making it highly desirable for demanding aerospace and automotive applications. Traditionally used in wrought forms (forged or machined), its adaptation for additive manufacturing presents both significant opportunities and challenges.
- Kompozisyon: Primarily aluminum (Al), with zinc (Zn, ~5.1-6.1%), magnesium (Mg, ~2.1-2.9%), and copper (Cu, ~1.2-2.0%) as major alloying elements. These elements contribute to its very high strength through precipitation hardening.
- Key Properties (Post-Heat Treatment, e.g., T6/T73):
- Very High Strength: Offers significantly higher tensile and yield strength compared to AlSi10Mg, approaching levels of some steel alloys but at roughly one-third the density.
- Mükemmel Yorulma Dayanımı: Crucial for components subjected to cyclic loading, like suspension parts.
- Good Hardness: Resists wear and abrasion better than many other aluminum alloys.
- Advantages for EV Suspension Parts:
- Maximum Lightweighting Potential: Its superior strength allows for thinner sections and more aggressive topology optimization, enabling further weight reduction in highly stressed components like uprights or control arms compared to AlSi10Mg.
- Yüksek Performanslı Uygulamalar: Ideal choice for motorsport EVs or performance road cars where maximizing strength and minimizing weight are critical design goals.
- Challenges & Processing Considerations in AM:
- Hot Cracking Susceptibility: The wide freezing range and composition of A7075 make it prone to solidification cracking (hot cracking) during the rapid heating/cooling cycles of LPBF. This has historically limited its widespread adoption in AM.
- Requires Advanced Process Control: Successfully printing A7075 typically requires specialized LPBF systems with precise control over parameters like laser power, scan speed, pre-heating, and gas flow. Modified compositions or nanoparticle inoculation are sometimes used to improve printability.
- Intensive Heat Treatment: Requires carefully controlled heat treatment cycles (e.g., T6, T73) to achieve desired strength, toughness, and stress corrosion cracking resistance.
- Powder Quality is Critical: Consistent powder chemistry, low contamination, and optimized PSD are even more crucial for processing challenging alloys like A7075.
- Met3dp’s Role: Successfully processing demanding alloys like A7075 requires both advanced equipment and superior powder quality. Met3dp’s investment in industry-leading powder production technologies (Gas Atomization and Plasma Rotating Electrode Process – PREP) allows them to potentially produce specialized powders like A7075 variants optimized for AM. Their advanced SEBM (Selective Electron Beam Melting) printers might also offer advantages for processing crack-sensitive alloys due to the vacuum environment and higher processing temperatures compared to LPBF. Consulting with experts like Met3dp is essential when considering high-strength aluminum alloys like A7075 for AM projects. They can advise on material suitability, process parameters, and necessary post-processing. For businesses looking to secure a reliable source, identifying a specialized A7075 metal powder bulk supplier or distributor with proven AM expertise is key.
Comparison Table: AlSi10Mg vs. A7075 for 3D Printed EV Suspension
Özellik | AlSi10Mg | A7075 (AM Processed) | Considerations for EV Suspension |
---|---|---|---|
Birincil Fayda | Balanced properties, good printability | Very high strength-to-weight | Choose based on specific load case and lightweighting target. |
Çekme Dayanımı | Good (after T6) | Excellent (significantly higher, after T6) | A7075 allows for more aggressive weight reduction under high stress. |
Yoğunluk | Low (~2.67 g/cm³) | Low (~2.81 g/cm³) | Both offer significant weight savings over steel. |
Printability (LPBF) | Mükemmel | Challenging (prone to hot cracking) | Requires specialized equipment and process control for A7075. |
Isıl İşlem | Required (e.g., T6) for optimal properties | Required (e.g., T6, T73), critical control | Post-processing complexity is higher for A7075. |
Korozyon Direnci | İyi | Moderate (can be susceptible to SCC) | Surface treatment (anodizing, coating) often recommended for A7075. |
Cost (Powder) | Orta düzeyde | Yüksek | A7075 is a premium material choice. |
Typical Use Case | General suspension parts, prototypes | Highly loaded components, motorsport | Match material to the specific demands of the component. |
Sayfalara Aktar
Conclusion on Materials:
Both AlSi10Mg and A7075 offer compelling advantages for 3D printed EV suspension components. AlSi10Mg represents a reliable, well-understood, and cost-effective choice for many applications, providing significant benefits over traditional methods. A7075 pushes the boundaries of performance, offering maximum strength and lightweighting potential for the most demanding scenarios, but requires careful consideration of its processing challenges. The choice depends heavily on the specific component requirements, performance targets, budget, and the capabilities of the chosen manufacturing partner. Partnering with a knowledgeable provider like Met3dp, who not only offers advanced printing solutions but also produces a wide range of yüksek performanslı metal tozları, ensures access to quality materials and the expertise needed to select and process them effectively for optimal results in EV suspension applications.
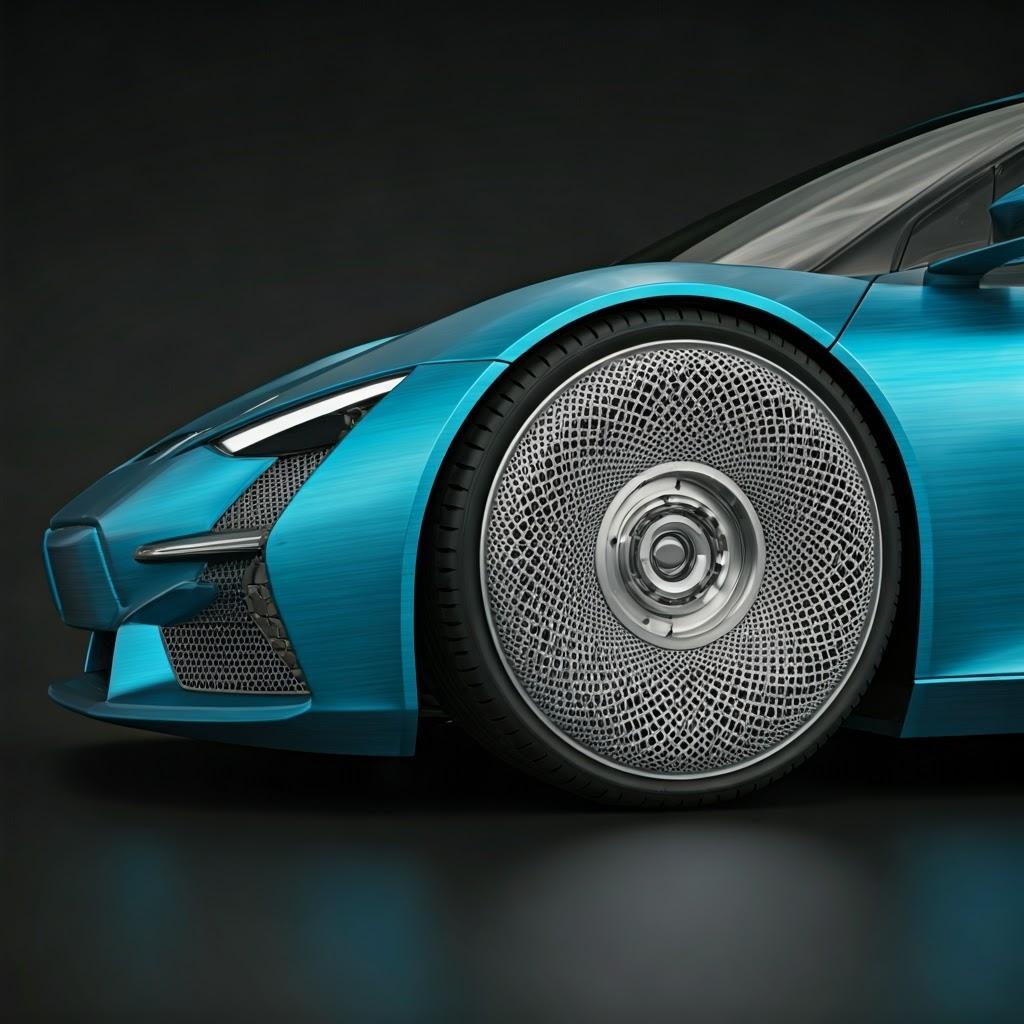
Design Considerations for Additive Manufacturing (DfAM) of EV Suspension Parts
Simply taking a suspension component designed for casting or forging and directly 3D printing it rarely unlocks the full potential of additive manufacturing. To truly leverage the benefits of AM – particularly lightweighting, part consolidation, and performance enhancement – engineers must embrace Design for Additive Manufacturing (DfAM). DfAM is not just a set of rules but a change in mindset, thinking natively about how parts are built layer by layer and how geometric freedom can be exploited. For critical, load-bearing components like EV suspension parts, applying DfAM principles is essential for success.
