Rocket Fairing Connectors 3D Printed in Ti Alloys
İçindekiler
The relentless pursuit of lighter, faster, and more cost-effective access to space places immense demands on every component within a launch vehicle system. Among the most critical, yet often overlooked, elements are the connectors used within the payload fairing assembly. These components play a vital role in maintaining structural integrity during the extreme conditions of launch and ensuring the successful deployment of valuable payloads. Traditionally manufactured using subtractive methods like CNC machining, these connectors are increasingly benefiting from the transformative capabilities of metal additive manufacturing (AM), particularly using high-performance titanium alloys like Ti-6Al-4V. This article delves into the world of 3D yazdırılmış rocket fairing connectors, exploring their function, the advantages offered by AM, the crucial role of material selection, and why partnering with an expert provider like Met3dp is key to leveraging this technology effectively.
Introduction: The Critical Role of Rocket Fairing Connectors in Space Missions
A rocket’s journey from the launchpad to orbit is a symphony of controlled power and precision engineering. Every single component, from the powerful engines to the smallest fastener, must perform flawlessly under conditions that push the boundaries of material science and structural design. Within this complex system, the payload fairing – the nose cone structure that protects satellites or other spacecraft during ascent through the atmosphere – is a critical subsystem. Its primary function is shielding the delicate and often multi-million or billion-dollar payload from aerodynamic forces, acoustic vibrations, and thermal loads encountered during the initial phases of flight. The structural integrity and timely, reliable separation of this fairing are paramount for mission success. Failure is not an option.
Holding this crucial protective shell together, and ensuring its segments connect seamlessly and separate cleanly when required, are the rocket fairing connectors. These components might seem small relative to the overall launch vehicle, but their role is disproportionately significant. They are the linchpins ensuring the fairing assembly maintains its aerodynamic shape and structural rigidity against immense forces. These forces include:
- Aerodynamic Pressure: As the rocket accelerates through the dense lower atmosphere at supersonic speeds, the air resistance exerts tremendous pressure on the fairing’s surface. Connectors must prevent buckling or deformation.
- Acoustic Vibrations: The roar of the rocket engines generates intense sound waves that vibrate throughout the vehicle structure. Connectors must dampen or withstand these vibrations without fatiguing or failing.
- Inertial Loads: During maneuvers and stage separations, the entire vehicle experiences significant g-forces. Connectors must bear these inertial loads without yielding.
- Termal Stresler: Aerodynamic heating can create temperature gradients across the fairing structure, inducing thermal stresses that connectors must accommodate.
Furthermore, these connectors are often involved in the pyrotechnic or mechanical systems responsible for jettisoning the fairing halves once the rocket reaches the vacuum of space, exposing the payload for deployment. This means they must not only provide strength during ascent but also function reliably as part of the separation sequence. Any malfunction – a connector failing under load, jamming during separation, or causing structural instability – could lead to catastrophic mission failure.
Given these extreme operational requirements, the design and manufacture of rocket fairing connectors have always been challenging. Traditional manufacturing approaches, primarily CNC machining from billet stock, often involve significant material waste (poor buy-to-fly ratios), long lead times, and limitations in geometric complexity. Complex shapes needed for optimal stress distribution or integration with separation systems can be difficult or prohibitively expensive to machine.
İşte burası metal katkılı üretim (AM)olarak da bilinir. metal 3D baskı, emerges as a game-changing technology. AM allows for the layer-by-layer construction of complex metal parts directly from a digital model, offering unprecedented design freedom, potential for weight reduction through optimization, part consolidation, and significantly reduced lead times compared to traditional methods, especially for intricate components. For rocket fairing connectors, AM enables engineers to:
- Optimize Designs: Create connectors with internal lattice structures or topology-optimized shapes that minimize mass while maximizing stiffness and strength, tailored precisely to the load paths experienced during launch.
- Consolidate Parts: Combine multiple components of a connector assembly into a single, integrated 3D printed part, reducing assembly time, potential points of failure, and overall system complexity.
- Accelerate Development: Rapidly iterate designs and produce functional prototypes or flight hardware much faster than traditional tooling and machining cycles allow.
- Utilize Advanced Materials: Effectively process high-performance aerospace alloys like Ti-6Al-4V, known for its exceptional strength-to-weight ratio and resilience, perfectly suited for the demands of space launch.
The implications for the aerospace industry, particularly for launch vehicle manufacturers and satellite operators, are profound. By leveraging AM for critical components like fairing connectors, companies can build lighter, more capable rockets, reduce launch costs, and accelerate the pace of innovation in space exploration and commercialization. Understanding the specific applications and the unique advantages AM brings to this component is crucial for engineers and procurement managers aiming to stay competitive in this rapidly evolving sector.
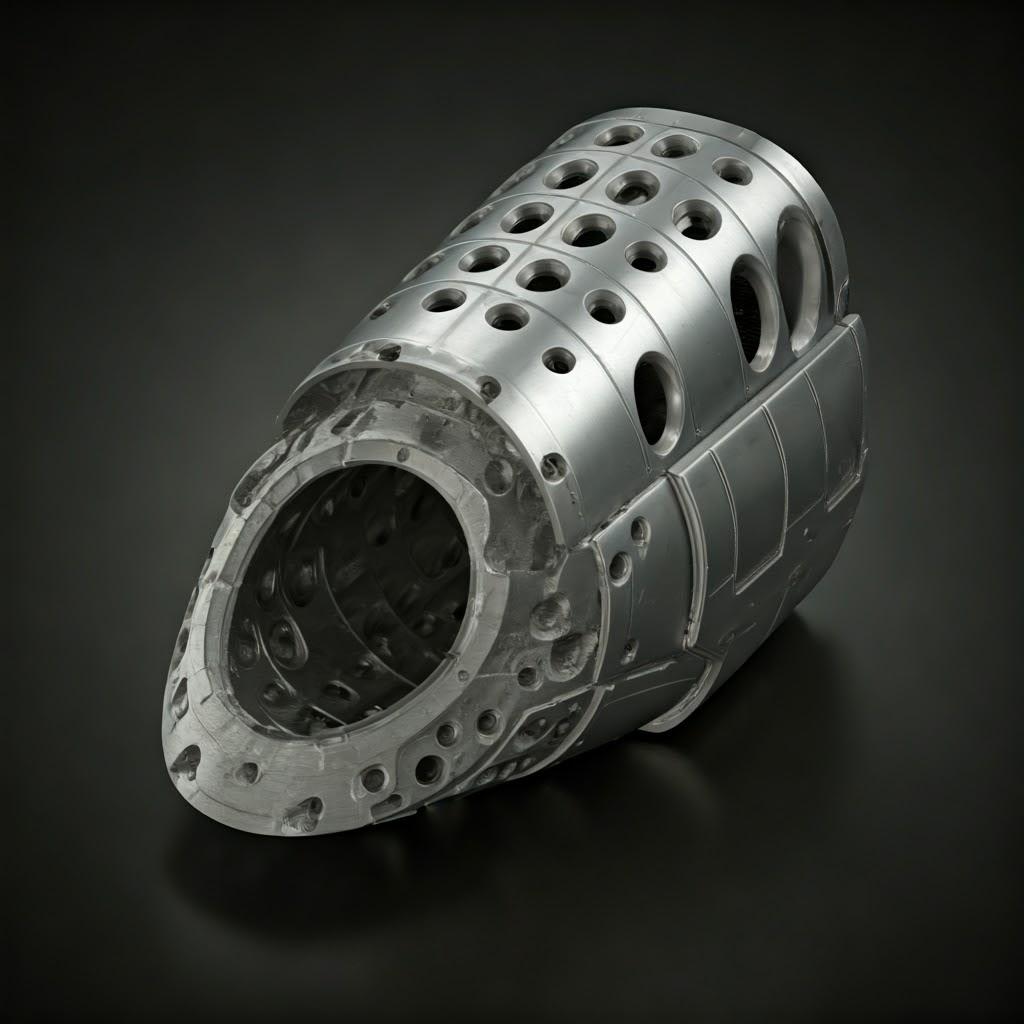
What are Rocket Fairing Connectors Used For? Applications and Demands
Rocket fairing connectors are specialized mechanical components designed explicitly for the unique environment and functional requirements of launch vehicle payload fairings. Their primary roles revolve around structural connection, load transfer, and often, facilitating separation. They are integral parts of the overall fairing assembly, which typically consists of two or more segments (often clamshell halves) that encapsulate the payload.
Core Functions and Applications:
- Segment Joining: The most fundamental role is to securely join the longitudinal seams where the fairing halves meet and potentially connect the fairing base to the launch vehicle’s interstage structure. They must maintain a precise alignment and create a near-continuous load path along these seams.
- Load Distribution: During ascent, the fairing experiences non-uniform aerodynamic pressures and intense vibrations. Connectors are strategically placed to distribute these loads effectively across the fairing structure, preventing stress concentrations that could lead to localized failure. They transfer tension, compression, and shear forces between the fairing panels.
- Maintaining Aerodynamic Profile: By holding the fairing segments rigidly together, connectors ensure the fairing maintains its intended aerodynamic shape. Any significant deformation could alter aerodynamic forces, potentially compromising vehicle stability and control.
- Integration with Separation Systems: In many designs, fairing connectors are integrated with the mechanisms that jettison the fairing halves once the vehicle is out of the atmosphere. This can involve:
- Frangible Joints: Connectors designed to break cleanly upon activation of a pyrotechnic charge (e.g., explosive bolts or linear shaped charges).
- Mechanical Latches: Connectors incorporating releasable latches triggered by pneumatic, hydraulic, or electro-mechanical actuators.
- Guides and Rails: Connectors may also serve as guides during the separation process, ensuring the fairing halves move away from the payload and vehicle cleanly without collision.
- Sealing: Depending on the design and payload sensitivity, connectors might contribute to sealing the fairing seams against atmospheric moisture or contaminants, although dedicated seals are also commonly used.
Industries and Systems Utilizing These Connectors:
The primary application is unequivocally within the havacılık ve uzay endüstrisi, specifically in the design and manufacture of:
- Expendable Launch Vehicles (ELVs): From small satellite launchers to heavy-lift rockets carrying large communications satellites or interplanetary probes (e.g., Ariane, Atlas, Delta, Falcon, Long March, Soyuz).
- Reusable Launch Vehicles (RLVs): Systems like SpaceX’s Starship or Blue Origin’s New Glenn, while potentially having different fairing recovery strategies, still require robust fairing structures and associated connectors during ascent.
- Sounding Rockets: Smaller rockets used for suborbital research also utilize fairings and connectors, albeit typically on a smaller scale.
- Füze Sistemleri: Certain types of long-range missiles employ protective shrouds or fairings during the boost phase, requiring similar connector technology.
Demands Placed on Fairing Connectors:
The operational environment imposes a stringent set of demands:
- Yüksek Mukavemet-Ağırlık Oranı: Every kilogram launched into orbit costs thousands of dollars. Connectors must be incredibly strong to handle the loads but also extremely lightweight to minimize their impact on overall vehicle mass and maximize payload capacity. This is a primary driver for using materials like titanium alloys.
