High-Temp Protection Tile Components: Revolutionizing Thermal Management with Metal 3D Printing
İçindekiler
Introduction – The Critical Role of High-Temperature Protection in Advanced Industries
In demanding sectors like aerospace, automotive, medical, and industrial manufacturing, components that can withstand extreme temperatures are not just desirable—they are essential for safety, efficiency, and performance. Thermal protection tile components play a pivotal role in these applications, acting as critical barriers against intense heat. Traditionally manufactured through conventional methods, these components are now being revolutionized by the advent of metal 3D baskı. This advanced manufacturing technique offers unprecedented design freedom, material optimization, and performance enhancements, opening new possibilities for creating high-temp protection tile components tailored to the most challenging environments. At https://met3dp.com/, we are at the forefront of this innovation, providing cutting-edge metal additive manufacturing solutions that are redefining the boundaries of thermal management.
What are High-Temp Protection Tile Components Used For?
High-temp protection tile components serve a multitude of critical functions across various industries. In the aerospace sector, they are integral to thermal barrier systems in engine components, exhaust nozzles, and heat shields, protecting sensitive structures from the extreme heat generated during flight and re-entry. The automotive industry utilizes these components in exhaust systems, turbocharger heat shields, and brake systems to manage high temperatures and ensure operational reliability. In medical applications, specialized high-temperature components are used in sterilization equipment and high-energy medical devices. Industrial manufacturing benefits from these tiles in furnaces, heat exchangers, and other high-temperature processing equipment, enhancing efficiency and extending equipment lifespan. The ability to customize the design and material properties of these tiles through metal 3D printing allows for optimized performance in each specific application, addressing unique thermal challenges with precision-engineered solutions.
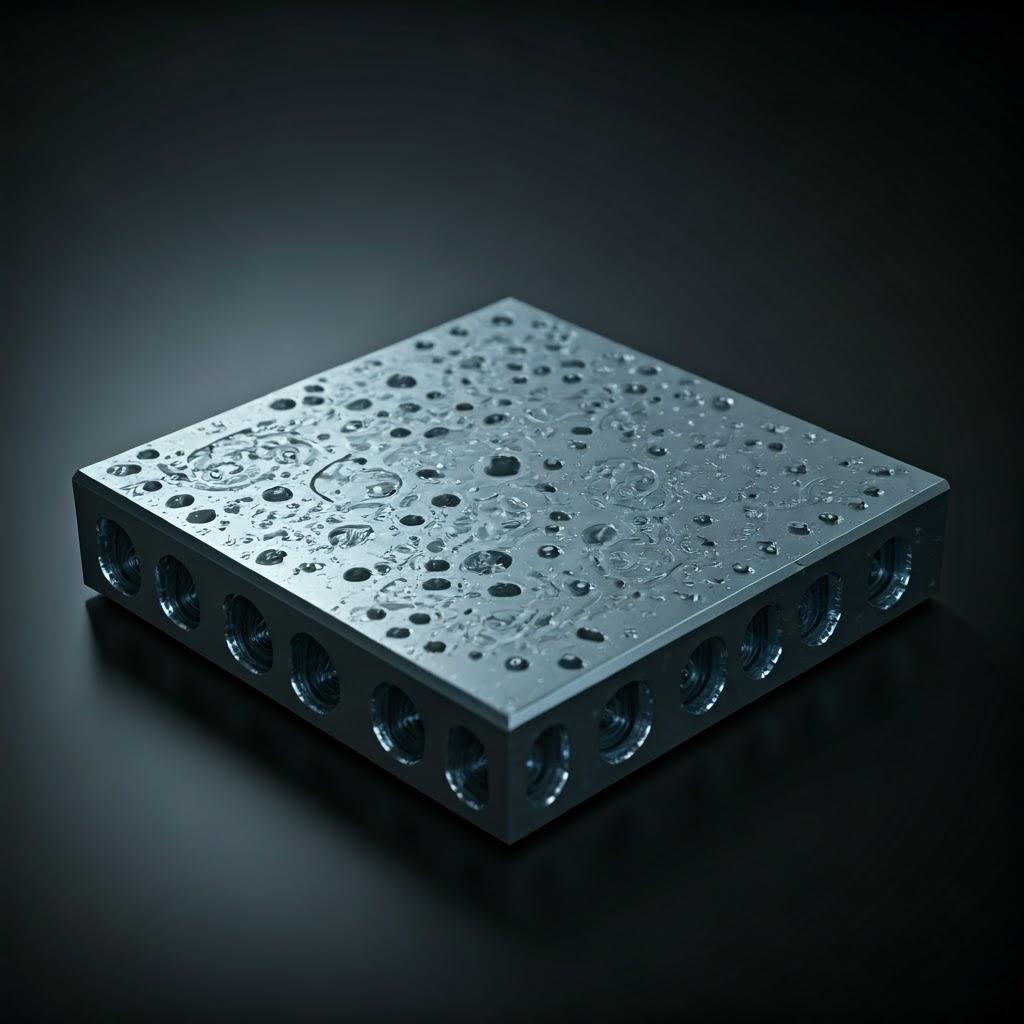
Why Use Metal 3D Printing for High-Temp Protection Tile Components?
Opting for metal 3D printing for the fabrication of high-temp protection tile components offers significant advantages over traditional manufacturing methods. Additive manufacturing enables the creation of complex geometries and intricate internal cooling channels that are often impossible or cost-prohibitive to achieve with conventional techniques. This design freedom allows for the optimization of heat dissipation and thermal management, leading to improved component performance and longevity. Furthermore, metal 3D printing facilitates the use of advanced, high-temperature alloys like IN625 and Haynes 282, which can be precisely tailored to meet specific thermal and mechanical requirements. This capability is particularly valuable for producing customized components with enhanced thermal resistance, durability, and reduced weight—critical factors in industries like aerospace and automotive. By leveraging our industry-leading print volume, accuracy, and reliability at https://met3dp.com/metal-3d-printing/, businesses can achieve superior performance and efficiency in their high-temperature applications.
