Motor Housing for Electric Vehicles via 3D Printing
İçindekiler
Introduction: Revolutionizing EV Motor Housings with Metal Additive Manufacturing
The automotive industry is undergoing a seismic shift, driven by the accelerating transition towards electric vehicles (EVs). This transition isn’t just about replacing internal combustion engines with batteries and electric motors; it’s fundamentally reshaping vehicle architecture, performance expectations, and manufacturing methodologies. At the heart of an EV’s powertrain lies the electric motor, and encasing this critical component is the motor housing. Traditionally manufactured through processes like casting or machining, EV motor housings are now prime candidates for disruption through advanced manufacturing techniques, particularly metal 3D baskıolarak da bilinir. eklemeli üretim (AM).
An EV motor housing serves multiple crucial functions: it provides structural support for the motor components, protects them from environmental factors and physical impacts, aids in thermal management by dissipating heat, and contributes to noise, vibration, and harshness (NVH) damping. As EV technology advances, demanding higher power densities, improved efficiency, and reduced weight, the design and manufacturing of motor housings become increasingly complex and critical. Engineers face the challenge of creating lighter, more intricate housings with integrated features like cooling channels, mounting points, and optimized geometries – challenges that often push the limits of conventional manufacturing.
İşte burası metal katkılı üretim emerges as a transformative solution. Unlike subtractive methods (machining) or formative methods (casting), AM builds parts layer by layer directly from digital models using high-performance metal powders. This approach unlocks unprecedented design freedom, enabling the creation of complex, lightweight structures that were previously impossible or prohibitively expensive to produce. For EV motor housings, this translates to significant opportunities for:
- Hafifletme: Reducing vehicle mass is paramount for extending range and improving performance. AM allows for topology optimization, creating housings with material only where structurally necessary, significantly cutting weight compared to traditional designs.
- Enhanced Thermal Management: Intricate internal cooling channels can be directly integrated into the housing design, improving heat dissipation from the motor and battery, boosting efficiency and longevity.
- Parça Konsolidasyonu: Multiple components previously assembled together can be redesigned and printed as a single, integrated part, reducing assembly time, potential points of failure, and overall complexity.
- Hızlı Prototipleme ve Yineleme: AM enables manufacturers to quickly produce and test different housing designs, accelerating development cycles and optimizing performance much faster than traditional tooling-based methods allow.
- On-Demand Production and Customization: Digital manufacturing facilitates flexible production schedules and the ability to create customized housing variants for specific vehicle models or performance requirements without the need for expensive tooling modifications.
Companies specializing in metal 3D baskı, such as Met3dp, are at the forefront of applying this technology to demanding automotive applications. With expertise in processing advanced materials and operating state-of-the-art printing systems, providers like Met3dp offer solutions that meet the rigorous quality and performance standards of the automotive sector. The ability to produce complex elektrikli araç bileşenleri using materials like high-strength aluminum alloys or nickel superalloys opens new avenues for EV motor housing design and performance optimization. As engineers and procurement managers seek advanced manufacturing solutions to gain a competitive edge in the burgeoning EV market, understanding the potential of metal AM for components like motor housings is becoming increasingly vital. This article explores the functions, benefits, materials, design considerations, and procurement strategies associated with using metal 3D printing for this critical automotive structural part.
Core Functions and Applications of EV Motor Housings
The EV motor housing, sometimes referred to as a motor casing or enclosure, is far more than just a simple cover. It’s a multifunctional, critical component within the EV powertrain system, directly impacting vehicle performance, reliability, and safety. Understanding its core functions is essential to appreciate why optimizing its design and manufacturing process through techniques like additive manufacturing offers significant advantages.
Key Functions:
- Structural Support and Alignment:
- The housing provides a rigid framework that holds the motor’s internal components (stator, rotor, bearings, shafts) in precise alignment. Maintaining these tight tolerances is crucial for efficient power transmission, minimizing wear, and ensuring the motor’s operational lifespan.
- It serves as the primary mounting interface, securely attaching the motor assembly to the vehicle chassis or transaxle. This requires high strength and stiffness to handle static loads and dynamic forces during acceleration, braking, and cornering.
- Protection:
- Environmental: The housing shields the sensitive internal motor components from external contaminants like dust, moisture, road debris, and chemicals. This sealing is critical for preventing corrosion, short circuits, and premature failure, especially given the underbody location of many EV motors.
- Physical Impact: It offers protection against impacts from road debris or minor collisions, safeguarding the motor’s integrity.
- Termal Yönetim:
- Electric motors generate significant heat during operation, particularly under high loads. Excessive heat can degrade motor performance, reduce efficiency, and damage components like windings and magnets.
- Bu motor casing function includes acting as a heat sink. The housing material and geometry are designed to absorb heat from the stator and other components and dissipate it to the surrounding environment or a dedicated cooling system (liquid or air). Effective thermal management EV systems often rely heavily on the housing’s design, sometimes incorporating integrated cooling channels or fins.
- Noise, Vibration, and Harshness (NVH) Damping:
- Electric motors operate at high frequencies and can generate unwanted noise and vibrations. The motor housing contributes to NVH performance by containing noise, damping vibrations, and preventing resonance that could be transmitted into the vehicle cabin. The housing’s mass, stiffness, and damping characteristics are tuned during the design phase.
- Electromagnetic Compatibility (EMC):
- The housing often provides electromagnetic shielding, minimizing the emission of electromagnetic interference (EMI) generated by the motor, which could affect other electronic systems in the vehicle. It also protects the motor from external electromagnetic fields.
Typical Applications and Industries:
While the primary focus here is on passenger Electric Vehicles (EVs), the principles and functions of motor housings extend to a broader range of applications:
- Passenger EVs (BEVs, PHEVs, HEVs): The largest and fastest-growing application, requiring lightweight, efficient, and cost-effective housings.
- Commercial Electric Vehicles: Electric buses, trucks, and delivery vans often require larger, more robust housings capable of handling higher loads and continuous operation.
- Electric Motorcycles and Scooters: Smaller scale, but still demanding lightweight and thermally efficient designs.
- Motorsport: High-performance electric race cars prioritize extreme lightweighting, maximum thermal performance, and rapid design iteration, making AM an ideal fit.
- Havacılık ve uzay: Electric propulsion systems for urban air mobility (UAM) vehicles and drones require housings meeting stringent aerospace standards for weight, reliability, and material performance.
- Industrial Automation: Electric motors are ubiquitous in robotics and machinery; housings protect motors in demanding factory environments.
Given these critical functions, the design and manufacturing of EV powertrain components like motor housings are subject to rigorous engineering and validation processes. The need for strong, lightweight, thermally conductive, and complex automotive structural parts makes the motor housing a compelling application for exploring the benefits of advanced manufacturing processes like metal 3D baskı. Procurement managers sourcing electric motor protection solutions and engineers designing next-generation powertrains are increasingly evaluating AM for its potential to deliver superior performance and design flexibility compared to traditional methods.
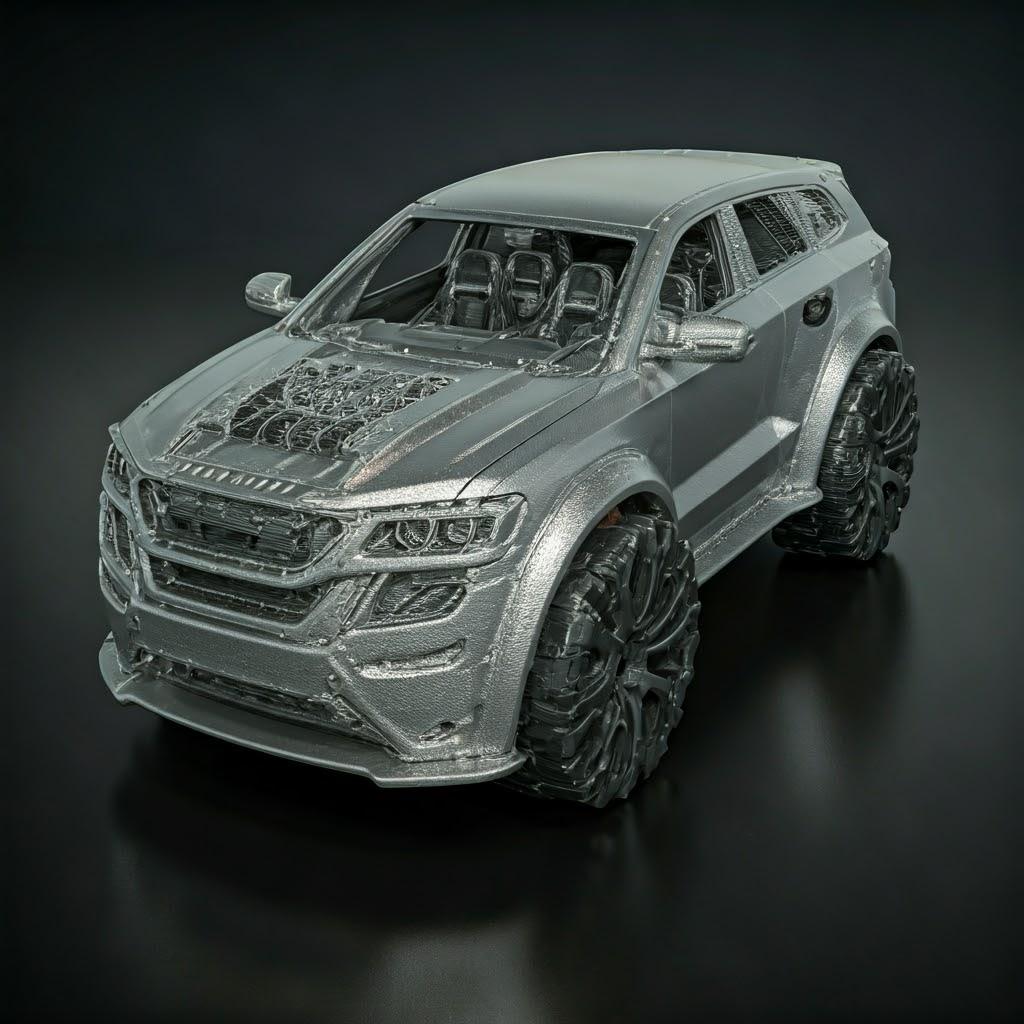
Why Metal 3D Printing Excels for EV Motor Housing Production
Traditional manufacturing methods for motor housings, primarily casting (die casting, sand casting) and CNC machining from billet, have served the industry well. However, they come with inherent limitations, particularly concerning design complexity, lead times for tooling, material waste (machining), and the ability to rapidly iterate or customize designs. Metal additive manufacturing (AM) offers a compelling alternative, presenting numerous advantages specifically beneficial for producing state-of-the-art EV motor housings.
