Custom Ducting for Aerospace via Metal AM
İçindekiler
Introduction: The Critical Role of Custom Ducting in Modern Aerospace Systems
Aerospace engineering pushes the boundaries of performance, efficiency, and reliability. Within the intricate network of systems that make up modern aircraft and spacecraft, ducting plays an often underestimated yet absolutely critical role. These are not mere pipes; they are highly engineered conduits responsible for the safe and efficient transport of air, fluids, and conditioned gases essential for propulsion, environmental control, avionics cooling, and numerous other vital functions. From the complex network of the Environmental Control System (ECS) ensuring passenger comfort and cabin pressurization, to the high-temperature bleed air ducts siphoning power from engines, and the delicate channels cooling sensitive electronic components, aerospace ducting is fundamental to flight safety and operational performance.
Traditionally, manufacturing these components has relied on methods like sheet metal forming, hydroforming, casting, welding, and extensive manual assembly. While proven, these techniques often face significant limitations when confronted with the increasing complexity and performance demands of next-generation aerospace designs. Key challenges include:
- Geometric Complexity: Modern designs often require ducts with intricate curves, varying cross-sections, and integrated features (flanges, mounting points) that are difficult, time-consuming, and expensive to produce using conventional means. Multi-part assemblies become necessary, introducing potential leak points, added weight, and increased assembly labor.
- Teslim Süreleri: Tooling creation, multi-step fabrication processes, and manual assembly contribute to long lead times, hindering rapid prototyping, design iteration, and efficient production schedules. This is particularly challenging in the fast-paced aerospace sector where quick adaptation and deployment are crucial.
- Ağırlık: Every kilogram saved on an aircraft translates to significant fuel savings or increased payload capacity over its operational lifetime. Traditional manufacturing methods, especially those involving multiple joined parts and heavy flanges, often result in ducting systems that are heavier than optimally desired.
- Part Count and Reliability: Assemblies comprising multiple sections joined by welding, brazing, or mechanical fasteners inherently introduce potential points of failure (leaks, stress concentrations). Reducing part count directly enhances system reliability and simplifies maintenance.
Recognizing these limitations, the aerospace industry is increasingly turning towards Metal Katmanlı Üretim (AM), commonly known as metal 3D baskı, as a transformative solution for producing custom aerospace components, especially complex ducting. AM technologies, such as Laser Powder Bed Fusion (LPBF) and Electron Beam Melting (EBM), build parts layer by layer directly from digital models using high-performance metal powders. This approach fundamentally changes the paradigm of duct manufacturing, offering unprecedented design freedom, enabling the creation of highly optimized, lightweight, and integrated ducting solutions that were previously impossible or prohibitively expensive to realize. Companies specializing in metal 3D baskı, like Met3dp, are at the forefront, providing the advanced equipment and materials necessary to unlock these benefits for demanding aerospace applications. This shift is not just about making existing duct designs differently; it’s about rethinking duct design itself to achieve superior performance and efficiency in aerospace systems.
Applications: Where is Metal AM Custom Ducting Utilized in Aerospace?
The versatility and unique capabilities of metal additive manufacturing have opened doors for its application across a wide spectrum of aerospace ducting needs. Its ability to produce complex, lightweight, and consolidated parts makes it ideal for systems where space is limited, weight is critical, and performance requirements are stringent. Procurement managers and engineers in aerospace are increasingly specifying metal AM for ducts in both new aircraft designs and for retrofitting or MRO (Maintenance, Repair, Overhaul) purposes.
Here are some key application areas where 3D printed aircraft ducting is making a significant impact:
- Çevresel Kontrol Sistemleri (ECS):
- Complex Duct Geometries: ECS ducting often involves intricate routing through confined spaces within the aircraft fuselage and wings. Metal AM allows the creation of ducts with smooth, complex curves, variable cross-sections, and integrated Y- or T-junctions as single monolithic parts, drastically reducing part count compared to traditional multi-piece assemblies.
- Optimized Airflow: AM enables the design of internal duct geometries optimized for minimal pressure drop and uniform airflow distribution, enhancing ECS efficiency and passenger comfort. Features like internal guide vanes can be directly printed into the duct.
- Integration: Brackets, mounting points, and sensor housings can be integrated directly into the duct design, simplifying installation and reducing assembly time and potential leak paths.
- Engine Bleed Air Systems:
- Yüksek Sıcaklık Performansı: Ducts carrying hot air bled from engine compressors operate under demanding temperature and pressure conditions. Specialized high-temperature metal powders (though less common than aluminum for standard ducting, materials like Inconel or titanium alloys can be used for high-temp sections via AM) can be employed, although for many duct sections, high-strength aluminum alloys like Scalmalloy® offer sufficient performance with significant weight savings.
- Complex Routing: Similar to ECS, bleed air ducts must navigate congested engine nacelles and pylons. AM allows for highly customized routing solutions manufactured as single pieces.
- Duvar Kalınlığı Optimizasyonu: AM permits precise control over wall thickness, allowing engineers to minimize weight while ensuring structural integrity under high pressure.
- Avionics and Electronics Cooling:
- Optimized Cooling Channels: Efficient cooling is vital for the reliability of modern avionics. Metal AM enables the creation of ducts and cold plates with highly complex internal cooling channels, conformal cooling passages, and integrated heat sink features designed using computational fluid dynamics (CFD) for maximum thermal performance.
- Miniaturization: AM can produce small, intricate ducting needed for cooling densely packed electronic components where traditional manufacturing methods would struggle.
- Malzeme Seçimi: Aluminum alloys like AlSi10Mg offer excellent thermal conductivity, making them ideal for cooling applications.
- Fuel and Hydraulic Lines:
- Integrated Systems: While less common than air ducts due to stringent certification requirements, there is growing interest in using AM for sections of fuel or hydraulic lines, potentially integrating them with structural components or creating complex manifolds to reduce connections and leak points. Materials with specific chemical compatibility would be selected.
- Space Applications:
- Extreme Lightweighting: In spacecraft, launch vehicles, and satellites, weight savings are paramount. Metal AM enables aggressive lightweighting of ducting and fluid conveyance systems through topology optimization and the use of advanced alloys.
- Hızlı Prototipleme: The ability to quickly iterate designs is crucial in the fast-evolving space sector. AM facilitates rapid production of prototype ducts for fit checks and functional testing.
Benefits Across Aircraft Types:
- Commercial Aviation: Focus on weight reduction for fuel efficiency, improved ECS performance for passenger comfort, and reduced MRO costs through higher reliability components.
- Defense Aviation: Emphasis on performance, rapid deployment of new designs or modifications, lightweighting for enhanced maneuverability and payload, and supply chain resilience for spare parts.
- Uzay Araştırmaları: Extreme lightweighting, high reliability, ability to create highly customized components for unique mission requirements.
The ability of metal AM to integrate features directly into the duct is a significant advantage for custom aircraft ducting suppliers. Instead of manufacturing a simple tube and then attaching flanges, brackets, or sensor ports in secondary operations (adding labor, weight, and potential failure points), AM allows these features to be grown as part of the duct itself. This inherent integration capability streamlines the supply chain, reduces assembly complexity on the aircraft, and ultimately leads to more reliable and efficient aerospace systems. As aerospace ducting manufacturers embrace this technology, engineers gain unprecedented freedom to design ducting that is perfectly tailored to its function and environment.
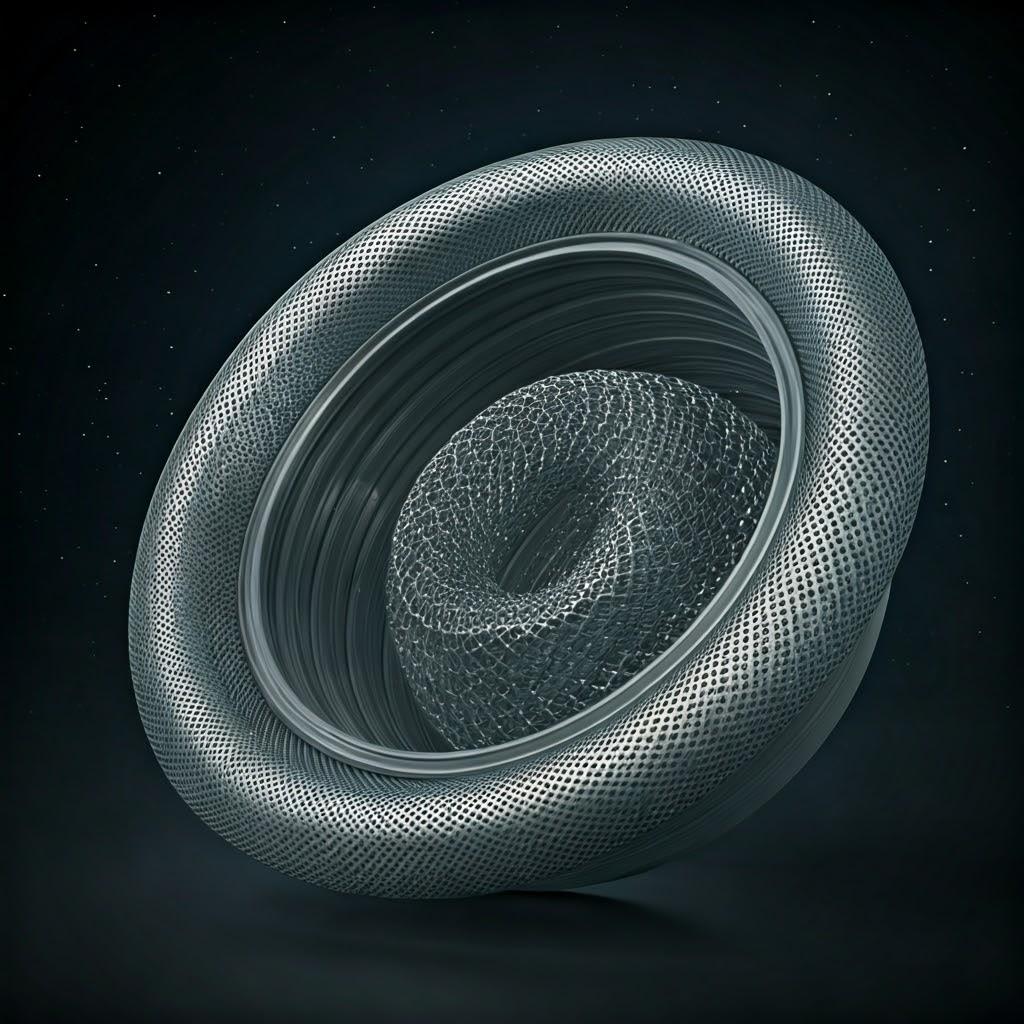
Why Metal 3D Printing for Aerospace Ducts? Unlocking Performance and Efficiency
The adoption of metal additive manufacturing for aerospace ducting isn’t just a novel manufacturing technique; it represents a fundamental shift offering tangible benefits that directly address the core challenges faced by aerospace engineers and procurement managers. Compared to traditional methods like sheet metal forming, casting, hydroforming, welding, and machining, metal AM benefits aerospace applications significantly, particularly in the realm of fluid and air conveyance systems. The advantages stem from the layer-by-layer fabrication process, which liberates design from many conventional manufacturing constraints.
