Aerospace-Grade Cooling Jackets via Additive Manufacturing
İçindekiler
Introduction: Revolutionizing Thermal Management with Custom Aerospace Cooling Jackets
The aerospace industry operates at the extremes of performance, pushing materials and components to their absolute limits. From the scorching heat within jet engine turbines to the critical temperature sensitivities of advanced avionics, effective thermal management is not just a requirement—it’s fundamental to safety, efficiency, and mission success. Managing heat effectively dictates component lifespan, fuel efficiency, and overall system reliability. Inadequate cooling can lead to catastrophic failures, reduced performance, and costly maintenance cycles, making advanced thermal solutions a constant focus for aerospace engineers and procurement managers seeking reliable aerospace thermal management strategies.
Traditionally, dissipating this intense heat has relied on cooling systems often involving complex assemblies of machined parts, castings, and brazed components. However, as aerospace designs become more compact, powerful, and integrated, the demands on thermal management systems intensify. This is where the concept of a custom cooling jacket becomes crucial. A cooling jacket is essentially a specialized casing or integrated structure designed to surround a heat-generating component. It incorporates internal channels or passages through which a coolant (liquid or gas) flows, absorbing excess heat and transferring it away from the critical area. These jackets are vital for maintaining optimal operating temperatures for components like:
- Turbine blades and nozzles
- Engine casings and combustion chambers
- High-power electronic modules (avionics)
- Hydraulic actuators and pumps
- Satellite propulsion and power systems
The challenge lies in creating cooling jackets that are not only effective but also lightweight, compact, and perfectly tailored to the intricate geometries of modern aerospace components. Traditional manufacturing methods often struggle to produce the highly complex internal channel networks needed for optimal thermal performance without resorting to multiple, heavy parts requiring complex joining processes, which introduce potential failure points.
This is where a paradigm shift is occurring, driven by the capabilities of metal katkılı üretim (AM), commonly known as metal 3D baskı. This transformative technology allows for the layer-by-layer construction of components directly from digital models, enabling the creation of geometries previously considered impossible or prohibitively expensive to manufacture. For aerospace cooling jackets, metal AM unlocks unprecedented design freedom, allowing engineers to design and produce yüksek performanslı bileşenler ile:
- Highly complex internal cooling channels: Following the exact contours of the heat source for maximum efficiency (conformal cooling).
- Optimized flow paths: Designed using fluid dynamics simulation to minimize pressure drop and maximize heat transfer.
- Integrated, single-piece designs: Eliminating the need for brazing or welding multiple parts, reducing weight and potential leak paths.
- Hafif yapılar: Utilizing topology optimization and advanced materials to minimize mass without sacrificing strength or thermal performance.
Companies specializing in geli̇şmi̇ş üreti̇m techniques, like Met3dp, are at the forefront of leveraging metal AM for these demanding applications. By combining cutting-edge printing technologies with high-performance metal powders, it’s now possible to manufacture aerospace-grade cooling jackets that offer superior thermal performance, reduced weight, and faster development cycles compared to conventional methods. This blog post will delve into the specifics of using metal AM for aerospace cooling jackets, exploring applications, design considerations, material choices like IN625 and AlSi10Mg, and how to partner with the right metal 3D printing aerospace supplier to achieve optimal results. For engineers and procurement specialists looking for next-generation thermal solutions, understanding the potential of metal AM is no longer optional—it’s essential for staying competitive.
Core Applications: Where are Custom Cooling Jackets Deployed in Aerospace?
Custom cooling jackets fabricated using metal additive manufacturing are finding increasingly critical roles across a wide spectrum of aerospace and related high-technology sectors. Their ability to provide targeted, highly efficient thermal management in complex, space-constrained environments makes them invaluable. Procurement managers sourcing aerospace component suppliers and engineers designing next-generation systems should be aware of the diverse applications where these advanced components deliver significant advantages.
Key Aerospace Applications:
- Gaz Türbini Motorları: This is perhaps the most demanding environment.
- Turbine Blade and Vane Cooling: Internal cooling passages within turbine blades and vanes are critical for allowing higher operating temperatures, boosting engine efficiency and power output. Metal AM enables incredibly intricate, conformal cooling channels that traditional casting struggles to replicate, leading to better cooling effectiveness and longer blade life.
- Combustion Chamber Liners: Cooling jackets integrated into or surrounding combustor liners help manage the extreme temperatures of fuel combustion, preventing material degradation and ensuring stable operation. AM allows for optimized channel designs tailored to specific heat flux patterns.
- Engine Casings and Structures: Specific areas of engine casings or structural components exposed to high temperatures can benefit from integrated cooling channels, managing thermal expansion and maintaining structural integrity.
- Nozzle Components: Exhaust nozzle components often require cooling to withstand high-velocity, high-temperature gas flows. AM allows for integrated cooling designs that are both effective and lightweight.
- Avionics and Electronics Cooling: Modern aircraft and spacecraft rely heavily on sophisticated electronics that generate significant heat.
- High-Power Processors and FPGAs: Custom cold plates or chassis with integrated micro-channel cooling jackets, often made from thermally conductive alloys like AlSi10Mg via AM, can directly cool powerful processing units in flight computers, radar systems, and electronic warfare suites.
- Power Electronics Modules: Converters, inverters, and power distribution units generate substantial heat. AM enables compact, conformally cooled enclosures or heat sinks that maximize heat dissipation in tightly packed avionics bays. Avionics cooling systems benefit immensely from the design freedom offered by AM.
- Integrated Thermal Management Chassis: Entire avionics enclosures can be designed with embedded cooling channels, providing a holistic thermal solution that reduces complexity and weight compared to attaching separate heat sinks.
- Hydraulic Systems: High-pressure hydraulic systems generate heat through fluid friction and pump operation.
- Actuator Manifolds: Cooling jackets integrated into hydraulic manifolds or surrounding actuators can prevent fluid overheating, ensuring consistent performance and extending seal life, particularly in demanding flight control applications.
- Pump Housings: Integrating cooling channels directly into pump housings can improve efficiency and reliability.
- Satellite and Spacecraft Thermal Control: Managing temperature extremes in the vacuum of space is critical.
- Propulsion Systems: Thruster components, particularly in chemical propulsion systems, require cooling during operation. AM allows for lightweight, intricate cooling jackets suitable for mass-sensitive spacecraft.
- Battery Systems: Maintaining optimal battery temperature is crucial for performance and longevity. Custom cooling plates or jackets manufactured via AM can provide efficient thermal regulation for satellite battery packs.
- Payload Instruments: Sensitive scientific instruments often require precise temperature control. AM enables the creation of highly customized thermal straps or cooled enclosures.
Beyond Aerospace:
The advantages of AM cooling jackets extend to other industries demanding high performance:
- Savunma: Cooling for directed energy weapons, radar systems, military vehicle electronics, and high-performance engines.
- Yüksek Performanslı Otomotiv: Engine components (turbochargers, pistons), battery cooling for electric vehicles, performance electronics cooling.
- Advanced Industrial Systems: Cooling for high-power lasers, specialized manufacturing equipment, robotics, and energy generation components.
Primary Functions:
Across these applications, aerospace parts manufacturing using AM for cooling jackets serves several key functions:
- Enhanced Heat Dissipation: Significantly improving the transfer of heat away from critical components.
- Temperature Stabilization: Maintaining components within their optimal operating temperature range, improving reliability and performance consistency.
- Performans Optimizasyonu: Allowing systems (like engines) to operate at higher temperatures or power levels safely.
- Component Life Extension: Reducing thermal stress and material degradation, leading to longer service life and lower maintenance costs.
- Ağırlık Azaltma: Achieving required thermal performance with less material compared to traditional multi-part assemblies.
The ability to tailor the cooling jacket design precisely to the component’s geometry and thermal load profile, combined with the capability to use advanced materials, makes metal AM a powerful tool for engineers tackling the toughest thermal challenges in engine thermal control and beyond.
