Additive Manufacturing of Guidance System Housings
İçindekiler
Revolutionizing Defense: Additive Manufacturing of Missile Guidance System Housings
The landscape of modern defense and aerospace technology is characterized by a relentless pursuit of higher performance, reduced weight, increased complexity, and faster development cycles. In this demanding environment, the components that make up critical systems, such as missiles, are under constant scrutiny for optimization. Among these vital components is the missile guidance system housing, a structure that, while perhaps not as outwardly complex as the electronics it protects, plays an absolutely crucial role in mission success. This housing is the shield and chassis for the sophisticated sensors, processors, and actuators that guide a missile to its target, ensuring accuracy and reliability under extreme operational conditions. Traditionally, manufacturing these housings involved subtractive methods like CNC machining from billet or complex casting processes, often leading to significant material waste, design limitations, and protracted lead times, particularly challenging for the specialized materials frequently required.
Girmek Katmanlı Üretim (AM), more commonly known as Metal 3D Baskı, a transformative technology that is fundamentally reshaping how high-performance components are designed and produced across industries, with the aerospace and defense sectors being prominent adopters. Instead of removing material, AM builds parts layer by layer directly from digital models, typically using high-energy sources like lasers or electron beams to fuse fine metal powders. This approach unlocks unprecedented design freedom, enables the creation of highly complex geometries previously impossible to manufacture, facilitates rapid prototyping, and offers the potential for significant weight reduction through techniques like topology optimization. For aerospace engineers striving to enhance missile performance and range, and for defense procurement specialists seeking more agile, cost-effective, and resilient supply chains, metal AM presents a compelling value proposition.
This article delves into the specific application of metal additive manufacturing for producing missile guidance system housings. We will explore the critical functions these components perform, articulate the distinct advantages AM offers over conventional manufacturing techniques for this application, and discuss the recommended materials, particularly 316L Paslanmaz Çelik and the high-performance Ti-6Al-4V titanyum alaşımı. Furthermore, we will cover essential design considerations (DfAM), achievable precision levels, vital post-processing steps, common challenges and their solutions, and guidance on selecting the right AM service provider – a critical step for ensuring quality and reliability in defense applications. This exploration is particularly relevant for engineers designing next-generation missile systems, procurement managers evaluating advanced manufacturing suppliers, and military component distributors seeking innovative solutions for their clients in the defense industrial base. The central thesis is clear: metal additive manufacturing is not just a viable alternative but often a superior method for producing guidance housings that meet the stringent demands of modern defense, enabling lighter, more complex, and rapidly iterated designs that push the boundaries of missile capabilities.
The Critical Function: What Are Missile Guidance Housings Used For?
To fully appreciate the impact of additive manufacturing in this domain, one must first understand the multifaceted and critical functions performed by a missile guidance system housing. It is far more than a simple container; it is an integral part of the missile’s structure and functionality, operating in some of the most demanding environments imaginable – from the high G-forces and intense vibrations of launch to the extreme temperatures and pressures encountered during flight through the atmosphere or space. Failure of the housing can lead directly to mission failure.
Key Functions of a Missile Guidance Housing:
- Protection of Sensitive Electronics: This is the primary and most obvious function. The housing shields the delicate and complex guidance package – including Inertial Measurement Units (IMUs), GPS receivers, seekers (RF, IR, optical), processors, data links, and associated circuitry – from physical shocks, impacts, vibrations, acoustic noise, and environmental hazards like dust, moisture, and corrosive agents. The integrity of this protection is paramount for the guidance system to operate reliably.
- Yapısal Bütünlük: The housing must withstand significant mechanical loads during launch, maneuvering, and potentially even impact (in some applications). It contributes to the overall structural integrity of the missile’s forward section. It needs to maintain its shape and dimensional stability under load to ensure the precise alignment of internal sensors and components. Poor structural integrity could lead to misalignment of sensors, rendering the guidance system inaccurate.
- Çevresel Sızdırmazlık: Guidance systems often require protection from humidity, corrosive atmospheres (e.g., saltwater spray for naval applications), sand, dust, and potentially chemical or biological agents. The housing, often in conjunction with gaskets or seals, must provide a hermetic or near-hermetic seal to prevent ingress that could damage electronics or impair sensor performance. The quality of mating surfaces and fastener interfaces, areas where AM requires careful consideration and often post-machining, is critical here.
- Termal Yönetim: The high-power electronics within the guidance section generate significant heat. Simultaneously, the missile experiences external aerodynamic heating, especially at supersonic and hypersonic speeds. The housing plays a role in managing this thermal load. It might need to conduct heat away from sensitive components to external heat sinks or the missile skin, or conversely, insulate components from extreme external temperatures. AM offers unique possibilities here, such as integrating conformal cooling channels directly into the housing structure, a feat difficult or impossible with traditional methods.
- Electromagnetic Compatibility (EMC) / Electromagnetic Interference (EMI) Shielding: Guidance electronics are highly sensitive to electromagnetic interference, both from external sources (e.g., radar, communications signals) and potentially from other subsystems within the missile itself. The housing material and design must provide adequate shielding to prevent EMI from disrupting the guidance system’s operation. Material choice (conductivity) and ensuring electrical continuity across housing sections and interfaces are key considerations.
- Precise Mounting and Alignment: The housing provides accurate mounting points and datums for the internal components. The precise physical relationship between sensors (like IMUs and seekers) and the missile airframe, maintained by the housing, is fundamental to accurate navigation and targeting. Dimensional stability and tight tolerances in critical areas are essential.
Types of Missile Systems:
Guidance housings are integral to virtually all guided missile types, each presenting unique challenges:
- Tactical Missiles: (e.g., air-to-air, surface-to-air, anti-tank): Often require high G-load tolerance, rapid response, high reliability, and increasingly, reduced weight for improved platform payload and range. Cost-effectiveness for larger quantities is also a factor.
- Strategic Missiles: (e.g., ICBMs, SLBMs): Demand extreme reliability, long shelf life, resistance to harsh environments (including potential radiation hardening requirements), and absolute precision. Weight is critical for maximizing range.
- Cruise Missiles: Require sustained flight performance, often involving complex airframes and sophisticated navigation systems housed within protective structures designed for aerodynamic efficiency and environmental resistance over long durations.
- Hypersonic Vehicles: Represent an emerging frontier with extreme thermal management challenges due to aerodynamic heating at Mach 5+ speeds. Housing materials and designs must withstand exceptionally high temperatures while protecting internal systems.
Industry Context and Supply Chain:
The production of missile guidance housings sits within a complex defense supply chain. Prime defense contractors often rely on a network of specialized aerospace component suppliers ve distribütörler for manufacturing these critical parts. Reliability, traceability, quality assurance (often mandated by standards like AS9100), and adherence to stringent security protocols (like ITAR in the US) are non-negotiable requirements for any defense manufacturer veya Tedarikçi in this space. Introducing AM into this established ecosystem requires careful validation and qualification but offers significant potential to streamline defense procurement and enhance logistical resilience, enabling faster delivery of advanced capabilities. The ability to source complex components from qualified AM providers like Met3dp, who understand the rigorous demands of the sector, becomes a strategic advantage.
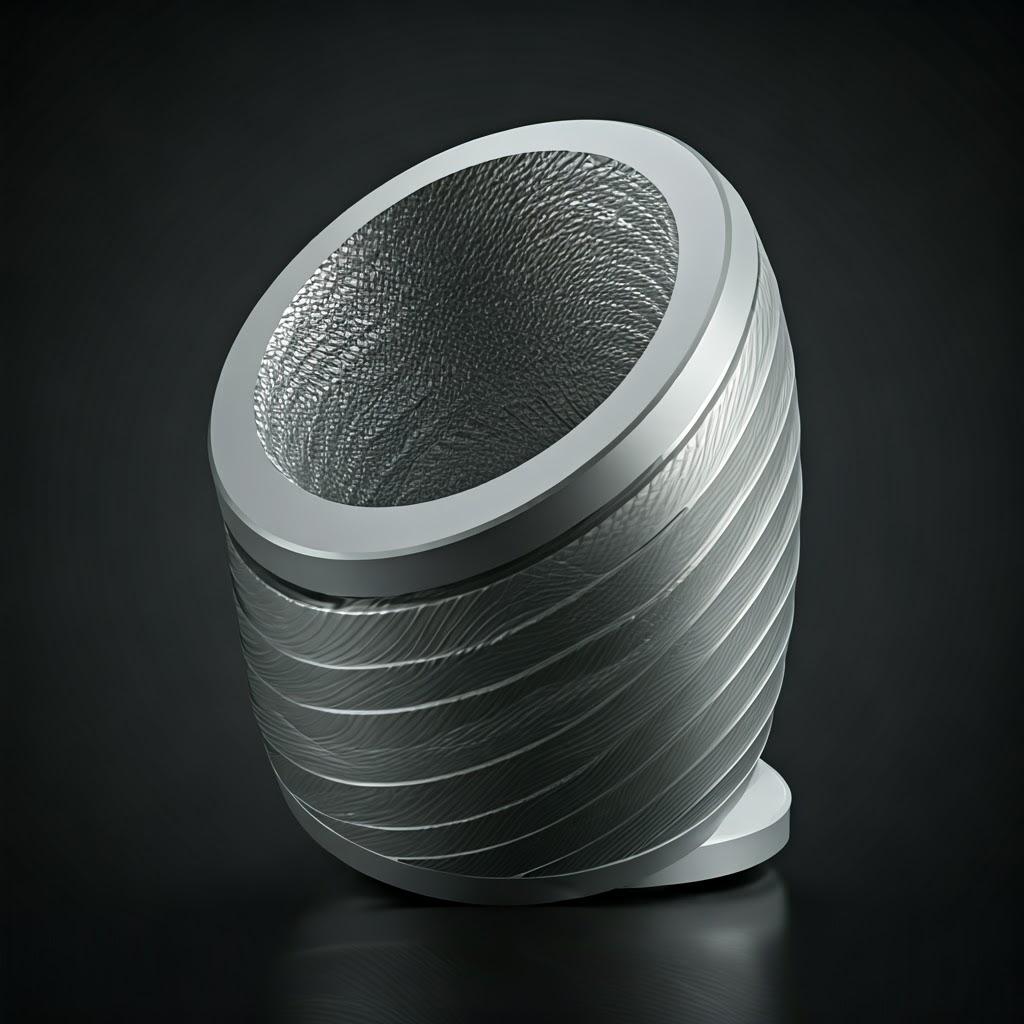
Why Choose Metal 3D Printing for Guidance Housings? Unlocking Performance and Efficiency
While traditional manufacturing methods like CNC machining and investment casting have served the defense industry for decades, they present inherent limitations, especially when dealing with the increasing complexity and performance demands of modern missile systems. Metal additive manufacturing offers a compelling suite of advantages that directly address these limitations, making it an increasingly attractive option for producing guidance system housings.
