Lightweight Camera Mounts for UAVs via 3D Printing
İçindekiler
Introduction: Revolutionizing UAV Imaging with 3D Printed Metal Camera Mounts
The Unmanned Aerial Vehicle (UAV), or drone, has transcended its origins in military applications to become an indispensable tool across a multitude of industries. From breathtaking cinematic videography and precision agriculture mapping to critical infrastructure inspection and rapid emergency response, the capabilities of UAVs are continually expanding. Central to many of these applications is the ability to carry sophisticated sensor payloads, most commonly high-resolution cameras, thermal imagers, LiDAR scanners, or multispectral sensors. The component tasked with securely holding, positioning, and often stabilizing these valuable payloads is the camera mount or gimbal system. Traditionally, these mounts have been manufactured using methods like CNC machining or injection molding, often involving trade-offs between weight, strength, complexity, and cost. However, a new manufacturing paradigm is fundamentally changing how these critical components are designed and produced: metal katkılı üretim (AM), more commonly known as metal 3D baskı.
Metal 3D baskı offers engineers and designers unprecedented freedom to create highly complex, topology-optimized, and exceptionally lightweight structures that were previously impossible or prohibitively expensive to manufacture. For UAV camera mounts, this translates directly into tangible performance benefits. Weight is arguably the most critical factor in UAV design; every gram saved on the airframe or payload components extends flight time, increases payload capacity, or enhances maneuverability. Metal AM allows for the creation of mounts that possess the high strength and rigidity required to protect expensive camera equipment and ensure stable imaging, even during aggressive flight maneuvers or in demanding environmental conditions, but at a significantly reduced mass compared to traditionally manufactured counterparts.
Imagine a camera mount for an industrial inspection drone tasked with examining wind turbines. It needs to be robust enough to withstand high winds and vibrations while precisely aiming a high-resolution camera, yet light enough to maximize the drone’s operational time on site. Or consider a high-end cinematic drone where vibration damping and smooth, precise camera movements are paramount for capturing flawless footage. Metal 3D printing enables the creation of mounts with intricate internal structures for vibration isolation and complex geometries for enhanced gimbal performance, all within a minimal weight envelope.
Furthermore, the additive nature of the process facilitates rapid design iteration and customization. Need a mount specifically designed for a new camera sensor with unique dimensions and mounting points? Metal AM allows for the swift production of bespoke designs without the need for expensive tooling changes associated with traditional methods. This agility is invaluable in the fast-paced world of drone technology, enabling manufacturers and operators to adapt quickly to new requirements and integrate the latest imaging technologies. Companies seeking a reliable UAV component supplier capable of delivering these advanced, hafif bileşenler are increasingly turning to specialists in metal additive manufacturing. The ability to produce custom drone payloads and mounts on-demand streamlines the supply chain and accelerates innovation in aerospace imaging ve industrial inspection drone applications. This technology isn’t just an alternative; it’s a revolutionary force enabling the next generation of high-performance UAV imaging systems.
Applications: Where are 3D Printed Metal Drone Camera Mounts Making an Impact?
The advantages of lightweight strength, design complexity, and customization offered by metal 3D printed camera mounts make them highly suitable for a diverse range of demanding UAV applications. Their adoption is growing rapidly across various sectors where performance, reliability, and payload efficiency are critical. Procurement managers and engineering teams sourcing components for drone surveillance systems, agricultural drone sensors, cinematic drone rigsve UAV inspection equipment are finding significant value in this technology.
1. Industrial Inspection & Asset Management:
- Uygulamalar: Inspecting wind turbines, power lines, bridges, oil and gas pipelines, solar farms, building facades, and other critical infrastructure.
- Requirements: High stability for clear imaging/scanning (visual, thermal, LiDAR), robustness to withstand environmental factors (wind, vibration), often requiring custom mounts for specific sensor packages. Lightweight designs are crucial for maximizing inspection range and flight time per battery charge.
- AM Advantage: Metal AM allows for topology-optimized mounts that provide maximum stiffness-to-weight ratio, ensuring sensor stability. Complex geometries can integrate vibration damping features directly into the mount structure. Customization enables rapid integration of new or specialized sensors required for specific inspection tasks. Reliability is paramount, and the robust nature of 3D printed metal parts ensures longevity even in harsh operating conditions. Sourcing these parts from a specialized drone component supplier with AM expertise guarantees quality.
2. Aerospace & Defense:
- Uygulamalar: Intelligence, Surveillance, and Reconnaissance (ISR), target acquisition, communications relays, border patrol.
- Requirements: Extreme durability, high strength-to-weight ratios, operation in demanding environments (temperature extremes, high G-forces), specific material properties (e.g., low thermal expansion, specific RF transparency), often stringent certification requirements (e.g., AS9100). Payloads can be highly sensitive and expensive.
- AM Advantage: Metal AM enables the use of aerospace-grade alloys (like high-strength aluminum or titanium alloys) to produce extremely lightweight yet robust mounts capable of meeting demanding military and aerospace specifications. Complex, conformal designs can be integrated seamlessly with the UAV airframe. The ability to create classified or highly customized designs quickly without extensive tooling is a significant advantage. The reliability offered by printed metal is crucial for mission success.
3. Cinematography & Broadcasting:
- Uygulamalar: Aerial filming for movies, television commercials, documentaries, live sports broadcasting.
- Requirements: Exceptional stability and vibration damping for smooth, jitter-free footage. Precise, repeatable movement control (often integrated into gimbals). Lightweight design to maximize flight time and allow for use on smaller, more agile drones. Ability to accommodate various professional camera and lens combinations.
- AM Advantage: Metal AM allows for the creation of intricate gimbal components and mounts with optimized mass distribution and integrated vibration isolation features (e.g., using lattice structures). High stiffness prevents unwanted flexure during rapid drone movements. Custom mounts can be quickly designed and produced for specific camera/lens setups, offering filmmakers greater flexibility. Achieving a professional aesthetic is also possible through post-processing.
4. Agriculture & Environmental Monitoring:
- Uygulamalar: Precision agriculture (crop scouting, yield monitoring using multispectral/hyperspectral cameras), environmental surveying (wildlife tracking, coastal erosion monitoring, forestry management), atmospheric research.
- Requirements: Ability to carry specialized sensors (multispectral, thermal, hyperspectral), durability for field use, cost-effectiveness for potentially large fleets, lightweight for maximizing coverage area per flight.
- AM Advantage: Metal AM provides durable and lightweight mounts tailored for specific agricultural drone sensors. The strength protects sensors during rough landings or operation in agricultural environments. For research applications requiring unique sensor combinations, AM allows for rapid development of custom drone payloads and mounting solutions without high NRE (Non-Recurring Engineering) costs.
5. Surveying & Mapping:
- Uygulamalar: Creating high-resolution maps, 3D models of terrain or structures, construction site monitoring, mining surveys.
- Requirements: Precise and stable positioning of cameras or LiDAR scanners is critical for data accuracy. Mounts must maintain sensor orientation consistently throughout the flight. Lightweight design is essential for maximizing flight duration over large survey areas.
- AM Advantage: The high stiffness of 3D printed metal mounts ensures minimal deflection, contributing to higher accuracy survey data. Complex geometries can be designed to place the sensor’s nodal point precisely or integrate cooling features for sensitive electronics. Topology optimization minimizes weight, allowing drones to cover larger areas efficiently.
6. Emergency Response & Public Safety:
- Uygulamalar: Search and rescue operations, disaster site assessment, situational awareness for law enforcement and firefighters, hazardous material incident monitoring.
- Requirements: Rapid deployment, reliability in adverse conditions, ability to carry thermal or zoom cameras, robustness.
- AM Advantage: Metal AM delivers highly durable mounts that can withstand the rigors of emergency deployment. Custom mounts for specific sensors used in public safety (e.g., gas detectors, high-intensity spotlights alongside cameras) can be produced quickly. The reliability ensures that critical imaging capabilities are available when needed most.
Across these diverse applications, the common threads are the need for lighter weight, higher strength, increased design freedom, and often, customization. Metal 3D printed camera mounts deliver on these requirements, pushing the boundaries of what’s possible with UAV technology. Companies acting as wholesale drone component providers veya distributors are increasingly stocking these advanced parts to meet growing market demand.
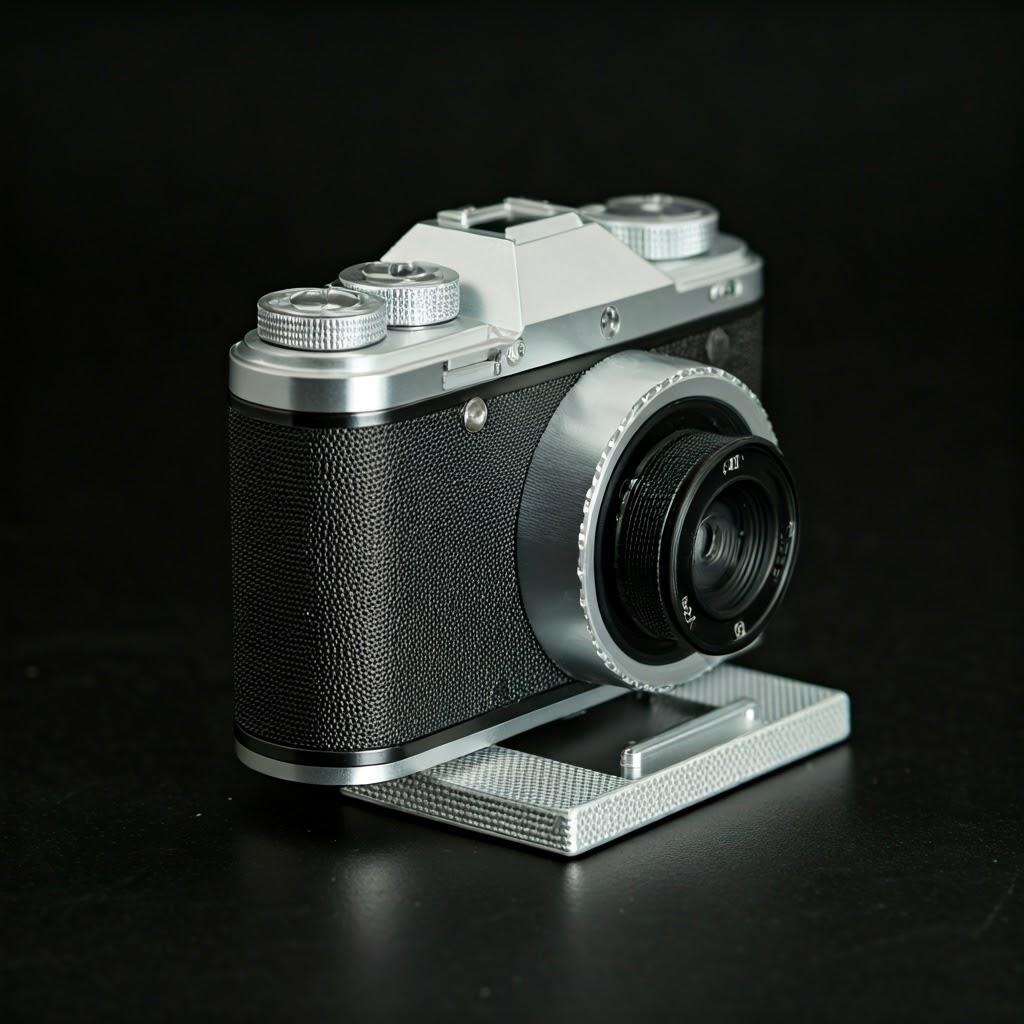
The Additive Advantage: Why Choose Metal 3D Printing for Drone Camera Mounts?
