Precision Sensor Mounts for Aerospace Applications
İçindekiler
Introduction: Custom Aerospace Sensor Mounts – Precision in Extreme Environments
In the demanding realm of aerospace, every component counts. From satellites orbiting the Earth to high-performance aircraft navigating the skies, the need for precision, reliability, and resilience under extreme conditions is paramount. Among the critical, yet often overlooked, components are sensor mounts. These structures, seemingly simple, play a vital role: they securely hold and accurately position sensitive instrumentation – the eyes and ears of any advanced aerospace system. Custom aerospace sensor mounts, engineered specifically for their unique application and environment, ensure that critical data acquisition systems function flawlessly, providing essential feedback for navigation, control, diagnostics, and mission success.
Traditionally, manufacturing these mounts involved subtractive methods like CNC machining, often leading to significant material waste, design limitations, and lengthy production cycles, especially for complex or low-volume custom parts. However, the advent of metal katkılı üretim (AM), or metal 3D baskı, is revolutionizing how these crucial components are designed and produced. This technology enables the creation of highly optimized, lightweight, and intricate sensor mounts directly from digital models, layer by layer, using specialized metal powders. For engineers and procurement managers in the aerospace sector seeking enhanced performance, reduced lead times, and greater design freedom, understanding the potential of metal AM for custom sensor mounts is essential.
The aerospace industry operates at the cutting edge, constantly pushing the boundaries of performance and efficiency. Sensor mounts must withstand:
- Aşırı Sıcaklıklar: From the cryogenic cold of deep space to the searing heat of engine components or atmospheric re-entry.
- Intense Vibrations: During launch, flight maneuvers, and normal operation, mounts must dampen or resist vibrations that could impair sensor accuracy or damage the device.
- High G-Forces: Acceleration and deceleration forces require mounts with exceptional structural integrity.
- Aşındırıcı Ortamlar: Exposure to fuels, hydraulic fluids, de-icing agents, or space radiation necessitates materials with high resistance.
- Strict Weight Constraints: Every gram saved contributes to fuel efficiency, payload capacity, or overall performance.
Metal 3D printing offers a powerful solution to meet these stringent requirements. By enabling designs previously impossible to manufacture, such as topology-optimized structures and integrated cooling channels, AM allows engineers to create sensor mounts that are not only lighter and stronger but also tailored precisely to the sensor’s functional needs and the platform’s operational environment. This capability is particularly valuable for custom aerospace components, where unique geometries and performance characteristics are often required. As a leader in metal 3D baskı solutions, Met3dp provides the advanced equipment and high-performance metal powders necessary to realize the full potential of additive manufacturing for critical applications like aerospace sensor mounts. Our expertise ensures that components meet the rigorous standards of the aerospace industry, delivering unparalleled precision and reliability.
Applications: Where Are Custom Aerospace Sensor Mounts Used?
Custom aerospace sensor mounts are indispensable across a vast spectrum of aerospace and defense applications. Their primary function is to provide a stable, precisely aligned platform for sensors, protecting them from environmental hazards while ensuring optimal data capture. The ability to customize these mounts using metal additive manufacturing allows for seamless integration into complex systems and optimization for specific operational demands.
Here’s a breakdown of key application areas:
1. Commercial Aviation: * Engine Monitoring: Mounts for vibration sensors, temperature probes (thermocouples, RTDs), and pressure transducers within or near engines. These require high-temperature resistant materials and robust designs to withstand intense vibrations. AM enables complex internal cooling channels or heat sinks integrated directly into the mount structure. * Airframe Sensing: Brackets for strain gauges, accelerometers, and temperature sensors on wings, fuselage, and landing gear to monitor structural health and aerodynamic loads. Lightweighting via AM is crucial here. * Cabin Environment: Mounts for air quality sensors, temperature sensors, and humidity sensors, often requiring integration into tight spaces within cabin panels or ductwork. AM allows for form-fitting designs. * Avionics Bays: Secure mounting for sensitive electronic sensors (gyroscopes, accelerometers for inertial navigation systems) requiring vibration damping and precise alignment. Custom AM mounts can incorporate specific damping features or complex geometries for optimal positioning.
2. Space Systems (Satellites, Launch Vehicles): * Satellite Payloads: Mounts for optical sensors, cameras, antennas, star trackers, and scientific instruments. These demand extreme dimensional stability across wide temperature fluctuations (thermal stability), low outgassing materials, and minimal weight. AM enables intricate, highly optimized structures that would be impossible to machine. * Launch Vehicles: Brackets for sensors monitoring propulsion systems (pressure, temperature, flow rate), structural loads during ascent, and guidance systems. These mounts must endure extreme G-forces, vibration, and acoustic loads. Material strength and robust design are key. * Space Stations & Habitats: Internal and external mounts for environmental monitoring sensors, radiation detectors, and equipment monitoring. Reliability and long operational life are critical.
3. Military Aircraft & Defense: * Fighter Jets & Bombers: Mounts for targeting pods, radar components, electronic warfare sensors, and air data sensors. These require high strength-to-weight ratios, aerodynamic profiles, and resistance to extreme flight dynamics and temperatures. AM allows for conformal mounting solutions and rapid prototyping of new sensor integrations. * Unmanned Aerial Vehicles (UAVs / Drones): Lightweight and compact mounts for cameras, LiDAR, environmental sensors, and communication systems. Weight reduction is often the primary driver, making topology-optimized AM mounts highly advantageous. Integration into complex airframes is simplified with custom AM designs. * Missiles & Munitions: Rugged mounts for guidance sensors (IR, radar seekers), proximity fuses, and telemetry sensors. Survivability under extreme acceleration and shock is essential.
4. Helicopters: * Rotor Systems: Mounts for blade tracking sensors, vibration sensors, and strain gauges. These must withstand significant cyclical loading and vibration. * Transmission & Engine: Brackets for temperature, pressure, and chip detector sensors, operating in high-temperature, high-vibration environments. * Airframe & Avionics: Similar sensing requirements to fixed-wing aircraft, often with unique spatial constraints requiring custom AM solutions.
Table: Sensor Mount Applications & Key AM Benefits
Uygulama Alanı | Typical Sensors | Key Environmental Challenges | Primary AM Benefits | Potential Materials (Examples) |
---|---|---|---|---|
Commercial Engine | Vibration, Temp (Thermocouples), Pressure | High Temp, High Vibration, Corrosion | Complex Geometries, Integrated Cooling, Consolidation | Inconel 718/625, Ti6Al4V |
Airframe (Fixed Wing) | Strain Gauges, Accelerometers, Temp | Vibration, Fatigue, Temp Cycling, Weight | Lightweighting (Topology Optimization), Consolidation | AlSi10Mg, Ti6Al4V, 316L |
Satellite Payload | Optical Sensors, Star Trackers, RF Antennas | Extreme Temp Cycling, Vacuum (Outgassing), Weight | Lightweighting, High Stiffness, Thermal Stability | AlSi10Mg, Ti6Al4V, Scalmalloy |
Launch Vehicle | Pressure, Temp, Strain, Guidance Sensors | Extreme G-Forces, Vibration, Acoustics | High Strength-to-Weight, Complex Geometries | Ti6Al4V, High-Strength Steels |
UAV/Drone | Cameras, LiDAR, Environmental, Comms | Weight, Size Constraints, Vibration | Extreme Lightweighting, Compact Integration | AlSi10Mg, Ti6Al4V, Polymers (non-metal) |
Military Aircraft | Targeting Pods, Radar, EW Sensors, Air Data | High G-Forces, Aerodynamic Loads, High Temp | Conformal Shapes, Rapid Prototyping, Strength | Ti6Al4V, AlSi10Mg, High-Strength Steels |
Helicopter Rotor | Blade Trackers, Vibration, Strain | High Cycle Fatigue, High Vibration | Durability, Complex Shapes for Fit | Ti6Al4V, Steel Alloys |
Sayfalara Aktar
The versatility of metal 3D printing allows aerospace engineers and procurement managers to source custom aerospace sensor mounts specifically designed for each unique application, moving beyond standardized off-the-shelf solutions towards optimized, high-performance components. Companies like Met3dp, with extensive experience in aerospace materials and eklemeli üretim süreçleri, are crucial partners in developing and producing these mission-critical parts.