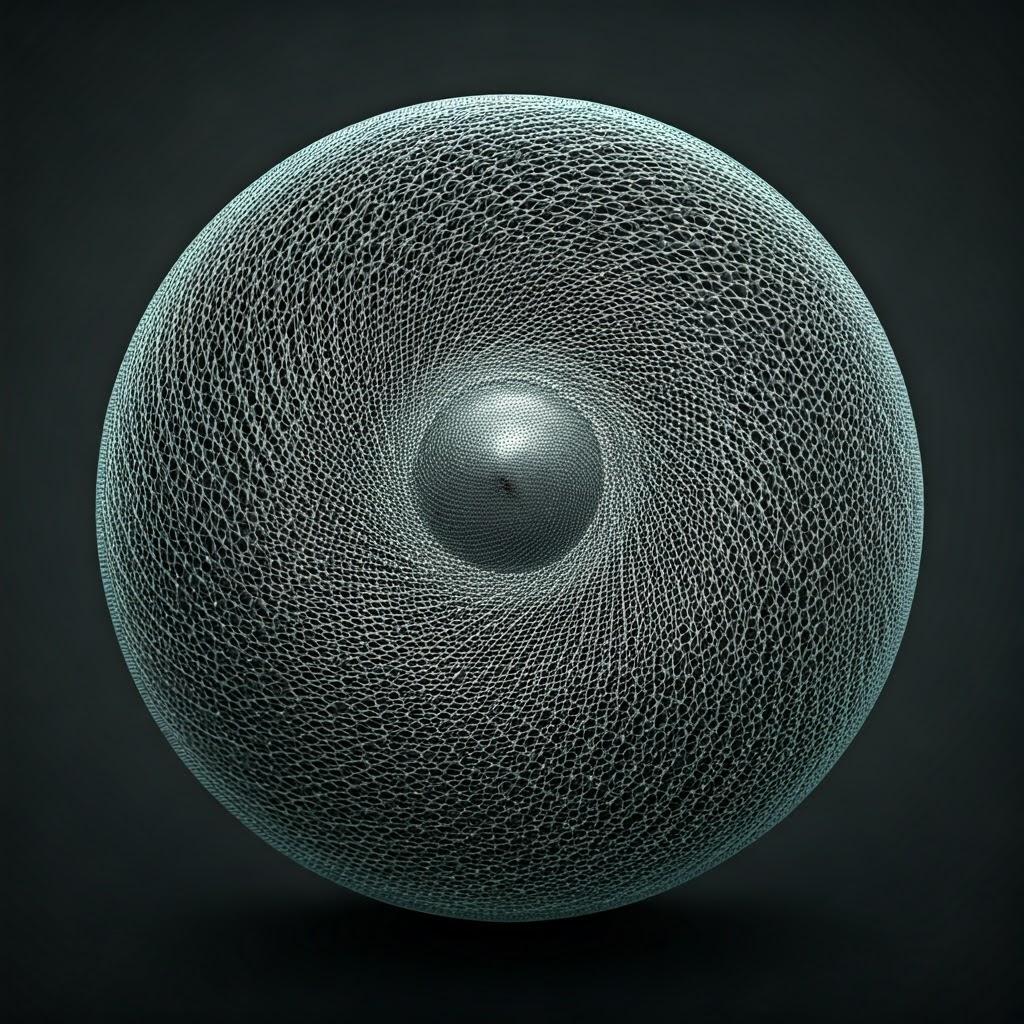
The Additive Advantage: Why Choose Metal 3D Printing for Aerospace Cooling Jackets?
While traditional manufacturing methods like CNC machining, casting, and brazing have served the aerospace industry for decades, they face inherent limitations when it comes to producing highly optimized cooling jackets. Creating complex internal geometries often involves intricate multi-step processes, compromises in design, increased part count, and significant weight penalties. Metal additive manufacturing fundamentally changes the equation, offering compelling additive manufacturing benefits specifically suited for advanced thermal management components like cooling jackets. Procurement managers and engineers evaluating metal AM vs CNC machining or casting need to understand these distinct advantages.
Limitations of Traditional Methods:
- İşleme: While precise, machining struggles to create complex, non-linear internal channels. Deep, curved passages are often impossible or require splitting the part into sections that must later be joined (usually by welding or brazing), adding weight, cost, and potential failure points.
- Oyuncu seçimi: Investment casting can produce complex shapes, but achieving thin walls, intricate internal cores with high accuracy, and excellent surface finish within channels can be challenging. Core removal can also be difficult, and porosity can be a concern. Design freedom is less than AM.
- Brazing/Welding: Joining multiple machined or cast sections introduces residual stresses, potential leak paths, and adds significant weight and manual labor costs. The joints themselves can also impede thermal transfer or create flow disturbances.
Advantages of Metal Additive Manufacturing (AM):
Metal AM processes, such as Laser Powder Bed Fusion (LPBF) and Selective Electron Beam Melting (SEBM), build parts layer by layer, offering unique capabilities:
- Benzersiz Tasarım Özgürlüğü: This is the most significant advantage. AM allows engineers to design for function, not just for manufacturability.
- Complex Internal Geometries: Create intricate, freeform internal cooling channels that precisely follow the contours of the heat source (conformal cooling channels). This maximizes surface area contact and heat transfer efficiency.
- Optimized Flow Paths: Design channels with varying cross-sections, integrated turbulators, or bio-inspired branching structures (e.g., mimicking vascular networks) to optimize coolant flow and minimize pressure drop, often guided by Computational Fluid Dynamics (CFD) simulation.
- Organic Shapes: Produce smooth, curved external shapes that integrate seamlessly with surrounding components.
- Parça Konsolidasyonu: Multiple components that would traditionally be manufactured separately and then assembled (e.g., a housing, multiple channel sections, inlet/outlet fittings) can often be integrated into a single, monolithic part.
- Reduced Part Count: Simplifies assembly, logistics, and supply chain management.
- Elimination of Joints: Removes potential leak paths and failure points associated with brazing or welding.
- Improved Structural Integrity: Monolithic parts can be stronger and stiffer than assemblies.
- Significant Weight Reduction: Critical for aerospace applications.
- Topology Optimization: Software tools can optimize material distribution, removing unnecessary mass while maintaining structural integrity and thermal performance. AM can directly produce these complex, lightweight structures.
- Thin Walls & Fine Features: AM processes can create features with thinner walls than often achievable with casting, directly reducing component weight.
- Malzeme Seçimi: Enables the use of high strength-to-weight ratio materials like Aluminum (AlSi10Mg) or Titanium alloys where appropriate. See how advanced metal 3D baskı technologies enable this.
- Hızlı Prototipleme ve Yineleme: AM allows for the quick production of functional prototypes directly from CAD models.
- Faster Development Cycles: Engineers can test multiple design variations quickly and cost-effectively, accelerating the optimization process.
- Reduced Tooling Costs: Eliminates the need for expensive molds or complex machining fixtures, especially beneficial for low-volume, high-value aerospace parts.
- Malzeme Verimliliği: Powder bed fusion processes typically use only the material needed for the part and support structures, resulting in less material waste compared to subtractive manufacturing, where significant amounts of raw material are often machined away.
Comparison Table: AM vs. Traditional Methods for Cooling Jackets
Özellik | Metal Katmanlı Üretim (AM) | Geleneksel İşleme | Geleneksel Döküm | Brazed/Welded Assemblies |
---|---|---|---|---|
Internal Complexity | Very High (Conformal, freeform channels) | Low to Medium (Linear limits) | Medium to High (Core limits) | Medium (Section limits) |
Parça Konsolidasyonu | High (Monolithic designs possible) | Düşük | Orta | Çok Düşük |
Ağırlık Azaltma | Excellent (Topology optimization, thin walls) | Orta düzeyde | Orta düzeyde | Low (Joints add weight) |
Tasarım Özgürlüğü | Çok Yüksek | Düşük | Orta | Düşük |
Prototipleme Hızı | Hızlı | Slow to Moderate | Slow (Tooling required) | Yavaş |
Kalıp Maliyeti | None / Minimal | Moderate (Fixtures) | High (Molds/Patterns) | Low (Jigs/Fixtures) |
Malzeme Atıkları | Low (Powder recycle possible) | High (Subtractive) | Orta düzeyde | Orta düzeyde |
Potential Weak Points | Support removal, internal finish (can be post-processed) | Feature limitations | Porosity, core shift | Joints (Leaks, stress) |
En Uygun Olanlar | Highly complex, optimized, lightweight, low-vol parts | High precision external features | Medium complexity, higher vol | Simpler channel designs |
Sayfalara Aktar
Choosing metal AM for aerospace cooling jackets is not just about adopting a new manufacturing technique; it’s about unlocking superior performance, achieving aerospace weight reduction targets, and accelerating innovation in thermal management – capabilities that are increasingly vital for demanding aerospace parts manufacturing.
Material Focus: IN625 and AlSi10Mg for High-Performance Cooling
Selecting the right material is paramount for the performance and reliability of aerospace cooling jackets, especially when produced via additive manufacturing. The chosen alloy must possess the right combination of thermal properties, mechanical strength (often at elevated temperatures), corrosion resistance, and compatibility with the AM process. For many demanding aerospace cooling applications, two materials stand out: the nickel-based superalloy Inconel 625 (IN625) and the aluminum alloy AlSi10Mg. Understanding their properties is crucial for engineers specifying components and for procurement teams sourcing metal tozu tedarikçileri like Met3dp, known for their high-quality, spherical powders optimized for AM.
Inconel 625 (IN625): The High-Temperature Workhorse
IN625 is a nickel-chromium-molybdenum-niobium superalloy renowned for its exceptional combination of high strength, toughness, and outstanding corrosion and oxidation resistance across a broad temperature range, from cryogenic levels up to ~1000°C (1800°F). These properties make it a primary choice for cooling jackets operating in harsh, high-temperature environments, such as those found in gas turbine engines.
- Key Properties & Benefits for Cooling Jackets:
- High Temperature Strength: Maintains excellent mechanical properties (tensile, creep, fatigue strength) even at extreme temperatures found in engine hot sections. This ensures the jacket retains its structural integrity under thermal and mechanical loads.
