3D Printed High-Load Robot Links
İçindekiler
Introduction to High-Strength Robot Links via Metal 3D Printing
In the ever-evolving landscape of industrial automation, the demand for robust, lightweight, and precisely engineered components is paramount. Robot links, the structural elements connecting a robot’s joints and enabling its movement, are critical for performance and reliability. Traditionally manufactured through subtractive methods, these crucial parts are now undergoing a revolution with the advent of metal 3D printing, also known as metal additive manufacturing. This innovative technology allows for the creation of complex geometries with enhanced material properties, opening up new possibilities for high-strength robot links across various industries. At Metal3DP, we are at the forefront of this transformation, providing cutting-edge 3D baskı equipment and high-performance metal powders to meet the demanding requirements of modern robotics. Our industry-leading print volume, accuracy, and reliability ensure that mission-critical robot links can be produced with unparalleled quality.
Applications of 3D Printed Robot Links in Modern Robotics
The versatility of metal 3D printing has broadened the application scope of high-strength robot links across a multitude of sectors.
- Havacılık ve uzay: In aerospace manufacturing, lightweight yet strong robotic arms are essential for assembly, inspection, and maintenance tasks within confined spaces. 3D printed robot links made from materials like M300 offer the high strength-to-weight ratio required for such demanding applications.
- Otomotiv: The automotive industry utilizes robots extensively in assembly lines for welding, painting, and material handling. 3D printed robot links enable the design of lighter and more efficient robotic arms, leading to increased productivity and reduced energy consumption.
- Tıbbi: In the medical field, precision and hygiene are critical. Robots with 3D printed links are used in surgical procedures, rehabilitation, and laboratory automation. The ability to customize designs and use biocompatible materials like certain stainless steels available at Metal3DP makes metal 3D printing an ideal choice.
- Endüstriyel Üretim: Across various industrial applications, from food processing to heavy machinery, robots perform repetitive and often strenuous tasks. High-strength robot links produced via 3D printing enhance the durability and longevity of these robots, ensuring consistent performance in demanding environments.
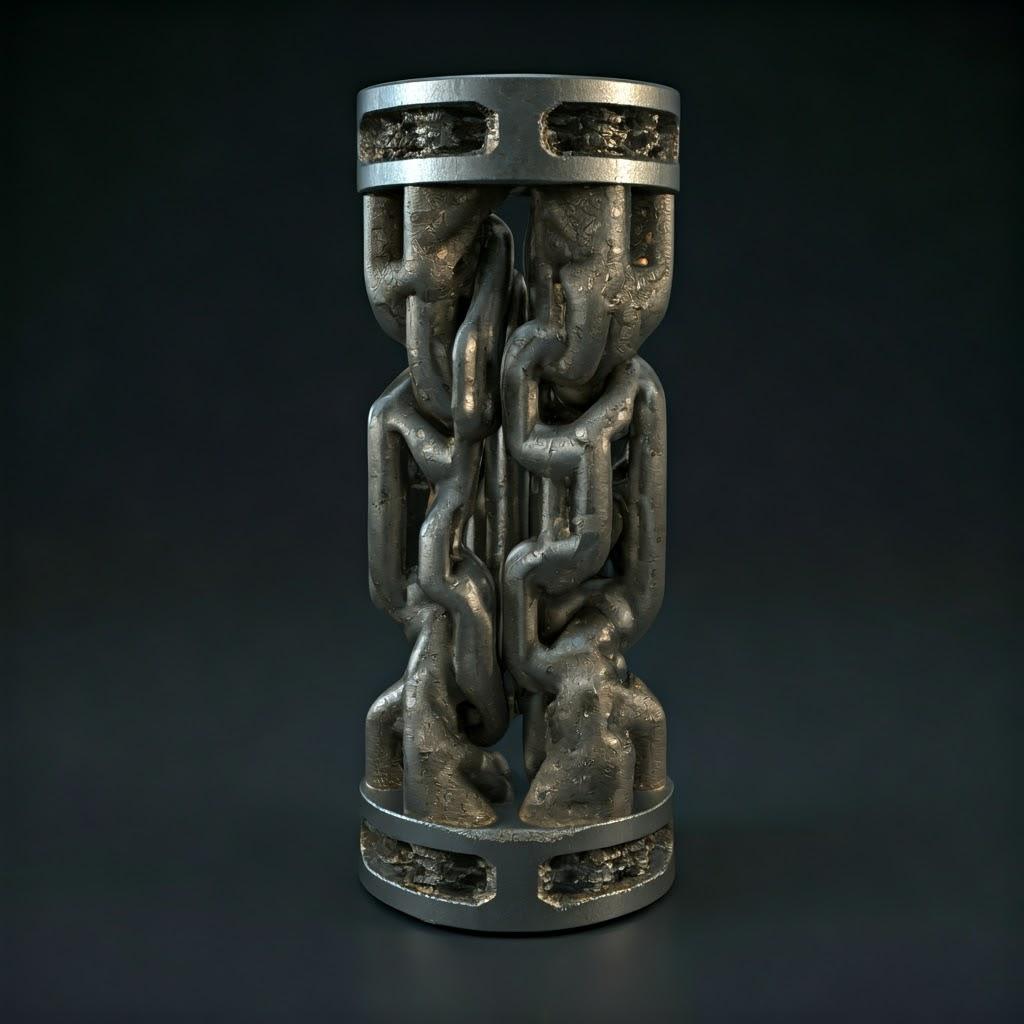
Advantages of Metal Additive Manufacturing for Robot Link Production
Opting for metal 3D printing over traditional manufacturing methods for robot links presents several compelling advantages:
- Tasarım Özgürlüğü ve Karmaşıklık: Additive manufacturing allows for the creation of intricate geometries that are simply not achievable with conventional techniques. This enables the optimization of robot link designs for weight reduction, improved stiffness, and integrated functionalities.
- Hafifletme: Materials like M300 and 1.2709, when processed through metal 3D printing, can result in lighter parts without compromising strength. This is crucial for robotic arms, as reduced weight translates to lower inertia, faster movements, and reduced energy consumption.
- Customization and Rapid Prototyping: Metal 3D printing facilitates the rapid production of custom robot links tailored to specific application requirements. This agility is invaluable for prototyping and low-volume production runs.
