High-Performance Nozzle Vanes via Additive Manufacturing
İçindekiler
Introduction to Turbine Nozzle Guide Vanes (NGVs): The Critical Hot Section Component
Turbine Nozzle Guide Vanes (NGVs), often referred to simply as nozzle vanes or stator vanes, are absolutely fundamental components situated within the challenging environment of a gas turbine’s hot section. Positioned typically between the combustor outlet and the first stage of turbine rotor blades, NGVs perform a series of critical functions that are indispensable for the efficient and safe operation of both aerospace jet engines and industrial gas turbines (IGTs) used in power generation and other heavy industries. Their primary role is aerodynamic: they take the high-temperature, high-pressure, and often turbulent gas flow exiting the combustor and precisely guide it onto the downstream rotor blades at the optimal angle, velocity, and flow profile. This controlled redirection of energy is paramount for maximizing the work extracted by the turbine rotor, directly influencing the overall thrust of a jet engine or the power output of an IGT.
The environment in which NGVs operate is arguably one of the most demanding within any mechanical system. They are continuously exposed to extreme temperatures, often exceeding 1200∘C (2192∘F) and approaching the melting point of many conventional alloys. This thermal load is coupled with significant pressure differentials and high-velocity gas streams laden with combustion byproducts, creating a highly oxidizing and potentially corrosive atmosphere. Furthermore, NGVs experience substantial thermal cycling during engine start-up, operation, and shutdown sequences, inducing significant thermomechanical stresses. These stresses, combined with the inherent static pressure loads and potential vibratory excitation from the turbulent flow, demand exceptional material properties and structural integrity. Failure of an NGV can have catastrophic consequences, leading to downstream damage to expensive rotor blades and potentially complete engine failure.
Given these severe operating conditions, NGVs must be manufactured from advanced materials, typically nickel-based or cobalt-based superalloys, renowned for their exceptional high-temperature strength, creep resistance (resistance to deformation under long-term stress at high temperature), fatigue strength (resistance to failure under cyclic loading), and resistance to oxidation and hot corrosion. Historically, investment casting has been the dominant manufacturing method for NGVs. While effective, casting intricate NGV geometries, especially those incorporating complex internal cooling passages necessary for modern high-efficiency turbines, presents significant manufacturing challenges, often leading to long lead times, potential casting defects, and limitations in design complexity. The intricate internal cooling networks, designed to bleed cooler air from the compressor stage through the vane structure to keep metal temperatures within acceptable limits, are crucial for increasing turbine inlet temperatures, which directly correlates with improved engine efficiency and reduced emissions. However, achieving these sophisticated cooling designs via traditional casting methods is often complex and costly.
The advent and maturation of metal additive manufacturing (AM), particularly laser powder bed fusion (L-PBF) and electron beam melting (EBM), offers a transformative approach to NGV production. AM technologies enable the layer-by-layer fabrication of highly complex geometries directly from digital models, overcoming many limitations associated with casting. This allows for the realization of optimized NGV designs with unprecedented internal cooling channel complexity, thinner trailing edges for improved aerodynamic efficiency, and potentially integrated features that reduce part count and assembly requirements. Furthermore, AM facilitates the use of advanced superalloys, potentially enabling new material compositions tailored specifically for the NGV application. For procurement managers and engineers in aerospace, power generation, and industrial manufacturing, understanding the capabilities and nuances of producing NGVs via metal AM is becoming increasingly critical for developing next-generation, high-performance turbine systems. This technology promises not only performance improvements but also potential benefits in supply chain responsiveness, component lifecycle management, and the ability to rapidly iterate on designs or produce bespoke components for specific operational needs. The transition towards AM for critical hot section components like NGVs represents a significant technological shift, demanding a thorough understanding of the process, materials, design considerations, and quality assurance requirements involved.
Applications and Demands: Where are NGVs Utilized?
Nozzle Guide Vanes are indispensable components across a spectrum of high-technology applications where gas turbines form the core power unit. Their presence is critical wherever the conversion of thermal energy from combusted fuel into rotational mechanical energy is required under extreme temperature and pressure conditions. The primary application domains include:
- Aerospace Jet Engines: This is perhaps the most widely recognized application. NGVs are found in virtually all types of jet engines, including:
- Turbofans: Used in commercial airliners and modern military aircraft, NGVs direct the hot gas flow from the combustor onto the high-pressure turbine (HPT) stages, which drive the compressor and the large front fan. The efficiency and durability of these HPT NGVs directly impact fuel consumption, thrust output, and engine reliability – critical factors for airline profitability and military mission effectiveness.
- Turbojets: Simpler jet engines, often found in older military aircraft or smaller applications, still rely on NGVs to guide gas onto the turbine stages driving the compressor.
- Turboprops/Turboshafts: Used in regional aircraft, helicopters, and some auxiliary power units (APUs), these engines use the turbine’s power primarily to drive a propeller or a shaft (e.g., for a helicopter rotor or generator). NGVs remain essential for efficient energy transfer in the hot section.
- Military Engines: Often push the boundaries of temperature and performance, demanding NGVs capable of withstanding even more extreme conditions and rapid thermal transients during combat maneuvers.
- Industrial Gas Turbines (IGTs): These turbines are workhorses in several key industrial sectors:
- Güç Üretimi: Large frame and aeroderivative gas turbines are extensively used in power plants for generating electricity, either in simple cycle or combined cycle configurations (where exhaust heat generates steam for a secondary steam turbine). NGVs in these massive turbines are crucial for maximizing electrical output efficiency and ensuring long operational lifetimes between maintenance intervals, directly impacting grid stability and the cost of electricity. Reliability and durability are paramount, as downtime is extremely costly.
- Petrol ve Gaz: IGTs provide mechanical drive for compressors and pumps along pipelines, in refineries, and on offshore platforms. NGVs in these applications must withstand potentially corrosive elements present in the fuel or environment, alongside high temperatures and pressures. Unplanned shutdowns can halt significant production operations.
- Mechanical Drive: Various industrial processes utilize gas turbines for direct mechanical drive of large machinery, such as compressors in chemical plants or large pumps.
Performance Demands Across Applications:
Regardless of the specific application, the fundamental demands placed on NGVs are consistently severe, although the relative importance of certain factors might shift:
- Extreme Temperature Capability: NGVs operate at the forefront of the turbine section, directly facing the combustor exit gas, which can reach temperatures well above 1300−1500∘C in advanced engines. Materials must maintain structural integrity and resist creep deformation under sustained high temperatures.
- High Thermomechanical Fatigue (TMF) Resistance: The repeated cycles of heating and cooling during engine start-up, load changes, and shutdown induce significant thermal gradients and stresses. NGVs must resist cracking and failure under these TMF conditions over thousands of operational cycles.
- Oxidation and Hot Corrosion Resistance: The high-temperature gas stream is highly oxidizing. If lower-grade fuels are used (more common in IGTs), contaminants like sulfur, vanadium, or sea salt (in marine environments) can lead to accelerated hot corrosion. NGV materials and potential coatings must resist this chemical degradation.
- Aerodynamic Efficiency: The shape of the NGV airfoils, including the smoothness of the surface and the sharpness of the trailing edge, directly impacts how effectively the gas flow energy is directed to the rotor blades. Poor aerodynamic performance leads to efficiency losses. Complex internal cooling schemes must be designed not to compromise the external aerodynamic profile significantly.
- Structural Integrity under Pressure Loading: NGVs must withstand the substantial pressure difference between their concave (pressure) and convex (suction) surfaces without excessive deformation or failure.
- Resistance to Foreign Object Damage (FOD) and Erosion: While less common than for rotor blades, NGVs can still be susceptible to damage from small particles ingested by the engine or from carbon deposits breaking off the combustor. Material toughness and potentially specialized coatings are important.
- Manufacturability of Complex Cooling: Modern high-efficiency turbines rely heavily on sophisticated internal cooling designs within the NGVs. These often involve intricate serpentine passages, arrays of tiny pin-fins, and precisely shaped film cooling holes exiting onto the vane surface. The manufacturing process must be capable of producing these features reliably and accurately.
- Reliability and Long Service Life: Especially in commercial aviation and power generation, NGVs are expected to operate reliably for thousands, or even tens of thousands, of hours between inspections or replacements. Unscheduled maintenance or premature failure is highly undesirable and costly.
Procurement managers and design engineers must constantly balance these demanding performance requirements against manufacturing costs, lead times, and material availability. The pursuit of higher turbine efficiencies (leading to lower fuel consumption and emissions) continually pushes operating temperatures higher, placing ever-increasing demands on NGV materials and cooling technologies. This relentless drive for performance is a key reason why advanced manufacturing techniques like metal AM are becoming increasingly attractive for NGV production.