- Structural Stiffness: Connectors must be sufficiently stiff to prevent undue flexing or deformation of the fairing under load, maintaining the aerodynamic shape and alignment.
- Yorulma Direnci: The intense, broadband acoustic vibrations generated by engines (often exceeding 140 dB) subject the entire structure, including connectors, to high-cycle fatigue loading. Connectors must resist crack initiation and propagation.
- Extreme Temperature Resilience: While ascent through the atmosphere is relatively short, connectors can experience significant temperature variations, from ambient ground temperatures to aerodynamic heating (potentially several hundred degrees Celsius on leading edges) and the cold soak of space after jettison (though their primary function is complete by then). They must maintain their mechanical properties across this range.
- Reliability: Given the mission-critical nature, fairing connectors require exceptionally high reliability. Failure is not an option, demanding rigorous design, analysis, manufacturing quality control, and testing protocols.
- Clean Separation (if applicable): For connectors involved in jettison, they must function flawlessly on command, ensuring a clean break or release without generating excessive debris that could endanger the payload or vehicle.
- Manufacturability and Cost-Effectiveness: While performance and reliability are paramount, the cost and speed of manufacturing are increasingly important, especially with the rise of commercial space ventures aiming for higher launch cadences.
Meeting these demanding requirements simultaneously is a significant engineering challenge. Traditional manufacturing methods often force compromises – for instance, achieving high strength might require thicker sections, increasing weight, or complex geometries for optimal load transfer might be prohibitively expensive to machine. Additive manufacturing provides a powerful new toolkit to overcome many of these traditional limitations, enabling the design and production of fairing connectors that are lighter, stronger, more complex, and potentially faster to produce. Companies like Met3dp, with expertise in aerospace-grade metal powders and printing systems, are crucial partners in realizing the potential of AM for these critical space components.
Why Use Metal 3D Printing for Rocket Fairing Connectors? Unlocking Performance and Efficiency
The decision to adopt metal additive manufacturing for a component as critical as a rocket fairing connector isn’t taken lightly. It requires a thorough evaluation against established traditional methods like CNC machining, casting, or forging. However, for fairing connectors, the advantages offered by AM, particularly Laser Powder Bed Fusion (LPBF) or Electron Beam Melting (EBM), are compelling and address many of the inherent challenges faced in their design and production. The benefits span performance enhancement, manufacturing efficiency, and supply chain improvements.
1. Unprecedented Design Freedom and Complexity:
- Topology Optimization & Generative Design: AM unshackles designers from the constraints of traditional manufacturing. Complex, organic shapes optimized purely for structural performance, often resembling bone structures, can be realized. Software tools can automatically generate designs that place material only where needed to withstand specific load paths, drastically reducing weight while maintaining or even increasing strength and stiffness. For fairing connectors, this means creating intricate internal lattices or smoothly varying cross-sections that would be impossible or astronomically expensive to machine.
- Internal Features: Cooling channels (if needed for extreme heating scenarios, though less common for fairings), hidden cavities for weight reduction, or integrated mounting points for sensors or separation system components can be built directly into the connector.
- Bionic Designs: Mimicking efficient structures found in nature becomes feasible, leading to highly optimized, lightweight yet robust connector designs.
2. Significant Weight Reduction (Lightweighting):
- Optimized Geometries: As mentioned above, topology optimization directly leads to using less material for the same or better performance. Reducing the mass of dozens or hundreds of connectors per fairing contributes significantly to lowering the overall launch vehicle dry mass.
- Malzeme Verimliliği: AM enables the use of high strength-to-weight ratio materials like Titanium alloys (e.g., Ti-6Al-4V) very effectively. While these materials can be machined, AM allows their use in highly optimized forms that maximize this benefit.
- Etki: Every kilogram saved in the upper stages or fairing translates directly into increased payload capacity or improved vehicle performance (e.g., higher achievable orbits). This is a primary economic driver in the launch industry.
3. Part Consolidation:
- Reduced Assembly Complexity: Traditionally, a fairing connector might consist of multiple machined pieces, brackets, and fasteners. AM allows these individual parts to be redesigned and consolidated into a single, monolithic printed component.
- Avantajlar:
- Reduced Part Count: Simplifies inventory management, logistics, and supply chain complexity.
- Elimination of Joints/Fasteners: Joints and fasteners are potential points of failure (fatigue, loosening) and add weight. A consolidated part is inherently more reliable.
- Faster Assembly: Reduces the time and labor required to assemble the fairing.
- Improved Structural Integrity: Eliminates stress concentrations often associated with bolted or riveted joints.
4. Lead Time Reduction and Rapid Iteration:
- Alet Eliminasyonu: Traditional manufacturing often requires significant upfront investment in custom tooling, jigs, and fixtures, which takes considerable time to design and produce. AM is a tool-less process; parts are built directly from the CAD model.
- Daha Hızlı Prototipleme: Design changes can be implemented quickly by modifying the digital model and printing a new iteration, drastically accelerating the development and qualification cycle compared to modifying traditional tooling.
- İsteğe Bağlı Üretim: AM allows for manufacturing parts closer to the point of need and potentially in smaller batch sizes without the economic penalties associated with traditional mass production setups. This improves responsiveness to changing launch schedules or design updates. For aerospace programs operating under tight deadlines, this agility is invaluable.
5. Improved Buy-to-Fly Ratio:
- Subtractive vs. Additive: CNC machining starts with a solid block or forging (billet) of material and removes (subtracts) large amounts to achieve the final shape. Especially for complex aerospace parts made from expensive materials like titanium, the ratio of the raw material purchased (buy) to the material in the final part (fly) can be very poor (e.g., 10:1 or even 20:1), meaning 90-95% of the expensive material becomes scrap chips.
- AM Efficiency: AM builds parts layer by layer, using primarily only the material needed for the part itself and necessary support structures. While some powder remains unfused and can often be recycled, the material waste is significantly lower, often improving the buy-to-fly ratio dramatically (e.g., closer to 2:1 or 3:1). This results in substantial cost savings, particularly for high-value materials like aerospace-grade titanium.
6. Enhanced Performance Potential:
- Tailored Material Properties: AM process parameters can sometimes be tuned to influence the microstructure (e.g., grain size, texture) of the resulting material, potentially offering tailored mechanical properties like enhanced fatigue strength or fracture toughness in specific areas of the connector.
- Functionally Graded Materials (Future Potential): Research is ongoing into AM techniques that could vary material composition within a single part, opening possibilities for connectors with different properties (e.g., high strength core, wear-resistant surface) in different regions, although this is not yet standard practice for critical components like fairing connectors.
Comparison Table: AM vs. Traditional Machining for Fairing Connectors
Özellik | Metal Additive Manufacturing (e.g., LPBF) | Geleneksel CNC İşleme | Advantage for Fairing Connectors |
---|---|---|---|
Tasarım Karmaşıklığı | High (complex internal structures, topology optimization) | Moderate to High (limited by tool access) | AM (Weight reduction, Perf.) |
Ağırlık Azaltma | Excellent potential via optimization | Limited by machinability & design rules | AM (Payload capacity) |
Parça Konsolidasyonu | High potential (integrating multiple parts) | Low potential (requires assembly) | AM (Reliability, Assembly) |
Lead Time (New Part) | Short (days/weeks – no tooling) | Long (weeks/months – tooling often needed) | AM (Development speed) |
Malzeme Atıkları | Low (additive process, powder recycling) | High (subtractive process, high buy-to-fly) | AM (Cost, Sustainability) |
Kalıp Maliyeti | Hiçbiri | High (custom jigs, fixtures) | AM (Cost, Flexibility) |
Yüzey İşlemi | Rougher (as-printed), requires post-processing | Good to Excellent | Talaşlı İmalat (As-is finish) |
Boyutsal Doğruluk | Good, often requires final machining for critical tolerances | Mükemmel | Talaşlı İmalat (Precision) |
Malzeme Özellikleri | Comparable to wrought (post-HIP), potentially tailorable micro. | Well-understood (wrought/forged standard) | Near Equivalent (post-process) |
Cost (Low Volume) | Potentially Lower (no tooling, less waste) | Potentially Higher (tooling amortization) | AM |
Cost (High Volume) | Can be higher per part (slower build rate) | Can be lower per part (faster cycle time) | Talaşlı İmalat (depends on scale) |
Sayfalara Aktar
While AM offers transformative advantages, it’s crucial to acknowledge that it’s not a universal replacement. Challenges related to surface finish, the need for post-processing (like heat treatment, HIP, and finish machining), and rigorous process control and qualification are critical considerations, especially for aerospace applications. However, for components like rocket fairing connectors where weight, complexity, and lead time are major drivers, the benefits offered by metal 3D printing, particularly when using optimized materials like Ti-6Al-4V supplied by expert manufacturers like Met3dp, present a compelling value proposition that is reshaping aerospace manufacturing.
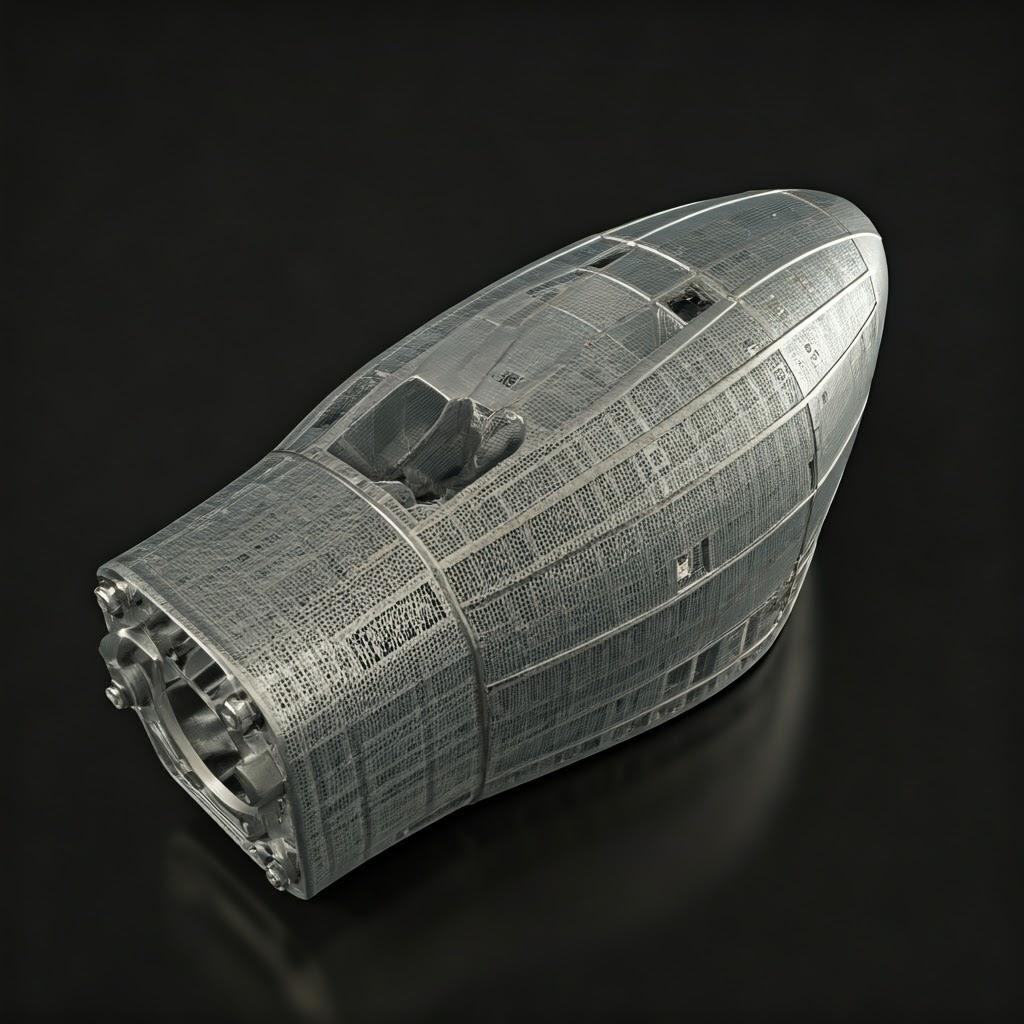
Recommended Materials: Ti-6Al-4V and Ti-6Al-4V ELI – The Aerospace Workhorses
The selection of material for any aerospace component is a critical decision governed by stringent performance requirements. For rocket fairing connectors, the material must provide an exceptional balance of high strength, low density, stiffness, fatigue resistance, and reliability across a relevant temperature range. Among the available engineering materials, titanium alloys, specifically Ti-6Al-4V (Sınıf 5) and its higher purity variant Ti-6Al-4V ELI (Sınıf 23), stand out as the preeminent choices for demanding aerospace applications, including additively manufactured components.