Key DfAM Principles for EV Suspension Components:
- Topology Optimization: This is often the starting point for radical lightweighting.
- Süreç: Engineers define the design space (maximum allowable volume), load cases (forces, moments), constraints (mounting points, keep-out zones), and optimization goals (e.g., minimize mass while maintaining stiffness). Specialized software then iteratively removes material from non-critical areas, leaving behind an optimized load-bearing structure.
- Result: Organic, often complex-looking geometries that efficiently distribute stress, achieving significant weight reductions (often 20-50% or more) compared to traditional designs. Control arms and uprights are prime candidates.
- Consideration: Optimized designs must still be manufacturable via AM, considering factors like overhangs and minimum feature sizes. Collaboration with AM experts during optimization is beneficial.
- Lattice Structures & Infill Strategies: AM allows for the creation of internal lattice structures – repeating unit cells – within otherwise solid volumes.
- Avantajlar: Dramatically reduces weight and material usage while maintaining tailored structural properties (stiffness, energy absorption). Can improve thermal management or vibration damping.
- Uygulama: Filling partially hollowed-out sections of control arms, uprights, or subframe components. Different lattice types (e.g., cubic, octet-truss) offer different properties.
- Consideration: Requires careful simulation (FEA) to validate performance. Powder removal from complex internal lattices can be challenging and must be considered during design.
- Support Structure Strategy & Overhangs: In powder bed fusion processes (like LPBF), downward-facing surfaces beyond a certain angle (typically <45 degrees from horizontal) require support structures to prevent collapse or warping during the build.
- Design Goal: Minimize the need for supports, as they consume extra material, add print time, require post-processing removal (which can damage surfaces), and can limit design freedom.
- Techniques:
- Oryantasyon: Choosing the optimal build orientation can significantly reduce support requirements.
- Kendini Destekleyen Açılar: Designing overhangs with angles greater than 45 degrees wherever possible.
- Chamfers/Fillets: Replacing sharp horizontal overhangs with angled or curved transitions.
- Designing for Removal: Ensuring supports are accessible for easy removal without damaging critical features. Breakaway points can be designed in.
- Suspension Specifics: Mounting bosses, connection points, and the arms of wishbones need careful orientation and potential local redesign to minimize supports.
- Minimum Wall Thickness & Feature Size: AM processes have limitations on the smallest features and thinnest walls they can reliably produce.
- Typical Limits (LPBF Aluminum): Minimum wall thickness might be around 0.4-0.8 mm, and minimum positive features (like pins) around 0.3-0.5 mm, depending on the specific machine and parameters.
- Design Rule: Ensure all structural walls and features meet or exceed the minimum manufacturable size for the chosen process and material. Overly thin walls can lead to incomplete melting or part failure.
- Etki: This influences the level of detail achievable in lightweighting features or small integrated brackets.
- Parça Konsolidasyonu: Actively look for opportunities to combine multiple adjacent parts into a single, more complex AM component.
- Example: An upright assembly might traditionally involve a main cast/forged body, a separate brake caliper bracket, sensor mounts, and dust shield attachments. A DfAM approach would aim to integrate all these functions into a single, topologically optimized printed upright.
- Avantajlar: Reduced assembly labor, elimination of fasteners (weight saving, potential failure points), improved structural efficiency.
- Requires: Holistic view of the suspension sub-assembly and collaboration between different engineering disciplines.
- Designing for Load Paths: AM allows aligning the material deposition, to some extent, with the primary stress directions in the component.
- Anizotropi: AM parts can exhibit anisotropic behavior (different properties in different directions relative to the build plate). While less pronounced in metals than polymers, it’s still a factor.
- Strategy: Orient the part during build setup so that critical tensile or fatigue loads are not acting perpendicular to the layer lines (typically the weakest direction, Z-axis). Simulation (FEA) is crucial to understand stress distribution.
- Simulation-Driven Design: Finite Element Analysis (FEA) is indispensable in DfAM for suspension parts.
- Validation: Used to verify the structural integrity, stiffness, and fatigue life of topologically optimized or lattice-filled designs under various load conditions (braking, cornering, impacts).
- Optimization Feedback: Results can guide further refinement of the geometry.
- Process Simulation: Increasingly used to predict thermal stresses, potential warping, and optimize support structures before printing, saving time and material.
Collaboration is Key: Successfully implementing DfAM for complex parts like EV suspensions often requires collaboration between design engineers and AM specialists. Companies like Met3dp possess not only advanced manufacturing capabilities but also deep application knowledge. Met3dp’s collective expertise in materials science, process parameters, and DfAM principles can provide invaluable guidance to automotive teams looking to optimize their suspension components for additive manufacturing. Engaging with such partners early in the design phase ensures manufacturability and maximizes the benefits achievable through AM. Procurement managers should look for suppliers who offer robust DfAM support as part of their service offering.
Achievable Tolerance, Surface Finish, and Dimensional Accuracy in Metal AM
While metal additive manufacturing offers incredible design freedom, it’s crucial for engineers and procurement managers to have realistic expectations regarding the achievable dimensional accuracy, tolerances, and surface finish of 3D printed EV suspension components. These factors directly impact component fit, function, and the need for subsequent post-processing steps. Understanding the capabilities and limitations of technologies like Laser Powder Bed Fusion (LPBF) is key to successful implementation.
Dimensional Accuracy & Tolerances:
- General Expectations: Metal AM processes like LPBF can achieve good dimensional accuracy, but typically not yet matching the precision of high-end CNC machining in the as-built state.
- Typical Tolerances: For well-controlled processes using aluminum alloys like AlSi10Mg or A7075, typical achievable tolerances often fall within the range of:
- Smaller Parts (<100mm): ±0.1 mm to ±0.2 mm
- Larger Parts (>100mm): ±0.1% to ±0.2% of the nominal dimension
- International standards like ISO 2768 (general tolerances) are often referenced, with AM parts typically achieving medium (m) or sometimes fine (f) classes for linear dimensions, depending on the specific feature, size, and process control. However, geometric tolerances (flatness, parallelism, position) might be looser without post-machining.