Bu benefits of additive manufacturing in the automotive sector are increasingly recognized, moving beyond prototyping into functional part production. For EV motor housings, these advantages translate into tangible improvements in performance, efficiency, and development speed.
Key Advantages of Metal AM for EV Motor Housings:
- Unprecedented Design Freedom & Complexity:
- Topology Optimization: AM allows designers to use software tools to determine the most efficient load paths and remove material from non-critical areas. This results in organic, highly optimized shapes that maintain structural integrity while drastically reducing weight – a key goal in EV design. Topology optimization for motor housings can yield weight savings of 20-50% or more compared to cast equivalents.
- Karmaşık Geometriler: AM builds parts layer by layer, enabling the creation of intricate internal features that are impossible or extremely difficult to achieve with casting or machining. This includes:
- Integrated Cooling Channels: Conformal cooling channels that precisely follow the contours of heat-generating components (like the stator) can be directly printed into the housing walls. This significantly improves thermal transfer efficiency compared to simple external fins or separate cooling jackets.
- Internal Ribbing and Lattices: Complex internal structures can enhance stiffness and strength without adding significant mass.
- Optimized Flow Paths: Fluid paths for lubrication or cooling can be designed for maximum efficiency without the constraints of traditional drilling or casting drafts.
- Parça Konsolidasyonu: Assemblies previously requiring multiple components (e.g., housing body, mounting brackets, cooling jackets, sensor mounts) can often be redesigned and printed as a single, integrated unit. This reduces part count, eliminates assembly steps and costs, minimizes potential leak paths, and improves overall structural integrity.
- Hafifletme:
- As mentioned, topology optimization and the ability to create thin-walled structures with internal lattices allow for significant mass reduction. Lighter EV parts directly contribute to increased vehicle range, improved acceleration and handling, and reduced overall energy consumption. Aluminum alloys like AlSi10Mg, commonly used in AM, offer excellent strength-to-weight ratios ideal for this purpose.
- Rapid Prototyping and Accelerated Development:
- AM eliminates the need for expensive and time-consuming tooling (e.g., casting molds). New EV motor housing designs can be printed directly from CAD files in days rather than weeks or months.
- This capability for rapid prototyping EV components allows engineers to quickly test multiple design iterations, perform functional testing (thermal, structural, NVH), and validate performance improvements much earlier in the development cycle. This drastically shortens time-to-market for new vehicle models or powertrain upgrades.
- On-Demand Production and Customization:
- AM enables on-demand automotive parts production without the need for large inventory stockpiles. Housings can be printed as needed, reducing warehousing costs and waste.
- It facilitates customization for low-volume vehicle variants, performance upgrades, or motorsport applications without incurring high tooling costs. Different internal channel designs or mounting configurations can be easily implemented by modifying the digital file.
- Malzeme Çok Yönlülüğü:
- AM processes can work with a growing range of high-performance metals relevant to automotive needs, including lightweight aluminum alloys (like AlSi10Mg) for general use and high-strength, temperature-resistant nickel superalloys (like IN625) for demanding high-performance or high-temperature applications. Companies like Met3dp specialize in developing and qualifying yüksek performanslı metal tozları optimized for AM processes like Selective Laser Melting (SLM) or Electron Beam Melting (EBM).
- Azaltılmış Malzeme Atığı:
- Compared to subtractive manufacturing (machining from billet), where significant amounts of material are cut away and become scrap, AM is an additive process. It uses only the material needed to build the part (plus support structures), resulting in significantly less waste, making it a more sustainable manufacturing approach, especially with expensive alloys.
Comparison Table: Metal AM vs. Traditional Methods for EV Motor Housings
Özellik | Metal Katmanlı Üretim (AM) | Traditional Casting (e.g., Die Casting) | Traditional Machining (from Billet) |
---|---|---|---|
Tasarım Karmaşıklığı | Very High (complex internal channels, lattices) | Moderate (limited by mold design, draft angles) | High (but internal features difficult/costly) |
Hafifletme | Excellent (topology optimization) | Good (can optimize, but limited by process) | Moderate (limited by starting billet shape) |
Parça Konsolidasyonu | Mükemmel | Sınırlı | Sınırlı |
Kalıp Maliyeti | Hiçbiri | High (mold costs) | Low (fixtures) |
Tooling Lead Time | Hiçbiri | Long (weeks/months) | Kısa |
Prototipleme Hızı | Very Fast (days) | Slow (requires tooling) | Moderate-Fast |
Malzeme Atıkları | Düşük (katkı maddesi işlemi) | Moderate (runners, gates, flash) | Yüksek (eksiltici süreç) |
Small Volume Cost | Rekabetçi | High (due to tooling amortization) | High (machining time) |
High Volume Cost | Higher (currently, improving) | Düşük | Yüksek |
Malzeme Seçenekleri | Growing Range (Al, Ti, Ni alloys, Steels) | Established Range (Al, Mg, Zn alloys) | Wide Range (any machinable block) |
Termal Yönetim | Excellent (integrated conformal channels) | Good (fins, basic channels possible) | Moderate (limited internal access) |
Min. Wall Thickness | Can achieve very thin walls | Limited by material flow in mold | Limited by tool access and rigidity |
Sayfalara Aktar
While casting remains dominant for high-volume, cost-sensitive production runs currently, metal 3D baskı offers compelling advantages for performance-driven applications, rapid development, complex designs, and low-to-mid volume production. As the technology matures, costs decrease, and print speeds increase, AM is poised to play an increasingly significant role in the manufacturing of critical EV powertrain components like motor housings. Partnering with an experienced eklemeli üretim provider like Met3dp, which understands the nuances of complex geometry manufacturing and material science, is key to unlocking these benefits for wholesale 3D printing needs or specialized component sourcing.
Optimal Materials for 3D Printed EV Motor Housings: AlSi10Mg and IN625 Deep Dive
Selecting the right material is paramount to the success of any engineering application, and 3D printed EV motor housings are no exception. The material choice directly influences the housing’s weight, strength, thermal conductivity, corrosion resistance, manufacturability, and cost. While various metal powders can be used in additive manufacturing, two stand out as particularly relevant for this application: AlSi10Mg (an aluminum alloy) ve IN625 (a nickel superalloy).
Understanding the properties and characteristics of these materials is crucial for engineers designing the components and for procurement managers sourcing metal 3D baskı hizmetleri. Leading powder suppliers and AM service providers, such as Met3dp, leverage their materials science expertise and advanced powder production techniques (like gas atomization) to offer yüksek performanslı metal tozları optimized for AM processes, ensuring consistent quality and desirable final part properties. Met3dp’s portfolio includes a wide range of materials, including stainless steels, superalloys, and various titanium alloys, showcasing their capability beyond the two discussed here, but AlSi10Mg and IN625 serve as excellent examples for EV motor housings. Explore Met3dp’s comprehensive product offerings for a wider view of available materials.
1. AlSi10Mg (Aluminum-Silicon-Magnesium Alloy)
AlSi10Mg is one of the most widely used aluminum alloys in metal additive manufacturing, particularly Laser Powder Bed Fusion (LPBF), often referred to as Selective Laser Melting (SLM). It’s essentially an AM-equivalent of traditional casting alloys like A360.
- Key Properties & Advantages for EV Motor Housings:
- Mükemmel Güç-Ağırlık Oranı: Aluminum alloys are inherently lightweight. AlSi10Mg offers good mechanical strength and hardness, especially after appropriate heat treatment, making it ideal for reducing vehicle mass without compromising structural integrity.
- Good Thermal Conductivity: Aluminum alloys conduct heat well, which is advantageous for dissipating heat generated by the electric motor. While not as conductive as pure aluminum, AlSi10Mg’s thermal properties are generally sufficient for many EV motor cooling requirements, especially when combined with AM-enabled optimized cooling channel designs.
- İyi Korozyon Direnci: Provides adequate resistance to environmental corrosion for typical automotive underbody conditions.
- Mükemmel Basılabilirlik: AlSi10Mg is known for its relatively good processability in LPBF systems. It has a suitable melting range and generally good flowability as a powder, leading to dense, high-quality parts when processed correctly.
- Maliyet-Etkinlik: Compared to titanium or nickel alloys, aluminum powders are significantly more cost-effective, making AlSi10Mg suitable for broader adoption in passenger EVs where cost is a major driver.
- İşlem Sonrası Seçenekleri: Can be readily heat-treated (e.g., T6 aging) to significantly enhance mechanical properties (strength, hardness). It can also be machined, polished, and anodized.
- Düşünceler:
- Lower High-Temperature Strength: Compared to steels or superalloys, aluminum alloys lose strength significantly at elevated temperatures (typically above 150-200°C). This may limit its use in extremely high-performance motors or environments with poor cooling.
- Süneklik: As-printed AlSi10Mg can be relatively brittle compared to wrought aluminum alloys. Heat treatments can improve ductility but often involve a trade-off with peak strength.
- Typical Use Case: Standard passenger EVs, commercial EVs, applications where lightweighting and good thermal performance at moderate operating temperatures are primary goals.
AlSi10Mg Properties Overview (Typical LPBF, Heat Treated)
Mülkiyet | Typical Value Range | Birim | Notlar |
---|---|---|---|
Yoğunluk | ~2.67 | g/cm3 | Hafif |
Nihai Çekme Dayanımı | 400 – 480 | MPa | Highly dependent on heat treatment (T6) |
Akma Dayanımı | 250 – 350 | MPa | Highly dependent on heat treatment (T6) |
Kopma Uzaması | 3 – 10 | % | Dövülmüş alaşımlara göre daha düşük süneklik |
Sertlik | 100 – 140 | Yüksek gerilim | İyi aşınma direnci |
Termal İletkenlik | 100 – 140 | W/(m⋅K) | Good for thermal management |
Max Operating Temp. | ~150 – 200 | ∘C | Strength degrades at higher temperatures |
Sayfalara Aktar
2. IN625 (Inconel® 625 – Nickel-Chromium Superalloy)
Inconel 625 is a high-performance nickel-based superalloy renowned for its exceptional combination of high strength, excellent fatigue life, outstanding corrosion/oxidation resistance, and superb performance at extreme temperatures (from cryogenic up to ~1000°C).
