Metal AM for Aerospace Sensor Mounts
İçindekiler
Introduction – The Critical Role of Aerospace Sensor Mounts and Metal Additive Manufacturing
Aerospace sensor mounts are indispensable components within modern aircraft and spacecraft, serving as the critical interface between sensitive sensors and the structural framework. These mounts must ensure the precise positioning, stability, and protection of vital instruments that collect data for navigation, environmental monitoring, safety systems, and mission-critical operations. The demanding operational environment of aerospace applications necessitates sensor mounts that exhibit exceptional strength-to-weight ratios, high durability, resistance to extreme temperatures and vibrations, and precise dimensional stability. Traditional manufacturing methods often present limitations in achieving these complex requirements efficiently and cost-effectively, particularly for intricate designs and low to medium production volumes. This is where metal additive manufacturing (AM), also known as metal 3D baskı, emerges as a transformative solution. Metal AM offers unparalleled design freedom, enabling the creation of optimized geometries with internal lattices and complex features that reduce weight while maintaining structural integrity. Furthermore, the ability to use high-performance metal powders, such as those offered by industry leaders like Metal3dp, allows for the fabrication of sensor mounts with tailored material properties to withstand the rigors of aerospace environments. By embracing metal 3D printing, aerospace engineers and procurement managers can unlock new possibilities in design innovation, performance enhancement, and streamlined supply chains. This blog post will explore the myriad benefits of utilizing metal AM for aerospace sensor mounts, delve into crucial design considerations, discuss the importance of material selection (highlighting Metal3dp’s advanced powder offerings), and provide guidance on choosing the right metal 3D printing service provider to ensure the successful realization of these critical components.
What are Aerospace Sensor Mounts Used For? Diverse Applications and Industry Needs
Aerospace sensor mounts play a pivotal role in a wide array of applications across the aviation and space industries. Their primary function is to securely and accurately position various types of sensors, ensuring they can effectively perform their intended tasks. The versatility of these mounts is evident in their deployment across numerous systems, including:
- Navigation Systems: Supporting inertial measurement units (IMUs), GPS antennas, and star trackers that provide crucial positional and orientational data for aircraft and spacecraft.
- Çevresel İzleme: Housing sensors that measure atmospheric conditions such as temperature, pressure, humidity, and air quality, as well as radiation levels.
- Safety Systems: Securing sensors for detecting ice formation, structural integrity monitoring, and proximity awareness to prevent collisions.
- Engine Monitoring: Mounting sensors that track engine performance parameters like temperature, pressure, vibration, and speed, contributing to safety and efficiency.
- Payload Instrumentation: Providing stable platforms for scientific instruments on satellites and spacecraft, ensuring accurate data collection for research and exploration.
- Communication Systems: Supporting antennas and transceivers that facilitate communication between aircraft/spacecraft and ground stations or other vehicles.
- Control Systems: Mounting sensors that provide feedback for flight control surfaces, ensuring precise and responsive aircraft maneuverability.
The specific requirements for an aerospace sensor mount vary significantly depending on the application. Factors such as the type and weight of the sensor, the operational environment (temperature extremes, vibration levels, exposure to corrosive elements), and the required precision of the sensor’s measurements all influence the design and material selection. Industries benefiting from advanced aerospace sensor mount solutions include:
- Commercial Aviation: For passenger and cargo aircraft requiring reliable navigation, safety, and environmental control systems.
- Military and Defense: For high-performance aircraft, drones, and spacecraft demanding robust and mission-critical sensor integration.
- Uzay Araştırmaları: For satellites, rockets, and spacecraft needing lightweight and durable mounts for scientific instruments and operational systems.
- İnsansız Hava Araçları (İHA'lar): For drones used in various applications, from surveillance to delivery, requiring lightweight and structurally sound sensor integration.
The demand for increasingly sophisticated sensors and the push for lighter, more efficient aerospace vehicles are driving the need for innovative manufacturing solutions like metal 3D printing, which can address the complex geometries and stringent performance requirements of modern aerospace sensor mounts.
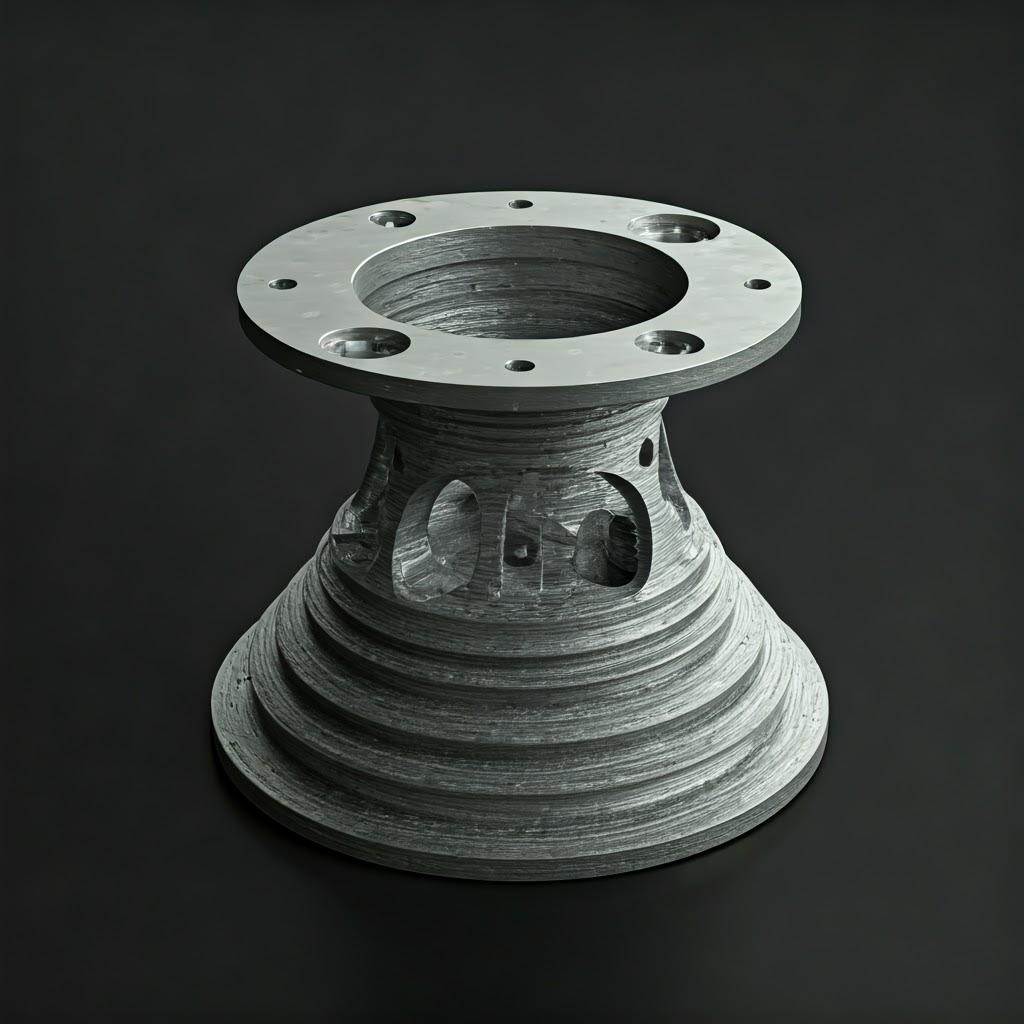
Why Use Metal 3D Printing for Aerospace Sensor Mounts? Advantages Over Traditional Manufacturing
Opting for metal 3D printing for the production of aerospace sensor mounts offers a compelling array of advantages compared to traditional manufacturing methods such as machining, casting, or forging. These benefits are particularly significant in the demanding aerospace sector, where performance, weight, and customization are paramount:
- Tasarım Özgürlüğü ve Karmaşıklık: Metal AM allows for the creation of intricate geometries, including internal lattices, thin walls, and complex curves, that are difficult or impossible to achieve with conventional methods. This design flexibility enables the optimization of the mount for weight reduction and improved structural performance.
