EV Thermal Interface Plates via High-Conductivity Alloys
İçindekiler
Introduction: The Critical Role of Thermal Interface Plates in Electric Vehicle Performance
The global shift towards sustainable transportation is accelerating at an unprecedented pace, with electric vehicles (EVs) at the forefront of this revolution. As consumers and fleet operators embrace electrification, the demands placed on EV technology intensify. Achieving longer driving ranges, faster charging times, enhanced safety, and extended battery lifespan are no longer aspirational goals but essential requirements for market success. Central to meeting these demands is mastering a fundamental engineering challenge: termal yönetim.
Electric vehicles, by their very nature, operate with high power densities. Key components such as the battery pack, electric motor, power electronics (inverters, converters, on-board chargers), and even charging systems generate significant amounts of heat during operation. Unlike internal combustion engine vehicles that readily expel heat through exhaust, EVs must dissipate thermal energy effectively through dedicated cooling systems. If this heat isn’t managed efficiently, it can lead to a cascade of negative consequences: reduced component efficiency, accelerated degradation of battery cells, performance throttling (derating), compromised safety (thermal runaway risk), and ultimately, a shorter vehicle lifespan and diminished user experience.
İşte burası Thermal Interface Plates (TIPs) play an indispensable, albeit often unseen, role. A Thermal Interface Plate is a specialized component engineered to facilitate the efficient transfer of heat between a heat-generating source (like a battery module or an inverter’s power module) and a cooling system component (such as a liquid-cooled cold plate or a heat sink). Its primary function is to minimize thermal resistance at the interface, ensuring that heat can flow away from critical components as rapidly and effectively as possible. Think of it as a crucial thermal bridge, conducting heat away from sensitive areas to maintain optimal operating temperatures.
The effectiveness of a TIP hinges significantly on the material it’s made from and its geometric design. Traditional materials and manufacturing methods often struggle to meet the escalating thermal challenges posed by next-generation EVs. This necessitates the exploration of high-conductivity alloys, materials specifically chosen for their exceptional ability to conduct heat. Metals like copper alloys (such as Copper-Chromium-Zirconium, CuCrZr) and specific aluminum alloys (like AlSi10Mg) offer superior thermal performance compared to conventional options.
However, simply selecting a high-conductivity material isn’t enough. The design of the TIP is equally critical. The ability to create complex shapes that conform perfectly to component surfaces, incorporate intricate internal cooling channels, or maximize surface area for heat exchange can dramatically enhance thermal performance. This is where metal katkılı üretim (AM), commonly known as metal 3D baskı, emerges as a transformative technology. AM liberates designers from the constraints of traditional manufacturing processes like casting or machining, enabling the creation of highly optimized, complex, and efficient thermal management components that were previously impossible or prohibitively expensive to produce.
As a leading provider of comprehensive additive manufacturing solutions, Met3dp recognizes the critical need for advanced thermal management in the EV industry. Specializing in both state-of-the-art metal 3D printing equipment and the production of high-performance metal powders, Met3dp is strategically positioned to empower engineers and procurement managers in the automotive sector. Our expertise in materials science, particularly with high-conductivity alloys produced via our advanced atomization techniques, combined with our industry-leading printer technology, enables the development and production of next-generation EV Thermal Interface Plates. This blog post delves into the specifics of using metal AM, particularly with high-conductivity alloys like CuCrZr and AlSi10Mg, to design and manufacture superior TIPs, addressing the challenges and unlocking new levels of performance for electric vehicles. We aim to provide valuable insights for engineering teams seeking cutting-edge solutions and procurement professionals sourcing reliable manufacturing partners for these critical components.
What are EV Thermal Interface Plates Used For? Functions and Applications
Thermal Interface Plates (TIPs) are fundamental components within the intricate thermal management architecture of an electric vehicle. Their core purpose is elegantly simple yet technically demanding: to serve as a highly efficient conduit for heat transfer between disparate components within the system. They effectively bridge the physical and thermal gap that inevitably exists between a heat source and a heat removal mechanism, minimizing the resistance to heat flow across this junction.
Primary Function: Minimizing Thermal Interface Resistance
Any time two solid surfaces are brought into contact, microscopic imperfections (roughness, lack of perfect flatness) create tiny air gaps. Air is a poor thermal conductor, meaning these gaps impede the flow of heat. Thermal Interface Resistance (TIR) quantifies this impedance. A high TIR means heat struggles to cross the boundary, leading to localized temperature increases in the heat-generating component. TIPs are designed to overcome this by:
- Providing a Conforming Surface: Ideally, a TIP perfectly matches the surface contours of both the heat source and the heat sink/cold plate, maximizing the real contact area.
- Utilizing High Thermal Conductivity Material: The bulk material of the TIP itself must offer minimal resistance to heat flow. This is why high-conductivity alloys are preferred.
- Facilitating Heat Spreading: TIPs often help spread concentrated heat from a small source (like a power semiconductor) over a larger area before it enters the primary cooling system, reducing peak temperatures.
Detailed Applications within Electric Vehicles:
The need for efficient thermal bridging via TIPs is pervasive throughout an EV’s powertrain and energy storage systems. Key application areas include:
- Battery Pack Cooling: This is arguably the most critical application. EV batteries operate optimally within a narrow temperature range. Excessive heat accelerates degradation, reduces capacity and cycle life, and in extreme cases, can trigger thermal runaway – a dangerous chain reaction. TIPs are used extensively here:
- Cell-to-Cell/Module: Conducting heat uniformly away from individual battery cells towards the module’s cooling interface.
- Module-to-Cold Plate: Ensuring efficient transfer of heat from the base of battery modules to a liquid-cooled cold plate, which circulates coolant to dissipate the heat, often via a radiator. TIPs here need to conform precisely to the module base and cold plate surface.
- Busbar Interfaces: High currents flowing through busbars generate heat; TIPs can help cool these connections.
- Power Electronics Cooling (Inverters, Converters, On-Board Chargers): These units handle high voltages and currents, converting DC battery power to AC for the motor (inverter) or managing charging functions (OBC, DC-DC converters). Semiconductor devices (IGBTs, MOSFETs) within these modules generate intense localized heat.
- Semiconductor-to-Heat Sink/Cold Plate: TIPs are placed directly beneath power modules to draw heat away rapidly and transfer it to air-cooled heat sinks or liquid-cooled plates. Maintaining lower operating temperatures for these semiconductors is vital for efficiency and reliability.
- Electric Motor Cooling: While some motors rely on air or oil cooling, high-performance motors often utilize liquid cooling jackets.
- Stator/Rotor Interfaces: TIPs can potentially be used to improve heat transfer from the motor’s stator windings or rotor components to the cooling jacket or housing, especially in compact, high-power-density designs.
- Charging System Components: High-power charging also generates heat, both within the vehicle’s charging port and associated electronics, potentially requiring TIPs for management.
Improving Component Reliability and Preventing Thermal Runaway:
Effective thermal management, significantly aided by high-performance TIPs, directly translates to improved component reliability and longevity. By keeping components within their optimal operating temperature windows, the rate of degradation is slowed, and the risk of sudden failure is reduced. In the context of lithium-ion batteries, preventing excessive heat buildup is paramount for safety. Well-designed TIPs contribute to uniform cell temperatures, mitigating the risk of localized hotspots that could potentially initiate thermal runaway. This makes TIPs a critical element not just for performance but for the fundamental safety of the vehicle. Procurement managers sourcing these components are essentially investing in the vehicle’s long-term health and safety profile.
Beyond Automotive: Broader Industrial Relevance
While this discussion focuses on EVs, the principles and applications of high-performance TIPs extend to numerous other industries requiring advanced thermal management for electronics and power systems. Examples include:
- Havacılık ve Savunma: Cooling sensitive avionics, radar systems, and power distribution units.
- Renewable Energy: Thermal management in solar inverters and wind turbine converters.
- Industrial Power Supplies and Motor Drives: Ensuring reliability in factory automation and high-power equipment.
- Tıbbi Cihazlar: Cooling components in diagnostic imaging equipment (MRI, CT scanners) or high-intensity therapeutic devices.
- High-Performance Computing: Managing heat loads in data centers and servers.
Engineers and wholesale thermal plate buyers in these sectors face similar challenges to their automotive counterparts, making the advancements in materials and manufacturing techniques discussed here highly relevant across the board. The ability to source reliable, high-performance TIPs, potentially in bulk for series production, is a common requirement.
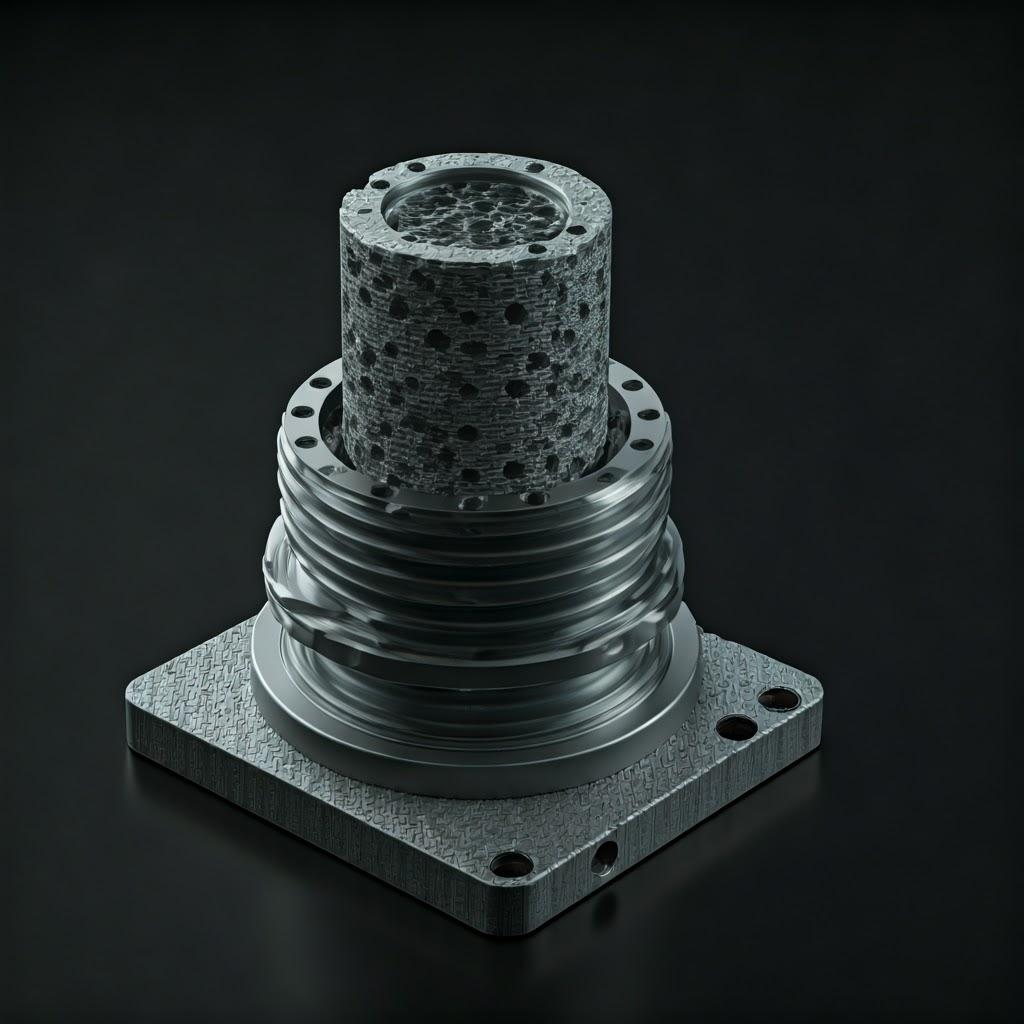
Why Use Metal 3D Printing for EV Thermal Interface Plates? Unlocking Design Freedom and Performance
For decades, engineers have relied on traditional manufacturing methods like casting, machining (CNC milling/turning), and stamping to produce thermal management components. While these techniques are mature and well-understood, they often impose significant limitations, particularly when tackling the complex thermal challenges presented by modern electric vehicles. The quest for higher efficiency, greater power density, and compact packaging demands thermal solutions that push beyond the capabilities of conventional manufacturing. This is where metal 3D baskı, or metal additive manufacturing (AM), offers a paradigm shift.