Let’s explore the key reasons why aerospace companies are increasingly choosing metal 3D printing for duct production:
- Unmatched Design Freedom & Complexity:
- Meydan okumak: Traditional methods struggle with highly complex geometries, organic shapes, internal features, and varying wall thicknesses without resorting to multi-part assemblies.
- AM Solution: Metal AM excels at producing intricate shapes directly from CAD data. This allows engineers to design ducts that precisely follow complex paths within the aircraft structure, optimize internal flow dynamics (e.g., smooth bends, integrated turning vanes), and vary wall thicknesses locally for optimal strength-to-weight ratios. Complex junctions (Y, T, multi-port manifolds) can be printed as a single, seamless component.
- Significant Part Consolidation:
- Meydan okumak: Conventional ducts are often assemblies of multiple formed or machined sections, flanges, brackets, and fasteners, held together by welding, brazing, or mechanical means. Each joint represents potential weight, added labor cost, an inspection point, and a possible leak or failure point.
- AM Solution: Perhaps the most compelling advantage for ducting is part consolidation aerospace. Metal AM can combine numerous individual components into a single, monolithic printed part. A complex duct assembly that might have previously consisted of 5, 10, or even more parts can often be redesigned and printed as one piece. This dramatically reduces:
- Assembly time and labor costs.
- The number of fasteners or welds required.
- Potential leak paths, enhancing system reliability.
- Overall system weight.
- Supply chain complexity (managing fewer part numbers).
- Rapid Prototyping and Accelerated Development Cycles:
- Meydan okumak: Creating tooling for traditional methods (e.g., hydroforming dies) is time-consuming and expensive, making design iterations slow and costly.
- AM Solution: Metal AM is a tool-less process. Designs can go from CAD model to physical metal prototype in a matter of days, not weeks or months. This allows engineers to quickly test form, fit, and even function, enabling faster design validation, iteration, and refinement, ultimately shortening the overall development cycle for new aircraft or system upgrades.
- Lightweighting Opportunities:
- Meydan okumak: Minimizing weight is a constant driver in aerospace design to improve fuel efficiency, increase payload, or enhance performance. Traditional manufacturing often leads to over-engineered or heavier-than-necessary components due to process limitations or the need for joining features.
- AM Solution: Metal AM enables significant lightweight aerospace ducting through several means:
- Topology Optimization: Software can optimize the duct’s geometry, removing material from low-stress areas while maintaining structural integrity, resulting in organic-looking, highly efficient structures.
- Kafes Yapılar: Internal lattice or gyroid structures can be incorporated to provide stiffness and support with minimal material usage.
- Precise Wall Thickness Control: Wall thickness can be varied precisely where needed, avoiding uniform, potentially overly thick walls.
- Malzeme Seçimi: AM allows the use of advanced lightweight, high-strength alloys like Scalmalloy® that might be difficult or impossible to form using traditional methods.
- Malzeme Verimliliği ve Azaltılmış Atık:
- Meydan okumak: Subtractive manufacturing (machining) starts with a solid block of material and removes large amounts, generating significant waste (buy-to-fly ratio). Forming processes can also result in scrap.
- AM Solution: Additive manufacturing builds parts layer by layer, using primarily only the material needed for the part itself and support structures (which can often be minimized through design). Unused powder in the build chamber can typically be recycled and reused, leading to higher material utilization rates and less waste compared to traditional subtractive methods.
- Improved Supply Chain Resilience & MRO:
- Meydan okumak: Long lead times for conventionally manufactured spare parts, especially for older aircraft or complex components, can ground an aircraft (Aircraft on Ground – AOG situations), leading to significant operational costs. Maintaining large inventories of diverse spare parts is also expensive.
- AM Solution: Metal AM enables on-demand manufacturing or distributed manufacturing closer to the point of need. Digital inventories (CAD files) can replace physical ones for certain parts. This allows for faster production of replacement ducts, potentially reducing AOG time and inventory holding costs for MRO providers.
Comparison: Additive Manufacturing vs Traditional Aerospace Ducting
Özellik | Traditional Manufacturing (Sheet Metal, Weldments, Castings) | Metal Additive Manufacturing (LPBF/EBM) | Advantage of AM |
---|---|---|---|
Tasarım Karmaşıklığı | Limited by forming/casting/joining capabilities | High geometric freedom, complex internal features possible | Enables highly optimized, integrated designs |
Part Count | Often requires multi-part assemblies | Enables significant part consolidation into single pieces | Reduced weight, assembly time, leak points, cost |
Teslim Süresi | Long (tooling, multi-step processes, assembly) | Short (tool-less, direct digital manufacturing) | Faster prototyping, quicker production |
Ağırlık | Often heavier due to joining methods, process limitations | Potential for significant lightweighting (topology opt.) | Improved fuel efficiency, payload, performance |
Kalıp Maliyeti | High initial cost for dies, molds, jigs | Hiçbir alete gerek yok | Lower cost for low-medium volumes, faster setup |
Malzeme Atıkları | Can be high (subtractive machining, forming scrap) | Generally lower (additive process, powder recycling) | More sustainable, potentially lower material cost |
Özelleştirme | Difficult and expensive for low volumes | High flexibility for customization per part | Ideal for bespoke solutions, rapid design changes |
Min. Feature Size | Limited by tooling and forming processes | High resolution, capable of fine features | Enables miniaturization, complex internal channels |
Sayfalara Aktar
While traditional methods remain viable for simpler, high-volume ducting, metal 3D printing offers compelling advantages for complex, performance-critical, or low-to-medium volume aerospace ducts. It empowers engineers to rethink component design, pushing the boundaries of what’s possible in terms of performance, weight reduction, and system integration, ultimately contributing to more advanced and efficient aircraft and spacecraft.
Recommended Materials for AM Aerospace Ducting: AlSi10Mg and Scalmalloy® Deep Dive
Selecting the right material is paramount when designing and manufacturing any aerospace component, and 3D printed ducts are no exception. The choice directly impacts weight, strength, thermal performance, durability, cost, and printability. For many aerospace ducting applications produced via metal additive manufacturing, particularly those involving ECS, avionics cooling, and low-to-medium temperature fluid conveyance, aluminum alloys are often the preferred choice due to their favorable combination of low density, good thermal conductivity, and adequate strength. Among the most commonly used and recommended metal powders for aerospace 3D printing of ducts are AlSi10Mg and the high-performance alloy Scalmalloy®.
Understanding the distinct properties and ideal use cases for each is crucial for engineers and procurement managers making material decisions. It’s also vital to partner with suppliers like Met3dp, who possess expertise in handling and processing these advanced materials, ensuring the highest quality aerospace-grade metal powders are used. Met3dp employs industry-leading gas atomization technologies to produce metallic spheres with the high sphericity and flowability essential for successful powder bed fusion processes, yielding dense, high-quality parts.
1. AlSi10Mg: The Versatile Workhorse
- Açıklama: AlSi10Mg is a widely used aluminum alloy in casting, and its characteristics translate well to Laser Powder Bed Fusion (LPBF). It contains silicon (Si) for improved fluidity and castability/printability and magnesium (Mg) for strengthening through heat treatment.
- Anahtar Özellikler:
- Hafif: Density of approximately 2.67g/cm3.
- İyi Basılabilirlik: Exhibits good behavior during the LPBF process, allowing for relatively fast build speeds and the creation of complex geometries.
- Mükemmel Termal İletkenlik: Suitable for applications requiring heat dissipation, such as electronics cooling ducts or heat exchangers.
- İyi Korozyon Direnci: Performs well in typical atmospheric conditions.
- Orta Güç: Offers good strength and hardness, especially after appropriate heat treatment (e.g., T6 stress relief and aging), suitable for many ducting pressure and structural load requirements.
- Uygun Maliyetli: Generally more economical than higher-performance alloys like Scalmalloy®.
- Typical Aerospace Ducting Applications: ECS ducting, avionics cooling cold plates and ducts, low-pressure fluid lines, brackets and structural supports integrated with ducts, prototypes requiring representative geometry and material type.
- Düşünceler: While strong, it doesn’t match the high strength or fatigue performance of Scalmalloy®, potentially limiting its use in highly stressed or fatigue-critical applications. Its properties can degrade at moderately elevated temperatures (above ~150-200°C).
2. Scalmalloy®: High-Performance Lightweighting Champion
- Açıklama: Scalmalloy® is a patented high-performance aluminum-magnesium-scandium (Al-Mg-Sc) alloy specifically developed for additive manufacturing by APWorks (an Airbus subsidiary). The addition of scandium and zirconium creates strengthening precipitates, resulting in properties superior to traditional aerospace aluminum alloys.
- Anahtar Özellikler:
- Olağanüstü Güç-Ağırlık Oranı: Offers specific strength comparable to high-strength aluminum alloys like 7075, but with the processability advantages of AM. Significantly stronger than AlSi10Mg, especially in terms of yield strength and ultimate tensile strength after heat treatment.