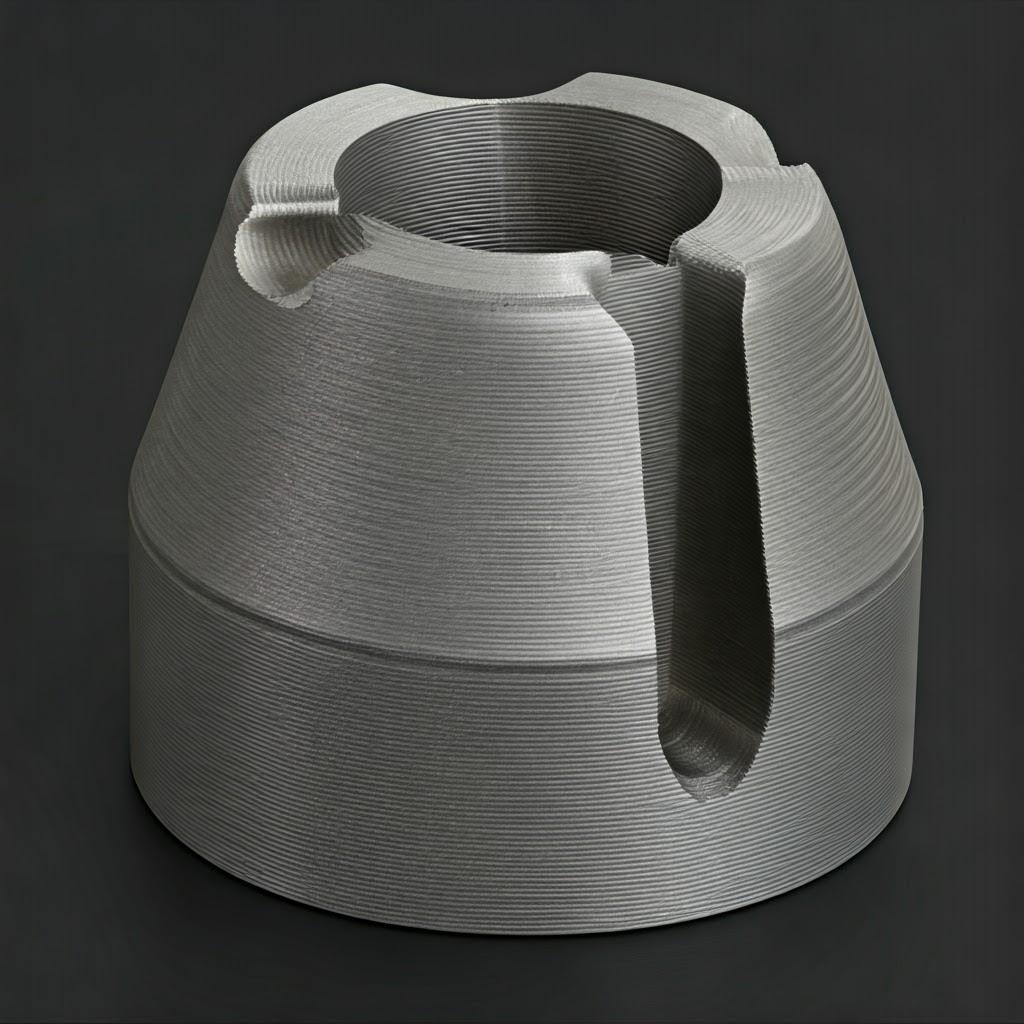
Revolutionizing NGV Production: Why Choose Metal Additive Manufacturing?
The decision to adopt metal additive manufacturing (AM) for producing critical components like Turbine Nozzle Guide Vanes stems from a confluence of compelling advantages that directly address the limitations of traditional methods, primarily investment casting, while unlocking new possibilities in performance, design, and supply chain agility. For engineers striving for higher efficiency and procurement managers seeking better value and responsiveness, metal AM presents a paradigm shift in NGV manufacturing.
Key Advantages of Metal AM for NGVs:
- Unprecedented Design Freedom for Complex Geometries: This is perhaps the most significant advantage. AM builds parts layer by layer, allowing for the creation of internal and external features that are extremely difficult, prohibitively expensive, or simply impossible to achieve with casting or machining.
- Optimized Internal Cooling: AM enables the design and fabrication of highly sophisticated internal cooling channels. This includes conformal cooling passages that closely follow the vane’s external shape, complex lattice structures or trip strips to enhance internal heat transfer, and precisely placed, uniquely shaped film cooling holes. Such advanced cooling allows turbine inlet temperatures to be raised significantly, boosting thermal efficiency, power output, and reducing fuel consumption/emissions, without exceeding the NGV material’s temperature limits.
- Improved Aerodynamics: Features like ultra-thin trailing edges, which reduce aerodynamic losses but are difficult to cast reliably, can be produced more consistently with AM. Complex curvatures and blended surfaces optimized through computational fluid dynamics (CFD) can be realized without the constraints imposed by mold creation and removal.
- Hafifletme: While mass is less critical for static NGVs than rotating blades, AM allows for topology optimization, placing material only where structurally necessary, potentially reducing overall engine weight slightly or enabling more intricate features without a weight penalty.
- Parça Konsolidasyonu: Complex NGV assemblies might traditionally consist of multiple cast or fabricated pieces brazed or welded together. AM allows for the possibility of printing such assemblies as a single, monolithic component. This eliminates joining processes (which can be points of weakness or require additional inspection), simplifies the supply chain, reduces assembly time and cost, and can improve overall structural integrity.
- Accelerated Prototyping and Design Iteration: The traditional process of creating casting tooling is time-consuming and expensive. Any design modification requires new tooling, significantly slowing down development cycles. With AM, design changes can be implemented digitally, and new prototype NGVs can be printed relatively quickly (days or weeks, compared to months for casting tooling). This rapid iteration capability allows engineers to test and refine NGV designs much faster, leading to optimized performance sooner in the development process. This agility is crucial in the competitive aerospace and power generation markets. Companies seeking to leverage this speed can explore metal 3D baskı services that specialize in rapid prototyping of high-performance components.
- Malzeme Verimliliği ve Azaltılmış Atık: AM processes, particularly powder bed fusion techniques like L-PBF and EBM, generally use material more efficiently than subtractive methods. While some support structures are needed and unfused powder must be recycled, the amount of raw material wasted compared to machining a part from a solid block is significantly lower. This is particularly relevant for expensive superalloys like IN738LC and Haynes 282 used in NGVs. Efficient powder reclamation and reuse are key aspects of sustainable AM operations.
- Potential for Novel Materials and Functionally Graded Materials (FGMs): While still an area of active research and development, AM opens the door to processing novel alloy compositions that may be difficult to cast. Furthermore, techniques could potentially allow for functionally graded materials, where the material composition or microstructure varies across the NGV part to optimize properties locally (e.g., higher temperature resistance near the leading edge, better ductility near the mounting points).
- On-Demand Production and Supply Chain Flexibility: AM enables digital manufacturing. NGV designs can be stored digitally and printed when needed, potentially reducing the need for large physical inventories. This “digital warehouse” concept can improve supply chain resilience, allowing for faster response to unexpected demand or the production of spare parts for legacy systems where original tooling no longer exists. It supports distributed manufacturing models, where parts could be printed closer to the point of use.
- Onarım ve Yenileme: Metal AM techniques like Directed Energy Deposition (DED) can also be used to repair damaged NGVs, such as restoring worn airfoil tips or repairing cracks, potentially extending the service life of these expensive components and reducing lifecycle costs.
Addressing B2B Considerations:
For wholesale buyers, NGV suppliers, and distributors, metal AM offers:
- Özelleştirme: Ability to offer customized NGV solutions for specific engine variants or operating conditions without the massive overhead of traditional tooling.
- Azaltılmış Teslim Süreleri: Shorter manufacturing cycles compared to casting can lead to faster fulfillment of orders, especially for smaller batch sizes or prototypes.
- Competitive Advantage: Offering AM-produced NGVs with superior performance (e.g., better cooling, higher efficiency) provides a distinct competitive edge in the market.
- Supply Chain Security: Reduced reliance on complex, geographically concentrated casting foundries potentially enhances supply chain stability.
While metal AM presents numerous advantages, it’s crucial to acknowledge that it also brings its own set of challenges, including the need for careful process control, specialized post-processing (like HIP and heat treatment), thorough non-destructive testing (NDT), and managing factors like residual stress and surface finish. However, the transformative potential for creating superior performance, next-generation NGVs often outweighs these challenges, driving significant investment and adoption in the aerospace and energy sectors. Partnering with experienced AM providers like Met3dp, who possess deep expertise in superalloy processing and quality control, is key to successfully leveraging these benefits.
Recommended Materials and Why They Matter: IN738LC and Haynes 282
The selection of materials for Turbine Nozzle Guide Vanes (NGVs) is fundamentally dictated by the extreme operating conditions they endure: scorching temperatures often exceeding 1100∘C, significant mechanical loads, corrosive combustion gases, and demanding requirements for long-term stability. Only a select group of materials, primarily precipitation-strengthened nickel-based superalloys, possess the necessary combination of properties. Among these, IN738LC (Low Carbon) ve Haynes 282 stand out as leading candidates frequently considered and utilized for NGV applications, especially when manufactured via additive manufacturing (AM). Understanding their specific attributes is crucial for engineers designing NGVs and procurement managers sourcing these critical components.
Superalloys: The Foundation of Hot Section Components
Nickel-based superalloys derive their exceptional high-temperature capabilities from a specific microstructure. The nickel matrix (gamma phase, γ) provides good ductility and corrosion resistance. This matrix is strengthened by finely dispersed precipitates of an intermetallic compound, typically Ni3(Al, Ti), known as the gamma prime phase (γ′). These γ′ precipitates are coherent with the γ matrix and effectively impede dislocation movement, which is the mechanism of plastic deformation, especially at elevated temperatures. Other alloying elements are added to further enhance specific properties:
- Krom (Cr): Provides oxidation and hot corrosion resistance by forming a protective chromium oxide (Cr2O3) scale.
- Kobalt (Co): Increases solid solution strength, raises the γ′ solvus temperature (the temperature at which γ′ dissolves back into the matrix, limiting the maximum operating temperature), and improves fatigue resistance.
- Molybdenum (Mo), Tungsten (W), Rhenium (Re): Contribute significantly to solid solution strengthening of the γ matrix, enhancing creep resistance.
- Aluminum (Al), Titanium (Ti), Niobium (Nb), Tantalum (Ta): Are primary formers of the strengthening γ′ phase. Their type and concentration dictate the volume fraction and stability of γ′.
- Carbon (C), Boron (B), Zirconium (Zr): Segregate to grain boundaries, forming carbides and borides that strengthen the grain boundaries and improve creep rupture life. However, excessive or improperly formed grain boundary phases can reduce ductility.
