Electronics Housings for Satellites 3D Printed in Al Alloys
İçindekiler
The aerospace industry, particularly satellite manufacturing, operates at the cutting edge of technology, demanding components that are not only lightweight and robust but also capable of withstanding extreme environmental conditions. Electronics housings, the protective shells for sensitive satellite circuitry, are critical components that exemplify these demanding requirements. Traditionally manufactured through subtractive methods like CNC machining, these housings are increasingly benefiting from the design freedom, weight reduction potential, and accelerated production timelines offered by metal additive manufacturing (AM), commonly known as 3D printing. This shift is particularly evident with the use of advanced aluminum alloys like AlSi10Mg and the high-performance Scalmalloy®, materials renowned for their excellent strength-to-weight ratio, thermal properties, and suitability for the harsh environment of space. This post delves into the specifics of using metal 3D printing to produce high-quality electronics housings for satellite applications, exploring the benefits, materials, design considerations, and supplier selection criteria crucial for aerospace engineers and procurement managers.
Introduction: Defining Space Electronics Housings and their Critical Role in Satellites
Space electronics housings are bespoke enclosures designed to protect the delicate electronic systems aboard satellites, rockets, and other spacecraft from the multitude of hazards encountered beyond Earth’s atmosphere. These hazards are diverse and severe, necessitating housings that offer uncompromising performance across several fronts.
Core Functions of Space Electronics Housings:
- Physical Protection: Shielding sensitive components (PCBs, processors, sensors, power units) from physical shocks, vibrations, and potential impacts during launch, deployment, and orbital maneuvering. The launch phase, in particular, subjects the satellite to extreme G-forces and vibrational loads.
- Environmental Shielding: Providing a barrier against the vacuum of space, micrometeoroid and orbital debris (MMOD) impacts, and extreme temperature fluctuations (ranging from hundreds of degrees Celsius in direct sunlight to far below freezing in shadow).
- Termal Yönetim: Efficiently dissipating heat generated by the internal electronics to prevent overheating, which can degrade performance or lead to component failure. This often requires intricate internal structures or integration with thermal straps and radiators.
- Electromagnetic Interference (EMI) Shielding: Protecting sensitive electronics from both internal and external electromagnetic interference, ensuring signal integrity and preventing malfunctions. The housing material and design play a crucial role in attenuating unwanted electromagnetic radiation.
- Yapısal Bütünlük: Contributing to the overall structural integrity of the satellite assembly, often serving as mounting points for other components or subsystems.
Why They Matter:
The reliability of satellite electronics is paramount. A failure in a critical system, such as communications, navigation, or power distribution, can jeopardize the entire mission, resulting in significant financial loss and the failure to achieve mission objectives. The electronics housing is the first line of defense for these vital systems. Its design and material properties directly impact:
- Mission Lifespan: A well-designed housing ensures electronics operate within their specified temperature and environmental limits, extending their operational life.
- Performans: Optimal thermal management and EMI shielding guarantee that electronics function as intended, delivering accurate data and reliable performance.
- Mass Budget: In aerospace, every gram counts. Lighter housings contribute significantly to reducing launch costs and potentially allow for more payload capacity.
- System Integration: Housings must integrate seamlessly with other satellite subsystems, including structural elements, wiring harnesses, and thermal control systems.
Traditionally, these housings were meticulously machined from solid blocks of aerospace-grade aluminum or titanium. While effective, this subtractive process often results in significant material waste (buy-to-fly ratio) and limitations in geometric complexity, particularly for features aimed at weight reduction or enhanced thermal management. The advent of metal 3D baskı offers a transformative approach, enabling the creation of highly optimized, lightweight, and complex housings previously unattainable. Companies like Met3dp, specializing in advanced metal powders and additive manufacturing systems, are at the forefront of enabling this transition, providing the materials and technology needed to produce space-grade components.
Applications: Key Use Cases for 3D Printed Electronics Housings in Aerospace
The unique capabilities of metal additive manufacturing, particularly Laser Powder Bed Fusion (LPBF) and Electron Beam Melting (EBM), have unlocked numerous applications for 3D printed electronics housings within the aerospace sector, especially for satellite platforms. The ability to create complex geometries, integrate multiple functions into a single part, and significantly reduce weight makes AM an ideal solution for various housing requirements.
Specific Use Cases:
- Highly Customized Enclosures for CubeSats and SmallSats:
- Meydan okumak: Small satellites have extremely tight constraints on mass, volume, and power. Housings must be incredibly compact and lightweight.
- AM Solution: 3D printing allows for the creation of bespoke enclosures perfectly tailored to the specific dimensions and layout of the electronics within a CubeSat or SmallSat standard (e.g., 1U, 3U, 6U). Complex internal features for mounting PCBs, connectors, and managing cables can be integrated directly into the housing design, minimizing part count and assembly time. Lightweight lattice structures or topology optimization can be applied to further reduce mass without compromising structural integrity.
- Housings with Integrated Thermal Management:
- Meydan okumak: Effectively dissipating heat from high-power electronics in the vacuum of space is critical. Traditional solutions often involve separate heat sinks, thermal straps, or heat pipes attached to the housing.
- AM Solution: Metal AM enables the direct integration of complex thermal management features into the housing itself. This can include:
- Internal Cooling Channels: Designing intricate channels within the housing walls for fluid cooling loops (if applicable).
- Optimized Heat Sinks: Printing complex fin geometries or lattice structures on the exterior or interior surfaces to maximize surface area for radiative cooling.
- Conformal Cooling: Channels that precisely follow the contours of heat-generating components for more efficient heat transfer.
- Materials like AlSi10Mg offer good thermal conductivity, suitable for these applications.
- Weight-Optimized Housings for Large Satellites and Deep Space Probes:
- Meydan okumak: Reducing the overall mass of large GEO communication satellites or interplanetary probes directly translates to lower launch costs or increased payload capacity for scientific instruments or fuel.
- AM Solution: Topology optimization software can be used in conjunction with AM to remove material from non-critical areas of the housing, resulting in organic-looking, highly efficient structures that meet all structural and thermal requirements with minimal mass. Scalmalloy®, with its superior strength-to-weight ratio compared to traditional aluminum alloys, is particularly advantageous here.
- Hızlı Prototipleme ve Yineleme:
- Meydan okumak: Aerospace development cycles are often long and expensive. Testing and iterating on housing designs using traditional manufacturing can be slow and costly.
- AM Solution: 3D printing allows engineers to quickly produce functional prototypes of electronics housings for fit checks, thermal testing, and vibration analysis. Design modifications can be implemented and reprinted in days rather than weeks or months, accelerating the development process significantly.
- Consolidated Assemblies:
- Meydan okumak: Traditional housings might consist of multiple machined parts (base, lid, brackets, internal supports) that need to be assembled using fasteners. Each interface and fastener adds weight, complexity, and potential points of failure.
- AM Solution: Additive manufacturing allows designers to consolidate multiple components into a single, monolithic printed part. This reduces part count, eliminates fasteners, simplifies assembly, improves structural integrity, and often reduces overall mass.
- Housings for RF (Radio Frequency) Electronics:
- Meydan okumak: Housings for RF components like amplifiers, filters, and antennas require specific geometries for optimal performance and effective EMI shielding.
- AM Solution: The precision of metal AM allows for the creation of complex internal geometries, waveguides, and shielding features tailored to specific RF requirements. The surface finish achievable with AM, potentially combined with post-processing, can meet the needs of high-frequency applications.
Industry Impact:
The adoption of 3D printed electronics housings is accelerating innovation across the satellite industry, from large established aerospace primes to agile NewSpace startups. Procurement managers are increasingly looking for suppliers who can leverage AM to deliver components faster, lighter, and with enhanced functionality. Wholesale suppliers of space components and specialized AM service providers are key enablers in this evolving supply chain.
