Gearbox Covers 3D Printed for Automotive and Aerospace
İçindekiler
Introduction: The Future of Gearbox Covers is Additive
Gearbox covers, seemingly simple components, play a mission-critical role in the heart of complex machinery. From the transmission in your car to the intricate actuators controlling aircraft flight surfaces, these covers serve as the first line of defense, protecting vital internal gears, bearings, and mechanisms from environmental contaminants while ensuring proper lubrication containment. They often contribute significantly to the structural integrity and thermal management of the entire gearbox assembly. In high-performance sectors like otomotiv ve havacılık ve uzay, the demands placed on these components are immense – requiring strength, durability, lightweight characteristics, and often complex geometries to fit within tightly constrained spaces.
Traditionally, manufacturing gearbox covers involved processes like casting or extensive CNC machining from billet material. While effective, these methods often face significant limitations:
- High Tooling Costs: Creating molds for casting or specialized fixtures for machining represents a substantial upfront investment, particularly prohibitive for low-volume production runs or prototypes.
- Long Lead Times: Tooling fabrication, process setup, and machining cycles can extend development and production timelines considerably, hindering rapid innovation.
- Design Constraints: Casting and machining processes impose limitations on geometric complexity. Features like internal cooling channels, thin walls with complex curvatures, or integrated mounting points can be difficult, expensive, or impossible to achieve.
- Malzeme Atıkları: Subtractive manufacturing, like CNC machining, inherently generates significant material scrap, increasing costs and environmental impact.
Girmek Metal Katmanlı Üretim (AM), commonly known as metal 3D baskı. This transformative technology builds parts layer by layer directly from digital CAD data using high-performance metal powders. For gearbox covers, metal AM unlocks a new paradigm, overcoming many traditional constraints and offering unprecedented advantages in design, performance, and supply chain efficiency. Industries demanding peak performance and rapid innovation, such as automotive engineering and aerospace manufacturing, are increasingly turning to metal AM to produce next-generation gearbox covers.
As a leader in metal additive manufacturing solutions, Met3dp provides the advanced technology and materials expertise required to leverage these benefits. Specializing in state-of-the-art Selective Electron Beam Melting (SEBM) printers and premium, highly spherical metal powders produced via cutting-edge gas atomization and PREP technologies, Met3dp empowers engineers and procurement managers to rethink how critical components like gearbox covers are designed, sourced, and manufactured. This post delves into the specifics of using metal AM for gearbox covers, focusing on recommended materials like AlSi10Mg and A7075, design considerations, and how to partner with the right metal 3D printing service provider En iyi sonuçlar için.
Core Functions and Applications: What are Gearbox Covers Used For?
Understanding the fundamental roles of a gearbox cover is crucial before exploring manufacturing methods. These components are far more than simple lids; they are integral parts of the system, performing several critical functions simultaneously. Procurement managers sourcing these parts need to ensure their B2B gearbox cover supply meets stringent functional requirements across various applications.
Core Functions of a Gearbox Cover:
- Protection:
- Çevresel Sızdırmazlık: Shielding sensitive internal gears, bearings, sensors, and lubricants from dust, dirt, moisture, chemicals, and other external contaminants that could cause wear, corrosion, or malfunction.
- Darbe Dayanımı: Providing a degree of protection against minor impacts or debris encountered during operation.
- Lubrication Management:
- Containment: Securely holding lubricating oils or greases within the gearbox housing, preventing leaks that could lead to component failure or environmental hazards.
- Sealing Interfaces: Ensuring tight seals at mating surfaces, shaft openings, and fastener points, often requiring precise dimensional accuracy and specific surface finishes.
- Yapısal Bütünlük:
- Rigidity & Stiffness: Contributing to the overall stiffness of the gearbox assembly, helping maintain precise gear alignment under load.
- Mounting Points: Often incorporating mounting bosses, flanges, or brackets for attaching the gearbox to the larger structure or for mounting auxiliary components (sensors, actuators, etc.).
- Load Bearing: In some designs, the cover may bear or transfer specific operational loads.
- Termal Yönetim:
- Heat Dissipation: Assisting in dissipating heat generated by gear friction, often aided by external fins or specific material choices with good thermal conductivity. Additive manufacturing allows for the integration of optimized cooling channels directly into the cover design.
These functions are critical across diverse and demanding industrial applications, particularly in the automotive and aerospace sectors.
Otomotiv Uygulamaları:
The automotive industry constantly seeks performance improvements, weight reduction for fuel efficiency (especially in EVs), and cost-effective manufacturing. Metal AM addresses these needs for various gearbox covers:
- Transmission Housings/Covers: Protecting the intricate gear sets in manual, automatic, dual-clutch (DCT), and continuously variable transmissions (CVTs). Lightweighting is a key driver here.
- Differential Covers: Sealing the differential gears and lubricant, often requiring high strength and durability, especially in performance vehicles or off-road applications. AM allows for integrated cooling fins or custom designs for aftermarket upgrades.
- Transfer Case Components: Protecting the mechanisms that distribute power in four-wheel-drive (4WD) and all-wheel-drive (AWD) systems. Durability and reliable sealing are paramount.
- Electric Vehicle (EV) Gear Reduction Units: Covers for EV gearboxes require precision sealing and potentially integrated features for cooling or sensor mounting.
İçin wholesale automotive parts distributors and Tier 1/2 suppliers, metal AM offers a flexible production method for both niche performance parts and potentially series production components, reducing reliance on expensive tooling.
Aerospace Applications:
In aerospace, the requirements are even more stringent, prioritizing minimal weight, maximum strength, absolute reliability, and resistance to extreme operating conditions. Metal AM is uniquely suited to meet these challenges:
- Actuator Gearbox Covers: Protecting gear mechanisms for flight control surfaces (ailerons, elevators, rudders), landing gear deployment, and other critical actuation systems. Complex shapes and extreme lightweighting are often required.
- Auxiliary Power Unit (APU) Gearbox Covers: Enclosing the gearbox that drives the APU generator and other accessories. High temperatures and vibration resistance are key considerations.
- Rotorcraft Transmission Covers: Components for helicopter main and tail rotor transmissions demand exceptional strength-to-weight ratios and fatigue resistance. Part consolidation through AM can reduce potential failure points.
- Engine Gearbox (Accessory Drive) Covers: Protecting the gears that drive engine accessories like fuel pumps, hydraulic pumps, and generators. Reliability and resistance to harsh engine environments are crucial.
Finding a reliable aerospace parts supplier with proven metal AM capabilities and the necessary certifications (like AS9100) is vital for procurement teams in this sector. Met3dp, with its focus on high-performance materials and process control, is positioned to meet these demanding requirements.
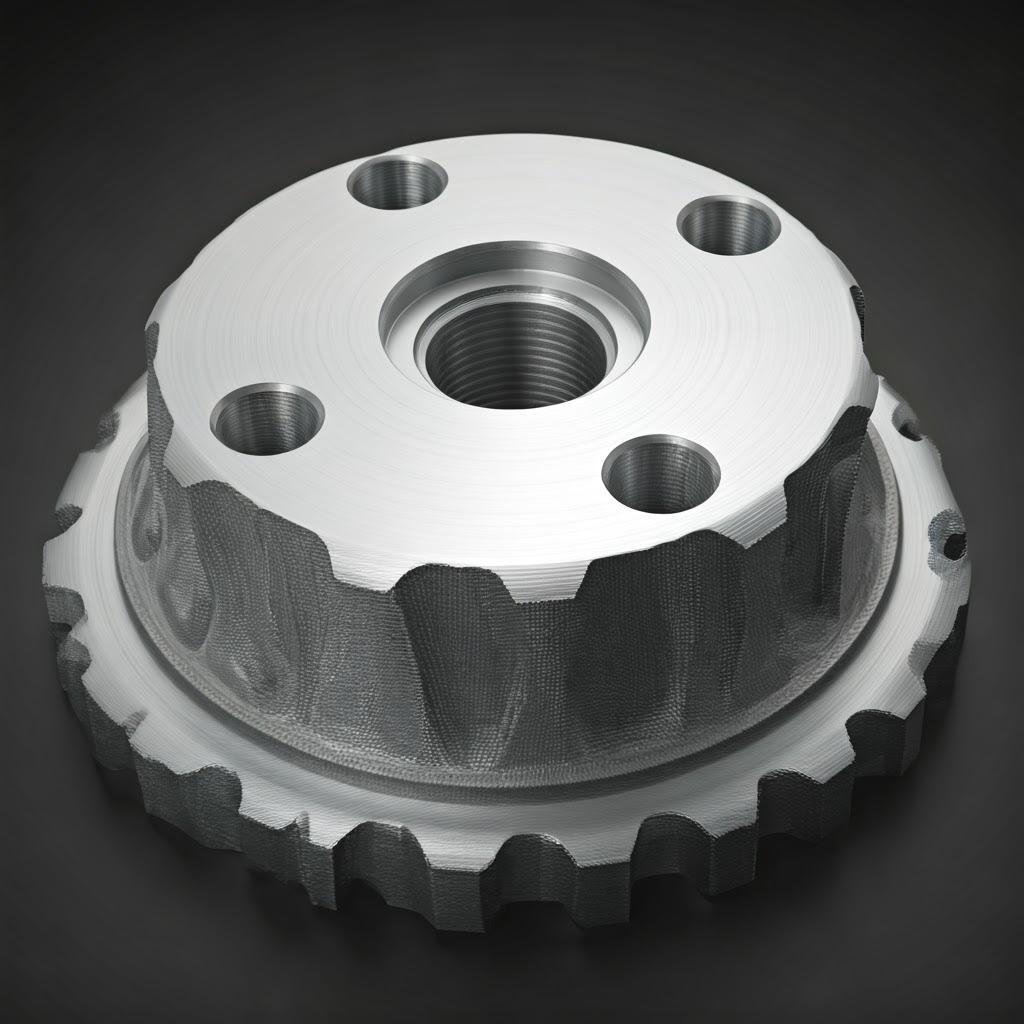
Additive Advantage: Why Use Metal 3D Printing for Gearbox Covers?