- Malzeme Verimliliği: Additive manufacturing minimizes material waste compared to subtractive methods, where significant amounts of material are removed to achieve the final shape. This leads to cost savings and a more sustainable manufacturing process.
- Geliştirilmiş Performans: The layer-by-layer manufacturing process in metal 3D printing can result in parts with superior mechanical properties, such as increased strength and fatigue resistance, essential for high-load robot links. Metal3DP’nin advanced powder making system ensures the production of high-quality metal powders that contribute to these enhanced properties.
Material Selection: Why M300 and 1.2709 Excel in High-Load Applications
The choice of metal powder is paramount in determining the final properties and performance of 3D printed robot links. M300 and 1.2709 are two exceptional materials renowned for their suitability in high-load applications:
M300 (Maraging Steel):
Mülkiyet | Açıklama | Benefits for Robot Links |
---|---|---|
Kimyasal Bileşim | Typically a nickel-cobalt-molybdenum steel with low carbon content. | High strength and toughness after heat treatment. |
Sertlik | Can achieve very high hardness levels (up to 55 HRC) after aging. | Excellent wear resistance and ability to withstand high loads without deformation. |
Çekme Dayanımı | Exhibits exceptional tensile strength (over 2000 MPa after heat treatment). | Ensures the robot link can withstand significant forces and stresses during operation. |
İşlenebilirlik | Relatively easy to machine in the annealed state before heat treatment, allowing for precise post-processing if required. | Facilitates achieving tight tolerances and smooth surface finishes. |
Uygulamalar | Widely used in aerospace tooling, high-performance automotive components, and injection molding. Its properties make it ideal for demanding structural applications like robot links. | Proven track record in high-stress environments, ensuring reliability and longevity of the robot. |
Sayfalara Aktar
1.2709 (Maraging Steel):
Mülkiyet | Açıklama | Benefits for Robot Links |
---|---|---|
Kimyasal Bileşim | Similar to M300, it’s a high-strength steel alloyed with nickel, cobalt, and molybdenum. | Offers a good balance of strength and ductility. |
Sertlik | Achieves high hardness (typically 50-54 HRC) after heat treatment. | Provides excellent resistance to wear and indentation. |
Çekme Dayanımı | Demonstrates high tensile strength (typically 1900-2100 MPa after heat treatment). | Enables the production of robot links capable of handling substantial loads. |
Kaynaklanabilirlik | Exhibits good weldability, which can be beneficial for certain assembly or repair scenarios, although 3D printed parts often minimize the need for welding. | Offers flexibility in manufacturing and potential for integration with other components. |
Uygulamalar | Commonly used in aerospace, motorsport, and tooling industries where high strength and toughness are critical. Its suitability extends to high-performance robot links. | Reliable performance in demanding applications, contributing to the overall efficiency and lifespan of the robotic system. |
Sayfalara Aktar
Metal3DP offers both M300 and 1.2709 high-quality metal powders, processed using advanced gas atomization and PREP technologies to ensure high sphericity and flowability, which are crucial for optimal 3D printing results.
