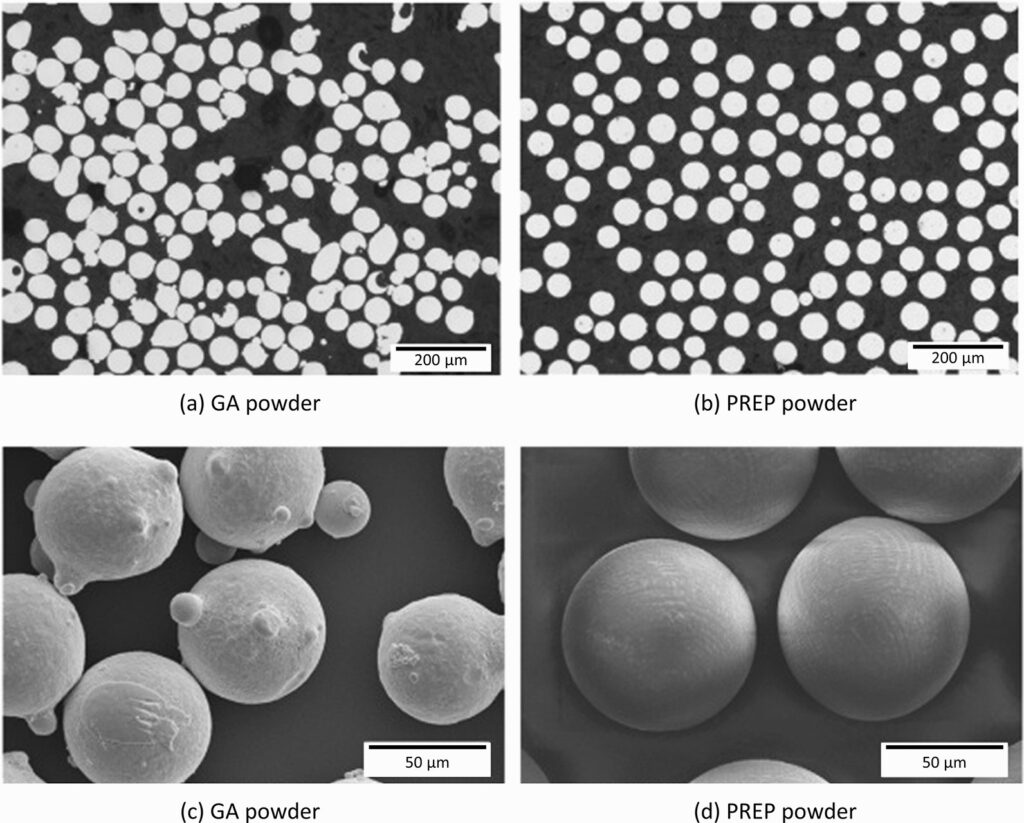
IN600 Tozu: Üstün Özelliklerini ve Sonsuz Kullanım Alanlarını Keşfedin
Düşük MOQ
Farklı ihtiyaçları karşılamak için düşük minimum sipariş miktarı sağlayın.
OEM VE ODM
Benzersiz müşteri ihtiyaçlarını karşılamak için özelleştirilmiş ürünler ve tasarım hizmetleri sağlayın.
Yeterli Stok
Hızlı sipariş işleme ve güvenilir ve verimli hizmet sağlayın.
Müşteri Memnuniyeti
Müşteri memnuniyetini merkeze alarak yüksek kaliteli ürünler sunmak.
bu makaleyi paylaş
İçindekiler
Yüksek performanslı ve dayanıklı malzemeler söz konusu olduğunda ekstrem ortamlar, IN600 tozu günümüzde mevcut en iyi seçeneklerden biridir. Bilinen dikkate değer direnç için OKSİDASYON, korozyonve yüksek sıcaklıklar, bu nikel bazlı alaşım, aşağıdaki gibi endüstriler için ideal bir çözümdür: ki̇myasal i̇şleme, havacılık ve uzay, nükleer güçve çok daha fazlası.
Bunun içinde kapsamlı rehber, bilmeniz gereken her şeyin derinliklerine dalacağız IN600 tozu-kendisinden Kompozisyon ve mekani̇k özelli̇kler onun için uygulamalar, fiyatlandırmave karşılaştırmalar diğer malzemelerle. İster bir mühendis, ister tedarik uzmanı olun, ister gelişmiş malzemelerle ilgilenen biri olun, bu kılavuz neden IN600 tozu çok yönlü ve yaygın olarak kullanılan bir alaşımdır.
