AlSi10Mg for Aerospace Brackets in Metal 3D Printing
İçindekiler
Introduction: The Critical Role of Aerospace Brackets and Additive Manufacturing
The aerospace industry operates at the zenith of engineering ambition, demanding unparalleled levels of safety, performance, and efficiency. Every component, regardless of its perceived simplicity, plays a vital role in the complex symphony of flight. Aerospace brackets, often unassuming in appearance, are prime examples of such critical components. These parts serve essential functions, from mounting crucial systems and supporting structural loads to routing vital lines for fuel, hydraulics, and electronics. Their design and manufacture are governed by the strictest standards, where failure is not an option, and optimization is a constant pursuit.
For decades, the production of aerospace brackets relied heavily on traditional manufacturing methods like CNC machining from billet or investment casting. While reliable, these methods often come with significant limitations, particularly concerning design complexity, material waste, and lead times. Machining intricate shapes can be time-consuming and generate substantial scrap material, while casting involves expensive tooling and can limit design possibilities. Furthermore, the relentless drive for improved aircraft performance hinges significantly on weight reduction. Lighter aircraft consume less fuel, offer greater payload capacity, or achieve longer range – critical factors influencing operational costs and mission capabilities. This imperative for lightweighting places immense pressure on designers to optimize every component, including brackets, without compromising structural integrity or safety.
Enter metal additive manufacturing (AM), commonly known as metal 3D baskı. This transformative technology is rapidly reshaping the landscape of aerospace component manufacturing. By building parts layer by layer directly from digital models using fine metal powders, AM unlocks unprecedented design freedom and enables the creation of highly optimized, lightweight structures that were previously impossible or prohibitively expensive to produce. Among the growing portfolio of materials suitable for aerospace AM, AlSi10Mg, an aluminum alloy, has emerged as a prominent choice for manufacturing aerospace brackets. Its compelling combination of low density, good mechanical properties, excellent processability via techniques like Laser Powder Bed Fusion (LPBF), and relative cost-effectiveness makes it ideal for a wide range of non-critical and semi-critical bracket applications.
This technological shift allows aerospace engineers and procurement managers to rethink bracket design and sourcing. It enables the production of parts that are not only lighter and potentially stronger but can also be manufactured faster, with less material waste, and with greater supply chain flexibility. As a leader in metal additive manufacturing solutions, including advanced printing systems and high-quality 3D printing metallic powders, Met3dp is at the forefront of this revolution, empowering aerospace companies to leverage the full potential of AM for components like brackets. This article delves into the specifics of using AlSi10Mg for aerospace brackets via metal 3D printing, exploring applications, advantages, material considerations, design principles, and crucial factors for successful implementation, guiding engineers and B2B procurement specialists in navigating this exciting technological frontier. The focus is on providing actionable insights for aerospace bracket manufacturing, understanding the role of additive manufacturing aerospace components, başarmak lightweight aerospace parts, and mastering AlSi10Mg 3D printing.
Applications: Where are 3D Printed AlSi10Mg Brackets Used?
The versatility of metal 3D printing, combined with the favorable properties of AlSi10Mg, opens up a vast range of applications for additively manufactured brackets within the aerospace sector and beyond. While traditionally manufactured brackets remain prevalent, AM is rapidly gaining traction for specific use cases where its unique advantages offer significant value. Procurement managers seeking innovative aerospace component suppliers are increasingly turning to AM specialists capable of delivering these optimized parts.
Specific Aerospace Bracket Examples:
- Structural Support Brackets: These brackets are integral to the airframe, contributing to load distribution and structural integrity in areas like fuselage frames, wing ribs, and empennage structures. While flight-critical primary structures often require extensive certification with materials like Titanium, AlSi10Mg is finding use in secondary structural applications where its strength-to-weight ratio offers significant benefits over heavier traditional designs. Topology optimization allows these brackets to efficiently handle complex load paths with minimal material.
- System Mounting Brackets: Aircraft are packed with complex systems, all requiring secure mounting. AlSi10Mg AM brackets excel here:
- Avionics Trays and Mounts: Securely holding sensitive electronic equipment, often requiring vibration damping features that can be integrated into the AM design.
- Hydraulic Line Brackets: Routing and securing hydraulic lines, often involving complex geometries to navigate tight spaces within the airframe or landing gear bays. AM allows for customized routing paths.
- Fuel Line Brackets: Similar to hydraulic lines, requiring secure mounting and potentially specific shapes to interface with other components.
- Electrical Harness Brackets/Clamps: Organizing and securing complex wiring looms throughout the aircraft. AM enables the creation of intricate clamp geometries tailored to specific harness diameters and routing paths.
- Ducting Supports: Holding environmental control system (ECS) ducts or anti-icing system ducts.
- Interior Brackets: Used in cabin interiors for mounting seats, overhead bins, galley equipment, or partitions. Weight savings here directly contribute to fuel efficiency over the aircraft’s lifetime. AM allows for aesthetically pleasing, lightweight designs.
- Engine Component Brackets (Non-Hot Section): While high-temperature engine sections demand superalloys or titanium, cooler sections can utilize AlSi10Mg brackets for mounting accessories, sensors, or external tubing.
Functional Requirements Met by AlSi10Mg:
The suitability of AlSi10Mg for these applications stems from its ability to meet key functional requirements:
- Load-Bearing Capacity: After appropriate heat treatment (typically T6), AlSi10Mg offers good strength and stiffness, sufficient for many secondary structural and system mounting roles.
- Vibration Resistance: AM allows for the design of brackets with integrated damping features or optimized geometries that minimize stress concentrations under vibration, crucial for avionics and system mounts.
- Termal Yönetim: AlSi10Mg possesses good thermal conductivity compared to titanium or steel alloys. This can be advantageous for brackets mounting heat-generating equipment, helping to dissipate heat more effectively.
- Karmaşık Geometri: AM readily produces the organic, intricate shapes often required to fit brackets into constrained spaces within an aircraft structure or to consolidate multiple functions into a single part.
Beyond Aerospace:
The advantages driving the adoption of 3D printed AlSi10Mg brackets in aerospace are equally relevant in other demanding industries:
- High-Performance Automotive/Motorsport: Weight reduction is paramount. Brackets for mounting engine accessories, suspension components, or electronic units benefit significantly from AlSi10Mg AM.
- Drones/Unmanned Aerial Vehicles (UAVs): Every gram saved extends flight time or increases payload capacity. Structural frame components, sensor mounts, and landing gear brackets are prime candidates. UAV bracket manufacturers are increasingly adopting AM.
- Satellites: Launch costs are directly tied to mass. Lightweighting brackets for mounting antennas, solar panels, or internal instruments using AlSi10Mg is highly beneficial.
- Industrial Equipment: Custom brackets for mounting sensors, actuators, or fixtures in specialized machinery can be produced quickly and cost-effectively without tooling.
Understanding these diverse AlSi10Mg applications ve metal AM use cases is crucial for designers and B2B tedarikçileri looking to leverage this technology. The ability to produce highly customized, 3D printed structural components on-demand reshapes sourcing strategies and enables performance improvements across multiple high-tech sectors.
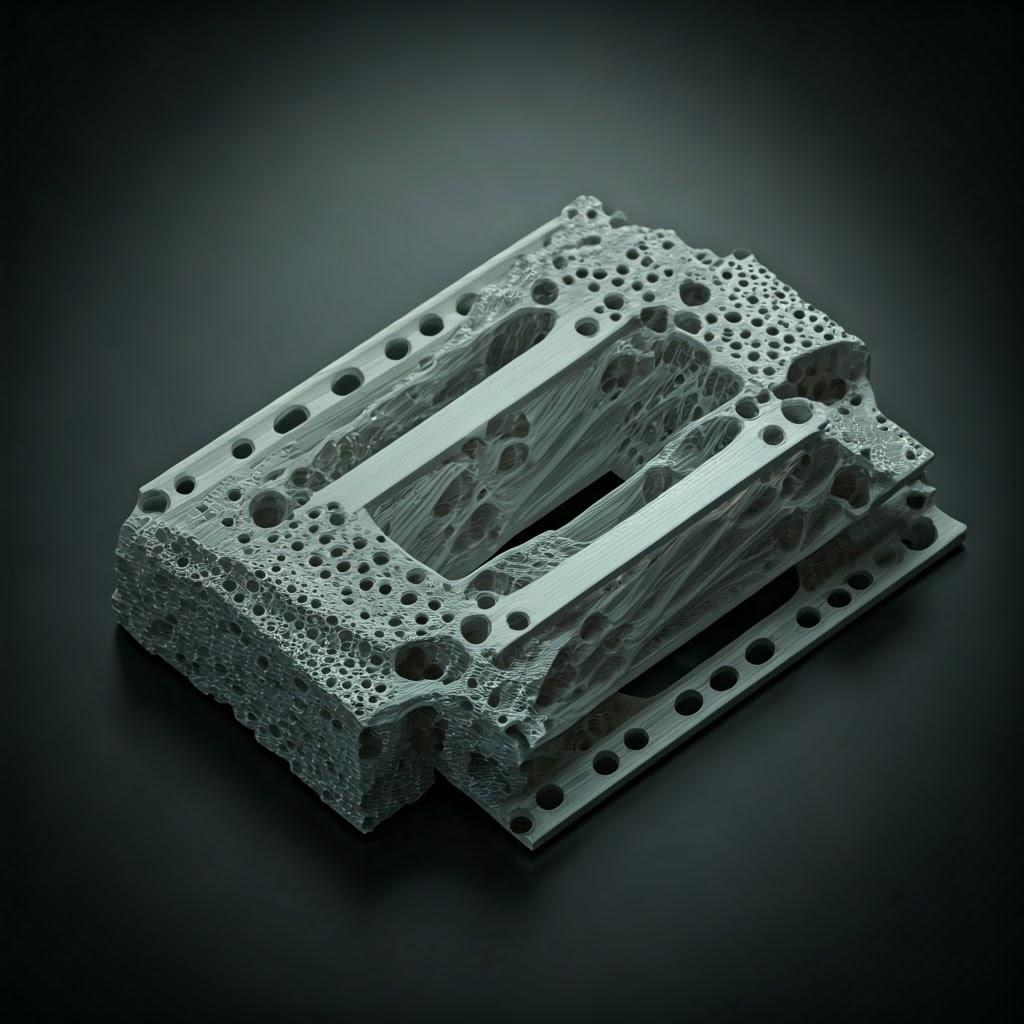
Why Metal 3D Printing for Aerospace Brackets? Advantages Over Traditional Methods
The decision to adopt metal additive manufacturing for aerospace brackets isn’t merely about embracing novelty; it’s driven by tangible, quantifiable advantages over established methods like CNC machining and investment casting. For engineers focused on performance and procurement managers evaluating total cost of ownership and supply chain resilience, the benefits of AM are compelling. Let’s explore these advantages in detail, highlighting why savvy manufacturers and aerospace component manufacturing partners are increasingly integrating AM.