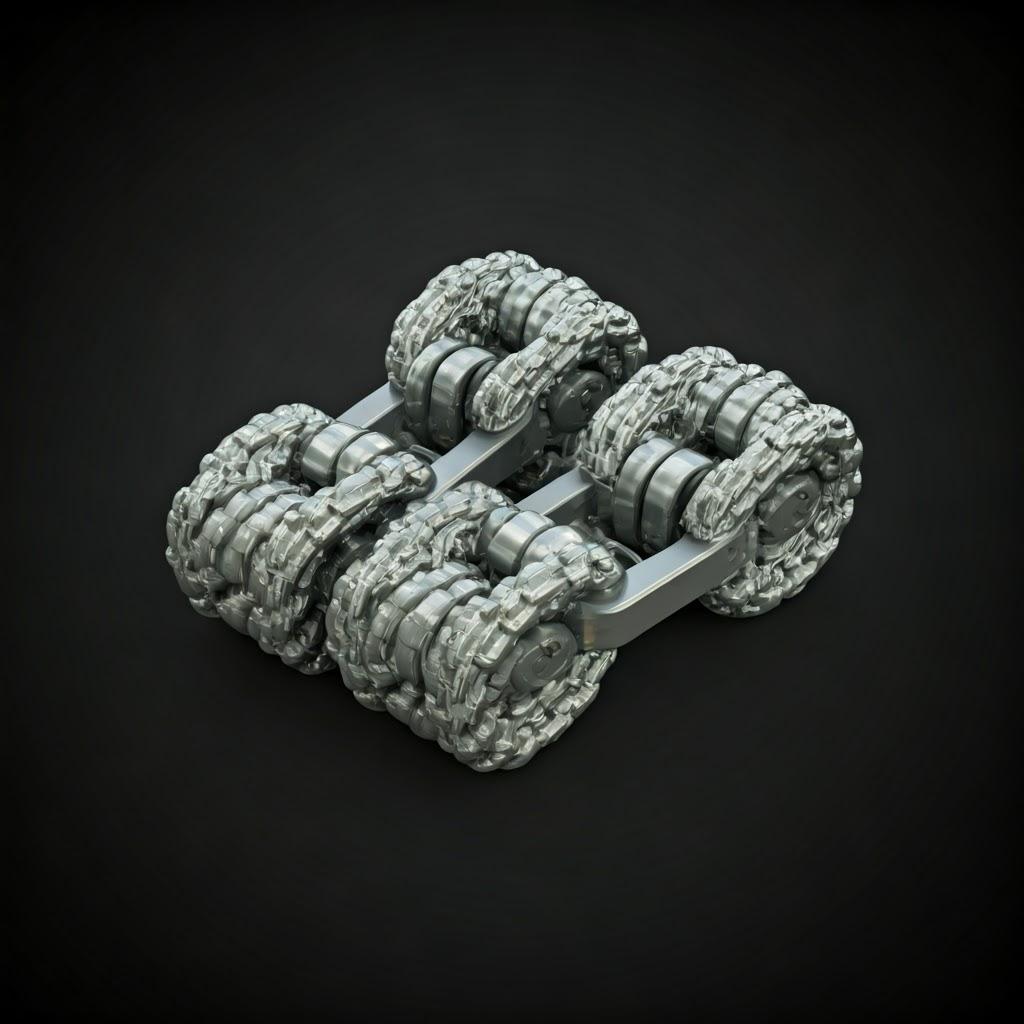
Design Optimization for 3D Printed High-Performance Robot Links
Designing robot links for metal 3D printing requires a different mindset compared to traditional manufacturing. To fully leverage the capabilities of additive manufacturing and achieve optimal performance, several design considerations are crucial:
- Topology Optimization: This computational method allows for the removal of material in non-critical areas while maintaining structural integrity. By analyzing the load paths, designers can create lightweight yet strong robot links with organic, optimized geometries that would be impossible to manufacture using conventional methods.
- Kafes Yapılar: Incorporating lattice structures within the robot link’s interior can significantly reduce weight without sacrificing stiffness. These intricate, repeating patterns provide excellent strength-to-weight ratios and can be tailored to specific load requirements.