- Key Properties & Advantages for EV Motor Housings:
- Olağanüstü Yüksek Sıcaklık Dayanımı: IN625 retains its mechanical properties at very high temperatures where aluminum alloys would fail. This makes it suitable for high-performance EV motors operating under extreme loads or in environments with limited cooling capacity.
- Üstün Korozyon Direnci: Offers superior resistance to a wide range of corrosive environments, including oxidation and chloride-ion stress-corrosion cracking. Ideal for harsh operating conditions or long-life requirements.
- Yüksek Mukavemet ve Tokluk: Provides significantly higher tensile and yield strength compared to AlSi10Mg, allowing for potentially thinner walls or more demanding structural loads. It also exhibits good toughness.
- Excellent Fatigue Life: Critical for components subjected to cyclic loading, as motor housings often are due to rotational forces and vibrations.
- Good Weldability/Printability: While more challenging to process than aluminum alloys due to its high melting point and thermal gradients, IN625 is generally considered one of the more processable nickel superalloys via LPBF. Achieving high density and good mechanical properties requires careful parameter optimization, an area where experienced providers like Met3dp excel.
- Düşünceler:
- Yüksek Yoğunluk: Nickel alloys are significantly denser than aluminum alloys (IN625 density is ~8.44 g/cm³ vs. ~2.67 g/cm³ for AlSi10Mg). Using IN625 will result in a much heavier housing unless designs are aggressively optimized to leverage its higher strength. This often counteracts lightweighting goals unless high temperature or strength are absolute necessities.
- Lower Thermal Conductivity: IN625 has much lower thermal conductivity (~10 W/(m·K)) compared to AlSi10Mg. This means heat dissipation aracılığıyla the housing material itself is less effective. Effective thermal management with IN625 relies more heavily on integrated cooling channel designs rather than conduction through the bulk material.
- Daha Yüksek Maliyet: Nickel superalloy powders are substantially more expensive than aluminum powders, and printing times can be longer due to the higher energy input required. This limits IN625 primarily to high-value, performance-critical applications.
- Post-Processing Complexity: Often requires specific stress-relieving heat treatments in vacuum or controlled atmospheres to optimize properties and minimize residual stress. Machining superalloys is also more challenging than machining aluminum.
- Typical Use Case: High-performance EVs (motorsport), luxury EVs with extreme performance demands, aerospace electric propulsion, applications requiring operation at very high temperatures or in highly corrosive environments.
IN625 Properties Overview (Typical LPBF, Stress Relieved/Aged)
Mülkiyet | Typical Value Range | Birim | Notlar |
---|---|---|---|
Yoğunluk | ~8.44 | g/cm3 | Significantly heavier than Aluminum |
Nihai Çekme Dayanımı | 850 – 1100 | MPa | Mükemmel güç |
Akma Dayanımı | 500 – 800 | MPa | High yield strength |
Kopma Uzaması | 20 – 40 | % | Good ductility/toughness for a superalloy |
Sertlik | 250 – 350 | Yüksek gerilim | Very hard and wear-resistant |
Termal İletkenlik | ~10 | W/(m⋅K) | Relatively low |
Max Operating Temp. | ~800 – 1000 | ∘C | Mükemmel yüksek sıcaklık performansı |
Sayfalara Aktar
Material Selection Summary:
Faktör | AlSi10Mg | IN625 | Primary Choice For: |
---|---|---|---|
Ağırlık | Excellent (Light) | Poor (Heavy) | AlSi10Mg for most passenger/commercial EVs |
Maliyet | Good (Lower) | Poor (High) | AlSi10Mg for cost-sensitive applications |
Termal İletkenlik | İyi | Zayıf | AlSi10Mg (unless complex cooling channels negate this) |
High Temp Strength | Zayıf | Mükemmel | IN625 for extreme temperature/performance applications |
Absolute Strength | İyi | Mükemmel | IN625 if maximum strength/durability is needed |
Korozyon Direnci | İyi | Mükemmel | IN625 for harsh environments |
Yazdırılabilirlik | İyi | Orta düzeyde | AlSi10Mg generally easier to process |
Sayfalara Aktar
Conclusion on Materials:
For the majority of EV motor housing applications, AlSi10Mg offers the best balance of properties – lightweight, good thermal conductivity, adequate strength, good printability, and lower cost. However, for niche applications demanding extreme temperature resistance, maximum strength, or superior corrosion resistance, IN625 provides capabilities that aluminum cannot match, albeit at the cost of increased weight and expense.
The choice depends heavily on the specific performance requirements, operating environment, and cost targets of the EV project. Collaborating with a knowledgeable automotive material selection expert or an AM service provider like Met3dp, who has experience processing both alüminyum alaşımlı 3D baskı materials and nickel superalloy additive manufacturing powders, is crucial for making the optimal selection and achieving desired results. Met3dp’s commitment to producing yüksek kaliteli metal tozları using advanced atomization techniques ensures that the starting material meets the stringent requirements for demanding applications like EV motor housings.
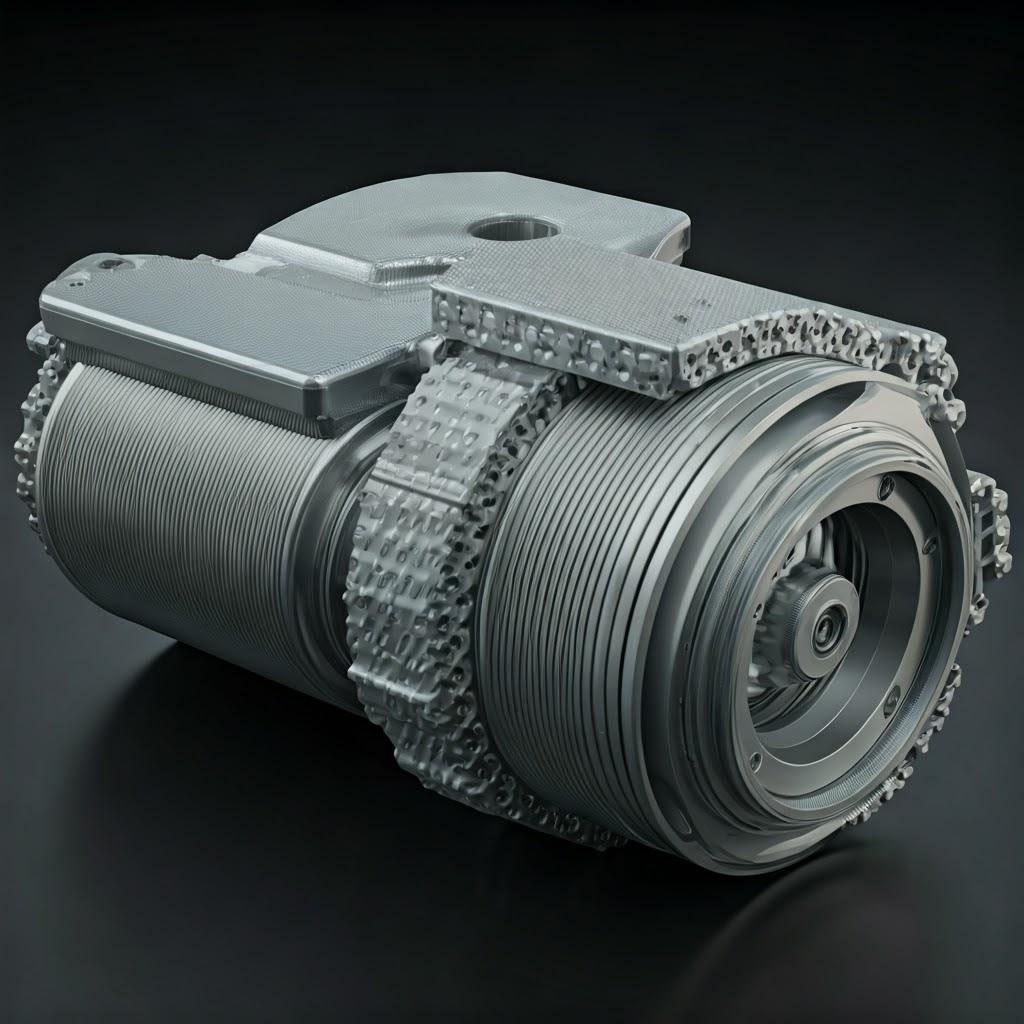
Design for Additive Manufacturing (DfAM) Principles for EV Motor Housings
Simply taking a design intended for casting or machining and sending it to a metal 3D printer rarely yields optimal results. To truly leverage the benefits of additive manufacturing—lightweighting, complex geometries, part consolidation, and enhanced thermal performance—engineers must embrace Katmanlı Üretim Tasarımı (DfAM) principles. DfAM is a design methodology that considers the capabilities and constraints of AM processes from the outset, leading to parts that are not only printable but also optimized for function and manufacturability. Applying DfAM automotive strategies is crucial when developing high-performance EV motor housings.
Key DfAM Considerations for EV Motor Housings:
- Topology Optimization and Generative Design:
- Concept: These computational tools use algorithms to determine the most efficient distribution of material within a defined design space, based on applied loads, constraints, and performance targets (e.g., minimize mass, maximize stiffness).
- Application for Housings: Start with the essential interfaces (mounting points, bearing seats, stator location) and define the maximum allowable volume. The software then generates organic, often complex-looking shapes that use material only where structurally required. This is the primary driver for achieving significant weight reduction in generative design EV components.
- Benefit: Drastic weight savings (often 20-50%+ vs. traditional designs), improved stiffness-to-weight ratio, and unique aesthetics.
- Consideration: Optimized shapes can be complex and require careful validation through simulation (FEA) and physical testing. Manufacturing these shapes is often only feasible with AM.
- Feature Integration and Part Consolidation:
- Concept: Redesign assemblies comprising multiple parts into a single, monolithic component.
