MIM Teknolojisi Üzerine Notlar
İçindekiler
Metal enjeksiyon kalıplama (MIM) geleneksel metal işleme ile plastik enjeksiyon kalıplama arasındaki boşluğu dolduran devrim niteliğinde bir üretim sürecidir. Plastik kalıplamanın hızı ve maliyet etkinliği ile karmaşık, neredeyse net şekilli metal parçalar yarattığınızı hayal edin - işte MIM'in büyüsü budur. Ancak daha derine inmeden önce, temel unsurları açıklayalım.
MIM Nedir ve Nasıl Çalışır?
MIM'i bir mutfak macerası olarak düşünün. En sevdiğiniz kurabiye tarifindeki un gibi ince toz haline getirilmiş bir metalle başlarsınız. Bu metal tozu ana bileşen olarak işlev görür ve belirli özellikleri nihai parçanın özelliklerini belirler. Farklı metal tozlarını daha sonra inceleyeceğiz. Daha sonra, hamurunuzdaki ıslak malzemelere benzer bir bağlayıcı malzeme karıştırılır. Bu bağlayıcı, kalıplama işlemi sırasında metal parçacıkları bir arada tutar.
Elde edilen ve hammadde olarak adlandırılan karışım daha sonra yüksek basınç altında bir kalıp boşluğuna enjekte edilir, tıpkı kurabiye hamurunun bir krema torbasından sıkılması gibi. Soğuduktan sonra, kırılgan ve hala bağlayıcı içeren "yeşil" bir parçaya sahip olursunuz. İşte burada benzetme biraz bozuluyor. Yeşil kısım, bağlayıcının ısı ve genellikle kimyasal bir çözücü kombinasyonuyla titizlikle çıkarıldığı bir ayıklama işlemine tabi tutulur. Kurabiye hamurunuzdaki çikolata parçacıklarını dikkatlice ayıkladığınızı ve geride sadece un yapısını bıraktığınızı düşünün.
Son olarak, parça sinterleme aşamasına girer. Bunu "öğütülmüş" hamurunuzu pişirmek gibi düşünün. Yüksek sıcaklıklar metal parçacıklarının birbirine bağlanmasına neden olarak ağ şekline yakın, yüksek yoğunluklu bir metal bileşen oluşturur.
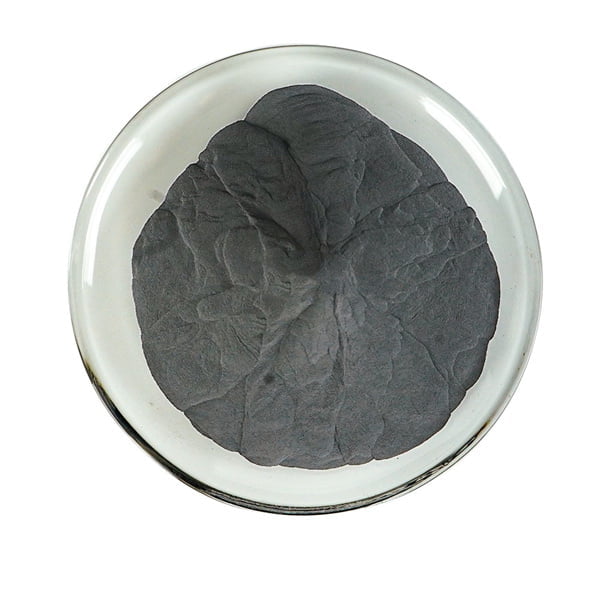
Cazibesini Ortaya Çıkarmak MIM: Faydalarına Bir Bakış
MIM, çeşitli sektörler için cazip bir seçim haline getiren büyüleyici bir dizi avantaja sahiptir. İşte sizi kazanabilecek bazı temel avantajlar:
- Karmaşık Geometriler: Geleneksel işlemenin aksine MIM, dar toleranslara sahip karmaşık şekiller üretmede mükemmeldir. Hassas dişlere sahip dişliler veya karmaşık tıbbi implantlar ürettiğinizi düşünün - MIM bu geometrileri kolaylıkla işleyerek maliyetli son işlemlerden tasarruf sağlar.
- Yüksek Üretim Oranları: MIM yüksek hacimli üretimde parlıyor. Her bir parçanın ayrı ayrı işlenmesine kıyasla, MIM'in hızlı kalıplama süreci üretim oranlarını önemli ölçüde artırarak daha hızlı geri dönüş süreleri ve potansiyel olarak daha düşük maliyetler sağlar.
- Malzeme Çok Yönlülüğü: MIM tek bir metalle sınırlı değildir. Her biri benzersiz özelliklere sahip çok çeşitli metal tozları kullanılabilir. Bu, parçanın mukavemetini, korozyon direncini ve diğer özelliklerini belirli uygulama ihtiyaçlarına göre uyarlamaya olanak tanır.