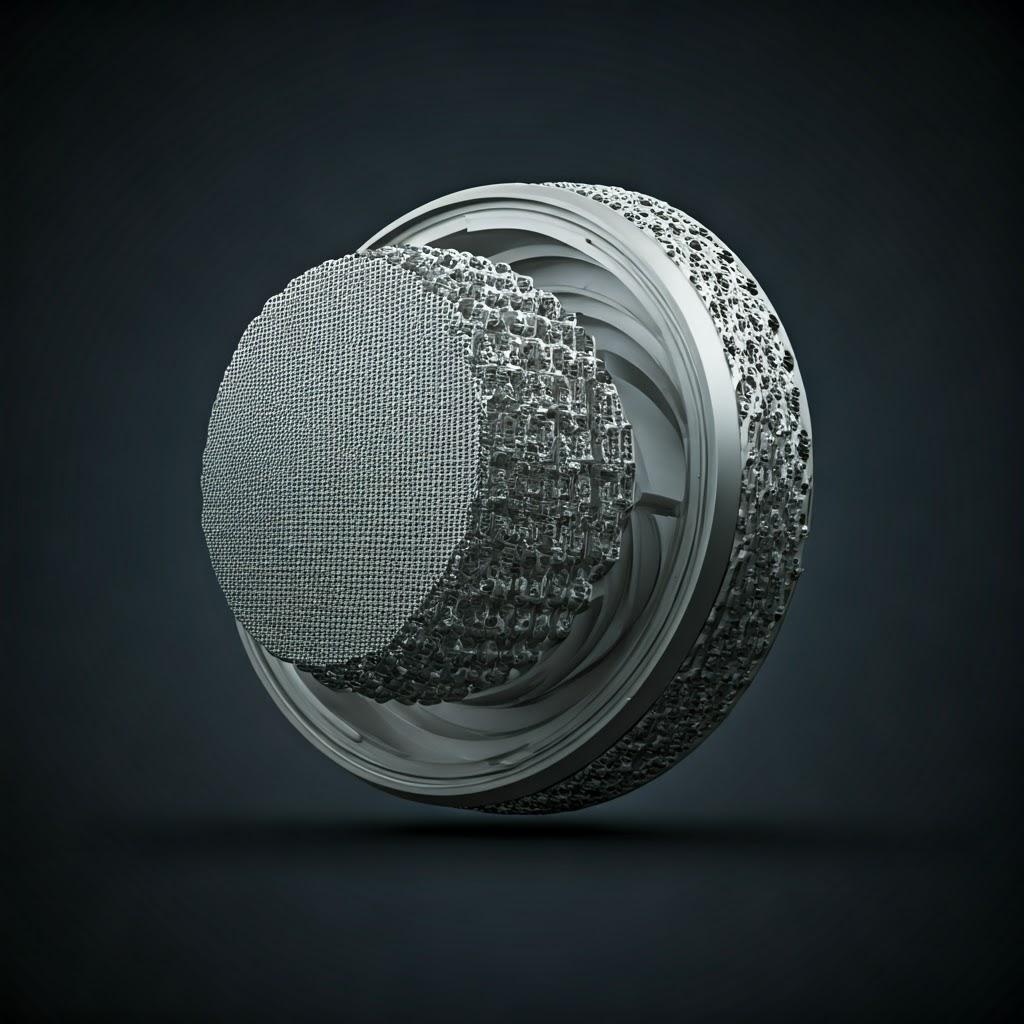
Why Metal AM? Advantages of Additive Manufacturing for Satellite Electronics Housings vs. Traditional Methods
While traditional manufacturing methods like CNC machining have long served the aerospace industry reliably, metal additive manufacturing presents a compelling suite of advantages specifically beneficial for producing satellite electronics housings. Understanding these benefits is crucial for engineers designing next-generation satellite systems and procurement managers sourcing these critical components.
Özellik | Traditional Manufacturing (CNC Machining) | Metal Additive Manufacturing (e.g., LPBF) | Advantage for Satellite Housings |
---|---|---|---|
Tasarım Özgürlüğü | Limited by tool access, cutter geometry, and axis constraints | Nearly unlimited geometric complexity possible | Enables topology optimization, integrated features (thermal, mounting), complex internal channels, organic shapes, part consolidation. |
Ağırlık Azaltma | Achieved by machining away material, limited optimization | Enables topology optimization, lattice structures, thin walls | Significant mass savings possible (often 20-50%+), reducing launch costs and increasing payload capacity. |
Malzeme Atıkları | High (buy-to-fly ratio often >10:1) | Low (powder reuse, near-net-shape production) | More sustainable, lower raw material cost contribution, especially for expensive alloys like titanium or Scalmalloy®. |
Parça Konsolidasyonu | Multiple parts often required, assembly needed | Ability to print multiple components as a single unit | Reduced assembly time, fewer fasteners (weight, failure points), improved structural integrity, simplified supply chain. |
Teslim Süresi | Can be long due to programming, setup, machining time | Faster for complex parts, rapid prototyping possible | Accelerated development cycles, quicker iteration, faster time-to-orbit for new satellite designs. |
Özelleştirme | High tooling/setup cost for low volumes or unique designs | Ideal for low-volume, high-complexity, bespoke parts | Cost-effective production of unique housings tailored to specific mission requirements without dedicated tooling. |
Integrated Features | Difficult/impossible to machine complex internal features | Can incorporate internal channels, cooling fins, shielding walls | Enhanced thermal management, improved EMI shielding, integrated functionality without assembly steps. |
Tedarik Zinciri | Relies on specialized machining shops, material suppliers | Enables distributed manufacturing, digital inventory | Potentially simplified logistics, on-demand production closer to the point of need. |
Sayfalara Aktar
Key Advantages Elaborated:
- Unprecedented Lightweighting: The primary driver for AM adoption in space is weight reduction. Launch costs are directly proportional to mass, often costing thousands of dollars per kilogram sent to orbit. AM techniques, especially when combined with topology optimization algorithms, allow engineers to design housings that meet stringent structural and thermal requirements using the absolute minimum amount of material. This is achieved by creating complex, often organic-looking shapes and internal lattice structures that are impossible to machine conventionally. Alloys like Scalmalloy®, specifically designed for AM, push this advantage further with their exceptional strength-to-weight ratio.
- Enhanced Thermal Performance: As electronics become more powerful and compact, managing heat becomes increasingly challenging, especially in the vacuum of space where convection cooling is absent. AM allows for the integration of sophisticated thermal management features directly into the housing structure. Imagine heat pipes or vapor chambers built içine the walls of the enclosure, or highly complex, optimized fin structures for radiative cooling – designs unachievable through machining. This leads to more reliable electronics operation and potentially longer mission life.
- Accelerated Innovation Cycles: The ability to move from a CAD design to a physical metal prototype in days allows engineering teams to test and iterate designs far more rapidly than with traditional methods. Fit checks, thermal vacuum tests, and vibration tests can be performed on AM prototypes early in the design cycle, catching potential issues and allowing for rapid refinement. This agility is particularly crucial for the fast-paced NewSpace sector.
- Complexity is (Almost) Free: In traditional manufacturing, increased complexity directly translates to increased cost (more machine time, complex tooling, multiple setups). In additive manufacturing, complexity has a much lower impact on cost. Printing a highly complex, optimized housing often takes a similar amount of time and resources as printing a simpler, blockier design of the same volume. This encourages engineers to fully exploit the design freedom offered by AM to maximize performance.
- Supply Chain Resilience and Part Consolidation: Reducing the number of individual parts in an assembly simplifies procurement, inventory management, quality control, and assembly processes. Printing a previously multi-part housing as a single unit eliminates potential points of failure at joints and fasteners and reduces the reliance on multiple suppliers and manufacturing processes. Leading providers like Met3dp offer integrated solutions, from high-quality metal tozları to advanced printing systems, streamlining the supply chain for aerospace manufacturers.
While AM offers significant advantages, it’s important to note that traditional machining often still excels in achieving very fine surface finishes and extremely tight tolerances without extensive post-processing, and it can be more cost-effective for very high-volume production of simpler designs. Often, a hybrid approach, using AM for the complex initial shape and CNC machining for critical interfaces and tolerances, provides the optimal solution.
Material Focus: AlSi10Mg and Scalmalloy® – Properties and Benefits for Space Applications
The choice of material is fundamental to the success of any space component, especially electronics housings. Aluminum alloys are frequently favored due to their low density, good thermal conductivity, and relative ease of processing. For additive manufacturing of satellite housings, two aluminum-based powders stand out: the established AlSi10Mg and the high-performance Scalmalloy®.
AlSi10Mg:
AlSi10Mg is one of the most widely used aluminum alloys in metal additive manufacturing, particularly via Laser Powder Bed Fusion (LPBF). It’s essentially an aluminum casting alloy adapted for AM processes.
- Kompozisyon: Primarily aluminum (Al), with significant additions of Silicon (Si, ~9-11%) and Magnesium (Mg, ~0.2-0.45%).
- Anahtar Özellikler:
- İyi Güç-Ağırlık Oranı: Offers moderate strength combined with low density (~2.67 g/cm³).
- Mükemmel Termal İletkenlik: Facilitates heat dissipation away from sensitive electronics.
- İyi Korozyon Direnci: Suitable for various environments, although specific coatings might be needed for long-term space exposure depending on the orbit and mission specifics.
- Mükemmel Basılabilirlik: Behaves well during the LPBF process, allowing for the creation of intricate details and relatively high resolution. It’s less prone to cracking compared to some other high-strength aluminum alloys during printing.
- Kaynaklanabilirlik: Can be welded if necessary, although AM often aims to eliminate such joints.
- Isıl İşlem Uygulanabilir: Mechanical properties can be significantly enhanced through post-print heat treatments (e.g., T6 solutionizing and aging).
- Benefits for Space Housings:
- Uygun Maliyetli: Generally less expensive than higher-performance alloys like Scalmalloy® or titanium.
- Well-Characterized: Extensive data exists on its properties and behavior in AM processes, reducing qualification hurdles.
- Good Balance: Offers a solid combination of mechanical strength, low weight, and thermal performance suitable for many satellite housing applications, especially where extreme structural loads are not the primary driver.
- Kullanılabilirlik: Widely available from numerous powder suppliers and offered by most metal AM service providers.
- Düşünceler:
- Lower strength compared to Scalmalloy® or titanium alloys.
- Mechanical properties can degrade at elevated temperatures (above ~150-200°C).
