3D Printed Power Housings for UAV Electronics
İçindekiler
Introduction: Revolutionizing UAV Design with 3D Printed Power Housings
The Unmanned Aerial Vehicle (UAV), or drone, industry is experiencing exponential growth, transforming sectors from defense and surveillance to agriculture, logistics, and infrastructure inspection. At the heart of every UAV lies a complex system of electronics, batteries, and power management components. Protecting these vital systems from harsh environmental conditions, electromagnetic interference (EMI), and physical impacts is paramount for mission success and operational reliability. Traditionally, housings for these sensitive electronics have been manufactured using methods like CNC machining from billet materials or injection molding for high-volume applications. However, the unique demands of the UAV sector – particularly the relentless drive for reduced weight, increased payload capacityve gelişmiş performans – are paving the way for innovative manufacturing solutions.
Girmek metal katkılı üretim (AM), commonly known as metal 3D baskı. This transformative technology is rapidly moving beyond prototyping into the production of end-use parts, and UAV power supply housings represent a prime application area. A power supply housing is more than just a box; it’s a critical subsystem component that must:
- Protect Sensitive Electronics: Shield internal components (power distribution boards, battery management systems, converters) from moisture, dust, vibration, shock, and temperature fluctuations encountered during flight.
- Ensure Structural Integrity: Provide robust support and mounting points for internal components and the overall UAV airframe, often contributing to the vehicle’s structural integrity.
- Manage Thermal Loads: Effectively dissipate heat generated by power electronics to prevent overheating and ensure optimal performance and longevity.
- Minimize Weight: Contribute as little weight as possible to maximize flight time, maneuverability, and payload capacity – a critical factor in UAV design.
- Potentially Offer EMI Shielding: Protect sensitive electronics from external electromagnetic interference and prevent the power system from interfering with other onboard sensors or communication systems.
Metal 3D printing offers a unique capability to address these multifaceted requirements in ways traditional manufacturing often cannot. By building parts layer by layer directly from digital models, AM enables the creation of highly complex, lightweight, and customized drone electronics enclosures optimized for specific mission profiles and environmental challenges. Companies specializing in additive manufacturing for aerospace are leveraging materials like aluminum alloys and stainless steels to produce durable, high-performance özel İHA parçaları, including power housings, that meet the stringent demands of this dynamic industry. This introduction explores how metal AM is not just an alternative but often a superior method for manufacturing the next generation of UAV power supply housings, driving innovation and performance across the sector. Understanding the capabilities of advanced metal 3D printing introduction technologies is becoming crucial for engineers and procurement managers aiming to stay competitive.
Applications: Where are 3D Printed UAV Power Housings Taking Flight?
The versatility of metal additive manufacturing allows for the production of power supply housings tailored to a wide spectrum of UAV platforms and operational environments. The ability to customize designs rapidly and cost-effectively for specific needs makes 3D printing particularly attractive across diverse UAV applications. Procurement managers seeking reliable commercial drone suppliers and engineers designing cutting-edge systems are increasingly turning to AM for these critical components.
Here are some key areas where 3D printed metal power housings are making a significant impact:
- Defense and Surveillance:
- Uygulamalar: Tactical reconnaissance UAVs, loitering munitions, border patrol drones, intelligence gathering platforms.
- Housing Requirements: Extreme durability, high reliability in harsh environments (temperature extremes, high G-forces), potential EMI shielding, low observability (specific coatings/finishes), lightweight for extended mission endurance.
- AM Advantage: Production of robust, complex housings with integrated features, often using aerospace-grade materials like specialized aluminum or titanium alloys (though AlSi10Mg and 316L are common starting points). Ability to create custom designs for specific payloads and mission requirements on shorter timelines than traditional tooling. Essential for defense UAV parts.
- Aerospace and Exploration:
- Uygulamalar: High-altitude long-endurance (HALE) UAVs, research drones, atmospheric sampling platforms.
- Housing Requirements: Extreme lightweighting is critical, high thermal stability for varying altitudes, resistance to UV radiation and potential atmospheric contaminants, stringent quality control and material traceability.
- AM Advantage: Topology optimization and generative design tools, enabled by AM, allow for significant weight reduction without compromising structural integrity. Aerospace 3D printing techniques enable complex internal cooling channels and consolidation of multiple parts into a single printed component, reducing assembly complexity and potential failure points.
- Commercial and Industrial Inspection:
- Uygulamalar: Infrastructure inspection (bridges, power lines, wind turbines), precision agriculture (crop monitoring), mapping and surveying, environmental monitoring.
- Housing Requirements: Good environmental sealing (IP rating), resistance to dust and moisture, durability for frequent deployment and retrieval, cost-effectiveness for fleet operations. Thermal management is important for drones operating close to structures or in direct sunlight.
- AM Advantage: Ability to produce durable housings with integrated seals or mounting features. Faster iteration for design improvements based on field feedback. Cost-effective production for low-to-mid volumes typical of specialized industrial drone manufacturing. Materials like 316L offer excellent corrosion resistance for coastal or industrial environments.
- Logistics and Delivery:
- Uygulamalar: Package delivery drones, medical supply transport UAVs.
- Housing Requirements: Lightweight to maximize payload, robust construction to withstand potential impacts during landing/delivery, reliable thermal management for potentially high-power systems, ease of access for maintenance.
- AM Advantage: Optimization for weight and strength. Potential for integrated features like battery locking mechanisms or status indicators. Rapid manufacturing allows quicker deployment of new drone designs or adaptations for different cargo types.
- Specialized Applications:
- Uygulamalar: Search and rescue drones, filmmaking UAVs, scientific research platforms.
- Housing Requirements: Highly customized designs based on unique sensor payloads or operating conditions, potentially requiring specific vibration damping or thermal insulation properties.
- AM Advantage: Unparalleled design freedom to create bespoke housings perfectly matched to the specific equipment and mission profile, enabling innovation in niche drone component use cases.
Across all these applications, the function of the 3D printed power housing remains critical: protect the power electronics, manage heat, contribute to structural integrity, and do so at the lowest possible weight. Metal AM provides the tools to achieve this balance effectively.
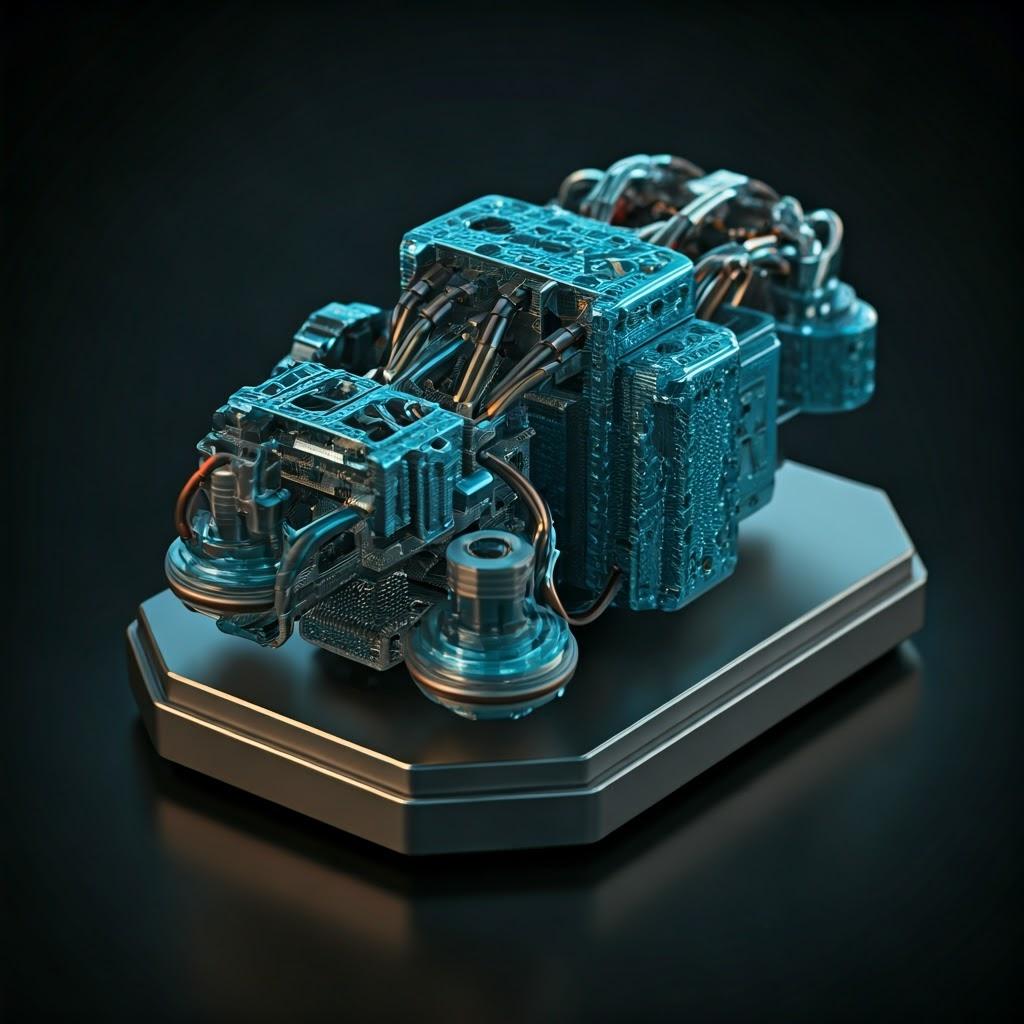
The Additive Advantage: Why Metal 3D Printing for UAV Power Housings?