Why Titanium Alloys?
Titanium alloys possess a unique combination of properties that make them highly desirable for aerospace structures:
- Mükemmel Güç-Ağırlık Oranı: This is arguably the most significant advantage. Titanium alloys are roughly 40-45% lighter than steel but can achieve comparable or even superior strength levels, especially at cryogenic and moderately elevated temperatures (up to around 300-400°C). For fairing connectors, this directly translates to significant weight savings.
- High Specific Strength: Strength divided by density is a key metric in aerospace design, and titanium alloys excel here.
- İyi Korozyon Direnci: Titanium naturally forms a stable, tenacious oxide layer (TiO2) that provides outstanding resistance to corrosion in various environments, including saltwater and oxidizing acids, which can be relevant during ground handling, transport, and storage.
- Good Fatigue Life: Titanium alloys generally exhibit good resistance to fatigue crack initiation and propagation, crucial for components subjected to the vibrational loads during launch.
- Biocompatibility (especially ELI grades): While not directly relevant for fairing connectors, the excellent biocompatibility of titanium alloys underscores their inertness and stability.
Ti-6Al-4V (Grade 5): The Industry Standard
Ti-6Al-4V is the most widely used titanium alloy, accounting for more than 50% of all titanium tonnage worldwide. It’s an alpha-beta alloy, meaning its microstructure contains both alpha and beta phases, offering a good balance of properties.
- Kompozisyon: Nominally 6% Aluminum (Al), 4% Vanadium (V), balance Titanium (Ti). Minor impurities like Iron (Fe), Oxygen (O), Carbon (C), and Nitrogen (N) are controlled within specified limits.
- Key Properties (Typical Annealed Wrought):
- Density: ~4.43 g/cm³
- Ultimate Tensile Strength (UTS): ~950 MPa (138 ksi)
- Yield Strength (YS): ~880 MPa (128 ksi)
- Elastic Modulus: ~114 GPa (16.5 Msi)
- Elongation: ~14%
- Advantages for Fairing Connectors:
- Yüksek Mukavemet: Provides the necessary load-bearing capacity.
- Weldability/Processability: Relatively well-understood processing characteristics for both traditional methods and AM.
- Availability & Cost: Being the most common grade, it’s more readily available and generally less expensive than more specialized titanium alloys.
- Extensive Database: A vast amount of data exists on its mechanical behavior, fatigue life, and environmental resistance, crucial for design and certification.
Ti-6Al-4V ELI (Grade 23): Enhanced Purity and Toughness
Ti-6Al-4V ELI (Extra Low Interstitials) is a higher-purity version of Grade 5. The primary difference lies in the stricter control and reduction of interstitial elements, particularly Oksijen (O) and Iron (Fe).
- Kompozisyon: Same nominal Al and V content as Grade 5, but with lower maximum limits for O, Fe, C, and N. For example, standard Grade 5 might allow up to 0.20% Oxygen, whereas Grade 23 typically limits it to 0.13% maximum.
- Key Properties (Compared to Grade 5):
- Geliştirilmiş Süneklik: Lower interstitials lead to significantly better elongation and reduction in area.
- Enhanced Fracture Toughness: More resistant to crack propagation, especially at cryogenic temperatures.
- Improved Fatigue Strength: Generally offers better high-cycle fatigue performance.
- Slightly Lower Strength: The increased purity comes at the cost of slightly lower UTS and YS compared to standard Grade 5 (e.g., UTS ~860 MPa, YS ~790 MPa).
- Advantages for Fairing Connectors:
- Damage Tolerance: The higher fracture toughness makes it more suitable for critical components where crack propagation resistance is paramount (a “damage tolerant” design philosophy).
- Reliability in Extreme Conditions: Better performance under cyclic loading and potentially at lower temperatures makes it a preferred choice for mission-critical applications requiring the highest level of structural integrity.
- Often Specified for Critical AM Parts: Due to the layer-by-layer nature of AM, ensuring excellent ductility and toughness in the final part is crucial, making ELI grades often favored for printed aerospace components.
Material Properties Comparison (Typical Values for AM Parts Post-HIP & Stress Relief)
Mülkiyet | Ti-6Al-4V (Grade 5) AM | Ti-6Al-4V ELI (Grade 23) AM | Birim | Significance for Connectors |
---|---|---|---|---|
Yoğunluk | ~4.42 | ~4.42 | g/cm³ | Low density is key for weight savings |
Ultimate Tensile Str. | 980 – 1150 | 900 – 1050 | MPa | Capacity to withstand maximum load before fracture |
Akma Dayanımı (0,2%) | 890 – 1050 | 820 – 950 | MPa | Point at which permanent deformation begins |
Elastik Modül | 110 – 120 | 110 – 120 | Not ortalaması | Stiffness; resistance to elastic deformation under load |
Kopma Uzaması | 8 – 15 | 10 – 18 | % | Ductility; ability to deform before fracturing |
Fracture Toughness KIC | 55 – 70 | 65 – 90 | MPa√m | Resistance to crack propagation (higher is better) |
Yorulma Dayanımı | İyi | Çok iyi | – | Resistance to failure under cyclic loading (vibrations) |
Max Service Temp. | ~350 – 400 | ~350 – 400 | °C | Upper limit for maintaining useful strength |
Sayfalara Aktar
(Note: Actual properties of AM parts depend heavily on the specific AM process used (LPBF, EBM), machine parameters, powder quality, build orientation, and post-processing steps like HIP and heat treatment. Values are indicative.)
The Importance of High-Quality Metal Powders
The final properties and reliability of an additively manufactured titanium connector are critically dependent on the quality of the metal powder used. Key powder characteristics include:
- Küresellik: Highly spherical powder particles ensure good flowability, which is essential for uniformly spreading thin layers in the powder bed fusion process, leading to consistent melting and density.
- Parçacık Boyutu Dağılımı (PSD): A controlled PSD ensures high packing density in the powder bed, minimizing voids and contributing to fully dense final parts. The optimal PSD depends on the specific AM machine and layer thickness used.
- Purity & Chemistry: The powder must strictly adhere to the chemical specifications (e.g., AMS standards for Ti-6Al-4V or ELI) with minimal contaminants (especially oxygen, nitrogen, carbon) and undesired elements. Contamination can severely degrade mechanical properties.
- Akışkanlık: Directly related to sphericity and PSD, good flowability ensures the recoater mechanism can spread even layers across the build platform.
- Absence of Satellites: Small, irregular particles attached to larger spherical ones (satellites) can hinder flowability and packing density.
- Low Porosity: Internal pores within the powder particles themselves can translate into porosity in the final part.
Met3dp’s Role in Supplying Aerospace-Grade Titanium Powders
Achieving these stringent powder characteristics requires advanced manufacturing processes. Met3dp utilizes industry-leading gas atomization and Plasma Rotating Electrode Process (PREP) technologies to produce high-quality, spherical metal powders optimized for additive manufacturing.
- Gaz Atomizasyonu: Molten metal is disintegrated by high-pressure inert gas jets, rapidly solidifying into fine, spherical droplets. Met3dp’s equipment employs unique nozzle and gas flow designs to maximize sphericity and yield within the desired PSD.
- PREP: A consumable electrode made of the target alloy is rotated at high speed while its tip is melted by a plasma torch. Centrifugal force ejects molten droplets, which solidify in flight into highly spherical powders with very high purity and minimal internal porosity or satellites. PREP is often favored for reactive materials like titanium and for applications demanding the absolute highest powder quality.
Met3dp manufactures a wide range of metal powders, including Ti-6Al-4V and Ti-6Al-4V ELI, specifically optimized for Laser Powder Bed Fusion (LPBF) and Selective Electron Beam Melting (SEBM) processes commonly used for aerospace components. Their rigorous quality control ensures chemical composition compliance, controlled PSD, high sphericity, excellent flowability, and low contamination levels, meeting the demanding standards of the aerospace industry. By partnering with a powder supplier like Met3dp, manufacturers of rocket fairing connectors can have confidence in the quality and consistency of their raw material, which is the foundation for producing reliable, high-performance flight hardware. Choosing between Ti-6Al-4V and Ti-6Al-4V ELI depends on the specific design requirements, criticality, and damage tolerance philosophy adopted for the connector, but both represent outstanding choices enabled by advanced powder manufacturing and additive processing.
Design Considerations for Additively Manufactured Fairing Connectors
Simply taking a design intended for CNC machining and sending it to a metal 3D printer rarely yields optimal results. Additive manufacturing operates under different principles and constraints, offering unique freedoms but also presenting specific challenges. To truly leverage AM’s benefits – lightweighting, part consolidation, enhanced performance – engineers must embrace Katmanlı Üretim Tasarımı (DfAM). DfAM is a methodology that involves designing parts specifically with the capabilities and limitations of the AM process in mind. For rocket fairing connectors, several DfAM principles are paramount:
1. Optimize for Load Paths (Topology Optimization & Generative Design):
- Concept: Use specialized software tools to determine the most efficient material distribution required to withstand the specific structural loads (tension, compression, shear, vibration) experienced by the connector during launch and fairing separation. The software essentially “carves away” unnecessary material, leaving behind an organic, often skeletal structure.
- Application to Connectors: Fairing connectors experience complex load combinations. Topology optimization can create lightweight yet stiff designs that efficiently transfer loads between fairing segments or to the separation system interface points. This directly contributes to the primary goal of weight reduction.
- Süreç: Requires defining design spaces, non-design spaces (e.g., mating interfaces, bolt holes), load cases, constraints (e.g., maximum stress, minimum stiffness), and manufacturing constraints specific to AM (e.g., minimum feature size, overhang angles).