Scalmalloy®:
Developed specifically for additive manufacturing by APWorks (an Airbus subsidiary), Scalmalloy® is a high-performance aluminum-magnesium-scandium (Al-Mg-Sc) alloy.
- Kompozisyon: Aluminum alloyed with Magnesium (Mg) and Scandium (Sc), along with minor additions of Zirconium (Zr). The Scandium addition is key to its high performance.
- Anahtar Özellikler:
- Olağanüstü Güç-Ağırlık Oranı: Significantly stronger than AlSi10Mg, approaching the strength of some titanium alloys (like Ti-6Al-4V) but with lower density (~2.67 g/cm³). It exhibits excellent specific strength (strength divided by density).
- High Ductility and Toughness: Offers good elongation and resistance to fracture, important for handling launch loads and preventing catastrophic failure.
- Mükemmel Kaynaklanabilirlik: Can be readily welded.
- Good Corrosion Resistance.
- Stable at Elevated Temperatures: Retains its strength better at higher temperatures compared to AlSi10Mg.
- İyi Basılabilirlik: Designed for AM (primarily LPBF), offering good processability despite its high strength.
- Benefits for Space Housings:
- Maximum Weight Savings: Its high specific strength allows for even more aggressive lightweighting through topology optimization compared to AlSi10Mg, critical for launch cost reduction.
- High Structural Performance: Ideal for housings that bear significant structural loads or require high stiffness.
- Improved Reliability: Enhanced ductility and toughness provide a greater safety margin against unexpected stresses or impacts.
- Performance in Demanding Environments: Better suited for applications involving higher operational temperatures or extreme structural demands.
- Düşünceler:
- Daha Yüksek Maliyet: The inclusion of Scandium makes Scalmalloy® significantly more expensive than AlSi10Mg.
- Kullanılabilirlik: Less widely available than AlSi10Mg, requiring suppliers with specific expertise and parameter sets. Met3dp, with its focus on high-performance metal powders and advanced AM systems, is positioned to support applications demanding materials like Scalmalloy®.
- ITAR Restrictions: Depending on the supplier and end-use, there might be export control considerations (ITAR – International Traffic in Arms Regulations) primarily relevant for US-based projects or suppliers.
Material Selection Summary Table:
Özellik | AlSi10Mg | Scalmalloy® | Recommendation for Space Housings |
---|---|---|---|
Primary Advantage | Cost-effective, well-understood, good balance | Highest strength-to-weight, high performance | Choose AlSi10Mg for cost-sensitive projects or moderate performance needs. Choose Scalmalloy® for maximum weight saving and high structural/thermal demands. |
Spesifik Güç | İyi | Mükemmel | Scalmalloy® enables more aggressive lightweighting. |
Termal İletkenlik | Çok iyi | Good (slightly lower than AlSi10Mg) | Both are suitable, AlSi10Mg has a slight edge if thermal conductivity is the absolute priority over strength. |
Maliyet | Daha düşük | Daha yüksek | Budget constraints may favor AlSi10Mg. |
Maturity & Data | Yüksek | Moderate (growing rapidly) | AlSi10Mg has a longer track record and more public data. |
Supplier Base | Geniş | More specialized | Ensure your chosen AM partner has proven experience with the selected material, especially Scalmalloy®. |
Sayfalara Aktar
Choosing the right aluminum alloy depends heavily on the specific mission requirements, budget constraints, and performance targets for the satellite electronics housing. Both AlSi10Mg and Scalmalloy® offer significant advantages over traditionally manufactured components, enabling lighter, more complex, and highly functional designs crucial for the advancement of space technology. Consulting with material experts and experienced additive manufacturing service providers like Met3dp is essential to making the optimal material choice for your application.
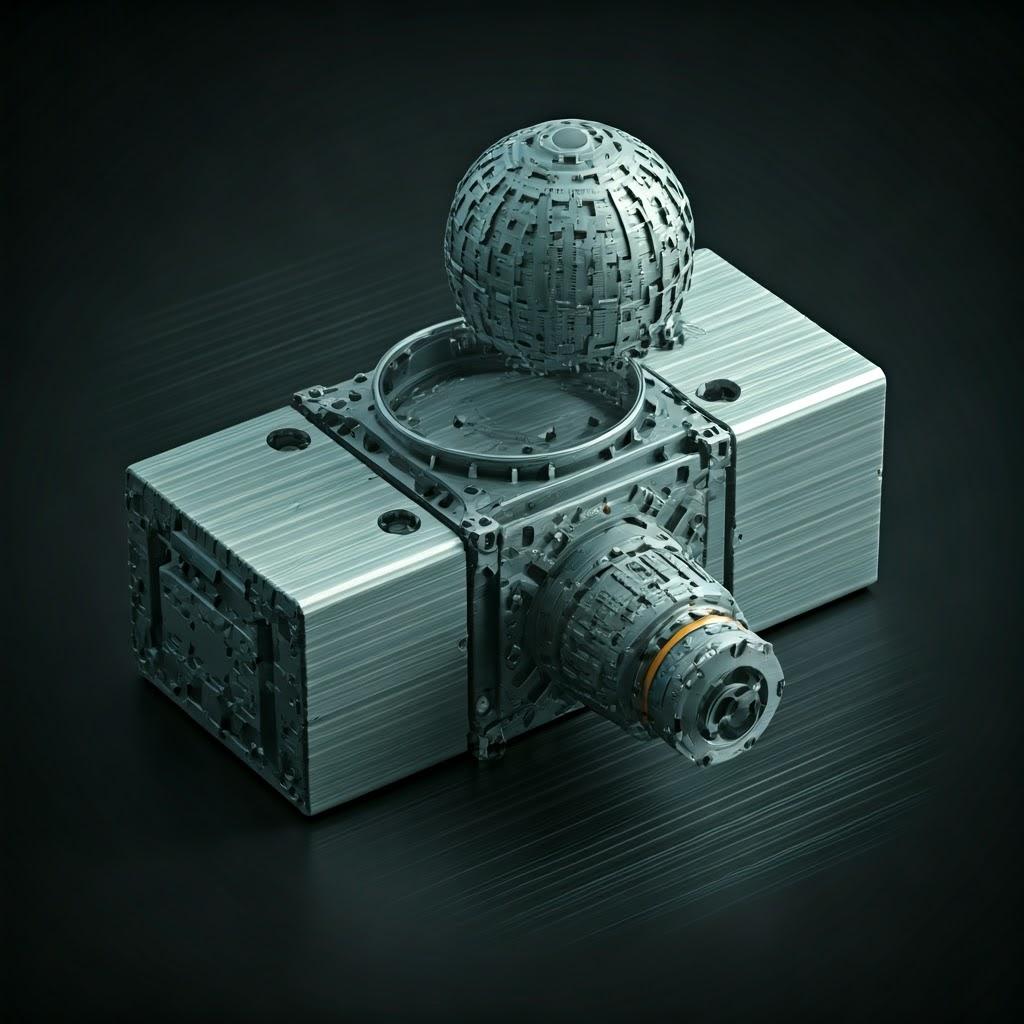
Design Optimization: Design for Additive Manufacturing (DfAM) Principles for Space Housings
Simply replicating a design intended for CNC machining using additive manufacturing rarely unlocks the full potential of the technology. To truly leverage the benefits of AM for space electronics housings—particularly lightweighting, integrated functionality, and improved thermal performance—engineers must embrace Design for Additive Manufacturing (DfAM). DfAM is a design philosophy that considers the capabilities and constraints of the AM process from the outset. Applying DfAM principles allows for the creation of highly optimized, innovative components that would be impossible or impractical to produce otherwise.
Key DfAM Principles for Aluminum Space Housings:
- Topology Optimization:
- Concept: Using software algorithms to remove material from areas where it’s not structurally necessary, based on defined load cases, constraints, and performance targets (e.g., minimize mass, maximize stiffness).
- Uygulama: Creates highly efficient, often organic-looking structures that maintain required strength and stiffness with significantly reduced mass. Ideal for lightweighting primary structures or brackets integrated into the housing. Requires careful definition of load paths, boundary conditions, and manufacturing constraints (e.g., minimum feature size, overhang angles).
- Benefit: Maximizes weight savings, directly impacting launch costs and satellite performance.
- Kafes Yapılar ve Dolgu:
- Concept: Incorporating internal lattice structures (e.g., honeycomb, gyroid, truss-like patterns) instead of solid material. These structures can be engineered for specific properties like high stiffness-to-weight ratio, energy absorption, or enhanced surface area.
- Uygulama: Used for internal support, further weight reduction in non-critical areas, or enhancing heat dissipation by increasing internal surface area for radiative or conductive cooling. Variable density lattices can be used to provide more support where needed.
- Benefit: Significant weight reduction, tunable mechanical properties, potential for improved thermal management.
- Parça Konsolidasyonu:
- Concept: Redesigning assemblies previously consisting of multiple parts into a single, monolithic component.
- Uygulama: Combining a housing base, lid, internal mounting brackets, and even thermal features into one printable part.
- Benefit: Reduces part count, eliminates fasteners (weight, assembly time, failure points), simplifies supply chain, improves structural integrity.