Recommended Materials and Why They Matter: IN625 and Haynes 282
When it comes to high-temp protection tile components, the choice of material is paramount. At Metal3DP, we recommend IN625 and Haynes 282 powders for their exceptional high-temperature performance and suitability for metal 3D printing.
IN625
IN625 is a nickel-chromium superalloy renowned for its high strength, excellent corrosion resistance, and outstanding heat resistance up to approximately 982°C (1800°F). Its unique composition, including significant amounts of molybdenum and niobium, provides exceptional resistance to creep and rupture at elevated temperatures. The properties of IN625 powder make it an ideal choice for applications demanding high structural integrity in extreme thermal environments, such as aerospace ducting systems and engine exhaust components. Our advanced powder making system ensures that the IN625 powder we offer exhibits high sphericity and excellent flowability, crucial for achieving dense, high-quality 3D printed parts with superior mechanical properties. You can learn more about our high-quality metal powders at https://met3dp.com/product/.
Key Properties of IN625:
Mülkiyet | Değer | Önem |
---|---|---|
Erime Noktası | 1290-1350 °C (2350-2462 °F) | Yüksek erime noktası, yüksek sıcaklıklarda performans sağlar. |
Çekme Dayanımı (Tavlanmış) | 827-1034 MPa (120-150 ksi) | High strength-to-weight ratio is crucial for demanding applications. |
Korozyon Direnci | Mükemmel | Suitable for harsh operating environments, including marine and chemical processing. |
Creep and Rupture Strength | Yüksek | Maintains structural integrity under prolonged stress at high temperatures. |
Thermal Conductivity (at 21 °C) | 9.8 W/m·°C | Important for heat dissipation in thermal management applications. |
Yoğunluk | 8,44 g/cm³ | Contributes to the overall weight of the component, critical in aerospace and automotive industries. |
Kaynaklanabilirlik | Mükemmel | Facilitates the creation of complex assemblies and allows for post-processing joining. |
Tipik Partikül Boyutu | 15-53 µm | Optimized for powder bed fusion 3D printing processes, ensuring good flowability and packing density. |
Uygulamalar | Aerospace, marine, nuclear, chemical processing | Versatile material suitable for a wide range of high-performance applications requiring resistance to heat and corrosion. |
Metal3DP Powder Advantage | High sphericity, low oxygen content | Enables the 3D printing of dense, high-quality metal parts with superior mechanical properties, a hallmark of our advanced powder making system. |
Sayfalara Aktar
Haynes 282
Haynes 282 is another advanced nickel-based superalloy that stands out for its exceptional creep strength, thermal stability, and oxidation resistance, particularly in the temperature range of 650-930°C (1200-1700°F). This patented alloy also offers good weldability and fabricability, making it well-suited for complex 3D printed geometries. The superior creep strength of Haynes 282 surpasses that of many other high-temperature alloys, positioning it as an excellent material for components in aerospace engines and industrial gas turbines that experience prolonged exposure to high temperatures and significant mechanical stress. Metal3DP’s commitment to high-quality metal powders ensures that our Haynes 282 powder enables the production of robust and reliable thermal protection tile components.
Key Properties of Haynes 282:
Mülkiyet | Değer | Önem |
---|---|---|
Erime Noktası | 1300-1375 °C (2372-2507 °F) | High melting range allows for service in very high-temperature environments. |
Tensile Strength (Room Temp) | 870 MPa (126 ksi) | High strength ensures structural integrity under load. |
Yield Strength (Room Temp) | 580 MPa (84 ksi) | Indicates the material’s resistance to permanent deformation. |
Elongation (Room Temp) | 44% | High ductility allows for some deformation before fracture, enhancing reliability. |
Sürünme Dayanımı | Excellent (650-930 °C / 1200-1700 °F) | Superior resistance to deformation under constant stress at high temperatures. |
Oksidasyon Direnci | Excellent (up to 900 °C / 1650 °F) | Protects the component from degradation in high-temperature, oxidizing environments. |
Yoğunluk | 8,94 g/cm³ | A balance of weight and performance for demanding applications. |
Kaynaklanabilirlik | İyi | Enables complex fabrications and repairs. |
Tipik Partikül Boyutu | 15-45 µm (customizable) | Optimized for various metal 3D printing techniques, ensuring consistent and high-quality builds. |
Uygulamalar | Aerospace, power generation, petrochemical | Ideal for components requiring exceptional high-temperature strength and oxidation resistance. |
Metal3DP Powder Advantage | Spherical morphology, controlled size distribution | Ensures excellent flowability and packing density for additive manufacturing, leading to high-performance, reliable 3D printed parts. |
Sayfalara Aktar
By offering these high-performance metal powders and leveraging our expertise in metal additive manufacturing, Metal3DP empowers industries to create thermal protection tile components with superior performance, tailored to their specific and demanding requirements. Contact us at https://met3dp.com/about-us/ to discuss how our capabilities can support your organization’s additive manufacturing goals.