Limitations of Traditional Manufacturing for TIPs:
- Oyuncu seçimi: While suitable for complex shapes, casting often struggles with achieving thin walls consistently, can suffer from porosity (which hinders thermal conductivity), and typically requires secondary machining for precise interface surfaces. Material choices can also be limited.
- Machining (CNC): Offers high precision and excellent surface finish but becomes increasingly expensive and wasteful (subtracting material from a solid block) as geometric complexity increases. Creating intricate internal cooling channels is extremely difficult or impossible. Certain high-performance materials, like some copper alloys, can be challenging and costly to machine.
- Stamping: Cost-effective for high-volume production of simple, thin sheet metal parts, but severely limited in terms of geometric complexity, material thickness, and the ability to create 3D features or internal channels.
Advantages of Metal AM for EV Thermal Interface Plates:
Metal AM builds parts layer by layer directly from a digital model, offering unprecedented design freedom and enabling features specifically tailored for thermal performance:
- Unmatched Geometric Complexity: This is arguably the most significant advantage. AM allows for:
- Konformal Soğutma Kanalları: Internal channels can be designed to perfectly follow the contours of heat sources (like curved battery cells) or navigate tight spaces, maximizing heat transfer efficiency in ways impossible with drilling or casting.
- Complex Internal Structures: Features like internal fins, pins, or lattice structures can be integrated directly into the TIP to dramatically increase the surface area for heat exchange with a liquid coolant or even enhance heat spreading within the plate itself.
- Thin-Walled Designs: AM processes can create very thin, yet structurally sound, walls, reducing material usage, weight, and thermal resistance.
- Parça Konsolidasyonu: Multiple components (e.g., a base plate, flow channels, mounting brackets) can often be integrated into a single, monolithic printed part. This reduces assembly time, potential leak points, and tolerance stack-up issues, leading to a more reliable and potentially lower-cost final assembly.
- Hafifletme: AM enables advanced lightweighting strategies without compromising thermal function:
- Topology Optimization: Software algorithms can determine the most efficient material distribution for thermal and structural loads, removing unnecessary material.
- Kafes Yapılar: Replacing solid sections with internal lattice structures can significantly reduce weight while maintaining rigidity and potentially enhancing fluid flow if used within channels. This is crucial in EVs where overall vehicle weight directly impacts range.
- Hızlı Prototipleme ve Yineleme: AM allows designers to quickly produce and test multiple design variations of a TIP. Thermal performance can be empirically validated much faster than with traditional methods that require tooling or complex machining setups. This accelerates the development cycle for optimized thermal solutions, allowing automotive additive manufacturing suppliers to deliver results faster.
- Material Flexibility and Optimization: Metal AM processes, like Selective Laser Melting (SLM) / Laser Powder Bed Fusion (LPBF) or Selective Electron Beam Melting (SEBM), can work with a wide range of metal powders, including high-conductivity alloys like CuCrZr that are known for their excellent thermal properties but can be difficult to process conventionally. AM allows fine-tuning of process parameters to optimize the microstructure and thus the final properties (like thermal conductivity) of the printed material. Met3dp’s experience with diverse materials ensures optimal results.
- Customization and On-Demand Production: TIP designs can be easily tailored for specific EV models, battery pack configurations, or power electronic modules without the need for expensive retooling. This is ideal for niche applications, performance variants, or accommodating design updates during the vehicle lifecycle. It also facilitates on-demand production, reducing inventory requirements for manufacturing partners.
Comparison: Metal AM vs. Traditional Methods for TIP Manufacturing
Özellik | Metal Katmanlı Üretim (AM) | Geleneksel Döküm | Traditional Machining (CNC) | Traditional Stamping |
---|---|---|---|---|
Geometrik Karmaşıklık | Very High (internal channels, lattices, conformal) | Moderate (limited by mold design) | Moderate (limited by tool access) | Low (mostly 2D/2.5D shapes) |
Internal Channels | Easily integrated, complex paths possible | Difficult, requires complex cores/molds | Very difficult / Impossible | Impossible |
Duvar Kalınlığı | Can achieve very thin walls (<0.5mm possible) | Limited (typically >2-3mm) | Limited by tool size/rigidity | Defined by sheet thickness |
Parça Konsolidasyonu | High potential | Moderate potential | Low potential | Very Low Potential |
Hafifletme | Excellent (topology opt., lattices) | Sınırlı | Limited (material removal only) | Limited by sheet form |
Malzeme Atıkları | Low (powder is largely recyclable) | Moderate (runners, gates) | Yüksek (eksiltici süreç) | Moderate (offcuts) |
Prototipleme Hızı | Fast (days) | Slow (weeks/months for tooling) | Moderate (depends on complexity) | Slow (requires dies) |
Kalıp Maliyeti | Hiçbiri | High (molds) | Low (standard tools, fixtures needed) | High (dies) |
Malzeme Seçimi | Wide (incl. difficult-to-machine alloys) | Moderate (specific casting alloys) | Wide (but cost varies significantly) | Limited (ductile sheet metals) |
High-Conductivity Cu | Feasible (e.g., CuCrZr) | Possible but challenging | Possible but challenging/costly | Generally unsuitable |
Ideal Volume | Prototypes, Low-to-Medium Volume, Custom Parts | Medium-to-High Volume | Prototypes, Low-to-Medium Volume | Very High Volume |
Parça Başına Maliyet | Higher at low volume, potentially lower for complex | Lower at very high volume | Varies greatly with complexity | Very low at very high volume |
Sayfalara Aktar
By leveraging these advantages, metal AM empowers engineers to design and produce EV Thermal Interface Plates that offer superior thermal performance, reduced weight, and integrated functionality, directly contributing to the overall efficiency, reliability, and range of electric vehicles. Partnering with an experienced metal AM service provider like Met3dp ensures access to the technology and expertise needed to realize these benefits.
Recommended High-Conductivity Materials: CuCrZr and AlSi10Mg Spotlight
Selecting the right material is paramount when designing a Thermal Interface Plate (TIP), especially for demanding EV applications where efficient heat dissipation is non-negotiable. While many metals conduct heat, certain alloys stand out for their exceptional thermal properties combined with adequate mechanical strength and suitability for additive manufacturing processes. The key properties governing material choice for TIPs include:
- Thermal Conductivity (k): The most critical property, measuring the material’s ability to conduct heat. Higher values mean faster heat transfer. Measured in W/(m·K).
- Mechanical Strength (Yield Strength, Tensile Strength): The TIP must withstand mechanical loads from clamping forces, vibrations, and handling without deformation or failure.
- Density (ρ): Lower density contributes to lightweighting, crucial for overall vehicle efficiency. Measured in g/cm³.
- Termal Genleşme Katsayısı (CTE): Important for managing thermal stresses when interfacing with dissimilar materials across operating temperature ranges.
- Korozyon Direnci: Particularly relevant if the TIP interfaces with liquid coolants or operates in humid environments.
- Yazdırılabilirlik: The ease and reliability with which the material can be processed using metal AM techniques (e.g., LPBF, SEBM).
For high-performance EV TIPs manufactured via AM, two materials have garnered significant attention: Copper-Chromium-Zirconium (CuCrZr) ve Aluminum-Silicon-Magnesium (AlSi10Mg).
Copper Alloy Spotlight: CuCrZr (e.g., C18150)
Copper and its alloys are renowned for their excellent thermal and electrical conductivity, second only to silver. CuCrZr is a precipitation-hardenable copper alloy that offers a compelling combination of high conductivity and relatively good mechanical strength, especially after appropriate heat treatment.
- Kompozisyon: Primarily copper, with small additions of chromium (Cr ~0.5-1.2%) and zirconium (Zr ~0.03-0.3%).
- Termal İletkenlik: This is the standout feature. Depending on the exact condition (as-printed vs. heat-treated), CuCrZr can achieve thermal conductivity values significantly higher than aluminum alloys or steels, often in the range of 300-340 W/(m·K) after optimal heat treatment (solution annealing and aging). This is vastly superior to stainless steels (~15 W/(m·K)) or even many aluminum alloys.
- Mekanik Özellikler: In the as-printed state, strength is moderate. However, post-print heat treatments (solutionizing followed by precipitation hardening/aging) significantly increase yield strength (potentially >350-450 MPa) and tensile strength (>450-550 MPa) with acceptable ductility. This makes it robust enough for typical clamping and operational loads.
- Zorluklar ve Değerlendirmeler:
- Yazdırılabilirlik: Copper alloys have high reflectivity and thermal conductivity, making them traditionally challenging for Laser Powder Bed Fusion (LPBF) systems, as the laser energy is readily reflected or conducted away, requiring higher laser power and optimized parameters. They are also prone to oxidation, necessitating stringent control over the inert atmosphere in the build chamber.
- Isıl İşlem: Achieving the optimal combination of conductivity and strength requires specific post-processing heat treatments, adding steps and cost to the manufacturing workflow.
