3D Printed Frames for Biomedical Implants
İçindekiler
Introduction: Pioneering Patient Care with 3D Printed Frames for Biomedical Implants
The landscape of biomedical engineering is undergoing a profound transformation, driven by innovations that promise enhanced patient outcomes and more personalized treatments. At the forefront of this revolution lies the application of metal additive manufacturing, more commonly known as metal 3D baskı, in the creation of intricate frames for biomedical implants. These meticulously designed and precisely fabricated structures are not just replacements for damaged or diseased tissues; they are bespoke solutions tailored to the unique anatomy and physiological needs of each individual. By leveraging the power of advanced metal powders and cutting-edge printing technologies, we are unlocking new possibilities in creating implants that exhibit superior biocompatibility, structural integrity, and functional performance. This blog post explores the critical role of 3D printed frames in the realm of biomedical implants, delving into their diverse applications, the compelling advantages of metal 3D printing in their production, and the key material considerations that underpin their success. Join us as we examine how this innovative approach is shaping the future of medical treatments and empowering patients to lead healthier, more fulfilling lives. At Metal3DP, we are proud to be at the vanguard of this exciting field, providing industry-leading solutions that are redefining the possibilities of medical device manufacturing.
What are 3D Printed Frames Used For in Biomedical Implants?
The versatility of 3D printed frames extends across a wide spectrum of medical specialties, offering solutions that address diverse clinical needs. İçinde ORTOPEDİ, these frames form the structural basis for customized joint replacements, spinal fusion cages, and fracture fixation devices. The ability to create patient-specific geometries ensures a precise fit, potentially leading to improved surgical outcomes, reduced recovery times, and enhanced long-term stability. For instance, a 3D printed acetabular cup for a hip replacement can be designed to perfectly match the patient’s pelvic anatomy, optimizing load distribution and minimizing wear. Similarly, in spinal surgery, 3D printed interbody fusion cages with tailored porous structures promote bone ingrowth, facilitating a more robust and lasting fusion.
Bu alanda dentistry, 3D printed frames are revolutionizing the creation of dental implants and prosthetics. From customized implant abutments that ensure optimal soft tissue contours to frameworks for partial dentures that offer superior fit and comfort, metal 3D printing enables the production of highly accurate and biocompatible dental solutions. The precision achievable with this technology minimizes the need for adjustments, leading to a more streamlined and patient-friendly treatment process.
The applications extend to cardiovascular implants as well. 3D printed frames can be used in the development of intricate stents with optimized geometries to improve blood flow and reduce the risk of restenosis. Furthermore, research is ongoing into the use of 3D printing for creating customized heart valve frames and other cardiovascular devices tailored to individual patient anatomies.
Beyond these core areas, 3D printed frames are also finding applications in craniofacial reconstruction, where patient-specific implants can be designed to repair complex bone defects resulting from trauma or surgery. İçinde otolaryngology, custom-designed middle ear implants are being explored to improve hearing outcomes. The ability to create complex, patient-matched structures with specific porosity and mechanical properties makes metal 3D printing an invaluable tool for addressing a wide array of biomedical challenges. The precision and customization offered by metal 3D printing, a core capability at Metal3DP, are crucial for these intricate medical applications. You can explore our advanced printing methods further on our website.
Uygulama Alanı | Examples of 3D Printed Frames | Temel Avantajlar |
---|---|---|
Ortopedi | Hip replacement acetabular cups, spinal fusion cages, fracture plates | Patient-specific fit, enhanced osseointegration, improved stability |
Dentistry | Implant abutments, partial denture frameworks, dental implants | High accuracy, biocompatibility, optimized soft tissue contours |
Kardiyovasküler | Stent frames, heart valve frames (research) | Optimized geometries for blood flow, potential for patient-specific designs |
Craniofacial | Reconstructive implants | Patient-matched fit for complex defects |
Otolaryngology | Middle ear implants (research) | Potential for improved hearing outcomes |
Sayfalara Aktar
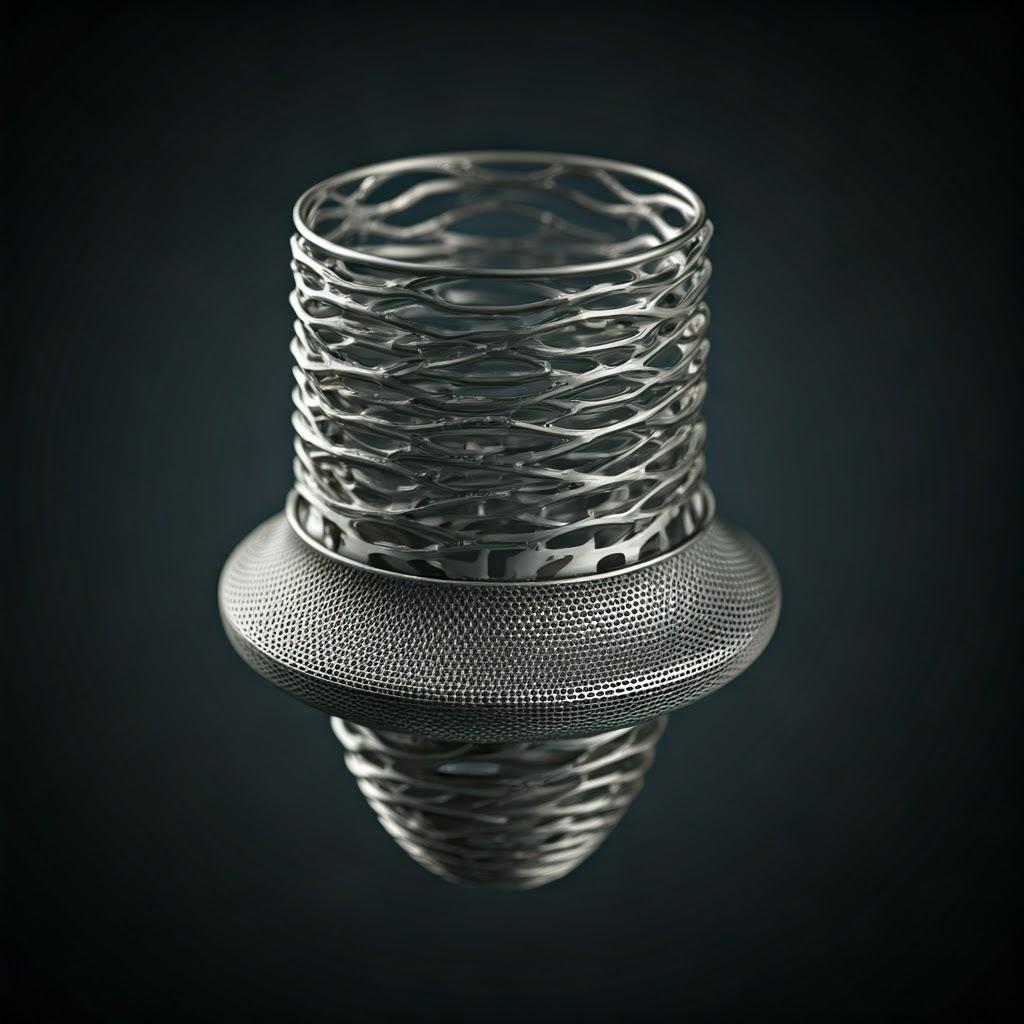
Why Use Metal 3D Printing for Biomedical Implant Frames?