- Hafifletme: By utilizing topology optimization and lattice structures, metal 3D printing can produce sensor mounts with significantly reduced weight without compromising strength. This is crucial in aerospace, where every kilogram saved translates to fuel efficiency gains and increased payload capacity.
- Malzeme Verimliliği: Additive manufacturing processes build parts layer by layer, minimizing material waste compared to subtractive methods like machining, where a significant portion of the raw material is removed. This can lead to substantial cost savings, especially when using expensive aerospace-grade alloys.
- Customization and Rapid Prototyping: Metal 3D printing facilitates the rapid creation of prototypes and customized designs without the need for expensive tooling. This agility allows for faster design iterations and the production of tailored sensor mounts for specific applications or sensor types.
- On-Demand Manufacturing and Reduced Lead Times: AM enables the production of parts on demand, reducing the need for large inventories and long lead times associated with traditional manufacturing processes. This can be particularly beneficial for low to medium volume production and spare parts.
- Integration of Features: Metal 3D printing allows for the integration of multiple components into a single part, reducing the need for assembly and the associated weight and potential failure points. This can include features like integrated cooling channels or mounting interfaces.
- Geliştirilmiş Performans: The ability to select and process high-performance metal powders, such as those offered by Metal3dp (https://met3dp.com/product/), allows for the creation of sensor mounts with superior mechanical properties, thermal management characteristics, and corrosion resistance tailored to specific aerospace environments.
- Supply Chain Optimization: Metal AM can enable decentralized manufacturing, potentially reducing reliance on complex global supply chains and offering greater control over production.
By leveraging these advantages, aerospace companies can achieve significant improvements in the design, performance, and manufacturing efficiency of their sensor mounts, ultimately contributing to safer, more efficient, and more advanced aircraft and spacecraft.
Recommended Materials and Why They Matter: High-Performance Metal Powders from Metal3dp
The selection of the appropriate metal powder is paramount in achieving the desired performance characteristics for aerospace sensor mounts produced via 3D printing. The extreme operating conditions encountered in aerospace applications demand materials with exceptional strength, stiffness, temperature resistance, corrosion resistance, and fatigue life. Metal3dp (https://met3dp.com/) offers a comprehensive portfolio of high-quality metal powders specifically engineered for additive manufacturing, making them an ideal partner for producing demanding aerospace components. For aerospace sensor mounts, the following materials are particularly relevant:
- 316L Paslanmaz Çelik: This austenitic stainless steel offers a good combination of strength, corrosion resistance, and weldability. It is a cost-effective option for applications where high strength and extreme temperature resistance are not the primary concerns, but good corrosion resistance is essential. Its biocompatibility also makes it suitable for certain cabin or life support system sensor mounts. Metal3dp’s 316L powder ensures high density and excellent flowability, leading to consistent and reliable printing. | Property | Value | Benefit | | :——————— | :—————————————- | :———————————————————————- | | Tensile Strength | ~550 MPa | Provides sufficient structural integrity for many aerospace applications. | | Corrosion Resistance | Excellent | Ensures long-term reliability in various atmospheric conditions. | | Temperature Resistance | Up to ~800°C (depending on application) | Suitable for moderate temperature environments within aircraft. | | Biocompatibility | Yes | Applicable for specific internal aerospace systems. |
- Ti-6Al-4V (Titanium Grade 5): This titanium alloy is renowned for its exceptional strength-to-weight ratio, excellent corrosion resistance, and high-temperature performance. It is a workhorse material in the aerospace industry, ideal for sensor mounts that require maximum strength with minimal weight, such as those located in critical structural areas or exposed to high stresses and temperatures. Metal3dp’s Ti-6Al-4V powder is produced using advanced techniques to ensure high purity, sphericity, and flowability, resulting in dense, high-performance printed parts. | Property | Value | Benefit | | :——————— | :—————————————- | :——————————————————————————- | | Tensile Strength | ~900 MPa | Offers superior strength for demanding aerospace applications. | | Density | ~4.43 g/cm³ | Provides an excellent strength-to-weight ratio, crucial for aerospace. | | Corrosion Resistance | Excellent | Ensures durability in harsh aerospace environments. | | Temperature Resistance | Up to ~400°C (long-term), higher short-term | Suitable for a wide range of aerospace operating temperatures. | | Biocompatibility | Yes | Can be used in medical-related aerospace applications. |
Metal3dp’s commitment to quality extends to their powder manufacturing processes (https://met3dp.com/about-us/), employing industry-leading gas atomization and PREP technologies to produce spherical powders with high sphericity and good flowability. This ensures optimal performance in metal 3D printing processes, leading to dense, high-quality aerospace sensor mounts with superior mechanical properties. The ability to tailor material properties through the selection of the right metal powder is a key advantage of using metal AM for aerospace applications, and Metal3dp provides the expertise and material selection necessary to achieve optimal results.