While traditional manufacturing methods like CNC machining and injection molding have served the drone industry well, metal additive manufacturing (AM) presents a compelling suite of advantages specifically suited to the challenges of designing and producing high-performance UAV camera mounts. Understanding these benefits is key for engineers and procurement managers looking to optimize drone performance, reduce lead times, and unlock new design possibilities. The decision to utilize metal AM vs CNC machining or other methods often hinges on leveraging these unique capabilities for lightweight design drone components and complex geometry manufacturing.
1. Unparalleled Design Freedom & Complexity:
- Benefit: AM builds parts layer by layer directly from a 3D CAD model, removing many of the constraints imposed by subtractive (machining) or formative (molding) processes. This allows for the creation of highly intricate and complex geometries that are impossible or impractical to produce otherwise.
- Application to Mounts:
- Topology Optimization: Algorithms can be used to remove material from non-critical areas, resulting in organic-looking, highly efficient structures that maintain strength and stiffness only where needed, drastically reducing weight.
- Internal Channels: Cooling channels for electronics, wiring conduits, or passages for vibration-damping fluids can be designed directly into the mount structure.
- Kafes Yapılar: Internal lattice or honeycomb structures can further reduce weight while maintaining structural integrity and providing unique properties like impact absorption or vibration damping.
- Parça Konsolidasyonu: Multiple components of a traditional mount assembly (brackets, arms, fasteners) can potentially be consolidated into a single, complex 3D printed part, reducing assembly time, potential points of failure, and overall weight.
2. Significant Weight Reduction (Lightweighting):
- Benefit: As mentioned, weight is paramount in UAV design. Metal AM excels at creating parts with exceptionally high strength-to-weight ratios.
- Application to Mounts: By leveraging topology optimization and complex geometries, metal AM can produce camera mounts that are significantly lighter (often 20-60% or more) than their machined or molded counterparts, while meeting or exceeding stiffness and strength requirements. This weight saving directly translates to longer flight times, increased payload capacity for additional sensors or batteries, or improved flight dynamics and agility. This focus on lightweight design drone components is a primary driver for AM adoption.
3. Rapid Prototyping & Iteration:
- Benefit: Metal AM allows for the direct production of functional metal prototypes without the need for tooling. Design changes can be implemented in CAD and a new version printed relatively quickly.
- Application to Mounts: This accelerates the development cycle significantly. Engineers can design, print, test, and refine camera mount designs in days or weeks, rather than months. This is crucial in the fast-evolving drone market, enabling rapid integration of new camera technologies or adaptation to specific mission requirements. This capability is invaluable for rapid prototyping UAV parts.
4. Customization & On-Demand Manufacturing:
- Benefit: Each part printed can be unique without significant cost penalties associated with tooling modifications. Production can be scaled according to demand.
- Application to Mounts: Metal AM is ideal for producing custom mounts tailored to specific UAV airframes, camera/sensor models, or unique operational requirements. This is particularly beneficial for specialized applications, research projects, or small-to-medium production runs. It also enables on-demand drone parts manufacturing, reducing the need for large inventory holdings and facilitating a more agile supply chain, a key interest for procurement drone parts managers.
5. Material Variety & Performance:
- Benefit: A growing range of high-performance metal powders are available for AM, including various aluminum alloys, titanium alloys, stainless steels, and superalloys.
- Application to Mounts: This allows designers to select the optimal material based on specific requirements such as strength, weight, temperature resistance, corrosion resistance, or cost. For drone mounts, lightweight, high-strength aluminum alloys like AlSi10Mg and A7075 (discussed next) are often ideal choices, offering performance comparable to or exceeding traditional materials. Access to a reliable metal tozu tedarikçisi with a diverse portfolio, like Met3DP, is crucial.
6. Reduced Material Waste:
- Benefit: Additive manufacturing typically uses only the material needed to build the part and its supports, resulting in significantly less material waste compared to subtractive processes like CNC machining, which start with a solid block and remove material.
- Application to Mounts: While powder recycling is essential, the buy-to-fly ratio (the weight of the raw material purchased compared to the weight of the final part) is generally much better in AM, especially for complex, lightweight parts. This can lead to cost savings, particularly with expensive materials like titanium.
Comparison Table: Metal AM vs. Traditional Methods for Drone Camera Mounts
Özellik | Metal 3D Printing (e.g., SLM/DMLS) | CNC İşleme | Injection Molding (Metal/Plastic) |
---|---|---|---|
Tasarım Karmaşıklığı | Very High (organic shapes, internal channels, lattices) | Moderate (limited by tool access) | High (but requires complex molds) |
Hafifletme | Excellent (via topology optimization) | Good (but limited by subtractive nature) | Moderate (design/material dependent) |
Lead Time (Proto) | Fast (days/weeks) | Moderate (weeks) | Very Slow (months for tooling) |
Lead Time (Prod.) | Moderate (scalable) | Fast (for established designs) | Very Fast (high volume) |
Customization Cost | Düşük | High (reprogramming/fixtures) | Very High (new molds) |
Kalıp Maliyeti | Hiçbiri | Low (fixtures) | Very High (molds) |
Malzeme Seçenekleri | Growing Range (Al, Ti, Steel, etc.) | Wide Range | More Limited (specific MIM powders or plastics) |
Parça Konsolidasyonu | High Potential | Low Potential | Moderate Potential |
Malzeme Atıkları | Low (additive nature) | High (subtractive nature) | Low (but runner/sprue waste) |
Ideal Volume | Prototypes, Low-to-Medium Volume, Custom | Medium-to-High Volume | Very High Volume |
Sayfalara Aktar
While metal AM offers significant advantages, it’s important to consider factors like surface finish (often requiring post-processing), achievable tolerances, and the need for specific design considerations (DfAM), which will be discussed in later sections. However, for creating the next generation of high-performance, lightweight, and customized UAV camera mounts, the additive manufacturing benefits are undeniable, making it a cornerstone technology for innovation in the drone industry.
Material Focus: Selecting AlSi10Mg and A7075 for Optimal Performance
Choosing the right material is fundamental to the success of any engineering project, and this holds particularly true for metal 3D printed drone camera mounts where the demands for low weight, high strength, stiffness, and durability are paramount. While metal additive manufacturing supports a wide array of materials, two aluminum alloys stand out as excellent candidates for this application: AlSi10Mg ve A7075. Understanding their respective properties and why they are well-suited for Laser Powder Bed Fusion (L-PBF) processes like Selective Laser Melting (SLM) or Direct Metal Laser Sintering (DMLS) is crucial for designers and metal tozu tedarikçileri.
AlSi10Mg: The Workhorse Aluminum Alloy for AM
AlSi10Mg is one of the most widely used and well-characterized aluminum alloys in metal additive manufacturing. It’s essentially a casting alloy adapted for AM processes, known for its excellent printability, good strength-to-weight ratio, and favorable thermal properties.
- Kompozisyon: Primarily aluminum, with silicon (around 10%) and magnesium (around 0.3-0.5%) as the main alloying elements. Silicon improves fluidity during melting and reduces solidification shrinkage, while magnesium enables precipitation hardening through heat treatment.
- Key Properties & Benefits for Drone Mounts:
- Mükemmel Basılabilirlik: Melts and solidifies reliably under laser exposure, allowing for the production of complex geometries and fine features with relatively low risk of cracking or porosity compared to other high-strength aluminum alloys. This makes it a reliable choice for service providers.
- İyi Güç-Ağırlık Oranı: While not the absolute strongest aluminum alloy, it offers a very competitive balance of strength and low density (approx. 2.67 g/cm³), making it ideal for lightweighting drone components.
- Good Thermal Properties: Exhibits good thermal conductivity, which can be beneficial for dissipating heat generated by camera electronics integrated near or within the mount.
- Korozyon Direnci: Offers decent corrosion resistance suitable for many operating environments.
- Isıl İşlem Uygulanabilir: Can be heat treated (typically a T6 cycle involving solutionizing and artificial aging) to significantly improve its strength and hardness, bringing its mechanical properties closer to those of traditional wrought alloys.
- Maliyet-Etkinlik: Generally more cost-effective and readily available as a powder compared to some higher-strength or more exotic alloys.
- Düşünceler:
- Its fatigue strength and fracture toughness may be lower than some high-strength wrought alloys like A7075, especially in the as-printed state.
- Achieving optimal properties relies heavily on proper printing parameters and post-process heat treatment.
A7075 (Aluminum 7075): High Strength for Demanding Applications
A7075 is a well-known aerospace aluminum alloy, renowned for its exceptional strength-to-weight ratio, rivaling that of some steels. Traditionally used in high-stress airframe components, its adaptation for additive manufacturing has been more challenging but offers significant performance gains where maximum strength is required. Zinc is the primary alloying element, along with magnesium and copper.
- Challenges in AM: A7075 is notoriously difficult to print using L-PBF due to its wide freezing range and susceptibility to solidification cracking (hot tearing) and porosity. The volatile nature of zinc under intense laser heat also poses challenges. Significant research and development, including specialized alloy modifications (sometimes denoted with suffixes like ‘RAM’ or ‘AM’), optimized printing parameters, and advanced thermal management strategies during printing, are required to successfully print dense, crack-free A7075 parts.
- Key Properties & Benefits for Drone Mounts:
- Olağanüstü Güç-Ağırlık Oranı: Offers significantly higher tensile and yield strength compared to AlSi10Mg, especially after appropriate heat treatment (e.g., T6 or T7x tempers). This allows for even greater lightweighting potential or the ability to withstand higher loads and impacts.
- High Hardness & Wear Resistance: Superior hardness makes it more resistant to scratches and wear.
- Mükemmel Yorulma Dayanımı: Generally exhibits better fatigue performance than AlSi10Mg, crucial for components subjected to vibrations and cyclic loading during drone flight.
- Düşünceler:
- Difficult Printability: Requires specialized expertise, advanced AM systems, and carefully controlled parameters. Not all service providers have validated processes for reliably printing A7075. This often translates to higher costs.
- Düşük Korozyon Direnci: Generally less corrosion resistant than AlSi10Mg or other aluminum series (like 5xxx or 6xxx). Surface treatments (e.g., anodizing, coating) are often necessary for protection, especially in marine or harsh environments.
- Heat Treatment Complexity: Achieving the desired high-strength tempers requires precise multi-stage heat treatment processes.