- Boyutsal Doğruluk: MIM parçaları etkileyici boyutsal hassasiyete sahiptir ve kapsamlı işleme sonrası ihtiyacı en aza indirir. Bu da tutarlı parça kalitesi ve daha az üretim israfı anlamına gelir.
- Maliyet-Etkinlik: Karmaşık parçaların yüksek hacimli üretimi için MIM, geleneksel işlemeye göre uygun maliyetli bir alternatif olabilir. Talaşlı işleme ihtiyacının azalması ve malzeme israfının en aza indirilmesi, ekonomik cazibesine katkıda bulunur.
MIM için Metal Tozları
Şimdi, MIM'in kalbi ve ruhu olan metal tozları dünyasına girelim. Seçilen spesifik toz, nihai parçanın özelliklerini önemli ölçüde etkiler. İşte bazı popüler seçeneklere bir bakış:
Paslanmaz Çelik Tozları:
- 316L: En yaygın kullanılan MIM paslanmaz çelik, mükemmel korozyon direnci ve biyouyumluluk sunarak tıbbi implantlar ve gıda işleme ekipmanları için idealdir.
- 17-4PH: Havacılık ve uzay bileşenleri gibi olağanüstü mekanik mukavemet gerektiren uygulamalar için mükemmel, yüksek mukavemetli, çökeltilerek sertleştirilebilir paslanmaz çelik.
Düşük Alaşımlı Çelik Tozları:
- 46XX Serisi: Bu çok yönlü düşük alaşımlı çelikler, otomotiv ve genel mühendislik uygulamaları için uygun hale getiren iyi bir mukavemet, tokluk ve uygun fiyat dengesi sunar.
Takım Çeliği Tozları:
- H13: Bu yüksek alaşımlı takım çeliği mükemmel aşınma direncine sahiptir, bu da onu metal şekillendirme işlemlerinde kullanılan kalıplar ve zımbalar için ideal kılar.
Nikel Bazlı Alaşım Tozları:
- Inconel 625: Bu yüksek performanslı nikel bazlı süper alaşım, yüksek sıcaklıklara ve korozyona karşı olağanüstü direnç sunarak jet motorları ve kimyasal işleme ekipmanları gibi zorlu uygulamalar için mükemmeldir.
Diğer Metal Tozları:
MIM bu seçeneklerle sınırlı değildir. Bakır, titanyum ve tungsten gibi diğer malzemeler de kullanılabilir ve bu çok yönlü teknolojinin potansiyel uygulamalarını genişletir.
Malzeme Seçimine Etki Eden Faktörler
İşiniz için doğru metal tozunu seçme MIM projesi, çeşitli faktörlerin dikkatle değerlendirilmesini gerektirir:
- İstenilen Özellikler: Parçanız için kritik özellikler nelerdir? Mukavemet, korozyon direnci, ısı toleransı - her metal tozu benzersiz bir özellik karışımı sunar.
- Geometrinin Karmaşıklığı: Bazı tozlar diğerlerine göre daha iyi akar ve karmaşık şekiller elde etme kabiliyetini etkiler.
- Maliyet Değerlendirmeleri: Malzeme maliyetleri önemli ölçüde değişebilir.
- Parça Boyutu: Toz partikül boyutu, nihai parçada elde edilebilecek minimum özellik boyutunu etkileyebilir.
- İşlem Sonrası Gereksinimler: Bazı metal tozları, sinterlemeden sonra daha iyi mukavemet için infiltrasyon veya gelişmiş mekanik özellikler için ısıl işlem gibi ek işlemler gerektirir. Bu ek adımlar toplam maliyeti ve üretim süresini etkileyebilir.
MIM Teknolojisi Uygulamaları
MIM'in çeşitli yetenekleri, çok çeşitli sektörlerde uygulanmasına kapı açmıştır. İşte öne çıkan bazı örnekler:
- Tıbbi Cihazlar: MIM'in karmaşık, biyouyumlu parçalar üretme yeteneği, onu eklem replasmanları, stentler ve cerrahi aletler gibi tıbbi implantların üretimi için ideal hale getirir.
- Havacılık ve Savunma: Bazı MIM malzemelerinin sunduğu yüksek mukavemet/ağırlık oranı ve ısı direnci, onları türbin kanatları ve motor parçaları gibi havacılık bileşenleri için uygun hale getirir. Ayrıca MIM, dar toleranslara sahip karmaşık ateşli silah bileşenleri üretebilir.
- Otomotiv: MIM, yüksek üretim hızlarıyla karmaşık şekiller oluşturma kabiliyeti nedeniyle dişliler, şanzıman bileşenleri ve yakıt sistemi parçaları gibi otomotiv uygulamalarında kendine yer bulmaktadır.