While traditional methods like casting and CNC machining have served the industry well, metal additive manufacturing presents a compelling suite of advantages specifically beneficial for producing advanced gearbox covers. Understanding these benefits allows engineers and procurement specialists to make informed decisions about leveraging AM for enhanced performance, reduced lead times, and optimized supply chains.
Let’s compare the approaches:
Özellik | Metal Katmanlı Üretim (AM) | Casting (e.g., Die Casting, Sand Casting) | CNC Machining (from Billet) |
---|---|---|---|
Tasarım Özgürlüğü | Very High (complex internal features, lattices) | Moderate (limited by mold complexity) | High (but subtractive limitations) |
Kalıp Maliyeti | None (digital manufacturing) | High (molds required) | Low to Moderate (fixtures may be needed) |
Lead Time (Proto) | Very Fast (days) | Slow (weeks to months for tooling) | Moderate (days to weeks) |
Lead Time (Prod) | Moderate (scalable but slower per part than casting) | Fast (high volume) | Moderate to Slow |
Malzeme Atıkları | Düşük (katkı maddesi işlemi) | Moderate (runners, gates) | Yüksek (eksiltici süreç) |
Hafifletme | Excellent (topology optimization, lattices) | Sınırlı | Moderate (pocketing) |
Parça Konsolidasyonu | Mükemmel | Zayıf | Zayıf |
Customization Cost | Düşük | Çok Yüksek | Yüksek |
Best Volume | Prototypes, Low-to-Mid Volume, Custom Parts | High Volume | Prototypes, Low-to-Mid Volume |
Sayfalara Aktar
Beyond this direct comparison, the specific advantages of metal AM for gearbox covers include:
- Eşsiz Tasarım Özgürlüğü: This is perhaps the most significant benefit. AM allows engineers to break free from Design for Manufacturability (DfM) constraints imposed by casting or machining.
- Karmaşık Geometriler: Create intricate internal cooling channels precisely following heat load paths, integrate sensor mounts seamlessly, or design organic, load-path-optimized shapes that are impossible to cast or machine.
- Topology Optimization: Utilize software to remove material from low-stress areas, creating highly efficient, lightweight structures that maintain or even increase stiffness and strength where needed. This is critical for aerospace and performance automotive applications.
- Kafes Yapılar: Incorporate internal lattice or honeycomb structures to drastically reduce weight while maintaining structural integrity, ideal for non-load-bearing sections or enhancing vibration damping.
- Significant Lightweighting: Directly tied to design freedom, AM enables substantial weight reduction compared to traditional methods. This translates to:
- Improved Fuel Efficiency: In automotive and aerospace, every gram saved counts towards better performance and lower emissions.
- Enhanced Vehicle Dynamics: Reduced unsprung mass (in differentials) or overall weight improves handling and acceleration.
- Increased Payload Capacity: In aerospace, weight savings allow for greater payload or extended range.
- Hızlı Prototipleme ve Yineleme: AM allows for the production of functional metal prototypes in days rather than weeks or months.
- Faster Development Cycles: Test multiple design variations quickly and affordably.
- Reduced Risk: Validate form, fit, and function early in the design process before committing to expensive tooling.
- Accelerated Innovation: Bring improved products to market faster.
- Economical Customization and Low-Volume Production: The absence of tooling makes AM highly cost-effective for:
- Bespoke or Niche Vehicles: Manufacturing covers for limited production runs, classic car restorations, or performance upgrades.
- Application-Specific Designs: Tailoring covers for unique operating environments or integration requirements without tooling penalties.
- Bridge Production: Producing initial batches while high-volume tooling is being prepared.
- Parça Konsolidasyonu: AM enables the integration of multiple components into a single, monolithic part.
- Reduced Assembly Time & Cost: Fewer parts to assemble means lower labor costs and faster production.
- Improved Reliability: Eliminating joints, fasteners, and seals reduces potential leak paths and failure points.
- Simplified Supply Chain: Fewer individual part numbers to manage.
- On-Demand Manufacturing & Supply Chain Optimization: AM facilitates a shift towards digital inventory and localized production.
- Reduced Warehousing: Print parts only when needed, minimizing physical stock and storage costs – a key benefit for toptan alıcılar managing inventory.
- Legacy Part Support: Recreate obsolete parts for which tooling no longer exists, directly from CAD data or scanned models.
- Tedarik Zinciri Dayanıklılığı: Reduce dependency on complex, geographically dispersed supply chains by enabling localized production closer to the point of need.
Leveraging these advantages requires expertise in both design for AM (DfAM) and the printing process itself. Companies like Met3dp, with advanced printers capable of handling complex geometries and a deep understanding of material science, are essential partners in realizing the full potential of additive manufacturing for automotive and aerospace parts.
Material Selection Spotlight: Recommended Powders (AlSi10Mg, A7075) and Why They Matter
The performance of a 3D printed gearbox cover hinges critically on the material chosen. Metal AM utilizes fine, spherical metal powders that are melted and fused layer by layer. The quality, characteristics, and suitability of this powder feedstock are paramount to achieving the desired mechanical properties, dimensional accuracy, and overall reliability of the final part. For gearbox covers in automotive and aerospace, aluminum alloys are often favored for their excellent balance of strength, weight, and corrosion resistance. Two prominent candidates available for metal AM are AlSi10Mg and A7075.
Understanding the properties and nuances of these materials is essential for engineers designing parts and procurement managers sourcing them from a high-quality metal powders supplier.
AlSi10Mg: The Versatile Workhorse
AlSi10Mg is an aluminum alloy containing silicon and magnesium, traditionally used in casting. Its behavior in AM processes like Selective Laser Melting (SLM) and Direct Metal Laser Sintering (DMLS) is well-understood, making it one of the most commonly used aluminum alloys in 3D printing.
- Composition Basics: Primarily Aluminum (Al), with ~9-11% Silicon (Si) and ~0.2-0.45% Magnesium (Mg).
- Key Properties (Typical Values for AM): | Property | As-Built | Heat Treated (T6) | Units | Notes | | :——————- | :——————- | :——————- | :———– | :—————————————- | | Ultimate Tensile Str | ~330 – 430 | ~300 – 360 | MPa | Strength comparable to casting | | Yield Strength | ~200 – 270 | ~230 – 290 | MPa | Good strength | | Elongation at Break | ~3 – 10 | ~6 – 10 | % | Moderate ductility | | Hardness | ~100 – 120 | ~90 – 110 | HV | Good wear resistance | | Density | ~2.67 | ~2.67 | g/cm³ | Lightweight | | Thermal Conductivity | ~120 – 150 | ~130 – 180 | W/(m·K) | Good heat dissipation | | Corrosion Resistance | Good | Good | – | Suitable for typical automotive environments |
- Benefits for Gearbox Covers:
- Mükemmel Basılabilirlik: Relatively easy to process with good dimensional accuracy and surface finish achievable.