- Mükemmel Korozyon Direnci: Resists oxidation and corrosion in aggressive environments, including combustion byproducts, jet fuel, hydraulic fluids, and saltwater exposure. Critical for longevity.
- Good Fabricability & Weldability: While AM eliminates traditional welding for part consolidation, the inherent weldability of IN625 is beneficial for the layer-by-layer fusion process in AM, leading to dense, robust parts. It also allows for post-print welding repairs or modifications if needed.
- Yorulma Direnci: Withstands cyclic thermal and mechanical loading common in aerospace operations.
- Good Thermal Stability: Resists degradation over long exposure to high temperatures.
- Suitability in AM: IN625 is well-established in powder bed fusion processes (LPBF and EBM). It generally processes well, allowing for the creation of complex geometries with good density and mechanical properties that often meet or exceed those of wrought counterparts after appropriate post-processing (like heat treatment).
- Typical Aerospace Applications: Turbine engine components (combustor liners, exhaust systems, turbine shrouds), high-temperature heat exchangers, rocket engine components. Its use in IN625 aerospace applications is widespread where extreme heat and corrosion resistance are required.
AlSi10Mg: The Lightweight Thermal Conductor
AlSi10Mg is a widely used aluminum alloy, roughly equivalent to casting alloy A360. It contains silicon and magnesium, which provide good strength, hardness, and excellent fluidity during the melting/solidification cycle inherent in AM, making it highly processable. Its primary advantages for cooling jackets are its low density and good thermal conductivity.
- Key Properties & Benefits for Cooling Jackets:
- Low Density / High Strength-to-Weight Ratio: Approximately one-third the density of steel or nickel alloys, making it ideal for applications where weight saving is critical (avionics, spacecraft structures, automotive).
- Good Thermal Conductivity: Efficiently transfers heat away from the component being cooled. While not as high as pure aluminum, its conductivity is significantly better than steels or nickel alloys, making it effective for moderate temperature applications.
- Excellent Processability in AM: One of the easiest aluminum alloys to process via LPBF, allowing for fine features, thin walls, and complex geometries with good surface finish and density.
- İyi Korozyon Direnci: Offers adequate resistance to atmospheric corrosion for many aerospace environments.
- İşlem Sonrası Seçenekleri: Can be heat-treated (e.g., T6 condition) to significantly enhance mechanical properties (strength and hardness).
- Suitability in AM: AlSi10Mg is arguably the most common aluminum alloy used in metal AM. Its characteristics are well understood, and established parameter sets exist for achieving high-quality parts.
- Typical Aerospace Applications: Avionics chassis and enclosures, electronics cold plates, heat sinks, structural brackets with integrated cooling, automotive thermal management components (heat exchangers, battery cooling), satellite components. The AlSi10Mg thermal properties and low weight make it perfect for these uses.
Choosing Between IN625 and AlSi10Mg:
The choice primarily depends on the operating temperature and the specific balance required between heat resistance, thermal conductivity, and weight:
Özellik | IN625 | AlSi10Mg | Decision Driver |
---|---|---|---|
Maksimum Sıcaklık | Very High (~1000°C) | Moderate (~150-200°C continuous use) | Operating Environment Temperature |
Ağırlık | Higher Density (~8.44 g/cm³) | Low Density (~2.67 g/cm³) | Weight Sensitivity (Critical for Avionics/Space) |
Thermal Cond. | Lower (~10 W/m·K) | Good (~120-140 W/m·K) | Heat Load Density / Efficiency Requirement |
Güç | Very High (Especially at temp) | Moderate (Good strength-to-weight) | Mechanical Loads on the Cooling Jacket |
Maliyet | Higher (Material & Processing) | Daha düşük | Bütçe Kısıtlamaları |
Birincil Kullanım | Engine Hot Sections, Extreme Temps | Avionics, Structures, Moderate Temps | Application Environment |
Sayfalara Aktar
Met3dp’s Role in Material Supply:
Sourcing high-quality, consistent metal powders is critical for successful additive manufacturing. Companies like Met3dp play a vital role by specializing in the production of aerospace-grade metal powders. Utilizing advanced techniques like gas atomization and Plasma Rotating Electrode Process (PREP), Met3dp ensures its Met3dp metal powders, including grades suitable for IN625 and AlSi10Mg applications, exhibit:
- Yüksek Küresellik: Promotes good powder flowability and uniform spreading in the AM machine.
- Low Porosity: Reduces defects in the final part.
- Controlled Particle Size Distribution (PSD): Ensures consistent melting behavior and final part density.
- Yüksek Saflıkta: Minimizes contaminants that could compromise material properties.
By partnering with knowledgeable metal tozu tedarikçileri like Met3dp, aerospace manufacturers can be confident in the quality of the raw material, which is the foundation for producing reliable, high-performance 3D printed cooling jackets. Their expertise extends beyond powders to include optimizing printing processes on equipment like their SEBM printers, ensuring customers achieve the desired results from these advanced materials.
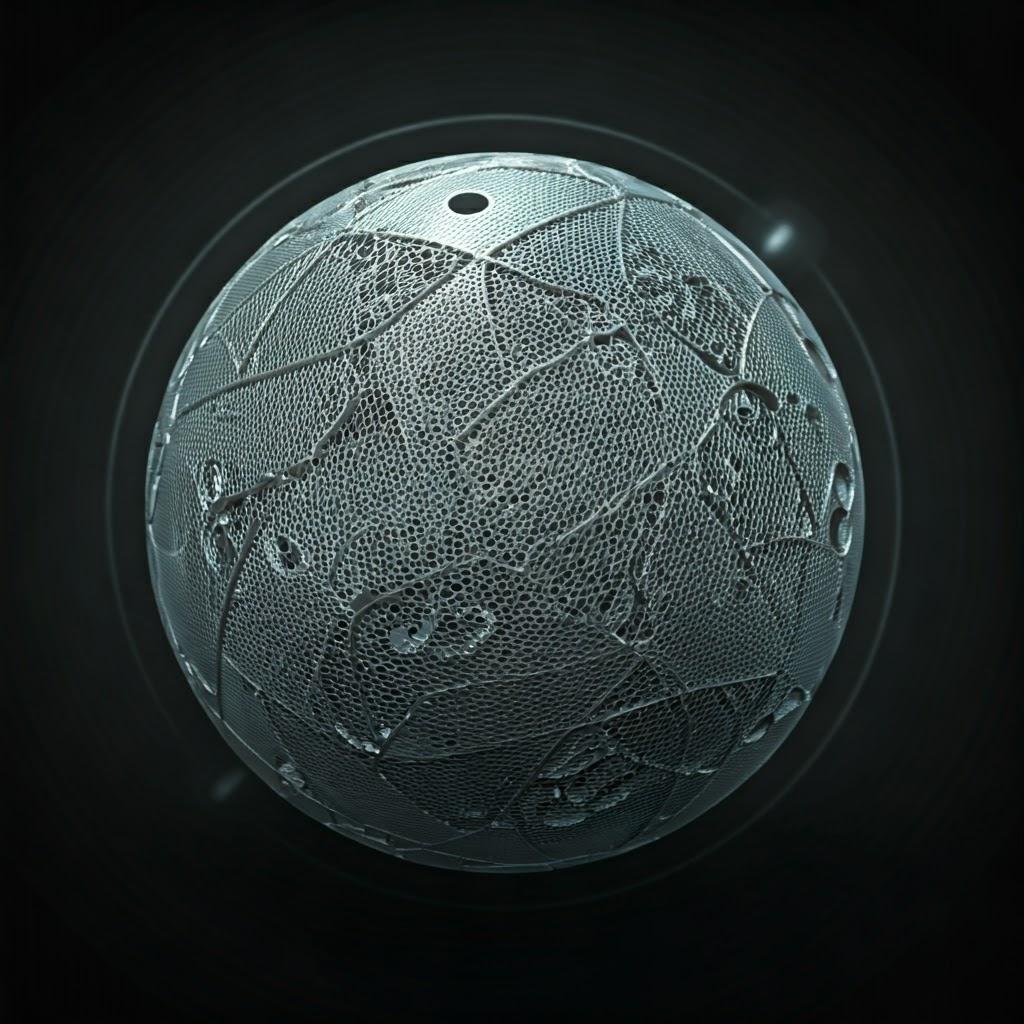
Design for Additive Manufacturing (DfAM): Optimizing Cooling Jacket Geometry
Simply replicating a design intended for traditional manufacturing using additive manufacturing often misses the true potential of the technology. To fully leverage the benefits of metal AM for aerospace cooling jackets—achieving maximum thermal performance, minimum weight, and optimal structural integrity—engineers must embrace Katmanlı Üretim Tasarımı (DfAM) principles. DfAM isn’t just about ensuring a part olabilmek be printed; it’s about actively designing features that capitalize on AM’s strengths while mitigating its constraints. This is crucial for optimizing cooling channels and creating truly superior components.
Core DfAM Principles for Cooling Jackets:
- Function-Driven Geometry (Complexity is Free):
- Konformal Soğutma Kanalları: Design internal channels that precisely follow the 3D contours of the heat-generating surface, maintaining a consistent distance for uniform and efficient heat extraction. This contrasts sharply with gun-drilled straight channels in machined parts.