IN738LC: The Established Workhorse
IN738LC is a well-established, precipitation-hardenable nickel-based superalloy that has been widely used for cast turbine components, including blades and vanes, for decades. Its adaptation to additive manufacturing processes like Laser Powder Bed Fusion (L-PBF) has been a significant focus area.
- Temel Nitelikler:
- Excellent High-Temperature Strength and Creep Resistance: IN738LC maintains significant strength and resists deformation under load at temperatures up to around 980∘C (1800∘F). This is primarily due to its substantial volume fraction of stable γ′ precipitates.
- Good Oxidation and Hot Corrosion Resistance: Primarily due to its high chromium content (~16%), it forms a stable protective oxide layer, offering good resistance in typical combustion environments.
- Kaynaklanabilirlik Hususları: The “LC” designation stands for “Low Carbon” (typically < 0.10%). Reducing carbon content improves weldability and reduces the tendency for detrimental carbide precipitation in heat-affected zones, which is also beneficial for the layer-by-layer fusion process in AM, reducing susceptibility to solidification cracking.
- Extensive Property Database: Due to its long history in casting, there is a vast amount of data available on its mechanical properties, creep behavior, fatigue life, and environmental resistance, providing a strong baseline for qualifying AM-produced IN738LC.
- Relevance for AM NGVs:
- Its proven performance in demanding turbine environments makes it a trusted choice.
- Its relatively good processability (compared to some even higher-temperature alloys) in L-PBF systems, particularly the low carbon variant, makes it feasible for AM production.
- Achieving the desired microstructure and properties in AM IN738LC requires careful control over printing parameters (laser power, speed, layer thickness, scan strategy) and specific post-processing heat treatments, often including Hot Isostatic Pressing (HIP) to close internal porosity and homogenization/solutioning/aging steps to optimize the γ′ precipitates and grain structure.
Haynes 282: The Advanced Contender
Haynes 282 is a newer generation, precipitation-strengthened nickel-based superalloy specifically developed for high-temperature applications in aerospace and industrial gas turbines. It was designed to offer a superior combination of creep strength, thermal stability, weldability, and fabricability compared to other alloys like Waspaloy or R-41.
- Temel Nitelikler:
- Outstanding Creep Strength: Haynes 282 exhibits significantly improved creep strength compared to alloys like Waspaloy and even approaches the performance of alloys like IN738LC or R-41 in the 650−900∘C (1200−1650∘F) range.
- Mükemmel Termal Kararlılık: It shows good resistance to aging embrittlement after long exposures at intermediate temperatures.
- Superior Fabricability and Weldability: Compared to many other superalloys of similar strength levels, Haynes 282 was specifically designed for easier fabrication and welding, exhibiting significantly reduced susceptibility to strain-age cracking. This characteristic translates favorably to additive manufacturing, making it less prone to cracking during the rapid heating and cooling cycles inherent in the process.
- Good Oxidation Resistance: Similar to IN738LC, it possesses good resistance to high-temperature oxidation.
- Relevance for AM NGVs:
- Its enhanced creep properties and thermal stability allow for potentially higher operating temperatures or longer component life compared to older alloys.
- Its superior processability/weldability makes it an attractive candidate for complex AM builds, potentially requiring less stringent parameter control or being more forgiving than alloys highly susceptible to cracking.
- It represents a step forward in material capability, enabling more demanding NGV designs or operating conditions. Like IN738LC, optimal properties in AM Haynes 282 are achieved through carefully controlled printing and post-processing, including HIP and multi-step heat treatments tailored to precipitate the strengthening γ′ phase effectively.
Material Properties Comparison (Illustrative)
Mülkiyet | IN738LC (Typical Cast/AM + Post-Processed) | Haynes 282 (Typical Wrought/AM + Post-Processed) | Significance for NGVs |
---|---|---|---|
Max Operating Temp. | ~980∘C (1800∘F) | ~900−950∘C (1650−1740∘F) * | Dictates ability to handle turbine inlet temperatures |
Sürünme Dayanımı | Mükemmel | Outstanding (esp. in mid-high temp range) | Resists deformation under long-term stress at temperature |
Tensile Strength (RT) | Yüksek | Çok Yüksek | Overall structural integrity |
Oksidasyon Direnci | İyi | İyi | Resists degradation from hot combustion gases |
Hot Corrosion Resist. | İyi | İyi | Resists attack from fuel/air contaminants |
Fabricability/AM Proc. | Moderate (LC helps) | Mükemmel | Ease of printing, reduced cracking susceptibility |
Termal Kararlılık | İyi | Mükemmel | Resists property degradation over long exposure times |
Sayfalara Aktar
Note: Maximum use temperature depends heavily on stress level and desired component life. Haynes 282 often excels in creep strength in specific intermediate-to-high temperature ranges relevant to NGVs.
Met3dp’s Role in Material Supply and Expertise
Choosing the right material is only part of the equation; ensuring the quality and consistency of the metal powder used for additive manufacturing is equally critical. Companies like Met3dp play a vital role in this ecosystem. Leveraging advanced powder production techniques such as Vacuum Induction Melting Gas Atomization (VIGA) and Plasma Rotating Electrode Process (PREP), Met3dp specializes in producing high-quality, spherical metal powders with controlled particle size distributions and high purity – essential characteristics for successful L-PBF and EBM processes.
Met3dp’s capabilities include the production of challenging superalloys like IN738LC and potentially Haynes 282, ensuring that manufacturers have access to reliable feedstock. Their expertise extends beyond powder production to encompass the entire AM workflow, including optimizing printing parameters for specific alloys and providing application development support. Accessing high-quality powders is fundamental, and procurement managers can explore Met3dp’s diverse range of offerings on their ürün sayfası. Partnering with a knowledgeable powder supplier and AM service provider ensures that the chosen material’s potential is fully realized in the final NGV component.
In summary, both IN738LC and Haynes 282 offer compelling properties for additively manufactured NGVs. IN738LC provides a proven track record and excellent high-temperature strength, while Haynes 282 offers potentially superior creep resistance in key temperature ranges combined with enhanced processability, making it highly suitable for complex AM geometries. The final selection depends on the specific performance targets, operating conditions, design complexity, and the manufacturer’s experience with processing these advanced superalloys.
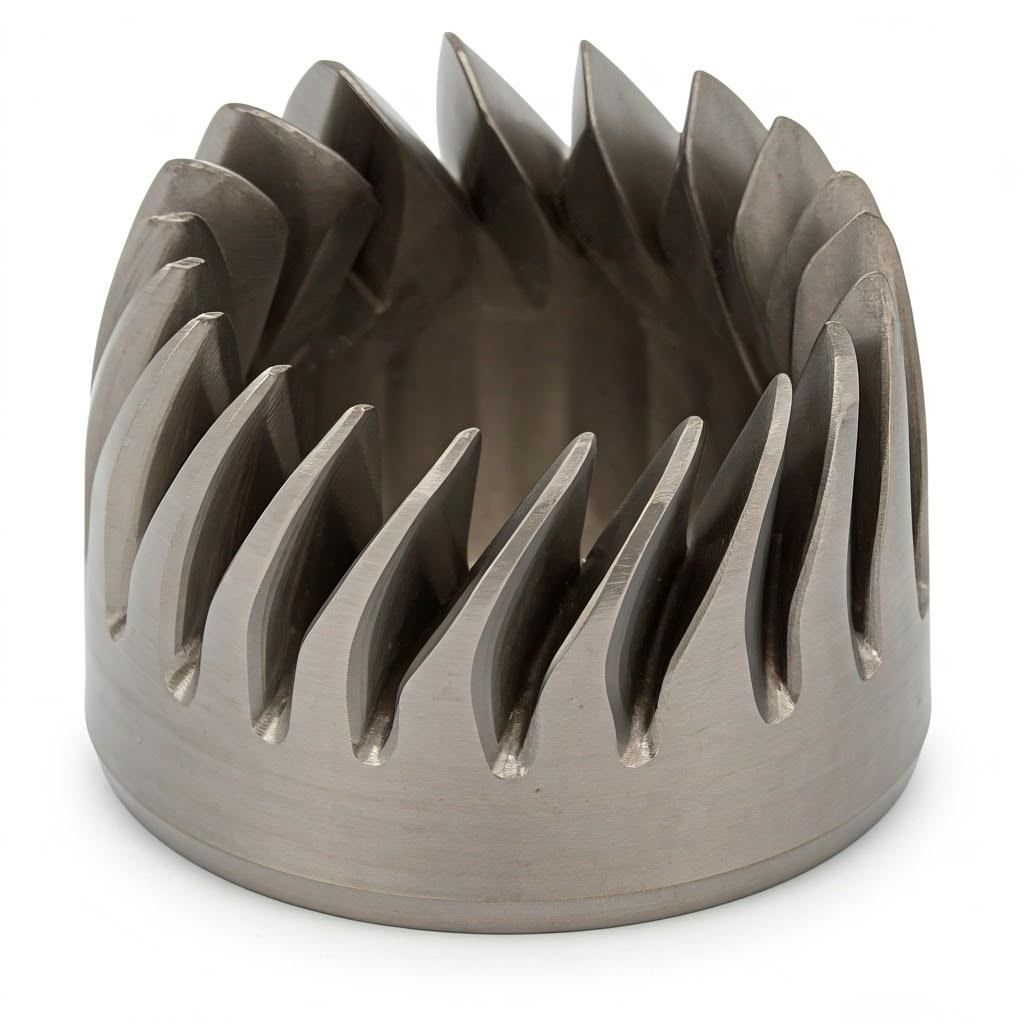
Design for Additive Manufacturing (DfAM) Principles for NGVs
Successfully leveraging metal additive manufacturing (AM) for Turbine Nozzle Guide Vanes (NGVs) is not merely about replicating existing cast designs using a different process. To truly unlock the potential of AM and achieve superior performance, engineers must embrace Design for Additive Manufacturing (DfAM) principles. DfAM involves rethinking the component’s architecture from the ground up, considering both the unique capabilities and the specific constraints of the layer-by-layer building process. Applying DfAM to NGVs focuses primarily on enhancing thermal management, improving aerodynamic efficiency, and ensuring manufacturability while maintaining structural integrity.