- Integration of Features: Metal 3D printing enables the integration of multiple functionalities into a single part. For robot links, this could include integrated cooling channels, cable routing pathways, or mounting features, reducing the need for additional components and assembly steps.
- Orientation and Support Structures: The orientation of the part during the printing process significantly impacts surface finish, support requirements, and mechanical properties. Careful consideration of the build orientation and the strategic placement of support structures are essential to minimize material usage, reduce post-processing effort, and ensure dimensional accuracy.
- Wall Thickness and Ribs: Optimizing wall thickness and incorporating reinforcing ribs can enhance the stiffness and strength of the robot link while keeping weight to a minimum. The minimum achievable wall thickness depends on the chosen metal powder and the capabilities of the 3D printer. Metal3DP’nin expertise in Selective Electron Beam Melting (SEBM) and Laser Powder Bed Fusion (LPBF) ensures that complex geometries with optimized wall thicknesses can be produced with high precision.
Achieving Precision: Tolerance, Surface Finish, and Dimensional Accuracy in 3D Printed Robot Links
For high-performance robot links, dimensional accuracy and surface finish are critical to ensure proper fit, functionality, and longevity. Metal 3D printing technologies have made significant strides in achieving tight tolerances and improved surface finishes:
- Tolerance: The achievable tolerance in metal 3D printing depends on factors such as the printing technology, material, part geometry, and post-processing. Typically, tolerances of ±0.1 to ±0.05 mm can be achieved. For critical dimensions, post-processing techniques like CNC machining can further improve accuracy to within a few micrometers.
- Yüzey İşlemi: The as-printed surface finish in metal 3D printing is generally rougher compared to machined surfaces. The surface roughness (Ra) typically ranges from 5 to 20 μm, depending on the printing parameters and powder particle size. For applications requiring smoother surfaces, post-processing methods such as polishing, grinding, or shot peening can be employed.
- Boyutsal Doğruluk: Dimensional accuracy refers to the ability of the 3D printed part to match the intended design dimensions. Factors affecting accuracy include material shrinkage during solidification, thermal gradients, and machine calibration. At Metal3DP, our state-of-the-art SEBM printers are known for their high accuracy and reliability, minimizing deviations from the intended design.
Parametre | Typical Range in Metal 3D Printing | Factors Influencing | Improvement Methods | Relevance to Robot Links |
---|---|---|---|---|
Hoşgörü | ±0.1 to ±0.05 mm | Technology, material, geometry, machine calibration | Precision machining, careful process control | Ensures proper assembly and functionality of the robotic arm. |
Yüzey Pürüzlülüğü (Ra) | 5 to 20 μm | Powder size, layer thickness, build orientation | Polishing, grinding, shot peening, chemical etching | Reduces friction, improves wear resistance, and can enhance fatigue life. |
Boyutsal Doğruluk | Varies with part size and complexity | Material shrinkage, thermal gradients, calibration | Optimized build parameters, post-processing inspection | Guarantees that the robot link fits correctly with other components and performs as intended. |