Limitations of Traditional Manufacturing:
- CNC İşleme:
- Malzeme Atıkları: Subtractive processes start with a solid block (billet) of material and cut away the excess. For complex geometries or parts made from expensive aerospace alloys like titanium, this can result in substantial (often >80-90%) material waste (buy-to-fly ratio), significantly increasing costs.
- Design Constraints: Tool access limits the complexity of internal features, thin walls, and organic shapes. Deep pockets or intricate internal channels can be difficult or impossible to machine.
- Tooling & Setup Time: While versatile, complex parts may require multiple setups, specialized tooling, and extensive programming time, increasing lead times and costs, especially for prototypes or low-volume runs.
- Yatırım Döküm:
- Tooling Costs & Lead Time: Requires the creation of molds/tools, which is expensive and time-consuming, making it generally unsuitable for prototyping or low-volume production.
- Design Limitations: Constraints exist regarding wall thickness, feature resolution, and achievable complexity compared to AM. Internal passages often require complex ceramic cores.
- Malzeme Özellikleri: Cast materials often exhibit different (sometimes inferior or less consistent) mechanical properties compared to wrought or AM materials, potentially requiring thicker sections (and thus more weight) to achieve the same strength. Porosity can also be a concern requiring inspection and potentially HIPing.
Advantages of Metal Additive Manufacturing for Guidance Housings:
Metal AM, particularly Powder Bed Fusion techniques like Laser Powder Bed Fusion (LPBF, also known as Selective Laser Melting or SLM) and Electron Beam Melting (EBM, with specific variants like Met3dp’s SEBM – Selective Electron Beam Melting), overcomes many of these hurdles:
- Benzersiz Tasarım Özgürlüğü: This is arguably the most significant advantage. AM allows engineers to:
- Create Complex Geometries: Internal cooling channels precisely following heat sources, intricate lattice structures for lightweighting while maintaining stiffness, smoothly blended organic shapes optimized for stress flow, and features impossible to machine or cast.
- Implement Topology Optimization: Use software to determine the most efficient material distribution to meet load requirements, resulting in highly optimized, lightweight structures that minimize mass while maximizing performance – critical for range and maneuverability in missiles.
- Integrate Functionality: Combine multiple components (e.g., housing, brackets, mounting features, thermal management elements) into a single printed part. This parça konsoli̇dasyonu reduces assembly time, minimizes potential leak paths or failure points at joints, simplifies inventory, and can further reduce weight and overall system complexity.
- Hızlı Prototipleme ve Yineleme: AM enables the production of functional prototypes directly from CAD data in days rather than weeks or months. This drastically accelerates design cycles, allowing engineers to test multiple design variations quickly, refine performance, and shorten the time-to-market for new missile systems or upgrades – a crucial factor in maintaining a technological edge in defense. Changes can be implemented simply by modifying the digital file, without the need for expensive tooling modifications.
- Material Efficiency (Reduced Buy-to-Fly Ratio): AM processes typically use only the material needed to build the part and necessary supports. While some powder is lost or requires recycling, the material waste is significantly lower compared to machining large billets of expensive materials like Ti-6Al-4V. This results in substantial cost savings, especially for high-value alloys, making AM economically viable even for relatively small production runs. This improved efficiency resonates well with defense procurement focused on optimizing budgets.
- Suitability for Low-to-Mid Volume Production: The economics of AM are less dependent on volume than traditional methods requiring dedicated tooling (like casting). This makes it ideal for the typical production volumes seen in many defense programs, which might range from single prototypes to hundreds or perhaps low thousands of units – a range where tooling costs for casting can be prohibitive, and the setup time for complex machining can be extensive.
- Supply Chain Agility and Resilience: AM enables on-demand manufacturing closer to the point of need. This can shorten lead times, reduce reliance on complex global supply chains (which can be vulnerable to disruption), and potentially enable distributed manufacturing capabilities for enhanced defense logistics. Spare parts or replacements for legacy systems can be produced without needing original tooling. Companies like Met3dp, offering comprehensive metal 3D baskı çözümleri, can become strategic partners in building these more resilient supply networks.
- Enabling Advanced Thermal Management: As mentioned, AM allows the integration of complex internal cooling channels directly within the housing walls, conforming precisely to heat-generating components. This enables far more efficient thermal management than traditional approaches (e.g., bolted-on heat sinks), which is critical for densely packed guidance electronics operating at high power levels or in high-temperature environments.
Comparative Overview:
Özellik | CNC İşleme | Yatırım Döküm | Metal Additive Manufacturing (LPBF/EBM) |
---|---|---|---|
Tasarım Karmaşıklığı | Moderate (limited by tool access) | Moderate (tooling constraints) | Çok Yüksek (complex internal/organic forms) |
Malzeme Atıkları | Yüksek | Low-Moderate | Düşük (near-net shape) |
Ağırlık Azaltma | Moderate (via pocketing) | Orta düzeyde | Yüksek (topology optimization, lattices) |
Parça Konsolidasyonu | Sınırlı | Sınırlı | Yüksek |
Lead Time (Proto) | Orta-Yüksek | Very High (due to tooling) | Düşük |
Kalıp Maliyeti | Low-Moderate (fixtures) | Yüksek | Hiçbiri |
Ideal Volume | Low to High | Yüksek | Düşük ila Orta |
Malzeme Seçenekleri | Wide (billet availability) | Moderate (castable alloys) | Growing (weldable/fusible alloys) |
Sayfalara Aktar
By leveraging these advantages, engineers can design missile guidance housings that are lighter, perform better (structurally and thermally), are produced faster, and potentially integrate more functions than ever before, directly contributing to the enhanced capability and effectiveness of future missile systems. The adoption of AM represents a strategic shift towards more agile and performance-driven manufacturing within the defense sector.
Material Selection for Mission Success: Recommended Powders (316L & Ti-6Al-4V) and Their Significance
The choice of material for a missile guidance housing is as critical as its design. The material must meet demanding structural, environmental, and sometimes thermal requirements while being compatible with the chosen manufacturing process. For metal additive manufacturing of these components, two materials stand out due to their properties, processability, and established use in demanding industries: 316L Paslanmaz Çelik ve Ti-6Al-4V Titanyum Alaşımı. The quality of the metal powder used is paramount for achieving reliable, high-density parts, making partnerships with expert powder producers like Met3dp essential. Met3dp utilizes advanced gas atomization and Plasma Rotating Electrode Process (PREP) technologies to manufacture high-sphericity, high-flowability metal powders optimized for AM processes, including not just these common alloys but also specialized materials like TiNi, TiTa, TiAl, TiNbZr, CoCrMo, various superalloys, and custom formulations crucial for cutting-edge applications.
Metal AM Processes:
Before diving into materials, it’s worth briefly mentioning the primary AM processes used:
- Lazer Toz Yatağı Füzyonu (LPBF): Uses a high-power laser to selectively melt and fuse regions of a powder bed layer by layer. Known for excellent accuracy and surface finish. It’s widely used for both 316L and Ti-6Al-4V.
- Electron Beam Melting (EBM / SEBM): Uses an electron beam in a vacuum environment to melt the powder. Typically operates at higher temperatures, which helps reduce residual stresses (especially beneficial for materials like Ti-6Al-4V). Often faster than LPBF for full-layer melts but may have a slightly rougher surface finish. Met3dp specializes in Seçici Elektron Işını Eritme (SEBM), offering printers with industry-leading print volume, accuracy, and reliability suitable for mission-critical aerospace parts.
Recommended Material Deep Dive:
1. 316L Paslanmaz Çelik:
- Kompozisyon: An austenitic stainless steel alloy containing chromium (16-18%), nickel (10-14%), molybdenum (2-3%), and low carbon (<0.03%, denoted by “L”).
- Anahtar Özellikler:
- Mükemmel Korozyon Direnci: Highly resistant to a wide range of corrosive environments, including atmospheric corrosion, marine environments, and various chemicals. Molybdenum enhances resistance to pitting and crevice corrosion.
- Good Mechanical Properties: Offers a good balance of strength, toughness, and ductility at room and moderately elevated temperatures.
- Weldability/Processability: Readily processable via LPBF and EBM/SEBM, achieving high densities (>99.5%).
- Maliyet-Etkinlik: Significantly less expensive than titanium alloys, making it a viable option when weight is not the absolute primary driver or for ground-based systems, test equipment, or training hardware.
- Manyetik Olmayan (in the annealed condition).
- Applications in Guidance Housings: Suitable for housings where extreme weight saving is less critical than robustness, cost, or specific corrosion resistance is paramount. Examples might include certain ground-launched systems, naval applications (due to saltwater resistance), prototypes where cost is a major factor, or internal structural elements not requiring the extreme strength-to-weight ratio of titanium.