- Outcome: Highly optimized, lightweight structures that are often impossible to manufacture conventionally.
2. Strategically Incorporate Lattice Structures:
- Concept: Replace solid volumes with internal, repeating geometric patterns (lattices or cellular structures). Different lattice types (e.g., cubic, octet-truss, gyroid) offer varying properties regarding stiffness, strength, energy absorption, and thermal conductivity.
- Application to Connectors:
- Hafifletme: Fill less critical internal volumes with low-density lattices to reduce mass while maintaining necessary structural support.
- Vibration Damping: Certain lattice geometries can be designed to absorb or damp mechanical vibrations, potentially improving fatigue life and protecting the payload from acoustic energy.
- Controlled Stiffness: Tailor the effective stiffness of the connector by varying lattice density or type in different regions.
- Düşünceler: Requires careful simulation and analysis to ensure the lattice provides adequate strength and fatigue resistance. Manufacturability (e.g., ability to remove trapped powder from closed cells) must also be considered. Open-cell structures are generally preferred for AM unless depowdering access is designed in.
3. Minimize and Optimize Support Structures:
- The Need for Supports: In powder bed fusion processes (like LPBF and EBM), downward-facing surfaces and overhangs beyond a certain angle (typically <45° from the horizontal for LPBF Ti-6Al-4V, though EBM can often handle shallower angles due to higher build chamber temperatures) require support structures. These supports anchor the part to the build plate, prevent warping due to thermal stresses, and provide a base for overhangs to build upon.
- DfAM Goal: Design the part to be as self-supporting as possible to minimize the volume of supports needed. Supports add material cost, increase build time, require significant post-processing effort for removal, and can negatively impact the surface finish where they attach.
- Strategies:
- Yapı Oryantasyonu: Carefully select the orientation of the connector on the build plate. Orienting critical surfaces upwards or vertically can reduce support needs. However, orientation also affects residual stress, surface finish on different faces, and potentially anisotropic mechanical properties. A trade-off analysis is often required.
- Kendini Destekleyen Açılar: Design overhangs with angles greater than the process-specific limit (e.g., >45°).
- Chamfers and Fillets: Replace sharp horizontal overhangs with chamfered or filleted edges that gradually build up.
- Designing for Removability: If supports are unavoidable, ensure they are accessible for removal tools (manual breaking, cutting tools, wire EDM). Avoid placing supports in intricate internal channels where they cannot be reached. Consider sacrificial layers or features designed to break away easily.
4. Manage Thermal Stresses and Warping:
- Sebep: The rapid heating and cooling cycles inherent in AM processes create significant thermal gradients, leading to internal residual stresses. These stresses can cause the part to warp or distort during the build or after removal from the build plate. Large, flat sections or abrupt changes in thickness are particularly prone to warping.
- DfAM Strategies:
- Avoid Large Solid Masses: Break up large volumes with internal voids or lattice structures.
- Gradual Thickness Transitions: Use generous fillets and smooth transitions between thick and thin sections.
- Ribbing/Stiffening Features: Add ribs strategically to increase stiffness and resist warping, particularly on thin walls or large flat areas.
- Oryantasyon: Orienting long, thin sections vertically can sometimes reduce warping compared to horizontal orientation, although this increases build height and time.
- Thermal Anchoring: Ensure adequate support structures are planned, especially for lower layers, to anchor the part firmly and conduct heat away.
5. Adhere to Process-Specific Design Rules:
- Minimum Wall Thickness: There’s a limit to how thin a stable wall can be reliably printed (depends on material, machine, parameters – often ~0.4-0.8 mm for Ti-6Al-4V LPBF).
- Minimum Özellik Boyutu: Small holes, pins, or slots may not resolve accurately below a certain size (e.g., small cooling channels or lettering).
- Hole Orientation: Horizontally printed holes often come out slightly elliptical and may require reaming or drilling post-process. Vertically printed holes tend to be more accurate. Consider designing holes slightly undersized if they will be finish-machined.
- Aspect Ratio: Very tall, thin features can be prone to instability or vibration during the build.
- Toz Giderme: For internal channels or cavities, ensure there are adequate openings designed in for removing unfused powder after the build. Trapped powder adds weight and can be detrimental.
6. CAD Model Preparation:
- Watertight Models: Ensure the 3D CAD model (often exported as an STL or 3MF file) is “watertight,” meaning it has no holes or self-intersecting surfaces. Errors in the digital model will translate into defects in the printed part.
- Appropriate Resolution: Use a suitable resolution/tolerance when exporting the mesh file (e.g., STL). Too coarse a mesh will result in faceted surfaces on the final part; too fine a mesh creates unnecessarily large files without adding practical accuracy.
- Collaboration with AM Provider: Work closely with the chosen additive manufacturing service provider, like Met3dp. Their engineers have deep expertise in the specific capabilities and constraints of their machines and processes (LPBF, SEBM, etc.) and can provide invaluable feedback on design manufacturability, optimal orientation, and support strategies.
By thoughtfully applying these DfAM principles, engineers can design rocket fairing connectors that are not only manufacturable via AM but are also significantly lighter, potentially stronger, and produced more efficiently than their traditionally manufactured counterparts. This design phase is critical for unlocking the true value of additive manufacturing in the demanding aerospace sector.
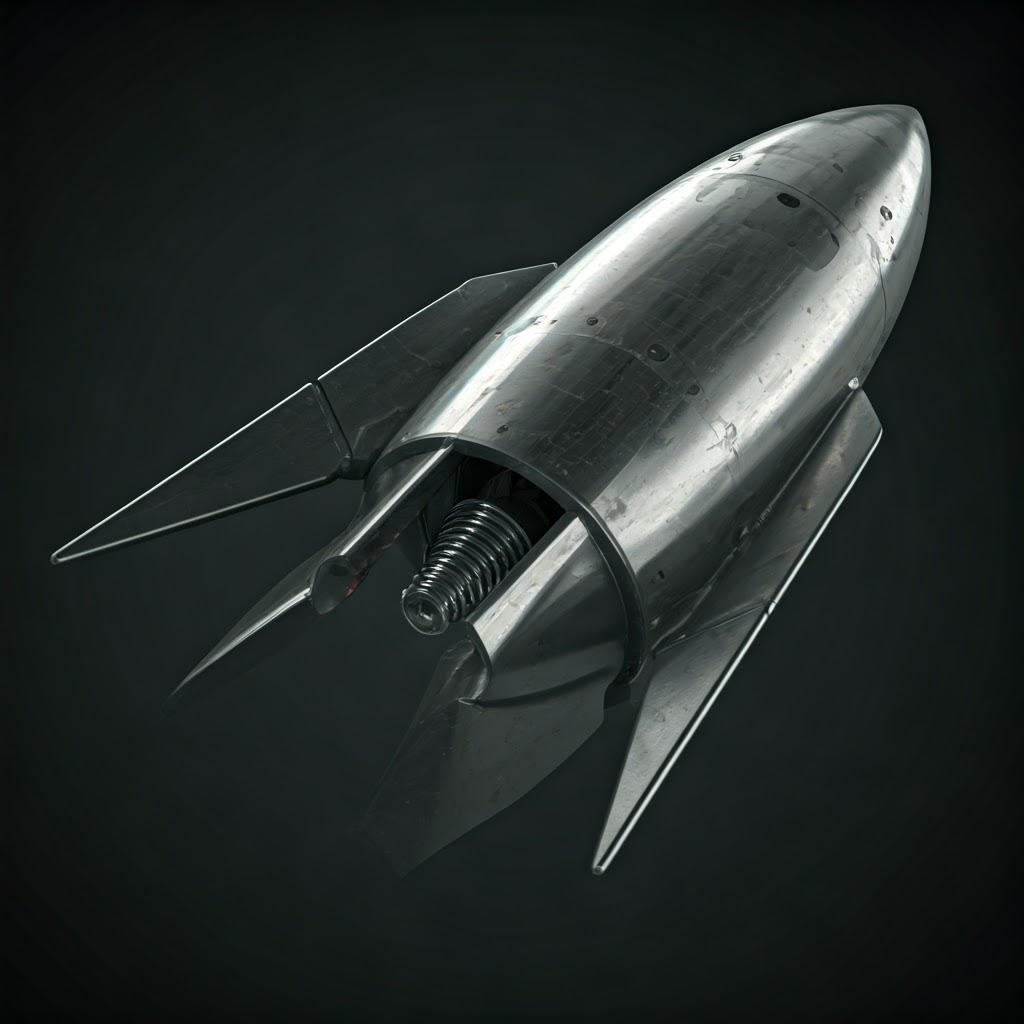
Achievable Tolerance, Surface Finish, and Dimensional Accuracy in 3D Printed Connectors
While metal additive manufacturing offers incredible geometric freedom, it’s essential for engineers and procurement managers to have realistic expectations regarding the dimensional accuracy and surface finish achievable directly from the printer (“as-built” condition). Unlike the precise surfaces often obtained directly from CNC machining, AM parts typically require post-processing to meet stringent aerospace tolerances and surface finish requirements, especially for critical mating surfaces or high-fatigue areas.
Yüzey İşlemi (Pürüzlülük):
- Nature of AM Surfaces: Layer-by-layer construction inherently creates a surface texture. In Laser Powder Bed Fusion (LPBF), partially melted powder particles adhering to the surface contribute significantly to roughness. Electron Beam Melting (EBM), operating at higher temperatures, often produces slightly rougher but less stressed surfaces.
- Typical As-Built Values:
- LPBF Ti-6Al-4V: Surface roughness (Ra – arithmetic average height) often ranges from 6 µm to 20 µm (approximately 240 to 800 µin). Vertical walls tend to be smoother than upward or downward-facing surfaces. Downward-facing surfaces where supports were attached are typically the roughest.
- EBM Ti-6Al-4V: As-built Ra values can be higher, potentially 20 µm to 40 µm (800 to 1600 µin).
- Factors Influencing Roughness:
- Katman Kalınlığı: Thinner layers generally produce smoother surfaces but increase build time.
- Süreç Parametreleri: Laser power, scan speed, beam focus (LPBF), or beam current/speed (EBM) significantly impact melt pool dynamics and surface texture.
- Yapı Oryantasyonu: Surfaces parallel to the build direction (vertical walls) are usually smoothest. Angled or “stair-stepped” surfaces are rougher. Top surfaces (last layers) can have specific textures.
- Toz Özellikleri: Particle size distribution affects packing and melting behavior.
- Aerospace Implications: For many aerospace applications, especially surfaces subject to fatigue or requiring precise mating, an Ra of 20 µm is too rough. Fatigue life, in particular, is highly sensitive to surface imperfections which act as stress concentrators. Therefore, secondary finishing operations are almost always required for critical surfaces on components like fairing connectors.
Dimensional Accuracy and Tolerance:
- As-Built Accuracy: The dimensional accuracy achievable directly from the AM process depends on machine calibration, material properties (shrinkage), thermal stresses, part geometry, and build orientation.
