3D Printing Injection Mold Cores with Maraging Steel
İçindekiler
Introduction – The Power of Metal 3D Printing for Advanced Injection Mold Cores
In today’s rapidly evolving manufacturing landscape, the demand for complex geometries, reduced lead times, and enhanced performance is constantly increasing. Traditional manufacturing methods for injection mold cores often face limitations in terms of design freedom, production speed, and material efficiency. Metal 3D baskı, also known as metal additive manufacturing, has emerged as a transformative technology, offering unprecedented capabilities for producing intricate and high-performance injection mold cores. This innovative approach empowers engineers and procurement managers across diverse industries such as aerospace, automotive, medical, and industrial manufacturing to reimagine tooling design and achieve superior results. At Metal3DP Teknoloji A.Ş., LTD, we are at the forefront of this revolution, providing industry-leading metal 3D printing equipment and high-performance metal powders to unlock the full potential of additive manufacturing for your tooling needs. Our commitment to accuracy, reliability, and innovation ensures that you can produce mission-critical parts with exceptional quality and efficiency.
What are 3D Printed Injection Mold Cores Used For? – Applications Across Industries
3D printed injection mold cores serve as critical components in the injection molding process, shaping the internal features and surface details of plastic or other materials. Their applications span a wide array of industries, driven by the unique advantages offered by metal additive manufacturing:
- Havacılık ve uzay: Manufacturing of complex internal cooling channels for molds used in producing lightweight and high-strength structural components, interior parts, and electronic housings. The ability to create intricate geometries allows for optimized thermal management, crucial for the performance and lifespan of aerospace parts.
- Otomotiv: Production of mold cores for intricate automotive components such as interior trims, dashboard elements, lighting housings, and under-the-hood parts. Metal 3D printing enables rapid prototyping and the creation of complex cooling systems within the mold, leading to faster cycle times and improved part quality for automotive suppliers.
- Tıbbi: Fabrication of mold cores for medical devices, including surgical instruments, diagnostic tools, and implantable components. The precision and material compatibility offered by metal 3D printing are essential for meeting the stringent requirements of the medical industry.
- Endüstriyel Üretim: Creation of mold cores for a diverse range of industrial products, from consumer electronics and household appliances to industrial machinery parts and packaging solutions. The flexibility of additive manufacturing allows for customized mold designs and efficient production of both small and large batches.
By leveraging the capabilities of metal 3D printing, businesses can achieve greater design flexibility, faster turnaround times, and improved part performance across these critical sectors. Explore our range of metal 3D printing services to discover how we can support your specific industry applications.
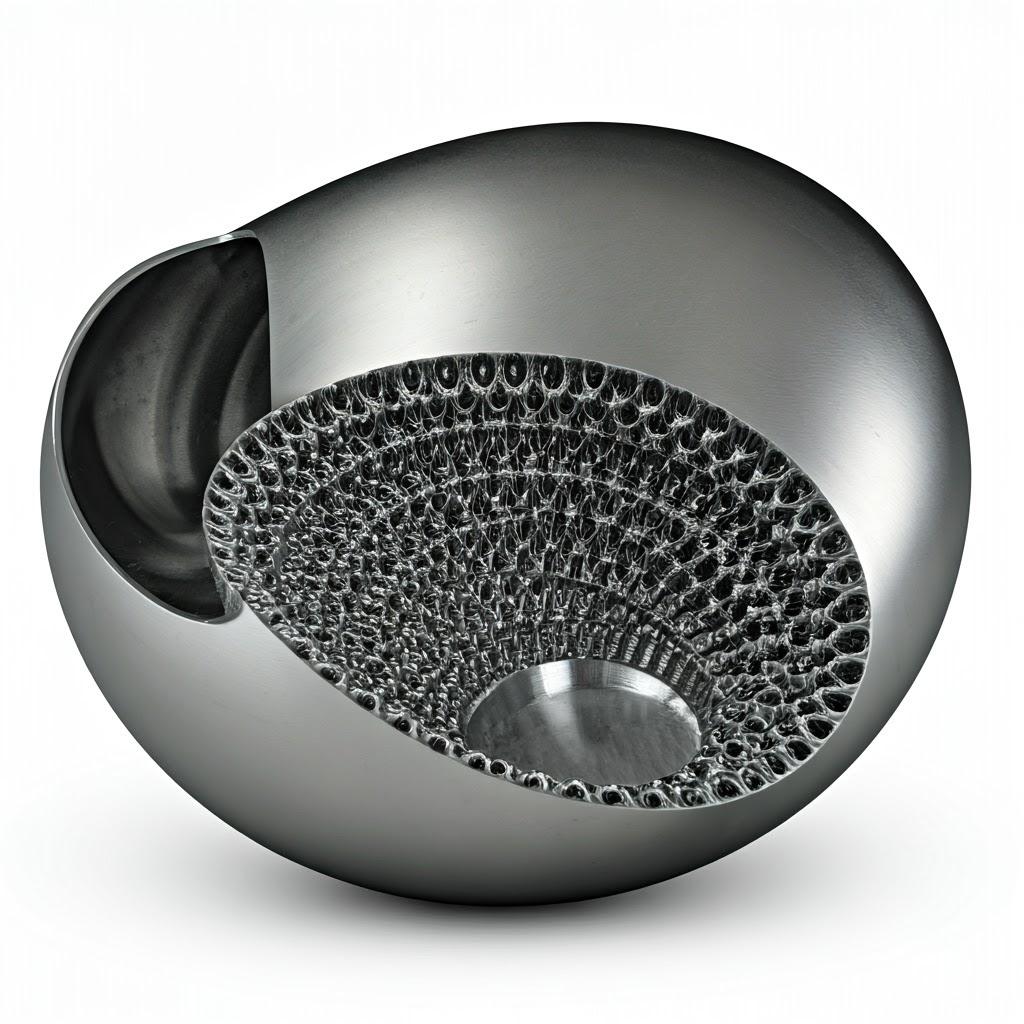
Why Choose Metal 3D Printing for Injection Mold Core Manufacturing? – Advantages for Tooling Suppliers
Opting for metal 3D printing for the manufacturing of injection mold cores offers a multitude of advantages over traditional subtractive manufacturing methods, making it an increasingly attractive solution for tooling suppliers and end-users alike:
- Enhanced Design Freedom: Additive manufacturing allows for the creation of complex internal geometries, such as conformal cooling channels that closely follow the contours of the mold cavity. This leads to more efficient heat dissipation, reduced cycle times, and improved part quality compared to conventionally drilled cooling channels.
- Rapid Prototyping and Reduced Lead Times: Metal 3D printing significantly accelerates the mold core production process. Prototypes can be created in a fraction of the time compared to traditional methods, enabling faster design iterations and quicker time-to-market for new products. This agility is crucial for toptan alıcılar looking for rapid solutions.
- Malzeme Verimliliği: Additive manufacturing builds parts layer by layer, minimizing material waste compared to subtractive processes where significant material is removed. This can lead to cost savings, especially when working with expensive materials.
- Customization and Complexity: Metal 3D printing excels at producing highly customized mold cores with intricate features that would be difficult or impossible to achieve with conventional machining. This opens up new possibilities for part design and functionality.
- Improved Part Quality and Consistency: The precise nature of metal 3D printing can result in mold cores with superior dimensional accuracy and surface finish, leading to higher quality molded parts with greater consistency.
- İsteğe Bağlı Üretim: Metal 3D printing enables the production of mold cores on demand, reducing the need for large inventories and allowing for greater flexibility in production planning.
As a leading provider of additive manufacturing solutions, Metal3DP is dedicated to helping tooling suppliers leverage these advantages to enhance their capabilities and deliver superior products to their customers.
Recommended Materials: 1.2709 and H13 for High-Performance Mold Cores – Properties and Benefits for Wholesale Buyers
Selecting the appropriate material is paramount for the performance and longevity of 3D printed injection mold cores. Metal3DP recommends two high-performance steel powders that are particularly well-suited for this application: 1.2709 and H13.
1.2709 (Maraging Steel):
- Kompozisyon: Typically composed of iron, nickel, cobalt, molybdenum, and titanium.
- Anahtar Özellikler:
- High Hardness and Strength: Achieves exceptional hardness and tensile strength after heat treatment, providing excellent wear resistance and durability for demanding injection molding applications.
- Excellent Toughness: Offers good resistance to cracking and chipping, crucial for molds subjected to repeated injection cycles.
- Good Machinability in Softened State: Can be easily machined before final heat treatment, allowing for precise finishing and feature integration.
- Dimensional Stability During Heat Treatment: Exhibits minimal distortion during the hardening process, ensuring high accuracy of the final mold core.
- Benefits for Wholesale Buyers: Mold cores made from 1.2709 offer extended tool life, reduced maintenance costs, and the ability to produce high-quality parts with tight tolerances.
H13 Tool Steel:
- Kompozisyon: A chromium-molybdenum hot work tool steel.
- Anahtar Özellikler:
- High Hot Hardness and Temper Resistance: Maintains its hardness and strength at elevated temperatures, making it suitable for molding high-temperature materials.
- Good Toughness and Ductility: Offers a good balance of strength and resistance to impact and wear.
- Excellent Thermal Fatigue Resistance: Withstands repeated heating and cooling cycles without significant degradation, crucial for long production runs.
- İyi İşlenebilirlik: Can be readily machined and polished to achieve the desired surface finish.
- Benefits for Wholesale Buyers: H13 mold cores provide a cost-effective solution for a wide range of injection molding applications, offering a good combination of performance and durability.