- Factors Influencing Accuracy:
- Printer Calibration & Condition: Regular calibration, laser focus, and machine health are critical. Met3dp emphasizes the industry-leading accuracy and reliability of their printers for mission-critical parts.
- Termal Stresler: The rapid heating and cooling inherent in AM induce internal stresses that can cause warping and distortion during the build or after removal from the build plate. Part geometry, orientation, and support strategy heavily influence this.
- Part Geometry & Size: Large, complex parts or those with significant changes in cross-section are more prone to deviation.
- Malzeme Özellikleri: Different alloys exhibit different shrinkage rates and thermal behavior.
- Süreç Parametreleri: Laser power, scan speed, layer thickness, and gas flow must be optimized for the specific material and geometry.
- Destek Yapıları: How well the part is anchored to the build plate affects stability and accuracy.
- İşlem sonrası: Stress relief heat treatments can cause minor dimensional changes; machining achieves final tight tolerances.
Yüzey İşlemi (Pürüzlülük):
- As-Built Surface: Parts directly out of an LPBF machine have a characteristic surface roughness resulting from the sintered powder particles.
- Typical Ra Values: For aluminum alloys, as-built surface roughness (Ra) typically ranges from 6 µm to 20 µm (micrometers), depending on orientation, parameters, and particle size. Upward-facing surfaces are generally smoother than downward-facing surfaces (supported) or vertical walls.
- Görünüş: Matte, slightly granular texture.
- Impact on Performance: For many suspension applications, the as-built surface may be acceptable for non-critical areas. However, for mating surfaces, bearing bores, or areas requiring specific flow characteristics or fatigue resistance, post-processing is necessary.
- Post-Processing for Improved Finish:
- CNC İşleme: Provides the smoothest, most precise surfaces (Ra < 1 µm possible). Essential for critical interfaces.
- Parlatma: Manual or automated polishing can significantly improve smoothness and aesthetics (Ra 1-3 µm achievable, lower with more effort).
- Tumbling/Vibratory Finishing: Can smooth surfaces and deburr edges, particularly for smaller parts (Ra 3-6 µm).
- Shot Peening/Blasting: Primarily used to improve fatigue life by inducing compressive stress, but also alters surface texture (typically makes it rougher but more uniform).
Managing Expectations & Design Implications:
- Critical Features: Engineers must identify surfaces and features requiring tight tolerances or specific finishes (e.g., bearing interfaces, mounting holes, connection points for ball joints). These areas should be designed with extra material (machining stock) to allow for post-machining to final specifications.
- Non-Critical Features: Surfaces not involved in precise mating or subject to high fatigue can often remain in the as-built or minimally processed state, saving cost and time.
- Supplier Capability: Discuss tolerance and finish requirements clearly with your chosen precision metal 3D printing supplier. They should be able to provide realistic estimates based on their equipment (like Met3dp’s reliable systems), process controls, and experience. Request sample parts or data from previous similar projects if possible.
- Cost Trade-off: Achieving tighter tolerances and finer surface finishes generally requires more intensive post-processing, adding to the overall cost and lead time. DfAM principles should aim to minimize the need for extensive finishing where possible.
In summary, while metal AM produces functional parts directly, achieving the very tight tolerances and smooth finishes required for certain features of EV suspension components usually necessitates secondary machining operations. Understanding the as-built capabilities and planning for necessary post-processing steps is crucial for effective design, cost estimation, and procurement when adopting AM for these demanding applications. Reliable equipment and process control, as offered by leading providers, form the foundation for achieving the best possible accuracy from the AM process itself.
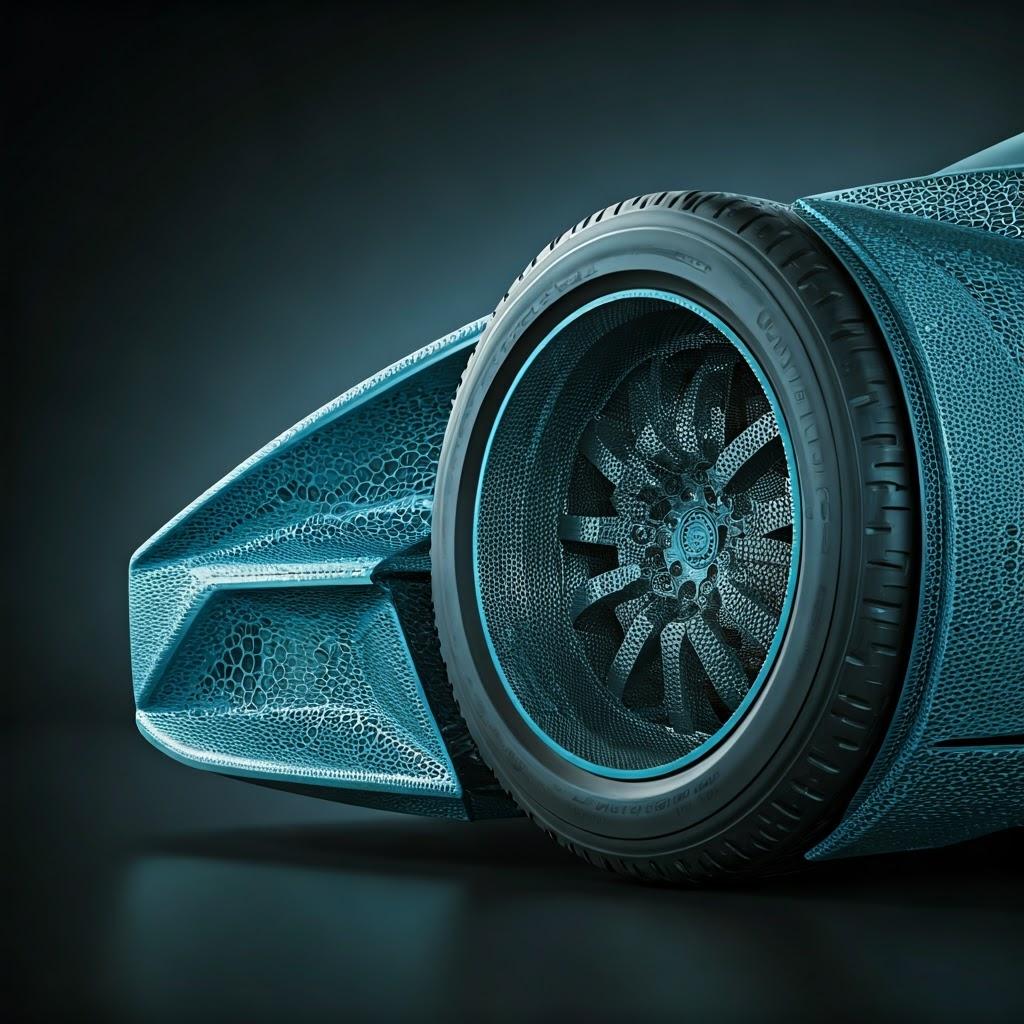
Essential Post-Processing Requirements for 3D Printed Suspension Components
Additive manufacturing is rarely the final step in producing functional, reliable EV suspension components. A series of essential post-processing steps are typically required to transform the as-built metal part into a finished product that meets stringent automotive standards for mechanical properties, dimensional accuracy, surface quality, and durability. Overlooking or underestimating these steps can compromise component performance and safety.