Material Selection Guide for Drone Camera Mounts:
Özellik | AlSi10Mg | A7075 (AM Version) | Recommendation Rationale for Drone Mounts |
---|---|---|---|
Yazdırılabilirlik | Mükemmel | Zorlu | AlSi10Mg is often preferred for faster development, lower risk, and broader supplier availability. A7075 requires specialized expertise. |
Strength (Yield) | Good (Excellent after T6) | Very High (Exceptional after T6/T7x) | Choose A7075 if absolute maximum strength or fatigue life is critical and justifies the complexity/cost. AlSi10Mg is sufficient for many demanding applications. |
Sertlik | İyi | Good (Similar to AlSi10Mg) | Both offer good stiffness suitable for stable camera platforms. Design (geometry) often plays a larger role in overall mount stiffness than the minor difference here. |
Yoğunluk | Low (~2.67 g/cm³) | Low (~2.81 g/cm³) | Both are lightweight; AlSi10Mg is slightly less dense. |
Ağırlık Azaltma | Mükemmel | Potentially Exceptional | A7075’s higher strength may allow for slightly more aggressive lightweighting via topology optimization, but AlSi10Mg already enables significant mass reduction. |
Yorulma Dayanımı | Orta düzeyde | Yüksek | A7075 is superior for high-vibration or high-cycle applications. Consider for mounts on high-endurance or aggressively flown UAVs. |
Corrosion Resist. | İyi | Moderate (Requires Protection) | AlSi10Mg is generally better for diverse environments unless A7075 parts are properly coated/anodized. |
Thermal Conduct. | İyi | Orta düzeyde | AlSi10Mg might be slightly better for passive heat dissipation from electronics. |
Maliyet ve Bulunabilirlik | Lower Cost, Widely Available | Higher Cost, Specialist Supply | AlSi10Mg provides a better cost-performance balance for many projects. A7075 is a premium option for performance-critical needs. |
Isıl İşlem | Standard T6 | Complex Multi-Stage | T6 for AlSi10Mg is a well-understood process offered by most AM service providers. A7075 heat treatment requires specific knowledge. |
Sayfalara Aktar
The Role of High-Quality Powders:
Regardless of the alloy chosen, the quality of the metal powder is critical for successful additive manufacturing. Powder characteristics such as sphericity, particle size distribution (PSD), flowability, and purity directly impact the density, mechanical properties, and surface finish of the final printed part.
Leading providers like Met3DP utilize advanced powder production techniques, such as industry-leading gas atomization and Plasma Rotating Electrode Process (PREP) technologies, to manufacture high-quality spherical metal powders optimized for AM processes. Onların Gelişmiş Toz Üretim Sistemi, employing unique nozzle and gas flow designs, ensures high sphericity and good flowability, crucial for achieving uniform powder bed layers and consistent melting behavior. While specializing in innovative alloys like TiNi, TiTa, TiAl, TiNbZr, CoCrMo, and various stainless steels and superalloys found on their ürün sayfası, reputable powder manufacturers often also produce standard high-quality aluminum alloys like AlSi10Mg suitable for demanding applications like drone mounts. Ensuring your metal tozu tedarikçisi adheres to stringent quality control measures is essential for achieving reliable and high-performance aerospace grade materials suitable for UAV components.
In conclusion, both AlSi10Mg and A7075 offer compelling advantages for 3D printing lightweight, high-performance drone camera mounts. AlSi10Mg represents a reliable, cost-effective, and widely accessible option with excellent printability and good all-around properties suitable for a vast range of applications. A7075 provides superior strength and fatigue performance for the most demanding scenarios, albeit with increased printing complexity and cost. The final selection depends on a careful analysis of the specific performance requirements, operating environment, budget, and the capabilities of the chosen manufacturing partner. Sources and related content
Design for Additive Manufacturing (DfAM): Optimizing Camera Mounts for Printing
Simply taking a design intended for CNC machining or casting and sending it to a metal 3D printer rarely yields optimal results. To truly unlock the potential of additive manufacturing for creating lightweight, high-performance drone camera mounts, engineers must embrace Katmanlı Üretim Tasarımı (DfAM) principles. DfAM is not just a suggestion; it’s a fundamental shift in design thinking that considers the unique opportunities and constraints of the layer-by-layer building process right from the conceptual stage. Applying DfAM principles allows for maximizing the benefits of metal AM, such as weight reduction, part consolidation, and performance enhancement, while mitigating potential printing challenges. For UAV components where performance metrics like weight and stiffness are critical, mastering DfAM is essential for competitive advantage. Effective CAD for 3D printing involves more than just modeling the final shape; it requires strategic planning for the build process itself.
Here are key DfAM considerations when designing metal drone camera mounts for processes like Laser Powder Bed Fusion (L-PBF), which includes Selective Laser Melting (SLM) and Direct Metal Laser Sintering (DMLS):
1. Topology Optimization:
- Concept: Using specialized software algorithms to iteratively remove material from a design space based on applied loads, constraints, and performance objectives (e.g., minimize weight, maximize stiffness). The result is often an organic, load-path-optimized structure.
- Application to Mounts: This is perhaps the most potent DfAM tool for topology optimization UAV components. Engineers can define the camera mounting points, the UAV interface points, anticipated vibration loads, and maximum stress constraints. The software then sculpts the mount geometry, placing material only where structurally necessary. This can lead to dramatic weight reductions (often exceeding 30-50%) compared to traditional designs, directly improving drone flight time and payload capacity, while ensuring the mount remains stiff and strong enough to guarantee stable imaging. The resulting complex, often skeletal or bio-inspired geometries are perfectly suited for AM production.
2. Lattice Structures & Infill:
- Concept: Incorporating internal periodic structures (like honeycombs, gyroids, or strut-based lattices) or varying infill densities within the solid volume of a part.
- Application to Mounts:Lattice structures drone mounts offer several advantages:
- Further Lightweighting: Replacing solid sections with low-density lattices significantly reduces mass while retaining substantial compressive strength and stiffness.
- Vibration Damping: Certain lattice types exhibit excellent energy absorption properties, helping to dampen vibrations transmitted from the drone airframe to the camera sensor, improving image quality.
- Kişiye Özel Özellikler: Different lattice types and cell sizes can be used in various regions of the mount to fine-tune local stiffness or damping characteristics.
- Termal Yönetim: Open-cell lattices can facilitate airflow or allow for the integration of heat sinks if camera electronics generate significant heat.
3. Support Structure Strategy & Minimization:
- Concept: L-PBF processes require support structures for overhangs (typically features angled less than 45 degrees from the horizontal build plane) and to anchor the part to the build plate, preventing warping and managing thermal stresses. However, supports consume extra material, add print time, and require post-processing removal, which can affect surface finish and potentially damage the part.
- Application to Mounts: Effective DfAM involves designing for metal AM ile support structure minimization in mind:
- Kendini Destekleyen Açılar: Design overhangs to be greater than 45 degrees whenever possible.
- Feature Orientation: Orient the part on the build plate strategically to minimize the extent and complexity of required supports. This might involve trade-offs with build time or surface finish on certain features.
- Incorporate Sacrificial Features: Sometimes, adding small fillets or chamfers can make an edge self-supporting.
- Design for Accessibility: Ensure support structures are placed where they can be easily accessed and removed without damaging critical features of the mount. Avoid supports on functional surfaces or complex internal channels if possible.
- Use Specialized Supports: Utilize tree supports or block supports generated by advanced slicing software, which can be easier to remove and use less material.
4. Part Orientation:
- Concept: The orientation in which the mount is printed on the build platform significantly impacts surface finish, accuracy, required supports, build time, and even anisotropic material properties (directional differences in strength).
- Application to Mounts:
- Yüzey İşlemi: Upward-facing surfaces generally have a better finish than downward-facing surfaces which interact with supports. Critical surfaces should ideally be oriented upwards or vertically.
- Doğruluk: Vertical walls tend to be more dimensionally accurate than features built purely in the horizontal plane. Holes printed vertically are typically rounder than those printed horizontally (which can be slightly teardrop-shaped).
- Supports: As mentioned, orientation dictates support needs.
- Anizotropi: While less pronounced in aluminum alloys compared to some other metals or polymers, mechanical properties can vary slightly depending on the build direction (X, Y vs. Z). For highly stressed components, this might be a consideration, requiring orientation alignment with the primary load paths. Simulation can help determine the optimal orientation.
5. Minimum Feature Size & Wall Thickness:
- Concept: AM processes have limitations on the smallest features (pins, holes, walls) they can reliably produce. This is dictated by the laser spot size, powder particle size, and process parameters.
- Application to Mounts: Ensure that walls are thick enough to print reliably and withstand handling/operational loads (typically >0.5mm – 1mm, depending on geometry and material). Small holes or fine details might require careful design and parameter tuning or could be better created through post-process machining. Avoid sharp internal corners, which can act as stress concentrators; use fillets instead.
6. Thermal Management Considerations:
- Concept: The rapid heating and cooling cycles during L-PBF generate significant thermal stresses within the part, potentially leading to warping or distortion, especially in large flat areas or thin features.
- Application to Mounts:
- Avoid Large Flat Bases: Break up large flat surfaces parallel to the build plate with slight angling or ribbing.
- Gradual Thickness Transitions: Avoid abrupt changes in cross-sectional area, which can exacerbate differential cooling and stress buildup. Use smooth transitions and fillets.
- Strategic Orientation: Orienting long, thin sections vertically rather than horizontally can help mitigate warping.
7. Part Consolidation:
- Concept: Leveraging the geometric freedom of AM to combine multiple components of a traditional assembly into a single, integrated printed part.
- Application to Mounts: A camera mount assembly might traditionally consist of multiple brackets, fasteners, damping elements, and interface plates. DfAM encourages designers to explore consolidating these into fewer, or even a single, complex monolithic part. This reduces assembly labor, eliminates potential failure points at joints, decreases parts count for procurement drone parts management, and often leads to further weight savings.
By thoughtfully applying these DfAM principles, designers can create metal drone camera mounts that are not only manufacturable via AM but are also lighter, stronger, more functional, and potentially more cost-effective in the long run compared to conventionally produced alternatives. Partnering with an experienced metal AM service provider who understands these nuances is crucial for success.