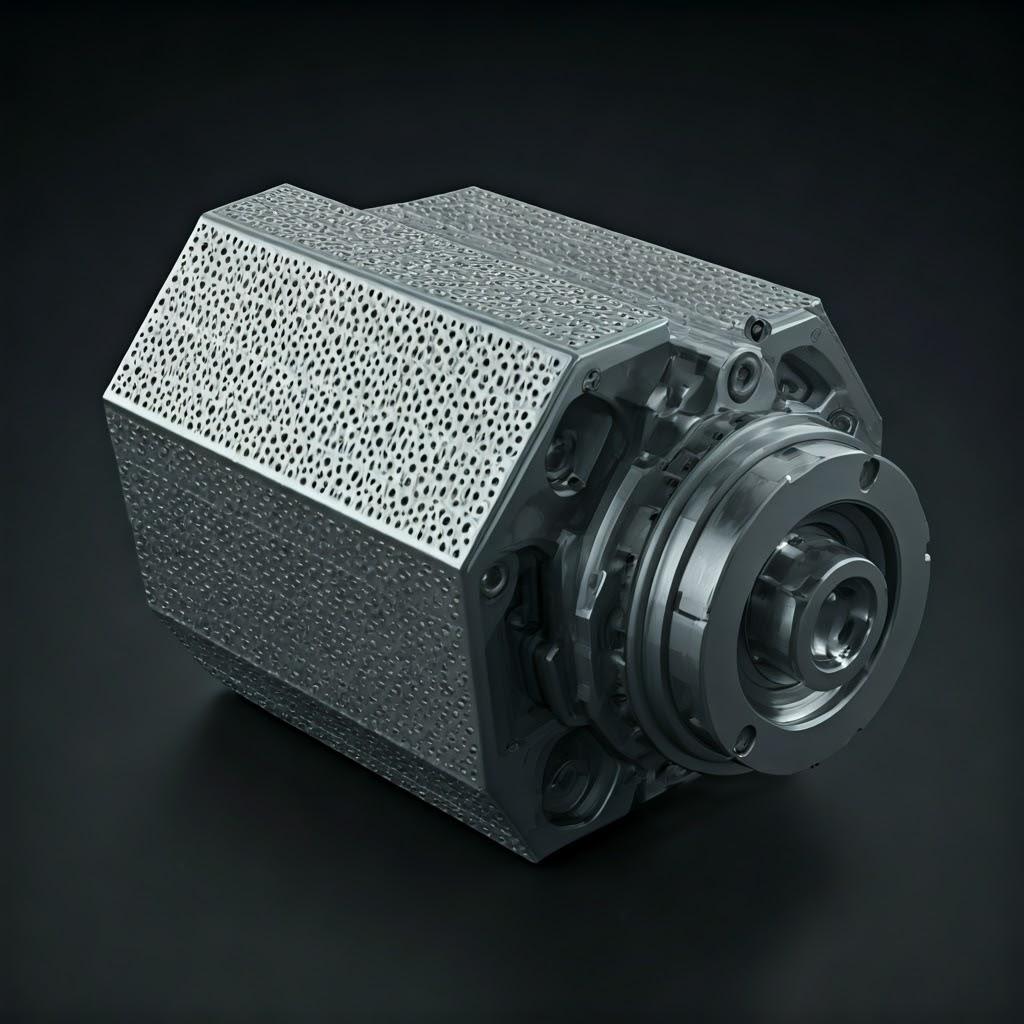
Design Considerations for Additive Manufacturing of High-Temp Protection Tiles
Designing high-temp protection tile components for metal 3D printing requires a different mindset compared to traditional manufacturing. To fully leverage the capabilities of additive manufacturing and ensure optimal performance, several key design considerations must be taken into account. These include optimizing the component’s geometry for heat dissipation, minimizing material usage while maintaining structural integrity, and designing for the specific powder bed fusion process being used.
Geometry Optimization for Thermal Management
One of the significant advantages of metal 3D printing is the ability to create complex internal features. For thermal protection tiles, this opens up possibilities for incorporating intricate cooling channels or lattice structures within the component. These internal designs can significantly enhance heat transfer and dissipation, allowing the tile to withstand higher temperatures for longer durations. Conformal cooling channels, for instance, can be designed to follow the contours of the heated surface, providing more efficient and uniform cooling compared to traditional drilled channels. Similarly, lightweight lattice structures can offer structural support while minimizing material and allowing for air or fluid flow to aid in cooling. When designing these internal features, it’s crucial to consider the flow characteristics of the chosen cooling medium and the pressure drop it will experience. Simulation tools can be invaluable in optimizing these designs for maximum thermal efficiency.
Minimizing Material Usage and Weight Reduction
In industries like aerospace and automotive, weight is a critical factor. Metal 3D printing allows for the creation of lightweight yet structurally sound components through topology optimization and the use of lattice structures. Topology optimization is a computational method that iteratively removes material from a design in non-critical areas, based on the applied loads and constraints, resulting in a part with the minimum possible weight while still meeting performance requirements. Lattice structures, which are periodic cellular structures, offer a high strength-to-weight ratio and can be tailored to specific load-bearing requirements. By strategically incorporating these design techniques, the weight of high-temp protection tiles can be significantly reduced without compromising their thermal protection capabilities or structural integrity. This not only improves the overall efficiency of the system but also reduces material costs.
Design for Powder Bed Fusion (PBF) Processes
The specific metal 3D printing process used, such as Selective Laser Melting (SLM) or Electron Beam Melting (EBM), will influence design considerations. For SLM, support structures are typically required to prevent warping and ensure proper heat dissipation during the build process. The design should account for the placement and removal of these supports, aiming for a balance between adequate support and ease of post-processing. EBM, on the other hand, often requires fewer support structures due to the higher build temperatures and the support provided by the surrounding powder. However, EBM may have different limitations in terms of feature resolution and surface finish. Understanding the specific capabilities and limitations of the chosen PBF process is crucial for designing functional and manufacturable high-temp protection tile components. This includes considering factors like minimum feature size, overhang angles, and the orientation of the part on the build platform. Collaborating with experienced metal 3D printing service providers like Metal3DP, who have a deep understanding of these process parameters (https://met3dp.com/printing-methods/), can ensure that designs are optimized for the chosen manufacturing method, leading to higher quality and more efficient production.
Tolerance, Surface Finish, and Dimensional Accuracy of 3D Printed Tiles
Achieving the required tolerance, surface finish, and dimensional accuracy is paramount for the functional integration of high-temp protection tile components within larger systems. Metal 3D printing technologies have advanced significantly in their ability to produce parts with tight tolerances and good surface finishes, but these aspects are influenced by several factors, including the chosen printing process, material, and post-processing techniques.