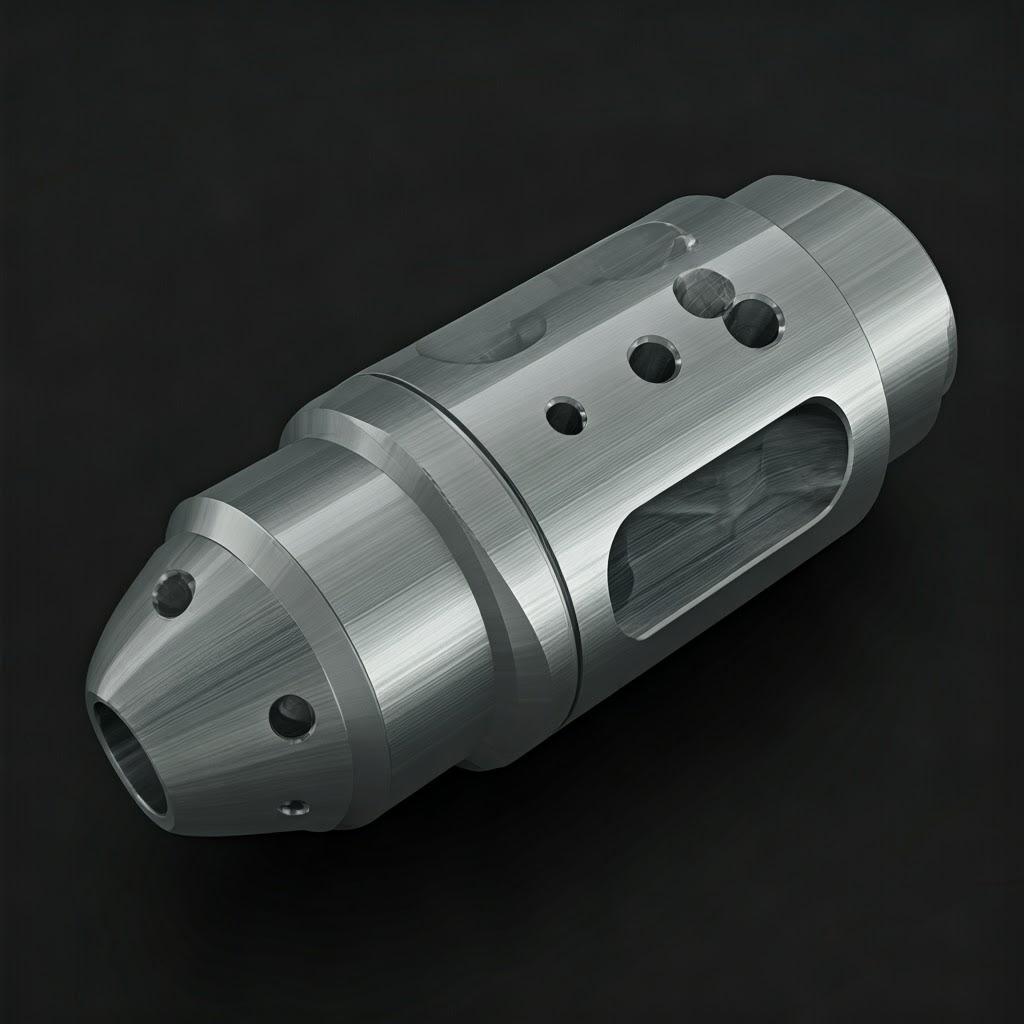
Design Considerations for Additive Manufacturing of Aerospace Sensor Mounts
Designing aerospace sensor mounts for metal additive manufacturing requires a different mindset compared to traditional methods. To fully leverage the capabilities of AM and achieve optimal performance, engineers must consider several key design principles:
- Topology Optimization: This computational technique can be used to identify and remove material from low-stress areas of the design, resulting in lightweight yet structurally sound parts. For aerospace sensor mounts, topology optimization can significantly reduce weight, leading to fuel savings and improved aircraft performance.
- Kafes Yapılar: Incorporating lattice structures within the interior of the mount can further reduce weight while maintaining or even enhancing stiffness and strength. These intricate, repeating patterns are only feasible with additive manufacturing and offer excellent energy absorption characteristics, which can be beneficial in high-vibration environments.
- Parçaların Birleştirilmesi: Metal AM allows for the integration of multiple components into a single, complex part. For sensor mounts, this could mean combining the mounting bracket, stiffening ribs, and cable routing features into one monolithic structure. Reducing the number of individual parts simplifies assembly, reduces potential failure points, and lowers overall weight.
