Electric Motor Shaft Housings via Metal 3D Printing
İçindekiler
Introduction – EV Motor Shaft Housings: The Core of Electric Mobility
The automotive industry is undergoing a seismic shift, driven by the relentless pursuit of electrification. Electric vehicles (EVs) are rapidly transitioning from niche products to mainstream transportation, reshaping not only how we drive but also how vehicles are designed, engineered, and manufactured. At the heart of this revolution lies the electric powertrain, a complex system where every component plays a critical role in delivering efficiency, performance, and reliability. Among these crucial elements is the EV Motor Shaft Housing, a component often overlooked yet fundamentally essential to the electric motor’s function and longevity.
An EV motor shaft housing serves as the protective enclosure and structural support for the motor’s rotating shaft and associated bearings. It ensures precise alignment, shields delicate internal components from environmental hazards (like debris, moisture, and contaminants), aids in thermal management by dissipating heat generated during operation, and provides mounting points for integrating the motor into the larger vehicle chassis and powertrain assembly. As EV technology advances, demanding higher power densities, increased efficiency, and more compact designs, the requirements placed upon components like the motor shaft housing become increasingly stringent. They must be lightweight to maximize vehicle range, strong enough to withstand operational stresses and vibrations, durable for long service life, and precisely manufactured to maintain tight tolerances critical for optimal motor performance.
Traditionally, these housings have been produced using methods like casting (die casting, sand casting) or extensive CNC machining from billet material. While effective, these conventional processes often face limitations, particularly when addressing the complex geometries, lightweighting opportunities, and rapid development cycles characteristic of the modern EV landscape. This is where metal katkılı üretim (AM), commonly known as metal 3D printing, emerges as a transformative technology. Metal AM offers unprecedented design freedom, enabling the creation of highly optimized, complex, and lightweight structures that are difficult or impossible to produce using traditional methods. It facilitates rapid prototyping and iteration, significantly accelerating development timelines, and allows for part consolidation, potentially reducing assembly complexity and overall system weight. For components like EV motor shaft housings, metal 3D printing presents a compelling value proposition, enabling manufacturers to push the boundaries of performance, efficiency, and innovation in electric mobility. Companies at the forefront of this technology, like Met3dp, are providing the advanced equipment and high-performance materials needed to realize the full potential of AM in demanding automotive applications. This exploration delves into the intricacies of leveraging metal 3D printing for EV motor shaft housings, examining the applications, benefits, materials, and considerations involved in adopting this cutting-edge manufacturing approach.
Applications and Functions: Where are EV Motor Shaft Housings Used?
The EV motor shaft housing is far more than just a simple cover; it’s a multi-functional component integral to the performance, reliability, and integration of the electric motor within the vehicle’s powertrain. Its design and execution directly impact motor efficiency, noise, vibration, harshness (NVH), thermal stability, and overall durability. Understanding its diverse functions highlights why optimizing its design and manufacturing process is so critical for EV manufacturers.
Key Functions and Applications:
- Structural Support and Alignment:
- Bearing Support: The housing provides precise mounting locations for the bearings that support the motor shaft. Accurate alignment is crucial to minimize friction, wear, and vibration, ensuring smooth rotation and maximizing motor lifespan. Misalignment can lead to premature bearing failure and reduced motor efficiency.
- Component Mounting: It acts as a rigid structure for mounting other motor components, such as sensors (position sensors, temperature sensors), encoders, and sometimes parts of the cooling system.
- Powertrain Integration: The housing features mounting points (flanges, bosses, bolt holes) for securely attaching the motor assembly to the gearbox, differential, or vehicle subframe. It must withstand the static and dynamic loads associated with vehicle operation, including torque reaction, acceleration, braking, and road-induced vibrations.
- Protection and Sealing:
- Environmental Shielding: The housing forms a barrier protecting the sensitive motor internals (rotor, stator windings, bearings, shaft) from environmental elements like dust, dirt, water spray, humidity, and road debris. This protection is vital for preventing corrosion, electrical shorts, and mechanical damage.
- Containment: It contains lubricants necessary for bearing function and prevents leakage, which could lead to component failure and environmental contamination. Effective sealing (often using gaskets or sealants in conjunction with precisely machined mating surfaces) is paramount.
- Termal Yönetim:
- Heat Dissipation: Electric motors generate significant heat during operation, particularly under high loads. The housing plays a role in conducting heat away from the motor core (stator and windings) and bearings to the surrounding environment or a dedicated cooling system (liquid or air). The material’s thermal conductivity and the housing’s surface area are important factors.
- Integration with Cooling Systems: Advanced housing designs, often enabled by AM, can incorporate integrated cooling channels for liquid cooling systems or optimized fin structures for enhanced air cooling. This allows for more effective thermal management, enabling higher power density and sustained performance without overheating.
- Noise, Vibration, and Harshness (NVH) Reduction:
- Stiffness and Damping: The housing’s structural rigidity influences the motor’s NVH characteristics. A stiff housing helps minimize vibrations originating from the motor’s electromagnetic forces and rotating components. The material choice and geometry can also contribute to damping vibrations, leading to a quieter and smoother driving experience – a key selling point for EVs.
- Acoustic Enclosure: To some extent, the housing acts as an acoustic barrier, helping to contain noise generated by the motor and gearbox.
Industry Context:
The EV motor shaft housing finds its application across the spectrum of electric vehicles, including:
- Battery Electric Vehicles (BEVs): From compact city cars to luxury sedans and high-performance sports cars.
- Plug-in Hybrid Electric Vehicles (PHEVs): Housing components for the electric motor part of the hybrid powertrain.
- Hybrid Electric Vehicles (HEVs): Similar applications within hybrid systems.
- Electric Commercial Vehicles: Including vans, trucks, and buses, where durability and reliability are paramount.
- Electric Two-Wheelers and Other Mobility Devices: Although often simpler, the fundamental principles apply.
As EV architectures evolve (e.g., in-wheel motors, integrated e-axles), the design and integration of motor housings become even more complex and critical, further favouring the design flexibility offered by additive manufacturing. The need for tailored solutions for specific vehicle platforms, performance targets, and packaging constraints makes AM an increasingly attractive option for producing these vital components.
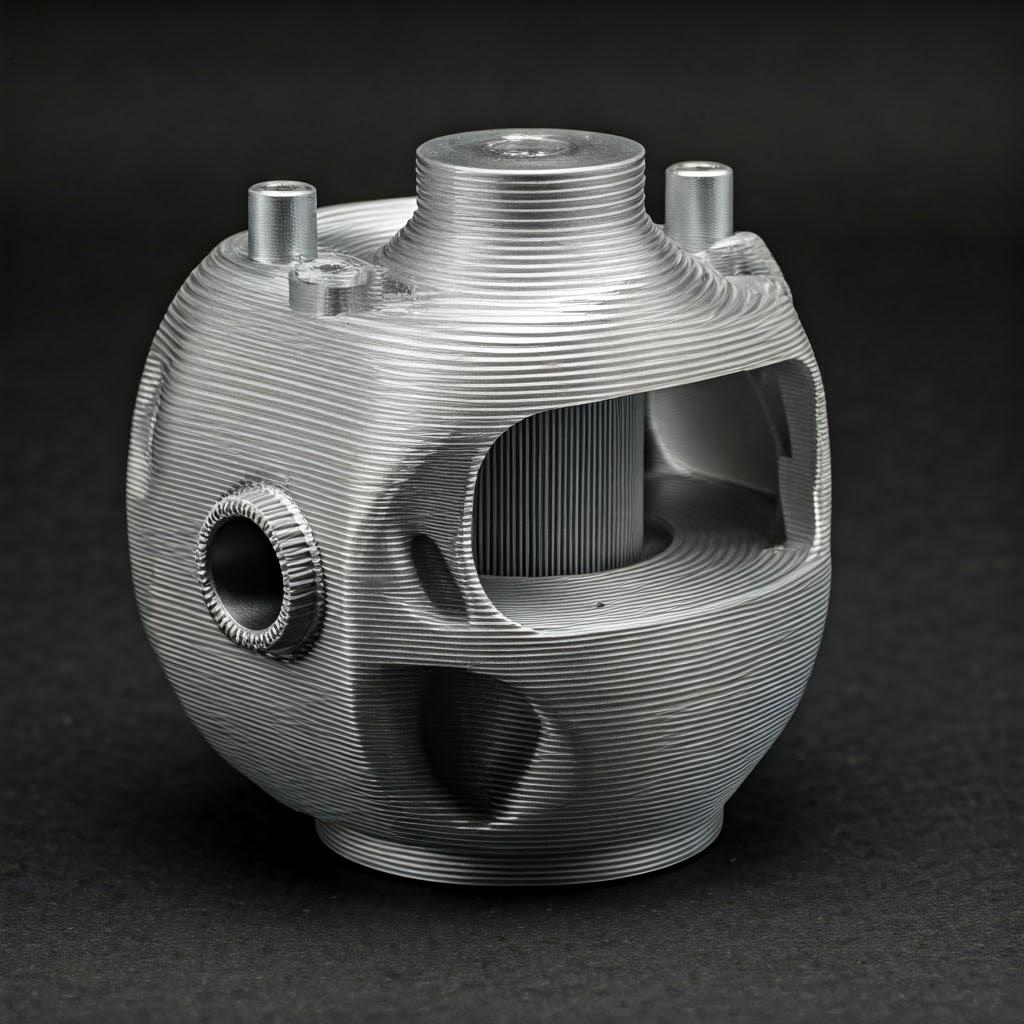
Why Choose Metal 3D Printing for EV Motor Shaft Housings?