Opting for metal 3D printing over traditional manufacturing methods for biomedical implant frames offers a compelling array of advantages that are critical in the demanding field of medical device fabrication.
One of the most significant benefits is the ability to create intricate and complex geometries. Traditional subtractive manufacturing processes often struggle with producing internal features, complex curves, and customized porous structures. Metal 3D printing, on the other hand, builds parts layer by layer, allowing for the creation of designs that were previously impossible. This freedom in design enables the development of implant frames with optimized shapes for better anatomical fit, enhanced stress distribution, and increased surface area for osseointegration – the process by which bone tissue grows into the implant. Metal3DP‘s industry-leading print volume and accuracy make us an ideal partner for producing these complex medical components.
Enhanced biocompatibility is another crucial advantage. Metal 3D printing allows for the precise control of the materials used, ensuring high purity and the use of biocompatible alloys like Ti-6Al-4V ELI and 316L. Furthermore, the ability to create tailored porous structures through 3D printing can promote better tissue ingrowth and vascularization, leading to improved implant integration and long-term acceptance by the body. Our high-quality metal powders at Metal3DP are specifically designed for such demanding applications. You can learn more about our metal 3D printing services on our website.
Patient-specific customization is perhaps one of the most transformative aspects of using metal 3D printing for implant frames. By leveraging medical imaging data such as CT scans and MRIs, it is possible to design and manufacture implants that perfectly match the unique anatomy of each patient. This level of personalization can lead to improved surgical precision, reduced operative times, better functional outcomes, and increased patient satisfaction.
Moreover, metal 3D printing can offer advantages in terms of malzeme verimliliği. Traditional manufacturing often involves significant material waste as material is removed to create the final part. Additive manufacturing, in contrast, only uses the material needed to build the component, potentially leading to cost savings, especially for complex, low-volume production runs typical of customized implants.
Finally, the rapid prototyping and iteration capabilities of metal 3D printing are invaluable in the development of new implant designs. Engineers and surgeons can quickly iterate on designs, produce prototypes, and evaluate their performance, accelerating the innovation cycle and leading to more effective and safer medical devices.
Avantaj | Açıklama | Benefit for Biomedical Implants |
---|---|---|
Intricate Geometries | Ability to create complex internal features, curves, and porous structures. | Optimized anatomical fit, enhanced stress distribution, increased osseointegration. |
Enhanced Biocompatibility | Precise control over material purity and the use of biocompatible alloys. Ability to create tailored porous structures. | Improved tissue ingrowth, vascularization, and long-term acceptance by the body. |
Hastaya Özel Özelleştirme | Manufacturing implants tailored to individual patient anatomy using medical imaging data. | Improved surgical precision, reduced operative times, better functional outcomes, increased patient satisfaction. |
Malzeme Verimliliği | Material is only used where needed, reducing waste compared to subtractive methods. | Potential cost savings, especially for complex, low-volume production. |
Rapid Prototyping & Iteration | Quick design iterations and prototype production. | Accelerated innovation cycle, faster development of more effective and safer medical devices. |
Sayfalara Aktar
Recommended Materials and Why They Matter
The selection of the appropriate metal powder is paramount in the 3D printing of high-quality biomedical implant frames. The chosen material must not only possess the necessary mechanical properties to withstand the physiological loads within the body but also exhibit excellent biocompatibility to ensure long-term safety and integration with surrounding tissues. Metal3DP offers a range of high-performance metal powders specifically designed for demanding applications like biomedical implants.
Two of the most commonly recommended metal powders for 3D printing biomedical implant frames are Ti-6Al-4V ELI (Extra-Low Interstitial) ve 316L Paslanmaz Çelik.
Ti-6Al-4V ELI is an alloy of titanium, aluminum, and vanadium, with extra-low levels of interstitial elements such as oxygen, nitrogen, carbon, and hydrogen. This reduction in interstitials enhances the alloy’s ductility and fracture toughness, making it particularly well-suited for load-bearing implants. Its key properties include:
- Mükemmel Biyouyumluluk: Titanium alloys are known for their exceptional biocompatibility, exhibiting minimal corrosion and eliciting a favorable tissue response. The ELI grade further enhances this by reducing the potential for adverse reactions.
- Yüksek Mukavemet-Ağırlık Oranı: Ti-6Al-4V ELI offers a superior strength-to-weight ratio compared to many other metallic biomaterials, allowing for the creation of strong yet lightweight implants.
- İyi Korozyon Direnci: The alloy forms a stable oxide layer on its surface, providing excellent resistance to corrosion in the harsh physiological environment of the human body.
- Osseointegration Potential: Titanium and its alloys promote osseointegration, facilitating the direct bonding of bone to the implant surface, which is crucial for long-term stability.
316L Paslanmaz Çelik is an austenitic stainless steel alloy containing chromium, nickel, and molybdenum, with a low carbon content (the “L” designation). It is another widely used material in medical implants due to its:
- Good Biocompatibility: While generally considered less biocompatible than titanium alloys, 316L stainless steel is still widely used for various implant applications, particularly where high mechanical strength is required.
- Yüksek Mukavemet ve Süneklik: 316L offers good mechanical strength and ductility, making it suitable for implants that need to withstand significant forces.
- Mükemmel Korozyon Direnci: The chromium content in 316L forms a passive oxide layer that provides excellent resistance to corrosion in bodily fluids.
- Maliyet-Etkinlik: Compared to titanium alloys, 316L stainless steel is generally more cost-effective, which can be a significant consideration for certain applications.
The choice between Ti-6Al-4V ELI and 316L often depends on the specific application requirements, including the load-bearing demands, the desired level of biocompatibility, and cost considerations. For applications requiring the highest level of biocompatibility and a superior strength-to-weight ratio, Ti-6Al-4V ELI is often the preferred choice. For applications where high strength and cost-effectiveness are key factors, 316L stainless steel may be a suitable option.
At Metal3DP, our advanced powder making system ensures the production of high-quality metal powders with high sphericity and good flowability, essential for achieving dense, high-quality 3D printed implant frames with superior mechanical properties. Our portfolio includes both Ti-6Al-4V ELI and 316L, among other innovative alloys, catering to the diverse needs of the biomedical industry.