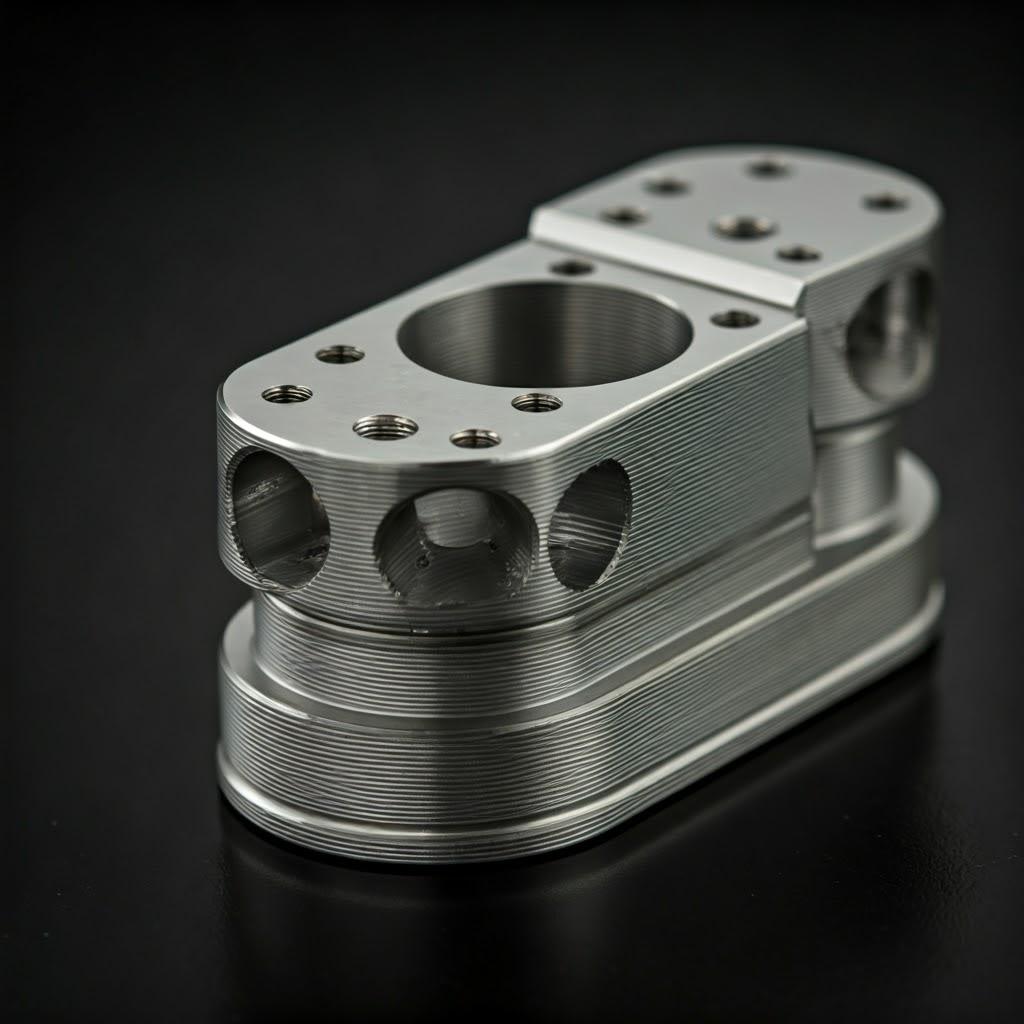
The Additive Advantage: Why Metal 3D Printing for Aerospace Sensor Mounts?
While traditional manufacturing methods like CNC machining have served the aerospace industry well, metal additive manufacturing offers compelling advantages, particularly for components like custom sensor mounts where complexity, weight, and performance are critical design drivers. Opting for metal 3D printing is not just about adopting a new technology; it’s about unlocking new possibilities in design, efficiency, and capability.
Here’s why metal AM is increasingly becoming the preferred method for producing high-performance aerospace sensor mounts:
1. Unprecedented Design Freedom & Complexity: * Topology Optimization: Algorithms can determine the most efficient material distribution to meet load requirements, resulting in organic, lightweight structures impossible to machine. This leads to significant weight savings without compromising stiffness or strength – crucial for aerospace. * Kafes Yapılar: Internal lattice or gyroid structures can be integrated into the mount design to further reduce weight, absorb energy/vibration, or facilitate heat dissipation. * Conformal Designs: Mounts can be designed to perfectly follow the curved or complex surfaces of airframes or engine casings, improving aerodynamics and simplifying assembly. * Internal Channels: Complex internal channels for cooling fluids, wiring passthroughs, or thermal management can be printed directly into the mount, eliminating the need for secondary drilling or assembly steps.
2. Lightweighting: * As mentioned, topology optimization and lattice structures enabled by AM allow for drastic reductions in component weight compared to parts machined from solid blocks. * Every kilogram saved on an aircraft or spacecraft translates to significant fuel savings, increased payload capacity, or improved maneuverability over the platform’s lifetime. Sensor mounts, while individually small, contribute collectively to overall platform weight, making AM an attractive option for weight-sensitive applications.
3. Part Consolidation: * Complex assemblies that previously consisted of multiple machined parts, fasteners, and brackets can often be redesigned and printed as a single, monolithic component. * This reduces part count, eliminates potential failure points at joints/fasteners, simplifies the supply chain (fewer parts to procure and track), speeds up assembly time, and lowers overall system weight. A sensor mount might integrate features like cable guides, vibration dampers, or thermal standoffs into one printed piece.
4. Rapid Prototyping and Iteration: * AM allows engineers to move quickly from a digital design (CAD model) to a physical metal prototype. * Design iterations for sensor placement, fit, or performance optimization can be tested much faster and more cost-effectively than with traditional tooling-based manufacturing. This accelerates the development cycle for new aircraft, satellites, or sensor systems.
5. Material Efficiency & Reduced Waste: * Additive manufacturing builds parts layer by layer, using only the material needed for the component and its support structures. This contrasts sharply with subtractive manufacturing (like CNC machining) which starts with a solid block of material and removes large amounts, generating significant scrap (buy-to-fly ratio). * While some powder is used for supports and some unfused powder needs recycling, the overall material utilization is often much higher in AM, especially for complex parts. This is particularly beneficial when using expensive aerospace-grade alloys.
6. Customization & On-Demand Manufacturing: * AM is ideal for producing highly customized, low-volume parts like specialized sensor mounts without the need for expensive tooling or molds. * This supports “just-in-time” manufacturing and makes it economically viable to produce bespoke designs tailored to specific sensor models, mounting locations, or operational requirements. It facilitates repairs or upgrades by enabling the production of obsolete or uniquely modified parts.
7. Enhanced Functional Performance: * The design freedom allows for optimizing not just weight and strength, but also functional aspects like vibration damping (through tailored geometries or lattice structures) and thermal management (via integrated cooling channels or optimized heat paths). This ensures the sensor performs optimally and survives harsh operating conditions.
Table: Metal AM vs. CNC Machining for Aerospace Sensor Mounts
Özellik | Metal Katmanlı Üretim (AM) | Geleneksel CNC İşleme | Advantage for Sensor Mounts |
---|---|---|---|
Tasarım Karmaşıklığı | High (Complex geometries, internal features easily made) | Limited (Restricted by tool access, setup complexity) | AM allows highly optimized, lightweight, multi-functional designs |
Hafifletme | Excellent (Topology optimization, lattices possible) | Moderate (Material removal, pocketing) | AM enables significant weight reduction |
Parça Konsolidasyonu | High (Multiple parts printable as one) | Low (Assemblies typically required) | AM reduces part count, assembly time, failure points |
Malzeme Atıkları | Low (Additive process, powder recycling) | High (Subtractive process, significant scrap) | AM is more sustainable, cost-effective for expensive materials |
Lead Time (Prototype) | Fast (Direct from CAD, no tooling) | Moderate-to-Slow (Requires setup, programming) | AM accelerates design iteration and testing |
Lead Time (Production) | Can be slower for high volumes, process dependent | Potentially faster for high volumes | AM excels at low-to-mid volume custom parts |
Kalıp Maliyetleri | None (Tool-less manufacturing) | High (Fixtures, specialized tools may be needed) | AM is cost-effective for custom/low-volume production |
Özelleştirme | High (Easy to modify designs per part) | Moderate (Requires reprogramming/setup changes) | AM is ideal for bespoke sensor mount solutions |
Sayfalara Aktar
Partnering with an experienced metal additive manufacturing service provider like Met3dp ensures that these advantages are fully realized. Met3dp utilizes state-of-the-art printing technologies, including advanced Powder Bed Fusion systems like Selective Electron Beam Melting (SEBM), coupled with high-quality, internally produced metal powders, to deliver aerospace components that meet the highest standards of performance and reliability. Our expertise in additive manufacturing printing methods allows us to select the optimal process for your specific sensor mount requirements.
Material Matters: Choosing 316L and AlSi10Mg for Sensor Mounts
Selecting the right material is fundamental to the success of any aerospace component, including sensor mounts. The material must not only withstand the operational environment but also be compatible with the chosen manufacturing process – in this case, metal additive manufacturing. For many aerospace sensor mount applications, two materials stand out due to their balance of properties, printability, and cost-effectiveness: 316L Paslanmaz Çelik ve AlSi10Mg Alüminyum Alaşım.
316L Stainless Steel (Austenitic Stainless Steel):
316L is a widely used austenitic chromium-nickel stainless steel alloy containing molybdenum, which enhances its corrosion resistance, particularly against chlorides and other industrial solvents. Its low carbon content (“L” signifies low carbon, typically < 0.03%) minimizes carbide precipitation during welding or heat treatment, preserving its corrosion resistance.
- Key Properties & Advantages for Aerospace Sensor Mounts:
- Mükemmel Korozyon Direnci: Crucial for mounts exposed to atmospheric moisture, de-icing fluids, fuel vapors, or marine environments (e.g., naval aircraft, coastal launch sites).
- Good Strength and Ductility: Offers a solid combination of mechanical strength and toughness, suitable for handling moderate structural loads and vibrations. It maintains good properties at both moderately elevated and cryogenic temperatures.
- Weldability & Formability: While less relevant for AM, its inherent good fabrication characteristics translate well to post-processing steps if needed.
- Biocompatibility (in some forms): Relevant if sensors are part of life support systems, though specific certifications are needed.
- İyi Basılabilirlik: 316L is well-characterized and reliably processed using common Powder Bed Fusion techniques (Laser and Electron Beam).
- Maliyet-Etkinlik: Generally more affordable than titanium alloys or nickel superalloys, making it a practical choice for less demanding applications.
- Düşünceler:
- Yoğunluk: Relatively dense compared to aluminum or titanium alloys (approx. 8 g/cm³), making it less ideal for applications where weight saving is the absolute top priority.
- Lower Strength-to-Weight Ratio: Compared to Ti6Al4V or high-strength aluminum alloys.
- Termal İletkenlik: Moderate thermal conductivity, which might be a factor if the mount needs to act as a heat sink or insulator.
- Typical Aerospace Applications for 316L Mounts: Brackets in non-critical structural areas, mounts for sensors in corrosive environments (e.g., fuel systems, environmental monitoring), ground support equipment interfaces, applications where moderate strength and high corrosion resistance are prioritized over minimal weight.