- Considerations for Defense Procurement:
- Yerleşik Malzeme: Widely understood and characterized, with extensive data available.
- Supply Chain: Powder is readily available from numerous metal tozu tedarikçileri, though quality consistency is key. Sourcing from reputable manufacturers like Met3dp ensures powder characteristics optimized for AM.
- Maliyet Faktörü: Attractive for programs with tighter budget constraints or where large quantities might be needed (relative to typical defense volumes).
Typical Properties of AM 316L (Post-Stress Relief):
Mülkiyet | Approximate Value (Varies with process/parameters) | Birim |
---|---|---|
Yoğunluk | >7.95 | g/cm³ |
Nihai Çekme Dayanımı | 500 – 650 | MPa |
Akma Dayanımı (0,2%) | 200 – 500 | MPa |
Kopma Uzaması | 30 – 60 | % |
Sertlik | ~150-200 | HV (Vickers) |
Elastisite Modülü | ~190 | Not ortalaması |
Sayfalara Aktar
2. Ti-6Al-4V (Grade 5 Titanium Alloy):
- Kompozisyon: An alpha-beta titanium alloy, the workhorse of the aerospace industry, containing ~6% Aluminum, ~4% Vanadium.
- Anahtar Özellikler:
- Mükemmel Güç-Ağırlık Oranı: Roughly half the density of steel but offers comparable or higher strength, making it ideal for weight-critical applications like missiles and aircraft.
- High Temperature Capability: Retains good strength up to around 350-400°C (660-750°F).
- Superb Corrosion Resistance: Forms a stable, passive oxide layer providing outstanding resistance to corrosion in many environments, including seawater and oxidizing acids.
- İşlenebilirlik: Well-suited for both LPBF and EBM/SEBM. EBM/SEBM, operating at higher temperatures, is often favored for Ti-6Al-4V as it helps produce parts with lower residual stress. Heat treatment (stress relief, annealing, or HIP) is typically required to optimize properties.
- Biyouyumluluk: While not relevant for guidance housings, its biocompatibility underscores its high purity and corrosion resistance.
- Applications in Guidance Housings: The preferred choice for most flight applications, especially air-launched missiles, strategic missiles, and hypersonic vehicles where minimizing weight is paramount for maximizing range, payload, and maneuverability. Its high strength ensures structural integrity under extreme G-loads and vibrations.
- Considerations for Aerospace Suppliers:
- Performance Driver: The go-to material for high-performance aerospace structures. Its benefits often justify the higher cost compared to steel or aluminum.
- Malzeme Maliyeti: Significantly more expensive than 316L, both in terms of raw powder cost and processing considerations (e.g., vacuum environment for EBM, argon atmosphere for LPBF).
- Processing Expertise: Requires careful control of process parameters and specific post-processing (heat treatment, potentially HIP) to achieve optimal, consistent properties. Partnering with experienced AM providers like Met3dp, who possess deep knowledge of processing titanium alloys with their advanced SEBM systems and high-quality powders, is crucial for havacılık tedarikçileri ve defense contractors. Explore Met3dp’s range of metal powders and products.
Typical Properties of AM Ti-6Al-4V (Post-Stress Relief / Annealed):
Mülkiyet | Approximate Value (Varies with process/parameters/heat treatment) | Birim |
---|---|---|
Yoğunluk | ~4.43 | g/cm³ |
Nihai Çekme Dayanımı | 900 – 1150 | MPa |
Akma Dayanımı (0,2%) | 800 – 1050 | MPa |
Kopma Uzaması | 6 – 15 | % |
Sertlik | ~300-350 | HV (Vickers) |
Elastisite Modülü | ~110-120 | Not ortalaması |
Sayfalara Aktar
Material Quality Matters:
Regardless of the alloy chosen, the quality of the starting metal powder directly impacts the final part’s integrity. Key powder characteristics include:
- Küresellik: Affects powder flowability and packing density, influencing the density and uniformity of the final part.
- Parçacık Boyutu Dağılımı (PSD): Must be optimized for the specific AM process and machine to ensure consistent melting and layer formation.
- Akışkanlık: Ensures uniform spreading of powder layers during the build process.
- Purity/Chemistry: Must meet stringent alloy specifications with low levels of impurities (especially interstitial elements like oxygen and nitrogen for titanium).
- Absence of Satellites: Small particles attached to larger ones, which can affect flowability and packing.
Met3dp’s commitment to producing high-quality powders using state-of-the-art gaz atomizasyonu ve PREP teknolojisi ensures that customers receive materials optimized for demanding applications like missile guidance housings. Their expertise extends beyond standard alloys to encompass innovative materials, positioning them as a key partner for companies pushing the envelope in aerospace and defense manufacturing.
Choosing between 316L and Ti-6Al-4V involves a trade-off analysis based on specific mission requirements, budget constraints, and performance targets. However, the ability of metal AM to effectively process both materials opens up significant possibilities for optimizing guidance housing design and production for the next generation of missile systems.
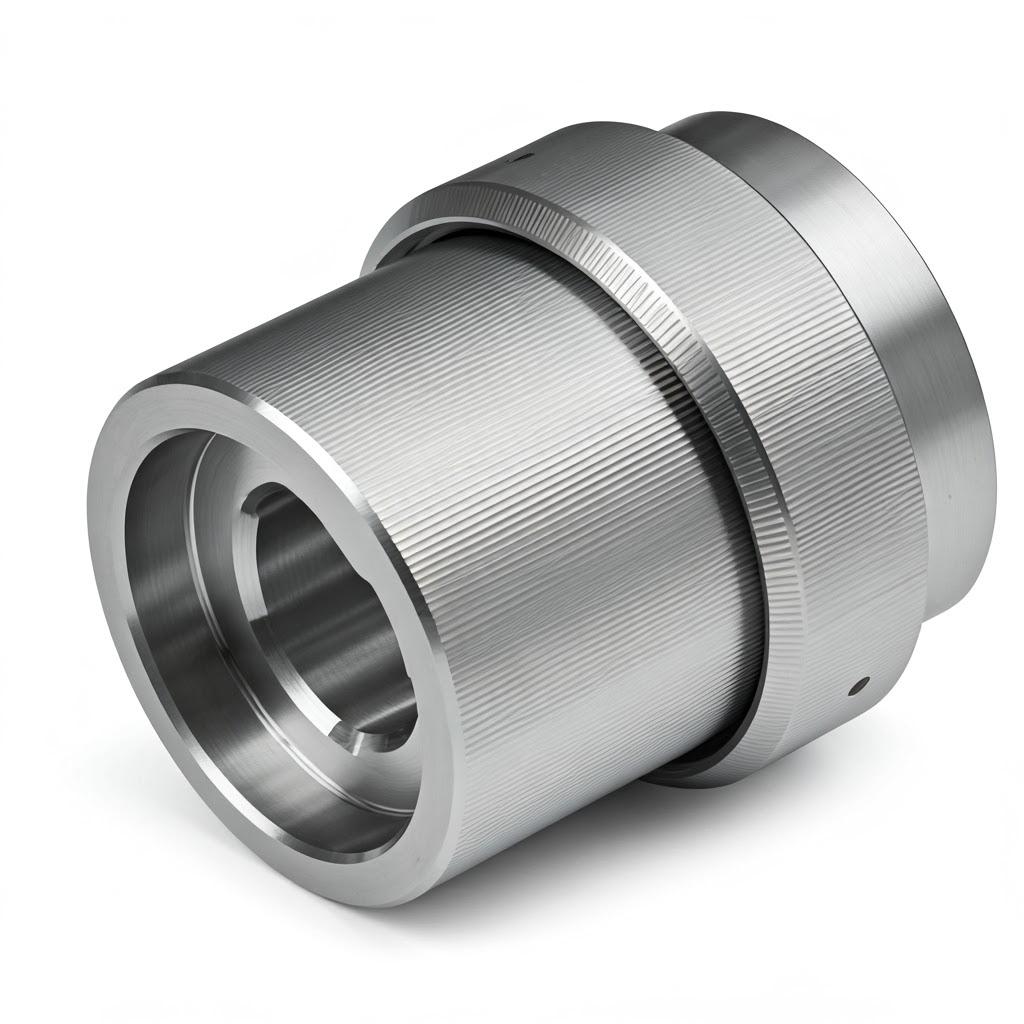
Designing for Additive: Optimizing Guidance Housings for Metal 3D Printing
Simply taking a design intended for CNC machining or casting and directly sending it to a metal 3D printer rarely yields optimal results. To truly harness the power of additive manufacturing for missile guidance housings, engineers must embrace Katmanlı Üretim Tasarımı (DfAM) principles. DfAM is not just about ensuring printability; it’s a paradigm shift focused on leveraging AM’s unique capabilities to enhance performance, reduce weight, consolidate parts, and minimize post-processing efforts. For critical components like guidance housings, applying DfAM thoughtfully is essential for mission success and requires close collaboration between design engineers and AM specialists, such as the application development team at Met3dp. Understanding the capabilities and limitations of processes like Seçici Elektron Işını Eritme (SEBM) or Laser Powder Bed Fusion (LPBF) is key to creating truly optimized designs.
Key DfAM Principles for Guidance Housings:
- Topology Optimization: This is a computational method used to find the most efficient distribution of material within a defined design space, subject to specific loads, boundary conditions, and constraints.
- Benefit for Housings: Generates lightweight, organic-looking structures that place material only where it’s structurally necessary to withstand launch G-forces, vibrations, and operational stresses. This can lead to significant weight savings (often 20-50% or more compared to traditionally designed parts) in Ti-6Al-4V housings, directly improving missile range and maneuverability.
- Düşünceler: Optimized designs often feature complex, freeform geometries that are only manufacturable via AM. Requires specialized software and engineering expertise to set up and interpret results correctly. Need to consider manufacturability constraints (e.g., minimum feature size, overhang angles) during optimization.