While traditional manufacturing methods like casting and machining have served the automotive industry well for decades, the unique demands of electric vehicle development are pushing engineers to explore more advanced production techniques. Metal additive manufacturing offers a suite of compelling advantages specifically suited to the challenges and opportunities presented by EV motor shaft housings. Comparing AM to conventional methods reveals why it’s rapidly gaining traction:
Metal AM vs. Traditional Manufacturing for EV Motor Shaft Housings:
Özellik | Metal Additive Manufacturing (e.g., LPBF, EBM) | Traditional Casting (e.g., Die Casting) | Traditional Machining (from Billet) |
---|---|---|---|
Tasarım Karmaşıklığı | Very High: Enables intricate internal features (cooling channels, lattice structures), organic shapes, topology optimization. | Moderate: Limited by mold draft angles, cores, and wall thickness constraints. Internal channels complex/costly. | Moderate to High: Dependent on machine axes and tooling access. Deep pockets or complex internal features difficult/expensive. |
Hafifletme | Excellent: Topology optimization and lattice structures allow significant weight reduction while maintaining stiffness. Material placed only where needed. | Good: Possible through material choice (e.g., aluminum) and basic ribbing, but limited by process constraints. | Fair: Weight reduction primarily through material removal, less efficient than topology optimization. Significant material waste. |
Parça Konsolidasyonu | High Potential: Multiple components (e.g., brackets, mounts, channel covers) can be integrated into a single printed part, reducing assembly time, joints, and potential leak paths. | Limited: Possible to some extent, but constrained by mold complexity. | Very Limited: Generally produces single, monolithic parts. Consolidation requires separate joining processes. |
Speed (Prototyping) | Very Fast: Ideal for rapid iteration and functional prototypes. Design changes implemented quickly without tooling. | Slow: Requires significant lead time for mold design and fabrication. Modifications are costly and time-consuming. | Moderate to Fast: Faster than casting for simple prototypes, but complex parts require extensive programming and setup. |
Speed (Production) | Moderate: Scaling requires multiple machines. Best suited for low-to-medium volumes or highly complex parts currently. Improving rapidly. | Very Fast: Excellent for high-volume production once tooling is established. Low per-part cost at scale. | Slow to Moderate: Dependent on complexity and volume. Can be costly for high volumes due to machine time and material waste. |
Kalıp Maliyetleri | None: Direct digital manufacturing eliminates the need for molds, dies, or specific fixtures. | Very High: Significant upfront investment in tooling. Economical only for large production runs. | Low to Moderate: Requires standard cutting tools and fixtures, but no part-specific hard tooling like molds. |
Malzeme Atıkları | Low: Uses powder material primarily where needed. Unfused powder is typically recycled within the process. | Moderate: Runners, gates, and flashing generate waste, though often recyclable. | High: Subtractive process inherently generates significant chip waste (swarf), especially for complex geometries starting from large billets. |
Malzeme Seçenekleri | Growing Range: Various alloys (Al, Ti, Steel, Ni-based) available, including custom alloys. Met3dp offers a wide portfolio. | Established Range: Primarily Al, Mg, Zn alloys for die casting; Fe, Steel, Al for sand casting. | Widest Range: Virtually any machinable metal bar/block stock can be used. |
İç Özellikler | Excellent: Complex internal cooling channels, passages, and lightweight structures easily created. | Difficult/Costly: Requires complex cores, inserts, or post-machining. | Very Difficult/Impossible: Limited access for cutting tools restricts complex internal geometry. |
Sayfalara Aktar
Key Advantages Summarized:
- Eşsiz Tasarım Özgürlüğü: Engineers can design the optimal housing based on performance requirements (structural, thermal, NVH) rather than being constrained by manufacturing limitations. This allows for:
- Topology Optimization: Algorithms determine the most efficient material distribution to meet load requirements, drastically reducing weight.
- Integrated Features: Cooling channels, sensor mounts, fluid passages, and complex surfaces can be built directly into the part.
- Organic Shapes: Smooth, complex curvatures optimized for flow (coolant or air) or stress distribution.
- Hızlı Prototipleme ve Yineleme: New designs or modifications can be printed and tested within days, compared to weeks or months for tooling changes in casting. This accelerates the EV development cycle significantly.
- Hafifletme: Crucial for extending EV range. AM enables housing designs that are 30-50% lighter than conventionally produced counterparts while maintaining or even increasing stiffness and performance.
- Parça Konsolidasyonu: Reducing the number of components in the motor assembly simplifies logistics, decreases assembly time and cost, eliminates potential failure points (like seals or fasteners), and can further reduce weight.
- On-Demand & Customized Production: Enables production of small batches, customized versions for different vehicle models, or spare parts without the need for large inventories or costly tooling.
- Improved Thermal Management: The ability to integrate complex, conformal cooling channels directly within the housing walls allows for highly efficient heat dissipation, critical for maintaining optimal operating temperatures in high-power density motors.
While metal AM might have higher per-part costs for very high volumes compared to established casting methods today, the overall benefits – particularly in terms of performance gains, development speed, and design optimization – make it an increasingly strategic choice for critical EV components like motor shaft housings, especially during development, low-to-mid volume production, and for high-performance applications. Accessing advanced metal 3D baskı çözümleri empowers manufacturers to innovate faster and create superior EV powertrains.
Material Matters: Selecting the Right Metal Powders (AlSi10Mg & 17-4PH)
The performance, durability, and cost-effectiveness of a 3D printed EV motor shaft housing are heavily dependent on the choice of material. Selecting the appropriate metal powder is crucial for meeting the demanding requirements of automotive applications. Two commonly recommended materials for this application, each offering a distinct set of properties, are AlSi10Mg (an aluminum alloy) ve 17-4PH (a precipitation-hardening stainless steel). Leading providers like Met3dp offer high-quality versions of these powders, specifically optimized for additive manufacturing processes.
1. AlSi10Mg (Aluminum-Silicon-Magnesium Alloy)
AlSi10Mg is one of the most widely used aluminum alloys in metal additive manufacturing, particularly Laser Powder Bed Fusion (LPBF/SLM). It’s essentially a casting alloy composition adapted for AM, known for its excellent balance of mechanical properties, low density, and good processability.
- Key Properties & Benefits for EV Motor Housings:
- Düşük Yoğunluk: Aluminum alloys are significantly lighter than steels (approx. 2.68 g/cm³ for AlSi10Mg vs. ~7.8 g/cm³ for 17-4PH). This translates directly into ağırlık tasarrufu for the housing, contributing to increased vehicle range and efficiency – a primary goal in EV design.
- Good Thermal Conductivity: Aluminum alloys generally offer good thermal conductivity (around 130-150 W/m·K after stress relief for AM AlSi10Mg), which is advantageous for dissipating heat generated by the motor. This aids in thermal management, potentially simplifying cooling system requirements.
- Excellent Processability: AlSi10Mg is well-understood and relatively easy to process using LPBF systems, allowing for fine details, thin walls, and complex geometries. It generally results in parts with good surface finish (as-built) compared to some other metals.
- İyi Güç-Ağırlık Oranı: While not as strong as steel, AlSi10Mg offers a very favourable strength-to-weight ratio, providing sufficient mechanical integrity for many housing applications after appropriate heat treatment (e.g., T6).
- Korozyon Direnci: Offers adequate corrosion resistance for typical automotive under-hood or powertrain environments, although coatings may be considered for enhanced protection in harsh conditions.
- Maliyet-Etkinlik: Aluminum powder is generally more cost-effective than specialized stainless steels or titanium alloys.
- Düşünceler:
- Lower absolute strength and stiffness compared to steel. Design may require thicker sections or reinforcing features (ribs, optimized topology) to achieve the same rigidity as a steel part.
- Lower operating temperature limits compared to steel. May not be suitable for extremely high-temperature motor designs without careful thermal management.
- Requires appropriate post-processing (stress relief and typically a T6 heat treatment) to achieve optimal mechanical properties and dimensional stability.
2. 17-4PH Stainless Steel (Precipitation-Hardening Martensitic Stainless Steel)
17-4PH (AISI 630) is a versatile chromium-nickel-copper stainless steel known for its excellent combination of high strength, good corrosion resistance, and toughness. It can be hardened to high levels through a single, low-temperature heat treatment (precipitation hardening or aging).
- Key Properties & Benefits for EV Motor Housings:
- Yüksek Mukavemet ve Sertlik: Significantly stronger and harder than aluminum alloys, especially after heat treatment (e.g., Condition H900). This allows for thinner wall sections while maintaining structural integrity and provides excellent wear resistance for bearing seats or mounting interfaces.
- İyi Korozyon Direnci: Offers superior corrosion resistance compared to AlSi10Mg, making it suitable for more demanding environments or where exposure to corrosive fluids is a concern.
- Higher Operating Temperatures: Maintains good mechanical properties at elevated temperatures compared to aluminum, offering a larger design margin for thermal management.
- Good Toughness: Exhibits good resistance to fracture, important for components subjected to shock loads or vibrations.
- Kaynaklanabilirlik: Can be welded if necessary, although less common for AM parts.
- Düşünceler:
- Higher Density: Significantly heavier than aluminum (almost 3 times denser). Using 17-4PH will result in a heavier housing unless aggressive topology optimization is employed, potentially offsetting some of the lightweighting benefits of AM.
- Lower Thermal Conductivity: Has significantly lower thermal conductivity (around 16-18 W/m·K) compared to aluminum. This means heat dissipation through the housing itself will be less effective, potentially requiring more sophisticated integrated cooling channels or external cooling solutions.
- İşleme Zorlukları: Can be more challenging to process via LPBF than AlSi10Mg, potentially requiring more careful parameter optimization to control residual stresses and achieve optimal density. Support structures may be more difficult to remove.
- Daha Yüksek Malzeme Maliyeti: 17-4PH powder is typically more expensive than AlSi10Mg powder.
Choosing Between AlSi10Mg and 17-4PH:
The optimal choice depends heavily on the specific requirements of the EV motor and vehicle platform:
- Seçin AlSi10Mg when:
- Lightweighting is the absolute top priority.