- Optimized Channel Cross-Sections: Move beyond simple circular channels. Design elliptical, rectangular, or variable cross-sections to optimize flow velocity, pressure drop, and heat transfer characteristics based on CFD analysis. Integrate features like internal fins or turbulators directly into the channel design to enhance turbulence and heat exchange, without needing separate inserts.
- Bio-Inspired Designs: Utilize branching, tree-like structures (biomimicry) for fluid distribution, potentially minimizing pressure loss while ensuring coolant reaches all critical areas.
- Parça Konsolidasyonu:
- Actively look for opportunities to combine multiple components (e.g., housing, internal baffles, inlet/outlet ports, mounting features) into a single, monolithic AM part. This reduces assembly time, eliminates joint failures, and often decreases overall weight.
- Lightweighting Strategies:
- Topology Optimization: Use software tools to analyze load paths and remove material from non-critical areas, resulting in organic, lattice-like structures that maintain required strength and stiffness with significantly reduced mass. This is ideal for aerospace applications where every gram counts.
- Kafes Yapılar: Incorporate internal lattice structures not just for weight reduction but potentially to enhance stiffness or even promote specific fluid mixing within larger plenums of the cooling jacket.
- Thin-Wall Design: Leverage AM’s ability (within process limits) to create thinner, yet structurally sound, walls compared to casting, directly reducing weight.
- Designing for the AM Process: Özel durumların anlaşılması additive manufacturing design rules associated with the chosen process (e.g., LPBF, SEBM) is critical.
- Overhangs and Support Structures: Design to minimize steep overhangs (typically >45 degrees from horizontal) that require extensive support structures. Supports consume material, add print time, can be difficult to remove (especially internally), and impact surface finish.
- Kendini Destekleyen Açılar: Design features with angles less than ~45 degrees where possible.
- Teardrop/Diamond Shapes: Use optimized shapes for horizontal holes or channels to make them self-supporting.
- Internal Supports: Carefully consider the strategy for supporting complex internal channels. Design for accessibility for powder removal and potentially sacrificial, easily removable support structures if absolutely necessary. Consulting with AM experts like Met3dp on optimal baskı yöntemleri and support strategies is highly beneficial.
- Minimum Feature Size & Wall Thickness: Adhere to the minimum printable feature size and wall thickness capabilities of the specific AM machine and material being used (e.g., typically 0.3-0.5 mm for walls, slightly larger for positive features).
- Residual Stress Management: Consider part orientation and geometry to minimize the buildup of residual stress during the print, reducing the risk of warping or cracking. Large, flat planes can be particularly susceptible.
- Toz Giderme: Ensure internal channels and cavities have adequate drainage paths designed in, allowing unfused powder to be easily removed after printing. Trapped powder is a critical defect.
- Overhangs and Support Structures: Design to minimize steep overhangs (typically >45 degrees from horizontal) that require extensive support structures. Supports consume material, add print time, can be difficult to remove (especially internally), and impact surface finish.
- Designing for Post-Processing:
- Machining Allowances: If critical interfaces require tight tolerances achievable only through machining, add extra stock material (machining allowance) to those specific surfaces in the AM design.
- Surface Finish Considerations: Design features with accessibility in mind if specific surfaces require polishing or other finishing treatments. Internal channel surface finish requirements should be considered early, potentially influencing channel diameter and shape for accessibility to processes like Abrasive Flow Machining (AFM).
Tools and Techniques:
- CAD Software: Modern CAD packages increasingly incorporate DfAM-specific tools.
- Simulation (CFD & FEA): Computational Fluid Dynamics (CFD) is essential for optimizing internal channel flow and heat transfer. Finite Element Analysis (FEA) validates structural integrity under thermal and mechanical loads and helps predict stress concentrations. Simulation can guide topology optimization.
- Topology Optimization Software: Generates material-efficient designs based on load cases and design constraints.
By adopting a DfAM mindset, engineers and designers can move beyond simply using AM as a substitute manufacturing method and start creating truly optimized, next-generation hafif havacılık ve uzay bileşenleri and cooling jackets that deliver unparalleled performance and efficiency. This often requires close collaboration with AM service providers who understand the nuances of the technology.
Achieving Precision: Tolerance, Surface Finish, and Dimensional Accuracy in AM Cooling Jackets
While metal additive manufacturing offers incredible geometric freedom, understanding the achievable levels of precision is critical for engineers designing parts and procurement managers setting specifications, especially for aerospace components with tight assembly requirements. Metal 3D printing tolerances, surface finish, and overall dimensional accuracy are influenced by the AM process itself, the material used, part geometry, and post-processing steps.
Tolerances:
- As-Built Tolerances: The tolerances achievable directly from the AM machine are typically looser than conventional CNC machining. Common industry standards often cite:
- General Tolerances: ±0.1 mm to ±0.3 mm for smaller features (e.g., up to 25 mm).
- Larger Features: ±0.5% to ±1.0% of the nominal dimension for larger features.
- These values can vary significantly based on the specific machine (LPBF often offers slightly tighter tolerances than EBM), material (e.g., IN625 vs. AlSi10Mg behavior), part size and geometry (thermal distortion effects), and calibration quality.
- Achieving Tighter Tolerances: For critical interfaces, mating surfaces, or features requiring precision fits, post-print machining is almost always necessary. Tolerances achievable with CNC machining on AM parts are comparable to those on wrought materials (e.g., ±0.01 mm to ±0.05 mm or tighter, depending on the operation). DfAM principles dictate adding machining stock only where needed.
Yüzey İşlemi (Pürüzlülük):
- As-Built Surface Finish: The surface finish of AM parts is inherently rougher than machined surfaces due to the layer-by-layer fusion of powder particles.
- Typical Values (Ra): Often ranges from 6 µm to 25 µm (Ra – Arithmetic Average Roughness), heavily dependent on:
- Oryantasyon: Upward-facing surfaces are generally smoother than downward-facing surfaces (which are influenced by support structures) and vertical walls (which show layer lines).
- Süreç Parametreleri: Laser/electron beam power, scan speed, layer thickness all play a role.
- Toz Özellikleri: Particle size distribution influences the achievable finish.
- Internal Channels: Achieving a smooth finish inside complex, narrow internal cooling channels is a significant challenge. As-built roughness can impact fluid flow (increased friction, pressure drop) and potentially trap contaminants.
- Typical Values (Ra): Often ranges from 6 µm to 25 µm (Ra – Arithmetic Average Roughness), heavily dependent on:
- Yüzey İşleminin İyileştirilmesi:
- Bead Blasting/Shot Peening: Common methods to provide a uniform matte finish and remove loose particles, typically improving Ra slightly and potentially inducing beneficial compressive stresses.
- Tumbling/Vibratory Finishing: Suitable for batches of smaller parts to deburr edges and smooth surfaces.
- CNC İşleme: Provides the best surface finish on accessible external surfaces or critical internal features (if reachable).
- Parlatma: Manual or automated polishing can achieve very smooth, mirror-like finishes on external surfaces.
- Abrasive Flow Machining (AFM) / Extrude Hone: Used specifically for smoothing and deburring internal channels by flowing an abrasive putty through them. Essential for optimizing flow in high-performance cooling jackets.
- Electrochemical Polishing: Can smooth complex geometries but requires careful process control.
Boyutsal Doğruluk:
- Tanım: Refers to how closely the final part conforms to the nominal dimensions specified in the CAD model.
- Etkileyen Faktörler:
- Thermal Effects: Warping and distortion due to residual stresses built up during the rapid heating and cooling cycles are major contributors to dimensional inaccuracy, especially in large or complex parts.
- Machine Calibration: Accurate laser/beam positioning and layer thickness control are crucial.
- Destek Yapıları: Inadequate support can lead to sagging or deformation during the build.
- İşlem sonrası: Heat treatment can cause minor dimensional changes (shrinkage/growth), which must be accounted for. Machining, if not performed carefully, can introduce errors.
- Ensuring Accuracy:
- Process Simulation: Simulating the build process can help predict potential distortion and optimize orientation and support strategies.
- Careful Parameter Development: Using validated parameters for the specific material and machine.
- Robust Support Strategy: Designing effective supports to anchor the part and manage thermal stresses.
- Stres Giderici: Performing appropriate heat treatment cycles immediately after printing.
- Metrology and Inspection: Utilizing advanced inspection techniques like 3D scanning (structured light or laser) and Coordinate Measuring Machines (CMM) is essential for validating the dimensional accuracy of complex AM parts, including internal features where accessible or through sectioning for first article inspection. This ensures dimensional accuracy aerospace standartları karşılanır.
Achieving the required precision for aerospace manufacturing partners often involves a combination of careful DfAM, optimized printing, essential post-processing, and rigorous quality control metal AM. While as-built tolerances and finishes may suffice for some features, critical areas typically necessitate secondary operations to meet stringent aerospace requirements.