- Orientation and Support Structures: The orientation of the part during the printing process significantly impacts surface finish, support requirements, and build time. Careful consideration of the optimal orientation can minimize the need for extensive post-processing and ensure critical surfaces meet the required specifications. Support structures are often necessary to prevent collapse or distortion during printing, especially for overhanging features. Designing with self-supporting angles and minimizing overhangs can reduce the amount of support material needed.
- Wall Thickness and Feature Size: Metal 3D printing processes have limitations on the minimum wall thickness and feature size that can be reliably produced. Designers must adhere to the design rules specific to the chosen printing technology and material to ensure manufacturability and structural integrity.
- Termal Yönetim: For sensors that generate heat or operate in high-temperature environments, incorporating cooling channels directly into the sensor mount via AM can be an effective thermal management solution. These internal channels can be designed to optimize airflow or liquid cooling, ensuring the sensor operates within its optimal temperature range.
- Datum Features and Tolerances: Integrating datum features into the design from the outset is crucial for ensuring accurate post-processing and assembly. These reference surfaces allow for precise alignment during machining or inspection. Specifying realistic tolerances based on the capabilities of the metal 3D printing process and the required functionality of the sensor mount is also essential.
By embracing these design considerations, engineers can harness the full potential of metal additive manufacturing to create high-performance, lightweight, and highly functional aerospace sensor mounts.
Tolerance, Surface Finish, and Dimensional Accuracy in Metal 3D Printed Sensor Mounts
Achieving the required tolerance, surface finish, and dimensional accuracy is critical for aerospace sensor mounts to ensure proper sensor function, reliable integration with other aircraft components, and long-term performance. Metal 3D printing technologies have advanced significantly in their ability to produce parts with tight tolerances and good surface finishes, but these aspects are influenced by several factors:
- Baskı Teknolojisi: Different metal AM processes, such as Selective Laser Melting (SLM), Direct Metal Laser Sintering (DMLS), and Electron Beam Melting (EBM) (https://met3dp.com/printing-methods/), offer varying levels of precision and surface finish. SLM and DMLS generally provide finer details and better surface finishes compared to EBM.
- Malzeme Seçimi: The type of metal powder used can also affect the achievable tolerance and surface finish. Finer powder particle sizes typically result in smoother surfaces and more precise features. Metal3dp’s range of high-quality powders is optimized for consistent and accurate printing.
- Süreç Parametreleri: The specific settings used during the printing process, such as laser power, scan speed, layer thickness, and build orientation, have a significant impact on the final part’s dimensional accuracy and surface roughness. Optimized process parameters are crucial for achieving the desired results.
- İşlem sonrası: In many cases, post-processing steps are necessary to achieve the final required tolerances and surface finish for aerospace sensor mounts. Common post-processing techniques include:
- İşleme: Precision CNC machining can be used to achieve tight tolerances on critical dimensions and create smooth, accurate mating surfaces.
- Yüzey İşlemi: Techniques like polishing, grinding, and blasting can improve the surface roughness of the printed part.
- Isıl İşlem: Stress relieving or other heat treatments can improve the mechanical properties and dimensional stability of the part.
Typical tolerances achievable with metal 3D printing can range from ±0.1 mm to ±0.05 mm, depending on the technology, material, and part geometry. Surface finishes generally range from Ra 5-20 µm in the as-built condition. However, with appropriate post-processing, these values can be significantly improved to meet stringent aerospace requirements. It is essential to consider the required tolerances and surface finish early in the design process to select the most suitable metal 3D printing technology and plan for any necessary post-processing steps. Collaboration with an experienced metal 3D printing service provider like Metal3dp is crucial to ensure that the final sensor mounts meet the demanding specifications of aerospace applications.
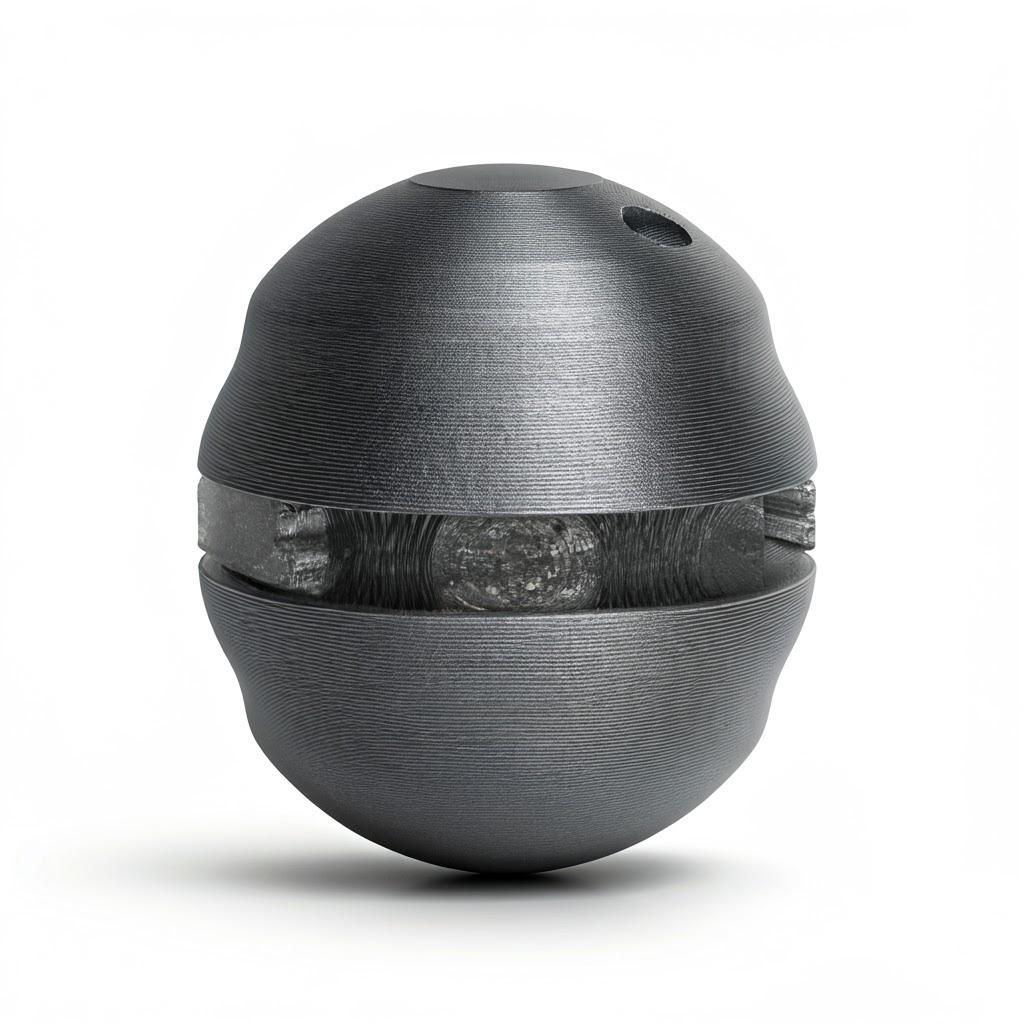
Post-Processing Requirements for Aerospace-Grade Metal Sensor Mounts
While metal 3D printing offers significant advantages in creating complex geometries, post-processing is often a necessary step to achieve the final properties, surface finish, and dimensional accuracy required for aerospace-grade sensor mounts. The specific post-processing requirements depend on the application, the chosen printing technology, and the desired final characteristics. Common post-processing steps include:
- Destek Kaldırma: Metal 3D printed parts often require support structures to prevent distortion during the build process. These supports must be carefully removed after printing, typically through machining, grinding, or wire Electrical Discharge Machining (EDM). The design of the part should aim to minimize the need for extensive support structures to reduce post-processing time and cost.
- Isıl İşlem: Heat treatment is often performed to relieve internal stresses, improve the mechanical properties (such as hardness, strength, and ductility), and ensure dimensional stability of the printed parts. The specific heat treatment cycle depends on the material and the desired final properties. For example, stress relieving is common for aerospace alloys to prevent warping or cracking in service.
- Yüzey İşlemi: As-built metal 3D printed parts typically have a rougher surface finish compared to machined parts. For aerospace sensor mounts that require smooth surfaces for aerodynamic performance, sealing, or aesthetic reasons, various surface finishing techniques can be employed, including:
- Media Blasting: Using abrasive particles to remove surface oxides and improve surface uniformity.
- Grinding and Polishing: Mechanical abrasion techniques to achieve smoother surface finishes and tighter tolerances on critical surfaces.
- Chemical Etching: Using chemical solutions to selectively remove surface layers and improve smoothness.
- CNC İşleme: For features requiring very tight tolerances or specific surface finishes that are difficult to achieve with 3D printing alone, CNC machining can be used as a secondary process. This is often applied to critical mating surfaces or mounting interfaces.
- Inspection and Quality Control: Rigorous inspection processes are essential to ensure that the final sensor mounts meet the stringent quality standards of the aerospace industry. This may involve dimensional measurements, non-destructive testing (NDT) such as dye penetrant inspection or ultrasonic testing to detect internal flaws, and material analysis to verify the chemical composition and microstructure.
- Coating and Surface Treatments: Depending on the application environment, surface coatings may be required to enhance corrosion resistance, wear resistance, or other specific properties. Examples include anodizing for aluminum alloys or passivation for stainless steels.
Understanding the necessary post-processing steps early in the design phase is crucial for optimizing the overall manufacturing process and ensuring the final aerospace sensor mounts meet all performance and quality requirements. Collaborating with a metal 3D printing service provider like Metal3dp, which has expertise in both printing and post-processing, can streamline the entire production流程 and ensure the delivery of high-quality, flight-ready components.
Common Challenges and How to Avoid Them in Metal AM of Sensor Mounts
While metal 3D printing offers numerous advantages for producing aerospace sensor mounts, several challenges can arise during the process. Understanding these potential issues and implementing strategies to mitigate them is crucial for successful outcomes:
- Çarpıtma ve Bozulma: Thermal stresses during the printing process can lead to warping or distortion of the part, especially for complex geometries or thin-walled structures.
- How to Avoid: Optimize part orientation to minimize stress buildup, use appropriate support structures to anchor the part to the build plate, and carefully control the build chamber temperature. Material selection and proper heat treatment post-printing can also help reduce warping.
- Support Removal Difficulties: Aggressively attached or difficult-to-access support structures can be challenging and time-consuming to remove, potentially damaging the part’s surface.
- How to Avoid: Design parts with self-supporting angles whenever possible, optimize support placement and geometry for easier removal, and consider using dissolvable support materials if available for the chosen metal and printing process.
- Porosity and Density Issues: Inconsistent melting or sintering of the metal powder can lead to internal porosity, reducing the part’s strength and fatigue life.
- How to Avoid: Utilize high-quality metal powders with good flowability, such as those offered by Metal3dp. Optimize printing parameters like laser power, scan speed, and layer thickness. Ensure a controlled build environment with appropriate inert gas flow. Hot Isostatic Pressing (HIP) can be used as a post-processing step to reduce porosity and improve density.
- Yüzey Pürüzlülüğü: As-built metal 3D printed parts typically have a rougher surface finish, which may not be suitable for all aerospace applications.
- How to Avoid: Optimize printing parameters for better surface finish, orient critical surfaces strategically during printing, and plan for appropriate post-processing techniques like machining, polishing, or blasting.
- Dimensional Inaccuracy: Deviations from the intended dimensions can occur due to factors like thermal expansion and contraction, as well as machine calibration issues.
- How to Avoid: Calibrate the 3D printer regularly, compensate for material shrinkage in the design phase, and use datum features for accurate post-processing and inspection.