- Tüketici Elektroniği: Elektronik cihazlarda kullanılan konektörler ve muhafazalar gibi küçük, karmaşık bileşenler MIM kullanılarak verimli bir şekilde üretilebilir.
- Telekomünikasyon: MIM, sıkı toleranslar ve boyutsal doğruluk elde etme kabiliyeti nedeniyle telekomünikasyon ekipmanı için karmaşık parçalar üretmek için kullanılır.
MIM'in Avantajları ve Sınırlamaları
MIM bir dizi cazip faydaya sahip olsa da, bilinçli kararlar vermek için sınırlamalarını kabul etmek çok önemlidir. İşte dengeli bir bakış açısı:
Avantajlar:
- Karmaşık Geometriler: Daha önce de tartışıldığı gibi, MIM karmaşık şekiller üretmede mükemmeldir ve karmaşık son işlemlere olan ihtiyacı azaltır.
- Yüksek Üretim Oranları: Yüksek hacimli üretim için MIM, geleneksel işleme yöntemlerine kıyasla hız ve verimlilik açısından önemli avantajlar sunmaktadır.
- Malzeme Çok Yönlülüğü: Çok çeşitli metal tozlarının kullanılabilmesi, parçaların özel uygulama ihtiyaçlarına göre uyarlanabilmesini sağlar.
- Boyutsal Doğruluk: MIM parçaları etkileyici bir boyutsal doğruluğa ulaşarak kapsamlı işleme sonrası ihtiyacı en aza indirir.
Sınırlamalar:
- Parça Boyutu Sınırlamaları: MIM kullanılarak üretilebilecek maksimum parça boyutunda sınırlamalar vardır. Çok büyük veya hacimli bileşenler bu süreç için uygun olmayabilir.
- Yüzey İşlemi: MIM parçaları tipik olarak işlenmiş bileşenlere kıyasla daha pürüzlü bir yüzey kalitesine sahiptir. Bu durum, uygulama gereksinimlerine bağlı olarak ek finisaj işlemleri gerektirebilir.
- Malzeme Özellikleri: Çeşitli metal tozları mevcut olsa da, geleneksel süreçlerle elde edilebilen bazı özellikler MIM ile tam olarak kopyalanamayabilir. Örneğin, bazı metallerde en yüksek mukavemet seviyelerine ulaşmak MIM ile zor olabilir.
- Geliştirme Maliyetleri: Bir MIM üretim hattı kurmak önemli ön maliyetler içerebilir. Bu, düşük üretim hacimli projeler için dikkate alınması gereken bir husus olabilir.
Seçme MIM Projeniz için
MIM, karmaşık metal parçaların üretimi için güçlü bir araç sunar. Ancak, MIM'in projeniz için doğru seçim olup olmadığını belirlemek için aşağıdaki faktörleri göz önünde bulundurun:
- Parça Karmaşıklığı: Parçanız sıkı toleranslara sahip karmaşık şekiller gerektiriyorsa, MIM mükemmel bir seçenek olabilir.
- Üretim Hacmi: Yüksek hacimli üretim için MIM, geleneksel işlemeye kıyasla önemli maliyet ve zaman tasarrufu sağlayabilir.
- Malzeme Gereksinimleri: Parçanız için gereken kritik özellikleri değerlendirin ve seçilen metal tozunun bunları sağlayabildiğinden emin olun.
- Proje Bütçesi: Potansiyel ön geliştirme maliyetleri ve işlem sonrası gereksinimler dahil olmak üzere MIM'in maliyet etkilerini göz önünde bulundurun.
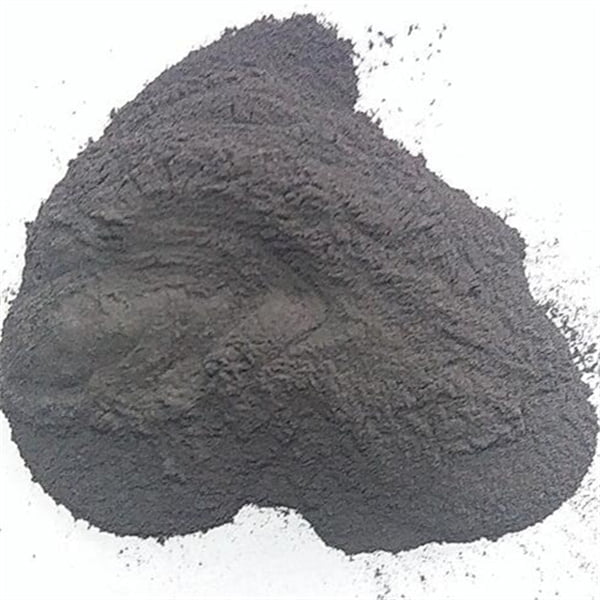
SSS
S: MIM'in geleneksel işlemeye göre avantajları nelerdir?