While traditional manufacturing methods like CNC machining and casting have served the industry well, metal additive manufacturing presents compelling advantages specifically tailored to the challenges of producing high-performance UAV power supply housings. Comparing traditional vs additive manufacturing reveals why engineers and procurement managers are increasingly adopting metal AM.
Key Advantages of Metal AM for UAV Power Housings:
- Unmatched Design Freedom & Complexity:
- Meydan okumak: Power housings often require intricate internal features for component mounting, cable routing, airflow management, and heat dissipation. Traditional methods struggle with complex internal geometries or require multi-part assemblies.
- AM Solution: AM builds parts layer-by-layer, enabling the creation of highly complex, monolithic structures. This allows for:
- Konformal Soğutma Kanalları: Integrating cooling channels that precisely follow the contours of heat-generating components for vastly improved thermal management.
- Internal Lattices: Utilizing complex lattice structures to reduce weight significantly while maintaining structural rigidity.
- Integrated Features: Designing mounting bosses, snap-fits, cable channels, and other features directly into the housing, reducing part count and assembly time.
- This capability is crucial for producing complex drone parts.
- Significant Weight Reduction (Lightweighting):
- Meydan okumak: Every gram saved on a UAV translates to longer flight times or increased payload capacity. Machining often leaves excess material, and designing for casting requires draft angles and uniform wall thicknesses that may not be weight-optimal.
- AM Solution: AM excels at creating lightweight structures through:
- Topology Optimization: Software algorithms determine the most efficient material distribution to withstand specific loads, removing unnecessary material.
- Generative Design: AI-driven design processes create organic, highly optimized shapes that are often impossible to manufacture traditionally.
- Thin Walls & Complex Geometries: Printing thinner, yet structurally sound walls and intricate internal supports.
- This focus on creating lightweight UAV components is a primary driver for AM adoption.
- Parça Konsolidasyonu:
- Meydan okumak: Traditional housings might consist of multiple machined or sheet metal parts fastened together, increasing weight, assembly time, and potential points of failure (e.g., seals between parts).
- AM Solution: Complex assemblies can often be redesigned and printed as a single, monolithic component. This reduces:
- Assembly labor and time.
- Need for fasteners and seals.
- Overall weight.
- Potential leak paths or failure points.
- Hızlı Prototipleme ve Yineleme:
- Meydan okumak: Developing and testing new UAV designs requires quick turnaround times for components. Traditional tooling (molds, fixtures) can be time-consuming and expensive to create and modify.
- AM Solution: AM requires no specific tooling. Design modifications can be implemented digitally and a new part printed relatively quickly (often within days). This accelerates the design-build-test cycle, enabling faster innovation and product development – a core benefit for rapid prototyping aerospace İhtiyaçlar.
- Customization and Low-Volume Production:
- Meydan okumak: UAVs are often produced in lower volumes than mass-market consumer goods, and customization for specific missions or payloads is common. Setting up traditional manufacturing lines for low volumes can be cost-prohibitive.
- AM Solution: AM is economically viable for producing unique or low-to-mid volume batches of parts. It allows for mass customization, where each housing can potentially be tailored without significant cost overhead associated with tooling changes. This supports on-demand parts manufacturing.
- Malzeme Çeşitliliği:
- Meydan okumak: Different applications require different material properties (e.g., thermal conductivity, corrosion resistance, strength-to-weight ratio).
- AM Solution: A growing range of metal powders, including high-performance aluminum alloys, stainless steels, titanium, and superalloys, are available for AM processes, allowing selection of the optimal material for the specific housing requirements.
While AM might have considerations regarding surface finish or initial part cost compared to high-volume traditional methods, the strategic advantages in design freedom, weight reduction, and speed-to-market often outweigh these factors for critical components like UAV power supply housings.
Material Selection: Choosing the Right Metal Powder for Optimal Performance
Selecting the appropriate material is fundamental to the success of any 3D printed component, especially for demanding applications like UAV power supply housings. The choice directly impacts weight, thermal performance, durability, environmental resistance, and cost. For UAV housings, two commonly recommended and highly effective metal powders are AlSi10Mg ve 316L Paslanmaz Çelik. Understanding their properties is key for engineers making design decisions and procurement managers sourcing materials or services.
Leading providers like Met3dp, utilizing advanced powder manufacturing techniques such as Vacuum Induction Melting Gas Atomization (VIGA) and Plasma Rotating Electrode Process (PREP), ensure the availability of high-quality, spherical metal powders crucial for achieving dense, reliable prints with superior mechanical properties.
1. Aluminum Alloy (AlSi10Mg): The Lightweight Champion
- Açıklama: AlSi10Mg is a widely used aluminum alloy known for its excellent combination of low density, good mechanical properties (strength and hardness), and castability/printability. It’s essentially a casting alloy adapted for additive manufacturing processes like Selective Laser Melting (SLM) and Direct Metal Laser Sintering (DMLS).
- Key Properties & Benefits for UAV Housings:
- Low Density (~2.67 g/cm³): This is the primary advantage. Significantly lighter than steel or titanium, directly contributing to UAV weight reduction, longer flight times, and increased payload capacity.
- Good Thermal Conductivity (~130-150 W/m·K): Effectively dissipates heat generated by power electronics, crucial for preventing overheating and ensuring component reliability. Enables designs with integrated heat sinks or cooling fins.
- İyi Güç-Ağırlık Oranı: Offers sufficient strength and stiffness for housing applications after appropriate heat treatment (e.g., T6).
- Mükemmel Basılabilirlik: Flows well and solidifies predictably during printing, allowing for complex geometries and fine features.
- Korozyon Direnci: Offers decent corrosion resistance, which can be further enhanced with surface treatments like anodizing or painting.
- Düşünceler:
- Lower absolute strength and fatigue resistance compared to steel or titanium.
- Requires heat treatment post-printing to achieve optimal mechanical properties.
- Can be more challenging to weld or machine post-print compared to some other alloys.
- Ideal Applications: Most UAV power housings where weight is the primary concern, and operating environments are not extremely corrosive. Defense, commercial, logistics, and inspection drones often benefit greatly from AlSi10Mg properties.