Achievable Tolerances in Metal 3D Printing
The achievable tolerances in metal 3D printing vary depending on the specific technology and machine used. Powder Bed Fusion (PBF) processes like SLM and EBM generally offer good dimensional accuracy, with typical tolerances ranging from ±0.1 to ±0.05 mm for smaller features. Larger dimensions may experience slightly larger deviations. Factors such as part orientation on the build platform, material shrinkage during solidification, and the calibration of the 3D printer can all affect the final dimensional accuracy. It’s crucial to discuss tolerance requirements with your metal 3D printing service provider early in the design process to ensure that the chosen technology and design approach can meet these specifications. At Metal3DP, our industry-leading accuracy ensures that your high-temp protection tile components are manufactured to the precise tolerances required for their critical applications.
Surface Finish Characteristics
The as-built surface finish of metal 3D printed parts is typically rougher compared to parts produced by subtractive manufacturing methods like CNC machining. In PBF processes, the surface roughness is influenced by the size of the metal powder particles and the layer thickness used during printing. Typical surface roughness (Ra) values for SLM and EBM parts can range from 5 to 20 µm. For many high-temp protection tile applications, this as-built surface finish may be acceptable. However, if smoother surfaces are required for improved aerodynamic performance or to facilitate coating adhesion, post-processing techniques such as polishing, abrasive blasting, or machining can be employed. The choice of post-processing will depend on the specific requirements of the application and the desired surface finish.
Factors Affecting Dimensional Accuracy
Several factors can influence the dimensional accuracy of metal 3D printed components. Material properties, particularly the thermal expansion and contraction behavior during the printing process, play a significant role. Complex geometries with varying cross-sections can also be more prone to distortions. Proper design for additive manufacturing, including the strategic placement of support structures and consideration of build orientation, can help mitigate these issues. Furthermore, the accuracy and calibration of the 3D printing equipment are critical. Reputable metal 3D printing service providers like Metal3DP maintain strict quality control measures and utilize advanced equipment to ensure consistent and accurate results. Post-processing steps, if required, must also be carefully controlled to avoid compromising the dimensional accuracy achieved during printing. By understanding these factors and working with an experienced partner, engineers and procurement managers can ensure that their 3D printed high-temp protection tile components meet the stringent dimensional requirements of their applications.
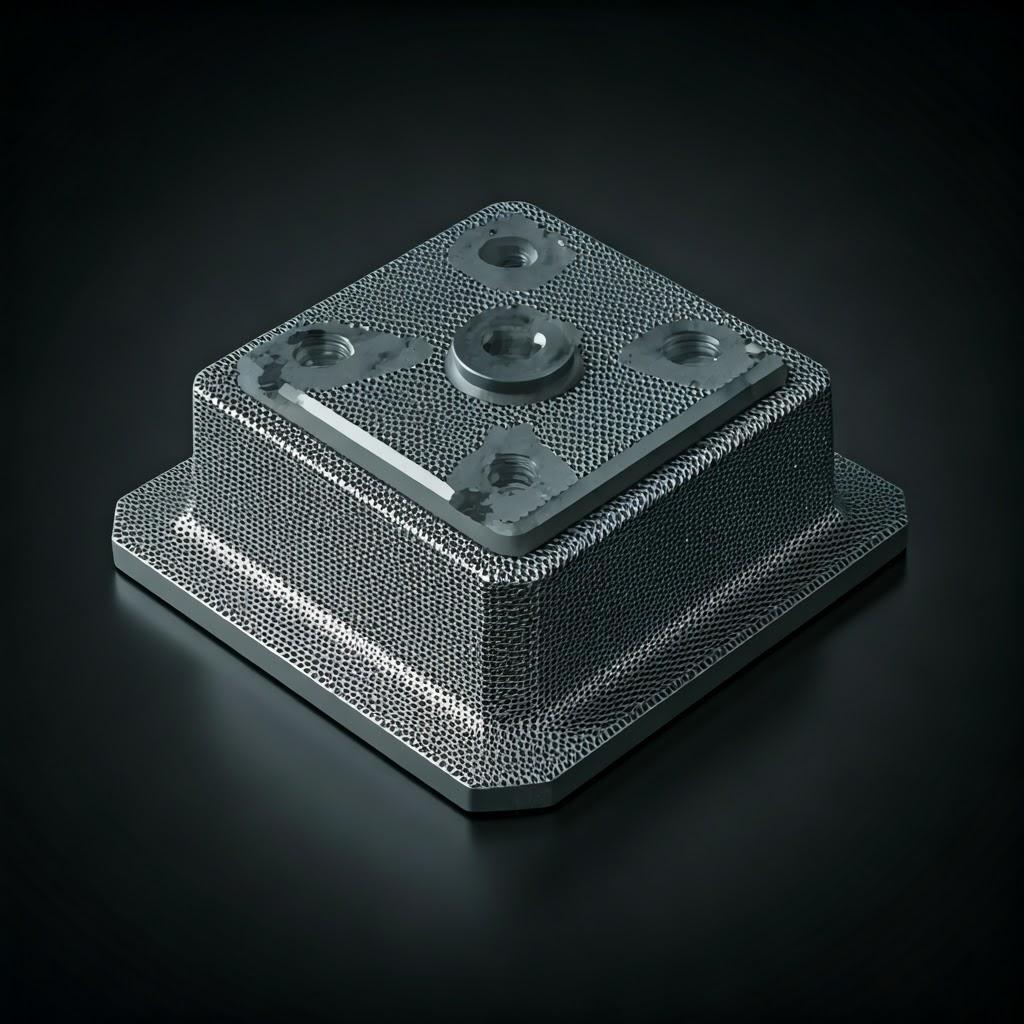
Post-Processing Requirements for Metal 3D Printed Tiles
While metal 3D printing offers near-net-shape manufacturing capabilities, post-processing steps are often necessary to achieve the final desired properties, surface finish, and dimensional accuracy of high-temp protection tile components. Common post-processing requirements include heat treatment, support removal, surface finishing, and specialized coatings.