- Operating temperatures are moderate.
- Good thermal conductivity is desired for passive heat dissipation.
- Cost is a significant driver.
- Sufficient structural performance can be achieved through design optimization.
- Seçin 17-4PH when:
- Maximum strength, stiffness, and durability are required.
- The housing experiences high mechanical loads or wear at interfaces.
- Operating temperatures are elevated.
- Superior corrosion resistance is necessary.
- Weight is a secondary concern, or significant lightweighting can be achieved through topology optimization despite the higher density.
- Lower thermal conductivity can be compensated for by integrated cooling design.
The Importance of Powder Quality:
Regardless of the alloy chosen, the quality of the metal powder is paramount for successful additive manufacturing. Factors like:
- Parçacık Boyutu Dağılımı (PSD): Affects powder bed density, flowability, and final part resolution.
- Küresellik: Highly spherical powders flow better and pack more densely, leading to higher quality prints with fewer voids.
- Kimyasal Bileşim: Must adhere strictly to specifications to ensure predictable material properties.
- Low Impurity Levels (e.g., Oxygen, Nitrogen): Impurities can negatively impact mechanical properties and weldability.
- Akışkanlık: Crucial for uniform powder spreading during the printing process.
Şirketler gibi Met3dp specialize in producing high-quality metal powders tailored for AM processes like LPBF and Electron Beam Melting (EBM). Their utilization of advanced techniques like Vacuum Induction Melting Gas Atomization (VIGA) ve Plazma Dönen Elektrot Prosesi (PREP) ensures the production of powders like AlSi10Mg and 17-4PH with high sphericity, controlled PSD, low impurity content, and excellent flowability. Using powders from a reputable Tedarikçi like Met3dp provides confidence in material consistency and performance, which is critical for demanding applications like EV motor shaft housings where reliability and quality are non-negotiable. Their expertise ensures that the foundational material meets the rigorous standards required for automotive component manufacturing.
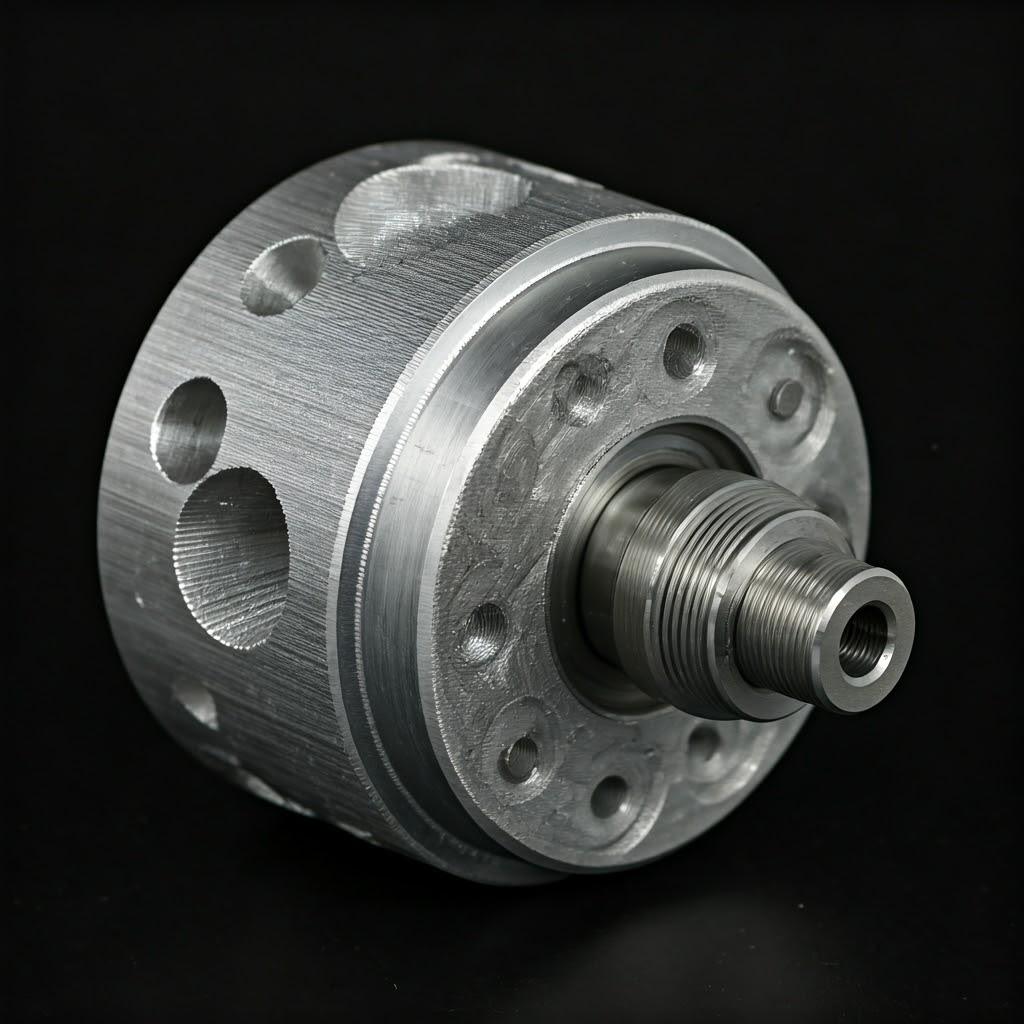
Design for Additive Manufacturing (DfAM) for Optimal EV Motor Shaft Housings
Simply replicating a design intended for casting or machining using metal 3D printing often fails to leverage the technology’s true potential and can even introduce new challenges. To fully exploit the benefits of additive manufacturing for components like EV motor shaft housings, engineers must embrace Katmanlı Üretim Tasarımı (DfAM) principles. DfAM is a design philosophy that considers the capabilities and constraints of the AM process from the outset, enabling the creation of parts that are not only manufacturable but also highly optimized for performance, weight, and function. Applying DfAM to EV motor shaft housings can unlock significant improvements.
Key DfAM Principles for EV Motor Shaft Housings:
- Topology Optimization:
- Concept: Using specialized software algorithms, topology optimization mathematically determines the most efficient material distribution within a defined design space, subject to specific load cases, constraints (e.g., mounting points, keep-out zones), and performance targets (e.g., minimize weight, maximize stiffness).
- Uygulama: For a motor housing, this means removing material from low-stress areas while reinforcing critical load paths. This often results in organic, bone-like structures that are significantly lighter (often 30-60% weight reduction) than traditional designs but possess equivalent or superior stiffness and strength. This is paramount for improving EV range.
- Düşünceler: Optimized designs can be complex and may require validation through simulation (FEA). Manufacturing constraints of the chosen AM process (e.g., minimum feature size, overhang angles) must be incorporated into the optimization setup.
- Kafes Yapılar ve Dolgu:
- Concept: Replacing solid volumes with internal lattice structures (e.g., gyroids, honeycombs, stochastic foams) can further reduce weight and material consumption while maintaining significant structural support or providing other functional benefits like vibration damping or enhanced surface area for heat exchange.
- Uygulama: Internal lattices can be selectively used within thicker sections of the housing walls to reduce mass without compromising overall rigidity. They can also be designed to absorb impact energy or dampen vibrations, improving NVH performance.
- Düşünceler: Lattice design requires careful analysis to ensure structural integrity. Powder removal from complex internal lattices can be challenging and must be planned for (e.g., designing sufficient drain/access holes).
- Parçaların Birleştirilmesi:
- Concept: Leveraging AM’s ability to build complex geometries, multiple components that would traditionally be manufactured separately and then assembled (e.g., housing body, mounting brackets, sensor holders, cooling channel covers) can be integrated into a single, monolithic printed part.
- Uygulama: Integrating brackets directly onto the housing eliminates fasteners, seals, and assembly steps. Cooling circuit components can be merged into the main body.
- Avantajlar: Reduces part count, simplifies supply chain and assembly, lowers assembly labor costs, eliminates potential leak paths or failure points at joints, and can further reduce overall weight.
- Integrated Functional Features:
- Concept: Designing features directly into the AM part that enhance its functionality.
- Application – Conformal Cooling Channels: Perhaps one of the most significant advantages for motor housings. AM allows the creation of complex cooling channels that precisely follow the contours of heat-generating areas (like stator interfaces or bearing seats) within the housing walls. This “conformal cooling” is far more effective than traditional drilled channels, enabling better thermal management, higher motor power density, and potentially eliminating the need for separate cooling jackets.
- Application – Sensor Mounts & Cable Routing: Precisely shaped mounting points for sensors, integrated channels or clips for cable management can be built directly into the housing structure.
- Application – Fluid Passages: Ports and passages for lubrication or coolant ingress/egress can be seamlessly integrated.
- Designing for Support Minimization:
- Concept: Laser Powder Bed Fusion (LPBF) typically requires support structures for overhanging features (usually below 45 degrees from the horizontal plane) to prevent distortion and anchor the part to the build plate. These supports consume extra material, add print time, and require removal in post-processing, which can be labor-intensive and potentially damage surfaces. DfAM aims to minimize or eliminate the need for supports.
- Techniques:
- Orientation Optimization: Selecting the optimal build orientation to minimize the extent of overhangs.
- Kendini Destekleyen Açılar: Designing overhangs with angles greater than the critical threshold (typically >45 degrees).
- Chamfers and Fillets: Replacing sharp horizontal edges with angled or curved surfaces (chamfers/fillets) can make features self-supporting.
- Sacrificial Features: Incorporating features specifically designed to support critical geometries during the build, which are then easily machined away during post-processing.
- Tear-Drop Shapes: Modifying circular horizontal holes into self-supporting tear-drop or diamond shapes.
- Powder Removal Considerations:
- Concept: Unfused metal powder must be removed from the finished part, especially from internal channels and cavities. Trapped powder adds weight and can pose a functional risk.