Sayfalara Aktar
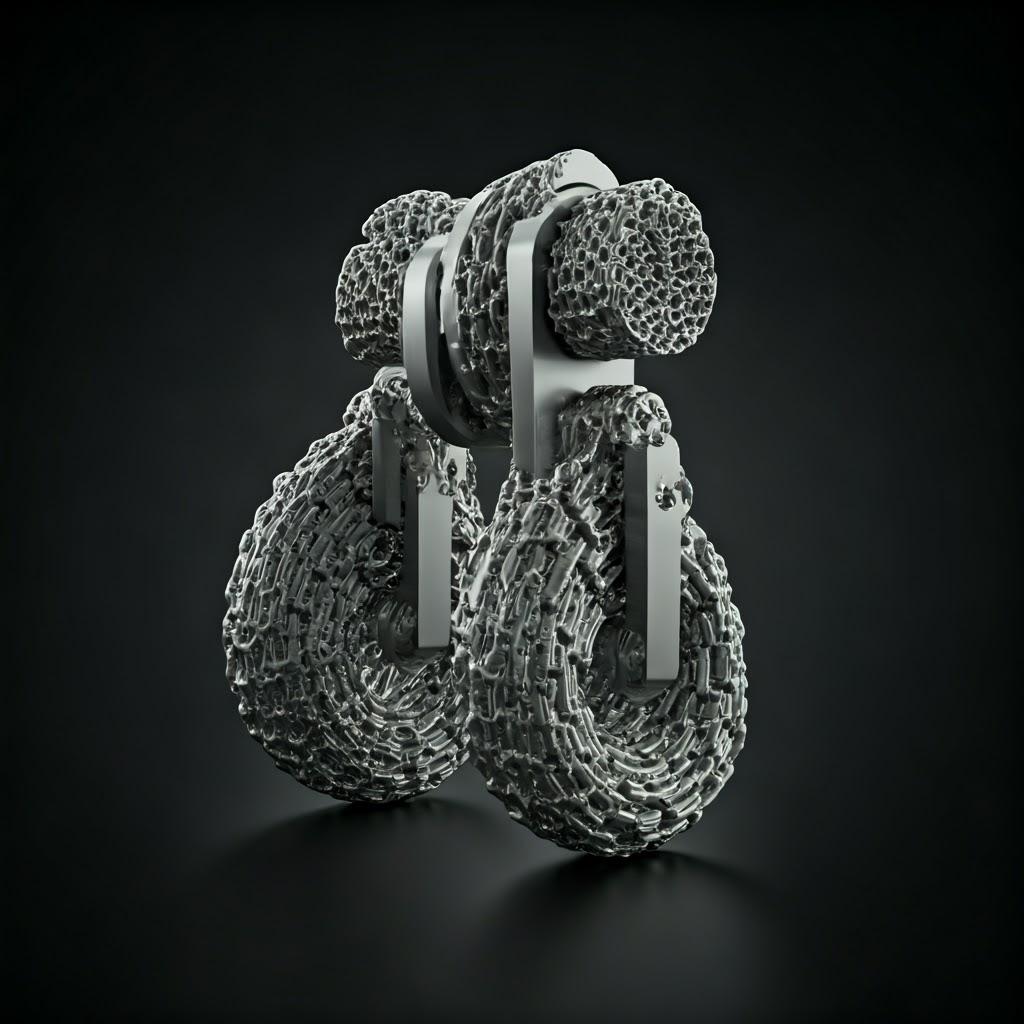
Essential Post-Processing for Durable 3D Printed Robot Links
While metal 3D printing offers significant advantages, post-processing steps are often necessary to achieve the desired mechanical properties, surface finish, and dimensional accuracy for robot links:
- Destek Kaldırma: Support structures are often required during the printing process to prevent warping and ensure proper geometry. These supports need to be carefully removed after printing, which can be a manual or automated process depending on the complexity of the part and the support material.
- Isıl İşlem: Heat treatment is crucial for achieving the desired mechanical properties of materials like M300 and 1.2709. Processes such as stress relieving, hardening, and aging are performed to optimize strength, hardness, and toughness.
- Yüzey İşlemi: As mentioned earlier, various surface finishing techniques can be employed to improve the surface roughness of 3D printed robot links. These include polishing, grinding, abrasive flow machining, and shot peening.
- CNC İşleme: For critical dimensions and features requiring very tight tolerances, CNC machining can be used as a secondary process after 3D printing. This hybrid approach combines the design freedom of additive manufacturing with the precision of subtractive manufacturing.
- Kaplama: Depending on the application environment, coatings may be applied to enhance corrosion resistance, wear resistance, or other specific properties of the robot link. Common coatings include hard chrome plating, anodizing, and powder coating.
Overcoming Challenges in Metal 3D Printing of Robot Links
While metal 3D printing offers numerous benefits, it also presents certain challenges that need to be addressed to ensure successful production of high-quality robot links:
- Çarpıtma ve Bozulma: Thermal stresses during the printing process can lead to warping and distortion, particularly in large or complex parts. Optimizing build orientation, using support structures, and controlling the printing environment are crucial to mitigate these issues.
- Gözeneklilik: Internal voids or pores can occur in 3D printed metal parts, which can negatively impact their mechanical properties. Selecting the right printing parameters, ensuring high-quality metal powder (like the ones offered by Metal3DP), and employing appropriate post-processing techniques like Hot Isostatic Pressing (HIP) can minimize porosity.
- Support Removal Damage: Improper removal of support structures can damage the surface of the robot link. Careful design of support structures and the use of appropriate removal techniques are essential.
- Residual Stresses: The rapid heating and cooling cycles during metal 3D printing can induce residual stresses in the part, which can lead to cracking or failure under load. Stress relieving heat treatments are necessary to alleviate these stresses.
- Cost and Scalability: The initial cost of metal 3D printing equipment and materials can be higher than traditional manufacturing methods. Scalability for large-volume production can also be a challenge. However, for complex, high-value parts and low-to-medium volume production, metal 3D printing can be cost-effective.