Common Post-Processing Steps for AM Aluminum Suspension Parts (AlSi10Mg, A7075):
- Stres Giderici / Isıl İşlem: This is arguably the most critical post-processing step for load-bearing AM components.
- Amacımız:
- Reduce Residual Stresses: The rapid heating/cooling cycles during LPBF create significant internal stresses within the part. These stresses can cause warping upon removal from the build plate, dimensional instability over time, and potentially lead to premature failure. Stress relief (typically done before removing supports) mitigates this.
- Achieve Desired Mechanical Properties: As-built aluminum alloys often have suboptimal strength and ductility. Heat treatment (specifically precipitation hardening cycles like T6) dissolves alloying elements into the aluminum matrix and then precipitates them as fine particles, significantly increasing strength, hardness, and durability.
- Typical Cycles:
- Stres Giderici: Heating to a moderate temperature (e.g., 300°C for AlSi10Mg) for a few hours.
- T6 Temper (Example):
- Çözüm Tedavisi: Heating to a high temperature (~500-540°C, below melting) to dissolve alloying elements.
- Söndürme: Rapid cooling (water or polymer) to trap elements in solution.
- Artificial Aging: Heating to a lower temperature (e.g., 150-180°C) for several hours to precipitate strengthening phases (Mg₂Si for AlSi10Mg; complex phases for A7075).
- Importance: Absolutely essential for parts made from AlSi10Mg and especially the high-strength A7075 to achieve their target properties and ensure long-term performance under cyclic loading. Process parameters (time, temperature) must be precisely controlled based on the specific alloy and desired properties.
- Amacımız:
- Part Removal from Build Plate & Support Removal:
- Separation: Parts are typically cut from the build plate using wire EDM (Electrical Discharge Machining) or a band saw.
- Destek Kaldırma: This can be labor-intensive. Supports are removed using manual tools (pliers, cutters), machining, or sometimes specialized vibration/chemical methods.
- Design Impact: As discussed in DfAM, designing for easy support access and removal is crucial to minimize manual labor and avoid damaging the part surface. Breakaway points can be incorporated.
- CNC İşleme: Required to achieve tight tolerances and specific surface finishes on critical features.
- Uygulamalar:
- Machining mating surfaces for precise assembly.
- Creating threads for fasteners.
- Boring holes for bearings, bushings, or ball joints to precise diameters and roundness.
- Achieving specific flatness or parallelism on mounting faces.
- Removing machining stock left intentionally during the design phase.
- Consideration: Requires accurate fixturing of the potentially complex AM part. The T6 heat treatment typically performed earlier makes the aluminum harder and more challenging to machine than in its annealed state.
- Uygulamalar:
- Surface Finishing & Cleaning: Improves aesthetics, corrosion resistance, and potentially fatigue life.
- Temizlik: Removing any residual powder, particularly from internal channels or complex lattice structures (may require compressed air, ultrasonic cleaning).
- Shot Peening: Bombarding the surface with small spherical media (shot) induces compressive residual stresses on the surface layer. This is highly effective at increasing fatigue life, which is critical for suspension components subjected to constant cyclic loads. It also creates a uniform matte texture.
- Tumbling/Vibratory Finishing: Smooths surfaces, removes minor burrs, and can provide a consistent finish.
- Parlatma: For aesthetic requirements or specific functional surfaces needing very low roughness.
- Anodizing: An electrochemical process that creates a hard, protective aluminum oxide layer. Improves corrosion and wear resistance, and allows for coloring (often used for aftermarket parts). Essential for enhancing the corrosion protection of alloys like A7075.
- Painting/Coating: Applying automotive-grade paints or specialized coatings (e.g., powder coating) for maximum environmental protection and desired aesthetics.
- Inspection & Quality Control (QC): Verifying that the finished part meets all specifications.
- Tahribatsız Muayene (NDT):
- CT Scanning (Computed Tomography): Provides detailed 3D visualization of the internal structure, allowing detection of porosity, inclusions, or internal cracks without destroying the part. Increasingly important for critical AM components.
- Dye Penetrant Inspection: Used to detect surface-breaking cracks.
- Ultrasonic Testing: Can detect subsurface flaws.
- Boyutsal Doğrulama: Using Coordinate Measuring Machines (CMM), 3D scanners, or traditional metrology tools to confirm critical dimensions and tolerances are met.
- Material Property Testing: Often involves testing representative samples printed alongside the main part (or sacrificial sections) to verify tensile strength, hardness, and microstructure after heat treatment.
- Tahribatsız Muayene (NDT):
Workflow & Supplier Choice: Managing these diverse post-processing steps requires careful planning and often involves multiple specialized vendors or a primary metal AM post-processing services provider with comprehensive capabilities. When selecting an AM partner for EV suspension components, procurement managers should inquire about their in-house post-processing capabilities and their network of trusted partners to ensure a streamlined, quality-controlled workflow from raw powder to finished, validated part.
Common Challenges in 3D Printing EV Suspension Parts and Mitigation Strategies
While metal additive manufacturing offers immense potential for EV suspension components, it’s not without its challenges. Understanding these potential issues and implementing effective mitigation strategies is crucial for achieving consistent, high-quality results suitable for demanding automotive applications. Collaborating with experienced partners like Met3dp, who understand the nuances of the process and materials, is key to navigating these hurdles.
1. Warping and Distortion:
- Meydan okumak: Significant temperature gradients during the LPBF process (melting at >600°C, surrounding powder near ambient) create internal stresses. As the part cools, these stresses can cause it to warp, distort, or even detach from the build plate, leading to dimensional inaccuracies or build failures. This is particularly prevalent in large parts or those with asymmetric geometries.
- Mitigation Strategies:
- Simulation: Thermal-mechanical process simulation can predict areas prone to high stress and distortion before printing, allowing for adjustments.
- Optimize Edilmiş Yönlendirme: Selecting a build orientation that minimizes large flat surfaces parallel to the build plate and reduces thermal gradients.
- Sağlam Destek Yapıları: Well-designed supports anchor the part firmly to the build plate, resist shrinkage forces, and help conduct heat away. Software tools can optimize support placement and type.
- Process Parameter Control: Fine-tuning laser parameters (power, speed, hatching patterns) can influence the thermal history and reduce stress accumulation. Advanced systems offer real-time monitoring.
- Stress Relief Heat Treatment: Performing a stress relief cycle immediately after printing, often before removing the part from the build plate, is crucial for relaxing internal stresses.
2. Porosity:
- Meydan okumak: The presence of small voids or pores within the printed material. Porosity can significantly degrade mechanical properties, particularly fatigue strength and ductility, making it unacceptable for critical suspension components. Pores can arise from gas trapped within the powder or melt pool (gas porosity) or incomplete melting/fusion between layers or scan tracks (lack of fusion porosity).
- Mitigation Strategies:
- High-Quality Metal Powder: This is paramount. Using powder with high sphericity, good flowability, low internal gas content, and controlled particle size distribution minimizes gas porosity. Met3dp’s focus on advanced gas atomization and PREP technologies directly addresses this, ensuring high-purity, dense powders. Procuring from a reputable metal powder distributor is essential.