- Design Strategies: Include strategically placed drain/access holes in the design to allow easy removal of powder after printing, particularly from internal cooling channels or lattice structures. Ensure internal passages are smooth and large enough to prevent powder blockage.
- Minimum Wall Thickness and Feature Size:
- Concept: Each AM process and material has limitations on the minimum wall thickness and feature size (e.g., pins, holes) that can be reliably produced.
- Uygulama: Ensure housing walls, ribs, and integrated features meet the minimum manufacturable dimensions (e.g., typically >0.4-0.5 mm for LPBF, though thicker is often more robust). Consult the specifications of the AM system being used, like those offered by Met3dp.
By systematically applying these DfAM principles, engineers can transform the EV motor shaft housing from a standard enclosure into a highly optimized, lightweight, and functionally integrated component. This requires a shift in thinking, moving beyond the constraints of traditional methods and fully embracing the geometric freedom offered by additive manufacturing. Collaborating with AM experts, such as the team at Met3dp, during the design phase can provide valuable insights into process capabilities and help maximize the benefits of DfAM for specific baskı yöntemleri.
Achieving Precision: Tolerance, Surface Finish, and Accuracy in 3D Printed Housings
While metal additive manufacturing offers incredible design freedom, achieving the necessary precision for functional components like EV motor shaft housings is critical. Aspects like dimensional accuracy, achievable tolerances on critical features (like bearing seats and mating flanges), and surface finish directly impact the performance, assembly, and longevity of the electric motor. Understanding what precision levels are typically achievable with metal AM is essential for setting realistic expectations and planning necessary post-processing steps.
Key Aspects of Precision in Metal AM:
- Boyutsal Doğruluk:
- Tanım: How closely the dimensions of the printed part match the nominal dimensions specified in the CAD model.
- Achievable Levels: Typical dimensional accuracy for metal AM processes like LPBF is often cited in the range of ±0.1 mm to ±0.2 mm for smaller dimensions (e.g., up to 100 mm), and around ±0.1% to ±0.2% for larger dimensions. However, this is highly dependent on several factors:
- Part Size and Geometry: Larger parts and complex geometries are more prone to thermal stresses during printing, which can cause warping and deviation.
- Yapı Oryantasyonu: How the part is oriented on the build plate affects thermal gradients, support requirements, and potential distortion.
- Malzeme: Different materials have different thermal properties and shrinkage rates.
- Machine Calibration: Accurate laser spot size, scanner calibration, and layer thickness control are crucial. High-quality machines, like those developed by Met3dp known for their industry-leading print volume, accuracy and reliability, are essential.
- Termal Yönetim: Controlling the temperature within the build chamber minimizes stress.
- İşlem sonrası: Stress relief heat treatments are vital for relaxing internal stresses and improving dimensional stability.
- Hafifletme: Careful design (DfAM), simulation of the build process, optimized build parameters, proper support strategies, and post-print stress relief are key to maximizing dimensional accuracy.
- Tolerances:
- Tanım: The permissible range of variation for a specific dimension. Critical features on a motor housing, such as bearing bore diameters, shaft seal surfaces, pilot diameters, and flange face flatness, require tight tolerances for proper function.
- As-Built vs. Post-Processed: Metal AM processes typically achieve tolerances comparable to investment casting, often within the range of ISO 2768-m (medium) or sometimes ISO 2768-f (fine) for as-built parts. However, achieving the very tight tolerances required for bearing fits (e.g., H7) or sealing surfaces usually necessitates post-process machining (CNC milling, turning, grinding) of those specific features.
- Typical Values:
- As-Built (LPBF): ±0.1 mm to ±0.3 mm common, potentially tighter on small features.
- Post-Machined Features: Tolerances of ±0.01 mm to ±0.05 mm or even tighter can be achieved, depending on the machining process.
- Strategy: Design the AM part with sufficient machining stock (e.g., 0.5 mm to 1.0 mm) on critical surfaces that require tight tolerances. The bulk of the complex geometry is created by AM, while precision machining delivers the final tolerance on key interfaces.
- Yüzey İşlemi (Pürüzlülük):
- Tanım: The measure of the fine-scale texture of a surface, often quantified by the average roughness (Ra). Surface finish affects friction, wear, sealing capability, and fatigue life.
- As-Built Finish: The as-built surface finish of LPBF parts is inherently rougher than machined surfaces due to the layer-by-layer fusion of powder particles.
- Top Surfaces: Generally smoother (Ra 5-15 µm).
- Vertical Walls: Moderate roughness (Ra 10-20 µm).
- Down-Facing/Supported Surfaces: Roughest surfaces (Ra 15-30 µm or more), often showing witness marks from support structures.
- Internal Channels: Can be difficult to finish and typically retain a rougher surface.
- Influence Factors: Layer thickness, laser parameters, powder particle size, and build orientation all influence as-built roughness. Materials like AlSi10Mg often yield slightly better finishes than steels in LPBF.
- Post-Processing for Improved Finish: Various methods can improve surface finish:
- Boncuk Kumlama / Kumlama: Provides a uniform matte finish, removes partially melted particles (improves Ra to ~5-10 µm).
- Yuvarlama / Vibrasyonlu Son İşlem: Uses media to smooth surfaces and edges, effective for batches of parts (can achieve Ra ~1-5 µm).
- Elektro parlatma: Electrochemical process that removes a thin layer of material, resulting in a very smooth and clean surface (Ra < 1 µm possible).
- CNC İşleme: Provides the best surface finish on specific features requiring smoothness (e.g., sealing faces, bearing bores, Ra < 0.8 µm easily achievable).
- Manual Polishing: Labor-intensive but can achieve mirror finishes if required.
Achievable Precision Summary Table (Typical Values for LPBF):
Parametre | As-Built Durum | After Machining (Specific Features) | After Surface Treatment (Overall) | Notlar |
---|---|---|---|---|
Boyutsal Doğruluk | ±0.1 to ±0.2 mm (or ±0.1-0.2%) | N/A (Defined by machining) | Largely unchanged | Highly dependent on size, geometry, material, process control. |
Toleranslar | ISO 2768-m / -f (approx.) | H7, ±0.01 – ±0.05 mm (or tighter) | Largely unchanged | Tight tolerances require machining. |
Yüzey Pürüzlülüğü (Ra) | 5 – 30 µm | < 0.8 µm (or better) | 1 – 10 µm (Blasting/Tumbling) | Varies significantly with surface orientation (top, side, supported). |
< 1 µm (Polishing) |
Sayfalara Aktar
Conclusion on Precision: While metal AM may not match the inherent precision of high-end CNC machining across the entire part in its as-built state, it provides a highly accurate net shape. By combining the geometric freedom of AM with targeted post-process machining on critical interfaces, manufacturers can achieve the required precision for demanding applications like EV motor shaft housings, benefiting from lightweighting and design optimization without compromising functional tolerances. Partnering with an AM provider like Met3dp, equipped with precise machines and robust quality control processes, is essential for achieving reliable and accurate results.
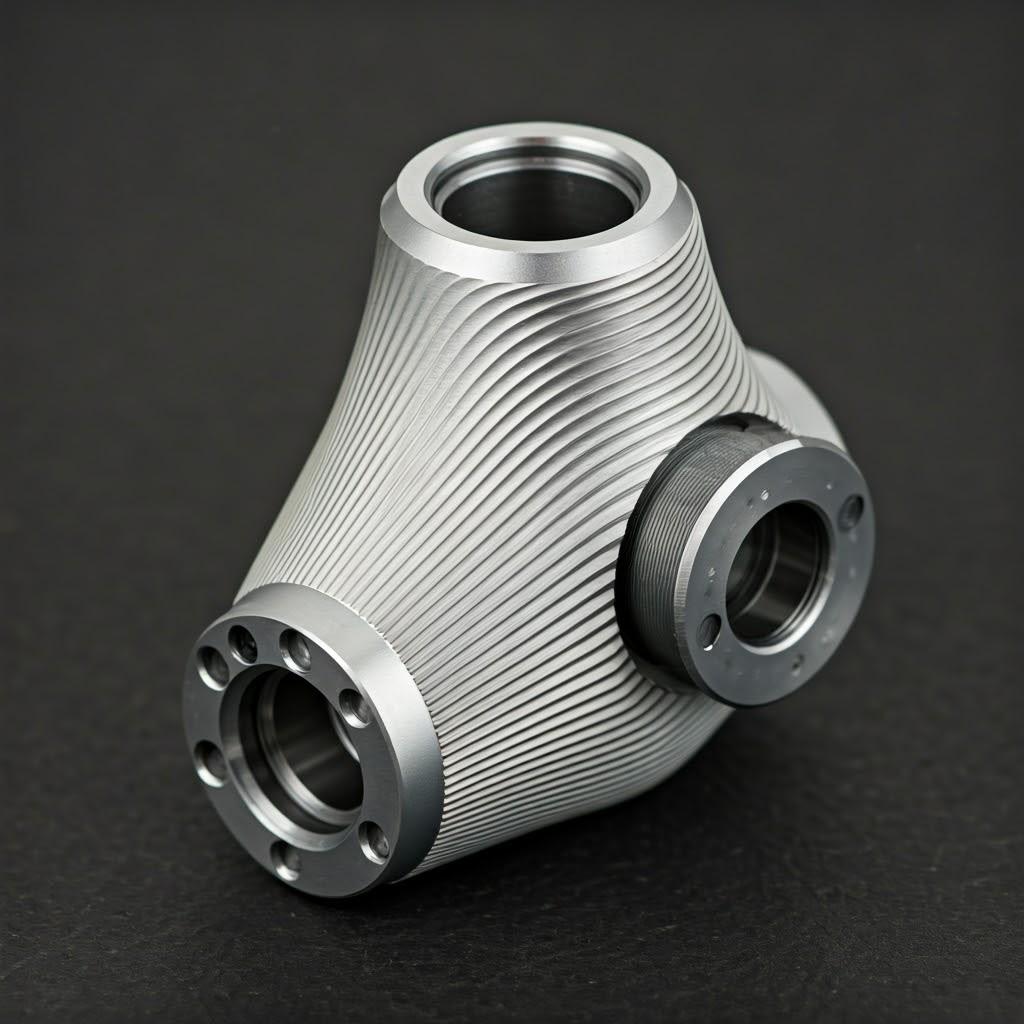
Beyond Printing: Essential Post-Processing for EV Motor Shaft Housings
The additive manufacturing build process is just the first step in creating a functional EV motor shaft housing. Once the part emerges from the printer, a series of crucial post-processing steps are required to transform the raw print into a finished component ready for assembly. These steps are necessary to relieve internal stresses, remove support structures, achieve required tolerances and surface finishes on critical features, and ensure the overall quality and reliability of the housing. The specific steps and their sequence can vary depending on the material (AlSi10Mg vs. 17-4PH), design complexity, and application requirements.