Malzeme | Anahtar Özellikler | Advantages for Biomedical Implants | Dikkate Alınması Gerekenler |
---|---|---|---|
Ti-6Al-4V ELI | Excellent biocompatibility, high strength-to-weight ratio, good corrosion resistance, promotes osseointegration | Ideal for load-bearing implants, minimizes adverse tissue reactions, long-term stability, excellent integration with bone | Higher cost compared to stainless steel |
316L Paslanmaz Çelik | Good biocompatibility, high strength and ductility, excellent corrosion resistance, cost-effective | Suitable for high-strength applications, good resistance to bodily fluids, more economical option | Generally considered less biocompatible than titanium alloys |
Sayfalara Aktar
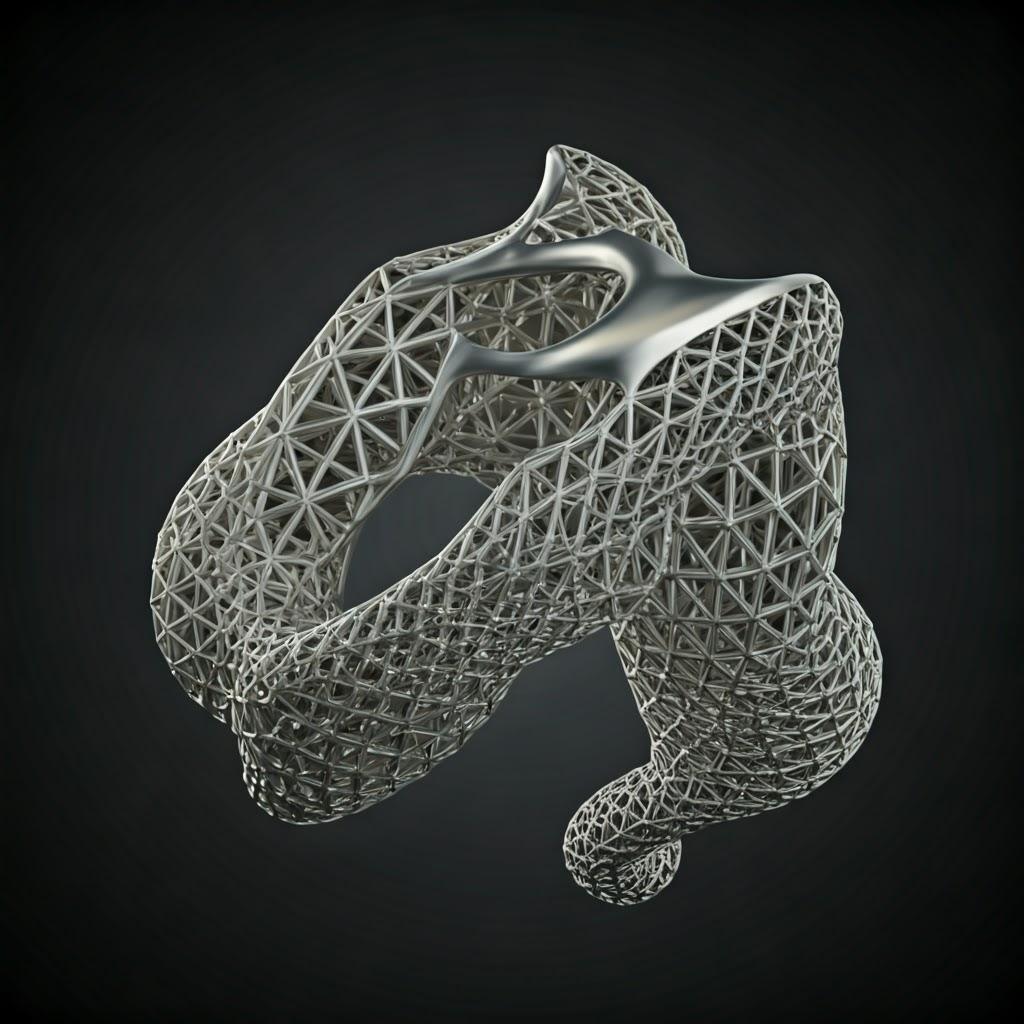
Design Considerations for Additive Manufacturing of Implant Frames
Designing biomedical implant frames for additive manufacturing requires a paradigm shift from traditional design principles. To fully leverage the capabilities of metal 3D printing, engineers must consider factors that optimize biocompatibility, osseointegration, mechanical performance, and the unique constraints and opportunities presented by the layer-by-layer manufacturing process.
Biyouyumluluk should be at the forefront of the design process. Material selection, as discussed earlier, is critical, but the design itself can also influence how the implant interacts with the body. For instance, avoiding sharp corners and edges can minimize stress concentrations and reduce the potential for tissue irritation. Surface topography, which can be controlled through the 3D printing process, plays a significant role in cell adhesion and proliferation. Designing surfaces with controlled roughness can promote better osseointegration. Metal3DP‘s expertise in material science and additive manufacturing allows us to guide you in designing for optimal biocompatibility.
Osseointegrasyon, the direct structural and functional connection between living bone and the surface of a load-carrying implant, is paramount for the long-term success of many orthopedic and dental implants. Design features that enhance osseointegration include porous structures that allow for bone ingrowth and promote vascularization. The pore size, shape, and interconnectivity are critical parameters that can be precisely controlled with metal 3D printing. Trabecular-like structures, for example, mimic the natural architecture of bone, providing a scaffold for bone cells to attach and grow.
Mechanical performance is another key design consideration. The implant frame must be able to withstand the physiological loads it will encounter within the body. Finite element analysis (FEA) can be a valuable tool in optimizing the geometry and material distribution to ensure adequate strength and stiffness while minimizing weight. The design should consider the direction of applied forces and incorporate features that enhance load transfer and reduce stress shielding, a phenomenon where the implant carries too much load, leading to bone resorption.
Patient-specific needs often dictate the design of custom implants. Utilizing medical imaging data allows for the creation of frames that perfectly match the patient’s anatomy, ensuring optimal fit and function. This personalization can involve complex contours and geometries that are only achievable with additive manufacturing.
Katmanlı Üretim Tasarımı (DfAM) principles are crucial for successful 3D printing. These include:
- Oryantasyon: The orientation of the part during printing can significantly impact surface finish, support requirements, and mechanical properties. Careful consideration of the build orientation is essential.
- Destek Yapıları: Overhanging features and complex geometries may require support structures to prevent collapse or distortion during printing. The design should aim to minimize the need for supports and consider how they will be removed post-printing.
- Wall Thickness and Feature Size: Minimum wall thicknesses and feature sizes are dictated by the capabilities of the 3D printer and the chosen material. Designers must adhere to these limitations to ensure successful printing.
- Internal Channels and Lattice Structures: Additive manufacturing allows for the creation of internal channels for drug delivery or cooling, as well as lightweight yet strong lattice structures to reduce weight and promote osseointegration.
By integrating these design considerations, engineers can create innovative and effective 3D printed frames for biomedical implants that enhance patient outcomes. Metal3DP‘s comprehensive solutions, spanning advanced metal powders and application development services, can assist you in navigating these complex design requirements.