- Material Property Variability: Inconsistent processing can lead to variations in the mechanical properties throughout the printed part.
- How to Avoid: Work with experienced metal 3D printing service providers like Metal3dp who have robust process control measures in place. Ensure consistent powder quality and strictly adhere to optimized printing parameters.
- Maliyet Değerlendirmeleri: Metal 3D printing can be more expensive than traditional manufacturing methods for high-volume production.
- How to Avoid: Focus on applications where the unique benefits of AM, such as design complexity and lightweighting, justify the cost. Optimize designs for efficient printing and minimize material usage and post-processing requirements.
By proactively addressing these potential challenges through careful design, material selection, process optimization, and collaboration with a knowledgeable metal 3D printing partner like Metal3dp, aerospace companies can successfully leverage the advantages of metal AM for their sensor mount applications.
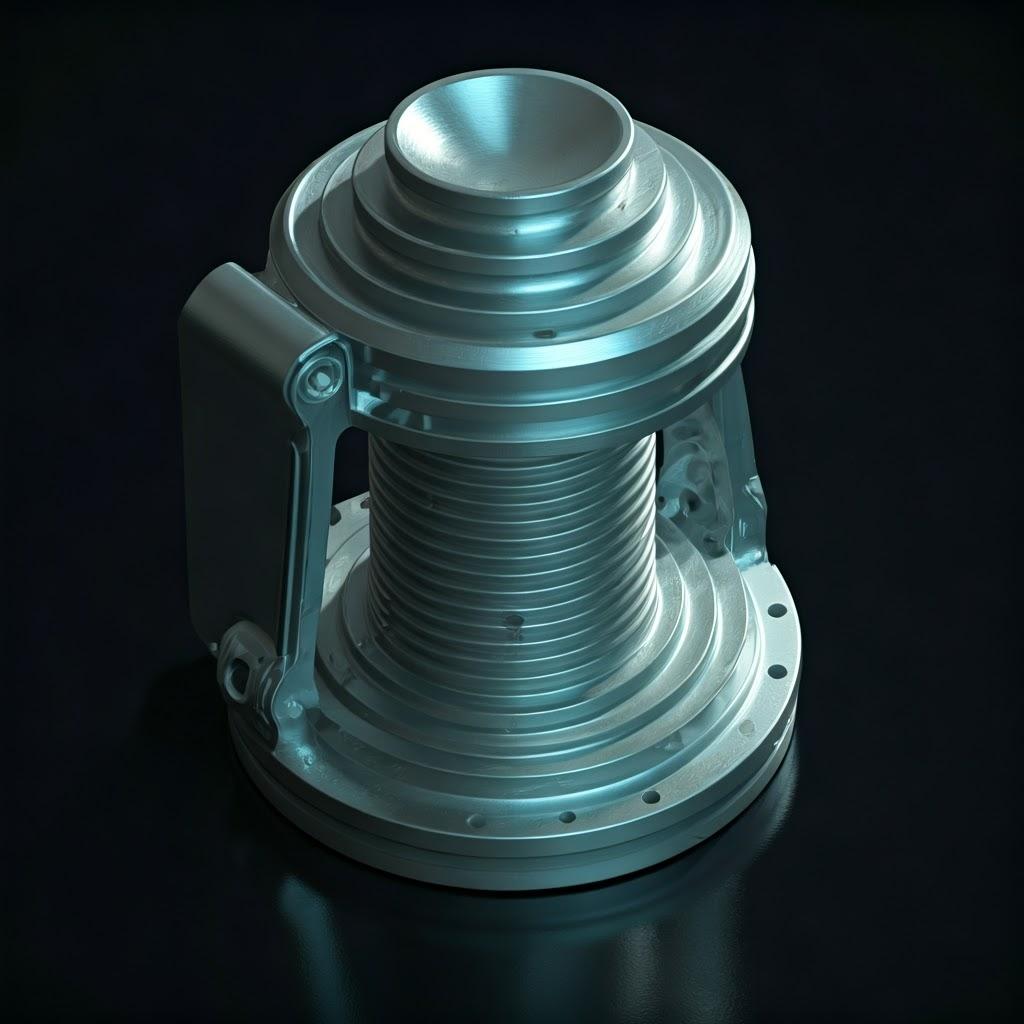
How to Choose the Right Metal 3D Printing Service Provider: Evaluating Metal3dp
Selecting the right metal 3D printing service provider is a critical decision that can significantly impact the success of your aerospace sensor mount project. Given the stringent requirements of the aerospace industry, it’s essential to partner with a provider that possesses the expertise, capabilities, and quality control measures necessary to deliver high-performance, reliable components. Metal3dp stands out as a leading provider of additive manufacturing solutions, and here are key factors to consider when evaluating a potential partner, including why Metal3dp is a strong contender:
- Material Expertise and Range: Ensure the provider has experience working with the specific aerospace-grade metal powders required for your application, such as 316L and Ti-6Al-4V. Metal3dp boasts extensive knowledge in processing a wide range of high-performance metal powders (https://met3dp.com/product/), including these critical alloys, and can advise on the optimal material selection for your sensor mounts.
- Printing Technology and Equipment: The service provider should possess advanced metal 3D printing equipment capable of achieving the required precision, surface finish, and material density for aerospace components. Metal3dp utilizes industry-leading Selective Electron Beam Melting (SEBM) printers, known for their accuracy and reliability in producing mission-critical parts.
- Quality Assurance and Certifications: Look for providers with robust quality management systems and relevant certifications, such as AS9100 for aerospace applications. This demonstrates their commitment to quality control, traceability, and process validation.
- Design and Engineering Support: An ideal partner should offer design and engineering expertise to help optimize your sensor mount design for additive manufacturing, considering factors like topology optimization, lightweighting, and support structure minimization. Metal3dp provides comprehensive solutions spanning application development services, leveraging decades of collective expertise in metal AM.