- Feature Integration:
- Concept: Designing functional features directly into the housing structure.
- Uygulama:
- Termal Yönetim: Integrated heat sinks (fins, pins), conformal cooling channels, heat pipes structures.
- Mounting Points: Custom bosses, threaded inserts (designed for post-print insertion or tapping), snap-fit features.
- Cable Routing: Internal channels or clips for managing wiring harnesses.
- EMI Koruması: Integrated shielding walls or compartments within the housing.
- Benefit: Enhanced functionality, reduced assembly complexity, improved performance (e.g., thermal efficiency).
- Designing for AM Process Constraints:
- Overhangs and Support Structures: AM processes like LPBF build layer by layer. Steep overhangs (typically >45 degrees from horizontal) require support structures during printing to prevent collapse or deformation. DfAM involves minimizing the need for supports by using self-supporting angles, chamfering edges, or reorienting the part during the design phase. Supports add material cost, print time, and post-processing effort (removal can damage surfaces).
- Duvar Kalınlığı: Minimum printable wall thickness depends on the machine, material (AlSi10Mg and Scalmalloy® generally allow thin walls), and design intent. DfAM ensures walls are sufficiently thick for structural integrity and printability but avoids excessive thickness to save weight and print time.
- Hole Orientation and Size: Small horizontal holes can be challenging to print accurately without supports. Designing holes vertically or using teardrop shapes can improve printability. Minimum hole size is also a constraint.
- Thermal Stress Management: Large, flat surfaces or abrupt changes in geometry can lead to warping due to thermal stresses during printing. DfAM incorporates design features like ribbed structures or gradual transitions to mitigate these stresses.
- Toz Giderme: Designs must allow for the removal of unfused powder from internal cavities and channels after printing. Include strategically placed drainage holes.
- Anisotropy Consideration:
- Concept: Mechanical properties of AM parts can differ slightly depending on the build direction (X, Y vs. Z axis) due to the layer-wise construction.
- Uygulama: Orienting the part optimally on the build plate to ensure the highest strength is aligned with the primary load directions. Critical features requiring specific strength should be designed considering potential anisotropy.
- Benefit: Ensures the final part meets performance requirements in critical load directions.
Tools and Techniques:
- CAD Software: Modern CAD packages increasingly incorporate DfAM features.
- Topology Optimization Software: Tools like Altair OptiStruct, Ansys Mechanical, Dassault Systèmes TOSCA.
- Simulation Software: FEA (Finite Element Analysis) and CFD (Computational Fluid Dynamics) are crucial for validating optimized designs under expected thermal and structural loads önce baskı.
- Collaboration with AM Experts: Working closely with experienced AM service providers, such as the team at Met3dp, provides invaluable feedback on design printability, material selection, and optimization strategies. Their expertise in various baskı yöntemleri ensures designs are feasible and optimized for production.
Implementing DfAM requires a shift in mindset for design engineers accustomed to traditional manufacturing constraints. However, the payoff in terms of performance gains, weight reduction, and accelerated innovation makes it an essential element of leveraging metal AM for demanding aerospace applications like satellite electronics housings.
Precision Matters: Achieving Tight Tolerances, Optimal Surface Finish, and Dimensional Accuracy
While AM offers incredible design freedom, achieving the precision required for space-grade components necessitates careful control over the entire process, from design to printing to post-processing. Aerospace engineers and procurement managers need realistic expectations regarding the tolerances, surface finish, and dimensional accuracy achievable with 3D printed aluminum alloys like AlSi10Mg and Scalmalloy®.
Boyutsal Doğruluk:
- Tanım: How closely the dimensions of the printed part match the original CAD model.
- Typical AM Capability: For well-controlled LPBF processes using Al alloys, typical dimensional accuracy is often cited in the range of ±0.1 mm to ±0.2 mm (or ±0.1-0.2% of the dimension, whichever is larger) for as-printed parts. However, this can vary significantly based on:
- Part size and geometry (larger parts may exhibit more deviation due to thermal effects).
- Machine calibration and condition.
- Material properties and powder quality.
- Build orientation and support strategy.
- Thermal stresses during printing and cooling.
- Achieving Higher Accuracy: For critical dimensions (e.g., mating interfaces, mounting points), post-print CNC machining is often employed to achieve tolerances in the range of ±0.01 mm to ±0.05 mm or even tighter, comparable to traditional machining. Designing the part with machining allowances on critical faces is a common DfAM strategy.
Tolerances:
- Tanım: The allowable variation in a dimension. Geometric Dimensioning and Tolerancing (GD&T) defines tolerances for form, orientation, location, and runout.
- AM vs. Machining: As-printed AM parts generally have looser tolerances compared to precision CNC machining. Achieving tight GD&T requirements often necessitates post-machining of specific features.
- Strategies:
- Design for Process: Specify looser tolerances on non-critical features to avoid unnecessary post-processing costs.
- Critical Feature Machining: Identify surfaces requiring tight tolerances (e.g., flatness, parallelism, position) and plan for post-machining operations. Add stock material (e.g., 0.5-1.0 mm) to these features in the AM design file.
- Süreç Kontrolü: Working with an AM provider with robust quality control, well-calibrated machines (like those utilized by Met3dp), and optimized parameters for AlSi10Mg or Scalmalloy® is crucial for minimizing as-printed deviations.
Yüzey İşlemi (Pürüzlülük):
- Tanım: The texture of the part’s surface, typically measured as Ra (average roughness).
- As-Printed Surface Finish: The surface finish of AM parts is inherently rougher than machined surfaces due to the layer-by-layer process and partially melted powder particles adhering to the surface.
- Top Surfaces: Generally smoother.
- Side Walls (Vertical): Show layer lines, Ra typically 8-15 µm for Al alloys via LPBF.
- Up-facing/Down-facing Surfaces: Down-facing (supported) surfaces are usually rougher due to support structure interaction, potentially Ra > 20 µm.
- Internal Channels: Can be difficult to smooth and often retain a higher roughness.
- Factors Influencing Roughness: Layer thickness, laser parameters, powder particle size distribution, build orientation, support removal method.
- Yüzey İşleminin İyileştirilmesi: Various post-processing techniques are available:
- Abrasive Blasting (Bead/Sand): Common for removing loose powder and providing a uniform matte finish (Ra ~ 5-10 µm).
- Tumbling/Mass Finishing: Vibratory finishing with media can smooth surfaces and round edges, particularly for smaller parts (Ra ~ 1-5 µm).
- CNC İşleme: Provides the best surface finish on specific features (Ra < 1 µm possible).
- Parlatma: Manual or automated polishing for achieving mirror-like finishes where required (e.g., optical interfaces), though less common for standard housings.
- Chemical Polishing/Etching: Can smooth surfaces but requires careful control.
Expectations for Space Housings:
- Non-critical Surfaces: As-printed or bead-blasted finishes are often acceptable for general surfaces, focusing on cleanliness and uniformity.
- Mating Interfaces: Usually require post-machining for flatness, tolerance, and a smoother finish (e.g., Ra 1.6-3.2 µm) to ensure proper sealing or thermal contact.
- Thermal Surfaces: Radiating surfaces may benefit from specific coatings rather than just smoothness, while conductive interfaces need to be flat and smooth (often machined).
- RF Applications: Surface finish can impact performance at high frequencies; specific Ra values may be required, often achieved through machining or polishing specific areas.
Achieving the necessary precision for satellite electronics housings involves a combination of optimized AM printing parameters and targeted post-processing. Clear communication between the design engineers and the AM service provider regarding critical dimensions, tolerances, and surface finish requirements is essential for a successful outcome. Partnering with providers like Met3dp, who understand the nuances of material properties, printing processes, and post-processing, ensures components meet the stringent demands of the aerospace industry.