Table: AlSi10Mg Key Properties (Typical Values after Heat Treatment)
Mülkiyet | Tipik Değer | Birim | Significance for UAV Housings |
---|---|---|---|
Yoğunluk | ~2.67 | g/cm³ | Critical for Lightweighting |
Tensile Strength (UTS) | 270 – 350+ | MPa | Structural integrity |
Akma Dayanımı (0,2%) | 190 – 250+ | MPa | Resistance to permanent deformation |
Kopma Uzaması | 3 – 10+ | % | Ductility, resistance to fracture |
Sertlik | 90 – 120+ | HBW | Wear and scratch resistance |
Termal İletkenlik | ~130 – 150 | W/(m-K) | Excellent for Heat Dissipation |
Max Operating Temp. | ~150 (dependent on load/time) | °C | Suitable for typical electronic heat loads |
Sayfalara Aktar
2. 316L Stainless Steel: The Durable Workhorse
- Açıklama: 316L is an austenitic stainless steel alloy containing chromium, nickel, and molybdenum. The ‘L’ denotes low carbon content, improving weldability and reducing sensitization (chromium carbide precipitation) during thermal cycles like printing. It is renowned for its excellent corrosion resistance and good mechanical properties.
- Key Properties & Benefits for UAV Housings:
- Mükemmel Korozyon Direnci: Highly resistant to rust and corrosion, even in marine or industrial environments, thanks to its chromium and molybdenum content. Ideal for UAVs operating near saltwater, in polluted areas, or requiring frequent cleaning/sterilization (e.g., medical delivery).
- Good Strength and Ductility: Offers higher strength and significantly better ductility (toughness) compared to AlSi10Mg, making it more resistant to impact and fatigue.
- Good Weldability & Machinability: Generally easier to post-process (weld, machine, polish) than aluminum alloys.
- Biocompatibility (for specific grades/processing): While less relevant for power housings, 316L is widely used in medical implants, indicating its inert nature.
- Düşünceler:
- Significantly Higher Density (~7.99 g/cm³): Nearly three times denser than AlSi10Mg, resulting in a much heavier housing if dimensions are identical. Design optimization (thin walls, lattices) is crucial to mitigate the weight penalty.
- Lower Thermal Conductivity (~16 W/m·K): Much less effective at dissipating heat compared to aluminum. Designs may require more aggressive cooling strategies (e.g., larger fins, forced airflow) if thermal management is critical.
- Ideal Applications: UAVs operating in harsh, corrosive environments (marine, coastal, industrial). Applications where extreme durability, impact resistance, or ease of sterilization are paramount, and where the weight penalty can be tolerated or offset through clever design. Essential for durable 316L stainless steel UAV Bileşenler.
Table: 316L Key Properties (Typical Values – Annealed/As-Printed)
Mülkiyet | Tipik Değer | Birim | Significance for UAV Housings |
---|---|---|---|
Yoğunluk | ~7.99 | g/cm³ | Weight Consideration (Requires Design Offset) |
Tensile Strength (UTS) | 500 – 650+ | MPa | High Structural Integrity |
Akma Dayanımı (0,2%) | 200 – 300+ | MPa | Good resistance to deformation |
Kopma Uzaması | 40 – 60+ | % | High Toughness and Impact Resistance |
Sertlik | ~150 – 200 | HBW | Good Durability |
Termal İletkenlik | ~16 | W/(m-K) | Poor Heat Dissipation (Requires Design Focus) |
Max Operating Temp. | ~425 – 870 | °C | High-temperature capability (rarely limiting factor) |
Sayfalara Aktar
Choosing Between AlSi10Mg and 316L:
The decision hinges on the primary requirements:
- Prioritize Weight Savings & Heat Dissipation? Seçin AlSi10Mg.
- Prioritize Corrosion Resistance & Durability? Seçin 316L, but be prepared to actively design for weight reduction and manage thermal performance.
Consulting with an experienced metal AM service provider, like Met3dp, who understands both the materials and the intricacies of UAV applications, is crucial. Their expertise in metal powder selection guide principles and access to high-purity powders ensures that the chosen material performs optimally in the final printed housing. Partnering with a provider knowledgeable in aerospace grade materials and their specific application nuances is key to success.
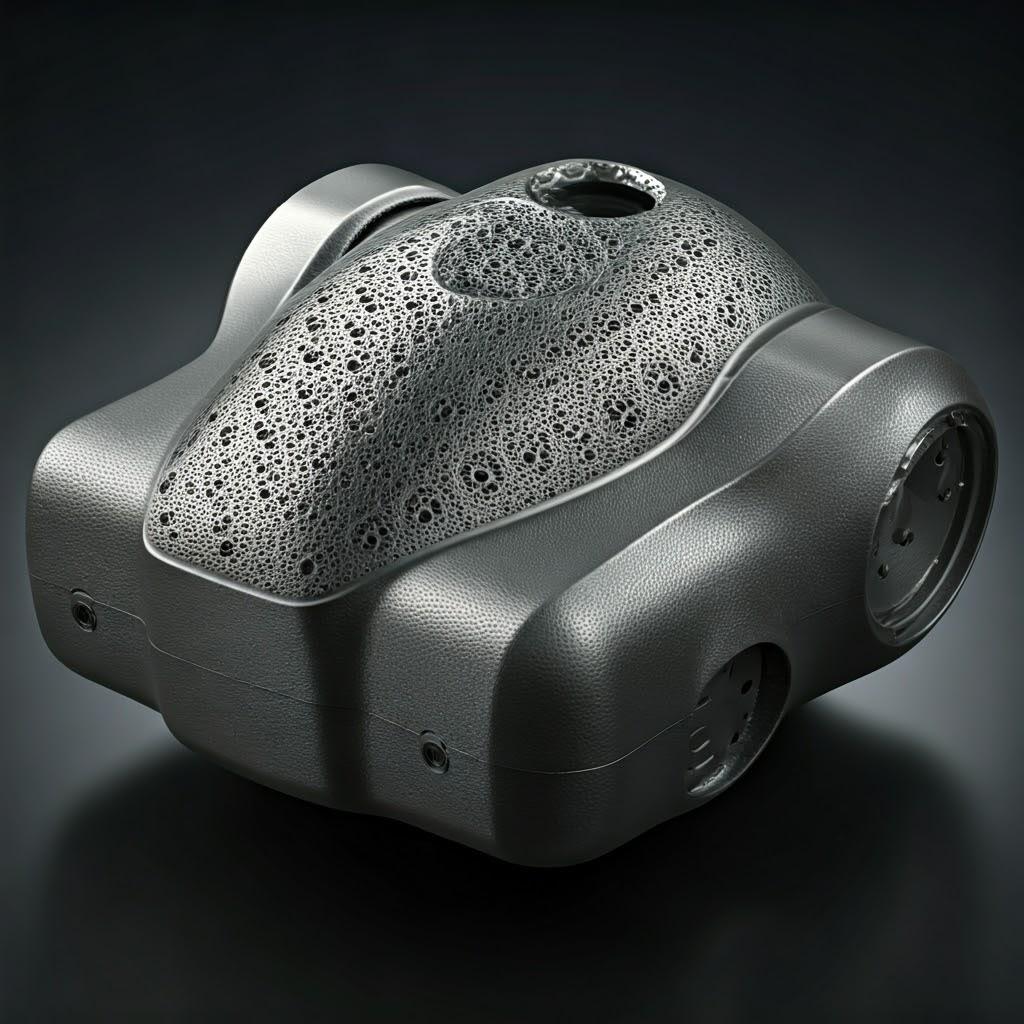
Design for Additive Manufacturing (DfAM): Optimizing Housings for Printability and Function
Simply replicating a design intended for CNC machining or casting into a 3D printable format rarely unlocks the full potential of additive manufacturing. To truly leverage the benefits of metal AM for UAV power supply housings – particularly weight reduction and enhanced thermal management – engineers must embrace Katmanlı Üretim Tasarımı (DfAM) principles. DfAM involves designing parts with the specific capabilities and constraints of the chosen AM process (like SLM, DMLS, or SEBM) in mind, right from the conceptual stage. Applying effective DfAM principles is crucial for optimizing performance, ensuring printability, minimizing post-processing efforts, and ultimately reducing costs.
Here are key DfAM considerations for UAV power supply housings:
- Leverage Topology Optimization and Generative Design:
- Concept: These computational tools help create highly efficient, often organic-looking structures by distributing material only where it’s needed to support defined loads and constraints.