- Excellent Ductility and Fatigue Strength: Exhibits good elongation and superior resistance to fatigue crack initiation and propagation, crucial for components subjected to cyclic loading and vibration common in aerospace environments.
- İyi Korozyon Direnci: Comparable or better than conventional high-strength aluminum alloys.
- Good Weldability (Post-Build): Can be welded if necessary for assembly or repair, although the goal of AM is often consolidation.
- Retains Strength at Moderate Temperatures: Performs better than AlSi10Mg at slightly elevated temperatures.
- Typical Aerospace Ducting Applications: Highly loaded structural ducts, fatigue-critical components, ducts requiring maximum weight savings without compromising strength, components operating in demanding vibration environments, bleed air system components (within temperature limits), replacements for traditionally machined high-strength aluminum parts.
- Düşünceler: Scalmalloy® powder is significantly more expensive than AlSi10Mg due to the cost of scandium and licensing. It may require specific heat treatment cycles to achieve its optimal properties, adding to processing time and cost. Print parameters may need careful optimization.
Comparison Table: AlSi10Mg vs. Scalmalloy® for AM Aerospace Ducting
Mülkiyet | AlSi10Mg (Typical Heat Treated – T6) | Scalmalloy® (Typical Heat Treated) | Significance for Aerospace Ducts |
---|---|---|---|
Yoğunluk | ~2.67g/cm3 | ~2.66g/cm3 | Both are lightweight; minimal difference in density. |
Yield Strength (YS) | ~230-280 MPa | ~450-500 MPa | Scalmalloy® is much stronger, allowing thinner walls/lighter parts. |
Nihai Çekme Dayanımı (UTS) | ~330-400 MPa | ~500-540 MPa | Scalmalloy® offers higher ultimate strength. |
Kopma Uzaması | ~6-10% | ~10-15% | Scalmalloy® generally offers better ductility and toughness. |
Yorulma Dayanımı | Orta düzeyde | High / Excellent | Scalmalloy® is superior for parts under vibration/cyclic load. |
Termal İletkenlik | ~130-150 W/(m·K) | ~110-130 W/(m·K) | AlSi10Mg is slightly better for pure heat dissipation needs. |
Maksimum Servis Sıcaklığı | ~150-200 °C | ~200-250 °C | Scalmalloy® retains strength better at slightly higher temps. |
Yazdırılabilirlik | Mükemmel | Good (requires optimized parameters) | Both are well-suited for LPBF; AlSi10Mg might be easier. |
Göreceli Maliyet | Daha düşük | Daha yüksek | Scalmalloy® cost justified by performance needs/weight savings. |
Primary Advantage | Versatility, Cost, Thermal Cond. | High Strength, Fatigue Resistance | Match material to specific application demands. |
Sayfalara Aktar
Importance of Powder Quality and Supplier Expertise:
Regardless of the alloy chosen, the quality of the raw material – the metal tozu – is critical for achieving the desired mechanical properties and defect-free parts in aerospace applications. This includes:
- Küresellik: Smooth, spherical powder particles ensure good flowability in the AM machine’s recoating system and uniform packing density in the powder bed, contributing to consistent melting and part density.
- Parçacık Boyutu Dağılımı (PSD): A controlled PSD is crucial for achieving high packing density and predictable melting behavior.
- Purity and Low Oxygen Content: Contaminants and excessive oxygen can lead to porosity and embrittlement, compromising mechanical properties.
- Batch-to-Batch Consistency: Ensuring consistent powder characteristics from one batch to the next is vital for repeatable part quality in production scenarios.
Companies like Met3dp, with advanced powder production facilities utilizing gas atomization and PREP technologies, and decades of collective expertise in metal additive manufacturing, play a vital role. They not only supply high-performance aerospace materials but also possess the process knowledge to optimize printing parameters for alloys like AlSi10Mg and Scalmalloy®, ensuring that the resulting custom aerospace ducts meet the stringent requirements of the industry. Partnering with a knowledgeable supplier guarantees access to high-quality powders and the expertise needed to successfully implement metal AM for these critical components. Sources and related content
Design for Additive Manufacturing (DfAM) Principles for Optimized Aerospace Ducting
Simply replicating a duct design intended for traditional manufacturing using metal additive manufacturing rarely unlocks the full potential of the technology. To truly leverage the benefits of AM – lightweighting, part consolidation, improved performance, and reduced lead times – engineers must embrace Katmanlı Üretim Tasarımı (DfAM) principles. DfAM involves rethinking the design process from the ground up, considering the unique capabilities and constraints of the chosen AM process, such as Laser Powder Bed Fusion (LPBF) or Electron Beam Melting (EBM), which are among the key baskı yöntemleri utilized for high-resolution metal parts. Applying DfAM to aerospace ducting allows for the creation of components that are not only manufacturable but also highly optimized for their specific function and operating environment.
Here are crucial DfAM principles for designing superior metal AM aerospace ducting:
- Optimize for Flow Efficiency:
- Goal: Minimize pressure drops, turbulence, and flow separation within the duct to enhance the efficiency of the system it serves (e.g., ECS, cooling).
- DfAM Techniques:
- Smooth Bends: Replace sharp elbows with generous, smooth curves enabled by AM’s geometric freedom.
- Optimized Cross-Sections: Vary the duct’s cross-sectional shape and area along its length to maintain optimal flow velocities and minimize pressure losses, guided by Computational Fluid Dynamics (CFD) analysis.
- Integrated Guide Vanes: Print internal guide vanes directly into complex junctions (T-junctions, Y-junctions, tight bends) to direct airflow smoothly and reduce turbulence, something extremely difficult or impossible with traditional methods.
- Surface Finish Considerations: While AM surfaces have inherent roughness, design choices can influence the final internal finish. Minimize features that could trap powder or hinder post-processing steps aimed at smoothing internal surfaces if required.
- Minimize Support Structures:
- Goal: Reduce the amount of support material needed during the printing process. Supports consume extra material, increase print time, require removal in post-processing (which can be difficult, costly, and risk damaging the part), and can negatively impact surface finish where they attach.
- DfAM Techniques:
- Yapı Oryantasyonu: Carefully select the part’s orientation on the build plate. Orienting features like overhangs and internal channels to be self-supporting (typically angles greater than 45° relative to the build plate) drastically reduces support needs.
- Self-Supporting Geometries: Design overhangs and bridges using angles known to be self-supporting for the specific material and process parameters (often >45°). Use chamfers or fillets instead of sharp horizontal overhangs.
- Internal Channel Design: Design internal channels with diamond, teardrop, or oval cross-sections instead of purely horizontal circular or square tops to promote self-support.
- Sacrificial Features: Incorporate features designed to be easily machined away later, which might provide temporary support during printing but are simpler to remove than intricate lattice supports.
- Support Integration: Design support structures that are easier to access and remove, considering tool paths for manual or CNC removal.
- Wall Thickness Optimization and Lightweighting:
- Goal: Achieve the required structural integrity and pressure containment with the minimum amount of material, thus reducing weight and print time.
- DfAM Techniques:
- Minimum Wall Thickness: Adhere to minimum printable wall thickness guidelines for the chosen material and AM process (typically 0.4-1.0 mm for LPBF, depending on feature size and geometry) to ensure feature resolution and prevent print failures.
- Variable Wall Thickness: Use Finite Element Analysis (FEA) to identify high-stress areas and locally thicken walls only where necessary, while thinning walls in low-stress regions. AM allows for smooth transitions between different thicknesses.
- Topology Optimization: Employ specialized software to algorithmically remove material from non-critical areas based on load cases and performance constraints. This often results in organic, bone-like structures that are highly efficient but impossible to manufacture traditionally. This is a key technique for achieving maximum lightweight aerospace ducting.
- Kafes Yapılar: Integrate internal lattice or gyroid structures within thicker sections or walls to provide structural support and stiffness with significantly reduced mass and material consumption compared to solid sections.
- Integrate Functional Features:
- Goal: Leverage AM’s ability to consolidate parts by integrating features directly into the duct design, reducing assembly complexity, weight, and potential leak points.
- DfAM Techniques:
- Built-in Flanges and Mounts: Design flanges, mounting brackets, bosses, and attachment points as integral parts of the duct geometry. Ensure these features are designed with DfAM principles in mind (e.g., self-supporting angles, appropriate thickness).
- Sensor Integration: Design integrated ports or housings for sensors (temperature, pressure, flow) directly within the duct wall.
- Consolidated Manifolds: Combine multiple duct paths or connections into a single, complex manifold component, eliminating numerous joints and fasteners.
- Texturing and Labeling: Add surface textures for grip or insulation, or print part numbers, logos, and orientation markers directly onto the component.
- Consider Post-Processing Requirements:
- Goal: Design the part in a way that facilitates necessary post-processing steps like support removal, heat treatment, surface finishing, and inspection.
- DfAM Techniques:
- Access for Support Removal: Ensure internal channels and complex features have access points for support removal tools or flushing processes. Avoid designing features where supports would be impossible to remove.
- Machining Allowances: If specific surfaces require high precision or smooth finishes (e.g., sealing faces on flanges), add extra stock material (machining allowance) in the design that can be precisely CNC machined later.
- Isıl İşlem Hususları: Design parts to minimize distortion during heat treatment cycles (e.g., uniform wall thicknesses where possible, avoiding large mass concentrations).
- Inspection Access: Ensure critical internal features are accessible for NDT methods like CT scanning or borescopic inspection if required.
Applying these metal AM design guidelines requires a collaborative approach between design engineers and AM manufacturing experts. Service providers like Met3dp, with deep expertise in additive manufacturing processes and materials, can offer invaluable DfAM support, helping customers optimize their aerospace duct designs to fully exploit the transformative potential of AM technology, leading to superior performance, reduced weight, and streamlined production for procurement teams sourcing these critical components.