- Kafes Yapılar ve Dolgu: AM allows for the creation of internal lattice structures – complex networks of interconnected struts or repeating unit cells.
- Benefit for Housings: Can drastically reduce weight in non-critical areas while maintaining required stiffness or providing energy absorption characteristics (vibration damping). Can also be used to create internal channels for fluid flow or heat transfer within the housing walls. Different lattice types (e.g., cubic, octet-truss) offer varying mechanical properties.
- Düşünceler: Requires careful analysis to ensure structural integrity. Powder removal from complex internal lattices can be challenging and must be planned for during design (e.g., incorporating drainage/access holes). Needs validation through simulation and testing.
- Parça Konsolidasyonu: AM enables the integration of multiple separate components into a single, monolithic printed part.
- Benefit for Housings: A guidance housing assembly might traditionally consist of the main body, cover, mounting brackets, internal supports, and potentially thermal straps. AM could potentially combine several of these elements. This reduces part count, eliminates fasteners and joints (potential failure points or leak paths), simplifies assembly, reduces overall weight, and streamlines the tedarik zinciri by reducing the number of individual components to source and manage.
- Düşünceler: Increases complexity of the single printed part. May make inspection or repair of internal features more difficult. Requires a holistic view of the assembly and careful functional decomposition.
- Minimum Wall Thickness and Feature Size: Every AM process and machine has limitations on the minimum thickness of walls and the smallest features (e.g., pins, holes) it can reliably produce.
- Benefit for Housings: Designing with these limits in mind ensures manufacturability and structural integrity. Thin walls are key to lightweighting, but walls that are too thin may warp during printing or lack sufficient strength.
- Düşünceler: Typical minimum wall thicknesses for LPBF/EBM might range from 0.3mm to 1.0mm, depending on the material, machine, orientation, and geometry. Small holes might need to be drilled post-print for accuracy. Consult your AM provider (like Met3dp) for specific machine capabilities.
- Destek Yapısı Stratejisi: Most Powder Bed Fusion processes require support structures for overhanging features (typically angles below 45 degrees from the horizontal build plane) and to anchor the part to the build plate, mitigating warping.
- Benefit for Housings: Well-designed supports ensure successful printing without distortion or collapse. Designing parts to minimize the need for supports (self-supporting angles, strategic orientation) reduces material usage, print time, and post-processing effort (support removal).
- Düşünceler: Support removal can be labor-intensive and potentially damage part surfaces, especially on internal or hard-to-reach features common in housings. Design should prioritize accessibility for support removal tools. Sometimes, supports must be left in inaccessible internal cavities if they don’t impede function. EBM/SEBM processes, operating at higher temperatures with powder sintering, often require fewer supports than LPBF.
- Yapı Oryantasyonu: The orientation of the housing on the build platform significantly impacts several factors.
- Benefit for Housings: Optimizing orientation can minimize support structures, improve surface finish on critical faces, reduce build time (by minimizing height), and influence final mechanical properties (due to potential anisotropy).
- Düşünceler: Anisotropy (directional variation in properties) can occur in AM parts. Critical load paths should ideally be aligned with the direction of maximum strength (often parallel to the build plate, but varies with process/material). Orientation affects thermal gradients and potential for warping. Often a trade-off between minimizing supports, maximizing surface quality on certain features, and optimizing properties.
- Termal Yönetim Özellikleri: AM allows for highly integrated thermal solutions.
- Benefit for Housings: Design intricate, conformal cooling channels that follow the exact contours of heat-generating electronic components inside the housing. Integrate thin, high-surface-area fins or pin structures directly into the housing walls to act as heat sinks. These are far more effective than traditional thermal management methods.
- Düşünceler: Requires Computational Fluid Dynamics (CFD) simulation to optimize channel design. Ensuring powder removal from complex internal channels is critical. Wall thickness and material choice influence thermal conductivity.
DfAM Workflow Integration:
Implementing DfAM effectively often involves:
- Collaboration: Early engagement between design engineers and AM manufacturing experts.
- Simulation: Using build simulation software to predict thermal stresses, distortion, and optimize orientation and support strategies before committing to a print.
- Yineleme: Leveraging AM’s rapid prototyping capability to test and refine DfAM strategies.
By thinking additively from the start, engineers designing missile guidance housings can unlock significant performance gains and manufacturing efficiencies, moving beyond simply replicating old designs to creating truly optimized components tailored for the unique capabilities of metal 3D printing. This approach is fundamental for havacılık tedarikçileri aiming to deliver cutting-edge solutions to defense contractors.
Precision Matters: Tolerance, Surface Finish, and Dimensional Accuracy in AM Housings
While additive manufacturing excels at producing complex geometries, achieving the tight tolerances, specific surface finishes, and high dimensional accuracy required for missile guidance housings often necessitates careful planning and frequently involves post-processing steps. Procurement managers and engineers must understand the inherent capabilities and limitations of AM processes like LPBF and EBM/SEBM regarding precision to set realistic expectations and specify requirements appropriately.
Achievable Tolerances:
- As-Built Tolerances: The dimensional accuracy directly off the printer typically falls within the range of ±0.1mm to ±0.3mm (or ±0.1% to ±0.2% of the dimension, whichever is larger) for well-controlled LPBF and EBM/SEBM processes. However, this can vary significantly based on:
- Part Size and Geometry: Larger parts and complex shapes are more prone to thermal distortion, potentially leading to larger deviations.
- Malzeme: Different materials exhibit varying shrinkage and stress characteristics during printing and cooling (e.g., Ti-6Al-4V is known for higher residual stress).
- Machine Calibration: Regular calibration and maintenance of the AM system are crucial. Met3dp’s focus on industry-leading accuracy and reliability in their printers addresses this directly.
- Build Parameters: Layer thickness, energy input, scan strategy all influence accuracy.
- Orientation and Supports: Affect thermal behavior and potential for distortion during the build and after support removal.
- Achieving Tighter Tolerances: Many features on a guidance housing, such as mating surfaces for sealing, interfaces with optical sensors, mounting points for PCBs, and fastener holes/threads, often require tolerances tighter than the typical as-built capabilities (e.g., ±0.025mm to ±0.05mm). These tighter tolerances are almost always achieved through post-process CNC machining of the critical features on the near-net shape AM part. DfAM should account for adding sufficient stock material (e.g., 0.5mm – 1.0mm) on these critical surfaces specifically for subsequent machining operations.
Yüzey İşlemi (Pürüzlülük):
- As-Built Surface Finish: The surface roughness (typically measured as Ra – arithmetic average roughness) of AM parts depends heavily on the process, material, orientation, and parameters.
- LPBF: Generally produces smoother surfaces, often in the range of 5-15 µm Ra. Upward-facing and vertical surfaces tend to be smoother than downward-facing surfaces (which are affected by supports) or sharply curved areas.
- EBM/SEBM: Tends to produce rougher surfaces, typically 20-40 µm Ra, due to larger powder particle sizes and higher processing temperatures causing some particle sintering.
- Internal Channels: Can be significantly rougher and harder to finish.
- Implications for Housings:
- Sızdırmazlık Yüzeyleri: As-built roughness is usually insufficient for effective O-ring or gasket sealing; these surfaces typically require machining or polishing.
- Mating Interfaces: Roughness can affect the precision of fit between the housing and other components.
- Fatigue Life: Rough surfaces can act as stress concentrators, potentially reducing fatigue life. Surface improvement may be needed for components subjected to high cyclical loading.
- Flow Resistance: Roughness in internal channels (e.g., for cooling) can increase flow resistance or pressure drop.
- Yüzey İşleminin İyileştirilmesi: Various post-processing techniques can be employed: bead blasting, tumbling, micro-machining, polishing, electropolishing. The choice depends on the required Ra value, material, geometry, and cost considerations.
Dimensional Accuracy & Stability:
- Factors Influencing Accuracy: Beyond initial print tolerances, factors like residual stress relief during heat treatment and stresses induced during support removal or machining can affect final dimensions.
- Importance of Stability: For guidance housings, dimensional stability over time and under varying temperatures is critical to maintain the alignment of sensitive internal components. Stress relief heat treatments are essential, especially for Ti-6Al-4V, to minimize residual stresses that could lead to distortion later in the component’s life cycle.
- Metrology and Inspection: Given the critical nature of guidance housings, rigorous inspection is non-negotiable. This is a key area for quality assurance managers içinde defense supply chain. Common methods include:
- Coordinate Measuring Machines (CMM): For precise verification of critical dimensions, tolerances, and geometric dimensioning and tolerancing (GD&T) features.
- 3D Laser Scanning / Structured Light Scanning: For comparing the overall geometry of the printed part against the original CAD model, identifying deviations and warpage.
- Computed Tomography (CT) Scanning: Increasingly used for non-destructively inspecting internal features, channels, lattice structures, and detecting internal defects like porosity. Essential for verifying complex AM parts.
Specification Best Practices:
Engineers and procurement specialists should clearly define tolerance and surface finish requirements on drawings and specifications, distinguishing between:
- As-built acceptable tolerances/finishes for non-critical features.
- Tighter tolerances/finishes required on specific critical features, indicating they will be achieved via post-machining.
Understanding these precision aspects allows for realistic design choices, appropriate planning for post-processing, and effective communication with the chosen metal 3D printing service provider, ensuring the final guidance housing meets all functional requirements. Explore the various 3D baskı yöntemleri and their respective precision capabilities.