- Uygulama: Define load cases (vibration, mounting points, internal component weight) and functional requirements (heat dissipation areas, access ports). Let the software generate lightweight yet strong designs that would be impossible or impractical to machine. This is paramount for topology optimization UAV Bileşenler.
- Benefit: Significant weight savings (often 20-50% or more compared to traditional designs) without compromising structural integrity.
- Integrate Functional Features:
- Concept: Consolidate multiple functions or components into a single printed part.
- Uygulama: Design integrated mounting bosses for PCBs, channels for cable routing, fixtures for connectors, and even elements of heat sinks or cold plates directly into the housing structure. Consider designing snap-fits or integrated closures to reduce the need for separate fasteners.
- Benefit: Reduced part count, simplified assembly, lower weight, and potentially improved reliability by eliminating joints and interfaces.
- Optimize for Thermal Management:
- Concept: Use AM’s geometric freedom to create superior cooling solutions.
- Uygulama:
- Konformal Soğutma Kanalları: Design internal channels that precisely follow the shape of heat-generating components (e.g., processors, power regulators) for direct and efficient heat extraction, potentially using liquid cooling or airflow.
- Optimized Heat Sink Fins: Create complex fin geometries (pin fins, lattices) with high surface area-to-volume ratios for improved passive air cooling.
- Material Choice Integration: Combine DfAM with material selection (e.g., using highly conductive AlSi10Mg) for maximum thermal performance.
- Benefit: Improved electronic component reliability and performance, potential for higher power density within the UAV. Integrating cooling channels effectively is a major AM advantage.
- Design for Printability (Minimize Supports & Stress):
- Concept: Orient the part and design features to reduce the need for support structures, which add print time, material cost, and post-processing effort. Minimize thermal stresses that can cause warping.
- Uygulama:
- Kendini Destekleyen Açılar: Design overhangs and internal channels with angles typically greater than 45 degrees from the horizontal plane to avoid the need for supports.
- Part Orientation: Choose a build orientation that minimizes the volume of required supports, especially on critical or hard-to-reach surfaces. Consider how orientation affects residual stress accumulation.
- Stress Reduction Features: Incorporate rounded corners instead of sharp edges, and design for uniform heat distribution where possible. Some AM processes, like Electron Beam Melting (EBM/SEBM) offered by providers like Met3dp, operate at higher temperatures, which can reduce residual stress but may have implications for surface finish and feature resolution compared to laser-based systems explored on their baskı yöntemleri sayfası.
- Benefit: Faster print times, lower material consumption, easier and cheaper post-processing (minimizing support structures), improved dimensional accuracy due to reduced stress.
- Consider Wall Thickness and Feature Size:
- Concept: AM processes have limitations on minimum printable wall thickness and feature resolution.
- Uygulama: Ensure walls are thick enough to be reliably printed and handle expected loads (typically >0.4-0.5mm for metal PBF). Design small features (holes, pins) within the resolution capabilities of the chosen machine and process. Factor in potential shrinkage or distortion.
- Benefit: Ensures part printability and structural soundness. Adhering to guidelines for wall thickness metal AM prevents print failures.
- Plan for Post-Processing:
- Concept: Design with downstream processes in mind.
- Uygulama: Include extra material (machining stock) on critical surfaces requiring tight tolerances or specific finishes. Ensure accessibility for support removal tools and CNC machining heads. Design features that facilitate handling and inspection.
- Benefit: Smoother workflow, reduced post-processing time and cost, ensures final part requirements can be met.
By incorporating these DfAM strategies, engineers can design UAV power supply housings that are not only lighter and perform better thermally but are also more efficient and cost-effective to produce using additive manufacturing. Collaboration with experienced AM service providers during the design phase can provide valuable insights and ensure optimal results.
Precision Matters: Tolerances, Surface Finish, and Accuracy in Printed Housings
While metal AM offers incredible design freedom, it’s essential for engineers and procurement managers to understand the levels of precision achievable directly from the printer and how this impacts the final UAV power supply housing. Factors like metal 3D printing tolerances, surface finish (Ra)ve genel olarak dimensional accuracy AM are critical for ensuring proper fit, assembly, sealing, and function.
Tolerances:
- As-Printed Tolerances: For typical metal Powder Bed Fusion (PBF) processes like SLM and DMLS, standard achievable tolerances are often in the range of:
- ± 0.1 mm to ± 0.2 mm for smaller features (e.g., up to 20-50 mm).
- ± 0.1% to ± 0.2% of the nominal dimension for larger features.
- Factors Influencing Tolerances: Machine calibration, laser spot size, layer thickness, material properties, thermal stresses during the build, part geometry, and support strategy all play a role.
- Implications for Housings: As-printed tolerances are often sufficient for general housing dimensions, non-critical mounting points, and internal clearance features. However, interfaces requiring precise fits (e.g., bearing seats, mating surfaces for sealing, precise connector locations) may require tighter control.
Surface Finish (Roughness – Ra):
- As-Printed Surface Finish: The surface finish of metal AM parts is inherently rougher than machined surfaces due to the layer-by-layer process and partially melted powder particles adhering to the surface.
- Vertical/Side Walls: Typically range from Ra 6 µm to Ra 15 µm (or higher), depending on the process, material, and parameters.
- Top Surfaces: Generally smoother.
- Down-Facing/Supported Surfaces: Often the roughest, showing witness marks from support structures.
- Factors Influencing Roughness: Layer thickness, particle size distribution of the powder, laser/beam energy input, and build orientation.
- Implications for Housings:
- Sealing: As-printed surfaces may not be suitable for creating effective environmental seals (e.g., IP ratings) without appropriate gasket design or post-processing.
- Thermal Contact: Surface roughness can increase thermal resistance at interfaces (e.g., between the housing and a heat-generating component).
- Estetik: May require smoothing if visual appearance is critical.
- Flow Resistance: Rough internal channels could slightly impede airflow or coolant flow compared to smooth channels.
Boyutsal Doğruluk:
- Tanım: Refers to how closely the final part conforms to the intended dimensions specified in the CAD model. It’s influenced by tolerances but also by potential warping or distortion.
- Causes of Inaccuracy: Residual thermal stresses built up during the heating and cooling cycles of printing can cause parts to warp or distort, especially for large, flat, or asymmetric designs. Inadequate support structures can exacerbate this.
- Hafifletme: Proper build simulation, optimized orientation, effective support strategies, stress-relief heat treatments, and process control are crucial for achieving tight tolerances and minimizing distortion.
Achieving Higher Precision:
When as-printed tolerances or surface finish are insufficient for specific features on the UAV power housing, post-processing becomes necessary:
- Post-Machining: Critical features requiring tighter tolerances (e.g., ±0.01 mm to ±0.05 mm) or smoother surface finishes (e.g., Ra < 1.6 µm) are typically achieved through post-machining 3D parts using CNC milling or turning. This is common for mating interfaces, sealing grooves, bearing bores, and precise alignment features. DfAM should account for adding machining stock in these areas.
- Yüzey İşlemleri: Processes like bead blasting, tumbling, polishing, or electro-polishing can improve the overall surface finish, remove loose particles, and enhance aesthetics or prepare surfaces for coatings.
Understanding the inherent precision of metal AM and planning for necessary quality control aerospace parts inspection and post-processing steps are vital for successfully implementing 3D printed power housings in demanding UAV applications. Clear communication of critical dimensions and tolerances with the AM service provider is essential.