- Ideal Applications: Situations demanding the absolute highest rate of heat dissipation, where the superior thermal conductivity justifies the potentially higher material and processing costs. Examples include cooling high-flux power semiconductors in inverters or critical battery module interfaces where minimizing temperature gradients is essential for safety and longevity.
- Met3dp’s Advantage: Successfully printing high-quality CuCrZr parts requires both optimized printing systems and superior powder quality. Met3dp leverages its Gelişmiş Toz Üretim Sistemi, employing industry-leading gas atomization and potentially Plasma Rotating Electrode Process (PREP) technologies. These methods produce highly spherical CuCrZr powder with excellent flowability and low oxygen content, crucial for achieving dense, defect-free prints with consistent properties. Our deep understanding of material-process interactions allows us to tailor printing strategies for challenging materials like copper alloys.
Aluminum Alloy Spotlight: AlSi10Mg
AlSi10Mg is one of the most widely used aluminum alloys in additive manufacturing, particularly via LPBF. It’s essentially a casting alloy adapted for AM, offering a good balance of thermal properties, mechanical strength, low density, and excellent printability.
- Kompozisyon: Primarily aluminum, with silicon (~9-11%) and magnesium (~0.2-0.45%) as the main alloying elements.
- Termal İletkenlik: While significantly lower than CuCrZr, the thermal conductivity of AM AlSi10Mg is still good, typically in the range of 120-180 W/(m·K), depending on the post-processing condition (as-printed vs. stress-relieved or T6 heat treated). This is considerably better than steels and sufficient for many EV thermal management applications.
- Mekanik Özellikler: AlSi10Mg exhibits good strength-to-weight characteristics. As-printed parts often have high strength due to the rapid solidification inherent in AM, with yield strengths potentially exceeding 230-280 MPa and tensile strengths over 350-450 MPa. Heat treatments (like stress relief or T6) can modify these properties, often increasing ductility at the expense of some strength.
- Mükemmel Basılabilirlik: AlSi10Mg is known for its good processability with LPBF systems. It has good laser absorption characteristics and generally produces dense parts with relative ease compared to copper alloys.
- Hafif: With a density of approximately 2,67 g/cm³, it’s significantly lighter than CuCrZr (~8.8-8.9 g/cm³), contributing to vehicle weight reduction.
- Korozyon Direnci: Aluminum alloys naturally form a passive oxide layer, providing good corrosion resistance in typical operating environments.
- Maliyet-Etkinlik: Both the powder and the printing process for AlSi10Mg are generally more cost-effective than for CuCrZr.
- Ideal Applications: A versatile choice suitable for a wide range of TIP applications where its thermal conductivity is sufficient, and its low weight and cost-effectiveness are advantageous. This includes many battery module cooling plates, inverter housings with integrated cooling, and general heat sinks where extreme thermal flux is not the primary driver.
- Met3dp’s Expertise: Met3dp possesses extensive experience in optimizing the LPBF process for AlSi10Mg, ensuring high density, excellent mechanical properties, and dimensional accuracy. Our high-quality AlSi10Mg powders, produced under rigorous quality control, provide the foundation for reliable and repeatable manufacturing outcomes for our B2B clients seeking aluminum AM components.
Material Properties Comparison (Typical Values – Can Vary with Process/Treatment):
Mülkiyet | Birim | 3D Printed CuCrZr (Heat Treated) | 3D Printed AlSi10Mg (As-Printed/Stress Relieved) | Wrought Copper (C11000) | Wrought Aluminum (6061-T6) | Paslanmaz Çelik (316L) |
---|---|---|---|---|---|---|
Termal İletkenlik | W/(m-K) | ~300 – 340 | ~120 – 150 | ~390 | ~167 | ~15 |
Elektriksel İletkenlik | % IACS | ~80 – 90 | ~30 – 40 | ~100 | ~40 | ~2 |
Yoğunluk | g/cm³ | ~8.89 | ~2.67 | 8.94 | 2.70 | ~8.0 |
Akma Dayanımı (0,2% Ofset) | MPa | ~350 – 450+ | ~230 – 280+ | ~70 | ~276 | ~200 |
Nihai Çekme Dayanımı | MPa | ~450 – 550+ | ~350 – 450+ | ~220 | ~310 | ~520 |
Sertlik | HRB / HV | ~75-85 HRB / ~140-180 HV | ~100-120 HV | ~40 HRF | ~95 HB | ~79 HRB |
Erime Aralığı | °C | ~1070 – 1080 | ~570 – 615 | 1083 | 582 – 652 | ~1375 – 1400 |
CTE (20-100°C) | µm/(m·°C) | ~17.0 | ~21.5 | 16.5 | 23.6 | ~16.0 |
Sayfalara Aktar
Note: Values for 3D printed materials are highly dependent on process parameters, build orientation, and post-processing. These are representative figures.
The Critical Role of Powder Quality:
The success of manufacturing high-performance TIPs via metal AM relies heavily on the quality of the raw material – the metal powder. Key powder characteristics influencing the final part include:
- Parçacık Boyutu Dağılımı (PSD): Affects powder bed density and flowability.
- Küresellik: Highly spherical particles flow better and pack more densely, leading to lower porosity in the final part.
- Akışkanlık: Ensures uniform spreading of powder layers during the printing process.
- Purity / Low Oxygen Content: Contaminants, especially oxygen, can degrade mechanical properties and thermal conductivity. This is critical for reactive materials like aluminum and alloys prone to oxidation like copper.
Met3dp’s commitment to producing yüksek kaliteli metal tozları is central to our value proposition. Our advanced manufacturing processes, including sophisticated gas atomization units with unique nozzle designs and potentially PREP for ultimate purity and sphericity, ensure our powders meet the stringent requirements for demanding applications like EV thermal management. By controlling these powder characteristics, we enable our customers to 3D print dense, high-quality metal parts with superior, reliable thermal and mechanical properties, providing bulk metal powder supply tailored for additive manufacturing success. Choosing the right material, processed from high-quality powder on capable machinery, is the foundation for effective 3D printed thermal interface plates.
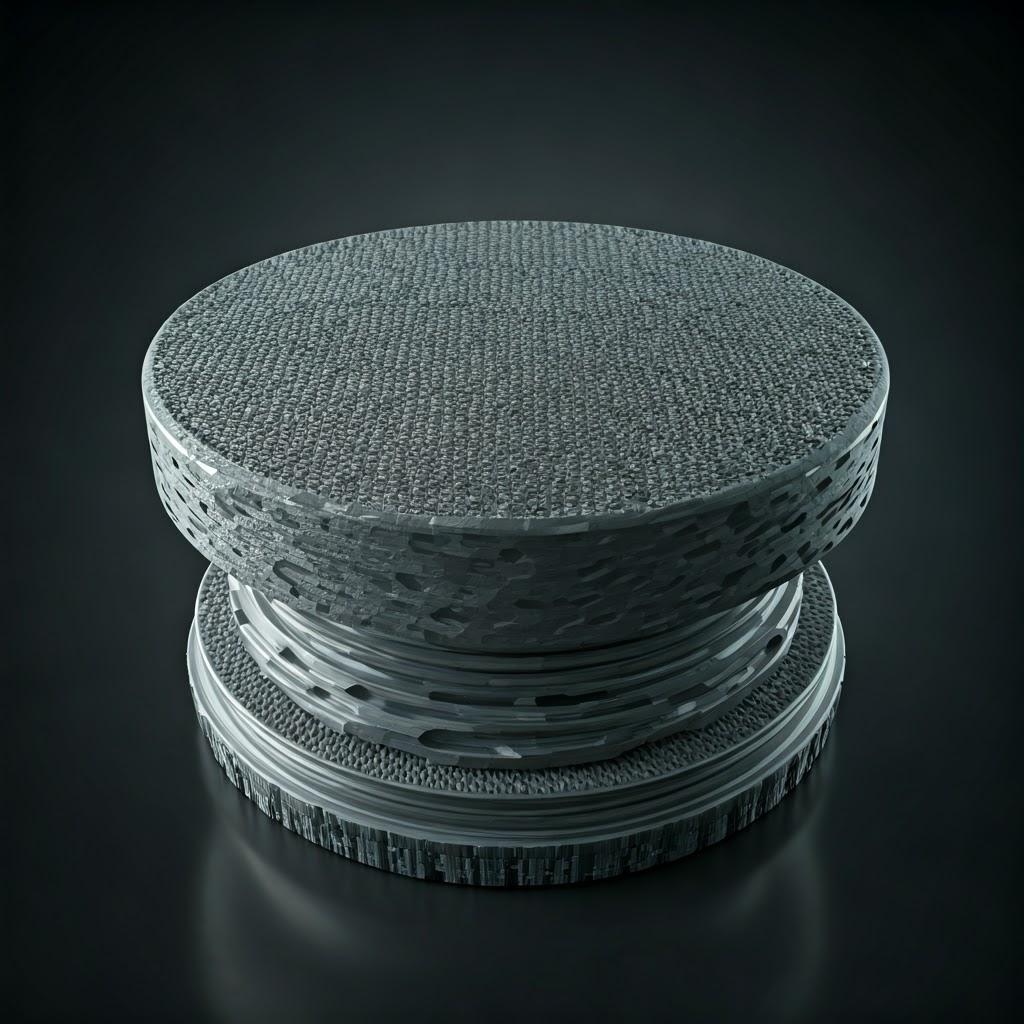
Design Considerations for Additively Manufactured Thermal Interface Plates
Leveraging the full potential of metal additive manufacturing (AM) for EV Thermal Interface Plates (TIPs) goes beyond simply replicating existing designs. It requires embracing Katmanlı Üretim Tasarımı (DfAM) principles – a design methodology that actively incorporates the unique capabilities and constraints of the AM process to optimize performance, reduce cost, and enhance manufacturability. For TIPs, DfAM focuses heavily on maximizing thermal efficiency while considering structural integrity, weight, and post-processing requirements. Engineers designing TIPs for AM should consider the following key aspects:
Optimizing Geometry for Heat Flow and Thermal Contact:
- Conformal Design: Unlike machined plates which are typically flat, AM allows the TIP surface to perfectly conform to the contours of the heat source (e.g., cylindrical battery cells, curved power module casings) and the heat sink/cold plate. This minimizes interfacial gaps and thermal contact resistance, significantly improving heat transfer efficiency. Designs should aim for maximum surface contact area on critical interfaces.
- Thin Walls: Metal AM can produce walls significantly thinner than casting, often below 1mm and potentially down to 0.3-0.5mm depending on the material, machine (like those offered by Met3dp), and geometry. Thin walls reduce the thermal resistance path through the TIP material itself and contribute to lightweighting. However, minimum thickness must also consider structural requirements and handling.