Common Post-Processing Workflow for Metal AM Housings:
- Powder Removal / Depowdering:
- Objective: Remove all loose, unfused metal powder from the part, especially from internal channels, cavities, and complex lattice structures.
- Yöntemler: Manual brushing, compressed air blow-off, vibration, ultrasonic cleaning (sometimes in a solvent bath). Careful design (DfAM) with adequate drain holes is crucial for effective depowdering of internal features like cooling channels. Automated depowdering stations are increasingly used for production.
- Importance: Trapped powder adds weight, can interfere with function (e.g., block cooling channels), and can become loose during operation. Complete removal is critical.
- Stress Relief Heat Treatment:
- Objective: Relieve internal stresses built up during the rapid heating and cooling cycles of the layer-by-layer printing process. These stresses can cause warping, distortion, and cracking during or after printing, particularly when removing the part from the build plate or during subsequent machining.
- Yöntemler: Performed while the part is often still attached to the build plate (especially for larger/complex parts) in an inert atmosphere furnace (e.g., Argon) to prevent oxidation. Typical cycles involve heating to a specific temperature below the material’s aging or annealing temperature, holding for a period, and then slowly cooling.
- AlSi10Mg: Typically ~300°C for 2 hours.
- 17-4PH: Typically ~600-650°C (sub-critical anneal) for 1-2 hours.
- Importance: Absolutely essential for dimensional stability, preventing distortion during support removal/machining, and improving overall part integrity.
- Yapı Plakasından Parça Çıkarma:
- Objective: Separate the printed housing(s) from the build plate.
- Yöntemler: Wire EDM (Electrical Discharge Machining) is common for precise, low-force cutting. Bandsawing or manual cutting may be used for less critical applications or specific geometries.
- Düşünceler: Must be done carefully to avoid damaging the part. Stress relief beforehand minimizes the risk of the part warping upon release from the plate’s constraint.
- Destek Yapısının Kaldırılması:
- Objective: Remove the temporary support structures required during the build process.
- Yöntemler: Supports are typically designed with weaker interfaces for easier removal. Methods include:
- Manual Break-off: Using pliers, chisels, or hand tools (suitable for accessible supports).
- İşleme: Milling or grinding away support structures, especially in critical or hard-to-reach areas.
- Wire EDM: Can sometimes be used for precise removal.
- Importance: Supports are non-functional and must be removed. The process can leave witness marks or rough patches (“nubs”) on the part surface that may require further finishing. DfAM aims to minimize the need for complex support removal.
- Solution Annealing & Aging Heat Treatment (Precipitation Hardening):
- Objective: Develop the final desired mechanical properties (strength, hardness, toughness) of the material.
- Yöntemler: This is a multi-step process, particularly critical for materials like AlSi10Mg and 17-4PH.
- AlSi10Mg (T6 Temper): Involves solution treatment (heating to ~515-535°C to dissolve precipitates), quenching (rapid cooling, often in water), and artificial aging (reheating to a lower temperature, ~160-175°C, for several hours) to precipitate hardening phases. This significantly increases strength and hardness.
- 17-4PH (e.g., H900, H1025, H1150): Typically supplied in the solution annealed condition (Condition A). Aging involves heating to a specific temperature (e.g., 482°C for H900, 552°C for H1025, 621°C for H1150) for 1-4 hours to achieve the desired balance of strength, toughness, and corrosion resistance. Lower aging temperatures yield higher strength but lower toughness.
- Importance: Tailors the material properties to meet the performance requirements of the housing. Must be performed after stress relief and major support removal but often before final machining to account for any minor dimensional changes.
- CNC İşleme:
- Objective: Achieve tight tolerances, specific surface finishes, and precise geometric features on critical interfaces.
- Applications for Housings:
- Bearing Bores/Seats: Machining to precise diameters and tolerances (e.g., H7) with smooth surface finish for proper bearing fit and function.
- Mating Flanges: Facing operations to ensure flatness and achieve required surface finish for sealing against gearboxes or other components.
- Seal Grooves/Surfaces: Machining grooves for O-rings or creating smooth surfaces for dynamic seals.
- Threaded Holes: Tapping or thread milling mounting holes.
- Pilot Diameters: Ensuring accurate diameters and concentricity for alignment with mating parts.
- Yöntemler: 3-axis or 5-axis CNC milling, turning (if geometry allows), grinding. Requires careful fixture design to hold the potentially complex AM part securely without distortion.
- Importance: Bridges the gap between AM’s net-shape capability and the high precision required for functional interfaces.
- Surface Finishing & Cleaning:
- Objective: Improve overall surface quality, remove contaminants, enhance appearance, or apply protective coatings.
- Yöntemler:
- Deburring: Removing sharp edges or burrs left from printing or machining.
- Bead Blasting / Shot Peening: Creates a uniform matte finish, cleans surfaces, can improve fatigue life (shot peening induces compressive stress).
- Yuvarlama / Vibrasyonlu Son İşlem: Smooths surfaces and edges, good for batches.
- Parlatma: For achieving very smooth surfaces where required (e.g., aesthetic reasons or specific sealing applications).
- Passivation (for 17-4PH): Chemical treatment to enhance the natural corrosion resistance of stainless steel by removing free iron and forming a thicker passive oxide layer.
- Anodizing / Conversion Coating (for AlSi10Mg): Provides enhanced corrosion protection and can offer a wear-resistant surface.
- Painting / Powder Coating: For aesthetics and additional environmental protection.
- Final Cleaning: Ensuring the part is free from machining fluids, blast media, fingerprints, and other contaminants before assembly.
- Importance: Ensures the final part meets aesthetic, functional (sealing, wear), and environmental resistance requirements.
- Inspection and Quality Control (QC):
- Objective: Verify that the finished housing meets all design specifications, dimensional tolerances, material properties, and quality standards.
- Yöntemler:
- Boyutsal Muayene: Using CMMs (Coordinate Measuring Machines), 3D scanners, calipers, micrometers to verify critical dimensions and tolerances.
- Tahribatsız Muayene (NDT): CT scanning (Computed Tomography) is invaluable for inspecting internal features (like cooling channels for blockages), detecting internal porosity or defects, and verifying wall thicknesses without destroying the part. Dye penetrant testing or magnetic particle testing can check for surface cracks.
- Material Property Verification: Hardness testing. Tensile testing on representative sample coupons printed alongside the part. Chemical analysis verification.
- Leak Testing: Pressurizing the housing (especially if it contains cooling channels or needs to seal lubricants) to check for leaks.
- Importance: Essential for ensuring the reliability and safety of a critical automotive component. Provides traceability and documentation.
The specific sequence and necessity of these steps must be carefully planned. For instance, machining is typically done after heat treatments that might cause distortion, but before surface finishing processes like blasting or anodizing. Effective post-processing is as critical as the printing process itself for delivering high-quality, functional metal AM components.
Overcoming Challenges in 3D Printing EV Motor Shaft Housings
While metal additive manufacturing offers transformative potential for EV motor shaft housings, it’s not without its challenges. Successfully implementing AM requires understanding these potential hurdles and employing strategies to mitigate them. Addressing these challenges is crucial for achieving consistent quality, reliability, and cost-effectiveness, particularly when moving from prototypes to series production.
Common Challenges and Mitigation Strategies:
- Residual Stress, Warping, and Distortion:
- Meydan okumak: The rapid, localized heating and cooling inherent in LPBF/EBM creates significant thermal gradients, leading to internal stresses within the part. These stresses can cause the part to warp during printing, crack, or distort upon removal from the build plate or during post-processing (especially heat treatment or machining). Large, flat sections or sharp transitions in thickness are particularly susceptible.
- Mitigation Strategies:
- Optimized Part Orientation: Orienting the part to minimize large cross-sectional areas per layer and reduce thermal gradients.
- Sağlam Destek Yapıları: Designing effective supports to anchor the part securely to the build plate, conduct heat away, and counteract shrinkage forces. Specialized software can help optimize support generation.
- Süreç Parametre Optimizasyonu: Fine-tuning laser power, scan speed, and hatching strategies to minimize thermal input and stress accumulation. Utilizing island scanning or other advanced scan patterns.
- Plaka Isıtması Oluşturun: Maintaining an elevated temperature in the build chamber/plate reduces the severity of thermal gradients.
- Termal Simülasyon: Using simulation software to predict stress distribution and potential distortion, allowing for design modifications or compensation factors before printing.
- Zorunlu Stres Giderici: Performing a stress relief heat treatment cycle immediately after printing and often before removing the part from the build plate is critical for relaxing stresses and ensuring dimensional stability.
- Gözeneklilik:
- Meydan okumak: The presence of small voids or pores within the printed material. Porosity can degrade mechanical properties (especially fatigue strength and ductility), compromise leak-tightness, and act as crack initiation sites. Causes include trapped gas within the powder, insufficient energy density leading to incomplete melting, keyholing effects (vapor depressions collapsing), or poor powder quality/handling.