Design Consideration | Açıklama | Impact on Biomedical Implants |
---|---|---|
Biyouyumluluk | Avoiding sharp edges, optimizing surface topography for cell adhesion. | Reduced tissue irritation, enhanced cell attachment and proliferation, improved long-term acceptance. |
Osseointegrasyon | Incorporating porous structures with controlled pore size, shape, and interconnectivity to mimic bone architecture. | Promotion of bone ingrowth and vascularization, leading to stronger and more stable implant fixation. |
Mekanik Performans | Optimizing geometry and material distribution using FEA to ensure adequate strength and stiffness while minimizing weight and stress shielding. | Ability to withstand physiological loads, reduced risk of implant failure, preservation of bone density around the implant. |
Patient-Specific Needs | Designing implants based on individual patient anatomy derived from medical imaging data. | Optimal fit and function, improved surgical precision, enhanced patient comfort and satisfaction. |
DfAM Principles | Considering build orientation, support structures, minimum feature sizes, and the potential for internal channels and lattice structures during the design phase. | Successful and efficient 3D printing, optimized surface finish and mechanical properties, reduced material usage and post-processing effort, creation of innovative functionalities. |
Sayfalara Aktar
Tolerance, Surface Finish, and Dimensional Accuracy in 3D Printed Implants
In the realm of biomedical implants, precision is paramount. The tolerance, surface finish, and dimensional accuracy of 3D printed frames directly impact their fit, functionality, and interaction with surrounding tissues. Achieving the required levels of precision necessitates a deep understanding of the metal 3D printing process, material behavior, and the capabilities of the printing equipment. Metal3DP‘s printers deliver industry-leading accuracy and reliability, crucial for mission-critical medical parts.
Hoşgörü refers to the allowable variation in the dimensions of a manufactured part. For biomedical implants, tight tolerances are often required to ensure proper fit with adjacent anatomical structures or other implant components. The achievable tolerance in metal 3D printing depends on several factors, including the printing technology (e.g., Selective Laser Melting (SLM), Electron Beam Melting (EBM)), the material being used, and the design of the part. Generally, metal 3D printing can achieve tolerances in the range of ±0.05 mm to ±0.2 mm, but this can vary depending on the specific application and the expertise of the service provider.
Yüzey kaplaması describes the texture of the implant surface. In biomedical applications, surface finish is critical for biocompatibility and osseointegration. A rougher surface can promote better bone cell adhesion and ingrowth, while a smoother surface may be required to minimize friction or wear in articulating joints. Metal 3D printed parts typically have a surface roughness that depends on the powder particle size and the printing parameters. Post-processing techniques, such as polishing, blasting, or etching, can be employed to achieve the desired surface finish.
Boyutsal doğruluk refers to the degree to which the printed part matches the intended design dimensions. High dimensional accuracy is essential for ensuring the implant fits correctly and functions as intended. Factors affecting dimensional accuracy in metal 3D printing include material shrinkage during solidification, thermal stresses, and potential warping. Careful process control, optimized build parameters, and经验丰富的操作人员 are crucial for achieving high dimensional accuracy.
Factors Influencing Precision in Metal 3D Printing:
- Printer Calibration and Maintenance: Regularly calibrated and well-maintained 3D printers are essential for consistent and accurate results.
- Malzeme Özellikleri: The thermal conductivity, melting point, and shrinkage behavior of the metal powder influence the final dimensions and surface finish.
- Build Parameters: Laser power, scan speed, layer thickness, and other printing parameters must be carefully optimized for the specific material and application.
- Destek Yapıları: The design and placement of support structures can affect the surface finish of supported areas.
- İşlem sonrası: Heat treatment can relieve internal stresses and improve dimensional stability, while surface treatments can modify the surface finish to meet specific requirements.
Achieving the required tolerance, surface finish, and dimensional accuracy for biomedical implant frames often involves a combination of optimized design, careful selection of printing parameters, and appropriate post-processing techniques. Working with an experienced metal 3D printing service provider like Metal3DP, which possesses the necessary expertise and equipment, is crucial for ensuring the quality and performance of these critical medical devices. Our commitment to accuracy and reliability ensures that your 3D printed implants meet the most stringent requirements.
Parametre | Açıklama | Importance for Biomedical Implants |
---|---|---|
Hoşgörü | Allowable variation in the dimensions of the printed part. | Ensures proper fit with adjacent anatomical structures or other implant components, critical for functionality and stability. |
Yüzey İşlemi | The texture of the implant surface, often quantified by roughness parameters. | Influences biocompatibility, osseointegration (rougher surfaces can promote bone ingrowth), and friction/wear in articulating joints (smoother surfaces may be required). |
Boyutsal Doğruluk | The degree to which the printed part matches the intended design dimensions. | Essential for ensuring the implant fits correctly within the patient’s anatomy and functions as intended, directly impacting surgical outcomes and patient well-being. |
Sayfalara Aktar
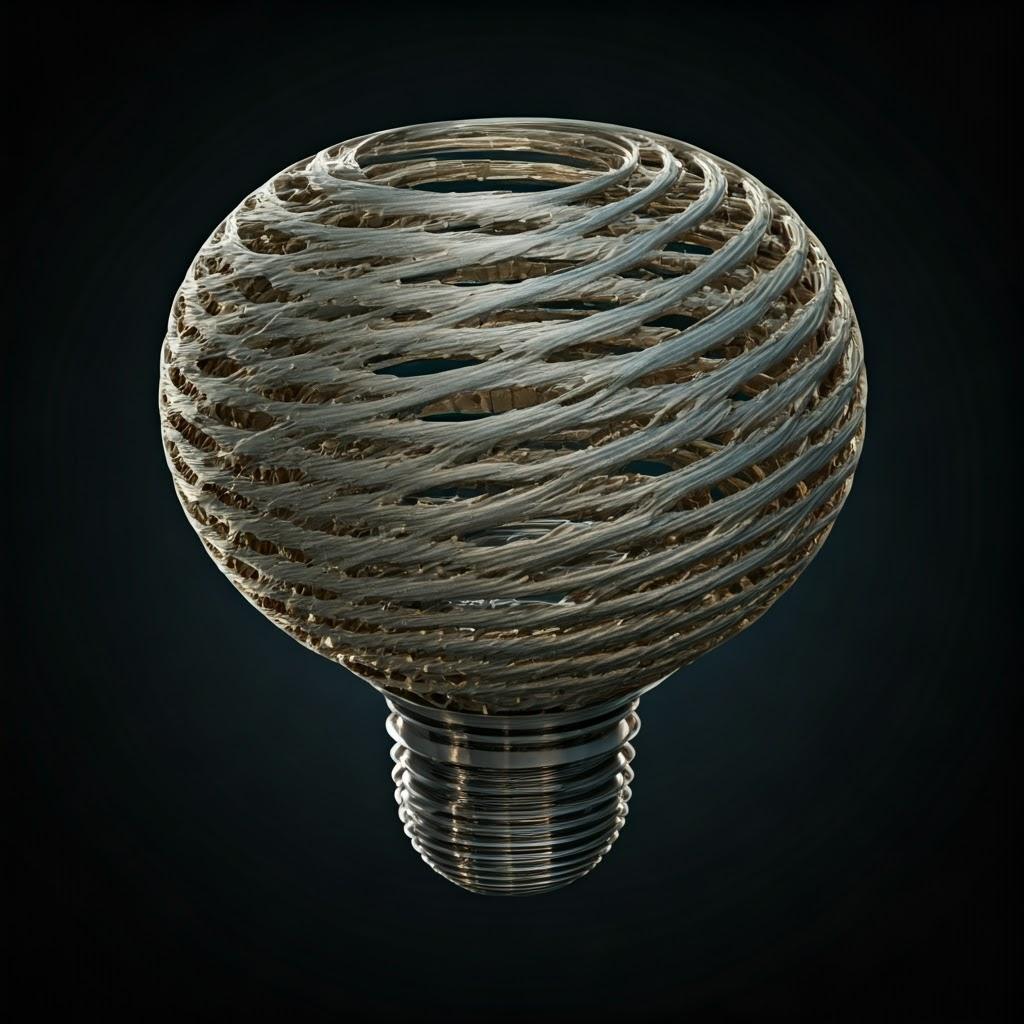
Post-Processing Requirements for Biomedical Implant Frames
Once a biomedical implant frame is 3D printed, it typically undergoes several post-processing steps to ensure it meets the stringent requirements for medical applications. These steps are crucial for achieving the desired mechanical properties, surface finish, biocompatibility, and sterility.