- Smooth Transitions & Filleting: Sharp internal corners can create stress concentrations and potentially hinder smooth fluid flow if internal channels are present. Incorporating fillets and smooth transitions in the design improves structural integrity and thermal performance. Avoid abrupt changes in cross-section where possible to manage thermal stresses during printing.
- Maximized Surface Area: Where applicable (e.g., interfacing with flowing air or liquid coolant), design features that maximize surface area for convective heat transfer. This could involve external fins or internal structures within cooling channels.
Incorporating Advanced Thermal Features:
- Internal Cooling Channels: This is a major advantage of AM. Channels can be designed with complex, non-linear paths to precisely target hotspots or navigate around other components.
- Microchannels: Very small channels (sub-millimeter) can dramatically increase the surface area-to-volume ratio for highly efficient liquid cooling, though pressure drop becomes a key design constraint.
- Optimized Channel Shapes: Channels don’t have to be circular; elliptical, rectangular, or bio-inspired shapes (like treelike branching) can be used to optimize flow and heat transfer for specific conditions. Computational Fluid Dynamics (CFD) simulations are invaluable here.
- Integrated Manifolds: Inlet and outlet manifolds for coolant flow can be directly integrated into the TIP design, reducing the need for separate components and potential leak points.
- Internal Structures (Pins, Fins, Tripods): For conduction-dominated interfaces, internal structures like pins or tripods can enhance thermal contact pressure and provide alternative heat paths, particularly useful when dealing with non-flat surfaces or thermal interface materials (TIMs). AM allows these to be intricate and precisely placed.
- Lattice Structures / Cellular Materials: Replacing solid sections of the TIP with optimized lattice structures offers several benefits:
- Hafifletme: Significant weight reduction while maintaining tailored stiffness and strength.
- Enhanced Convection: If designed for fluid flow, lattices can induce turbulence and increase surface area, improving heat transfer to a coolant. TPMS (Triply Periodic Minimal Surfaces) lattices are particularly interesting for their high surface area and good structural properties.
- Vibration Damping: Lattices can offer better vibration damping characteristics compared to solid materials.
Wall Thickness, Feature Size, and Overhangs:
- Minimum Özellik Boyutu: AM processes have limitations on the smallest features they can reliably produce (e.g., hole diameter, wall thickness, pin size). This depends on the specific AM technology (LPBF typically offers finer resolution than SEBM), laser/beam spot size, layer thickness, and material. Designers must be aware of the specific machine capabilities (e.g., Met3dp’s printer specifications) when designing fine features.
- Kendini Destekleyen Açılar: AM requires support structures for overhanging features below a certain angle relative to the build plate (typically <45 degrees for most metal processes). Designing features with angles above this threshold (“self-supporting angles”) drastically reduces the need for supports, simplifying post-processing and reducing material waste. Where overhangs are necessary, consider designing them to be easily accessible for support removal.
- Hole Orientation: Vertical holes generally print with better accuracy and roundness than horizontal holes, which may require supports and might exhibit a slightly elliptical shape due to the layered construction.
Destek Yapısı Stratejisi:
Support structures are often necessary evils in metal AM. They anchor the part to the build plate, support overhangs, and help conduct heat away during the printing process, mitigating warping. However, they consume extra material, add print time, and require removal in post-processing, which can leave witness marks.
- Minimize Supports on Critical Surfaces: Avoid placing supports on functional interfaces (where the TIP contacts the heat source or sink) or within complex internal channels if possible, as removal can be difficult and potentially damage the surface or affect flatness.
- Design for Removal: When supports are unavoidable, design them for easier access and removal (e.g., using supports with smaller contact points, ensuring line-of-sight for tools). Sometimes, incorporating features into the design specifically to aid support removal is beneficial.
- Orientation Optimization: The orientation of the part on the build plate significantly impacts support locations, surface finish on different faces, print time, and potential for distortion. Software tools can help find the optimal orientation based on minimizing supports, maximizing surface quality, or reducing thermal stress.
Utilizing Simulation:
Given the complexities of heat transfer and fluid flow in advanced TIP designs, simulation tools are essential during the DfAM process:
- Thermal Simulation (FEA): Predicts temperature distributions, identifies hotspots, and evaluates the overall thermal resistance of the TIP design under operating conditions. Allows comparison of different design iterations virtually.
- Computational Fluid Dynamics (CFD): Models fluid flow (coolant) through internal channels, predicts pressure drop, and analyzes convective heat transfer coefficients. Essential for optimizing channel geometry and lattice structures for liquid or air cooling.
- Topology Optimization: Software automatically optimizes material layout within a defined design space based on structural loads, thermal loads, and performance objectives (e.g., minimize thermal resistance, minimize weight). This often results in organic-looking, highly efficient structures well-suited for AM.
By carefully considering these DfAM principles, engineers can unlock the full potential of metal AM to create EV Thermal Interface Plates that are not just manufactured differently, but perform significantly better than their traditionally made counterparts, directly impacting EV performance and reliability. Collaboration with experienced AM providers like Met3dp early in the design phase can provide valuable insights into process capabilities and limitations.
Achieving Precision: Tolerance, Surface Finish, and Dimensional Accuracy in 3D Printed TIPs
While metal additive manufacturing offers unparalleled design freedom, achieving the required precision for functional components like EV Thermal Interface Plates is critical. Engineers and procurement managers need a clear understanding of the typical tolerances, surface finish, and overall dimensional accuracy achievable with metal AM, as well as the factors influencing these characteristics. These aspects directly impact the TIP’s fit, assembly, and most importantly, its thermal performance at critical interfaces.
Typical Tolerances in Metal AM:
The achievable dimensional tolerances depend heavily on the specific AM process (LPBF generally offers tighter tolerances than SEBM or DED), the material being printed, the size and complexity of the part, the quality and calibration of the AM machine, and post-processing steps.
- General Tolerances (LPBF): For well-controlled processes and medium-sized parts, typical tolerances are often in the range of ±0.1 mm to ±0.2 mm for the initial few centimeters, with an additional tolerance per centimeter of length (e.g., ±0.002 mm/mm). Smaller features might achieve tighter tolerances (e.g., ±0.05 mm).
- Large Parts: Achieving tight tolerances across large parts (e.g., >300-500 mm) is more challenging due to cumulative thermal effects (shrinkage, warping).
- Post-Machining: For critical dimensions, particularly mating surfaces requiring high flatness or specific fits, post-print CNC machining is often employed to achieve much tighter tolerances, potentially down to ±0.01 mm to ±0.05 mm or better, similar to conventional machining capabilities.
Factors Influencing Dimensional Accuracy:
- Thermal Shrinkage and Stress: As the molten metal solidifies and cools layer by layer, it shrinks. Non-uniform cooling leads to internal stresses, which can cause warping and distortion, affecting final dimensions. Material properties (CTE), scan strategy, and support structures play a crucial role here.
- Machine Calibration: Accurate laser/beam positioning, spot size consistency, and layer thickness control are fundamental. Regular calibration and maintenance of the AM system are essential.
- Süreç Parametreleri: Laser power, scan speed, hatch spacing, and gas flow (in LPBF) significantly influence the melt pool dynamics, solidification rate, and resulting microstructure, all of which can affect dimensional accuracy and stability.
- Toz Özellikleri: Consistent powder quality (PSD, morphology, flowability) ensures uniform layer spreading and predictable melting behavior.
- Part Geometry and Orientation: Complex geometries and the orientation on the build plate influence heat buildup, support requirements, and potential for distortion.
Surface Finish (Roughness – Ra):
Surface finish is particularly critical for TIPs because rough surfaces increase thermal contact resistance. Roughness traps air in the valleys between mating surfaces, hindering heat flow. A smoother surface allows for more intimate contact and better thermal transfer, especially when used with Thermal Interface Materials (TIMs).
- As-Printed Surface Finish: The surface roughness (Ra) of as-printed metal AM parts is typically higher than machined surfaces.
- LPBF: Typical Ra values range from 5 µm to 20 µm, depending on material, parameters, and surface orientation.
- Vertical Walls: Generally exhibit lower Ra compared to up-facing or down-facing surfaces.
- Down-Facing Surfaces (Supported): Often show the highest roughness due to contact with support structures. Witness marks from support removal can also affect local roughness.
- Up-Facing Surfaces: Can be smoother but may exhibit some “stair-stepping” effects depending on the layer thickness and surface curvature.
- Powder Particle Size: Finer powders generally lead to smoother finishes but may have flowability challenges.
- Yüzey İşleminin İyileştirilmesi:
- Oryantasyon: Orienting critical surfaces vertically or as up-facing surfaces can yield better as-printed finishes.
- Parametre Optimizasyonu: Fine-tuning process parameters can influence surface melt behavior.
- İşlem sonrası: Essential for achieving smooth finishes comparable to machining. Steps like bead blasting, sandblasting, polishing, electropolishing, or micro-machining can significantly reduce Ra values, often down to <1 µm or even lower if required.
Metrology and Quality Assurance:
Verifying that the printed TIP meets the specified dimensional and surface finish requirements is crucial. Common metrology techniques include:
- Coordinate Measuring Machines (CMMs): Provide highly accurate point measurements for verifying critical dimensions, flatness, and geometric tolerances.
- 3D Laser Scanning / Structured Light Scanning: Capture the full geometry of the part, allowing comparison to the original CAD model and detailed analysis of deviations, warping, and surface profiles.
- Surface Profilometers: Measure surface roughness (Ra, Rz, etc.) on specific areas.
- Tahribatsız Muayene (NDT): Techniques like CT scanning can be used to inspect internal features (like channels) and detect internal porosity.
Met3dp, serving demanding industries such as aerospace, medical, and automotive, understands the paramount importance of precision and reliability. Our commitment extends from utilizing high-quality powders and industry-leading printing equipment to implementing rigorous quality control processes. We work closely with clients to define achievable tolerances and surface finish requirements, leveraging process optimization and appropriate post-processing routes to deliver mission-critical components that meet stringent specifications. Ensuring dimensional accuracy and appropriate surface finish is integral to the value proposition found across the solutions offered on the Met3dp website.
Procurement Considerations:
When sourcing 3D printed TIPs, procurement managers should clearly specify required tolerances (using Geometric Dimensioning and Tolerancing – GD&T standards), critical surface finish values (Ra), and inspection requirements in technical drawings and requests for quotation (RFQs). Understanding the interplay between design complexity, material choice, AM process capabilities, and post-processing is key to managing expectations and ensuring the final component meets the demanding functional requirements of EV thermal management systems.