Key DfAM Considerations for AM NGVs:
- Revolutionizing Internal Cooling Architecture: This is where AM offers the most significant breakthroughs for NGVs.
- Konformal Soğutma Kanalları: Unlike straight, drilled passages common in some conventionally made parts, AM allows cooling channels to precisely follow the complex 3D contour of the NGV airfoil shape. This maintains a more uniform distance between the cooling fluid and the hot external surface, leading to more effective and efficient cooling, reducing peak metal temperatures, and minimizing thermal gradients that cause stress.
- Complex Channel Geometries: Serpentine passages with intricate turns, varying cross-sections, and integrated turbulators (ribs or other features designed to trip the boundary layer and enhance convective heat transfer inside the channel) can be readily incorporated. AM can create turbulator shapes and densities previously impossible, maximizing internal heat pickup.
- Optimized Film Cooling Holes: AM allows for the direct printing of film cooling holes with optimized shapes (e.g., diffusion-shaped or conical exits), orientations, and placements. This improves the effectiveness of the protective cool air film layered onto the vane’s external surface, further shielding it from the hot gas stream with potentially less cooling air consumption (improving overall engine efficiency).
- Integrated Pin-Fin Arrays: Dense arrays of small pins within internal cavities can significantly increase the surface area for heat transfer, providing highly effective cooling in specific regions, such as the trailing edge. AM can produce finer and more complex pin-fin designs than casting allows.
- Thin Wall Structures and Trailing Edge Optimization:
- NGV aerodynamic performance is sensitive to the thickness of the trailing edge; thinner edges generally reduce aerodynamic losses. Investment casting struggles to reliably produce very thin trailing edges due to metal flow limitations and fragility.
- AM, particularly L-PBF, can achieve significantly thinner walls and sharper trailing edges with greater consistency. However, DfAM requires careful consideration of the minimum printable wall thickness for the chosen material and process, thermal stresses accumulating in thin sections during the build, and the need for potential localized support structures. The design must balance aerodynamic benefit with structural integrity and manufacturability.
- Destek Yapısı Stratejisi: AM processes like L-PBF require support structures for overhanging features (typically angles below ~45 degrees relative to the build plate) and to anchor the part, preventing warpage due to thermal stresses.
- Minimizing Supports: DfAM encourages designing parts to be self-supporting where possible by orienting surfaces above the critical overhang angle. However, the complex geometry of NGVs often makes extensive support necessary.
- Designing for Removability: Supports must be removable without damaging the part. This is especially challenging for internal cooling channels. DfAM involves designing internal passages with geometries that either avoid the need for internal supports or incorporate features that facilitate support removal (e.g., access ports, channels designed for abrasive flow machining). The connection points of supports to the main part should be designed for easy detachment and minimal surface scarring.
- Impact on Surface Finish: Areas where supports are removed will typically have a rougher surface finish that may require additional post-processing, especially on critical aerodynamic surfaces or within cooling channels where roughness affects heat transfer and pressure drop.
- Managing Residual Stress: The rapid heating and cooling cycles inherent in AM generate significant residual stresses within the part.
- Part Orientation: How the NGV is oriented on the build plate affects stress accumulation, support requirements, and surface finish on different features. DfAM includes optimizing build orientation.
- Termal Yönetim Özellikleri: Sometimes, sacrificial features or specific scan strategies (patterns used by the laser or electron beam) can be employed to help manage heat flow and reduce stress buildup during the print.
- Geometry Considerations: Abrupt changes in cross-section or large bulky features can exacerbate stress issues. DfAM promotes smoother transitions and potentially incorporates stress-relieving geometric features where appropriate.
- Feature Integration and Part Consolidation: As mentioned earlier, DfAM encourages engineers to look for opportunities to combine multiple components (e.g., an airfoil and its mounting platform or sealing features) into a single printed part, reducing assembly complexity and potential failure points.
- Lattice Structures and Topology Optimization (Limited Applicability): While widely used in other AM applications for lightweighting, the primary structural and thermal demands on NGVs often limit the use of extensive lattice structures or aggressive topology optimization in the main load-bearing or heat-affected zones. However, they might find niche applications in non-critical areas like platforms or mounting features if weight reduction is a key driver and does not compromise performance.
Implementing DfAM requires a shift in mindset for designers accustomed to traditional manufacturing constraints. It necessitates close collaboration between design engineers, materials scientists, and AM process specialists. Utilizing simulation tools for thermal analysis, fluid dynamics (CFD), and mechanical stress prediction, specifically adapted for AM processes, is crucial for optimizing NGV designs and predicting their performance before committing to printing. The goal is not just to make the part additively, but to make a daha iyi part because it was made additively.
Achieving Precision: Tolerance, Surface Finish, and Dimensional Accuracy in AM NGVs
While metal additive manufacturing offers unparalleled geometric freedom, achieving the tight tolerances, specific surface finishes, and overall dimensional accuracy required for demanding applications like Turbine Nozzle Guide Vanes necessitates careful process control, realistic expectations, and often, targeted post-processing. Engineers and procurement managers must understand the levels of precision attainable with AM technologies like Laser Powder Bed Fusion (L-PBF) and Electron Beam Melting (EBM) when applied to high-performance superalloys.
Tolerances in Metal AM:
The achievable tolerances in metal AM depend on several factors:
- AM Technology: EBM typically builds faster and with lower residual stress due to the high-temperature vacuum environment, but often results in a rougher surface finish and slightly looser tolerances compared to L-PBF. L-PBF generally offers finer feature resolution and tighter ‘as-built’ tolerances.
- Machine Calibration and Condition: Well-maintained, high-quality AM systems are crucial. Consistent laser/electron beam spot size, power delivery, and precise powder layer recoating directly impact accuracy. Met3dp utilizes industry-leading printers known for their accuracy and reliability, which is fundamental for producing mission-critical parts.
- Malzeme: Different superalloys behave differently during melting and solidification, affecting shrinkage and potential distortion.
- Part Size and Geometry: Larger parts or parts with complex features and varying cross-sections are more prone to thermal distortion, affecting final tolerances.
- Yapı Oryantasyonu: The orientation on the build plate influences how thermal stresses accumulate and can affect the accuracy of specific features.
- İşlem sonrası: Stress relief and HIP cycles can cause minor, predictable dimensional changes that must be accounted for.
Typical As-Built Tolerances (L-PBF):
- For smaller features (e.g., < 50 mm): Often in the range of ±0.05 to ±0.15 mm (±0.002 to ±0.006 inches).
- For larger dimensions (e.g., > 100 mm): Typically ±0.1% to ±0.2% of the dimension.
It’s crucial to note that these are general guidelines. Achieving tighter tolerances often requires specific process optimization and may necessitate finish machining on critical surfaces. Tolerances are usually tighter parallel to the build plane than perpendicular to it (Z-axis).
Yüzey İşlemi (Pürüzlülük):
Surface finish is a critical parameter for NGVs, impacting:
- Aerodynamic Performance: Rough surfaces increase friction drag, reducing turbine efficiency. Smooth airfoil surfaces are essential.
- Cooling Efficiency: Surface roughness inside cooling channels significantly affects the heat transfer coefficient and the pressure drop of the cooling air. Optimal cooling design relies on predictable internal surface conditions.
- Fatigue Life: Surface imperfections can act as stress concentrators, potentially initiating fatigue cracks.
Typical As-Built Surface Roughness (Ra):
Surface Orientation | L-PBF (Typical Ra) | EBM (Typical Ra) | Notlar |
---|---|---|---|
Top Surfaces | 5 – 15 $\mu$m | 20 – 40 $\mu$m | Generally smoother |
Vertical Walls (Z-axis) | 8 – 20 $\mu$m | 25 – 50 $\mu$m | Layer lines visible |
Upward-Facing Slopes | 10 – 25 $\mu$m | 30 – 60 $\mu$m | Depends on angle |
Downward-Facing Slopes | 15 – 30+ $\mu$m | 35 – 70+ $\mu$m | Rougher due to support contact or lack thereof |
Supported Surfaces | 20 – 40+ $\mu$m | 40 – 80+ $\mu$m | Roughness depends on support type/density |
Sayfalara Aktar
Note: Ra = Arithmetic Average Roughness. Values are approximate and vary significantly with parameters and material.
For many NGV applications, the ‘as-built’ surface finish, especially from L-PBF, might be acceptable for internal cooling passages, but external airfoil surfaces often require post-processing (e.g., polishing, abrasive flow machining) to achieve the required aerodynamic smoothness (often targeting Ra < 3-5 $\mu$m). Internal channels may also undergo finishing processes if very low friction factors are needed.
Dimensional Accuracy and Verification:
Ensuring the final NGV meets all geometric specifications is paramount. This involves:
- Süreç Kontrolü: Maintaining tight control over all AM parameters (laser power, scan speed, layer thickness, gas flow, powder quality, etc.) is fundamental.
- Metroloji: Comprehensive measurement is required after printing and often after key post-processing steps.
- Coordinate Measuring Machines (CMMs): Used for precise measurement of discrete points, features, and overall dimensions.
- 3D Scanning (Laser or Structured Light): Captures the full geometry of the part, allowing comparison to the original CAD model and assessment of overall form, warp, and surface deviations.