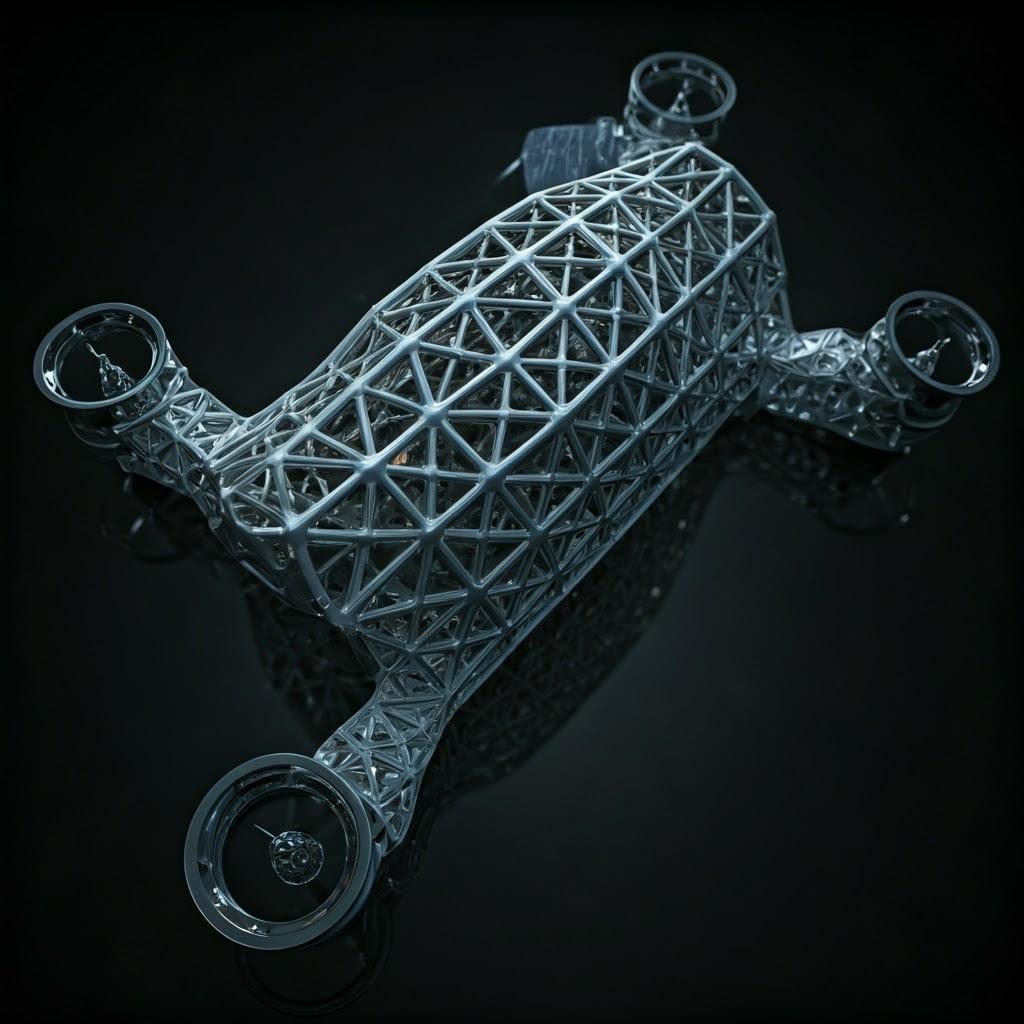
Beyond the Print: Essential Post-Processing Steps for UAV Housings
The journey of a metal 3D printed UAV power supply housing doesn’t end when the printer stops. Several crucial post-processing steps are typically required to transform the raw printed part into a functional, reliable component ready for assembly. Understanding these steps is vital for procurement managers evaluating quotes and engineers designing the overall workflow. Common surface finishing options and treatments ensure the part meets performance and durability requirements.
Key Post-Processing Steps:
- Stres Giderici / Isıl İşlem:
- Amacımız: To relieve internal stresses built up during the rapid heating and cooling cycles of the printing process. These stresses can lead to distortion, cracking, or premature failure if not addressed. Heat treatment also helps homogenize the material’s microstructure and achieve the desired final mechanical properties (strength, hardness, ductility).
- Süreç: Parts are heated in a controlled atmosphere furnace to specific temperatures and durations, followed by controlled cooling. The exact cycle (heat treatment metal AM) depends heavily on the material (e.g., solution treatment and aging for AlSi10Mg, annealing or stress relief for 316L) and application requirements.
- Gereklilik: Almost always mandatory for critical structural components like UAV housings to ensure dimensional stability and mechanical performance.
- Yapı Plakasından Parça Çıkarma:
- Amacımız: To detach the printed part(s) from the metal base plate they were built upon.
- Süreç: Typically done using wire EDM (Electrical Discharge Machining) or a bandsaw. Care must be taken to avoid damaging the parts.
- Destek Yapısının Kaldırılması:
- Amacımız: To remove the temporary support structures required during printing for overhangs and complex features.
- Süreç: Can range from simple manual break-off for accessible supports to more complex support removal 3D printing methods involving hand tools, machining, or specialized tooling, especially for internal channels or intricate geometries. DfAM plays a huge role in minimizing the difficulty and cost of this step.
- Düşünceler: Can be labor-intensive and time-consuming. May leave witness marks on the surface that require further finishing.
- CNC İşleme:
- Amacımız: To achieve tighter tolerances, critical dimensions, flat sealing surfaces, threaded holes, or smoother surface finishes on specific features that cannot be met by the as-printed part.
- Süreç: Using traditional CNC milling or turning centers to precisely machine designated areas of the 3D printed part. Requires careful fixture design to hold the complex geometry securely. Often provided as part of CNC machining services by comprehensive AM providers.
- Gereklilik: Frequently required for interfaces, mounting points, and sealing surfaces on UAV power housings.
- Surface Finishing & Cleaning:
- Amacımız: To improve surface roughness, remove loose powder particles, enhance aesthetics, or prepare the surface for coating.
- Processes:
- Bead Blasting/Sand Blasting: Propels media against the surface to create a uniform matte finish, remove loosely adhering powder, and potentially improve fatigue life (shot peening).
- Tumbling/Vibratory Finishing: Uses abrasive media in a rotating or vibrating drum to smooth surfaces and deburr edges, particularly effective for batches of smaller parts.
- Parlatma: Manual or automated polishing for achieving very smooth, reflective surfaces (less common for internal housings unless required for specific sealing or thermal reasons).
- Temizlik: Thorough cleaning to remove any residual powder, machining fluids, or contaminants before assembly or coating.
- Coating / Surface Treatment (Optional but common):
- Amacımız: To enhance specific properties like corrosion resistance, wear resistance, electrical insulation, or EMI shielding.
- Processes for AlSi10Mg: Anodizing (improves corrosion/wear resistance, provides color options), Chromate Conversion Coating (corrosion resistance, primer for paint), Painting/Powder Coating.
- Processes for 316L: Passivation (enhances natural corrosion resistance by removing free iron), Electropolishing (smooths and improves corrosion resistance), specialized coatings (e.g., PVD/CVD for wear). Passivation stainless steel is a common step.
- Gereklilik: Depends on the operating environment and specific functional requirements of the coating 3D printed parts.
- Inspection and Quality Control:
- Amacımız: To verify that the final part meets all dimensional, material, and functional specifications.
- Süreç: Dimensional inspection (CMM, 3D scanning), material testing (if required), visual inspection, NDT (Non-Destructive Testing like CT scanning for internal defects, if critical).
Each post-processing step adds time and cost to the overall production cycle. Effective DfAM and clear communication with the AM service provider about required final specifications are essential to optimize this workflow.
Navigating Challenges: Overcoming Hurdles in Metal AM for Housings
While metal additive manufacturing offers transformative potential for UAV power housings, it’s not without its challenges. Awareness of these potential hurdles allows engineers and procurement managers to work proactively with their AM partners to mitigate risks and ensure successful outcomes. Robust quality assurance metal AM protocols are essential throughout the process.
Common Challenges and How to Avoid Them:
- Warping and Distortion (Residual Stress):
- Meydan okumak: The intense, localized heating and rapid cooling inherent in PBF processes create internal stresses. These stresses can cause parts, especially large or asymmetric ones, to warp during printing or after removal from the build plate, leading to dimensional inaccuracy.
- Mitigation Strategies:
- Termal Simülasyon: Use simulation software during the design phase to predict stress accumulation and optimize part orientation and support strategies.