- Application for Housings: Integrate features like mounting brackets, fluid connectors, sensor housings, cable routing channels, and even elements of the cooling system directly into the main motor housing structure.
- Benefit: Reduces part count, eliminates assembly labor and potential failure points (seals, fasteners), simplifies supply chain management, and can improve overall performance and reduce weight.
- Consideration: Requires a holistic view of the motor system during design. Repairability might be affected if a single integrated feature is damaged.
- Design for Thermal Management:
- Concept: Utilize AM’s ability to create complex internal geometries to enhance heat dissipation.
- Application for Housings:
- Konformal Soğutma Kanalları: Design intricate channels that precisely follow the shape of heat sources (like the stator windings). These channels can have optimized cross-sections and surface textures (e.g., internal pins/fins) to maximize heat transfer to the coolant (liquid or air).
- Entegre Isı Alıcılar: Print thin, high-surface-area fins or lattice structures directly onto the housing surface or within internal cavities to increase heat dissipation to the surroundings.
- Benefit: Significantly improved thermal performance compared to traditional housings, allowing motors to run cooler, operate at higher power densities, or have reduced reliance on external cooling systems.
- Consideration: Requires CFD (Computational Fluid Dynamics) analysis to optimize channel design for flow rate, pressure drop, and heat transfer. Ensuring channels are free of powder after printing requires careful process control and post-processing.
- Support Structure Optimization:
- Concept: Laser Powder Bed Fusion (LPBF) typically requires support structures to anchor the part to the build plate, support overhanging features (typically angles below 45 degrees from horizontal), and manage thermal stresses during printing. DfAM aims to minimize the need for these supports or make them easier to remove.
- Application for Housings:
- Oryantasyon: Choose the optimal build orientation to minimize the amount of down-facing surfaces that require support.
- Kendini Destekleyen Açılar: Design overhangs with angles greater than 45 degrees where possible.
- Incorporate Sacrificial Features: Design features specifically intended to act as supports that can be easily machined or broken away.
- Design for Access: Ensure support structures are accessible for removal tools (manual or CNC). Avoid supports in critical internal channels where removal is difficult or impossible.
- Benefit: Reduces print time (less material to print), lowers material consumption, simplifies post-processing (support removal can be time-consuming and costly), and improves surface finish on supported surfaces. Support structure reduction is a key goal for cost-effective AM.
- Consideration: Requires understanding the specific limitations of the chosen AM process and material. Some features may inherently require supports regardless of optimization.
- Wall Thickness and Feature Size:
- Concept: AM processes have limitations on minimum printable wall thickness and feature size, which vary depending on the machine, material, and parameters used.
- Application for Housings: Avoid designing walls or features that are too thin to be reliably printed or handled post-print (e.g., typically >0.4-0.5 mm for robust features in LPBF). Ensure sufficient thickness around critical areas like bearing seats or mounting points.
- Benefit: Ensures part printability, structural integrity, and reduces the risk of print failures or damage during handling/post-processing. Wall thickness considerations AM are fundamental.
- Consideration: Minimum feature sizes also apply to gaps and channels – ensure cooling channels are large enough to be reliably printed and cleared of powder.
- Designing for Post-Processing:
- Concept: Consider the requirements for downstream processes like heat treatment, support removal, machining, and surface finishing during the initial design phase.
- Application for Housings:
- Machining Allowances: Add extra material (machining stock) to surfaces requiring high precision or specific finishes (e.g., bearing bores, mating flanges, sealing surfaces).
- Access for Tools: Ensure surfaces requiring machining or finishing are accessible to tools.
- Fixturing Points: Design reference features or datums that can be used for locating and clamping the part during post-processing steps like CNC machining.
- Benefit: Streamlines the entire production workflow, reduces post-processing costs and time, and ensures final part specifications can be met.
- Material Considerations:
- Concept: The choice of material (e.g., AlSi10Mg vs. IN625) influences design possibilities due to differences in printability, mechanical properties, thermal properties, and minimum feature sizes.
- Application for Housings: A design optimized for the high strength of IN625 might allow for thinner walls than one using AlSi10Mg for the same load case. Conversely, a design relying heavily on thermal conductivity might favor AlSi10Mg.
- Benefit: Ensures the design leverages the chosen material’s strengths and accounts for its limitations.
Leveraging DfAM Expertise:
Successfully implementing DfAM requires expertise not only in CAD and simulation but also a deep understanding of the specific AM process being used. Collaborating with experienced AM service providers, like Met3dp, who offer wholesale 3D printing design services or application engineering support, can significantly accelerate the learning curve and lead to better outcomes. Their engineers understand the nuances of their machines and materials, providing valuable feedback on design printability, optimization potential, and cost implications. Embracing DfAM is not just about making a part printable; it’s about unlocking the full potential of additive manufacturing to create superior EV motor housings.
Achieving Precision: Tolerance, Surface Finish, and Dimensional Accuracy in 3D Printed Housings
While metal additive manufacturing offers incredible design freedom, a common question from engineers and procurement managers revolves around the achievable precision: Can 3D printed motor housings meet the tight tolerances, surface finish requirements, and dimensional accuracy demanded by automotive powertrain applications? The answer is yes, but it requires careful process control, understanding the inherent characteristics of AM, and often incorporating targeted post-processing steps.
Understanding As-Printed Capabilities:
Metal AM processes, particularly Laser Powder Bed Fusion (LPBF), can achieve relatively good dimensional accuracy and detail resolution directly from the machine. However, several factors influence the “as-printed” state:
- Thermal Effects: The repeated melting and solidification process induces thermal stresses, which can lead to minor warping or distortion, especially in large or complex parts like motor housings.
- Layerwise Construction: The nature of building layer by layer inherently creates a stepped surface, particularly on curved or angled features. This affects both surface roughness and precise dimensional accuracy.
- Powder Particle Size: The size of the metal powder particles used influences the minimum feature resolution and achievable surface finish.
- Laser Parameters: Factors like laser power, scan speed, and layer thickness directly impact melt pool dynamics, density, surface quality, and accuracy.
- Destek Yapıları: Areas where support structures were attached will typically have a rougher surface finish after removal and may require further processing.
Typical As-Printed Tolerances and Surface Finish (LPBF):
- Boyutsal Doğruluk: Generally falls within the range of ±0.1 mm to ±0.3 mm or ±0.1% to ±0.2% of the nominal dimension, whichever is larger. This can vary significantly based on part size, geometry, material, and machine calibration. For larger housings, cumulative errors can become more significant.
- Surface Roughness (Ra):
- Top Surfaces: Typically smoother, often in the range of 6-12 µm Ra.
- Vertical Walls: Slightly rougher due to layer lines, perhaps 8-15 µm Ra.
- Supported Down-Facing Surfaces: Significantly rougher after support removal, potentially >20-30 µm Ra.
- Internal Channels: Can be challenging to measure and control, often rougher than external surfaces.
Achieving Tighter Tolerances and Improved Finishes:
For many features on an EV motor housing, the as-printed state may suffice. However, critical interfaces require higher precision and smoother finishes than typically achievable directly from the printer.
- Bearing Seats/Bores: Require tight tolerances (often within tens of microns) and smooth finishes (Ra < 1.6 µm or better) for proper bearing fit and function.
- Mating Flanges: Need flatness and parallelism controls, along with specific surface finishes for sealing (gasket or O-ring grooves).
- Alignment Features: Dowel pin holes or locating surfaces require precise positioning and dimensions.
These critical features are typically addressed through post-process machining:
- CNC İşleme: The most common method. The 3D printed housing is fixtured, and critical features are machined (milling, turning, boring, drilling, grinding) to achieve the required dimensional accuracy 3D printing cannot hit directly. This allows tolerances comparable to fully machined parts (e.g., ±0.01 mm to ±0.05 mm) and desired surface finishes. Designing with machining stock (as per DfAM) is essential.
- Other Finishing Techniques: Depending on requirements, processes like polishing, lapping, or honing can be used for specific surfaces demanding extremely fine finishes.
Quality Control and Inspection:
Ensuring the final housing meets specifications requires robust quality control procedures:
- Boyutsal Muayene: Using Coordinate Measuring Machines (CMMs), 3D scanners, or traditional metrology tools to verify dimensions, tolerances, and geometric dimensioning and tolerancing (GD&T) callouts.
- Yüzey Pürüzlülüğü Ölçümü: Using profilometers to quantify surface finish (Ra, Rz) on critical areas.
- Tahribatsız Muayene (NDT): Techniques like X-ray or CT scanning can be employed to inspect internal features (like cooling channels for blockages) and check for internal defects (like porosity) if required by supplier quality standards.
- Material Property Verification: Testing tensile bars printed alongside the main part to verify material properties meet specifications.
Met3dp’s Commitment to Precision:
Achieving consistent metal AM tolerances and quality requires meticulous process control, well-maintained equipment, and deep expertise. Companies like Met3dp pride themselves on delivering industry-leading print volume, accuracy, and reliability. This commitment involves:
- Advanced Machine Calibration: Ensuring printers operate within tight parameters.
- Optimize Edilmiş Süreç Parametreleri: Developed through extensive testing for specific materials like AlSi10Mg and IN625.
- Powder Quality Control: Utilizing high-quality, spherical powders produced via advanced methods like gas atomization, ensuring consistent flowability and melting behavior. Learn more about Met3dp’s approach to metal 3D baskı.
- Integrated Post-Processing: Offering or coordinating necessary machining and finishing services to meet final part specifications.
- Robust Quality Management Systems: Implementing rigorous inspection protocols to guarantee automotive part precision.
Summary Table: Precision Capabilities
Özellik | As-Printed (Typical LPBF) | Post-Machined (Targeted Areas) | Notlar |
---|---|---|---|
Boyutsal Tolerans | ±0.1 to ±0.3 mm or ±0.1-0.2% | ±0.01 to ±0.05 mm (or tighter) | Machining required for high-precision fits. |
Surface Finish (Ra) | 6 – 30+ µm | <0.8 to 3.2 µm (typical) | Varies significantly by surface orientation (as-printed). |
Feature Complexity | Çok Yüksek | Limited by tool access | AM enables complex internal features not easily machined. |
Achievable Precision | Orta düzeyde | Çok Yüksek | Combination achieves complex shapes with precise interfaces. |
Sayfalara Aktar
In conclusion, while as-printed parts have limitations, metal katkılı üretim, when combined with targeted post-processing like CNC machining, can absolutely meet the stringent tolerance, surface finish, and dimensional accuracy requirements for functional EV motor housings. Understanding where to leverage AM’s strengths (complex geometries) and where to apply traditional finishing (precision interfaces) is key to successful implementation. Procurement managers should look for katkı maddesi üretim tedarikçileri who demonstrate strong capabilities in both printing and post-processing, backed by robust quality control systems.