Heat Treatment for Property Enhancement
Heat treatment is a critical post-processing step for many metal 3D printed parts, including high-temp protection tiles made from materials like IN625 and Haynes 282. The rapid solidification inherent in powder bed fusion processes can result in non-equilibrium microstructures with residual stresses. Heat treatment processes, such as stress relieving, annealing, hot isostatic pressing (HIP), or solution annealing followed by aging, are employed to homogenize the microstructure, reduce residual stresses, and optimize the mechanical properties of the material. For high-temperature applications, specific heat treatment cycles are essential to ensure that the components can withstand the intended operating temperatures and loads without creep or failure. The specific heat treatment parameters will depend on the alloy and the desired final properties.
Destek Yapısının Kaldırılması
Powder Bed Fusion (PBF) processes often require the use of support structures to anchor the part to the build plate, prevent warping due to thermal stresses, and support overhanging features. Once the printing process is complete, these support structures need to be removed. The method of support removal depends on the material and the design of the supports. For some materials, supports can be manually broken off, while others may require specialized tools or machining. Careful design of the support structures during the initial design phase can significantly impact the ease and cost of removal. Minimizing the need for extensive support structures through optimized part orientation and design features is a key consideration in additive manufacturing.
Surface Finishing Techniques
As mentioned earlier, the as-built surface finish of metal 3D printed parts can be relatively rough. For applications requiring smoother surfaces, several post-processing techniques are available. These include:
- Media Blasting: Using abrasive media to remove loosely adhered particles and reduce surface roughness.
- Parlatma: Mechanical or chemical polishing to achieve a smoother, often reflective surface.
- Machining (CNC): Precision machining to achieve tight tolerances and smooth surface finishes on critical areas.
- Vapor Smoothing: A chemical process that smooths surfaces by selectively melting the outer layers.
The choice of surface finishing technique will depend on the specific requirements of the application, such as aerodynamic performance, sealing requirements, or aesthetic considerations.
Specialized Coatings for Enhanced Performance
In demanding high-temperature environments, applying specialized coatings can further enhance the performance and lifespan of metal 3D printed protection tiles. These coatings can provide additional resistance to oxidation, corrosion, and wear. Examples of such coatings include:
- Termal Bariyer Kaplamalar (TBC'ler): Typically ceramic-based coatings that provide thermal insulation, allowing the metallic substrate to operate at lower temperatures.
- Hard Coatings: Such as carbides or nitrides, to improve wear resistance in abrasive environments.
- Corrosion-Resistant Coatings: To protect against chemical attack in harsh operating conditions.
The selection and application of these coatings require specialized expertise to ensure proper adhesion and performance at high temperatures. Collaborating with a metal 3D printing service provider that offers comprehensive post-processing services, including heat treatment, surface finishing, and specialized coatings, can streamline the manufacturing process and ensure the final components meet the required specifications. Metal3DP’s comprehensive solutions (https://met3dp.com/) encompass these critical post-processing steps, ensuring the delivery of high-performance, ready-to-use high-temp protection tile components.
Common Challenges and How to Avoid Them in 3D Printing High-Temp Tiles
While metal 3D printing offers numerous advantages for producing high-temp protection tile components, several challenges can arise during the process. Understanding these potential issues and implementing appropriate strategies to avoid them is crucial for achieving high-quality, reliable parts. Common challenges include warping and distortion, issues with support removal, and porosity within the printed material.
Warping and Distortion Due to Thermal Stresses
One of the primary challenges in metal 3D printing, particularly with high-temperature alloys, is warping and distortion. These issues arise due to the significant thermal gradients and residual stresses that can develop during the layer-by-layer build process. As each layer is solidified, it contracts upon cooling, and if this contraction is constrained by previously solidified layers or the build plate, internal stresses build up. These stresses can lead to deformation of the part, especially in thin-walled sections or components with large flat areas, which are common in protection tile designs.
Strategies to Minimize Warping and Distortion:
- Optimized Part Orientation: Orienting the part on the build platform in a way that minimizes the cross-sectional area of each layer and reduces the overhang of unsupported features can help mitigate thermal stresses.
- Strategic Support Placement: Properly designed and strategically placed support structures not only provide mechanical support but also help to dissipate heat and anchor the part to the build plate, reducing the likelihood of warping. Simulation tools can aid in optimizing support design.
- Controlled Build Chamber Temperature: Maintaining a consistent and elevated build chamber temperature, especially in processes like EBM, reduces the temperature gradient between the solidified layer and the surrounding powder bed, thus minimizing thermal stresses.
- Stress Relief Heat Treatment: Post-printing stress relief heat treatment is often essential to reduce residual stresses within the part, thereby improving its dimensional stability and mechanical properties.
- Build Plate Preheating: Preheating the build plate can reduce the temperature differential between the first layer and the subsequent layers, leading to more uniform solidification and reduced warping.
Issues with Support Structure Removal
Support structures, while necessary for many geometries in metal 3D printing, can sometimes be challenging to remove without damaging the part’s surface. The interface between the support and the part can be particularly problematic. Improperly designed or overly robust supports can be difficult to detach, potentially leaving behind surface defects or requiring extensive post-processing.
Strategies for Easier Support Removal:
- Optimized Support Design: Using thinner support structures with breakaway points or designing supports with a less dense interface with the part can facilitate easier removal.
- Material Selection for Supports: In some cases, using a different material for the supports that has a lower bonding strength to the part material can aid in removal.
- Proper Tooling and Techniques: Employing the correct tools and techniques for support removal, such as specialized cutting tools, wire EDM, or dissolvable supports (where applicable), is crucial to avoid damaging the part.
- Design for Minimal Supports: Modifying the part design to minimize the need for supports through self-supporting angles and optimized orientation can significantly reduce post-processing effort.
Porosity in Metal 3D Printed Parts
Porosity, or the presence of voids within the printed material, can negatively impact the mechanical properties and performance of high-temp protection tiles, especially their resistance to thermal stress and oxidation. Porosity can arise from various factors, including insufficient laser or electron beam power, improper powder flow and packing, or inadequate shielding gas.