- İyi Güç-Ağırlık Oranı: Offers substantial strength suitable for many automotive and some less demanding aerospace applications while keeping weight low.
- Good Thermal Properties: Helps dissipate heat generated within the gearbox.
- Korozyon Direnci: Performs well in typical operating environments.
- Uygun Maliyetli: Generally more affordable than higher-strength aerospace alloys.
- Ideal Applications: Automotive transmission covers, differential covers, industrial machinery casings, prototypes requiring functional testing, components where moderate strength and good thermal performance are key.
A7075: The High-Strength Champion
A7075 is a high-performance aluminum alloy known for its exceptional strength, often comparable to some steels, making it a staple in the aerospace industry. Its primary alloying elements are zinc, magnesium, and copper. While highly desirable for its properties, printing A7075 using AM presents more challenges than AlSi10Mg.
- Composition Basics: Primarily Aluminum (Al), with significant amounts of Zinc (Zn, ~5.1-6.1%), Magnesium (Mg, ~2.1-2.9%), and Copper (Cu, ~1.2-2.0%).
- Key Properties (Typical Values for AM – Highly process-dependent): | Property | Heat Treated (T6/T7x) | Units | Notes | | :——————- | :——————– | :—— | :——————————————— | | Ultimate Tensile Str | ~500 – 570+ | MPa | Significantly stronger than AlSi10Mg | | Yield Strength | ~450 – 500+ | MPa | Very high yield strength | | Elongation at Break | ~3 – 9 | % | Lower ductility than AlSi10Mg, process critical | | Hardness | ~150 – 170 | HV | Very hard | | Density | ~2.81 | g/cm³ | Slightly denser than AlSi10Mg, still light | | Thermal Conductivity | ~130 | W/(m·K) | Good heat dissipation | | Corrosion Resistance | Moderate | – | Can be susceptible to stress corrosion cracking |
- Benefits for Gearbox Covers:
- Olağanüstü Güç-Ağırlık Oranı: Ideal for applications demanding maximum strength with minimal weight, critical for aerospace structures and high-performance automotive components.
- High Fatigue Strength: Withstands cyclic loading well, important for components subject to vibration and stress cycles.
- Challenges & Considerations in AM:
- Yazdırılabilirlik: A7075 is prone to solidification cracking (hot cracking) during the rapid heating and cooling cycles of laser-based AM due to its wide solidification range. This requires carefully optimized print parameters, specific laser strategies, and often modified alloy compositions tailored for AM.
- Isıl İşlem: Requires specific and complex multi-stage heat treatments (T6, T7x variants) to achieve optimal strength and mitigate issues like stress corrosion cracking.
- Maliyet: The powder itself and the specialized printing/processing required make it more expensive than AlSi10Mg.
- Ideal Applications: Aerospace structural components, flight control actuator housings, high-performance motorsport gearbox parts, applications where maximum strength and low weight are non-negotiable.
Why These Materials Matter for Gearbox Covers:
The choice between AlSi10Mg and A7075 (or other specialized alloys) depends entirely on the specific requirements of the gearbox cover:
- Stress & Load: High-stress applications favor A7075’s superior strength.
- Weight Targets: Both are lightweight, but A7075 offers better strength için its weight, crucial for aerospace.
- Çalışma Sıcaklığı: Both offer good thermal conductivity, but material properties at elevated temperatures should be considered.
- Çevre: AlSi10Mg generally offers sufficient corrosion resistance for automotive use; aerospace applications might require additional surface treatments for A7075 depending on exposure.
- Bütçe: AlSi10Mg is typically the more budget-friendly option.
Met3dp’s Powder Excellence:
Achieving the theoretical properties of these alloys in a finished AM part starts with exceptionally high-quality powder. Met3dp utilizes industry-leading gas atomization and Plasma Rotating Electrode Process (PREP) technologies to produce metal powders with:
- Yüksek Küresellik: Ensures excellent powder flowability and consistent spreading during the printing process, leading to uniform melt pools and dense final parts.
- Low Porosity: Minimizes internal gas pores within the powder particles.
- Controlled Particle Size Distribution (PSD): Optimized PSD ensures good packing density and predictable melting behavior.
- Yüksek Saflıkta: Strict control over raw materials and processing prevents contamination that could degrade material properties.
Beyond AlSi10Mg and A7075, exploring Met3dp’s comprehensive portfolio of high-performance metal powders reveals options including Titanium alloys (like Ti6Al4V, TiNi, TiTa), Cobalt Chrome (CoCrMo), various Stainless Steels, and Nickel-based Superalloys, catering to an even wider range of demanding applications. Partnering with a provider like Met3dp, who controls powder production and understands its critical role in the AM process, ensures that engineers can confidently select and utilize the best material for their gearbox cover needs, achieving parts with superior mechanical properties and reliability.
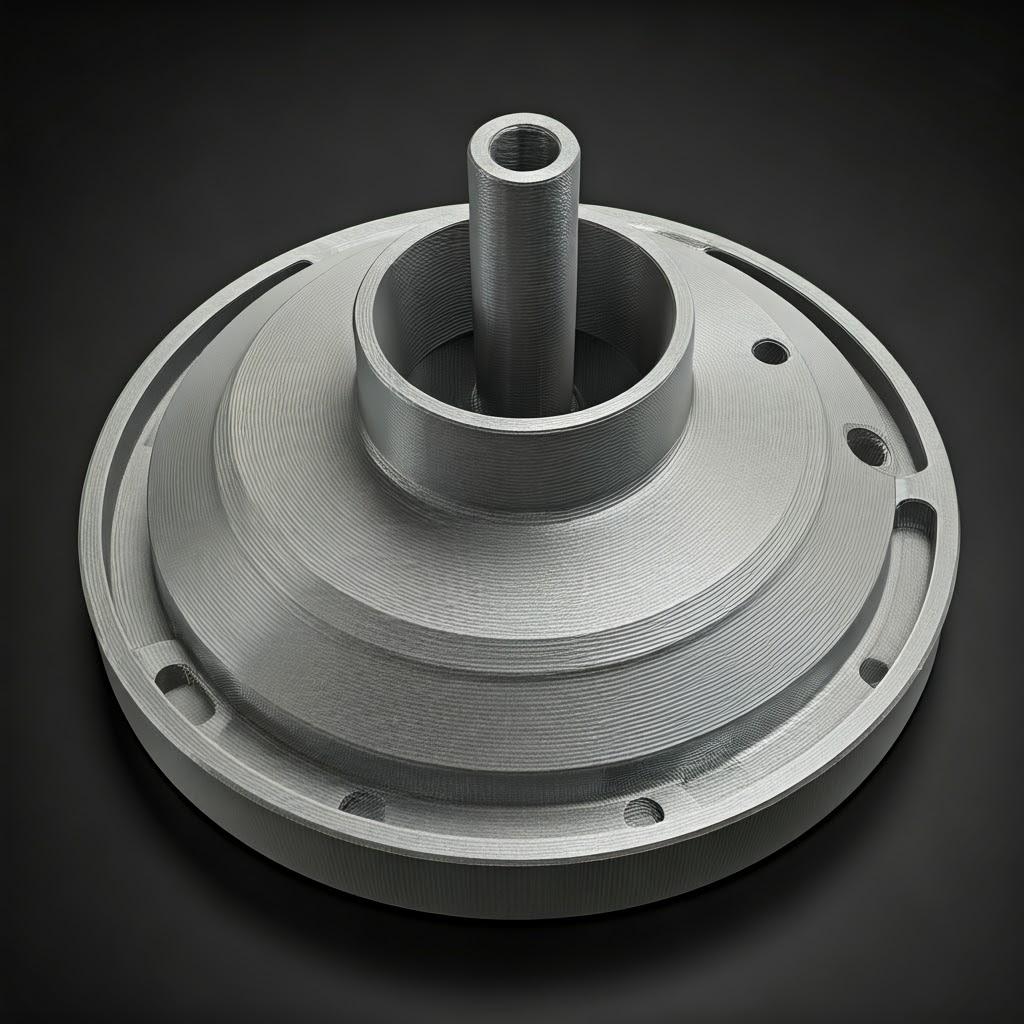
Designing for Additive: Key Considerations for 3D Printed Gearbox Covers
Simply replicating a design intended for casting or machining into a 3D printer rarely harnesses the full potential of additive manufacturing. To truly leverage the benefits of lightweighting, part consolidation, and enhanced performance for gearbox covers, engineers must embrace Katmanlı Üretim Tasarımı (DfAM) principles. DfAM is not just about making a part yazdırılabilir; it’s about designing it optimally for the AM process and the intended application. Neglecting DfAM can lead to longer print times, excessive support structures, higher costs, and suboptimal performance.