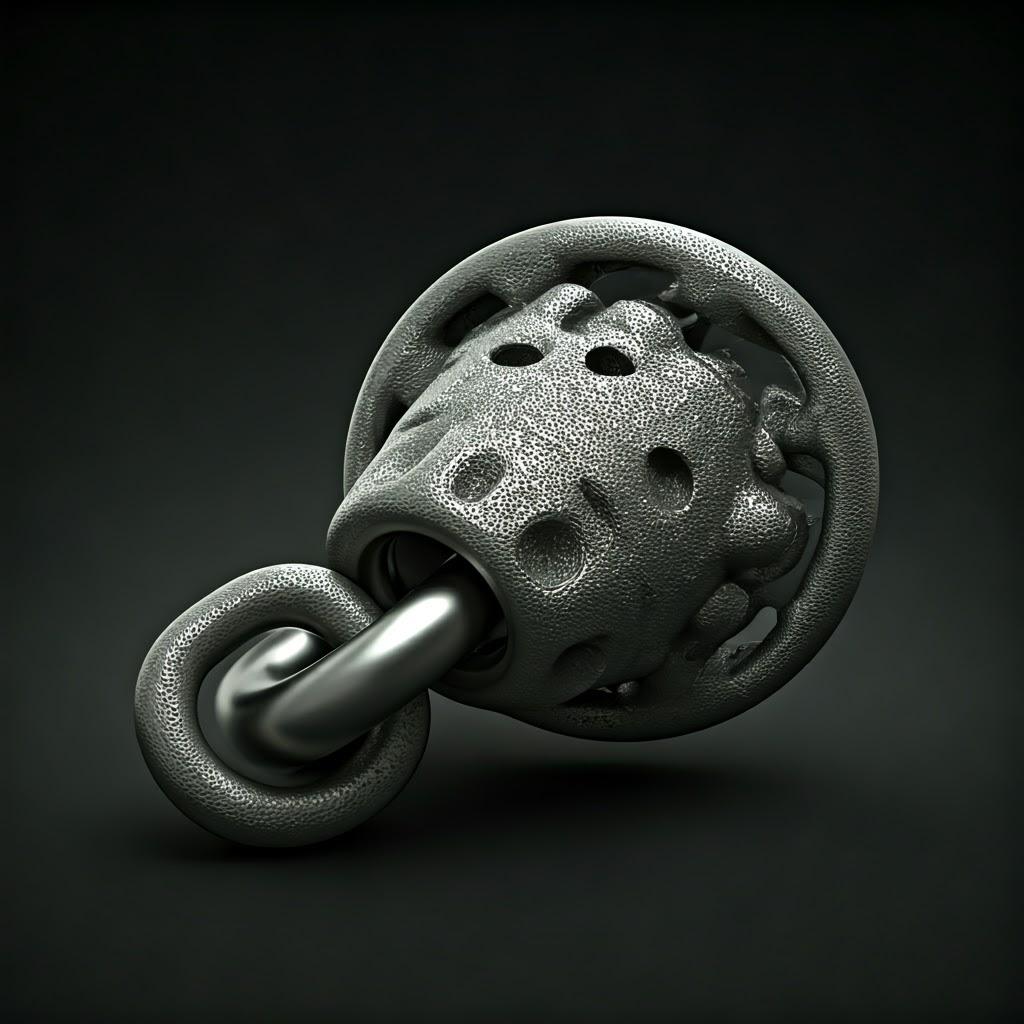
Selecting a Reliable Metal 3D Printing Service Provider for Robot Links
Choosing the right metal 3D printing service provider is crucial for obtaining high-quality robot links that meet your specific requirements. Consider the following factors when evaluating potential suppliers:
- Technology and Material Capabilities: Ensure the provider has experience with the specific metal powders required for your application (e.g., M300, 1.2709) and utilizes advanced printing technologies like Selective Electron Beam Melting (SEBM) or Laser Powder Bed Fusion (LPBF). Metal3DP offers both SEBM and LPBF technologies, along with a wide range of high-performance metal powders.
- Quality Assurance and Certifications: Look for providers with robust quality management systems and relevant certifications (e.g., ISO 9001, AS9100 for aerospace). This ensures that their processes are controlled and that the manufactured parts meet stringent quality standards.
- Design and Engineering Support: A good service provider should offer design optimization and engineering support to help you tailor your robot link designs for additive manufacturing, ensuring optimal performance and manufacturability.