- Computed Tomography (CT) Scanning: Essential for non-destructively verifying the geometry and integrity of internal cooling channels and detecting internal defects like porosity.
- Quality Management Systems: Adherence to rigorous quality standards (e.g., AS9100 for aerospace) ensures traceability, process repeatability, and thorough documentation.
Achieving the required precision for NGVs via AM is a multi-faceted challenge involving design optimization (DfAM), careful selection of AM process and parameters, high-quality equipment like those utilized by Met3dp, and appropriate post-processing and metrology strategies. It requires a deep understanding of the interplay between materials, process physics, and design intent.
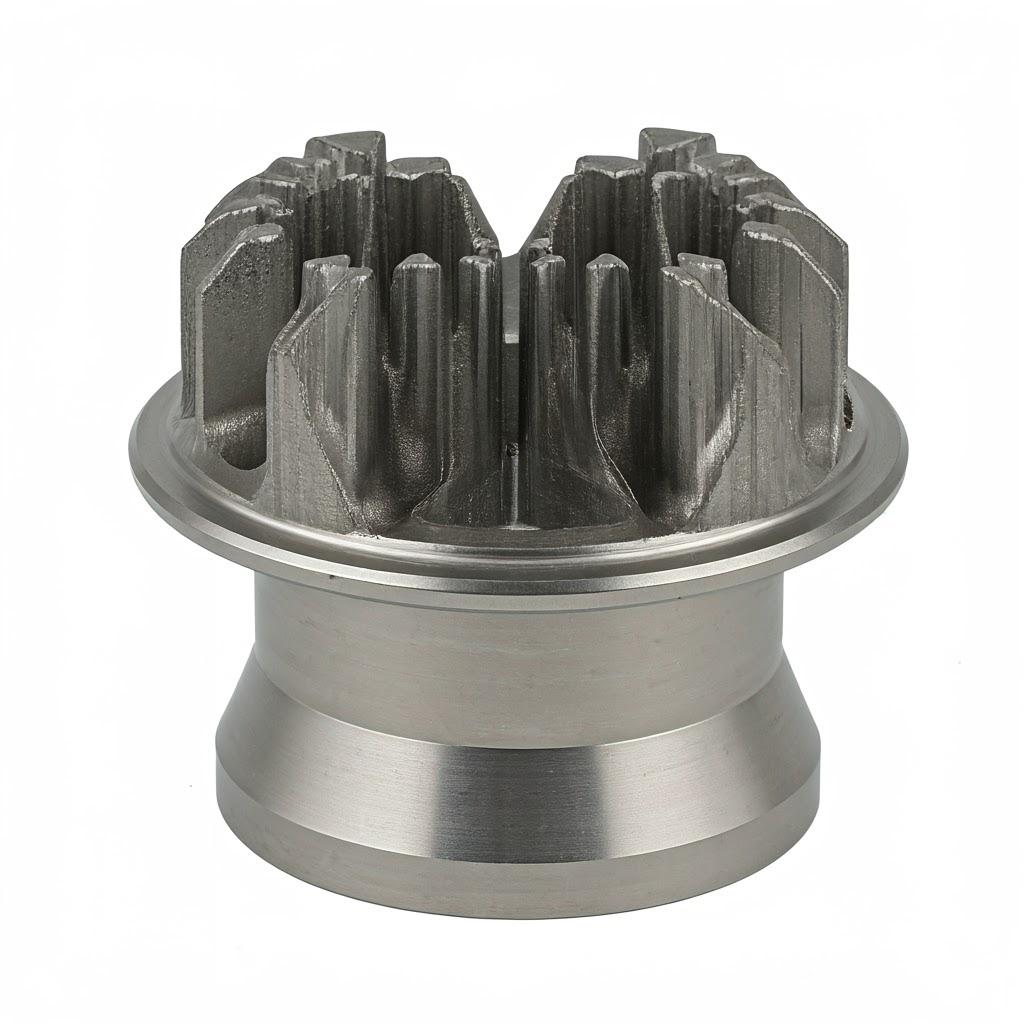
Essential Post-Processing Steps for AM Nozzle Guide Vanes
Producing a Nozzle Guide Vane using metal additive manufacturing is only the first stage of the manufacturing journey. The ‘as-built’ part, fresh off the printer, possesses the desired complex geometry but typically lacks the required material properties, surface finish, and dimensional tolerances for demanding turbine applications. A series of carefully controlled post-processing steps are essential to transform the raw AM part into a flight-worthy or service-ready component. These steps are particularly critical for precipitation-strengthened superalloys like IN738LC and Haynes 282.
Common Post-Processing Workflow for AM NGVs:
- Stress Relief Heat Treatment:
- Amacımız: To alleviate the high residual stresses built up during the rapid heating and cooling cycles of the AM process. These stresses can cause distortion upon removal from the build plate or even lead to cracking.
- Prosedür: Typically performed while the NGV is still attached to the build plate, often in an inert atmosphere (e.g., argon or vacuum) furnace. The temperature and duration depend on the alloy and part geometry but are generally below the aging temperature to avoid altering the microstructure significantly at this stage.
- Yapı Plakasından Çıkarma:
- Amacımız: To separate the printed NGV(s) from the base plate they were built upon.
- Yöntemler: Commonly achieved using wire Electrical Discharge Machining (wire EDM) or abrasive sawing. Care must be taken to avoid damaging the parts.
- Destek Yapısının Kaldırılması:
- Amacımız: To remove the temporary structures that supported overhanging features during the build.
- Yöntemler: This can be a labor-intensive process, often involving manual breaking or cutting, grinding, or CNC machining. Accessing internal supports within complex cooling channels can be particularly challenging and may require specialized techniques or designing the supports for easier removal.
- Sıcak İzostatik Presleme (HIP):
- Amacımız: This is a crucial step for virtually all critical AM superalloy components. HIP closes internal microporosity (gas pores or lack-of-fusion voids) that may be present after printing, significantly improving fatigue life, ductility, and overall material integrity. It also helps to further homogenize the microstructure.
- Prosedür: The parts are subjected to high temperature (below the alloy’s melting point but high enough for creep/diffusion) and high isostatic pressure (using an inert gas like Argon) simultaneously in a specialized HIP vessel. Typical parameters for nickel superalloys might be in the range of 1120−1260∘C (2050−2300∘F) and 100-200 MPa (15-30 ksi) for several hours. Specific cycles depend heavily on the alloy (e.g., IN738LC vs. Haynes 282).
- Solution Annealing and Aging Heat Treatments:
- Amacımız: To develop the desired final microstructure and mechanical properties, primarily by controlling the precipitation of the strengthening gamma prime (γ′) phase.
- Prosedür: This typically involves multiple steps:
- Çözüm Tedavisi: Heating to a high temperature (below the incipient melting point but above the γ′ solvus) to dissolve existing precipitates and homogenize the alloy composition, followed by rapid cooling (quenching).
- Aging Treatment(s): Heating to one or more intermediate temperatures for specific durations to precipitate the fine, strengthening γ′ particles in the desired size and distribution. The exact temperatures and times are critical and specific to the alloy (e.g., standard heat treatments for IN738LC involve solutioning around 1120∘C followed by aging around 845∘C; Haynes 282 often uses higher solution temperatures ~1150∘C and multiple aging steps). These treatments are usually performed in vacuum or inert atmosphere furnaces.
- Machining (CNC):
- Amacımız: To achieve final dimensional accuracy and surface finish on critical features that cannot be adequately produced by AM alone.
- Areas: This commonly includes mounting surfaces (e.g., fir tree roots if applicable, though less common for NGVs, or platform interfaces), mating faces between adjacent vanes, and potentially airfoil surfaces if extremely tight profile tolerances are required. Machining superalloys is challenging due to their high strength and work-hardening tendencies, requiring appropriate tools, speeds, and feeds.
- Yüzey İşlemi:
- Amacımız: To achieve the required aerodynamic smoothness on external surfaces and potentially modify the surface characteristics inside cooling passages.
- Yöntemler:
- Abrasive Blasting/Grit Blasting: Can provide a uniform matte finish and remove minor imperfections.
- Polishing/Lapping: Used for achieving very smooth surfaces (low Ra) on external airfoils.
- Abrasive Flow Machining (AFM) or Electrochemical Polishing (ECP): Can be used to smooth internal cooling passages, reducing friction and improving flow efficiency, though access can be a limitation.
- Coating Application:
- Amacımız: To provide additional protection against the harsh turbine environment.
- Türler:
- Termal Bariyer Kaplamalar (TBC'ler): Ceramic coatings (typically Yttria-Stabilized Zirconia – YSZ) applied to external surfaces to insulate the metal vane from the hot gas stream, allowing for higher gas temperatures or reducing metal temperatures for longer life. Requires a metallic bond coat (often MCrAlY type).
- Environmental Barrier Coatings (EBCs): Sometimes used in conjunction with or instead of TBCs, particularly in environments with high water vapor content or specific corrosive species.
- Yöntemler: Typically applied via plasma spray or electron beam physical vapor deposition (EB-PVD). Surface preparation is critical for coating adherence.
- Inspection and Quality Control (NDT):
- Amacımız: To verify the integrity of the NGV after all processing steps.
- Yöntemler: Includes dimensional checks (CMM, 3D scanning), surface finish measurements, Fluorescent Penetrant Inspection (FPI) for surface-breaking cracks, Ultrasonic Testing (UT), and critically, CT scanning to verify internal channel integrity and check for any remaining internal defects post-HIP.
The entire post-processing chain must be carefully planned and executed. Understanding these steps is crucial for accurately estimating final component cost, lead time, and performance. Companies like Met3dp understand the importance of this integrated approach, offering expertise not just in the initial print but also in the requirements that follow. Exploring different baskı yöntemleri and their associated post-processing needs is key to successful implementation.