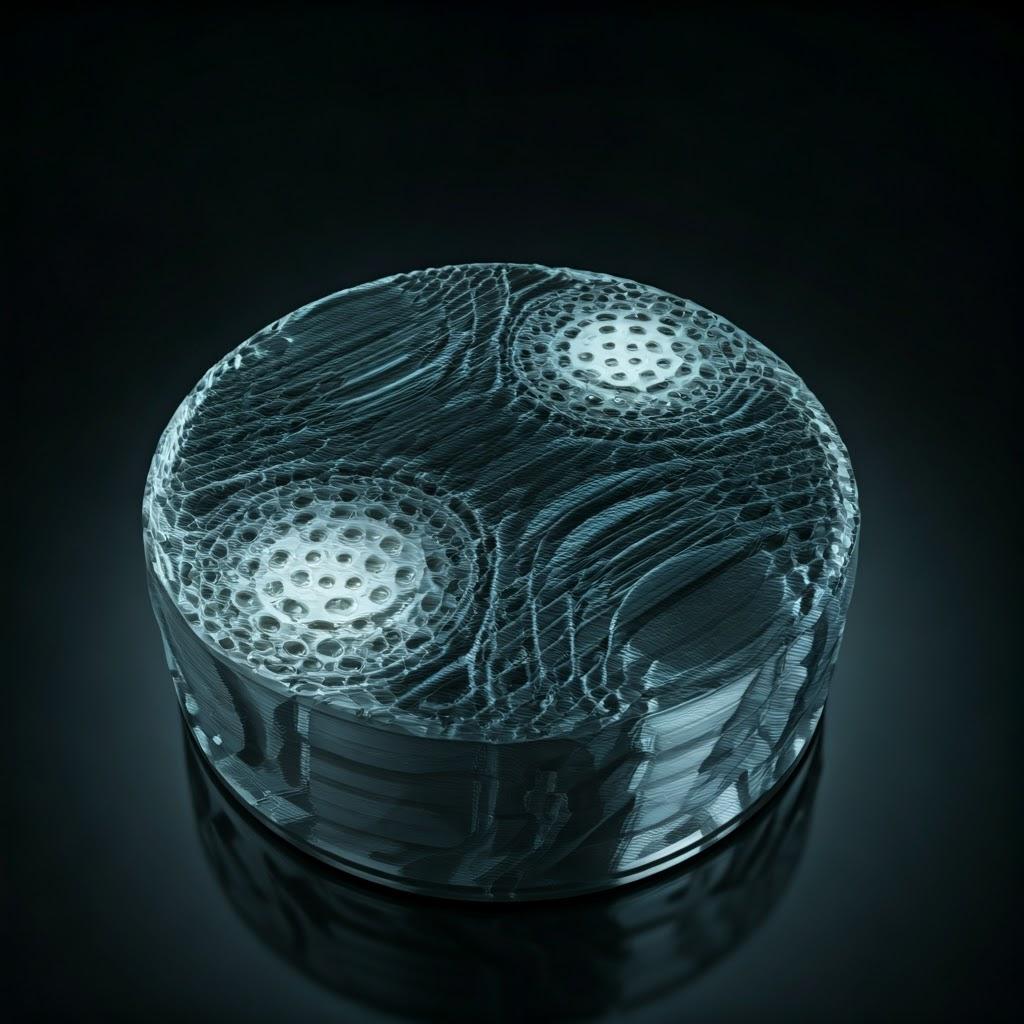
Beyond the Print: Essential Post-Processing Steps for Aerospace Cooling Jackets
A common misconception about metal additive manufacturing is that the part coming off the printer is immediately ready for use. For demanding applications like aerospace cooling jackets, the “print” is often just one step in a more comprehensive workflow. Metal AM post-processing is critical to ensure the part achieves the required material properties, dimensional accuracy, surface finish, and overall integrity. Neglecting these steps can compromise performance and safety.
Common Post-Processing Stages for AM Cooling Jackets:
- Powder Removal / Depowdering:
- Objective: Remove all unfused metal powder trapped within the part, especially from complex internal cooling channels and cavities. Trapped powder can impede coolant flow, add weight, and potentially dislodge during operation.
- Yöntemler: Manual brushing, compressed air jets, vibration, ultrasonic cleaning baths. Access holes designed during DfAM are crucial. For intricate internal networks, specialized flushing or flow-through systems may be needed. Complete powder removal is non-negotiable for quality.
- Stres Giderici:
- Objective: Reduce the internal residual stresses built up during the rapid heating and cooling cycles of the AM process. High residual stress can lead to distortion (warping) during or after removal from the build plate, cracking, and reduced fatigue life.
- Method: A specific heat treatment cycle performed önce removing the part from the build plate (if possible) or immediately after. The temperature and duration depend on the material (e.g., different cycles for IN625 vs. AlSi10Mg) and part geometry. This is arguably the most critical first step after depowdering.
- Yapı Plakasından Parça Çıkarma:
- Objective: Separate the printed part(s) from the metal build plate they were fused to during the printing process.
- Yöntemler: Typically done using Wire EDM (Electrical Discharge Machining) or a bandsaw. Care must be taken to avoid damaging the part.
- Destek Yapısının Kaldırılması:
- Objective: Remove the temporary support structures required during the build process for overhangs and complex features. Support removal additive manufacturing can be challenging, especially for internal supports within cooling channels.
- Yöntemler: Manual breaking/cutting (for easily accessible supports), CNC machining, grinding, EDM. Access for tools is key. Poorly removed supports can leave undesirable surface artifacts or block channels. DfAM aims to minimize the need for difficult-to-remove supports.
- Heat Treatment (Solution Annealing, Aging, Hot Isostatic Pressing – HIP):
- Objective: Optimize the material’s microstructure and mechanical properties (strength, ductility, hardness, fatigue life) to meet aerospace specifications. As-built AM parts often have non-equilibrium microstructures.
- Yöntemler:
- Solution Annealing & Aging: Standard heat treatments used for alloys like AlSi10Mg (T6 condition) and some nickel superalloys to achieve desired strength and ductility through precipitation hardening.
- Sıcak İzostatik Presleme (HIP): A process involving high temperature and high inert gas pressure applied simultaneously. HIP is highly effective at closing internal microporosity (improving density), enhancing fatigue properties, and reducing data scatter in mechanical performance. Often specified for critical aerospace components made from IN625 or titanium alloys. HIP requires specialized equipment and adds cost but significantly improves part integrity. Specifying heat treatment aerospace parts often includes HIP.
- Surface Finishing & Machining:
- Objective: Achieve the required surface roughness, dimensional tolerances on critical features, and prepare surfaces for sealing or coating.
- Yöntemler:
- CNC İşleme: Used for critical dimensions, mating surfaces, thread tapping, achieving smooth sealing faces. Requires careful fixture design for complex AM shapes. CNC machining 3D printed parts is standard practice for high-precision requirements.
- Taşlama: For flat surfaces requiring high precision and smooth finish.
- Parlatma: For achieving very low Ra values on specific external surfaces.
- Abrasive Flow Machining (AFM): Critical for smoothing internal cooling channels, improving flow efficiency and cleanability.
- Bead Blasting / Shot Peening: For a uniform finish and potentially improved fatigue life (shot peening induces compressive stress).
- Cleaning & Inspection:
- Objective: Ensure the part is free from contaminants (machining fluids, blasting media, debris) and meets all dimensional and quality specifications.
- Yöntemler: Final cleaning processes, dimensional inspection (CMM, 3D scanning), surface finish measurements, NDT (Non-Destructive Testing) such as CT scanning (Computed Tomography) to verify internal channel integrity and check for porosity, or Fluorescent Penetrant Inspection (FPI) for surface crack detection.
The specific sequence and necessity of these steps depend heavily on the application requirements, material choice, and part complexity. Working with an experienced AM provider who has robust post-processing capabilities is essential for successfully manufacturing flight-worthy aerospace cooling jackets.
Navigating Challenges: Common Issues in AM Cooling Jacket Production & Solutions
While metal additive manufacturing offers significant advantages for producing complex cooling jackets, it’s not without its challenges. Awareness of potential metal 3D printing defects and manufacturing hurdles is crucial for engineers and procurement managers to set realistic expectations and collaborate effectively with AM providers to mitigate risks. A reliable metal AM supplier like Met3dp leverages its expertise and process control to navigate these challenges.
Common Challenges & Mitigation Strategies:
- Warping and Distortion (Residual Stress):
- Sorun: Uneven heating and cooling causes internal stresses that can deform the part, especially large, flat sections or asymmetric geometries, often manifesting after removal from the build plate or during post-heat treatment.
- Hafifletme:
- Simulation: Use thermal simulation software to predict distortion and optimize part orientation on the build plate.
- Oryantasyon: Choose an orientation that minimizes large cross-sectional changes between layers and balances thermal mass.
- Support Strategy: Design robust support structures to anchor the part securely and act as heat sinks. Specialized support patterns can help manage stress.
- Süreç Parametreleri: Optimize laser/beam parameters (scan strategy, power, speed) to minimize thermal gradients.
- Immediate Stress Relief: Perform stress relief heat treatment before removing the part from the build plate whenever feasible.