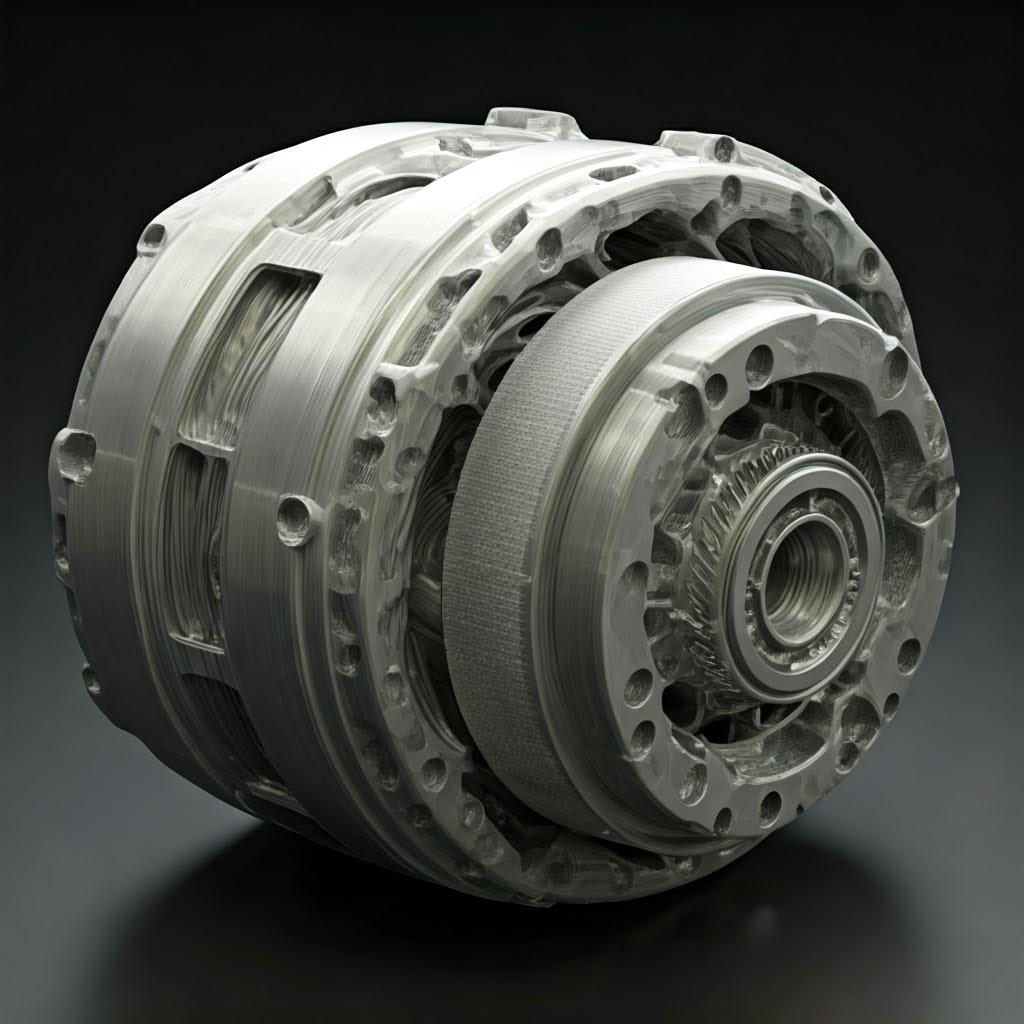
Essential Post-Processing Steps for Functional EV Motor Housings
A metal 3D printed part, like an EV motor housing, rarely comes off the build plate ready for final assembly. A series of post-processing steps are typically required to transform the raw printed component into a functional, reliable part meeting all engineering specifications. These steps are critical for ensuring mechanical properties, dimensional accuracy, surface quality, and overall performance. Understanding these common procedures is essential for estimating total lead times and costs associated with procuring AM parts.
Common Post-Processing Workflow for Metal AM Housings:
- Stres Giderici / Isıl İşlem:
- Amacımız: The rapid heating and cooling cycles inherent in LPBF can build up significant internal stresses within the printed part. If not relieved, these stresses can cause distortion (especially after removal from the build plate) or negatively impact mechanical properties, potentially leading to premature failure. Heat treatment is also used to achieve the desired final material microstructure and mechanical properties (e.g., strength, hardness, ductility).
- Süreç: The housing (often while still attached to the build plate) is placed in a furnace and subjected to a specific thermal cycle (heating to a target temperature, holding for a set duration, and controlled cooling). The exact cycle depends heavily on the material (AlSi10Mg requires different treatments than IN625) and the desired final properties (e.g., stress relief only vs. full solutionizing and aging for AlSi10Mg T6 condition). Treatments for reactive materials (like Titanium alloys, though less common for housings) or high-integrity parts may require vacuum or inert atmosphere furnaces to prevent oxidation.
- Importance: Absolutely critical for dimensional stability and achieving optimal, consistent material properties. It’s often the very first step after printing.
- Yapı Plakasından Çıkarma:
- Amacımız: To separate the printed housing(s) from the metal build plate they were printed on.
- Süreç: Typically done using wire EDM (Electrical Discharge Machining) or a bandsaw. Wire EDM offers higher precision and a cleaner cut, minimizing stress on the part, but is slower. Bandsawing is faster but less precise and may require more subsequent finishing near the cut line.
- Importance: A necessary step to liberate the part for further processing.
- Destek Yapısının Kaldırılması:
- Amacımız: To remove the temporary support structures required during the printing process.
- Süreç: This can be a combination of manual and automated methods. Supports may be broken off by hand or using pliers (for easily accessible, light supports), machined away using CNC, ground off, or sometimes removed using specialized tools. Access can be challenging, especially for internal supports within complex housing geometries. DfAM plays a crucial role here in designing supports for easier removal.
- Importance: Essential for achieving the final part geometry and accessing internal features. Can be one of the most time-consuming and labor-intensive post-processing steps if not optimized during design. Support removal challenges are a common bottleneck.
- CNC İşleme:
- Amacımız: To achieve tight tolerances, critical surface finishes, and precise geometric features (flatness, parallelism, perpendicularity) on specific areas of the housing that cannot be achieved in the as-printed state.
- Süreç: As discussed previously, features like bearing bores, mating flanges, sealing grooves, and precision mounting points are machined using milling, turning, drilling, boring, etc. This requires careful fixturing of the often complex AM part.
- Importance: Critical for ensuring proper fit, assembly, sealing, and function of the motor housing within the larger EV powertrain system.
- Surface Finishing / Smoothing:
- Amacımız: To improve the overall surface finish beyond the as-printed or post-machined state, either for functional reasons (e.g., improving fluid flow in cooling channels, reducing friction) or aesthetics.
- Süreç: A wide range of surface finishing techniques can be applied:
- Media Blasting: Using abrasive media (beads, grit) to create a uniform matte finish and remove minor surface imperfections or loose powder particles. Different media achieve different finishes.
- Tumbling/Vibratory Finishing: Using abrasive media in a rotating or vibrating bowl to deburr edges and smooth surfaces, particularly effective for batch processing smaller parts, though potentially applicable to specific housing features.
- Parlatma: Manual or automated polishing using progressively finer abrasives to achieve smooth, reflective surfaces.
- Elektro parlatma: An electrochemical process that removes a thin layer of material, smoothing surfaces and improving corrosion resistance, particularly effective on certain alloys like stainless steels or IN625.
- Abrasive Flow Machining (AFM): Pumping an abrasive putty through internal channels to smooth them – potentially useful for optimizing cooling channel performance.
- Importance: Depends on application requirements. Essential for sealing surfaces, potentially beneficial for flow paths, and sometimes desired for appearance.
- Cleaning and Inspection:
- Amacımız: To remove any residual powder, machining fluids, or debris, and to verify the part meets all specifications before shipment.
- Süreç: Thorough cleaning using appropriate solvents or aqueous solutions, potentially including ultrasonic cleaning. Final inspection using CMM, 3D scanning, NDT methods, and visual checks.
- Importance: Ensures part cleanliness (critical for assembly) and verifies quality conformance.
- Coating / Plating (Optional):
- Amacımız: To add specific surface properties not inherent to the base material, such as enhanced wear resistance, corrosion protection, specific thermal properties, or electrical insulation/conductivity.
- Süreç: Applying various coating 3D printed parts techniques like anodizing (for aluminum), painting, powder coating, plating (nickel, chrome), or specialized ceramic coatings.
- Importance: Application-specific; may be required for extended durability or specific functional requirements in harsh environments.
Integrating Post-Processing:
Efficiently managing this multi-step workflow requires careful planning and coordination. Leading AM service providers often offer a suite of in-house or closely managed B2B post-processing services. This integration streamlines the process, reduces lead times, and ensures accountability throughout the production cycle. When evaluating suppliers, inquire about their specific post-processing capabilities and quality control measures for each step relevant to your EV motor housing requirements.
Navigating Common Challenges in Metal AM for Motor Housings and Mitigation Strategies
While metal additive manufacturing offers significant advantages for producing EV motor housings, it’s not without its challenges. Understanding potential pitfalls and implementing effective mitigation strategies is crucial for ensuring successful outcomes, consistent quality, and cost-effective production. Engineers and procurement managers should be aware of these common issues when specifying and sourcing 3D printed components.
Key Challenges and How to Address Them:
- Çarpıtma ve Bozulma:
- Meydan okumak: The high thermal gradients during LPBF can cause internal stresses that lead to warping, either during the build or after removal from the build plate. This is particularly prevalent in large, flat sections or complex geometries like motor housings.
- Mitigation Strategies:
- Termal Simülasyon: Use simulation software to predict stress accumulation and potential distortion areas early in the design phase.
- Optimized Build Orientation: Orient the part to minimize large flat areas parallel to the build plate and manage heat distribution.