- Optimize Edilmiş Süreç Parametreleri: Ensuring sufficient energy density (laser power, scan speed, layer thickness) to fully melt the powder and achieve good fusion between layers. Correct inert gas flow within the build chamber removes processing by-products.
- Sıcak İzostatik Presleme (HIP): A post-processing step involving high temperature and high isostatic pressure. HIP can effectively close internal pores (both gas and lack-of-fusion), significantly improving density and mechanical properties. Often specified for critical aerospace and medical parts, and increasingly considered for demanding automotive AM components.
3. Support Structure Removal Difficulty:
- Meydan okumak: While necessary, support structures can be difficult and time-consuming to remove, especially from complex internal geometries or delicate features. Removal processes can potentially damage the part surface or leave undesirable marks (witness marks).
- Mitigation Strategies:
- DfAM: Designing parts to be self-supporting where possible (angles >45°), minimizing the volume of supports needed.
- Accessible Supports: Ensuring supports are placed in areas that are easily reachable with tools or machining after the build.
- Optimized Support Design: Using support structures with lower density, specialized geometries (e.g., tree supports), or designed breakaway points to facilitate easier removal. AM software offers various support strategies.
- Appropriate Removal Techniques: Using the right tools and techniques (manual breaking, machining, wire EDM) based on the support type and part geometry.
4. Residual Stress Management:
- Meydan okumak: Even if warping is controlled during the build, residual stresses remain within the part. These can affect long-term dimensional stability, reduce fatigue life, and increase susceptibility to cracking, especially in high-strength alloys like A7075.
- Mitigation Strategies:
- Mandatory Heat Treatment: As mentioned previously, stress relief and appropriate aging/tempering heat treatments (like T6) are essential not just for mechanical properties but also for significantly reducing residual stresses to acceptable levels.
- Simulation-Guided Support: Supports can be strategically placed not only to prevent warping but also to help manage stress accumulation during the build.
- Plaka Isıtması Oluşturun: Some LPBF machines offer build plate heating, which can reduce thermal gradients and lower residual stress levels, particularly beneficial for crack-sensitive alloys.
5. Material Property Validation & Consistency:
- Meydan okumak: Ensuring that the mechanical properties (strength, ductility, fatigue life) of the final printed and post-processed part consistently meet the design specifications and automotive requirements. Properties can be influenced by powder batch variations, minor process parameter drifts, and post-processing consistency.
- Mitigation Strategies:
- Rigorous Process Control: Implementing strict quality control throughout the workflow, from powder qualification to printing parameter monitoring and post-processing validation. Leading providers like Met3dp emphasize the reliability and process stability of their equipment.
- Malzeme Sertifikasyonu: Using certified metal tozları with traceable chemistry and properties.
- Batch Testing: Printing test coupons alongside actual parts for each build or batch and performing destructive testing (tensile tests, hardness tests, metallography) to verify properties.
- Tahribatsız Muayene (NDT): Employing methods like CT scanning to ensure internal integrity for every critical part.
- Standartlaştırma: Adhering to established industry standards (ASTM, ISO, SAE) for AM processes, materials, testing, and qualification.
Addressing these challenges requires a combination of careful design (DfAM), high-quality materials, advanced and well-maintained equipment, precisely controlled processes, thorough post-processing, and rigorous quality assurance. It highlights the importance of partnering with an experienced metal AM service provider or investing in robust in-house capabilities supported by reputable equipment manufacturers like Met3dp.
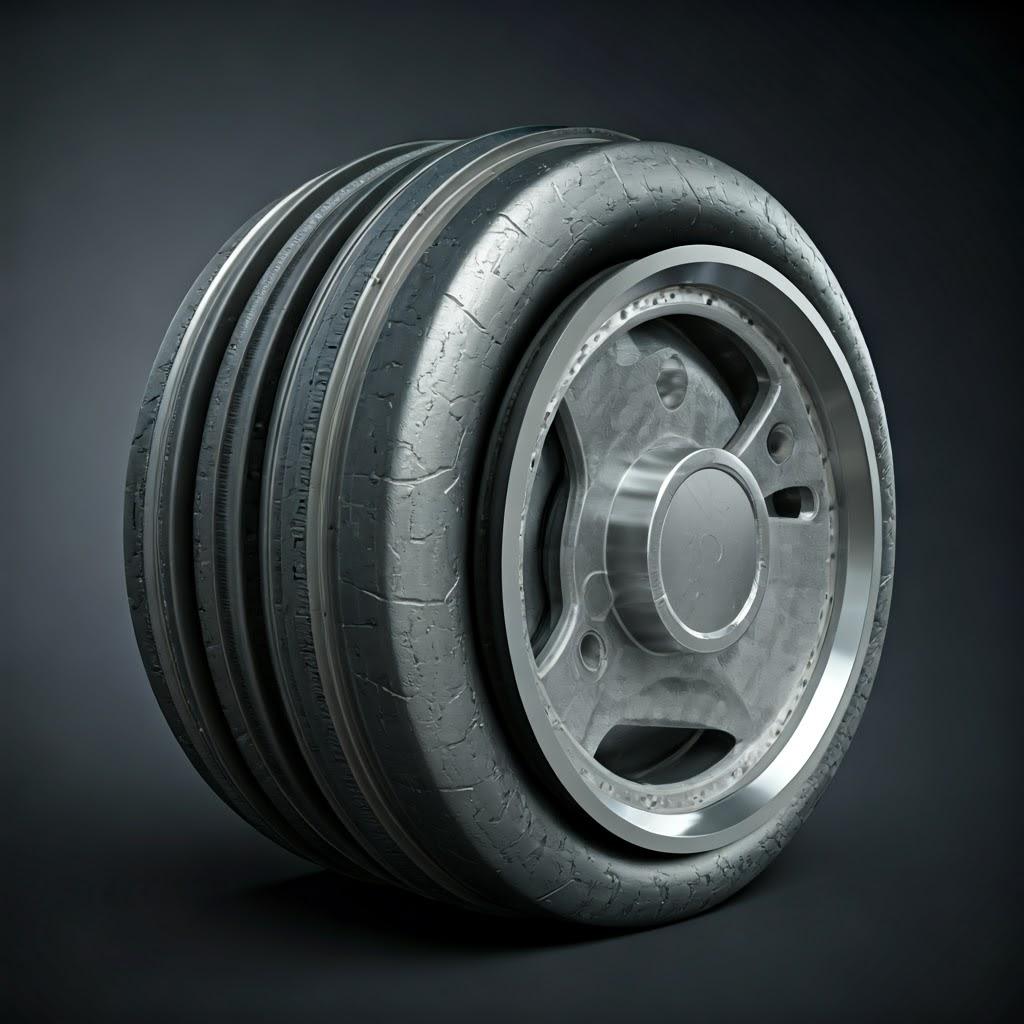
How to Choose the Right Metal 3D Printing Service Provider or Equipment Supplier for EV Components
Selecting the right partner for producing critical components like EV suspension parts via metal additive manufacturing is as crucial as the design and material selection itself. Whether you are seeking a service bureau for contract manufacturing or considering investing in in-house equipment, the evaluation criteria remain demanding, reflecting the high stakes of automotive applications. Making the wrong choice can lead to costly delays, substandard parts, and potential safety risks. For procurement managers and engineering leads, a thorough vetting process is essential.