- Typical LPBF Tolerances: For well-calibrated systems printing Ti-6Al-4V, general tolerances might be in the range of ±0.1 mm to ±0.3 mm (±0.004″ to ±0.012″) for smaller dimensions (e.g., up to 100 mm), potentially increasing for larger parts due to accumulated thermal effects.
- Typical EBM Tolerances: EBM often exhibits slightly lower as-built accuracy compared to LPBF due to higher process temperatures and powder sintering effects, perhaps in the range of ±0.2 mm to ±0.5 mm.
- Geometric Complexity: Achieving tight tolerances on highly complex, freeform geometries produced by topology optimization can be more challenging than on simpler prismatic shapes.
- Sınırlamalar: AM processes struggle to consistently achieve the sub-0.05 mm (sub-0.002″) tolerances commonly required for aerospace interfaces, bearing fits, or precise alignments directly from the build.
- Need for Post-Machining: To meet typical aerospace drawing tolerances for critical features (e.g., bolt holes, mating faces, alignment pins/bores), post-process CNC machining is standard practice for AM metal parts. The AM process creates the near-net shape, and machining provides the final precision where needed. Designs must account for this, leaving sufficient machining stock (e.g., 0.5 mm to 1.5 mm) on critical surfaces.
Metrology and Quality Control:
- Verification is Key: Ensuring the final connector meets all dimensional and surface specifications requires robust metrology.
- Techniques:
- Coordinate Measuring Machines (CMM): Provide high-accuracy point measurements for verifying critical dimensions, hole locations, and geometric dimensioning and tolerancing (GD&T) callouts.
- 3D Laser Scanning / Structured Light Scanning: Capture dense point clouds of the entire part surface, allowing comparison to the original CAD model to assess overall form deviation and surface characteristics. Useful for complex geometries.
- Surface Profilometers: Contact or non-contact instruments measure surface roughness parameters like Ra, Rz (maximum peak-to-valley height), etc.
- Computed Tomography (CT) Scanning: Provides non-destructive internal inspection, capable of measuring internal features and detecting voids or defects (discussed further under NDT).
Achievable Specifications Summary Table:
Parametre | As-Built (Typical LPBF Ti-6Al-4V) | As-Built (Typical EBM Ti-6Al-4V) | Post-Processed (Machining/Polishing) | Significance for Connectors |
---|---|---|---|---|
Yüzey Pürüzlülüğü (Ra) | 6 – 20 µm | 20 – 40 µm | < 3.2 µm, < 1.6 µm, even < 0.8 µm | Critical for fatigue life, friction, mating surface quality |
General Tolerance | ±0.1 to ±0.3 mm | ±0.2 to ±0.5 mm | ±0.01 to ±0.05 mm (feature dependent) | Ensures proper fit, assembly, alignment |
Özellik Çözünürlüğü | ~0.4 – 0.8 mm | ~0.8 – 1.2 mm | Defined by machining capability | Limits minimum size of printable details (pins, thin walls) |
Sayfalara Aktar
In summary, while metal AM produces the complex near-net shape of the fairing connector, achieving the final, precise dimensions and smooth surface finishes required for reliable aerospace performance necessitates careful planning for, and execution of, post-processing steps, particularly CNC machining and surface finishing. Understanding these achievable limits is crucial for setting realistic design specifications and cost estimates.
Essential Post-Processing Requirements for Titanium Titanium Fairing Connectors
An additively manufactured metal part, upon removal from the build chamber, is rarely ready for its final application, especially not for a critical aerospace component like a rocket fairing connector. A series of essential post-processing steps are required to relieve internal stresses, consolidate the material to full density, remove support structures, achieve the required dimensions and surface finish, and verify integrity. For Ti-6Al-4V and Ti-6Al-4V ELI connectors, these steps typically include:
1. Stress Relief Annealing:
- Amacımız: To significantly reduce the high residual stresses induced during the rapid heating and cooling cycles of the AM process. These stresses, if not relieved, can cause distortion during subsequent machining or even premature failure in service.
- Süreç: The part, often while still attached to the build plate to provide restraint against warping, is heated in a vacuum or inert atmosphere furnace to a specific temperature below the beta transus (the temperature at which the alloy transforms significantly), held for a period (soaking), and then slowly cooled.
- Typical Cycle for Ti-6Al-4V: Temperatures range from 650°C to 850°C (1200°F to 1560°F), with hold times of 1 to 4 hours, followed by furnace cooling or controlled inert gas cooling. The exact cycle depends on the specific AM process used (LPBF vs. EBM) and part geometry.
- Importance: This is a critical first step for dimensional stability and reliable mechanical performance. Skipping or improperly performing stress relief can lead to significant problems downstream.
2. Hot Isostatic Pressing (HIP):
- Amacımız: To eliminate internal microporosity (small voids) that can sometimes remain after the AM process due to factors like gas entrapment or incomplete fusion between layers. Porosity acts as stress concentrators and severely degrades fatigue life and fracture toughness. HIP consolidates the material to near 100% theoretical density.
- Süreç: The part is subjected to both high temperature and high inert gas pressure (typically Argon) simultaneously in a specialized HIP vessel. The pressure collapses internal voids, diffusion bonding the material across the void interface.
- Typical Cycle for Ti-6Al-4V: Temperatures around 900°C to 950°C (1650°F to 1740°F) – often above the stress relief temperature but below the beta transus to maintain a fine grain structure – and pressures of 100 MPa to 200 MPa (15,000 psi to 30,000 psi), held for 2 to 4 hours.
- Avantajlar: Significantly improves ductility, fatigue strength, fracture toughness, and overall material consistency, bringing the properties of AM titanium very close to, or sometimes exceeding, those of traditional wrought material.
- Requirement: HIPing is considered mandatory for most critical aerospace components made via AM, including fairing connectors, to ensure maximum material integrity and reliability.
3. Support Structure Removal & Build Plate Separation:
- Amacımız: To remove the temporary structures used during the build process and separate the part(s) from the metal build plate.
- Yöntemler:
- Manuel Kaldırma: Supports designed to be relatively weak can sometimes be broken off by hand or with simple tools. Care must be taken not to damage the part surface.
- Cutting/Machining: Band saws, grinders, or CNC machining may be used to cut the part from the build plate or remove bulky support structures.
- Tel EDM (Elektrik Deşarjlı İşleme): Often used for precise separation from the build plate or for removing supports in hard-to-reach areas without inducing mechanical stress.
- Zorluklar: Support removal can be labor-intensive and time-consuming, especially for complex geometries with internal supports. Gouging or scarring the part surface is a risk. DfAM principles aimed at minimizing supports are crucial here.
4. CNC Machining:
- Amacımız: To achieve the final dimensional accuracy, tolerances, and surface finishes required on critical features that cannot be met by the as-built AM process.
- Areas Typically Machined:
- Mating surfaces connecting to other fairing segments or structures.
- Bolt holes (drilling/reaming/tapping to precise size and location).
- Alignment features (pins, bores).
- Any surface requiring a specific smooth finish (e.g., Ra < 1.6 µm) for fatigue or sealing purposes.
- Süreç: Utilizes standard CNC milling, turning, or grinding operations. Requires careful fixture design to hold the often complex AM part geometry securely without distortion. Machining strategies must account for the potentially harder or slightly different microstructure of AM materials compared to wrought stock.
5. Surface Finishing:
- Amacımız: To improve the overall surface finish beyond the as-built state, remove marks from support structures, or prepare surfaces for inspection or coating.
- Yöntemler:
- Grit Blasting / Sand Blasting: Provides a uniform matte finish, removes loose particles, and can provide some compressive stress benefit. Different media (alumina, glass beads) produce different finishes.
- Yuvarlama / Vibrasyonlu Son İşlem: Uses abrasive media in a rotating or vibrating drum to deburr edges and smooth surfaces, particularly effective for batches of smaller parts.
- Parlatma: Manual or automated polishing can achieve very smooth, mirror-like finishes where required, although this is labor-intensive.
- Chemical Etching / Electropolishing: Can smooth surfaces but requires careful control and may not be suitable for all geometries or tolerance requirements.
- Anodizing (Type II or Type III): While primarily for corrosion resistance or color-coding in other applications, a thin anodize layer might occasionally be specified for identification or minor wear resistance on certain connector areas.
6. Non-Destructive Testing (NDT) and Inspection:
- Amacımız: To verify the internal and external integrity of the finished connector without damaging it, ensuring it is free from critical defects like cracks, large pores, or inclusions.
- Common NDT Methods for AM Titanium:
- Visual Inspection (VT): Basic inspection for surface defects, damage, or irregularities.
- Liquid Penetrant Inspection (LPI / FPI): Detects surface-breaking cracks or porosity by applying a dye that seeps into defects and is then made visible.
- Radiographic Testing (RT) / Computed Tomography (CT): X-ray based methods used to detect internal defects like porosity, inclusions, or lack-of-fusion voids. CT scanning provides a full 3D view of the internal structure and can also be used for dimensional verification of internal features. CT is becoming increasingly vital for qualifying critical AM parts.
- Ultrasonic Testing (UT): Uses sound waves to detect internal flaws, although complex geometries can make interpretation challenging.
- Final Dimensional Inspection: Using CMM, scanners, or hand gauges to confirm all dimensions and GD&T callouts are within specification after all processing steps.
The specific sequence and combination of these post-processing steps will be defined in the component’s manufacturing plan and must be performed by qualified personnel using certified equipment, especially for aerospace hardware. Partnering with a service provider like Met3dp, who understands these intricate post-processing requirements and has established relationships with certified facilities, is crucial for delivering flight-ready rocket fairing connectors.