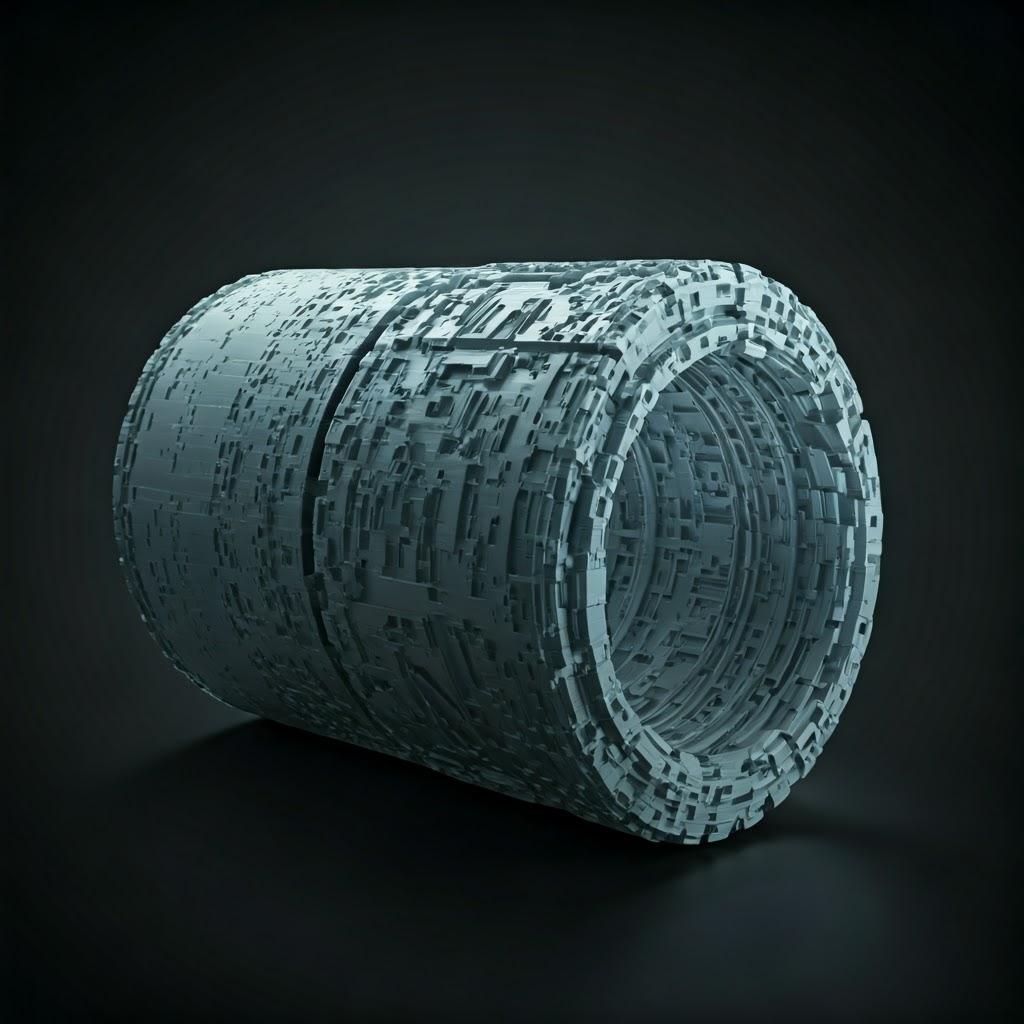
Post-Processing: Essential Finishing Steps for Space-Grade Aluminum Housings
Parts produced via metal additive manufacturing, especially those destined for the demanding environment of space, are rarely ready for use immediately after emerging from the printer. A series of post-processing steps are typically required to achieve the final desired properties, tolerances, surface finish, and cleanliness. Understanding these steps is crucial for planning production timelines and costs for 3D printed aluminum electronics housings.
Common Post-Processing Steps for AM Aluminum (AlSi10Mg, Scalmalloy®) Housings:
- Toz Giderme:
- Süreç: Removing unfused metal powder trapped within the part, especially in internal channels, complex geometries, or lattice structures. This is typically done using compressed air, vibration, and specialized powder handling systems immediately after the build finishes, often within the machine’s controlled atmosphere.
- Importance: Ensures part cleanliness, prevents loose powder from interfering with electronics or mechanisms, and allows for powder recycling. Designs must incorporate powder escape holes (DfAM principle).
- Meydan okumak: Complete removal from very intricate internal features can be difficult and requires careful design and process control.
- Stres Giderici:
- Süreç: A heat treatment cycle applied to the part while still attached to the build plate (or shortly after removal). The part is heated to a moderate temperature (e.g., ~300°C for AlSi10Mg) and held for a specific duration before slow cooling.
- Importance: Relieves internal stresses built up during the rapid heating and cooling cycles of the layer-by-layer printing process. This prevents warping or distortion when the part is removed from the build plate and during subsequent machining or thermal treatments.
- Gereklilik: Almost always required for aluminum AM parts, especially those with complex geometries or large footprints.
- Yapı Plakasından Parça Çıkarma:
- Süreç: Separating the printed housing(s) from the metal build plate they were fused to during printing. Common methods include:
- Tel EDM (Elektrik Deşarjlı İşleme): Precise method, minimal force applied to the part, good surface finish at the cut. Often preferred for delicate or high-value parts.
- Şerit Testere: Faster and potentially cheaper but less precise and imparts more mechanical stress. Requires careful handling.
- Consideration: The removal method can influence downstream finishing requirements near the base of the part.
- Süreç: Separating the printed housing(s) from the metal build plate they were fused to during printing. Common methods include:
- Destek Yapısının Kaldırılması:
- Süreç: Manually or mechanically removing the support structures generated during the build to prop up overhangs and stabilize the part. Supports are typically designed with weaker connection points to the main part. Removal involves breaking, cutting, or machining them away.
- Importance: Supports are necessary for printing but are not part of the final component.
- Meydan okumak: Can be labor-intensive. Removal can leave witness marks or rough areas (“nubs”) on the part surface that require further finishing (grinding, blending, machining). DfAM aims to minimize support dependency.
- Heat Treatment (Solutionizing & Aging – e.g., T6):
- Süreç: A multi-stage thermal process to significantly improve the mechanical properties (strength, hardness, ductility) of the aluminum alloy.
- Çözüm Tedavisi: Heating to a high temperature (near the alloy’s melting point, e.g., ~530°C for AlSi10Mg) to dissolve alloying elements into a solid solution.
- Söndürme: Rapid cooling (usually in water) to trap the elements in solution.
- Aging (Artificial): Reheating to a lower temperature (e.g., ~160-180°C) for an extended period allows controlled precipitation of strengthening phases.
- Importance: Crucial for achieving the desired mechanical performance specified in datasheets, especially for load-bearing applications. AlSi10Mg and Scalmalloy® derive much of their strength from proper heat treatment.
- Consideration: Heat treatment can cause slight dimensional changes (warpage), which must be accounted for, potentially requiring machining sonra heat treatment for final tolerances. Requires accurately controlled furnace atmospheres.
- Süreç: A multi-stage thermal process to significantly improve the mechanical properties (strength, hardness, ductility) of the aluminum alloy.
- Machining (CNC):
- Süreç: Using traditional subtractive machining (milling, drilling, turning) to achieve tight tolerances, specific surface finishes, or features that are difficult or impossible to create accurately with AM alone.
- Uygulama: Creating flat mating surfaces, precise hole diameters and locations, threaded holes (tapping), smooth sealing grooves, achieving GD&T requirements.
- Gereklilik: Frequently required for critical interfaces on aerospace components. Parts are designed with extra material (‘machining stock’) in these areas.
- Yüzey İşlemi:
- Süreç: Improving the surface texture and appearance. As discussed previously, this can include:
- Boncuk Kumlama / Kumlama: Cleaning, deburring, uniform matte finish.
- Tumbling / Mass Finishing: Smoothing, edge rounding.
- Parlatma: Achieving smooth, reflective surfaces.
- Grinding/Blending: Smoothing areas where supports were removed.
- Importance: Aesthetics, preparation for coatings, meeting specific Ra requirements.
- Süreç: Improving the surface texture and appearance. As discussed previously, this can include:
- Temizlik:
- Süreç: Final cleaning steps to remove any residual powder, machining fluids, fingerprints, or other contaminants before inspection, coating, or assembly. May involve ultrasonic cleaning, solvent wiping, or specialized aerospace cleaning procedures.
- Importance: Critical for space applications where outgassing and contamination control are paramount.
- Inspection and Quality Control (QC):
- Süreç: Verifying dimensions (using CMMs, scanners), checking for defects (visual, CT scanning for internal flaws), material property verification (if required), and ensuring all specifications are met.
- Importance: Essential for ensuring the reliability and safety of space-grade hardware.
- Surface Treatments / Coatings (Optional):
- Süreç: Applying specific coatings for enhanced properties.
- Anodizing: Improves corrosion resistance and wear resistance, can provide thermal control properties (varying emissivity/absorptivity).
- Chromate Conversion Coating (e.g., Alodine): Corrosion protection and paint/primer adhesion.
- Painting/Priming: For thermal control, corrosion protection, or identification.
- Plating (e.g., Nickel, Gold): For conductivity, solderability, specific RF properties.
- Importance: Tailoring the housing’s surface properties to the specific requirements of the space environment and electronic interfaces.
- Süreç: Applying specific coatings for enhanced properties.
The specific sequence and necessity of these steps depend heavily on the housing design, material (AlSi10Mg vs. Scalmalloy® may have slightly different heat treat cycles), and application requirements. Collaborating with a full-service provider capable of managing the entire workflow from printing through post-processing and inspection is highly advantageous for aerospace projects.
Mitigating Risks: Common Challenges in 3D Printing Housings and Effective Solutions
While metal AM offers transformative potential, it’s not without its challenges, especially when producing high-stakes components like satellite electronics housings. Awareness of potential issues and implementing mitigation strategies throughout the design and manufacturing process is key to success.