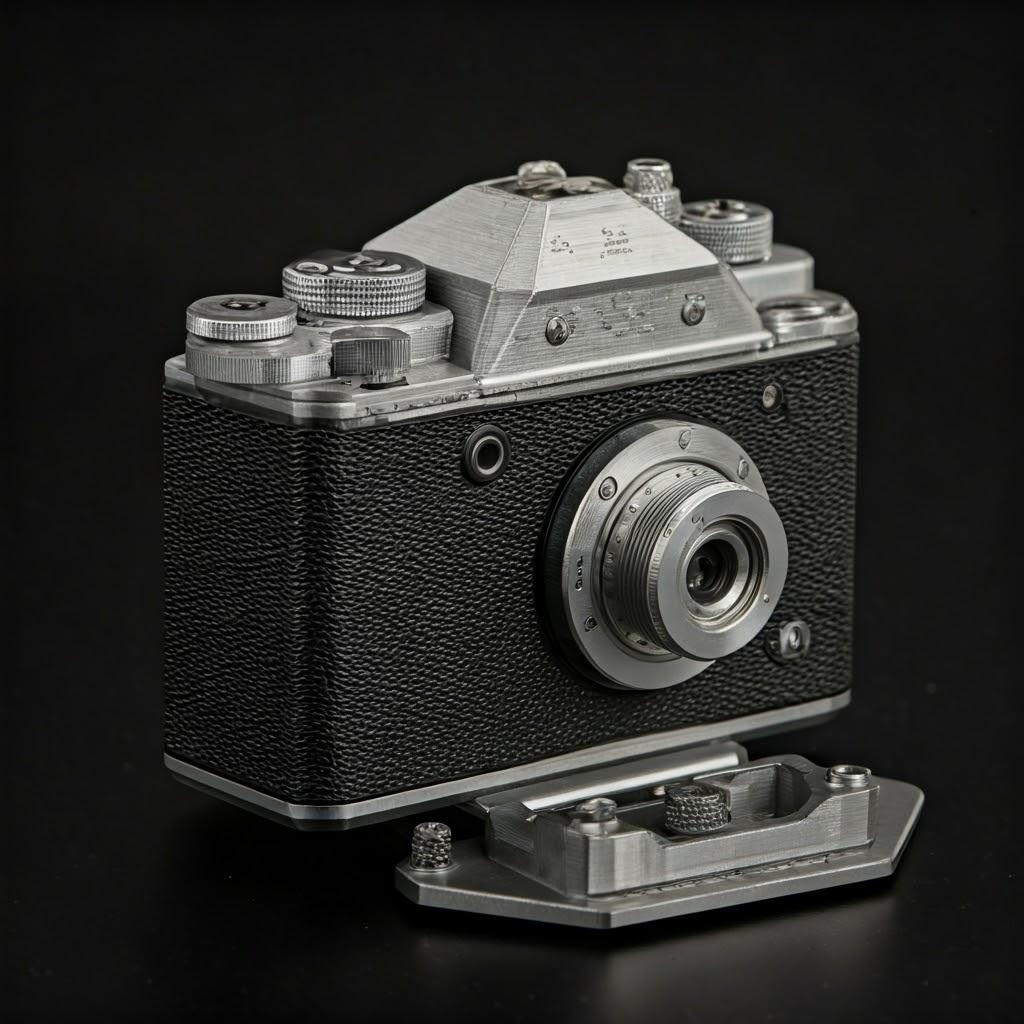
Precision Matters: Achieving Tight Tolerances and Superior Surface Finish
While metal additive manufacturing unlocks incredible design freedom, potential users, especially engineers and procurement managers involved in sourcing precision drone components, need a clear understanding of the achievable levels of accuracy and surface quality. For a drone camera mount, dimensional precision is crucial for ensuring correct alignment with both the UAV airframe and the camera/sensor package. Surface finish can impact aesthetics, fatigue life, and the fit of mating components. Understanding the capabilities and limitations of metal 3D printing accuracy ve surface roughness metal AM is key to setting realistic expectations and planning necessary post-processing steps.
Dimensional Accuracy & Tolerances:
Metal L-PBF processes like SLM and DMLS are capable of producing parts with good dimensional accuracy, but it’s generally not as precise as high-precision CNC machining directly from the machine.
- Typical As-Printed Tolerances: For well-calibrated industrial machines printing optimized designs, typical achievable tolerances are often in the range of:
- ±0.1 mm to ±0.2 mm for smaller dimensions (e.g., up to 100 mm).
- ±0.1% to ±0.2% for larger dimensions.
- Factors Influencing Accuracy:
- Machine Calibration: Regular calibration of the laser scanning system, optics, and build platform leveling is critical.
- Süreç Parametreleri: Laser power, scan speed, layer thickness, and hatch patterns significantly impact melt pool stability and final part dimensions. Optimized parameters for specific material/machine combinations are essential.
- Thermal Effects: Residual stresses built up during printing can cause warping and distortion, affecting final dimensions. Part design (DfAM), orientation, and support strategy play a huge role in managing these stresses. Stress relief heat treatments after printing are standard practice to stabilize the part.
- Destek Kaldırma: The process of removing support structures can sometimes slightly affect the dimensions or surface quality of the areas where supports were attached.
- Part Removal: Cutting the part from the build plate can release some residual stress, potentially causing minor dimensional changes.
- Toz Özellikleri: Consistent powder quality (particle size, morphology) contributes to predictable melting and solidification.
- Achieving Tighter Tolerances: For critical features like mounting interfaces, bearing bores, or alignment pins requiring tolerances tighter than the standard as-printed capability, post-process CNC machining is typically employed. It’s common practice in DfAM to design parts with extra material (machining allowance, typically 0.5mm – 1mm) specifically on surfaces that will be machined to final tolerances.
Yüzey İşlemi (Pürüzlülük):
The surface finish of as-printed metal AM parts is inherently rougher than machined surfaces due to the layer-by-layer process and the partially melted powder particles adhering to the surface.
- Typical As-Printed Surface Roughness (Ra):
- Vertical Walls (Side Faces): Generally smoother, often in the range of 6μm to 15μm Ra.
- Top Surfaces: Can be slightly rougher due to the final layer’s exposure, perhaps 10μm to 20μm Ra.
- Down-Facing / Overhanging Surfaces: Tend to be the roughest, influenced by the interaction with support structures. Ra values can range from 15μm to 30μm or higher, depending on the angle and support strategy.
- Factors Influencing Surface Finish:
- Katman Kalınlığı: Thinner layers generally produce smoother surfaces but increase build time.
- Powder Particle Size: Finer powders can lead to smoother finishes but may pose challenges with flowability.
- Süreç Parametreleri: Laser energy density and scanning strategy affect the surface melt characteristics.
- Part Orientation: As noted, surface orientation relative to the build direction has a significant impact. Up-facing and vertical surfaces are typically best.
- Yüzey İşleminin İyileştirilmesi: For applications requiring smoother finishes (e.g., for aesthetics, fatigue performance, sealing surfaces, or bearing fits), various post-processing techniques are used:
- Abrasive Blasting (Bead/Sand Blasting): Common for achieving a uniform matte finish and removing loose powder. Can slightly improve Ra values (5μm – 10μm).
- Tumbling/Vibratory Finishing: Parts are tumbled with media to smooth surfaces and edges. Effective for batches of smaller parts, can achieve Ra around 1μm – 5μm.
- Elektro parlatma: An electrochemical process that removes a thin layer of material, resulting in a very smooth, bright, and clean surface. Can achieve Ra < 1μm.
- CNC İşleme: Provides the best control over surface finish for specific features, easily achieving Ra < 1.6μm or much lower if required.
- Manual Polishing: For achieving mirror finishes on specific areas, though labor-intensive.
Quality Control & Assurance:
Ensuring the dimensional stability drone parts require involves rigorous quality control additive manufacturing processes. This includes:
- Süreç İçi İzleme: Some advanced AM systems incorporate sensors to monitor melt pool characteristics, layer consistency, and thermal profiles during the build, allowing for real-time quality assessment.
- Post-Build Inspection:
- Boyutsal Ölçüm: Using calipers, micrometers, CMM (Coordinate Measuring Machines), or 3D scanning to verify critical dimensions against the CAD model and specifications.
- Yoğunluk Ölçümü: Assessing part density (e.g., using the Archimedes method) to check for internal porosity.
- Tahribatsız Muayene (NDT): Techniques like CT (Computed Tomography) scanning are invaluable for detecting internal defects (voids, cracks, inclusions) and verifying complex internal geometries (like lattice structures or channels) without destroying the part. Dye penetrant testing or ultrasonic testing might also be used.
- Material Testing: Performing tensile tests, hardness tests, or fatigue tests on representative samples printed alongside the main parts to verify mechanical properties meet specifications.
Summary Table: Precision & Finish
Parametre | As-Printed (Typical L-PBF) | Post-Processed (Common Methods) | Considerations for Drone Mounts |
---|---|---|---|
Hoşgörü | ±0.1−0.2 mm or ±0.1%−0.2% | < ±0.05 mm (via CNC Machining) | Identify critical interfaces requiring tighter tolerances; design with machining allowance. |
Yüzey Pürüzlülüğü (Ra) | 6μm−30+μm (orientation dependent) | < 1μm−10μm (Blasting, Polishing, Machining) | Specify required finish based on function (fit, fatigue, aesthetics); plan post-processing. |
Kalite Güvence | Process Control, Basic Inspection | CMM, 3D Scan, NDT (CT Scan), Material Testing | Define critical QA steps based on application risk; factor inspection time/cost. |
Sayfalara Aktar
Achieving the necessary precision and finish for drone camera mounts using metal AM is entirely feasible but requires careful DfAM, process control, and often, planned post-processing steps. Collaborating with a knowledgeable service provider who understands these factors and possesses robust quality control additive manufacturing procedures is essential for obtaining reliable, high-quality precision drone components.
Beyond Printing: Essential Post-Processing for Metal Camera Mounts
The journey of a metal 3D printed drone camera mount doesn’t end when the printer stops. The “as-printed” part, fresh off the build plate and encased in powder, requires several crucial post-processing steps to transform it into a functional, reliable component ready for assembly and operation. These steps are not optional extras; they are integral to achieving the desired mechanical properties, dimensional accuracy, surface finish, and overall quality required for demanding UAV applications. Understanding these common procedures, from powder removal AM için heat treatment aluminum alloys ve surface finishing metal parts, is vital for accurate project planning, costing, and lead time estimation.
Common Post-Processing Steps for Metal AM Drone Mounts:
- Powder Removal (Depowdering):
- Amacımız: To remove unfused metal powder trapped within the part (especially in internal channels or complex geometries) and adhering to the surface.
- Yöntemler: Typically involves compressed air blow-off, brushing, vacuuming, and sometimes ultrasonic cleaning baths within a controlled environment to safely handle the fine metal powder. For complex internal structures like lattices or channels, specialized depowdering equipment and techniques may be necessary. Effective powder removal AM is critical to prevent contamination and ensure subsequent processes are effective.
- Stres Giderici:
- Amacımız: The rapid heating and cooling cycles inherent in L-PBF create significant residual stresses within the printed part. These stresses can cause warping upon removal from the build plate or lead to premature failure under load. Stress relief is a thermal cycle (heating the part to a specific temperature below its aging temperature and holding it) performed önce removing the part from the build plate.
- Method: The entire build plate with the attached part(s) is placed in a furnace under a controlled atmosphere (typically argon or vacuum to prevent oxidation) and heated according to a profile specific to the alloy (e.g., for AlSi10Mg, around 300°C for 2 hours). This allows the internal stresses to relax without altering the microstructure significantly.
- Yapı Plakasından Parça Çıkarma:
- Amacımız: To separate the printed mount(s) from the metal build plate they were fused to during printing.
- Yöntemler: Commonly done using wire EDM (Electrical Discharge Machining) or a bandsaw. Care must be taken to avoid damaging the part. The interface layer between the part and the plate, often designed as part of the support structure, is cut through.
- Destek Yapısının Kaldırılması:
- Amacımız: To remove the temporary support structures required during the build process.
- Yöntemler: This can be a labor-intensive process depending on the complexity and location of the supports. Methods include:
- Manual breaking/clipping (for easily accessible, light supports).
- Machining (milling, grinding) for more robust or integrated supports.
- Wire EDM or manual tooling for delicate areas.
- Care is essential to avoid damaging the part surface where supports were attached. Marks or “witness lines” from supports are common and may require further finishing.