For gearbox covers, several key DfAM principles are particularly relevant:
- Topology Optimization: This is a powerful computational technique used to create the most efficient load-bearing structures.
- Süreç: Finite Element Analysis (FEA) simulates operational loads (stress, vibration, thermal) on an initial design volume. Topology optimization software then intelligently removes material from areas experiencing low stress, leaving material only where it’s structurally necessary to carry the loads.
- Avantajlar: Achieves significant weight reductions (often 20-50% or more) while maintaining or even improving stiffness and strength. Creates organic, efficient shapes difficult to achieve otherwise.
- Tools: Software like Altair Inspire, Ansys Discovery, Dassault Systèmes CATIA Generative Design, or nTopology are commonly used.
- Uygulama: Ideal for aerospace gearbox covers where weight is paramount, and high-performance automotive components.
- Kafes Yapılar: Incorporating internal or external lattice structures (also known as cellular structures) can further enhance performance.
- Türler: Strut-based lattices, surface-based lattices like Triply Periodic Minimal Surfaces (TPMS).
- Avantajlar: Drastically reduce weight while maintaining high stiffness, improve energy absorption (vibration damping), increase surface area for better heat dissipation, facilitate fluid flow if designed as open-cell.
- Uygulama: Filling non-load-critical internal volumes of the cover, creating lightweight stiffening ribs, enhancing thermal management sections.
- Wall Thickness Management: AM allows for thin walls, but minimums and variations must be considered.
- Minimums: Depending on the AM process (SLM, DMLS, SEBM), material, and feature geometry, minimum printable wall thickness is typically between 0.4,textmm and 0.8,textmm. Designing below this can lead to failed builds.
- Uniformity & Transitions: While variable thickness is possible, sudden drastic changes should be avoided. Smooth transitions prevent stress concentrations and improve printability. Avoid overly thick sections, which can increase thermal stress, print time, and cost.
- Destek Yapısı Stratejisi: Metal AM processes typically require support structures for features overhanging the build plate at angles typically greater than 45 degrees, and for bridging horizontal gaps.
- Gereklilik: Supports anchor the part to the build plate, prevent warping, and provide a base for overhanging features to build upon.
- Minimizasyon: Orient the part strategically on the build platform during print preparation to minimize the amount of overhangs requiring support. This reduces print time, material usage, and post-processing effort.
- Design for Removal: Design features like chamfers (e.g., 45-degree angles) instead of sharp 90-degree overhangs where possible (self-supporting angles). Ensure supports are accessible for easy removal without damaging the part surface. Consider the tools needed for removal (manual, machining).
- Feature Integration & Part Consolidation: One of AM’s strengths is combining multiple functionalities into a single component.
- Örnekler: Integrate mounting brackets, sensor housings, fluid connectors, or complex internal cooling channels directly into the gearbox cover design.
- Avantajlar: Reduces part count, eliminates assembly steps and associated labor costs, removes potential leak paths or failure points at joints, simplifies inventory management for B2B procurement.
- Powder Removal Considerations: For complex internal geometries or channels, ensuring unfused powder can be removed after printing is crucial.
- Tasarım: Incorporate strategically placed escape holes or access ports in the design. Ensure internal channels are sufficiently wide and have smooth transitions to allow powder to flow out. Avoid creating enclosed voids where powder can become permanently trapped.
- Consequences: Trapped powder adds weight and can potentially dislodge during operation, causing contamination or damage.
Successfully implementing DfAM requires a shift in thinking and often benefits from collaboration with AM experts. Providers like Met3dp can offer guidance during the design phase, helping customers optimize their gearbox cover designs to maximize the benefits of additive manufacturing and ensure successful, cost-effective production.
Precision Matters: Tolerance, Surface Finish, and Dimensional Accuracy
For gearbox covers to function correctly – sealing effectively, mating properly with housings, and providing accurate mounting points – achieving specific levels of precision is essential. Metal additive manufacturing processes can produce parts with good accuracy, but it’s crucial to understand the achievable levels of tolerance, surface finish, and overall dimensional accuracy, and how these compare to traditional methods.
Tolerances:
Tolerance refers to the permissible limit or limits of variation in a physical dimension.
- General AM Tolerances: As a general guideline, metal AM processes like SLM, DMLS, and SEBM can typically achieve tolerances within the range of ISO 2768-m (medium) or sometimes finer for specific small features. This often translates to approximately pm0.1,textmm to pm0.3,textmm over moderate dimensions (e.g., up to 100,textmm), with potentially larger deviations over very large parts due to thermal effects. Understanding different metal 3D baskı yöntemleri is key, as processes like Met3dp’s SEBM, operating at higher temperatures, can sometimes result in lower residual stress and potentially better stability for certain geometries, though SLM/DMLS might offer finer feature resolution.
- Etkileyen Faktörler: Achieved tolerances depend heavily on machine calibration, the specific material being printed (thermal expansion/contraction), part geometry and size (thermal mass, stress accumulation), build orientation, support strategy, and post-print heat treatments.
- Critical Features: For features requiring very tight tolerances – such as bearing bores, shaft seal diameters, mating flange flatness, or threaded holes – the as-built AM tolerance is often insufficient. These features typically require post-process CNC machining to achieve tolerances in the range of pm0.01,textmm to pm0.05,textmm, consistent with traditional manufacturing standards. It’s vital to identify these critical features early and incorporate machining allowances into the AM design.
Surface Finish (Roughness, Ra):
Surface finish, often quantified by average roughness (Ra), describes the texture of a surface.
- As-Built Roughness: Metal AM parts inherently have a rougher surface finish compared to machined parts. The typical Ra value depends on factors like:
- Process & Material: Different machine types and metal powders yield slightly different finishes.
- Katman Kalınlığı: Thinner layers generally produce smoother surfaces.
- Oryantasyon: Up-facing surfaces (parallel to layers) and steeply angled surfaces tend to be smoother (Ra typically 5−15,mutextm). Down-facing surfaces and those requiring supports are generally rougher (Ra potentially 15−25,mutextm or more) due to support contact points and the nature of layer formation.
- Post-Processing Effects: Surface finish can be significantly improved through various post-processing steps:
- Bead Blasting: Provides a uniform matte finish, typically reducing Ra to around 3−6,mutextm.
- Tumbling/Vibro-Polishing: Can achieve smoother finishes, especially on external surfaces.
- Machining/Grinding/Polishing: Can achieve very smooth finishes (Ra < 1,mutextm) on specific functional surfaces.
- Importance: Surface finish is critical for sealing surfaces (gaskets, O-rings), bearing contact areas, fatigue life (smoother surfaces reduce stress concentrators), and aesthetics. Requirements must be clearly defined on engineering drawings.
Boyutsal Doğruluk:
Dimensional accuracy refers to how closely the final part conforms to the nominal dimensions specified in the CAD model.
- Achieving Accuracy: Ensuring accuracy involves more than just machine precision. It requires:
- Rigorous Process Control: Maintaining stable melt pool conditions, consistent energy input, and controlled atmospheric conditions during the build.
- Machine Calibration: Regular calibration ensures the energy source (laser/electron beam) and motion systems are performing correctly.
- Thermal Management & Simulation: Understanding and compensating for thermal expansion and contraction during the build and cool-down phases is critical, sometimes involving simulation to predict and counteract distortion.
- Post-Build Metrology: Verification using Coordinate Measuring Machines (CMM), 3D laser scanning, or structured light scanning compares the physical part to the original CAD data, generating detailed inspection reports. This is a standard part of quality assurance for precision manufacturing B2B Hizmetler.
Met3dp understands the criticality of precision for industries like aerospace and automotive. Our commitment is reflected in utilizing industry-leading equipment, robust process controls, and rigorous quality checks to deliver metal AM parts with exceptional accuracy and reliability, suitable for mission-critical applications.