Strategies to Minimize Porosity:
- Optimize Edilmiş Süreç Parametreleri: Carefully calibrating and optimizing the printing parameters, such as laser power, scan speed, layer thickness, and powder feed rate, is essential for achieving dense, fully consolidated parts.
- Yüksek Kaliteli Metal Tozları: Using high-quality metal powders with good sphericity and flowability, like those produced by Metal3DP’s advanced powder making system, ensures uniform packing and consistent melting.
- Proper Shielding Gas Flow: Maintaining an inert atmosphere with proper shielding gas flow during the printing process prevents oxidation and ensures a clean melt pool, reducing the formation of porosity.
- Sıcak İzostatik Presleme (HIP): Post-printing HIP treatment involves subjecting the parts to high pressure and temperature in an inert atmosphere, which effectively eliminates internal porosity and further enhances the material’s density and mechanical properties.
By understanding these common challenges and implementing the recommended avoidance strategies, manufacturers can leverage the full potential of metal 3D printing to produce high-quality, high-performance thermal protection tile components. Metal3DP’s expertise in metal additive manufacturing and our commitment to quality control help our customers navigate these challenges effectively.
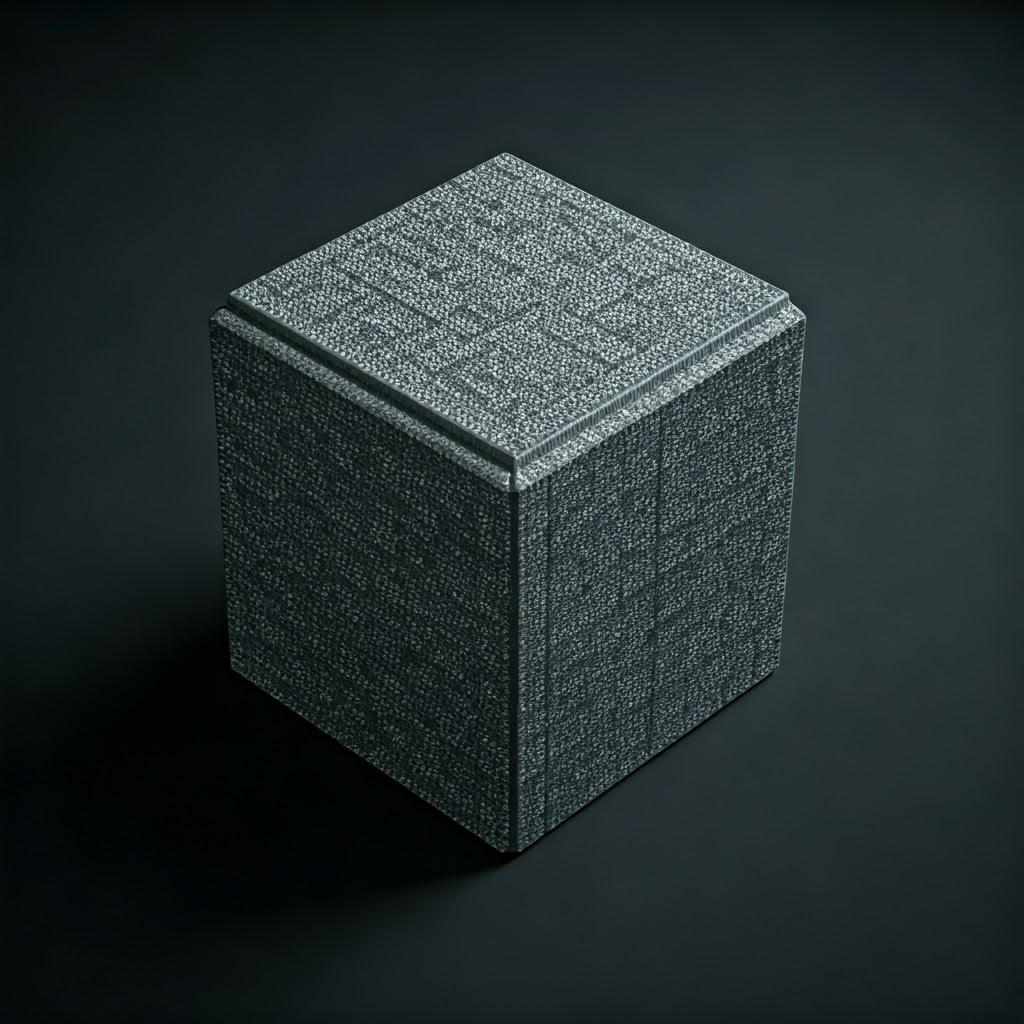
How to Choose the Right Metal 3D Printing Service Provider
Selecting the right metal 3D printing service provider is a critical decision that can significantly impact the success of your project, especially when it comes to producing high-performance components like high-temp protection tiles. Several key factors should be considered when evaluating potential suppliers to ensure they can meet your specific requirements for material capabilities, quality standards, and project timelines.
Evaluating Material Capabilities and Expertise
The first and foremost consideration is whether the service provider has experience working with the specific high-temperature alloys required for your application, such as IN625 and Haynes 282. They should possess a deep understanding of the material properties, the optimal printing parameters for these alloys, and the necessary post-processing steps to achieve the desired performance characteristics. Inquire about their material portfolio, their experience with similar applications, and whether they can provide material data sheets and testing reports. A provider like Metal3DP, with our in-house expertise in advanced metal powders (https://met3dp.com/product/), offers a significant advantage in this regard.
Assessing Quality Standards and Certifications
Quality is paramount, especially for components used in critical applications. Ensure that the service provider adheres to stringent quality control processes and holds relevant industry certifications, such as ISO 9001, AS9100 (for aerospace), or ISO 13485 (for medical devices). These certifications indicate a commitment to maintaining high standards in their operations and the quality of their output. Ask about their inspection procedures, dimensional accuracy verification methods, and non-destructive testing capabilities.