Toz Giderme: After the printing process, any loose or partially sintered powder must be carefully removed from the implant frame, especially from internal channels and porous structures. This is often done using techniques such as compressed air, vacuuming, and ultrasonic cleaning.
Stress Relief Heat Treatment: Metal 3D printing can induce residual stresses in the part due to the rapid heating and cooling cycles. Heat treatment is often performed to relieve these stresses, which can improve the mechanical properties and dimensional stability of the implant. The specific heat treatment cycle depends on the material and the desired outcome.
Destek Yapısının Kaldırılması: If support structures were used during printing, they need to be carefully removed without damaging the delicate features of the implant frame. This can be done manually using cutting tools or with automated methods like wire electro-discharge machining (EDM).
Yüzey Modifikasyonu: The as-printed surface finish may not be suitable for the intended application. Various surface modification techniques can be employed to achieve the desired roughness or smoothness. These include:
- Parlatma: Used to create a smooth surface, often required for articulating surfaces or to reduce the risk of bacterial adhesion.
- Blasting: Involves propelling abrasive particles at the surface to create a controlled roughness, which can enhance osseointegration.
- Etching: Chemical etching can also be used to modify the surface topography and improve biocompatibility.
- Kaplama: Applying biocompatible coatings, such as hydroxyapatite, can further enhance osseointegration and promote tissue growth.
Cleaning and Sterilization: Before implantation, the medical device must be thoroughly cleaned to remove any residual contaminants from the manufacturing process. Sterilization is a critical step to eliminate all viable microorganisms and prevent infections. Common sterilization methods for metal implants include autoclaving (steam sterilization), ethylene oxide gas sterilization, and gamma irradiation. The choice of sterilization method must be compatible with the implant material and design.
Quality Control and Inspection: Throughout the post-processing steps, rigorous quality control and inspection procedures are essential to ensure that the implant meets the required specifications. This may involve dimensional measurements, surface roughness analysis, and non-destructive testing methods to detect any internal defects.
The specific post-processing requirements for a 3D printed biomedical implant frame will depend on the material, the intended application, and regulatory requirements. Working with a knowledgeable metal 3D printing service provider like Metal3DP, which has experience in handling medical-grade materials and adhering to strict quality standards, is crucial for ensuring the safety and efficacy of the final implant. We understand the critical nature of these post-processing steps and have the expertise to perform them to the highest standards.
Post-Processing Step | Açıklama | Importance for Biomedical Implants |
---|---|---|
Toz Giderme | Removing loose or partially sintered powder from the printed part. | Ensures a clean and functional implant, especially important for internal features and porous structures. |
Stress Relief Heat Treatment | Heating the printed part to a specific temperature and holding it for a certain time to reduce internal residual stresses. | Improves mechanical properties and dimensional stability, reducing the risk of warping or failure after implantation. |
Destek Yapısının Kaldırılması | Carefully removing the support structures used during printing without damaging the implant. | Ensures the correct geometry and surface finish of the implant. |
Yüzey Modifikasyonu | Applying techniques like polishing, blasting, etching, or coating to achieve the desired surface roughness or biocompatibility. | Optimizes osseointegration, reduces friction and wear, minimizes bacterial adhesion, and enhances tissue integration. |
Cleaning and Sterilization | Removing contaminants and eliminating all viable microorganisms from the implant surface. | Critical for preventing infections and ensuring the safety of the medical device for implantation. |
Quality Control & Inspection | Performing dimensional measurements, surface analysis, and non-destructive testing to verify the implant meets specifications. | Ensures the quality, safety, and efficacy of the final medical device, meeting regulatory requirements and ensuring patient well-being. |
Sayfalara Aktar
Common Challenges and How to Avoid Them in 3D Printing Implant Frames
While metal 3D printing offers numerous advantages for creating biomedical implant frames, several challenges can arise during the process. Understanding these potential issues and implementing strategies to mitigate them is crucial for achieving consistent and high-quality results.
Material Purity and Biocompatibility: Ensuring the metal powder used for printing meets the stringent purity and biocompatibility standards required for medical implants is paramount. Contamination during powder handling or the printing process can compromise the safety and efficacy of the implant. Çözüm: Source materials from reputable suppliers with certifications relevant to medical device manufacturing. Implement strict protocols for powder handling and storage to prevent contamination. Consider using inert gas environments during printing to minimize oxidation. Metal3DP employs industry-leading gas atomization and PREP technologies to research and manufacture high-quality 3D printing metallic powders, ensuring material purity.
Mevzuata Uygunluk: Medical devices are subject to stringent regulatory requirements, such as those set forth by the FDA in the United States or the MDR in Europe. Meeting these requirements, which cover material testing, manufacturing processes, and quality control, can be complex for 3D printed implants, especially patient-specific devices. Çözüm: Engage with regulatory experts early in the design and development process. Establish a robust quality management system that complies with relevant standards (e.g., ISO 13485). Maintain thorough documentation of materials, processes, and testing. Metal3DP partners with organizations to implement 3D printing and accelerate digital manufacturing transformations, including navigating regulatory landscapes.
Dimensional Accuracy and Warping: Achieving the required dimensional accuracy for precise fit within the body can be challenging due to factors like material shrinkage and thermal stresses during printing. Warping, the distortion of the part during or after printing, can also occur, especially with complex geometries or thin-walled structures. Çözüm: Optimize part design to minimize large flat areas and sharp corners. Carefully control build parameters, such as laser power and scan speed. Employ stress-relieving heat treatments post-printing. Optimize build orientation and support structures to minimize distortion. Metal3DP‘s printers are known for their industry-leading accuracy, minimizing these issues.
Porosity and Mechanical Properties: Achieving dense, fully consolidated parts with consistent mechanical properties is crucial for load-bearing implants. Porosity, the presence of voids within the material, can weaken the implant and increase the risk of failure. Çözüm: Optimize printing parameters to ensure complete melting and fusion of the metal powder. Use high-quality metal powders with good flowability and sphericity. Consider hot isostatic pressing (HIP) post-processing to reduce porosity and enhance mechanical properties. Our advanced powder making system at Metal3DP produces metallic spheres with high sphericity and good flowability, contributing to dense, high-quality prints.
Long-Term Stability within the Body: Biomedical implants must maintain their structural integrity and biocompatibility over extended periods within the harsh physiological environment. Corrosion, wear, and degradation of the material can lead to implant failure or adverse tissue reactions. Çözüm: Select biocompatible materials with proven long-term performance in the intended application. Optimize surface treatments to enhance corrosion resistance and wear properties. Conduct thorough in-vitro and in-vivo testing to evaluate the long-term stability of the implant.