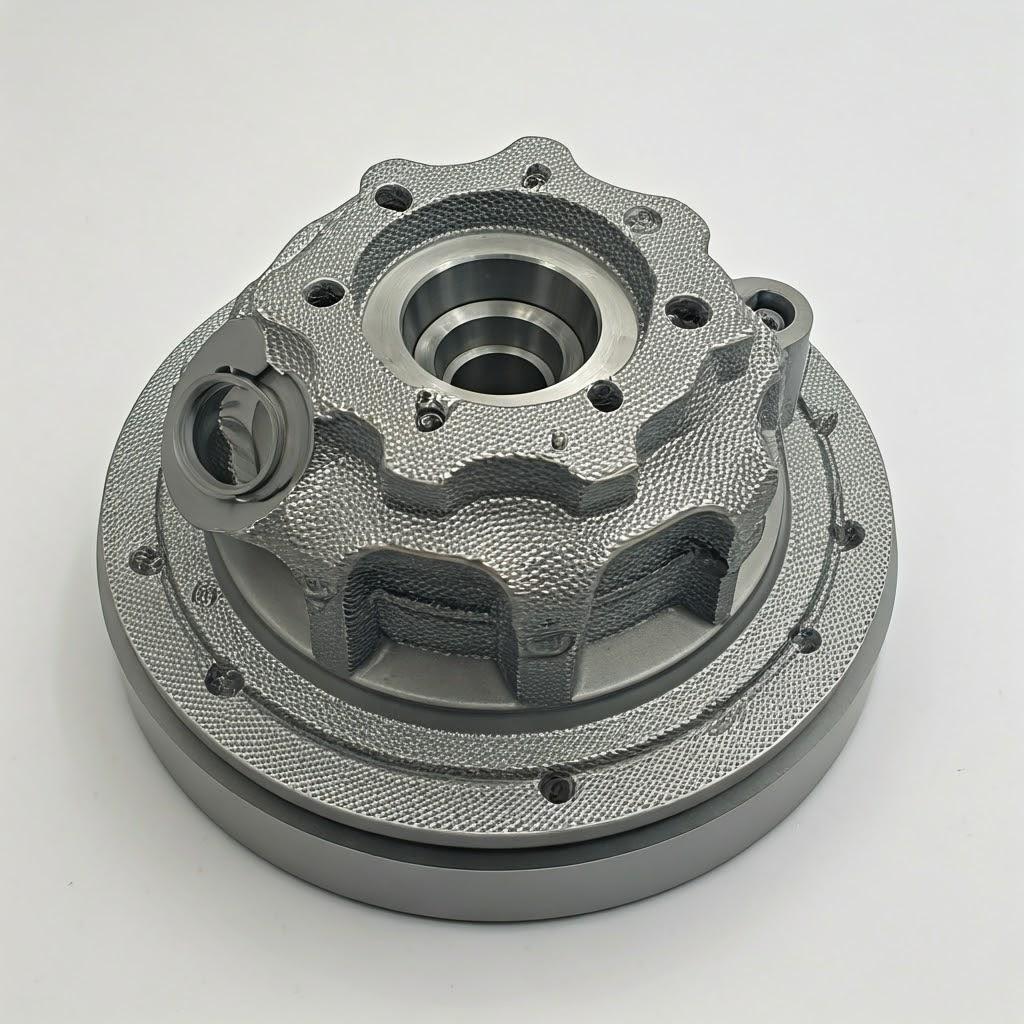
Beyond the Build: Post-Processing Requirements for Gearbox Covers
A common misconception about metal 3D printing is that parts come out of the machine ready to use. In reality, for functional engineering components like gearbox covers, the printing process is just the first step. A series of post-processing operations are nearly always required to transform the as-built part into a finished product that meets specifications for mechanical properties, dimensional accuracy, surface finish, and overall quality. Planning for these steps is essential for budgeting, determining lead times, and ensuring the final part performs as expected.
Common post-processing steps for 3D printed metal gearbox covers include:
- Stres Giderici / Isıl İşlem: This is arguably the most critical post-processing step for most metal AM parts, especially those made from aluminum alloys like AlSi10Mg and A7075.
- Amacımız: The rapid heating and cooling cycles inherent in AM build processes create significant internal stresses within the part. Heat treatment relieves these stresses, preventing potential distortion or cracking later, stabilizes the material’s microstructure, and develops the final desired mechanical properties (strength, ductility, hardness).
- Süreç: Parts are heated in a controlled furnace atmosphere to specific temperatures for defined durations, followed by controlled cooling or quenching, and sometimes aging steps (e.g., achieving a T6 temper for AlSi10Mg involves solutionizing, quenching, and artificial aging). A7075 requires even more complex, multi-stage heat treatments to optimize its properties and mitigate stress corrosion cracking risks.
- Timing: Stress relief is often performed immediately after printing, sometimes even before removing the part from the build plate, to minimize distortion risk.
- Part Removal & Support Removal: Once cooled (and potentially stress-relieved), the part needs to be separated from the build plate and have its support structures removed.
- Yöntemler: Part removal often involves wire EDM or sawing. Support removal can be done manually (breaking or cutting), using hand tools, or via CNC machining for more integrated or difficult-to-reach supports.
- Düşünceler: This step can be labor-intensive and requires care to avoid damaging the part surface. DfAM plays a key role in designing supports for easier removal.
- Machining (CNC): As discussed previously, as-built AM tolerances and surface finishes are often insufficient for critical functional features.
- Uygulamalar: Machining is used to achieve tight tolerances and smooth finishes on mating flanges, bearing and seal bores, mounting holes (drilling/tapping threads), gasket grooves, and any other precision interface surfaces.
- Integration: Requires careful planning to ensure sufficient material (“machining stock” or “offset”) is left on relevant surfaces during the AM design phase.
- Surface Finishing & Cleaning: Various techniques can be applied to clean the part and achieve the desired surface texture and properties.
- Temizlik: Essential to remove any residual unfused powder, especially from internal channels. Methods include compressed air blowing, bead blasting (which also provides a uniform finish), ultrasonic cleaning, and solvent washing.
- Surface Texture Improvement: Bead blasting (uniform matte), shot peening (compressive stress, fatigue life improvement), tumbling/vibro-polishing (smoothing edges and surfaces), manual grinding/polishing (for specific high-finish areas).
- Kaplamalar: Applying surface treatments for enhanced performance or protection:
- Anodizing (for Aluminum): Improves corrosion resistance and wear resistance, can be decorative (colored). Essential for anodizing 3D printed aluminum parts exposed to harsh environments.
- Painting/Powder Coating: For corrosion protection and aesthetics.
- Chemical Conversion Coatings (e.g., Alodine/Chromate): Improve corrosion resistance and paint adhesion.
- Specialized Coatings: Thermal barrier coatings, wear-resistant coatings (e.g., PVD/CVD).
- Inspection & Quality Control: Final verification ensures the part meets all specifications before shipping.
- Boyutsal Muayene: Using CMM, 3D scanning, or traditional metrology tools to verify tolerances.
- Tahribatsız Muayene (NDT): Methods like Computed Tomography (CT scanning) can inspect internal structures for defects like porosity or cracks without damaging the part. Dye Penetrant Testing (DPT) or Magnetic Particle Inspection (MPI – for ferrous materials) can identify surface-breaking defects.
- Material Property Verification: May involve testing witness coupons printed alongside the part to confirm mechanical properties post-heat treatment.
Bir seçim metal AM service provider that offers a comprehensive suite of post-processing capabilities, either in-house or through trusted partners, streamlines the production process. Met3dp provides end-to-end solutions, managing these critical steps to deliver finished gearbox covers that meet the demanding requirements of automotive and aerospace customers.
Navigating Challenges: Common Issues in 3D Printing Gearbox Covers and Solutions
While metal additive manufacturing offers tremendous advantages, it’s a complex process with potential challenges that need to be understood and proactively managed. Awareness of common issues allows engineers and suppliers to implement mitigation strategies, ensuring the successful production of high-quality gearbox covers. Partnering with an experienced AM process optimization supplier like Met3dp, who possesses deep expertise in materials science and process physics, is key to navigating these potential hurdles.