- Effective Support Structures: Use robust supports strategically placed to anchor the part securely and counteract thermal stresses. Design supports to be thermally conductive where needed.
- Optimized Scan Strategies: Employ specific laser scanning patterns (e.g., island scanning, chessboard patterns) to distribute heat more evenly and reduce localized stress buildup.
- Stress Relief Heat Treatment: Perform appropriate stress relief cycles immediately after printing, often before removing the part from the build plate, to relax internal stresses.
- Malzeme Seçimi: Some materials are inherently more prone to cracking or warping than others; consider this during material selection if design constraints allow.
- Gözeneklilik:
- Meydan okumak: Small voids or pores can form within the printed material due to trapped gas, incomplete powder fusion (Lack of Fusion – LoF), or keyholing effects (vapor depression collapse). Porosity can degrade mechanical properties (especially fatigue life), compromise pressure tightness, and act as crack initiation sites.
- Mitigation Strategies:
- Yüksek Kaliteli Toz: Kullanım yüksek performanslı metal tozları with controlled particle size distribution, low gas content, and good sphericity/flowability. Met3dp’s use of advanced gas atomization and PREP technologies addresses this directly.
- Optimize Edilmiş Süreç Parametreleri: Develop and strictly control printing parameters (laser power, scan speed, layer thickness, hatch spacing, gas flow) validated for the specific material and machine to ensure full melting and fusion. Parameter optimization is key expertise for providers like Met3dp.
- Inert Atmosphere Control: Maintain a high-purity inert gas environment (Argon or Nitrogen) within the build chamber to minimize oxidation and gas pickup.
- Sıcak İzostatik Presleme (HIP): An optional post-processing step where the part is subjected to high temperature and high pressure gas. HIP can effectively close internal pores, significantly improving density and mechanical properties, especially fatigue strength. Often used for critical aerospace or medical parts, but can be considered for high-performance housings.
- NDT Inspection: Use X-ray or CT scanning to detect internal porosity in critical areas.
- Support Removal Difficulties:
- Meydan okumak: Removing support structures, especially from complex internal geometries like cooling channels or intricate lattice structures, can be difficult, time-consuming, and risks damaging the part. Residual support material or surface marks can affect performance or require extensive finishing.
- Mitigation Strategies:
- DfAM for Support Reduction: Design parts to be self-supporting where possible (using >45° angles), choose optimal orientations, and use topology optimization tools that consider support minimization.
- Optimized Support Design: Use support types (e.g., thin walls, cone supports, tree supports) that are easier to remove and leave minimal contact points (‘witness marks’) on the part surface. Utilize software features for generating breakaway supports.
- Accessibility Planning: Ensure support structures are designed with clear access paths for removal tools (manual or CNC). Avoid supports in deep, inaccessible internal cavities unless absolutely necessary and planned for (e.g., soluble supports, though less common in metal AM, or designing for AFM finishing).
- Specialized Removal Techniques: Employ appropriate tools and techniques, potentially including wire EDM for precise cutting near the part surface or CNC machining for bulk removal.
- Residual Powder Removal:
- Meydan okumak: Unsintered powder can become trapped within internal channels, cavities, or complex lattice structures. If not fully removed, it can impede fluid flow (in cooling channels), add weight, or become dislodged during operation.
- Mitigation Strategies:
- DfAM: Design internal channels with sufficient diameter and smooth transitions to facilitate powder removal. Include drainage holes where appropriate. Avoid creating powder traps.
- Optimized Depowdering Procedures: Utilize vibration, compressed air jets, and careful part manipulation during the breakout phase immediately after printing to remove the bulk of loose powder.
- Thorough Cleaning Processes: Implement rigorous cleaning protocols, potentially involving ultrasonic cleaning, flushing with solvents, or specialized equipment designed for cleaning internal channels.
- Teftiş: Use borescope inspection or CT scanning to verify internal channels are clear.
- Surface Finish Variability:
- Meydan okumak: As-printed surface finish varies significantly depending on orientation (top, vertical, supported down-skin) and features (e.g., layer stepping on shallow angles). Achieving a consistent finish or meeting specific Ra requirements often necessitates post-processing.
- Mitigation Strategies:
- Orientation Optimization: Orient the part to place critical surfaces in orientations that naturally produce better finishes (e.g., upward-facing or vertical).
- Parametre Ayarlama: Fine-tune contouring parameters during printing for improved wall finish.
- Targeted Post-Processing: Plan for necessary machining, blasting, tumbling, or polishing operations on surfaces requiring specific finishes, incorporating necessary stock allowances in the design.
- Achieving Tight Tolerances:
- Meydan okumak: As discussed earlier, as-printed parts have dimensional limitations. Achieving the very tight tolerances required for bearing fits or mating surfaces reliably requires post-machining.
- Mitigation Strategies:
- DfAM for Machining: Designate critical features and add sufficient machining stock. Include datum features for accurate fixturing.
- Integrated Machining Capabilities: Partner with an AM supplier who has in-house or tightly controlled external CNC machining capabilities and expertise in machining AM parts.
- Robust Quality Control: Implement thorough dimensional inspection (CMM) after machining.
Partnering to Overcome Challenges:
Navigating these common challenges in metal AM requires a combination of good design practices (DfAM), optimized and controlled printing processes, and effective post-processing strategies. Working closely with an experienced additive manufacturing service provider like Met3dp is invaluable. Their engineers can provide design feedback, leverage validated process parameters for materials like AlSi10Mg ve IN625, and manage the post-processing workflow to mitigate risks and ensure the final EV motor housing meets all performance and quality requirements. Troubleshooting 3D prints and proactively addressing potential issues is part of the value proposition offered by established providers.
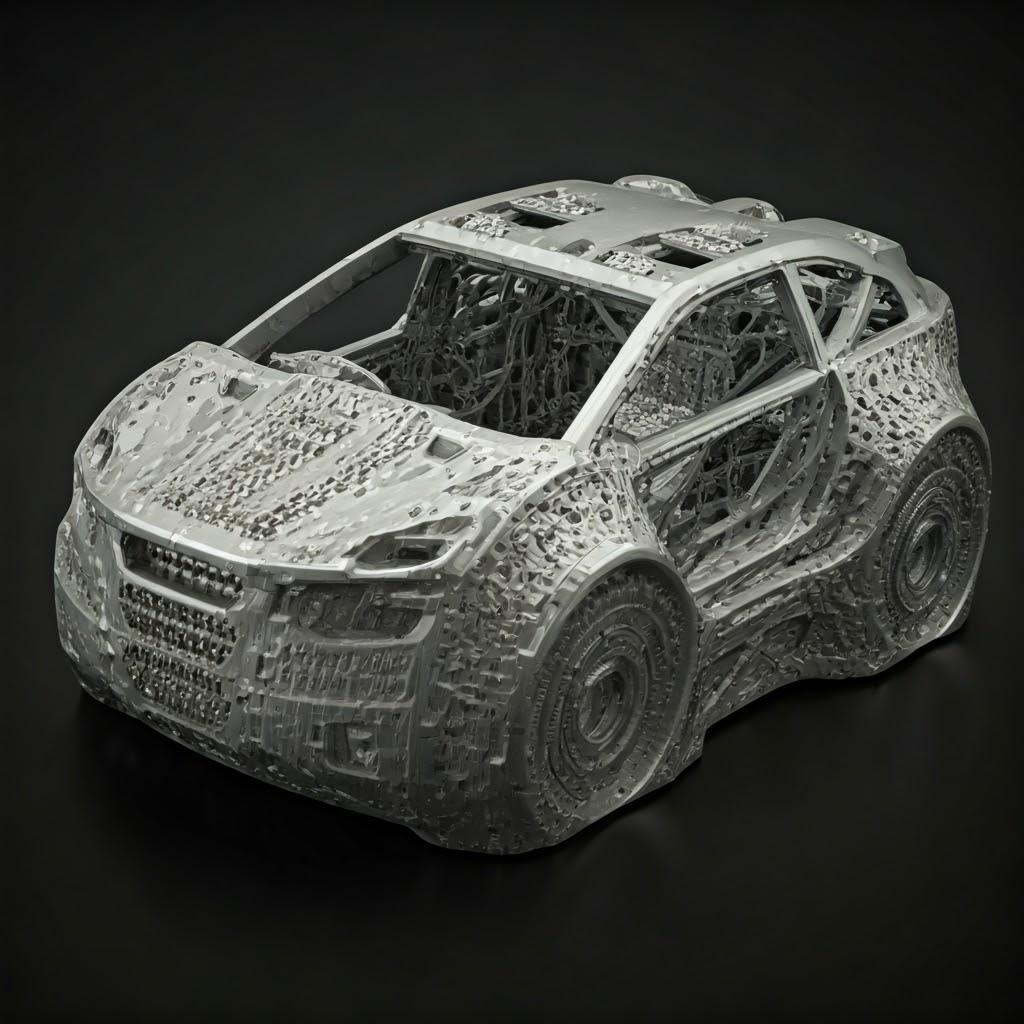
Selecting the Ideal Metal 3D Printing Service Provider for Automotive Needs
Choosing the right manufacturing partner is as critical as the design and material selection when adopting metal additive manufacturing for demanding applications like EV motor housings. Not all metal 3D printing service bureaus are created equal. The automotive industry demands stringent quality, reliability, and traceability, requiring suppliers with specific expertise, robust processes, and a deep understanding of the sector’s requirements. Evaluating potential AM suppliers requires looking beyond just price and considering a range of crucial factors.
Key Criteria for Evaluating Metal AM Suppliers:
- Technical Expertise and Engineering Support:
- DfAM Capabilities: Does the supplier offer Design for Additive Manufacturing support? Can their engineers collaborate with your team to optimize the motor housing design for printability, performance, and cost-effectiveness, leveraging techniques like topology optimization and feature integration?
- Materials Science Knowledge: Do they possess in-depth knowledge of the materials relevant to your application (e.g., AlSi10Mg, IN625)? Can they advise on material selection trade-offs and expected performance based on their processing parameters? Look for providers like Met3dp, who not only use but also manufacture yüksek kaliteli metal tozları, demonstrating a fundamental understanding of material behavior. Learn more about Met3dp and their foundational expertise.