- Optimized Build Parameters: AM providers fine-tune parameters (laser power, scan speed) to minimize thermal gradients.
- Effective Support Structures: Strategically placed supports anchor the part and help dissipate heat.
- Appropriate Heat Treatment: Post-print stress relief cycles are crucial for relieving residual stress (residual stress management).
- Process Choice: Processes like EBM/SEBM operating at elevated temperatures can inherently reduce stress levels for some geometries and materials.
- Gözeneklilik:
- Meydan okumak: Small voids or pores can form within the printed material due to trapped gas or incomplete fusion between powder particles. Excessive porosity can compromise mechanical strength, fatigue life, and the ability of the housing to provide a hermetic seal.
- Mitigation Strategies:
- Yüksek Kaliteli Toz: Using powders with controlled particle size distribution, high sphericity, and low internal gas content (as produced by Met3dp’s advanced atomization) is fundamental.
- Optimized Print Parameters: Careful control over energy density (laser/beam power, speed, hatch spacing, layer thickness) is critical for full melting and consolidation.
- Kontrollü Atmosfer: Maintaining a high-purity inert gas atmosphere (Argon or Nitrogen) in the build chamber minimizes oxidation and gas pickup.
- Sıcak İzostatik Presleme (HIP): A post-processing step involving high temperature and pressure can close internal pores (adds significant cost, typically only for highly critical applications).
- NDT Inspection: CT scanning can detect internal porosity if required for critical metal 3D printing defects analysis.
- Support Removal Difficulty:
- Meydan okumak: Supports are necessary but add complexity. Removing them, especially from internal channels or intricate features within a housing, can be difficult, time-consuming, and risk damaging the part. Incomplete removal can impede fluid flow or trap debris.
- Mitigation Strategies:
- DfAM: Design for self-supporting angles (>45°) wherever possible. Use topology optimization or lattice structures that inherently minimize the need for supports. Design features for accessibility if supports are unavoidable.
- Optimized Support Structures: Use easily removable support types (e.g., thin-walled or perforated supports) where appropriate.
- Process Selection: Some processes might allow for different support strategies.
- Specialized Removal Techniques: Utilise appropriate tools, machining, or sometimes chemical etching (less common for these materials).
- Surface Finish Limitations:
- Meydan okumak: As discussed earlier, the as-printed surface finish can be rough, potentially impacting sealing, thermal contact, or aesthetics. Achieving very smooth finishes requires additional steps.
- Mitigation Strategies:
- Orientation Optimization: Print critical surfaces at orientations that naturally produce better finishes (e.g., vertical walls).
- Parameter Adjustment: Finer layer thicknesses can sometimes improve finish but increase print time.
- İşlem sonrası: Plan for necessary machining, blasting, tumbling, or polishing steps based on requirements.
- Achieving Consistent Material Properties:
- Meydan okumak: Ensuring consistent microstructure and mechanical properties throughout the part and between different builds requires tight process control.
- Mitigation Strategies:
- Strict Process Control: AM providers must maintain rigorous control over machine calibration, parameters, powder quality, and atmosphere.
- Standardized Procedures: Following established procedures for printing and heat treatment.
- Material Testing: Performing regular tensile tests or other characterization on witness coupons printed alongside parts.
- Reputable Suppliers: Partnering with experienced providers like Met3dp, who have deep materials science expertise and robust quality management systems, is crucial for mitigating many of these metal 3D printing challenges.
By understanding these potential challenges and implementing appropriate DfAM strategies, process controls, and post-processing steps, high-quality, reliable 3D printed metal UAV power supply housings can be consistently manufactured.
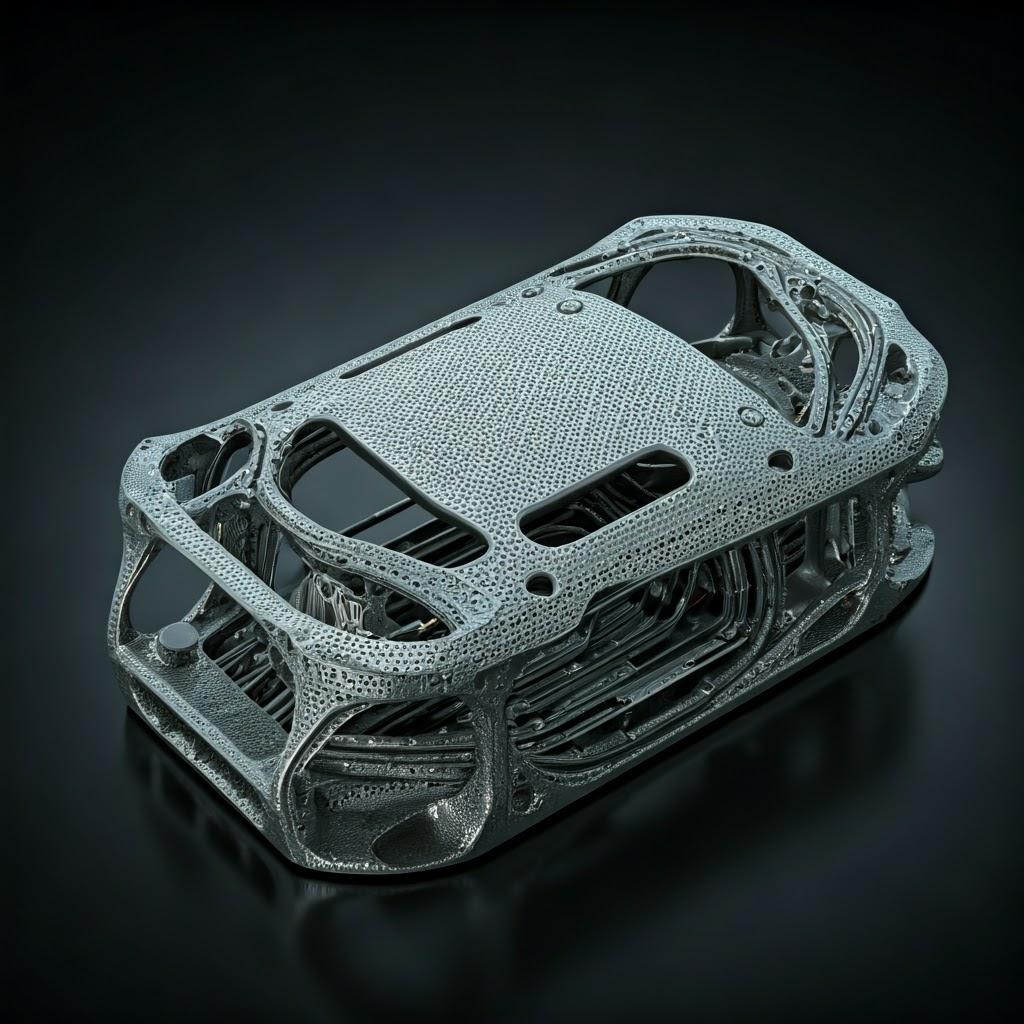
Supplier Selection: Finding Your Ideal Metal 3D Printing Partner for UAV Components
Choosing the right manufacturing partner is as critical as the design and material selection when producing high-stakes components like UAV power supply housings. The quality, reliability, and performance of the final part heavily depend on the expertise, equipment, and processes of your chosen metal AM service provider. For procurement managers and engineering teams venturing into additive manufacturing, choosing a 3D printing bureau requires careful evaluation based on several key criteria, especially when dealing with components for aerospace or demanding industrial applications.
Key Criteria for Evaluating Metal AM Suppliers:
- Industry Experience & Expertise:
- Requirement: Look for providers with proven experience in your specific industry (e.g., aerospace, defense, automotive, medical) and, ideally, with similar components (housings, enclosures, thermal management parts). They should understand the unique demands and quality expectations.
- Evaluation: Ask for case studies, references, and examples of past projects relevant to UAV components. Assess their team’s engineering depth and DfAM support capabilities. Do they understand the challenges of aerospace 3D printing supplier requirements?
- Certifications and Quality Management:
- Requirement: Robust quality management systems are non-negotiable for critical parts.