1. Unprecedented Design Freedom:
- Topology Optimization: This is arguably the most transformative advantage. Using specialized software, engineers can define load cases, constraints, and design spaces, allowing algorithms to iteratively remove material from non-load-bearing areas. The result is highly organic, skeletal structures that are optimized for maximum stiffness and strength with minimal weight. These intricate geometries are often impossible or impractical to achieve using subtractive machining (which involves cutting material away) or casting (which relies on molds). Topology optimization routinely yields weight savings of 20-60% or more for brackets compared to traditionally designed counterparts, directly impacting fuel efficiency and payload capacity.
- Parça Konsolidasyonu: Traditional designs often require multiple simple parts (brackets, shims, fasteners) to be assembled to perform a complex mounting or support function. Metal AM allows designers to consolidate these multiple components into a single, complex, monolithic part. This dramatically reduces:
- Part Count: Simplifies inventory, logistics, and bill of materials (BOM).
- Assembly Time & Labor: Reduces the need for manual assembly and associated costs.
- Ağırlık: Eliminates the need for heavy fasteners (bolts, rivets).
- Potential Failure Points: Fewer joints and interfaces mean improved reliability.
- Complex Geometries & Internal Features: AM builds parts layer by layer, enabling the creation of internal channels (e.g., for cooling or conformal wiring), complex curved surfaces, and thin-walled structures without the limitations imposed by cutting tools or mold extraction. This allows for brackets with integrated functionality beyond simple mounting.
2. Significant Weight Reduction:
As mentioned, topology optimization is a primary driver, but AM enables weight reduction through other means as well:
- Use of Lightweight Materials: AM processes like LPBF work exceptionally well with inherently lightweight aerospace alloys like AlSi10Mg and Ti-6Al-4V.
- Kafes Yapılar: AM allows for the incorporation of internal lattice or cellular structures within solid parts. These structures significantly reduce mass while maintaining high levels of stiffness and strength, ideal for optimizing bracket performance beyond what simple topology optimization can achieve. Comparing metal 3D printing vs CNC machining, subtractive methods start with a solid block and remove material, often leaving behind bulk that isn’t structurally necessary but is difficult to machine away. AM builds only the necessary material, leading to inherently more efficient designs.
3. Accelerated Lead Times & Rapid Prototyping:
- Alet Eliminasyonu: Traditional casting requires significant lead time (weeks or months) and cost to design and produce molds. CNC machining requires programming and potentially complex fixture design. AM requires only a digital CAD file, drastically reducing the setup time.
- Hızlı Prototipleme: Producing functional prototypes of bracket designs takes days with AM, compared to weeks or months traditionally. This allows engineers to iterate designs much faster, test functionality quickly, and accelerate the product development cycle. This agility is crucial in the fast-paced aerospace sector. Rapid prototyping aerospace parts allows for faster design validation and quicker progression to final production.
- İsteğe Bağlı Üretim: AM enables the production of spare parts or small series batches on demand, reducing the need for large inventories and warehousing costs. This is particularly valuable for legacy aircraft or situations requiring urgent replacements.
4. Improved Material Efficiency & Sustainability:
- Near-Net Shape Manufacturing: AM processes typically use only the material needed to build the part and its support structures. While some powder is used for supports, and unsintered powder needs careful handling and recycling, the overall material utilization is often significantly higher than traditional subtractive manufacturing, especially for complex parts machined from large billets. Reducing material waste lowers costs and contributes to sustainability goals.
- Powder Recyclability: Unfused powder in the build chamber during LPBF can typically be sieved and reused multiple times (with appropriate quality checks), further improving material efficiency. Leading providers like Met3dp emphasize powder quality and traceability, crucial for maintaining properties during recycling.
5. Enhanced Supply Chain Flexibility & Resilience:
- Dijital Envanter: Designs exist as digital files, which can be sent electronically to any capable AM facility globally for production. This enables decentralized manufacturing, producing parts closer to the point of need and reducing shipping costs and lead times.
- Reduced Tooling Dependence: Eliminating hard tooling simplifies the supply chain, reduces storage costs, and removes the risk of tool damage or loss.
- Mitigating Obsolescence: For older aircraft, where original tooling may no longer exist, AM allows for the reverse engineering and direct digital manufacturing of obsolete brackets, ensuring continued airworthiness.
- Agile Sourcing: Companies can work with a network of qualified metal 3D baskı hizmeti sağlayıcıları veya wholesale 3D printing services, diversifying their supplier base and enhancing resilience against disruptions. Optimizing aerospace supply chain solutions is a key driver for AM adoption.
In summary, the benefits of additive manufacturing for aerospace brackets extend far beyond just creating complex shapes. They encompass significant improvements in performance (weight), speed (lead time), cost (material efficiency, assembly reduction), and supply chain strategy, making it a compelling alternative or complement to traditional methods for forward-thinking aerospace organizations.
AlSi10Mg & Ti-6Al-4V: Recommended Materials Deep Dive
Choosing the right material is fundamental to the success of any engineering application, and this holds particularly true for aerospace components where performance and reliability are paramount. For 3D printed aerospace brackets, two metallic alloys stand out: AlSi10Mg (an aluminum alloy) and Ti-6Al-4V (a titanium alloy). While other alloys exist, these two cover a vast range of bracket requirements, offering distinct advantages depending on the specific application demands. Understanding their properties and processing considerations is crucial for engineers designing parts and for procurement specialists sourcing from metal powder distributors or full-service AM providers.
AlSi10Mg: The Versatile Workhorse
AlSi10Mg is one of the most widely used aluminum alloys in metal additive manufacturing, particularly via Laser Powder Bed Fusion (LPBF). It’s essentially a casting alloy composition adapted for AM processes.
- Kompozisyon: Primarily Aluminum (Al), with ~9-11% Silicon (Si) and 0.2-0.45% Magnesium (Mg).
- Silisyum (Si): Significantly improves the alloy’s fluidity in the molten state and reduces solidification shrinkage. This enhances its “printability” in LPBF, allowing for the successful creation of fine features and complex geometries with reduced risk of cracking.
- Magnezyum (Mg): Allows the alloy to be precipitation hardened through heat treatment (typically a T6 cycle involving solutionizing and artificial aging). This process significantly increases the material’s strength and hardness compared to its as-built state.
- Key Properties & Advantages for Brackets:
- Mükemmel Güç-Ağırlık Oranı: While not as high as titanium alloys, AlSi10Mg offers a very competitive strength-to-weight ratio compared to traditional steel or even many wrought aluminum alloys, making it ideal for lightweighting brackets.
- Good Processability (LPBF): Melts and solidifies predictably under laser exposure, allowing for relatively fast build speeds and good feature resolution. It’s one of the more established and well-characterized materials for LPBF.
- Good Thermal Conductivity: Aluminum alloys generally possess good thermal conductivity (around 130-150 W/m·K for AM AlSi10Mg). This is beneficial for brackets that mount heat-generating components, helping to dissipate heat away from sensitive systems.
- İyi Korozyon Direnci: Offers adequate resistance to atmospheric corrosion for many aerospace environments. Performance can be further enhanced through surface treatments like anodizing or painting if required.
- Kaynaklanabilirlik: Can be welded, although specific procedures might be required depending on the post-processing state.
- Maliyet-Etkinlik: Compared to titanium alloys, AlSi10Mg powder is significantly less expensive, making it a more economical choice for brackets where the ultimate performance of titanium is not strictly necessary.
- Düşünceler:
- Lower Temperature Capability: Not suitable for applications experiencing temperatures significantly above 150-170°C, where mechanical properties begin to degrade noticeably.
- Lower Absolute Strength than Titanium: While strong for its weight, it doesn’t match the absolute strength or fatigue resistance of Ti-6Al-4V.
- Heat Treatment Required: Achieving optimal mechanical properties typically requires a post-build heat treatment (T6 cycle), adding a step and cost to the process.
Met3dp’s Commitment to Powder Quality: The consistency and quality of the metal powder are critical for achieving reliable and repeatable results in aerospace AM. Met3dp utilizes industry-leading Gaz Atomizasyonu and Plasma Rotating Electrode Process (PREP) technologies to produce yüksek kaliteli metal tozları, including AlSi10Mg. Our advanced atomization techniques ensure: * Yüksek Küresellik: Spherical powder particles flow easily and pack densely in the powder bed, leading to more uniform layers and parts with lower porosity. * Controlled Particle Size Distribution (PSD): Optimized PSD ensures good flowability and efficient melting during the LPBF process. * Low Impurity Levels: Rigorous quality control minimizes oxygen and other contaminants that can degrade material properties. * Batch-to-Batch Consistency: Essential for repeatable manufacturing outcomes required by aerospace standards. As a trusted AlSi10Mg powder distributor and AM solutions provider, Met3dp ensures that the foundational material meets the stringent demands of aerospace bracket production.
Ti-6Al-4V (Grade 5 / Grade 23): The High-Performance Option
Ti-6Al-4V (often referred to as Ti64) is the workhorse of the titanium industry and widely used in aerospace for its exceptional properties. Grade 5 is the standard, while Grade 23 (ELI – Extra Low Interstitials) offers improved ductility and fracture toughness, often preferred for critical applications.
- Kompozisyon: Primarily Titanium (Ti), with ~6% Aluminum (Al) and ~4% Vanadium (V).
- Key Properties & Advantages for Brackets:
- Outstanding Strength-to-Weight Ratio: Offers one of the best strength-to-weight ratios among engineering metals, exceeding that of AlSi10Mg and high-strength steels. This allows for extremely lightweight and strong bracket designs.
- Mükemmel Korozyon Direnci: Highly resistant to corrosion in a wide range of aggressive environments, including saltwater and various industrial chemicals. Ideal for brackets exposed to harsh conditions.
- High Temperature Capability: Maintains good mechanical properties at elevated temperatures (up to ~400°C), making it suitable for brackets near engines or in high-speed aircraft structures.
- Mükemmel Yorulma Dayanımı: Critical for components subjected to cyclic loading, common in aircraft structures.
- Biocompatibility (Less relevant for brackets): Widely used for medical implants due to its biocompatibility.
- Düşünceler:
- Daha Yüksek Malzeme Maliyeti: Titanium powder is significantly more expensive than aluminum powder.
- Higher Density: While the strength-to-weight ratio is excellent, its density (~4.43 g/cm³) is higher than AlSi10Mg (~2.67 g/cm³). A Ti64 bracket might be stronger but not necessarily lighter than a well-optimized AlSi10Mg equivalent unless the design fully leverages its superior strength.
- More Challenging Processing: Titanium alloys generally require more carefully controlled LPBF parameters (e.g., inert atmosphere purity) and can have slower build rates compared to AlSi10Mg. They are also more reactive and require stringent powder handling protocols.