Key Criteria for Evaluating Metal AM Suppliers (Service Bureaus & Equipment Providers):
- Material Expertise & Availability:
- Alloy Specialization: Does the supplier have proven, documented experience specifically with the required aluminum alloys (AlSi10Mg, A7075, or others)? Can they provide material datasheets based on their actual printed and heat-treated results?
- Powder Quality & Sourcing: Where do they source their metal powders? Do they have stringent quality control for incoming powder batches (chemistry, particle size distribution, flowability, morphology)? Suppliers like Met3dp, who manufacture their own high-quality metal powders using advanced techniques like Gas Atomization and PREP, offer greater control and traceability over this critical input material. Look for suppliers who can guarantee powder consistency, which is vital for reliable part properties – a key concern for any wholesale metal 3D printing services engagement.
- Range of Materials: While you may need specific alloys now, does the supplier offer a broader portfolio, indicating deep materials science knowledge and potential for future projects?
- Technological Capability & Equipment:
- Printer Technology: Are they using industry-leading equipment (e.g., LPBF, SEBM) suitable for the chosen material and application?
- Printer Specifications: Consider build volume (can they accommodate your part size?), laser power/beam control (influences speed and feature resolution), inert atmosphere control, and crucially, in-process monitoring capabilities (melt pool monitoring, thermal imaging) which enhance quality assurance. Met3dp prides itself on printers delivering industry-leading print volume, accuracy, and reliability.
- Range of Services: If using a service bureau, do they offer end-to-end solutions? This includes DfAM consultation, printing, post-processing (stress relief, heat treatment, machining, finishing), and quality inspection. A single point of contact simplifies procurement and project management.
- Yazılım: Do they utilize advanced simulation software for topology optimization and process simulation?
- Quality Management & Certifications:
- Quality Management System (QMS): Is the supplier certified to recognized standards like ISO 9001? This indicates a commitment to consistent processes and quality.
- Industry-Specific Standards: While full IATF 16949 certification (automotive QMS) might be rare for pure AM service providers currently, inquire about their awareness, compliance level, or roadmap towards it, especially if series production is intended. At minimum, they should demonstrate robust traceability, process control, and documentation practices aligned with automotive expectations.
- Süreç Kontrolü: How do they monitor and control critical process parameters? How do they ensure build-to-build consistency?
- Traceability: Can they provide full traceability from raw powder batch to finished part, including process data and post-processing records? This is non-negotiable for critical automotive components.
- Industry Experience & Proven Track Record:
- Automotive Experience: Have they successfully completed projects for other automotive clients, particularly in the EV sector or for structural/suspension applications?
- Case Studies & References: Can they provide relevant case studies or client references demonstrating their capabilities with similar parts or materials?
- Application Engineering Support: Do they have engineers who understand automotive requirements and can provide meaningful DfAM support and application development assistance? Met3dp highlights its decades of collective expertise in metal AM and application development.
- Capacity, Scalability & Lead Time:
- Üretim Kapasitesi: Do they have sufficient machine capacity to handle your prototyping needs and potentially scale to low-volume production if required? What is their typical machine utilization rate?
- Teslim Süreleri: Can they provide realistic and reliable lead time estimates for quoting, printing, and post-processing? How do they manage scheduling and potential bottlenecks, especially in the post-processing chain? Understand their standard vs. expedited options.
- Scalability Plan: If you anticipate increasing volumes, discuss their ability and strategy to scale production – adding machines, qualifying additional suppliers, etc.
- Technical Support & Partnership Approach:
- Communication: Are they responsive, transparent, and collaborative?
- DfAM Consultation: Do they proactively offer design advice to optimize parts for AM, reduce cost, and improve manufacturability?
- Problem Solving: How do they handle unexpected issues or build failures? A good partner works collaboratively to find solutions.
- Long-Term View: Are they interested in building a strategic partnership rather than just fulfilling transactional orders? This is vital for ongoing innovation and supply chain stability.
Choosing Equipment Suppliers (In-House Production):
If considering bringing metal AM in-house, many of the same criteria apply when evaluating equipment manufacturers like Met3dp:
- Machine Reliability & Performance: Proven uptime, accuracy, consistency.
- Material Processing Capabilities: Ability to reliably process the required alloys (AlSi10Mg, A7075).
- Training & Technical Support: Comprehensive training programs, responsive service technicians, application support.
- Powder Supply: Availability of qualified, high-quality powders compatible with their systems. Met3dp’s vertical integration (printers and powders) offers a significant advantage here.
- Software Ecosystem: User-friendly build preparation software, process monitoring tools.
- Upgrade Path & Future Development: Manufacturer’s commitment to ongoing R&D and machine upgrades.
Advice for Procurement Managers:
- Define Requirements Clearly: Provide detailed specifications: CAD models, material, tolerances, surface finish, required certifications, quantities, delivery dates.
- Request Sample Parts: Ask potential suppliers to produce a benchmark part or provide samples demonstrating their quality with the specific alloy.
- Conduct Audits: If possible, perform on-site audits (or thorough virtual audits) to assess their facilities, processes, and quality systems.
- Consider Total Cost of Ownership: Don’t just focus on the per-part price. Factor in DfAM support, quality assurance, reliability, and the cost of potential failures or delays.
- Build Relationships: Fostering strong relationships with key metal AM suppliers can provide access to innovation and capacity, especially in a rapidly evolving market.
Ultimately, selecting the right metal AM partner is a strategic decision. Look for providers who demonstrate not just technical proficiency but also a deep understanding of automotive requirements, a commitment to quality, and a collaborative approach. Companies like Met3dp, offering integrated solutions from advanced powders to reliable printing systems and expert support, represent the type of partner needed to successfully leverage AM for demanding applications like EV suspension components.
Cost Factors and Lead Time Analysis for 3D Printed EV Suspension Parts
While the performance benefits of 3D printed EV suspension components are compelling, understanding the associated costs and lead times is crucial for making informed business decisions, particularly for procurement managers and project leaders evaluating manufacturing options. Metal additive manufacturing has a different cost structure compared to traditional methods, making it more or less competitive depending on factors like complexity, volume, and design optimization.
Breakdown of Cost Drivers in Metal AM (LPBF):
- Malzeme Maliyeti:
- Powder Price: The cost per kilogram of the chosen metal powder (e.g., AlSi10Mg is less expensive than A7075 or titanium alloys). Prices vary based on alloy, quality specifications, and purchase volume (bulk discounts may apply from powder distributors).
- Material Consumed: The actual volume of the part dictates the primary material cost.
- Destek Yapıları: Material used for supports adds to the cost. Optimized design (DfAM) minimizes this.
- Powder Recycling/Waste: While much unused powder can be recycled, there are losses during handling and sieving, and powder degrades over multiple uses, eventually needing replacement. This contributes fractionally to the cost.
- Machine Time (Amortization & Operation):
- Makine Maliyeti: Metal AM systems represent a significant capital investment. This cost is amortized over the machine’s lifetime and factored into the hourly operating rate.
- Yapım süresi: The primary driver. This depends on:
- Part Volume: Larger parts take longer.
- Part Height: Directly influences the number of layers.
- Katman Kalınlığı: Thinner layers improve resolution but increase build time.
- Laser Power & Scan Speed: Faster parameters reduce time but must be balanced with quality.
- Yuvalama: Printing multiple parts simultaneously in one build maximizes machine utilization and reduces per-part time/cost.
- Consumables: Inert gas (Argon/Nitrogen), filters, recoater blades, etc.