AlSi10Mg Aluminum Alloy (Casting Aluminum Alloy):
AlSi10Mg is a hypoeutectic aluminum-silicon alloy containing magnesium. It’s traditionally a casting alloy known for its good castability, but it has become one of the most popular alloys for metal AM due to its excellent printability and favorable properties after heat treatment.
- Key Properties & Advantages for Aerospace Sensor Mounts:
- Low Density / High Strength-to-Weight Ratio: This is the primary advantage. Aluminum alloys are significantly lighter than steels or titanium (approx. 2.68 g/cm³), making AlSi10Mg ideal for weight-critical aerospace applications like UAVs, satellites, and aircraft components.
- Good Mechanical Properties (after heat treatment): While weaker than steels or titanium alloys in absolute terms, heat-treated AlSi10Mg offers excellent specific strength (strength divided by density). T6 heat treatment significantly improves its tensile strength and hardness.
- Mükemmel Basılabilirlik: Processes very well with Laser Powder Bed Fusion (LPBF/SLM), allowing for fine details and complex geometries.
- Good Thermal Conductivity: Aluminum alloys conduct heat well, which can be advantageous if the sensor mount needs to help dissipate heat generated by the sensor or surrounding electronics.
- Korozyon Direnci: Offers good resistance to atmospheric corrosion.
- Düşünceler:
- Alt Sıcaklık Sınırı: Aluminum alloys lose strength significantly at elevated temperatures (typically above 150-200°C), making them unsuitable for mounts near engines or other high-temperature zones.
- Lower Absolute Strength & Fatigue Life: Compared to titanium or steel alloys, AlSi10Mg has lower fatigue strength and fracture toughness, which needs careful consideration in high-cycle or high-load applications. Design optimization (e.g., stress reduction features) is crucial.
- İşlem Sonrası Gereksinimler: Typically requires stress relief and a T6 heat treatment (solutionizing and artificial aging) to achieve optimal mechanical properties. Machining may be needed for critical tolerance features.
- Typical Aerospace Applications for AlSi10Mg Mounts: Lightweight brackets and mounts for airframes, satellite structures, UAV payloads, avionics enclosures, non-critical structural components where weight saving is paramount and operating temperatures are moderate.
Table: Comparison of 316L and AlSi10Mg for AM Sensor Mounts
Mülkiyet | 316L Paslanmaz Çelik | AlSi10Mg Alüminyum Alaşım | Key Implication for Sensor Mounts |
---|---|---|---|
Yoğunluk | High (~8.0 g/cm³) | Low (~2.68 g/cm³) | AlSi10Mg preferred for weight-critical applications (UAVs, space). |
Güçten Ağırlığa | Orta düzeyde | High (especially after T6 treatment) | AlSi10Mg offers better specific strength. |
Korozyon Direnci | Mükemmel | Good (atmospheric) | 316L better for harsh chemical/marine environments. |
Max Service Temp. | Moderate (~400-600°C, varies) | Low (~150-200°C) | 316L suitable for warmer locations; AlSi10Mg limited to cooler areas. |
Termal İletkenlik | Low-Moderate | Yüksek | AlSi10Mg better if mount needs to act as a heat sink. |
Stiffness (Modulus) | High (~193 GPa) | Moderate (~71 GPa) | 316L provides higher rigidity for the same geometry. |
Printability (LPBF) | İyi | Mükemmel | Both process well, AlSi10Mg often allows finer features. |
İşlem Sonrası | Stress relief common; Machining possible | Stress relief & T6 heat treat typical | AlSi10Mg requires heat treatment for optimal properties. |
Cost (Powder) | Orta düzeyde | Moderate-Low | Material cost is a factor, but overall part cost depends on design. |
Sayfalara Aktar
Met3dp’s Role in Material Excellence:
Choosing the right material is only part of the equation. The quality of the metal powder used in the AM process significantly impacts the final part’s properties, including density, microstructure, and mechanical performance. Met3dp addresses this critical aspect directly. As a company specializing in both additive manufacturing equipment ve production of high-performance metal powders, we ensure optimal material integrity from start to finish.
Met3dp employs industry-leading powder production technologies, including Vacuum Induction Melting Gas Atomization (VIGA) ve Plazma Dönen Elektrot Prosesi (PREP). These advanced methods allow us to produce metal powders, including grades like 316L and potentially aluminum alloys (check specific portfolio), with:
- Yüksek Küresellik: Ensures excellent powder flowability and uniform spreading during the printing process, leading to denser, more consistent parts.
- Low Satellite Content: Minimizes irregularities that can affect packing density and melt pool stability.
- Controlled Particle Size Distribution (PSD): Optimized PSD tailored for specific AM processes (like LPBF or SEBM) ensures predictable melting behavior and good surface finish.
- Yüksek Saflıkta: Minimizing oxygen and other contaminants is crucial for achieving desired mechanical properties and corrosion resistance in the final part.
By controlling powder production internally, Met3dp offers customers greater confidence in the material quality and traceability, which is essential for demanding sectors like aerospace. Whether you require 316L for its robustness and corrosion resistance or AlSi10Mg for its lightweight advantages, Met3dp provides not only the printing services but also the high-quality, aerospace-suitable powders necessary for success. Explore our range of metal powders and printing solutions to find the best fit for your custom aerospace sensor mount needs.
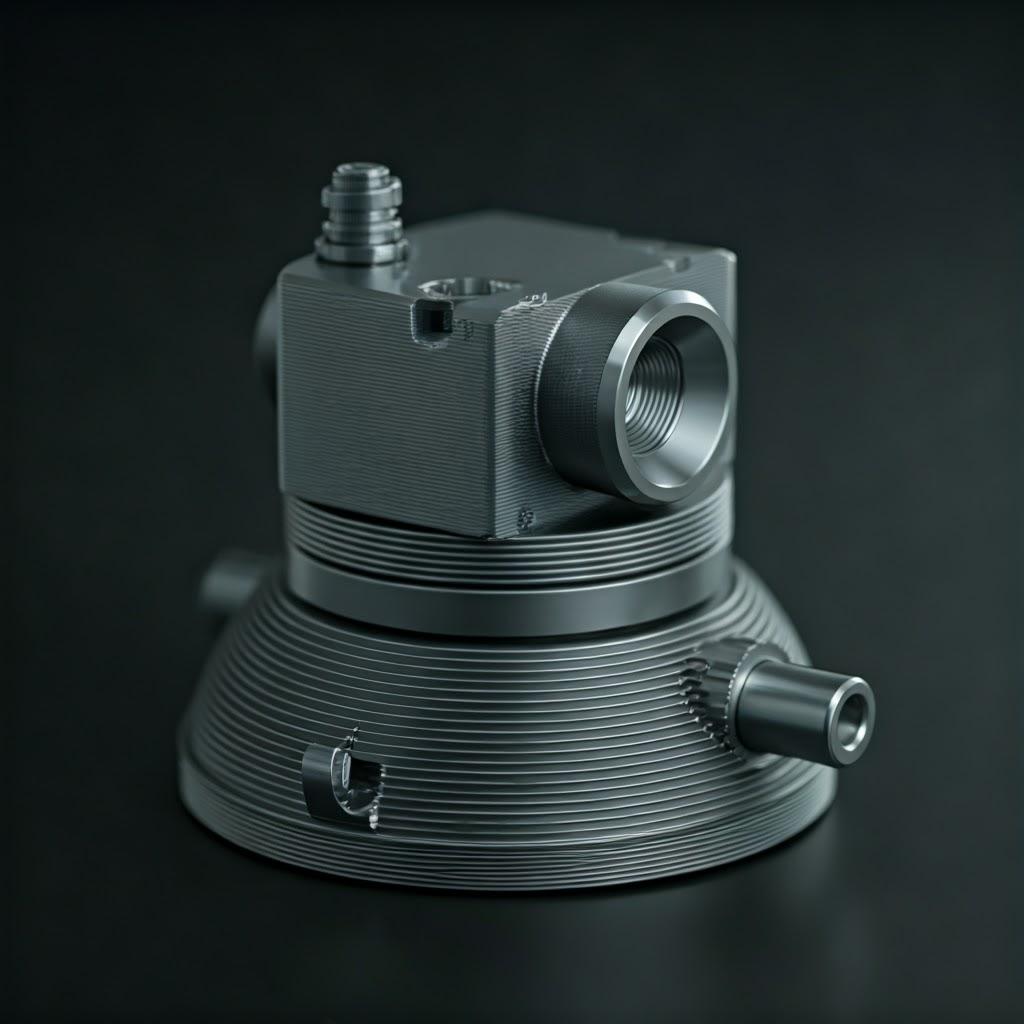
Design for AM: Optimizing Sensor Mount Geometry for 3D Printing
Transitioning from traditional manufacturing to metal additive manufacturing (AM) requires more than simply sending an existing CAD file to the printer. To truly leverage the power of AM and produce high-performance, reliable aerospace sensor mounts, engineers must embrace Katmanlı Üretim Tasarımı (DfAM) principles. DfAM involves rethinking component design to align with the capabilities and constraints of the layer-by-layer building process, unlocking benefits like weight reduction, improved functionality, and enhanced manufacturability. Optimizing sensor mount geometry specifically for AM is crucial for achieving aerospace performance targets.
Key DfAM considerations for aerospace sensor mounts include:
1. Part Orientation: * Etki: The orientation of the part on the build plate significantly affects support structure requirements, build time, surface finish on different faces, and potentially anisotropic mechanical properties (properties varying with direction). * Sensor Mount Specifics: Orienting a mount to minimize supports on critical interfacing surfaces or complex features is vital. Downward-facing surfaces (overhangs) below a certain angle (typically < 45 degrees from horizontal, process dependent) require support structures, which leave witness marks upon removal and can impact surface finish. Flat surfaces often achieve better finish when oriented horizontally, while vertical walls tend to have better dimensional accuracy. For sensor mounts, aligning critical bores or mounting interfaces to be self-supporting or easily post-machined is often preferred. * Strategy: Analyze the geometry to balance minimizing support volume (reduces material cost, build time, post-processing effort) with achieving desired surface finish and dimensional accuracy on key features. Simulation tools can help predict the impact of different orientations.