IN600 Tozuna Genel Bakış
IN600 tozu olarak da bilinir Alaşım 600 veya Nikel 600Bu bir nikel-krom-demir alaşımı çok çeşitli etkilere karşı oldukça dirençlidir aşındırıcı medya ve oksitleyici ortamlarAşırı koşullar altında performans gösterme yeteneği, onu aşağıdaki uygulamalar için popüler bir seçim haline getirir: ısıl işlem, kimyasal elleçlemeve yüksek sıcaklık işlemleri.
Temel Özellikler
- Korozyon Direnci: Aşağıdakilere karşı mükemmel direnç Klorürler, oksitleyici asitlerve organik/inorganik bileşikler.
- Termal Kararlılık: Gücünü ve bütünlüğünü korur yüksek sıcaklıklar 1093°C'ye (2000°F) kadar.
- Çok Yönlü Uygulamalar: Şunlar için uygundur toz metalurjisi, 3D baskı, termal spreyve döküm.
- Mekanik Dayanıklılık: Aşağıdaki koşullarda bile iyi mekanik özellikler sunar: stres ve yüksek sıcaklıklı ortamlar.
Daha derinlemesine inceleyelim Kompozisyon ve Özellikler . IN600 tozu onu bu kadar eşsiz kılan şeyin ne olduğunu anlamak için.
IN600 Tozunun Bileşimi ve Temel Özellikleri
Bu ki̇myasal bi̇leşi̇m . IN600 tozu ona bu özelliği veren şey yüksek performans çeşitli zorlu ortamlarda. Öncelikle şunlardan oluşur nikel, önemli miktarda Krom ve Demirdiğer unsurların yanı sıra, buna katkıda bulunan güç ve oksidasyona karşı direnç.
Kimyasal Bileşim
Element | Yüzde (%) | Alaşımdaki Rolü |
---|---|---|
Nikel (Ni) | 72.0 dakika | Üstün performans sağlayan temel eleman korozyon direnci ve yüksek sıcaklık özellikleri. |
Krom (Cr) | 14.0-17.0 | Sağlar oksidasyon direnci ve performansı artırır aşındırıcı ortamlar. |
Demir (Fe) | 6.0-10.0 | Mekanik ekler güç ve alaşımın işlenebilirliğine katkıda bulunur stres yüksek sıcaklıklarda. |
Manganez (Mn) | 1.0 maks. | Geliştirir Kaynaklanabilirlik ve korumaya yardımcı olur yapısal bütünlük. |
Silisyum (Si) | 0,5 maks. | Alaşımın direncini artırır OKSİDASYON ve geliştirir dökülebilirlik. |
Karbon (C) | 0,15 maks. | İyileştirmeye yardımcı olur mekanik sertlik ve güçözellikle de yüksek sıcaklıklar. |
Sülfür (S) | 0,015 maks. | Önlemek için minimumda tutulur kırılganlık ve sürdürmek Süneklik. |
Bakır (Cu) | 0,5 maks. | Ek bilgi sağlar korozyon direnciözellikle de deniz ortamları. |
Mekanik ve Termal Özellikler
IN600 tozu bütünlüğünü korumak için tasarlanmıştır yüksek stres ve yüksek sıcaklık uygulamalar. Aşağıda mekanik ve termal özelli̇kler Bu da onu aşırı koşullar için en güvenilir malzemelerden biri haline getirir.
Mülkiyet | Değer/Açıklama |
---|---|
Yoğunluk | 8,42 gr/cm³ |
Erime Noktası | 1370-1425°C |
Çekme Dayanımı | Oda sıcaklığında 550 MPa |
Akma Dayanımı | Oda sıcaklığında 240 MPa |
Kopma Uzaması | 35% |
Sürünme Direnci | Mükemmel, kadar 870°C |
Termal İletkenlik | 14,9 W/m·K |
Oksidasyon Direnci | 'ye kadar oksidatif ortamlarda iyi performans gösterir. 1093°C |
Kaynaklanabilirlik | İyi, ancak şunları gerektirir ön ısıtma ve çatlamaları önlemek için kaynak sonrası ısıl işlemler |
IN600 Tozunun Avantajları: Onu Öne Çıkaran Nedir?