Here’s a breakdown of common challenges and their solutions:
Meydan Okuma | Açıklama | Hafifletme Stratejileri |
---|---|---|
Warping & Distortion | The part deforms or lifts from the build plate during or after printing due to uneven heating/cooling and built-up thermal stresses. | * Build Simulation: Software predicts thermal stress and distortion, allowing for compensation or design changes pre-print. <br> * Optimize Edilmiş Yönlendirme: Positioning the part to minimize large flat areas parallel to the build plate and manage heat distribution. <br> * Sağlam Destek Yapıları: Securely anchoring the part, especially vulnerable overhangs and edges, to counteract warping forces. <br> * Process Parameter Tuning: Adjusting laser/beam power, scan speed, and layer thickness to manage thermal input. <br> * Prompt Stress Relief: Performing heat treatment immediately after the build while potentially still on the plate. |
Artık Stres | Internal stresses remain locked within the part after solidification and cooling, potentially leading to reduced fatigue life, distortion during machining, or even cracking. | * Optimized Scan Strategies: Using specific patterns (e.g., checkerboard scanning) to distribute heat more evenly. <br> * Effective Heat Treatment: Implementing appropriate stress relief and annealing cycles tailored to the alloy (critical for high-stress parts). <br> * Process Selection: Certain processes like SEBM (used by Met3dp), which operate at elevated build chamber temperatures, inherently generate lower residual stress compared to some laser-based systems. |
Gözeneklilik | Small voids or pores within the material, which can be caused by trapped gas during atomization/melting or incomplete fusion between layers/scan lines. Reduces density and mechanical properties (especially fatigue strength). | * Yüksek Kaliteli Toz: Using powder with low internal gas porosity, high sphericity, and good flowability (like those produced via Met3dp’s gas atomization/PREP). <br> * Optimized Print Parameters: Ensuring sufficient energy density (power, speed, hatch spacing) for complete melting and fusion. <br> * Kontrollü Atmosfer: Maintaining a high-purity inert gas environment (Argon/Nitrogen) in the build chamber to prevent oxidation and contamination. <br> * Sıcak İzostatik Presleme (HIP): A post-processing step involving high temperature and pressure to close internal voids (adds cost but significantly improves density and properties). |
Support Removal Issues | Supports are difficult, time-consuming, or costly to remove, potentially damaging the part surface in the process. | * DfAM: Designing parts to minimize the need for supports (e.g., using self-supporting angles <45°, optimizing orientation). <br> * Support Design: Using specialized support structures (e.g., thin, easily breakable contact points, tree supports) generated by build preparation software. <br> * Erişilebilirlik: Ensuring removal tools (manual or CNC) can access the support structures. |
Powder Removal Difficulty | Unfused metal powder becomes trapped within intricate internal channels, hollow sections, or complex lattice structures. | * DfAM: Designing adequate escape holes or access ports, ensuring internal channels are large enough and smoothly transitioned for powder flow. <br> * Post-Print Cleaning: Utilizing thorough cleaning procedures like compressed air jets, vibration tables, or specialized flushing systems during post-processing. |
Malzeme Özelliği Değişimi | Inconsistent mechanical properties (strength, ductility) within a single part or between different build cycles. | * Strict Process Control: Maintaining tight control over all print parameters (energy input, temperature, atmosphere). <br> * Machine Calibration & Maintenance: Regular checks and calibration ensure consistent machine performance. <br> * Consistent Powder Quality: Using powder from qualified batches with controlled characteristics. <br> * Standardized Post-Processing: Applying identical, validated heat treatment cycles. <br> * Rigorous Quality Assurance: Implementing batch testing, witness coupons, and NDT to verify consistency. |
Sayfalara Aktar
Addressing these challenges requires a deep understanding of the interplay between material science, process physics, and design. Collaborating with a knowledgeable metal AM provider is crucial for troubleshooting issues and implementing robust AM process control quality measures, ultimately ensuring the reliability and performance of 3D printed gearbox covers for demanding applications.
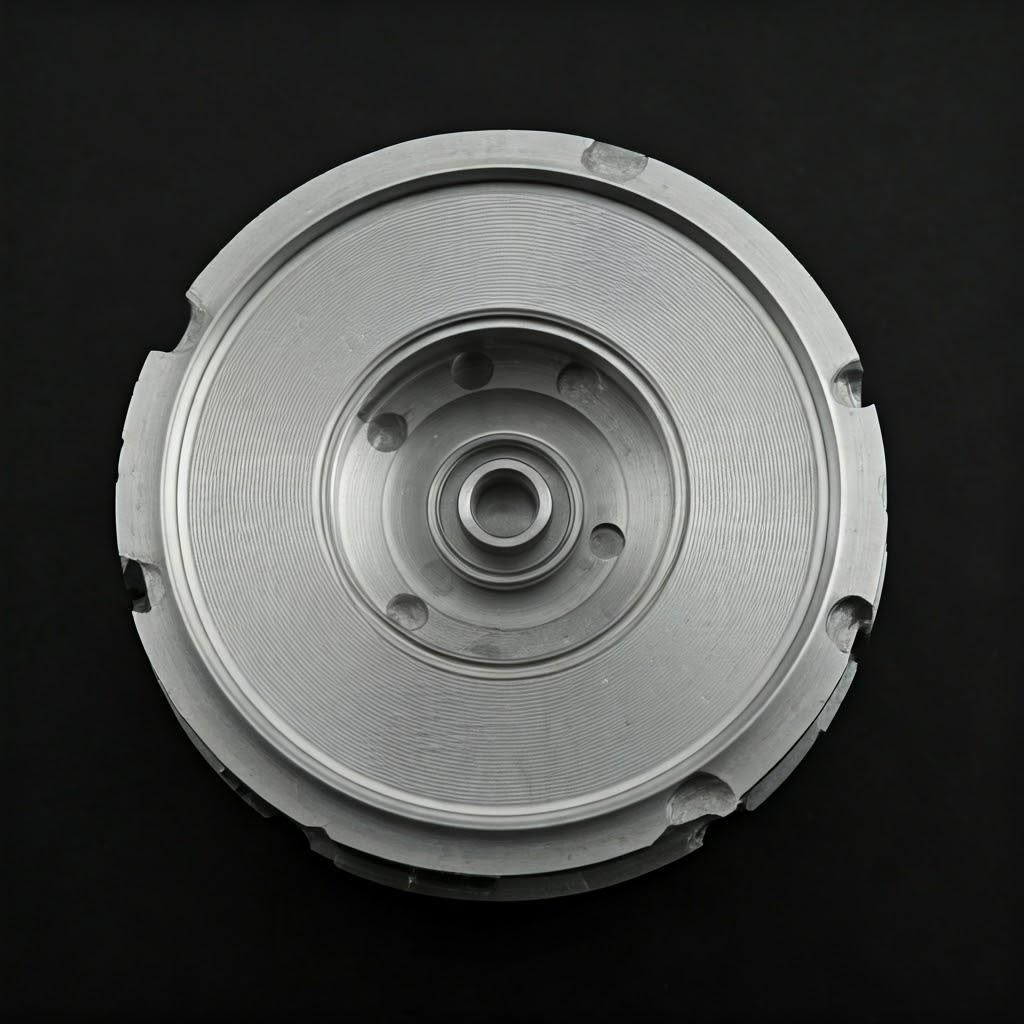
Supplier Selection: How to Choose the Right Metal 3D Printing Service Provider
Selecting the right additive manufacturing partner is as critical as the design and material selection, especially when dealing with high-performance components like gearbox covers for aerospace and automotive applications. The quality, reliability, and expertise of your chosen supplier directly impact the success of your project. For B2B procurement managers and engineering teams, evaluating potential suppliers requires a thorough assessment of their capabilities, quality systems, and experience.
Here are key criteria to consider when choosing a metal 3D printing service provider:
- Material Expertise & Availability:
- Portfolio: Do they offer the specific alloys you need (e.g., AlSi10Mg, A7075)? Do they have experience printing these materials successfully, particularly challenging ones like high-strength aluminum alloys?
- Toz Kalitesi: Where do they source their powders? Do they have robust quality control for incoming powder batches? Suppliers like Met3dp, who manufacture their own yüksek kaliteli metal tozları using advanced atomization techniques (Gas Atomization, PREP), often have better control and deeper understanding of material characteristics.
- Technology & Equipment:
- Process Suitability: Which AM process(es) do they utilize (SLM, DMLS, SEBM, EBM, Binder Jetting)? Is the process appropriate for your chosen material, desired feature resolution, and mechanical property requirements? Met3dp utilizes industry-leading SEBM printers known for high productivity and processing capabilities for materials like titanium alloys and certain superalloys.
- Capabilities: What is the size of their machine park? What are their maximum build volumes? What level of accuracy and resolution can their machines achieve? Ensure their equipment can accommodate your part size and precision needs.
- Endüstri Sertifikaları: Certifications provide objective evidence of a supplier’s commitment to quality and process control, often essential for regulated industries.