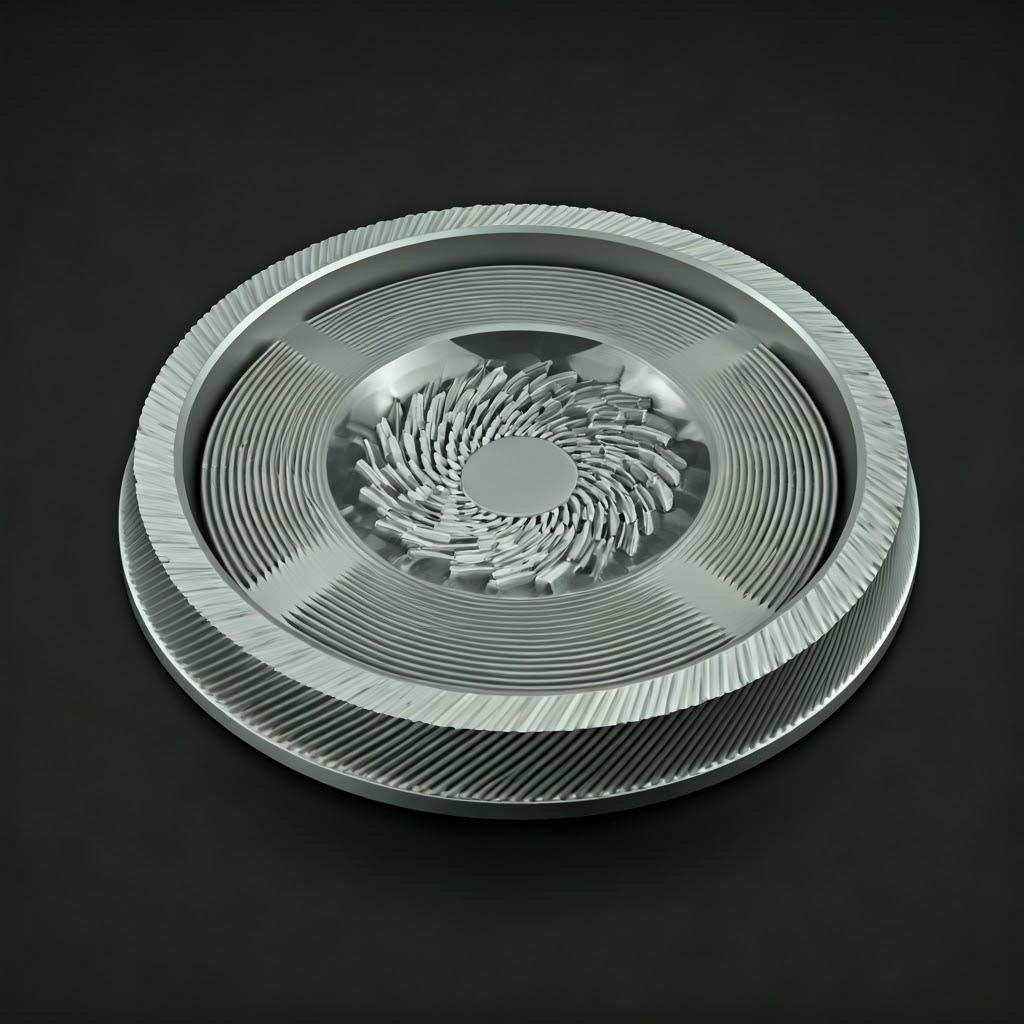
Post-Processing Pathways for Enhanced TIP Performance and Reliability
Producing a Thermal Interface Plate using metal additive manufacturing rarely stops when the part comes out of the printer. For the vast majority of engineering applications, particularly demanding ones like EV thermal management, post-processing is an essential sequence of steps required to transform the as-printed component into a functional, reliable part that meets all performance specifications. As-printed parts often possess internal stresses, require support structures to be removed, may not meet final tolerance or surface finish requirements, and might need property enhancement (especially for alloys like CuCrZr).
Understanding the typical post-processing workflow is crucial for engineers designing the parts (to facilitate these steps) and for procurement managers evaluating suppliers and understanding total manufacturing time and cost. The specific steps depend heavily on the material used (e.g., CuCrZr vs. AlSi10Mg), the complexity of the part, and the application requirements.
Common Post-Processing Steps for 3D Printed Metal TIPs:
- Stres Giderici / Isıl İşlem: This is often one of the first steps after printing, usually performed while the part is still attached to the build plate.
- Amacımız: The rapid heating and cooling cycles inherent in AM create significant internal stresses within the part. These stresses can cause distortion during removal from the build plate or later in the component’s life. Heat treatment relaxes these stresses. For certain alloys, it’s also crucial for achieving desired microstructures and properties.
- AlSi10Mg: Typically undergoes a stress relief cycle (e.g., 2-3 hours at ~300°C) to reduce internal stresses and stabilize the microstructure without significantly altering mechanical properties. A T6 heat treatment (solutionizing + aging) can also be applied to improve ductility, although potentially reducing strength slightly and affecting thermal conductivity.
- CuCrZr: Heat treatment is critical for developing its high thermal conductivity and mechanical strength. This usually involves a two-step process:
- Çözelti Tavlama: Heating to a high temperature (~950-1000°C) to dissolve the Cr and Zr precipitates into the copper matrix, followed by rapid quenching.
- Precipitation Hardening (Aging): Reheating to a lower temperature (~450-550°C) for a specific duration allows fine Cr and Zr precipitates to form, which strengthen the material and simultaneously allow for high thermal/electrical conductivity. Precise control of this process is vital.
- Atmosphere Control: Heat treatments are typically performed in vacuum furnaces or controlled inert atmospheres (like argon or nitrogen) to prevent oxidation, especially critical for copper alloys.
- Yapı Plakasından Çıkarma: Once heat treated (if applicable), the part needs to be separated from the build plate it was printed on.
- Yöntemler: This is commonly done using wire Electrical Discharge Machining (wire EDM) or a bandsaw. Wire EDM offers a precise cut close to the part’s base, minimizing material waste and subsequent machining needs.
- Destek Yapısının Kaldırılması: This can be one of the most labor-intensive and delicate post-processing steps.
- Yöntemler: Depending on the design and location, supports might be removed manually (using pliers, cutters), via CNC machining, or sometimes using electrochemical methods. Access can be challenging, especially for internal supports within complex channels.
- Surface Impact: Support removal inevitably leaves witness marks or scars on the surfaces where they were attached. These areas often require additional finishing steps if surface quality is critical. Designing supports for easy removal (see DfAM section) is highly beneficial.
- CNC İşleme: Even with the precision of modern AM systems, critical features often require secondary machining to meet tight tolerances or specific surface requirements.
- Amacımız: Achieving critical flatness on mating surfaces (essential for low thermal contact resistance), machining precise hole diameters and locations, creating threaded holes, or achieving very smooth surface finishes (low Ra) on specific areas.
- Düşünceler: Requires careful fixture design to hold the potentially complex AM part securely without distortion. Sufficient stock material must be included in the AM design on surfaces that require machining.
- Yüzey İşlemi: Various techniques can be used to achieve the desired surface texture, cleanliness, or aesthetic appearance.
- Abrasive Blasting (Bead/Sand Blasting): Propels media against the surface to create a uniform, clean, matte finish. Can help remove loosely attached powder particles and slightly reduce surface roughness. Choice of media (glass beads, aluminum oxide) affects the resulting finish.
- Yuvarlama / Vibrasyonlu Son İşlem: Uses abrasive media in a rotating or vibrating bowl to deburr edges and smooth surfaces, particularly effective for batches of smaller parts.
- Parlatma: Mechanical or electrochemical polishing can achieve very smooth, mirror-like finishes (Ra < 0.1 µm) where extremely low thermal contact resistance or specific optical properties are needed.
- Micro-Machining: Can achieve highly controlled surface textures or finishes on specific areas.
- Coatings and Surface Treatments: Applying coatings can enhance specific properties.
- Korozyon Direnci: Anodizing (for aluminum alloys like AlSi10Mg), Nickel plating, or specialized paints/coatings can protect the TIP from corrosive coolants or environments.
- Improved Thermal Interface: Certain coatings can act as integrated TIMs or improve wetting/adhesion for subsequently applied TIMs.
- Wear Resistance / Hardness: Hard coatings might be applied if the TIP experiences wear.
- Cleaning and Inspection: Final cleaning to remove any machining fluids, blasting media, or contaminants is essential. Final inspection (dimensional, visual, NDT if required) verifies that the part meets all specifications before shipment.
Workflow Examples:
- AlSi10Mg TIP (Moderate Tolerance): Print -> Stress Relief (on plate) -> Wire EDM from plate -> Support Removal (manual/machined) -> Bead Blasting -> Final Inspection.
- CuCrZr TIP (High Performance/Tight Tolerance): Print -> Solution Anneal + Age Heat Treatment (on plate or after removal depending on stress) -> Wire EDM from plate -> Support Removal (careful, potentially machined) -> CNC Machining (critical faces for flatness/Ra) -> Optional Polishing/Coating -> Final Inspection.
Supplier Capability:
Bir seçim yaparken metal AM manufacturing partner, it’s crucial to assess their post-processing capabilities. Do they perform these steps in-house, or do they manage a network of trusted subcontractors? Met3dp understands that post-processing is integral to delivering a finished component and works with clients to define the most efficient and effective pathway, ensuring the final TIP meets all functional requirements. Managing this entire workflow is key to providing a reliable component supply solution for B2B customers.
Navigating Common Challenges in Printing EV Thermal Interface Plates
While metal additive manufacturing unlocks significant possibilities for EV Thermal Interface Plates, it’s not without its challenges. Understanding these potential hurdles and the strategies employed by experienced additive manufacturing service providers like Met3dp to overcome them is crucial for ensuring successful outcomes, particularly when dealing with high-conductivity materials and complex geometries.
1. Warping and Distortion:
- Meydan okumak: The intense localized heating from the laser or electron beam, followed by rapid cooling and solidification, creates significant thermal gradients within the part during the build process. This leads to the buildup of internal residual stresses. If these stresses exceed the material’s yield strength at elevated temperatures, the part can warp, distort, or even crack, especially in large, flat geometries typical of some TIP designs or parts with significant variations in cross-section. High-conductivity materials like CuCrZr can exacerbate this due to faster heat dissipation, potentially leading to steeper gradients.
- Mitigation Strategies:
- Optimized Part Orientation: Orienting the part to minimize large flat areas parallel to the build plate and reduce thermal mass concentrations.
- Sağlam Destek Yapıları: Well-designed supports anchor the part securely to the build plate and act as heat sinks, helping to manage thermal gradients more effectively.
- Süreç Parametre Optimizasyonu: Tailoring laser/beam power, scan speed, and scan strategy (e.g., island scanning, layer staggering) to minimize localized overheating and achieve more uniform cooling.