Merak ediyor olabilirsiniz - ne yapar IN600 tozu çok özel ve neden bir sonraki projeniz için bunu düşünmelisiniz? Pekala, birkaç tane var temel avantajlar Bu onu diğer alaşımlardan ayıran özelliktir.
1. Üstün Korozyon Direnci
Yüksekliği sayesinde nikel ve Krom İçerik, IN600 tozu geniş bir yelpazedeki etkilere karşı oldukça dirençlidir korozif ortamlardahil olmak üzere Klorürler, buharve oksitleyici asitler. Bu, onu aşağıdakiler için ideal kılar kimyasal işleme tesisleri, nükleer reaktörlerve deni̇z uygulamalari malzemelerin sürekli olarak zorlu koşullara maruz kaldığı yerler.
2. Yüksek Sıcaklık Performansı
IN600 tozu koruyabilir mekanik bütünlük ve oksidasyon direnci kadar olan sıcaklıklarda 1093°C (2000°F). Bu, onu şu tür uygulamalar için paha biçilmez hale getirir: gaz türbi̇nleri̇, Fırınlarve azaltılmış yakıt tüketimi, malzemelerin aşırı ısıya uzun süre maruz kalmaya dayanması gerektiği durumlarda.
3. Çok Yönlü Üretim Seçenekleri
Kullanıyor olsanız da geleneksel döküm, toz metalurjisiveya eklemeli üretim gibi teknikler 3D baskı, IN600 tozu son derece uyumludur. küresel morfoloji ve tutarlı parçacık boyutu dağıtım için idealdir termal sprey süreçler ve doğrudan metal lazer sinterleme (DMLS).
4. Mükemmel Mekanik Güç
Yüksek sıcaklık ortamlarında bile, IN600 tozu korur yapısal bütünlükBu onu, başvurulacak bir malzeme haline getirir yüksek stresli uygulamalar nerede sürünme direnci ve uzun süreli dayanıklılık kritiktir.
IN600 Tozunun Uygulamaları: Nerelerde Kullanılır?
Olağanüstü özellikleri göz önüne alındığında, IN600 tozu en çok kullanılanlardan bazılarında kullanılır. zorlu sektörler. Daha yakından bir göz atalım uygulamalar bu alaşımın gerçekten parladığı yer.
Sektöre Göre Yaygın Kullanımlar
Endüstri | Uygulama |
---|---|
Havacılık ve Uzay | Gaz türbini kanatları, art yakıcılarve egzoz si̇stemleri̇ yüksek sıcaklık oksidasyon direnci gerektiren. |
Kimyasal İşleme | Boru tesisatı, gemilerve azaltılmış yakıt tüketimi taşımada kullanılır aşındırıcı kimyasallar gibi sülfürik asit ve Klorürler. |
Nükleer Enerji | Buhar jeneratörleri, kontrol çubuklarıve azaltılmış yakıt tüketimi Hem korozyonun hem de ısı direncinin kritik öneme sahip olduğu nükleer reaktörlerde. |
Isıl İşlem | Fırın bileşenleri, susturucularve imbikler yüksek sıcaklıktaki ortamlarda kullanılır. |
Denizcilik Endüstrisi | Isı eşanjörleri, valflerve boru tesisatı sistemlere maruz kalan deniz suyu ve deniz atmosferleri. |
3D Baskı | Katmanlı üretim yüksek performanslı parçalar için karmaşık geometrilerin havacılık ve uzay ve enerji̇ sektörleri̇. |
IN600 Toz için Özellikler, Boyutlar ve Standartlar
Satın almaya karar vermeden önce IN600 tozu, çeşitli anlamak önemlidir spesifikasyonlar, boyutlarıve standartlar Bu malzemeye uygulananlar. Bu faktörler, onun performans ve UYGUNLUK özel uygulamanız için.