- ISO 9001: A fundamental certification indicating a structured approach to quality management.
- AS9100: Essential for aerospace applications, this standard builds upon ISO 9001 with additional requirements specific to the aerospace and defense industries (traceability, risk management, process control). An AS9100 certified supplier demonstrates a commitment to the highest quality standards.
- Evaluation: Verify current certifications. Inquire about their quality control procedures, material traceability protocols, inspection capabilities (CMM, NDT), and how they ensure process repeatability.
- Requirement: Robust quality management systems are non-negotiable for critical parts.
- Material Capabilities & Powder Quality:
- Requirement: The provider must offer the specific materials you need (e.g., AlSi10Mg, 316L, or potentially more advanced alloys) and have documented experience printing them successfully. Crucially, they should use high-quality metal powders.
- Evaluation: Confirm material availability and their experience level with those specific alloys. Ask about their powder sourcing and quality control measures. Companies like Met3dp, who manufacture their own high-purity spherical powders using advanced Gas Atomization and PREP technologies, offer an advantage in material consistency and quality control right from the source. Explore their range of Met3dp additive manufacturing solutions.
- Equipment & Technology:
- Requirement: The supplier should possess well-maintained, industrial-grade AM equipment suitable for your part’s size, complexity, and material. This includes not just printers but also necessary post-processing equipment (heat treatment ovens, CNC machines, finishing tools).
- Evaluation: Inquire about their specific printer models (e.g., SLM, DMLS, SEBM), build volume capabilities, and maintenance schedules. Understand their in-house post-processing capabilities versus what they outsource. Companies with integrated capabilities, like Met3dp’s offering of both printers (including SEBM with its unique advantages for certain applications) and powders, often provide a more streamlined workflow.
- Engineering & DfAM Support:
- Requirement: An ideal partner acts as more than just a print service. They should offer engineering support to help optimize your design for additive manufacturing (DfAM), suggest improvements for printability or performance, and troubleshoot potential issues.
- Evaluation: Discuss their DfAM support process. Are their engineers accessible? Can they provide feedback on your design files? Do they offer simulation services (thermal, stress)?
- Capacity & Lead Times:
- Requirement: Ensure the supplier has the capacity to meet your volume requirements within acceptable lead times, for both prototypes and potential production runs.
- Evaluation: Discuss their current capacity, typical lead times for similar projects, and their ability to scale production if needed. Request realistic additive manufacturing lead time estimates for your specific project.
- Communication & Project Management:
- Requirement: Clear, consistent communication and effective project management are vital for a smooth partnership.
- Evaluation: Assess their responsiveness during the quoting process. Understand who your primary point of contact will be and how progress will be reported.
Evaluating AM vendors thoroughly using these criteria will help you select a partner like Met3dp, who not only possesses the technical capabilities but also aligns with your quality standards and project goals, ultimately ensuring the successful production of reliable UAV power supply housings.
Understanding Costs and Timelines: Factors Influencing Production
One of the primary considerations for adopting any manufacturing technology is its economic viability and production speed. Understanding the key drivers behind metal 3D printing cost factors and typical lead times is crucial for budgeting, project planning, and comparing AM to traditional methods for UAV power supply housings.
Major Cost Drivers:
- Part Design & Complexity:
- Volume & Size: Larger parts consume more material and require longer machine time, directly increasing costs. The overall bounding box size affects how many parts can fit on a build plate.
- Karmaşıklık: While AM handles complexity well, highly intricate designs might require more extensive support structures, longer print times due to detailed scanning paths, and potentially more complex post-processing (especially support removal), impacting cost per part AM.
- Duvar Kalınlığı: Very thin walls can sometimes slow down print speeds for stability, while overly thick sections increase material usage and time.
- Malzeme Seçimi:
- Toz Maliyeti: The raw material cost varies significantly between different metal powders. Standard alloys like 316L or AlSi10Mg are generally less expensive than titanium alloys or specialized superalloys. Material cost 3D printing is a direct input.
- Material Usage: Factors like part volume and the amount of support material needed directly influence total material consumption.
- Makine Zamanı:
- Yapım süresi: This is often the largest cost component. It depends on the part height (number of layers), the area to be scanned per layer, the chosen layer thickness, and the machine’s scanning speed. Optimizing build plate utilization by nesting multiple parts can reduce per-part machine time costs.
- Machine Depreciation & Operating Costs: The high capital cost of industrial metal AM systems and their operational expenses (energy, inert gas, maintenance) are factored into machine hour rates.
- Labor & Post-Processing:
- Setup & Teardown: Labor involved in preparing the build file, setting up the machine, loading powder, and removing parts after printing.
- İşlem sonrası: This can be a significant cost factor. Costs include:
- Heat treatment cycles.
- Labor for support removal (can be substantial for complex parts).
- CNC machining for critical features (post-processing costs).
- Surface finishing (blasting, polishing).
- Quality inspection and certification.
- Quantity & Batch Size:
- Ölçek Ekonomileri: While AM is good for low volumes, there are still efficiencies gained with larger batches. Setup costs are amortized over more parts, and build plates can be utilized more efficiently. However, the per-part cost reduction is generally less dramatic than with high-volume methods like injection molding. Minimum order quantity 3D printing might apply, or per-part costs might be significantly higher for single prototypes.
Typical Lead Times:
Lead time is the duration from order confirmation to part shipment. For metal AM UAV housings, it typically involves several stages:
- Pre-Processing (1-3 days): Order review, build file preparation, scheduling.
- Printing (1-5+ days): Highly dependent on part height, volume, and number of parts per build. Complex or tall housings can take several days of continuous printing.
- Cooling & Depowdering (0.5-1 day): Allowing the build chamber and parts to cool safely, removing parts, and recovering unused powder.
- Post-Processing (2-10+ days): This stage often has the most variability.
- Heat Treatment: Typically 1-2 days (including furnace time and cooling).
- Support Removal/Machining: Can range from hours to several days depending on complexity.
- Surface Finishing/Coating: Adds further time depending on the process.
- Inspection: Depends on requirements.
- Shipping (Variable): Depends on location and chosen method.
Overall Lead Time: A typical range for a prototype metal AM UAV housing might be 1 to 3 weeks. Production batches might take longer, depending on quantity and required resources. It’s crucial to get specific additive manufacturing lead time estimates from your supplier based on your final design and requirements. While potentially longer than simple CNC machining for a single part, AM can be faster when considering complex geometries that would require multiple setups or tooling for traditional methods, especially during the iterative design phase. Understanding these UAV component pricing drivers and timelines helps set realistic expectations for projects.