- Gözeneklilik:
- Sorun: Small voids or pores within the material can reduce density, compromise mechanical properties (especially fatigue strength), and potentially act as crack initiation sites. Porosity can arise from gas entrapment during melting or incomplete fusion between layers (Lack-of-Fusion).
- Hafifletme:
- Toz Kalitesi: Use high-quality, dry powder with controlled morphology and low internal gas porosity (Met3dp’s focus on advanced powder production is key here).
- Optimized Parameters: Develop and utilize validated process parameters (power, speed, layer thickness, hatching) specific to the material and machine to ensure complete melting and fusion.
- Shielding Gas: Maintain a high-purity inert gas atmosphere (Argon or Nitrogen) in the build chamber to prevent oxidation and gas pickup.
- Sıcak İzostatik Presleme (HIP): The most effective post-processing method to close internal porosity and improve density. Often mandatory for critical parts.
- Cracking (Solidification or Liquation Cracking):
- Sorun: Cracks can form during solidification or in the heat-affected zone due to thermal stresses, particularly in crack-sensitive alloys or complex geometries with high stress concentrations.
- Hafifletme:
- Malzeme Seçimi: Some alloys are inherently more prone to cracking during AM than others.
- Parametre Optimizasyonu: Adjust parameters to reduce thermal gradients and cooling rates.
- Preheating: For some materials/processes (like EBM), preheating the powder bed reduces thermal shock.
- Geometry Design: Avoid sharp corners and abrupt changes in thickness that act as stress concentrators.
- Stres Giderici: Prompt stress relief is crucial.
- Support Removal Difficulty:
- Sorun: Supports, especially complex internal ones within cooling channels, can be extremely difficult and time-consuming to remove completely without damaging the part. Remnants can obstruct flow or break off later.
- Hafifletme:
- DfAM: Design parts to be self-supporting as much as possible. Minimize overhang angles.
- Optimized Support Design: Use support structures specifically designed for easier removal (e.g., conical supports, lower-density structures, specific interface layers).
- Erişilebilirlik: Design access ports or features to allow tools or processes like AFM to reach internal areas.
- Malzeme Seçimi: Some support materials or designs are engineered to be chemically dissolved or more easily broken away (less common in high-temp metal AM).
- Powder Removal from Internal Channels:
- Sorun: Ensuring all unfused powder is removed from long, narrow, or tortuous internal cooling passages can be very difficult. Trapped powder is a critical failure risk.
- Hafifletme:
- DfAM: Design channels with sufficient diameter and smooth bends. Incorporate multiple inlet/outlet ports and drainage holes specifically for powder removal. Avoid dead-end cavities.
- Optimize Edilmiş Yönlendirme: Orient the part to facilitate powder drainage during the build and depowdering process.
- Thorough Cleaning Procedures: Utilize multi-step cleaning involving vibration, compressed air, potentially ultrasonic cleaning, and flow-through flushing.
- Teftiş: Use methods like endoscopy (borescope inspection) or CT scanning to verify channel clearance.
- Surface Finish Inside Channels:
- Sorun: The inherent roughness of as-built AM surfaces inside channels increases pressure drop and can reduce thermal efficiency.
- Hafifletme:
- Süreç Optimizasyonu: Fine-tuning parameters can slightly improve internal finish.
- DfAM: Design channels large enough to allow for post-processing.
- İşlem sonrası: Employ Abrasive Flow Machining (AFM) or similar techniques specifically designed to smooth internal passages.
Successfully navigating these additive manufacturing challenges requires a combination of smart design (DfAM), meticulous process control, appropriate post-processing, and rigorous inspection. Partnering with an experienced AM service provider, such as Met3dp, who understands these complexities and possesses the necessary equipment and expertise, is crucial for mitigating risks and achieving high-quality, reliable aerospace cooling jackets. You can explore their comprehensive approach on their main site: https://met3dp.com/.
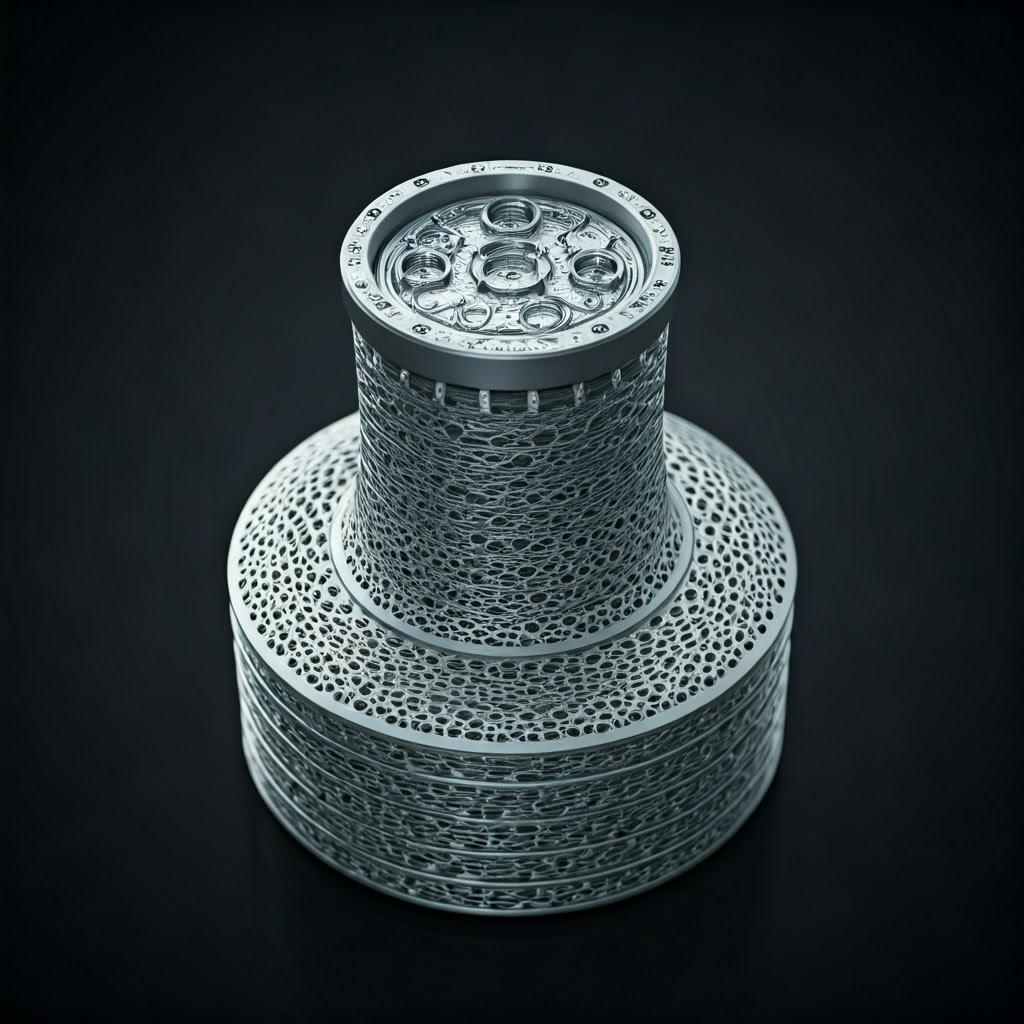
Supplier Selection: Choosing the Right Metal 3D Printing Service Partner for Aerospace
Selecting the right manufacturing partner is always critical in aerospace, but it takes on even greater importance when dealing with advanced technologies like metal additive manufacturing for complex components such as cooling jackets. The capabilities, expertise, and quality systems of your chosen metal AM service provider will directly impact the success of your project. For procurement managers and engineering teams involved in procurement additive manufacturing, evaluating potential suppliers requires a specific focus beyond traditional manufacturing assessments.
Key Criteria for Evaluating Aerospace AM Suppliers:
- Aerospace Certifications & Quality Management:
- AS9100 Certification: This is the standard quality management system (QMS) for the aviation, space, and defense industries. Certification to AS9100 (or equivalent, like EN 9100) demonstrates a provider’s commitment to rigorous quality processes, traceability, risk management, and continuous improvement essential for aerospace components. Always verify the scope of the certification.
- Robust QMS: Even without AS9100, a supplier must demonstrate a mature QMS covering process control, material handling, traceability, non-conformance management, and inspection protocols.
- Material Expertise & Portfolio:
- Specific Alloy Experience: Does the supplier have proven experience printing and post-processing the required alloy (e.g., IN625, AlSi10Mg)? Ask for case studies or evidence of successful projects with these materials.
- Powder Quality Control: How do they manage powder sourcing, testing, handling, storage, and recycling? Do they work with reputable powder manufacturers or produce their own high-quality powders, like Met3dp does with its advanced atomization techniques? Consistency in powder quality is crucial for repeatable results.
- Material Characterization: Do they have capabilities for material testing (tensile, fatigue, microstructure) to validate properties of printed parts?
- Equipment Capabilities & Technology:
- Appropriate AM Technology: Do they operate the right type of AM machines (e.g., LPBF, SEBM) best suited for your material and application? Do they have printers with sufficient build volume for your cooling jacket size?