The table below summarizes the key properties of these recommended powders:
Mülkiyet | 1.2709 (Maraging Steel) | H13 Takım Çeliği |
---|---|---|
Hardness (after heat treat) | Up to 54 HRC | 42-52 HRC |
Çekme Dayanımı | Up to 2000 MPa | Up to 1700 MPa |
Sertlik | Mükemmel | İyi |
Sıcak Sertlik | İyi | Yüksek |
Termal Yorulma Direnci | Adil | Mükemmel |
Machinability (softened) | İyi | İyi |
Boyutsal Kararlılık | Mükemmel | İyi |
Tipik Uygulamalar | High-performance molds, complex geometries | General-purpose molds, high-temperature molding |
Sayfalara Aktar
Our advanced powder making system ensures the production of high-quality metal powders with consistent properties, enabling our customers to 3D print dense, high-quality metal parts with superior mechanical properties. Contact us to discuss your specific material requirements and find the optimal solution for your injection mold core applications. Sources and related content
Design Considerations for Additively Manufactured Mold Cores – Optimizing Geometry and Cooling Channels
Designing for metal 3D printing requires a different mindset compared to traditional manufacturing. To fully leverage the capabilities of additive manufacturing for injection mold cores, several key design considerations should be taken into account:
- Konformal Soğutma Kanalları: One of the most significant advantages of 3D printing is the ability to create conformal cooling channels that closely follow the contours of the mold cavity. This optimized cooling significantly improves heat transfer, leading to:
- Reduced Cycle Times: Faster cooling allows for quicker solidification of the molded part, shortening the overall production cycle.
- Geliştirilmiş Parça Kalitesi: Uniform cooling minimizes warpage, sink marks, and other defects, resulting in higher quality molded components.
- Extended Mold Life: Efficient thermal management reduces thermal stress on the mold core, prolonging its lifespan.
- Internal Features and Complexity: Metal 3D printing enables the creation of intricate internal features, such as complex cooling circuits, ejector pin guides, and integrated sensors, which would be difficult or impossible to produce with conventional methods. This allows for functional integration and design optimization.
- Wall Thickness and Support Structures: Careful consideration of wall thickness is crucial to balance part strength and material usage. Support structures are often necessary to support overhanging features during the printing process. Design for minimal support requirements can reduce post-processing time and material waste. Our team at Metal3DP can provide expert guidance on optimizing your designs for additive manufacturing.
- Yüzey İşlemi: The as-printed surface finish of metal 3D printed parts can vary depending on the printing process and parameters. Incorporating design features that minimize the need for extensive post-processing, such as strategically oriented surfaces, can improve efficiency.
- Material Selection and Orientation: The chosen material and the orientation of the part during printing can significantly impact its mechanical properties and dimensional accuracy. Considering the stress loads and critical dimensions of the mold core early in the design process is essential.
By embracing these design principles, engineers can unlock the full potential of metal 3D printing to create high-performance and efficient injection mold cores.
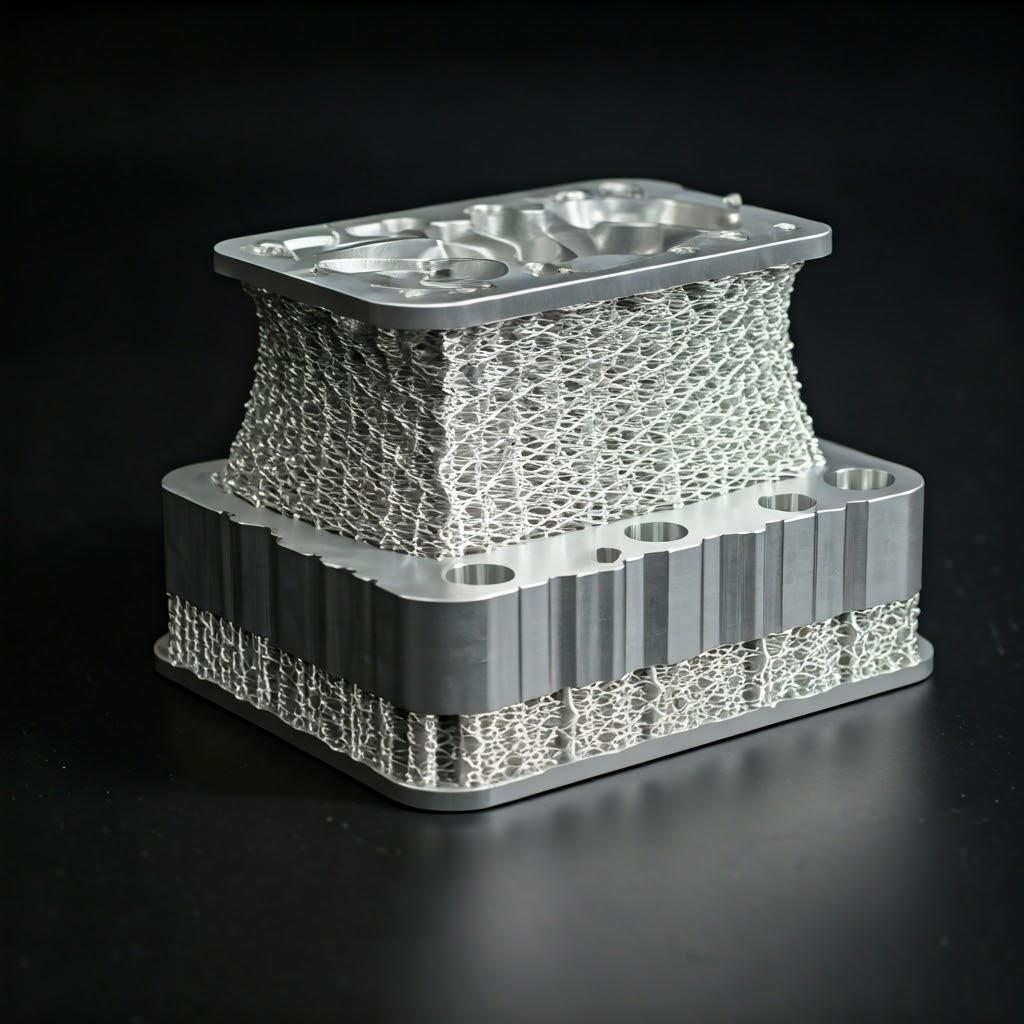
Achieving Precision: Tolerance, Surface Finish, and Dimensional Accuracy in 3D Printed Mold Cores
Dimensional accuracy, tolerance, and surface finish are critical factors for injection mold cores, as they directly impact the quality and functionality of the final molded parts. Metal 3D printing technologies offered by Metal3DP are capable of achieving impressive levels of precision:
- Boyutsal Doğruluk: Depending on the specific printing technology and material, metal 3D printing can achieve dimensional accuracies in the range of ±0.1 mm or even finer for critical features. This accuracy ensures proper fit and function within the mold assembly.
- Tolerance: Tolerances achievable with metal 3D printing typically range from ±0.05 mm to ±0.2 mm. Tighter tolerances can often be achieved through post-processing steps such as CNC machining. Understanding the required tolerances for your specific application is crucial for selecting the appropriate printing parameters and post-processing methods.
- Yüzey İşlemi: The as-printed surface finish can vary depending on the metal powder particle size and the layer thickness used during the printing process. Typical surface roughness values (Ra) can range from 5 µm to 20 µm. For applications requiring smoother surfaces, post-processing techniques like polishing or surface grinding can be employed.
The table below provides a general overview of the achievable precision with metal 3D printing for mold cores:
Parametre | Achievable Range | Notlar |
---|---|---|
Boyutsal Doğruluk | ±0.1 mm or better | Dependent on technology, material, and part size. |
Hoşgörü | ±0.05 mm to ±0.2 mm | Can be improved with post-processing. |
Yüzey Pürüzlülüğü (Ra) | 5 µm to 20 µm | Can be improved with polishing, grinding, or other surface treatments. |
Sayfalara Aktar
At Metal3DP, our industry-leading printers deliver high accuracy and reliability, ensuring that your 3D printed mold cores meet the stringent requirements of your applications.
Streamlining Production: Post-Processing Requirements for Metal 3D Printed Mold Cores
While metal 3D printing offers significant advantages in creating complex geometries, post-processing is often required to achieve the final desired properties and finish of injection mold cores. Common post-processing steps include:
- Destek Kaldırma: Metal 3D printed parts often require support structures to prevent collapse or distortion during the printing process. These supports need to be carefully removed after printing, typically through machining, grinding, or wire EDM.
- Stress Relief Heat Treatment: To alleviate internal stresses that may have built up during the printing process, a stress relief heat treatment is often performed. This improves the dimensional stability and mechanical properties of the mold core.
- Sıcak İzostatik Presleme (HIP): HIP is a process that applies high pressure and temperature to the printed part, reducing porosity and further enhancing its density and mechanical strength.
- CNC İşleme: For achieving very tight tolerances or specific surface finishes on critical features, CNC machining may be employed as a secondary operation. This can be used to refine dimensions, add threads, or create high-precision mating surfaces.
- Yüzey İşlemi: Depending on the application requirements, various surface finishing techniques can be used, such as polishing, grinding, or coating, to achieve the desired surface roughness and wear resistance.
- Kaplama: Applying specialized coatings can enhance the surface hardness, corrosion resistance, or wear properties of the mold core, extending its lifespan and improving the quality of the molded parts.
The specific post-processing requirements will depend on the material, the complexity of the mold core, and the intended application. Metal3DP offers comprehensive solutions, including guidance on optimal post-processing workflows to ensure the highest quality and performance of your 3D printed injection mold cores.