- Süreç Optimizasyonu: Can they demonstrate experience in developing and controlling optimized printing parameters for consistent, high-density parts with desired mechanical properties?
- Technology and Equipment:
- Relevant AM Processes: Do they operate the appropriate metal AM technology for your needs, typically Laser Powder Bed Fusion (LPBF/SLM) for intricate housings? Some providers might also offer Electron Beam Melting (EBM), which has advantages for certain materials like titanium alloys but different surface finish and accuracy characteristics. Understanding different baskı yöntemleri and their suitability is key.
- Machine Park: What is the size, age, and manufacturer of their printer fleet? Do they have sufficient capacity to handle your prototyping and potential low-to-mid volume production needs? Redundancy (multiple machines capable of running your part) is important for mitigating downtime risks.
- Maintenance and Calibration: Do they have rigorous procedures for machine maintenance and calibration to ensure consistent performance?
- Material Capabilities and Quality Control:
- Malzeme Portföyü: Do they offer the specific alloys you require (e.g., AlSi10Mg, IN625)? What is the breadth of their material offerings?
- Powder Handling and Management: How do they handle, store, recycle, and test metal powders to ensure quality and prevent contamination or degradation? Traceability of powder batches is crucial. Met3dp’s vertical integration, including advanced Powder Making Systems (Gas Atomization, PREP), provides inherent control over powder quality from the source.
- Malzeme Sertifikasyonu: Can they provide material certifications confirming the powder meets required specifications (e.g., chemical composition, particle size distribution)?
- Post-Processing Capabilities:
- Şirket İçi ve Dış Kaynaklı: What post-processing steps (heat treatment, support removal, CNC machining, surface finishing, inspection) do they perform in-house versus manage through external partners? In-house capabilities generally offer better control, faster turnaround, and clearer accountability.
- Uzmanlık alanı: Do they have demonstrated expertise in the specific post-processing steps required for your housing (e.g., precision machining of AM parts, complex support removal)?
- Quality Management System (QMS) and Certifications:
- Sertifikalar: Does the supplier hold relevant quality certifications? ISO 9001 is a baseline expectation. While IATF 16949 (the automotive standard) adoption is still evolving in the AM industry, suppliers demonstrating progress towards or compliance with its principles show a commitment to automotive requirements. Other relevant certifications might include AS9100 (aerospace).
- Traceability: Can they provide full traceability from raw powder batch to final shipped part, including process data logs?
- Inspection Capabilities: Do they have the necessary metrology equipment (CMM, 3D scanners, surface profilometers) and NDT capabilities (X-ray, CT scanning if required) along with trained personnel?
- Experience and Track Record:
- Sektör Deneyimi: Have they successfully completed projects for the automotive industry or similar high-requirement sectors (e.g., aerospace, medical)? Can they provide relevant case studies or references?
- Parça Karmaşıklığı: Do they have experience printing parts of similar size, complexity, and material to your EV motor housing?
- Lead Time and Responsiveness:
- Quoting Speed: How quickly can they provide detailed quotes?
- Stated Lead Times: What are their typical lead times for additive manufacturing projects, considering printing and all necessary post-processing? Are these realistic and reliable?
- Communication: Are they responsive to inquiries and proactive in communication throughout the project?
- Cost Structure:
- Şeffaflık: Is their pricing structure clear and detailed, breaking down costs for setup, material, printing, and post-processing? (See next section for more on costs).
- Value: Does the quoted price reflect the level of expertise, quality, and service offered? The cheapest option may not provide the necessary quality or reliability for a critical component like a motor housing.
Why Partner with Met3dp?
Met3dp, headquartered in Qingdao, China, positions itself as a leading provider of comprehensive katkı üretim çözümleri. Their strengths align well with the requirements for producing critical automotive components:
- Integrated Solutions: Offering SEBM printers, advanced metal powders produced in-house, and application development services.
- Malzeme Uzmanlığı: Specializing in high-performance metal powders, including standard alloys and innovative compositions (TiNi, TiTa, TiAl, etc.), produced using industry-leading gas atomization and PREP technologies for high quality.
- Focus on Performance: Emphasizing industry-leading print volume, accuracy, and reliability for mission-critical parts.
- Decades of Collective Expertise: Bringing significant experience in metal AM to support customer projects.
By carefully evaluating potential suppliers against these criteria, engineering and procurement additive manufacturing teams can select a partner capable of reliably delivering high-quality, functional 3D printed EV motor housings that meet the demanding standards of the automotive industry.
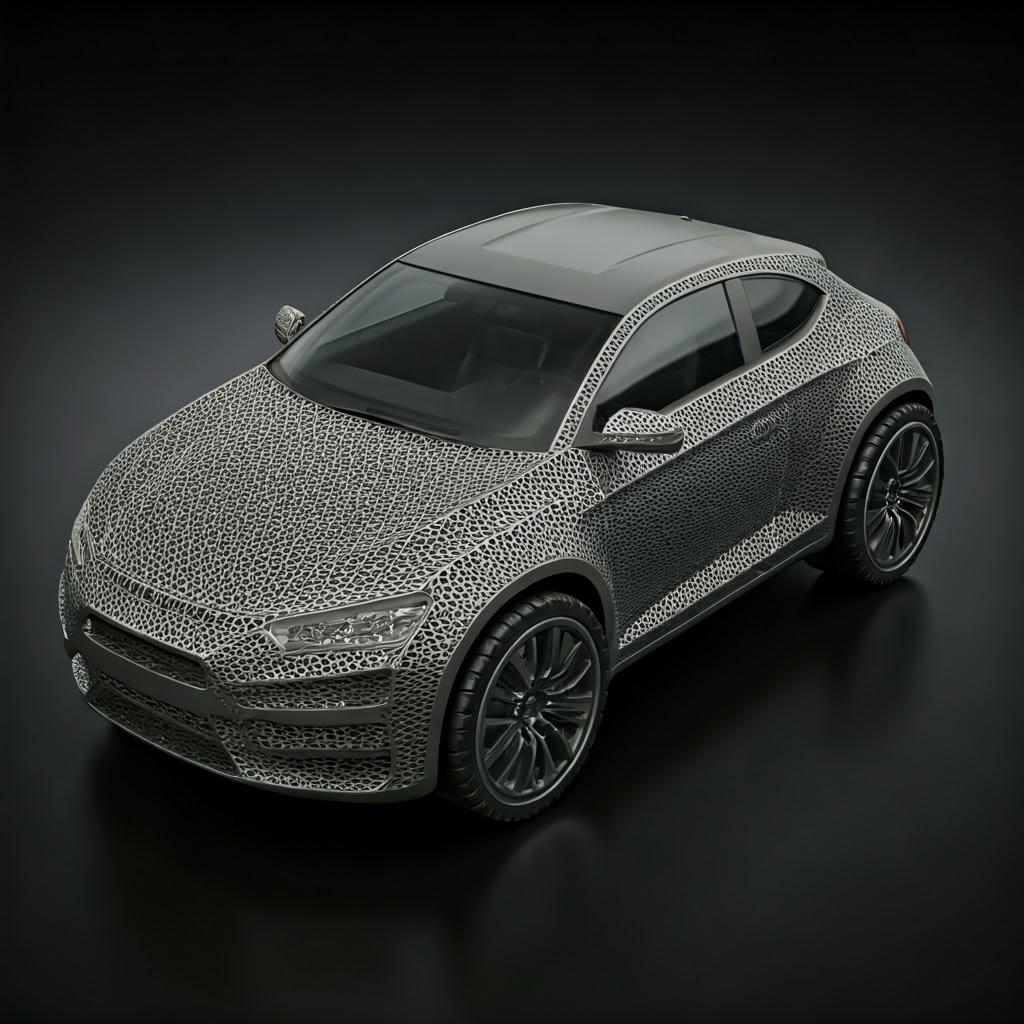
Understanding Cost Factors and Lead Times for 3D Printed EV Motor Housings
While the technical benefits of metal AM for EV motor housings are compelling, practical adoption hinges on understanding the associated costs and production timelines. Unlike traditional high-volume manufacturing where tooling amortization dominates, AM costs are driven by different factors. A clear understanding of this metal 3D printing cost analysis is crucial for project budgeting and procurement decisions.
Key Factors Influencing Cost:
- Malzeme Maliyeti:
- Powder Price: The cost per kilogram of the chosen metal powder. Nickel superalloys (IN625) are significantly more expensive than aluminum alloys (AlSi10Mg). Titanium alloys fall somewhere in between.
- Part Volume & Density: The total volume of material required to print the part, including supports. Denser materials (like IN625) will result in higher material costs for the same volume compared to lighter materials (like AlSi10Mg).
- Powder Refresh Rate: AM processes require refreshing used powder with virgin powder; this operational cost is factored into pricing.
- Machine Time / Print Time:
- Machine Hourly Rate: Service providers charge based on the time their expensive AM machines are occupied. Rates vary based on machine type, size, and capabilities.
- Part Volume & Height: Larger parts and taller parts (in the build orientation) take longer to print, directly increasing machine time costs.
- Parça Karmaşıklığı: Highly complex geometries might require more intricate scanning strategies or support structures, potentially increasing print time slightly.
- Nesting/Build Density: Printing multiple parts simultaneously in one build job can improve machine utilization and potentially lower the per-part cost, especially relevant for bulk additive manufacturing pricing.
- Destek Yapıları:
- Hacim: The amount of material used for supports adds to material costs.
- Print Time: Printing supports adds to the overall machine time.
- Sökme İşçiliği/Süresi: Removing supports, especially complex or internal ones, requires significant labor and/or specialized processes (machining, EDM), adding substantially to post-processing costs. DfAM efforts to minimize supports directly impact cost.
- İşlem sonrası:
- Isıl İşlem: Costs vary depending on the required cycle (simple stress relief vs. full aging), furnace time, and atmosphere requirements (air vs. vacuum/inert).
- İşleme: Complexity, number of features requiring machining, required tolerance/finish levels, and fixturing difficulty all impact CNC machining costs.
- Yüzey İşlemi: Costs depend on the chosen method (blasting, tumbling, polishing) and the required surface area/quality level.
- Inspection/QA: Costs associated with dimensional inspection (CMM time), NDT (if required), material testing, and documentation generation.
- Labor and Engineering:
- File Preparation/Setup: Time required for engineers to prepare the CAD file, orient the part, generate supports and toolpaths, and set up the build job.