2. Support Structures: * Gereklilik: Supports are often required in metal Powder Bed Fusion (PBF) processes (like LPBF and SEBM) to anchor the part to the build plate, counteract warping due to thermal stresses, and support overhanging features during the build. * Design Implications: Supports consume material, add build time, and require removal in post-processing, which can be labor-intensive and potentially damage the part if not done carefully. * DfAM Strategies for Supports: * Çıkıntıları En Aza İndirin: Design features with self-supporting angles (typically > 45 degrees). Use chamfers instead of fillets on downward-facing edges where possible. * Optimize Support Design: Use easily removable support types (e.g., conical, perforated, tree-like supports where applicable by the AM provider). Integrate support structures that are accessible for removal tools. Consider sacrificial features designed to be machined away later, which might incorporate the necessary support. * Internal Channels: Design internal channels with diamond, teardrop, or circular cross-sections that are self-supporting, avoiding the need for internal supports that are difficult or impossible to remove.
3. Wall Thickness and Feature Size: * Process Limits: AM processes have minimum printable wall thicknesses and feature sizes (e.g., pins, holes). Attempting to print features below these limits can lead to defects or build failures. * Sensor Mount Considerations: Ensure walls are thick enough for structural integrity but avoid overly thick sections which can increase residual stress, build time, and material consumption. Thin, tall walls may be prone to distortion. For sensor mounts needing high stiffness, consider topology-optimized designs rather than just thickening walls uniformly. * Guidelines: Typical minimum wall thicknesses for metal PBF might range from 0.3 mm to 1.0 mm, depending on the material, machine, and feature aspect ratio. Consult with your AM provider, like Met3dp, for specific guidelines related to their equipment (e.g., SEBM capabilities) and materials.
4. Topology Optimization: * Concept: Using software algorithms to optimize the material layout within a defined design space, based on applied loads, constraints, and performance objectives (e.g., minimize weight, maximize stiffness). * Aerospace Benefit: This is a cornerstone of lightweighting in aerospace. It results in organic, load-path-driven structures that remove material from low-stress areas, often achieving weight savings of 30-70% or more compared to traditional designs, while meeting or exceeding performance requirements. * Sensor Mount Application: Ideal for complex brackets that must withstand specific vibration frequencies or static loads while adding minimal weight to the overall assembly. The resulting geometry is often only manufacturable via AM.
5. Lattice Structures: * Concept: Incorporating internal periodic structures (like cubic, octet-truss, or gyroid lattices) within the solid volume of a part. * Avantajlar: * Further Lightweighting: Reduces mass while maintaining reasonable structural integrity. * Vibration Damping/Energy Absorption: The lattice can be designed to absorb specific frequencies or impact energy, potentially beneficial for protecting sensitive sensors. * Termal Yönetim: Increased surface area can aid heat dissipation if needed. * Sensor Mount Application: Integrating lattices into less critical sections of a mount can save weight. Designing specific lattice types can help tune the mount’s natural frequency to avoid resonance with the surrounding structure or equipment.
6. Part Consolidation: * Strategy: Redesigning assemblies previously made of multiple parts (e.g., a bracket, clamp, fasteners) into a single, monolithic AM component. * Sensor Mount Example: A sensor mount assembly might include the main bracket, a retaining clip, and perhaps integrated vibration isolation features. DfAM allows combining these into one printable part. * Avantajlar: Reduces part count, eliminates fasteners (potential failure points), simplifies inventory and assembly, often reduces overall weight and cost.
7. Hole Orientation and Design: * Meydan okumak: Small horizontal holes or holes printed directly on the build plate can be challenging to produce accurately without supports or distortion. Very small vertical holes may trap powder. * DfAM Solutions: Orient parts so critical holes are vertical or self-supporting (teardrop shape). Design holes slightly undersized if they require high precision, allowing for finish machining or reaming in post-processing. Add features to allow powder removal from internal cavities or blind holes.
Table: DfAM Principles for Aerospace Sensor Mounts
DfAM Principle | Amaç | Key Strategy for Sensor Mounts | Fayda |
---|---|---|---|
Part Orientation | Minimize supports, optimize finish/accuracy | Orient critical surfaces up/vertically, consider anisotropic properties | Reduced post-processing, better surface quality, faster build |
Destek Yapıları | Minimize need, ensure removability | Design self-supporting angles (>45°), use optimized/accessible supports | Lower cost, less labor, reduced risk of part damage |
Duvar Kalınlığı | Ensure printability & structural integrity | Adhere to min. thickness rules, avoid excessively thick sections | Prevent build failures, manage stress, optimize material use |
Topology Optimization | Minimize weight, maximize stiffness | Apply FEA-driven optimization based on load cases | Significant weight reduction, improved performance |
Kafes Yapılar | Lightweighting, vibration damping, thermal | Integrate lattices in low-stress areas or for specific functions | Enhanced functionality, further weight savings |
Parça Konsolidasyonu | Reduce part count, simplify assembly | Redesign multi-part assemblies as single AM components | Lower assembly cost, improved reliability, simpler logistics |
Hole Design | Ensure accuracy, powder removal | Orient vertically, use self-supporting shapes, consider post-machining | Achievable tolerances, functional internal features |
Sayfalara Aktar
Applying these DfAM principles requires a collaborative approach between design engineers and AM specialists. Engaging with an experienced aerospace component supplier familiar with the nuances of metal 3D printing, such as Met3dp, early in the design process can save significant time and cost, ensuring the final sensor mount is optimized for both performance and manufacturability.
Achieving Precision: Tolerances, Surface Finish, and Accuracy in AM Sensor Mounts
Aerospace applications demand high levels of precision. Sensor mounts, in particular, often require tight tolerances for proper alignment with mating parts and accurate positioning of the sensor itself. Dimensional accuracy and surface finish are critical parameters influenced by the AM process, material choice, and post-processing steps. Understanding what metal 3D printing can achieve is crucial for engineers and procurement managers.
Dimensional Accuracy and Tolerances:
- Tanım: Dimensional accuracy refers to how closely the final printed part conforms to the dimensions specified in the CAD model. Tolerance defines the permissible range of variation for a given dimension.
- Achievable Levels: Metal Powder Bed Fusion (PBF) processes, including Laser PBF (LPBF/SLM) and Electron Beam PBF (SEBM), typically achieve dimensional accuracies in the range of ±0.1 mm to ±0.5 mm or ±0.1% to ±0.2% of the nominal dimension, whichever is larger. However, this is a general guideline and depends heavily on:
- Part Size and Geometry: Larger parts and complex geometries tend to accumulate more thermal stress, potentially leading to greater deviation.
- Malzeme: Different materials exhibit varying shrinkage and stress characteristics during melting and solidification (e.g., aluminum alloys have higher thermal expansion than steels).
- Makine Kalibrasyonu ve Durumu: Regular calibration and maintenance of the AM system are vital for consistent accuracy.
- Build Parameters: Layer thickness, scan strategy, and energy input influence the melt pool dynamics and resulting precision.
- Termal Yönetim: The effectiveness of heating/cooling strategies within the build chamber impacts stress and distortion. SEBM, operating at higher build chamber temperatures, often results in lower residual stress compared to LPBF, potentially aiding accuracy for certain geometries and materials.
- Meeting Tight Tolerances: For features requiring tolerances tighter than the standard AM process capability (e.g., critical mounting interfaces, precise bore diameters), post-process machining (CNC milling, turning, grinding) is typically employed. It’s common DfAM practice to design parts with extra material (machining stock) on critical surfaces specifically for finishing operations.
Yüzey İşlemi (Pürüzlülük):
- Tanım: Surface finish describes the texture of a surface, often quantified by the average roughness parameter, Ra (measured in micrometers, $\mu$m). Lower Ra values indicate smoother surfaces.
- As-Built Surface Finish: The surface finish of metal AM parts directly off the printer depends on several factors:
- Oryantasyon: Upward-facing surfaces and vertical walls generally have better finishes than downward-facing surfaces that required support structures. Side-facing or “stair-stepped” surfaces on shallow angles can exhibit higher roughness.
- Katman Kalınlığı: Thinner layers generally produce smoother surfaces but increase build time.
- Powder Particle Size: Finer powders can lead to smoother finishes but may pose challenges in flowability or handling.
- İşlem Türü: LPBF often produces smoother as-built surfaces (typically Ra 6-15 $\mu$m) compared to SEBM (typically Ra 20-40 $\mu$m), primarily due to larger layer thicknesses and powder sizes often used in SEBM.
- Yüzey İşleminin İyileştirilmesi: If the as-built roughness is insufficient for the application (e.g., for sealing surfaces, fatigue-critical areas, or aesthetic requirements), various post-processing techniques can be used:
- Abrasive Blasting (Bead Blasting, Sand Blasting): Provides a uniform matte finish, removes loose powder, and can slightly improve fatigue life (Ra 5-10 $\mu$m often achievable).
- Tumbling/Vibratory Finishing: Uses media to smooth surfaces and edges, particularly effective for batches of smaller parts (Ra 1-5 $\mu$m possible).
- Micro-Machining/Polishing: Can achieve very smooth, mirror-like finishes (Ra<0.8 $\mu$m or even lower) but is typically localized to specific areas due to cost and effort.
- Elektro parlatma: An electrochemical process that removes material, smoothing peaks and potentially improving corrosion resistance.