By proactively addressing these common challenges through careful material selection, optimized design and processing, and adherence to regulatory standards, it is possible to consistently produce high-quality 3D printed frames for biomedical implants that improve patient outcomes. Metal3DP‘s decades of collective expertise in metal additive manufacturing position us as a trusted partner in overcoming these challenges.
Common Challenge | Çözüm |
---|---|
Material Purity & Biocompatibility | Source certified materials, implement strict powder handling protocols, use inert gas environments during printing. |
Mevzuata Uygunluk | Engage with regulatory experts, establish a robust quality management system (e.g., ISO 13485), maintain thorough documentation. |
Dimensional Accuracy & Warping | Optimize part design, carefully control build parameters, employ stress-relieving heat treatments, optimize build orientation and support structures. |
Gözeneklilik ve Mekanik Özellikler | Optimize printing parameters, use high-quality powders, consider hot isostatic pressing (HIP) post-processing. |
Uzun Vadeli İstikrar | Select biocompatible materials, optimize surface treatments, conduct thorough in-vitro and in-vivo testing. |
Sayfalara Aktar
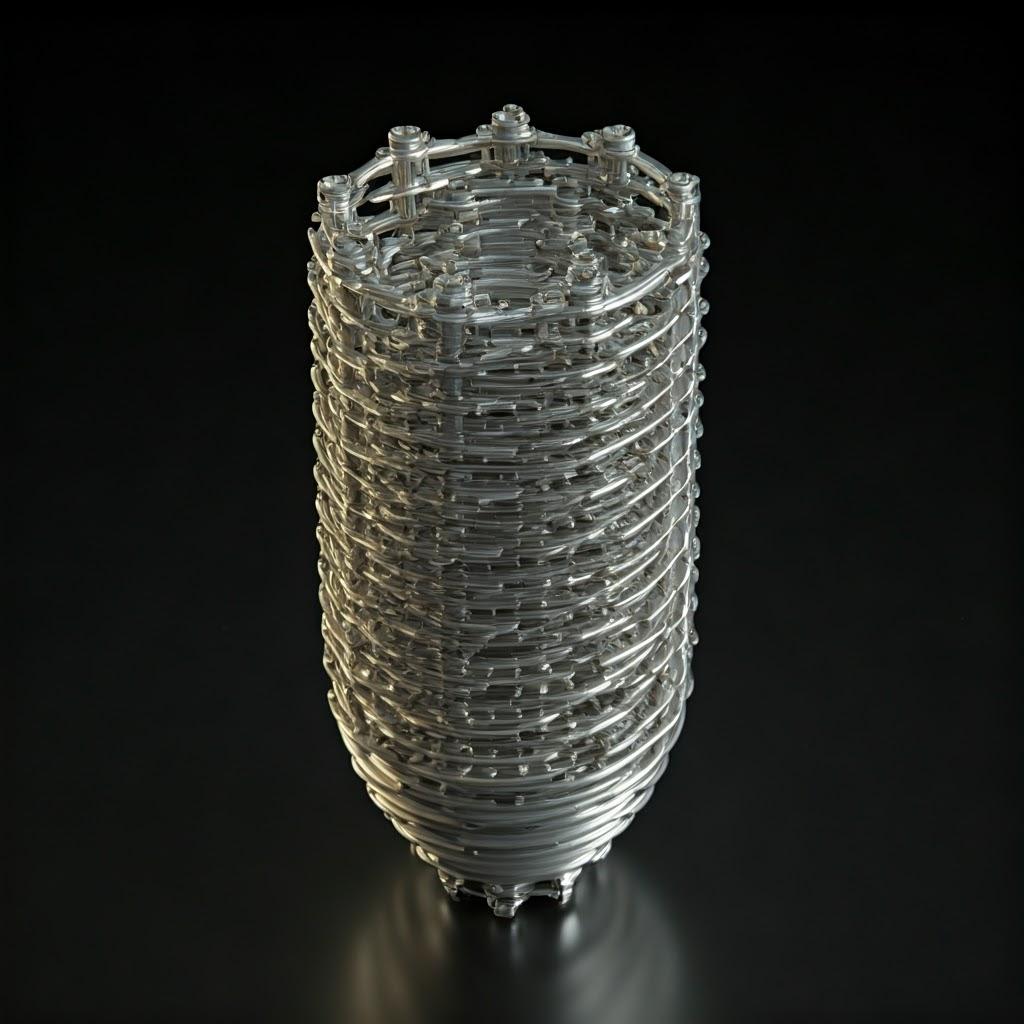
How to Choose the Right Metal 3D Printing Service Provider for Medical Implants
Selecting the appropriate metal 3D printing service provider is a critical decision for companies venturing into the production of biomedical implant frames. The right partner will possess the expertise, certifications, and capabilities necessary to ensure the quality, safety, and regulatory compliance of these life-critical devices. Here are key criteria to consider when evaluating potential suppliers:
Industry Experience and Focus: Look for a provider with a proven track record in manufacturing medical devices or components. Experience with the specific materials and applications relevant to your implant frame is highly valuable. A company with a strong understanding of the medical device industry’s unique demands and regulations will be better equipped to meet your needs. Metal3DP has decades of collective expertise in metal additive manufacturing and partners with organizations in the medical field.
Material Capabilities: Ensure the service provider has experience working with the biocompatible metal powders required for your implant, such as Ti-6Al-4V ELI and 316L. They should have established protocols for material handling, traceability, and testing to guarantee the quality and purity of the materials used. Inquire about their advanced powder making system and the quality control measures they have in place. Metal3DP manufactures a wide range of high-quality metal powders optimized for medical applications.
Printing Technology and Equipment: The type of metal 3D printing technology used (e.g., SLM, EBM) can impact the achievable precision, surface finish, and material properties. Understand the provider’s equipment capabilities, including build volume, accuracy, and the range of materials they can process. Providers with industry-leading print volume, accuracy, and reliability are preferred for critical medical parts. Metal3DP‘s printers are designed to deliver such high standards.
Quality Management System and Certifications: A robust quality management system is essential for medical device manufacturing. The service provider should hold relevant certifications, such as ISO 13485 (Medical devices — Quality management systems — Requirements for regulatory purposes). These certifications demonstrate their commitment to quality, process control, and regulatory compliance.
Post-Processing Capabilities: As discussed earlier, post-processing is a critical step in the manufacturing of biomedical implants. Evaluate the provider’s in-house capabilities for powder removal, heat treatment, surface modification (e.g., polishing, blasting, coating), cleaning, and sterilization. Outsourcing these steps can add complexity and potentially increase lead times.
Regulatory Understanding and Support: The provider should have a thorough understanding of the regulatory requirements for medical devices in your target markets (e.g., FDA, MDR). They should be able to provide support with documentation, material testing, and process validation to facilitate regulatory submissions.
Design for Additive Manufacturing (DfAM) Expertise: A service provider with expertise in DfAM can help optimize your implant design for the 3D printing process, potentially improving performance, reducing material usage, and minimizing post-processing requirements. They can offer guidance on design features that enhance biocompatibility and osseointegration. Metal3DP provides comprehensive solutions spanning design optimization and application development.