Understanding Technology and Equipment
Different metal 3D printing technologies (e.g., SLM, EBM, DED) have varying strengths and limitations in terms of achievable tolerances, surface finish, build volume, and cost-effectiveness. Understand which technologies the service provider utilizes and whether their equipment is well-maintained and calibrated. For high-temp protection tiles, precision and the ability to handle complex geometries are often crucial. Metal3DP’s industry-leading print volume, accuracy, and reliability ensure that we can handle a wide range of demanding applications.
Reviewing Experience and Case Studies
A reputable service provider should have a proven track record of successfully completing projects similar to yours. Ask for case studies or references that demonstrate their experience in producing high-performance metal parts for your industry. Their portfolio should showcase their capabilities and the quality of their work.
Evaluating Lead Times and Production Capacity
Understand the service provider’s typical lead times for projects of your size and complexity. Their production capacity should be sufficient to meet your current and future needs. Inquire about their workflow, from design to post-processing and delivery, to ensure it aligns with your project timelines.
Considering Cost Structure and Transparency
Obtain a detailed breakdown of the costs involved, including printing, material, support removal, post-processing, and any additional services. A transparent pricing structure will help you understand the overall investment and avoid unexpected costs. Compare quotes from multiple providers, but remember that the cheapest option may not always be the best, especially if it compromises quality or material expertise.
Assessing Communication and Customer Support
Effective communication and responsive customer support are essential for a smooth and successful project. The service provider should be readily available to answer your questions, provide technical guidance, and keep you informed throughout the manufacturing process.
By carefully evaluating these factors, you can choose a metal 3D printing service provider that is the right fit for your high-temp protection tile component needs, ensuring high quality, reliable performance, and a successful partnership. Contact Metal3DP (https://met3dp.com/about-us/) to explore how our comprehensive metal additive manufacturing solutions can power your organization’s goals.
Cost Factors and Lead Time for 3D Printed Tiles
Understanding the factors that influence the cost and lead time for metal 3D printed high-temp protection tile components is essential for effective project planning and budgeting. Several variables come into play, including material costs, build time, post-processing requirements, and the complexity of the design.
Malzeme Maliyetleri
The cost of the metal powder is a significant factor in the overall price of a 3D printed part. High-performance alloys like IN625 and Haynes 282 are typically more expensive than standard metals due to their complex compositions and specialized manufacturing processes. The quantity of material required for the part, which is influenced by its size and density, will directly impact the material cost. Optimizing the design to minimize material usage, as discussed earlier, can help mitigate this factor.
Build Time and Machine Utilization
The time it takes to 3D print a component depends on several factors, including the size and complexity of the part, the layer thickness used, and the number of parts being printed simultaneously on the build platform. Longer build times translate to higher machine utilization costs. Complex geometries or large volumes will naturally require more time to print. Efficient nesting of multiple parts on the build platform can help to optimize machine utilization and reduce the cost per part.
İşlem Sonrası Maliyetler
As outlined previously, post-processing steps such as heat treatment, support removal, surface finishing, and specialized coatings can add significantly to the overall cost and lead time. The complexity and extent of these processes will depend on the specific requirements of the application. For instance, intricate surface finishing or the application of specialized thermal barrier coatings will involve additional time and expense.
Design Complexity and Optimization
The complexity of the design can indirectly affect both cost and lead time. Highly intricate geometries may require more support structures, leading to increased material usage and post-processing time. Design iterations and optimizations aimed at reducing material, simplifying support structures, or improving printability can influence the overall cost and timeline of the project.
Üretim Hacmi
The quantity of parts being produced can also impact the cost per unit. Generally, larger production volumes can lead to economies of scale, potentially reducing the per-part cost. However, for very high volumes, traditional manufacturing methods might become more cost-effective than 3D printing.
Lead Time Considerations
The total lead time for 3D printed high-temp protection tiles encompasses several stages:
- Design and Optimization: Initial design work and any necessary optimizations for additive manufacturing.
- Material Sourcing: Procurement of the required metal powder, especially for specialized alloys.
- Baskı Süresi: The duration of the 3D printing process itself.
- İşlem sonrası: Time required for heat treatment, support removal, surface finishing, and coatings.
- Quality Control and Inspection: Thorough inspection to ensure the parts meet the required specifications.
- Shipping and Delivery: The time taken to transport the finished parts.
Lead times can vary significantly depending on the complexity of the project, the availability of materials, the service provider’s capacity, and the required post-processing. It’s crucial to discuss lead time expectations with your metal 3D printing service provider early in the project to ensure they align with your schedule. Metal3DP is committed to providing efficient and transparent timelines for the production of high-quality metal 3D printed parts.