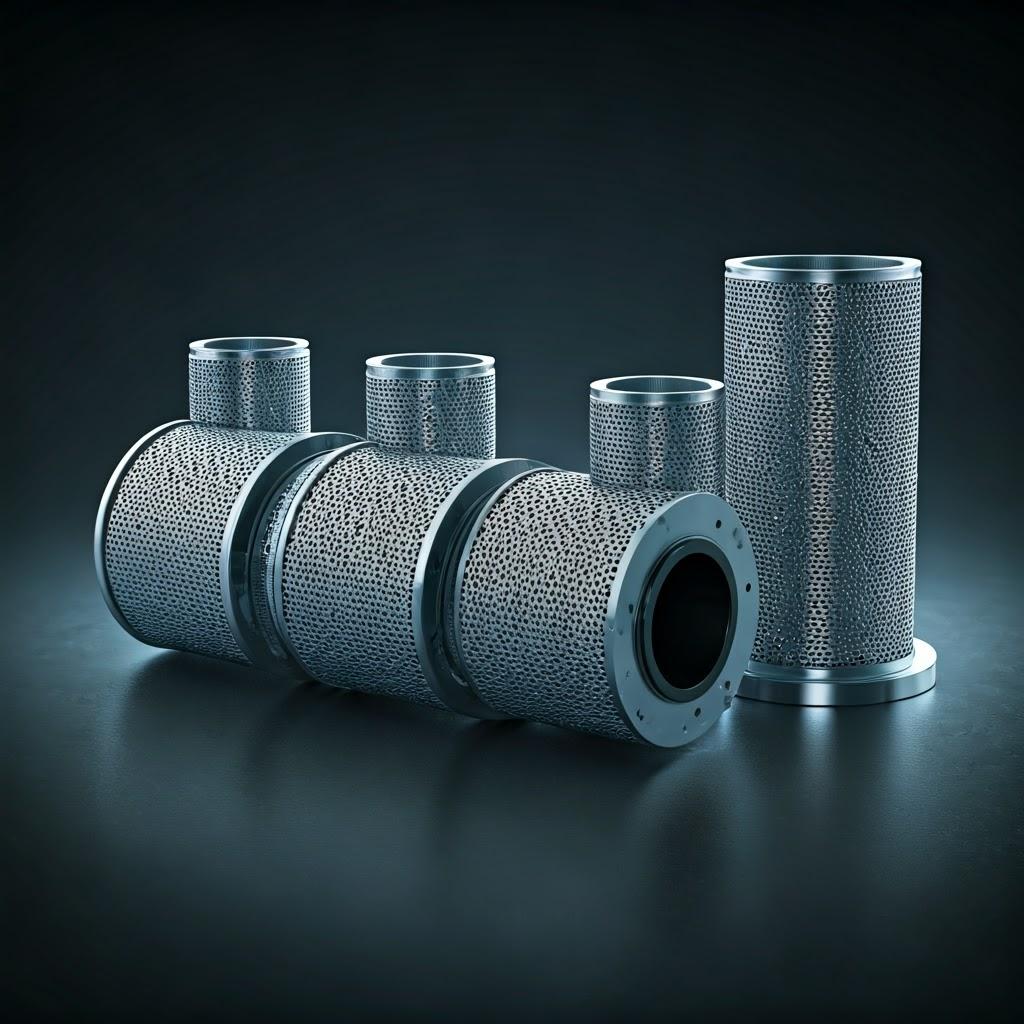
Achievable Tolerance, Surface Finish, and Dimensional Accuracy in Metal AM Ducts
Engineers and procurement managers specifying metal AM for aerospace ducting need realistic expectations regarding the achievable precision. While AM offers incredible geometric freedom, it differs significantly from subtractive machining in terms of typical tolerances and as-built surface finish. Understanding these aspects is crucial for design, cost estimation, and determining necessary post-processing steps. The final dimensional accuracy additive manufacturing delivers depends on the AM process (LPBF generally offers higher accuracy than EBM), machine calibration, material properties, part geometry, build orientation, and post-processing.
Tolerances:
- As-Built Tolerances: For Laser Powder Bed Fusion (LPBF), the most common process for aluminum alloy ducts (AlSi10Mg, Scalmalloy®), typical achievable tolerances are often in the range of:
- ±0.1 mm to ±0.2 mm for smaller features (e.g., up to 50-100 mm).
- ±0.1% to ±0.2% of the nominal dimension for larger features.
- Factors Influencing Tolerances:
- Machine Calibration: Regular and precise calibration of the laser scanner system, optics, and build platform movement is critical.
- Thermal Effects: Residual stresses built up during the layer-wise heating and cooling cycles can cause minor warping or distortion, especially in large or complex parts. DfAM and appropriate build strategies help mitigate this.
- Parça Geometrisi ve Boyutu: Larger parts and those with significant overhangs or thin walls may exhibit greater deviation.
- Destek Yapıları: The location and density of support structures can influence the dimensional accuracy of the surfaces they touch.
- Malzeme Özellikleri: Different alloys have varying shrinkage rates and thermal conductivity, affecting final dimensions.
- Achieving Tighter Tolerances: For critical interfaces, mounting points, sealing surfaces, or features requiring precision fits, the as-built tolerances may not be sufficient. In these cases, post-processing machining (CNC milling, turning, grinding) is employed. By designing the part with appropriate machining allowances (extra material, typically 0.5-2.0 mm), tolerances comparable to traditional machining (down to ±0.01 mm or even tighter) can be achieved on specific features.
Yüzey İşlemi:
- As-Built Surface Roughness (Ra): Metal AM parts inherently have a textured surface finish due to the layer-wise nature of the process and the partially melted powder particles adhering to the surface. Typical as-built surface finish metal AM (LPBF) values (Ra – arithmetic average roughness) are often in the range of:
- Top Surfaces: Relatively smooth, Ra 5-15 µm.
- Vertical Walls: Moderate roughness, Ra 10-20 µm.
- Up-facing/Down-facing Surfaces (supported): Rougher, Ra 15-30 µm or more, influenced heavily by support structures and powder adhesion.
- Factors Influencing Surface Finish:
- Katman Kalınlığı: Thinner layers generally result in smoother surfaces but increase build time.
- Powder Particle Size: Finer powders can lead to smoother finishes but may pose challenges for flowability.
- Laser Parameters: Beam spot size, scan speed, and energy density affect melt pool dynamics and surface texture.
- Yapı Oryantasyonu: Surfaces built at angles closer to horizontal (up-facing or down-facing) tend to be rougher than vertical walls due to the “stair-stepping” effect and support interactions.
- Yüzey İşleminin İyileştirilmesi: For applications requiring smoother surfaces (e.g., improved fluid dynamics, sealing, aesthetics, or fatigue performance), various post-processing techniques are used:
- Media Blasting (Bead Blasting, Sand Blasting): Provides a uniform matte finish, removes loose powder, and can slightly improve Ra (e.g., down to Ra 5-10 µm).
- Tumbling/Vibratory Finishing: Uses abrasive media in a tumbling barrel or vibratory bowl to smooth surfaces and deburr edges (can achieve Ra 1-5 µm).
- Chemical Polishing/Etching: Can achieve very smooth finishes but requires careful process control and may affect dimensional accuracy.
- CNC Machining/Polishing: Offers the highest level of smoothness (Ra < 1 µm or even mirror finishes) on specific surfaces but adds cost and lead time.
Dimensional Accuracy and Inspection:
- Ensuring Consistency: Achieving consistent dimensional accuracy across production runs requires robust process control, regular machine maintenance and calibration, strict powder quality management, and standardized post-processing procedures.
- Metrology and Inspection: Verifying the dimensional accuracy and integrity of aerospace parts inspection for AM ducts is critical. Common techniques include:
- Coordinate Measuring Machines (CMM): Provide high-accuracy measurements of external features and specific points.
- 3D Laser Scanning/Structured Light Scanning: Capture the full geometry of the part for comparison against the original CAD model, identifying deviations across the entire surface. Useful for complex shapes.
- Computed Tomography (CT) Scanning: Essential for non-destructively inspecting internal channels and features, detecting internal defects (porosity), and verifying internal dimensions and wall thicknesses. This is particularly crucial for complex, consolidated ducting where internal access is limited.
- Borescopes: Used for visual inspection of internal duct surfaces.
Aerospace suppliers specializing in metal AM, like Met3dp, understand the nuances of tolerance and surface finish control. They work closely with customers to define acceptable limits based on application requirements, optimize designs using DfAM, implement rigorous process controls, and leverage appropriate post-processing and inspection techniques to deliver flight-ready components that meet the demanding LPBF aerospace quality standards. Procurement managers should ensure potential suppliers have robust quality management systems (QMS) and the necessary metrology equipment to validate part conformity.
Essential Post-Processing Steps for Flight-Ready Metal AM Ducting
Producing a custom aerospace duct doesn’t end when the 3D printer stops. The “green” part, fresh off the build plate, requires several crucial post-processing metal AM aerospace steps to transform it into a functional, reliable, flight-ready component. These steps are essential to relieve internal stresses, remove support structures, achieve the required dimensional accuracy and surface finish, ensure material properties meet specifications, and verify part integrity. The specific sequence and intensity of these steps depend on the material (AlSi10Mg vs. Scalmalloy®), part complexity, design specifications, and aerospace quality requirements.
Key post-processing stages typically include:
- Stress Relief Heat Treatment:
- Why: The rapid heating and cooling cycles inherent in LPBF create significant residual stresses within the metal part. These stresses can cause distortion (warping) after the part is removed from the build plate or during subsequent machining, and can negatively impact mechanical properties, particularly fatigue life. Stress relief is arguably the most critical initial post-processing step for LPBF aluminum parts.
- How: Parts, often while still attached to the build plate, are heated in a furnace to a specific temperature below the alloy’s aging or solutionizing temperature (e.g., typically 250-350°C for AlSi10Mg and potentially similar or slightly different for Scalmalloy®, following specific guidelines), held for a defined period (e.g., 1-2 hours), and then slowly cooled. This allows the internal stresses to relax without significantly altering the microstructure. Precise control of temperature and ramp rates is vital.
- Importance: Skipping or improperly performing stress relief can lead to dimensional instability and premature component failure.
- Yapı Plakasından Parça Çıkarma:
- Why: The part is metallurgically bonded to the metal build plate during printing.