MIM, karmaşık geometriler üretme yeteneği, yüksek üretim oranları ve malzeme çeşitliliği gibi çeşitli avantajlar sunar. Ek olarak, MIM iyi bir boyutsal doğruluk elde edebilir ve potansiyel olarak kapsamlı işleme sonrası işleme ihtiyacını azaltır.
S: MIM'in sınırlamaları nelerdir?
MIM ile elde edilebilecek maksimum parça boyutunda sınırlamalar vardır. Ayrıca, MIM parçaları tipik olarak işlenmiş bileşenlere kıyasla daha pürüzlü bir yüzey kalitesine sahiptir. MIM ile elde edilebilen malzeme özellikleri de geleneksel süreçlerle elde edilebilenlerden biraz farklı olabilir.
S: MIM'de ne tür metal tozları kullanılabilir?
MIM'de paslanmaz çelik, düşük alaşımlı çelik, takım çeliği, nikel bazlı alaşımlar ve diğerleri dahil olmak üzere çok çeşitli metal tozları kullanılabilir. Seçilen spesifik toz, nihai parçanın özelliklerini önemli ölçüde etkiler.
S: MIM düşük hacimli üretim için uygun mudur?
MIM yüksek hacimli üretim için iyi bir seçenek olabilirken, ön geliştirme maliyetleri düşük hacimli projeler için avantajlardan daha ağır basabilir. Bu gibi durumlarda geleneksel işleme daha uygun olabilir.
MIM Teknolojisinin Geleceği:
MIM teknolojisi, malzemeler, işleme teknikleri ve tasarım yazılımlarındaki ilerlemelerle sürekli olarak gelişmektedir. İşte ufuktaki bazı heyecan verici olasılıklar:
- Yeni Metal Tozları: Daha yüksek mukavemet, daha iyi korozyon direnci gibi gelişmiş özelliklere sahip yeni metal tozlarının geliştirilmesi ve hatta fonksiyonel derecelendirilmiş parçaların basılabilmesi MIM uygulamalarını genişletecektir.
- Katmanlı Üretim Entegrasyonu: MIM'i 3D baskı gibi eklemeli üretim teknikleriyle birleştirmek, daha da karmaşık geometriler oluşturmak ve potansiyel olarak parçaları kişiselleştirmek için umut vaat ediyor.
- Sürdürülebilirlik İyileştirmeleri: MIM süreci sırasında atıkların azaltılması ve enerji tüketiminin en aza indirilmesi devam eden araştırma alanlarıdır. Sürdürülebilir uygulamalar gelecekte giderek daha önemli hale gelecektir.
Sonuç
MIM teknolojisi, karmaşık, net şekle yakın metal parçaların yüksek üretim verimliliğiyle üretilmesi için cazip bir çözüm sunar. Yeteneklerini, sınırlamalarını ve tasarım hususlarını anlamak, projenize uygunluğu hakkında bilinçli kararlar vermenizi sağlar. MIM teknolojisi gelişmeye devam ettikçe, metal üretiminin geleceğini şekillendirmede daha da önemli bir rol oynamaya hazırlanıyor.
Paylaş
MET3DP Technology Co, LTD, merkezi Qingdao, Çin'de bulunan lider bir katmanlı üretim çözümleri sağlayıcısıdır. Şirketimiz, endüstriyel uygulamalar için 3D baskı ekipmanları ve yüksek performanslı metal tozları konusunda uzmanlaşmıştır.
İşletmeniz için en iyi fiyatı ve özelleştirilmiş Çözümü almak için sorgulayın!
İlgili Makaleler
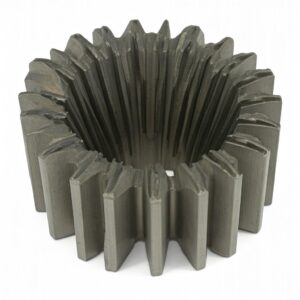
Yüksek Performanslı Nozul Kanat Segmentleri: Metal 3D Baskı ile Türbin Verimliliğinde Devrim
Daha Fazla Oku "Met3DP Hakkında
Son Güncelleme
Bizim Ürünümüz
BİZE ULAŞIN
Herhangi bir sorunuz var mı? Bize şimdi mesaj gönderin! Mesajınızı aldıktan sonra tüm ekibimizle talebinize hizmet edeceğiz.
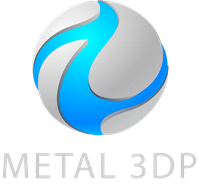
3D Baskı ve Katmanlı Üretim için Metal Tozları