- Manual Post-Processing: Labor involved in build plate removal, manual support removal, basic finishing, cleaning, and handling.
- Sipariş Hacmi:
- Prototipleme: Single parts or very small batches incur higher per-part costs due to setup amortization.
- Low-to-Mid Volume Production: Per-part costs typically decrease with increasing volume due to better machine utilization (nesting), optimized workflows, and potential volume discounts on materials or services. However, AM costs generally don’t decrease as steeply with volume as traditional casting after tooling amortization.
Cost Comparison Snapshot (Illustrative):
Üretim Yöntemi | Kalıp Maliyeti | Per-Part Cost (Low Vol) | Per-Part Cost (High Vol) | Lead Time (First Parts) | Lead Time (Production) | Complexity Handling |
---|---|---|---|---|---|---|
Metal AM (e.g., LPBF) | Hiçbiri | Moderate – High | Moderate – High | Fast (Days/Weeks) | Orta düzeyde | Mükemmel |
Basınçlı Döküm | Çok Yüksek | High (Tool Amort.) | Çok Düşük | Slow (Months) | Hızlı | Orta düzeyde |
Sand Casting | Low-Moderate | Orta düzeyde | Orta düzeyde | Moderate (Weeks) | Orta düzeyde | İyi |
CNC Machining (Billet) | Çok Düşük | Çok Yüksek | Çok Yüksek | Moderate-Fast | Yavaş | Yüksek |
Sayfalara Aktar
(Note: This is a simplified comparison; actual costs depend heavily on specific part geometry, material, and volume.)
Factors Influencing Lead Time:
Bu AM production time or total lead time for a 3D printed EV motor housing includes several stages:
- Quoting & Order Processing: (1-5 days)
- File Preparation & Scheduling: (1-3 days)
- Baskı: (1-7+ days, highly dependent on part size, height, and nesting)
- Cooldown & Depowdering: (0.5-1 day)
- Isıl İşlem: (1-3 days, including furnace time and cooling)
- Build Plate Removal & Support Removal: (1-3 days, highly variable based on complexity)
- CNC İşleme: (2-7+ days, dependent on complexity and shop loading)
- Surface Finishing / Other Steps: (1-5 days, depends on requirements)
- Quality Inspection & Shipping: (1-3 days)
Total typical lead times can range from 2 weeks for simpler prototypes with minimal post-processing to 6-8 weeks or more for complex housings requiring extensive machining and finishing.
Factors affecting lead time:
- Supplier Queue: Current workload and machine availability at the service provider.
- Parça Karmaşıklığı: Affects print time, support removal, and machining time.
- İşlem Sonrası Gereksinimler: Each additional step adds time. Machining often represents a significant portion of the post-print timeline.
- Quality Requirements: Extensive inspection or testing adds time.
- Malzeme: Some materials print faster than others; heat treatment cycles vary.
When planning projects, it’s crucial to discuss lead time expectations early with potential suppliers and understand the timelines associated with each step of the process. Building buffer time into the schedule is advisable, especially for initial prototypes or complex parts.
Frequently Asked Questions (FAQ) about 3D Printed EV Motor Housings
Here are answers to some common questions engineers and procurement managers have when considering metal additive manufacturing for EV motor housings:
1. Is metal 3D printing strong enough for a structural component like an EV motor housing?
Cevap: Absolutely. Metal AM processes like Laser Powder Bed Fusion (LPBF), when properly controlled, produce parts with densities typically exceeding 99.5%, often reaching 99.9%. The resulting mechanical properties (tensile strength, yield strength, fatigue life) of common AM materials like AlSi10Mg (after heat treatment) or IN625 are comparable, and sometimes even superior, to those achieved through traditional casting methods for the same alloys. With appropriate design (DfAM), material selection (e.g., using high-strength AlSi10Mg-T6 or IN625), process control, and post-processing (like heat treatment), 3D printed metal housings can readily meet or exceed the structural and durability requirements for demanding automotive applications. Extensive testing and validation are, of course, essential parts of the development process, just as they would be for cast or machined parts.
2. How does the cost of a 3D printed EV motor housing compare to traditional casting?
Cevap: The cost comparison depends heavily on production volume and part complexity.
- Prototyping & Low Volume (e.g., <50-100 units): Metal AM is often significantly cheaper and faster because it avoids the high upfront cost and long lead time associated with casting tooling (molds).
- Mid Volume (e.g., hundreds to low thousands): The cost can be competitive, especially if AM enables significant lightweighting (reducing material cost) or part consolidation (reducing assembly cost), or if the design complexity makes casting difficult or requires multiple casting steps.
- High Volume (e.g., >5,000-10,000+ units): Traditional die casting typically becomes more cost-effective on a per-part basis due to the full amortization of tooling costs and faster cycle times. However, AM’s value proposition often lies in enabling superior performance (better thermal management, lighter weight) or accelerating development, which can outweigh per-part cost differences in certain scenarios. Metal 3D printing cost analysis should consider the total cost of ownership and performance benefits, not just the manufacturing price.
3. Can the complex internal cooling channels designed with AM be reliably printed and cleaned?
Cevap: Yes, this is one of the key advantages of AM, but it requires careful execution.
- Baskı: Modern LPBF systems can create intricate internal channels with relatively high fidelity. DfAM principles are crucial – designing channels large enough (typically >1-2 mm diameter, depending on length and complexity) and with smooth paths to avoid powder trapping and facilitate printing. Self-supporting channel shapes (e.g., diamond or teardrop cross-sections) are often preferred over simple circles for horizontal sections.
- Temizlik: Thorough powder removal is critical. This involves optimized orientation during printing to allow drainage, careful breakout procedures (vibration, compressed air), and potentially specialized cleaning steps like ultrasonic cleaning or abrasive flow machining (AFM) for critical applications. Inspection using borescopes or CT scanning can verify channel cleanliness. Experienced AM providers have established protocols for reliably producing parts with clean, functional internal channels.
4. What are the typical lead times for getting a functional prototype of a 3D printed motor housing?
Cevap: As outlined in the previous section, lead times vary based on complexity, size, material, and required post-processing. For a typical passenger car sized EV motor housing prototype made from AlSi10Mg requiring heat treatment, support removal, and some critical feature machining, a lead time of 3 ila 6 hafta is a reasonable estimate. Simpler prototypes with minimal post-processing might be faster (2-3 weeks), while highly complex parts or those requiring extensive machining or specialized finishing could take longer (6-8+ weeks). It’s essential to get specific lead time quotes from suppliers based on your final design and specifications.
Conclusion: The Future of EV Powertrains is Additive
The relentless drive for efficiency, performance, and innovation in the electric vehicle market demands manufacturing solutions that transcend traditional limitations. Metal additive manufacturing has unequivocally emerged as a powerful enabler, offering transformative potential for critical components like EV motor housings.
As we’ve explored, the advantages are compelling:
- Eşsiz Tasarım Özgürlüğü: Enabling topology optimization for radical lightweighting, complex internal cooling channels for superior thermal management, and part consolidation for simplified assemblies.
- Accelerated Innovation: Facilitating rapid prototyping and design iteration, slashing development times compared to tooling-dependent methods.
- Performans Geliştirme: Delivering lighter, stiffer, and cooler-running components that contribute directly to increased vehicle range, better performance, and enhanced durability.
- Malzeme Esnekliği: Utilizing advanced materials like high-performance aluminum alloys (AlSi10Mg) and nickel superalloys (IN625) tailored to specific application needs.
While challenges related to precision, post-processing, and cost exist, they are being systematically addressed through advancements in DfAM principles, process control, automation, and strong partnerships between automotive innovators and expert AM service providers. Understanding the nuances of design, material selection, post-processing, cost factors, and supplier capabilities is key to successfully leveraging metal AM adoption in the automotive sector.
The journey requires a shift in thinking – designing için the process to unlock its full potential. It also requires collaboration with partners who possess not only the technology but also the deep expertise in materials science, process optimization, and quality assurance necessary for producing mission-critical advanced automotive components.
Met3dp, with its integrated approach encompassing advanced powder production, state-of-the-art printing systems, and comprehensive application support, represents the type of partner needed to navigate this transition. Their focus on accuracy, reliability, and material quality provides a solid foundation for developing next-generation EV powertrain components.
The future of electric vehicles is intrinsically linked to manufacturing innovation. Metal additive manufacturing is no longer just a prototyping tool; it is a viable, compelling production solution for components like motor housings, paving the way for lighter, faster, more efficient, and ultimately, more sustainable electric vehicles. As the technology continues to mature and scale, its role in shaping the future of electric vehicles will only grow.
Ready to explore how metal additive manufacturing can revolutionize your EV components? Contact the experts at Met3dp today to discuss your project requirements and discover how their cutting-edge systems and powders can power your organization’s additive manufacturing goals.
Paylaş
MET3DP Technology Co, LTD, merkezi Qingdao, Çin'de bulunan lider bir katmanlı üretim çözümleri sağlayıcısıdır. Şirketimiz, endüstriyel uygulamalar için 3D baskı ekipmanları ve yüksek performanslı metal tozları konusunda uzmanlaşmıştır.
İşletmeniz için en iyi fiyatı ve özelleştirilmiş Çözümü almak için sorgulayın!
İlgili Makaleler
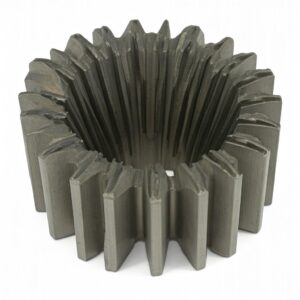
Yüksek Performanslı Nozul Kanat Segmentleri: Metal 3D Baskı ile Türbin Verimliliğinde Devrim
Daha Fazla Oku "Met3DP Hakkında
Son Güncelleme
Bizim Ürünümüz
BİZE ULAŞIN
Herhangi bir sorunuz var mı? Bize şimdi mesaj gönderin! Mesajınızı aldıktan sonra tüm ekibimizle talebinize hizmet edeceğiz.
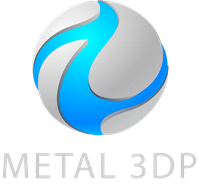
3D Baskı ve Katmanlı Üretim için Metal Tozları