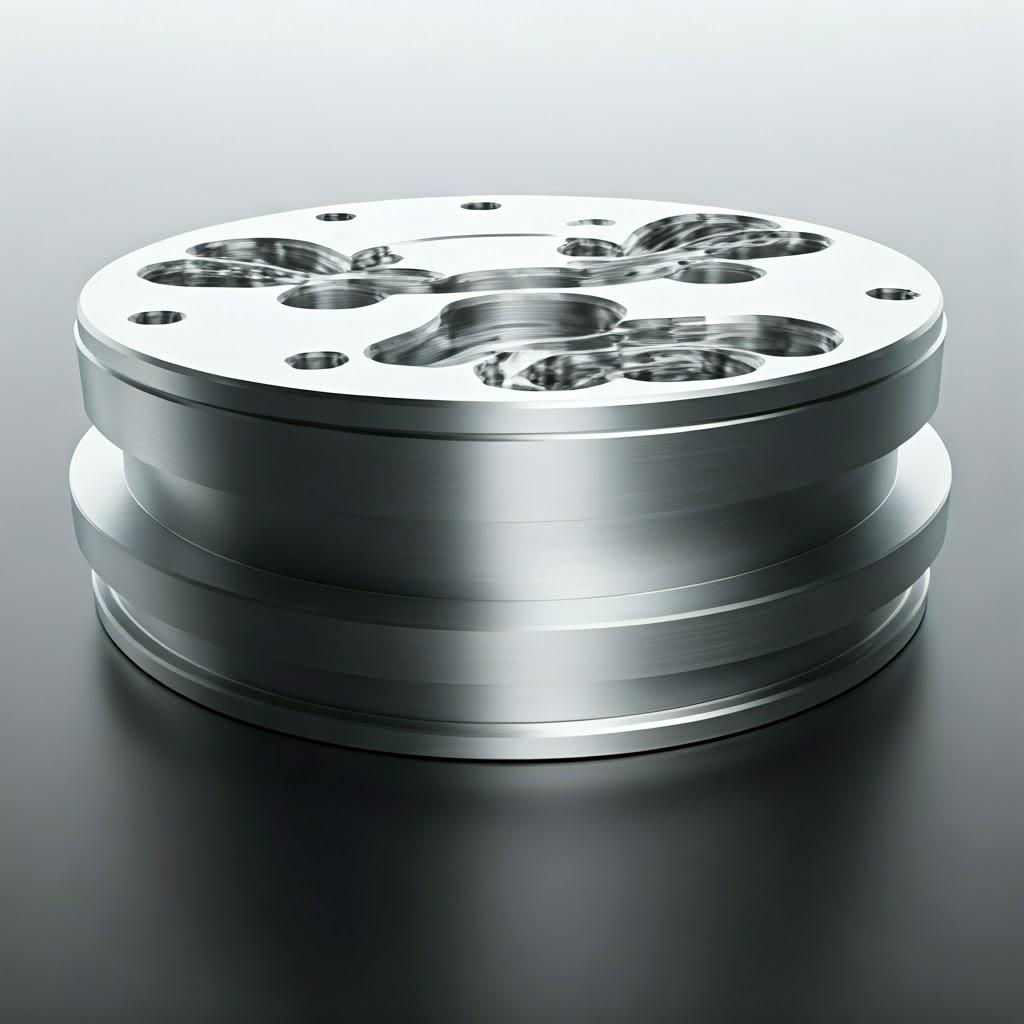
Beyond the Build: Post-Processing Requirements for AM Guidance Housings
A common misconception about additive manufacturing is that parts come out of the printer ready to use. For demanding applications like missile guidance housings, the printing process is often just the first step in a multi-stage manufacturing workflow. Post-processing is typically essential to achieve the required material properties, dimensional accuracy, surface finish, and overall part integrity. These steps add cost and time but are non-negotiable for ensuring the reliability and performance demanded in aerospace and defense.
Common Post-Processing Steps for AM Guidance Housings (316L & Ti-6Al-4V):
- Stres Giderici / Isıl İşlem: This is arguably the most critical post-processing step, especially for Ti-6Al-4V.
- Amacımız: The rapid heating and cooling inherent in PBF processes induce significant internal stresses within the printed part. These stresses can cause distortion (warpage) after the part is removed from the build plate or later in its service life, and can negatively impact mechanical properties, particularly fatigue life. Heat treatment relieves these stresses and homogenizes the microstructure. For Ti-6Al-4V, it’s also used to tailor specific microstructures (e.g., alpha-beta phases) to achieve desired strength and ductility combinations (annealing).
- Süreç: Parts are typically heat-treated while still attached to the build plate (for stress relief) in a controlled atmosphere furnace (vacuum or inert gas like Argon, especially crucial for Titanium to prevent oxygen uptake). Specific temperature cycles and durations depend on the material and desired properties (e.g., Ti-6Al-4V stress relief might be ~650-800°C, while annealing might be higher). 316L generally requires lower temperatures for stress relief (~550-650°C).
- Importance: Failure to perform proper stress relief can lead to dimensional instability and premature failure.
- Removal from Build Plate & Support Structure Removal:
- Amacımız: Separating the part(s) from the build plate and removing the temporary support structures generated during the print.
- Süreç: Typically done using wire EDM (Electrical Discharge Machining), band sawing, or manual breaking/cutting. Support removal can be manual (using hand tools, pliers) or sometimes aided by machining.
- Zorluklar: Can be labor-intensive, especially for complex internal supports. Risk of damaging the part surface during removal. DfAM plays a key role in designing supports for easier removal. Access to internal channels or cavities for support removal must be considered.
- Sıcak İzostatik Presleme (HIP):
- Amacımız: To eliminate internal porosity (gas pores or lack-of-fusion voids) that can sometimes occur during the AM process, and to further improve microstructure and mechanical properties, particularly fatigue strength, toughness, and ductility. It essentially achieves near-100% density.
- Süreç: Involves subjecting the part to high temperature (below melting point) and high isostatic pressure (using an inert gas like Argon) simultaneously in a specialized HIP vessel.
- Uygulanabilirlik: Commonly applied to critical Ti-6Al-4V components in aerospace where fatigue life and defect elimination are paramount. Less common but sometimes used for 316L if maximum density and properties are required. Adds significant cost and lead time.
- CNC İşleme:
- Amacımız: To achieve tight tolerances on critical features, create precise sealing surfaces, machine threads, drill precise holes, and improve surface finish on specific areas.
- Süreç: Standard multi-axis CNC milling or turning operations are used on the near-net shape AM part. Requires careful fixture design to hold potentially complex AM geometries securely without distortion. Sufficient machining allowance must be included in the AM design.
- Gereklilik: Almost always required for guidance housings to meet interfacing and sealing requirements.
- Yüzey İşlemi:
- Amacımız: To improve the as-built surface roughness for aesthetic, functional (e.g., sealing, friction reduction), or fatigue life reasons.
- Processes:
- Abrasive Blasting (Bead/Sand): Common method to achieve a uniform matte finish, remove loose powder particles, and slightly improve fatigue resistance (compressive stress).
- Tumbling/Vibratory Finishing: Uses abrasive media in a rotating or vibrating drum to smooth surfaces and deburr edges, suitable for batches of smaller parts.
- Parlatma: Manual or automated polishing for achieving very smooth, mirror-like finishes on specific surfaces (e.g., optical interfaces, critical sealing zones).
- Elektro parlatma: An electrochemical process that removes a thin layer of material, smoothing surfaces and improving corrosion resistance (particularly effective for 316L).
- Temizlik:
- Amacımız: To remove any residual powder, machining fluids, fingerprints, or other contaminants before final inspection, assembly, or coating.
- Süreç: Typically involves ultrasonic cleaning baths with appropriate solvents or detergents. Critical for ensuring internal channels are clear.
- Kaplamalar:
- Amacımız: To provide enhanced environmental protection, wear resistance, specific thermal properties, or electromagnetic shielding.
- Processes for Housings:
- Passivation (for 316L): Chemical treatment to enhance the passive oxide layer, improving corrosion resistance.
- Anodizing (for Ti-6Al-4V): Electrolytic process to grow a controlled oxide layer, improving wear resistance, corrosion resistance, and providing an electrically insulating surface (can also be colored). Type II (decorative/corrosion) or Type III (hardcoat) are common.
- Plating (e.g., Nickel, Gold): For enhanced conductivity, solderability, or wear resistance on specific areas.
- Painting/Priming: For camouflage, additional corrosion protection, or thermal control. Requires proper surface preparation.
- EMI Shielding Coatings: Conductive paints or platings applied to internal or external surfaces.
- Tahribatsız Muayene (NDT): While technically an inspection step, NDT is often integrated into the post-processing workflow.
- Amacımız: To verify the internal and external integrity of the part without damaging it. Essential for flight-critical defense components.
- Yöntemler: Dye Penetrant Inspection (DPI) for surface-breaking cracks, Ultrasonic Testing (UT) for internal flaws, Radiographic Testing (X-ray) or Computed Tomography (CT) for detecting internal voids, inclusions, and verifying complex internal geometries.
Workflow Considerations:
The specific sequence and combination of these post-processing steps depend heavily on the application requirements, material choice, AM process used, and cost/lead time constraints. Planning this workflow is a crucial part of the manufacturing process development, requiring expertise often found with experienced metal additive manufacturing service providers gibi Met3dp, who offer comprehensive solutions beyond just printing. Understanding these steps is vital for procurement managers to accurately assess project timelines and costs.
Navigating Challenges in AM for Defense Components: Solutions and Best Practices
While metal additive manufacturing offers numerous advantages for producing missile guidance housings, it is not without its challenges. Successfully implementing AM for critical defense applications requires acknowledging potential issues and proactively implementing robust solutions and best practices throughout the design, manufacturing, and qualification process. Anticipating and mitigating these challenges is key to ensuring the reliability and performance expected by defense contractors and end-users.
Common Challenges and Mitigation Strategies:
- Çarpıtma ve Bozulma:
- Sebep: Uneven heating and cooling during the layer-by-layer fusion process creates internal stresses that can cause the part to warp or distort, especially after removal from the build plate. Thin features, large flat areas, and significant overhangs are particularly susceptible. Ti-6Al-4V is more prone due to its lower thermal conductivity and higher coefficient of thermal expansion compared to steels.