- Mitigation Strategies:
- Yüksek Kaliteli Toz: Using powder with controlled particle size distribution, high sphericity, low internal gas porosity, and proper handling to avoid moisture absorption is crucial. Sourcing from reputable suppliers like Met3dp, known for their advanced powder making systems, is key.
- Optimize Edilmiş Süreç Parametreleri: Ensuring sufficient energy density (laser power, speed, layer thickness) for full melting and fusion between layers, without excessive energy that causes keyholing or spatter.
- Inert Atmosphere Control: Maintaining a high-purity inert gas atmosphere (Argon or Nitrogen) in the build chamber minimizes oxidation and reactions that can lead to gas porosity.
- Sıcak İzostatik Presleme (HIP): A post-processing step involving high temperature and high pressure (using an inert gas). HIP can effectively close internal pores, significantly increasing density (often to >99.9%) and improving mechanical properties, particularly fatigue life. Often considered for critical components requiring maximum reliability, though it adds cost and time.
- NDT Inspection: Using CT scanning to detect and quantify internal porosity levels.
- Support Removal Difficulties:
- Meydan okumak: Removing support structures, especially from internal channels, complex geometries, or delicate features, can be time-consuming, labor-intensive, and risks damaging the part surface. Inaccessible internal supports may be impossible to remove completely.
- Mitigation Strategies:
- DfAM for Support Minimization: Designing parts with self-supporting angles, using fillets/chamfers, optimizing orientation, and leveraging topology optimization can drastically reduce the need for supports.
- Optimized Support Design: Using support structures with lower density, specific geometries (e.g., tree supports), and easily breakable connection points. Software tools can automate optimized support generation.
- Accessible Design: Ensuring adequate access for tools if manual removal is required. Designing internal channels large enough and smooth enough for powder/support removal.
- Machinable Supports: Designing supports in locations where they can be easily removed via CNC machining during post-processing.
- Malzeme Seçimi: Some materials may require more robust supports than others.
- Achieving Leak-Tightness:
- Meydan okumak: For housings containing cooling channels or needing to seal lubricants, ensuring leak-tightness is paramount. Porosity, micro-cracks, or surface finish issues on sealing faces can lead to leaks.
- Mitigation Strategies:
- Achieving High Density: Optimizing print parameters and potentially using HIP to minimize porosity.
- DfAM for Sealing: Designing appropriate grooves for O-rings or specifying smooth, flat mating surfaces. Ensuring sufficient wall thickness around fluid passages.
- Post-Process Machining: Machining sealing faces to achieve the required flatness and surface finish.
- Surface Treatments/Impregnation: In some cases, sealant impregnation processes can be used to seal minor residual porosity (though less ideal than achieving density inherently).
- Rigorous Leak Testing: Implementing pressure decay or immersion leak testing as part of the QC process.
- Cost-Effectiveness for Series Production:
- Meydan okumak: While excellent for prototypes and complex parts, the per-part cost of metal AM can be higher than traditional methods like casting for very high volumes due to factors like machine throughput, powder cost, and necessary post-processing.
- Mitigation Strategies:
- Tasarım Optimizasyonu: Maximizing lightweighting and part consolidation benefits to offset higher manufacturing costs through improved performance or reduced assembly costs.
- Nesting and Build Optimization: Printing multiple parts simultaneously on a single build plate to maximize machine utilization.
- Otomasyon: Implementing automated solutions for powder handling, depowdering, and post-processing steps to reduce labor costs.
- Process Efficiency Improvements: Utilizing faster machines, optimizing parameters for speed (while maintaining quality), and reducing support structure volume.
- Targeted Application: Focusing AM on applications where its benefits (complexity, lightweighting, speed-to-market) provide the highest value proposition, complementing traditional methods for simpler, high-volume parts.
- Collaboration: Working closely with experienced AM service providers like Met3dp who have optimized workflows and economies of scale can help manage costs effectively.
By proactively addressing these challenges through careful design, process control, material selection, and post-processing strategies, manufacturers can confidently leverage metal 3D printing to produce high-performance, reliable, and increasingly cost-effective EV motor shaft housings.
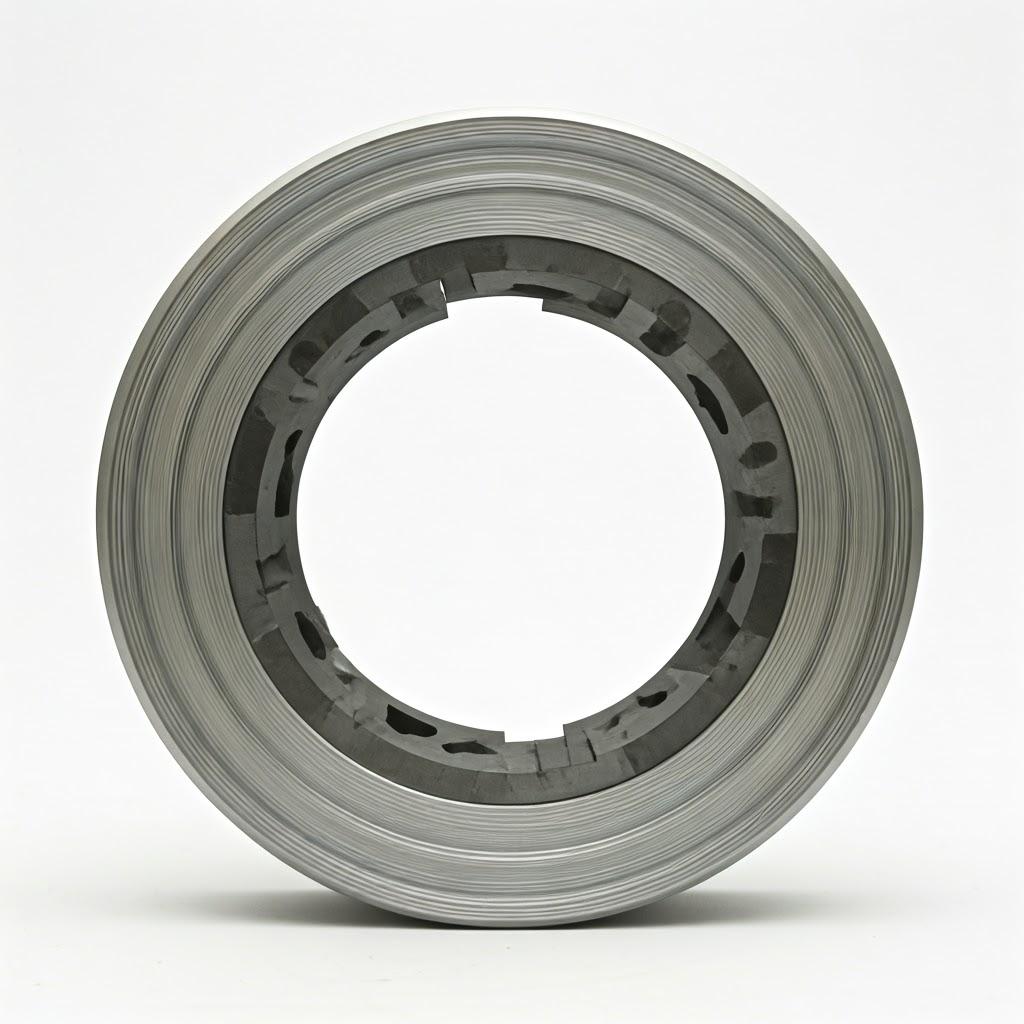
Selecting Your Manufacturing Partner: Finding the Best Metal 3D Printing Service Provider
Choosing the right manufacturing partner is as critical as perfecting the design or selecting the ideal material when adopting metal additive manufacturing for demanding applications like EV motor shaft housings. The difference between a successful AM implementation and a frustrating experience often hinges on the capabilities, expertise, and quality commitment of your chosen service provider. For engineers and procurement managers navigating the landscape of metal AM suppliers, evaluating potential partners requires looking beyond just price and considering a comprehensive set of factors.
Metal AM Hizmet Sağlayıcılarını Değerlendirmek için Temel Kriterler:
- Proven Expertise and Experience:
- Track Record: Look for a provider with demonstrable experience in producing complex metal parts, ideally within the automotive sector or specifically for EV powertrain components. Case studies, testimonials, and examples of past projects are valuable indicators.
- Malzeme Uzmanlığı: Ensure they have extensive experience processing the specific materials you intend to use (e.g., AlSi10Mg, 17-4PH). Different alloys require different parameter sets and handling procedures. Ask about their experience with similar applications and materials.
- Industry Knowledge: Do they understand the specific requirements and challenges of the automotive industry, such as NVH, thermal management, durability, and regulatory compliance?
- Technical Capabilities & Equipment:
- Technology Match: Do they operate the appropriate AM technology (e.g., Laser Powder Bed Fusion – LPBF/SLM, Electron Beam Melting – EBM) best suited for your housing’s requirements (resolution, material, features)?
- Machine Park: Assess the quality, quantity, and build volume of their printers. A diverse and modern machine park (like the systems offered by Met3dp) suggests capacity, redundancy, and access to the latest technology for accuracy and reliability. Consider build envelope size for larger housings.
- Material Portfolio & Quality Control: Do they offer the certified materials you need? Critically, evaluate their powder handling and quality control processes. Do they source from reputable suppliers or, like Met3dp, manufacture their own high-quality powders using advanced methods like VIGA or PREP, ensuring consistency and traceability? Ask about powder recycling procedures and batch testing.
- Kalite Yönetim Sistemi (KYS) & Sertifikalar:
- Sertifikalar: ISO 9001 certification is a baseline requirement for quality management. For automotive series production, IATF 16949 certification is highly desirable, indicating adherence to stringent automotive quality standards. Ask what certifications the provider holds.