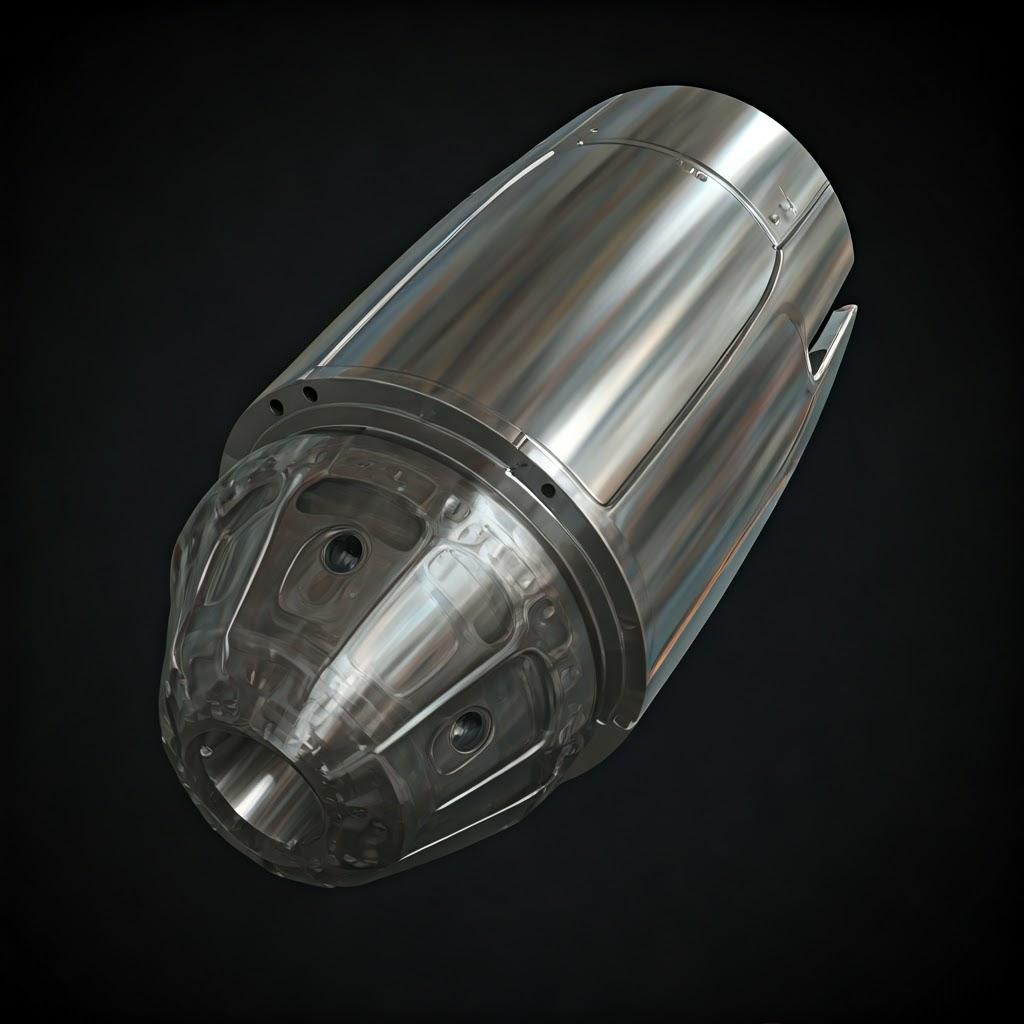
Common Challenges in 3D Printing Fairing Connectors and Mitigation Strategies
While metal AM offers significant advantages, producing high-quality, reliable rocket fairing connectors using this technology is not without its challenges. Understanding these potential issues and implementing effective mitigation strategies during design, simulation, printing, and post-processing is critical for success. Here are some of the most common challenges:
1. Residual Stress and Warping:
- Meydan okumak: As discussed under DfAM, the thermal cycles inherent in AM induce residual stresses. Excessive stress can cause the connector to warp during the build, detach from supports, crack, or distort dimensionally after removal from the build plate. Titanium alloys, with their relatively low thermal conductivity, can be susceptible.
- Mitigation Strategies:
- Simulation: Utilize process simulation software to predict thermal gradients and stress accumulation for a given geometry, orientation, and support strategy. This allows for optimization before printing.
- Optimized Build Orientation: Select an orientation that minimizes large flat areas parallel to the build plate and reduces thermal gradients.
- Sağlam Destek Yapıları: Use well-designed supports (type, density, location) to anchor the part effectively and conduct heat away. Consider stress-reducing support patterns.
- Optimized Scan Strategies: Employ specific laser/electron beam scan patterns (e.g., island scanning, fractal patterns) designed to distribute heat more evenly and reduce localized stress buildup. Machine providers often have proprietary strategies.
- Process Parameter Control: Fine-tuning parameters like laser power, scan speed, and layer thickness can influence thermal history and stress levels.
- Immediate Stress Relief: Perform stress relief annealing as soon as possible after the build, ideally before removing the part from the build plate, to relax internal stresses before they cause significant distortion.
2. Support Structure Removal Difficulties:
- Meydan okumak: Supports, while necessary, can be difficult, time-consuming, and costly to remove, especially if they are located in complex internal channels or intricate external features common in optimized connector designs. Improper removal can damage the part surface, compromising fatigue life or dimensional accuracy.
- Mitigation Strategies:
- DfAM for Support Minimization: Design the connector to be as self-supporting as possible using appropriate angles and fillets.
- Design for Access: Ensure any required supports are placed in locations accessible for removal tools. Avoid “trapped” supports.
- Optimized Support Design: Utilize support types (e.g., thin-walled, conical, lattice supports) that are easier to remove and minimize contact points with the part surface. Software tools often allow customization of support structures.
- Appropriate Removal Techniques: Select the best removal method (manual, machining, wire EDM) based on support location, geometry, and material.
- Sacrificial Features: Sometimes, small features are added to the design specifically to aid support removal or protect the part surface during removal.
3. Porosity (Internal Voids):
- Meydan okumak: Small internal pores can form during the AM process due to trapped gas within the powder, gas evolution from the melt pool, or incomplete fusion between powder particles or layers (Lack of Fusion – LoF). Porosity significantly degrades mechanical properties, particularly fatigue strength and ductility.
- Mitigation Strategies:
- Yüksek Kaliteli Toz: Use high-purity, spherical metal powder with low internal gas porosity and controlled particle size distribution. Sourcing powder from reputable suppliers like Met3dp, who utilize advanced atomization techniques (Gas Atomization, PREP) and rigorous quality control, is crucial. Proper powder handling and storage (e.g., inert atmosphere, controlled humidity) and recycling protocols (sieving to remove contaminants/degraded powder) are also essential.
- Optimize Edilmiş Süreç Parametreleri: Develop and qualify robust process parameters (laser power, scan speed, hatch spacing, layer thickness, atmosphere control) that ensure complete melting and fusion throughout the build. Parameter optimization is key to minimizing both gas and LoF porosity.
- Sıcak İzostatik Presleme (HIP): As previously mentioned, HIP is highly effective at closing internal gas porosity and LoF voids, significantly enhancing material integrity. It is considered essential for critical applications.
- NDT Detection: Utilize CT scanning to detect and characterize internal porosity, ensuring it remains below acceptable limits defined by aerospace standards or component specifications.
4. Surface Finish Imperfections:
- Meydan okumak: Achieving the required smooth surface finish directly via AM is difficult. As-built surfaces can have roughness, partially melted particles, or witness marks from support structures that can act as crack initiation sites under fatigue loading.
- Mitigation Strategies:
- Orientation and Parameter Optimization: While limited, optimizing build orientation and parameters can slightly improve the finish on certain surfaces.
- Post-Processing Finishing: Budget for and implement appropriate surface finishing techniques (machining, polishing, blasting, tumbling) tailored to the specific requirements of different surfaces on the connector.
- Yüzey Pürüzlülüğü Ölçümü: Verify surface finish using profilometry to ensure compliance with specifications.
5. Contamination Control:
- Meydan okumak: Titanium alloys are highly reactive, especially at elevated temperatures. Contamination by oxygen, nitrogen, carbon, or other elements during powder handling, printing, or post-processing can embrittle the material and severely degrade its properties. Cross-contamination between different alloy types in a shared machine is also a risk.
- Mitigation Strategies:
- Inert Atmosphere: Ensure the AM build chamber maintains a high-purity inert atmosphere (typically Argon) with very low oxygen levels (<100-500 ppm, depending on criticality).
- Powder Handling Protocols: Implement strict procedures for handling, storing, loading, and recycling metal powders to prevent atmospheric exposure and cross-contamination. Use dedicated equipment for different materials if possible. Regular powder testing is recommended.
- Machine Cleaning: Thorough cleaning of the build chamber and powder handling systems between different material builds is essential.
- Post-Processing Environment: Control the atmosphere during heat treatment (vacuum or inert gas).
6. Build Failures and Process Monitoring:
- Meydan okumak: AM builds can sometimes fail mid-process due to issues like recoater crashes (interference with a warped part), delamination between layers, insufficient powder deposition, or machine malfunctions. Identifying the root cause is crucial for prevention.
- Mitigation Strategies:
- In-Situ Monitoring: Utilize available monitoring systems (e.g., melt pool monitoring, thermal imaging, layer imaging) to detect anomalies during the build in real-time.
- Robust Process Planning: Careful build setup, validated parameters, and preventative machine maintenance.
- Root Cause Analysis: Implement procedures for investigating any build failures to identify and correct the underlying cause (e.g., support strategy, parameters, machine issue, powder quality).
- Experienced Provider: Working with an experienced AM service provider like Met3dp, which has robust process controls, quality management systems, and skilled operators, significantly reduces the risk of build failures.
Addressing these challenges requires a combination of careful design, process simulation, high-quality materials and equipment, meticulous process control, thorough post-processing, and rigorous quality assurance. While demanding, overcoming these hurdles allows the aerospace industry to harness the transformative benefits of AM for producing next-generation rocket fairing connectors.
How to Choose the Right Metal 3D Printing Service Provider for Aerospace Components
Selecting the right additive manufacturing partner is paramount when dealing with flight-critical aerospace components. The supplier’s capabilities, quality systems, and expertise directly impact the reliability, performance, and airworthiness of the final part. Simply choosing the provider with the lowest quote or fastest advertised lead time can be detrimental. A rigorous evaluation process is necessary, focusing on several key areas:
1. Aerospace Certifications and Quality Management System (QMS):
- AS9100 Certification: This is the internationally recognized QMS standard for the aviation, space, and defense industries. It incorporates ISO 9001 requirements along with additional criteria specific to aerospace quality, safety, and reliability. Possession of a current AS9100 certification is often a non-negotiable requirement for suppliers manufacturing flight hardware. It demonstrates a commitment to rigorous process control, traceability, risk management, and continuous improvement.
- ISO 9001: A foundational quality management standard. While good, it typically lacks the specific aerospace focus of AS9100.
- NADCAP Accreditations: The National Aerospace and Defense Contractors Accreditation Program provides specific process accreditations. Look for NADCAP accreditation for special processes the provider performs or manages, such as:
- Heat Treating
- Tahribatsız Muayene (NDT)
- Materials Testing
- Welding (relevant if post-AM assembly is needed)
- Machining (less common, but available)
- Robust QMS: Beyond certifications, evaluate the provider’s internal QMS documentation, process control procedures, operator training programs, equipment calibration schedules, and systems for managing non-conformances and corrective actions.
2. Technical Expertise and Engineering Support:
- DfAM Expertise: Does the provider offer Design for Additive Manufacturing support? Can their engineers review your connector design and provide feedback on manufacturability, optimal orientation, support strategies, and potential topology optimization or lattice integration? This collaborative approach is invaluable.
- Materials Science Knowledge: Deep understanding of the metallurgy of titanium alloys (Ti-6Al-4V, ELI) and how AM processing affects microstructure and mechanical properties is crucial. They should understand the nuances of different AM technologies (LPBF vs. EBM) and their impact on material characteristics.
- Process Simulation: Does the provider utilize process simulation software to predict thermal behavior, residual stress, and potential distortion önce printing? This proactive approach can save significant time and cost by avoiding build failures.
- Parameter Development: For novel or highly critical applications, does the provider have experience developing and qualifying custom process parameters tailored to specific performance requirements?
3. Equipment, Technology, and Capacity:
- Makine Yetenekleri: What specific AM machines do they operate (e.g., EOS, SLM Solutions, Concept Laser/GE Additive, Arcam/GE Additive)? Are these machines well-maintained and calibrated? Do they have experience with the specific technology best suited for your connector (LPBF often offers finer features and finish, while EBM can be faster for bulkier parts and may result in lower residual stress)?