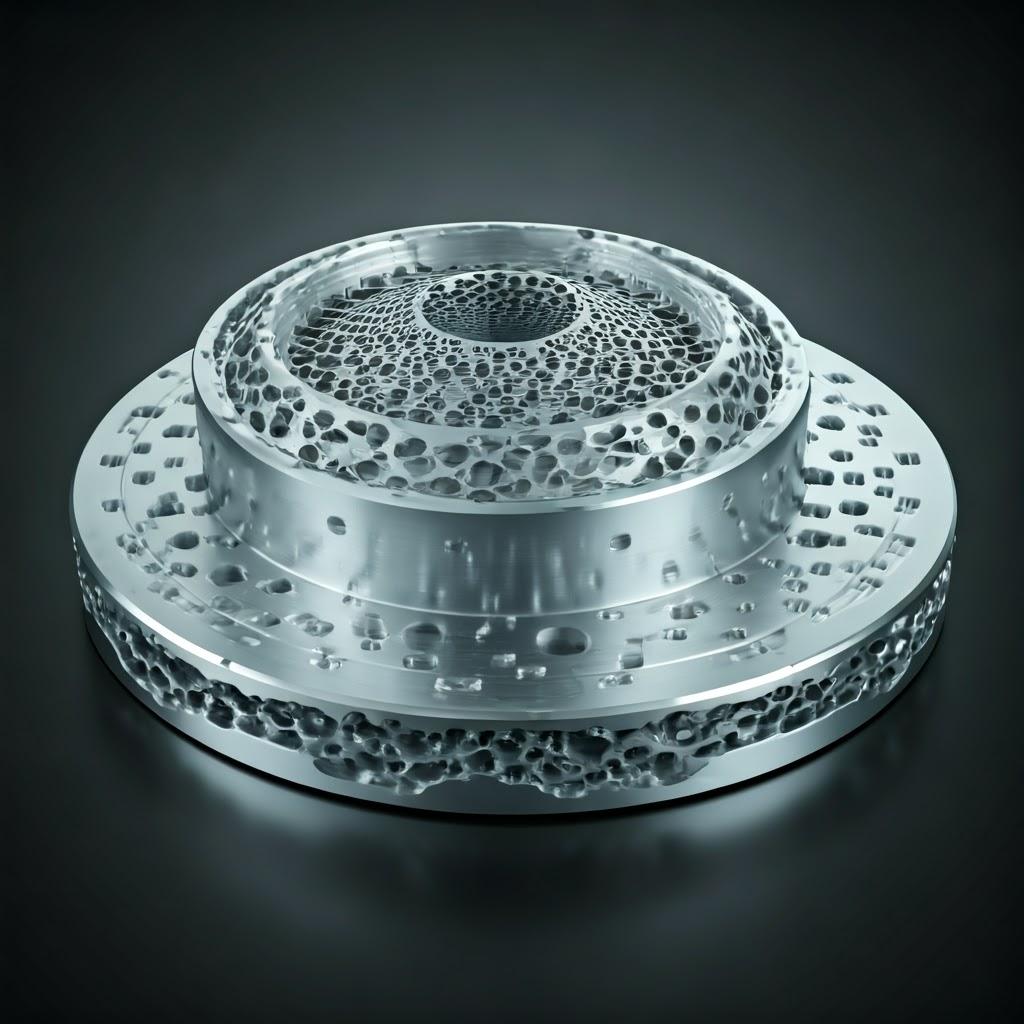
Overcoming Challenges in Metal 3D Printing of Mold Cores – Solutions for Warping and Porosity
While metal 3D printing offers numerous benefits, certain challenges can arise during the process. Understanding these potential issues and implementing appropriate strategies can mitigate them:
- Çarpıtma ve Bozulma: Thermal stresses during the printing process can sometimes lead to warping or distortion of the mold core. Strategies to minimize this include:
- Optimized Part Orientation: Orienting the part strategically on the build platform can reduce the build-up of internal stresses.
- Support Structure Optimization: Properly designed support structures can help to anchor the part and prevent deformation.
- Controlled Cooling Rates: Managing the cooling rate during the printing process can minimize thermal gradients and reduce stress.
- Stress Relief Heat Treatment: As mentioned earlier, post-printing heat treatment can effectively relieve internal stresses.
- Gözeneklilik: The presence of pores or voids within the printed part can compromise its mechanical strength and fatigue resistance. Measures to minimize porosity include:
- Optimized Printing Parameters: Adjusting laser power, scan speed, and layer thickness can influence the density of the printed part.
- Yüksek Kaliteli Metal Tozları: Using high-quality, spherical metal powders with good flowability, such as those offered by Metal3DP, is crucial for achieving dense parts.
- Inert Build Atmosphere: Printing in an inert atmosphere minimizes oxidation and contamination, which can contribute to porosity.
- Sıcak İzostatik Presleme (HIP): HIP is an effective post-processing method for closing internal pores and increasing the density of the printed part.