- How: Typically done after stress relief. Common methods include:
- Tel EDM (Elektrik Deşarjlı İşleme): Offers a precise, clean cut with minimal mechanical stress on the part. Often preferred for delicate or complex components.
- Şerit Testere: Faster and more economical for simpler geometries or less critical parts, but introduces more mechanical force.
- CNC İşleme: Can be used to precisely cut the part free, sometimes integrated with initial rough machining steps.
- Destek Yapısının Kaldırılması:
- Why: Supports are necessary during the build but are non-functional and must be removed. Support removal metal AM can be one of the most labor-intensive and challenging post-processing steps, especially for ducts with complex internal channels.
- How: Methods depend on support location, density, and geometry:
- Manuel Kaldırma: Breaking or cutting easily accessible supports using hand tools.
- CNC İşleme: Milling or grinding away support structures, particularly effective for external supports or accessible internal features.
- Wire EDM/Electrochemical Machining (ECM): Sometimes used for intricate or hard-to-reach internal supports, though less common for standard ducting.
- Abrasive Flow Machining (AFM) or Chemical Etching: Can potentially smooth internal channels and help remove internal support remnants, but requires careful control.
- DfAM Impact: Designing for minimal, easily accessible supports (as discussed in the DfAM section) significantly simplifies this stage.
- Yüzey İşlemi:
- Why: To remove loose powder, improve surface smoothness (reduce Ra), achieve a uniform appearance, prepare surfaces for coating, or meet specific aerodynamic or fluid dynamic requirements.
- How: As detailed previously:
- Media Blasting (Bead, Grit): Standard step for cleaning and achieving a uniform matte finish.
- Tumbling/Vibratory Finishing: For general smoothing and deburring.
- CNC İşleme: For achieving high precision and smooth finishes on critical interfaces (flanges, sealing surfaces).
- Polishing (Manual or Automated): For achieving very low Ra values where required.
- Chemical Treatments: For specific smoothing or passivation needs.
- Further Heat Treatments (If Required):
- Why: Beyond stress relief, some alloys require additional heat treatments to achieve their final desired mechanical properties (strength, hardness, ductility).
- How:
- Aging/Precipitation Hardening: Essential for alloys like Scalmalloy® and optional for AlSi10Mg (T6 condition) to achieve maximum strength. Involves heating to a specific temperature (e.g., lower than stress relief, potentially ~150-200°C for Al alloys) for an extended period (hours) to allow strengthening precipitates to form. Exact cycles are alloy-specific.
- Solution Annealing & Aging: More complex cycles sometimes used, involving heating to a high temperature to dissolve precipitates, quenching, and then aging.
- Kontrol: Precise furnace control and adherence to material-specific heat treatment recipes are critical.
- Non-Destructive Testing (NDT) and Inspection:
- Why: To verify the internal and external integrity of the duct, ensure it’s free from critical defects (porosity, cracks), and confirm dimensional accuracy before it’s certified for flight. Aerospace NDT methods are rigorously applied.
- How:
- Visual Inspection: Basic check for external defects, surface finish issues.
- Boyutsal Muayene: Using CMM, 3D scanning (as detailed previously).
- Computed Tomography (CT) Scanning: Increasingly vital for AM aerospace parts. Provides a full 3D view of the internal structure, allowing detection of porosity, inclusions, internal geometry verification, and wall thickness measurements throughout complex duct paths.
- Pressure Testing / Leak Testing: Functionally testing the duct to ensure it can withstand operating pressures without leakage, critical for ECS, bleed air, and fluid lines.
- Fluorescent Penetrant Inspection (FPI): Used to detect surface-breaking cracks or defects.
Successfully navigating these post-processing steps requires significant expertise, specialized equipment, and robust quality control procedures. Aerospace manufacturers and metal AM service provider aerospace companies like Met3dp invest heavily in these capabilities, offering comprehensive solutions that encompass not just printing but also the critical downstream processes needed to deliver fully qualified, flight-ready custom aerospace ducts. When evaluating suppliers, procurement teams must scrutinize their post-processing capabilities and quality certifications (e.g., AS9100).
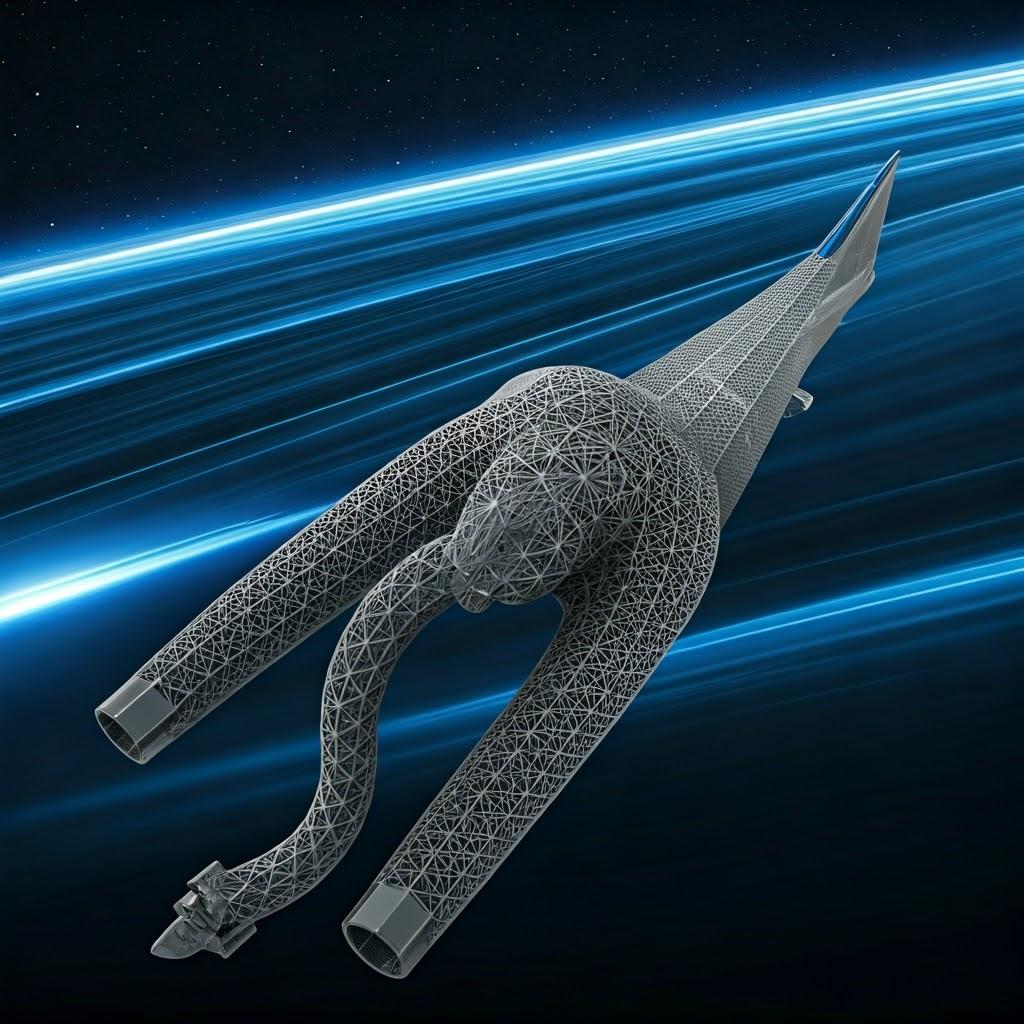
Common Challenges in Metal AM for Aerospace Ducting and Mitigation Strategies
While metal additive manufacturing offers transformative advantages for aerospace ducting, it’s not without its challenges. Recognizing these potential hurdles and implementing effective mitigation strategies is crucial for successful adoption and ensuring the production of high-quality, reliable components. Engineers, manufacturing specialists, and aerospace AM quality control teams must work together to navigate these common issues.
- Residual Stress and Distortion:
- Meydan okumak: The intense, localized heating and rapid cooling inherent in LPBF generate significant residual stresses within the printed part. These stresses can lead to warping or distortion, especially after removal from the build plate or during post-processing (e.g., machining). Distortion can compromise dimensional accuracy and potentially lead to part failure.
- Mitigation Strategies:
- DfAM: Design parts with more uniform wall thicknesses, avoid large solid masses, and incorporate features that add stiffness during the build.
- Optimized Build Orientation & Supports: Strategically orient the part on the build plate and use appropriate support structures to anchor the part effectively and manage thermal gradients.
- Optimize Edilmiş Süreç Parametreleri: Fine-tuning laser power, scan speed, and scan strategy (e.g., island scanning) can help reduce stress build-up. Expertise from providers like Met3dp in process parameter development is key.
- Zorunlu Stres Giderici: Implementing a properly controlled stress relief heat treatment cycle immediately after printing and before part removal is essential for aluminum alloys.
- Termal Simülasyon: Using simulation software during the design phase to predict stress accumulation and distortion, allowing for design or process adjustments beforehand.
- Gözeneklilik:
- Meydan okumak: Small voids or pores can form within the printed metal due to trapped gas (e.g., argon shield gas, gas dissolved in powder) or process instabilities (e.g., “keyholing” where the laser vaporizes material improperly). Porosity can significantly degrade mechanical properties, particularly fatigue strength, and act as crack initiation sites. Porosity control metal AM is critical for aerospace.
- Mitigation Strategies:
- Yüksek Kaliteli Toz: Use aerospace-grade metal powders with low gas content, controlled particle size distribution, and high sphericity. Strict powder handling protocols (e.g., controlled atmosphere storage, sieving) are vital to prevent moisture absorption and contamination. Met3dp’s focus on advanced gas atomization ensures high powder quality.
- Optimize Edilmiş Süreç Parametreleri: Careful optimization of laser power, scan speed, layer thickness, hatch spacing, and shielding gas flow is crucial to ensure stable melting and minimize pore formation.
- Sıcak İzostatik Presleme (HIP): For critical applications requiring maximum density, HIP (applying high temperature and isostatic pressure) can be used as a post-processing step to close internal voids. However, it adds significant cost and lead time and is less commonly required for typical ducting compared to highly stressed structural parts.