- Yapı Hacmi: Ensure their machines have a large enough build envelope to accommodate the size of your fairing connector(s).
- Material Dedication: Does the provider dedicate specific machines to particular materials (especially reactive ones like titanium) to prevent cross-contamination? This is a critical quality control aspect.
- In-Situ Monitoring: Do their machines incorporate melt pool monitoring, thermal sensors, or layer imaging capabilities? While not foolproof, these tools can provide valuable data for quality assurance and early detection of build anomalies.
- Capacity and Redundancy: Do they have sufficient machine capacity to meet your required lead times? Do they have multiple machines capable of running your part to provide redundancy in case of maintenance or unexpected downtime?
4. Material Capabilities and Handling:
- Malzeme Portföyü: Do they routinely process Ti-6Al-4V and Ti-6Al-4V ELI to aerospace standards (e.g., AMS specifications)? What other relevant aerospace materials do they offer?
- Powder Sourcing and Quality Control: Where do they source their metal powders? Do they have stringent incoming quality checks for powder chemistry, particle size distribution (PSD), morphology, and flowability? Do they partner with reputable powder manufacturers known for high quality, like Met3dp, which employs advanced gas atomization and PREP technologies?
- Powder Handling and Traceability: What are their procedures for powder storage (inert environment), handling, loading, sieving, and recycling? Robust protocols are essential to prevent contamination and ensure lot-to-lot consistency. Full material traceability from raw powder batch to finished part is mandatory for aerospace.
5. Post-Processing Capabilities:
- In-House vs. Managed Network: Does the provider have in-house capabilities for critical post-processing steps like stress relief, HIP, support removal, CNC machining, surface finishing, and NDT? If not, do they have a well-managed network of qualified and certified (e.g., NADCAP) subcontractors? Managing a complex supply chain for post-processing requires significant expertise.
- Uzmanlık alanı: Ensure they (or their partners) have specific expertise in post-processing AM titanium parts, which can behave differently from wrought materials during machining or heat treatment.
6. Experience and Track Record:
- Aerospace Experience: Have they successfully produced similar aerospace components, particularly structural parts or flight hardware? Can they provide relevant case studies or references (within confidentiality limits)?
- Problem Solving: Ask about their experience overcoming common AM challenges (warping, porosity, etc.) for demanding applications.
7. Communication, Project Management, and Support:
- Responsiveness: Are they communicative and responsive to inquiries and technical questions?
- Project Management: Do they assign a dedicated point of contact or project manager? How do they handle project tracking and reporting?
- Şeffaflık: Are they transparent about their processes, capabilities, and potential risks or challenges?
8. Location and Logistics:
- Proximity: While not always the primary factor, proximity can sometimes simplify logistics, communication, and site audits.
- Shipping and Handling: Do they have experience securely packaging and shipping sensitive, high-value aerospace components?
Met3dp as a Potential Partner:
Şirketler gibi Met3dp exemplify many of these desired qualities. With headquarters specializing in both additive manufacturing equipment (including SEBM printers known for processing titanium effectively) and the production of high-performance metal powders (Ti-6Al-4V, Ti-6Al-4V ELI, and others via advanced atomization), they possess deep materials and process expertise. Their focus on industry-leading print accuracy and reliability, combined with decades of collective expertise in metal AM, positions them as a knowledgeable partner. While evaluating any provider requires due diligence against all the criteria above, a company with end-to-end understanding from powder creation to printing solutions offers significant advantages.
Choosing the right AM service provider is a strategic decision. A thorough evaluation based on these criteria will help ensure that your 3D printed rocket fairing connectors meet the demanding quality, reliability, and performance standards required for successful space missions.
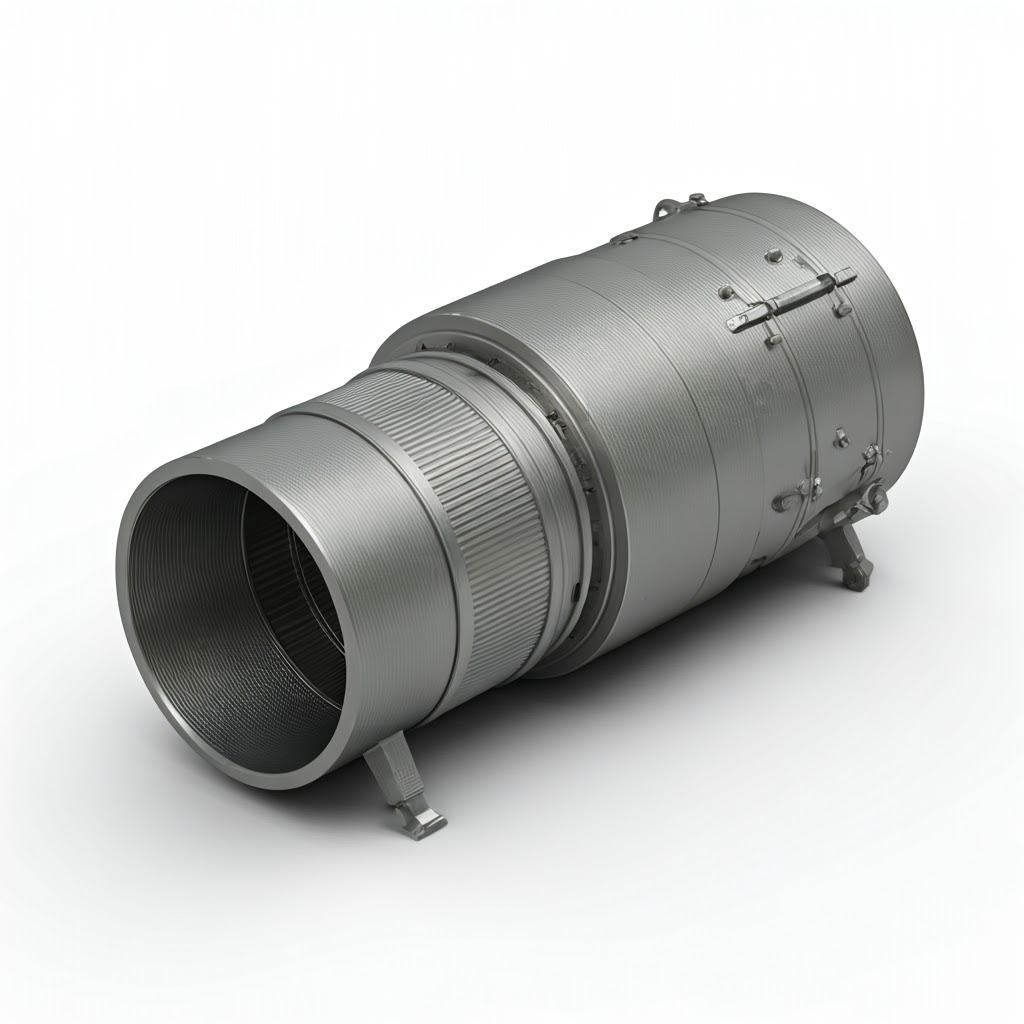
Understanding Cost Factors and Lead Times for 3D Printed Fairing Connectors
While additive manufacturing offers compelling technical benefits, understanding the associated costs and typical lead times is crucial for project planning, budgeting, and comparing AM to traditional manufacturing methods. The cost structure for metal AM parts like fairing connectors is influenced by several interacting factors:
Key Cost Drivers:
- Malzeme Maliyeti:
- Powder Price: Aerospace-grade titanium powders (Ti-6Al-4V, ELI) are inherently expensive due to the energy-intensive extraction and advanced atomization processes required. Cost is typically calculated per kilogram. ELI grades are generally more expensive than standard Grade 5 due to higher purity requirements.
- Part Volume & Density: The amount of powder directly consumed in building the part (including any sacrificial features) is a primary cost component. Topology optimization and lattice structures directly reduce this.
- Support Structure Volume: Material used for supports also adds to the cost, reinforcing the need for DfAM to minimize them.
- Powder Recycling/Refresh Rate: While unfused powder can often be sieved and reused, there’s typically a refresh rate (adding a percentage of virgin powder) and eventual retirement of powder batches, the cost of which is factored in. The efficiency of powder reuse impacts overall material cost per part.
- Buy-to-Fly Ratio: Although significantly better than machining, the AM buy-to-fly ratio (total powder consumed including supports vs. final part weight) still influences cost.
- Makine Zamanı (İnşa Zamanı):
- Machine Depreciation & Operation: High-value metal AM machines have significant capital costs, maintenance requirements, and operational expenses (power, inert gas, consumables). These are amortized into an hourly machine rate.
- Build Height: Primarily determines the number of layers required. More layers mean longer build time.
- Part Volume/Area per Layer: The volume or cross-sectional area that needs to be scanned (melted) by the laser or electron beam on each layer dictates the time spent scanning per layer. Complex geometries or multiple parts nested together increase this time.
- Scan Strategy & Parameters: Scan speed, hatch spacing, layer thickness, and recoating time all influence the overall build speed. Thinner layers improve resolution but increase build time significantly.
- Nesting Efficiency: Printing multiple connectors (or other parts) simultaneously in one build (nesting) can improve machine utilization and reduce cost per part, provided the build height isn’t excessively increased.
- İşçilik Maliyetleri:
- Build Preparation: CAD file processing, build layout planning, support structure generation, machine setup. Requires skilled technicians/engineers.
- Machine Operation/Monitoring: While largely automated, builds require supervision.
- Part Removal & Cleaning: Extracting parts from the build chamber, removing bulk powder.
- Destek Kaldırma: Often a manual or semi-automated process, can be very labor-intensive depending on complexity.
- Post-Processing & Finishing: Labor associated with heat treatment, HIP loading/unloading, machining setup/operation, manual polishing, inspection.
- İşlem Sonrası Maliyetler:
- Stress Relief & Heat Treatment: Furnace time, energy, inert gas/vacuum costs.
- Sıcak İzostatik Presleme (HIP): This is a specialized and often expensive process performed by dedicated facilities. Cost depends on cycle time and vessel volume utilization.
- CNC İşleme: Cost of programming, fixturing, machine time, tooling for achieving final tolerances and finishes.
- Yüzey İşlemi: Costs associated with blasting, tumbling, polishing, etc.
- Tahribatsız Muayene (NDT): Costs for LPI, CT scanning, UT based on equipment usage and technician interpretation time. CT scanning, while invaluable, can be costly.
- Quality Assurance and Documentation:
- Inspection Labor: Time spent on dimensional checks (CMM, scanning), visual inspection.
- Documentation: Generating material certifications, traceability records, inspection reports required for aerospace compliance adds overhead.
- Enerji Tüketimi: Metal AM processes, particularly EBM and the associated powder production and post-processing steps (furnaces, HIP), are energy-intensive.
Ölçek Ekonomileri: Unlike injection molding or casting, AM doesn’t typically have massive tooling costs to amortize. However, economies of scale still apply:
- Machine Utilization: Printing multiple parts per build reduces the setup cost per part.
- Powder Batch Size: Larger powder purchases can sometimes yield slightly lower per-kg costs.