Table: Typical Precision Parameters for Metal AM Sensor Mounts
Parametre | Process Influence | Typical As-Built Range (PBF) | Post-Processing Impact | Sensor Mount Relevance |
---|---|---|---|---|
Boyutsal Tolerans | Machine, Material, Geometry, Thermal Stress | ±0.1−0.5 mm or ±0.1−0.2% | Machining achieves tighter tolerances | Critical for mounting interfaces, sensor alignment |
Surface Roughness (Ra) | Orientation, Layer Thickness, Powder Size, Process | LPBF: 6-15 $\mu$m; SEBM: 20-40 $\mu$m | Blasting, Tumbling, Polishing improve | Affects fit, fatigue life, sealing, aesthetics |
Özellik Çözünürlüğü | Laser/Beam Spot Size, Layer Thickness, Powder Size | ~0.1 – 0.5 mm min feature size | Machining for very fine details | Limits minimum wall thickness, hole size, intricate details |
Sayfalara Aktar
Met3dp’s Commitment to Precision:
Achieving consistent accuracy and desired surface finish requires not only optimized design but also robust process control and high-quality equipment. Met3dp understands the critical nature of precision in aerospace. Our company prides itself on providing industry-leading additive manufacturing solutions. As detailed further when you learn Hakkımızda, Met3dp focuses on:
- Advanced AM Systems: Utilizing printers, including our specialized SEBM systems, designed for accuracy and reliability, crucial for mission-critical aerospace parts.
- Yüksek Kaliteli Metal Tozları: Our internally produced powders, manufactured using VIGA and PREP technologies, ensure consistent particle size distribution and morphology, contributing to predictable melting behavior and better surface quality.
- Süreç Uzmanlığı: Decades of collective expertise in metal AM allow us to optimize build parameters and strategies for specific materials (like 316L and AlSi10Mg) and geometries, maximizing achievable precision.
- Kalite Kontrol: Implementing rigorous quality checks throughout the manufacturing process, from powder validation to final part inspection.
By partnering with Met3dp, aerospace engineers and procurement managers gain access to technology and expertise dedicated to meeting the stringent precision requirements of custom sensor mounts and other critical components.
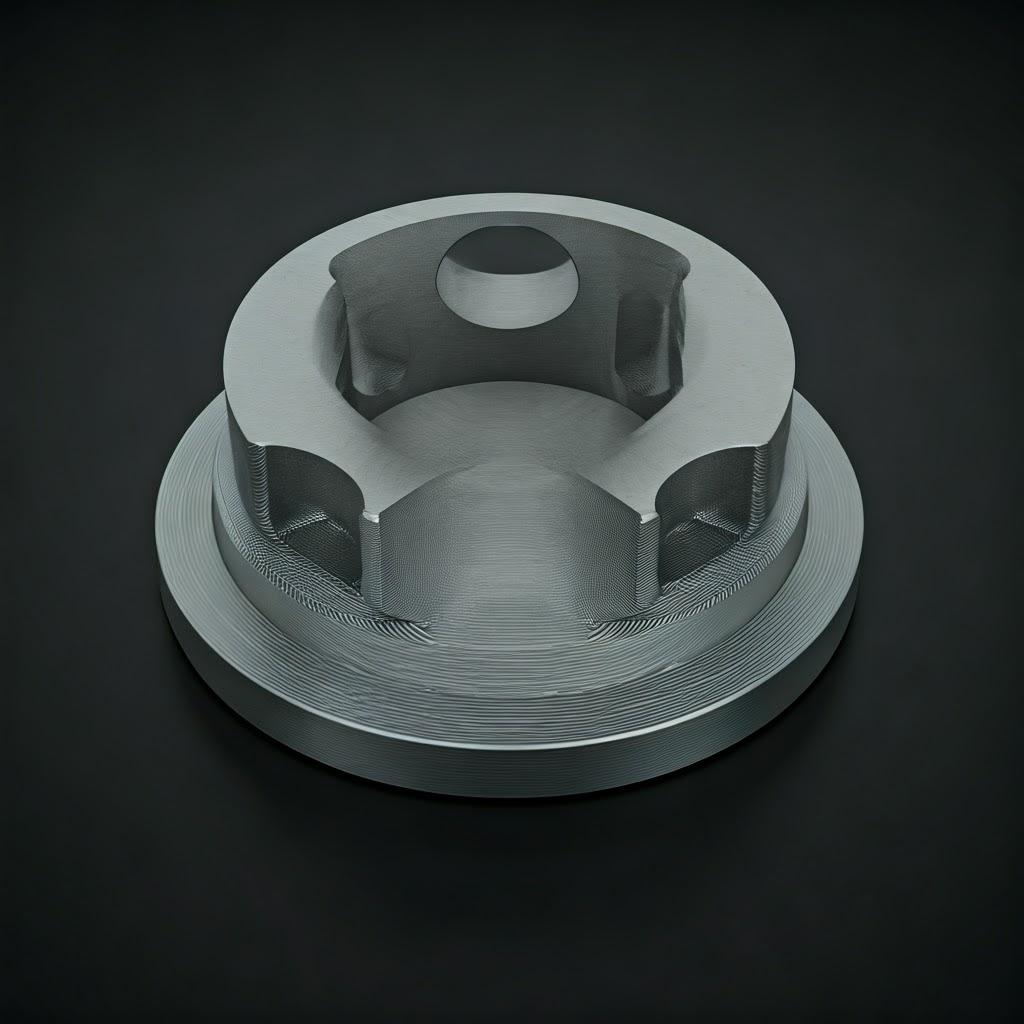
Post-Processing: Refining Metal 3D Printed Sensor Mounts for Aerospace
Parts produced by metal additive manufacturing rarely go directly from the printer into service, especially in demanding sectors like aerospace. Post-processing steps are almost always necessary to achieve the required material properties, dimensional tolerances, surface finish, and overall part integrity. Understanding these steps is crucial for accurately estimating costs, lead times, and ensuring the final sensor mount meets all specifications.
Common post-processing stages for metal AM aerospace sensor mounts include:
1. Stress Relief: * Amacımız: The rapid heating and cooling cycles inherent in PBF processes create internal stresses within the printed part. These stresses can cause distortion or warping, especially after the part is removed from the build plate or during subsequent machining. Stress relief involves heating the part (while still attached to the build plate, if possible) to a specific temperature below the material’s critical transformation point and holding it for a set duration, followed by slow cooling. * Importance: This is often the first crucial step to ensure dimensional stability for subsequent operations and in the final application. It’s standard practice for most metal AM parts, particularly those made from alloys like Ti6Al4V, AlSi10Mg, and certain steels.
2. Part Removal from Build Plate: * Method: Typically done using wire EDM (Electrical Discharge Machining), sawing, or grinding, depending on the part geometry, material, and support structure design. * Consideration: Care must be taken to avoid damaging the part. The choice of removal method can influence the required machining stock on the base surface.
3. Support Structure Removal: * Method: This can range from simple manual breakaway (for well-designed supports) to more involved cutting, grinding, or machining. Access can be challenging for complex internal geometries. * Etki: This step is often labor-intensive and can leave witness marks or burrs on the part surface, potentially requiring further finishing. DfAM plays a huge role in simplifying support removal.
4. Heat Treatment (Beyond Stress Relief): * Amacımız: To achieve desired final material properties (e.g., strength, hardness, ductility, fatigue life). The specific treatment depends on the alloy and application requirements. * Examples for Sensor Mount Materials: * AlSi10Mg: Typically requires a full T6 heat treatment (solution heat treatment followed by artificial aging) to significantly increase strength and hardness. Without T6, the as-built properties are much lower. * 316L Paslanmaz Çelik: Often used in the as-built or stress-relieved condition. Solution annealing might be performed to maximize corrosion resistance or ductility if required, but full hardening treatments are not applicable to this austenitic grade. * Other Aerospace Alloys (e.g., Ti6Al4V): May require specific annealing cycles or Hot Isostatic Pressing (HIP) to improve fatigue properties and reduce internal microporosity. * Kontrol: Heat treatments must be performed in calibrated furnaces with controlled atmospheres (e.g., vacuum or inert gas) to prevent oxidation and ensure uniform properties.
5. Hot Isostatic Pressing (HIP): * Amacımız: Primarily used to eliminate internal microporosity (voids) that can sometimes remain after the AM process. HIP subjects the part to high temperature (below melting point) and high isostatic pressure (using an inert gas like Argon) simultaneously. This collapses internal voids, leading to a fully dense part. * Benefit: Significantly improves fatigue life, fracture toughness, and overall mechanical property consistency, often required for critical aerospace components subjected to cyclic loading. * Uygulama: More common for fatigue-critical parts or materials like titanium alloys, but can be considered for high-performance steel or aluminum mounts depending on requirements and cost considerations.
6. Machining (CNC Milling, Turning, Grinding): * Amacımız: To achieve tight dimensional tolerances on critical features (mounting holes, interfacing surfaces, sensor seating areas) that cannot be met by the as-built AM process. Also used to improve surface finish on specific areas. * Consideration: Requires careful fixture design to hold potentially complex AM geometries. Machining AM parts can sometimes differ from machining wrought materials due to microstructure variations. DfAM should account for tool access and leave adequate machining stock (0.5−2.0 mm typically).
7. Surface Finishing: * Amacımız: To achieve the required surface roughness (Ra), improve fatigue resistance, enhance cleanability, or prepare the surface for coating. * Yöntemler: As discussed previously – bead blasting, tumbling, polishing, electropolishing. The choice depends on the desired finish, part geometry, material, and cost.
8. Cleaning and Inspection: * Amacımız: Final cleaning to remove any machining fluids, blasting media, or contaminants. Inspection ensures the part meets all dimensional, surface finish, and potentially NDT (Non-Destructive Testing) requirements (e.g., dye penetrant testing for surface cracks, CT scanning for internal defects). * Importance: Crucial final step before delivery, especially for certified aerospace hardware.