- Lower Thermal Conductivity: Significantly lower thermal conductivity (~6.7 W/m·K) compared to aluminum, which might be a disadvantage if the bracket needs to help dissipate heat.
Material Comparison Table:
Özellik | AlSi10Mg (LPBF, T6 Heat Treated) | Ti-6Al-4V (LPBF, Stress Relieved) | Birim | Notlar |
---|---|---|---|---|
Yoğunluk | ~2.67 | ~4.43 | g/cm³ | Significant difference impacts final part weight |
Akma Dayanımı (0,2%) | ~230 – 290 | ~900 – 1100 | MPa | Ti64 is significantly stronger |
Nihai Çekme Dayanımı | ~330 – 430 | ~1000 – 1200 | MPa | Ti64 has higher ultimate strength |
Kopma Uzaması | ~3 – 10 | ~6 – 15 | % | Varies with build orientation/parameters |
Elastisite Modülü | ~70 | ~110 – 115 | Not ortalaması | Measures stiffness |
Max Operating Temp. | ~150 | ~400 | °C | Approximate practical limit |
Termal İletkenlik | ~130 – 150 | ~6.7 | W/(m-K) | AlSi10Mg better for heat dissipation |
Göreceli Malzeme Maliyeti | Daha düşük | Daha yüksek | – | Significant cost difference |
Tipik Uygulamalar | Secondary structures, system mounts, prototypes, cost-sensitive parts | Primary/secondary structures, high-stress parts, high-temp areas, critical components | – | Application dictates material choice |
Sayfalara Aktar
(Note: Property values are approximate and can vary based on specific process parameters, build orientation, heat treatment, and testing standards. Always refer to supplier datasheets for specific values.)
Choosing Between AlSi10Mg and Ti-6Al-4V:
The selection process involves balancing performance requirements, operating environment, and cost:
- Seçin AlSi10Mg when:
- Weight reduction is important, but absolute maximum strength isn’t the primary driver.
- Operating temperatures are moderate (<150°C).
- Cost is a significant consideration.
- Good thermal conductivity is beneficial.
- The bracket is for secondary structural or system mounting applications.
- Seçin Ti-6Al-4V when:
- Maximum strength-to-weight ratio is critical.
- High fatigue strength is required.
- Operating temperatures are elevated (>150°C).
- Excellent corrosion resistance is necessary.
- The application involves primary structures or flight-critical components (subject to rigorous certification).
- Budget allows for the higher material and processing costs.
Her ikisi de AlSi10Mg properties ve Ti-6Al-4V aerospace grade capabilities make them invaluable tools in the aerospace materials comparison for additive manufacturing. Partnering with an experienced AM provider like Met3dp, who understands the nuances of these materials and possesses advanced Lazer Toz Yatağı Füzyonu (LPBF) capabilities and superior powder quality control through techniques like gaz atomizasyonu, ensures that the chosen material delivers the expected performance for demanding aerospace bracket applications. Ensuring full material certification aerospace traceability is a standard practice for reputable suppliers.
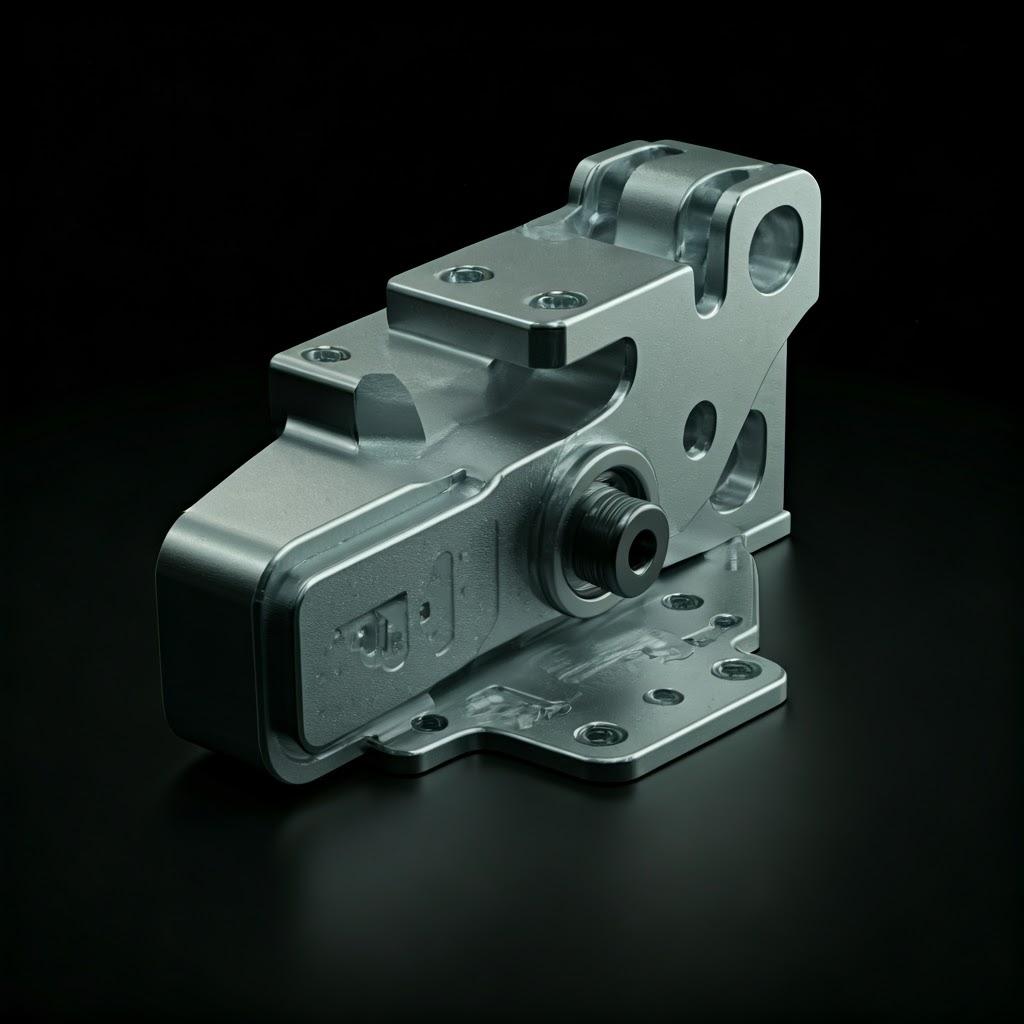
Design for Additive Manufacturing (DfAM) for Aerospace Brackets
Simply taking a bracket design originally intended for CNC machining or casting and sending it to a metal 3D printer rarely unlocks the full potential of additive manufacturing. To truly harness the benefits outlined earlier – significant weight reduction, part consolidation, and enhanced performance – engineers must embrace Katmanlı Üretim Tasarımı (DfAM). DfAM is not just about ensuring a part olabilmek be printed; it’s a fundamental shift in design thinking that leverages the unique capabilities and accounts for the specific constraints of the AM process, particularly Laser Powder Bed Fusion (LPBF) used for AlSi10Mg and Ti-6Al-4V brackets. Aerospace companies working with an experienced katkı maddesi üretim tedarikçisi will benefit greatly from collaborative DfAM efforts.
Shifting the Design Paradigm:
Traditional Design for Manufacturing (DfM) focuses on simplifying geometry for ease of machining (e.g., avoiding deep pockets, favouring prismatic shapes) or casting (e.g., draft angles, uniform wall thickness for flow). DfAM, conversely, encourages complexity where it adds function or reduces weight, while carefully managing aspects critical to the layer-by-layer build process. Key DfAM principles for aerospace brackets include:
- Leveraging Topology Optimization: As introduced previously, this is a cornerstone of DfAM for structural parts like brackets.
- Süreç: Engineers define the design space (the maximum allowable volume for the bracket), specify connection points (where it bolts to the airframe or mounts equipment), define load scenarios (forces, vibrations, accelerations it must withstand), and set objectives (e.g., minimize mass, maximize stiffness).
- Yazılım: Uzmanlaşmış topology optimization software (often integrated within CAD platforms like Siemens NX, CATIA, Creo, or as standalone tools like Altair Inspire, nTopology, Ansys Discovery) uses algorithms like Solid Isotropic Material with Penalization (SIMP) or Level Set Methods to determine the most efficient load paths.
- Çıktı: The raw output is often an organic, mesh-like structure that needs refinement. Designers must interpret these results, smooth jagged edges, potentially reconstruct the geometry using CAD tools (subdivision modeling or standard B-rep) to ensure manufacturability and meet other design constraints (e.g., clearance for wiring, access for fasteners).
- Benefit: Creates the lightest possible bracket that still meets all performance requirements, often resulting in bio-inspired, efficient forms unattainable traditionally.
- Minimizing Support Structures: LPBF requires support structures for several reasons:
- Çıkıntılar: Features angled below a certain threshold (typically ~45 degrees relative to the build plate) require underlying support to prevent collapse or deformation during printing.
- Thermal Conduction: Supports help conduct heat away from the part into the build plate, reducing thermal stress and warping.
- Anchoring: They anchor the part firmly to the build plate, preventing movement or warping during the build.
- Zorluk: Supports consume extra material (increasing cost), add significantly to print time, require laborious post-processing removal (adding cost and potentially damaging the surface), and can leave witness marks on the final part surface. Therefore, minimizing support structures is a primary DfAM goal.
- Strategies:
- Design for Self-Support: Wherever possible, design features with angles greater than the critical self-supporting angle (e.g., >45°). Chamfering downward-facing holes or using tear-drop shapes instead of simple circular horizontal holes can eliminate the need for internal supports.
- Strategic Part Orientation: The orientation of the bracket on the build plate profoundly impacts support requirements. Part orientation strategy involves complex trade-offs: minimizing support volume vs. minimizing build height (print time) vs. optimizing surface finish on critical faces vs. potentially influencing anisotropic mechanical properties. Experienced AM engineers use specialized software to simulate different orientations and find the optimal balance. For example, orienting a large flat bracket vertically might drastically reduce supports compared to printing it flat.
- Clever Feature Design: Incorporating sacrificial ribs or modifying geometry slightly to avoid shallow overhangs.
- Optimizing Wall Thickness and Feature Sizes:
- Minimum Wall Thickness: LPBF processes have limits on the thinnest walls they can reliably produce (often around 0.4-0.5 mm), influenced by powder characteristics and machine parameters. Designing below this limit risks incomplete features or failure.
- Maximum Wall Thickness: Very thick sections (> approx. 10-20 mm, depending on material and geometry) can accumulate excessive thermal stress, potentially leading to cracking or distortion. DfAM encourages hollowing thick sections or incorporating internal lattice structures 3D printing to reduce mass and mitigate thermal issues while maintaining stiffness.