- Termal Simülasyon: Using simulation tools during the design phase to predict areas prone to high stress and modify the design or support strategy accordingly.
- Stress Relief Heat Treatment: Performing this step promptly after printing (often while still on the build plate) is critical for relaxing residual stresses before they cause distortion during removal or machining.
2. Support Structure Removal Complexity:
- Meydan okumak: While essential, support structures can be difficult and time-consuming to remove, especially from intricate internal channels, delicate features, or difficult-to-access areas common in optimized TIP designs. Improper removal can damage the part surface, compromise feature integrity, or leave residual material affecting fluid flow or thermal contact.
- Mitigation Strategies:
- DfAM for Support Reduction: Designing parts with self-supporting angles (>45°) wherever possible, using internal channels shaped to avoid needing extensive internal supports (e.g., teardrop shapes for horizontal channels).
- Support Optimization Software: Utilizing advanced software features to generate supports that are strong where needed but have weaker, easily breakable connection points to the part itself.
- Strategic Orientation: Choosing a build orientation that minimizes the need for supports on critical or hard-to-reach surfaces.
- Access Planning: Ensuring the design allows physical or tool access for support removal. Sometimes sacrificial features are added solely to provide access or break points.
- Post-Processing Method Selection: Choosing appropriate removal methods (manual, machining, potentially electrochemical polishing for some materials/geometries).
3. Achieving Full Density and Avoiding Porosity:
- Meydan okumak: Porosity (the presence of small voids within the printed material) is detrimental to both the mechanical integrity and the thermal conductivity of a TIP. Voids act as insulators, impeding heat flow, and can serve as initiation sites for cracks under stress. Porosity can arise from several sources:
- Lack of Fusion: Insufficient energy input fails to completely melt the powder particles or fuse adjacent layers/tracks.
- Keyhole Porosity: Excessive energy density creates a vapor depression that becomes unstable and collapses, trapping gas within the solidifying metal.
- Gas Porosity: Gas trapped within the powder particles or dissolved in the melt pool gets trapped during rapid solidification.
- Mitigation Strategies:
- Yüksek Kaliteli Toz: Using powder with high sphericity, good flowability, controlled particle size distribution, and low internal gas content (like those produced by Met3dp’s advanced atomization) is fundamental.
- Process Parameter Development: Rigorous optimization of parameters (laser power, scan speed, layer thickness, hatch spacing, focus) specific to the material and machine to ensure stable melt pool dynamics and complete fusion. This often involves extensive Design of Experiments (DoE).
- Atmosphere Control: Maintaining a high-purity inert gas atmosphere (e.g., Argon) in the build chamber minimizes oxidation and contamination that can lead to porosity.
- Kalite Kontrol: Employing NDT methods like CT scanning for critical parts to inspect for internal porosity. Density measurements (e.g., using the Archimedes method) are also common QC checks.
4. Powder Handling and Safety:
- Meydan okumak: Many metal powders used in AM, particularly reactive materials like aluminum and titanium alloys, pose safety risks (flammability, explosibility) and health hazards if not handled correctly. Maintaining powder purity and preventing cross-contamination between different material types is also crucial. Copper powders, while less reactive than aluminum, still require careful handling to avoid oxidation.
- Mitigation Strategies:
- Controlled Environments: Handling powders in controlled areas with appropriate ventilation, grounding, and spark prevention measures.
- Kişisel Koruyucu Ekipman (KKE): Use of respirators, gloves, eye protection, and conductive clothing.
- Inert Gas Handling: Sieving, loading, and storing reactive powders under an inert gas atmosphere whenever possible.
- Toz Yaşam Döngüsü Yönetimi: Strict procedures for tracking powder usage, recycling unused powder (after quality checks), and preventing cross-contamination through dedicated equipment or thorough cleaning protocols. Met3dp employs rigorous safety and handling protocols aligned with industry best practices.
5. Material Consistency and Repeatability:
- Meydan okumak: Ensuring that every TIP produced has consistent material properties (thermal conductivity, mechanical strength) and dimensional accuracy, both within a single build and from batch to batch, is essential for reliable series production. Variations can arise from powder batch differences, machine drift, or slight environmental changes.
- Mitigation Strategies:
- Powder Quality Control: Stringent testing and certification of incoming powder batches. Careful management of recycled powder.
- Machine Calibration and Monitoring: Regular calibration of laser/beam systems, galvo scanners, and gas flow. In-process monitoring techniques (e.g., melt pool monitoring) can provide real-time quality feedback.
- Standardized Procedures: Implementing robust Standard Operating Procedures (SOPs) for machine setup, operation, and post-processing.
- Statistical Process Control (SPC): Monitoring key process variables and part characteristics to detect and correct drift over time.
- Traceability: Maintaining detailed records linking specific parts to powder batches, machine parameters, and operator logs.
By acknowledging these challenges and implementing robust mitigation strategies rooted in deep process understanding, material science expertise, and rigorous quality control, experienced providers like Met3dp can reliably deliver high-performance, 3D printed EV Thermal Interface Plates that meet the demanding requirements of the automotive industry.
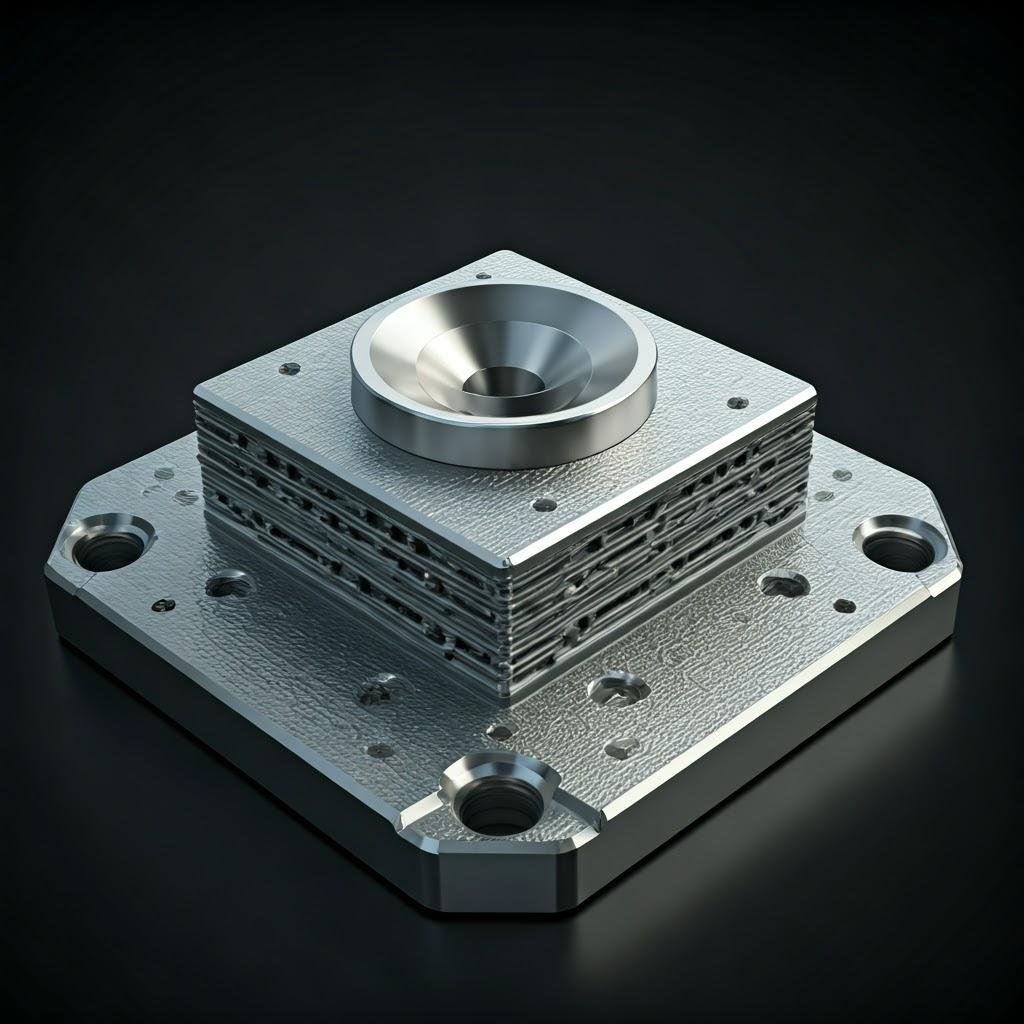
Selecting the Right Metal 3D Printing Partner for EV Components
Choosing the right manufacturing partner is as critical as perfecting the design or selecting the optimal material for your EV Thermal Interface Plates (TIPs). The unique demands of additive manufacturing, especially with advanced materials like high-conductivity alloys for critical applications, necessitate a partner with specific expertise, robust processes, and a commitment to quality. For engineers and procurement managers navigating the landscape of metal AM service providers, evaluating potential partners based on a defined set of criteria is essential for mitigating risks and ensuring project success.
Here are key factors to consider when selecting a metal 3D printing partner for demanding EV components like TIPs:
1. Material Expertise and Access:
- Proven Experience: Does the provider have demonstrable experience printing the specific alloys required (CuCrZr, AlSi10Mg, or others)? Ask for case studies, sample parts, or material datasheets derived from their process.
- Powder Sourcing and Quality Control: Where do they source their powders? Do they have rigorous incoming quality control checks for powder characteristics (PSD, morphology, chemistry, flowability)? A partner like Met3dp, which manufactures its own yüksek kaliteli metal tozları using advanced techniques like gas atomization and PREP, offers significant advantages in material consistency and traceability.
- Material Portfolio Breadth: While your current need might be specific, does the partner work with a range of materials? This indicates broader expertise and potential flexibility for future projects. Met3dp’s portfolio includes not only common alloys but also innovative materials like TiNi, TiTa, TiAl, and superalloys.
2. Technological Capability and Capacity:
- Appropriate Printing Technology: Do they possess the right AM technology for your needs? Laser Powder Bed Fusion (LPBF/SLM) is commonly used for high-resolution TIPs made from AlSi10Mg and CuCrZr. Selective Electron Beam Melting (SEBM) might be advantageous for other materials (like pure copper or refractory metals) due to its vacuum environment and higher power. Understanding the nuances of different baskı yöntemleri and ensuring the partner has well-maintained, industrial-grade machines is vital.
- Machine Quality and Calibration: Are their machines from reputable manufacturers? What are their calibration and maintenance schedules? Consistency starts with reliable equipment.
- Build Volume and Capacity: Can their machines accommodate the size of your TIP? Do they have sufficient machine capacity to handle your prototyping volumes and potentially scale to low-to-medium series production, meeting required lead times?