- NDT Inspection: Use CT scanning to detect and quantify internal porosity, ensuring it remains within acceptable limits defined by aerospace standards.
- Support Removal Difficulties:
- Meydan okumak: Removing support structures, especially from complex internal channels or intricate geometries within a duct, can be time-consuming, costly, and risk damaging the part surface. Inaccessible internal supports can be a major obstacle.
- Mitigation Strategies:
- DfAM Focus: Prioritize designing for minimal supports through optimal orientation and self-supporting geometries (>45° angles, teardrop shapes for channels).
- Accessible Support Design: Design supports to be as accessible as possible for manual or tool-based removal. Utilize support types that break away more easily where appropriate.
- Specialized Removal Techniques: Employ advanced techniques like abrasive flow machining or chemical etching for internal channels, though these require careful control and validation.
- Sacrificial Features: Design features specifically intended to be machined away later, which might simplify internal support structures.
- Process Simulation: Simulate the build process to anticipate challenging support areas and adjust the design accordingly.
- Powder Management and Traceability:
- Meydan okumak: Ensuring the quality, consistency, and traceability of metal powders is paramount in aerospace. Improper handling can lead to contamination (e.g., moisture, cross-contamination between alloys), degradation, and inconsistent part properties. Maintaining full traceability from powder batch to finished part is an aerospace requirement.
- Mitigation Strategies:
- Strict Powder Handling Protocols: Implement controlled environment storage, proper sieving procedures before reuse, batch tracking, and dedicated equipment for different materials to prevent cross-contamination.
- Toz Yaşam Döngüsü Yönetimi: Monitor powder chemistry and properties over multiple reuse cycles to ensure they remain within specification.
- Robust QMS: Maintain a rigorous Quality Management System (e.g., compliant with AS9100) that includes detailed procedures for powder management and traceability.
- Supplier Qualification: Work with reputable powder suppliers like Met3dp who demonstrate strong quality control in their powder manufacturing processes.
- Ensuring Consistency and Repeatability:
- Meydan okumak: Achieving identical properties and dimensions from part-to-part and batch-to-batch requires stringent process control over numerous variables (machine calibration, laser performance, gas flow, powder quality, thermal conditions).
- Mitigation Strategies:
- Süreç İzleme: Utilize in-situ monitoring systems (e.g., melt pool monitoring, thermal imaging) to track build consistency in real-time.
- Regular Machine Calibration & Maintenance: Adhere to strict schedules for machine calibration (laser power, scanner accuracy) and preventative maintenance.
- Standardized Procedures: Implement standardized operating procedures (SOPs) for machine setup, build execution, powder handling, and post-processing.
- Statistical Process Control (SPC): Use SPC techniques to monitor key process parameters and part characteristics to ensure stability and identify potential deviations.
- Thorough Qualification & Validation: Implement comprehensive process validation and part qualification protocols according to aerospace standards.
Addressing these metal AM challenges aerospace requires a combination of robust design practices (DfAM), advanced process knowledge, meticulous process control, rigorous quality assurance, and capable equipment. Partnering with an experienced metal AM provider equipped to handle these complexities is essential for successfully implementing additive manufacturing for demanding applications like custom aerospace ducting.
How to Select the Right Metal Additive Manufacturing Service Provider for Aerospace Ducting
Choosing the right manufacturing partner is a critical decision for aerospace engineers and procurement managers looking to leverage metal AM for custom ducting. The quality, reliability, and airworthiness of the final component depend heavily on the supplier’s capabilities, expertise, and adherence to stringent aerospace standards. Selecting a subpar provider can lead to project delays, cost overruns, non-conforming parts, and potential safety risks. Therefore, a thorough evaluation process is essential when choosing aerospace 3D printing supplier.
Here are key criteria to evaluate when selecting a metal AM service provider aerospace partner:
- Aerospace Certifications and Quality Management System (QMS):
- AS9100 Certification: This is the fundamental requirement for suppliers manufacturing flight hardware for the aerospace industry. It demonstrates a robust QMS tailored to the specific demands of aerospace quality, safety, and traceability. Do not proceed with suppliers lacking this certification for critical ducting applications.
- ISO 9001: A general QMS standard, often a prerequisite for AS9100.
- NADCAP Accreditation: While AS9100 covers the overall system, NADCAP provides specific accreditation for special processes like heat treatment, non-destructive testing (NDT), welding, etc. If the supplier performs these critical post-processing steps in-house, NADCAP accreditation for those specific processes provides additional assurance of competence.
- Documented QMS: Request evidence of their documented quality manual, procedures for process control, material handling, traceability, corrective actions, and configuration management.
- Technical Expertise and Engineering Support:
- DfAM Capabilities: Does the supplier offer Design for Additive Manufacturing support? Can their engineers collaborate with your team to optimize the duct design for printability, performance, weight reduction, and cost-effectiveness? Look for evidence of successful DfAM implementation in past projects.
- Malzeme Uzmanlığı: Assess their experience with the specific alloys required (e.g., AlSi10Mg, Scalmalloy®). Do they understand the nuances of printing and heat-treating these materials? Do they have in-house material scientists or metallurgists?
- Process Knowledge: Evaluate their understanding of the chosen AM process (likely LPBF for aluminum ducts), including parameter development, process monitoring, and troubleshooting common issues like distortion or porosity.
- Simulation Capabilities: Do they utilize simulation tools for thermal analysis, stress prediction, or topology optimization to support design and manufacturing planning?
- Machine Park, Technology, and Capacity:
- Appropriate Technology: Ensure they operate well-maintained LPBF machines suitable for the required materials and part size. Inquire about machine make, model, age, and maintenance schedules. Companies like Met3dp not only provide services but also manufacture their own advanced printing equipment (including SEBM systems, though less common for aluminum ducting), demonstrating deep technological understanding.
- Yapı Hacmi: Verify their machines have adequate build volume for the largest duct components you anticipate producing.
- Capacity and Redundancy: Assess their overall capacity to meet your required lead times for both prototypes and potential production volumes. Do they have multiple machines to offer redundancy in case of downtime?
- Environment Control: Ensure their facility maintains appropriate environmental controls (temperature, humidity, cleanliness) necessary for consistent AM production.
- Powder Handling and Material Management:
- Powder Quality Control: How do they ensure the quality of incoming metal powders? Do they perform acceptance testing?
- Handling and Storage: What are their procedures for storing, handling, sieving, blending, and tracking powders to prevent contamination (especially moisture and cross-alloy contamination) and ensure traceability? This is critical for aerospace additive manufacturing partners.
- Traceability: Can they demonstrate full material traceability from the raw powder batch to the final serialized part, including powder reuse cycles? Met3dp’s vertical integration, including manufacturing their own high-quality metal tozları, offers significant advantages in ensuring material quality and traceability.
- Post-Processing Capabilities:
- Şirket İçi ve Dış Kaynaklı: Determine which essential post-processing steps (stress relief, support removal, CNC machining, surface finishing, heat treatment, NDT) are performed in-house versus subcontracted. In-house capabilities generally offer better control over quality, lead time, and process integration.
- Equipment and Expertise: Evaluate the quality and suitability of their post-processing equipment (furnaces, CNC machines, finishing tools, NDT systems). Do they have skilled technicians operating this equipment?
- NDT Capabilities: Specifically inquire about their NDT capabilities, especially CT scanning for internal inspection of complex ducts, pressure testing, and FPI. Ensure these meet aerospace requirements.
- Track Record and Experience:
- Aerospace Experience: Look for demonstrable experience in producing components, particularly ducting or similar geometries, for aerospace customers. Ask for case studies, references (if possible within confidentiality limits), and examples of past projects.
- Problem Solving: Discuss their approach to handling challenges encountered during past projects. A capable supplier will be transparent about challenges and demonstrate effective problem-solving skills.
- Communication, Project Management, and Cost:
- Responsiveness: Evaluate their communication responsiveness and clarity during the quoting and evaluation process.
- Project Management: Understand their project management approach, including how they handle timelines, progress reporting, and customer communication.
- Cost Transparency: Ensure their quotes provide a clear breakdown of costs (material, machine time, post-processing, NDT, etc.) and that the pricing is competitive yet reflects the high quality required for aerospace. Be wary of quotes that seem too low, as they may indicate compromises on quality or process control.
Supplier Evaluation Checklist Summary:
Kriterler | Anahtar Sorular | Importance (Aerospace) |
---|---|---|
AS9100 Sertifikasyonu | Is the supplier currently AS9100 certified? Is the scope relevant? | Mandatory |
DfAM / Engineering Support | Can they help optimize the design? Do they have relevant expertise? | Çok Yüksek |
Malzeme Uzmanlığı | Do they have proven experience with AlSi10Mg / Scalmalloy®? Powder handling protocols? | Çok Yüksek |
LPBF Machine Capability | Suitable machines? Well-maintained? Adequate build volume & capacity? | Çok Yüksek |
İşlem Sonrası | In-house capabilities (Heat Treat, Machining, NDT)? NADCAP for special processes? CT Scanning available? | Çok Yüksek |
QMS & Traceability | Documented procedures? Full material & process traceability? | Mandatory |
Aerospace Track Record | Proven experience with aerospace parts? Case studies/references? | Yüksek |
Communication & Cost | Responsive? Transparent pricing? Clear project management? | Yüksek |
Sayfalara Aktar
Doğru seçimi yapmak metal AM service provider is an investment in quality and reliability. Thoroughly vetting potential partners against these criteria will significantly increase the likelihood of success in producing high-quality, flight-ready custom aerospace ducts.