- Tekdüzelik: While AM allows varied thickness, striving for relatively uniform wall thickness can help manage thermal gradients and reduce stress.
- Small Features: Minimum printable hole diameters, pin sizes, and gap widths are also limited by the process resolution (laser spot size, powder particle size). These limitations must be considered during design (e.g., designing holes slightly larger to allow for finishing, or planning to drill small holes post-print).
- Incorporating Lattice Structures:
- Function: These internal, repeating cellular structures (e.g., strut-based lattices like cubic or octet-truss, or surface-based TPMS – Triply Periodic Minimal Surfaces) can significantly reduce weight while providing tailored stiffness, energy absorption, or even thermal management properties.
- Application in Brackets: Can be used as infill for thicker sections identified by topology optimization, or to create brackets with specific vibration damping characteristics.
- Düşünceler: Requires specialized software for generation. Must ensure lattice cells are large enough for effective powder removal after printing. Inspection of internal lattice integrity can be challenging (often requiring CT scanning).
- Managing Stress Concentrations:
- Importance: While AM enables complex shapes, fundamental mechanical design principles still apply. Sharp internal corners act as stress raisers, potentially initiating cracks, especially under fatigue loading common in aerospace.
- DfAM Approach: Incorporate generous fillets and smooth transitions between features, particularly where topology optimization might create sharp junctions. Use Finite Element Analysis (FEA) to simulate stress distribution in the AM part geometry and refine the design to eliminate high-stress areas.
- Designing for Post-Processing: Consider how the part will be handled after printing. Ensure access for support removal tools, consider adding machining allowances on surfaces requiring high precision, and design features compatible with desired finishing processes (e.g., surfaces suitable for anodizing).
Mastering these additive manufacturing design guidelines is key to producing superior aerospace brackets. It often involves close collaboration between design engineers and AM process experts, like those at Met3dp, who understand the intricate relationship between design choices and manufacturing outcomes in designing for LPBF.
Achievable Tolerances, Surface Finish, and Dimensional Accuracy
While metal AM offers incredible design freedom, it’s crucial for engineers and procurement managers to have realistic expectations regarding the achievable precision directly off the printer. Understanding the typical tolerances, surface finish, and overall dimensional accuracy of LPBF-produced AlSi10Mg and Ti-6Al-4V brackets is essential for determining if post-machining is required and for planning inspection strategies. These factors directly influence fit, assembly, and performance.
Typical Tolerances:
- General Dimensional Accuracy: As a rule of thumb, for well-controlled LPBF processes using quality machines and materials like AlSi10Mg and Ti-6Al-4V, typical achievable tolerances are often cited in the range of:
- +/- 0.1 mm to +/- 0.2 mm for smaller features (e.g., up to 100 mm).
- +/- 0.1% to +/- 0.2% of the nominal dimension for larger features.
- It’s important to note that these are general guidelines for the as-built state (after stress relief but before machining). Specific tolerances depend heavily on the part geometry, size, orientation, material, and the specific machine/process parameters used.
- Karşılaştırmak: These tolerances are generally looser than what can be achieved with precision CNC machining (which can easily reach +/- 0.01 to 0.05 mm or tighter). Therefore, critical interfaces, bearing bores, or surfaces requiring very precise fits on AM brackets almost always require post-machining.
- GD&T: Applying Geometric Dimensioning and Tolerancing (GD&T) to AM parts is crucial for defining functional requirements clearly. However, the unique nature of AM (layer-wise building, potential for minor anisotropy, as-built surface texture) means careful consideration is needed when defining datums and specifying form, orientation, location, and runout tolerances. Consulting with an AM provider experienced in GD&T additive manufacturing is recommended.
Factors Influencing Accuracy and Tolerances:
Achieving the best possible dimensional accuracy LPBF requires careful control over numerous factors:
- Machine Calibration: Regular calibration of the printer’s scanners, laser focus, and build plate leveling is critical.
- Süreç Parametreleri: Laser power, scan speed, layer thickness, hatch spacing, and scan strategy all influence the melt pool size and stability, affecting dimensional accuracy and surface finish. Optimized parameter sets (often developed by machine manufacturers or expert providers like Met3dp) are crucial.
- Thermal Effects: The rapid heating and cooling inherent in LPBF create thermal gradients and residual stresses. These can cause warping or distortion, particularly in large or complex parts, impacting final dimensions. Effective support structures and stress relief heat treatments are vital mitigation strategies.
- Part Geometry and Orientation: Large flat surfaces parallel to the build plate are more prone to warping. Tall, thin features can be challenging to build accurately. Orientation affects heat buildup and support needs, both influencing accuracy.
- Toz Kalitesi: Consistent particle size distribution, morphology (sphericity), and flowability of the metal powder contribute to uniform powder bed density and predictable melting, impacting accuracy and defect rates.
- Support Strategy: Inadequate or poorly designed supports can allow the part to shift or warp during the build.
Surface Finish (Surface Roughness):
The surface finish of as-built metal AM parts is characteristically rougher than machined surfaces due to the layer-by-layer process and the partially melted powder particles adhering to the surface.
- Measurement: Surface roughness is typically quantified using the parameter Ra (arithmetical mean deviation of the roughness profile), measured in micrometers (µm).
- Typical As-Built Ra Values (LPBF AlSi10Mg/Ti64):
- Vertical Walls: Generally offer the best finish, perhaps Ra 6 – 15 µm.
- Up-facing Surfaces (Top skins): Often slightly rougher than vertical walls, Ra 8 – 20 µm.
- Down-facing Surfaces (Supported): Typically the roughest due to contact with support structures, Ra 15 – 30 µm or higher, depending on support type and removal process.
- Stepped Surfaces (Stair-stepping effect): Curved or angled surfaces approximated by layers can exhibit visible stepping, impacting perceived smoothness.
- Karşılaştırmak: Machined surfaces commonly achieve Ra 0.8 – 3.2 µm or much smoother with grinding/polishing (Ra < 0.1 µm). Cast surfaces vary widely but are often rougher than as-built AM unless polished.
- Implications: The as-built surface finish additive manufacturing might be acceptable for some non-critical bracket surfaces. However, for mating faces, sealing surfaces, or areas prone to fatigue initiation, the roughness is often too high and requires improvement through post-processing (e.g., bead blasting, tumbling, machining, polishing). The Ra surface roughness chart should be consulted alongside functional requirements.
Inspection and Validation:
Given the inherent variability and the criticality of aerospace components, robust inspection methods are non-negotiable:
- Coordinate Measuring Machines (CMM): Used for precise measurement of critical dimensions, hole locations, and geometric tolerances defined by GD&T. Requires careful fixture design for AM parts. CMM inspection aerospace protocols are well-established.
- 3D Laser Scanning / Structured Light Scanning: Captures millions of data points across the entire part surface, creating a 3D model that can be compared directly to the original CAD file. Excellent for verifying overall form, detecting warping, and performing surface deviation analysis. Increasingly used for qualifying AM parts.
- Tahribatsız Muayene (NDT): As discussed further in post-processing, methods like CT scanning can inspect internal geometry and detect flaws (porosity, inclusions) that impact structural integrity, which also relates to achieving the intended internal dimensions.
Understanding the achievable metal 3D printing tolerances and surface finish allows engineers to design accordingly (e.g., adding machining stock) and enables procurement managers to specify realistic requirements and appropriate inspection levels when working with AM service providers. Partnering with a provider like Met3dp, equipped with both advanced printing technology and comprehensive metrology capabilities, ensures parts meet the necessary specifications.
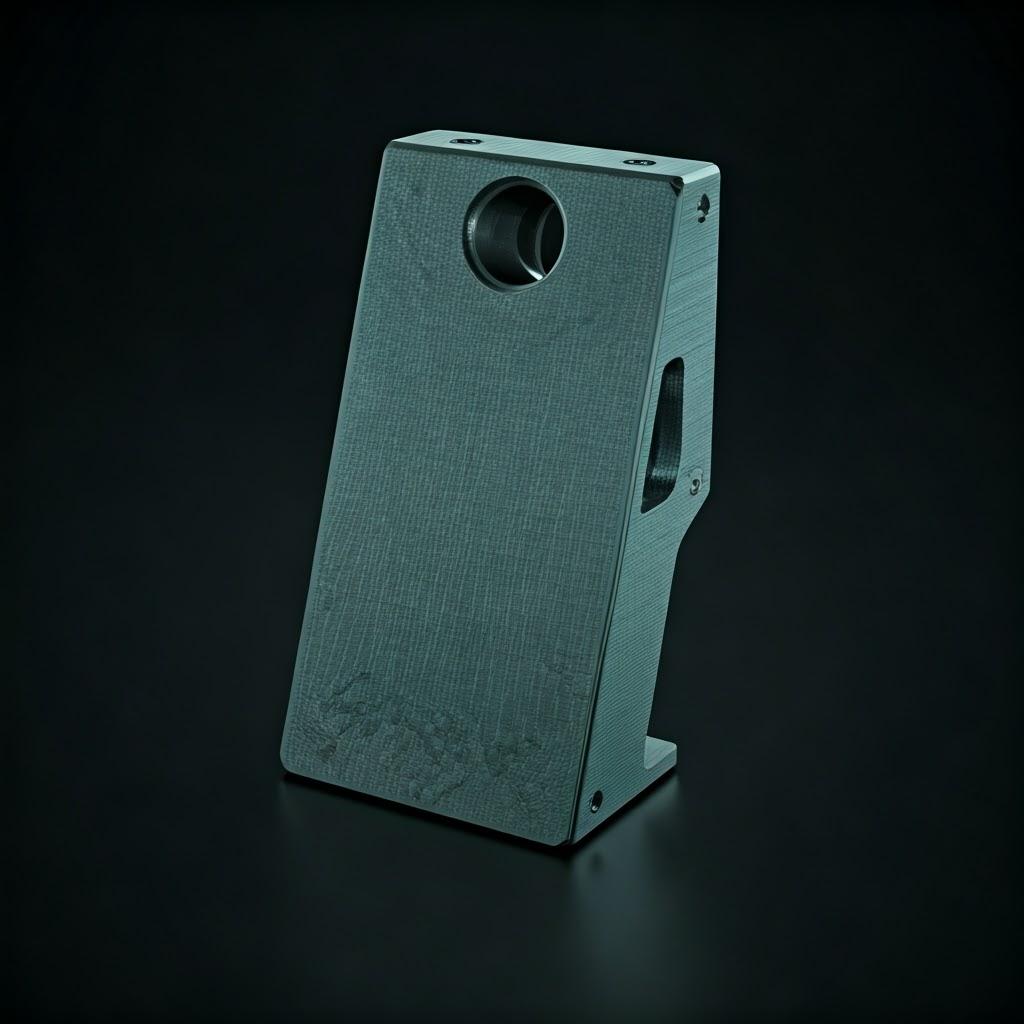
Essential Post-Processing Steps for 3D Printed Brackets
Printing the aerospace bracket is only the first major step in the additive manufacturing workflow. A series of essential post-processing operations are almost always required to transform the raw, as-built part into a functional, flight-ready component. These steps are critical for achieving the desired mechanical properties, dimensional accuracy, surface finish, and overall quality demanded by the aerospace industry. Procurement managers should ensure potential AM suppliers have robust capabilities and quality control for these crucial stages.