Table: Post-Processing Steps and Their Purpose for AM Sensor Mounts
Post-Processing Step | Primary Purpose | Typical Application for 316L Mounts | Typical Application for AlSi10Mg Mounts | Aerospace Relevance |
---|---|---|---|---|
Stres Giderici | Reduce internal stress, prevent distortion | Recommended | Gerekli | Ensures dimensional stability |
Part & Support Removal | Separate part from plate & supports | Gerekli | Gerekli | Necessary fabrication steps |
Heat Treatment (e.g., T6) | Optimize mechanical properties (strength, hardness) | Optional (e.g., solution anneal) | Essential (T6 for strength) | Critical for meeting performance specifications |
HIP | Eliminate internal porosity, improve fatigue life | Optional (if fatigue is critical) | Optional (if fatigue is critical) | Enhances reliability for critical, high-cycle parts |
Talaşlı İmalat | Achieve tight tolerances, specific finishes | As needed for critical features | As needed for critical features | Ensures proper fit, alignment, and function |
Yüzey İşlemleri | Improve roughness (Ra), fatigue, aesthetics | Blasting/Tumbling common; Polishing optional | Blasting/Tumbling common; Polishing optional | Meets surface requirements, improves fatigue performance |
Cleaning & Inspection | Ensure cleanliness, verify specifications | Gerekli | Gerekli | Final quality assurance, certification compliance |
Sayfalara Aktar
The extent and sequence of post-processing add significantly to the overall cost and lead time of metal AM parts. It’s vital for procurement managers and engineers to clearly define all post-processing requirements in their specifications and discuss these early with their AM supplier. Met3dp works closely with clients to establish the most efficient and effective post-processing route to ensure their custom aerospace sensor mounts meet all functional and quality demands.
Navigating Challenges: Overcoming Hurdles in AM for Sensor Mounts
While metal additive manufacturing offers transformative advantages, it’s not without its challenges, particularly when producing high-stakes components for the aerospace industry. Awareness of potential issues and partnering with an experienced provider who employs robust mitigation strategies are key to successful implementation.
Common challenges in producing metal AM sensor mounts include:
1. Warping and Distortion: * Sebep: Uneven heating and cooling during the layer-by-layer process induce thermal stresses. As these stresses accumulate, they can cause the part to warp or distort, especially thin sections, large flat areas, or parts with significant changes in cross-section. * Hafifletme: * DfAM: Design parts with features that minimize stress concentration; avoid large, unsupported flat areas parallel to the build plate. * Oryantasyon: Choose build orientations that minimize stress build-up in critical areas. * Destek Yapıları: Use well-designed supports to anchor the part securely and manage thermal gradients. * Process Simulation: Thermal simulation software can predict areas prone to high stress and distortion, allowing for design or parameter adjustments before printing. * Süreç Parametreleri: Optimized scan strategies (e.g., island scanning, alternating hatch directions) and potentially pre-heating (inherent in SEBM) can reduce stress. * Stres Giderici: Post-build stress relief heat treatment is crucial.
2. Residual Stress: * Sebep: Similar to warping, residual stresses are locked into the material after cooling. Even if the part doesn’t visibly warp, high residual stress can negatively impact fatigue life, fracture toughness, and dimensional stability, potentially causing issues during machining or service life. * Hafifletme: * Similar to Warping: DfAM, orientation, supports, simulation, optimized parameters (especially thermal management like SEBM’s higher build temperature). * Stress Relief Heat Treatment: Essential for reducing residual stresses to acceptable levels.
3. Porosity: * Sebep: Small internal voids or pores can form due to incomplete melting, gas entrapment (from powder or shielding gas), or keyholing (vapor depression instability) during the melt process. * Etki: Porosity reduces material density, degrades mechanical properties (especially fatigue strength and ductility), and can act as crack initiation sites. * Hafifletme: * Yüksek Kaliteli Toz: Using powder with consistent spherical morphology, controlled PSD, and low internal gas porosity (as produced by Met3dp’s VIGA/PREP methods) is fundamental. Proper powder handling and storage to avoid moisture absorption are also critical. * Optimize Edilmiş Süreç Parametreleri: Precise control over laser/electron beam power, scan speed, layer thickness, and shielding gas atmosphere minimizes pore formation. Parameter development is key. * Sıcak İzostatik Presleme (HIP): The most effective method for closing internal gas porosity, significantly improving material integrity for critical applications.
4. Cracking: * Sebep: Can occur during printing (solidification cracking) or subsequent heat treatment due to high residual stresses exceeding the material’s strength, particularly in crack-sensitive alloys (e.g., certain high-strength aluminum or nickel alloys). * Hafifletme: * Malzeme Seçimi: Choose alloys with good weldability/printability where possible. * DfAM: Avoid sharp internal corners or features that act as stress concentrators. * Süreç Kontrolü: Optimized thermal management, potentially lower energy density parameters, and stress relief cycles can help. * Alloy Modification: Sometimes minor adjustments in alloy chemistry (within specification) can improve printability.
5. Support Removal Difficulties: * Sebep: Poorly designed supports (too dense, inaccessible locations), strong bonding between support and part, or delicate part features prone to damage during removal. * Hafifletme: * DfAM: Design supports for easy access and removal (e.g., using perforations, lower density interfaces). Minimize the need for supports through smart design and orientation. * Süreç Parametreleri: Optimize support interface parameters for adequate adhesion during build but easier separation afterward. * Post-Processing Teknikleri: Utilize appropriate tools and methods (e.g., wire EDM for clean cuts near the part).
6. Surface Finish Imperfections: * Sebep: Partially sintered powder particles adhering to the surface (“downskin” roughness on overhangs), stair-stepping effects on curved surfaces, witness marks from support removal. * Hafifletme: * Oryantasyon: Optimize orientation for best finish on critical surfaces. * Süreç Parametreleri: Fine-tune contouring parameters and layer thickness. * İşlem sonrası: Utilize appropriate surface finishing techniques (blasting, tumbling, polishing) to achieve the required Ra.
Başarı için Ortaklık:
Navigating these challenges requires deep expertise in materials science, process physics, DfAM, and rigorous quality control. This is where partnering with a knowledgeable and capable AM service provider becomes invaluable. Met3dp combines its strengths in high-quality powder production, advanced printing technology (including SEBM which inherently reduces thermal stress for some materials), and comprehensive application support to help clients overcome these hurdles. Our team works collaboratively to optimize designs, refine processes, and implement appropriate post-processing and quality assurance measures, ensuring your custom aerospace sensor mounts are delivered reliably and meet all performance criteria. If you’re encountering challenges or looking to explore the possibilities of metal AM for demanding applications, we encourage you to visit our main site at https://met3dp.com/ and contact our team to discuss your specific needs.
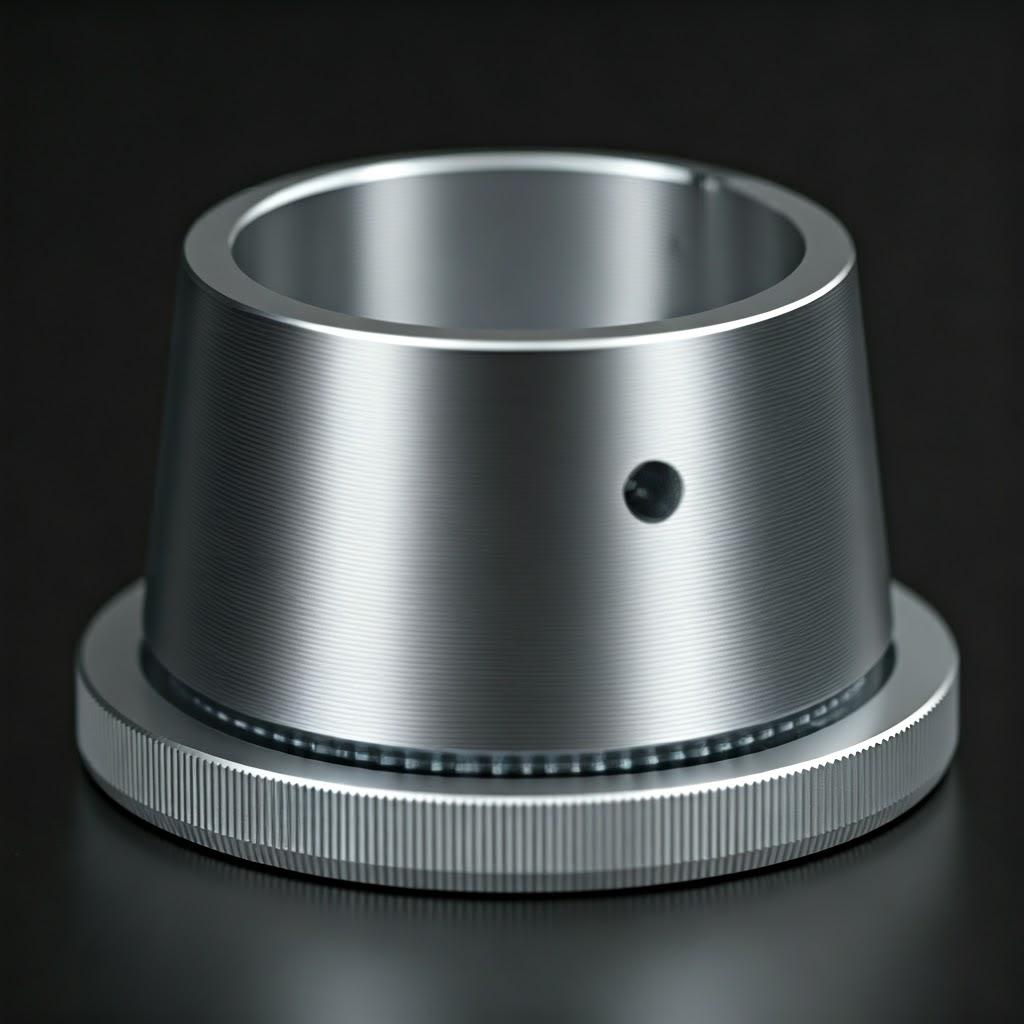
Supplier Selection: Choosing Your Metal 3D Printing Partner for Aerospace Components
Selecting the right additive manufacturing (AM) service provider is as critical as optimizing the design or choosing the correct material, especially for aerospace components where quality, reliability, and traceability are non-negotiable. The capabilities, expertise, and quality systems of your metal 3D printing service provider will directly impact the success of your custom aerospace sensor mount project. Procurement managers and engineers need a structured approach to evaluate potential partners.