- Post-Processing Services: Verify the availability of essential post-processing services such as heat treatment, surface finishing, and CNC machining, as these are often critical for achieving the final properties and dimensions of the robot links.
- Experience and Expertise: Choose a provider with a proven track record in manufacturing similar components for your industry. Their experience can help anticipate potential challenges and ensure a smooth production process.
- Communication and Transparency: Clear and consistent communication is essential for a successful partnership. The provider should be responsive to your inquiries and provide regular updates on the progress of your project.
- Lead Times and Scalability: Discuss lead times for production and the provider’s capacity to handle your current and future volume requirements.
- Cost Structure: Understand the pricing model and all associated costs, including printing, materials, post-processing, and shipping.
Understanding the Cost and Lead Time for 3D Printed Robot Link Manufacturing
The cost and lead time for manufacturing 3D printed robot links are influenced by several factors:
- Malzeme Maliyetleri: The type and quantity of metal powder used significantly impact the overall cost. High-performance alloys like M300 and 1.2709 can be more expensive than standard metals.
- Build Volume and Complexity: Larger and more complex parts require more printing time and material, leading to higher costs. The build volume of the 3D printer also plays a role in the number of parts that can be produced simultaneously. Metal3DP’nin industry-leading print volume allows for the efficient production of larger components or multiple smaller parts.
- Baskı Süresi: The duration of the printing process depends on factors such as part size, layer thickness, and the chosen printing technology. Longer print times translate to higher machine costs.
- İşlem Sonrası Gereksinimler: The extent of post-processing needed (e.g., support removal, heat treatment, machining, finishing) adds to both the cost and the lead time.
- Miktar: While 3D printing is often cost-effective for low to medium volumes, the unit cost can decrease with larger production runs due to economies of scale.
- Kurşun zamanı: The total lead time includes the time for design finalization, print preparation, the actual printing process, post-processing, and quality inspection. It can vary significantly depending on the complexity of the part, the availability of the printing equipment, and the workload of the service provider.
It’s essential to discuss these factors in detail with your chosen metal 3D printing service provider to obtain an accurate cost estimate and realistic lead time for your robot link manufacturing project.
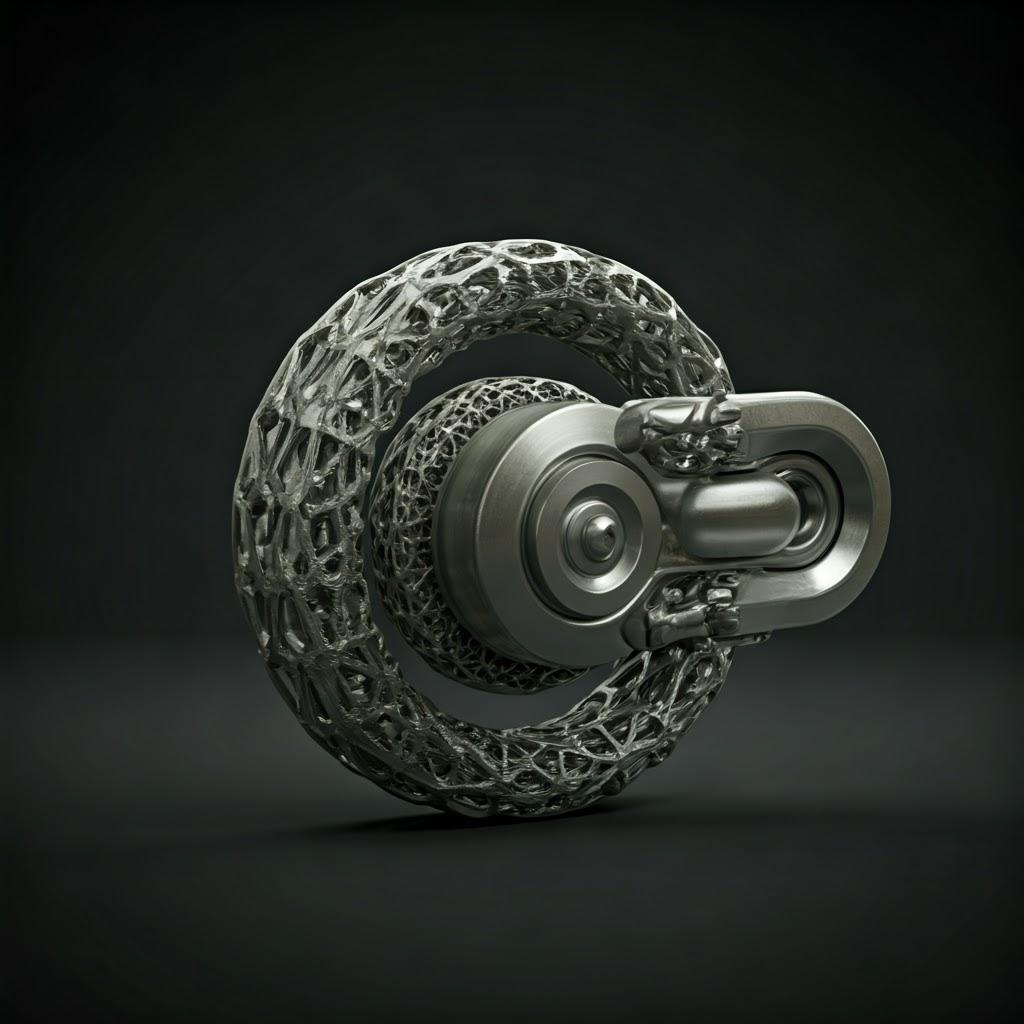
Sıkça Sorulan Sorular (SSS)
- What are the typical tolerances achievable with metal 3D printing for robot links?