- ISO 9001: Foundational quality management system certification.
- AS9100: Required for aerospace suppliers, indicating stringent quality controls for aerospace components.
- IATF 16949: Quality standard for the automotive supply chain.
- ISO 13485: Required for medical device manufacturing. Verify that the supplier holds certifications relevant to your industry and application.
- Quality Management System (QMS): Beyond certifications, delve into their internal quality practices.
- Traceability: Can they track materials and process parameters from raw powder to finished part?
- Süreç İzleme: Do they employ real-time monitoring during the build?
- Toz İşleme: What are their procedures for powder storage, recycling, and testing to prevent contamination and ensure consistency?
- Calibration & Maintenance: How often are machines calibrated and maintained?
- Teftiş: What metrology and NDT capabilities do they possess?
- Technical Support & DfAM Expertise: A valuable supplier acts as a partner, not just a printer.
- Consultation: Can they review your design and provide constructive feedback for AM optimization (DfAM)?
- Engineering Support: Do they have engineers on staff who can assist with material selection, process optimization, or troubleshooting?
- Experience & Case Studies: Proven experience builds confidence.
- Relevant Projects: Have they produced parts similar in complexity, material, or application (e.g., powertrain components, structural aerospace parts)?
- Sektör Odaklı: Do they have a track record within the automotive or aerospace sectors? Ask for non-confidential case studies or references.
- Post-Processing Capabilities: Ensure they can provide or manage the full suite of necessary post-processing steps.
- In-house vs. Partners: Do they perform heat treatment, machining, finishing, and NDT in-house, or do they have a network of qualified partners? A single point of contact managing the entire workflow simplifies procurement.
- Lead Time & Capacity:
- Responsiveness: Can they provide quotes promptly?
- Turnaround Time: Can their stated lead times meet your project deadlines for both prototypes and potential series production?
- Capacity: Do they have sufficient machine availability to handle your order volumes without significant delays?
- Cost Transparency & Value:
- Quoting: Is their pricing structure clear and detailed? Are all costs (printing, material, supports, post-processing, inspection) included?
- Value Proposition: Evaluate the total value offered, considering quality, reliability, support, and lead time, not just the initial per-part price.
Met3dp aligns strongly with these criteria, offering a unique combination of advanced SEBM technology, in-house production of high-performance metal powders, comprehensive post-processing management, and decades of collective expertise in metal additive manufacturing. Learn more about Met3dp’s commitment to quality and innovation and how we partner with organizations to deliver mission-critical parts for demanding industries.
Budgeting and Timelines: Cost Factors and Lead Time for B2B Gearbox Cover Orders
For engineers managing project budgets and procurement managers responsible for sourcing components efficiently, understanding the cost drivers and typical lead times associated with metal 3D printing is crucial. While AM offers significant advantages, its cost structure and production timelines differ from traditional methods.
Cost Factors for 3D Printed Gearbox Covers:
The price of a metal AM gearbox cover is influenced by several interacting factors:
- Part Geometry (Volume & Complexity):
- Hacim: Larger parts consume more material and require longer printing times.
- Karmaşıklık: Highly intricate designs or those requiring extensive support structures increase both print time and post-processing effort (support removal). Design optimization (e.g., topology optimization) can reduce volume and thus cost.
- Material Choice & Cost:
- Powder Price: High-performance alloys like A7075, titanium alloys, or superalloys are inherently more expensive raw materials than common alloys like AlSi10Mg or stainless steels.
- Toz Kalitesi: Premium powders with high sphericity, controlled PSD, and low contamination (like those from Met3dp) command higher prices but result in better part quality and potentially higher print success rates.
- Print Time (Machine Utilization):
- Build Height: Taller parts take longer to print, layer by layer.
- Number of Parts per Build: Maximizing the number of parts printed simultaneously in one build job reduces the effective machine time cost per part.
- Parameters: Layer thickness (thicker = faster but rougher), scan speed, and hatching density all influence build time.
- Destek Yapıları:
- Hacim: Supports consume material (often the same expensive alloy) that is later removed and potentially scrapped or recycled.
- Removal Effort: Complex or extensive supports require significant labor or machining time for removal, adding cost.
- İşlem Sonrası Gereksinimler: Each additional step adds cost:
- Isıl İşlem: Furnace time, energy consumption, specialized cycles (especially for alloys like A7075).
- İşleme: Setup time, machining time (dependent on complexity and material hardness), tooling wear.
- Bitiriyorum: Labor and consumables for bead blasting, polishing, coating application (anodizing, painting).
- Teftiş: Time for CMM, scanning, NDT procedures, and report generation.
- Order Volume (Wholesale & B2B):
- Ölçek Ekonomileri: While not as dramatic as casting (where tooling amortization dominates), cost per part generally decreases with higher volumes in AM. This is due to optimizing machine setup, maximizing parts per build, batching post-processing operations, and potential volume discounts on powder. Wholesale 3D printing services often offer tiered pricing based on quantity.
Lead Time Factors:
The total time from order placement to receiving finished parts involves multiple stages:
- Pre-Processing: CAD file check, DfAM review/optimization, build simulation, quote generation, order confirmation (can take days).
- Print Queue: Waiting time for an available machine at the service provider (variable, depends on workload).
- Baskı: Actual machine runtime (hours to multiple days).
- Cool-Down & Stress Relief: Necessary time buffer before handling and heat treatment (hours to a day).
- İşlem sonrası: Support removal, heat treatment cycles (can take >24 hours), machining, finishing, inspection (can collectively take several days to weeks depending on complexity and batching).
- Nakliye: Transit time.
Typical Ranges (Estimates):
- Prototipler: Often 1 to 3 weeks, depending on complexity and provider queue.
- Low-Volume Production (e.g., 10-100 units): Typically 4 to 8 weeks or longer, highly dependent on part size, complexity, post-processing intensity, and required quality assurance.
Getting an Accurate Quote:
To receive a reliable quote and realistic lead time estimate, provide potential suppliers with a complete technical data package:
- 3D CAD Model (STEP or other neutral format preferred)
- 2D Engineering Drawing (clearly defining tolerances, critical dimensions, surface finish requirements on specific features)
- Material Specification (e.g., AlSi10Mg T6, A7075 T73)
- Post-Processing Details (areas requiring machining, coating type/spec)
- Inspection & Certification Needs (e.g., CMM report required, material certs, AS9100 compliance)
- Required Quantity
- Target Delivery Date
Clear and comprehensive information enables suppliers to provide accurate pricing and timelines. Explore Met3dp’s comprehensive metal 3D baskı hizmetleri and contact us with your project details for a tailored quote.
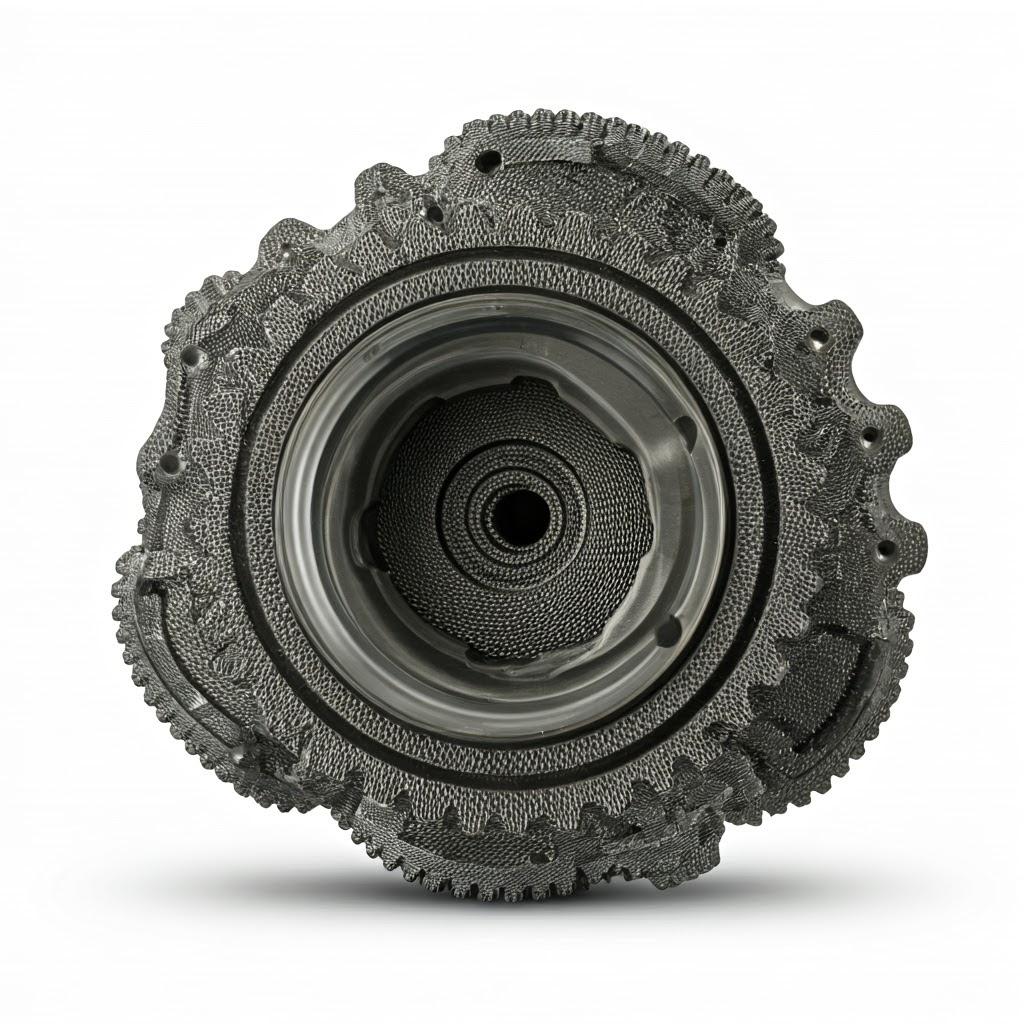
Frequently Asked Questions (FAQ) about 3D Printed Gearbox Covers
Q1: Can 3D printed gearbox covers handle the same operational loads as cast or machined parts?