Common Challenges & Mitigation Strategies:
Meydan Okuma | Açıklama | Hafifletme Stratejileri |
---|---|---|
Warping and Distortion | Parts deform during or after printing due to residual thermal stresses from rapid heating/cooling cycles. | Tasarım: Use DfAM (ribs, gradual transitions), minimize large flat areas. <br> Süreç: Robust stress relief heat treatment önce removing from build plate. Optimize print parameters (laser power, scan strategy). Ensure stable build plate heating. |
Support Structure Issues | Difficult/costly removal, damage to part surface during removal, inability to remove supports from internal areas. | Tasarım: Minimize overhangs (<45°), use self-supporting geometries (chamfers, fillets), design accessible supports, orient part to reduce support needs. <br> Süreç: Optimize support design (density, connection points). Use precise removal methods (EDM). Plan for surface finishing post-removal. |
Gözeneklilik | Small voids or gas bubbles trapped within the printed material, potentially reducing strength and fatigue life. | Süreç: Use high-quality, dry powder (like those manufactured by Met3dp using advanced atomization). Optimize print parameters (energy density, scan speed, layer thickness). Ensure proper inert gas atmosphere (Argon/Nitrogen) in build chamber. <br> Post-Process: Hot Isostatic Pressing (HIP) can close internal pores but adds cost/time. |
Çatlama | Cracks appearing during printing or cooling, particularly in alloys susceptible to hot tearing (less common in AlSi10Mg/Scalmalloy® than some other Al alloys). | Tasarım: Avoid sharp internal corners, manage thermal gradients. <br> Süreç: Optimize print parameters, use build plate heating, select appropriate alloys (AlSi10Mg/Scalmalloy® have good printability). Perform stress relief promptly. |
Kötü Yüzey İşlemi | Rough surfaces, especially on down-facing areas or where supports were attached. | Tasarım: Orient part for best finish on critical surfaces. <br> Süreç: Optimize parameters (layer thickness, laser settings). <br> Post-Process: Implement appropriate surface finishing steps (blasting, tumbling, machining, polishing). |
Dimensional Inaccuracy | Part dimensions deviate significantly from the CAD model beyond acceptable tolerances. | Tasarım: Account for shrinkage/distortion, add machining stock for critical dimensions. <br> Süreç: Calibrate machine regularly. Optimize parameters. Perform stress relief. Control thermal environment. <br> Post-Process: Use CNC machining for critical tolerances. |
Incomplete Powder Removal | Residual powder trapped in internal channels or complex features. | Tasarım: Include powder escape holes in strategic locations. Avoid overly complex, inaccessible internal voids. <br> Süreç: Use effective depowdering techniques (vibration, compressed air). Implement thorough cleaning protocols. |
Malzeme Özelliği Değişimi | Inconsistent mechanical properties within a part or between builds. | Süreç: Use consistent, high-quality powder batches. Maintain strict process control (parameters, atmosphere). Ensure proper and consistent heat treatment cycles. Implement regular testing and qualification procedures. |
Cost Overruns | Underestimating the cost of printing, post-processing, or iteration. | Planning: Obtain detailed quotes covering all steps (printing, heat treatment, machining, finishing, inspection). Use DfAM to optimize for cost (reduce supports, minimize post-processing). Factor in potential prototyping/iteration costs. |
Uzun Teslim Süreleri | Delays due to machine availability, complex post-processing, or unexpected issues. | Planning: Work with suppliers offering sufficient capacity. Clearly define requirements upfront. Optimize design for manufacturability. Build buffer time into project schedules. Explore partnerships with vertically integrated providers. |
Sayfalara Aktar
The Role of the AM Partner:
Mitigating these risks heavily relies on the expertise and capabilities of the chosen additive manufacturing service provider. Key factors include:
- Süreç Kontrolü: Robust quality management systems (e.g., AS9100 certification for aerospace), well-maintained and calibrated equipment.
- Malzeme Uzmanlığı: Deep understanding of AlSi10Mg and Scalmalloy® behavior during printing and post-processing. Access to high-quality, characterized powders, potentially through direct relationships with powder manufacturers like Met3dp.
- Engineering Support: Ability to provide DfAM feedback and collaborate on design optimization.
- Comprehensive Services: In-house capabilities for essential post-processing steps (heat treatment, machining, finishing, inspection) streamline the workflow and reduce handoffs.
- Tecrübe: Proven track record with similar aerospace components and materials.
By proactively addressing these potential challenges through smart design, rigorous process control, and collaboration with capable partners, aerospace companies can confidently leverage the benefits of metal AM for producing reliable, high-performance satellite electronics housings.
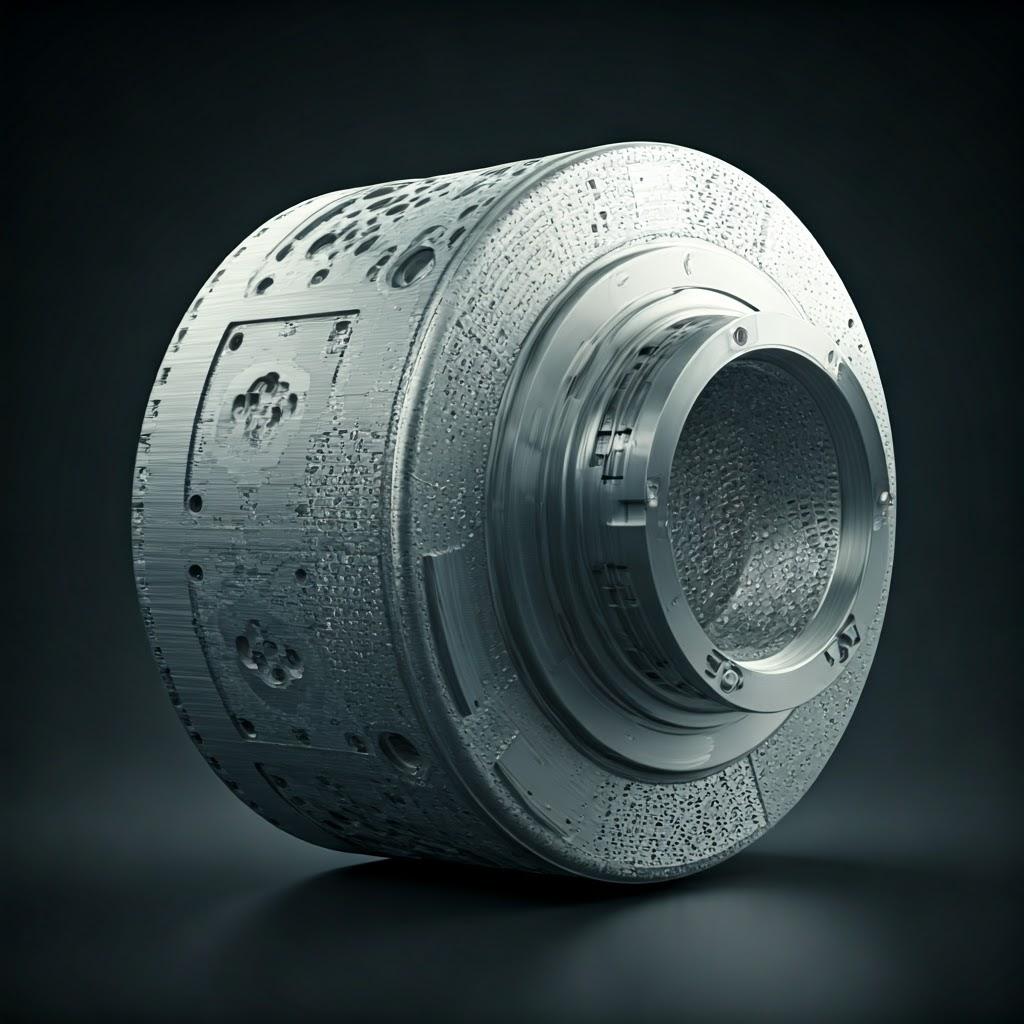
Supplier Selection: Choosing the Right Metal Additive Manufacturing Partner for Aerospace Components
Selecting the appropriate additive manufacturing partner is as critical as the design and material choice when producing high-reliability components like satellite electronics housings. The right supplier acts as more than just a manufacturer; they are a crucial partner in ensuring the component meets stringent aerospace requirements for quality, performance, and traceability. Procurement managers and engineering teams should evaluate potential suppliers based on a comprehensive set of criteria.
Key Evaluation Criteria for AM Suppliers:
- Aerospace Experience and Certifications:
- Requirement: Proven track record manufacturing components for the aerospace industry. Familiarity with space-grade requirements, documentation standards, and quality expectations.
- Indicators:
- AS9100 Certification: The standard for Quality Management Systems in the Aviation, Space, and Defense industries. This is often a non-negotiable requirement.
- Case Studies/References: Demonstrable experience with similar projects, materials (AlSi10Mg, Scalmalloy®), and component types (housings, brackets, RF components).
- ITAR Registration: Necessary if dealing with defense-related or export-controlled projects (primarily relevant for US-based projects/suppliers).
- Technical Expertise and Engineering Support:
- Requirement: Deep understanding of the chosen AM process (e.g., LPBF), materials science (specifically aluminum alloys for space), and DfAM principles. Ability to provide constructive feedback on designs for printability, performance optimization, and cost reduction.
- Indicators:
- In-house Engineering Team: Availability of experienced AM engineers and materials scientists.
- DfAM Consultation Services: Offering support during the design phase.
- Process Simulation Capabilities: Ability to simulate the build process to predict and mitigate risks like distortion.