Here are key criteria to consider when choosing a metal AM supplier for aerospace components:
1. Aerospace Certifications and Quality Management System (QMS): * Importance: The aerospace industry demands rigorous quality standards. While specific project requirements vary, suppliers demonstrating commitment to aerospace quality are preferred. * Key Standard: AS9100 certification is the internationally recognized QMS standard for the aviation, space, and defense industries. A supplier with AS9100 certification demonstrates robust processes for traceability, configuration management, risk management, and process control tailored to aerospace needs. * Evaluation: Ask potential suppliers about their current certifications (AS9100, ISO 9001) and their roadmap for achieving higher-level certifications if not already held. Review their Quality Manual and understand their approach to process validation and non-conformance management.
2. Technical Expertise and DfAM Support: * Importance: The supplier should be more than just a machine operator; they should be a technical partner. Deep expertise in metallurgy, AM process physics, and especially Design for Additive Manufacturing (DfAM) is crucial. * Evaluation: Assess the engineering capabilities of the supplier’s team. Do they offer DfAM consultation services? Can they provide expert advice on material selection, orientation strategies, support structure design, and topology optimization specific to your sensor mount? Review case studies or examples of similar aerospace projects they have completed.
3. Equipment Capabilities and Technology: * Importance: The supplier must possess the right AM technology (e.g., Laser Powder Bed Fusion – LPBF/SLM, Electron Beam Melting – SEBM) suitable for your chosen material (316L, AlSi10Mg, or others) and part requirements (resolution, surface finish, build volume). * Evaluation: Inquire about their specific machine models, build envelope sizes, beam type (laser/electron), and process monitoring capabilities. Understand their machine maintenance and calibration schedules. A provider like Met3dp, offering specialized technologies like SEBM known for lower residual stress in certain materials, might provide an advantage for specific applications. Assess if their equipment scale matches your potential production volume needs (prototyping vs. serial production).
4. Material Portfolio and Quality Control: * Importance: The supplier must offer the specific aerospace-grade materials you require (e.g., 316L, AlSi10Mg) and demonstrate stringent control over material quality and handling. * Evaluation: Verify their material sourcing – do they use certified powders from reputable suppliers, or do they, like Met3dp, produce high-quality powders internally using advanced methods like VIGA or PREP? How do they manage powder traceability (batch control), storage (environment control), handling, and recycling to prevent contamination and ensure consistency? Request material datasheets based on their actual printed and processed components, not just generic powder specs.
5. Post-Processing Capabilities: * Importance: As discussed, post-processing is essential. An ideal supplier either has comprehensive in-house capabilities (stress relief, heat treatment, support/part removal, basic finishing) or well-managed partnerships with certified providers for specialized processes (HIP, advanced machining, coating, NDT). * Evaluation: Understand which post-processing steps they perform in-house versus outsource. Verify the quality control measures for outsourced processes. Ensure their capabilities align with the full scope of requirements for your sensor mount (e.g., T6 heat treatment for AlSi10Mg, precision machining, required surface finish).
6. Track Record and Aerospace Experience: * Importance: Experience matters, especially in aerospace. A supplier with a proven track record of successfully delivering aerospace components understands the industry’s unique demands regarding documentation, quality, and timelines. * Evaluation: Ask for references or case studies specifically within the aerospace sector. Inquire about their experience with parts of similar complexity, material, and criticality to your sensor mount.
7. Communication and Project Management: * Importance: Clear, timely communication and transparent project management are vital for complex projects. * Evaluation: Assess their responsiveness during the quoting and initial discussion phases. Understand their project management approach – who will be your primary point of contact? How will progress be tracked and reported?
8. Location and Logistics: * Importance: While not always the top factor, supplier location can impact shipping costs, lead times, and the ease of conducting site audits or collaborative reviews if necessary. * Evaluation: Consider the logistical implications based on the supplier’s location relative to your facilities.
Table: Supplier Evaluation Checklist for Aerospace AM Sensor Mounts
Kriterler | Key Questions to Ask Potential Suppliers | Why It Matters for Sensor Mounts |
---|---|---|
Certifications/QMS | Are you AS9100 / ISO 9001 certified? Can we review your Quality Manual? How do you handle traceability? | Ensures adherence to stringent aerospace quality standards |
Technical Expertise/DfAM | What DfAM support do you offer? What’s your experience with [material]? Can you show aerospace examples? | Optimizes design for performance, manufacturability, and cost |
Equipment/Technology | What machine types/sizes? Process monitoring? Calibration frequency? SEBM available? | Ensures capability to produce the part with required precision/material |
Material Control | How do you source/validate powder? How is powder handled/recycled/tracked? Datasheets available? | Guarantees material integrity and consistent properties |
İşlem Sonrası | What capabilities in-house vs. outsourced? How are external partners qualified? | Ensures all required finishing/treatment steps are performed correctly |
İz Kaydı | Can you provide aerospace references/case studies? Experience with similar parts? | Demonstrates ability to meet aerospace expectations |
Communication/PM | Who is the contact? How is progress reported? What is your quoting process? | Facilitates smooth project execution and issue resolution |
Location/Logistics | Where are you located? What are typical shipping arrangements/times? | Impacts lead time, cost, and potential for collaboration |
Sayfalara Aktar
Met3dp, headquartered in Qingdao, China, positions itself as a leading provider of comprehensive additive manufacturing solutions. With a focus on both industry-leading 3D printing equipment (including SEBM systems) and the in-house production of high-performance metal powders (including stainless steels, superalloys, and potentially aluminum alloys – check current portfolio), Met3dp emphasizes quality control from material source to final part. Our team possesses deep expertise in metal AM, ready to partner with aerospace clients to develop and manufacture mission-critical components like custom sensor mounts, enabling next-generation manufacturing transformations.
Cost & Lead Time: Understanding the Economics of AM Sensor Mounts
While metal additive manufacturing unlocks significant design and performance benefits, understanding the cost structure and typical lead times is essential for project planning and budgeting, particularly for procurement managers comparing AM to traditional methods like CNC machining. The economics of AM differ from subtractive manufacturing, influenced heavily by factors beyond just raw material weight.
Key Cost Drivers for Metal AM Sensor Mounts:
- Part Design Complexity & Volume:
- Karmaşıklık: Highly intricate designs with complex internal features or extensive lattice structures can increase design/setup time and potentially build time. However, complexity is where AM often shines, enabling designs impossible otherwise.
- Hacim: The physical bounding box volume of the part influences how much space it takes up in the build chamber and, to some extent, the amount of powder used. More significantly, the actual volume of printed material directly impacts cost.
- Material Type and Cost:
- Metal powders for AM, especially specialized aerospace alloys, are significantly more expensive per kilogram than bulk wrought materials used in machining. The cost varies greatly between materials (e.g., AlSi10Mg < 316L < Ti6Al4V < Inconel).
- The amount of material used (part volume + support volume) is a major cost factor.
- Support Structure Volume:
- Supports consume material and add to the build time. More importantly, they require significant post-processing labor for removal and surface finishing. Designs optimized via DfAM to minimize supports will generally be less expensive.
- Makine Zamanı (İnşa Zamanı):
- This is often the largest cost component. It’s primarily driven by the height of the part(s) in the build chamber (determining the number of layers) and the area that needs to be scanned per layer.
- Printing multiple parts simultaneously (nesting) within the build chamber can significantly reduce the cost per part by maximizing machine utilization.
- Factors like layer thickness (thinner = longer time), scan strategy, and machine overhead rates influence this cost.
- İşlem Sonrası Gereksinimler:
- Each post-processing step (stress relief, heat treatment, HIP, machining, finishing) adds cost due to labor, equipment usage, and potentially specialized external services.
- The level of post-processing required depends entirely on the application’s requirements for tolerance, surface finish, and mechanical properties. High-precision machining or extensive polishing can significantly increase costs.
- Quality Assurance and Inspection:
- The level of required inspection (visual, dimensional, NDT like CT scanning or dye penetrant, material testing) impacts cost. Aerospace components often require higher levels of inspection and documentation compared to industrial parts.
- Sipariş Miktarı:
- While AM avoids tooling costs, there are still setup costs associated with preparing the build file and loading the machine. These setup costs are amortized over the number of parts produced. Therefore, the cost per part generally decreases with larger batch sizes, although the effect might be less pronounced than in traditional high-volume manufacturing.
Typical Lead Times:
Lead time for metal AM sensor mounts is the sum of several stages:
- Design Finalization & Quoting: Depends on design maturity and supplier responsiveness (typically 1-5 days).
- Build Preparation: File preparation, build layout planning, machine setup (typically 1-3 days).
- Printing (Build Time): Highly variable, depends on part height, density, and number of parts in the build. Can range from hours for very small parts to several days or even over a week for tall or densely packed large builds.
- İşlem sonrası: This can be a significant portion of the lead time. Stress relief/heat treatment cycles take time (hours to days including cooling), support removal and basic finishing take labor time, and machining or specialized processes add further delays (potentially 1-3 weeks or more depending on complexity and external vendor queues).