Overcoming Challenges in 3D Printing High-Temperature Superalloy NGVs
While metal additive manufacturing unlocks significant potential for Turbine Nozzle Guide Vanes, printing high-performance nickel-based superalloys like IN738LC and Haynes 282 presents a unique set of challenges that must be carefully managed to ensure component quality, reliability, and repeatability. These challenges stem from the inherent physics of rapidly melting and solidifying complex alloys in a layer-wise fashion.
Key Challenges and Mitigation Strategies:
- Çatırdıyor: Superalloys, particularly those with high amounts of γ′ forming elements, can be susceptible to various forms of cracking during or after the AM process.
- Solidification Cracking: Occurs in the melt pool during solidification due to shrinkage strains and the presence of low-melting-point phases or impurities segregating to grain boundaries.
- Hafifletme: Careful control of laser/beam parameters (power, speed, focus), optimizing scan strategies (e.g., island scanning, specific hatch patterns) to manage thermal gradients, using high-purity powders with controlled composition, and selecting alloys with inherently better weldability (like Haynes 282).
- Strain-Age Cracking (Post-Weld Heat Treatment Cracking): Can occur during subsequent heat treatments (stress relief or aging) as residual stresses are relieved and precipitation occurs, particularly in alloys sensitive to specific temperature ranges.
- Hafifletme: Appropriate stress relief cycles immediately after printing, carefully controlled heating and cooling rates during post-processing heat treatments, selecting alloys less prone to this phenomenon (again, Haynes 282 shows advantages here).
- Solidification Cracking: Occurs in the melt pool during solidification due to shrinkage strains and the presence of low-melting-point phases or impurities segregating to grain boundaries.
- Residual Stress and Distortion: The extreme thermal gradients between the molten pool and surrounding solidified material lead to significant internal stresses.
- Effects: Can cause part distortion (warpage) during the build (potentially leading to recoater crashes), cracking, or distortion after removal from the build plate. Residual stresses can also negatively impact fatigue life.
- Hafifletme:
- Süreç Parametreleri: Optimizing scan strategy (e.g., shorter scan vectors, alternating directions), pre-heating the build plate (standard in EBM, possible in some L-PBF systems), using robust support structures.
- Design (DfAM): Designing parts with smoother transitions, avoiding large bulky sections where stress can concentrate.
- İşlem sonrası: Mandatory stress relief heat treatment before removal from the build plate is crucial. HIP also helps relieve residual stresses.
- Gözeneklilik: Small voids within the printed material can act as crack initiation sites and degrade mechanical properties, especially fatigue life.
- Türler: Gas porosity (trapped shielding gas or dissolved gases coming out of solution) and lack-of-fusion porosity (insufficient melting between layers or scan tracks).
- Hafifletme:
- Süreç Optimizasyonu: Fine-tuning energy density (laser/beam power, speed, hatch spacing) to ensure complete melting and fusion, controlling shielding gas flow and quality.
- Toz Kalitesi: Using high-quality, spherical powder with low internal porosity and controlled moisture content. Sourcing from reputable suppliers like Met3dp ensures consistent powder characteristics.
- İşlem sonrası: Hot Isostatic Pressing (HIP) is extremely effective at closing both gas and lack-of-fusion pores, significantly improving material density and mechanical integrity.
- Microstructure Control: Achieving the desired fine-grained, homogeneous microstructure with optimally distributed strengthening precipitates (γ′) is critical for performance but challenging due to the rapid solidification inherent in AM.
- Zorluklar: Can lead to columnar grain growth (anisotropic properties), elemental segregation, and non-optimal precipitate size/distribution in the as-built state.
- Hafifletme: Careful control of printing parameters, specific scan strategies to influence grain structure, and, most importantly, tailored post-processing heat treatments (solutioning, aging) designed specifically for AM microstructures, often involving homogenization steps and HIP.
- Support Structure Removal (Internal): Removing supports from within complex, narrow internal cooling channels without damaging the passage walls is difficult and time-consuming.
- Hafifletme: DfAM plays a key role – designing channels to be self-supporting where possible, optimizing support geometry for easier access and fracture, incorporating washout ports, and considering post-processing methods like abrasive flow machining (AFM) or chemical etching designed to smooth internal surfaces and potentially remove support remnants. Thorough inspection (e.g., CT scanning) is needed to verify complete removal.
- Powder Removal (Internal): Ensuring all unfused powder is removed from intricate internal passages after the build is critical for cooling effectiveness. Trapped powder can block channels or sinter during heat treatment.
- Hafifletme: Designing channels with sufficient diameters and smooth paths to facilitate powder removal via vibration and inert gas blow-out. Incorporating specific drain holes or access points. Using CT scanning for verification is often necessary.
- Non-Destructive Testing (NDT) and Inspection: The complex geometries enabled by AM, particularly internal features, make thorough inspection challenging. Standard NDT methods may need adaptation.
- Zorluklar: Detecting small internal flaws, verifying internal channel dimensions and wall thicknesses, assessing surface finish inside channels.
- Hafifletme: Heavy reliance on CT scanning for internal geometry and defect detection. Advanced ultrasonic techniques may be adapted. Robust process monitoring and control during the build are also key components of quality assurance, reducing the likelihood of defects forming in the first place.
Overcoming these challenges requires deep expertise in materials science, AM process physics, thermal engineering, and rigorous quality control methodologies. Partnering with an experienced AM service provider like Met3dp, which combines advanced equipment with in-depth knowledge of processing demanding materials like IN738LC and Haynes 282, is essential for successfully manufacturing high-quality, reliable NGVs for critical applications.
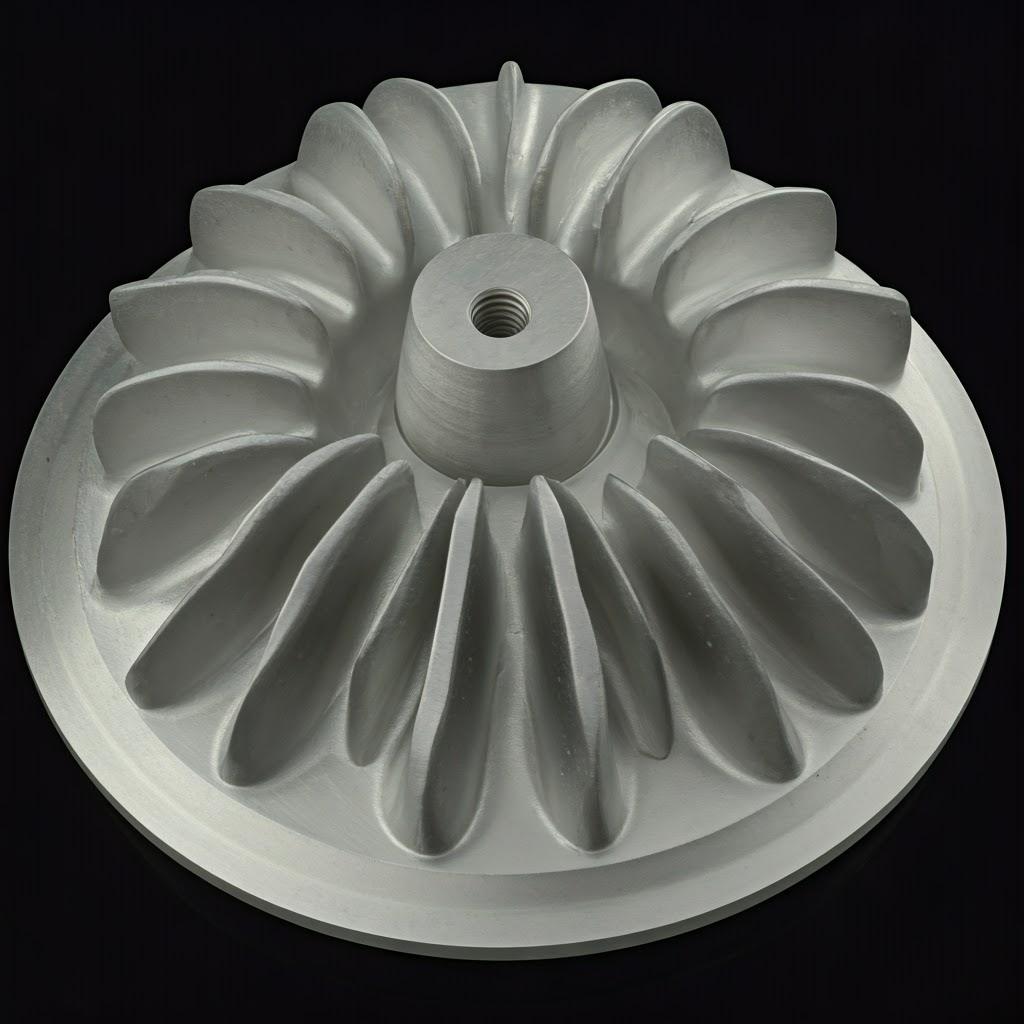
Selecting Your Partner: How to Choose the Right Metal AM Service Provider for NGVs
Manufacturing mission-critical components like Turbine Nozzle Guide Vanes (NGVs) using additive manufacturing demands more than just access to a 3D printer. The complexity of the component, the challenging nature of superalloys like IN738LC and Haynes 282, and the stringent quality requirements necessitate partnering with a highly capable and experienced metal AM service provider. Selecting the right partner is crucial for mitigating risks, ensuring component performance, and achieving successful project outcomes. Procurement managers and engineering teams should evaluate potential suppliers based on a comprehensive set of criteria:
- Proven Expertise with Superalloys and Turbine Components:
- Track Record: Does the provider have demonstrable experience printing IN738LC, Haynes 282, or comparable nickel-based superalloys? Can they share case studies or examples (within confidentiality limits) of similar complex, high-temperature components they have produced, ideally within the aerospace or power generation sectors?