1. Removal from Build Plate:
- The printed bracket(s) are initially fused to the metal build plate via the first layers and support structures.
- Common removal methods include:
- Wire Electrical Discharge Machining (Wire EDM): Precise method, often used for delicate parts or when a clean cut close to the part base is needed.
- Şerit Testere: Faster method suitable for less delicate parts or where some excess material near the base is acceptable for later removal.
- Care must be taken during this step to avoid damaging the parts.
2. Stress Relief / Heat Treatment:
- This is arguably the most critical post-processing step for achieving desired material properties and ensuring dimensional stability. Residual stresses build up during the rapid heating and cooling cycles of LPBF, which can lead to warping and unpredictable mechanical behavior if not addressed.
- AlSi10Mg: Typically undergoes a T6 heat treatment:
- Çözüm üretiyorum: Heating the part to a specific high temperature (e.g., ~530°C) to dissolve the Mg and Si elements into the aluminum matrix.
- Söndürme: Rapidly cooling (often in water or polymer) to trap these elements in a supersaturated solid solution.
- Artificial Aging: Reheating to a lower temperature (e.g., ~160-180°C) for a specific duration to allow controlled precipitation of Mg2Si phases, which significantly strengthen and harden the alloy. The exact heat treatment AlSi10Mg T6 cycle parameters (times, temps) influence the final balance of strength and ductility.
- Ti-6Al-4V:
- Stress Relief Anneal: Typically heated to 650-800°C followed by slow cooling. This reduces internal stresses induced during printing, minimizing distortion during subsequent steps like support removal or machining. It doesn’t significantly alter the microstructure or strength imparted by the rapid solidification during AM.
- Sıcak İzostatik Presleme (HIP): Often recommended, especially for critical aerospace components. This process involves subjecting the part to high temperature (just below the melting point) ve high inert gas pressure (e.g., Argon) simultaneously. HIP treatment aerospace effectively closes internal porosity (gas pores, lack of fusion voids) that might have formed during printing, significantly improving fatigue life, ductility, and fracture toughness. HIP can sometimes be combined with heat treatment cycles.
- Ekipman: These treatments require precisely controlled furnaces, often with inert atmospheres (like Argon or Nitrogen) or vacuum capabilities to prevent oxidation, especially crucial for titanium.
3. Support Structure Removal:
- Removing the support structures generated during the build is often a manual and labor-intensive process, contributing significantly to post-processing time and cost.
- Methods depend on support design and accessibility:
- Manuel Kaldırma: Using pliers, cutters, grinders, or specialized tools to break or cut away supports. Well-designed supports incorporate features (e.g., perforations, smaller contact points) to facilitate easier breaking.
- İşleme: Milling or grinding away supports, especially useful for supports in difficult-to-reach areas or where a smoother surface finish is required at the contact point.
- Electrochemical Machining (ECM): Less common but can be used for specific materials/geometries.
- Effective DfAM practices that minimize support volume and ensure accessibility are key to reducing the effort and cost associated with support removal metal AM.
4. Machining for Critical Features:
- As discussed under tolerances, AM parts often require secondary machining to achieve tight tolerances, specific surface finishes, or features not possible in the as-built state.
- Common machining operations for brackets include:
- Milling mating faces to ensure flatness and achieve GD&T requirements.
- Drilling, reaming, or boring holes to precise diameters and positional tolerances for fasteners or bearings.
- Threading holes.
- Creating specific sealing surfaces.
- CNC machining 3D prints requires careful fixture design to hold the often complex AM part geometry securely without distortion. Combining AM with machining (hybrid manufacturing) leverages the benefits of both processes.
5. Surface Finishing:
- Çeşitli surface finishing aerospace parts techniques are employed to improve roughness, clean the surface, enhance fatigue life, or prepare for coatings.
- Common methods:
- Boncuk Kumlama / Kumlama: Propelling fine media (glass beads, ceramic, aluminum oxide) at the surface. Cleans the part, removes partially sintered particles, creates a uniform matte finish, and can slightly improve fatigue resistance by inducing compressive stress. Media type and pressure must be controlled.
- Shot Peening: Similar to blasting but uses spherical metallic shot with controlled intensity to impart a deeper compressive stress layer, significantly enhancing fatigue life – often a requirement for critical aerospace components.
- Yuvarlama / Vibrasyonlu Son İşlem: Placing parts in a tumbler with abrasive media. Good for smoothing edges and surfaces of multiple smaller parts simultaneously, though less precise than blasting or machining.
- Parlatma: Using progressively finer abrasives to achieve a smooth, reflective surface (low Ra). Typically reserved for specific functional requirements or aesthetic purposes.
- Anodizing (AlSi10Mg): An electrochemical process that creates a hard, wear-resistant, and corrosion-resistant oxide layer on the surface of aluminum parts. Can also be dyed various colors. Anodizing aluminum is a common finish for AlSi10Mg brackets.
- Painting / Coating: Applying specialized aerospace primers and topcoats for enhanced corrosion protection or specific properties (e.g., thermal barrier coatings, dry film lubricants). Surface preparation (cleaning, potentially anodizing or conversion coating) is critical for adhesion.
6. Quality Control & Inspection (Post-Processing Phase):
- Inspection occurs throughout the post-processing workflow.
- Final inspection verifies that all previous steps have been completed correctly and the part meets all specifications.
- This includes:
- Boyutsal Doğrulama: CMM or 3D scanning after machining and heat treatment.
- Surface Finish Measurement: Using profilometers to check Ra values.
- Tahribatsız Muayene (NDT):
- Visual Inspection (VT): Checking for obvious flaws, surface imperfections.
- Dye Penetrant Inspection (PT): Reveals surface-breaking cracks.
- Computed Tomography (CT) Scanning: X-ray based method to visualize internal structures and detect internal defects like porosity or inclusions, increasingly vital for qualifying critical AM aerospace parts.
- Material Property Verification: Often involves destructive testing of sample coupons printed alongside the main parts (e.g., tensile testing to confirm heat treatment effectiveness).
Successfully executing these post-processing steps requires significant expertise, specialized equipment, and rigorous quality control systems. When selecting an AM manufacturing partner, verifying their in-house or managed capabilities for these critical operations is paramount for ensuring the delivery of flight-worthy aerospace brackets. Met3dp offers comprehensive katkı üretim çözümleri that encompass not only printing but also guidance on necessary post-processing to meet application requirements.
Common Challenges in Printing Aerospace Brackets and Mitigation Strategies
While metal 3D printing offers numerous advantages for aerospace brackets, the LPBF process is complex and not without its challenges. Understanding potential issues and the strategies employed by experienced service providers to mitigate them is crucial for ensuring successful outcomes, consistent quality, and reliable parts. Engineers and procurement managers should be aware of these factors when evaluating suppliers and project feasibility.
1. Warping and Distortion:
- Meydan okumak: Due to the intense localized heating by the laser and subsequent rapid cooling, significant thermal gradients develop within the part and between the part and the build plate during the LPBF process. This leads to the build-up of internal residual stresses. If these stresses exceed the material’s yield strength at elevated temperatures, the part can warp, curl up from the build plate, or distort from its intended geometry. This is one of the most common metal 3D printing defects.
- Mitigation Strategies:
- Optimized Part Orientation: Orienting the part to minimize large, flat cross-sections parallel to the build plate can reduce stress accumulation. Minimizing build height can also sometimes help.
- Effective Support Structures: Robust supports are crucial not only for overhangs but also for anchoring the part firmly to the build plate, resisting warping forces, and helping to conduct heat away more uniformly. Support design (type, density, contact points) is critical.
- Süreç Parametre Optimizasyonu: Fine-tuning laser power, scan speed, and scan strategy (e.g., using checkerboard patterns or island scanning) can help manage the temperature distribution and reduce peak stresses. Experienced providers like Met3dp invest heavily in process parameter development.
- Plaka Isıtması Oluşturun: Pre-heating the build plate (common for Ti-6Al-4V, less so but sometimes used for AlSi10Mg) reduces the thermal gradient between the molten material and the underlying substrate, lowering stress build-up.
- Stress Relief Heat Treatment: Performing a stress relief cycle immediately after printing (before removal from the build plate in some cases) is essential for relaxing internal stresses and preventing distortion during subsequent handling and machining.
2. Residual Stress:
- Meydan okumak: Even if macroscopic warping is avoided, significant residual stresses remain locked within the as-built part. These stresses can negatively impact fatigue life, fracture toughness, and dimensional stability (potentially causing distortion when material is removed during machining). Residual stress mitigation birincil endişe kaynağıdır.
- Mitigation Strategies:
- Süreç Kontrolü: As with warping, optimized process parameters and scan strategies help minimize stress induction.
- Termal Yönetim: Effective support design and potentially build plate heating play a role.
- Mandatory Heat Treatment: Appropriate post-build heat treatment (stress relief anneal for Ti-6Al-4V, solutionizing/aging T6 for AlSi10Mg) is the primary method for significantly reducing residual stresses to acceptable levels.
3. Porosity:
- Meydan okumak: Small voids or pores within the printed material can act as stress concentrators, significantly degrading mechanical properties, particularly fatigue strength and fracture toughness. Porosity is unacceptable for critical aerospace components. Porosity control LPBF hayati önem taşır.
- Types and Causes:
- Gas Porosity: Typically spherical, caused by dissolved shielding gas (Argon) getting trapped during rapid solidification or by gas released from the powder itself.
- Lack of Fusion Porosity: Irregularly shaped voids caused by insufficient melting and fusion between adjacent melt tracks or layers. Often results from incorrect parameters (too low power, too high speed) or inconsistent powder spreading.
- Mitigation Strategies:
- Yüksek Kaliteli Toz: Using powder with low trapped gas content, controlled sphericity, and optimized particle size distribution is crucial. Met3dp’s advanced atomization processes focus on producing powder with these characteristics. Proper powder handling and storage to prevent moisture pickup are also key.
- Optimize Edilmiş Süreç Parametreleri: Ensuring sufficient energy density (combination of laser power, speed, hatch distance) to fully melt the powder and achieve good overlap between melt tracks.
- Shielding Gas Control: Maintaining a high-purity inert gas atmosphere (Argon) in the build chamber with low oxygen levels prevents oxidation and reduces gas porosity issues. Proper gas flow dynamics are important.
- Machine Maintenance: Regular calibration and maintenance of the printer’s laser, optics, and powder delivery system.