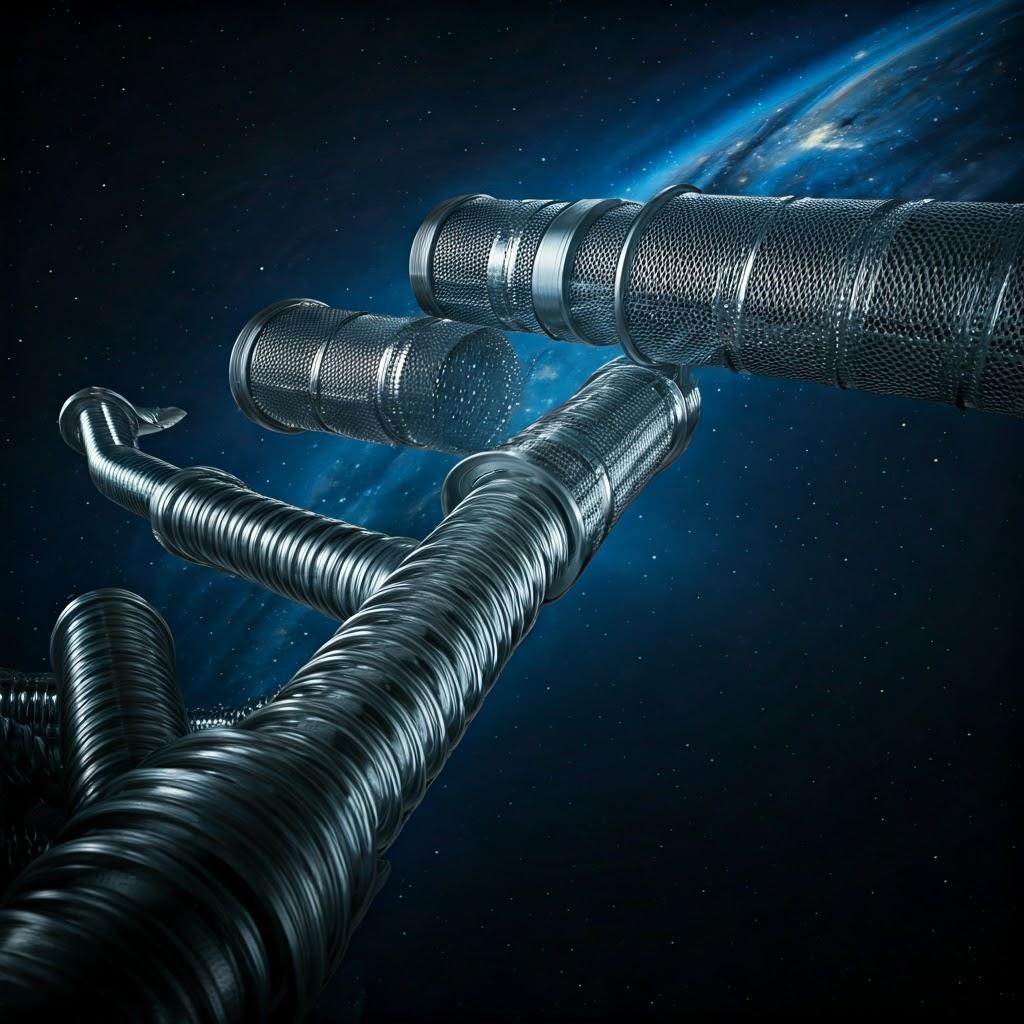
Understanding Cost Factors and Lead Times for Custom Metal AM Aerospace Ducts
While metal additive manufacturing offers significant advantages, understanding the associated costs and lead times is crucial for project planning, budgeting, and comparing AM against traditional manufacturing methods. Both metal 3D printing cost aerospace uygulamalar ve additive manufacturing lead time aerospace projects are influenced by a complex interplay of factors.
Maliyet Faktörleri:
The final price of a 3D printed aerospace duct is driven by several key elements:
- Material Choice and Consumption:
- Alloy Cost: High-performance alloys like Scalmalloy® are significantly more expensive per kilogram than standard AlSi10Mg due to raw material costs (scandium) and licensing.
- Part Volume: The physical volume of the final part dictates the amount of core material required.
- Support Structure Volume: Material used for support structures also contributes to cost. Optimized DfAM to minimize supports directly reduces material consumption.
- Powder Recycling Efficiency: The supplier’s ability to efficiently recycle unused powder impacts the overall material cost attributed to the part.
- Makine Zamanı:
- Build Height: Print time is primarily driven by the number of layers, meaning taller parts take longer, regardless of how many parts are nested on the build plate.
- Parça Karmaşıklığı: Complex geometries may require slower laser scanning speeds or more intricate support structures, increasing build time.
- Nesting Efficiency: How effectively multiple parts (or a single large part) utilize the build platform volume impacts machine time amortization per part. Suppliers skilled in build preparation can optimize nesting.
- Machine Hourly Rate: Different machines and suppliers have varying operational costs that factor into the price.
- Design and Setup Labor:
- DfAM & Optimization: If significant engineering effort is required from the supplier to optimize the design for AM, this cost may be factored in.
- Build Preparation: Time spent by technicians preparing the build file (orientation, support generation, slicing) contributes to labor costs.
- Post-Processing Intensity:
- Destek Kaldırma: Complex, hard-to-reach supports require significantly more labor and potentially specialized techniques (CNC, EDM), increasing costs.
- Isıl İşlem: Costs associated with furnace time, energy, and labor for stress relief and any required aging cycles.
- İşleme: The extent of CNC machining required for tolerances and surface finish on critical features is a major cost driver. More machined surfaces = higher cost.
- Yüzey İşlemi: Costs vary significantly depending on the method (blasting is standard; tumbling, polishing, chemical treatments add cost).
- İşçi: Manual labor for finishing, inspection, and handling throughout the post-processing workflow.
- Non-Destructive Testing (NDT) and Quality Assurance:
- CT Scanning: While invaluable for internal inspection, CT scanning is expensive due to equipment cost and specialized analysis time. Requirements for 100% CT scanning significantly impact cost.
- Other NDT: Costs associated with FPI, pressure testing, etc.
- Boyutsal Muayene: Time required for CMM or 3D scanning.
- Documentation: Generating the extensive quality documentation and traceability reports required for aerospace adds overhead.
- Miktar:
- Setup Amortization: Setup costs (engineering, build preparation) are amortized over the number of parts produced. Per-part costs decrease significantly for larger batches compared to single prototypes.
- Learning Curve: For repeat orders, efficiencies gained can sometimes lead to lower costs.
Total Cost of Ownership (TCO) Perspective: Karşılaştırma yaparken cost analysis 3D printed ducts vs. traditional methods, it’s important to consider the Total Cost of Ownership. While the per-part cost of a complex AM duct might be higher than a simple traditionally formed tube section, AM often wins when considering:
- Reduced assembly labor (due to part consolidation).
- Elimination of tooling costs (significant for low-medium volumes).
- Reduced inventory costs (fewer part numbers).
- Potential for weight savings leading to lower operational fuel costs over the aircraft’s lifetime.
- Improved reliability (fewer joints/leak points) leading to lower MRO costs.
Teslim Süreleri:
Additive manufacturing lead time aerospace projects are typically faster than traditional methods for initial prototypes or low volumes due to the elimination of tooling. However, lead times can vary significantly:
- Quoting & Design Phase: Initial consultation, DfAM optimization (if needed), and quote generation can take days to weeks.
- Build Preparation: Preparing the final build file usually takes hours to a couple of days, depending on complexity.
- Machine Queue: Lead time often depends on the supplier’s current machine backlog. High-demand periods can mean waiting days or weeks for machine availability.
- Print Time: Can range from hours for small parts to several days or even over a week for large, tall, or complex builds.
- İşlem sonrası: This is often the largest variable component of the lead time:
- Cool-down & Stress Relief: Typically 1-2 days.
- Part Removal & Support Removal: Highly variable, from hours to several days depending on complexity.
- Machining & Finishing: Can add days or weeks depending on the extent required and machine shop scheduling.
- Heat Treatment (Aging): Can add 1-2 days (including furnace time).
- NDT & Inspection: Can take several days, especially if extensive CT scanning and analysis are required.
- Nakliye: Depends on location and shipping method.
Indicative Lead Times:
- Simple Prototypes (minimal post-processing): 1-3 hafta
- Complex Prototypes (significant post-processing/NDT): 3-6 hafta
- Production Parts: Highly dependent on quantity, complexity, and required process controls. Lead times need to be established based on capacity planning and scheduling with the supplier.
Clear communication with the chosen metal AM service provider regarding specific requirements for tolerances, surface finish, NDT, and quantity is essential for obtaining accurate cost estimates and realistic lead time projections for your custom aerospace ducting project.