- Material Capabilities and Quality Control:
- Requirement: Ability to process the specific aluminum alloy required (AlSi10Mg, Scalmalloy®) with validated parameters. Stringent control over powder quality, handling, storage, and traceability.
- Indicators:
- Validated Parameter Sets: Documented and proven machine parameters for the specific alloy ensuring consistent material properties.
- Powder Management: Robust procedures for powder sourcing, testing (e.g., chemistry, particle size distribution), handling (inert atmosphere), storage, and recycling/traceability. Companies like Met3dp, which manufacture their own high-quality powders using advanced gas atomization and PREP technologies, often have an advantage in material control.
- Material Certifications: Providing material test certificates with shipped parts.
- Equipment and Facilities:
- Requirement: State-of-the-art, well-maintained AM equipment (printers) suitable for the required part size and material. Sufficient capacity to meet project timelines. Controlled manufacturing environment.
- Indicators:
- Machine Fleet: Number, type, and build volume of relevant metal AM systems (e.g., LPBF machines). Redundancy is a plus.
- Facility Standards: Cleanliness, environmental controls (humidity, temperature), safety protocols.
- Technology Adoption: Investment in current-generation technology for higher accuracy and reliability.
- Post-Processing Capabilities:
- Requirement: In-house or tightly managed external capabilities for all necessary post-processing steps identified earlier (stress relief, heat treatment, support removal, CNC machining, surface finishing, cleaning).
- Indicators:
- Integrated Services: Offering a “one-stop-shop” experience simplifies project management, improves quality control, and can reduce lead times.
- Specialized Equipment: Controlled atmosphere furnaces for heat treatment, precision CNC machines (5-axis), validated cleaning processes.
- Network Management: If outsourcing certain steps, robust procedures for managing and qualifying subcontractors.
- Quality Management System (QMS) and Inspection:
- Requirement: Comprehensive QMS beyond basic certification. Advanced inspection capabilities to verify part integrity and dimensional accuracy. Full traceability from powder to final part.
- Indicators:
- Detailed Inspection Reports: Providing thorough documentation with each shipment.
- Inspection Technologies: CMM (Coordinate Measuring Machines), 3D scanning, potentially NDT (Non-Destructive Testing) like CT scanning for internal defect analysis if required.
- Traceability: Lot tracking for powder batches, build logs, post-processing records.
- Communication and Project Management:
- Requirement: Clear, responsive communication. Dedicated points of contact. Proactive project management to ensure timelines are met.
- Indicators:
- Responsiveness: Timely replies to inquiries and requests for updates.
- Şeffaflık: Openness about capabilities, potential challenges, and project status.
- Defined Processes: Clear workflows for quoting, order processing, change management, and reporting.
Finding Potential Suppliers:
- Industry Directories & Networks: Online databases, aerospace manufacturing associations.
- Trade Shows & Conferences: Events focused on additive manufacturing and aerospace.
- Tavsiyeler: Consulting with peers or industry experts.
- Direct Inquiry: Reaching out to established providers known for quality, such as Met3dp, whose comprehensive solutions span printers, advanced metal powders, and application development services.
Thorough supplier vetting is crucial for aerospace procurement. Issuing Requests for Quotation (RFQs) with detailed specifications, conducting site audits (if feasible), and potentially starting with smaller qualification builds can help ensure the chosen partner meets all technical and quality requirements for producing mission-critical satellite components.
Cost & Timeline: Understanding Cost Drivers and Lead Times for 3D Printed Housings
While additive manufacturing offers significant advantages, understanding the factors influencing cost and lead time is essential for effective project planning and budgeting when producing 3D printed satellite electronics housings. Both can vary considerably based on numerous factors.
Key Cost Drivers:
- Part Volume and Mass:
- Etki: Larger, heavier parts consume more material (especially expensive alloys like Scalmalloy®) and take longer to print, directly increasing costs.
- Hafifletme: DfAM techniques like topology optimization and lattice structures are key to minimizing volume while meeting requirements.
- Malzeme Türü:
- Etki: The cost of aerospace-grade metal powders varies significantly. Scalmalloy® is considerably more expensive than AlSi10Mg due to the inclusion of Scandium. Titanium alloys (if considered) are typically more expensive than aluminum.
- Hafifletme: Select the most cost-effective material that meets all performance requirements. Don’t over-specify if AlSi10Mg suffices.
- Part Complexity and Design:
- Etki: While AM handles complexity well, certain features can increase costs:
- Extensive Support Structures: Increase print time, material consumption (supports are often the same expensive material), and post-processing labor for removal and finishing.
- Very Thin Walls/Features: May require slower printing parameters for stability and accuracy.
- Trapped Internal Powder: Designs requiring complex internal cleaning procedures add labor cost.
- Hafifletme: Optimize the design using DfAM to minimize supports, ensure self-draining features, and avoid features below stable printing limits.
- Etki: While AM handles complexity well, certain features can increase costs:
- Print Time:
- Etki: Machine time is a major cost component. Print time depends on part volume, height (number of layers), exposure parameters, and the number of parts nested onto a single build plate.
- Hafifletme: Optimize part orientation for Z-height. Nest multiple parts efficiently onto the build plate (supplier responsibility, but design can influence nesting).
- İşlem Sonrası Gereksinimler:
- Etki: Each post-processing step (stress relief, heat treatment, support removal, machining, finishing, inspection) adds cost (labor, equipment time, consumables). Tight tolerances requiring extensive CNC machining significantly increase costs.
- Hafifletme: Clearly define requirements. Specify tight tolerances and fine surface finishes sadece where functionally necessary. Design parts to minimize support and machining needs.
- Quality Assurance and Inspection:
- Etki: Stringent aerospace inspection requirements (CMM, NDT like CT scanning, detailed reporting) add significant cost compared to industrial parts.
- Hafifletme: Clearly specify necessary inspection levels based on part criticality. Discuss requirements with the supplier upfront.
- Sipariş Hacmi:
- Etki: While AM is good for low volumes, there are still setup costs (build preparation, machine setup). Per-part costs tend decrease slightly with larger batches due to better build plate utilization and amortized setup, though the effect is less pronounced than with traditional tooling-based manufacturing.
- Hafifletme: Consolidate orders where possible, but AM remains cost-effective even for single units or very small runs compared to tooling costs for injection molding or casting.
Typical Lead Times:
Lead time refers to the total time from order placement to part delivery. For 3D printed aluminum space housings, this can range from a few weeks to several monthsbağlı olarak:
- Supplier Queue and Capacity: High demand or limited machine availability can increase waiting times.
- Print Time: Can range from hours to several days depending on part size, complexity, and build plate nesting.
- Post-Processing Complexity: Heat treatment cycles take time (hours to days). CNC machining setup and runtime can add days. Complex finishing or coating adds further time. Waiting for external processing steps adds transit and queue time.
- Inspection Requirements: Detailed inspection and documentation generation take time.
- Prototyping/Iterations: If design validation or multiple iterations are needed, the overall project timeline extends.
- Parça Karmaşıklığı: Highly complex parts requiring intricate support removal or internal cleaning will take longer.
Lead Time Breakdown (Example – Highly Variable):
- Quoting & Order Processing: 1-5 days
- Build Preparation & Scheduling: 1-7 days
- Baskı: 1-5 days
- Stress Relief & Powder Removal: 1-2 gün
- Part Removal & Support Removal: 1-3 gün
- Heat Treatment (e.g., T6): 1-3 days (including furnace time and cooling)
- CNC İşleme: 2-10 days (depending on complexity and shop loading)
- Surface Finishing/Cleaning: 1-3 gün
- Inspection & Documentation: 1-5 days
- Nakliye: 1-5 days (depending on location)
Total Estimated Lead Time: ~2 weeks (very simple, minimal post-pro) to 8+ weeks (complex, extensive post-pro, high demand).
Strategies for Managing Cost & Lead Time:
- Engage Suppliers Early: Discuss design concepts for manufacturability feedback.
- Açık RFQ: Provide detailed drawings, specifications (tolerances, finish, inspection), and material requirements.
- Optimize Design (DfAM): Reduce mass, minimize supports, plan for post-processing efficiently.
- Realistic Specifications: Avoid over-tolerancing or unnecessary finishing requirements.
- Open Communication: Maintain dialogue with the supplier regarding timelines and potential issues.
By understanding these drivers, engineers and procurement managers can better estimate budgets, plan project timelines, and work collaboratively with AM partners to achieve cost-effective and timely delivery of high-quality satellite electronics housings.