- Typical tolerances range from ±0.1 to ±0.05 mm in the as-printed condition. For critical dimensions, post-processing like CNC machining can achieve tolerances of a few micrometers.
- Is heat treatment always necessary for 3D printed metal robot links?
- Heat treatment is often crucial for achieving the desired mechanical properties, such as strength and hardness, in materials like M300 and 1.2709. The specific heat treatment cycle depends on the alloy and the application requirements.
- Can metal 3D printed robot links be as strong as those manufactured traditionally?
- Yes, when the printing process is optimized and the correct materials and post-processing are employed, metal 3D printed robot links can achieve comparable or even superior strength-to-weight ratios compared to traditionally manufactured parts. The layer-by-layer build process can result in unique microstructures that enhance mechanical properties.
Conclusion: The Future of High-Strength Robot Links Lies in Metal 3D Printing
Metal 3D printing is revolutionizing the way high-strength robot links are designed and manufactured. Its ability to produce complex geometries, reduce weight, enhance performance, and enable customization makes it an increasingly attractive alternative to traditional manufacturing methods for industries ranging from aerospace to medical. Companies like Metal3DP are at the forefront of this innovation, providing advanced 3D printing equipment and high-quality metal powders such as M300 and 1.2709 that are ideally suited for demanding robotic applications. By understanding the design considerations, material properties, post-processing requirements, and how to choose the right service provider, engineers and procurement managers can leverage the power of metal additive manufacturing to create next-generation, high-performance robot links that drive efficiency and innovation in their respective fields. Contact Metal3DP today to explore how our comprehensive metal AM solutions can power your organization’s additive manufacturing goals.
Paylaş
MET3DP Technology Co, LTD, merkezi Qingdao, Çin'de bulunan lider bir katmanlı üretim çözümleri sağlayıcısıdır. Şirketimiz, endüstriyel uygulamalar için 3D baskı ekipmanları ve yüksek performanslı metal tozları konusunda uzmanlaşmıştır.
İşletmeniz için en iyi fiyatı ve özelleştirilmiş Çözümü almak için sorgulayın!
İlgili Makaleler
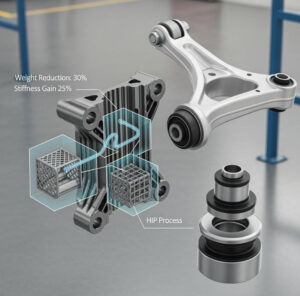
Metal 3D Printed Subframe Connection Mounts and Blocks for EV and Motorsport Chassis
Daha Fazla Oku "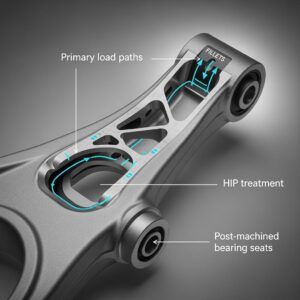
Metal 3D Printing for U.S. Automotive Lightweight Structural Brackets and Suspension Components
Daha Fazla Oku "Met3DP Hakkında
Son Güncelleme
Bizim Ürünümüz
BİZE ULAŞIN
Herhangi bir sorunuz var mı? Bize şimdi mesaj gönderin! Mesajınızı aldıktan sonra tüm ekibimizle talebinize hizmet edeceğiz.