- İşçilik Maliyetleri:
- Setup: Preparing the build file, loading powder, setting up the machine.
- Monitoring: Although often automated, some level of monitoring may be required.
- Breakdown/Cleaning: Removing the build, cleaning the part and the machine.
- İşlem sonrası: Significant labor is involved in support removal, machining, finishing, and inspection. This can often exceed the print time cost for complex parts requiring extensive finishing.
- İşlem Sonrası Maliyetler: Each step adds cost:
- Isıl İşlem: Furnace time, energy consumption.
- Destek Kaldırma: Labor, tools, potential for slight part damage/rework.
- İşleme: CNC machine time, programming, fixturing, tooling. Cost depends heavily on the number of features needing machining and the required precision.
- Yüzey İşlemi: Shot peening, tumbling, polishing, anodizing, painting – each has associated equipment, consumables, and labor costs.
- Teftiş: NDT (CT scanning can be expensive), CMM programming and operation time.
- Engineering & Design Costs:
- DfAM & Optimization: Time spent by engineers redesigning the part for AM, performing topology optimization, and running simulations. While an upfront investment, effective DfAM can significantly reduce material and print time costs later.
- Quality Assurance & Qualification: Costs associated with developing procedures, batch testing, documentation, and potential certification efforts.
Factors Influencing Lead Time:
- Quoting: Initial DfAM review and quote generation can take a few days.
- Print Time: From hours for small parts to several days for large, complex suspension components or nested builds.
- Machine Availability: Scheduling backlog at the service provider.
- İşlem sonrası: This often constitutes the longest portion of the lead time. Heat treatment cycles take hours, machining depends on complexity, and coordinating multiple external finishing steps adds significant time. A streamlined workflow with a single provider offering multiple services can shorten this.
- Typical Lead Time (Prototype): For a single complex suspension prototype (e.g., an upright) requiring printing, heat treatment, and some machining, lead times of 1-4 hafta are common, depending heavily on the factors above.
- Miktar: Printing multiple parts takes longer, but nesting can improve per-part time. Post-processing time often scales linearly with quantity.
- Nakliye: Transit time from the supplier.
Cost-Effectiveness vs. Traditional Methods:
- Prototypes & Low Volume (<~50-500 units): Metal AM is often highly cost-competitive or even cheaper because it eliminates the need for expensive tooling (molds/dies). The higher per-part cost is offset by avoiding huge upfront tooling investments.
- High Complexity: For parts with intricate geometries, internal channels, or topology-optimized designs that are difficult or impossible to cast/forge/machine, AM can be cost-effective even at slightly higher volumes because it enables designs that deliver significant performance or weight benefits (value-based costing).
- Parça Konsolidasyonu: If AM allows combining multiple parts into one, the savings in assembly, fasteners, and inventory can offset a higher individual part cost.
- Medium-to-High Volume (>~500-1000+ units): Traditional methods like casting and forging typically become more cost-effective per part once tooling costs are amortized over large quantities.
- Break-Even Point: The exact crossover volume depends heavily on part complexity, size, material, and the cost of traditional tooling. A detailed cost analysis is needed for each specific component.
Tips for Procurement & Cost Estimation:
- Provide Complete Information: Accurate quotes require detailed 3D CAD models (ideally native and STEP), material specifications, clear identification of critical tolerances and surfaces, finishing requirements, quantity needed, and desired delivery date.
- Leverage DfAM: Engage with suppliers early to optimize the design for AM, minimizing supports, material usage, and potentially post-processing needs.
- Consider Batching: Ordering multiple different parts or slightly higher quantities to be printed together (if feasible) can sometimes lead to better per-part pricing due to optimized machine utilization.
- Discuss Post-Processing Options: Understand the cost implications of different finishing levels. Does every surface need machining, or can some remain as-built?
Understanding the cost structure and lead time dynamics of metal AM allows for realistic budgeting, project planning, and strategic decision-making when considering this technology for EV suspension components. While not always the cheapest option, particularly at high volumes, its ability to deliver complex, lightweight, high-performance parts rapidly without tooling investment makes it a powerful tool in the EV development arsenal.
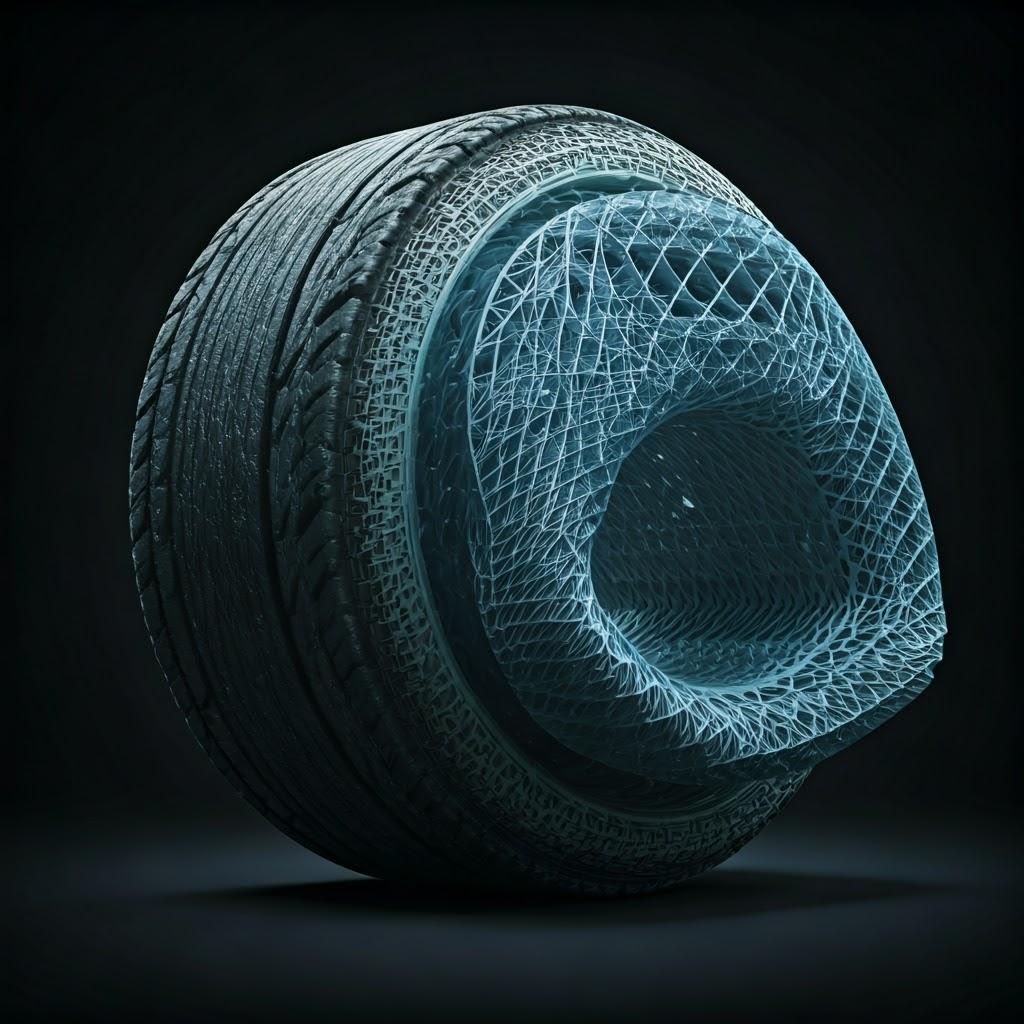
Sıkça Sorulan Sorular (SSS)
Q1: Are 3D printed aluminum suspension components strong enough for automotive use?