Teknik Özellikler
Şartname | Detaylar |
---|---|
Parçacık Boyutu | Tipik olarak şu aralıklardadır 15 ila 45 mikron için toz metalurjisi ve eklemeli üretim. |
Toz Morfolojisi | Genel olarak KÜRESEL üstün akışkanlık için 3D baskı ve termal sprey uygulamalar. |
ASTM Standartları | ASTM B168 nikel-krom-demir alaşımlı sac ve levhalar için. |
ISO Standartları | ISO 15156 korozyona dayanıklı alaşımlar için kullanılır ekşi gaz ortamları. |
UNS Numarası | UNS N06600 |
AMS Standartları | AMS5540, nikel-krom-demir alaşımları için kullanılır havacılık ve uzay ve yüksek sıcaklık uygulamaları. |
Bu standartlar aşağıdakileri sağlar IN600 tozu satın aldığınız ürün için gerekli eşikleri karşılıyor performans ve güvenilirlik kendi sektörünüzde.
IN600 Tozunun Tedarikçileri ve Fiyatlandırması
Fiyatlandırma IN600 tozu çeşitli faktörlere bağlı olarak değişebilir Tedarikçi, parçacık boyutuve sipariş hacmiAşağıda bu yüksek performanslı alaşım için bilinen bazı tedarikçiler ve yaklaşık fiyat aralıkları yer almaktadır.
Tedarikçiler ve Fiyatlandırma
Tedarikçi | Fiyat Aralığı (kg başına) | Notlar |
---|---|---|
Höganäs AB | $600 – $850 | Metal tozları konusunda uzmanlaşmıştır eklemeli üretim ve termal sprey uygulamalar. |
Marangoz Teknolojisi | $620 – $880 | Özel parçacık boyutları ve formülasyonları sunar toz metalurjisi ve 3D baskı. |
Oerlikon Metco | $610 – $870 | IN600 tozu sağlar termal sprey kaplamalar ve eklemeli üretim. |
Sandvik | $630 – $890 | Aşağıdaki endüstriler için gelişmiş malzemeler sağlar: havacılık ve uzay ve petrol ve gaz. |
Kennametal | $620 – $880 | Yüksek performanslı nikel alaşımlarına odaklanmaktadır zorlu uygulamalar. |
Fiyatı IN600 tozu tipik olarak Kilogram başına $600 ila $890bağlı olarak Tedarikçi ve belirli parçacık boyutu Gereksinimler.
IN600 Tozunun Artılarını ve Eksilerini Karşılaştırma
Bir karar vermeden önce, aşağıdakileri tartmak önemlidir: avantajlar ve sınırlamalar . IN600 tozuÇok sayıda fayda sağlamasına rağmen, bazı avantajları da vardır: Dezavantajlar uygulamanıza bağlı olarak dikkate alınması gerekenler.
Avantajlar
Avantaj | Açıklama |
---|---|
Korozyon Direnci: Geniş bir yelpazede üstün performans korozif ortamlar. | Kullanım için ideal ki̇myasal i̇şleme ve deni̇z uygulamalari. |
Yüksek Sıcaklık Kararlılığı: Yüksek sıcaklıklarda mekanik özelliklerini korur. | İçin mükemmel gaz türbi̇nleri̇, azaltılmış yakıt tüketimive fırın bileşenleri. |
Çok Yönlü Üretim: Şunlar için uygundur 3D baskı, termal spreyve toz metalurjisi. | Şunlar için izin verir karmaşık geometriler ve yüksek performansli parçalar. |
Oksidasyon Direnci: Oksidatif ortamlarda iyi performans gösterir 1093°C. | Kullanışlı yüksek sıcaklık uygulamaları gibi Fırınlar ve gaz türbi̇nleri̇. |
Mekanik Dayanım: Mekanik özelliklerini korur stres ve yüksek ısı. | Sağlar uzun süreli dayanıklılık zorlu uygulamalarda. |
Sınırlamalar
Sınırlama | Açıklama |
---|---|
Yüksek Maliyet: Diğer birçok malzemeden daha pahalıdır. | Şunlar için uygun olmayabilir bütçeye duyarlı uygulamalar. |
Sınırlı Kullanılabilirlik: Her zaman büyük miktarlarda hazır bulunmaz. | Şunlara yol açabilir daha uzun teslim süreleriözellikle özel formülasyonlar veya büyük siparişler için. |
Makine için Zorlu: Hassas işleme için özel aletler gerektirir. | Artırabilir işleme süresi ve maliyetlerözellikle karmaşık parçalar için. |
Çok Yüksek Sıcaklıklarda Oksidasyon: Oksidasyon yukarıda bir sorun haline gelebilir 1093°C. | Gerekebilir kaplamalar veya özel muameleler aşırı üst sıcaklık sınırları için. |
SSS
İşte en sık sorulan sorulardan bazıları: IN600 tozuBu materyali daha iyi anlamanıza yardımcı olacak kısa ama bilgilendirici yanıtlarla birlikte.