- Post-Processing Capabilities: Understand the provider’s in-house or partnered post-processing capabilities, including support removal, heat treatment, surface finishing, and machining. Metal3dp offers comprehensive solutions, ensuring that your parts receive the necessary post-processing to meet aerospace standards.
- Inspection and Testing: Inquire about their inspection and testing procedures to ensure dimensional accuracy and material integrity. A reliable provider will have stringent quality control measures in place.
- Lead Times and Production Capacity: Evaluate the provider’s ability to meet your production volume and delivery timelines. Metal3dp’s industry-leading print volume and efficient processes contribute to reliable lead times.
- Communication and Collaboration: Effective communication and a collaborative approach are crucial for a successful partnership. 1 Choose a provider that is responsive, transparent, and willing to work closely with your team. 2 1. ominfowave.com ominfowave.com 2. inbouncy.com inbouncy.com
- Industry Experience and Reputation: Consider the provider’s track record and experience in serving the aerospace industry. Metal3dp has a strong reputation as a leading provider of metal AM equipment and materials for aerospace and other demanding fields.
By carefully evaluating these factors and considering Metal3dp’s comprehensive capabilities in metal AM equipment, high-quality metal powders, and application development, you can make an informed decision and choose a partner that will contribute to the successful production of your aerospace sensor mounts.
Cost Factors and Lead Time for Metal 3D Printed Aerospace Sensor Mounts
Understanding the cost drivers and typical lead times associated with metal 3D printing of aerospace sensor mounts is essential for effective project planning and budgeting. Several factors influence the overall cost and production timeline:
- Malzeme Maliyetleri: The cost of the metal powder is a significant factor. Aerospace-grade alloys like Ti-6Al-4V can be expensive. The volume of material required for the part and support structures will directly impact the material cost. Metal3dp’s advanced powder making system aims to provide high-quality powders cost-effectively.
- Yapım süresi: The time it takes to print a part depends on its size, complexity, and the chosen printing technology. Longer build times translate to higher machine operation costs. Optimizing part orientation and design for efficient printing can help minimize build time.
- İşlem Sonrası Maliyetler: The extent of post-processing required (support removal, heat treatment, surface finishing, machining, inspection) will add to the overall cost and lead time. Complex geometries often necessitate more extensive post-processing.
- İşçilik Maliyetleri: Design optimization, print setup, machine operation, post-processing, and quality control all involve labor costs.
- Machine Depreciation and Overhead: The cost of the 3D printing equipment and the overhead associated with operating the facility are factored into the pricing.
- Üretim Hacmi: While metal AM can be cost-effective for low to medium volumes and complex designs, the cost per part may decrease with higher production volumes, depending on the specific technology and part geometry.
- Complexity of the Part: More intricate designs with internal features or thin walls may require more complex printing strategies and post-processing, impacting both cost and lead time.
Lead Time Considerations:
Lead times for metal 3D printed aerospace sensor mounts can vary depending on factors such as:
- Design Complexity and Optimization: Initial design and optimization for AM can take time.
- Malzeme Durumu: The availability of the required metal powder can influence the start of production. Metal3dp manufactures a wide range of high-quality metal powders, potentially reducing lead times associated with material sourcing.
- Baskı Süresi: As mentioned earlier, the build time is a direct component of the lead time.
- Post-Processing Duration: The complexity and number of post-processing steps will affect the overall lead time.
- Quality Control and Inspection: Thorough inspection processes are necessary but can add to the lead time.
- Supplier’s Capacity and Scheduling: The workload and scheduling of the chosen metal 3D printing service provider will impact turnaround times.