- Metallurgical Knowledge: Do they possess in-house materials science expertise relevant to superalloy metallurgy, phase transformations during AM and heat treatment, and defect mitigation?
- Appropriate Technology and Equipment:
- AM Systems: Do they operate well-maintained, industrial-grade Laser Powder Bed Fusion (L-PBF) or Electron Beam Melting (EBM) systems suitable for reactive superalloys? Are the machines equipped with necessary process monitoring capabilities?
- End-to-End Capabilities: Does the provider offer, either in-house or through qualified partners, the full suite of necessary post-processing capabilities? This includes stress relief, HIP (Hot Isostatic Pressing), vacuum/inert atmosphere heat treatment furnaces capable of precise superalloy cycles, multi-axis CNC machining, advanced surface finishing techniques, and NDT labs. A vertically integrated provider often offers better control and potentially shorter lead times.
- Robust Quality Management System (QMS) and Certifications:
- Sertifikalar: Is the provider certified to relevant industry standards? AS9100 is the benchmark for aerospace manufacturing, demonstrating a commitment to rigorous quality control, traceability, and risk management. ISO 9001 is a fundamental requirement.
- Süreç Kontrolü: Do they have documented procedures for every step, from powder handling and machine setup to post-processing and inspection? How do they ensure process repeatability and consistency?
- Traceability: Can they provide full material and process traceability for each NGV produced?
- Material Management and Expertise:
- Toz İşleme: Superalloy powders require careful handling in controlled environments to prevent contamination and moisture pickup. What are their procedures for powder storage, handling, sieving, and testing (e.g., chemistry, Particle Size Distribution – PSD, flowability)?
- Powder Sourcing/Production: Do they source powder from reputable, qualified suppliers, or do they have in-house powder production capabilities? Companies like Met3dp, for instance, leverage advanced atomization techniques (Gas Atomization, PREP) to manufacture high-quality spherical metal powders optimized for AM, including superalloys. This in-house capability provides greater control over powder quality and potentially tailored solutions. Understanding a provider’s material foundation is critical. You can learn more about Met3dp’s comprehensive approach and expertise on their Hakkımızda sayfası.
- Malzeme Yeterliliği: Do they have experience qualifying AM materials and processes to specific customer or industry standards?
- Engineering and Design Support (DfAM):
- Collaboration: Does the provider offer Design for Additive Manufacturing (DfAM) support? Can their engineers collaborate with your team to optimize the NGV design for printability, performance (especially cooling), and cost-effectiveness?
- Simulation: Do they utilize simulation tools for predicting thermal behavior, residual stress, and printability issues?
- Inspection and Non-Destructive Testing (NDT) Capabilities:
- In-house NDT: Given the criticality of NGVs and the complexity of AM parts, in-house NDT capabilities are highly advantageous. This should ideally include Fluorescent Penetrant Inspection (FPI), Ultrasonic Testing (UT), and critically, high-resolution Computed Tomography (CT) scanning for verifying internal features and detecting internal defects.
- Metroloji: Do they have calibrated CMMs and 3D scanning equipment to perform thorough dimensional verification against the CAD model and technical drawings?
- Capacity, Scalability, and Lead Time Reliability:
- Üretim Hacmi: Can the provider handle your required production volumes, from prototypes to potential serial production?
- Lead Time Commitment: Can they provide realistic and reliable lead time estimates, considering the entire workflow including post-processing queues? What is their track record for on-time delivery?
- B2B Focus and Partnership Approach:
- Tedarikçi Güvenilirliği: Do they understand the procurement requirements of industrial and aerospace sectors? Are they financially stable and positioned as a long-term partner?
- Communication: Is communication clear, responsive, and technically competent?
Choosing an AM partner for NGVs is a strategic decision. It requires thorough due diligence beyond just comparing price quotes. The provider’s technical depth, quality systems, and demonstrated experience with similar demanding applications are paramount to ensuring the delivery of reliable, high-performance components.
Understanding Cost Drivers and Lead Times for Additively Manufactured NGVs
While additive manufacturing offers significant performance and design advantages for Nozzle Guide Vanes, it’s essential for procurement managers and engineers to understand the factors that influence the cost and manufacturing lead time of these components. Comparing AM costs directly to traditional casting requires a nuanced approach, often involving a total lifecycle cost perspective that accounts for potential performance gains.
Key Cost Drivers for AM NGVs:
- Raw Material Cost:
- Nickel-based superalloys like IN738LC and Haynes 282 are inherently expensive materials. The cost of high-quality, AM-grade spherical powder is a primary driver.
- Powder recyclability impacts overall cost; efficient sieving and reuse of unfused powder are crucial, but require quality control to prevent degradation.
- AM Machine Time:
- This includes the actual time spent printing the NGV layer by layer, which depends on the part volume, height (number of layers), complexity, and how many parts can be nested onto a single build plate.
- Machine amortization, operational costs (power, inert gas, consumables), and maintenance also contribute.
- İşçilik Maliyetleri:
- Skilled labor is required for machine setup, build monitoring, part removal, extensive support structure removal (often manual), and various post-processing tasks. Labor associated with quality assurance and documentation is also significant.
- İşlem Sonrası Maliyetler: These can represent a substantial portion of the total cost:
- Stres Giderici: Furnace time and energy consumption.
- HIP: Access to HIP units is specialized and costly; the process involves long cycles at high temperature and pressure.
- Isıl İşlem: Complex multi-step solution and aging cycles require precise furnace control (vacuum or inert atmosphere) and long durations.
- İşleme: CNC machining of superalloys is slow and tool-intensive due to material hardness and work hardening. The extent of machining required significantly impacts cost.
- Yüzey İşlemi: Techniques like polishing or AFM add cost based on labor, consumables, and equipment time.
- Kaplama: TBC/EBC application involves specialized equipment and materials.
- Quality Assurance and Inspection:
- Rigorous NDT, particularly CT scanning for internal validation, adds considerable cost.
- Dimensional inspection (CMM, scanning) and documentation required for aerospace/industrial components take time and resources.
- Design Complexity and Support Volume:
- Highly intricate cooling channels or complex external geometries may increase print time slightly but can significantly increase the difficulty (and thus cost) of support removal and inspection.
- The volume of support material required also adds to print time and material consumption (though supports are often made of the same material and recycled).
- Sipariş Hacmi:
- Significant economies of scale can be achieved with larger batch sizes due to optimized nesting on build plates, spreading setup costs, and more efficient post-processing workflows. Prototype costs per part are typically much higher than serial production costs.
Lead Time Factors for AM NGVs:
Lead time is the total duration from order placement to final part delivery. For AM NGVs, it comprises several stages:
- Pre-Processing: File preparation, DfAM review (if needed), build simulation, support generation, and build plate nesting (Can range from hours to days).
- Baskı Süresi: The actual time the part spends in the AM machine. Depending on size, complexity, and nesting, this can range from 2-3 days to over a week for large NGV segments.
- Post-Processing Queue & Cycle Times: This is often the most significant portion of the lead time.
- Wait times for stress relief, HIP (often batched), heat treatment furnaces, and CNC machining centers can add days or weeks.
- The duration of each post-processing step itself (e.g., HIP cycles are hours, heat treatments can be 10-24+ hours per step, machining takes hours).
- Support removal and finishing add manual labor time.
- Inspection Time: Thorough NDT and dimensional inspection require dedicated time slots and analysis.
Typical Lead Times:
- Prototipler: Depending on complexity and post-processing requirements, prototype AM NGVs might be delivered in 3-8 weeks.
- Serial Production: For established processes, lead times might stabilize, but the inherent complexity of the post-processing chain means they are still typically measured in weeks or months, though often significantly faster than the 6-18+ months often required for developing new investment casting tooling and initial production runs.
Comparison to Casting: While the per-part cost of AM NGVs may sometimes be higher than mature casting processes (especially for simpler designs or very high volumes), the calculus changes when considering:
- Kalıp Maliyetleri: AM avoids the extremely high cost and long lead time associated with creating complex casting molds and cores.
- Kurşun zamanı: AM offers much faster turnaround for prototypes, design iterations, and potentially initial production batches or spare parts.
- Performance Benefits: The enhanced cooling and aerodynamic efficiency achievable with AM can translate into significant lifecycle savings through improved fuel efficiency, increased power output, or longer component life, often justifying a higher initial part cost.
Understanding these cost and lead time dynamics allows for informed decisions when considering AM for NGV production, balancing upfront investment against downstream performance gains and supply chain agility.