- Kalite Kontrol Prosedürleri: Understand their QC process throughout the workflow – from incoming powder inspection to in-process monitoring (e.g., melt pool monitoring), post-processing checks, and final inspection (dimensional, NDT).
- Traceability: Ensure they have robust systems for material batch traceability and process documentation, crucial for automotive compliance.
- Integrated Post-Processing Capabilities:
- In-House vs. Networked: Does the provider offer essential post-processing steps (stress relief, heat treatment, support removal, CNC machining, surface finishing) in-house, or do they manage a network of trusted partners? In-house capabilities often lead to better integration, control, and potentially faster lead times.
- Machining Expertise: Given the need for precise machining on critical features of housings, evaluate their CNC machining capabilities or their relationship with qualified machine shops experienced with AM parts.
- NDT Capabilities: Access to Non-Destructive Testing, especially CT scanning for internal inspection, is crucial for verifying the integrity of complex housings.
- Engineering and Design Support:
- DfAM Expertise: A valuable partner should offer Design for Additive Manufacturing (DfAM) support, helping you optimize your housing design to leverage AM benefits fully (lightweighting, feature integration, support reduction).
- Simulation Capabilities: Can they perform build process simulation to predict and mitigate potential issues like distortion or thermal stress?
- Collaborative Approach: Look for a partner willing to work collaboratively with your engineering team, providing feedback and suggestions for improvement.
- Capacity, Lead Times, and Scalability:
- Capacity: Can they accommodate your required volumes, from single prototypes to low- or medium-volume production runs?
- Lead Time Transparency: Do they provide realistic and reliable lead time estimates for printing and post-processing? How do they communicate progress and potential delays?
- Ölçeklenebilirlik: If you anticipate increasing production volumes, does the provider have the capacity or a clear plan to scale up?
- Cost Structure and Communication:
- Transparent Pricing: Is their quoting process clear and detailed, breaking down costs associated with material, printing, supports, and post-processing?
- Responsiveness: How quickly and effectively do they respond to inquiries, technical questions, and requests for quotes? Good communication is vital throughout the project lifecycle.
Finding a partner like Met3dp, which not only develops and manufactures its own industry-leading AM systems and yüksek kaliteli metal tozları but also offers comprehensive application development services, can provide a distinct advantage. Their integrated approach, rooted in deep expertise across the entire metal AM value chain, ensures a holistic understanding of the process, from powder characteristics to final part performance. Their focus on delivering solutions for mission-critical parts in demanding industries like aerospace, medical, and automotive positions them as a knowledgeable and capable partner for developing innovative EV components. Taking the time to thoroughly vet potential suppliers against these criteria will significantly increase the likelihood of a successful outcome for your EV motor shaft housing project.
Understanding Costs and Lead Times for 3D Printed EV Motor Shaft Housings
While the technical benefits of metal 3D printing for EV motor shaft housings are compelling, understanding the associated costs and typical timelines is crucial for project planning, budgeting, and making informed manufacturing decisions. Both cost and lead time can vary significantly based on a multitude of factors.
Factors Influencing the Cost of 3D Printed Housings:
- Material Type and Volume:
- Toz Maliyeti: Different metal powders have vastly different costs per kilogram. Aluminum alloys like AlSi10Mg are generally more affordable than stainless steels like 17-4PH, titanium alloys, or nickel superalloys.
- Part Volume: The sheer volume of the housing directly impacts the amount of powder consumed. DfAM techniques like topology optimization and lattice structures are key to reducing material usage and thus cost.
- Support Structure Volume: Supports also consume material and add to the overall powder usage. Minimizing supports through DfAM reduces cost.
- AM Machine Time:
- Yapım süresi: This is often the most significant cost driver. It depends on:
- Part Height: Taller parts require more layers, increasing print time.
- Part Volume/Complexity: More material to melt per layer and complex scan paths increase time.
- Number of Parts per Build: Nesting multiple housings or other parts onto a single build plate maximizes machine utilization and reduces the effective machine time cost per part.
- Layer Thickness & Parameters: Thicker layers print faster but reduce resolution and surface finish; thinner layers improve detail but increase time. Optimized parameters balance speed and quality.
- Machine Depreciation & Operational Costs: The cost of acquiring, operating (power, gas), and maintaining expensive industrial metal AM systems is factored into the hourly machine rate.
- Yapım süresi: This is often the most significant cost driver. It depends on:
- Tasarım Karmaşıklığı:
- Yazdırılabilirlik: Highly complex designs with intricate features or extensive overhangs may require more sophisticated support strategies and longer print times.
- İşlem sonrası: Complex internal channels or features can make depowdering and support removal more challenging and time-consuming.
- Support Structure Requirements:
- Hacim: As mentioned, supports use material and add print time.
- Removal Labor: Removing supports, especially intricate or internal ones, requires manual labor or dedicated machining time, adding significant cost.
- Post-Processing Intensity:
- Heat Treatments: Stress relief and aging cycles require furnace time and energy. Complex or multiple cycles add cost.
- CNC İşleme: The extent of machining required for critical tolerances significantly impacts cost. More features requiring tight tolerances mean more machining setup and runtime. 5-axis machining is more expensive than 3-axis.
- Yüzey İşlemi: Basic blasting is relatively inexpensive, while extensive polishing, anodizing, or coating adds cost through labor, materials, and specialized equipment.
- Teftiş: Basic dimensional checks are standard, but extensive CMM programming/runtime or NDT like CT scanning adds considerable cost, reserved for critical applications or qualification parts.
- İşçilik Maliyetleri:
- Includes machine setup, build monitoring, depowdering, support removal, part handling, machining, finishing, inspection, and quality assurance documentation.
- Sipariş Hacmi:
- Prototipler: Typically have the highest per-part cost due to setup, programming, and lack of optimization for volume.
- Low-to-Medium Volume: Costs per part decrease as processes are optimized, build plates are nested efficiently, and some automation may be employed. Economies of scale become more apparent.
Factors Influencing Lead Times:
- Design Finalization & Preparation: Time required for DfAM review, build simulation, support generation, and build file preparation. (Can be 1-5 days).
- Machine Queue Time: Availability of the appropriate AM machine. Popular machines or materials may have backlogs. (Can range from days to weeks).
- Print Time: The actual duration of the AM build process. (Typically 12 hours to several days, depending on part size, height, and quantity per build).
- İşlem sonrası: This often constitutes a significant portion of the total lead time.
- Cooling & Depowdering: (Hours to 1 day).
- Stres Giderici: (1 day, including furnace cycle and cooling).
- Part Removal & Support Removal: (Hours to days, depending on complexity).
- Heat Treatment (Aging): (1-2 days, including furnace cycles and cooling).
- CNC İşleme: (Days to weeks, depending on complexity, fixture design, machine availability).
- Surface Finishing & Inspection: (Days to a week or more, depending on requirements).
- Nakliye: Transit time to your facility.
Typical Lead Time Estimates (Highly Variable):
- Prototipler: 1 to 3 weeks is common, assuming rapid quoting, minimal queue time, and standard post-processing.
- Low Volume Production Batches (e.g., 10-100 units): 4 to 8 weeks might be expected, allowing for optimized nesting, batch post-processing, and scheduling of resources like machining centers.
Conclusion on Cost & Lead Time: While potentially faster than tooling-based methods for initial prototypes, the overall lead time for fully finished, production-quality metal AM parts involves significant post-processing time. Costs are driven by material, machine time, and post-processing intensity. Obtaining detailed quotes from potential suppliers based on finalized designs and clearly defined requirements is essential for accurate budgeting and planning. Open communication with your AM partner about cost drivers and lead time expectations is key to a successful project.
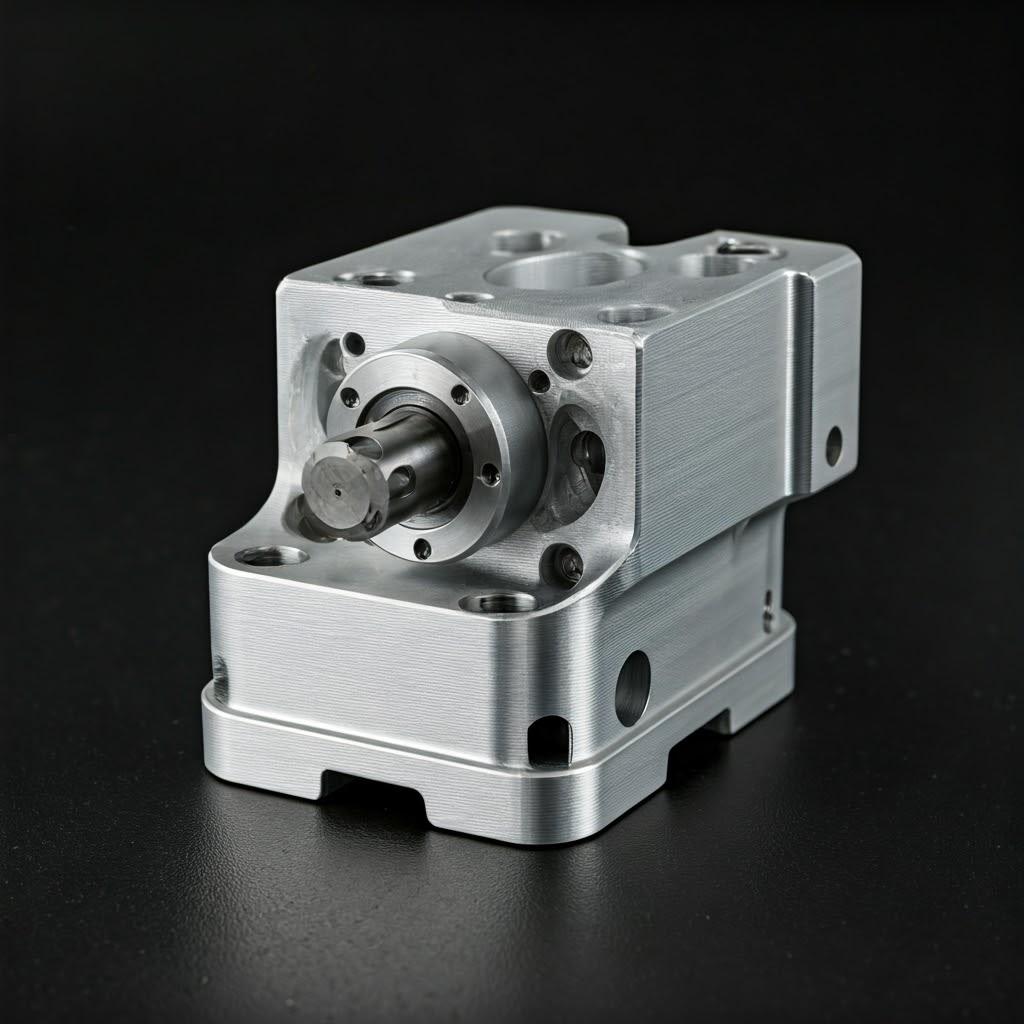
FAQ: Metal 3D Printed EV Motor Shaft Housings
Here are answers to some frequently asked questions regarding the use of metal additive manufacturing for EV motor shaft housings:
Q1: What are the main advantages of using metal 3D printing for EV motor housings compared to traditional casting?