- Post-Processing Batches: Processing multiple parts together in heat treatment, HIP, or finishing can reduce the per-part cost of these steps. However, the primary cost driver often remains the machine time and material consumption per individual part. Significant cost reduction usually comes from design optimization (reducing volume/height/supports) rather than just increasing batch size.
Lead Time Factors:
Lead time for a 3D printed fairing connector, from order placement to delivery of a finished, inspected part, can vary significantly but is often considerably shorter than traditional methods involving complex tooling or forging procurement. Typical lead times might range from 2 to 8 weeks, but this depends heavily on:
- Tasarım Karmaşıklığı: More complex parts may require more intricate support planning and longer build/post-processing times.
- Build Preparation & Queue Time: Time required for file prep, build simulation, and waiting for machine availability (provider’s backlog).
- Print Time: Actual duration of the AM build (can range from hours to several days depending on size/complexity/nesting).
- Post-Processing Duration: This is often the largest component of the lead time.
- Stress relief/Heat Treatment: 1-2 days (including furnace cycles).
- HIP: Can take several days, including shipping to/from a specialized facility and the cycle time itself (often run in batches).
- Support Removal & Machining: Highly variable, from days to weeks depending on complexity and shop scheduling.
- NDT & Inspection: Days, depending on methods required and reporting.
- Nakliye: Time for final delivery.
Factors Reducing Lead Time:
- Optimized DfAM (minimal supports, reduced build height/volume).
- Provider capacity and efficient scheduling.
- In-house post-processing capabilities (eliminates shipping time between steps).
- Streamlined QA procedures.
Requesting Quotes: When requesting quotes for 3D printed fairing connectors, provide a detailed package including:
- Final CAD model (native and STL/3MF).
- Detailed 2D drawings with all dimensions, GD&T, material specifications (Ti-6Al-4V or ELI, specific AMS standard), required surface finishes, and NDT callouts.
- Specification of all required post-processing steps (Stress Relief, HIP, Machining details, Finishing).
- Required certifications (AS9100 compliance, material certs, certificate of conformance).
- Quantity needed and desired delivery date.
Clear and comprehensive information allows providers to generate accurate quotes and realistic lead time estimates. Understanding these cost and time components helps in making informed decisions about adopting AM for aerospace applications.
Frequently Asked Questions (FAQ) about 3D Printed Rocket Fairing Connectors
1. How does the strength of 3D printed Ti-6Al-4V compare to traditionally wrought or machined Ti-6Al-4V?
When properly processed using optimized parameters and subjected to mandatory post-processing like Stress Relief and Hot Isostatic Pressing (HIP), the mechanical properties (Tensile Strength, Yield Strength, Elongation, Fatigue Strength) of additively manufactured Ti-6Al-4V (both Grade 5 and Grade 23 ELI) can be highly comparable, and sometimes even slightly superior in certain aspects (like yield strength), to standard wrought annealed Ti-6Al-4V. HIP is crucial for closing internal porosity, which significantly boosts ductility and fatigue life, bringing AM material properties in line with aerospace requirements. However, properties can be anisotropic (directionally dependent) based on build orientation, which must be considered in design and testing. Rigorous material testing and qualification are always necessary for flight hardware.
2. Is metal additive manufacturing certified for producing flight-critical hardware like fairing connectors?
Yes, metal AM processes and materials, including Ti-6Al-4V produced via LPBF and EBM, are increasingly being certified and used for flight-critical applications in aerospace, including structural components on launch vehicles, satellites, and aircraft. Achieving flight qualification is a rigorous process involving:
- Mature Process Control: Demonstrating stable, repeatable manufacturing processes.
- Material Characterization: Extensive testing to establish material property allowables according to industry standards (e.g., MMPDS, AMS specs).
- Certified Suppliers: Utilizing AS9100 certified providers with robust QMS.
- Part-Specific Qualification: Often involves building and destructively testing initial parts, extensive NDT, and demonstrating that the final component meets all performance and reliability requirements defined by the launch provider or regulatory body (e.g., NASA, FAA). Many organizations have successfully flown AM titanium structural parts.
3. Is 3D printing generally cheaper than CNC machining for producing rocket fairing connectors?
It depends heavily on several factors:
- Karmaşıklık: For highly complex geometries achieved through topology optimization or requiring intricate internal features, AM can be significantly cheaper because machining such features would be extremely difficult, time-consuming, or impossible.
- Parça Konsolidasyonu: If AM allows multiple machined parts to be consolidated into one printed part, the savings in assembly time, fasteners, and potential failure points can outweigh a potentially higher per-part AM cost.
- Malzeme Atıkları: For expensive materials like titanium, the significantly better buy-to-fly ratio of AM compared to subtractive machining often leads to substantial raw material cost savings, making AM more cost-effective, especially for complex parts where machining waste would be high.
- Hacim: For very simple connector designs produced in high volumes, traditional CNC machining might still be cheaper due to faster cycle times once set up. However, fairing connectors are often complex and produced in relatively low volumes (tens or hundreds per vehicle), scenarios where AM often shines.
- Lead Time Value: The significantly reduced lead time offered by AM can have intrinsic value, enabling faster development cycles or meeting tight launch schedules, which might justify a higher per-part cost. A detailed cost analysis comparing AM (including all post-processing) with the traditional method for the specific connector design is necessary.
4. Besides Ti-6Al-4V, what other metal materials could potentially be used for 3D printing fairing connectors?
While Ti-6Al-4V (Grades 5 & 23) is the dominant choice due to its excellent balance of properties, other materials processed via AM could be considered depending on specific requirements:
- High-Strength Aluminum Alloys (e.g., Scalmalloy®, AlSi10Mg): Offer lower density than titanium but also lower strength and temperature capability. Suitable for less demanding connector applications where weight saving is paramount and loads/temperatures are lower. Scalmalloy® offers significantly higher strength than traditional printable aluminum alloys.
- Stainless Steels (e.g., 17-4PH, 316L): Stronger and stiffer than aluminum, cheaper than titanium, but also significantly heavier. May be used in specific locations where high strength is needed and weight is less critical, or for ground support equipment interfacing with the fairing. 17-4PH offers high strength after heat treatment.
- Nickel-Based Superalloys (e.g., Inconel 718, 625): Offer excellent strength at elevated temperatures, far exceeding titanium or aluminum. Typically overkill and too heavy/expensive for fairing connectors unless there’s an unusual localized high-temperature requirement. More common in engine components. For most fairing connector applications balancing strength, stiffness, low weight, and fatigue resistance, Ti-6Al-4V remains the optimal choice currently available for metal AM.
5. How can you verify the integrity of complex internal features or lattice structures created by AM?
This is a critical challenge addressed by Non-Destructive Testing (NDT), primarily X-Ray Computed Tomography (CT) Scanning. CT scanning creates a full 3D reconstruction of the part, allowing engineers to:
- Visualize Internal Geometries: Check if internal channels are clear of powder and match the design intent.
- Inspect Lattice Structures: Verify the integrity of lattice struts and nodes.
- Detect Internal Defects: Identify porosity, inclusions, or lack-of-fusion defects deep within the part that other NDT methods might miss.
- Perform Metrology: Measure internal dimensions and wall thicknesses non-destructively. CT scanning is becoming an indispensable tool for qualifying complex AM parts with internal features, providing a high degree of confidence in their structural integrity.
Conclusion: Advancing Space Exploration with Additively Manufactured Titanium Connectors
The journey to space remains one of humanity’s most challenging and inspiring endeavors. Success hinges on optimizing every single component for performance, reliability, and efficiency. Rocket fairing connectors, though perhaps small components in the grand scheme of a launch vehicle, play an undeniably critical role in protecting valuable payloads and ensuring mission success.
Metal additive manufacturing, particularly using robust and lightweight titanium alloys like Ti-6Al-4V and its high-purity ELI variant, represents a significant leap forward in how these vital connectors can be designed and produced. The advantages are clear and compelling:
- Benzersiz Tasarım Özgürlüğü: Enabling topology-optimized and lattice structures for maximum lightweighting without compromising strength.
- Parça Konsolidasyonu: Reducing assembly complexity, weight, and potential failure points.
- Azaltılmış Teslim Süreleri: Accelerating development cycles and improving responsiveness to launch schedules.
- Improved Material Efficiency: Minimizing waste of expensive aerospace materials through near-net shape production.
- Geliştirilmiş Performans: Achieving mechanical properties comparable or superior to traditional methods through careful process control and post-processing like HIP.
However, realizing these benefits requires a holistic approach. It demands embracing Design for Additive Manufacturing (DfAM) principles, understanding the nuances of achievable tolerances and surface finishes, implementing crucial post-processing steps like heat treatment and HIP, and diligently addressing potential manufacturing challenges through robust process control and quality assurance.
Critically, success depends on choosing the right partners. This includes selecting high-quality, aerospace-grade metal powders from expert manufacturers and collaborating with experienced AM service providers who possess the necessary certifications (AS9100), technical expertise, validated processes, and comprehensive capabilities spanning design support through final inspection.
Met3dp stands at the forefront of this technological advancement, offering both industry-leading metal AM systems and high-performance spherical metal powders, including Ti-6Al-4V, manufactured using state-of-the-art atomization techniques. Our deep expertise in materials science and additive manufacturing processes enables us to support aerospace clients in leveraging AM technology to its fullest potential.
By embracing metal 3D printing for components like fairing connectors, the aerospace industry can continue to push the boundaries of launch vehicle performance, reduce costs, and accelerate the pace of space exploration and commercialization. It’s a technology that doesn’t just offer incremental improvements; it enables fundamentally new approaches to designing and building the vehicles that will carry us further into the final frontier.
Ready to explore how additive manufacturing can optimize your critical aerospace components? Contact the experts at Met3dp today to discuss your project requirements and learn how our advanced metal powders and AM solutions can elevate your manufacturing capabilities.
Paylaş
MET3DP Technology Co, LTD, merkezi Qingdao, Çin'de bulunan lider bir katmanlı üretim çözümleri sağlayıcısıdır. Şirketimiz, endüstriyel uygulamalar için 3D baskı ekipmanları ve yüksek performanslı metal tozları konusunda uzmanlaşmıştır.
İşletmeniz için en iyi fiyatı ve özelleştirilmiş Çözümü almak için sorgulayın!
İlgili Makaleler
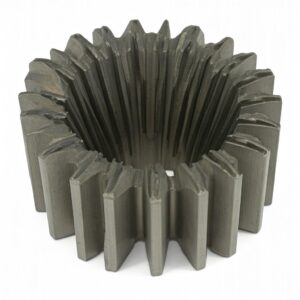
Yüksek Performanslı Nozul Kanat Segmentleri: Metal 3D Baskı ile Türbin Verimliliğinde Devrim
Daha Fazla Oku "Met3DP Hakkında
Son Güncelleme
Bizim Ürünümüz
BİZE ULAŞIN
Herhangi bir sorunuz var mı? Bize şimdi mesaj gönderin! Mesajınızı aldıktan sonra tüm ekibimizle talebinize hizmet edeceğiz.
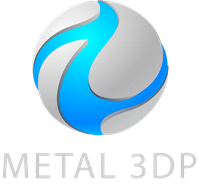
3D Baskı ve Katmanlı Üretim için Metal Tozları