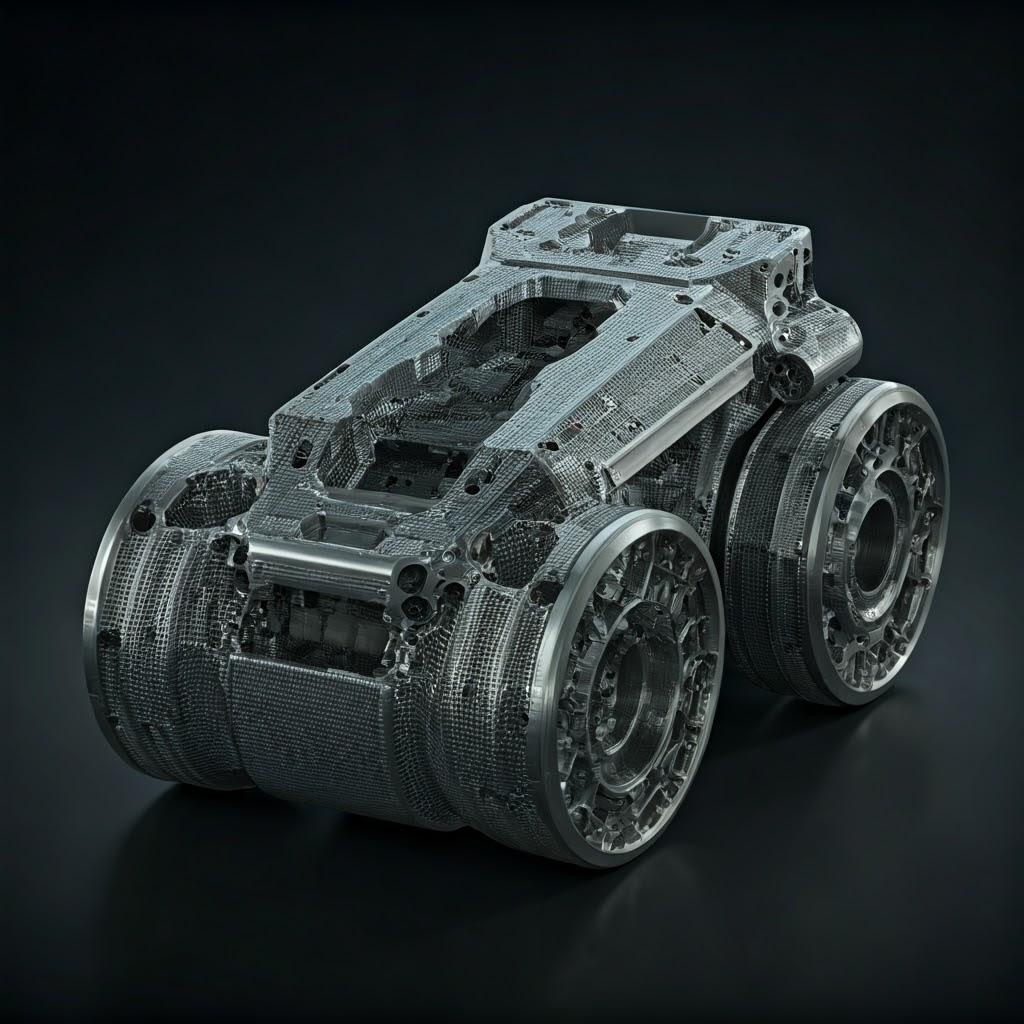
Sıkça Sorulan Sorular (SSS)
Here are answers to some common questions engineers and procurement managers have about using metal 3D printing for UAV power supply housings:
- Q1: How does the strength and durability of 3D printed metal housings compare to machined ones?
- A: When using appropriate materials (like AlSi10Mg or 316L) and proper post-processing (especially heat treatment), metal 3D printed parts can achieve mechanical properties (tensile strength, yield strength) that are comparable, and sometimes even superior in specific aspects (e.g., fatigue life due to fine microstructure), to wrought or cast materials typically used for machining. However, properties can be anisotropic (directionally dependent) based on build orientation. It’s crucial to design and process the part correctly to meet the required 3D printing durability. For instance, Met3dp’s high-quality powders and controlled printing processes aim to produce dense parts with excellent mechanical properties suitable for demanding applications.
- Q2: What are the typical lead times for prototype and production batches of UAV housings?
- A: As detailed previously, prototype lead times typically range from 1 to 3 weeks, depending on complexity and post-processing needs. For production batches, lead times depend heavily on the quantity, available machine capacity, and the extent of post-processing and quality assurance required. It could range from several weeks to a few months. It’s best to discuss specific additive manufacturing lead time requirements with your chosen supplier early in the process.
- Q3: Can complex internal features for cooling or cable routing be effectively printed?
- A: Yes, this is one of the key strengths of metal AM. Complex internal channels, conformal cooling passages, integrated cable conduits, and intricate lattice structures that are impossible or extremely difficult to create with traditional methods can be readily produced. However, DfAM principles must be applied to ensure channels are self-supporting where possible or designed for effective support removal and powder evacuation.
- Q4: What information is needed to get an accurate quote for a 3D printed housing?
- A: To provide an accurate quote, suppliers typically need:
- A 3D CAD model (STEP or STL format preferred).
- Material specification (e.g., AlSi10Mg, 316L).
- Quantity required (prototype vs. production).
- Critical dimensions, tolerances, and surface finish requirements clearly marked (ideally on a 2D drawing accompanying the 3D model).
- Post-processing requirements (heat treatment, specific machining, finishing, coating).
- Any required certifications or specific quality inspection procedures.
- Desired lead time.
- A: To provide an accurate quote, suppliers typically need:
- Q5: Is metal 3D printing more expensive than CNC machining for UAV housings?
- A: It depends. For simple, blocky designs easily machined from standard stock, CNC machining might be cheaper, especially at higher volumes. However, for highly complex geometries, parts requiring significant weight reduction through topology optimization, consolidated assemblies, or low-volume custom parts, metal AM often becomes more cost-effective. The true cost comparison AM vs CNC should consider the total cost of ownership, including potential savings from reduced weight, simplified assembly, and improved performance enabled by AM’s design freedom.
Conclusion: Elevating UAV Performance with Advanced Metal Additive Manufacturing
The demands placed on modern UAVs – longer flight times, heavier payloads, enhanced reliability, and operation in diverse environments – necessitate innovation in every component, including the critical power supply housing. As we’ve explored, metal additive manufacturing offers a powerful suite of tools to meet these challenges head-on.
By leveraging the benefits of metal AM recapped below, engineers and procurement managers can unlock significant advantages:
- Benzersiz Tasarım Özgürlüğü: Create complex, optimized geometries impossible with traditional methods.
- Significant Weight Reduction: Utilize topology optimization and lightweight materials like AlSi10Mg to maximize flight performance.
- Enhanced Thermal Management: Integrate conformal cooling channels and optimized heat sinks directly into the housing.
- Parça Konsolidasyonu: Reduce assembly complexity, weight, and potential failure points.
- Rapid Iteration & Customization: Accelerate development cycles and produce mission-specific components efficiently.
Choosing the right material, applying sound DfAM principles, understanding post-processing requirements, and selecting an experienced manufacturing partner are key to harnessing these benefits. Companies like Met3dp, with their deep expertise spanning advanced metal tozları, cutting-edge printing equipment (including SLM and SEBM systems), and comprehensive katkı üretim çözümleri, stand ready to support this digital manufacturing transformation. They bridge the gap between innovative design and reliable production, providing the high-quality materials and manufacturing expertise needed for critical UAV components.
Embracing metal additive manufacturing for UAV power supply housings is not just about adopting a new production technique; it’s about enabling the next generation of high-performance unmanned systems. Contact the Met3dp experts today to discuss your specific requirements and discover how their capabilities can elevate your UAV designs. Explore the possibilities further on their website: https://met3dp.com/.
Paylaş
MET3DP Technology Co, LTD, merkezi Qingdao, Çin'de bulunan lider bir katmanlı üretim çözümleri sağlayıcısıdır. Şirketimiz, endüstriyel uygulamalar için 3D baskı ekipmanları ve yüksek performanslı metal tozları konusunda uzmanlaşmıştır.
İşletmeniz için en iyi fiyatı ve özelleştirilmiş Çözümü almak için sorgulayın!
İlgili Makaleler
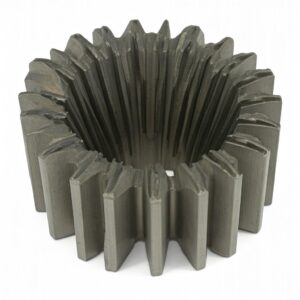
Yüksek Performanslı Nozul Kanat Segmentleri: Metal 3D Baskı ile Türbin Verimliliğinde Devrim
Daha Fazla Oku "Met3DP Hakkında
Son Güncelleme
Bizim Ürünümüz
BİZE ULAŞIN
Herhangi bir sorunuz var mı? Bize şimdi mesaj gönderin! Mesajınızı aldıktan sonra tüm ekibimizle talebinize hizmet edeceğiz.
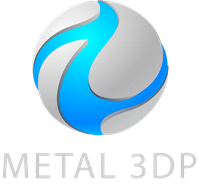
3D Baskı ve Katmanlı Üretim için Metal Tozları
ÜRÜN
cONTACT BİLGİLERİ
- Qingdao Şehri, Shandong, Çin
- [email protected]
- [email protected]
- +86 19116340731