- Heat Treatment (Solution Annealing & Aging):
- Amacımız: To homogenize the microstructure and significantly enhance the mechanical properties (strength, hardness, ductility) of the alloy. This is particularly crucial for alloys like AlSi10Mg and A7075 to achieve their optimal performance characteristics.
- Method: This typically involves:
- Çözelti Tavlama: Heating the part to a high temperature (e.g., ~530°C for AlSi10Mg, ~470-490°C for A7075) to dissolve alloying elements into a solid solution, followed by rapid quenching (in water or gas) to lock them in place.
- Artificial Aging (Precipitation Hardening): Heating the part to a lower temperature (e.g., ~160°C for AlSi10Mg T6, specific multi-stage cycles for A7075 T6/T7x) for a set duration. This causes fine precipitates of the alloying elements to form within the metal matrix, obstructing dislocation movement and thereby increasing strength and hardness.
- Düşünceler: Precise control over temperature, time, and atmosphere (vacuum or inert gas) is critical. Heat treatment aluminum alloys like A7075 requires particularly complex cycles to achieve desired tempers without compromising other properties. Distortion can sometimes occur during heat treatment, potentially requiring fixtures or subsequent straightening/machining. Reputable AM providers possess the necessary calibrated equipment and metallurgical expertise.
- Yüzey İşlemi:
- Amacımız: To improve the surface quality (reduce roughness), achieve a desired aesthetic appearance, remove support witness marks, or prepare the surface for coating.
- Methods (as detailed previously):
- Abrasive Blasting (Bead, Sand): Creates a uniform matte finish.
- Tumbling/Vibratory Finishing: Smooths surfaces and edges, good for batches.
- Elektro parlatma: Creates a very smooth, bright finish.
- Manual Grinding/Polishing: For specific areas or achieving high-gloss finishes.
- The choice depends on the required Ra value, component geometry, material, and cost considerations.
- CNC İşleme:
- Amacımız: To achieve tight tolerances on critical features, create precision interfaces (e.g., mounting holes, bearing seats), improve surface finish on specific areas, or create features difficult to print accurately (e.g., very small holes, sharp edges).
- Method: Using standard CNC milling or turning centers. Parts must be properly fixtured. As mentioned in DfAM, designing parts with machining stock on critical surfaces (CNC machining 3D prints) is standard practice.
- Inspection & Quality Assurance:
- Amacımız: To verify dimensional accuracy, check for internal/external defects, and confirm material properties after all processing steps.
- Methods (as detailed previously): CMM, 3D scanning, NDT (CT, dye penetrant), hardness testing, tensile testing (on samples). Comprehensive quality assurance drone components protocols are essential before deployment.
- Surface Treatments & Coatings:
- Amacımız: To enhance corrosion resistance, improve wear resistance, provide electrical insulation, or alter aesthetic properties.
- Yöntemler:
- Anodizing (for Aluminum): Creates a hard, corrosion-resistant oxide layer. Can also be dyed various colors. Type II (decorative) and Type III (hardcoat) are common. Essential for A7075 in many environments.
- Chromate Conversion Coating (Alodine/Iridite): Provides corrosion protection and a good base for paint.
- Painting/Powder Coating: For aesthetics and additional environmental protection.
- Specialized Coatings: E.g., PVD/CVD coatings for extreme wear resistance (less common for mounts but possible).
- Proper surface preparation before metal parts coating is crucial for adhesion.
Integrating Post-Processing into the Workflow:
It’s crucial for procurement managers and engineers to recognize that these post-processing steps add to both the final cost and the overall lead time of the 3D printed component. A reliable AM service provider, like Met3DP, which offers comprehensive solutions spanning printers, powders, and application development, will typically factor these necessary steps into their quotations and project timelines. Their expertise ensures that each step is performed correctly, using calibrated equipment and validated procedures, ultimately delivering a drone camera mount that meets all specifications and performance requirements. Discussing post-processing needs early in the design and quoting phase is essential for a successful project outcome.
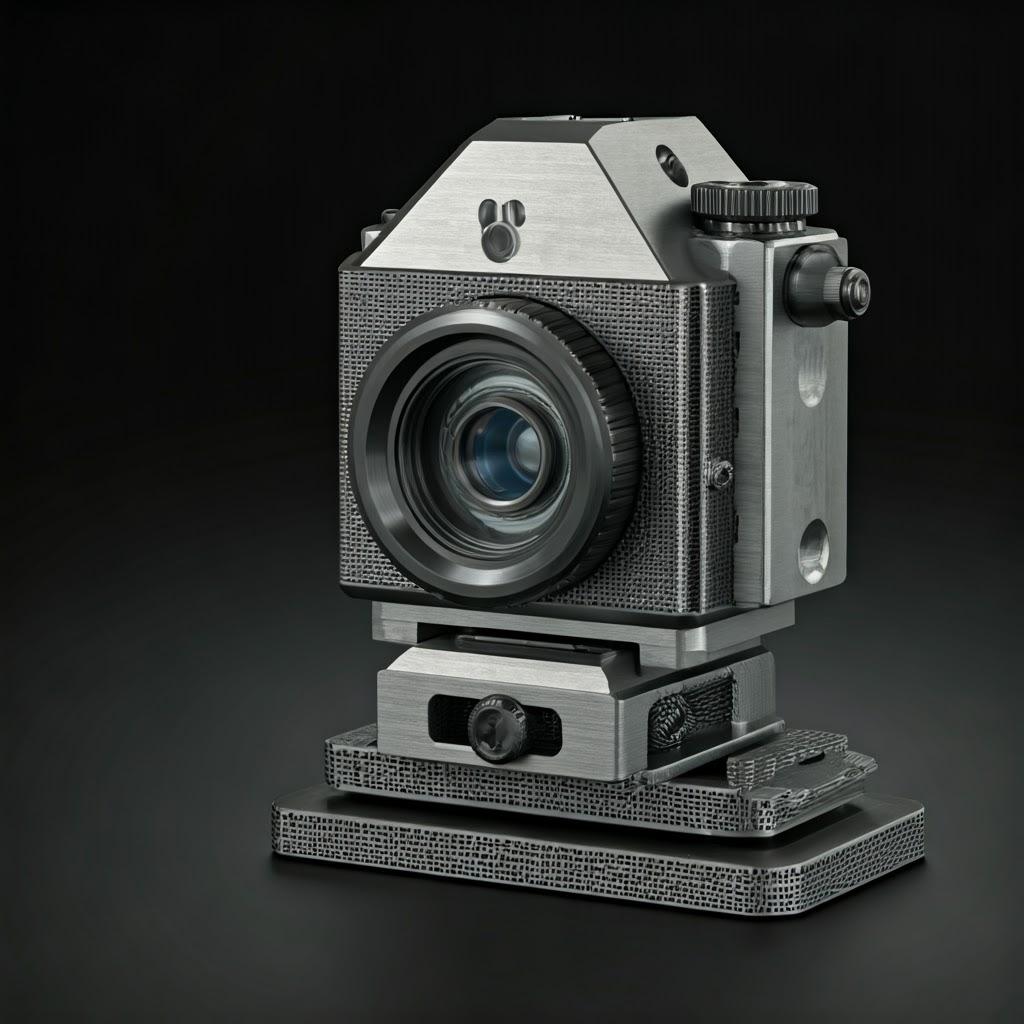
Navigating Challenges: Overcoming Hurdles in Metal AM for Drone Parts
While metal additive manufacturing offers transformative potential for producing lightweight, complex drone camera mounts, the technology is not without its challenges. Understanding these potential hurdles and the strategies to mitigate them is crucial for ensuring successful builds, reliable parts, and cost-effective production. Engineers, designers, and procurement teams should be aware of common issues like warping metal 3D printing, porosity reduction AMve support removal challenges to work effectively with their AM service provider and achieve reliable drone parts manufacturing.
1. Warping and Distortion (Residual Stress):
- Meydan okumak: The intense, localized heating from the laser and subsequent rapid cooling creates significant temperature gradients within the part during the L-PBF process. This leads to the build-up of internal residual stresses. If these stresses exceed the material’s yield strength at elevated temperatures, or upon release from the build plate, the part can warp, distort, or even crack. Thin features, large flat areas parallel to the build plate, and asymmetric designs are particularly susceptible.
- Mitigation Strategies:
- DfAM: Design parts with gradual thickness transitions, avoid large unsupported flat sections, and incorporate ribbing or corrugation to increase stiffness.
- Yapı Oryantasyonu: Strategically orient the part to minimize stress concentration and the build-up of thermal gradients across large sections. Often, orienting the longest dimension vertically helps.
- Destek Yapıları: Use robust support structures, properly designed not just for overhangs but also to anchor the part securely to the build plate, acting as heat sinks and resisting distortion forces. Advanced software can simulate stress and optimize support placement.
- Süreç Parametreleri: Optimize laser scanning strategy (e.g., island scanning, alternating hatch directions) to distribute heat input more evenly and reduce localized overheating.
- Termal Yönetim: Some machines offer build plate heating, which can reduce the thermal gradient between the part and the plate.
- Stress Relief Heat Treatment: Performing a stress relief cycle önce removing the part from the build plate is standard practice and highly effective at reducing internal stresses and preventing distortion upon removal.
2. Porosity:
- Meydan okumak: The presence of small voids or pores within the printed material. Porosity can significantly degrade mechanical properties, particularly fatigue strength, fracture toughness, and ductility. It can arise from several sources:
- Gas Porosity: Trapped gas (e.g., argon shield gas, dissolved gases within the powder) within the melt pool that doesn’t escape before solidification.
- Keyhole Porosity: Caused by excessive laser energy density, leading to deep, unstable melt pools that collapse and trap vapor/gas.
- Lack-of-Fusion Porosity: Insufficient energy density or improper overlap between scan tracks/layers, resulting in incomplete melting and bonding between powder particles or layers.
- Mitigation Strategies:
- Toz Kalitesi: Use high-quality, spherical powder with low internal porosity and controlled particle size distribution. Proper powder handling and storage are crucial to prevent moisture absorption and contamination. Met3DP’s focus on yüksek kaliteli metal tozları using advanced atomization techniques addresses this at the source.
- Parametre Optimizasyonu: Develop and strictly adhere to validated process parameters (laser power, scan speed, layer thickness, hatch spacing) optimized for the specific material and machine to ensure stable melting and proper fusion. This is a core expertise area for established service providers.
- Shielding Gas Flow: Ensure proper inert gas flow (typically Argon) within the build chamber to effectively remove processing byproducts and prevent oxidation/contamination of the melt pool.
- Kalite Kontrol: Utilize NDT methods like CT scanning, especially for critical components, to detect and quantify internal porosity. Density measurements also provide an indication of overall porosity levels.
3. Support Structure Removal & Surface Marks:
- Meydan okumak: While necessary, support structures can be difficult and time-consuming to remove, especially from complex internal geometries or delicate features. The removal process itself can potentially damage the part or leave undesirable witness marks on the surface.
- Mitigation Strategies:
- DfAM: Minimize the need for supports through clever design (self-supporting angles, optimal orientation). Design supports for easier removal (e.g., using smaller contact points, perforation, specific support types like tree supports). Ensure accessibility for removal tools.
- Process Planning: Choose support types and parameters (e.g., density, fragmentation) that balance support effectiveness with ease of removal.