While it’s difficult to provide exact cost figures and lead times without specific part details, engaging with a provider like Metal3dp for a detailed quotation and production timeline is crucial. They can assess your specific requirements and provide an accurate estimate based on your design, material selection, and desired quantity. Understanding these cost and lead time factors will enable you to make informed decisions and effectively integrate metal 3D printing into your aerospace manufacturing processes.
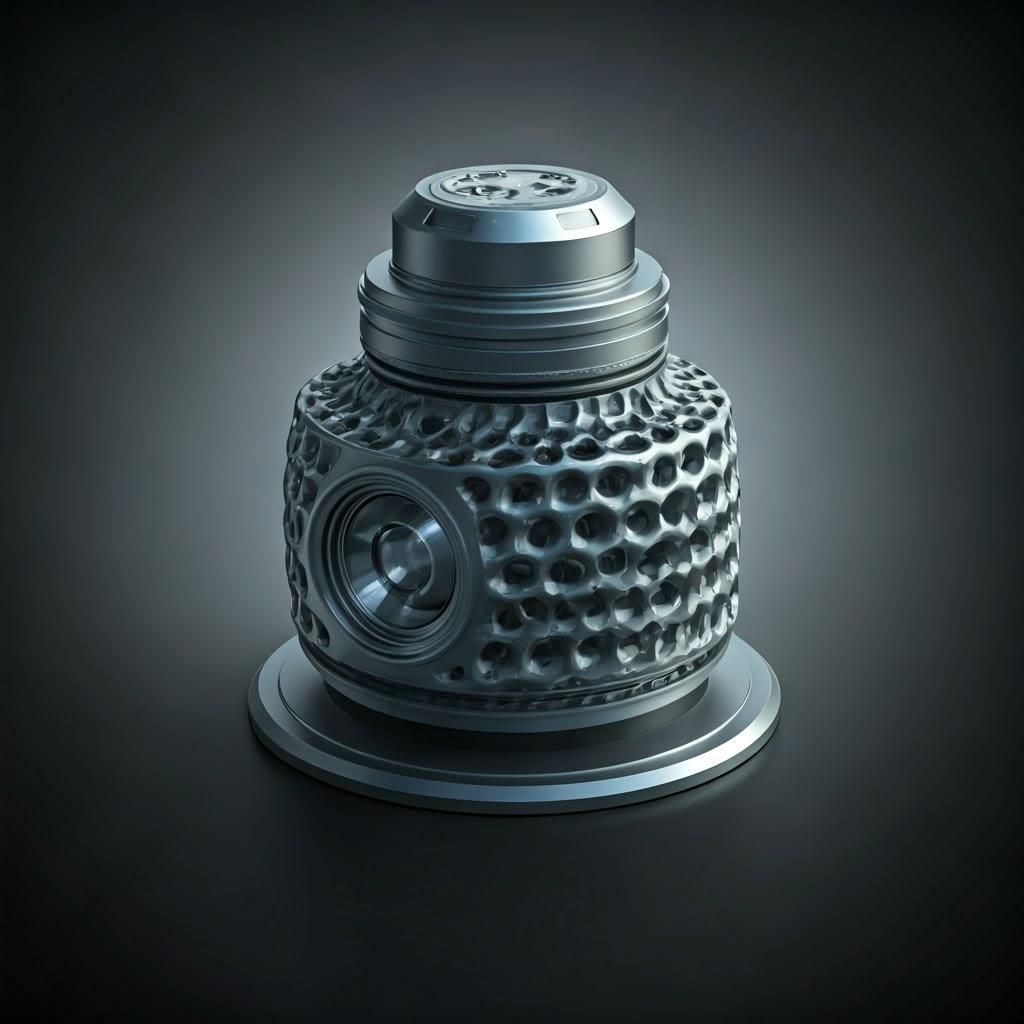
Sıkça Sorulan Sorular (SSS)
- What are the key advantages of using metal 3D printing for aerospace sensor mounts? Metal 3D printing offers significant advantages such as design freedom for complex geometries, lightweighting through topology optimization and lattice structures, material efficiency, rapid prototyping and customization, on-demand manufacturing, and the ability to use high-performance materials like those offered by Metal3dp, leading to enhanced performance and integrated features.
- Which metal powders are typically used for aerospace sensor mounts? Commonly used metal powders include stainless steels like 316L for good strength and corrosion resistance, and titanium alloys like Ti-6Al-4V for exceptional strength-to-weight ratio and high-temperature performance. Metal3dp (https://met3dp.com/) provides a range of high-quality metal powders optimized for additive manufacturing, suitable for various aerospace applications.
- What level of precision and surface finish can be expected from metal 3D printed sensor mounts? The achievable tolerance and surface finish depend on the printing technology, material, and process parameters. Generally, tolerances of ±0.1 mm to ±0.05 mm and surface finishes of Ra 5-20 µm can be achieved in the as-built condition. Post-processing techniques like machining and polishing can further improve these values to meet stringent aerospace requirements.
- Is metal 3D printing cost-effective for aerospace sensor mounts? Metal 3D printing can be cost-effective for low to medium production volumes, complex designs, and when the benefits of lightweighting and performance enhancements outweigh the initial production costs. Optimizing designs for AM and minimizing post-processing can also improve cost-effectiveness. Consulting with a provider like Metal3dp for a specific quotation is recommended.
- What are some common post-processing steps for metal 3D printed aerospace sensor mounts? Common post-processing steps include support removal, heat treatment for stress relief and improved mechanical properties, surface finishing (polishing, grinding, blasting), CNC machining for tight tolerances, and rigorous inspection to ensure quality and dimensional accuracy.
Conclusion – The Future of Aerospace Sensor Mounts with Metal 3D Printing and Metal3dp
Metal 3D printing is revolutionizing the design and manufacturing of aerospace sensor mounts, offering unprecedented opportunities for innovation, performance enhancement, and supply chain optimization. The ability to create complex, lightweight structures with tailored material properties using advanced metal powders from providers like Metal3dp (https://met3dp.com/about-us/) is crucial for meeting the demanding requirements of the aerospace industry. By embracing the design freedoms offered by AM, carefully selecting the right materials, and partnering with experienced service providers like Metal3dp, aerospace engineers and procurement managers can unlock new levels of efficiency, performance, and customization in their sensor mount solutions, paving the way for the next generation of aircraft and spacecraft. Contact Metal3dp to explore how their comprehensive metal AM capabilities can power your organization’s additive manufacturing goals.
Paylaş
MET3DP Technology Co, LTD, merkezi Qingdao, Çin'de bulunan lider bir katmanlı üretim çözümleri sağlayıcısıdır. Şirketimiz, endüstriyel uygulamalar için 3D baskı ekipmanları ve yüksek performanslı metal tozları konusunda uzmanlaşmıştır.
İşletmeniz için en iyi fiyatı ve özelleştirilmiş Çözümü almak için sorgulayın!
İlgili Makaleler
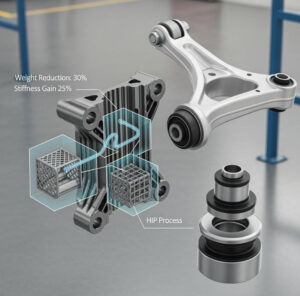
Metal 3D Printed Subframe Connection Mounts and Blocks for EV and Motorsport Chassis
Daha Fazla Oku "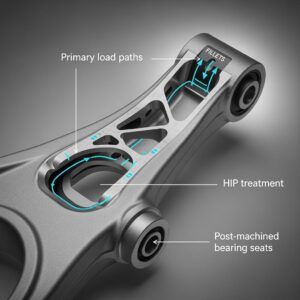
Metal 3D Printing for U.S. Automotive Lightweight Structural Brackets and Suspension Components
Daha Fazla Oku "Met3DP Hakkında
Son Güncelleme
Bizim Ürünümüz
BİZE ULAŞIN
Herhangi bir sorunuz var mı? Bize şimdi mesaj gönderin! Mesajınızı aldıktan sonra tüm ekibimizle talebinize hizmet edeceğiz.