- Hafifletme:
- Build Simulation: Use specialized software to predict thermal behavior and distortion, allowing for compensation in the design or optimization of build orientation and support strategy.
- Optimize Edilmiş Yönlendirme: Orient the part to minimize thermal gradients across large sections and reduce the build height if possible.
- Sağlam Destek Yapıları: Use well-designed supports to anchor the part securely to the build plate and conduct heat away. Consider stress-reducing support designs.
- Optimized Scan Strategies: Employ specific laser/electron beam scan patterns (e.g., island scanning, checkerboard patterns) to distribute heat more evenly and reduce localized stress buildup.
- Process Parameter Control: Maintain tight control over parameters like beam power, speed, layer thickness, and chamber temperature (especially important in EBM/SEBM where higher pre-heat reduces thermal gradients).
- İnşaat Sonrası Stres Giderme: Perform stress relief heat treatment while the part is still attached to the build plate whenever possible.
- Residual Stress Management:
- Sebep: Similar to warping, residual stresses are inherent to the PBF process. Even if warping is controlled, high residual stresses can negatively impact fatigue life, fracture toughness, and dimensional stability over time.
- Hafifletme:
- Isıl İşlem: Appropriate stress relief and annealing cycles are crucial for reducing residual stresses to acceptable levels.
- HIPing: Can help relieve stress while also closing pores.
- Tasarım Hususları: Avoid sharp internal corners or abrupt changes in thickness, which act as stress concentrators.
- Process Choice: EBM/SEBM generally produces parts with lower residual stress than LPBF due to the higher processing temperatures.
- Gözeneklilik Kontrolü:
- Sebep: Small internal voids can form due to trapped gas (gas porosity, often spherical) or incomplete melting/fusion between layers or scan tracks (lack-of-fusion porosity, often irregular). Porosity acts as a defect, reducing density, strength, and especially fatigue life.
- Hafifletme:
- Yüksek Kaliteli Toz: Use powder with controlled particle size distribution, high sphericity, good flowability, and low trapped gas content, sourced from reputable metal tozu tedarikçileri gibi Met3dp. Proper powder handling and storage (e.g., avoiding moisture contamination) are essential.
- Optimize Edilmiş Süreç Parametreleri: Ensure correct energy density (power, speed, hatch spacing, layer thickness) to achieve complete melting and fusion without excessive vaporization or spatter. Requires extensive process development and qualification.
- Kontrollü Atmosfer: Maintain a high-purity inert gas atmosphere (Argon/Nitrogen for LPBF) or high vacuum (EBM/SEBM) to minimize contamination and gas pickup.
- Sıcak İzostatik Presleme (HIP): Highly effective at closing both gas and lack-of-fusion porosity, significantly improving fatigue properties, often specified for critical Ti-6Al-4V parçalar.
- NDT (CT Scanning): Used to detect and characterize internal porosity.
- Destek Yapısı Kaldırma Zorlukları:
- Sebep: Complex internal geometries, delicate features, or poorly designed supports can make removal time-consuming, costly, and risk damaging the part. Access can be a major issue for internal channels within housings.
- Hafifletme:
- DfAM for Minimal Supports: Design parts with self-supporting angles (>45°) where possible. Orient the part to minimize overhangs requiring support.
- Optimized Support Design: Use support structures designed for easier removal (e.g., smaller contact points, perforations, specific geometries). Software tools can assist with this.
- Accessibility Planning: Ensure adequate access paths are designed into the part for tools to reach and remove internal supports. Consider designing features to be machined away later if they obstruct support removal.
- Process Selection: EBM/SEBM often requires fewer supports than LPBF.
- Specialized Removal Techniques: Utilize appropriate tools, potentially including micro-machining or electrochemical methods for difficult supports.
- Achieving Consistent Material Properties:
- Sebep: Variations in process parameters, powder batches, machine calibration, or post-processing can lead to inconsistencies in microstructure and mechanical properties (strength, ductility, fatigue life) both within a single part and between different builds. Anisotropy (direction-dependent properties) is also inherent to some extent.
- Hafifletme:
- Robust Process Control: Implement strict quality control measures for incoming powder, machine calibration, parameter monitoring during the build (e.g., melt pool monitoring), and post-processing steps.
- Süreç Kalifikasyonu: Thoroughly qualify the entire process (machine, material, parameters, post-processing) according to relevant standards (e.g., SAE AMS standards for aerospace).
- Material Testing: Perform regular tensile testing, hardness testing, and microstructural analysis on witness coupons built alongside actual parts to verify properties for each build or batch.
- Standartlaştırma: Adhere to industry best practices and standards (e.g., those developed by ASTM F42 committee, SAE AMS).
- Supplier Expertise: Partner with experienced AM service providers like Met3dp, who have established process control protocols and expertise in producing parts with consistent properties, leveraging their knowledge from both printer manufacturing and powder production.
- Yeterlilik ve Sertifikasyon:
- Sebep: For flight-critical defense components, demonstrating equivalence or superiority to traditionally manufactured parts requires a rigorous qualification and certification process, which can be time-consuming and expensive. Lack of universally accepted, detailed standards for certain AM aspects can be a hurdle.
- Hafifletme:
- Adopt Existing Standards: Utilize established aerospace standards where applicable (e.g., AS9100 for quality management, MMPDS for material property data if available for AM materials, specific AMS specifications for processes and materials).
- Develop Robust Internal Standards: Create comprehensive internal specifications covering the entire AM workflow, from powder to final part inspection.
- Protoyping and Extensive Testing: Generate statistically significant data through extensive mechanical testing (static, fatigue, fracture toughness), NDT, and potentially functional testing of the component under simulated operational conditions.
- Collaboration: Work closely with certification authorities and prime contractors early in the development process.
- Leverage Supplier Data: Reputable suppliers often have significant internal data on their processes and materials that can support qualification efforts.
Addressing these challenges requires a combination of advanced technology, process expertise, rigorous quality control, and a DfAM mindset. While obstacles exist, the significant benefits offered by AM for missile guidance housings make overcoming these challenges a worthwhile endeavor for organizations seeking to advance their defense capabilities.
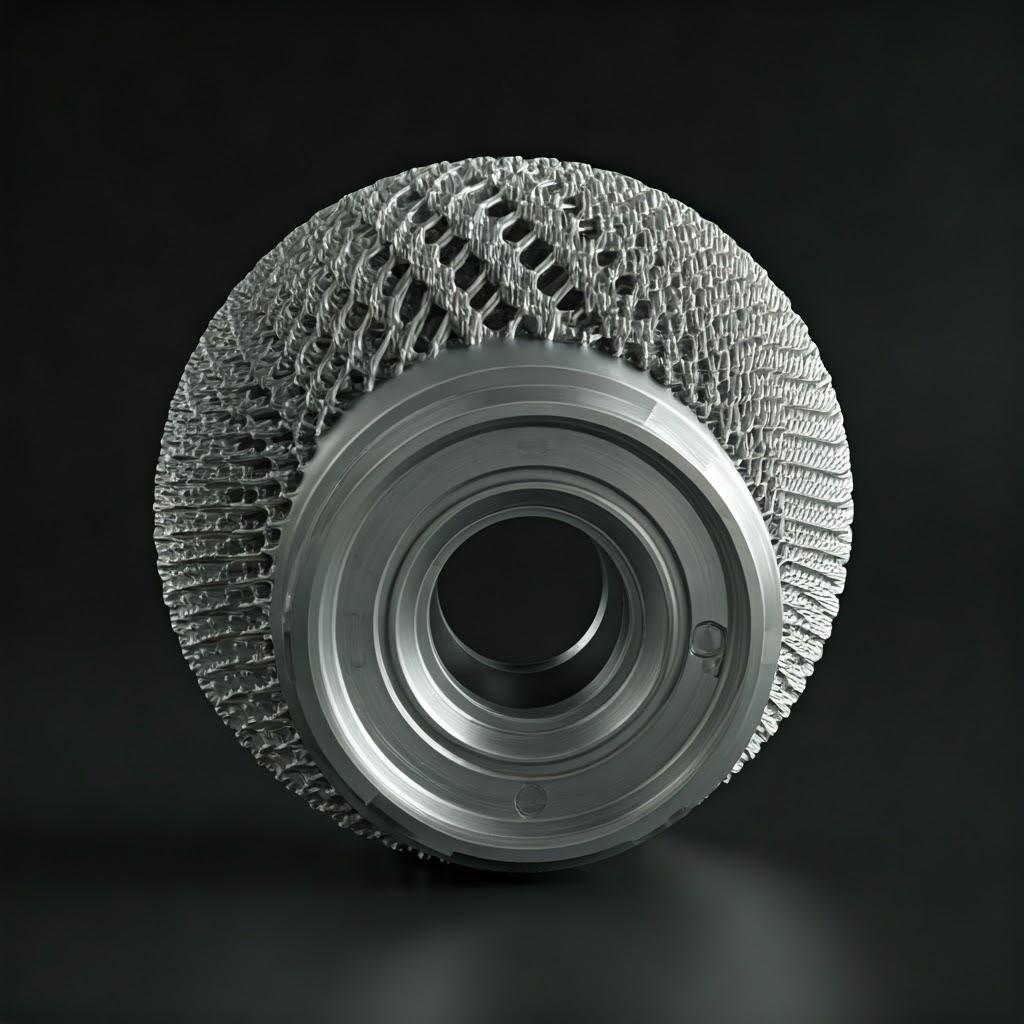
Selecting Your Strategic Partner: How to Choose the Right Metal 3D Printing Service Provider for Defense Projects
Choosing the right manufacturing partner is always critical, but when dealing with additive manufacturing for sensitive defense components like missile guidance housings, the selection process demands exceptional rigor. The capabilities, expertise, quality systems, and security protocols of your chosen metal 3D printing service provider will directly impact the success, reliability, and compliance of your project. For procurement managers ve engineering leads navigating the AM landscape, evaluating potential suppliers requires looking beyond mere printing capabilities to assess their suitability as a long-term strategic partner within the demanding defense supply chain.