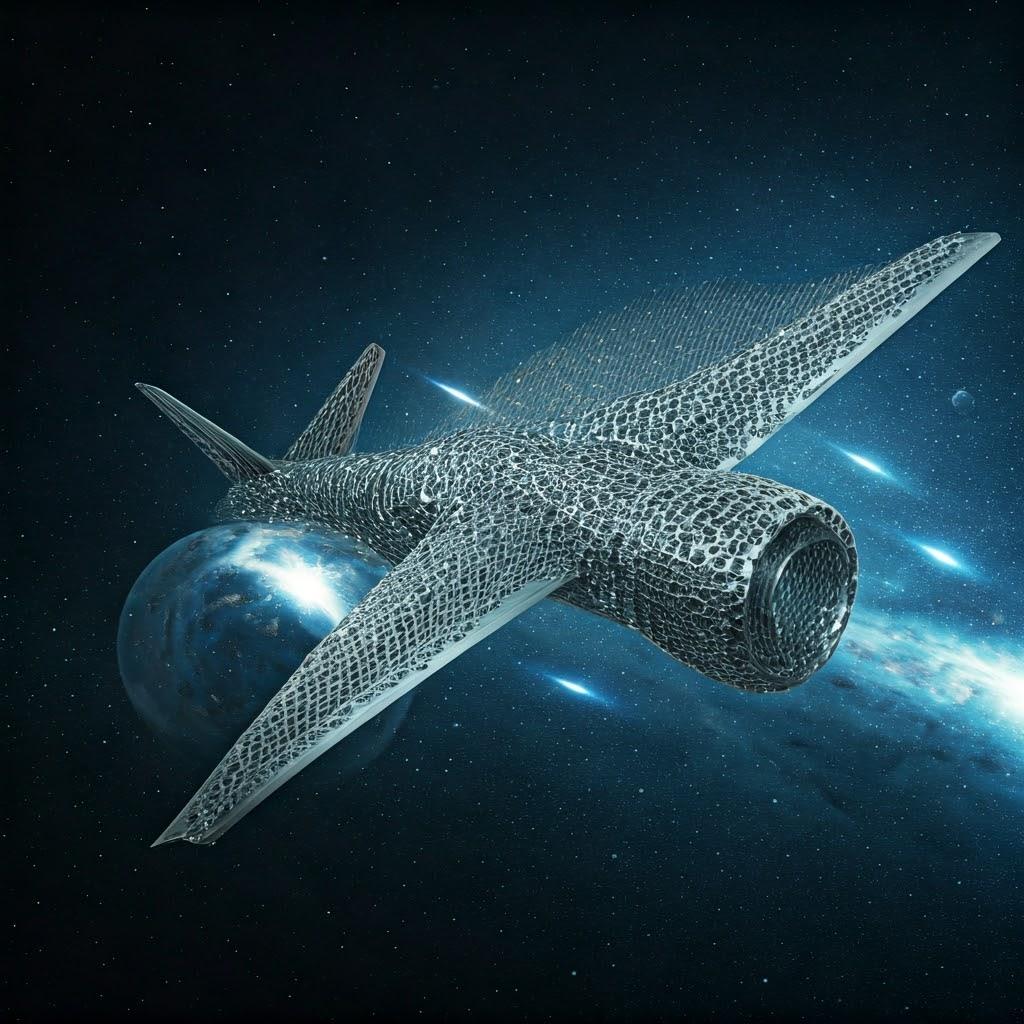
Frequently Asked Questions (FAQ) about Metal AM for Aerospace Ducting
Here are answers to some common questions engineers and procurement managers have about using metal additive manufacturing for aerospace ducting:
Q1: How does the performance (strength, fatigue life, pressure containment) of AM ducts compare to traditionally manufactured ones?
A1: When designed properly using DfAM principles and manufactured using qualified processes and materials (like AlSi10Mg or Scalmalloy®), metal AM ducts can exhibit performance that is comparable or even superior to traditionally manufactured counterparts.
- Güçlü: High-strength alloys like Scalmalloy® offer specific strength meeting or exceeding many conventional aerospace aluminum alloys. Part consolidation eliminates weak points like welds or joints.
- Fatigue Life: The layer-wise nature requires careful process control and often specific post-processing (like appropriate heat treatments and sometimes surface finishing) to achieve optimal fatigue performance, especially with alloys like Scalmalloy® which are known for excellent fatigue resistance when processed correctly. Porosity control is critical.
- Basınç Muhafazası: Well-designed and manufactured AM ducts with sufficient wall thickness and verified internal integrity (via pressure testing and CT scanning) reliably meet demanding pressure requirements. The ability to optimize flow paths can even improve aerodynamic performance compared to ducts with sharp bends made traditionally.
Q2: What are the qualification requirements for 3D printed aerospace ducts intended for flight?
A2: Qualification is a rigorous, multi-step process defined by airworthiness authorities (FAA, EASA) and specific customer requirements. It typically involves:
- Malzeme Yeterliliği: Establishing statistically robust data for the mechanical properties (tensile, fatigue, fracture toughness, etc.) of the specific alloy processed through the specific AM machine and parameter set. This often involves extensive testing according to standards like MMPDS or internal company specifications.
- Process Specification: Documenting and freezing the entire manufacturing process, including machine parameters, powder handling, build orientation strategies, support strategies, and all post-processing steps (heat treatment, finishing, NDT).
- Kısmi Yeterlilik: Demonstrating through analysis and testing (dimensional inspection, NDT like CT scanning, proof pressure testing, functional testing, potentially fatigue testing of the final part) that the specific duct design, manufactured using the qualified material and process, meets all performance and safety requirements. Traceability and configuration management are paramount.
Q3: Can existing duct designs, originally made for sheet metal or casting, be directly printed using metal AM?
A3: While technically possible to print a geometry based on an old design, it is strongly discouraged and misses the primary benefits of AM. Directly printing a design intended for traditional methods often results in:
- Excessive support structures (as the design wasn’t optimized for self-support).
- Heavier weight than necessary (lacks topology optimization or variable wall thickness).
- Potentially suboptimal performance (doesn’t leverage AM’s ability for complex flow paths).
- Higher cost (due to inefficiencies in printing and post-processing). Re-designing the duct using Katmanlı Üretim Tasarımı (DfAM) principles is highly recommended to leverage part consolidation, lightweighting, and performance optimization opportunities, leading to a superior and often more cost-effective final component.
Q4: What is the typical internal surface roughness of an additively manufactured duct, and how does it affect performance?
A4: The as-built internal surface roughness (Ra) of an LPBF duct typically ranges from 10-30 µm, depending heavily on the orientation of the surface relative to the build direction (upward/downward facing surfaces and low angles are rougher) and whether supports were attached.
- Etki: This roughness is higher than drawn tubing or machined surfaces and can slightly increase pressure drop compared to a perfectly smooth theoretical duct. However, AM’s ability to create smoother, more gradual bends often offsets this effect compared to traditional ducts with sharp, turbulence-inducing elbows.
- Improvement: If very low internal roughness is required for specific high-performance aerodynamic applications, post-processing techniques like abrasive flow machining (AFM) or chemical polishing can be employed, though they add cost and complexity. For many ECS and cooling applications, the as-built roughness is acceptable, especially when weighed against the design optimization benefits.
Q5: Are there limitations on the size of ducts that can be 3D printed?
A5: Yes, the primary limitation is the build volume of the metal AM machine. Common industrial LPBF machines have build volumes typically ranging from approximately 250 x 250 x 300 mm up to 400 x 400 x 400 mm, with some larger systems becoming available (e.g., 600 mm or 800 mm in X/Y).
- Large Ducts: If a duct’s overall dimensions exceed the build volume, it can be designed as multiple sections that are printed separately and then joined using traditional methods like aerospace-qualified welding or specialized joining techniques. However, this reintroduces joints, somewhat negating the part consolidation benefit.
- Design Consideration: Engineers should consider machine build volume during the DfAM phase. Sometimes, clever orientation or minor design modifications can allow a seemingly oversized duct to fit within the available build envelope.
Conclusion: Embracing Metal AM for Next-Generation Aerospace Ducting Solutions
The landscape of aerospace manufacturing is undergoing a significant transformation, and metal additive manufacturing stands at the forefront of this evolution, particularly for complex components like custom ducting. As we’ve explored, the limitations of traditional manufacturing methods – restricted geometric complexity, long lead times, high tooling costs, and challenges in lightweighting – are effectively addressed by the capabilities of metal AM technologies like Laser Powder Bed Fusion.
For engineers and procurement managers in the aerospace sector, embracing metal AM adoption aerospace strategies for ducting offers compelling advantages:
- Benzersiz Tasarım Özgürlüğü: Enabling the creation of highly optimized, complex duct geometries with integrated features, leading to improved airflow efficiency and performance.
- Significant Part Consolidation: Reducing weight, assembly time, cost, and potential leak points by combining multiple components into a single, monolithic part.
- Accelerated Development & Production: Facilitating rapid prototyping and faster transition to production through tool-less manufacturing.
- Substantial Lightweighting: Utilizing topology optimization and advanced, high-strength lightweight alloys like AlSi10Mg and Scalmalloy® to reduce aircraft weight, enhancing fuel efficiency and payload capacity.
- Enhanced Supply Chain Agility: Enabling on-demand production of spare parts and reducing reliance on complex traditional supply chains.
While challenges related to process control, post-processing, and qualification exist, they are being effectively managed through advancements in technology, the development of robust standards, and the expertise of specialized aerospace additive manufacturing partners. The selection of the right materials, adherence to rigorous DfAM principles, meticulous post-processing, and comprehensive NDT are all critical elements for success.
Bu future of aerospace manufacturing undoubtedly involves a deeper integration of additive manufacturing. For custom ducting, metal AM is not just an alternative; it’s a strategic enabler for designing and building next-generation aircraft and spacecraft that are lighter, more efficient, and more reliable. By understanding the technology’s capabilities and partnering with knowledgeable suppliers, aerospace companies can unlock significant competitive advantages.
Met3dp, with its deep expertise spanning advanced metal AM systems, high-quality powder production, and comprehensive application support, is ideally positioned to help aerospace companies navigate this transition. We encourage you to explore how metal additive manufacturing can revolutionize your approach to aerospace ducting.
Ready to explore custom metal AM solutions for your aerospace ducting needs? Contact Met3dp today to discuss your project with our additive manufacturing experts and discover how we can help you achieve your performance and efficiency goals.
Paylaş
MET3DP Technology Co, LTD, merkezi Qingdao, Çin'de bulunan lider bir katmanlı üretim çözümleri sağlayıcısıdır. Şirketimiz, endüstriyel uygulamalar için 3D baskı ekipmanları ve yüksek performanslı metal tozları konusunda uzmanlaşmıştır.
İşletmeniz için en iyi fiyatı ve özelleştirilmiş Çözümü almak için sorgulayın!
İlgili Makaleler
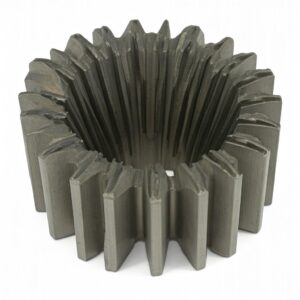
Yüksek Performanslı Nozul Kanat Segmentleri: Metal 3D Baskı ile Türbin Verimliliğinde Devrim
Daha Fazla Oku "Met3DP Hakkında
Son Güncelleme
Bizim Ürünümüz
BİZE ULAŞIN
Herhangi bir sorunuz var mı? Bize şimdi mesaj gönderin! Mesajınızı aldıktan sonra tüm ekibimizle talebinize hizmet edeceğiz.
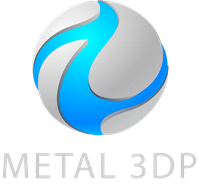
3D Baskı ve Katmanlı Üretim için Metal Tozları