- Skilled Labor: Support removal often requires careful manual work by trained technicians.
- İşlem sonrası: Plan for subsequent finishing steps (blasting, tumbling, machining) to remove witness marks if surface aesthetics or function require it.
4. Achieving Consistent Material Properties:
- Meydan okumak: The rapid solidification and complex thermal history during AM can lead to fine-grained, non-equilibrium microstructures that differ from traditional wrought or cast materials. Achieving consistent mechanical properties (strength, ductility, fatigue life) across the part and between different builds requires tight control.
- Mitigation Strategies:
- Validated Processes: Partner with service providers who have well-documented, validated processes for the specific material, machine, and post-processing steps (especially heat treatment).
- Süreç İzleme: Utilize machines with in-situ monitoring capabilities where possible.
- Rigorous Testing: Implement a robust quality control plan including material testing (e.g., tensile bars printed alongside parts) to verify properties for each build or batch.
- Standartlaştırma: Adhere to industry standards (e.g., ASTM, ISO AM standards) for process control and material specification.
5. Powder Handling, Recycling, and Safety:
- Meydan okumak: Metal powders, especially reactive ones like aluminum or titanium, can be hazardous (flammable, respirable). Handling, sieving, blending, and recycling unused powder require specialized equipment and strict safety protocols to prevent contamination, degradation, and safety incidents. Maintaining powder traceability and quality through recycling loops is critical.
- Mitigation Strategies:
- Controlled Environments: Use dedicated powder handling stations with proper ventilation, grounding, and inert atmosphere capabilities where needed.
- Safety Protocols: Implement strict PPE (Personal Protective Equipment) requirements and handling procedures.
- Toz Yaşam Döngüsü Yönetimi: Track powder batches, usage history, and recycling cycles. Perform regular quality checks (e.g., PSD analysis, chemistry) on recycled powder to ensure it meets specifications. Partnering with providers like Met3DP, who manufacture their own powders and understand these requirements deeply, is advantageous.
6. Cost Management:
- Meydan okumak: Metal AM can have higher initial costs per part compared to traditional methods, especially for simpler designs or very high volumes, due to expensive machines, materials, and skilled labor. Failed builds or extensive post-processing add to the cost.
- Mitigation Strategies:
- DfAM for Value: Focus AM on applications where its unique benefits (complexity, lightweighting, consolidation) provide significant value that outweighs the cost.
- Optimize Design: Minimize build time and material usage through topology optimization and efficient support strategies.
- Yuvalama: Print multiple parts simultaneously on the build plate to improve machine utilization.
- Process Reliability: Work with experienced providers with high first-time-right rates to minimize costly build failures.
- Post-Processing Planning: Factor necessary post-processing into the initial cost estimation.
Navigating these challenges successfully requires a combination of smart design (DfAM), robust process control, advanced equipment, rigorous quality assurance, and experienced personnel. This is where established companies with deep expertise in specific baskı yöntemleri like L-PBF and materials science excel, providing the necessary foundation for reliable drone parts manufacturing. By understanding these potential issues and proactively addressing them, the full benefits of metal AM for drone camera mounts can be realized.
Supplier Selection: Choosing the Right Metal 3D Printing Partner for UAV Components
Selecting the appropriate manufacturing partner is arguably one of the most critical decisions when adopting metal additive manufacturing for high-stakes applications like UAV camera mounts. The quality, reliability, cost-effectiveness, and timely delivery of your components hinge on the capabilities and expertise of your chosen metal AM service provider. Given the technical complexities involved in metal L-PBF, DfAM, material science, and post-processing, not all providers are created equal. For engineers and procurement managers involved in drone parts manufacturer evaluation ve bulk drone component sourcing, a thorough vetting process is essential. Here’s a comprehensive guide to evaluating potential partners:
1. Technical Expertise & Engineering Support:
- Materials Knowledge: Do they have deep expertise in the specific alloys you require (e.g., AlSi10Mg, A7075)? Can they advise on material selection based on your application’s demands? Do they understand the nuances of printing specific alloys, including potential challenges and required heat treatments?
- DfAM Capability: Can they provide DfAM support? Will their engineers collaborate with your team to optimize the mount design for printability, lightweighting, support minimization, and performance? Look for evidence of successful topology optimization or lattice structure implementation.
- Process Knowledge: Do they possess a fundamental understanding of the L-PBF process physics? Can they explain how they optimize parameters for density, accuracy, and surface finish? What is their approach to process validation and control?
- Problem Solving: How do they handle build failures or unexpected issues? Do they have systematic troubleshooting procedures?
2. Equipment Capability & Capacity:
- Machine Technology: What specific L-PBF machines do they operate? Are they modern, well-maintained industrial systems from reputable manufacturers? Do they have machines suitable for the required build volume and material? (While Met3DP specializes in SEBM printers, many comprehensive providers operate multiple AM technologies, including L-PBF systems ideal for aluminum).
- Capacity & Redundancy: Do they have sufficient machine capacity to meet your required lead times, for both prototyping and potential series production? Do they have multiple machines capable of running your material to provide redundancy in case of maintenance or breakdowns?
- Ancillary Equipment: Do they possess the necessary calibrated equipment for post-processing, particularly furnaces for stress relief and heat treatment under controlled atmospheres, depowdering stations, and basic finishing tools?
3. Quality Management Systems & Certifications:
- ISO 9001: This is a fundamental requirement, indicating a documented quality management system for consistency and traceability.
- AS9100 (Aerospace): If your drone components are intended for aerospace, defense, or high-reliability applications, partnering with an aerospace certified supplier holding AS9100 certification is often mandatory. This signifies adherence to stricter quality control, traceability, and risk management protocols.
- Material Traceability: How do they track metal powder batches from sourcing through production and recycling? Can they provide full material certifications and traceability records for your parts?
- Inspection Capabilities: What dimensional inspection equipment (CMM, 3D scanners) and NDT capabilities (e.g., CT scanning, FPI) do they possess in-house or through certified partners?
4. Experience & Track Record:
- Relevant Industry Experience: Have they successfully produced parts for the UAV, aerospace, automotive, or medical industries? Can they provide case studies or references (while respecting confidentiality)? Experience with UAV component supplier requirements is a plus.
- Specific Alloy Experience: How many successful builds have they completed using AlSi10Mg or, more critically, the challenging A7075 alloy? Proven experience significantly reduces risk.
- Parça Karmaşıklığı: Can they showcase examples of complex parts they have printed, demonstrating their ability to handle intricate geometries, thin walls, and internal features similar to your camera mount design?
5. Post-Processing Capabilities:
- Şirket İçi ve Dış Kaynaklı: Which post-processing steps (stress relief, heat treatment, support removal, machining, finishing, coating) do they perform in-house? Having critical steps like heat treatment and CNC machining in-house often leads to better control, faster turnaround, and accountability. If outsourced, what is their process for managing and qualifying their subcontractors?
- Uzmanlık alanı: Do they have metallurgical expertise for heat treatment and skilled technicians for support removal and finishing? Do they have CNC machining capabilities suitable for achieving your required tolerances and finishes?
6. Communication, Project Management & Support:
- Responsiveness: Are they responsive to inquiries and requests for quotes?
- Project Management: Do they assign a dedicated point of contact for your project? How do they manage project timelines and communicate progress?
- Şeffaflık: Are they open about their processes, capabilities, and potential challenges?
7. Location & Logistics:
- Nakliye: Consider shipping costs and times, especially for international suppliers. Understand customs and import/export regulations if applicable.
- Site Visits: Is it possible to visit their facility for an audit or assessment?
8. Cost & Value:
- Quoting Clarity: Are their quotes detailed and transparent, breaking down costs for printing, material, support, post-processing, and NQA?
- Value Proposition: Don’t select solely on the lowest price. Consider the provider’s expertise, quality system, reliability, and support, which contribute to the overall value and reduce risks associated with failed builds or poor-quality parts.
Highlighting Met3DP’s Strengths:
When evaluating potential partners, companies like Met3DP present a compelling profile for specific needs, particularly highlighting their deep materials science background. Key strengths often include:
- Materials Expertise: As a company that researches, develops, and manufactures its own yüksek kaliteli metal tozları gelişmiş kullanarak gaz atomizasyonu ve PREP teknolojileri, Met3DP possesses inherent expertise in material behavior during AM processes. Their portfolio includes innovative alloys alongside standard materials, showcasing R&D capability.
- Integrated Solutions: Offering solutions that span Hakkımızda – including specialized SEBM printers (known for specific advantages with materials like titanium and refractory metals) and advanced metal powders – indicates a comprehensive understanding of the AM ecosystem. While L-PBF is key for aluminum drone mounts, a provider with broad AM knowledge is valuable.
- Sektör Odaklı: Their stated focus on mission-critical parts in aerospace, medical, and automotive fields aligns with the high-reliability requirements often needed for drone components.
- Tecrübe: Decades of collective expertise in metal additive manufacturing suggests a mature understanding of the technology and its application.
Supplier Evaluation Checklist Summary:
Criterion | Anahtar Sorular | Önem |
---|---|---|
Teknik Uzmanlık | DfAM support? Material knowledge (AlSi10Mg/A7075)? Process understanding? Problem-solving? | Çok Yüksek |
Equipment & Capacity | Suitable L-PBF machines? Capacity/Redundancy? Post-processing equipment? | Yüksek |
Kalite Sistemleri | ISO 9001? AS9100 (if needed)? Material traceability? Inspection/NDT capabilities? | Çok Yüksek |
Experience & Track Record | UAV/Aerospace experience? Specific alloy experience? Complex part examples? References? | Yüksek |
İşlem Sonrası | In-house capabilities (Heat Treat, Machining)? Expertise? Subcontractor management? | Yüksek |
Communication & Support | Responsiveness? Project management? Transparency? | Orta-Yüksek |
Location & Logistics | Shipping considerations? Audit possibility? | Orta |
Maliyet ve Değer | Quote clarity? Value beyond price (quality, reliability)? | Yüksek |
Sayfalara Aktar
Doğru seçimi yapmak metal AM service provider is a strategic decision. Thoroughly evaluating potential partners against these criteria will significantly increase the likelihood of receiving high-quality, reliable drone camera mounts that meet performance expectations and contribute to a successful drone component supply chain.