- Sıcak İzostatik Presleme (HIP): Especially for Ti-6Al-4V and critical applications, HIP is highly effective at closing internal porosity through high pressure and temperature, leading to near-fully dense parts.
4. Support Removal Difficulty:
- Meydan okumak: While necessary, poorly designed or overly dense supports can be extremely difficult and time-consuming to remove without damaging the part surface. Supports in internal channels or hard-to-reach areas pose significant challenges.
- Mitigation Strategies:
- DfAM Focus: Designing parts to be self-supporting as much as possible is the best strategy. See DfAM section.
- Optimized Support Structures: Using specialized support generation software to create structures that are strong enough during the build but easier to remove (e.g., using conical points, perforated walls, tree supports). Matching support type to material (AlSi10Mg supports are generally easier to remove than Ti-6Al-4V).
- Accessibility Planning: Ensuring design allows physical access for tools required for support removal.
- Appropriate Removal Techniques: Selecting the right tools and methods based on the support type and location.
5. Powder Handling and Safety:
- Meydan okumak: Fine metal powders, particularly aluminum and titanium, are reactive and pose potential fire, explosion, and health hazards if not handled correctly. Metal powder safety her şeyden önemlidir.
- Mitigation Strategies:
- Inert Environments: Handling reactive powders (especially Ti) under an inert Argon atmosphere whenever possible (e.g., during loading, unloading, sieving).
- Grounding: Ensuring all equipment (printers, sieves, vacuum cleaners) is properly grounded to prevent static discharge, which could ignite powder clouds.
- Explosion-Proof Equipment: Using ATEX-rated or appropriately designed vacuum cleaners and other equipment for powder handling.
- Kişisel Koruyucu Ekipman (KKE): Mandatory use of respirators (to prevent inhalation), conductive footwear, flame-retardant clothing, and safety glasses.
- Powder Management Procedures: Strict protocols for powder storage, transport, loading, recycling (sieving), and disposal. Limiting quantities of loose powder.
- Facility Design: Appropriate ventilation, atmospheric monitoring, and spill containment measures.
- Eğitim: Ensuring all personnel handling powder are thoroughly trained on the risks and safety procedures. Experienced providers like Met3dp maintain rigorous safety protocols.
6. Surface Finish Irregularities:
- Meydan okumak: Achieving a perfectly uniform surface finish directly from the printer is difficult. Issues include roughness on down-facing surfaces, visible layer lines (“stair-stepping”), and witness marks from support structures.
- Mitigation Strategies:
- Orientation Optimization: Positioning critical surfaces vertically or as up-facing surfaces where possible.
- Parametre Ayarlama: Contour scans and specific skin strategies can improve surface finish on certain features.
- Effective Post-Processing: Selecting the appropriate surface finishing methods (blasting, tumbling, machining, polishing) based on the required final finish. See Post-Processing section.
Addressing these challenges requires a combination of robust DfAM practices, optimized and validated process parameters, high-quality materials, appropriate post-processing techniques, rigorous quality control, and adherence to strict safety protocols. Partnering with a knowledgeable and experienced metal AM service provider like Met3dp, who proactively manages these potential issues, is key to successfully implementing metal 3D printing for demanding aerospace bracket applications.
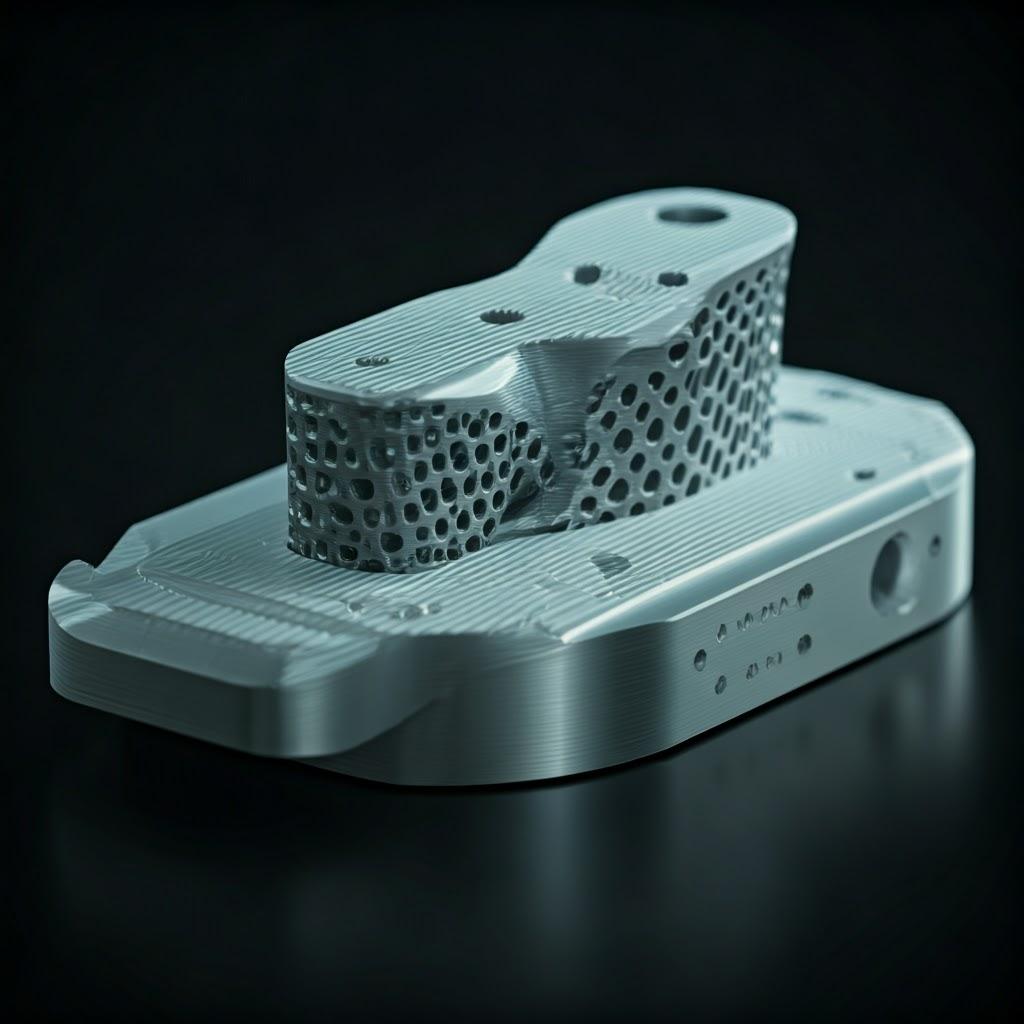
Choosing Your Metal 3D Printing Service Provider for Aerospace Components
Selecting the right manufacturing partner is arguably one of the most critical decisions when adopting metal additive manufacturing for aerospace components like brackets. Unlike procuring standard off-the-shelf hardware, AM involves intricate processes where the supplier’s expertise, equipment, process control, and quality systems directly impact the integrity and performance of the final part. Simply choosing the cheapest quote can lead to substandard parts, project delays, and potentially catastrophic failures in demanding aerospace applications. It’s not just about finding a metal 3D printing service provider; it’s about establishing a collaborative relationship with a knowledgeable aerospace additive manufacturing supplier who understands the unique challenges and stringent requirements of the industry.
Engineers and procurement managers must conduct thorough due diligence when evaluating metal AM bureaus or potential AM partners. Here are key criteria to consider:
Key Evaluation Criteria for Aerospace AM Suppliers:
- Aerospace Certifications & Quality Management System (QMS):
- AS9100 Certification: This is the internationally recognized Quality Management System standard specific to the Aviation, Space, and Defense industries. 1 AS9100 builds upon ISO 9001 but includes additional requirements crucial for aerospace, focusing on safety, airworthiness, product conformity, configuration management, risk management, and traceability throughout the supply chain. Partnering with an AS9100 certified supplier provides significant assurance that robust processes are in place. Ask potential suppliers for their certification status or their documented path towards achieving it. 1. www.citizensjournal.us www.citizensjournal.us
- NADCAP Accreditation: While AS9100 covers the overall QMS, NADCAP (National Aerospace and Defense Contractors Accreditation Program) provides specific accreditation for ‘special processes’. For AM suppliers, relevant NADCAP accreditations might include Heat Treating, Non-Destructive Testing (NDT), and potentially Materials Testing Laboratories if they perform these activities in-house. If a supplier outsources these critical processes, ensure their subcontractors hold the necessary NADCAP approvals.
- Robust Internal QMS: Beyond certifications, evaluate the supplier’s internal QMS documentation. How do they handle process control, document control, corrective and preventive actions (CAPA), employee training, equipment calibration, and supplier management? A mature QMS is essential for consistent results. Met3dp understands the criticality of these systems and is committed to implementing industry-leading quality practices. Learn more about our commitment on our Hakkımızda sayfa.
- Machine Capability, Capacity, and Technology:
- Appropriate Technology: Ensure the supplier utilizes Laser Powder Bed Fusion (LPBF) systems suitable for processing AlSi10Mg and/or Ti-6Al-4V reliably.
- Machine Fleet: What specific machine models do they operate? Different manufacturers (e.g., EOS, SLM Solutions, Renishaw, Trumpf, Velo3D, Farsoon – and Met3dp’s own advanced systems) have varying capabilities regarding build volume, laser power/number, minimum feature size, and process monitoring.
- Capacity and Redundancy: Do they have sufficient machine capacity to handle your projected volumes and meet lead time requirements? Having multiple machines provides redundancy in case of maintenance or downtime.
- Süreç İzleme: Inquire about their use of in-situ process monitoring tools (e.g., melt pool monitoring, thermal imaging) which can provide valuable data for quality assurance, although interpreting this data effectively is still an evolving field.
- Material Expertise and Quality Control:
- Material Focus: Do they specialize in the specific alloys you require (AlSi10Mg, Ti-6Al-4V)? Deep expertise in processing these materials is vital.
- Powder Sourcing and Handling: Where do they source their powder? Do they use powder certified to aerospace specifications? What are their procedures for incoming powder inspection, storage (preventing contamination/moisture), handling (especially reactive Ti), and traceability (linking powder batch to specific builds and parts)?
- Powder Recycling (Re-use): Using recycled powder is standard practice to improve cost-effectiveness, but it must be managed carefully. What is their powder re-use strategy? How many times is powder reused? What testing is done on recycled powder to ensure its properties haven’t degraded (e.g., chemistry, particle size distribution, flowability)? Met3dp’s focus extends to producing high-quality powders with superior consistency, understanding that input material quality is foundational.
- Malzeme Sertifikasyonu: Can they provide full material traceability and Certificates of Conformance (CoCs) for both the powder used and the final parts?
- Engineering and DfAM Support:
- Teknik Uzmanlık: Does the supplier have experienced AM engineers and metallurgists on staff? Can they provide meaningful DfAM support – helping you optimize your bracket design for printability, weight reduction, and performance?