A: Yes, when designed, manufactured, and processed correctly. The key lies in selecting the appropriate alloy (like high-strength A7075 for demanding parts or the reliable AlSi10Mg), utilizing Design for Additive Manufacturing (DfAM) principles including topology optimization and simulation (FEA) to ensure structural integrity under load, employing high-quality metal powders (like those produced by Met3dp), ensuring a dense print through optimized process parameters, and performing essential post-processing steps like T6 heat treatment to achieve the required mechanical properties (strength, fatigue life, ductility). Rigorous testing and validation, often including physical testing alongside simulation, are crucial, just as with traditionally manufactured components. Metal AM parts meeting these criteria are used in motorsport and increasingly find their way into niche and high-performance road vehicles.
Q2: How does the cost of 3D printed suspension parts compare to cast or forged parts?
A: It depends heavily on volume and complexity.
- Prototypes & Low Volume (e.g., < 500 parts): 3D printing is often significantly cheaper because it avoids the extremely high upfront costs of casting molds or forging dies (which can run into tens or hundreds of thousands of dollars).
- High Volume (e.g., > 1000 parts): Traditional methods usually become more cost-effective per part, as the tooling cost is amortized over many units.
- Karmaşıklık: For highly complex designs that are difficult or impossible to cast/forge, or parts benefiting significantly from AM-enabled lightweighting or part consolidation, 3D printing can offer better value even at moderate volumes due to performance gains or assembly savings. A detailed cost analysis comparing tooling investment, per-part costs, and potential value benefits (like weight savings) is needed for specific cases.
Q3: What quality certifications should I look for in a metal AM supplier for automotive parts?
A: Look for suppliers with a robust Quality Management System (QMS).
- ISO 9001: This is a fundamental certification indicating established quality processes, documentation, and continuous improvement practices. It should be considered a minimum requirement for any professional manufacturing operation.
- IATF 16949: This is the specific QMS standard for the automotive industry. While full certification might still be emerging among dedicated AM service bureaus, suppliers demonstrating awareness, alignment with its principles (e.g., rigorous process control, traceability, risk management – FMEA), or progress towards compliance are preferable, especially for series production intent.
- Material Certifications: Ensure the supplier uses certified powders and can provide material test reports verifying the properties of printed and processed parts.
- Traceability: The ability to trace parts back to specific powder batches and process data is critical.
Q4: Can existing suspension component designs be directly 3D printed?
A: While technically possible, it’s generally not recommended and fails to leverage the key advantages of AM. Designs created for casting or machining often contain features (like draft angles or uniform wall thicknesses) that are unnecessary or suboptimal for 3D printing. Directly printing them might result in heavier, more expensive parts that require excessive support structures. To maximize benefits like lightweighting and performance, existing designs should be re-evaluated and optimized using Design for Additive Manufacturing (DfAM) principles, potentially involving topology optimization, lattice structures, and part consolidation.
Q5: What is the typical lead time for a prototype EV suspension component using metal 3D printing?
A: Lead times can vary significantly based on part size, complexity, material, required post-processing, and supplier backlog. However, for a complex prototype like an EV suspension upright requiring printing in aluminum (e.g., AlSi10Mg), heat treatment, support removal, and some critical CNC machining, a typical lead time might range from 1 to 4 weeks. This is often considerably faster than the months it could take to procure traditional tooling and receive first-off parts from casting or forging processes, highlighting AM’s advantage in accelerating development cycles. Always confirm lead times with your specific supplier based on your detailed requirements.
Conclusion: Accelerating EV Innovation with Metal Additive Manufacturing
The relentless drive towards electrification in the automotive industry demands continuous innovation, particularly in areas critical to overcoming range limitations and enhancing vehicle dynamics. Suspension systems, pivotal for both performance and efficiency, stand to gain immensely from the transformative capabilities of metal additive manufacturing. As we’ve explored, using advanced aluminum alloys like the versatile AlSi10Mg and the high-strength A7075, metal AM enables the creation of EV suspension components that are significantly lighter, structurally optimized, and feature complex geometries previously unattainable through traditional methods.
The benefits are clear: reduced unsprung mass translates directly to improved handling, better ride comfort, and increased energy efficiency or range. Part consolidation simplifies assembly lines and enhances reliability. The speed of AM facilitates rapid prototyping, allowing engineers to iterate designs faster and accelerate the entire vehicle development process. While challenges exist around DfAM, process control, and post-processing, they are increasingly being overcome through advanced equipment, high-quality materials, and deepening expertise within the industry.
Successfully implementing metal AM for these critical applications hinges on a holistic approach – embracing DfAM principles from the outset, carefully selecting the right materials for the job, understanding the nuances of the manufacturing process, and meticulously planning for necessary post-processing and validation. Crucially, it requires partnering with knowledgeable and capable suppliers or investing in proven in-house technology.
Met3dp stands as a leader in this space, providing comprehensive solutions that empower automotive manufacturers to harness the full potential of metal AM. With industry-leading SEBM printers known for accuracy and reliability, advanced metal powder production capabilities ensuring material quality, and decades of collective expertise in additive manufacturing, Met3dp is ideally positioned to support the development and production of next-generation EV suspension components.
Whether you are an engineer seeking to push the boundaries of lightweight design, a procurement manager looking for reliable additive manufacturing procurement pathways, or an automotive OEM aiming to integrate cutting-edge technology into your vehicles, metal AM offers a compelling route forward. We encourage you to explore how this technology can revolutionize your approach to EV component design and manufacturing.
Ready to accelerate your EV innovation? Contact Met3dp today to discuss your project requirements and discover how our advanced metal additive manufacturing solutions can help you achieve your goals.
Paylaş
MET3DP Technology Co, LTD, merkezi Qingdao, Çin'de bulunan lider bir katmanlı üretim çözümleri sağlayıcısıdır. Şirketimiz, endüstriyel uygulamalar için 3D baskı ekipmanları ve yüksek performanslı metal tozları konusunda uzmanlaşmıştır.
İşletmeniz için en iyi fiyatı ve özelleştirilmiş Çözümü almak için sorgulayın!
İlgili Makaleler
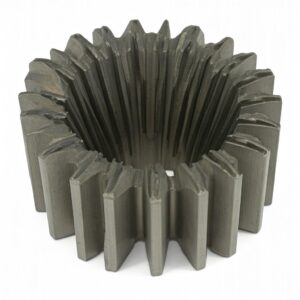
Yüksek Performanslı Nozul Kanat Segmentleri: Metal 3D Baskı ile Türbin Verimliliğinde Devrim
Daha Fazla Oku "Met3DP Hakkında
Son Güncelleme
Bizim Ürünümüz
BİZE ULAŞIN
Herhangi bir sorunuz var mı? Bize şimdi mesaj gönderin! Mesajınızı aldıktan sonra tüm ekibimizle talebinize hizmet edeceğiz.
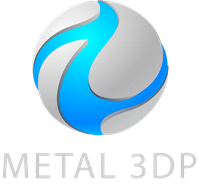
3D Baskı ve Katmanlı Üretim için Metal Tozları