- Support Removal Challenges: Removing support structures from complex geometries can sometimes be challenging and may leave surface marks. Designing for minimal support and utilizing appropriate support removal techniques can address this.
By understanding these potential challenges and implementing appropriate design and processing strategies, manufacturers can effectively leverage metal 3D printing to produce high-quality injection mold cores. Contact our experts at Metal3DP for guidance on overcoming these challenges and optimizing your metal additive manufacturing processes.
How to Choose the Right Metal 3D Printing Service Provider for Mold Core Production – Key Criteria for Procurement Managers
Selecting the right metal 3D printing service provider is crucial for ensuring the success of your injection mold core projects. Procurement managers should consider several key criteria when evaluating potential suppliers:
- Material Capabilities: Ensure the service provider offers the specific metal powders required for your application, such as 1.2709 and H13. Verify the quality and consistency of their powders. Metal3DP boasts a wide range of high-quality metal powders optimized for various additive manufacturing processes.
- Printing Technology and Equipment: Understand the types of metal 3D printing technologies the provider utilizes (e.g., Laser Powder Bed Fusion (LPBF), Electron Beam Melting (EBM)). Ensure their equipment is well-maintained and capable of achieving the required accuracy and build volume for your mold cores.
- Expertise and Experience: Evaluate the provider’s experience in manufacturing injection mold cores or similar tooling applications. Look for case studies or testimonials that demonstrate their capabilities and understanding of the specific requirements of the tooling industry. Metal3DP has decades of collective expertise in metal additive manufacturing.
- Design and Engineering Support: A good service provider should offer design optimization services for additive manufacturing, including guidance on conformal cooling channels, support structure design, and material selection.
- Post-Processing Capabilities: Inquire about the in-house or partnered post-processing services offered, such as support removal, heat treatment, CNC machining, and surface finishing. Ensure they can meet your required specifications.
- Quality Control and Certifications: Verify the provider’s quality control processes and any relevant certifications (e.g., ISO 9001, AS9100 for aerospace). This ensures that the manufactured mold cores meet stringent quality standards.
- Lead Times and Pricing: Obtain clear information on lead times for manufacturing and any associated costs. Compare pricing structures and ensure they align with your budget and project timelines.