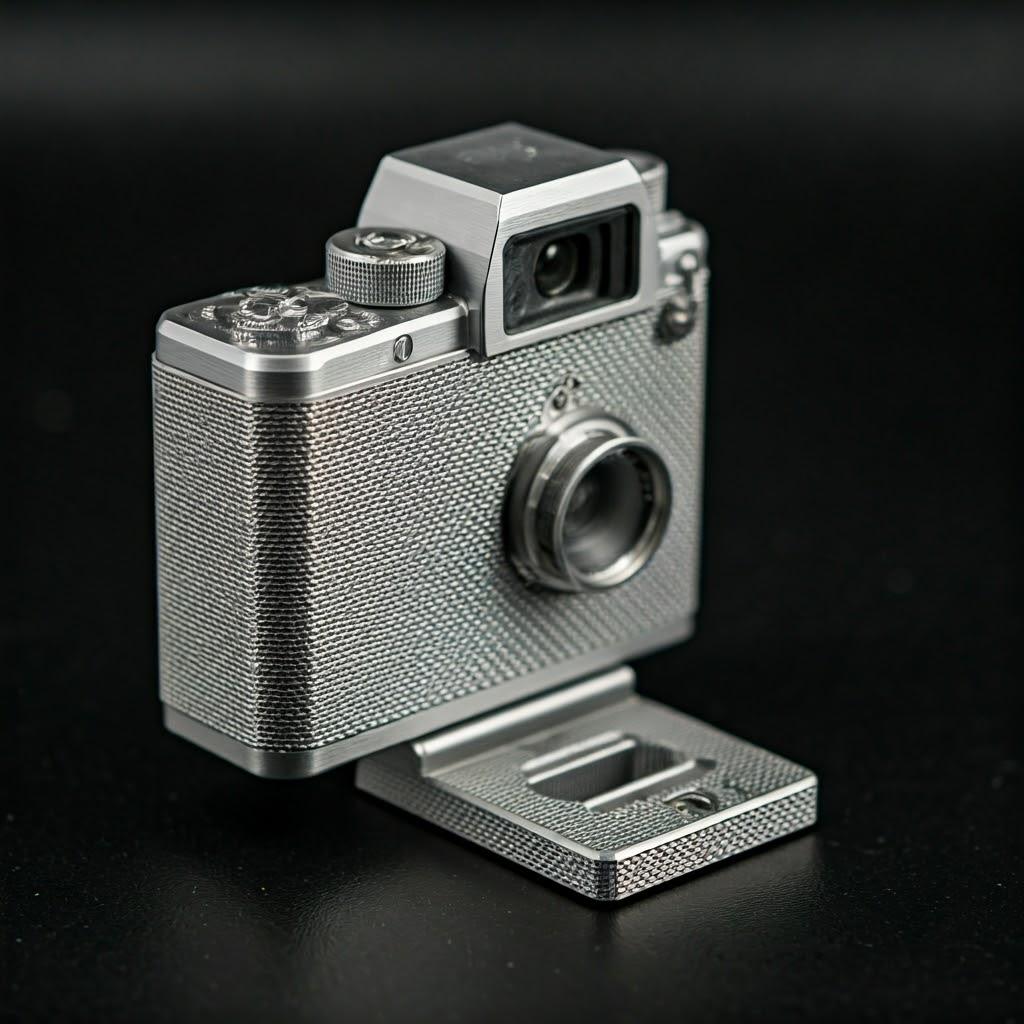
Cost Dynamics and Lead Times: Budgeting for 3D Printed Metal Mounts
One of the most frequent considerations for adopting any new manufacturing technology revolves around cost and production speed. Engineers and procurement managers need realistic estimates of metal 3D printing cost factors ve additive manufacturing lead time to accurately budget for projects and manage supply chains effectively. While metal AM can sometimes carry a higher per-part price compared to traditional methods for simple geometries in high volumes, its value proposition often lies in areas like reduced assembly costs, enhanced performance through lightweighting, and accelerated development cycles. Understanding what drives costs and timelines is key to leveraging metal AM strategically for drone camera mounts.
Factors Influencing Cost:
Bu cost per part AM for a metal drone camera mount is influenced by a combination of factors:
- Malzeme Maliyeti:
- Powder Price: The cost per kilogram of the chosen metal powder (e.g., AlSi10Mg is generally less expensive than specialized A7075 AM grades or titanium alloys). High-quality, AM-optimized powders from reputable suppliers command premium pricing but ensure better results.
- Powder Consumption: This includes the material in the final part artı the material used for support structures artı any powder lost or degraded during handling and recycling. Efficient DfAM (minimizing supports, using topology optimization) helps reduce consumption.
- Makine Zamanı (İnşa Zamanı):
- Part Volume & Height: Larger or taller parts naturally take longer to print layer by layer.
- Parça Karmaşıklığı: Highly intricate designs or those requiring extensive support structures increase print time.
- Nesting & Build Density: Printing multiple parts simultaneously (nesting) on a single build plate utilizes the machine more efficiently, reducing the amortized machine time cost per part. However, filling the build plate increases the overall build duration.
- Layer Thickness & Parameters: Thinner layers improve resolution but increase build time; optimized parameters balance speed and quality.
- Machine Hourly Rate: Industrial metal AM systems represent significant capital investment, and their operational costs (energy, gas, maintenance) contribute to a high hourly rate, which is factored into the part cost.
- İşçilik Maliyetleri:
- Pre-Processing: Time spent by engineers/technicians for build preparation (file setup, orientation, support generation, slicing).
- İşlem sonrası: This is often a significant cost driver. It includes labor for depowdering, stress relief, part removal, support removal (can be very time-intensive), heat treatment, surface finishing, CNC machining, inspection, and quality assurance. The more complex the part and the stricter the requirements, the higher the post-processing labor cost.
- Support Structure Volume:
- Supports consume material and machine time to print.
- They require significant labor to remove.
- Minimizing supports through DfAM directly reduces cost.
- Part Complexity & Design:
- While AM handles complexity well, extremely intricate designs olabilmek increase build time and post-processing difficulty (e.g., removing powder/supports from complex internal channels or lattices).
- However, AM’s ability to consolidate assemblies into single parts can reduce overall product cost by eliminating assembly labor and fastener costs.
- Quality Assurance Requirements:
- The level of inspection and testing required (basic dimensional checks vs. CMM, CT scanning, material testing) adds cost. Stricter requirements (e.g., for aerospace certification) significantly increase QA costs.
- Sipariş Hacmi:
- Like most manufacturing processes, there are economies of scale. Setup costs are amortized over larger batches. While AM has no tooling cost, the cost per part generally decreases with higher volumes due to more efficient machine utilization and batch post-processing, although the effect might be less dramatic than in mass production methods like injection molding. Wholesale drone parts pricing reflects these volume considerations.
Factors Influencing Lead Time:
Bu additive manufacturing lead time from order placement to shipped parts depends on several variables:
- Build Preparation: Time required for file check, DfAM review (if needed), orientation, support strategy, and slicing (typically 1-3 days, depending on complexity and communication).
- Machine Availability & Queue: The service provider’s current workload and machine availability for the required material. Lead times can fluctuate based on demand.
- Yapım süresi: The actual time the part spends printing in the machine (can range from hours for small parts to several days for large, complex builds or full plates).
- Post-Processing Time: This often takes longer than the printing itself. Stress relief, cooling, part removal, support removal, heat treatment cycles (which can take a full day or more including ramp-up/down), machining setup and runtime, finishing, and inspection all add significant time (can range from 2-3 days to several weeks for complex parts with extensive requirements).
- Shipping Time: Transit time to the customer’s location.
Typical Lead Time Estimates (General Guide):
- Prototypes (1-10 units): Often 1-3 weeks, depending heavily on complexity and post-processing needs. Expedited services may be available at higher cost.
- Low-Volume Production (10-100 units): Typically 3-6 weeks, allowing for batch processing and scheduling efficiencies.
- Higher Volumes: Depends greatly on capacity, part size, and whether dedicated machine time is allocated.
Return on Investment (ROI) Considerations:
While the direct cost per part AM might sometimes seem high, evaluating the ROI metal 3D printing offers requires a broader perspective:
- Reduced Time-to-Market: Faster prototyping and iteration cycles accelerate product development.
- Geliştirilmiş Performans: Lightweighting via topology optimization can translate to significant operational savings (e.g., longer drone flight times, higher payload capacity) or competitive advantages.
- Parça Konsolidasyonu: Reducing assembly time, part count, and potential points of failure saves costs downstream.
- Supply Chain Agility: On-demand manufacturing reduces inventory holding costs and allows for faster response to changing needs, improving the drone component supply chain.
- Özelleştirme: Ability to produce bespoke or low-volume custom mounts economically.
By carefully considering these cost drivers and lead time factors, and by working closely with an experienced metal AM provider to optimize designs and processes, companies can effectively budget for and strategically implement 3D printed metal drone camera mounts, unlocking significant performance and operational benefits.
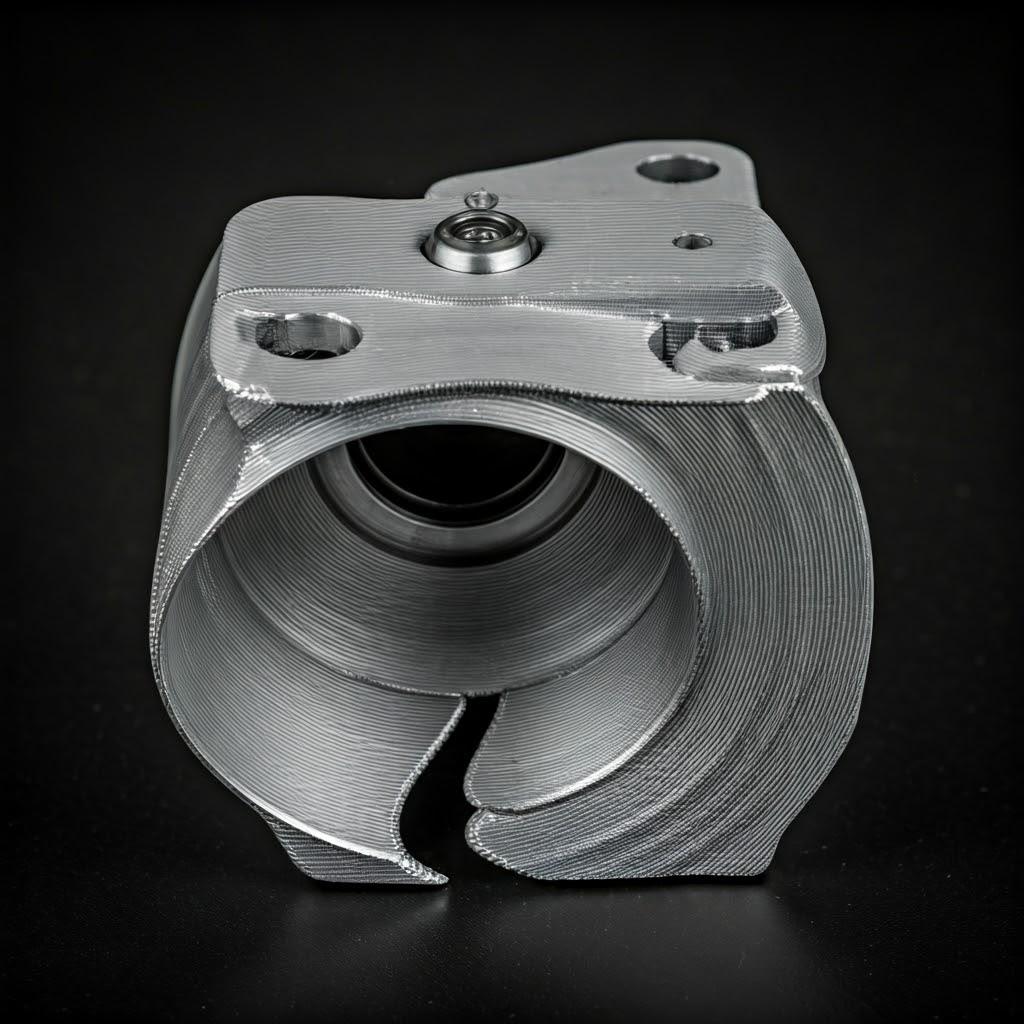
Frequently Asked Questions (FAQ): Metal 3D Printed Drone Camera Mounts
Here are answers to some common questions engineers and procurement managers have about using metal additive manufacturing for drone camera mounts:
1. How does the strength and durability of a 3D printed aluminum mount (e.g., AlSi10Mg or A7075) compare to a traditionally CNC machined mount from a solid block of the same or similar alloy (e.g., 6061-T6 or 7075-T6)?