Key Evaluation Criteria for AM Service Providers:
- Certifications and Compliance: This is often the first filter for defense applications.
- AS9100: The standard for Quality Management Systems in the Aerospace industry. Essential for demonstrating commitment to quality, traceability, and process control required for flight hardware.
- ITAR Compliance (International Traffic in Arms Regulations): Absolutely critical for any supplier handling US defense-related projects or technical data. Ensure the provider is registered and has robust procedures to control access to sensitive information and hardware. Equivalent regulations in other countries must also be considered (e.g., German BAFA export controls).
- ISO 9001: A general quality management standard, often a prerequisite for AS9100.
- Cybersecurity Compliance: Increasingly important, standards like NIST SP 800-171 or CMMC (Cybersecurity Maturity Model Certification) in the US may be required to protect controlled unclassified information (CUI).
- Material Expertise and Sourcing:
- Relevant Alloy Experience: Demonstrated experience printing and post-processing the specific alloys required (e.g., Ti-6Al-4V, 316L) to aerospace standards. Ask for evidence of material characterization data and process validation.
- Powder Quality and Traceability: Does the provider have stringent controls for sourcing, testing, handling, and recycling metal powders? Full traceability from powder batch to final part is essential. Providers like Met3dp, who manufacture their own high-quality powders using advanced gaz atomizasyonu ve PREP teknolojileri, offer a distinct advantage in ensuring powder consistency and traceability right from the source. Explore the company’s background and commitment to quality.
- Broader Material Portfolio: While you may need Ti-6Al-4V now, a provider with expertise across a wider range of aerospace alloys (superalloys, aluminum alloys, specialized titanium grades like those offered by Met3dp – TiNi, TiTa, etc.) indicates deeper material science knowledge.
- Technological Capability and Capacity:
- Appropriate AM Technology: Do they operate the right type of machines (LPBF, EBM/SEBM) for your material and application needs? Met3dp’s SEBM printers, for instance, offer benefits like lower residual stress for Ti-6Al-4V and potentially faster build rates for certain geometries.
- Machine Fleet and Build Volume: Ensure they have sufficient capacity (number and size of machines) to meet your prototyping and potential production volume needs within required lead times. Redundancy (multiple machines) is also important for risk mitigation.
- In-house Post-Processing: Does the provider offer critical post-processing services (heat treatment, HIP, CNC machining, NDT) in-house or through qualified partners? A vertically integrated solution can streamline the workflow, improve quality control, and shorten lead times.
- Advanced Monitoring/Control: Do their machines incorporate melt pool monitoring or other in-process quality control measures?
- Experience, Track Record, and Expertise:
- Aerospace/Defense Experience: Have they successfully completed projects of similar complexity and criticality for other aerospace or defense clients? Case studies, references (where permissible), and examples of past work are valuable indicators.
- Application Engineering Support: Do they offer DfAM expertise? Can their engineers collaborate with your team to optimize the guidance housing design for additive manufacturing, identify potential issues early, and recommend best practices? Met3dp emphasizes providing comprehensive solutions, including application development services.
- Problem-Solving Skills: AM can present unexpected challenges. Look for a partner with demonstrated troubleshooting skills and a deep understanding of the process physics.
- Quality Management System (QMS):
- Robust Inspection Capabilities: In-house CMM, 3D scanning, metallography lab, and ideally NDT capabilities (or strong partnerships for NDT) are essential for verifying part quality.
- Process Control Documentation: They should have well-documented procedures for every step, from design review and build setup to post-processing and final inspection.
- Continuous Improvement Culture: Look for evidence of ongoing efforts to refine processes and improve quality.
- Project Management and Communication:
- Clear Communication Channels: A dedicated point of contact, regular progress updates, and responsiveness are crucial, especially for complex defense projects.
- Teknik Destek: Easy access to knowledgeable technical staff to discuss design, material, and process issues.
- Project Planning: Ability to provide realistic quotes, lead times, and manage project milestones effectively.
- Security Protocols:
- Data Security: Secure systems for handling sensitive CAD models, technical specifications, and project information (NDAs, secure file transfer, access controls).
- Physical Security: Controlled access to manufacturing facilities where defense components are being produced.
Evaluating potential metal katkı imalat tedarikçileri against these criteria will help ensure you select a partner capable of delivering high-quality, compliant missile guidance housings, contributing to the success and reliability of critical defense systems. Don’t just look for a vendor; seek a strategic partner invested in your success.
Understanding the Investment: Cost Factors and Lead Time for AM Guidance Housings
Additive manufacturing introduces different cost structures and lead time dynamics compared to traditional methods. For defense procurement teams and project managers, understanding these factors is crucial for accurate budgeting, scheduling, and comparing AM against conventional alternatives for missile guidance housings.
Breakdown of Cost Drivers in Metal AM:
- Malzeme Maliyeti:
- Powder Type: The single biggest material cost differentiator. Ti-6Al-4V powder is significantly more expensive (often 5-10x or more) than 316L stainless steel powder. Other exotic aerospace alloys can be even pricier.
- Volume Used: The amount of powder consumed to print the part and its supports. DfAM techniques like topology optimization and lattice structures directly impact this by reducing part volume.
- Powder Recycling/Refresh Rates: Efficient powder handling and recycling strategies employed by the service provider can influence costs, though strict quality control is needed to ensure reused powder meets specifications. Sourcing high-quality powder from reliable manufacturers like Met3dp ensures optimal performance and potentially better yields.
- Machine Time (Amortization & Operation):
- Yapım süresi: The time the AM machine is occupied printing the part. Influenced by part volume (more material = longer print), part height (more layers = longer print), complexity (more intricate scanning = longer print), and chosen layer thickness (thinner layers = better resolution but longer time). Multiple parts can often be nested onto a single build plate to improve machine utilization.
- Machine Hourly Rate: Reflects the capital cost of the sophisticated AM equipment, maintenance, consumables (e.g., filters, inert gas), energy consumption, and facility overheads. EBM/SEBM machines might have different operating cost profiles than LPBF machines.
- İşçilik Maliyetleri:
- Pre-Processing: CAD model preparation, DfAM consultation, build simulation, build file setup.
- Machine Operation: Setting up the build, monitoring the process, removing the completed build.
- İşlem sonrası: This can be a significant labor component – manual support removal, finishing, inspection, fixture design and setup for machining.
- Kalite Güvencesi: Inspection, testing, documentation generation.
- İşlem Sonrası Maliyetler:
- Heat Treatment/HIP: Furnace time, energy, inert gas/vacuum requirements, specialized equipment costs (especially for HIP).
- İşleme: CNC machine time, tooling, programming, fixture costs. The extent of machining required heavily influences cost.
- Yüzey İşlemi: Costs vary widely depending on the method (blasting is relatively cheap, extensive manual polishing is expensive).
- NDT: Equipment and certified personnel costs for methods like CT scanning can be substantial but are often mandatory.
- Development and Engineering Costs:
- DfAM Efforts: Initial engineering time spent optimizing the design for AM.
- Simulation: Software licenses and expertise for build process or performance simulation.
- Süreç Kalifikasyonu: Costs associated with developing and validating the manufacturing process, especially for new or highly critical components.
- Quality Assurance and Certification Costs:
- Generating required documentation, performing qualification testing, maintaining certifications (AS9100, ITAR).
Factors Influencing Lead Time:
- Part Complexity and Size: Larger and more complex parts naturally take longer to print and potentially longer to post-process.
- Print Queue / Machine Availability: The service provider’s current workload and machine availability directly impact when a build can be started. Booking capacity in advance may be necessary for urgent projects.
- Extent of Post-Processing: Parts requiring extensive machining, multiple heat treatment cycles, HIP, complex finishing, or rigorous NDT will have significantly longer lead times than simpler parts requiring minimal finishing.
- Testing and Validation: If specific functional testing or extensive material property validation is required, this adds time.
- Sipariş Hacmi: While AM setup is fast, printing time scales with volume. However, multiple parts can often be printed simultaneously up to the build chamber capacity. Post-processing can become a bottleneck for larger batches if not adequately planned for. Considerations for toptan veya toplu si̇pari̇ş logistics and scheduling are important for production scenarios.
- Supplier Responsiveness: Communication efficiency and project management capabilities of the chosen partner.
Managing Expectations:
While AM enables rapid prototyping, the total lead time for a fully qualified, post-processed production part like a guidance housing can still range from several weeks to a few months, depending heavily on the factors above. It’s crucial to have open discussions with potential AM suppliers to get realistic quotes and lead time estimates based on finalized designs and specifications. While AM might sometimes appear more expensive per part than high-volume traditional methods on the surface, a total cost of ownership analysis – considering reduced material waste, assembly simplification, shorter development cycles, and improved performance – often reveals significant overall value, particularly for complex, low-to-mid volume defense components.