- Communication and Customer Support: Assess the provider’s responsiveness, communication clarity, and overall customer support. A strong partner will work collaboratively with you throughout the project.
By carefully evaluating these criteria, procurement managers can select a metal 3D printing service provider that can reliably deliver high-quality injection mold cores that meet their specific needs.
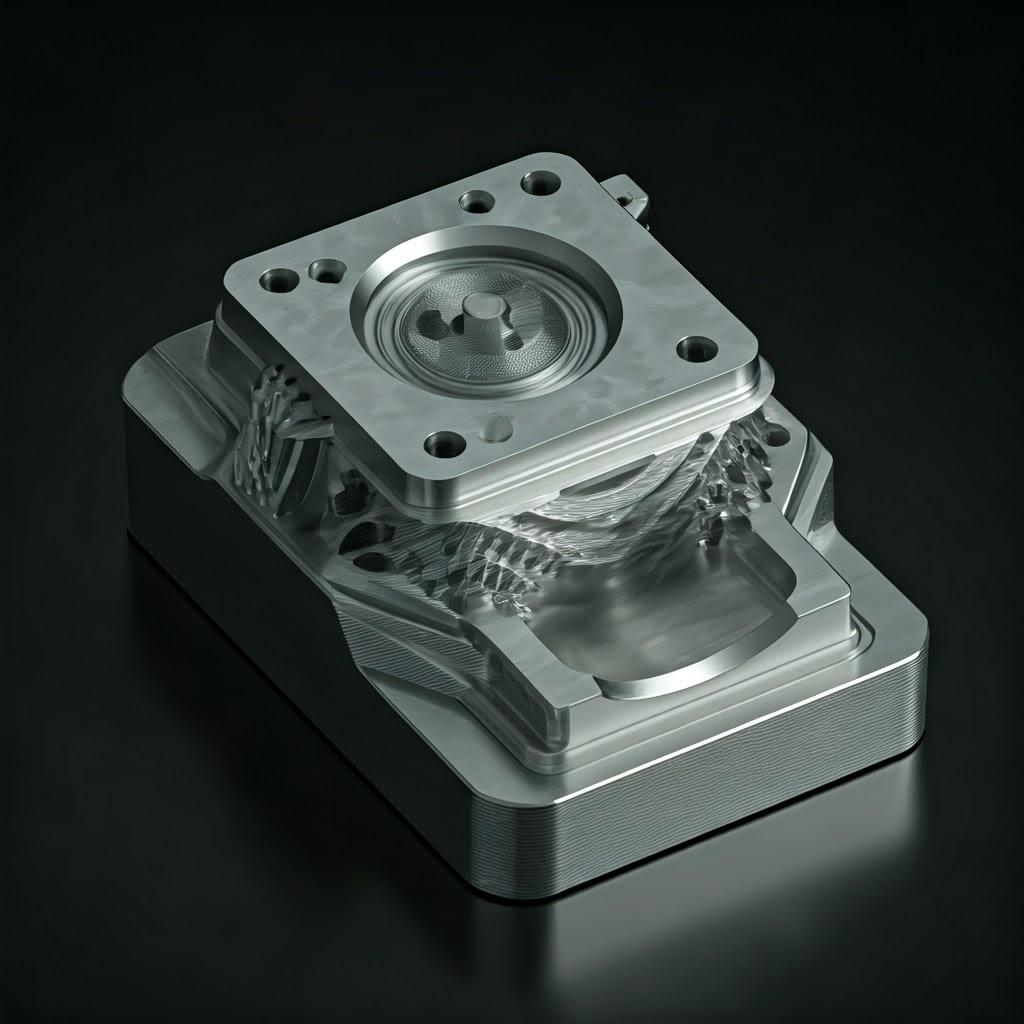
Understanding Cost Factors and Lead Times for 3D Printed Injection Mold Cores – A Guide for Budgeting and Planning
The cost and lead time for producing injection mold cores using metal 3D printing are influenced by several factors. Understanding these can help with budgeting and project planning:
Maliyet Faktörleri:
- Malzeme Maliyetleri: The type and quantity of metal powder used are significant cost drivers. Specialized alloys like 1.2709 can be more expensive than standard tool steels like H13.
- Yapım süresi: The duration of the printing process directly impacts the cost. Longer build times, often associated with larger or more complex parts, will increase expenses.
- İşlem Sonrası Maliyetler: The extent of post-processing required (e.g., support removal, heat treatment, machining, polishing) will add to the overall cost.
- Machine Usage and Overhead: Service providers factor in the cost of operating and maintaining their 3D printing equipment.
- Design and Engineering Fees: If design optimization or engineering support is required, these services will also contribute to the cost.
Teslim Süreleri:
- Part Complexity and Size: More intricate or larger mold cores will typically require longer printing times.
- Malzeme Durumu: The availability of the chosen metal powder can affect lead times. Metal3DP maintains a stock of high-quality powders to minimize delays.
- Printing Queue and Capacity: The service provider’s current workload and machine availability will influence lead times.
- Post-Processing Duration: The time required for post-processing steps can vary depending on the complexity and the specific techniques used.
- Shipping and Logistics: Transportation time should be factored into the overall lead time.
While metal 3D printing can sometimes have a higher upfront cost compared to traditional methods for simple geometries, it can be more cost-effective for complex designs and low-to-medium volume production, especially when considering factors like reduced material waste and faster time-to-market. Obtaining detailed quotes from potential service providers like Metal3DP and discussing your specific requirements will provide a clearer understanding of the cost and lead time for your project.
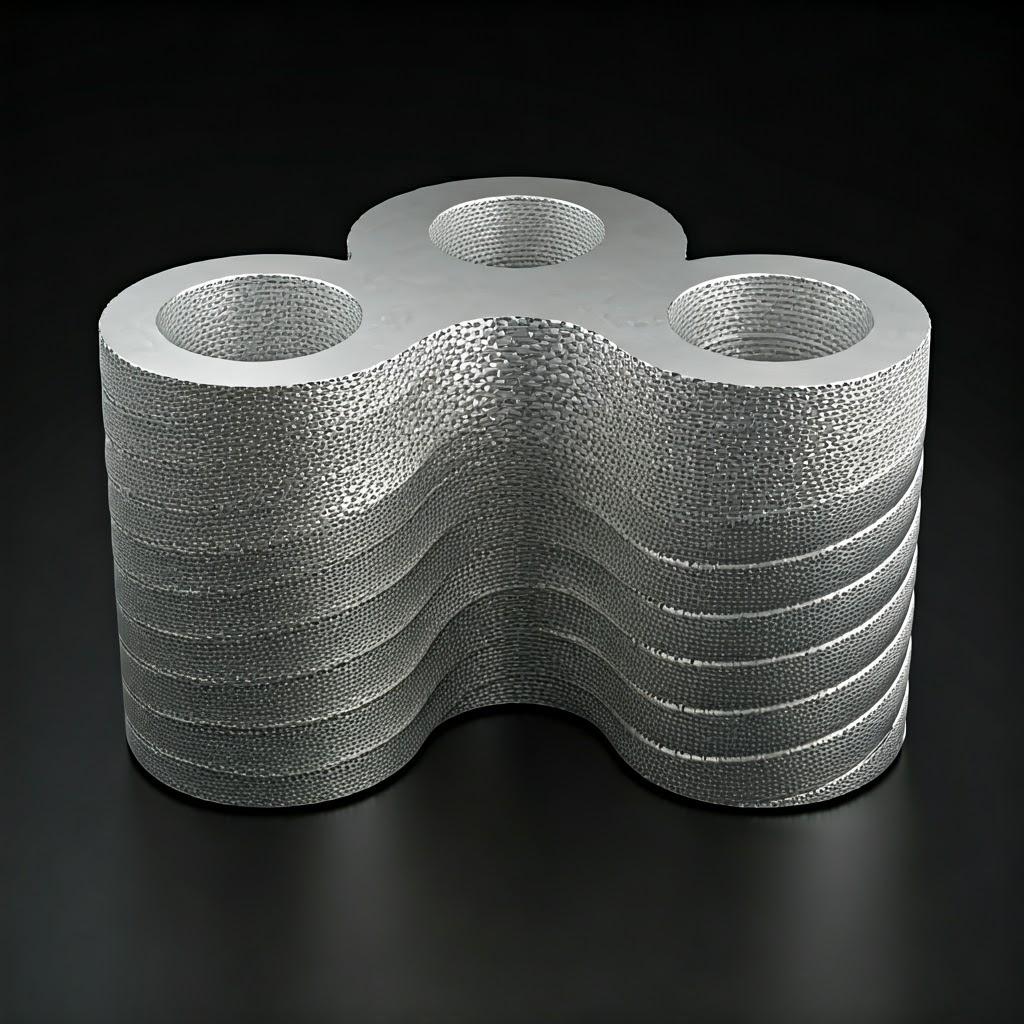
Frequently Asked Questions (FAQ) – Addressing Common Inquiries about 3D Printing Mold Cores
- Q: Can metal 3D printed mold cores achieve the same lifespan as conventionally manufactured cores?