Soru | Cevap |
---|---|
IN600 tozu ne için kullanılır? | Genellikle şu alanlarda kullanılır havacılık ve uzay, ki̇myasal i̇şlemeve nükleer güç yüksek uygulamalar sıcaklık ve korozyon direnci gerekli. |
IN600 tozunun fiyatı ne kadar? | Fiyatı şu kadardır: Kilogram başına $600 ila $890bağlı olarak Tedarikçi ve parçacık boyutu. |
IN600 tozu 3D baskıda kullanılabilir mi? | Evet, yaygın olarak eklemeli üretim gibi süreçler doğrudan metal lazer sinterleme (DMLS) ve elektron ışını eritme (EBM). |
IN600 tozu hangi sektörlerde kullanılır? | Gibi sektörler havacılık ve uzay, ki̇myasal i̇şleme, nükleer güçve deni̇z uygulamalari genellikle şunun için kullanılır yüksek performans uygulamalar. |
IN600 tozunu korozyona dayanıklı kılan nedir? | Yüksek nikel ve Krom IN600'deki içerik mükemmel direnç sağlar oksitleyici asitler, Klorürlerve yüksek sıcaklıklı ortamlar. |
IN600 tozunun başlıca avantajları nelerdir? | Bu teklifler yüksek sıcaklık kararlılığı, korozyon direncive mekanik dayanımiçin ideal hale getirir. ekstrem ortamlar. |
IN600 tozunun kullanımının sınırlamaları nelerdir? | Ana sınırlamalar şunlardır yüksek maliyet ve işleme zorluğuartırabilen ÜRETİM SÜRESİ ve maliyetler. |
IN600 tozu yüksek sıcaklık ortamlarına uygun mudur? | Evet, IN600 tozu, 1093°Ciçin ideal hale getirir. gaz türbi̇nleri̇, Fırınlarve azaltılmış yakıt tüketimi. |
IN600 tozu aşındırıcı ortamlara dayanabilir mi? | Kesinlikle. Yüksek kalitesi sayesinde nikel ve Krom İçerik, IN600'de mükemmel korozyon direnci sağlar kimyasal ve deniz atmosferleri. |
Son Düşünceler: IN600 Tozu Projeniz İçin Uygun mu?
Aşağıdakileri sunan bir malzeme arıyorsanız olağanüstü korozyon direnci, yüksek sıcaklık performansıve mekanik dayanım, IN600 tozu piyasadaki en iyi seçeneklerden biridir. Üretim süreçlerindeki çok yönlülüğü gibi 3D baskı, termal spreyve geleneksel döküm çeşitli endüstrilere uyarlanabilir hale getirir, havacılık ve uzay için ki̇myasal i̇şleme.
Her ne kadar IN600 tozu diğer malzemelere kıyasla daha yüksek bir fiyata gelebilir, uzun süreli dayanıklılık ve güvenilirlik genellikle ilk yatırımdan daha ağır basar. İster yüksek performanslı bileşenler tasarlıyor olun, ister gaz türbi̇nleri̇, nükleer reaktörlerveya aşındırıcı kimyasal ortamlar, IN600 tozu En zorlu projelerinizin taleplerini karşılayabilir.
Sonuç olarak, projeniz dayanıklı malzemeler gerektiriyorsa ekstrem koşullar sunarken uzun ömürlü performans, IN600 tozu her alanda beklentileri karşılayan en iyi adaylardan biri.
Belki ürünlerimiz hakkında daha fazla bilgi edinmek istersiniz
Son Fiyat Alın
Met3DP Hakkında
Ürün Kategorisi
SICAK SATIŞ
BİZE ULAŞIN
Herhangi bir sorunuz var mı? Bize şimdi mesaj gönderin! Mesajınızı aldıktan sonra tüm ekibimizle talebinize hizmet edeceğiz.
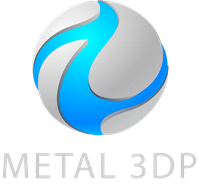
3D Baskı ve Katmanlı Üretim için Metal Tozları