This is a critical question touching on 3D printed gimbal strength ve metal AM durability UAV. The answer requires nuance:
- Malzeme Özellikleri: When printed using optimized parameters and subjected to appropriate post-processing (especially heat treatment), the intrinsic material properties of AM AlSi10Mg-T6 or AM A7075-T6 can be very comparable, and in some cases even slightly superior (e.g., yield strength due to finer grain structure), to their traditional counterparts like cast A360 or wrought 6061-T6 / 7075-T6. AM A7075, when processed correctly, aims to match the high strength levels of wrought 7075-T6.
- Potential Weaknesses: AM parts can be more susceptible to fatigue failure if internal defects (like porosity) are present or if the surface finish is poor (acting as crack initiation sites). Anisotropy (directional properties) can also be a factor, though typically less pronounced in aluminum than some other AM metals. Proper process control and NDT are crucial to mitigate these risks.
- Design Advantage: The key advantage of AM often lies not in matching the bulk material properties exactly, but in using DfAM and topology optimization. An AM mount might use less material overall but place it more intelligently along load paths. This means the final component’s performance (stiffness-to-weight ratio, specific strength) can significantly exceed that of a traditionally designed and machined part, even if the base material properties are only comparable. The optimized AM design achieves the required strength and stiffness with much less weight.
- Sonuç: A well-designed, properly printed, and heat-treated metal AM drone mount made from AlSi10Mg or A7075 can absolutely meet or exceed the strength and durability requirements of demanding applications, often providing superior performance-to-weight compared to traditionally machined components. The key is rigorous process control, appropriate post-processing, and intelligent design (DfAM).
2. What is the typical lifespan or operational durability of a metal AM drone mount, especially considering factors like vibration and environmental exposure?
Metal AM durability UAV components depend heavily on design, material, process quality, and the operating environment.
- Fatigue Life: This is often the primary life-limiting factor for components subjected to drone vibrations and flight loads.
- Malzeme Seçimi: High-strength alloys like A7075 generally offer better fatigue resistance than AlSi10Mg.
- Defects: Internal porosity acts as stress concentrators and drastically reduces fatigue life. Ensuring high part density (>99.5%, often >99.8%) through optimized printing is critical.
- Yüzey İşlemi: Rougher surfaces, especially as-printed ones or those with support witness marks, can be initiation sites for fatigue cracks. Post-processing like bead blasting, tumbling, or machining critical areas improves fatigue performance.
- Tasarım: Avoiding sharp corners and designing for smooth stress flow using DfAM principles is essential.
- Environmental Factors:
- Corrosion: AlSi10Mg has good corrosion resistance. A7075 is more susceptible and typically requires protective coatings like anodizing or painting, especially in humid or marine environments. The coating’s durability then becomes a factor.
- Sıcaklık: Aluminum alloys maintain good properties over the typical operating range for most drones. Extreme temperatures might require different material considerations.
- Lifespan Expectation: When designed, manufactured, and post-processed correctly, a metal AM drone mount should have a lifespan comparable to or exceeding that of a traditionally manufactured equivalent designed for the same operational loads. Its durability stems from using robust engineering metals combined with optimized designs. Fatigue life is often the design driver, and working with an experienced AM provider to ensure high density and good surface finish is paramount for long-term reliability. Regular inspection as part of the drone maintenance schedule is recommended.
3. Is metal AM cost-effective for producing custom or low-volume drone camera mounts compared to CNC machining? What about higher volumes compared to injection molding?
Evaluating the custom drone mount cost-effectiveness requires comparing AM to alternatives based on volume and complexity:
- Prototypes & Custom/Low Volume (1-50 units): Metal AM is often highly cost-effective in this range.
- Kalıp Maliyeti Yok: Unlike injection molding (which requires expensive molds) or sometimes even complex fixtures for CNC, AM goes directly from CAD to part.
- Complexity is (Almost) Free: AM excels at complex geometries that might require extensive setup, multiple operations, or specialized tooling for CNC machining, making AM cheaper for intricate designs.
- Hız: Faster turnaround for initial prototypes or custom one-offs compared to sourcing tooling or complex CNC programming.
- Medium Volume (50-1000 units): This is often a crossover range where the best choice depends on the specific part.
- CNC İşleme: For simpler geometries, CNC machining often becomes more cost-effective per part as volumes increase due to faster cycle times once programmed.
- Metal AM: Can remain competitive for highly complex, topology-optimized, or consolidated parts where the performance benefits (lightweighting) provide significant value, or where assembly steps are eliminated. Wholesale drone parts pricing for AM parts will show some volume discount, but perhaps less dramatically than machining.
- High Volume (1000+ units):
- Injection Molding (Plastic/MIM): For very high volumes where the design is stable, the high upfront tooling cost of injection molding (for plastics or Metal Injection Molding – MIM) gets amortized, leading to the lowest cost per part if the design complexity and material properties are suitable. Plastic mounts are common for consumer drones, while MIM could be an option for some metal designs.
- CNC İşleme: Remains viable for high volumes if the geometry is suitable and metal properties are required.
- Metal AM: Generally not the most cost-effective option for basit parts at very high volumes compared to molding or conventional machining. Its strength remains in high-value, complex components where its unique capabilities justify the cost, or where design flexibility is still needed.
Comparison Summary:
Özellik | Metal AM (L-PBF) | CNC İşleme | Injection Molding (Plastic/MIM) |
---|---|---|---|
Kalıp Maliyeti | Hiçbiri | Düşük (Fikstürler) | Very High (Molds) |
Karmaşıklık | Handles High Complexity | Orta Karmaşıklık | High Complexity Possible |
Lead Time (1) | Hızlı | Orta düzeyde | Very Slow |
Cost (1-50) | Often Lowest | Orta-Yüksek | Prohibitive |
Cost (50-1k) | Competitive (Complex) | Often Lower (Simple) | High (MIM) / Low (Plastic) |
Cost (1k+) | Daha yüksek | Rekabetçi | Lowest (If Suitable) |
Sayfalara Aktar
Therefore, metal AM is exceptionally well-suited and often the most cost-effective method for prototyping, customization, and low-volume production of drone camera mounts, especially complex, lightweight designs. For higher volumes, a careful cost-benefit analysis comparing AM’s performance advantages against the per-part costs of CNC machining or potentially injection molding is required.
Conclusion: Elevating UAV Performance with Advanced Metal Additive Manufacturing
The landscape of Unmanned Aerial Vehicle technology is one of constant innovation, driven by the pursuit of greater endurance, enhanced capabilities, and improved operational efficiency. In this pursuit, the strategic adoption of advanced manufacturing techniques plays a pivotal role. As we’ve explored, metal katkılı üretim, specifically Laser Powder Bed Fusion, has emerged as a powerful enabler for creating the next generation of high-performance drone components, particularly sophisticated camera mounts and gimbal systems.
By leveraging the unparalleled design freedom of AM, engineers can now craft camera mounts that are radically different from their predecessors. Through topoloji optimizasyonu and the use of intricate lattice structures, components can be meticulously engineered for maximum stiffness and strength precisely where needed, while shedding every unnecessary gram of weight. This hafifletme capability translates directly into tangible benefits: extended flight times, the ability to carry more sensors or larger batteries, improved maneuverability, and reduced overall system mass. For industries relying on UAVs for critical tasks – from aerospace surveillance and infrastructure inspection to precision agriculture and cinematic artistry – these performance gains are invaluable.
The journey involves more than just printing, however. Success hinges on a holistic approach encompassing:
- Intelligent Design (DfAM): Thinking additively from the start to optimize geometry, minimize supports, and plan for post-processing.
- Strategic Material Selection: Choosing high-performance alloys like AlSi10Mg or A7075, sourced as high-quality powders from expert manufacturers.
- Controlled Processing: Utilizing validated printing parameters and rigorous quality control to ensure part density and integrity.
- Essential Post-Processing: Implementing necessary steps like stress relief, heat treatment, support removal, machining, and finishing to achieve final specifications.
- Careful Supplier Selection: Partnering with an experienced and capable metal AM service provider equipped with the right technology, expertise, and quality systems.
While challenges related to cost, precision, and process control exist, they are being continuously addressed through technological advancements and growing industry expertise. The ability to rapidly prototype, iterate designs, produce highly customized solutions, and consolidate complex assemblies offers a compelling value proposition that often outweighs the initial per-part cost considerations, especially for low-to-medium volumes or performance-critical applications.
Bu future of drone manufacturing will undoubtedly see increased integration of metal AM, moving beyond prototyping into series production for a wider range of structural and functional components. It facilitates a more agile and resilient drone component supply chain, etkinleştirme strategic sourcing drone parts based on performance and on-demand availability rather than solely traditional constraints.
For companies looking to push the boundaries of UAV performance, exploring the potential of metal 3D printing for camera mounts and other critical components is no longer just an option – it’s a strategic imperative. By partnering with knowledgeable experts and embracing the possibilities of additive manufacturing, you can elevate your UAV systems to new heights of capability and efficiency.
To learn more about how advanced metal powders and additive manufacturing solutions can revolutionize your drone components, explore the comprehensive resources and expertise available at Met3DP. Discover the potential of cutting-edge Met3DP solutions and begin your journey towards next-generation UAV performance today.
Paylaş
MET3DP Technology Co, LTD, merkezi Qingdao, Çin'de bulunan lider bir katmanlı üretim çözümleri sağlayıcısıdır. Şirketimiz, endüstriyel uygulamalar için 3D baskı ekipmanları ve yüksek performanslı metal tozları konusunda uzmanlaşmıştır.
İşletmeniz için en iyi fiyatı ve özelleştirilmiş Çözümü almak için sorgulayın!
İlgili Makaleler
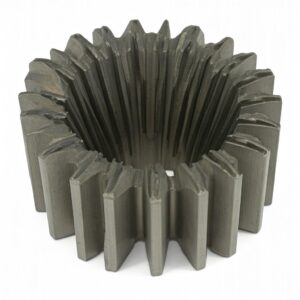
Yüksek Performanslı Nozul Kanat Segmentleri: Metal 3D Baskı ile Türbin Verimliliğinde Devrim
Daha Fazla Oku "Met3DP Hakkında
Son Güncelleme
Bizim Ürünümüz
BİZE ULAŞIN
Herhangi bir sorunuz var mı? Bize şimdi mesaj gönderin! Mesajınızı aldıktan sonra tüm ekibimizle talebinize hizmet edeceğiz.
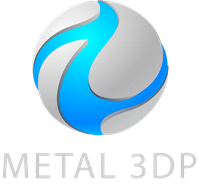
3D Baskı ve Katmanlı Üretim için Metal Tozları