- Machine Maintenance & Calibration: Are their machines well-maintained and regularly calibrated to ensure accuracy and repeatability?
- Capacity & Redundancy: Do they have sufficient machine capacity to meet your lead time requirements, including potential redundancy in case of machine downtime?
- Engineering & DfAM Support:
- Teknik Uzmanlık: Does the supplier employ engineers and technicians with deep expertise in AM processes, materials science, and DfAM principles? Can they provide valuable feedback on your design to optimize it for printability, performance, and cost?
- Collaborative Approach: A good partner acts as an extension of your team, collaborating on design iterations and problem-solving. Companies like Met3dp emphasize this partnership approach, leveraging decades of collective expertise. Learn more about their philosophy and background Hakkımızda.
- Kapsamlı İşlem Sonrası Yetenekleri:
- Şirket İçi ve Dış Kaynaklı: Does the supplier have in-house capabilities for critical post-processing steps like stress relief, heat treatment (including potentially HIP), support removal, precision CNC machining, surface finishing (including internal channel treatments like AFM), and NDT/inspection? Relying heavily on external subcontractors can add lead time, cost, and logistical complexity.
- Süreç Kontrolü: Are their post-processing steps well-documented and controlled under their QMS?
- Inspection and Metrology:
- Advanced Capabilities: Do they possess the necessary equipment (CMM, 3D scanners, CT scanners, borescopes) and expertise for thorough dimensional inspection, internal feature validation, and NDT of complex AM parts?
- Reporting: Can they provide comprehensive inspection reports documenting compliance with specifications?
- Track Record & Experience:
- Aerospace Project History: Have they successfully delivered similar components for other aerospace clients? Can they provide (non-confidential) references or case studies?
- Endüstri İtibarı: What is their reputation within the aerospace and AM industries?
Questions to Ask Potential Suppliers:
- What is your experience with printing [Specific Alloy, e.g., IN625] for aerospace applications?
- Can you describe your powder handling and quality control procedures?
- What is your typical process flow for a component like this, including all post-processing steps?
- Which post-processing operations do you perform in-house?
- How do you handle support structure design and removal for complex internal channels?
- What methods do you use to verify internal channel clearance and surface finish?
- What are your capabilities for dimensional inspection and NDT?
- Can you provide an example of how you’ve helped a client optimize a design for AM?
- What are your standard lead times for parts of this complexity and material?
- Are you AS9100 certified? Can you provide a copy of your certificate and scope?
Choosing the right partner is crucial for leveraging the full potential of aerospace 3D printing services. Look for suppliers like Met3dp who offer comprehensive solutions, from high-quality powders and advanced printing equipment (like their SEBM systems) to expert engineering support and robust quality assurance, ensuring your demanding Met3dp capabilities align with project needs.
Understanding Investment: Cost Factors and Lead Times for AM Cooling Jackets
While additive manufacturing offers significant performance and design benefits, understanding the associated costs and lead times is essential for project planning and budgeting. The metal 3D printing cost for an aerospace cooling jacket is influenced by a complex interplay of factors, often differing significantly from traditional manufacturing cost structures. Similarly, additive manufacturing lead time can offer advantages but is also subject to various influences.
Key Cost Drivers for AM Cooling Jackets:
- Malzeme Maliyeti:
- Powder Price: High-performance aerospace-grade metal powders (especially nickel superalloys like IN625) are significantly more expensive than standard engineering alloys. Cost depends on the alloy, required quantity, and supplier.
- Powder Consumption: The cost is directly related to the volume (and thus weight) of the final part, plus any material used for support structures. Material efficiency is high, but the raw material itself is costly. Powder recycling programs can help mitigate costs over time.
- Machine Time (Print Time):
- Build Volume & Complexity: The larger and more complex the part, the longer it takes to print layer by layer. Print time is often a primary cost driver. Factors include part height, total volume, and the density of features on each layer.
- Machine Hourly Rate: AM machines represent a significant capital investment, and their operating costs (power, gas, maintenance) contribute to the hourly rate charged by service providers.
- Destek Yapıları:
- Hacim: Supports consume expensive powder material.
- Print Time: Printing supports adds to the overall build time.
- Sökme İşçiliği/Süresi: Removing supports, especially complex internal ones, can be labor-intensive and require specialized processes, adding significant cost. DfAM to minimize supports is key for cost optimization.
- Post-Processing Intensity:
- Isıl İşlem: Standard stress relief and aging cycles add cost; more advanced processes like HIP add significantly more due to specialized equipment and longer cycle times.
- İşleme: The extent of required CNC machining (number of setups, complexity of features) directly impacts cost.
- Yüzey İşlemi: Processes like AFM for internal channels, polishing, or specialized coatings add costs based on labor, consumables, and equipment time.
- Teftiş: Rigorous NDT (like CT scanning) and CMM inspection add cost but are often non-negotiable for critical aerospace parts.
- Engineering & Setup:
- DfAM Support: If design optimization or significant engineering consultation is required from the AM provider, this will factor into the cost.
- Build Preparation: Setting up the build file, planning orientation and supports, and machine setup involves skilled labor time.
- Quantity & Batching:
- Ölçek Ekonomileri: While AM is suited for low volumes, printing multiple parts in a single build (batching) can slightly reduce the per-part cost by optimizing machine utilization and setup time. However, the per-part material and print time costs remain largely constant. Wholesale additive manufacturing pricing might apply for larger, regular orders.
Factors Influencing Lead Time:
- Design & Preparation: Time required for design finalization, DfAM checks, simulation (if needed), and build file preparation.
- Machine Availability: Queue times for suitable AM machines at the service provider. High demand for specific machines or materials can impact lead times.
- Print Time: Can range from hours for small parts to many days or even weeks for very large, complex components.
- Post-Processing Queue & Duration: Each post-processing step (heat treatment, machining, finishing, inspection) adds time. HIP cycles, for example, can take a full day or more, plus queue times. Support removal can be a bottleneck.
- Shipping & Logistics: Time required for transportation from the AM provider to your facility.
Comparing AM Costs & Lead Times to Traditional Methods:
It’s crucial to consider the total cost and value proposition:
- Unit Cost: For very simple parts produced in high volumes, traditional methods are often cheaper per unit. For highly complex, low-volume parts like optimized cooling jackets, AM can be competitive or even cheaper when factoring in eliminated tooling and assembly costs.
- Kurşun zamanı: AM excels at rapid prototyping and can often deliver initial functional parts much faster than methods requiring tooling (casting) or complex multi-axis machining setups. For production parts, the total lead time depends heavily on post-processing requirements.
- Performance Value: The cost analysis must include the value derived from AM’s benefits – weight reduction (fuel savings), improved thermal performance (efficiency, component life), part consolidation (reliability), and design possibilities unobtainable otherwise.
Tips for Optimizing Cost:
- Embrace DfAM: Minimize supports, consolidate parts, use topology optimization.
- Optimize for Batching: If multiple units are needed, discuss batching opportunities with the supplier.
- Specify Requirements Clearly: Avoid over-specifying tolerances or surface finishes where not strictly necessary.
- Consider Material Choice: Use the most cost-effective material that meets all performance requirements (e.g., AlSi10Mg is generally less expensive than IN625 if temperatures allow).
Understanding the cost components and lead time factors allows for better budgeting, planning, and informed discussions with potential aerospace component pricing suppliers. Exploring the range of materials and solutions available, such as those detailed under Met3dp’s product offerings, can help identify the most effective options.