A: Absolutely. When designed appropriately, using the correct high-performance metal powders (like AlSi10Mg or A7075), and subjected to proper post-processing (especially heat treatment), metal AM gearbox covers can meet or even exceed the mechanical performance of traditionally manufactured counterparts. Additive manufacturing allows for optimized designs (like topology optimization) that place material precisely where needed for strength, achieving excellent strength-to-weight ratios. Critical features are often CNC machined post-printing to match the tolerances of fully machined parts. The key lies in careful engineering, material selection (e.g., using high-strength A7075 for demanding loads), process control, and thorough validation.
Q2: What is the typical cost difference between AM and traditional methods for gearbox covers?
A: The cost comparison depends heavily on production volume and part complexity.
- Prototypes & Low Volume (e.g., 1-100 parts): Metal AM is often significantly daha uygun maliyetli because it eliminates the need for expensive tooling (molds for casting, complex fixtures for machining).
- High Volume (e.g., 1000+ parts): Traditional casting typically becomes daha ekonomik per part due to the amortization of tooling costs over large quantities. CNC machining costs are driven by complexity and cycle time, remaining relatively constant per part regardless of volume but often involving high material waste. It’s important to consider the total value proposition of AM, including reduced lead times for development, potential for lightweighting (improving fuel efficiency/performance), part consolidation, and supply chain flexibility, which can sometimes justify a higher per-part cost.
Q3: What information does a supplier like Met3dp need for an accurate quote?
A: To provide an accurate quote and lead time, Met3dp (and most reputable AM service providers) requires a complete technical data package. This typically includes:
- 3D CAD Modeli: Preferably in a neutral format like STEP.
- 2D Mühendislik Çizimi: Specifying critical dimensions, geometric tolerances (GD&T), surface finish requirements for specific features (e.g., sealing faces, bearing bores), and material callouts.
- Material Specification: Clearly state the desired alloy (e.g., AlSi10Mg, A7075) and the required final condition or temper (e.g., T6, T73), indicating the necessary heat treatment.
- İşlem Sonrası İhtiyaçlar: Indicate any required machining, surface treatments (anodizing, painting), or special cleaning procedures.
- Inspection & Certification: Specify any required inspections (e.g., CMM report, NDT like CT scanning) or certifications (e.g., material certs, certificate of conformity).
- Miktar: Number of parts required.
- Desired Delivery Date: Hedef zaman çizelgeniz.
Q4: Are there limitations on the size of gearbox covers that can be 3D printed?
A: Yes, the maximum size of a single-piece gearbox cover that can be 3D printed is limited by the build volume (X, Y, Z dimensions) of the specific additive manufacturing machine used. Build volumes vary significantly across different machine models and manufacturers. Typical powder bed fusion systems might range from around 250×250×300mm to 500×500×500mm, with some larger format machines exceeding these dimensions. Met3dp utilizes printers offering industry-leading print volume. It’s essential to check the specific capabilities of your chosen service provider. For parts exceeding the maximum build volume, it’s sometimes feasible to print them in multiple sections that are later joined together (e.g., by welding), but this requires additional design considerations and process steps.
Conclusion: Driving Innovation with Additively Manufactured Gearbox Covers
Metal additive manufacturing represents a fundamental shift in how critical components like gearbox covers can be conceptualized, designed, and produced. Moving beyond the constraints of traditional casting and machining, metal AM unlocks a powerful combination of benefits directly applicable to the demanding automotive and aerospace sectors. The ability to create complex, topology-optimized geometries allows for unprecedented hafifletme, directly contributing to improved fuel efficiency, enhanced vehicle dynamics, and increased payload capacity. Parça konsolidasyonu simplifies assemblies, reducing weight, potential failure points, and manufacturing complexity.
The speed of AM facilitates hızlı prototipleme and iterative design cycles, accelerating innovation and reducing time-to-market for new powertrain and actuation systems. Furthermore, the technology enables cost-effective customization and low-volume production, catering to niche markets, performance upgrades, and legacy part replacement. By enabling talep üzerine üretim, AM fosters more resilient and flexible supply chains, reducing reliance on extensive physical inventories and long lead times – a significant advantage for B2B suppliers and wholesale distributors.
Successfully harnessing these advantages requires the right combination of design expertise (DfAM), appropriate material selection (like versatile AlSi10Mg or high-strength A7075), tightly controlled manufacturing processes, and comprehensive post-processing. Choosing a knowledgeable and capable additive manufacturing partner is paramount.
Met3dp stands at forefront of this technological evolution. With our advanced SEBM printing systems delivering industry-leading volume, accuracy, and reliability, coupled with our in-house production of high-quality, highly spherical metal powders via cutting-edge atomization techniques, we provide end-to-end solutions for the most demanding applications. Our team brings decades of collective expertise in metal AM, offering comprehensive services spanning DfAM consultation, application development, printing, post-processing, and rigorous quality assurance.
We invite engineers and procurement managers in the automotive, aerospace, medical, and industrial sectors to explore the transformative potential of metal additive manufacturing for their gearbox cover requirements and beyond. Partner with Met3dp to leverage our cutting-edge systems and materials expertise, and accelerate your journey towards next-generation manufacturing.
Ziyaret etmek Met3dp.com to learn more or contact us today to discuss your specific project needs. Let us show you how Metal3DP can power your organization’s additive manufacturing goals.
Paylaş
MET3DP Technology Co, LTD, merkezi Qingdao, Çin'de bulunan lider bir katmanlı üretim çözümleri sağlayıcısıdır. Şirketimiz, endüstriyel uygulamalar için 3D baskı ekipmanları ve yüksek performanslı metal tozları konusunda uzmanlaşmıştır.
İşletmeniz için en iyi fiyatı ve özelleştirilmiş Çözümü almak için sorgulayın!
İlgili Makaleler
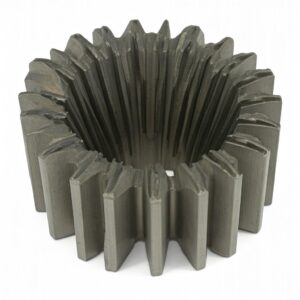
Yüksek Performanslı Nozul Kanat Segmentleri: Metal 3D Baskı ile Türbin Verimliliğinde Devrim
Daha Fazla Oku "Met3DP Hakkında
Son Güncelleme
Bizim Ürünümüz
BİZE ULAŞIN
Herhangi bir sorunuz var mı? Bize şimdi mesaj gönderin! Mesajınızı aldıktan sonra tüm ekibimizle talebinize hizmet edeceğiz.
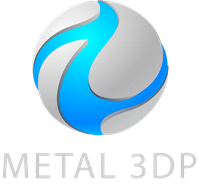
3D Baskı ve Katmanlı Üretim için Metal Tozları