A: Metal 3D printing offers several key advantages over traditional casting for EV motor housings: * Tasarım Özgürlüğü: Enables highly complex geometries, including topology-optimized structures and integrated conformal cooling channels, which are difficult or impossible to cast. * Hafifletme: Allows for significant weight reduction (often 30-60%) while maintaining or improving stiffness, crucial for enhancing EV range and performance. * Rapid Prototyping & Iteration: Facilitates much faster design cycles, allowing engineers to test and refine housing designs quickly without waiting for expensive and time-consuming tooling modifications. * Parça Konsolidasyonu: Enables the integration of multiple components (e.g., brackets, mounts) into a single printed part, reducing assembly complexity, weight, and potential failure points. * Improved Thermal Management: Integrated conformal cooling channels offer superior heat dissipation compared to conventional designs, allowing for higher motor power density. * Alet Eliminasyonu: Avoids the high upfront cost and long lead times associated with casting molds or dies, making it cost-effective for prototypes, low-to-medium volumes, and customized designs.
Q2: Which material is generally better for an EV motor housing: AlSi10Mg or 17-4PH Stainless Steel?
A: There isn’t a single “better” material; the choice depends entirely on the specific performance priorities and operating conditions of the EV motor: * Choose AlSi10Mg if: The primary goal is minimizing weight (due to its low density) and leveraging its good termal iletkenlik for heat dissipation. It’s suitable for applications with moderate operating temperatures and mechanical loads where its favourable strength-to-weight ratio is sufficient (often enhanced by topology optimization). It is also generally more cost-effective. * Choose 17-4PH Stainless Steel if: High strength, stiffness, hardness, and durability are paramount, or if the housing experiences elevated operating temperatures veya gerektirir üstün korozyon di̇renci̇. Its high strength allows for potentially thinner walls in certain areas, but its high density means aggressive design optimization is needed to save weight. Its lower thermal conductivity must be accounted for in the thermal management strategy (e.g., relying more on integrated liquid cooling).
Q3: Is metal 3D printing suitable for mass production of EV motor housings?
A: Metal 3D printing is increasingly viable for series productionözellikle de low-to-medium volumes (hundreds to potentially thousands of parts per year) or for applications where its unique benefits justify a potentially higher per-part cost compared to high-volume casting. * Strengths for Production: Ideal for highly complex, optimized designs where performance gains outweigh cost premiums; offers flexibility for design variations or customized batches; avoids tooling investment. * Challenges for Mass Production: For very high volumes (tens or hundreds of thousands per year), traditional die casting often remains more cost-effective due to faster cycle times once tooling is made. However, AM machine speeds are increasing, multi-laser systems enhance productivity, and automation in post-processing is improving. * Current Status: It’s often used for performance variants, niche EV models, pre-production runs, or specific components where its advantages are critical. A thorough cost-benefit analysis comparing optimized AM designs with traditional methods is necessary for each specific case. The technology is rapidly evolving, making it progressively more competitive for larger volumes.
Q4: What quality standards and inspections should I expect for 3D printed automotive components like motor housings?
A: For automotive components, especially those in the powertrain, rigorous quality control is essential. You should expect or specify the following: * Quality Management System: The provider should operate under a certified QMS, ideally IATF 16949 for automotive series production, or at minimum ISO 9001. * Malzeme Sertifikasyonu: Full traceability of powder batches and certification verifying chemical composition and properties according to relevant standards (e.g., ASTM, ISO). * Process Control & Documentation: Documented procedures for printing, heat treatment, machining, etc., with records maintained for traceability. In-process monitoring data if available. * Boyutsal Muayene: Verification of critical dimensions and tolerances using calibrated equipment like CMMs or 3D scanners, with reports provided. Comparison to the nominal CAD model and GD&T specifications. * Tahribatsız Muayene (NDT): Depending on criticality, CT scanning is highly recommended to inspect internal integrity (porosity, defects, channel clearance) and verify complex internal geometries. Dye penetrant or other surface inspection methods may also be required. * Mechanical Property Verification: Hardness testing on the final part. Tensile testing performed on sample coupons printed alongside the components to verify that heat treatments achieved the required material properties (yield strength, tensile strength, elongation). * Leak Testing: If applicable (e.g., for integrated cooling channels), pressure decay or other leak testing methods should be performed.
Conclusion: Accelerating EV Innovation with Metal Additive Manufacturing
The journey towards sustainable transportation is inextricably linked with innovation in electric vehicle technology. At the core of this evolution lies the powertrain, where components like the EV motor shaft housing play a critical, albeit often unsung, role. As we’ve explored, metal additive manufacturing is fundamentally reshaping how these essential components can be designed, optimized, and produced. Moving beyond the constraints of traditional casting and machining, metal AM empowers engineers to achieve unprecedented levels of performance and efficiency.
The ability to leverage Katmanlı Üretim Tasarımı (DfAM) unlocks truly optimized structures through topology optimization and lattice infill, resulting in significant hafifletme – a key factor in extending EV range. The geometric freedom inherent in AM allows for the seamless integration of complex features, most notably conformal cooling channels that promise revolutionary improvements in thermal management, enabling higher power densities and more compact motor designs. Furthermore, the capacity for parça konsoli̇dasyonu simplifies assembly, reduces potential failure points, and contributes further to weight savings.
While the choice of material – whether the lightweight and thermally conductive AlSi10Mg or the high-strength, durable 17-4PH paslanmaz çelik – depends on specific application demands, the quality of the metal powder feedstock is universally critical. Advanced powder production techniques ensure the material consistency needed for reliable printing. Achieving the required hassas necessitates a combination of accurate AM systems and targeted post-processing, particularly CNC işleme for critical interfaces and appropriate ısıl işlemler to optimize material properties and ensure dimensional stability.
Successfully navigating the adoption of metal AM also involves acknowledging and overcoming challenges related to residual stress, porosity, and support removal, often through careful process control and DfAM strategies. Crucially, selecting a manufacturing partner with deep expertise, robust quality systems, comprehensive capabilities (including post-processing), and a collaborative approach is paramount. Understanding the factors driving cost and lead time allows for realistic project planning and evaluation of AM’s value proposition against conventional methods, especially as the technology matures towards higher volume production.
In conclusion, metal 3D printing is not merely an alternative manufacturing method for EV motor shaft housings; it is an enabling technology that accelerates innovation. It provides the tools to create lighter, stronger, more efficient, and functionally integrated components faster than ever before. As the electric vehicle market continues its exponential growth, metal additive manufacturing will undoubtedly play an increasingly vital role in shaping the next generation of powertrains.
For companies looking to explore the potential of metal AM for their EV components or other demanding applications, partnering with a leader in the field is essential. Met3dp, with its comprehensive portfolio of advanced SEBM printers, yüksek performanslı metal tozları, and extensive application expertise, stands ready to help you harness the power of additive manufacturing. We encourage you to visit our website or contact us to discuss how our solutions can drive your organization’s additive manufacturing goals and accelerate your path to innovation.
Paylaş
MET3DP Technology Co, LTD, merkezi Qingdao, Çin'de bulunan lider bir katmanlı üretim çözümleri sağlayıcısıdır. Şirketimiz, endüstriyel uygulamalar için 3D baskı ekipmanları ve yüksek performanslı metal tozları konusunda uzmanlaşmıştır.
İşletmeniz için en iyi fiyatı ve özelleştirilmiş Çözümü almak için sorgulayın!
İlgili Makaleler
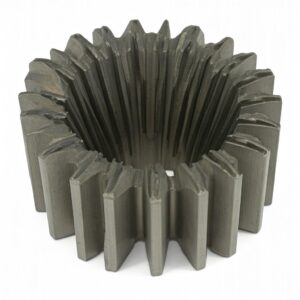
Yüksek Performanslı Nozul Kanat Segmentleri: Metal 3D Baskı ile Türbin Verimliliğinde Devrim
Daha Fazla Oku "Met3DP Hakkında
Son Güncelleme
Bizim Ürünümüz
BİZE ULAŞIN
Herhangi bir sorunuz var mı? Bize şimdi mesaj gönderin! Mesajınızı aldıktan sonra tüm ekibimizle talebinize hizmet edeceğiz.
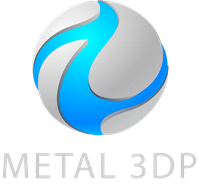
3D Baskı ve Katmanlı Üretim için Metal Tozları