3. Industry Experience and Understanding:
- Automotive Sector Experience: Does the provider understand the specific requirements and quality expectations of the automotive industry? Familiarity with concepts like PPAP (Production Part Approval Process), APQP (Advanced Product Quality Planning), and traceability is advantageous, even if full IATF 16949 certification isn’t always mandatory for prototype suppliers.
- Thermal Management Application Knowledge: Have they worked on similar thermal management components before? Understanding the functional requirements of a TIP beyond just the geometry is beneficial for DfAM collaboration and troubleshooting.
4. Quality Management Systems:
- Sertifikalar: Is the provider certified to relevant quality standards, such as ISO 9001? While IATF 16949 certification is more common for high-volume automotive suppliers, ISO 9001 demonstrates a fundamental commitment to quality processes, documentation, and continuous improvement, crucial for reliable B2B component supply.
- Süreç Kontrolü: What measures do they take to monitor and control the printing process in real-time (e.g., melt pool monitoring, sensor data)?
- Inspection Capabilities: Do they have the necessary metrology equipment (CMM, 3D scanners, surface profilometers) and NDT capabilities (e.g., CT scanning for internal inspection) in-house or through certified partners?
5. Post-Processing Capabilities:
- Comprehensive Services: As discussed previously, post-processing is critical. Does the partner offer the required steps (heat treatment, machining, surface finishing, coating) in-house? If not, do they have a well-managed and qualified network of subcontractors? A single point of contact managing the entire workflow simplifies procurement and ensures accountability.
- Expertise in Finishing: Do they have specific expertise in the required post-processing, such as the complex heat treatment cycles for CuCrZr or precision machining of AM parts?
6. Technical Support and Collaboration:
- DfAM Assistance: Does the provider offer design support or consultation to help optimize your TIP design for additive manufacturing, improving performance and reducing cost?
- Application Development: Are they willing to collaborate on developing novel solutions or tackling challenging requirements? Met3dp prides itself on partnering with organizations to accelerate their digital manufacturing transformations.
- Communication and Project Management: Is their communication clear, responsive, and professional? Do they have effective project management processes?
7. Lead Time, Scalability, and Cost:
- Realistic Lead Times: Do they provide clear and realistic lead time estimates for quoting, production, and post-processing?
- Ölçeklenebilirlik: Can they support your project from initial prototypes through to potential low or medium-volume production runs? What is their plan for scaling capacity if needed?
- Transparent Pricing: Is their pricing structure clear and detailed? Do they offer competitive pricing relative to the quality and service provided? (See next section for more on cost).
Questions to Ask Potential Metal AM Partners:
- Can you provide examples/case studies of similar parts you’ve printed in [specific material, e.g., CuCrZr]?
- What is your process for qualifying and testing incoming metal powders?
- Describe your quality management system and relevant certifications.
- What AM machines do you operate, and what are their build volumes and typical tolerances?
- What post-processing steps do you perform in-house versus subcontract?
- How do you ensure part density and manage residual stress?
- Can you provide DfAM feedback on our initial design?
- What are your standard lead times for prototypes vs. small series production?
- What inspection methods will be used to verify our part requirements?
- Can you support PPAP documentation if required for future production phases?
Selecting the right partner is an investment in the success of your project. A capable, communicative, and quality-focused supplier like Met3dp, with integrated capabilities spanning materials, equipment, and application expertise, can significantly de-risk the adoption of metal AM for critical components like EV Thermal Interface Plates.
Understanding Cost Factors and Lead Times for 3D Printed TIPs
For procurement managers and engineers evaluating the feasibility of using metal additive manufacturing for EV Thermal Interface Plates, a clear understanding of the cost structure and typical lead times is essential. While AM offers significant performance and design advantages, its cost dynamics differ from traditional manufacturing methods.
Breakdown of Cost Components in Metal AM:
The final price of a 3D printed metal TIP is influenced by several key factors:
- Malzeme Maliyeti:
- Powder Price: The cost per kilogram of the metal powder. High-performance alloys like CuCrZr are generally significantly more expensive than more common alloys like AlSi10Mg or stainless steels.
- Part Volume/Weight: The amount of powder directly consumed to build the part.
- Support Structure Volume: Powder used for support structures also contributes to material cost, though unused powder within the build chamber is largely recyclable.
- Powder Refresh Rate: A certain percentage of recycled powder is often mixed with virgin powder, affecting overall material cost over time.
- Machine Time (Amortization & Operation):
- Yapım süresi: This is often the largest cost driver. It depends on:
- Part Height: Primarily determines the number of layers and thus build duration. Taller parts take longer.
- Part Volume/Area per Layer: Influences the time spent scanning each layer.
- Karmaşıklık: Intricate features or extensive support structures can increase print time.
- Nesting Efficiency: Printing multiple parts simultaneously in one build (nesting) can reduce cost per part by optimizing machine utilization.
- Machine Cost Amortization: Industrial metal AM systems represent a significant capital investment, and their hourly operating rate reflects this.
- Consumables: Costs associated with filters, inert gas (Argon/Nitrogen), and machine wear.
- Yapım süresi: This is often the largest cost driver. It depends on:
- İşçilik Maliyetleri:
- Setup & Teardown: Preparing the build file, setting up the machine, loading powder, removing the finished build, and initial cleaning.
- Post-Processing Labor: Manual support removal, machining setup and operation, finishing tasks (blasting, polishing), inspection. This can be a significant cost component, especially for complex parts or those requiring extensive finishing.
- İşlem Sonrası Maliyetler:
- Isıl İşlem: Costs associated with furnace time, energy consumption, and controlled atmospheres (vacuum/inert gas).
- İşleme: Costs based on CNC machine time, tooling, and programming/setup.
- Surface Finishing/Coating: Costs associated with specific treatments like blasting, polishing, plating, or anodizing.
- Quality Assurance and Inspection:
- Metroloji: Costs for CMM measurements, 3D scanning, or surface roughness checks.
- NDT: Costs for non-destructive testing like CT scanning, if required for critical internal inspection.
- Documentation: Costs associated with generating quality reports or certifications.
- Design Complexity & DfAM:
- Support Requirements: Designs requiring extensive or difficult-to-remove supports increase both material cost and post-processing labor. DfAM optimization can significantly reduce this.
- Wall Thickness/Features: Very fine features or thin walls might require slower printing speeds or specific parameters, potentially increasing machine time.
Factors Influencing Lead Times:
Lead time refers to the total time from order placement (or RFQ submission) to receiving the finished parts. Key influencing factors include:
- Quotation Time: Providers need time to analyze the design, plan the build layout, estimate post-processing, and generate a quote (typically 1-5 business days).
- Design Review & Preparation: Time for potential DfAM feedback, file preparation (support generation, slicing), and build planning.
- Machine Queue/Availability: The provider’s current workload and machine availability significantly impact when a build can be started. This is often the most variable factor.
- Print Time: The actual duration of the AM build process (can range from hours for small parts to several days for large or complex builds).
- Post-Processing Time: Can vary significantly depending on the required steps. Heat treatment cycles take hours, extensive CNC machining can take hours or days, and complex support removal adds time. Outsourced steps add logistical time. (Can range from 1-2 days to 1-2 weeks or more).
- Quality Control & Shipping: Time for final inspection, packaging, and transit.
Typical Timelines (Estimates):
- Prototypes (1-10 units): Often 1-4 weeks, depending heavily on complexity, material, post-processing, and current queue. Expedited services may be available at higher cost.
- Low-Volume Series (10-100+ units): Lead times might extend to 4-8 weeks or more, requiring dedicated machine time and potentially batch processing through post-processing steps. Planning and forecasting are crucial here.
Strategies for Cost and Lead Time Optimization:
- Design for Additive Manufacturing (DfAM): Optimizing the design to reduce supports, minimize build height (if possible), consolidate parts, and facilitate post-processing is the most effective strategy.
- Malzeme Seçimi: Choose the most cost-effective material that meets performance requirements (e.g., use AlSi10Mg if CuCrZr’s extreme conductivity isn’t strictly necessary).
- Batching Orders: Ordering multiple parts (identical or different) to be printed in the same build (nesting) improves machine utilization and often reduces the cost per part.
- Relax Tolerances/Finishes: Only specify tight tolerances and fine finishes on critical features where functionally required; relaxing requirements on non-critical areas reduces post-processing needs.
- Clear Communication: Providing clear drawings (GD&T), specifications, and requirements upfront streamlines the quoting and production process.
Experienced metal AM solution providers like Met3dp work transparently with clients, providing detailed quotes outlining cost drivers and realistic lead times. They can also offer valuable DfAM advice to help optimize designs for cost-effectiveness without compromising performance.
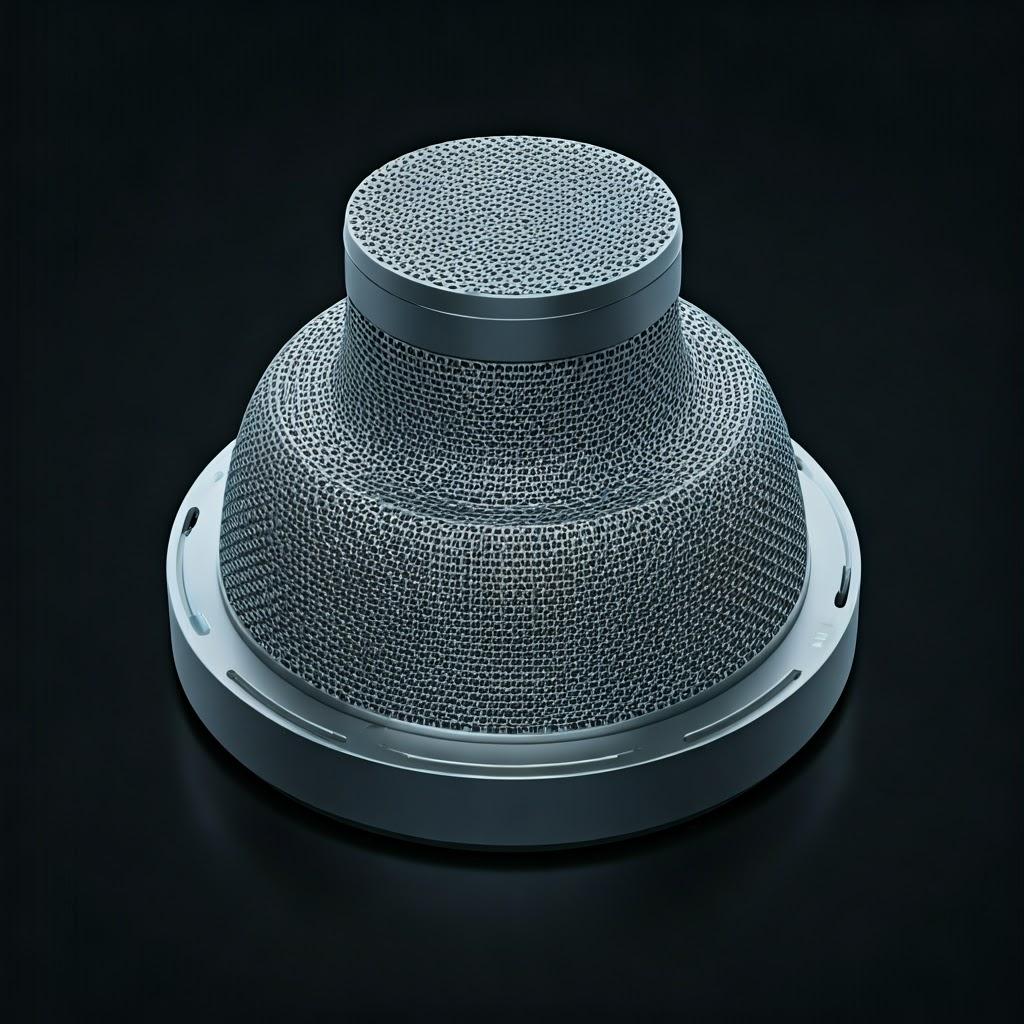
Frequently Asked Questions (FAQ) about 3D Printed EV Thermal Interface Plates
Here are answers to some common questions engineers and procurement managers have when considering metal additive manufacturing for EV Thermal Interface Plates:
Q1: How does the thermal conductivity of 3D printed CuCrZr or AlSi10Mg compare to their wrought or cast counterparts?