- Collaborative Approach: Are they willing to work collaboratively with your design team, offering suggestions for orientation, support strategy, and feature design? This partnership approach often yields the best results. Met3dp prides itself on decades of collective expertise in metal AM, offering comprehensive solutions.
- Post-Processing Capabilities:
- Şirket İçi ve Dış Kaynaklı: Do they perform critical post-processing steps like heat treatment (with aerospace-grade calibrated furnaces and atmosphere control), support removal, precision CNC machining, surface finishing (blasting, peening, polishing), and NDT in-house? In-house capabilities generally allow for better process control, integration, and potentially faster lead times.
- Managed Supply Chain: If they outsource certain steps, how do they qualify and manage these subcontractors? Do the subcontractors hold necessary certifications (e.g., NADCAP for heat treat/NDT)?
- Track Record and Experience:
- Aerospace Experience: Have they successfully produced parts (specifically brackets or similar structural/system components) for other aerospace customers? Proven experience in the sector is invaluable.
- Case Studies/References: Can they provide non-confidential examples of relevant projects or allow you to speak with existing customers?
- Stability and Reputation: Consider the supplier’s business stability and reputation within the industry.
- Inspection and Metrology:
- Ekipman: Do they possess the necessary metrology equipment (CMMs, 3D scanners, surface profilometers) calibrated to traceable standards?
- NDT Capabilities: What NDT methods (VT, PT, potentially UT, RT, CT) do they offer in-house or through certified partners? CT scanning capability is increasingly important for internal inspection of critical AM parts.
Finding Potential Suppliers:
Resources for identifying potential metal AM service distributors and providers include:
- Online manufacturing marketplaces and directories (e.g., Hubs, Xometry, Thomasnet, specialist AM directories).
- Aerospace and AM industry trade shows and conferences.
- Referrals from industry contacts.
- Direct engagement with established AM solution providers known for quality, such as Met3dp.
Carefully choosing an AM partner based on these criteria, rather than solely on price, is a strategic investment that significantly increases the likelihood of successfully implementing reliable, high-performance 3D printed AlSi10Mg or Ti-6Al-4V brackets for your aerospace applications.
Cost Analysis and Lead Time Expectations for AM Aerospace Brackets
One of the most common questions from procurement managers and engineers considering metal additive manufacturing is: “How much does it cost, and how long does it take?” While AM offers compelling advantages, understanding the cost structure and realistic lead times is crucial for project planning, budgeting, and comparing AM against traditional manufacturing methods. The additive manufacturing pricing model differs significantly from subtractive or formative processes.
Complexity of AM Costing:
Unlike CNC machining where cost might be heavily driven by machine time and material block size, or casting where tooling is a major upfront expense, metal 3D printing cost is influenced by a complex interplay of factors related to the printing process itself and the extensive post-processing required. It’s rarely as simple as cost per kilogram of material.
Key Factors Influencing Cost:
- Material Type and Volume:
- Toz Maliyeti: There’s a significant difference in raw material cost. Aerospace-grade Ti-6Al-4V powder can be 5-10 times more expensive than AlSi10Mg powder.
- Part Volume: The actual volume of material making up the final bracket directly impacts cost.
- Support Volume: Material used for support structures also adds to the cost. Well-optimized designs using DfAM minimize support material waste.
- Procurement Model: Costs may differ if sourcing finished parts from a service provider versus procuring powder directly from a metal powder distributor for in-house printing. Wholesale 3D printing services may offer volume discounts.
- Print Time (Machine Utilization):
- Build Height: LPBF builds layer by layer, so the taller the part (in the build orientation), the longer it takes to print, regardless of its volume. This is a major cost driver. Nesting multiple shorter parts in a single build is more cost-effective than printing one very tall part.
- Part Volume & Density: Larger volume parts naturally take longer to scan and fuse. Dense, solid parts take longer than those incorporating lightweight lattice structures.
- Number of Parts per Build: Setup time (loading powder, machine preparation) is amortized across all parts in a build. Printing multiple brackets simultaneously (nesting) significantly reduces the per-part cost compared to printing one at a time.
- Scan Strategy & Parameters: Build parameters optimized for speed vs. quality/accuracy impact print time.
- Machine Hourly Rate:
- This rate reflects the capital cost of the sophisticated LPBF machine, maintenance, facility overheads, energy consumption, and skilled labor required to operate it. Rates vary between providers and machine types.
- Post-Processing Requirements (Often Significant):
- Isıl İşlem: Furnace time, energy, and potentially inert gas consumption add cost. Complex cycles like T6 or HIP are more expensive than simple stress relief.
- Destek Kaldırma: Primarily driven by manual labor time. Complex, inaccessible supports significantly increase this cost.
- İşleme: Cost depends on the complexity of the machining operations, number of setups required, and CNC machine time.
- Yüzey İşlemi: Labor and materials/consumables for blasting, tumbling, polishing, anodizing, etc. Shot peening requires specialized equipment and control.
- Teftiş: Labor for visual/dimensional checks. Equipment time and specialized analysis for CMM, 3D scanning, and particularly NDT methods like CT scanning can add substantial cost, especially when required for 100% of parts in critical applications.
- Sipariş Hacmi:
- Ölçek Ekonomileri: While AM is known for cost-effectiveness at low volumes (prototypes, small batches), unit costs do decrease with larger orders due to amortization of setup/programming time and optimized build nesting. Ask suppliers about pricing tiers for different quantities.
- Design Complexity (DfAM Impact):
- A bracket design optimized using DfAM principles (e.g., minimized volume/weight, self-supporting features, integrated functionality) will inherently cost less to produce via AM than a non-optimized or directly translated traditional design due to reduced material use, shorter print times, and less post-processing effort. Investing in DfAM upfront pays dividends in production cost.
Typical Lead Time Expectations:
Lead time additive manufacturing is generally much faster than traditional methods involving tooling (casting) but can vary widely based on the factors above.
- Prototipler: For single parts or very small batches (1-5) with standard post-processing (e.g., stress relief, basic support removal, bead blast), lead times of 5-15 business days are common. Expedited services may be available at a premium.
- Production Series (Small to Medium Volume): For batches of tens to hundreds of brackets, lead times can range from 3 to 8 weeks, depending heavily on:
- Part complexity and print time per build.
- Total number of parts required.
- Complexity of post-processing (multi-step heat treatments, extensive machining, complex finishing, rigorous NDT).
- Supplier’s current capacity and backlog.
- Required documentation and certification package.
Cost Comparison: AM vs. Traditional Methods:
There’s often a break-even analysis AM dikkate alınması gerekenler:
- Very Low Volume (1-10s): AM is often highly cost-competitive, especially for complex brackets, as it avoids high tooling costs associated with casting or complex fixture costs for machining.
- Low to Medium Volume (10s-100s): AM remains competitive, particularly if weight reduction and design complexity offer significant value. The cost comparison with multi-axis CNC machining depends heavily on part complexity.
- High Volume (1000s+): Traditional methods like investment casting or high-speed machining typically become more cost-effective per part due to economies of scale, unless the unique benefits of AM (extreme lightweighting, part consolidation impossible otherwise) justify a potential per-part cost premium.
Obtaining Accurate Quotes:
To get reliable cost estimates and aerospace component cost analysis, provide potential suppliers with:
- 3D CAD models (STEP format preferred).
- 2D drawings specifying critical dimensions, GD&T, required surface finishes, and inspection requirements.
- Material specification (AlSi10Mg or Ti-6Al-4V, including any specific grade or heat treatment).
- Quantity required and desired delivery schedule.
- Any specific certification or documentation requirements.
Understanding these cost drivers and lead time factors allows for better budgeting, realistic scheduling, and informed decisions when incorporating 3D printed AlSi10Mg or Ti-6Al-4V brackets into aerospace projects.
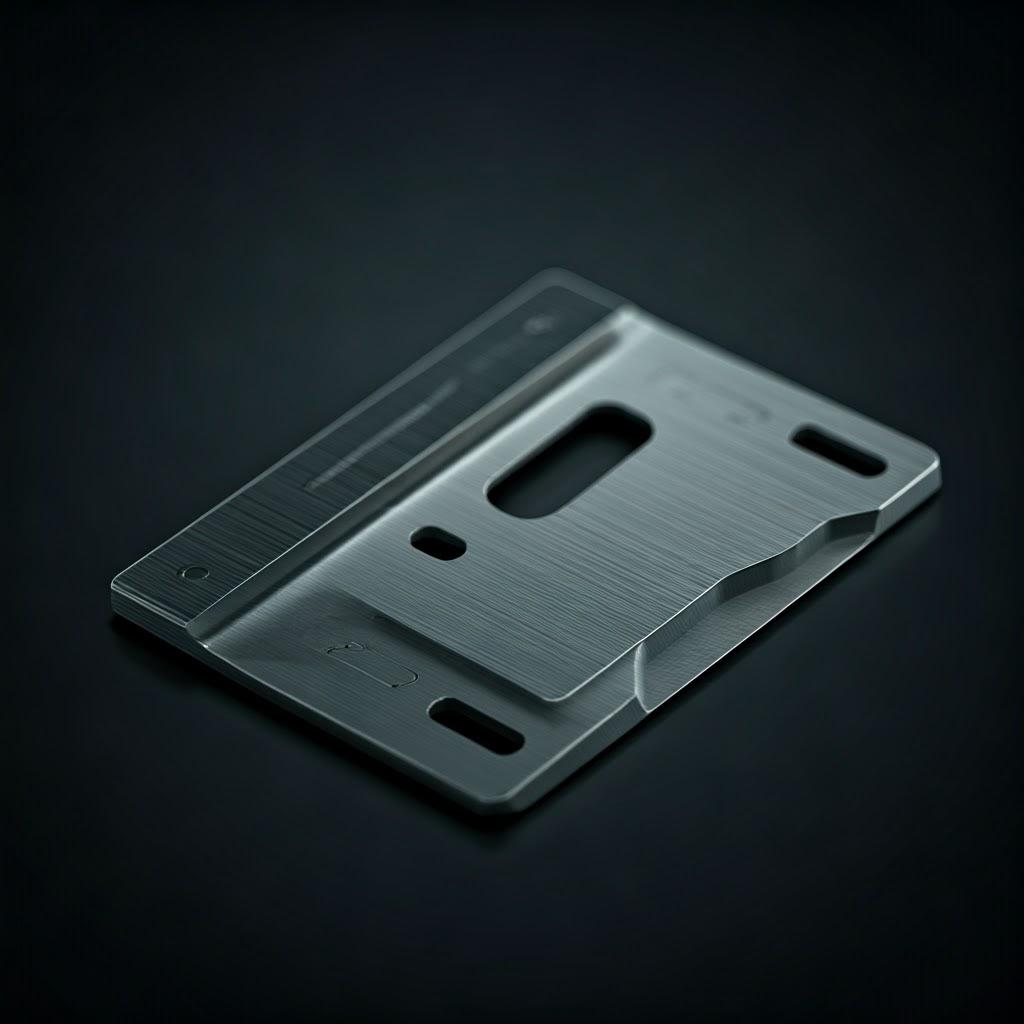
Frequently Asked Questions (FAQ) about AlSi10Mg Aerospace Brackets
Here are answers to some common questions engineers and procurement managers have regarding the use of 3D printed AlSi10Mg for aerospace brackets:
1. Is 3D printed AlSi10Mg suitable for flight-critical applications?
Generally, AlSi10Mg produced via LPBF is more commonly used for secondary structural elements ve system mounting brackets rather than primary, flight-critical structures (e.g., main wing spars, landing gear components). While strong for its weight, its fatigue properties and fracture toughness are typically lower than optimized wrought aluminum alloys (like 7075-T6) or aerospace-grade titanium alloys like Ti-6Al-4V. Flight-critical applications demand extremely high levels of demonstrated reliability, damage tolerance, and predictable performance under extreme conditions, often requiring extensive and costly qualification programs involving statistical material property generation and component testing. While specific, highly controlled AlSi10Mg applications might achieve certification for less demanding critical parts with significant analysis and testing, Ti-6Al-4V (often with HIP treatment) is more frequently considered for additively manufactured critical components due to its superior intrinsic properties. The suitability always depends on rigorous engineering analysis of the specific part’s load case, operating environment, safety factors, and certification requirements defined by regulatory bodies (e.g., FAA, EASA).