Communication and Project Management: Effective communication and project management are crucial for a successful partnership. The provider should be responsive, transparent, and able to provide regular updates on the progress of your project.
By carefully evaluating potential metal 3D printing service providers based on these criteria, you can select a partner that will contribute to the successful development and manufacturing of your biomedical implant frames. Consider reaching out to Metal3DP to explore how our capabilities can power your organization’s additive manufacturing goals in the medical field. You can find more information about our company on our about us page.
Değerlendirme Kriterleri | Önemli Hususlar | Questions to Ask Potential Providers |
---|---|---|
Industry Experience & Focus | Proven track record in medical device manufacturing, understanding of relevant materials and applications, knowledge of medical device regulations. | Can you provide examples of medical implants or components you have manufactured? What is your experience with the specific materials required for my implant? Are you familiar with medical device regulatory requirements? |
Malzeme Yetenekleri | Experience with biocompatible metal powders (e.g., Ti-6Al-4V ELI, 316L), material handling and traceability protocols, quality control measures for powders. | What biocompatible metal powders do you offer? What are your material traceability procedures? What quality control tests do you perform on your metal powders? |
Printing Technology & Equipment | Type of 3D printing technology used, build volume, accuracy specifications of printers, range of materials processed. | What type of metal 3D printing technology do you use? What is the build volume and achievable accuracy of your printers? What other materials can you process? |
Quality Management & Certifications | Relevant certifications (e.g., ISO 13485), adherence to quality management systems, process control measures. | Are you ISO 13485 certified? Can you provide details about your quality management system? What process control measures do you have in place? |
Post-Processing Yetenekleri | In-house capabilities for powder removal, heat treatment, surface modification, cleaning, and sterilization. | What post-processing services do you offer in-house? What are your cleaning and sterilization protocols for medical devices? |
Regulatory Understanding & Support | Knowledge of medical device regulations in your target markets, ability to provide support with documentation and validation. | Are you familiar with the regulatory requirements for medical devices in [your target market]? Can you assist with documentation and validation processes? |
DfAM Expertise | Experience in optimizing designs for additive manufacturing, knowledge of design features that enhance biocompatibility and osseointegration. | Do you offer design for additive manufacturing services? Can you provide guidance on optimizing my implant design for 3D printing? |
Communication & Project Management | Responsiveness, transparency, ability to provide regular updates, clear communication protocols. | What are your standard communication protocols? Can you provide a project management plan for my project? Who will be my main point of contact? |
Sayfalara Aktar
Cost Factors and Lead Time for 3D Printed Biomedical Implant Frames
Understanding the factors that influence the cost and lead time for 3D printed biomedical implant frames is essential for effective budgeting and project planning. These factors can vary significantly depending on the complexity of the design, the material used, production volume, and the chosen service provider.
Maliyet Faktörleri:
- Malzeme Maliyetleri: The cost of the metal powder is a significant factor. Materials like Ti-6Al-4V ELI are generally more expensive than 316L stainless steel. The quantity of material required, which is influenced by the part’s size and density, will also impact the overall cost.
- Tasarım Karmaşıklığı: More intricate designs may require more complex printing parameters and post-processing, potentially increasing costs. Features like internal channels, fine details, and complex curves can add to the manufacturing cost.
- Yapım süresi: The duration of the printing process directly affects the machine time and associated operational costs. Larger parts or those requiring finer layer thicknesses will generally have longer build times.
- İşlem Sonrası Maliyetler: The extent and complexity of post-processing steps, such as support removal, heat treatment, surface finishing, and sterilization, will contribute to the final cost. Specialized surface treatments or coatings will add to these expenses.
- Quality Assurance and Testing: The costs associated with quality control procedures, material testing, and dimensional inspection are essential for ensuring the safety and efficacy of medical implants and will be factored into the overall price.
- Üretim Hacmi: For larger production runs, economies of scale can often be achieved, reducing the per-unit cost. However, custom, patient-specific implants are typically produced in low volumes, which may result in higher per-unit costs.
- Service Provider Fees: The pricing structure of the metal 3D printing service provider, including setup fees, printing rates, and post-processing charges, will significantly impact the total cost.
Kurşun zamanı:
- Design and Engineering: The time required for design optimization, simulation, and preparation for 3D printing. For custom implants based on medical imaging, this phase can take longer.
- Baskı Süresi: The actual duration of the 3D printing process, which depends on the part’s size, complexity, and the number of parts being printed simultaneously.
- Post-Processing Time: The time needed to complete all necessary post-processing steps, which can vary depending on the complexity of the required treatments.
- Quality Control and Inspection: The time allocated for thorough quality checks and testing.
- Regulatory Considerations: Depending on the classification of the implant and the regulatory requirements, additional time may be needed for testing, documentation, and approvals.
- Shipping and Logistics: The time taken for the finished implants to be shipped to the end user.
It’s important to engage in detailed discussions with potential metal 3D printing service providers to obtain accurate cost estimates and lead times for your specific project. Providing clear design specifications, material requirements, and desired quantities will enable them to provide a more precise quotation. Remember that prioritizing quality and regulatory compliance is paramount in medical device manufacturing, and these factors can influence both cost and lead time. Metal3DP is committed to providing transparent and competitive pricing while maintaining the highest standards of quality and efficiency. Contact us to discuss your specific needs and obtain a detailed quotation.