- Quality Inspection & Shipping: Final checks and transit time (typically 1-5 days depending on level and location).
Overall Lead Time: For custom aerospace sensor mounts, typical lead times from order placement to delivery can range from 2 to 8 weeks, heavily dependent on the factors above, particularly post-processing complexity and required quality validation. Rush services may be available at a premium cost.
Table: Factors Influencing Cost & Lead Time of AM Sensor Mounts
Faktör | Maliyet Üzerindeki Etkisi | Impact on Lead Time | Mitigation / Optimization |
---|---|---|---|
Part Volume/Complexity | Higher volume = more material; Complexity may add time | Complexity can increase print/post-processing time | DfAM (topology optimization), focus complexity where needed |
Malzeme Türü | Higher cost alloys increase price significantly | Minor impact (unless affects print speed/parameters) | Select appropriate material based on requirements |
Destek Yapıları | Material cost + significant labor cost for removal | Adds labor time in post-processing | DfAM to minimize supports, design for easy removal |
Machine Time | Major cost driver (based on height/area/layers) | Often the longest single step (days/weeks) | Optimize orientation, nesting multiple parts |
İşlem Sonrası | Adds significant cost (labor, equipment, services) | Can be the longest cumulative part of lead time | Specify only necessary steps, DfAM for finishing ease |
Quality/Inspection | Higher levels increase cost | Adds time for testing and documentation | Clearly define minimum required QA levels |
Sipariş Miktarı | Higher quantity reduces cost per part (amortizes setup) | Larger batches take longer to print/process | Balance batch size with demand and lead time needs |
Sayfalara Aktar
Met3dp provides comprehensive quoting based on your specific design files (CAD models) and technical requirements. By understanding your application, material needs, and post-processing specifications, we can offer tailored solutions and transparent pricing. Explore our range of materials and printing services and contact us for a detailed quote on your custom aerospace sensor mount project.

Frequently Asked Questions (FAQ): Aerospace Sensor Mounts via Metal AM
Here are answers to some common questions engineers and procurement managers have about using metal 3D printing for aerospace sensor mounts:
1. Is metal 3D printing suitable and reliable enough for flight-critical aerospace sensor mounts? * Cevap: Yes, metal AM is increasingly being adopted for flight-critical components, including sensor mounts, across the aerospace industry, provided rigorous processes are followed. Success depends on several factors: * Mature Process Control: Using qualified machines with validated process parameters for the specific material (e.g., 316L, AlSi10Mg, Ti6Al4V). * High-Quality Materials: Utilizing aerospace-grade metal powders with controlled chemistry and physical properties, along with strict powder handling protocols. * Appropriate Post-Processing: Implementing necessary steps like stress relief, heat treatment (e.g., T6 for AlSi10Mg), and potentially HIP to ensure desired material properties and eliminate defects like porosity. * Rigorous Quality Assurance: Employing comprehensive NDT methods (CT scanning, dye penetrant) and dimensional inspection, backed by a robust QMS (ideally AS9100 certified). * DfAM: Designing the part specifically for the AM process to manage stresses and optimize performance. * When these conditions are met, metal AM parts can exhibit mechanical properties comparable or even superior (e.g., specific strength) to traditionally manufactured counterparts. Partnering with an experienced aerospace AM supplier like Met3dp is key to ensuring reliability.
2. How does the cost of a metal 3D printed sensor mount compare to one produced by traditional CNC machining? * Cevap: The cost comparison is nuanced and depends heavily on the specific part and production volume: * Low Volume / High Complexity: For highly complex geometries (e.g., topology optimized, intricate internal features) or very low production volumes (prototypes, one-offs, small batches), metal AM is often daha uygun maliyetli than CNC machining. This is because AM avoids the high tooling/fixture costs and extensive programming time associated with machining complex parts from billet. * Simple Geometry / High Volume: For relatively simple bracket geometries produced in high volumes, traditional CNC machining is typically daha az pahalı per part due to faster cycle times and lower raw material costs (bulk vs. powder). * Parça Konsolidasyonu: If AM allows consolidating multiple machined parts into a single printed component, the total system cost (including assembly labor and reduced inventory) can be lower with AM, even if the individual printed part cost seems higher initially. * Lightweighting Value: The cost comparison should also consider the downstream value of weight savings achieved through AM in aerospace applications (fuel efficiency, payload capacity), which can often justify a higher per-part cost. * It’s best to get quotes for both methods based on the specific sensor mount design and quantity to make an informed decision.
3. What information does an AM supplier need to provide an accurate quote for a custom aerospace sensor mount? * Cevap: To provide an accurate quote and assess manufacturability, suppliers like Met3dp typically require the following information: * 3D CAD Modeli: A high-quality 3D model in a standard format (e.g., STEP, IGES, STL). Native CAD files are sometimes helpful but STEP is usually preferred for interoperability. * 2D Drawings (if available): Drawings that clearly define critical dimensions, tolerances, surface finish requirements (Ra), and any specific features that need special attention (e.g., GD&T callouts). * Material Specification: The desired metal alloy (e.g., 316L, AlSi10Mg, Ti6Al4V) including any specific grade or standard (e.g., ASTM). * İşlem Sonrası Gereksinimler: Details on required heat treatments (stress relief, T6, annealing, HIP), machining operations (which features, tolerances), surface finish specifications, and any coating needs. * Quality & Inspection Requirements: Specify the level of inspection needed (e.g., standard dimensional check, CMM report, NDT requirements like CT scan or FPI, material certifications). Mention if AS9100 compliance is required. * Sipariş Miktarı: The number of parts required per order and anticipated annual volume, if applicable. * Uygulama Bağlamı (İsteğe bağlı ancak yararlı): Briefly describing the sensor type, operating environment, and key performance drivers can help the supplier offer better DfAM advice or suggest optimizations.
Conclusion: Elevating Aerospace Performance with 3D Printed Sensor Mounts
In the relentless pursuit of higher performance, greater efficiency, and enhanced capabilities within the aerospace industry, every component design offers an opportunity for innovation. Custom aerospace sensor mounts, though seemingly small, are critical enablers of system functionality, providing stable and precise platforms for vital instrumentation in extreme environments. Metal additive manufacturing has emerged as a powerful technology uniquely suited to producing these components, offering a paradigm shift away from the constraints of traditional manufacturing.
As we’ve explored, leveraging metal AM for sensor mounts using materials like robust 316L paslanmaz çelik or lightweight AlSi10Mg alüminyum alaşımı provides compelling advantages:
- Eşsiz Tasarım Özgürlüğü: Enabling complex, topology-optimized, and conformal geometries previously unattainable.
- Significant Lightweighting: Reducing component mass through efficient material distribution and lattice structures, crucial for flight applications.
- Parça Konsolidasyonu: Simplifying assemblies, reducing part count, and enhancing reliability by printing multiple functions into a single piece.
- Rapid Iteration & Customization: Accelerating development cycles and enabling bespoke solutions tailored to specific sensor and platform needs.
However, realizing these benefits requires a holistic approach. Success hinges on embracing Katmanlı Üretim Tasarımı (DfAM) principles from the outset, carefully considering material selection, understanding achievable tolerances and surface finishes, planning necessary post-processing steps, and proactively addressing potential manufacturing challenges.
Crucially, the journey relies on collaboration with a knowledgeable and capable metal additive manufacturing partner. Choosing a supplier with proven aerospace experience, robust quality systems (working towards standards like AS9100), advanced equipment, high-quality material control, and comprehensive technical expertise is paramount.
Met3dp stands ready to be that partner. With our foundation in producing high-performance metal powders using industry-leading VIGA and PREP technologies, coupled with advanced SEBM and other printing systems, we offer an integrated approach to metal additive manufacturing. Our team is committed to helping aerospace engineers and procurement managers navigate the complexities of AM, from design optimization through post-processing and quality validation, ensuring your custom sensor mounts meet the demanding requirements of the aerospace sector.
The future of aerospace manufacturing is increasingly intertwined with additive technologies. By embracing metal 3D printing for components like sensor mounts, companies can unlock new levels of performance, accelerate innovation, and maintain a competitive edge.
Contact Met3dp today to explore how our cutting-edge systems, advanced metal powders, and application development services can power your organization’s additive manufacturing goals and elevate the performance of your next aerospace project.
Paylaş
MET3DP Technology Co, LTD, merkezi Qingdao, Çin'de bulunan lider bir katmanlı üretim çözümleri sağlayıcısıdır. Şirketimiz, endüstriyel uygulamalar için 3D baskı ekipmanları ve yüksek performanslı metal tozları konusunda uzmanlaşmıştır.
İşletmeniz için en iyi fiyatı ve özelleştirilmiş Çözümü almak için sorgulayın!
İlgili Makaleler
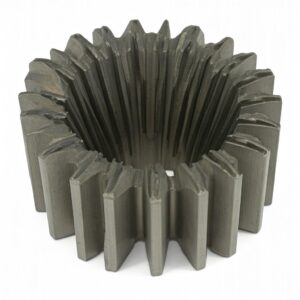
Yüksek Performanslı Nozul Kanat Segmentleri: Metal 3D Baskı ile Türbin Verimliliğinde Devrim
Daha Fazla Oku "Met3DP Hakkında
Son Güncelleme
Bizim Ürünümüz
BİZE ULAŞIN
Herhangi bir sorunuz var mı? Bize şimdi mesaj gönderin! Mesajınızı aldıktan sonra tüm ekibimizle talebinize hizmet edeceğiz.
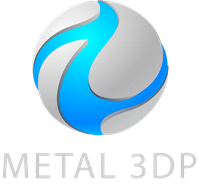
3D Baskı ve Katmanlı Üretim için Metal Tozları