- A1: The thermal conductivity of AM metals can be very close to, but is often slightly lower than, their wrought counterparts. This is primarily due to the unique microstructure created by the rapid solidification process in AM, which typically results in very fine grains and potentially some micro-segregation or residual porosity (though high-density parts >99.5% are routinely achieved).
- İçin AlSi10Mg, as-printed conductivity might be around 120-130 W/(m·K), increasing to potentially 150-180 W/(m·K) after appropriate heat treatment (approaching cast values but typically lower than wrought alloys like 6061-T6).
- İçin CuCrZr, achieving high conductivity relies heavily on optimized printing parameters and correct post-print heat treatment (solutionizing and aging). Properly processed AM CuCrZr can reach thermal conductivities of 300-340 W/(m·K), which is very competitive and often exceeds cast copper alloys, though perhaps slightly below the ~390 W/(m·K) of pure wrought copper (C11000).
- Crucially, AM allows complex geometries that enhance overall thermal performance (e.g., via internal channels), often outweighing minor differences in bulk material conductivity compared to simpler shapes made from wrought materials.
Q2: What are the typical size limitations for printing large EV thermal interface plates?
- A2: Size limitations are determined by the build volume of the industrial metal AM machines used. Common build volumes for LPBF systems range from medium-sized (e.g., 250 x 250 x 300 mm) to larger formats (e.g., 400 x 400 x 400 mm, 500 x 280 x 360 mm, or even up to 800 mm in one dimension on some systems). Met3dp offers printers with industry-leading print volumes suitable for many automotive components. For TIPs exceeding the dimensions of a single build, designs can sometimes be segmented and joined in post-processing (e.g., by welding or brazing), although this adds complexity. The primary challenges with very large AM parts are managing thermal stresses/warpage during the build and handling during post-processing.
Q3: Can features like integrated sensor housings or fluid connectors be directly printed into the TIP?
- A3: Absolutely. This is a key strength of additive manufacturing – part consolidation. Features such as:
- Housings or mounting points for temperature sensors or pressure sensors.
- Integrated fluid inlet/outlet ports or manifolds (potentially with threads added in post-processing or designed for specific fittings).
- Mounting brackets or alignment features.
- Flow turbulators or internal fins within channels. can often be directly incorporated into the TIP design and printed as a single monolithic part. This reduces part count, eliminates assembly steps, minimizes potential leak paths (for fluid connectors), and can lead to more compact and efficient overall systems.
Q4: Is metal AM suitable for high-volume production of thermal interface plates for EVs?
- A4: The suitability of metal AM for high-volume production (typically meaning tens or hundreds of thousands of parts per year in automotive terms) is evolving.
- Current State: Metal AM excels in prototyping, custom parts, bridge production, and low-to-medium volume series (hundreds to thousands of parts per year), especially for components with high geometric complexity where the design freedom adds significant value (like TIPs with optimized internal channels). For these applications, AM can be cost-competitive or even cheaper than traditional methods requiring expensive tooling.
- High Volume Challenges: İçin basit TIP geometries produced in very high volumes, traditional methods like stamping or casting currently often maintain a cost advantage due to faster cycle times per part once tooling is established.
- Future Trends: However, AM printing speeds are increasing, machine costs are gradually decreasing, and multi-laser systems are improving productivity. As the technology matures and automation increases, the economic crossover point for higher volume production is shifting, making AM increasingly viable for series production in the automotive sector, particularly where its performance benefits are critical. Met3dp is actively involved in advancing the productivity and reliability of metal AM systems.
Q5: What quality assurance steps are taken to guarantee the performance of 3D printed TIPs?
- A5: Ensuring the quality and performance of critical components like TIPs requires a multi-faceted QA approach throughout the manufacturing process:
- Powder Control: Certification of chemical composition, particle size distribution, morphology, and flowability for each powder batch. Management of powder reuse/recycling.
- Süreç İzleme: Real-time monitoring of key parameters during the build (laser power, melt pool characteristics, oxygen levels, temperature).
- Density Checks: Measurement of part density (e.g., Archimedes method) to ensure minimal porosity (typically aiming for >99.5% density). CT scanning can be used for critical parts to visualize internal porosity.
- Boyutsal Muayene: Verification of geometric dimensions and tolerances using CMMs or 3D scanning, compared against the original CAD model and GD&T specifications.
- Surface Finish Measurement: Using profilometers to confirm Ra values meet requirements on critical surfaces.
- Material Property Testing: For critical applications or during process validation, mechanical testing (tensile tests, hardness) and potentially thermal conductivity testing may be performed on representative samples printed alongside the parts.
- Traceability: Maintaining records linking each part to the specific powder batch, machine, build parameters, and post-processing steps. Met3dp implements comprehensive quality control procedures tailored to the requirements of industries like automotive, aerospace, and medical, ensuring reliable and high-performance components.
Conclusion: Accelerating EV Thermal Management Innovation with Metal Additive Manufacturing
The relentless drive for improved performance, extended range, faster charging, and enhanced safety in electric vehicles hinges critically on effective thermal management. Thermal Interface Plates (TIPs) are vital components in this system, acting as crucial bridges for heat dissipation from batteries, power electronics, and motors. As power densities increase, traditional manufacturing methods often fall short in creating TIPs with the geometric complexity and material properties needed for optimal performance.
Metal additive manufacturing has emerged as a powerful enabler, offering transformative advantages for EV TIP development and production. By unshackling designers from conventional constraints, AM facilitates:
- Benzersiz Tasarım Özgürlüğü: Creating complex internal cooling channels, conformal surfaces, and lightweight lattice structures optimized for heat transfer.
- Enhanced Thermal Performance: Maximizing heat dissipation through optimized geometries and the use of high-conductivity alloys like CuCrZr ve AlSi10Mg.
- Parça Konsolidasyonu: Integrating multiple functions into a single component, reducing assembly complexity and potential failure points.
- Rapid Innovation Cycles: Accelerating prototyping and design iteration for faster development of superior thermal solutions.
The successful implementation of metal AM for these demanding applications depends not only on the technology itself but critically on the choice of materials and the expertise of the manufacturing partner. High-quality metal powders with consistent characteristics are the foundation, while optimized printing processes and rigorous post-processing pathways are essential to unlock the full potential of alloys like CuCrZr and AlSi10Mg. Navigating the challenges of warping, support removal, and achieving precision requires deep process knowledge and robust quality control.
Selecting a partner with proven expertise in materials science, advanced AM systems, comprehensive post-processing capabilities, and a thorough understanding of the target industry’s requirements is paramount. Met3dp stands at the forefront of this technological evolution, offering a complete ecosystem for metal additive manufacturing. As detailed on our Hakkımızda page, we provide:
- Advanced Metal Powders: High-quality spherical powders, including high-conductivity alloys, manufactured using industry-leading Gas Atomization and PREP technologies.
- Industry-Leading Printers: State-of-the-art SEBM and LPBF systems delivering exceptional accuracy, reliability, and build volume.
- Kapsamlı Çözümler: Expert support spanning DfAM, application development, process optimization, and post-processing management.
- Proven Expertise: Decades of collective experience serving mission-critical applications in aerospace, medical, automotive, and industrial manufacturing.
By partnering with Met3dp, companies can leverage the full power of metal additive manufacturing to develop and produce next-generation EV Thermal Interface Plates, pushing the boundaries of thermal management and accelerating the transition to a sustainable electric future.
Ready to optimize your EV thermal management with metal 3D printing? Contact Met3dp today to discuss your project requirements and explore how our advanced materials and manufacturing solutions can drive innovation for your organization.
Paylaş
MET3DP Technology Co, LTD, merkezi Qingdao, Çin'de bulunan lider bir katmanlı üretim çözümleri sağlayıcısıdır. Şirketimiz, endüstriyel uygulamalar için 3D baskı ekipmanları ve yüksek performanslı metal tozları konusunda uzmanlaşmıştır.
İşletmeniz için en iyi fiyatı ve özelleştirilmiş Çözümü almak için sorgulayın!
İlgili Makaleler
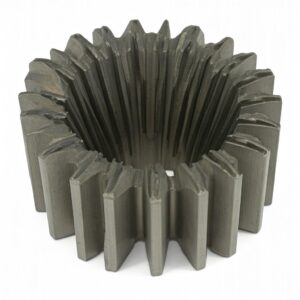
Yüksek Performanslı Nozul Kanat Segmentleri: Metal 3D Baskı ile Türbin Verimliliğinde Devrim
Daha Fazla Oku "Met3DP Hakkında
Son Güncelleme
Bizim Ürünümüz
BİZE ULAŞIN
Herhangi bir sorunuz var mı? Bize şimdi mesaj gönderin! Mesajınızı aldıktan sonra tüm ekibimizle talebinize hizmet edeceğiz.
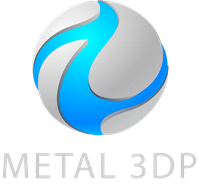
3D Baskı ve Katmanlı Üretim için Metal Tozları