2. What are the fatigue properties of AM AlSi10Mg brackets compared to wrought aluminum?
This is a critical consideration for aerospace components subjected to cyclic loading. As-built or stress-relieved/T6 heat-treated AlSi10Mg produced by LPBF typically exhibits lower high-cycle fatigue (HCF) strength compared to common wrought aluminum alloys like 6061-T6 or 7075-T6. Several factors contribute to this:
- Mikroyapı: The rapidly solidified microstructure of AM parts is different from the wrought structure.
- Potential Defects: Microporosity (even at low levels <0.1%) can act as initiation sites for fatigue cracks.
- Yüzey İşlemi: The inherent roughness of as-built AM surfaces can significantly reduce fatigue life compared to smooth machined surfaces. Down-facing surfaces and areas with support contact points are often most critical.
- Anizotropi: Fatigue properties can sometimes vary depending on the build orientation relative to the loading direction. Mitigation/Improvement: Post-processing steps like Sıcak İzostatik Presleme (HIP) (though less common and potentially less effective for Al alloys than Ti) can help close internal pores, and surface treatments like shot peening can introduce beneficial compressive residual stresses to significantly improve fatigue life. Machining critical surfaces smooth also helps. However, designers must use appropriate fatigue data specific to the AM material and process (including post-processing) and apply suitable safety factors, often requiring dedicated fatigue testing for validation, especially for parts experiencing significant cyclic loads.
3. Can existing bracket designs (made for machining or casting) be directly 3D printed?
Technically, yes, a CAD model designed for machining can usually be converted to an STL file and printed. However, doing so is highly suboptimal and generally not recommended. It completely misses the primary advantages of additive manufacturing. Directly printing a design optimized for subtractive methods typically results in:
- Excessive Weight: The design likely includes bulk material easily machined away but inefficient from a structural load-path perspective.
- Extensive Support Needs: Features designed for tool access (e.g., flat bottoms, right-angled overhangs) often require significant support structures in AM, increasing print time, material waste, and post-processing labor.
- Longer Print Times: The non-optimized volume and support structures increase build time.
- Higher Costs: Increased material usage, print time, and post-processing labor make it more expensive than necessary. To truly benefit from AM, brackets should be re-designed or newly designed using DfAM principles. This involves leveraging topology optimization, designing self-supporting features, consolidating parts, and optimizing for the layer-wise build process. This requires an investment in design effort but yields significantly lighter, often better-performing, and ultimately more cost-effective AM components.
4. What quality certifications are essential for aerospace AM suppliers?
As mentioned previously, the foundational QMS certification is AS9100. This demonstrates the supplier has implemented aerospace-specific controls for quality, traceability, risk management, and configuration management. For suppliers performing ‘special processes’ in-house, NADCAP accreditation for those processes (e.g., Heat Treatment, Non-Destructive Testing, Welding, Materials Testing) provides further assurance of technical competence and process control specific to those operations. Additionally, robust malzeme sertifikasyonu processes, ensuring incoming powder meets required specifications (e.g., AMS standards for chemistry and PSD) and providing full traceability from powder batch to final part, are crucial. Customers should verify a potential supplier’s current certification status and the scope of their accreditations.
5. How does Met3dp ensure the quality of its AlSi10Mg powder?
Met3dp recognizes that premium quality metal powder is the foundation for high-performance additive manufacturing, especially in demanding sectors like aerospace. We ensure the quality of our AlSi10Mg powder through a multi-faceted approach rooted in advanced production technology and rigorous quality control:
- Advanced Production: We employ industry-leading Gaz Atomizasyonu ve PREP (Plazma Döner Elektrot Prosesi) technologies. These methods are optimized to produce metal powders with yüksek küresellik (improving flowability and packing density) and low satellite content, which are critical for consistent melting and achieving dense parts in LPBF. Explore more about our company and technology at Met3dp.com.
- Strict Raw Material Control: We carefully select and test raw materials to ensure they meet stringent purity requirements before atomization.
- Süreç Kontrolü: Atomization parameters are tightly controlled to achieve the desired Particle Size Distribution (PSD) optimized for LPBF processes and specific customer requirements.
- Comprehensive Quality Testing: Each batch of powder undergoes extensive testing in our well-equipped laboratory, including:
- Chemical Composition Analysis (e.g., via ICP-OES) to verify it meets AlSi10Mg specifications.
- Particle Size Distribution Measurement (e.g., via laser diffraction).
- Morphology Assessment (e.g., via SEM) to confirm high sphericity and minimal satellites.
- Flowability Testing (e.g., Hall Flowmeter) and Apparent/Tap Density measurements.
- Gas Content Analysis (Oxygen, Nitrogen) where critical.
- Batch Traceability: Rigorous lot control and documentation ensure full traceability from raw materials through atomization to the final packaged powder.
- Certificates of Analysis (CoA): We provide customers with detailed CoAs for each powder batch, confirming its compliance with agreed-upon specifications. This commitment to quality ensures that customers using Met3dp’s AlSi10Mg powder can have confidence in the consistency and performance of their additively manufactured aerospace components.
Conclusion: Elevating Aerospace Design with AlSi10Mg Additive Manufacturing
The journey through the intricacies of using AlSi10Mg for aerospace brackets via metal 3D printing reveals a technology brimming with transformative potential. Additive manufacturing, specifically Laser Powder Bed Fusion, is not merely an alternative production method; it’s an enabler of innovation, allowing aerospace engineers to break free from the constraints of traditional manufacturing and achieve unprecedented levels of design optimization, weight reduction, and component consolidation.
AlSi10Mg has firmly established itself as a versatile and valuable material in the aerospace AM toolkit. Its favorable combination of low density, good mechanical properties (when properly heat treated), excellent processability, and relative cost-effectiveness makes it an ideal candidate for a wide array of secondary structural brackets and system mounting components. The ability to leverage topology optimization and DfAM principles with AlSi10Mg allows for the creation of highly efficient, lightweight brackets that contribute directly to improved fuel economy, increased payload capacity, and overall aircraft performance – key drivers in the competitive aerospace market. While Ti-6Al-4V remains the choice for higher-stress, higher-temperature applications, AlSi10Mg provides a compelling balance of performance and value for many bracket needs.
However, successfully implementing AM for aerospace components requires more than just access to a printer and powder. It demands a holistic approach encompassing:
- Intelligent Design: Embracing DfAM principles to maximize benefits.
- Malzeme Bilimi: Understanding material properties and the critical role of powder quality.
- Süreç Kontrolü: Mastering the complexities of the LPBF process.
- Rigorous Post-Processing: Implementing essential steps like heat treatment, finishing, and inspection.
- Kalite Güvencesi: Adhering to stringent aerospace standards like AS9100.
Perhaps most importantly, success hinges on choosing the right manufacturing partner. The ideal partner, like Met3dp, brings not only state-of-the-art equipment for printing and powder production but also deep expertise across the entire AM workflow. They act as collaborators, offering DfAM support, ensuring process stability, managing complex post-processing chains, and providing the rigorous quality control and traceability mandated by the aerospace sector.
Bu future of aerospace manufacturing will undoubtedly see additive manufacturing play an increasingly significant role. As the technology matures, materials improve, and design tools become more sophisticated, AM will continue to unlock new possibilities for creating lighter, stronger, and more efficient aircraft. AlSi10Mg 3D printed brackets are a prime example of this ongoing revolution, demonstrating tangible benefits today.
For engineers and procurement managers looking to explore the potential of AlSi10Mg bracket solutions or other metal AM applications, the time to engage is now. We invite you to leverage Met3dp aerospace capabilities. Contact Met3dp today to discuss your specific component challenges and discover how our comprehensive additive manufacturing innovation, encompassing industry-leading printers, advanced metal powders, and extensive application expertise, can help you achieve your aerospace manufacturing goals and elevate your designs to new heights.
Paylaş
MET3DP Technology Co, LTD, merkezi Qingdao, Çin'de bulunan lider bir katmanlı üretim çözümleri sağlayıcısıdır. Şirketimiz, endüstriyel uygulamalar için 3D baskı ekipmanları ve yüksek performanslı metal tozları konusunda uzmanlaşmıştır.
İşletmeniz için en iyi fiyatı ve özelleştirilmiş Çözümü almak için sorgulayın!
İlgili Makaleler
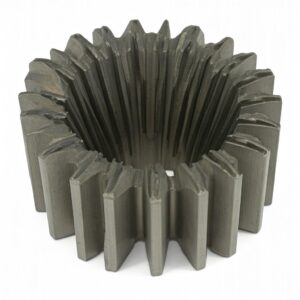
Yüksek Performanslı Nozul Kanat Segmentleri: Metal 3D Baskı ile Türbin Verimliliğinde Devrim
Daha Fazla Oku "Met3DP Hakkında
Son Güncelleme
Bizim Ürünümüz
BİZE ULAŞIN
Herhangi bir sorunuz var mı? Bize şimdi mesaj gönderin! Mesajınızı aldıktan sonra tüm ekibimizle talebinize hizmet edeceğiz.
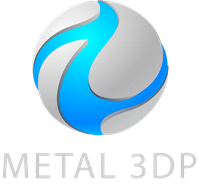
3D Baskı ve Katmanlı Üretim için Metal Tozları