- A: Yes, with proper material selection (like 1.2709 or H13), optimized design, and appropriate post-processing, metal 3D printed mold cores can achieve comparable or even longer lifespans than conventionally manufactured cores, especially due to the possibility of incorporating conformal cooling for better thermal management.
- Q: Is metal 3D printing cost-effective for producing single injection mold cores?
- A: Metal 3D printing can be cost-effective for single, complex mold cores, especially when the design incorporates features that are difficult or impossible to achieve with traditional methods. The reduced lead time and design flexibility can also provide significant value. For very simple geometries and high volumes, traditional methods might still be more economical.
- Q: What is the typical turnaround time for a 3D printed injection mold core?
- A: Turnaround times vary depending on the size and complexity of the mold core, the chosen material, and the required post-processing. It can range from a few days to several weeks. Contact Metal3DP with your specific requirements for a more accurate estimate.
Conclusion – Embracing the Future of Injection Molding with Metal 3D Printing
Metal 3D printing is revolutionizing the production of injection mold cores, offering unparalleled design freedom, reduced lead times, and the potential for enhanced performance through features like conformal cooling. For industries demanding high-quality, complex tooling solutions, such as aerospace, automotive, medical, and industrial manufacturing, the advantages of metal additive manufacturing are becoming increasingly compelling. By leveraging the expertise and advanced technologies offered by companies like Metal3DP Teknoloji A.Ş., LTD, businesses can unlock new possibilities in injection molding, leading to improved part quality, faster innovation cycles, and a more efficient manufacturing process. Embracing metal 3D printing for injection mold cores is not just an advancement; it’s a strategic move towards the future of manufacturing.
Paylaş
MET3DP Technology Co, LTD, merkezi Qingdao, Çin'de bulunan lider bir katmanlı üretim çözümleri sağlayıcısıdır. Şirketimiz, endüstriyel uygulamalar için 3D baskı ekipmanları ve yüksek performanslı metal tozları konusunda uzmanlaşmıştır.
İşletmeniz için en iyi fiyatı ve özelleştirilmiş Çözümü almak için sorgulayın!
İlgili Makaleler
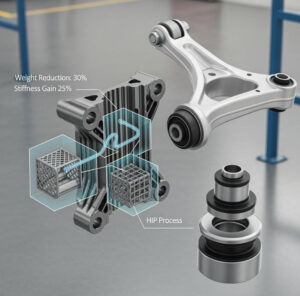
Metal 3D Printed Subframe Connection Mounts and Blocks for EV and Motorsport Chassis
Daha Fazla Oku "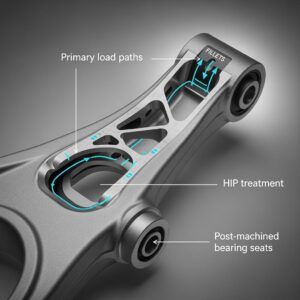
Metal 3D Printing for U.S. Automotive Lightweight Structural Brackets and Suspension Components
Daha Fazla Oku "Met3DP Hakkında
Son Güncelleme
Bizim Ürünümüz
BİZE ULAŞIN
Herhangi bir sorunuz var mı? Bize şimdi mesaj gönderin! Mesajınızı aldıktan sonra tüm ekibimizle talebinize hizmet edeceğiz.