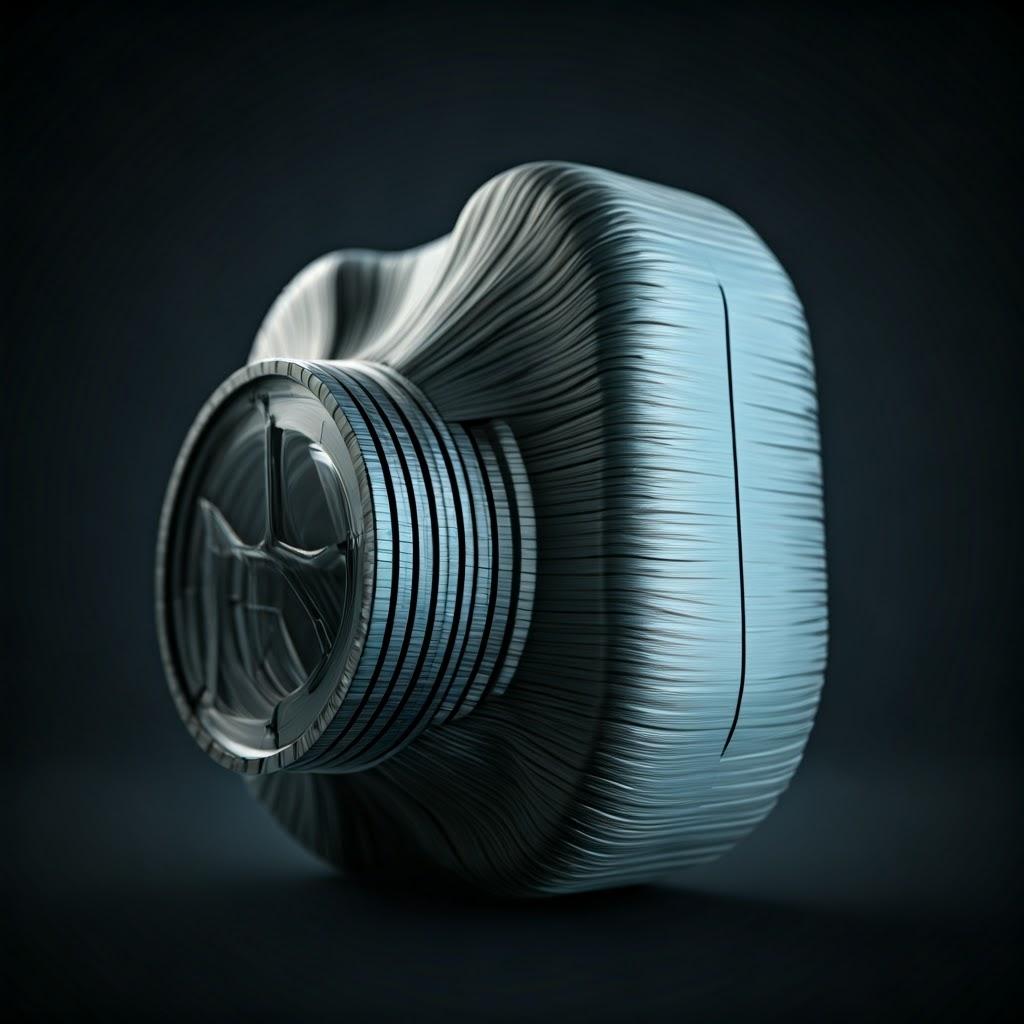
FAQ: Frequently Asked Questions about 3D Printed Space Electronics Housings
Here are some common questions regarding the use of additive manufacturing for satellite electronics housings using aluminum alloys:
- Is 3D printed aluminum (AlSi10Mg / Scalmalloy®) strong enough for space launch conditions?
- Cevap: Yes, when processed correctly. Both AlSi10Mg and especially Scalmalloy®, after appropriate heat treatment (like T6), exhibit mechanical properties suitable for handling the significant vibration, shock, and acoustic loads experienced during satellite launch. Scalmalloy® offers strength comparable to some titanium grades at a lower density, making it exceptionally well-suited for demanding structural applications. Proper design validation using FEA simulation based on accurate AM material properties, combined with rigorous qualification testing (vibration, shock tests), is essential to ensure survivability. Partnering with suppliers experienced in aerospace qualification is key.
- What are the typical surface finish limitations, and how do they impact thermal or RF performance?
- Cevap: As-printed surfaces using LPBF typically have a roughness (Ra) of 8-15 µm on vertical walls and potentially higher on supported surfaces. While often acceptable for general structure, critical interfaces usually require post-processing.
- Thermal: For conductive interfaces, a smooth, flat surface (achieved via machining, Ra < 3.2 µm or better) is needed for good thermal contact. For radiative surfaces, specific coatings (anodizing, paints with known emissivity/absorptivity) applied after potentially basic smoothing (like bead blasting) are often more critical than the underlying Ra value itself.
- RF Performance: At higher frequencies, surface roughness can increase signal loss (conductor loss). Depending on the frequency and application (e.g., waveguides, filters integrated into the housing), machining or polishing specific RF-critical surfaces to achieve a lower Ra might be necessary. Simulation and testing are crucial to determine the required surface finish.
- Cevap: As-printed surfaces using LPBF typically have a roughness (Ra) of 8-15 µm on vertical walls and potentially higher on supported surfaces. While often acceptable for general structure, critical interfaces usually require post-processing.
- How does the cost of a 3D printed aluminum housing compare to one CNC machined from a solid block?
- Cevap: It depends heavily on complexity, volume, and material buy-to-fly ratio.
- For highly complex geometries: AM is often daha uygun maliyetli because complexity is less of a cost driver than with machining. Machining complex shapes requires intricate setups, specialized tooling, and significant machine time, leading to high costs.
- For simple, blocky designs: Traditional CNC machining might be cheaper, especially at higher volumes, as machine time per part can be lower once set up.
- Malzeme Atıkları: AM has a much lower buy-to-fly ratio (less material waste) than machining from billet, which is a significant cost factor for expensive materials like Scalmalloy® or titanium. AM becomes more competitive as material cost increases or part complexity rises.
- Weight Savings: While not a direct manufacturing cost, the potential for significant weight reduction via AM (topology optimization) can lead to substantial launch cost savings, making the total mission cost lower even if the per-part manufacturing cost is slightly higher.
- A detailed cost analysis comparing optimized AM designs with machined alternatives, including material utilization and post-processing, is needed for a definitive comparison on a case-by-case basis.
- Cevap: It depends heavily on complexity, volume, and material buy-to-fly ratio.
Conclusion: The Future of Satellite Components: Leveraging Aluminum AM for Performance and Innovation
The journey into space demands continuous innovation, pushing the boundaries of material science, design engineering, and manufacturing technology. For satellite electronics housings, metal additive manufacturing using advanced aluminum alloys like AlSi10Mg and the high-performance Scalmalloy® represents a significant leap forward. As we’ve explored, AM is not merely an alternative production method; it’s an enabler of next-generation satellite design.
The ability to radically reduce weight through topology optimization and lattice structures directly translates into lower launch costs and greater payload capacity – critical factors in the economics of space exploration and commercialization. The design freedom inherent in AM allows engineers to integrate complex thermal management features, consolidate assemblies, and create bespoke enclosures perfectly tailored to the mission’s needs, improving reliability and performance in the harsh environment of space. Furthermore, the accelerated prototyping and production cycles offered by AM fuel faster innovation, allowing satellite developers to iterate designs and deploy new capabilities more rapidly than ever before.
While challenges in precision, post-processing, and process control exist, they are being actively addressed through advancements in DfAM methodologies, machine technology, material science, and robust quality management systems. Choosing the right manufacturing partner—one with aerospace expertise, validated processes, comprehensive capabilities, and a commitment to quality, like Met3dp—is paramount to successfully navigating these challenges and realizing the full potential of AM. Met3dp’s foundation in producing high-quality metal powders coupled with their expertise in additive manufacturing equipment and application development positions them as a valuable partner in this technological transformation.
For engineers and procurement managers in the aerospace sector, embracing metal additive manufacturing for components like electronics housings is no longer just an option; it’s becoming a strategic imperative. By leveraging the unique advantages of aluminum AM, the industry can continue to build lighter, more capable, and more cost-effective satellites, driving the future of communication, observation, and exploration beyond Earth.
Paylaş
MET3DP Technology Co, LTD, merkezi Qingdao, Çin'de bulunan lider bir katmanlı üretim çözümleri sağlayıcısıdır. Şirketimiz, endüstriyel uygulamalar için 3D baskı ekipmanları ve yüksek performanslı metal tozları konusunda uzmanlaşmıştır.
İşletmeniz için en iyi fiyatı ve özelleştirilmiş Çözümü almak için sorgulayın!
İlgili Makaleler
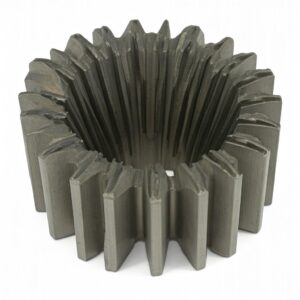
Yüksek Performanslı Nozul Kanat Segmentleri: Metal 3D Baskı ile Türbin Verimliliğinde Devrim
Daha Fazla Oku "Met3DP Hakkında
Son Güncelleme
Bizim Ürünümüz
BİZE ULAŞIN
Herhangi bir sorunuz var mı? Bize şimdi mesaj gönderin! Mesajınızı aldıktan sonra tüm ekibimizle talebinize hizmet edeceğiz.
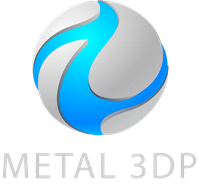
3D Baskı ve Katmanlı Üretim için Metal Tozları