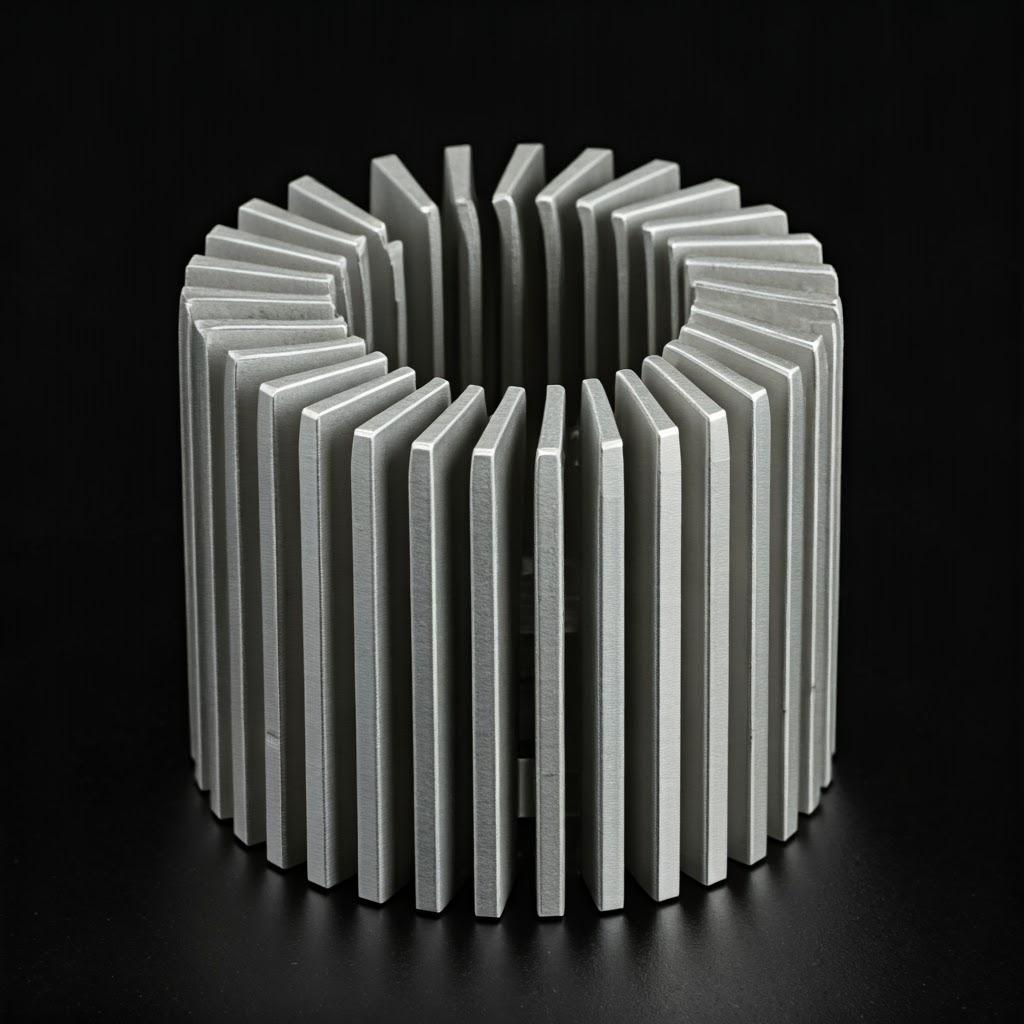
Frequently Asked Questions (FAQ) about 3D Printed NGVs
Q1: Can additively manufactured NGVs truly match or exceed the mechanical properties of traditionally cast NGVs?
A: Yes, with appropriate process control, high-quality powder, and optimized post-processing (including mandatory HIP and tailored heat treatments), AM NGVs made from superalloys like IN738LC or Haynes 282 can achieve mechanical properties (tensile strength, creep resistance, fatigue life) that meet or even exceed those of their cast counterparts. The finer grain structure often resulting from AM can enhance fatigue properties, while HIP effectively eliminates internal porosity common in castings. However, achieving these properties requires rigorous process qualification and validation specific to the AM process, material, and component geometry, often mandated by aerospace and industrial standards. Properties can also be more isotropic (uniform in different directions) compared to the sometimes columnar grain structures in investment castings.
Q2: How complex can the internal cooling channels really be when 3D printing NGVs?
A: Metal AM enables significantly greater complexity in internal cooling channel design compared to investment casting. This includes:
- Conformal Channels: Passages that closely follow the airfoil’s external shape for uniform cooling.
- Karmaşık Geometriler: Serpentine paths with tight bends, varying cross-sections, and sophisticated internal features like trip strips or turbulators to enhance heat transfer.
- Fine Features: Integration of delicate structures like lattice networks or dense pin-fin arrays for highly efficient localized cooling (e.g., in the trailing edge).
- Optimized Outlets: Direct printing of shaped film cooling holes for better aerodynamic performance of the cooling film. The practical limit is determined by factors like minimum printable feature size, powder removal constraints, support structure requirements and removal access, and the ability to non-destructively inspect the final channels (typically via CT scanning).
Q3: Is 3D printing NGVs a cost-effective alternative to investment casting?
A: The cost-effectiveness depends heavily on several factors:
- Karmaşıklık: For NGVs with highly complex internal cooling designs required for top-tier performance, AM can be more cost-effective than trying to achieve similar complexity via intricate (and fragile) ceramic cores in casting.
- Hacim: For very high production volumes of established, simpler designs, investment casting often maintains a lower per-part cost due to mature processes and amortization of tooling. However, for low-to-medium volumes, prototypes, or spare parts (where tooling may not exist), AM avoids the massive upfront tooling costs and long lead times of casting, making it economically viable.
- Lifecycle Value: The performance benefits enabled by AM (e.g., improved fuel efficiency due to better cooling allowing higher temperatures, longer component life) can result in significant operational savings over the engine’s life, often outweighing a potentially higher initial component cost. A thorough cost-benefit analysis considering tooling, lead time, volume, complexity, and lifecycle performance impact is needed for each specific case.
Q4: What non-destructive testing (NDT) methods are essential for ensuring the quality of AM NGVs?
A: Given the critical application and complex geometry (especially internal), a multi-faceted NDT approach is typically required:
- Computed Tomography (CT) Scanning: This is arguably the most crucial method for AM NGVs. It allows detailed, non-destructive visualization and measurement of internal cooling channels (checking for blockages, wall thickness variations, overall geometry conformance) and detection of internal defects like porosity or lack of fusion that may remain even after HIP.
- Fluorescent Penetrant Inspection (FPI): Used to detect surface-breaking cracks or porosity.
- Dimensional Metrology: CMM and 3D scanning are used to verify external dimensions, airfoil profiles, and feature locations against the specification.
- Ultrasonic Testing (UT): Can be adapted for detecting subsurface flaws, although complex geometries can make interpretation challenging.
- Eddy Current Testing: May be used for detecting surface or near-surface flaws and material sorting. The specific NDT requirements are typically defined by industry standards (e.g., aerospace) and customer specifications.
Conclusion: The Future of High-Performance NGVs is Additive
The relentless pursuit of higher efficiency, reduced emissions, and improved durability in gas turbines necessitates continuous innovation in critical hot section components. Turbine Nozzle Guide Vanes, operating at the harsh interface between combustor and turbine rotor, are prime candidates for leveraging the transformative capabilities of metal additive manufacturing. As we’ve explored, AM techniques like L-PBF and EBM, when applied to advanced superalloys such as IN738LC and Haynes 282, offer compelling advantages over traditional manufacturing methods.
The ability to realize unprecedented geometric complexityözellikle de internal cooling architectures, allows engineers to design NGVs that enable higher turbine operating temperatures, directly translating to significant gains in thermal efficiency and power output. The tasarım özgürlüğü afforded by AM facilitates optimized aerodynamic profiles, thinner trailing edges, and the potential for parça konsoli̇dasyonu, streamlining assembly and potentially enhancing structural integrity. Furthermore, the capacity for rapid prototyping and design iteration dramatically accelerates development cycles, bringing next-generation turbine technology to market faster.
However, successfully manufacturing high-quality, reliable NGVs via AM requires navigating distinct challenges. Careful malzeme seçimi, adherence to rigorous Katmanlı Üretim Tasarımı (DfAM) principles, meticulous process control, comprehensive post-processing (including essential steps like HIP and tailored heat treatments), and thorough non-destructive testing are all non-negotiable elements for success.
Choosing the right manufacturing partner – one with deep expertise in superalloys, robust quality systems, advanced equipment, and end-to-end capabilities – is paramount. Companies like Met3dp stand at the forefront of this technological shift, offering not only industry-leading metal AM printers and high-quality, specialized metal powders produced in-house but also the crucial application development support needed to turn complex designs into functional, high-performance components. Their integrated approach ensures that the full potential of additive manufacturing can be harnessed for demanding applications like NGVs.
The journey towards widespread adoption of AM for critical rotating and static turbine components is well underway. For engineers and procurement managers in the aerospace, power generation, and industrial sectors, embracing metal additive manufacturing for NGVs is no longer just an option; it is increasingly becoming a strategic imperative for achieving competitive advantage and developing the high-performance, sustainable energy systems of the future.
Ready to explore how additive manufacturing can revolutionize your turbine components? Visit Met3dp to learn more about our advanced metal powders, printing systems, and comprehensive AM solutions.
Paylaş
MET3DP Technology Co, LTD, merkezi Qingdao, Çin'de bulunan lider bir katmanlı üretim çözümleri sağlayıcısıdır. Şirketimiz, endüstriyel uygulamalar için 3D baskı ekipmanları ve yüksek performanslı metal tozları konusunda uzmanlaşmıştır.
İşletmeniz için en iyi fiyatı ve özelleştirilmiş Çözümü almak için sorgulayın!
İlgili Makaleler
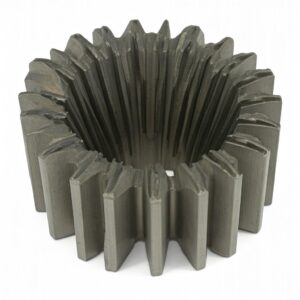
Yüksek Performanslı Nozul Kanat Segmentleri: Metal 3D Baskı ile Türbin Verimliliğinde Devrim
Daha Fazla Oku "Met3DP Hakkında
Son Güncelleme
Bizim Ürünümüz
BİZE ULAŞIN
Herhangi bir sorunuz var mı? Bize şimdi mesaj gönderin! Mesajınızı aldıktan sonra tüm ekibimizle talebinize hizmet edeceğiz.
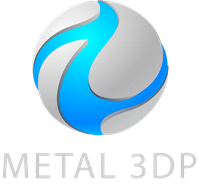
3D Baskı ve Katmanlı Üretim için Metal Tozları