Faktör | Maliyet Üzerindeki Etkisi | Impact on Lead Time |
---|---|---|
Malzeme | Higher cost for advanced alloys like Ti-6Al-4V ELI compared to standard materials. Larger part volume increases material consumption and cost. | Material availability can sometimes affect lead time. |
Tasarım | Complex geometries may require more intricate printing and post-processing, increasing costs. | Complex designs may take longer to prepare for printing and may require more complex post-processing. |
Build Time | Longer print times increase machine costs and overall production expenses. | Directly contributes to longer manufacturing lead times. |
İşlem Sonrası | Extensive or specialized post-processing steps (e.g., coatings) will increase costs. | Adds to the overall manufacturing lead time, depending on the complexity of the required processes. |
Kalite Güvence | Thorough testing and inspection procedures add to the overall cost but are essential for medical devices. | Can extend the lead time depending on the complexity and duration of the required tests and inspections. |
Üretim Hacmi | Lower volumes (e.g., custom implants) typically have higher per-unit costs due to limited economies of scale. | May have shorter overall lead times for very small quantities but longer per-unit lead times compared to mass production. |
Service Provider | Pricing structures vary; factor in setup fees, printing rates, and post-processing charges. | Lead times can vary significantly based on the provider’s capacity, scheduling, and efficiency. |
Sayfalara Aktar
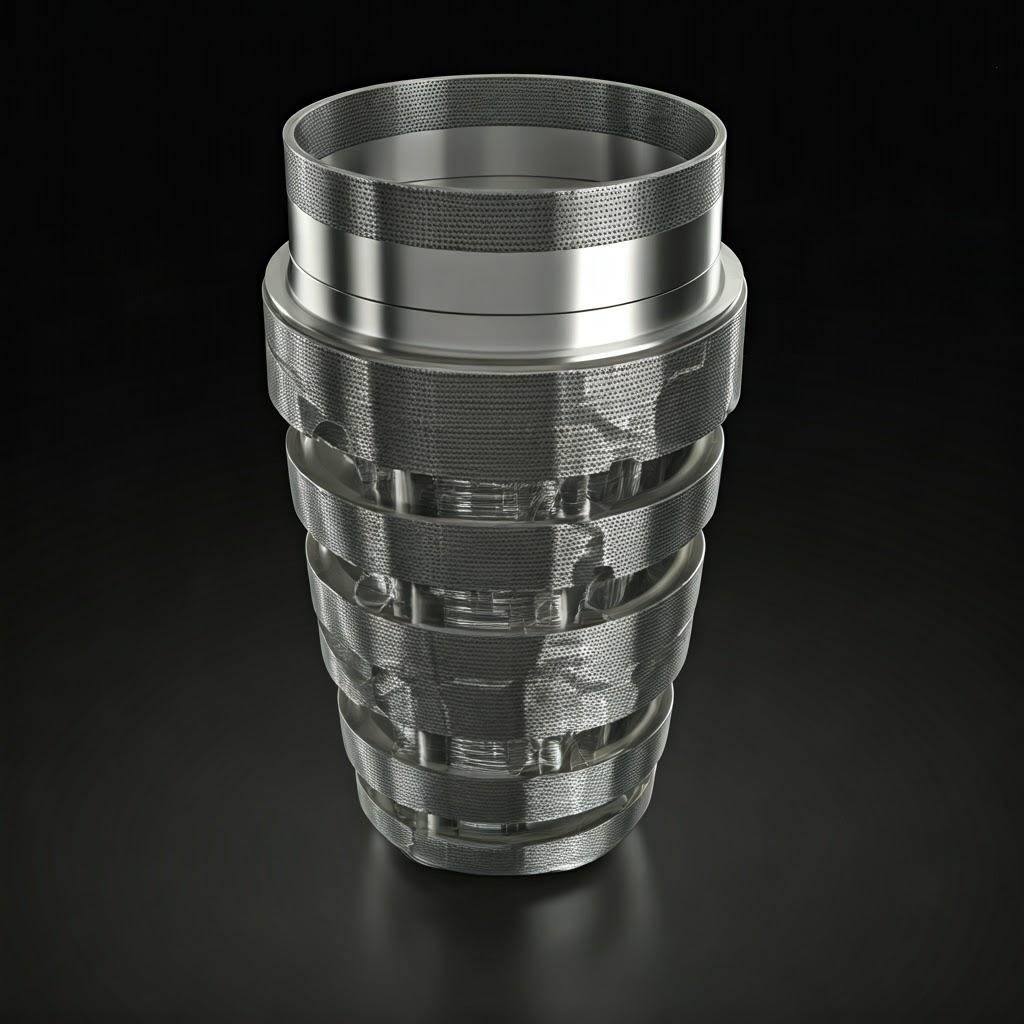
Sıkça Sorulan Sorular (SSS)
Q: Are 3D printed metal implants safe for long-term use inside the human body? A: Yes, when manufactured using biocompatible materials like Ti-6Al-4V ELI or 316L stainless steel and adhering to strict quality control and regulatory standards, 3D printed metal implants can be safe for long-term use. Proper material selection, surface treatment, and sterilization are crucial factors in ensuring biocompatibility and preventing adverse tissue reactions over time.
Q: Can metal 3D printing create custom-sized implants for individual patients? A: Absolutely. One of the significant advantages of metal 3D printing is its ability to produce patient-specific implants based on medical imaging data. This customization allows for a precise fit, potentially leading to improved surgical outcomes and patient satisfaction.
Q: What are the common materials used for 3D printing biomedical implants? A: The most common materials include titanium alloys (like Ti-6Al-4V ELI), stainless steel (like 316L), and cobalt-chromium alloys. The choice of material depends on the specific application requirements, including mechanical properties, biocompatibility needs, and cost considerations. Metal3DP offers a range of high-quality metal powders, including these commonly used alloys. You can explore our product offerings on our website.
Q: How does the cost of 3D printed metal implants compare to traditionally manufactured implants? A: The cost comparison can vary depending on factors such as design complexity, production volume, and material used. For highly customized, low-volume implants, 3D printing can often be more cost-effective than traditional methods. For high-volume production of standard designs, traditional manufacturing may still be more economical. However, the unique benefits of 3D printing, such as design flexibility and patient-specific customization, often provide added value.
Conclusion: Shaping the Future of Biomedical Implants with Metal 3D Printing
Metal 3D printing is revolutionizing the field of biomedical implants, offering unprecedented opportunities for creating customized, high-performance medical devices. The ability to produce intricate geometries, enhance biocompatibility through tailored porous structures, and utilize advanced materials like Ti-6Al-4V ELI and 316L is transforming patient care across various medical disciplines.
At Metal3DP, we are at the forefront of this innovation, providing industry-leading metal 3D printing equipment and high-quality metal powders that enable the creation of mission-critical parts for aerospace, medical, automotive, and other fields. Our commitment to accuracy, reliability, and material excellence makes us a trusted partner for organizations looking to leverage the power of additive manufacturing in the biomedical sector.
By understanding the design considerations, precision requirements, post-processing needs, and potential challenges associated with 3D printing implant frames, and by choosing the right service provider, companies can unlock the full potential of this transformative technology. The future of biomedical implants is being shaped by the advancements in metal 3D printing, promising more personalized, effective, and ultimately, life-enhancing solutions for patients worldwide. Contact Metal3DP today to explore how our comprehensive additive manufacturing solutions can help you achieve your goals in the medical industry.
Paylaş
MET3DP Technology Co, LTD, merkezi Qingdao, Çin'de bulunan lider bir katmanlı üretim çözümleri sağlayıcısıdır. Şirketimiz, endüstriyel uygulamalar için 3D baskı ekipmanları ve yüksek performanslı metal tozları konusunda uzmanlaşmıştır.
İşletmeniz için en iyi fiyatı ve özelleştirilmiş Çözümü almak için sorgulayın!
İlgili Makaleler
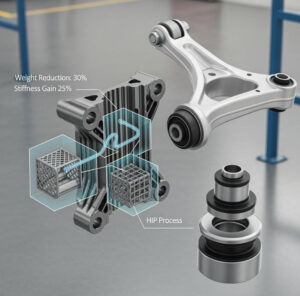
Metal 3D Printed Subframe Connection Mounts and Blocks for EV and Motorsport Chassis
Daha Fazla Oku "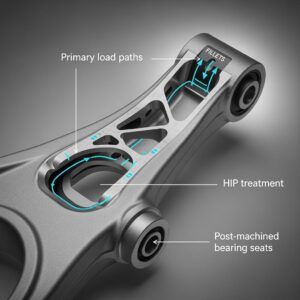
Metal 3D Printing for U.S. Automotive Lightweight Structural Brackets and Suspension Components
Daha Fazla Oku "Met3DP Hakkında
Son Güncelleme
Bizim Ürünümüz
BİZE ULAŞIN
Herhangi bir sorunuz var mı? Bize şimdi mesaj gönderin! Mesajınızı aldıktan sonra tüm ekibimizle talebinize hizmet edeceğiz.