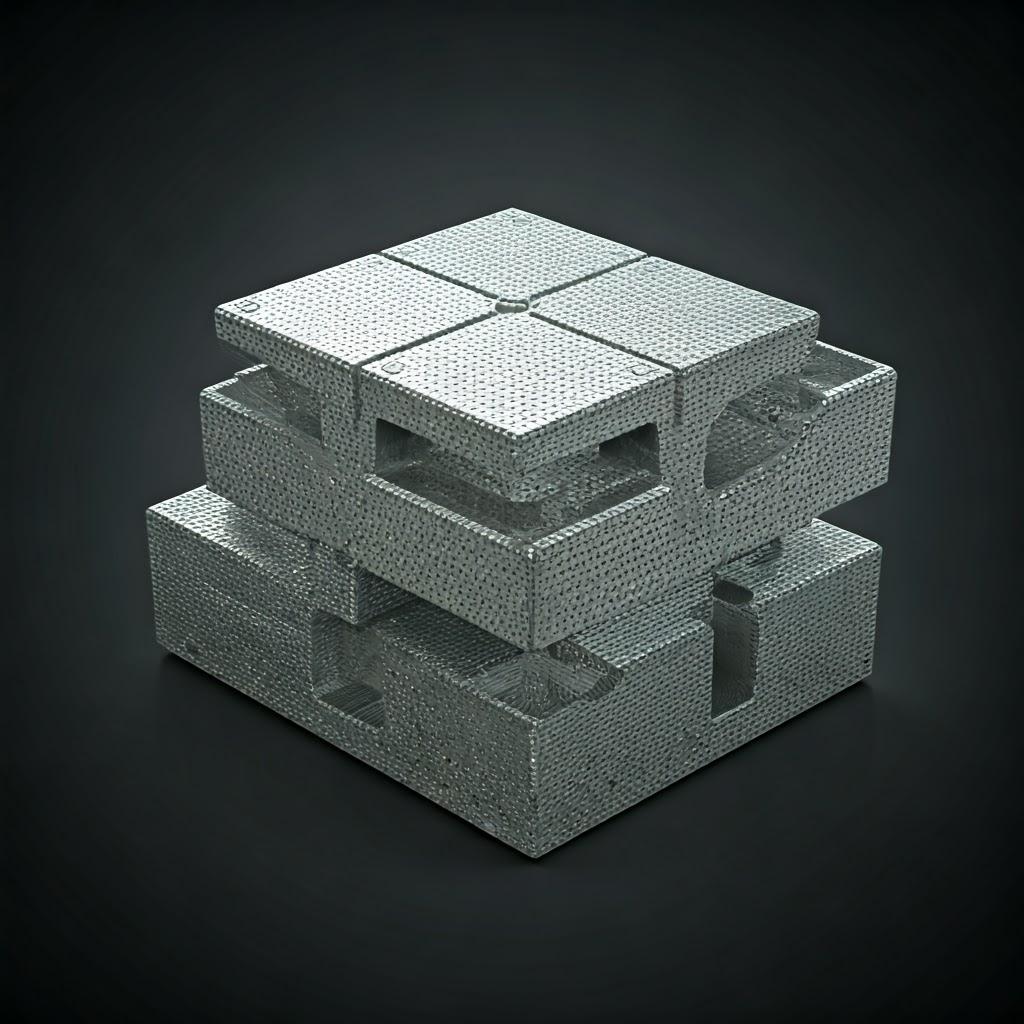
Sıkça Sorulan Sorular (SSS)
What are the typical applications of metal 3D printed high-temp protection tiles?
Metal 3D printed high-temp protection tiles find critical applications in aerospace (engine components, heat shields), automotive (exhaust systems, turbocharger heat shields), industrial manufacturing (furnace linings, heat exchangers), and specialized medical equipment (sterilization devices). Their ability to be customized for complex geometries and manufactured from high-performance alloys like IN625 and Haynes 282 makes them ideal for demanding thermal management scenarios.
Can metal 3D printed tiles offer better thermal protection than traditionally manufactured ones?
Yes, in many cases. Metal 3D printing allows for design optimizations such as integrated cooling channels and lightweight lattice structures that can enhance heat dissipation and reduce weight compared to traditionally manufactured tiles. Furthermore, the ability to precisely control material composition and microstructure through advanced metal powders and optimized printing parameters can lead to superior thermal resistance and durability.
What is the typical lead time for a small batch of custom-designed high-temp protection tiles?
Lead times can vary depending on the complexity of the design, the availability of the chosen metal powder, the printing technology used, and the required post-processing steps. For a small batch of custom-designed high-temp protection tiles, the lead time could range from a few weeks to several months. It is best to consult with a metal 3D printing service provider like Metal3DP to get a precise estimate based on your specific requirements.
Conclusion – Embracing the Future of Thermal Management with Metal 3D Printing
Metal 3D printing is revolutionizing the way high-temp protection tile components are designed and manufactured. The ability to create complex, optimized geometries from advanced materials like IN625 and Haynes 282 offers significant advantages in terms of performance, weight reduction, and customization for demanding applications across aerospace, automotive, medical, and industrial sectors. By understanding the design considerations, achievable tolerances, post-processing requirements, and potential challenges, engineers and procurement managers can effectively leverage this transformative technology. Choosing the right metal 3D printing service provider, one with expertise in high-temperature alloys and a commitment to quality, is crucial for success. At Metal3DP, we are dedicated to providing cutting-edge metal additive manufacturing solutions, combining our advanced powder technology, industry-leading printing capabilities, and comprehensive post-processing services to empower our customers to push the boundaries of thermal management. Contact us today to explore how our expertise can help you realize the full potential of metal 3D printed high-temp protection tile components for your critical applications.
Paylaş
MET3DP Technology Co, LTD, merkezi Qingdao, Çin'de bulunan lider bir katmanlı üretim çözümleri sağlayıcısıdır. Şirketimiz, endüstriyel uygulamalar için 3D baskı ekipmanları ve yüksek performanslı metal tozları konusunda uzmanlaşmıştır.
İşletmeniz için en iyi fiyatı ve özelleştirilmiş Çözümü almak için sorgulayın!
İlgili Makaleler
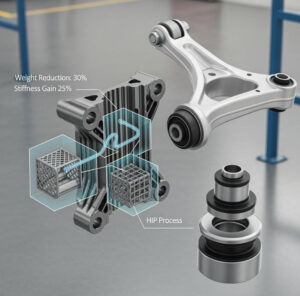
Metal 3D Printed Subframe Connection Mounts and Blocks for EV and Motorsport Chassis
Daha Fazla Oku "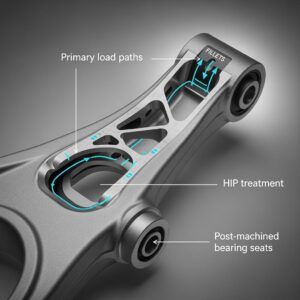
Metal 3D Printing for U.S. Automotive Lightweight Structural Brackets and Suspension Components
Daha Fazla Oku "Met3DP Hakkında
Son Güncelleme
Bizim Ürünümüz
BİZE ULAŞIN
Herhangi bir sorunuz var mı? Bize şimdi mesaj gönderin! Mesajınızı aldıktan sonra tüm ekibimizle talebinize hizmet edeceğiz.