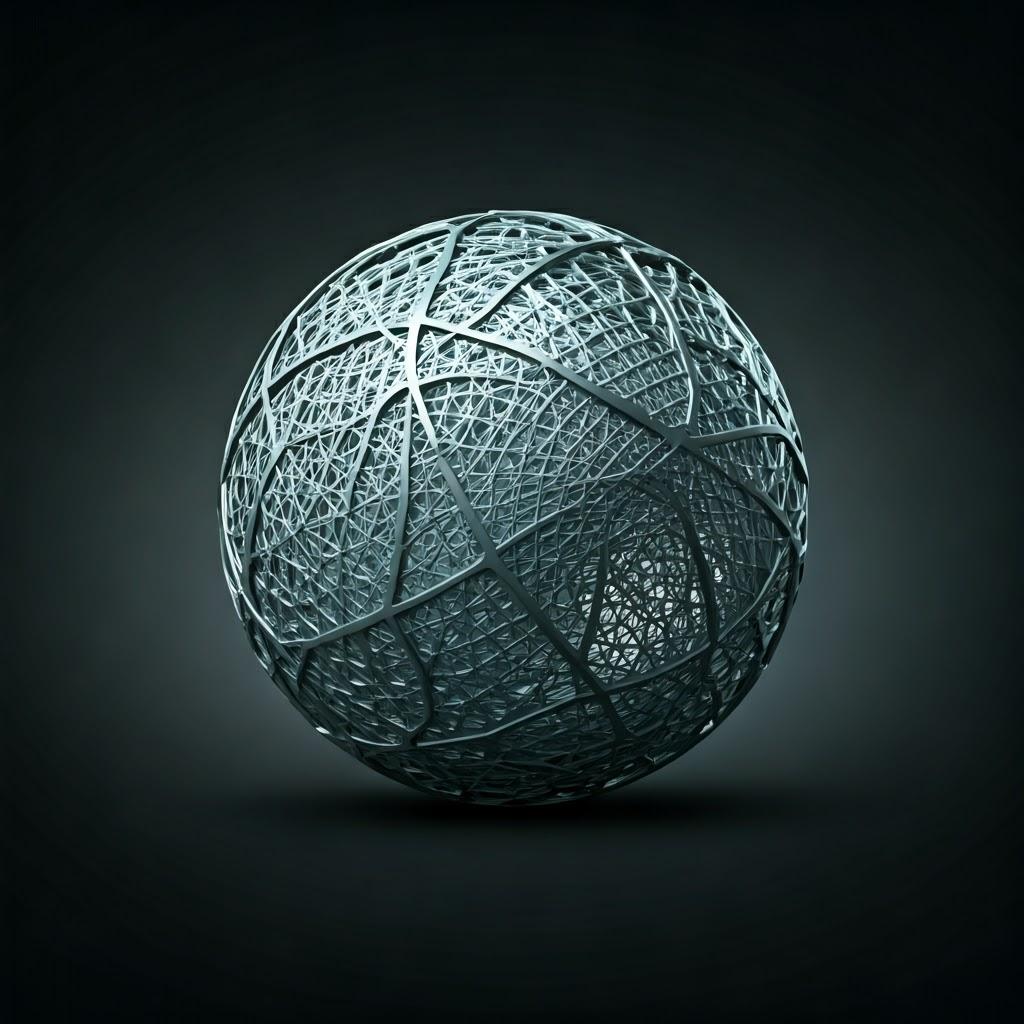
Frequently Asked Questions (FAQ) about 3D Printed Aerospace Cooling Jackets
Here are answers to some common questions engineers and procurement specialists have when considering metal additive manufacturing for aerospace cooling jackets:
Q1: What level of detail and complexity can be achieved inside the cooling channels?
- A: Metal AM excels at creating highly complex internal geometries that are impossible with traditional methods. This includes:
- Conformal Channels: Channels that precisely follow curved surfaces.
- Fine Features: Internal ribs, turbulators, or complex cross-sections can often be printed directly. Minimum channel diameters typically range from 0.5 mm to 1.0 mm, depending on the process, material, and powder removal considerations.
- Sınırlamalar: Very sharp corners might be slightly rounded, and the as-built surface finish inside channels will be rougher than machined surfaces (typically 10-25 µm Ra). Powder removal becomes challenging for extremely narrow (<0.5mm) or highly tortuous paths. DfAM is key to designing achievable complexity.
Q2: How do 3D printed cooling jackets compare in performance to traditionally made ones?
- A: When designed using DfAM principles, 3D printed cooling jackets often significantly daha iyi performans traditionally made counterparts.
- Thermal Efficiency: Conformal channels and optimized internal features lead to more effective and uniform heat transfer, potentially allowing for higher system power levels or reduced coolant flow requirements.
- Ağırlık: Part consolidation and topology optimization enable substantial weight savings compared to multi-part brazed or welded assemblies.
- Reliability: Eliminating joints (brazes/welds) removes potential leak paths and failure points, increasing component integrity.
- Malzeme Özellikleri: With proper process control and post-processing (especially HIP), the mechanical properties of AM materials like IN625 or AlSi10Mg can meet or exceed those of cast or even wrought equivalents.
Q3: Are 3D printed metal cooling jackets flight-certified?
- A: Achieving flight certification for AM parts is a rigorous process but is becoming increasingly common. It’s not the part itself that is certified in isolation, but rather the entire process used to produce it consistently and reliably. This involves:
- Süreç Kalifikasyonu: Demonstrating stable, repeatable manufacturing processes (printing parameters, post-processing).
- Malzeme Yeterliliği: Extensive testing to establish material properties and ensure they meet design allowables.
- Part-Specific Qualification: Non-destructive testing (NDT) and potentially destructive testing on representative parts to verify integrity and performance against specifications.
- Certified Supplier: Working with an AS9100 certified supplier with experience in aerospace qualification is crucial.
- Status: Many non-critical and semi-critical AM components are already flying. Qualification for critical components like high-pressure turbine parts or primary structures is ongoing and advancing rapidly across the industry. Discuss specific qualification requirements early with your AM provider.
Q4: What information is needed to get an accurate quote for a custom cooling jacket?
- A: To provide an accurate quote, an AM service provider typically needs:
- 3D CAD Modeli: A dimensionally accurate model in a standard format (e.g., STEP, IGES).
- Material Specification: Clearly define the required alloy (e.g., IN625, AlSi10Mg) and any specific material standards (e.g., AMS specifications).
- Technical Drawings: 2D drawings indicating critical dimensions, tolerances, surface finish requirements (especially for machined features or internal channels), and any specific inspection callouts.
- Quantity Required: Number of units needed (for prototyping or production).
- İşlem Sonrası Gereksinimler: Specify required heat treatments (stress relief, HIP, T6 aging), machining operations, surface finishes, and NDT requirements (e.g., CT scan, FPI).
- Application Context: Briefly describing the operating environment (temperature, pressure, fluid type) can help the provider offer DfAM suggestions or confirm material suitability.
- Quality Requirements: Any specific quality clauses or certification needs (e.g., AS9100 compliance).
Providing comprehensive information upfront allows the supplier to accurately assess the complexity, estimate costs, and determine the necessary process steps for your aerospace component pricing.
Conclusion: The Future of Aerospace Thermal Management is Additive
The relentless pursuit of higher performance, increased efficiency, and reduced weight in the aerospace industry demands continuous innovation in every aspect of design and manufacturing. Thermal management, once addressed through conventional means, now stands to be revolutionized by the capabilities of metal additive manufacturing. As we’ve explored, using AM to produce custom cooling jackets offers transformative advantages:
- Unmatched Design Complexity: Enabling conformal cooling channels and optimized geometries for superior thermal performance.
- Significant Weight Reduction: Through part consolidation and topology optimization, crucial for aerospace applications.
- Accelerated Development: Facilitating rapid prototyping and design iteration.
- Yüksek Performanslı Malzemeler: Leveraging advanced alloys like IN625 for extreme temperatures and AlSi10Mg for lightweight thermal conductivity.
While challenges related to process control, post-processing, and qualification exist, they are being actively addressed through advancements in technology, materials science, and the growing expertise of specialized AM providers. The path forward involves embracing DfAM principles, selecting the right high-performance materials, and partnering with knowledgeable suppliers who possess the necessary certifications, equipment, and process controls.
Şirketler gibi Met3dp are pivotal in this transformation, offering not just Met3dp additive solutions through advanced printing technologies like SEBM and high-quality powder production, but also the crucial expertise needed to navigate the complexities of aerospace AM. Their focus on industry-leading accuracy, reliability, and comprehensive solutions makes them an ideal partner for organizations looking to implement metal 3D printing for demanding applications like custom cooling jackets.
Geleceğin havacılık ve uzay üretimi will undoubtedly see increased adoption of additive manufacturing for critical components. For thermal management systems, AM is not just an alternative; it’s an enabling technology, unlocking levels of performance and integration previously unattainable. Engineers and procurement managers who understand and leverage the power of AM for components like cooling jackets will be at the forefront of designing and building the next generation of aerospace systems.
Ready to explore how metal additive manufacturing can revolutionize your aerospace thermal management challenges? Contact Met3dp today to discuss your specific cooling jacket requirements and discover how our expertise and advanced capabilities can power your innovation.
Paylaş
MET3DP Technology Co, LTD, merkezi Qingdao, Çin'de bulunan lider bir katmanlı üretim çözümleri sağlayıcısıdır. Şirketimiz, endüstriyel uygulamalar için 3D baskı ekipmanları ve yüksek performanslı metal tozları konusunda uzmanlaşmıştır.
İşletmeniz için en iyi fiyatı ve özelleştirilmiş Çözümü almak için sorgulayın!
İlgili Makaleler
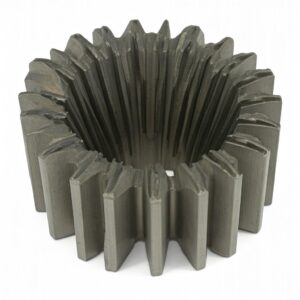
Yüksek Performanslı Nozul Kanat Segmentleri: Metal 3D Baskı ile Türbin Verimliliğinde Devrim
Daha Fazla Oku "Met3DP Hakkında
Son Güncelleme
Bizim Ürünümüz
BİZE ULAŞIN
Herhangi bir sorunuz var mı? Bize şimdi mesaj gönderin! Mesajınızı aldıktan sonra tüm ekibimizle talebinize hizmet edeceğiz.
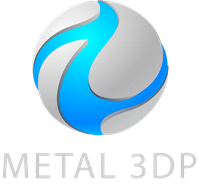
3D Baskı ve Katmanlı Üretim için Metal Tozları