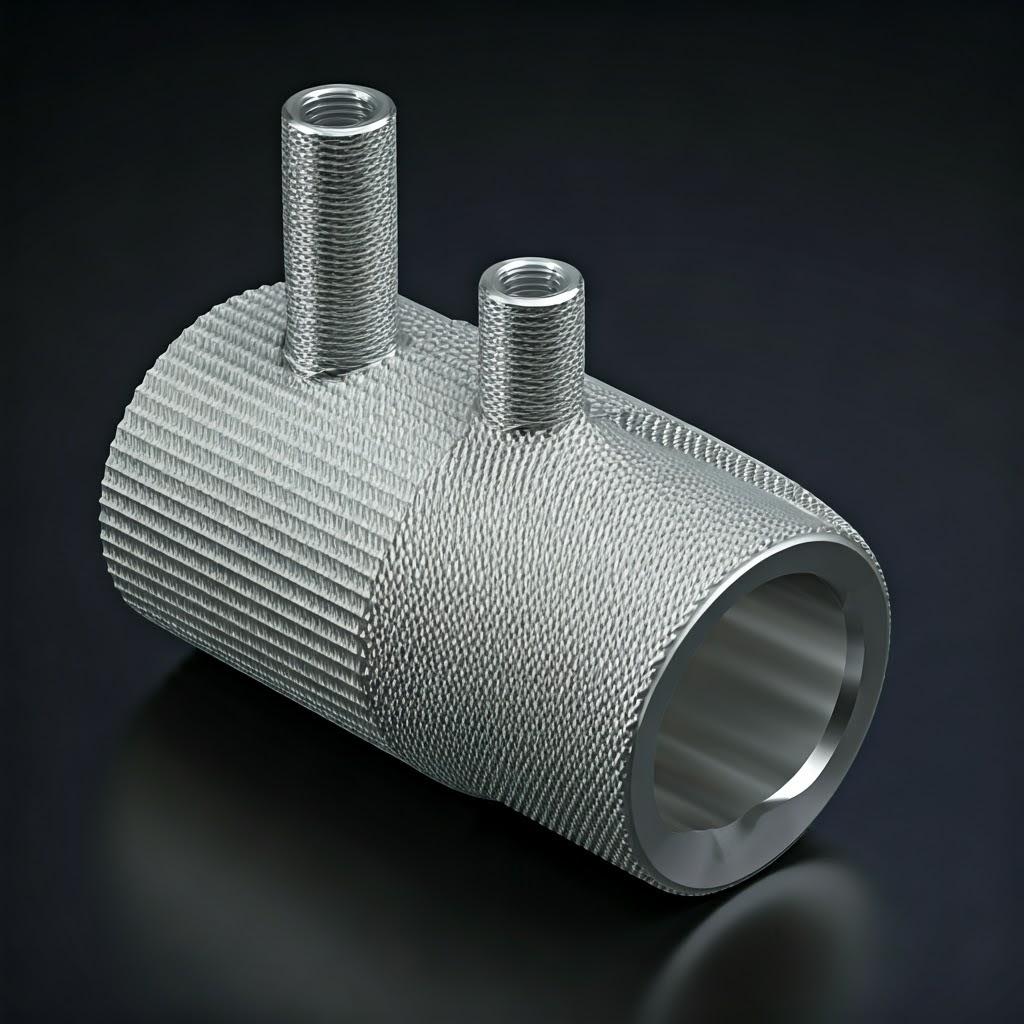
Frequently Asked Questions (FAQ) for AM Missile Guidance Housings
Here are answers to some common questions engineers and procurement specialists have about using metal additive manufacturing for missile guidance housings:
- Q1: Is metal 3D printing truly mature enough for flight-critical components like guidance housings?
- A: Yes, metal AM, particularly LPBF and EBM/SEBM, has matured significantly and is increasingly used for flight-critical applications in aerospace and defense, including engine components, structural brackets, and housings. Success hinges on using well-characterized materials (like Ti-6Al-4V ve 316L), employing robust process controls, performing necessary post-processing (especially heat treatment/HIP), conducting rigorous NDT and inspection, and adhering to stringent quality management systems like AS9100. Qualification requires thorough testing and validation, but the technology itself is capable of producing parts meeting demanding aerospace requirements when executed correctly by experienced providers.
- Q2: How do the mechanical properties of 3D printed Ti-6Al-4V compare to traditional wrought or cast titanium?
- A: When processed correctly (optimized parameters) and appropriately post-processed (stress relief, annealing, and often HIP), the mechanical properties of AM Ti-6Al-4V can meet or even exceed those of cast Ti-6Al-4V and approach the properties of wrought material, particularly in terms of static strength. Fatigue properties, especially after HIPing to remove porosity, can also be excellent. However, properties can exhibit some anisotropy (variation based on build direction). It’s crucial to design and test based on characterized properties specific to the AM process and post-processing route used, rather than assuming direct equivalence to wrought specifications without validation. Organizations like Met3dp invest heavily in understanding and optimizing the properties achievable with their SEBM printers and powders.
- Q3: What level of security and confidentiality can be expected when outsourcing sensitive defense components like guidance housings?
- A: Reputable metal additive manufacturing service providers serving the defense industry must have robust security measures in place. For US projects, ITAR registration and compliance are mandatory, involving strict controls over access to technical data and hardware by non-US persons. Secure data handling protocols (encrypted transfer, access controls, secure storage), physical facility security, employee vetting, and comprehensive Non-Disclosure Agreements (NDAs) are standard practice. Always verify a potential supplier’s security credentials and protocols before sharing sensitive project information.
- Q4: Can we just take our existing guidance housing design (made via CNC) and print it directly?
- A: While technically possible, it’s rarely the optimal approach. Directly printing a design optimized for subtractive manufacturing often results in a part that is heavier, requires more support material, takes longer to print, and doesn’t leverage the key benefits of AM (like complexity for free, topology optimization, part consolidation). To maximize the value of AM, designs should be reviewed and ideally re-imagined using Katmanlı Üretim Tasarımı (DfAM) principles to exploit its unique capabilities for weight reduction, performance enhancement, and integrated features.
- Q5: What are the typical batch sizes or production volumes where AM makes sense for guidance housings?
- A: Metal AM excels in several scenarios for guidance housings:
- Prototipleme: Producing functional prototypes quickly for fit, form, and limited functional testing.
- Low-to-Medium Volume Production: Typically ranging from single units up to hundreds or potentially low thousands. In this range, the high tooling costs of casting are avoided, and AM can be competitive with complex multi-axis CNC machining, especially if DfAM provides significant weight or performance benefits.
- Karmaşık Geometriler: When the design incorporates features (internal channels, lattices, extreme topology optimization) that are impossible or prohibitively expensive to make conventionally, AM becomes enabling technology regardless of volume.
- Legacy Parts / Obsolete Tooling: Re-manufacturing spare parts for older systems where original tooling no longer exists.
- Bridge Production: Producing initial batches while high-volume tooling is being prepared.
- A: Metal AM excels in several scenarios for guidance housings:
Conclusion: The Future Flight Path – AM Enabling Next-Generation Missile Systems
The journey through the additive manufacturing of missile guidance housings reveals a technology that has firmly moved beyond novelty into a vital enabler for next-generation defense capabilities. By leveraging the unique advantages of metal AM – unparalleled design freedom, the ability to create lightweight and highly complex structures using advanced materials like 316L ve Ti-6Al-4V, rapid iteration potential, and the opportunity for part consolidation – engineers can design guidance systems that are lighter, more robust, thermally efficient, and ultimately contribute to more capable and effective missile systems.
While challenges related to process control, post-processing, precision, and qualification remain, they are being actively addressed through advancements in technology, the development of industry standards, and the growing expertise of specialized service providers. The key lies in adopting a DfAM mindset and partnering with knowledgeable and capable suppliers who possess the requisite certifications (AS9100, ITAR), technological infrastructure, material expertise, and rigorous quality management systems.
Şirketler gibi Met3dp exemplify the integrated approach needed, offering not only industry-leading SEBM yazıcıları known for accuracy and reliability but also producing high-quality metal tozları optimized for additive processes through advanced atomization techniques. Their focus on providing comprehensive solutions, spanning equipment, materials, and application development, positions them as a valuable partner for aerospace and defense organizations looking to implement metal 3D printing and accelerate their digital manufacturing transformation.
As the defense landscape continues to demand higher performance, faster development, and more resilient supply chains, metal additive manufacturing will undoubtedly play an increasingly critical role. For engineers and procurement managers involved in developing and sourcing missile components, embracing AM is no longer just an option; it’s a strategic imperative for maintaining a technological edge.
Ready to explore how metal additive manufacturing can revolutionize your missile guidance system components? Contact Met3dp today to discuss your specific project requirements and learn how our cutting-edge systems, advanced metal powders, and deep application expertise can power your organization’s additive manufacturing goals and contribute to the future flight path of defense technology. Visit our website to learn more Hakkımızda and our capabilities.
Paylaş
MET3DP Technology Co, LTD, merkezi Qingdao, Çin'de bulunan lider bir katmanlı üretim çözümleri sağlayıcısıdır. Şirketimiz, endüstriyel uygulamalar için 3D baskı ekipmanları ve yüksek performanslı metal tozları konusunda uzmanlaşmıştır.
İşletmeniz için en iyi fiyatı ve özelleştirilmiş Çözümü almak için sorgulayın!
İlgili Makaleler
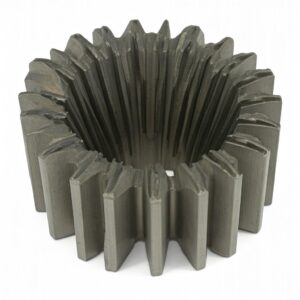
Yüksek Performanslı Nozul Kanat Segmentleri: Metal 3D Baskı ile Türbin Verimliliğinde Devrim
Daha Fazla Oku "Met3DP Hakkında
Son Güncelleme
Bizim Ürünümüz
BİZE ULAŞIN
Herhangi bir sorunuz var mı? Bize şimdi mesaj gönderin! Mesajınızı aldıktan sonra tüm ekibimizle talebinize hizmet edeceğiz.
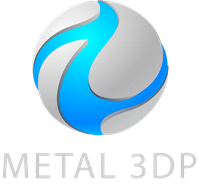
3D Baskı ve Katmanlı Üretim için Metal Tozları